Arbolito faça você mesmo em casa. Como fazer blocos de concreto de madeira com suas próprias mãos? A fase final da produção em vídeo
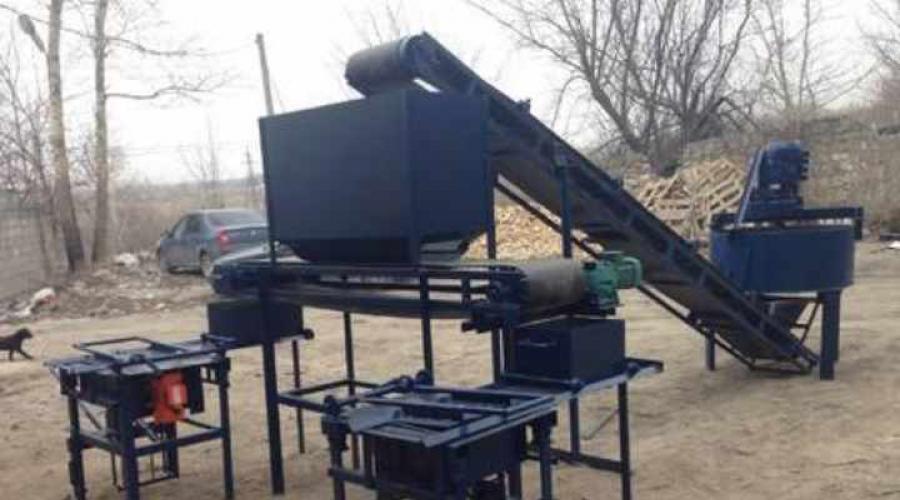
Hoje em dia, os preços da energia estão a crescer todos os dias, por isso, na construção de uma casa, a questão do calor e do isolamento térmico vem à tona.
No momento, existem diferentes tecnologias para isolar o edifício.
Para isolamento de edifícios, use diferentes externos ou internos.
Mas muitos problemas são resolvidos na fase de construção, caso sejam utilizados materiais de construção com boas qualidades de isolamento térmico durante a construção do edifício.
Neste artigo, mostraremos como fazer blocos com suas próprias mãos.
Arbolite costumava ser usado com muita frequência na construção de edifícios, mas com o tempo esse material foi esquecido e em nosso tempo nem todos os desenvolvedores sabem que esse material de construção existe.
Não faz muito tempo, esse material voltou a ser procurado e começou a aparecer à venda em lojas de ferragens ou mercados. Mas se não for possível comprar esse material, você terá a oportunidade de fazer você mesmo.
Então, vamos analisar o que é concreto de madeira e quais são suas vantagens.
Composto
Além disso, essas substâncias podem causar processos de fermentação em blocos acabados, o que leva à formação de vazios, inchaço da superfície e similares. Para remover os efeitos de substâncias negativas, eles são neutralizados com uma solução de cloreto de cálcio, sulfato de alumínio ou "vidro líquido" e, para neutralizar a vida biológica do material, é tratado com um anti-séptico.
O próximo passo na fabricação de blocos de concreto de madeira é a adição de ingredientes ligantes à massa do cavaco. Vários plastificantes também são adicionados à massa. Em seguida, a massa resultante é enviada para moldagem.
A tecnologia de conformação pode ser diferente, por exemplo, prensagem ou compactação em um suporte vibratório. Depois de preenchidos, os formulários são enviados para a área de secagem. No local de secagem, os blocos futuros são secos por dois dias a uma temperatura de 60 graus.
Após a secagem, se necessário, os blocos são modificados mecanicamente e só então os blocos acabados são enviados ao armazém para armazenamento e venda. O número de componentes não é exato e, portanto, pode estar dentro de certos limites, dependendo dos produtos específicos e de sua finalidade.
Se for necessário fabricar produtos de grande porte a partir de arbalita, são usados reforços adicionais e a instalação de placas embutidas tecnológicas e alças de aparelhamento.
Blocos de arbolito faça você mesmo
O número de produção em pequena escala de blocos de arbalita cresceu significativamente recentemente e esse material de construção começou a aparecer cada vez mais à venda.
Mas esses blocos podem ser feitos com suas próprias mãos. E assim o que é necessário para a produção de blocos de concreto de madeira com suas próprias mãos.
Materiais e estoque necessários

Processo de manufatura
As etapas de produção dos blocos de concreto de madeira são descritas a seguir.
Preparação de polpa de madeira
É limpo de sujeira, poeira e terra.
A madeira precisa ser limpa de açúcares dissolvidos, para isso a madeira pode ser mantida ao ar livre por três meses.
Mas é melhor tratar a madeira com uma solução de cloreto de cálcio a 1,5% (200 litros por 1 m³ de madeira). Nesta solução, a madeira é mantida por até três dias com agitação regular.
Mas o segundo método de processamento é adequado apenas para coníferas. Você ainda pode processar madeira com "vidro líquido", mas essa substância degrada a qualidade dos blocos acabados.
