Cięcie plazmą powietrzną zrób to sam – technologia działania. Montaż domowej przecinarki plazmowej Inwerterowa przecinarka plazmowa, jak spawać metal
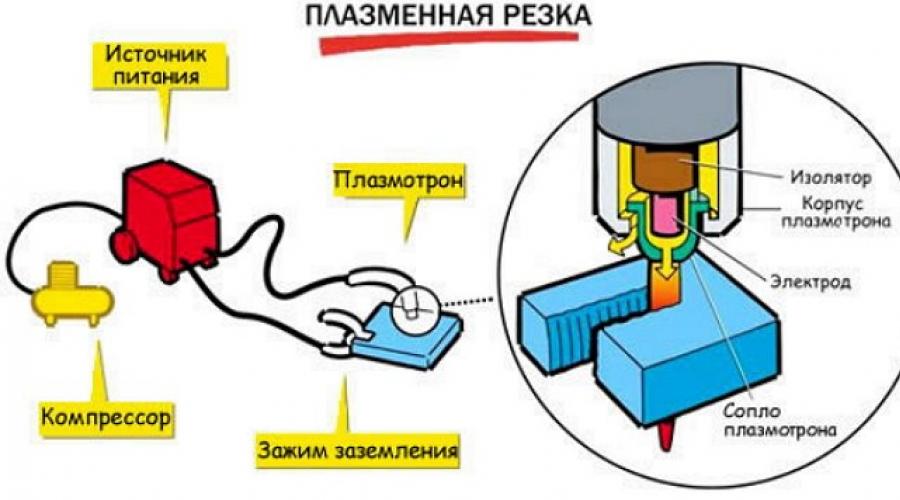
Przeczytaj także
Fabryczna maszyna do cięcia plazmowego. Nasze zadanie: zrobić analog własnymi rękami
Wykonanie funkcjonalnej przecinarki plazmowej własnymi rękami z seryjnego falownika spawalniczego nie jest tak trudne, jak mogłoby się wydawać na pierwszy rzut oka. Aby rozwiązać ten problem, konieczne jest przygotowanie wszystkich elementów konstrukcyjnych takiego urządzenia:
- przecinarka plazmowa (zwana także palnikiem plazmowym);
- falownik spawalniczy lub transformator, który będzie działał jako źródło prądu elektrycznego;
- kompresor, za pomocą którego wytworzy się strumień powietrza niezbędny do wytworzenia i ochłodzenia przepływu plazmy;
- kable i węże umożliwiające łączenie wszystkich elementów konstrukcyjnych urządzenia w jeden system.
Przecinarki plazmowe, także te domowe, z powodzeniem wykorzystywane są przy wykonywaniu różnorodnych prac zarówno na produkcji, jak i w domu. Urządzenie takie jest niezastąpione w sytuacjach, gdy konieczne jest wykonanie dokładnego, cienkiego i wysokiej jakości cięcia metalowych detali. Niektóre modele przecinarek plazmowych, ze względu na swoją funkcjonalność, pozwalają na wykorzystanie ich jako spawarki. Spawanie to odbywa się w atmosferze gazu osłonowego argonem.
Wybierając źródło prądu do uzupełnienia domowego palnika plazmowego, należy zwrócić uwagę na moc prądu, jaką takie źródło może generować. Najczęściej wybiera się w tym celu falownik, zapewniający wysoką stabilność procesu cięcia plazmowego i pozwalający na bardziej ekonomiczne zużycie energii. Różni się od transformatora spawalniczego kompaktowymi wymiarami i niewielką wagą, falownik jest wygodniejszy w użyciu. Jedyną wadą stosowania inwertorowych przecinarek plazmowych jest trudność w wycinaniu za ich pomocą zbyt grubych elementów.
Montując domowe urządzenie do cięcia plazmowego, możesz skorzystać z gotowych schematów, które łatwo znaleźć w Internecie. Ponadto w Internecie znajduje się film na temat wykonania przecinarki plazmowej własnymi rękami. Korzystając z gotowego schematu podczas montażu takiego urządzenia, bardzo ważne jest jego ścisłe przestrzeganie, a także zwrócenie szczególnej uwagi na zgodność elementów konstrukcyjnych ze sobą.
Schematy przecinarki plazmowej na przykładzie urządzenia APR-91
Rozważając schemat obwodu elektrycznego, jako dawcę wykorzystamy APR-91.
Schemat sekcji mocy (kliknij, aby powiększyć)
Obwód sterujący przecinarką plazmową (kliknij, aby powiększyć)
Obwód oscylatora (kliknij, aby powiększyć)
Elementy domowej roboty maszyny do cięcia plazmowego
Pierwszą rzeczą, którą musisz znaleźć, aby wykonać domową przecinarkę plazmową, jest źródło zasilania, w którym będzie generowany prąd elektryczny o wymaganych właściwościach. Najczęściej stosuje się je w tym charakterze, co tłumaczy się szeregiem ich zalet. Dzięki swoim właściwościom technicznym sprzęt taki zapewnia wysoką stabilność generowanego napięcia, co pozytywnie wpływa na jakość cięcia. Praca z falownikami jest znacznie wygodniejsza, co tłumaczy się nie tylko ich kompaktowymi wymiarami i niewielką wagą, ale także łatwością konfiguracji i obsługi.
