Introdução de um método de recuperação profunda de calor de gases de combustão. Dispositivo de recuperação de calor de gases de combustão e método de operação. Comparação de tecnologias de recuperação de calor de produtos de combustão
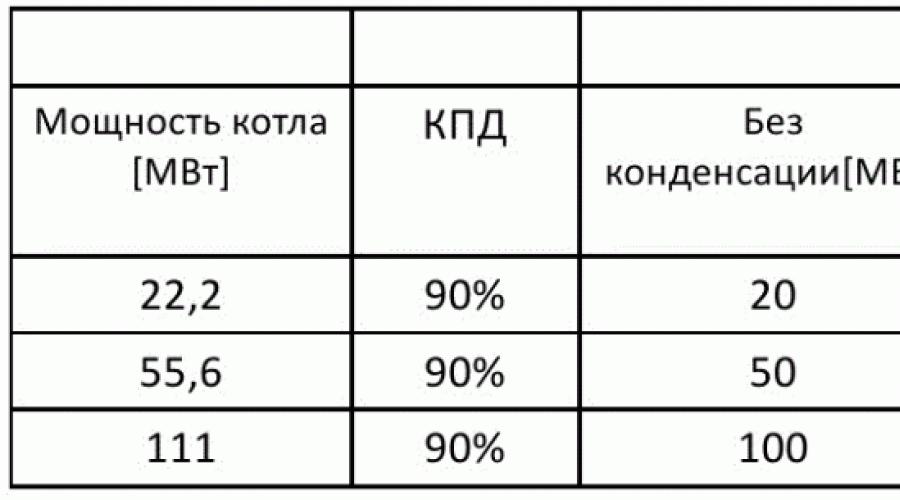
Avaliação da eficiência da recuperação profunda da produção de combustão de caldeiras de usinas
POR EXEMPLO. Shadek, Candidato a Engenharia, especialista independente
Palavras-chave: produtos de combustão, recuperação de calor, equipamentos de caldeiras, eficiência energética
Um dos métodos para resolver o problema da economia de combustível e melhoria da eficiência energética das caldeiras é o desenvolvimento de tecnologias para recuperação profunda do calor dos gases de exaustão das caldeiras. Oferecemos um esquema de processo de uma usina com unidades de turbina a vapor (STU) que permite a recuperação profunda do calor dos produtos de combustão da caldeira do condensador STU usando resfriador-condensado com custos mínimos sem o uso de unidades de bomba de calor.
Descrição:
Uma das formas de solucionar o problema de economia de combustível e aumento da eficiência energética das caldeiras é desenvolver tecnologias para aproveitamento profundo do calor dos gases de exaustão das caldeiras. Propomos um esquema tecnológico de uma usina com unidades de turbina a vapor (STU). ), que permite, com custo mínimo, sem a utilização de unidades de bomba de calor, realizar o aproveitamento profundo do calor dos gases de exaustão da caldeira devido à presença de um resfriador - condensado do condensador PTU.
EG Shadek, Ph.D. tecnologia. ciências, especialista independente
Uma das maneiras de resolver o problema de economia de combustível e aumento da eficiência energética das caldeiras é desenvolver tecnologias para o aproveitamento profundo do calor dos gases de combustão das caldeiras. Oferecemos um esquema tecnológico de uma usina com unidades de turbina a vapor (STU), que permite, com um custo mínimo, sem a utilização de unidades de bomba de calor, realizar um aproveitamento profundo do calor dos produtos de combustão que saem da caldeira devido à presença de um resfriador - condensado do condensador STU.
A utilização profunda do calor dos produtos de combustão (CP) é garantida quando eles são resfriados abaixo da temperatura do ponto de orvalho, igual a 50–55 0 C para CP do gás natural. Neste caso, ocorrem os seguintes fenômenos:
- condensação de vapor de água (até 19–20% do volume ou 12–13% do peso dos produtos de combustão),
- utilização do calor físico do PS (40–45% do conteúdo total de calor),
- utilização do calor latente de vaporização (60–55%, respectivamente).
Foi estabelecido anteriormente que a economia de combustível durante a utilização profunda em comparação com uma caldeira com eficiência de passaporte (máxima) de 92% é de 10–13%. A relação entre a quantidade de calor recuperado e a potência térmica da caldeira é de cerca de 0,10–0,12, e a eficiência da caldeira no modo de condensação é de 105% com base no poder calorífico inferior do gás.
Além disso, durante a reciclagem profunda na presença de vapor de água no PS, a emissão de emissões nocivas é reduzida em 20–40% ou mais, o que torna o processo amigo do ambiente.
Outro efeito da reciclagem profunda é a melhoria das condições e da vida útil do caminho do gás, uma vez que a condensação está localizada na câmara onde está instalado o trocador de calor de recuperação, independentemente da temperatura do ar externo.
Reciclagem profunda para sistemas de aquecimento
Nos países ocidentais avançados, a utilização profunda para sistemas de aquecimento é realizada por meio de caldeiras de água quente do tipo condensação equipadas com um economizador de condensação.
A temperatura geralmente baixa da água de retorno (30–40 0 C) com um cronograma de temperatura típico, por exemplo 70/40 0 C, nos sistemas de aquecimento desses países permite a recuperação profunda de calor em um economizador de condensação equipado com coleta e remoção de condensado e unidade de tratamento (e posteriormente utilizá-la para alimentar a caldeira). Este esquema garante o modo de funcionamento de condensação da caldeira sem refrigerante artificial, ou seja, sem a utilização de unidade de bomba de calor.
A eficácia e rentabilidade da reciclagem profunda para caldeiras de aquecimento não necessitam de comprovação. As caldeiras de condensação são amplamente utilizadas no Ocidente: até 90% de todas as caldeiras fabricadas são de condensação. Essas caldeiras também são utilizadas em nosso país, embora não as produzamos.
Na Rússia, ao contrário dos países com climas quentes, a temperatura na linha de retorno das redes de aquecimento é geralmente superior ao ponto de orvalho, e a utilização profunda só é possível em sistemas de quatro tubos (que são extremamente raros) ou quando se utilizam bombas de calor. A principal razão para o atraso da Rússia no desenvolvimento e implementação da utilização profunda é o baixo preço do gás natural, os elevados custos de capital devido à inclusão de bombas de calor no esquema e os longos períodos de retorno.
Reciclagem profunda para caldeiras de usinas de energia
A eficiência de utilização profunda para caldeiras de usinas de energia (Fig. 1) é significativamente maior do que para caldeiras de aquecimento, devido à carga estável (KIM = 0,8–0,9) e grandes capacidades unitárias (dezenas de megawatts).
Vamos estimar o recurso térmico dos produtos de combustão das caldeiras das estações, tendo em conta a sua elevada eficiência (90–94%). Este recurso é determinado pela quantidade de calor residual (Gcal/h ou kW), que depende unicamente da potência térmica da caldeira P K e temperatura atrás de caldeiras a gás T 1УХ, que na Rússia é aceito em temperaturas não inferiores a 110–130 0 C por dois motivos:
- aumentar a tiragem natural e reduzir a pressão (consumo de energia) do exaustor de fumos;
- para evitar a condensação de vapor de água em porcos, condutas e chaminés.
Análise estendida de uma grande variedade 1 de dados experimentais de testes de equilíbrio e comissionamento realizados por organizações especializadas, mapas de desempenho, estatísticas de relatórios de estações, etc. e os resultados dos cálculos de valores de perda de calor com produtos de combustão de exaustão q 2 , a quantidade de calor recuperado 2 P UT e seus indicadores derivados em uma ampla gama de cargas de caldeiras de estações são apresentados na Tabela. 13. O objetivo é determinar q 2 e proporções de quantidades P K, q 2 e P UT em condições típicas de operação de caldeira (Tabela 2). No nosso caso, não importa qual caldeira: vapor ou água quente, industrial ou aquecimento.
Tabela de indicadores. 1, destacados em azul, foram calculados usando o algoritmo (ver ajuda). Cálculo do processo de reciclagem profunda (definição P UT, etc.) foram realizados de acordo com a metodologia de engenharia fornecida e descrita em. O coeficiente de transferência de calor “produtos de combustão – condensado” no trocador de calor de condensação foi determinado de acordo com a metodologia empírica do fabricante do trocador de calor (OJSC Heating Plant, Kostroma).
Os resultados indicam a alta eficiência econômica da tecnologia de utilização profunda para caldeiras de estação e a rentabilidade do projeto proposto. O período de retorno dos sistemas varia de 2 anos para uma caldeira de potência mínima (Tabela 2, caldeira nº 1) a 3–4 meses. Os índices resultantes β, φ, σ, bem como os itens de economia (Tabela 1, linhas 8–10, 13–18) permitem avaliar imediatamente as capacidades e indicadores específicos de um determinado processo, caldeira.
Recuperação de calor em um aquecedor a gás
O esquema tecnológico usual de uma usina envolve o aquecimento do condensado em um aquecedor a gás (parte das superfícies traseiras da caldeira, economizador) utilizando os gases de combustão que saem da caldeira.
Após o condensador, o condensado é enviado por bombas (às vezes através de uma unidade de dessalinização em bloco - doravante denominada BOU) para um aquecedor a gás, após o qual entra no desaerador. Quando a qualidade do condensado é normal, a unidade de tratamento de água é desviada. Para evitar a condensação do vapor de água dos gases de combustão nos últimos tubos do aquecedor a gás, a temperatura do condensado à sua frente é mantida em pelo menos 60 0 C pela recirculação do condensado aquecido para a entrada.
Para reduzir ainda mais a temperatura dos gases de combustão, um trocador de calor água-água resfriado pela água de reposição da rede de aquecimento é frequentemente incluído na linha de recirculação de condensado. O aquecimento da água da rede é realizado pelo condensado de um aquecedor a gás. Com o resfriamento adicional dos gases em 10 0 C, podem ser obtidos cerca de 3,5 Gcal/h de carga de aquecimento em cada caldeira.
Para evitar que o condensado ferva no aquecedor a gás, válvulas de controle de alimentação são instaladas atrás dele. Seu principal objetivo é distribuir o fluxo de condensado entre as caldeiras de acordo com a carga térmica da unidade de turbina a vapor.
Sistema de recuperação profunda com trocador de calor de condensação
Como pode ser visto no diagrama de fluxo (Fig. 1), o vapor condensado do coletor de condensado é fornecido pela bomba 14 para o tanque coletor 21, e daí para o coletor de distribuição 22. Aqui, o condensado, usando o controle automático da estação sistema (veja abaixo), é dividido em duas correntes: uma é fornecida à unidade de utilização profunda 4, ao trocador de calor de condensação 7, e a segunda ao aquecedor de baixa pressão (LPH) 18, e depois ao desaerador 15. O a temperatura do vapor condensado do condensador da turbina (cerca de 20–35 0 C) permite que os produtos de combustão sejam resfriados no trocador de calor do condensador 7 até os 40 0 C necessários, ou seja, garantem uma utilização profunda.
O vapor condensado aquecido do trocador de calor de condensação 7 é alimentado através do HDPE 18 (ou desvio 18) para o desaerador 15. O condensado do produto de combustão obtido no trocador de calor de condensação 7 é drenado para a panela e tanque 10. A partir daí é alimentado no tanque de condensado contaminado 23 e bombeado pela bomba de drenagem 24 para o tanque reserva de condensado 25, a partir do qual a bomba de condensado 26 através do regulador de fluxo é fornecida para a seção de purificação de condensado de produtos de combustão (não mostrada na Fig. 1), onde é processado usando tecnologia conhecida. O condensado purificado dos produtos de combustão é fornecido ao HDPE 18 e depois ao desaerador 15 (ou diretamente ao 15). Do desaerador 15, um fluxo de condensado puro é fornecido pela bomba de alimentação 16 ao aquecedor de alta pressão 17 e deste à caldeira 1.