Antes de iniciar a próxima etapa de trabalho, as lascas de madeira devem ser tratadas com argamassa de cal. Afinal, a solução neutraliza completamente o processo químico na árvore e confere propriedades anti-sépticas à árvore.
As aparas de madeira são embebidas em uma solução de cal apagada (5 a 10%) por três horas, depois as aparas são jogadas em uma peneira para vidro da água. Depois disso, a madeira bruta é usada para preparar uma mistura de concreto-partícula.
Fazendo uma mistura
Prepare uma mistura para a formação de blocos.
Água e lascas de madeira e vidro líquido (não mais de 1%) são carregados na betoneira. Quando a massa estiver na forma de uma pasta líquida, adicione um pouco (M-400) e aumente a quantidade de água. Proporções: levamos quatro partes de água para quatro partes de maravalha e três partes de cimento.
Depois de adicionar todos os componentes, a solução é agitada até obter uma massa homogênea, a massa deve ser plástica e ao mesmo tempo quebradiça. Se a massa for comprimida em um punho, ela deve manter sua forma.
moldagem
No final do dia, a cofragem é removida ou os blocos secos são removidos. Os blocos são colocados sob um dossel para secagem e endurecimento. Esse processo leva aproximadamente duas ou três semanas, dependendo da umidade e temperatura do ar.
Para obter concreto de madeira de alta qualidade, é necessário entender que a produção de concreto de madeira é fundamentalmente diferente da produção de todos os outros tipos de concreto leve, tanto leve (concreto de poliestireno, concreto de argila expandida) quanto celular (concreto aerado e espuma de concreto).
Componentes de concreto de madeira:
1) lascas de madeira.
2) cimento.
3) aditivos químicos.
4) água.
Apesar do pequeno número de componentes e da aparente facilidade de fabricação, a produção de concreto de madeira é um processo trabalhoso, visto que cavacos de madeira e cimento não aderem naturalmente um ao outro. E para obter um único material, é necessário observar vários pontos tecnológicos, caso contrário você não obterá concreto de madeira. Ao mesmo tempo, deve-se entender que nesta seção estamos falando sobre a obtenção de concreto de madeira de alta qualidade que atende a todos os requisitos do GOST 19222-84.
A produção de concreto de madeira na estação fria é possível com uma temperatura interna 24 horas estável de pelo menos + 12 + 15 graus. A uma temperatura mais baixa, há um problema com a hidratação do cimento e, consequentemente, com a qualidade do bloco.
Atenção especial na produção de concreto de madeira deve ser dada ao enchimento - lascas de madeira. Para obter concreto de madeira de alta qualidade, lascas de madeira de coníferas, principalmente pinho e abeto, são mais adequadas. De acordo com GOST 19222-84, o seguinte deve ser usado como cargas orgânicas: madeira triturada de resíduos madeireiros, serraria e marcenaria de espécies de coníferas (abeto, pinheiro, abeto) e madeira dura (bétula, álamo, faia, álamo), cânhamo e linho fogueira, caules picados de algodão e palha de arroz triturada. Além disso, o concreto de madeira pode ser feito com base em lascas de larício. Mas o uso de cavacos de madeira de lariço exige um aumento radical no volume de aditivos químicos para o processamento de cavacos de madeira, pelo menos 2 vezes em comparação com o pinho.
Lascas de madeira (uma forma de cavacos de madeira). Para a fabricação de concreto de madeira, os cavacos devem ter uma determinada forma. Os agregados orgânicos devem atender aos seguintes requisitos:
A) madeira triturada: - o tamanho das partículas de madeira não deve exceder 40 mm de comprimento, 10 mm de largura e 5 mm de espessura;
B) cinzas de cânhamo e linho, talos de algodão triturados e palha de arroz triturada: o comprimento das partículas não deve exceder 40 mm; o teor de estopa e estopa não deve ser superior a 5% em peso da mistura de agregados secos.
Madeira picada, fogo de cânhamo e linho, talos de algodão picados e palha de arroz não devem apresentar sinais visíveis de mofo e podridão, bem como impurezas de materiais estranhos (pedaços de argila, camada vegetativa do solo, pedras, areia, etc.), e no inverno, impurezas de gelo ou neve.
A madeira é um material anisotrópico, portanto, as lascas de madeira devem ter uma forma de agulha com um fator de forma (a proporção do maior para o menor tamanho) igual a 5-10, uma espessura de 3-5 mm e um comprimento máximo de até 25 milímetros. As partículas desta forma têm valores absolutos mais próximos de deformações de umidade ao longo e através das fibras e, portanto, ao contrário do enchimento com um fator de forma menor, podem reduzir o impacto negativo das deformações de umidade do enchimento de madeira na formação da estrutura e na resistência da madeira concreto.
Os melhores resultados são obtidos com madeira lascada especialmente preparada a partir de resíduos de madeira grumosa de lenha, obtida de acordo com um esquema típico de duas etapas: obtenção de lascas em picadores e, em seguida, lascamento e homogeneização em moinhos de martelos.