Inwertorowe przecinarki plazmowe dzięki swojej kompaktowości i niewielkiej wadze pozwalają na pracę nawet w najbardziej niedostępnych miejscach, co jest niemożliwe w przypadku nieporęcznych i ciężkich transformatorów spawalniczych. Ogromną zaletą zasilaczy inwerterowych jest to, że charakteryzują się dużą wydajnością. Dzięki temu są to urządzenia bardzo energooszczędne.
W niektórych przypadkach transformator spawalniczy może służyć jako źródło zasilania przecinarki plazmowej, ale jego użycie wiąże się ze znacznym zużyciem energii. Należy również wziąć pod uwagę, że każdy transformator spawalniczy charakteryzuje się dużymi wymiarami i znaczną wagą.
Głównym elementem aparatu przeznaczonego do cięcia metalu za pomocą strumienia plazmy jest przecinarka plazmowa. To właśnie ten element wyposażenia zapewnia jakość cięcia, a także skuteczność jego realizacji.
Aby wytworzyć strumień powietrza, który zostanie przekształcony w strumień plazmy o wysokiej temperaturze, w konstrukcji przecinarki plazmowej zastosowano specjalną sprężarkę. Prąd elektryczny z falownika i przepływ powietrza ze sprężarki są dostarczane do przecinarki plazmowej za pomocą pakietu kabli i węży.
Centralnym elementem roboczym przecinarki plazmowej jest palnik plazmowy, którego konstrukcja składa się z następujących elementów:
- dysze;
- kanał, przez który dostarczany jest strumień powietrza;
- elektroda;
- izolator, który jednocześnie pełni funkcję chłodzącą.
Pierwszą rzeczą, którą należy zrobić przed wyprodukowaniem palnika plazmowego, jest dobór odpowiedniej dla niego elektrody. Najpopularniejszymi materiałami używanymi do produkcji elektrod do cięcia plazmowego są beryl, tor, cyrkon i hafn. Po podgrzaniu na powierzchni tych materiałów tworzą się ogniotrwałe warstwy tlenkowe, które zapobiegają aktywnemu zniszczeniu elektrod.
Niektóre z powyższych materiałów po podgrzaniu mogą wydzielać związki niebezpieczne dla zdrowia człowieka, co należy wziąć pod uwagę przy wyborze rodzaju elektrody. Tak więc podczas stosowania berylu powstają radioaktywne tlenki, a pary toru w połączeniu z tlenem tworzą niebezpieczne substancje toksyczne. Całkowicie bezpiecznym materiałem, z którego wykonane są elektrody do plazmatronów jest hafn.
Dysza odpowiada za powstawanie strumienia plazmy, dzięki któremu następuje cięcie. Należy zwrócić szczególną uwagę na jego produkcję, ponieważ jakość przepływu pracy zależy od właściwości tego elementu.
Najbardziej optymalna jest dysza o średnicy 30 mm. Dokładność i jakość cięcia zależy od długości tego elementu. Jednak nie należy również robić zbyt długiej dyszy, ponieważ przyczynia się to do jej zbyt szybkiego zniszczenia.
Jak wspomniano powyżej, konstrukcja przecinarki plazmowej koniecznie obejmuje sprężarkę, która tworzy i dostarcza przepływ powietrza do dyszy. Ten ostatni jest niezbędny nie tylko do wytworzenia strumienia plazmy wysokotemperaturowej, ale także do chłodzenia elementów aparatu. Zastosowanie sprężonego powietrza jako czynnika roboczego i chłodzącego oraz falownika generującego prąd roboczy o natężeniu 200 A pozwala na efektywne cięcie części metalowych, których grubość nie przekracza 50 mm.
Aby przygotować przecinarkę plazmową do pracy należy podłączyć palnik plazmowy z falownikiem i sprężarką powietrza. Aby rozwiązać ten problem, stosuje się pakiet węża kablowego, który stosuje się w następujący sposób.
- Kabel, którym będzie dostarczany prąd elektryczny, łączy falownik z elektrodą przecinarki plazmowej.
- Wąż do dostarczania sprężonego powietrza łączy wylot sprężarki z plazmatronem, w którym z napływającego strumienia powietrza powstanie strumień plazmy.
Cechy przecinarki plazmowej
Aby wykonać przecinarkę plazmową za pomocą falownika do jej produkcji, musisz zrozumieć, jak działa takie urządzenie.
Po włączeniu falownika prąd elektryczny z niego zaczyna płynąć do elektrody, co prowadzi do zapłonu łuku elektrycznego. Temperatura łuku płonącego pomiędzy elektrodą roboczą a metalową końcówką dyszy wynosi około 6000–8000 stopni. Po zapaleniu łuku do komory dyszy dostarczane jest sprężone powietrze, które przechodzi ściśle przez wyładowanie elektryczne. Łuk elektryczny podgrzewa i jonizuje przepływające przez niego powietrze. W rezultacie jego objętość wzrasta setki razy i staje się zdolna do przewodzenia prądu elektrycznego.
