Processo de combustão de gás. Gás natural. Processo de combustão O que é formado durante a combustão incompleta do gás natural
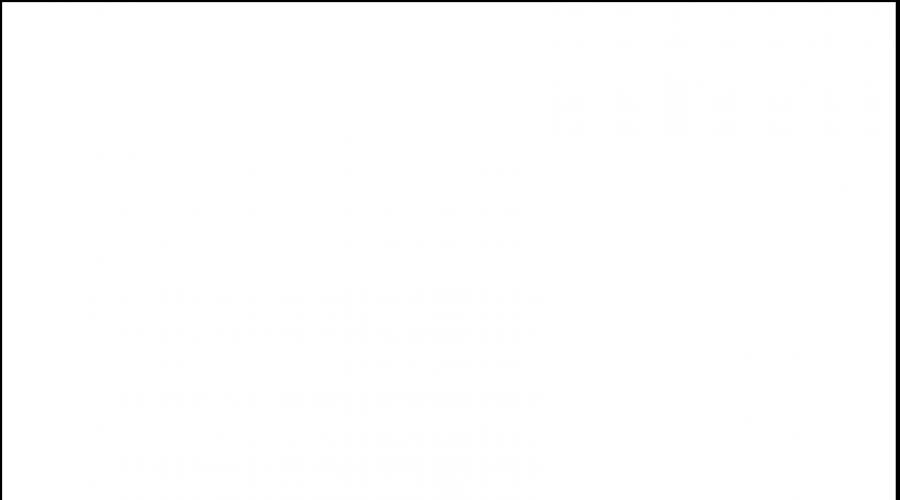
Características do metano
§ Incolor;
§ Não tóxico (não venenoso);
§ Inodoro e insípido.
§ O metano consiste em 75% de carbono e 25% de hidrogênio.
§ A gravidade específica é de 0,717 kg/m 3 (2 vezes mais leve que o ar).
§ ponto de inflamaçãoé a temperatura inicial mínima na qual a combustão começa. Para o metano é 645 o.
§ Temperatura de combustão- esta é a temperatura máxima que pode ser alcançada durante a combustão completa do gás se a quantidade de ar necessária para a combustão corresponder exatamente às fórmulas químicas de combustão. Para o metano é 1100-1400 o e depende das condições de combustão.
§ Calor de combustão– esta é a quantidade de calor que é liberada durante a combustão completa de 1 m 3 de gás e é igual a 8.500 kcal/m 3.
§ Velocidade de propagação da chama igual a 0,67 m/seg.
Mistura gás-ar
Qual gás contém:
Até 5% não queima;
De 5 a 15% explode;
Mais de 15% queima quando ar adicional é fornecido (tudo isso depende da proporção do volume de gás no ar e é chamado limites explosivos)
Os gases combustíveis são inodoros; para detectá-los no ar em tempo hábil e detectar vazamentos com rapidez e precisão, o gás é odorizado, ou seja, exala um cheiro. Para tanto, utiliza-se ETILMERCOPTANO. A taxa de odorização é de 16 g por 1000 m 3. Se houver 1% de gás natural no ar, você deverá cheirá-lo.
O gás usado como combustível deve atender aos requisitos GOST e conter impurezas prejudiciais por 100m 3 não mais do que:
Sulfeto de hidrogênio 0,0 2 G /m.cubo
Amônia 2 gr.
Ácido cianídrico 5 g.
Resina e pó 0,001 g/m3
Naftaleno 10 gr.
Oxigênio 1%.
A utilização do gás natural tem uma série de vantagens:
· ausência de cinzas e poeiras e remoção de partículas sólidas para a atmosfera;
· elevado calor de combustão;
· facilidade de transporte e combustão;
· o trabalho do pessoal de serviço é facilitado;
· as condições sanitárias e higiênicas nas caldeiras e áreas adjacentes são melhoradas;
· ampla gama de controle automático.