Para a produção de concreto de madeira, é desejável usar cimentos de alta qualidade, pelo menos a partir de M400 e acima. A solução mais ideal no momento em termos de relação preço-qualidade é o uso de cimento de grau M500 e superior. Ao usar cimento, deve-se ter em mente que suas características serão inferiores às declaradas pelo fabricante. No momento, a marca de cimento da maioria dos fornecedores e fabricantes não corresponde à declarada e costuma ser inferior em pelo menos 40 a 50 unidades. Ao mesmo tempo, muitas vezes há casos ao comprar cimento M500, na verdade você compra cimento M400. Tudo isso deve ser levado em consideração ao calcular o volume de cimento.
Chips e cimento não aderem um ao outro sem pré-tratamento de cavacos com aditivos químicos. Tal processamento é necessário para eliminar o açúcar dos cavacos, o que impede a adesão de cavacos e cimento, além de acelerar o endurecimento do concreto de madeira. Uma lista de possíveis aditivos químicos para eliminar açúcares e acelerar o endurecimento do concreto de madeira é fornecida em CH 549-82: cloreto de cálcio GOST 450-77; copo de água GOST 13078–67; bloco de silicato GOST 13079–67; sulfato de alumina GOST 5155–74; óxido de cálcio (cal) GOST 9179-77.
A aplicação prática real de aditivos químicos mostrou que agora para a produção de concreto de madeira, ou cloreto de cálcio é usado principalmente (sozinho e em combinação com vidro líquido) ou sulfato de alumina (sozinho e em combinação com cal).
Os aditivos são introduzidos na composição da mistura de arbólitos exclusivamente na forma de soluções aquosas, ou seja, após pré-embebição e dissolução em água.
Na União Soviética, a produção de arbólito era muito difundida e os principais métodos de compactação da mistura de arbólito eram: prensagem cíclica (decapagem imediata), vibração com carga (decapagem imediata), vibrocompressão com tampa de fixação, vibro-laminação de potência, colocação e compactação camada por camada, etc. Cada um desses métodos tem vantagens e desvantagens. O critério para avaliar a otimalidade da estrutura compactada é o seguinte: quanto mais compactada for a estrutura do concreto de madeira, menor deve ser a pressão de dilatação e a magnitude relativa da deformação por dilatação. Durante a vibrocompactação com carga, as partículas de enchimento de madeira, movendo-se uma em relação à outra, ocupam a posição ideal na estrutura do concreto de madeira, proporcionando a maior área das zonas de contato; ao mesmo tempo, a redeformação - raspressovka - diminui. Com o método usual de prensar a mistura de arbólitos para obter produtos de mesma densidade média, as partículas de carga de madeira são comprimidas, causando deformações elásticas, o que leva à despressurização do produto moldado e, finalmente, à diminuição da resistência final.
Produção de concreto de madeira usando tamper manual no piso da sala.
Esta é a forma mais econômica de produzir concreto de madeira ao abrir um empreendimento. É necessário ter um misturador do tipo forçado; um recipiente no qual o produto químico será diluído. aditivos; recipientes de medição com os quais cimento e lascas de madeira serão despejados no misturador; moldes de aço nos quais o arbólito será compactado; um carrinho no qual a mistura de arbólitos será transportada do misturador para os moldes; uma superfície plana na qual o bloco será formado (piso de concreto, madeira compensada, palete com superfície de madeira compensada); paletes sobre os quais o concreto de madeira acabado será dobrado.
A produção de concreto de madeira em uma máquina vibratória com carga é uma das maneiras mais otimizadas de produzir concreto de madeira em termos de custos ao abrir um empreendimento. Apesar de tais máquinas não serem vendidas atualmente, seu design não é complicado e permite que qualquer empresa industrial que fabrique máquinas-ferramentas as fabrique de acordo com elas. tarefa do cliente. Além disso, uma versão simples dessa máquina pode ser feita de forma independente, com a ajuda de um soldador profissional.
Na máquina, vibrar com uma carga pode produzir tanto uma pequena quantidade de concreto de madeira por mês (150-200 m3), quanto muito maior, de 400 m3 por mês ou mais.
Os aditivos químicos são pré-diluídos em um recipiente com água. Agite a solução antes de usar.
Lascas de madeira são despejadas no misturador. Requisitos para cavacos: além do tamanho, os cavacos devem estar com uma quantidade mínima de sujeira; a quantidade de casca não deve ser superior a 10-15%; os cavacos não devem ser frescos, pelo menos os cavacos (árvore) devem ser de 1-2 meses após o corte. Ideal para 3-4 meses.
O misturador é iniciado e no processo de mistura dos chips, uma solução aquosa de produto químico é derramada. aditivos. A mistura dura pelo menos 10-20 segundos e, em seguida, o cimento é derramado.