Assim, o calor dos produtos de combustão utilizados no trocador de calor de condensação economiza o combustível consumido no fluxograma do processo da usina para aquecimento do condensado da estação na frente do desaerador e no próprio desaerador.
O trocador de calor de condensação é instalado na câmara 35 na junção da caldeira 27 com o duto de gás (Fig. 2c). A carga térmica do trocador de calor de condensação é regulada por bypass, ou seja, pela remoção de parte dos gases quentes além do trocador de calor de condensação através do canal de bypass 37 com válvula borboleta (gate) 36.
O mais simples seria o esquema tradicional: um economizador de condensação, mais precisamente as seções traseiras do economizador da caldeira, como um aquecedor a gás, mas operando em modo de condensação, ou seja, resfriando os produtos da combustão abaixo da temperatura do ponto de orvalho. Mas, ao mesmo tempo, surgem dificuldades estruturais e operacionais (manutenção, etc.), exigindo soluções especiais.
Vários tipos de trocadores de calor são aplicáveis: casco e tubo, tubo reto, com aletas serrilhadas, placas ou um design eficiente com uma nova forma de superfície de troca de calor com um pequeno raio de curvatura (regenerador RG-10, NPC "Anod" ). Neste esquema, seções do bloco de troca de calor baseadas em um aquecedor bimetálico da marca VNV123-412-50ATZ (OJSC Heating Plant, Kostroma) são usadas como trocador de calor de condensação.
A escolha da disposição dos troços e das ligações de água e gás permite variar e garantir a velocidade da água e dos gases dentro dos limites recomendados (1–4 m/s). A chaminé, a câmara e o caminho do gás são feitos de materiais resistentes à corrosão, revestimentos, em particular aços inoxidáveis, plásticos - esta é uma prática geralmente aceita.
* Não há perdas de calor devido à combustão química incompleta.
Características de reciclagem profunda com trocador de calor de condensação
A elevada eficiência da tecnologia permite regular a potência térmica do sistema dentro de uma ampla faixa, mantendo a sua rentabilidade: o grau de bypass, a temperatura dos produtos de combustão atrás do trocador de calor de condensação, etc. trocador de calor de condensação QUT e, consequentemente, a quantidade de condensado fornecida a ele pelo coletor 22 (Fig. 1 ), é determinado como ideal (e não necessariamente máximo) de acordo com cálculos técnicos e econômicos e considerações de projeto, levando em consideração parâmetros operacionais , capacidades e condições do esquema tecnológico da caldeira e da estação como um todo.
Após o contato com os produtos da combustão do gás natural, o condensado mantém alta qualidade e requer limpeza simples e barata - descarbonização (e nem sempre é o caso) e desgaseificação. Após o tratamento no local de tratamento químico de água (não mostrado), o condensado é bombeado através de um regulador de fluxo para a linha de condensado da estação - para o desaerador e depois para a caldeira. Se o condensado não for aproveitado, ele é drenado para o esgoto.
Na unidade de coleta e processamento de condensado (Fig. 1, pos. 8, 10, Fig. 2, pos. 23-26), é usado equipamento padrão bem conhecido de sistemas de reciclagem profunda (ver, por exemplo).
A instalação produz uma grande quantidade de excesso de água (condensado de vapor de água proveniente da combustão de hidrocarbonetos e ar soprado), pelo que o sistema não necessita de ser recarregado.
Temperatura dos produtos de combustão na saída do trocador de calor de condensação T 2УХ é determinado pela condição de condensação do vapor de água nos produtos de combustão dos gases de escape (na faixa de 40–45 0 C).
Para evitar a formação de condensado no caminho do gás e principalmente na chaminé, é fornecido um desvio, ou seja, desviar parte dos produtos de combustão através de um canal de desvio além da unidade de utilização profunda para que a temperatura da mistura de gás atrás dele está na faixa de 70–90 0 C. Ignorar piora todos os indicadores do processo. O modo ideal é trabalhar com bypass na estação fria e no verão, quando não há perigo de condensação e formação de gelo, sem ele.
A temperatura dos gases de combustão da caldeira (geralmente 110–130 0 C) permite que o condensado seja aquecido no trocador de calor de condensação na frente do desaerador até os 90–100 0 C necessários. : tanto aquece o condensado (cerca de 90 0 C) quanto resfria a combustão dos produtos (até 40 0 C) até a condensação.
Comparação de tecnologias de recuperação de calor de produtos de combustão
Ao tomar uma decisão sobre o aproveitamento do calor dos produtos da combustão da caldeira, deve-se comparar a eficácia do sistema de aproveitamento profundo proposto e do esquema tradicional com um aquecedor a gás como o análogo e concorrente mais próximo.
Para o nosso exemplo (ver referência 1), obtivemos a quantidade de calor recuperada durante a utilização profunda P UT igual a 976 kW.
Assumimos que a temperatura do condensado na entrada do aquecedor de condensado a gás é de 60 0 C (veja acima), enquanto a temperatura dos produtos de combustão na saída dele é de pelo menos 80 0 C. Então o calor dos produtos de combustão utilizado no aquecedor a gás, ou seja, a economia de calor, será igual a 289 kW, o que é 3,4 vezes menor que no sistema de reciclagem profunda. Assim, o “preço de emissão” no nosso exemplo é de 687 kW, ou, numa base anual, 594.490 m 3 de gás (com KIM = 0,85) custando cerca de 3 milhões de rublos. O ganho aumentará com a potência da caldeira.
Vantagens da tecnologia de reciclagem profunda
Concluindo, podemos concluir que, além da economia de energia, com o aproveitamento profundo dos produtos da combustão da caldeira da usina, são alcançados os seguintes resultados:
- redução da emissão de óxidos tóxicos CO e NOx, garantindo a limpeza ambiental do processo;
- obter água adicional em excesso e, assim, eliminar a necessidade de água de reposição da caldeira;
- a condensação do vapor de água dos produtos de combustão está localizada em um local - no trocador de calor de condensação. Além do leve arrastamento de respingos após o eliminador de gotículas, a condensação no caminho de gás subsequente e a destruição associada dos dutos de gás devido aos efeitos corrosivos da umidade, a formação de gelo no caminho e especialmente na chaminé são eliminadas;
- em alguns casos, o uso de trocador de calor água-água torna-se opcional; não há necessidade de recirculação: misturar parte dos gases quentes com os resfriados (ou condensado aquecido com os frios) para aumentar a temperatura dos produtos da combustão de exaustão para evitar condensação no caminho do gás e na chaminé (economizando energia e dinheiro) .
Literatura
- Shadek E., Marshak B., Anokhin A., Gorshkov V. Recuperação profunda de calor de gases residuais de geradores de calor // Caldeiras industriais e de aquecimento e mini-CHPs. 2014. Nº 2 (23).
- Shadek E. Trigeração como tecnologia para economizar recursos energéticos // Economia de energia. 2015. Nº 2.
- Shadek E., Marshak B., Krykin I., Gorshkov V. Recuperação de trocador de calor de condensação – modernização de caldeiras // Caldeiras industriais e de aquecimento e mini-CHP. 2014. Nº 3 (24).
- Kudinov A. Economia de energia em instalações geradoras de calor. M.: Engenharia Mecânica, 2012.
- Ravich M. Método simplificado de cálculos termotécnicos. M.: Editora da Academia de Ciências da URSS, 1958.
- Berezinets P., Olkhovsky G. Tecnologias avançadas e usinas de energia para a produção de energia térmica e elétrica. Seção seis. 6.2 turbinas a gás e usinas de ciclo combinado a gás. 6.2.2. Usinas de ciclo combinado. JSC "VTI". “Tecnologias ambientais modernas no setor energético.” Coleta de informações ed. V. Ya. M.: Editora MPEI, 2007.
1 Fonte primária de dados: inspeção de caldeiras de água quente (11 unidades em três caldeiras de redes de aquecimento), coleta e processamento de materiais.
2 Metodologia de cálculo, em particular P UT, cedido.
Detentores da patente RU 2436011:
A invenção refere-se à engenharia de energia térmica e pode ser utilizada em qualquer empresa que opere caldeiras a combustíveis de hidrocarbonetos. O objetivo da invenção é aumentar a eficiência do uso do calor de condensação de baixo teor do vapor de água contido nos gases de combustão. O dispositivo de recuperação de calor dos gases de combustão contém um trocador de calor de placas de superfície gás-gás, no qual os gases de combustão originais são resfriados, aquecendo os gases de combustão secos em contracorrente. Os gases de combustão úmidos resfriados são alimentados em um trocador de calor-condensador de placas de superfície gás-ar, onde o vapor de água contido nos gases de combustão é condensado, aquecendo o ar. O ar aquecido é utilizado para aquecer as instalações e cobrir as necessidades do processo de combustão do gás na caldeira. O condensado após processamento adicional é usado para compensar perdas na rede de aquecimento ou no ciclo da turbina a vapor. Os gases de combustão secos são fornecidos por um exaustor de fumos adicional ao aquecedor descrito acima, onde são aquecidos para evitar possível condensação de vapor de água nas condutas de fumos e na chaminé e são direcionados para a chaminé. 2 n.p. voar, 1 doente.
A invenção refere-se à engenharia de energia térmica e pode ser utilizada em qualquer empresa que opere caldeiras a combustíveis de hidrocarbonetos.
Uma instalação de caldeira conhecida contém um esquentador de contacto ligado na entrada à conduta de gases de escape da caldeira, e na saída através de uma conduta de saída de gases equipada com exaustor de fumos para a chaminé, e um esquentador com aquecimento e vias de ar ( Certificado de Direitos Autorais da URSS nº 1086296, F22B 1/18 datado de 15.04 1984).
A instalação funciona da seguinte maneira. A maior parte dos gases da caldeira entra na conduta de exaustão e o resto dos gases entra na conduta de aquecimento. Da chaminé de exaustão, os gases são direcionados para um aquecedor de água de contato, onde ocorre a condensação do vapor d'água contido nos gases de combustão. Os gases então passam pelo eliminador de gotas e entram no canal de saída de gases. O ar externo entra no aquecedor de ar, onde é aquecido pelos gases que passam pelo caminho de aquecimento, e é direcionado para o canal de saída dos gases, onde se mistura com os gases resfriados e reduz o teor de umidade destes.
Imperfeições. Qualidade inaceitável da água aquecida para utilização no sistema de aquecimento. Utilização de ar aquecido apenas para fornecê-lo à chaminé, a fim de evitar a condensação do vapor d'água. Baixo grau de recuperação de calor dos gases de combustão, uma vez que a principal tarefa era secar os gases de combustão e reduzir a temperatura do ponto de orvalho.
Os aquecedores do tipo KSk (Kudinov A.A. Economia de energia em instalações de geração de calor. - Ulyanovsk: UlSTU, 2000. - 139, p. 33), constituídos por um trocador de calor de superfície gás-água, são conhecidos comercialmente produzidos pela Usina de Aquecimento de Kostroma. cuja superfície de troca de calor é composta por tubos bimetálicos aletados, filtro, válvula de distribuição, eliminador de gotejamento e soprador hidropneumático.
Os aquecedores do tipo KSk funcionam da seguinte forma. Os gases de combustão entram na válvula de distribuição, que os divide em dois fluxos, o fluxo principal do gás é direcionado através de um filtro de malha para o trocador de calor, o segundo através da linha de desvio da chaminé. No trocador de calor, o vapor d'água contido nos gases de combustão condensa-se em tubos aletados, aquecendo a água que neles flui. O condensado resultante é coletado em uma panela e bombeado para o circuito de alimentação da rede de aquecimento. A água aquecida no trocador de calor é fornecida ao consumidor. Na saída do recuperador de calor, os gases de combustão secos são misturados com os gases de combustão originais da linha de derivação de fumos e enviados através de um exaustor de fumos para a chaminé.