Za pomocą dyszy do cięcia plazmowego strumień plazmy powstaje z przewodzącego strumienia powietrza, którego temperatura aktywnie wzrasta i może osiągnąć 25–30 tysięcy stopni. Prędkość przepływu plazmy, dzięki której wycinane są części metalowe, na wyjściu z dyszy, wynosi około 2-3 metry na sekundę. W momencie, gdy strumień plazmy zetknie się z powierzchnią metalowej części, zaczyna przez nią płynąć prąd elektryczny z elektrody, a łuk początkowy gaśnie. Nowy łuk, który pali się pomiędzy elektrodą a przedmiotem obrabianym, nazywany jest cięciem.
Charakterystyczną cechą cięcia plazmowego jest to, że obrabiany metal topi się dopiero w miejscu, w którym jest wystawiony na działanie strumienia plazmy. Dlatego bardzo ważne jest, aby punkt naświetlania plazmy znajdował się dokładnie pośrodku elektrody roboczej. Jeśli zlekceważysz ten wymóg, możesz spotkać się z zakłóceniem przepływu powietrza i plazmy, co oznacza pogorszenie jakości cięcia. Aby spełnić te ważne wymagania, zastosowano specjalną (styczną) zasadę dopływu powietrza do dyszy.
Należy także zadbać o to, aby zamiast jednego nie tworzyły się jednocześnie dwa strumienie plazmy. Wystąpienie takiej sytuacji, spowodowanej nieprzestrzeganiem trybów i zasad procesu technologicznego, może spowodować awarię falownika.
Ważnym parametrem przy cięciu plazmowym jest prędkość przepływu powietrza, która nie powinna być zbyt duża. Dobrą jakość cięcia i szybkość wykonania zapewnia prędkość strumienia powietrza wynosząca 800 m/s. W takim przypadku prąd dostarczany z aparatu inwerterowego nie powinien przekraczać 250 A. Wykonując pracę w takich trybach, należy liczyć się z tym, że w tym przypadku zwiększy się przepływ powietrza wykorzystywanego do wytworzenia przepływu plazmy.
Samodzielne wykonanie przecinarki plazmowej nie jest trudne, jeśli przestudiujesz niezbędny materiał teoretyczny, obejrzysz film szkoleniowy i poprawnie wybierzesz wszystkie niezbędne elementy. Jeśli posiadasz w swoim domowym warsztacie takie urządzenie, zmontowane w oparciu o falownik szeregowy, możesz własnymi rękami wykonać wysokiej jakości nie tylko cięcie, ale także spawanie plazmowe.
Jeśli nie masz do dyspozycji falownika, możesz zmontować przecinarkę plazmową za pomocą transformatora spawalniczego, ale wtedy będziesz musiał pogodzić się z jej dużymi gabarytami. Ponadto przecinarka plazmowa wykonana na bazie transformatora nie będzie miała bardzo dobrej mobilności, ponieważ trudno ją przenosić z miejsca na miejsce.
Domowi rzemieślnicy zajmujący się obróbką metalu stają przed koniecznością cięcia metalowych półfabrykatów. Można to zrobić za pomocą szlifierki kątowej (szlifierki), przecinarki tlenowej lub przecinarki plazmowej.
- Bułgarski. Jakość cięcia jest bardzo wysoka. Niemożliwe jest jednak wykonanie cięcia figurowego, zwłaszcza jeśli dotyczy to otworów wewnętrznych o zakrzywionych krawędziach. Ponadto istnieją ograniczenia dotyczące grubości metalu. Niemożliwe jest cięcie cienkich blach za pomocą szlifierki. Główną zaletą jest przystępna cena;
- Przecinarka tlenowa. Możliwość wycięcia otworu o dowolnej konfiguracji. Jednak osiągnięcie równego cięcia jest w zasadzie niemożliwe. Krawędzie okazują się podarte, z kroplami stopionego metalu. Grubości większe niż 5 mm są trudne do cięcia. Urządzenie nie jest zbyt drogie, ale do pracy wymaga dużego zapasu tlenu;
- Przecinarka plazmowa. Tego urządzenia nie można nazwać niedrogim, ale wysoki koszt jest uzasadniony jakością cięcia. Po cięciu przedmiot praktycznie nie wymaga dodatkowej obróbki.
Biorąc pod uwagę cenę, która jest zaporowa dla większości domowych rzemieślników, wielu rzemieślników „Kulibiny” wykonuje przecinarkę plazmową.
Sposobów jest kilka – można stworzyć konstrukcję całkowicie od podstaw lub skorzystać z gotowych urządzeń. Na przykład ze spawarki, nieco zmodernizowanej do nowych zadań.
Wykonanie przecinarki plazmowej własnymi rękami to prawdziwe zadanie, ale najpierw musisz zrozumieć, jak to działa.
Ogólny schemat pokazano na ilustracji:
Urządzenie do cięcia plazmowego
Jednostka mocy.
Można go zaprojektować na różne sposoby. Transformator ma duże wymiary i wagę, ale pozwala na cięcie grubszych detali.
Zużycie energii elektrycznej jest wyższe, należy to wziąć pod uwagę przy wyborze punktu podłączenia. Zasilacze tego typu są mało wrażliwe na zmiany napięcia wejściowego.