O cimento é vazado de forma a cobrir o máximo de área de cavaco com pasta de cimento. O ideal é 100%. Depois de derramar o cimento, a mistura dura pelo menos 2-3 minutos. Depois que o cimento é despejado no misturador, é indesejável adicionar água ao misturador, pois a água lavará a pasta de cimento dos cavacos e isso pode levar a uma diminuição da resistência dos blocos.
Na plataforma vibratória da máquina, os paletes são colocados sob os blocos, um ao lado do outro. Uma forma comum é então abaixada sobre esses paletes para o número necessário de blocos. O formulário é fixado na máquina durante o período de produção do bloco. O formulário é preenchido com uma mistura de arbólito pronta.
É aconselhável empilhar os blocos um em cima do outro não antes de 3-4 dias. Dobre os blocos em 3 fileiras de altura e mais preferencialmente não antes de 6-7 dias após a fabricação.
Os blocos podem ser transportados para os clientes de 10 a 15 dias após a produção em clima seco e não antes de 15 a 20 dias em clima úmido.
Os blocos de arbolito têm sido usados em construções baixas desde meados dos anos 40 do século passado. Naquela época, muitas fábricas para sua produção foram construídas. Hoje em dia, continua a ser um material de construção popular.
Os blocos de arbolito são feitos de serragem, aparas, cimento, água e produtos químicos. Eles pertencem à classe de concreto leve. Seu uso depende do índice de densidade. Eles podem ser usados:
- como material isolante de calor;
- para a construção de paredes sem carga;
- para a construção de edifícios comerciais.
Se o índice de densidade for inferior a 500 kg / m3, o concreto de madeira é considerado isolante de calor. Se este indicador estiver na faixa de 500 a 800 kg/m3, então é estrutural. As vantagens do uso de blocos de concreto de madeira estão no baixo custo dos componentes e, portanto, no custo total do material.
Os blocos de arbolito (concreto serragem) são bons isolantes térmicos. Eles acumulam perfeitamente e retêm o calor na casa. A produção de blocos é bastante simples, então você mesmo pode fazê-los.
Vantagens e desvantagens
Para avaliar blocos de concreto de serragem como material de construção, você precisa descobrir quais são seus prós e contras. Eles têm as seguintes vantagens:

A maior desvantagem dos blocos de concreto de madeira é a alta permeabilidade à umidade. Se o material acumular muita umidade, ele pode até desmoronar.
Esta desvantagem é combatida através da aplicação de revestimentos protetores especiais, cobrindo as paredes com camadas de barreira hidro e vapor. Além disso, os blocos de arbolito são instáveis para roedores.
As paredes podem ser protegidas de roedores com revestimento de placas OSB, malha de arame ou, após a construção da fundação, fazer uma concretagem de 50 cm de altura.
Assista à nossa compilação de vídeos sobre o tema:
Tecnologia de manufatura
A produção de blocos de concreto de serragem consiste nas seguintes etapas:

Autofabricação
Atrativo na produção de blocos de madeira é o baixo custo das matérias-primas, baixos custos de mão de obra e tecnologia de produção simples. Portanto, você pode fazer blocos de arbólito com suas próprias mãos. Esses blocos não podem ser usados para paredes de suporte, pois em casa é impossível cumprir toda a tecnologia.
O processo de produção manual leva muito tempo. Uma vez que levará três meses para secar a serragem para se livrar da sacarose, e também levará pelo menos três meses para atingir a densidade necessária dos blocos de madeira.
Se a duração da produção não o assustar, você pode começar a fazer blocos com suas próprias mãos. Antes de tudo, você precisa preparar a quantidade necessária de serragem, aparas ou lascas homogêneas.
Eles podem permanecer após o trabalho de carpintaria, você pode obter serragem com um picador, organizar em uma serraria onde são queimados ou jogados fora. A serragem pode ser substituída por agulhas, cascas ou folhagens. Neste caso, os componentes adicionados não devem exceder 5% do total de carga de madeira.
O tamanho do enchimento não deve ter mais de 5 mm de espessura e não mais de 25 mm de comprimento. Se os tamanhos forem maiores, o enchimento é passado por um moedor de granalha para obter o tamanho desejado.
Além disso, de acordo com a tecnologia, é necessário suportar a serragem no ar por até 90 dias para que a sacarose evapore. Ao mesmo tempo, a serragem deve ser agitada o tempo todo para que o ar entre em todas as camadas e a sacarose evapore uniformemente. Para efeito máximo, a serragem pode ser regada com óxido de cálcio.
Após a secagem, a serragem é peneirada em uma peneira para eliminar as impurezas. A serragem pronta é umedecida com água e misturada com cimento grau 400 ou 500. As proporções durante a mistura são as seguintes: 4 partes de água, 3 partes de madeira e 3 partes de cimento.
O material é submetido a tratamento químico pela adição de vidro líquido à água. Para acelerar o processo, você pode adicionar cloreto de cálcio à polpa de madeira. Além disso, uma mistura de sulfato de alumínio e sulfato de cálcio na proporção de 50/50 é usada como aditivo para blocos. Cal hidratada é adicionada para desinfecção.