Ao utilizar gás natural, são necessárias precauções especiais porque... o vazamento é possível através de vazamentos na junção do gasoduto e conexões. A presença de mais de 20% de gás em uma sala causa asfixia; seu acúmulo em volume fechado de mais de 5% a 15% leva à explosão da mistura gás-ar. A combustão incompleta libera monóxido de carbono, que é venenoso mesmo em baixas concentrações (0,15%).
Combustão de gás natural
Queimandoé chamada de combinação química rápida de partes inflamáveis do combustível com o oxigênio do ar, ocorre em altas temperaturas, é acompanhada pela liberação de calor com formação de chama e produtos de combustão. A combustão acontece completo e incompleto.
Combustão total– Ocorre quando há oxigênio suficiente. Falta de oxigênio causa combustão incompleta, em que é liberado menos calor do que com monóxido de carbono total (tem efeito tóxico para o pessoal operacional), forma-se fuligem na superfície da caldeira e aumenta a perda de calor, o que leva ao consumo excessivo de combustível, diminuição da eficiência da caldeira, e poluição do ar.
Os produtos da combustão do gás natural são– dióxido de carbono, vapor de água, algum excesso de oxigênio e nitrogênio. O excesso de oxigênio está contido nos produtos de combustão apenas nos casos em que a combustão ocorre com excesso de ar, e o nitrogênio está sempre contido nos produtos de combustão, porque é um componente do ar e não participa da combustão.
Os produtos da combustão incompleta do gás podem ser monóxido de carbono, hidrogénio e metano não queimados, hidrocarbonetos pesados, fuligem.
Reação do metano:
CH 4 + 2O 2 = CO 2 + 2H 2 O
De acordo com a fórmula Para a combustão de 1 m 3 de metano são necessários 10 m 3 de ar, que contém 2 m 3 de oxigênio. Na prática, para queimar 1 m 3 de metano é necessário mais ar, levando em consideração todos os tipos de perdas, para isso é utilizado um coeficiente; PARA excesso de ar, que = 1,05-1,1.
Volume de ar teórico = 10 m3
Volume de ar prático = 10*1,05=10,5 ou 10*1,1=11
Completude da combustão o combustível pode ser determinado visualmente pela cor e natureza da chama, bem como por meio de um analisador de gás.
Chama azul transparente - combustão completa do gás;
Vermelho ou amarelo com listras esfumaçadas – a combustão está incompleta.
A combustão é regulada aumentando o fornecimento de ar para a fornalha ou diminuindo o fornecimento de gás. Este processo usa ar primário e secundário.
Ar secundário– 40-50% (misturado com gás no forno da caldeira durante a combustão)
Ar primário– 50-60% (misturado com gás no queimador antes da combustão) uma mistura gás-ar é usada para combustão
A combustão caracteriza velocidade de distribuição de chamaé a velocidade na qual o elemento frontal da chama distribuído por fluxo relativamente fresco de mistura gás-ar.
A taxa de combustão e propagação da chama depende de:
· na composição da mistura;
· na temperatura;
· da pressão;
· na proporção de gás e ar.
A taxa de combustão determina uma das principais condições para o funcionamento confiável da sala da caldeira e a caracteriza separação de chama e avanço.
Quebra de chama– ocorre se a velocidade da mistura gás-ar na saída do queimador for superior à velocidade de combustão.
Razões para separação: aumento excessivo do fornecimento de gás ou vácuo excessivo na fornalha (tiragem). A separação da chama é observada durante a ignição e quando os queimadores são ligados. A separação da chama leva à contaminação por gás do forno e dos dutos de gás da caldeira e à explosão.
Avanço da chama– ocorre se a velocidade de propagação da chama (velocidade de queima) for maior que a velocidade de saída da mistura gás-ar do queimador. A ruptura é acompanhada pela combustão da mistura gás-ar dentro do queimador, o queimador aquece e falha. Às vezes, uma ruptura é acompanhada por um estalo ou explosão dentro do queimador. Neste caso, não só o queimador, mas também a parede frontal da caldeira podem ser destruídos. O overshoot ocorre quando há uma diminuição acentuada no fornecimento de gás.
Se a chama se apagar e romper, o pessoal de manutenção deve interromper o fornecimento de combustível, descobrir e eliminar a causa, ventilar a fornalha e as condutas de combustão durante 10-15 minutos e reacender o fogo.