Imperfeições. Para que o trocador de calor opere no modo de condensação de toda a sua parte convectiva, é necessário que a temperatura de aquecimento da água no pacote convectivo não ultrapasse 50°C. Para usar essa água em sistemas de aquecimento, ela deve ser aquecida adicionalmente.
Para evitar a condensação do vapor de água residual dos gases de combustão nas condutas e na chaminé, parte dos gases de origem é misturada através de um canal de derivação com os gases de combustão secos, aumentando a sua temperatura. Com esta mistura, o teor de vapor de água nos gases de combustão também aumenta, reduzindo a eficiência da recuperação de calor.
Uma instalação conhecida para reciclagem de calor de gases de combustão (patente RF nº 2193727, F22B 1/18, F24H 1/10 datada de 20 de abril de 2001), contendo um sprinkler instalado no duto de gás com bicos de distribuição, um trocador de calor de recuperação e um trocador de calor de refrigerante intermediário, cujo caminho aquecido é conectado na entrada ao coletor de umidade. O sprinkler está localizado na frente dos trocadores de calor especificados, instalados um em frente ao outro e à mesma distância do sprinkler, cujos bicos são direcionados no sentido oposto aos trocadores de calor. A instalação está adicionalmente equipada com um permutador de calor para reaquecimento da água de rega instalado na conduta de gás e localizado acima do aspersor, cujo percurso aquecido está ligado na entrada ao permutador de calor do refrigerante intermédio e na saída ao aspersor. Todos os trocadores de calor são superficiais, tubulares. Os tubos podem ter aletas para aumentar a superfície de aquecimento.
Existe um método conhecido de operação desta instalação (patente RF nº 2193728, F22B 1/18, F24H 1/10 datada de 20 de abril de 2001), segundo o qual os gases de combustão que passam pelo duto de combustão são resfriados abaixo do ponto de orvalho e removido da instalação. Na instalação, a água é aquecida num permutador de calor de recuperação e distribuída ao consumidor. A superfície externa do trocador de calor de recuperação é irrigada com um refrigerante intermediário - água de um aspersor com bicos distribuidores direcionados ao fluxo de gases. Neste caso, o refrigerante intermediário é pré-aquecido em um trocador de calor instalado no duto de gás oposto ao trocador de calor de recuperação e à mesma distância do sprinkler que o trocador de calor de recuperação. Em seguida, o refrigerante intermediário é fornecido a um trocador de calor para reaquecimento da água de irrigação instalada no duto de gás e localizado acima do sprinkler, aquecido até a temperatura desejada e enviado ao sprinkler.
Dois fluxos independentes de água circulam na instalação: limpo, aquecido através de uma superfície de transferência de calor, e irrigante, aquecido pelo contato direto com os gases de exaustão. Um fluxo limpo de água flui dentro dos tubos e é separado por paredes do fluxo contaminado de água de irrigação. Um feixe de tubos desempenha a função de um bico projetado para criar uma superfície de contato desenvolvida entre a água de irrigação e os gases de exaustão. A superfície externa do bico é lavada por gases e água de irrigação, o que intensifica a troca de calor no aparelho. O calor dos gases de exaustão é transferido para a água que flui no interior dos tubos do bico ativo de duas maneiras: 1) devido à transferência direta de calor dos gases e da água de irrigação; 2) devido à condensação na superfície do bico de parte do vapor d'água contido nos gases.
Imperfeições. A temperatura final da água aquecida na saída do bocal é limitada pela temperatura úmida dos gases no termômetro. Ao queimar gás natural com uma proporção de excesso de ar de 1,0-1,5, a temperatura de bulbo úmido dos gases de combustão é de 55-65°C. Esta temperatura não é suficiente para utilizar esta água no sistema de aquecimento.
Os gases de combustão saem do aparelho com umidade relativa de 95-100%, o que não exclui a possibilidade de condensação do vapor d'água dos gases no tubo de exaustão posterior.
O mais próximo da invenção reivindicada em termos de uso, essência técnica e resultado técnico alcançado é um trocador de calor (patente RF nº 2323384, F22B 18/01 de 30/08/2006), contendo um trocador de calor de contato, um eliminador de gotas, trocador de calor gás-gás conectado por circuito de fluxo direto, dutos de gás, tubulações, bomba, sensores de temperatura, válvulas de controle. Ao longo do fluxo de água circulante do trocador de calor de contato, um trocador de calor água-água e um trocador de calor água-ar com um canal de desvio ao longo do fluxo de ar estão localizados em série.
Método de operação do trocador de calor. Os gases de exaustão pelo duto de gás entram na entrada do trocador de calor gás-gás, passando sequencialmente por suas três seções, depois para a entrada do trocador de calor de contato, onde, passando por um bico lavado pela água circulante, são resfriados abaixo o ponto de orvalho, liberando calor sensível e latente para a água circulante. Em seguida, os gases resfriados e úmidos são liberados da maior parte da água líquida transportada em um eliminador de gotas, aquecidos e secos em pelo menos uma seção do trocador de calor gás-gás, enviados para uma chaminé por um exaustor de fumaça e liberados no atmosfera. Ao mesmo tempo, a água circulante aquecida da bandeja do trocador de calor de contato é bombeada para o trocador de calor água-água, onde aquece a água fria da tubulação. A água aquecida no permutador de calor é fornecida às necessidades de abastecimento de água quente de processo e sanitária ou a um circuito de aquecimento de baixa temperatura.
Em seguida, a água reciclada entra no trocador de calor água-ar, aquece pelo menos parte do ar soprado vindo de fora da sala através do duto de ar, resfriando até a temperatura mínima possível, e entra no trocador de calor de contato através do distribuidor de água, onde retira calor dos gases, lavando-os simultaneamente das partículas suspensas, e absorve alguns dos óxidos de nitrogênio e enxofre. O ar aquecido do trocador de calor é fornecido por um ventilador para um aquecedor de ar padrão ou diretamente para a fornalha. A água reciclada é filtrada, se necessário, e processada por métodos conhecidos.
As desvantagens deste protótipo são:
A necessidade de um sistema de controle devido à utilização do calor recuperado para fins de abastecimento de água quente devido à variabilidade da programação diária de consumo de água quente.
A água aquecida no permutador de calor, fornecida para as necessidades de abastecimento de água quente ou num circuito de aquecimento de baixa temperatura, necessita de ser levada à temperatura pretendida, uma vez que não pode ser aquecida no permutador de calor acima da temperatura do circuito de retorno água, que é determinada pela temperatura de saturação do vapor d'água nos gases de combustão. O baixo aquecimento do ar no trocador de calor água-ar não permite que esse ar seja utilizado para aquecimento ambiente.
A tarefa definida é simplificar a tecnologia de recuperação de calor e aumentar a eficiência do uso do calor de condensação de baixo teor do vapor de água contido nos gases de combustão.
Este problema é resolvido da seguinte maneira.
É proposto um dispositivo para recuperação de calor de gases de combustão, contendo um trocador de calor gás-gás, um condensador, um eliminador de gotejamento inercial, dutos de gás, dutos de ar, ventiladores e uma tubulação, caracterizado por o trocador de calor de placas de superfície gás-gás ser feito de acordo com um circuito de contrafluxo, um trocador de calor de placas gás-ar de superfície é instalado como condensador, em Um exaustor de fumaça adicional é instalado no duto de gás dos gases de combustão secos a frio, um duto de gás para misturar parte dos gases de combustão secos aquecidos; é instalado na frente do exaustor de fumaça adicional.
Também é proposto um método de operação de um dispositivo de recuperação de calor de gases de combustão, segundo o qual os gases de combustão são resfriados em um trocador de calor gás-gás, aquecendo os gases de combustão secos, o vapor de água contido nos gases de combustão é condensado no condensador, uma parte do ar de sopro é aquecida, caracterizada pelo fato de que no gás-gás em um trocador de calor, os gases de combustão secos são aquecidos pelo resfriamento dos gases de combustão originais usando um esquema de contrafluxo sem regulação da vazão do gás, o vapor de água é condensado em um trocador de calor-condensador de placa gás-ar de superfície, aquecendo o ar e o ar aquecido é usado para aquecer e cobrir as necessidades do processo de combustão, e o condensado após processamento adicional é usado para compensar perdas na rede de aquecimento ou vapor ciclo da turbina, no duto de gás dos gases de combustão secos a frio, a resistência aerodinâmica do caminho do gás é compensada por um exaustor de fumaça adicional, na frente do qual é misturada parte dos gases de combustão secos aquecidos, excluindo a condensação do vapor de água residual transportado afastada pelo fluxo do condensador, a temperatura do ar aquecido é regulada através de mudanças na velocidade do exaustor de fumaça dependendo da temperatura do ar externo.
Os gases de combustão da fonte são resfriados em um trocador de calor de placas de superfície gás-gás, aquecendo os gases de combustão secos.
A diferença é a utilização de um trocador de calor de placas de superfície sem nenhum controle de fluxo de gás, onde o meio de aquecimento (todo o volume dos gases de combustão úmidos) e o meio aquecido (todo o volume dos gases de combustão secos) se movem em contracorrente. Neste caso, ocorre um resfriamento mais profundo dos gases de combustão úmidos a uma temperatura próxima ao ponto de orvalho do vapor d'água.
Em seguida, o vapor de água contido nos gases de combustão é condensado em um trocador de calor-condensador de placa de superfície gás-ar, aquecendo o ar. O ar aquecido é utilizado para aquecer ambientes e atender às necessidades do processo de combustão. O condensado após processamento adicional é usado para compensar perdas na rede de aquecimento ou no ciclo da turbina a vapor.
A diferença entre o método proposto é que o meio aquecido é o ar frio fornecido pelos ventiladores do ambiente. O ar é aquecido de 30 a 50°C, por exemplo de -15 a 33°C. O uso de ar com temperatura negativa como meio de resfriamento permite aumentar significativamente a pressão da temperatura no condensador ao usar contrafluxo. O ar aquecido a 28-33°C é adequado para aquecimento ambiente e alimentação à caldeira para garantir a combustão do gás natural. O cálculo térmico do circuito mostra que o caudal do ar aquecido é 6 a 7 vezes superior ao caudal dos gases de combustão originais, o que permite cobrir totalmente as necessidades da caldeira, aquecer a oficina e outras instalações do empresa, e também fornecer parte do ar para a chaminé para reduzir a temperatura do ponto de orvalho ou para um terceiro consumidor .
A resistência aerodinâmica do caminho do gás na combustão de gases de combustão frios e secos é compensada por um exaustor de fumaça adicional. Para evitar a condensação do vapor de água residual transportado pelo fluxo do condensador, uma parte dos gases de combustão secos e aquecidos (até 10%) é misturada na frente do exaustor de fumaça adicional. A temperatura do ar aquecido é regulada alterando o caudal dos gases de combustão secos, ajustando a velocidade do exaustor de fumos em função da temperatura do ar exterior.
Os gases de combustão secos são fornecidos por um exaustor de fumos ao aquecedor acima descrito, onde são aquecidos para evitar uma possível condensação de vapor de água nas condutas de fumos e na chaminé e são direcionados para a chaminé.
O dispositivo de recuperação de calor dos gases de combustão mostrado no desenho contém um duto de gás 1 conectado a um trocador de calor 2, que é conectado a um condensador 4 através de um duto de gás 3. O condensador 4 possui um coletor de gotas inercial 5 e está conectado ao condensado tubulação de descarga 6. O ventilador 7 está conectado ao duto de ar frio 8 com o condensador 4. O condensador 4 é conectado pelo duto de ar 9 ao consumidor de calor. A conduta de gases de combustão seca 10 está ligada ao permutador de calor 2 através de um exaustor de fumo 11. A conduta de gases de combustão aquecida a seco 12 está ligada ao permutador de calor 2 e é direcionada para a chaminé. O duto de gás 12 está conectado ao duto de gás 10 por um duto de gás adicional 13, que contém um amortecedor 14.