A mistura acabada é carregada em um misturador de concreto e misturada. Se a mistura for de alta qualidade, ela deve ser quebradiça e não mudar de forma ou borrar quando comprimida.
O concreto de madeira resultante é derramado em formas preparadas. Os formulários devem ser revestidos com linóleo para que a solução não grude nas paredes do formulário.
A solução despejada nos moldes deve ser bem agitada para remover todo o ar. Você pode bater nas paredes com um martelo, e é melhor usar um vibrador. Nos moldes, a mistura é mantida por três dias. Em seguida, os blocos acabados devem ficar por mais três semanas em uma sala com temperatura de pelo menos 15 graus.
A seguir está uma lista de equipamentos que podem ser necessários na produção de concreto de madeira com suas próprias mãos:

Equipamento adicional será de cerca de 50.000 rublos. Se levarmos em conta outras despesas, que chegam a 75.000 rublos, serão necessários cerca de 900.000 rublos para organizar a produção de concreto de madeira com nossas próprias mãos.
O preço dos blocos acabados é apresentado abaixo.
Assista nossa seleção de vídeos para a produção de concreto de madeira:
Arbolite são blocos leves e bastante fortes de serragem e cimento, que são usados como material de construção, garagens e construções agrícolas. A tecnologia de sua produção foi inventada na Holanda nos anos 30 do século XX (Durisol é o nome original). Em nosso país, esse material se espalhou após os anos 60.
Se você é guiado pela tecnologia holandesa patenteada e pelo GOST doméstico, é possível produzir blocos de concreto de madeira de alta qualidade apenas em condições industriais. No entanto, esse recurso não impede quem deseja economizar seu dinheiro. Por vários anos, este material de construção barato, leve e durável foi reproduzido com sucesso em casa. Para fazer concreto de madeira de alta qualidade com suas próprias mãos, você só precisa levar em consideração algumas das nuances que afetam significativamente o resultado final.
Componentes de concreto de madeira
A primeira informação importante necessária para tornar os blocos de serragem utilizáveis diz respeito à sua composição. O material principal são lascas de madeira. Onde obtê-lo e o que deve ser, é brevemente descrito abaixo. O segundo componente é o fichário. O cimento geralmente desempenha seu papel, e a marca é selecionada não inferior a 400. Bem, o terceiro componente é a argamassa de água ou cal.
Em condições industriais, além dos componentes acima, também são usados vários aditivos que têm um efeito positivo na resistência e outras características dos blocos de concreto de madeira. Para a fabricação de material em casa, será suficiente estocar cal.
Em alguns casos, a adição de vidro líquido é praticada. No entanto, isso não é necessário. Tal componente torna os blocos mais duráveis, mas ao mesmo tempo frágeis.
Onde obter cavacos de madeira para a fabricação de blocos de concreto de madeira
Normalmente a principal matéria-prima é retirada de grandes serrarias. Também agora existe a oportunidade de adquirir uma máquina especial para triturar madeira. Neste caso, certas condições devem ser observadas. Em primeiro lugar, o comprimento dos chips deve ser preferencialmente de 25 milímetros. É com esse tamanho que a madeira servirá não apenas como enchimento, mas também como base de reforço.
Em segundo lugar, é desejável eliminar vários tipos de lixo das lascas de madeira - terra, casca, pedaços de madeira grandes e não moídos. Na produção, este procedimento é realizado usando peneiras vibratórias especiais. Em casa, se as aparas de madeira estiverem muito sujas, podem ser lavadas em água. Isso também eliminará a serragem empoeirada.
Como neutralizar o açúcar na madeira
A celulose presente nos cavacos afetará negativamente a qualidade dos blocos de concreto de madeira no futuro. Para se livrar do açúcar em casa, existem duas maneiras bastante acessíveis. A mais simples delas é manter os cavacos ao ar livre com reviravoltas periódicas. Este procedimento geralmente leva pelo menos 3 meses.
Para acelerar o processo de neutralização do açúcar contido na madeira, você pode usar argamassa de cal. As fichas são mantidas nele por várias horas. Ao final do procedimento, a solução não é drenada, mas serve para preparar a mistura imediatamente antes da formação dos blocos.
Preparação da mistura de arbolito
De acordo com a mesma tecnologia holandesa, é impossível misturar matérias-primas de alta qualidade de lascas de madeira e cimento em um misturador de concreto comum. Leva muito tempo para obter uma consistência homogênea sem grumos. Na produção, eles usam máquinas de mistura forçada. No entanto, como mostra a experiência, a mistura de arbólitos pode até ser preparada manualmente com uma pá comum, e isso não afeta tanto a qualidade.
A ordem de trabalho deve ser aproximadamente a seguinte. Cerca de 5-7 porções de lascas de madeira embebidas em argamassa de cal são colocadas na betoneira. 3-4 porções de cimento também são carregadas lá. Se você planeja adicionar componentes químicos, eles também são colocados nesta fase, levando em consideração a proporção. Após o carregamento, tudo é bem misturado.