Cięcie plazmowe jest aktywnie wykorzystywane w wielu dziedzinach przemysłu. Jednak przecinarka plazmowa może być całkiem przydatna dla prywatnego mistrza. Urządzenie pozwala na cięcie dowolnych materiałów przewodzących i nieprzewodzących z dużą szybkością i jakością. Technologia pracy umożliwia obróbkę dowolnych części lub tworzenie wycięć kształtowych, co odbywa się za pomocą wysokotemperaturowego łuku plazmowego. Przepływ tworzą podstawowe elementy – prąd elektryczny i powietrze. Ale zalety korzystania z urządzenia są nieco przyćmione ceną modeli fabrycznych. Aby zapewnić sobie możliwość pracy, możesz stworzyć przecinarkę plazmową własnymi rękami. Poniżej podajemy szczegółową instrukcję postępowania wraz z listą potrzebnego sprzętu.
Co wybrać: transformator czy falownik?
Ze względu na obecność cech i parametrów urządzeń do cięcia plazmowego można je podzielić na typy. Największą popularność zyskały falowniki i transformatory. Koszt urządzenia każdego modelu zostanie określony na podstawie deklarowanych cykli mocy i pracy.
Falowniki są lekkie, kompaktowe i zużywają minimalną ilość energii elektrycznej. Wady sprzętu obejmują zwiększoną wrażliwość na zmiany napięcia. Nie każdy falownik jest w stanie pracować w specyficznych warunkach naszej sieci elektrycznej. Jeśli system ochrony urządzenia ulegnie awarii, należy skontaktować się z centrum serwisowym. Również inwerterowe przecinarki plazmowe mają ograniczenie mocy znamionowej do nie więcej niż 70 amperów i krótki okres włączania sprzętu przy wysokim prądzie.
Transformator jest tradycyjnie uważany za bardziej niezawodny niż falownik. Nawet przy zauważalnym spadku napięcia tracą tylko część mocy, ale nie pękają. Ta właściwość determinuje wyższy koszt. Przecinarki plazmowe oparte na transformatorze mogą pracować i być włączone przez dłuższy czas. Podobne urządzenia stosowane są w automatycznych liniach CNC. Negatywną stroną transformatorowej przecinarki plazmowej będzie jej znaczna waga, duże zużycie energii i rozmiar.
Maksymalna grubość metalu, jaką może ciąć przecinarka plazmowa, wynosi od 50 do 55 milimetrów. Średnia moc sprzętu wynosi 150 - 180 A.
Średni koszt urządzeń fabrycznych
Oferta przecinarek plazmowych do ręcznego cięcia materiałów jest obecnie naprawdę ogromna. Kategorie cenowe również są różne. Na cenę urządzeń wpływają następujące czynniki:
- Rodzaj urządzenia;
- Producent i kraj produkcji;
- Maksymalna możliwa głębokość cięcia;
- Model.
Decydując się na rozpatrzenie możliwości zakupu przecinarki plazmowej, należy zainteresować się kosztem dodatkowych elementów i podzespołów do sprzętu, bez których trudno będzie w pełni funkcjonować. Średnie ceny urządzeń w zależności od grubości ciętego metalu wynoszą:
- Do 6 mm – 15 000 – 20 000 rubli;
- Do 10 mm – 20 000 – 25 000;
- Do 12 mm – 32 000 – 230 000;
- Do 17 mm – 45 000 – 270 000;
- Do 25 mm – 81 000 – 220 000;
- Do 30 mm – 150 000 – 300 000.
Popularne urządzenia to „Gorynych”, „Resanta” IPR-25, IPR-40, IPR-40 K.
Jak widać rozpiętość cenowa jest szeroka. Pod tym względem rośnie znaczenie domowej przecinarki plazmowej. Po przestudiowaniu instrukcji całkiem możliwe jest stworzenie urządzenia, które w niczym nie będzie gorsze pod względem właściwości technicznych. Możesz wybrać falownik lub transformator w cenie znacznie niższej niż prezentowane ceny.
Zasada działania
Po naciśnięciu przycisku zapłonu uruchamia się źródło prądu dostarczającego prąd o wysokiej częstotliwości do narzędzia roboczego. Pomiędzy końcówką umieszczoną w przecinarce (palniku plazmowym) a elektrodą powstaje łuk (pilotujący). Zakres temperatur od 6 do 8 tysięcy stopni. Warto zauważyć, że łuk roboczy nie powstaje natychmiast; występuje pewne opóźnienie.
Następnie sprężone powietrze dostaje się do wnęki plazmatronu. Do tego właśnie zaprojektowano kompresor. Przechodząc przez komorę z łukiem pilotującym na elektrodzie, nagrzewa się i zwiększa swoją objętość. Procesowi towarzyszy jonizacja powietrza, która przekształca je w stan przewodzący.
Przez wąską dyszę palnika plazmowego powstały strumień plazmy jest dostarczany do przedmiotu obrabianego. Prędkość przepływu wynosi 2 – 3 m/s. Powietrze w stanie zjonizowanym może nagrzać się do 30 000°C. W tym stanie przewodność elektryczna powietrza jest zbliżona do przewodności elementów metalowych.
Po zetknięciu plazmy z ciętą powierzchnią następuje wyłączenie łuku pilotującego i rozpoczęcie pracy łuku roboczego. Następnie w punktach cięcia przeprowadza się stapianie, z którego roztopiony metal jest wdmuchiwany dostarczanym powietrzem.