O trocador de calor 2 e o condensador 4 são trocadores de calor de placas de superfície feitos de pacotes modulares unificados, dispostos de tal forma que o refrigerante flui em contracorrente. Dependendo do volume dos gases de combustão a serem secos, o aquecedor e o condensador são formados por um número calculado de embalagens. O bloco 7 é formado por vários ventiladores para alterar o fluxo de ar aquecido. O condensador 4 na saída dos gases de combustão secos possui um coletor de gotas inercial 5, feito em forma de venezianas verticais, atrás do qual está embutido um duto de gás 10. Um amortecedor 14 é instalado no duto de gás 13 para o ajuste inicial do gás. reserva de temperatura, que evita a condensação de vapor d'água residual no exaustor de fumaça 11.
Método de funcionamento de um dispositivo de recuperação de calor de gases de combustão.
Os gases de combustão úmidos entram no trocador de calor 2 através da chaminé 1, onde sua temperatura é reduzida a uma temperatura próxima ao ponto de orvalho. Os gases de combustão resfriados através da chaminé 3 entram no condensador 4, onde o vapor de água neles contido é condensado. O condensado é descarregado pela tubulação 6 e, após processamento adicional, é utilizado para repor perdas na rede de aquecimento ou no ciclo da turbina a vapor. O calor da condensação é utilizado para aquecer o ar frio, que é fornecido pelos ventiladores 7 do ambiente. O ar aquecido 9 é direcionado para a sala de produção da sala das caldeiras para ventilação e aquecimento. Desta sala o ar é fornecido à caldeira para garantir o processo de combustão. Os gases de combustão secos 10 passam por um eliminador de gotejamento inercial 5, são fornecidos por um exaustor de fumaça 11 ao trocador de calor 2, onde são aquecidos e direcionados para a chaminé 12. O aquecimento dos gases de combustão secos é necessário para evitar a condensação da água residual vapor nas condutas e na chaminé. Para evitar que gotas de umidade caiam no exaustor de fumaça 11, levadas pelo fluxo de gases de combustão secos do condensador, parte dos gases de combustão secos aquecidos (até um décimo) da chaminé 12 através da chaminé 13 é fornecida para a chaminé 10, onde a humidade arrastada evapora.
A temperatura do ar aquecido é regulada alterando a vazão dos gases de combustão secos, alterando a velocidade do exaustor de fumaça 11 dependendo da temperatura do ar externo. Com uma diminuição na vazão dos gases de combustão úmidos, a resistência aerodinâmica do caminho do gás do dispositivo diminui, o que é compensado por uma diminuição na velocidade do exaustor de fumaça 11. O exaustor de fumaça 11 fornece uma diferença na pressão de os gases de combustão e o ar no condensador para evitar que os gases de combustão entrem no ar aquecido.
Um cálculo de verificação mostra que para uma caldeira a gás natural com potência de 6 MW, com vazão de gases de combustão úmidos de 1 m 3 / s e temperatura de 130 ° C, o ar é aquecido de -15 a 30 ° C , com vazão de 7 m 3 / s. A vazão de condensado é de 0,13 kg/s, a temperatura dos gases de combustão secos na saída do aquecedor é de 86°C. A potência térmica de tal dispositivo é de 400 kW. A área total da superfície de troca de calor é de 310 m2. A temperatura do ponto de orvalho do vapor de água nos gases de combustão diminui de 55 para 10°C. A eficiência da caldeira aumenta 1% apenas devido ao aquecimento do ar frio na quantidade de 0,9 m 3 /s necessária para a combustão do gás natural. Ao mesmo tempo, o aquecimento deste ar é responsável por 51 kW da potência do dispositivo, e o restante do calor é utilizado para aquecimento do ar das instalações. Os resultados dos cálculos da operação de tal dispositivo em várias temperaturas externas são apresentados na Tabela 1.
A Tabela 2 mostra os resultados do cálculo de variantes do dispositivo para outras taxas de fluxo de gases de combustão secos, a uma temperatura do ar exterior de -15°C.
tabela 1 | |||||||
DISPOSITIVO PARA RECICLAGEM DE CALOR DE GASES DE FUMOS E MÉTODO DE SEU FUNCIONAMENTO | |||||||
Consumo de gases de combustão | Fluxo de ar | Temperatura do ar | Potência térmica do dispositivo | ||||
antes | depois | ||||||
m 3 /s | m 3 /s | °C | °C | kW | kg/s | °C | °C |
0,7 | 5,4 | 0 | 37,0 | 262 | 0,09 | 90,7 | 19/8 |
0,8 | 6/2 | -5 | 33,2 | 316 | 0,10 | 89,0 | 16,2 |
1 | 7,0 | -10 | 33,2 | 388 | 0,13 | 87/4 | 15,1 |
1 | 7,0 | -15 | 29,6 | 401 | 0,13 | 86,0 | 10,0 |
1 | 6,2 | -20 | 30,2 | 402 | 0,13 | 86,3 | 10,8 |
1 | 6,2 | -25 | 26,6 | 413 | 0,13 | 84,8 | 5,5 |
mesa 2 | |||||||
Consumo de gases de combustão | Fluxo de ar | Temperatura do ar aquecido | Potência térmica do dispositivo | Consumo do condensado resultante | Área total de superfície de troca de calor | Temperatura dos gases de combustão secos | Temperatura do ponto de orvalho do vapor de água em gases secos |
m 3 /s | m 3 /s | °C | kW | kg/s | m 2 | °C | °C |
2 | 13,2 | 31,5 | 791 | 0,26 | 620 | 86,8 | 12,8 |
5 | 35,0 | 29,6 | 2007 | 0,65 | 1552 | 86,0 | 10,0 |
10 | 62,1 | 35,6 | 4047 | 1,30 | 3444 | 83,8 | 9,2 |
25 | 155,3 | 32,9 | 9582 | 3,08 | 8265 | 86,3 | 18,6 |
50 | 310,8 | 32,5 | 19009 | 6,08 | 13775 | 85,6 | 20,0 |
1. Dispositivo para recuperação de calor de gases de combustão, contendo um trocador de calor gás-gás, um condensador, um eliminador de gotas inerciais, dutos de gás, dutos de ar, ventiladores e uma tubulação, caracterizado por o trocador de calor de placas de superfície gás-gás ser feito de acordo com um circuito de contrafluxo, e um trocador de calor gás-ar de superfície é instalado como um trocador de calor de placas condensadoras, um exaustor de fumaça adicional é instalado no duto de gás de gases de combustão secos a frio, um duto de gás para misturar parte do seco aquecido gases de combustão são instalados na frente do exaustor de fumaça adicional.
2. O método de operação do dispositivo de recuperação de calor dos gases de combustão, segundo o qual os gases de combustão são resfriados em um trocador de calor gás-gás, aquecendo os gases de combustão secos, condensando o vapor de água contido nos gases de combustão no condensador, aquecendo parte do ar de sopro, caracterizado pelo fato de que no gás-gás em um trocador de calor, os gases de combustão secos são aquecidos pelo resfriamento dos gases de combustão originais usando um esquema de contrafluxo sem regulação da vazão de gás, o vapor de água é condensado em um gás de superfície- trocador de calor-condensador de placas de ar, aquecendo o ar e o ar aquecido é utilizado para aquecer e cobrir as necessidades do processo de combustão, e o condensado após processamento adicional é utilizado para compensar perdas na rede de aquecimento ou no ciclo da turbina a vapor, em conduta de gás dos gases de combustão secos a frio, a resistência aerodinâmica do percurso do gás é compensada por um exaustor de fumos adicional, em frente ao qual se mistura parte dos gases de combustão secos aquecidos, excluindo a condensação do vapor de água residual transportado pelo fluxo a partir do condensador, a temperatura do ar aquecido é regulada alterando a velocidade do exaustor de fumos em função da temperatura do ar exterior.
Patentes semelhantes:
A invenção refere-se a um trocador de calor de gases de escape, em particular a um refrigerador de gases de escape, para recirculação de gases de escape em automóveis de acordo com o preâmbulo do parágrafo 1 das reivindicações.
A invenção refere-se a um gerador de vapor no qual, em um canal de gás de combustão que flui o gás de combustão aproximadamente na direção horizontal, há uma superfície de aquecimento evaporativo de fluxo direto, que contém uma pluralidade de tubos geradores de vapor conectados em paralelo para o fluxo de fluido com uma pluralidade de coletores de saída conectados após alguns tubos do gerador de vapor no lado do fluido.
A invenção refere-se à engenharia de energia térmica e pode ser utilizada em caldeiras de calor residual de usinas de cogeração e destina-se ao aproveitamento de gases de exaustão de uma unidade de turbina a gás utilizada em sistemas de fornecimento de calor para aquecimento de edifícios residenciais, instalações industriais, bem como para outros necessidades económicas e técnicas.
A invenção se refere a um gerador de vapor de fluxo direto, no qual uma superfície de aquecimento evaporativo de fluxo direto está localizada no canal de gás de combustão, que flui com o gás de combustão aproximadamente na direção horizontal, que contém uma pluralidade de tubos geradores de vapor conectados em paralelo para o fluxo de fluido.
A invenção se refere a um gerador de vapor de fluxo direto, no qual uma superfície de aquecimento evaporativo está localizada em um duto de gás de fluxo para o gás de combustão fluindo aproximadamente na direção vertical, que contém uma pluralidade de tubos geradores de vapor conectados em paralelo para o fluxo de fluido .
A invenção se refere a um gerador de vapor de fluxo direto de tipo horizontal, no qual em um canal de gás de combustão que flui aproximadamente horizontalmente há uma superfície de aquecimento evaporativo de fluxo direto, que contém uma pluralidade de tubos geradores de vapor conectados em paralelo para o fluxo de fluido, e uma superfície de aquecimento de superaquecimento conectada após a superfície de aquecimento evaporativo de fluxo direto, que contém uma pluralidade de tubos de superaquecimento conectados em paralelo para o fluxo de fluido evaporado.
A invenção refere-se a uma caldeira de calor residual caracterizada pela presença de um reator, cuja parte inferior é adjacente a dois queimadores, e o porco de alimentação dos gases de combustão é adjacente à superfície lateral do reator, enquanto os gases de combustão que saem do o fornecimento de gás de combustão entra na zona de combustão ativa do reator, que está localizada em sua parte inferior, um sistema de recuperação de calor de gases de combustão que entra no reator da caldeira de calor residual, um tubo de exaustão de gases de combustão do reator, que contém um gás de combustão adicional sistema de recuperação de calor e pelo menos um exaustor de fumaça
A invenção refere-se ao campo da construção de caldeiras navais e pode ser utilizada em caldeiras de recuperação estacionárias operando em conjunto com motores diesel ou turbinas a gás. O problema técnico resolvido pela invenção é criar uma unidade de recuperação com características de desempenho melhoradas, cujas superfícies de aquecimento da caldeira a vapor possam ser limpas sem parar o motor principal, reduzir o consumo de água doce e melhorar o desempenho ambiental e a eficiência de transferência de calor. Esta tarefa é conseguida pelo facto de a instalação de recuperação com caldeira a vapor incluir uma caldeira a vapor com circulação forçada, que se apresenta em forma de caixa, na qual se encontram as superfícies de aquecimento em forma de pacotes de tubos, e uma superfície de aquecimento limpeza dispositivo composto por elementos de limpeza separados, além de dutos de entrada e saída de gases com amortecedores. Neste caso, o duto de gás de entrada com amortecedor é conectado à parte superior da carcaça, e o duto de gás de saída com amortecedor é conectado à parte inferior da carcaça, a instalação contém adicionalmente uma câmara de limpeza de gás úmido e um tanque, os elementos para limpeza das superfícies de aquecimento estão localizados entre as superfícies de aquecimento, que são conectadas ao tanque por uma tubulação com uma bomba. A câmara de purificação de gás úmido está localizada na carcaça e é conectada ao tanque por meio de uma tubulação de drenagem com um portão. 2 salário voar, 1 doente.