Você pode verificar a exatidão da preparação da mistura de arbólitos pelo toque. Se estiver um pouco quebradiço e mantiver sua forma depois de ser espremido em um punho, tudo será feito corretamente.
Formando blocos de concreto de madeira
Como fazer sem casamento? Você pode fazer o trabalho de duas maneiras. Se você comprar uma máquina de moldagem especial, não haverá problemas. Uma opção mais econômica é a produção de blocos peça por peça. Para isso, são montadas caixas de madeira com fundo removível. Dentro do formulário é estofado com linóleo ou polietileno grosso. Para facilitar a remoção da massa carregada após a secagem, o acabamento é pré-revestido com água e sabão.
Depois de carregar a mistura de arbólito em moldes, os produtos podem ser infundidos por 10 dias a uma temperatura não inferior a 15 ° C. Se o tempo estiver mais frio, o tempo deve aumentar. Neste caso, a temperatura negativa do ar é inaceitável.
Além disso, para obter a máxima resistência, recomenda-se cobrir os blocos de concreto de serragem com filme plástico. Assim, o processo de hidratação será mais eficiente.
Mais sobre ferramentas de produção
É impossível se envolver na produção de material precisamente de alta qualidade sem:
- Cortador de cavacos para concreto de madeira. Também chamado de britador de martelo. O preço estimado de uma nova máquina é de 45 a 50 mil rublos. O cortador de cavacos produz cavacos que são convenientes na produção (comprimento não superior a 25 mm). É para a produção na fazenda subsidiária que basta instalar uma máquina do tipo martelo rotativo. Plantas:
- Máquina para blocos de concreto de madeira. Novamente, no trabalho, você precisará de um dispositivo não em escala industrial, mas de sua miniversão. Como a produção em pequena escala de concreto de madeira está ganhando força, respectivamente, e no preço dos equipamentos para garagens, galpões e pequenas zonas industriais. O equipamento custará ao comerciante privado os mesmos 50-60 mil. Um bloco pode ser produzido em um minuto, o que dá até 6,5 metros cúbicos de material por dia de trabalho (aproximadamente até 450 blocos)
- Betoneiras. O aparelho do tipo gravitacional habitual na construção não funcionará. Para uma mistura de qualidade, seu ciclo não é suficiente. Porque mesmo a produção própria, em pequena escala, requer um aparelho do tipo forçado (misturador de argamassa). Geralmente eles também são feitos com as próprias mãos.
- Imprensa. Em um volume pequeno, é permitido compactar a mistura manualmente, mas uma linha de fluxo privada já requer uma vibropress. A empresa Rifey provou ser excelente.
Aparelho "Rifey".
Mas o dispositivo mais comum para a linha de produção é o Condor 1, custando a partir de 265 mil rublos.
No entanto, uma fazenda subsidiária privada aceita qualquer meio auxiliar, portanto, também é costume usar as mini-máquinas "Builder-1" ou "Hephaestus-1" no trabalho.
- formas especiais. Nada complicado aqui, você pode carimbar caixas comuns por conveniência. Mas existem alguns truques. Por exemplo, costuma-se colar as áreas internas com oleado. Isso é perfeito para uma solução de secagem. Às vezes, a mineração de petróleo é simplesmente derramada no fundo do molde. Existem muitas inovações, mas o mais importante é o processo de encaixe no próprio molde. Imediatamente, a composição não pode ser montada uniformemente, portanto, 3 ou 4 marcadores são feitos com compactação periódica.
Arbolito faça você mesmo de juncos
De fato, a composição desse material inclui madeira triturada e cimento. Tal massa da mistura pode solidificar sob a ação de uma força elétrica.
Mais popularmente, esse material é chamado de concreto de madeira. Sua diferença é que qualquer espécie de árvore pode ser escolhida como serragem. Não é proibido adicionar palha uniforme à composição. Na aparência, esse arbólito é semelhante às folhas comuns de aglomerado:
Peculiaridades:
- Baixa condutividade térmica;
- Excelente isolamento acústico;
- Material à prova de fogo (o fogo não se espalha pelos blocos, mas sai na parte interna);
- Mais leve que tijolo ou madeira;
- Com composição adequada, o fator de resistência não é inferior ao concreto de espuma.
A tecnologia de produção é simples, não complicada. Como fazer certo:
- A madeira e os juncos devem ser esmagados. Para isso existe um picador.
- Em seguida, os ingredientes naturais são simplesmente embebidos em água.
- Em seguida, a brita é colocada em um misturador do tipo forçado, onde são adicionados cimento e aditivos. Estes últimos são necessários para uma melhor resistência e velocidade de endurecimento.
- Às vezes, corantes são adicionados.
- A mistura é compactada manualmente em um molde de aço (cofragem).
- Em seguida vem a corrente elétrica.