O processo de combustão do combustível gasoso pode ser dividido em 4 etapas:
1. Vazamento de gás do bocal do queimador para o dispositivo do queimador sob pressão e em velocidade aumentada.
2. Formação de uma mistura de gás e ar.
3. Ignição da mistura combustível resultante.
4. Combustão de uma mistura inflamável.
Gasodutos
O gás é fornecido ao consumidor por meio de gasodutos - externo e interno– para postos de distribuição de gás localizados fora da cidade, e deles através de gasodutos até pontos reguladores de gás fraturamento hidráulico ou dispositivo de controle de gás GRU empreendimentos industriais.
Os gasodutos são:
· alta pressão da primeira categoria acima de 0,6 MPa até 1,2 MPa inclusive;
· alta pressão da segunda categoria acima de 0,3 MPa a 0,6 MPa;
· pressão média da terceira categoria acima de 0,005 MPa a 0,3 MPa;
· baixa pressão da quarta categoria até 0,005 MPa inclusive.
MPa – significa Mega Pascal
Apenas gasodutos de média e baixa pressão são instalados na sala das caldeiras. O trecho do gasoduto da rede de distribuição de gás (cidade) até as instalações junto com o dispositivo de desconexão é denominado entrada.
O gasoduto de entrada é considerado o trecho que vai do dispositivo de desconexão na entrada se for instalado fora da sala até o gasoduto interno.
Deve haver válvula na entrada do gás na sala da caldeira em local iluminado e conveniente para manutenção. Deve haver um flange isolante na frente da válvula para proteção contra correntes parasitas. Em cada ramal do gasoduto até a caldeira são fornecidos pelo menos 2 dispositivos de desligamento, um dos quais instalado diretamente na frente do queimador. Além das ferragens e instrumentação do gasoduto, deve ser instalado um dispositivo automático na frente de cada caldeira para garantir o funcionamento seguro da caldeira. Para evitar a entrada de gases no forno da caldeira em caso de dispositivos de corte defeituosos, são necessárias velas de purga e gasodutos de segurança com dispositivos de corte, que devem estar abertos quando as caldeiras estiverem ociosas. Os gasodutos de baixa pressão são pintados de amarelo nas salas das caldeiras, e os gasodutos de média pressão são pintados de amarelo com anéis vermelhos.
Queimadores a gás
Queimadores a gás- um dispositivo queimador de gás destinado a fornecer ao local de combustão, dependendo dos requisitos tecnológicos, uma mistura gás-ar preparada ou gás e ar separados, bem como garantir a combustão estável do combustível gasoso e controlar o processo de combustão.
Os seguintes requisitos se aplicam aos queimadores:
· os principais tipos de queimadores devem ser produzidos em série nas fábricas;
· os queimadores devem garantir a passagem de uma determinada quantidade de gás e a integralidade da sua combustão;
· garantir uma quantidade mínima de emissões nocivas para a atmosfera;
· deve operar sem ruído, separação de chama ou ruptura;
· deve ser de fácil manutenção e conveniente para inspeção e reparo;
· se necessário, poderá ser utilizado como combustível de reserva;
· amostras de queimadores recém-criados e existentes estão sujeitas a testes GOST;
A principal característica dos queimadores é a sua Poder Térmico, que é entendido como a quantidade de calor que pode ser liberada durante a combustão completa do combustível fornecido pelo queimador. Todas essas características podem ser encontradas na ficha técnica do queimador.
A combustão é uma reação que converte a energia química de um combustível em calor.
A combustão pode ser completa ou incompleta. A combustão completa ocorre quando há oxigênio suficiente. Sua falta causa combustão incompleta, durante a qual é liberado menos calor do que durante a combustão completa, e o monóxido de carbono (CO), que tem efeito tóxico para o pessoal operacional, forma-se fuligem, depositando-se na superfície de aquecimento da caldeira e aumentando a perda de calor, o que leva ao consumo excessivo de combustível e à diminuição da eficiência da caldeira, poluição do ar.