A invenção refere-se a energia e pode ser utilizada em trocadores de calor de gases de escape, em particular resfriadores de gases de escape para recirculação de gases de escape em automóveis, com canais trocadores de calor adaptados para o fluxo de gases de escape e aerodinâmicos com refrigerante, que terminam em uma distribuição e/ ou câmara de coleta, localizada na câmara de distribuição e/ou coleta com um dispositivo com canais guia, em que o dispositivo com canais guia tem uma área de entrada para o gás de exaustão, uma área de saída para o gás de exaustão e uma pluralidade de canais de fluxo que se estendem da área de entrada dos gases de escape até a área de saída dos gases de escape, que são inclinados entre si em relação a um amigo. A concentração dos canais de fluxo na seção transversal é de 100 a 600 unidades/pol. quadrada e o comprimento dos canais de fluxo é de 15 a 100 mm. Com este arranjo, o fluxo dos gases de escape na direção de desvio, a velocidade do fluxo, a área da seção transversal, a distribuição do fluxo e outros parâmetros de fluxo são afetados. 14 salário voar, 7 doentes.
A invenção refere-se à energia e pode ser utilizada em geradores de vapor de fluxo direto. O gerador de vapor contém um trocador de calor, coletores de líquido e vapor. O trocador de calor contém vários blocos trocadores de calor do mesmo projeto. O bloco de troca de calor contém um conjunto de tubos espirais de transferência de calor, um cilindro central e mangas. Tubos espirais de transferência de calor com diferentes raios de curvatura são colocados em uma espiral concêntrica no espaço entre tubos entre o cilindro central e a luva, formando uma ou mais colunas de transferência de calor. Uma saída do coletor de líquido é conectada à tubulação principal de abastecimento de água e a segunda saída do coletor de líquido é conectada a um feixe de tubos espirais de transferência de calor. Uma saída do coletor de vapor é conectada à tubulação de vapor principal e a segunda saída do coletor de vapor é conectada a um feixe de tubos espirais de transferência de calor. Dentro da porção de conexão do coletor de fluido, cada tubo espiral de transferência de calor é fornecido com um diafragma fixo e removível. 6 salário voar., 6 doentes.
A invenção refere-se à engenharia de energia térmica e pode ser utilizada para recuperar calor de gases de combustão de caldeiras, fornos industriais, emissões de ventilação ao aquecer o ar durante a geração de eletricidade. Um complexo dispositivo de recuperação de calor de gases residuais contém uma caixa equipada com tubos de gás e ar, dentro da qual é colocada uma embalagem composta por placas perfuradas que formam canais de gás e ar entre si, e a perfuração das placas é feita em forma de ranhuras horizontais , escalonados entre si, nos quais são colocados elos termoelétricos, constituídos por inserções ovais feitas de material dielétrico elástico resistente à corrosão, dentro dos quais são colocadas fileiras em zigue-zague compostas por conversores termiônicos, cada um dos quais é um par de pedaços de fio desencapado feitos de diferentes metais M1 e M2, soldados nas extremidades entre si, e as próprias fileiras em zigue-zague são conectadas entre si em série por meio de fios de conexão, formando seções termoelétricas conectadas a coletores de carga elétrica e terminais. Este design da recicladora aumenta sua confiabilidade e eficiência. 5 doentes. .
A presente invenção refere-se a um trocador de calor para resfriamento de gases quentes por meio de um fluido de resfriamento, dito trocador de calor compreendendo: pelo menos um recipiente orientado verticalmente contendo um banho de fluido de resfriamento e possuindo um espaço para coleta da fase de vapor gerada acima do dito banho de fluido de resfriamento, um elemento tubular vertical inserido no referido recipiente, aberto nas extremidades e coaxial com o referido recipiente, um canal em espiral que envolve o eixo do recipiente, inserido no referido elemento tubular coaxial, uma saída para a fase de vapor gerada em a parte superior do referido contêiner, em que pelo menos uma linha de transporte é inserida na parte inferior do contêiner vertical, aberta em duas extremidades, das quais uma está conectada ao contêiner vertical e a outra é livre e localizada fora do contêiner especificado, e a linha de transporte especificada é tubular e se projeta lateralmente para fora do trocador de calor especificado, contém pelo menos um canal interno central que está em comunicação fluida com o canal espiral e se estende verticalmente ao longo de um elemento tubular inserido no recipiente vertical, o canal tendo um canal externo camisa na qual circula um fluido refrigerante. O resultado técnico é aumentar a segurança e o desempenho do sistema de troca de calor. 3 n. e 17 salário voar, 1 doente.
A invenção refere-se à engenharia de energia térmica e pode ser utilizada em qualquer empresa que opere caldeiras a combustível de hidrocarbonetos
Detentores da patente RU 2606296:
A invenção refere-se à engenharia de energia térmica e pode ser utilizada em qualquer empresa que opere caldeiras a combustíveis de hidrocarbonetos.
Os aquecedores do tipo KSk (Kudinov A.A. Economia de energia em instalações de geração de calor. - Ulyanovsk: UlSTU, 2000. - 139, p. 33), constituídos por um trocador de calor de superfície gás-água, são conhecidos comercialmente produzidos pela Usina de Aquecimento de Kostroma. cuja superfície de troca de calor é composta por tubos bimetálicos aletados, filtro, válvula de distribuição, eliminador de gotejamento e soprador hidropneumático.
Os aquecedores do tipo KSk funcionam da seguinte forma. Os gases de combustão entram na válvula de distribuição, que os divide em dois fluxos, o fluxo principal do gás é direcionado através de um filtro de malha para o trocador de calor, o segundo através da linha de desvio da chaminé. No trocador de calor, o vapor d'água contido nos gases de combustão condensa-se em tubos aletados, aquecendo a água que neles flui. O condensado resultante é coletado em uma panela e bombeado para o circuito de alimentação da rede de aquecimento. A água aquecida no trocador de calor é fornecida ao consumidor. Na saída do recuperador de calor, os gases de combustão secos são misturados com os gases de combustão originais da linha de derivação de fumos e enviados através de um exaustor de fumos para a chaminé.
Para que o trocador de calor opere no modo de condensação de toda a sua parte convectiva, é necessário que a temperatura de aquecimento da água no pacote convectivo não ultrapasse 50°C. Para usar essa água em sistemas de aquecimento, ela deve ser aquecida adicionalmente.
Para evitar a condensação do vapor de água residual dos gases de combustão nas condutas e na chaminé, parte dos gases de origem é misturada nos gases de combustão secos através de um canal de derivação, aumentando a sua temperatura. Com esta mistura, o teor de vapor de água nos gases de combustão também aumenta, reduzindo a eficiência da recuperação de calor.
É conhecido um trocador de calor (RU 2323384 C1, IPC F22B 1/18 (2006.01), publicado em 27 de abril de 2008), contendo um trocador de calor de contato, um eliminador de gotas, um trocador de calor gás-gás conectado de acordo com um circuito de fluxo direto , dutos de gás, tubulações, bomba, sensores de temperatura, válvulas - reguladores. Ao longo do fluxo de água circulante do trocador de calor de contato, um trocador de calor água-água e um trocador de calor água-ar com um canal de desvio ao longo do fluxo de ar estão localizados em série.
Um método conhecido de operação deste trocador de calor. Os gases de exaustão pelo duto de gás entram na entrada do trocador de calor gás-gás, passando sequencialmente por suas três seções, depois para a entrada do trocador de calor de contato, onde, passando por um bico lavado pela água circulante, são resfriados abaixo o ponto de orvalho, liberando calor sensível e latente para a água circulante. Em seguida, os gases resfriados e úmidos são liberados da maior parte da água líquida transportada em um eliminador de gotas, aquecidos e secos em pelo menos uma seção do trocador de calor gás-gás, enviados para uma chaminé por um exaustor de fumaça e liberados no atmosfera. Ao mesmo tempo, a água circulante aquecida da bandeja do trocador de calor de contato é bombeada para o trocador de calor água-água, onde aquece a água fria da tubulação. A água aquecida no permutador de calor é fornecida às necessidades de abastecimento de água quente de processo e sanitária ou a um circuito de aquecimento de baixa temperatura.
Em seguida, a água reciclada entra no trocador de calor água-ar, aquece pelo menos parte do ar soprado vindo de fora da sala através do duto de ar, resfriando até a temperatura mínima possível, e entra no trocador de calor de contato através do distribuidor de água, onde retira calor dos gases, lavando-os simultaneamente das partículas suspensas, e absorve alguns dos óxidos de nitrogênio e enxofre. O ar aquecido do trocador de calor é fornecido por um ventilador para um aquecedor de ar padrão ou diretamente para a fornalha. A água reciclada é filtrada, se necessário, e processada por métodos conhecidos.
Para implementar este método, é necessário um sistema de controle devido à utilização do calor recuperado para fins de abastecimento de água quente devido à variabilidade da programação diária de consumo de água quente.
A água aquecida no permutador de calor, fornecida para as necessidades de abastecimento de água quente ou num circuito de aquecimento de baixa temperatura, necessita de ser levada à temperatura pretendida, uma vez que não pode ser aquecida no permutador de calor acima da temperatura do circuito de retorno água, que é determinada pela temperatura de saturação do vapor d'água nos gases de combustão. O baixo aquecimento do ar no trocador de calor água-ar não permite que esse ar seja utilizado para aquecimento ambiente.
O mais próximo da invenção reivindicada é um dispositivo e método para utilizar o calor dos gases de combustão (RU 2436011 C1, IPC F22B 1/18 (2006.01), publicado em 10/12/2011).
O dispositivo de recuperação de calor dos gases de combustão contém um trocador de calor de placas de superfície gás-gás feito de acordo com um circuito de contrafluxo, um condensador de placas de superfície gás-ar, um coletor de gotas inercial, dutos de gás, um exaustor de fumaça, dutos de ar, ventiladores e uma tubulação.
Os gases de combustão de alimentação são resfriados em um trocador de calor de placas de superfície gás-gás, aquecendo os gases de combustão secos. O aquecimento e o meio aquecido movem-se em contracorrente. Neste caso, os gases de combustão úmidos são profundamente resfriados a uma temperatura próxima ao ponto de orvalho do vapor d'água. Em seguida, o vapor de água contido nos gases de combustão é condensado em um trocador de calor de placas de superfície gás-ar - um condensador, que aquece o ar. O ar aquecido é utilizado para aquecer as instalações e cobrir as necessidades do processo de combustão. O condensado após processamento adicional é usado para compensar perdas na rede de aquecimento ou no ciclo da turbina a vapor. Para evitar a condensação do vapor de água residual transportado pelo fluxo do condensador, uma parte dos gases de combustão secos e aquecidos é misturada na frente do exaustor de fumaça adicional. Os gases de combustão secos são fornecidos por um exaustor de fumos ao aquecedor acima descrito, onde são aquecidos para evitar uma possível condensação de vapor de água nas condutas de fumos e na chaminé e são direcionados para a chaminé.
As desvantagens deste método são que é utilizado predominantemente o calor latente de condensação do vapor de água contido nos gases de combustão. Se o trocador de calor recuperativo resfriar os gases de combustão originais a uma temperatura próxima ao ponto de orvalho do vapor d'água, então o aquecimento dos gases de combustão secos de exaustão será excessivo, o que reduz a eficiência da reciclagem. A desvantagem é o uso de apenas um meio de aquecimento - o ar.
O objectivo da invenção é aumentar a eficiência da recuperação de calor dos gases de combustão através da utilização do calor latente de condensação do vapor de água e do aumento da temperatura dos próprios gases de combustão.