- A tensão deve ser aplicada a uma forma de aço (este é um tipo de eletrodo).
Assim, é possível produzir tanto blocos para venda quanto um tipo monolítico de divisórias logo no canteiro de obras.
A fase final da produção em vídeo
Diz VLADIMIR SHVYLEV.
As características do concreto de madeira merecem atenção se você quiser construir uma casa de um ou dois andares. Não o último fator ao escolhê-lo é que é bastante simples fazer paredes monolíticas e blocos de arbolito com suas próprias mãos. O conjunto completo de equipamentos necessários depende de onde você pode comprar chips prontos ou você mesmo deve fazer. Para completar o quadro, é considerada a tecnologia completa para a produção de concreto de madeira.
O principal componente do concreto de madeira
90% do concreto de madeira consiste em cavacos de madeira, então o primeiro passo é cuidar de sua compra ou colheita. É melhor que as tábuas de pinho sirvam como material para isso, mas não há nada contra o uso de outros GOSTs.
Uma das nuances da produção de blocos de concreto de madeira é a utilização da madeira, por ser um material natural contendo compostos de açúcar em sua composição. Se não forem neutralizados, posteriormente reagirão com os componentes restantes do concreto de madeira, o que pelo menos provocará seu inchaço. Para evitar isso, as tábuas, e de preferência lascas de madeira prontas, são mantidas por um mês ao ar livre.
Uma maneira mais rápida é embeber lascas de madeira em soluções químicas, que é realizada por 3 dias. Para sua preparação, são utilizados sulfato de alumínio (sulfato de alumínio), cloreto de cálcio, cal apagada ou vidro líquido. Esses componentes estão disponíveis comercialmente e são fáceis de encontrar em lojas agrícolas.
A prática mostrou que a melhor solução é o sulfato de alumínio, que, após reagir com os açúcares, fortalece o bloco de concreto de madeira. O vidro líquido não é recomendado - aumenta a fragilidade do material acabado.
Muitas receitas para blocos de arbólitos do tipo faça você mesmo também omitem essa etapa, adicionando produtos químicos neutralizantes diretamente durante a mistura da mistura de arbólitos. Neste caso, suas proporções são observadas em cerca de 3% do peso total do cimento utilizado.
Cortador de cavacos para concreto de madeira
Se uma construção em grande escala está sendo iniciada e nem sempre é possível comprar a quantidade de lascas de madeira, você não pode prescindir de um picador de madeira. Este dispositivo tritura as placas em lascas, que ficam completamente prontas para uso (se a madeira estiver envelhecida).
O princípio do dispositivo é muito simples - um disco de metal (geralmente 50 cm de diâmetro) é colocado no eixo, no qual são feitas cavas (3-4, dependendo do modelo), localizadas uma em relação à outra em um ângulo de 120° ou 90°. Perto de cada recorte, em ângulo com ele, é presa uma faca, que corta um pedaço da placa e o introduz na cava, após o que entra na câmara de britagem, onde é levado ao tamanho final.
A criação e operação do picador é claramente mostrada no vídeo a seguir:
Apesar da aparente simplicidade do design, nem todo mundo tem um picador de madeira feito por conta própria, pois é necessária uma máquina de torneamento e fresagem para fazer um eixo e um volante com facas. Este equipamento para o processamento de componentes de concreto de madeira terá que ser encomendado pelo menos parcialmente na lateral.
Se o torno não for uma questão insolúvel, como fazer um picador de madeira é mostrado no diagrama a seguir.
Preparação da solução: proporções
Não há segredos especiais aqui - você só precisa misturar todos os componentes. Há apenas uma limitação - a partir do momento em que o amassamento é concluído e até que a solução entre no recipiente de moldagem, não devem passar mais de 15 minutos. Após este tempo, inicia-se a reação química do cimento.
O procedimento básico para encher o tanque do misturador (relação de componentes em baldes para um lote):
- Chips adormecem. Se foi previamente embebido em uma solução, você não pode secá-lo - o próximo componente ainda adicionará água. Quantidade - 6 baldes.
- Cloreto de cálcio (ou outro componente) é adicionado à água. Proporções - 2-4% em peso de cimento, que será utilizado para a mistura (1 balde). Visualmente, isso é cerca de 1-2 copos cheios. Tudo é misturado e despejado no misturador para as lascas de madeira e o misturador começa. Um balde de água também é levado.
- Quando as lascas de madeira estiverem uniformemente umedecidas, é hora de adicionar o cimento. É despejado no misturador e agora temos que esperar até que todos os chips estejam uniformemente cobertos com cimento - tudo deve se tornar a cor correspondente. A marca de cimento utilizada é 500.
Formação de blocos de concreto de madeira
Quando a solução estiver pronta, ela é despejada em um recipiente adequado e agora deve ser consumida em 15 minutos. Para formar e fazer blocos de arbolito com suas próprias mãos, muitos métodos foram inventados - na produção, são cofragens dobráveis para 6 a 12 blocos e, em casa, geralmente são feitas um de cada vez em estênceis caseiros.