Para queimar 1 m 3 de metano, são necessários 10 m 3 de ar, que contém 2 m 3 de oxigênio. Para garantir a combustão completa do gás natural, o ar é fornecido ao forno com um ligeiro excesso. A relação entre o volume de ar realmente consumido V d e o V t teoricamente necessário é chamada de coeficiente de excesso de ar = V d / V t. Este indicador depende do projeto do queimador de gás e do forno: quanto mais perfeitos forem, menor. . É necessário garantir que o coeficiente de excesso de ar não seja inferior a 1, pois isso leva à combustão incompleta do gás. Um aumento na proporção de excesso de ar reduz a eficiência da unidade caldeira.
A integridade da combustão do combustível pode ser determinada usando um analisador de gás e visualmente - pela cor e natureza da chama:
azulado transparente - combustão completa;
vermelho ou amarelo - a combustão está incompleta.
A combustão é regulada aumentando o fornecimento de ar ao forno da caldeira ou diminuindo o fornecimento de gás. Este processo utiliza ar primário (misturado com gás no queimador - antes da combustão) e secundário (combinado com gás ou mistura gás-ar no forno da caldeira durante a combustão).
Nas caldeiras equipadas com queimadores de difusão (sem alimentação de ar forçado), o ar secundário, sob a influência do vácuo, entra no forno pelas portas de purga.
Nas caldeiras equipadas com queimadores de injeção: o ar primário entra no queimador por injeção e é regulado por uma arruela de ajuste, e o ar secundário entra pelas portas de purga.
Nas caldeiras com queimadores misturadores, o ar primário e secundário é fornecido ao queimador por um ventilador e controlado por válvulas de ar.
A violação da relação entre a velocidade da mistura gás-ar na saída do queimador e a velocidade de propagação da chama leva à separação ou salto da chama nos queimadores.
Se a velocidade da mistura gás-ar na saída do queimador for maior que a velocidade de propagação da chama, há separação, e se for menor, há ruptura.
Se a chama explodir e romper, o pessoal de manutenção deverá apagar a caldeira, ventilar a fornalha e os fumos e reacender a caldeira.
O combustível gasoso é cada vez mais utilizado a cada ano em diversos setores da economia nacional. Na produção agrícola, o combustível gasoso é amplamente utilizado para fins tecnológicos (para aquecimento de estufas, estufas, secadores, complexos pecuários e avícolas) e domésticos. Recentemente, tornou-se cada vez mais utilizado em motores de combustão interna.
Em comparação com outros tipos, os combustíveis gasosos apresentam as seguintes vantagens:
queima em quantidade teórica de ar, o que garante alta eficiência térmica e temperatura de combustão;
durante a combustão não forma produtos indesejáveis de destilação a seco e compostos de enxofre, fuligem e fumaça;
é fornecido com relativa facilidade através de gasodutos a instalações de consumo remotas e pode ser armazenado centralmente;
inflama facilmente em qualquer temperatura ambiente;
requer custos de produção relativamente baixos, o que significa que é um tipo de combustível mais barato em comparação com outros tipos;
pode ser utilizado na forma comprimida ou liquefeita para motores de combustão interna;
possui altas propriedades antidetonantes;
não forma condensação durante a combustão, o que garante uma redução significativa do desgaste das peças do motor, etc.
Ao mesmo tempo, o combustível gasoso também possui certas propriedades negativas, que incluem: efeito tóxico, formação de misturas explosivas quando misturado com ar, fácil escoamento através de vazamentos nas conexões, etc. os regulamentos de segurança relevantes são necessários.
A utilização de combustíveis gasosos é determinada pela sua composição e propriedades da parte hidrocarbonada. Os mais utilizados são o gás natural ou associado proveniente de campos de petróleo ou gás, bem como gases industriais provenientes de refinarias de petróleo e outras plantas. Os principais componentes desses gases são os hidrocarbonetos com número de átomos de carbono em uma molécula de um a quatro (metano, etano, propano, butano e seus derivados).