No método proposto de recuperação profunda de calor de gases de combustão, bem como no protótipo, os gases de combustão são pré-resfriados em um trocador de calor de placas de superfície gás-gás, aquecendo os gases de combustão secos e o vapor de água contido na combustão os gases são condensados no condensador, aquecendo o ar.
De acordo com a invenção, entre o permutador de calor e o condensador, os gases de combustão são arrefecidos a uma temperatura próxima do ponto de orvalho do vapor de água, aquecendo a água.
As caldeiras a gás têm uma alta temperatura dos gases de combustão (130°C para grandes caldeiras de energia, 150°C-170°C para pequenas caldeiras). Para resfriar os gases de combustão antes da condensação, são utilizados dois dispositivos: um trocador de calor recuperativo gás-gás e um aquecedor de água de recuperação.
Os gases de combustão da fonte são pré-resfriados em um trocador de calor de placas de superfície gás-gás, aquecendo os gases de combustão secos 30-40°C acima da temperatura de saturação do vapor de água neles contido, para criar uma reserva de temperatura para possível resfriamento de os gases de combustão na tubulação. Isso permite reduzir a área de troca de calor do trocador de calor recuperativo em comparação com o protótipo e aproveitar de forma útil o calor restante dos gases de combustão.
Uma diferença significativa é a utilização de um aquecedor de água a gás de contato para o resfriamento final dos gases de combustão úmidos a uma temperatura próxima ao ponto de orvalho do vapor d'água. À entrada do termoacumulador, os gases de combustão apresentam uma temperatura bastante elevada (130°C-90°C), o que permite aquecer a água até 50°C-65°C com evaporação parcial. Na saída de um aquecedor de água de contato gás-água, os gases de combustão apresentam temperatura próxima ao ponto de orvalho do vapor d'água que contêm, o que aumenta a eficiência do aproveitamento da superfície de troca de calor no condensador, elimina a formação de zonas secas do condensador e aumenta o coeficiente de transferência de calor.
O método de utilização do calor dos gases de combustão é mostrado na Fig.1.
A Tabela 1 apresenta os resultados do cálculo de verificação da opção de instalação de caldeira a gás natural com capacidade de 11 MW.
O método de utilização profunda do calor dos gases de combustão é realizado da seguinte forma. Os gases de combustão da fonte 1 são pré-resfriados em um trocador de calor de placas de superfície gás-gás 2, aquecendo os gases de combustão secos. A seguir, os gases de combustão 3 são finalmente arrefecidos num aquecedor de água de contacto gás-água 4 até uma temperatura próxima do ponto de orvalho do vapor de água, pulverizando água, para a qual é aconselhável utilizar o condensado obtido no condensador. Nesse caso, parte da água evapora, aumentando o teor de umidade dos gases de combustão, e o restante é aquecido à mesma temperatura. O vapor de água contido nos gases de combustão 5 é condensado em um trocador de calor de placas de superfície gás-ar - um condensador 6 com eliminador de gotas 7, que aquece o ar. O condensado 8 é fornecido para aquecimento a um aquecedor de água a gás de contato 4. O calor da condensação é utilizado para aquecer o ar frio, que é fornecido pelos ventiladores 9 do ambiente através de um duto de ar 10. O ar aquecido 11 é enviado para o sala de produção da caldeira para ventilação e aquecimento. Desta sala o ar é fornecido à caldeira para garantir o processo de combustão. Os gases de combustão secos 12 são fornecidos por um exaustor de fumaça 13 a um trocador de calor de placas de superfície gás-gás 2 para aquecimento e enviados para a chaminé 14.
Para evitar a condensação do vapor de água residual transportado pelo fluxo do condensador, uma parte dos gases de combustão secos e aquecidos 15 (até 10%) é misturada na frente do exaustor de fumaça 13 (até 10%), o valor do qual é inicialmente ajustado pelo amortecedor 16.
A temperatura do ar aquecido 11 é regulada alterando a vazão dos gases de combustão secos 1 ou alterando a vazão do ar ajustando a velocidade do exaustor de fumaça 13 ou ventiladores 9 dependendo da temperatura do ar externo.
O trocador de calor 2 e o condensador 6 são trocadores de calor de placas de superfície feitos de pacotes modulares unificados, dispostos de tal forma que o refrigerante flui em contracorrente. Dependendo do volume dos gases de combustão a serem secos, o aquecedor e o condensador são formados por um número calculado de embalagens. O aquecedor de água 4 é um trocador de calor gás-água de contato que fornece resfriamento adicional dos gases de combustão e aquecimento da água. A água aquecida 17 após processamento adicional é usada para compensar perdas na rede de aquecimento ou no ciclo da turbina a vapor. O bloco 9 é formado por vários ventiladores para alterar o fluxo de ar aquecido.
A Tabela 1 apresenta os resultados do cálculo de verificação da opção de instalação de caldeira a gás natural com capacidade de 11 MW. Os cálculos foram realizados para uma temperatura externa de -20°C. O cálculo mostra que a utilização de um esquentador de contacto gás-água 4 leva ao desaparecimento da zona seca no condensador 6, intensifica a troca de calor e aumenta a potência da instalação. A percentagem de calor recuperado aumenta de 14,52 para 15,4%, enquanto a temperatura do ponto de orvalho do vapor de água nos gases de combustão secos diminui para 17°C. Aproximadamente 2% da energia térmica não é utilizada, mas é utilizada para recuperação - aquecimento dos gases de combustão secos a uma temperatura de 70°C.
Método de aproveitamento profundo do calor dos gases de combustão, segundo o qual os gases de combustão são pré-resfriados em um trocador de calor de placas de superfície gás-gás, aquecendo os gases de combustão secos, resfriados em um aquecedor de água a uma temperatura próxima ao ponto de orvalho de vapor de água, aquecendo a água, condensando o vapor de água contido nos gases de combustão no condensador, aquecendo o ar, caracterizado por ser instalado um aquecedor de água a gás tubular de superfície entre o trocador de calor e o condensador para resfriar os gases de combustão úmidos e aquecer água, enquanto a recuperação de calor principal ocorre no condensador ao aquecer o ar, e a recuperação de calor adicional ocorre no aquecedor de água.
Patentes semelhantes:
A invenção refere-se à engenharia petroquímica e pode ser utilizada para craqueamento de óleo combustível, bem como para aquecimento de meios de processo (por exemplo, óleo, emulsão de óleo, gás, misturas destes) e para outros processos tecnológicos que requerem fornecimento intensivo de calor.
A invenção refere-se ao campo da engenharia de energia térmica e pode ser utilizada em sistemas de aquecimento e ar condicionado. A invenção reside no fato de que a conexão de tubos com aletas de troca de calor em uma fileira e fileiras entre si é feita sequencialmente, um tubo por passagem em um ramal, e os tubos de troca de calor adjacentes em uma fileira são conectados entre si em série por transições entre tubos na forma de curvas acentuadas e são equipados com tampões de reparo e proteção facilmente removíveis, o número de tubos conectados em série em uma fileira e o número total de cursos em todas as fileiras são selecionados dependendo dos parâmetros reais do rede de aquecimento existente e determinada pelas características hidráulicas do termoacumulador.
Um radiador elétrico que usa processadores de computação como fonte de calor. Este radiador para instalações domésticas e industriais, utilizando processadores de computação como fontes de calor, contém uma caixa aquecida que realiza a transferência de calor entre a fonte de calor e o ar circundante, um número Q de processadores distribuídos em um número P de placas de circuito impresso formando um calor fonte do radiador e um poderoso meio que realiza cálculos através de sistemas de informação externos, uma interface homem-máquina que permite controlar a computação e a energia térmica gerada pelo radiador, uma fonte de alimentação estabilizada para vários componentes eletrônicos, uma interface de rede que permite você conecte o radiador a redes externas.
A invenção destina-se à implementação de reações de reforma a vapor e pode ser utilizada na indústria química. O reator trocador de calor contém uma pluralidade de tubos tipo baioneta (4) suspensos no teto superior (2), estendendo-se até o nível do fundo inferior (3) e encerrados em um invólucro (1) contendo entrada (E) e saída (S ) tubos para gases de combustão.
A invenção fornece um sistema e método para conversão de vapor-gás. O método de cogeração vapor-gás baseado na gaseificação e metanação de biomassa inclui: 1) gaseificação de biomassa misturando oxigênio e vapor de água obtido de uma unidade de separação de ar com biomassa, transportando a mistura resultante através de um bico até o gaseificador, gaseificação de biomassa a uma temperatura de 1500-1800°C e uma pressão de 1-3 MPa com a produção de gás bruto gaseificado e transporte de vapor superaquecido com uma pressão de 5-6 MPa, obtido como resultado de uma rápida recuperação de calor, para o vapor turbina; 2) conversão e purificação: de acordo com os requisitos da reação de metanação, ajuste a proporção hidrogênio/carbono do gás gaseificado bruto gerado na etapa 1) para 3:1 usando a reação de conversão e extraia a baixa temperatura o gás gaseificado bruto usando metanol para dessulfuração e descarbonização, resultando em gás de síntese purificado; 3) realização de metanação: introdução do gás de síntese purificado do estágio 2) na seção de metanação, que consiste em uma seção de metanação primária e uma seção de metanação secundária, a seção de metanação primária contendo um primeiro reator de metanação primário e um segundo reator de metanação primário conectados em série ; permitindo que uma porção do gás de processo do segundo reator primário de metanação retorne à entrada do primeiro reator primário de metanação para se misturar com o gás de alimentação fresco e então ser capaz de entrar no primeiro reator primário de metanação, de modo que a concentração de reagentes no a entrada do primeiro reator primário de metanação é reduzida e a temperatura do leito catalítico é controlada pelo gás de processo; introdução de gás de síntese após metanação primária em uma seção de metanação secundária contendo um primeiro reator de metanação secundário e um segundo reator de metanação secundário conectados em série, onde uma pequena quantidade de CO não reagido e uma grande quantidade de CO2 são convertidas em CH4, e transporte da pressão intermediária superaquecida vapor gerado na seção de metanação para turbina a vapor; e 4) concentração de metano: concentração de gás natural sintético metano contendo vestígios de nitrogênio e vapor de água obtida na etapa 3) usando adsorção por oscilação de pressão, de modo que a concentração molar de metano atinja 96% e o poder calorífico do gás natural sintético atinja 8256 kcal/Nm3.
A invenção refere-se à engenharia de energia térmica. O método de recuperação profunda de calor dos gases de combustão inclui o pré-resfriamento dos gases de combustão em um trocador de calor de placas de superfície gás-gás, aquecendo os gases de combustão secos com contracorrente para criar uma reserva de temperatura que evita a condensação do vapor de água residual na chaminé. O resfriamento adicional dos gases de combustão a uma temperatura próxima ao ponto de orvalho do vapor d'água é realizado em um aquecedor de água de contato gás-água, que aquece a água. Os gases de combustão úmidos resfriados são alimentados em um trocador de calor de placas de superfície gás-ar - um condensador, onde o vapor de água contido nos gases de combustão é condensado, aquecendo o ar. Os gases de combustão secos são fornecidos por um exaustor de fumos adicional a um permutador de calor de placas de superfície gás-gás, onde são aquecidos para evitar uma possível condensação de vapor de água nas condutas de fumos e na chaminé e são direcionados para a chaminé. Resultado técnico: aumento da eficiência da recuperação de calor dos gases de combustão através da utilização do calor latente de condensação do vapor de água e do aumento da temperatura dos próprios gases de combustão. 1 il., 1 aba.
Sistema de condensação de gases de combustão para caldeiras da empresa “ AprotechEngenhariaAB" (Suécia)O sistema de condensação dos gases de combustão permite a captação e recuperação de grandes quantidades de energia térmica contida nos gases de combustão húmidos da caldeira, que normalmente é descarregada para a atmosfera através da chaminé.