Um dos métodos de produção de vídeo:
A tecnologia de fabricação de concreto de madeira oferece duas opções de moldagem:
- Decapagem rápida - após a presa inicial do cimento. Na verdade, este é um processo ininterrupto - a formação de um bloco (preenchimento da solução em um molde), prensagem (ou vibroprensagem), decapagem e envio para secar. Juntamente com a preparação da solução, mesmo uma pessoa pode fazer 80-100 blocos por dia. A vantagem do método é a rapidez na fabricação de novos blocos de concreto de madeira e o processo ininterrupto.
- Desmoldagem em um dia - após o teste de pressão, o bloco é deixado no molde por 24 horas, após o que é realizada apenas a desmoldagem e a secagem final. Fazer blocos de arbólito com suas próprias mãos dessa maneira pode ser ainda mais rápido, mas somente se houver um número suficiente de formas nas quais o arbólito possa ser deixado durante a noite. As vantagens do método são a forma próxima do ideal do bloco, que, após a pega do concreto, não tem a possibilidade de sequer a menor distorção.
Quanto pior a geometria dos blocos, mais espessas serão as juntas de cimento entre eles, que formam pontes frias. Para reduzir a condutividade térmica, os blocos recebem um formato em ziguezague, que quebra essa ponte, impedindo a saída direta de calor.
Para formar blocos, uma máquina especial ou estênceis são usados - todo esse equipamento para blocos de concreto de madeira pode ser feito à mão.
Usando a máquina
Ambos os dispositivos podem ser usados em qualquer um dos métodos, mas sua máquina geralmente é feita para desmoldagem rápida, a fim de aumentar o ritmo de produção. Sua vantagem indiscutível é a prensagem do bloco na mesa vibratória. O processo de formação em si é simples e o equipamento pode ser confiável para trabalhadores com treinamento mínimo.
Operação semiautomática da máquina em vídeo:
- A mistura acabada é despejada em um recipiente medidor (1), que se move sobre as guias (2), despejando a solução no molde (3).
- Uma tampa (5) da prensa é instalada no topo da solução (sua altura pode ser ajustada com pinos (6) para pessoas de diferentes alturas) e pressionada com uma alavanca (7).
- Após pressionar, a mesa vibratória (8) é ligada. Ele funciona por 20 a 30 segundos e desliga automaticamente (você pode usar o relé de tempo mais simples) - você não pode pressioná-lo por mais tempo, porque o cimento será sacudido para o fundo do bloco.
- A alavanca é dobrada para trás (9), a tampa da prensa é removida (10) e o molde é levantado (11), para o qual o pedal é pressionado.
O bloco de concreto de madeira acabado pode ser levado para secar (12). Após 2-3 dias, ganhará força suficiente para o transporte.
Para usar o método de cofragem em um dia, o molde é dobrável e removível, e a tampa superior pode ser fixada nele com travas ou de outra maneira conveniente. Após a compactação, o bloco é retirado diretamente do molde e enviado para decantação.
Arbolit usando um estêncil
Dois tipos principais de moldes são usados - na forma de uma caixa sem fundo e topo, bem como dobráveis, na forma de duas letras "G", que se encaixam no fundo para formar uma caixa rígida coberta com uma tampa. Ele, por sua vez, também é fixado com travas separadas que são cortadas nas paredes laterais.
Independentemente de qual molde é usado, o algoritmo básico é o seguinte:
- A caixa está sendo preparada para o enchimento da mistura de arbólitos. A passagem é colocada sobre uma superfície dura (1), coberta com celofane (para que o bloco não grude), toda a caixa é molhada por dentro.
- A primeira camada da mistura é derramada, compactada, a segunda camada é adicionada por cima, se necessário a terceira e coberta com uma tampa. Na caixa passante encontra-se (2) opressão (um peso ou algo adequado), para um dobrável, a parte superior é fixada com travas (3).
- Se você tiver um perfurador à mão, poderá caminhar ao longo da tampa, isso substituirá a mesa vibratória.
- Dependendo da tecnologia utilizada, a cofragem é desmontada ou a forma é deixada em repouso.
Se uma caixa passante é rapidamente desmoldada, primeiro ela se levanta (4), então a opressão é removida e a tampa é removida. O bloco é enviado para secagem junto com a base sobre a qual foi formado.
Brevemente sobre os principais
A produção de concreto de madeira de alta qualidade em casa não é uma tarefa fora do comum. A única dificuldade séria pode ser a busca por um picador. Em casos extremos, pode ser feito ou encomendado, mas se houver um lugar para comprar lascas de madeira prontas, esse problema será removido.
As lascas de madeira usadas devem ser mantidas ao sol por cerca de um mês para neutralizar a matéria orgânica em seu interior. Você pode usar para a solução e se molhar.
Existem duas maneiras principais de retirar os blocos acabados. Para escolher o caminho certo, faz sentido fazer blocos de teste e comparar os resultados.