Os gases naturais provenientes dos campos de gás consistem quase inteiramente em metano (82...98%), com pouco uso de combustível gasoso para motores de combustão interna. A frota cada vez maior de veículos requer cada vez mais combustível. É possível resolver os mais importantes problemas económicos nacionais de abastecimento estável de motores automóveis com portadores de energia eficientes e de redução do consumo de combustíveis líquidos de origem petrolífera através da utilização de combustíveis gasosos - petróleo liquefeito e gases naturais.
Para automóveis, são utilizados apenas gases de alto ou médio teor calórico. Ao funcionar com gás de baixa caloria, o motor não desenvolve a potência necessária e a autonomia do veículo também é reduzida, o que não é economicamente rentável. Pai). São produzidos os seguintes tipos de gases comprimidos: coque natural, coque mecanizado e coque enriquecido
O principal componente inflamável desses gases é o metano. Tal como acontece com o combustível líquido, a presença de sulfeto de hidrogênio no combustível gasoso é indesejável devido ao seu efeito corrosivo nos equipamentos a gás e nas peças do motor. O número de octanas dos gases permite aumentar os motores dos automóveis em termos de taxa de compressão (até 10...12).
A presença de cianogênio CN no gás automotivo é extremamente indesejável. Quando combinado com a água, forma ácido cianídrico, sob a influência do qual se formam pequenas fissuras nas paredes dos cilindros. A presença de substâncias resinosas e impurezas mecânicas no gás leva à formação de depósitos e contaminantes em equipamentos de gás e peças de motores.
Um defeito semelhante está associado a um mau funcionamento do sistema de automação da caldeira. Tenha em atenção que é estritamente proibido operar a caldeira com a automação desligada (por exemplo, se o botão de arranque for pressionado à força). Isto pode levar a consequências trágicas, pois se o fornecimento de gás for brevemente interrompido ou se a chama for extinta por um forte fluxo de ar, o gás começará a fluir para a sala. Para entender os motivos da ocorrência de tal defeito, vamos dar uma olhada mais de perto no funcionamento do sistema de automação. Na Fig. A Figura 5 mostra um diagrama simplificado deste sistema. O circuito consiste em um eletroímã, uma válvula, um sensor de tiragem e um termopar. Para ligar a ignição, pressione o botão Iniciar. A haste conectada ao botão pressiona a membrana da válvula e o gás começa a fluir para o dispositivo de ignição. Depois disso, o acendedor acende. A chama piloto toca o corpo do sensor de temperatura (termopar). Após algum tempo (30...40 s), o termopar aquece e um EMF aparece em seus terminais, o que é suficiente para acionar o eletroímã. Este último, por sua vez, fixa a haste na posição inferior (conforme Fig. 5). O botão Iniciar agora pode ser liberado. O sensor de tração é composto por uma placa bimetálica e um contato (Fig. 6). O sensor está localizado na parte superior da caldeira, próximo à tubulação de exaustão dos produtos da combustão para a atmosfera. Se um tubo estiver entupido, sua temperatura aumentará drasticamente. A placa bimetálica aquece e interrompe o circuito de alimentação de tensão do eletroímã - a haste não é mais segurada pelo eletroímã, a válvula fecha e o fornecimento de gás é interrompido.



Os produtos de combustão do gás natural são dióxido de carbono, vapor de água, algum excesso de oxigênio e nitrogênio. Os produtos da combustão incompleta do gás podem ser monóxido de carbono, hidrogênio e metano não queimados, hidrocarbonetos pesados e fuligem.
Quanto mais dióxido de carbono CO 2 nos produtos de combustão, menos monóxido de carbono CO haverá neles e mais completa será a combustão. O conceito de “teor máximo de CO 2 nos produtos de combustão” foi introduzido na prática. A quantidade de dióxido de carbono nos produtos de combustão de alguns gases é mostrada na tabela abaixo.