Różnice pomiędzy urządzeniami bezpośrednimi i pośrednimi
Istnieją różne typy urządzeń różniących się zasadą działania. W urządzeniach działających bezpośrednio zakłada się działanie łuku elektrycznego. Przyjmuje kształt cylindryczny i jest bezpośrednio podłączony do strumienia gazu. Taka konstrukcja sprzętu umożliwia zapewnienie wysokiej temperatury łuku (aż do 20 000°C) oraz wysoce wydajnego układu chłodzenia pozostałych elementów przecinarki plazmowej.
W urządzeniach o działaniu pośrednim zakłada się, że działanie jest mniej wydajne. To determinuje ich niższy rozkład w produkcji. Cechą konstrukcyjną urządzenia jest to, że aktywne punkty obwodu są umieszczone na specjalnych elektrodach wolframowych lub rurze. Częściej stosuje się je do ogrzewania i natryskiwania, ale praktycznie nie stosuje się ich do cięcia. Najczęściej stosowany przy naprawach samochodów.
Cechą wspólną jest obecność w konstrukcji filtra powietrza (przedłuża żywotność elektrody, zapewnia szybki rozruch sprzętu) i chłodnicy (stwarza warunki do długotrwałej pracy urządzenia bez przerwy). Doskonałym wskaźnikiem jest zdolność urządzenia do ciągłej pracy przez 1 godzinę z 20-minutową przerwą.
Projekt
Przy odpowiedniej chęci i umiejętnościach każdy może stworzyć domową przecinarkę plazmową. Aby jednak mógł on w pełni i skutecznie funkcjonować, należy przestrzegać pewnych zasad. Wskazane jest wypróbowanie falownika, ponieważ To on jest w stanie zapewnić stabilny dopływ prądu i stabilną pracę łuku. Dzięki temu nie będzie żadnych przerw, a zużycie energii elektrycznej zostanie znacząco zmniejszone. Warto jednak wziąć pod uwagę, że przecinarka plazmowa oparta na inwerterze poradzi sobie z cieńszą grubością metalu niż transformator.
Wymagane komponenty
Przed rozpoczęciem prac montażowych należy przygotować szereg komponentów, materiałów i wyposażenia:
- Falownik lub transformator o odpowiedniej mocy. Aby wyeliminować błąd, należy określić planowaną grubość cięcia. Na podstawie tych informacji wybierz odpowiednie urządzenie. Biorąc jednak pod uwagę cięcie ręczne, warto wybrać falownik, bo... waży mniej i zużywa mniej energii elektrycznej.
- Palnik plazmowy lub przecinarka plazmowa. Istnieją również pewne osobliwości wyboru. Do pracy z materiałami przewodzącymi lepiej jest wybrać działanie bezpośrednie, a do materiałów nieprzewodzących działanie pośrednie.
- Sprężarka sprężonego powietrza. Należy zwrócić uwagę na moc znamionową, gdyż musi ona wytrzymać nałożone obciążenie i dopasowywać się do pozostałych podzespołów.
Wąż kablowy. Wymagane do podłączenia wszystkich podzespołów przecinarki plazmowej i doprowadzenia powietrza do palnika plazmowego.
Dobór zasilacza
Pracę przecinarki plazmowej zapewnia zasilacz. Generuje określone parametry prądu i napięcia elektrycznego i dostarcza je do zespołu tnącego. Główną jednostką zasilającą może być:
- falownik;
- Transformator.
Do wyboru zasilacza należy podejść z uwzględnieniem cech urządzeń opisanych powyżej.
Palnik plazmowy
Palnik plazmowy to generator plazmy. Jest to narzędzie robocze, w którym powstaje strumień plazmy, który bezpośrednio tnie materiały.
Główne cechy urządzenia to:
- Tworzenie ultrawysokiej temperatury;
- Prosta regulacja aktualnej mocy, start i stop trybów pracy;
- Kompaktowe wymiary;
- Niezawodność działania.
Strukturalnie palnik plazmowy składa się z:
- Elektroda/katoda zawierająca cyrkon lub hafn. Metale te charakteryzują się wysokim poziomem emisji termojonowej;
- Dysza jest zasadniczo odizolowana od elektrody;
- Mechanizm wirujący gaz tworzący plazmę.
Dysza i elektroda są elementami eksploatacyjnymi palnika plazmowego. Jeśli przecinarka plazmowa obrabia przedmiot o wielkości do 10 milimetrów, wówczas jeden zestaw elektrod zużywa się w ciągu 8 godzin pracy. Zużycie następuje równomiernie, co pozwala na ich jednoczesną wymianę.
Jeśli elektroda nie zostanie wymieniona w odpowiednim czasie, jakość cięcia może ulec pogorszeniu - zmienia się geometria cięcia lub na powierzchni pojawiają się fale. Wkładka hafnu w katodzie stopniowo się wypala. Jeśli ma produkcję większą niż 2 milimetry, wówczas elektroda może spalić i przegrzać plazmatron. Oznacza to, że wymiana elektrod w niewłaściwym momencie doprowadzi do szybkiej awarii pozostałych elementów narzędzia roboczego.
Wszystkie plazmatrony można podzielić na 3 grupy objętościowe:
- Łuk elektryczny - ma co najmniej jedną anodę i katodę, które są podłączone do źródła prądu stałego;
- Wysoka częstotliwość - nie ma elektrod i katod. Komunikacja z zasilaczem opiera się na zasadzie indukcyjno-pojemnościowej;
- Połączone - działa pod wpływem prądu o wysokiej częstotliwości i wyładowań łukowych.