O sistema de recuperação de calor/condensação de gases de combustão permite aumentar o fornecimento de calor aos consumidores em 6–35% (dependendo do tipo de combustível queimado e dos parâmetros de instalação) ou reduzir o consumo de gás natural em 6–35%
Vantagens principais:
- Economia de combustível (gás natural) - carga térmica igual ou aumentada da caldeira com menor combustão de combustível
- Redução de emissões - CO2, NOx e SOx (na queima de carvão ou combustíveis líquidos)
- Obtenção de condensado para o sistema de reposição da caldeira
Princípio da Operação:
O sistema de recuperação de calor/condensação dos gases de combustão pode funcionar em duas fases: com ou sem recurso a um sistema de humidificação do ar fornecido aos queimadores da caldeira. Se necessário, é instalado um purificador antes do sistema de condensação.
No condensador, os gases de combustão de exaustão são resfriados com água de retorno da rede de aquecimento. Quando a temperatura dos gases de combustão diminui, uma grande quantidade de vapor de água contido nos gases de combustão condensa. A energia térmica da condensação do vapor é utilizada para aquecer a rede de aquecimento de retorno.
O resfriamento adicional do gás e a condensação do vapor d'água ocorrem no umidificador. O meio de resfriamento no umidificador é o ar soprado fornecido aos queimadores da caldeira. Como o ar soprado é aquecido no umidificador e o condensado quente é injetado no fluxo de ar na frente dos queimadores, ocorre um processo adicional de evaporação nos gases de exaustão da caldeira.
O ar soprado fornecido aos queimadores da caldeira contém uma quantidade maior de energia térmica devido ao aumento da temperatura e da umidade.
Isto leva a um aumento na quantidade de energia nos gases de combustão que entram no condensador, o que por sua vez leva a uma utilização mais eficiente do calor pelo sistema de aquecimento urbano.
A unidade de condensação dos gases de combustão também produz condensado que, dependendo da composição dos gases de combustão, será posteriormente purificado antes de ser alimentado no sistema da caldeira.
Efeito econômico.
Comparação da potência térmica nas seguintes condições:
- Sem condensação
- Condensação de gases de combustão
- Condensação juntamente com umidificação do ar fornecido para combustão
O sistema de condensação dos gases de combustão permite que a sala da caldeira existente:
- Aumentar a produção de calor em 6,8% ou
- Reduzir o consumo de gás em 6,8%, bem como aumentar a receita com a venda de cotas de CO,NO
- O tamanho do investimento é de cerca de 1 milhão de euros (para uma caldeira com capacidade de 20 MW)
- O período de retorno é de 1 a 2 anos.
Economia dependendo da temperatura de retorno:
Enviar seu bom trabalho na base de conhecimento é simples. Use o formulário abaixo
Estudantes, estudantes de pós-graduação, jovens cientistas que utilizam a base de conhecimento em seus estudos e trabalhos ficarão muito gratos a você.
Postado em http://www.allbest.ru/
Ministério da Educação e Ciência da Federação Russa
Instituição estadual de ensino de ensino profissional superior
Universidade Politécnica Nacional de Pesquisa de Perm
Filial de Berezniki
Teste
na disciplina “Economia de Recursos”
no tema “Aproveitamento do calor dos gases de combustão”
O trabalho foi realizado por um aluno
grupos EiU- 10z(2)
Pauwels Yu.S.
O trabalho foi verificado pelo professor
Nechaev N.P.
Berezniki 2014
Introdução
1. Informações gerais
3. Caldeiras de calor residual
Conclusão
Introdução
Os gases na tecnologia são usados principalmente como combustível; matérias-primas para a indústria química: agentes químicos para soldagem, tratamento químico-térmico gasoso de metais, criação de atmosfera inerte ou especial, em alguns processos bioquímicos, etc.; refrigerantes; fluido de trabalho para execução de trabalhos mecânicos (armas de fogo, motores a jato e projéteis, turbinas a gás, usinas de ciclo combinado, transporte pneumático, etc.): ambiente físico para descarga de gases (em tubos de descarga de gases e outros dispositivos).
Vamos dar uma olhada mais de perto no uso de gases de combustão residuais.
recuperador de calor de combustão de gás
1. Informações gerais
Os gases de combustão são produtos da combustão de combustíveis de origem orgânica, escapando do espaço de trabalho das unidades metalúrgicas aquecidas.
Gases de exaustão (recursos energéticos secundários) são gases gerados a partir da combustão de combustíveis, bem como de processos tecnológicos, saindo de uma fornalha ou unidade.
A utilização do calor sensível pelos gases residuais é determinada pela sua quantidade, composição, capacidade calorífica e temperatura. A temperatura mais alta dos gases de exaustão dos conversores de oxigênio é (1600-1800 °C), a mais baixa é a temperatura dos gases de exaustão dos aquecedores de ar dos altos-fornos (250-400 °C). A utilização do calor dos gases residuais é organizada de diferentes maneiras. Com o resfriamento regenerativo ou fechado, o calor dos gases de exaustão é utilizado para aumentar diretamente a eficiência do processo tecnológico (aquecimento de regeneradores ou recuperadores, carga ou produto de processo, etc.). Se, como resultado do resfriamento regenerativo, nem todo o calor dos gases de exaustão for utilizado, serão utilizadas caldeiras de calor residual. O calor físico dos gases residuais também é usado para gerar eletricidade em unidades de turbina a gás integradas. O pó de forno do gás de alto forno contido nos gases de exaustão e os óxidos de ferro nos gases dos fornos abertos e conversores de oxigênio são capturados em unidades de purificação de gases e devolvidos ao processo tecnológico como produto de reciclagem.
2. Regeneradores e recuperadores para aquecimento de ar e gás
Conforme mencionado acima, o aquecimento do ar e do gás é realizado em regeneradores ou recuperadores utilizando o calor dos gases de combustão que saem das câmaras de trabalho dos fornos. Os regeneradores são utilizados em fornos de fundição de aço a céu aberto, nos quais o aquecimento do ar e do gás atinge 1000 - 1200°. O princípio de funcionamento dos regeneradores é aquecer alternadamente dois bicos de tijolos intensivos em calor (grades) com gases que escapam da câmara de trabalho do forno, seguido pela passagem de gás ou ar aquecido através do bico aquecido. O aquecimento de gás ou ar em regeneradores está associado à mudança destes para aquecimento ou resfriamento. Isso requer mudanças periódicas na direção do movimento da chama na câmara de trabalho do forno, o que exige a troca dos dispositivos de combustão; assim, todo o processo do forno torna-se reversível. Isso complica o projeto do forno e aumenta o custo de sua operação, mas contribui para a distribuição uniforme das temperaturas no espaço de trabalho do forno.
O princípio de funcionamento do recuperador, que é um trocador de calor de superfície, consiste na transferência contínua de calor, dos gases de combustão que saem da câmara de trabalho do forno, para o ar aquecido ou combustível gasoso.
O recuperador é caracterizado pelo movimento contínuo de gases em uma direção, o que simplifica muito o projeto dos fornos e reduz o custo de construção e operação.
Na Fig. A Figura 1 mostra um trocador de calor cerâmico comum, no qual os tubos são constituídos por elementos cerâmicos octogonais, e o espaço entre os tubos é coberto por telhas moldadas. Os gases de combustão movem-se dentro dos tubos e o ar aquecido move-se para fora (na direção transversal). A espessura da parede dos tubos é de 13 a 16 mm e representa uma resistência térmica significativa. O coeficiente de transferência de calor (em relação à superfície do ar) é de 6 - 8 W/(m 2 graus). Os elementos dos recuperadores cerâmicos são feitos de argila refratária ou alguma outra massa refratária mais condutora de calor, seguida de queima. As vantagens dos recuperadores cerâmicos são a elevada resistência ao fogo e a boa resistência térmica - o material não se deteriora quando passam pelo recuperador gases de combustão com temperatura muito elevada.
Arroz. 1. Recuperador cerâmico tubular.
1 - ar aquecido; 2 - gases de combustão; 3 - ar frio; 4 - tubos cerâmicos; 5 - partições.
As desvantagens dos trocadores de calor cerâmicos incluem sua baixa densidade, alta capacidade térmica, má transferência de calor dos gases de combustão para o ar e interrupção das conexões dos elementos devido a choques e distorções. Essas desvantagens limitam muito a distribuição dos recuperadores cerâmicos, sendo utilizados apenas em fornos de operação contínua instalados em oficinas onde não existem mecanismos de impacto (por exemplo, martelos a vapor).
Os mais difundidos são os recuperadores metálicos, que apresentam as perspectivas de desenvolvimento mais favoráveis. A viabilidade econômica da instalação de tais recuperadores é confirmada pelo rápido retorno dos custos de construção (0,25 - 0,35 anos).
Os recuperadores metálicos são caracterizados pela transferência eficiente de calor, baixa capacidade térmica e, conseqüentemente, rápida prontidão para operação normal e alta densidade. Os elementos dos recuperadores metálicos são feitos de vários metais, dependendo da temperatura de operação do material e da composição dos gases de combustão que passam pelo recuperador. Metais ferrosos simples - aço carbono e ferro fundido cinzento - começam a oxidar intensamente em baixas temperaturas (500 ° C) e, portanto, ferro fundido e aço resistentes ao calor são utilizados para a fabricação de recuperadores, que contêm níquel, cromo, silício, alumínio como aditivos de liga, titânio, etc., que aumentam a resistência do metal à incrustação.
A solução de projeto de um recuperador de baixa temperatura com aquecimento de ar até 300 - 400 °C é relativamente simples. A criação de um recuperador de alta temperatura para aquecimento de ar e combustível gasoso até 700 - 900 °C representa um sério problema técnico que ainda não foi completamente resolvido. Sua complexidade reside em garantir o funcionamento confiável dos recuperadores durante a operação de longo prazo ao utilizar gases de combustão de alta temperatura que transportam partículas sólidas suspensas de cinzas, carbono negro, carga, etc., o que causa desgaste abrasivo. Quando estas partículas saem do fluxo, a superfície de aquecimento do recuperador no lado do gás fica contaminada. Quando o ar está empoeirado, a superfície de aquecimento também fica contaminada no lado do ar. Tubos individuais de feixes de tubos recuperadores, embutidos em placas de tubos, operam ao longo do fluxo de gases sob diferentes condições de temperatura, aquecem e se expandem de maneira diferente.
Esta diferença na expansão do tubo requer compensações diferentes, o que é difícil de conseguir. Na Fig. A Figura 2 mostra um projeto bem-sucedido de um recuperador tubular, cuja superfície de aquecimento consiste em alças suspensas livremente soldadas em coletores (caixas). O recuperador consiste em duas seções através das quais o ar passa sequencialmente em direção aos gases de combustão que se movem através dos feixes de tubos. O recuperador em forma de loop possui boa compensação de expansão térmica, condição muito importante para uma operação confiável.
Arroz. 2. Recuperador tubular em forma de alça para instalação em porco (também pode ser instalado no teto do forno).
Na Fig. A Figura 3 mostra um diagrama esquemático de um recuperador de fenda de radiação de alta temperatura, composto por dois cilindros de aço formando um vão concêntrico através do qual o ar aquecido é conduzido em alta velocidade. Dentro do cilindro, os gases de combustão quentes se movem e irradiam para a superfície do cilindro interno. Um recuperador tubular é mais confiável em operação do que um com fenda. As vantagens dos recuperadores de radiação são: menor consumo de aço resistente ao calor devido à intensa troca de calor radiante sob condições de altas temperaturas dos gases (800 - 1200 °C) e menor sensibilidade da superfície de aquecimento à contaminação. Deve ser instalado um recuperador convectivo após o recuperador de radiação, pois a temperatura dos gases após o recuperador de radiação ainda é muito elevada.
Arroz. 3. Esquemas de recuperadores de aço por radiação.
a - anel (ranhura); b - tubular com tela de linha única.