A quantidade de dióxido de carbono nos produtos da combustão de gás
Usando os dados da tabela e conhecendo a porcentagem de CO 2 nos produtos de combustão, você pode determinar facilmente a qualidade da combustão do gás e o coeficiente de excesso de ar a. Para isso, por meio de um analisador de gases, deve-se determinar a quantidade de CO 2 nos produtos da combustão do gás e dividir o valor de CO 2max retirado da tabela pelo valor resultante. Assim, por exemplo, se durante a queima do gás os produtos de sua combustão contiverem 10,2% de dióxido de carbono, então o coeficiente de excesso de ar na fornalha
α = análise CO 2max /CO 2 = 11,8/10,2 = 1,15.
A forma mais avançada de controlar o fluxo de ar no forno e a integridade de sua combustão é analisar os produtos da combustão por meio de analisadores automáticos de gases. Os analisadores de gases coletam periodicamente uma amostra dos gases de exaustão e determinam o conteúdo de dióxido de carbono neles, bem como a quantidade de monóxido de carbono e hidrogênio não queimado (CO + H 2) em porcentagem de volume.
Se a leitura do ponteiro do analisador de gás na escala (CO 2 + H 2) for zero, isso significa que a combustão está completa e não há monóxido de carbono ou hidrogênio não queimado nos produtos de combustão. Se a seta se desviar de zero para a direita, os produtos da combustão contêm monóxido de carbono e hidrogênio não queimado, ou seja, ocorre combustão incompleta. Em outra escala, a agulha do analisador de gases deve mostrar o teor máximo de CO 2max nos produtos de combustão. A combustão completa ocorre na porcentagem máxima de dióxido de carbono, quando o ponteiro da escala CO + H 2 está em zero.
CH 4+ 2 × O 2 +7,52 × N 2 = CO 2 +2× H2O + 7,5× N 2 +8500 Kcal
Ar:
, daí a conclusão:
por 1 m 3 O 2 há 3,76 m 3N 2
Ao queimar 1 m 3 de gás, devem ser consumidos 9,52 m 3 de ar (desde 2 + 7,52). Após a combustão completa do gás, é liberado o seguinte:
· Dióxido de carbono CO2;
· Vapor de água;
· Nitrogênio (lastro de ar);
· O calor é liberado.
Quando 1 m 3 de gás é queimado, são liberados 2 m 3 de água. Se a temperatura dos gases de combustão de exaustão na chaminé for inferior a 120 °C e o tubo for alto e não isolado, então estes vapores de água condensam-se ao longo das paredes da chaminé até à sua parte inferior, de onde entram num tanque ou linha de drenagem através de um buraco.
Para evitar a formação de condensação na chaminé, é necessário isolar a chaminé ou reduzir a altura da chaminé, calculando previamente a tiragem na chaminé (ou seja, é perigoso reduzir a altura da chaminé).
Produtos da combustão completa do gás.
· Dióxido de carbono;
· Vapor de água.
Produtos da combustão incompleta de gás.
· Monóxido de carbono CO;
· Hidrogênio H2;
· Carbono C.
Em condições reais, para combustão de gás, o fornecimento de ar é ligeiramente maior do que o calculado pela fórmula. A relação entre o volume real de ar fornecido para combustão e o volume calculado teoricamente é chamada de coeficiente de excesso de ar (a). Não deve ser superior a 1,05...1,2:
O excesso de ar excessivo reduz a eficiência. caldeira
À volta da cidade:
175 kg de combustível padrão são gastos para gerar 1 Gcal de calor.
Por comércio:
162 kg de combustível padrão são gastos para gerar 1 Gcal de calor.
O excesso de ar é determinado pela análise dos gases de combustão com um dispositivo.
Coeficienteao comprimento do espaço de combustão não é o mesmo. No início da fornalha no queimador, e quando os gases de combustão saem pela chaminé, é maior do que o calculado devido a fugas de ar pelo revestimento (caixa) com fugas da caldeira.
Esta informação aplica-se a caldeiras que operam sob vácuo, quando a pressão na fornalha é inferior à atmosférica.
Caldeiras que operam sob pressão excessiva de gás no forno da caldeira são chamadas de caldeiras pressurizadas. Nessas caldeiras, o revestimento deve ser muito estanque para evitar que os gases de combustão entrem na sala da caldeira e envenenem as pessoas.