W oparciu o metodę stabilizacji łuku wszystkie plazmatrony można również podzielić na gazowe, wodne i magnetyczne. Układ taki jest niezwykle istotny dla działania instrumentu, gdyż tworzy kompresję przepływu i mocuje go na środkowej osi dyszy.
Obecnie w sprzedaży dostępne są różne modyfikacje palników plazmowych. Być może będziesz musiał przestudiować oferty i kupić gotową. Jednak całkiem możliwe jest wykonanie domowej roboty w domu. To wymaga:
- Dźwignia. Konieczne jest zapewnienie otworów na przewody.
- Przycisk.
- Odpowiednia elektroda dostosowana do prądu.
- Izolator.
- Zawirowacz przepływu.
- Dysza. Najlepiej zestaw o różnych średnicach.
- Wskazówka. Należy zapewnić ochronę przed rozpryskami.
- Wiosna dystansowa. Pozwala zachować szczelinę pomiędzy powierzchnią a dyszą.
- Dysza do usuwania nagaru i fazowania.
Prace można prowadzić jednym palnikiem plazmowym dzięki wymiennym głowicom o różnych średnicach, które kierują przepływ plazmy na detal. Należy zwrócić uwagę, że one, podobnie jak elektrody, stopią się podczas pracy.
Dysza zabezpieczona jest nakrętką zaciskową. Bezpośrednio za nim znajduje się elektroda i izolator, który zapobiega zajarzeniu łuku w niewłaściwym miejscu. Następnie umieszcza się zawirowywacz przepływu, aby wzmocnić efekt łuku. Wszystkie elementy umieszczone są w obudowie z fluoroplastiku. Niektóre rzeczy możesz zrobić sam, ale inne będą musiały zostać zakupione w sklepie.
Fabryczny palnik plazmowy pozwoli na dłuższą pracę bez przegrzania, dzięki systemowi chłodzenia powietrzem. Jednak przy krótkotrwałym cięciu nie jest to istotny parametr.
Oscylator
Oscylator to generator wytwarzający prąd o wysokiej częstotliwości. Podobny element znajduje się w obwodzie przecinarki plazmowej pomiędzy źródłem prądu a palnikiem plazmowym. Potrafi działać według jednego z następujących schematów:
- Wytworzenie krótkotrwałego impulsu, który sprzyja tworzeniu się łuku bez dotykania powierzchni produktu. Zewnętrznie wygląda jak mały piorun zasilany z końca elektrody.
- Wsparcie stałonapięciowe o wysokiej wartości napięcia nałożonej na prąd spawania. Zapewnia zachowanie stabilnego utrzymania łuku.
Sprzęt pozwala na szybkie utworzenie łuku i rozpoczęcie cięcia metalu.
W większości mają one podobną strukturę i składają się z:
- Prostownik napięciowy;
- Jednostka magazynująca ładunek (kondensatory);
- Jednostka mocy;
- Moduł tworzenia impulsów. Zawiera obwód oscylacyjny i iskiernik;
- Blok kontrolny;
- Transformator podwyższający;
- Urządzenie monitorujące napięcie.
Głównym zadaniem jest modernizacja napięcia wejściowego. Zwiększa się częstotliwość i poziom napięcia, skracając czas działania do mniej niż 1 sekundy. Sekwencja pracy jest następująca:
- Naciśnięto przycisk na nożu;
- W prostowniku prąd wyrównuje się i staje się jednokierunkowy;
- Ładunek gromadzi się w kondensatorach;
- Prąd jest dostarczany do obwodu oscylacyjnego uzwojeń transformatora, zwiększając poziom napięcia;
- Impuls jest kontrolowany przez obwód sterujący;
- Impuls powoduje wyładowanie na elektrodzie, zapalając łuk;
- Impuls się kończy;
- Po zatrzymaniu cięcia oscylator przedmuchuje palnik plazmowy przez kolejne 4 sekundy. Dzięki temu osiąga się chłodzenie elektrody i obrabianej powierzchni.
W zależności od rodzaju oscylatora można go wykorzystać na różne sposoby. Jednak ogólną cechą jest wzrost napięcia do 3000–5000 woltów i częstotliwości od 150 do 500 kHz. Główne różnice dotyczą odstępów czasu działania prądu o wysokiej częstotliwości.
Do stosowania w przecinarce plazmowej zaleca się zastosowanie oscylatora umożliwiającego bezkontaktowe zajarzanie łuku. Podobne elementy służą do pracy w spawarkach argonowych. Zawarte w nich elektrody wolframowe szybko się stępią, jeśli wejdą w kontakt z produktem. Włączenie oscylatora do obwodu aparatu pozwoli na utworzenie łuku bez kontaktu z płaszczyzną części.
Zastosowanie oscylatora może znacznie zmniejszyć zapotrzebowanie na drogie materiały eksploatacyjne i usprawnić proces cięcia. Odpowiednio dobrany sprzęt zgodnie z planowanymi pracami pozwala na poprawę ich jakości i szybkości.
Elektrody
Elektrody odgrywają ważną rolę w procesie tworzenia, utrzymywania łuku i bezpośredniego cięcia. Kompozycja zawiera metale, dzięki którym elektroda nie przegrzewa się i nie przedwcześnie zapada się podczas pracy z łukiem w wysokich temperaturach.