Na Fig. A Figura 4 mostra um recuperador com tubos de dupla circulação. O ar frio passa primeiro pelos tubos internos e depois entra no coletor de ar quente através de um espaço concêntrico de tubos. Os tubos internos atuam como superfície de aquecimento indireto.
Os recuperadores tubulares são caracterizados pela alta densidade e, portanto, também podem ser utilizados para aquecimento de combustíveis gasosos. O coeficiente de transferência de calor pode atingir 25 - 40 W/(m 2 graus). Os recuperadores de placas são mais difíceis de fabricar, menos densos e duráveis, e raramente são usados. Os recuperadores instalados separadamente do forno ocupam algum espaço adicional na oficina, em muitos casos isso impede a sua utilização, porém, muitas vezes é possível localizar com sucesso os recuperadores no forno ou sob o forno.
Arroz. 4. Recuperador tubular em aço com dupla circulação.
3. Caldeiras de calor residual
O calor dos gases de combustão que saem dos fornos, além do aquecimento do ar e do combustível gasoso, pode ser utilizado em caldeiras de calor residual para gerar vapor de água. Enquanto o gás e o ar aquecidos são utilizados na própria unidade do forno, o vapor é enviado para consumidores externos (para produção e necessidades energéticas).
Em todos os casos, deve-se buscar a maior recuperação de calor, ou seja, devolvê-lo ao espaço de trabalho do forno na forma de calor dos componentes de combustão aquecidos (combustível gasoso e ar). De facto, o aumento da recuperação de calor conduz à redução do consumo de combustível e à intensificação e melhoria do processo tecnológico. No entanto, a presença de recuperadores ou regeneradores nem sempre exclui a possibilidade de instalação de caldeiras de calor residual. Em primeiro lugar, as caldeiras de calor residual encontraram aplicação em grandes fornos com uma temperatura relativamente alta dos gases de combustão de exaustão: em fornos siderúrgicos abertos, em fornos reverberatórios para fundição de cobre, em fornos rotativos para queima de clínquer de cimento, na produção de cimento seco, etc. .
Arroz. 5. Caldeira de calor residual tubular a gás TKZ tipo KU-40.
1 - superaquecedor a vapor; 2 - superfície do tubo; 3 - exaustor de fumaça.
O calor dos gases de combustão que saem dos regeneradores dos fornos abertos com temperatura de 500 - 650 ° C é utilizado em caldeiras de calor residual tubulares a gás com circulação natural do fluido de trabalho. A superfície de aquecimento das caldeiras a gás consiste em tubos de fumo, dentro dos quais os gases de combustão passam a uma velocidade de aproximadamente 20 m/s. O calor dos gases para a superfície de aquecimento é transferido por convecção e, portanto, aumentar a velocidade aumenta a transferência de calor. As caldeiras a gás são fáceis de operar, não necessitam de forro ou moldura durante a instalação e possuem alta densidade de gás.
Na Fig. A Figura 5 mostra uma caldeira a gás da planta Taganrog com produtividade média D av = 5,2 t/h com expectativa de passagem de gases de combustão de até 40.000 m 3 / h. A pressão do vapor produzido pela caldeira é de 0,8 Mn/m2; temperatura 250°C. A temperatura do gás antes da caldeira é de 600 °C, atrás da caldeira 200 - 250 °C.
Nas caldeiras com circulação forçada, a superfície de aquecimento é constituída por serpentinas, cuja localização não é limitada pelas condições de circulação natural, pelo que tais caldeiras são compactas. As superfícies da bobina são feitas de tubos de pequeno diâmetro, por exemplo d = 32×3 mm, o que alivia o peso da caldeira. Com circulação múltipla, quando a relação de circulação é de 5 a 18, a velocidade da água nos tubos é significativa, pelo menos 1 m/s, como resultado a precipitação de sais dissolvidos da água nas serpentinas é reduzida, e cristalino a escala é lavada. No entanto, as caldeiras devem ser alimentadas com água purificada quimicamente usando filtros de troca catiônica e outros métodos de tratamento de água que atendam aos padrões de água de alimentação para caldeiras a vapor convencionais.
Arroz. 6. Esquema de uma caldeira de calor residual com circulação forçada múltipla.
1 - superfície economizadora; 2 - superfície de evaporação; 3 - superaquecedor a vapor; 4 - tambor coletor; 5 - bomba de circulação; 6 - coletor de lodo; 7 - exaustor de fumaça.
Na Fig. A Figura 6 mostra um diagrama da colocação das superfícies de aquecimento da serpentina em chaminés verticais. A movimentação da mistura vapor-água é realizada por uma bomba de circulação. Projetos de caldeiras deste tipo foram desenvolvidos por Tsentroenergochermet e Gipromez e são fabricados para vazões de gases de combustão de até 50 - 125 mil m 3 / h com uma produção média de vapor de 5 a 18 t / h.
O custo do vapor é de 0,4 a 0,5 rublos/t em vez de 1,2 a 2 rublos/t para o vapor extraído de turbinas a vapor de usinas termelétricas e de 2 a 3 rublos/t para o vapor de caldeiras industriais. O custo do vapor é composto pelos custos de energia para acionamento dos exaustores de fumaça, custos de preparação da água, depreciação, reparos e manutenção. A velocidade do gás na caldeira varia de 5 a 10 m/seg, o que garante uma boa transferência de calor. A resistência aerodinâmica do caminho do gás é de 0,5 - 1,5 kN/m 2, portanto a unidade deve ter tiragem artificial do exaustor de fumaça. O aumento da tiragem que acompanha a instalação de caldeiras de calor residual, via de regra, melhora o funcionamento dos fornos abertos. Estas caldeiras são muito difundidas nas fábricas, mas para o seu bom funcionamento é necessário proteger as superfícies de aquecimento do transporte de poeiras e partículas de escória e limpar sistematicamente as superfícies de aquecimento do arrastamento, soprando com vapor sobreaquecido, lavando com água (quando o caldeira está parada), por vibração, etc.
Arroz. 7. Seção transversal da caldeira de calor residual KU-80. 1 - superfície de evaporação; 2 - superaquecedor; 3 - tambor; 4 - bomba de circulação.
Para aproveitar o calor dos gases de combustão provenientes dos fornos reverberatórios de fundição de cobre, são instaladas caldeiras aquatubulares com circulação natural (Fig. 7). Os gases de combustão, neste caso, têm uma temperatura muito elevada (1100 - 1250 °C) e estão contaminados com poeiras em quantidades até 100 - 200 g/m3, algumas das poeiras têm elevadas propriedades abrasivas (abrasão), a outra parte é em um estado amolecido e pode escória na superfície de aquecimento da caldeira. É o elevado teor de poeiras dos gases que nos obriga a abandonar temporariamente a recuperação de calor nestes fornos e a limitar-nos à utilização de gases de combustão em caldeiras de calor residual.
A transferência de calor dos gases para as superfícies de evaporação da tela ocorre de forma muito intensa, garantindo a vaporização intensiva das partículas de escória, que quando resfriadas granulam e caem no funil de escória, o que evita a escória da superfície de aquecimento convectiva da caldeira. A instalação de tais caldeiras para utilização de gases com temperatura relativamente baixa (500 - 700 ° C) é impraticável devido à fraca transferência de calor por radiação.
No caso de equipar fornos de alta temperatura com recuperadores metálicos, é aconselhável instalar caldeiras de calor residual diretamente atrás das câmaras de trabalho dos fornos. Neste caso, a temperatura dos gases de combustão na caldeira desce para 1000 - 1100 °C. Nessa temperatura, já podem ser enviados para a seção resistente ao calor do recuperador. Se os gases carregam muito pó, a caldeira de recuperação é disposta em forma de peneira granuladora de escória de caldeira, o que garante a separação do arraste dos gases e facilita o funcionamento do recuperador.
Conclusão
À medida que aumentam os custos de extração de combustíveis e produção de energia, aumenta a necessidade de seu aproveitamento mais completo quando convertidos em gases combustíveis, calor do ar aquecido e da água. Embora a utilização de recursos energéticos secundários esteja frequentemente associada a investimentos de capital adicionais e a um aumento no número de pessoal de serviço, a experiência de empresas líderes confirma que a utilização de recursos energéticos secundários é economicamente muito lucrativa.
Lista de literatura usada
1. Rosengart Yu.I. Recursos energéticos secundários da metalurgia ferrosa e sua utilização. - K.: “Escola Superior”, 2008. - 328s.
2. Shchukin A. A. Fornos industriais e instalações de gás de fábricas. Livro didático para universidades. Ed. 2º, revisado M., "Energia", 1973. 224 p. com doente.
3. Kharaz D.I. Formas de utilização de recursos energéticos secundários nas indústrias químicas / D.I. - M.: Química, 1984. - 224 p.
Postado em Allbest.ru
Documentos semelhantes
Descrição do processo de preparação de combustível sólido para combustão em câmara. Criação de um esquema tecnológico de produção de energia e calor. Realização de cálculos do balanço material e térmico da unidade caldeira. Métodos para limpar gases de combustão de óxidos de enxofre e nitrogênio.
trabalho do curso, adicionado em 16/04/2014
Projeto de recuperador. Cálculo da resistência ao longo da trajetória do movimento do ar, perdas totais. Seleção de fãs. Cálculo das perdas de pressão ao longo do trajeto dos gases de combustão. Projeto de porco. Determinação da quantidade de gases de combustão. Cálculo da chaminé.
trabalho do curso, adicionado em 17/07/2010
Fundamentos teóricos da absorção. Soluções de gases em líquidos. Revisão e características dos métodos de absorção para purificação de gases de escape de impurezas ácidas, avaliação de suas vantagens e desvantagens. Cálculo tecnológico de dispositivos de purificação de gases.
trabalho do curso, adicionado em 02/04/2015
Cálculo de uma instalação de recuperação de calor de gases residuais de um forno de clínquer numa fábrica de cimento. Purificadores para tratamento complexo de gases de combustão. Parâmetros dos trocadores de calor do primeiro e segundo estágios. Determinação dos parâmetros econômicos do sistema projetado.
trabalho do curso, adicionado em 15/06/2011
Características dos gases de combustão. Desenvolvimento de uma malha de controle. Analisador de gases: finalidade e escopo, condições de operação, funcionalidade. Conversor eletropneumático série 8007. Válvula de controle com atuador pneumático.
trabalho do curso, adicionado em 22/07/2011
Tipos e composição dos gases formados durante a decomposição dos hidrocarbonetos petrolíferos durante seus processos de refino. Utilização de instalações de separação de gases saturados e insaturados e de centrais móveis de gás-gasolina. Aplicação industrial de gases de processamento.
resumo, adicionado em 11/02/2014
Sistema de gestão da qualidade da fundição de alumínio Novokuznetsk. Formação de gás durante a produção eletrolítica de alumínio. Características da tecnologia de limpeza a seco de gases de exaustão, tipos de reatores, dispositivos para captura de alumina fluorada.
relatório prático, adicionado em 19/07/2015
Execute cálculos de combustão de combustível para determinar a quantidade de ar necessária para a combustão. Composição percentual dos produtos de combustão. Determinação das dimensões do espaço de trabalho do forno. Seleção do revestimento refratário e método de eliminação dos gases de combustão.
trabalho do curso, adicionado em 03/05/2009
Descrição do esquema tecnológico para instalação de recuperação de calor de gases residuais de forno de processo. Cálculo do processo de combustão, composição do combustível e capacidades térmicas específicas médias dos gases. Cálculo do balanço térmico do forno e sua eficiência. Equipamento de caldeira de calor residual.
trabalho do curso, adicionado em 07/10/2010
Cálculo da combustão de uma mistura de coqueria e gases naturais de acordo com determinadas composições. Calor de combustão do combustível. O processo de aquecimento do metal nos fornos, as dimensões do espaço de trabalho. Emissividade dos produtos da combustão para o metal, tendo em conta o calor refletido na alvenaria.