Kupując elektrody do przecinarki plazmowej, konieczne jest wyjaśnienie ich składu. Zawartość berylu i toru powoduje powstawanie szkodliwych oparów. Nadają się do pracy w odpowiednich warunkach, przy zapewnieniu odpowiedniej ochrony pracownika tj. wymagana jest dodatkowa wentylacja. Z tego powodu do zastosowania w życiu codziennym lepiej kupić elektrody hafnowe.
Kompresor i kabel - węże
Konstrukcja większości domowych przecinarek plazmowych obejmuje sprężarki i węże kierujące powietrze do palnika plazmowego. Ten element konstrukcyjny umożliwia nagrzanie łuku elektrycznego do temperatury 8000°C. Dodatkową funkcją jest przeczyszczenie kanałów roboczych, oczyszczenie ich z zanieczyszczeń i usunięcie kondensatu. Dodatkowo sprężone powietrze pomaga schłodzić elementy urządzenia podczas długotrwałej pracy.
Do obsługi przecinarki plazmowej można zastosować konwencjonalną sprężarkę sprężonego powietrza. Wymiana powietrza odbywa się za pomocą cienkich węży z odpowiednimi złączami. Na wlocie znajduje się zawór elektryczny, który reguluje proces dopływu powietrza.
W kanale łączącym urządzenie z palnikiem umieszcza się kabel elektryczny. Dlatego konieczne jest umieszczenie tutaj węża o dużej średnicy, w którym zmieści się kabel. Przepływające powietrze pełni także funkcję wentylacyjną, gdyż jest w stanie schłodzić drut.
Masę należy wykonać z kabla o przekroju 5 mm2. Musi być zacisk. W przypadku słabego kontaktu z podłożem przełączenie łuku roboczego na łuk rezerwowy będzie problematyczne.
Schemat
Teraz możesz znaleźć wiele schematów, za pomocą których możesz złożyć urządzenie wysokiej jakości. Film pomoże Ci szczegółowo zrozumieć symbole. Odpowiedni rysunek schematyczny urządzenia można wybrać spośród przedstawionych poniżej.
Montaż
Przed rozpoczęciem procesu montażu zaleca się wyjaśnienie kompatybilności wybranych komponentów. Jeśli nigdy wcześniej nie montowałeś przecinarki plazmowej własnymi rękami, powinieneś skonsultować się z doświadczonymi rzemieślnikami.
Procedura montażu zakłada następującą kolejność:
- Przygotuj wszystkie zmontowane komponenty;
- Montaż obwodu elektrycznego. Zgodnie ze schematem podłączony jest falownik/transformator i kabel elektryczny;
- Podłączenie kompresora i dopływu powietrza do aparatu i plazmatronu za pomocą węży elastycznych;
- Dla własnego bezpieczeństwa możesz zastosować zasilacz UPS, biorąc pod uwagę pojemność akumulatora.
Szczegółową technologię montażu sprzętu przedstawiamy na filmie.
Sprawdzanie przecinarki plazmowej
Po połączeniu wszystkich węzłów w jedną strukturę należy sprawdzić funkcjonalność.
Należy pamiętać, że testowanie i pracę z przecinarką plazmową należy wykonywać w odzieży ochronnej i przy użyciu środków ochrony osobistej.
Konieczne jest włączenie wszystkich urządzeń i naciśnięcie przycisku palnika plazmowego, dostarczającego prąd do elektrody. W tym momencie w plazmotronie powinien powstać łuk o wysokiej temperaturze, przechodzący pomiędzy elektrodą a dyszą.
Jeśli zmontowany sprzęt do cięcia plazmowego jest w stanie ciąć metal o grubości do 2 cm, wszystko zostanie wykonane poprawnie. Należy zauważyć, że domowe urządzenie wykonane z falownika nie będzie w stanie wyciąć części o grubości większej niż 20 milimetrów, ponieważ nie ma wystarczającej mocy. Aby ciąć grube produkty, będziesz musiał użyć transformatora jako źródła zasilania.
Zalety domowego urządzenia
Korzyści, jakie zapewnia maszyna do cięcia plazmą powietrzną są trudne do przecenienia. Potrafi dokładnie ciąć blachę. Po pracy nie ma potrzeby dalszej obróbki końcówek. Główną zaletą jest skrócenie czasu pracy.
To już są przekonujące powody, aby samemu złożyć sprzęt. Obwód nie jest skomplikowany, więc każdy może tanio przerobić falownik lub półautomat.
Podsumowując, zwróćmy uwagę na fakt, że do pracy z przecinarką plazmową niezbędny jest doświadczony specjalista. Najlepiej jeśli jest to spawacz. Jeśli masz niewielkie doświadczenie, zalecamy najpierw przestudiować technologię pracy ze zdjęciami i filmami, a następnie zacząć wykonywać przydzielone zadania.
Cięcie plazmowe to metoda obróbki pustych części metalowych strumieniem plazmy. Metoda ta pozwala na cięcie metalu, wystarczy bowiem wykonać to w taki sposób, aby materiał przewodził prąd elektryczny. W porównaniu do podobnych metod, cięcie plazmowe metali pozwala na szybszy i wyższej jakości proces bez użycia masywnych walców i specjalnych dodatków.
W ten sposób możliwa jest obróbka różnorodnych blach, rur o różnych średnicach, kształtowanie i sortowanie produktów. Podczas obróbki uzyskuje się wysokiej jakości cięcie, które wymaga minimalnego wysiłku czyszczenia. Nawet przy pomocy tej technologii można wyeliminować różne niedoskonałości powierzchni metalu, takie jak wybrzuszenia, szwy i nierówności, i przygotować je do spawania, wiercenia i innych operacji.
Cięcie plazmowe blachy jest metodą niezwykle efektywną.
W odróżnieniu od innych metod może być stosowana do obróbki metali żelaznych i nieżelaznych. Dzięki temu nie ma konieczności przygotowywania powierzchni i oczyszczania jej z zanieczyszczeń, które mogłyby utrudniać zajarzenie łuku. W branży głównym konkurentem tej metody jest obróbka laserowa, która charakteryzuje się jeszcze większą precyzją, ale jednocześnie wymaga znacznie droższego sprzętu.
W domu nie ma odpowiedników konkurentów dla urządzenia plazmowego.
Jakość cięcia plazmowego metali
Technologia cięcia plazmowego
Cięcie plazmowe odbywa się za pomocą specjalnego urządzenia, które ma wymiary zbliżone do konwencjonalnej spawarki. Początkowo urządzenia te były duże, ale w miarę ich ulepszania stały się mniejsze.
Urządzenie podłączane jest do sieci zasilającej 220V dla sprzętu AGD i 380V dla zastosowań przemysłowych.
W procesie produkcyjnym cięcie odbywa się na maszynach CNC, które składają się z jednego lub większej liczby palników wraz z mechanizmami ich przesuwania.
Maszyna może realizować pomiary według konkretnego programu, co znacznie ułatwia pracę kilku arkuszy w tym samym cięciu.
Aby wytworzyć strumień plazmy, należy podłączyć system do sprężarki lub przewodu powietrznego.
Sprężone powietrze dostarczane do urządzenia musi być wolne od zanieczyszczeń, kurzu i wilgoci. W tym celu przed urządzeniem instalowane są filtry powietrza i osuszacze. Bez takich urządzeń zużycie elektrod i innych elementów będzie przyspieszać szybciej. Palniki plazmowe chłodzone cieczą również wymagają instalacji hydraulicznej.
Ręczne cięcie rur stalowych
Cięcie okrągłe rur stalowych
pojazd z własnym napędem
Technologia cięcia plazmą powietrzną pozwala uzyskać wysokiej jakości krawędzie (brak zasysania i tarcia) oraz brak wypaczeń (także na blachach o małej grubości).
Umożliwia to późniejsze spawanie oczyszczonego metalu bez obróbki wstępnej.
Ręczne cięcie metali na próbce
Esencja arkusza plazmowego
Cięcie plazmowe stali w życiu codziennym odbywa się za pomocą urządzeń, na których długość rur sięga 12 m.
Urządzenia ręczne posiadają głowicę tnącą wyposażoną w uchwyt z napędem silnikowym. Urządzenia takie wykorzystują chłodzenie powietrzem, ponieważ jest prostsze w konstrukcji i nie wymaga dodatkowych agregatów chłodniczych. Chłodzenie wodne stosowane jest w instalacjach przemysłowych, gdzie cięcie plazmowe blach stalowych jest bardziej wydajne, jednak koszt urządzeń jest wyższy.
Technologia plazmy tlenowej
Cięcie plazmą tlenową wymaga specjalnej elektrody i dyszy, która jako materiał eksploatacyjny ma znaczący wpływ na temperaturę. Najpierw rozpoczyna się łuk pomocniczy, który jest wzbudzany przez wyładowanie spowodowane przez generator prądu stałego. Dzięki łukowi powstaje palnik plazmowy o długości 20-40 mm. Kiedy palnik dotknie metalu, pojawia się łuk roboczy i łuk pomocniczy zostaje wyłączony.
Jak zrobić spawarkę plazmową własnymi rękami?
W ten sposób plazma pełni rolę przewodnika pomiędzy urządzeniem a obrabianym przedmiotem. Powstały łuk jest samowystarczalny, tworząc plazmę w wyniku jonizacji cząsteczek powietrza.
Cięcie plazmowe z wykorzystaniem cieczy roboczej w temperaturach do 25000°C.
Cięcie plazmowe rur o dużych średnicach i innych zbiorników
Cięcie i spawanie plazmowe można wykonywać w warsztatach i warsztatach, a także w plenerze.
Metoda ta może nie być tak wydajna jak elektrownia gazowa przy pracach remontowo-budowlanych bez centralnego układu zasilania energią elektryczną i sprężonym powietrzem. W takim przypadku wymagany jest wystarczająco mocny generator, który zapewni zasilanie urządzenia i sprężarki.
Podobnie jak cięcie płomieniem gazowym, tę metodę można stosować do obróbki pustych elementów o różnych rozmiarach i kształtach.
Cięcie plazmowe rur o dużych średnicach nie stwarza żadnych problemów: wykonuje się je ręcznie lub przy użyciu maszyn samobieżnych. Stały palnik obraca się na zewnątrz rury. Zastosowanie maszyn samobieżnych zapewnia precyzyjne i płynne cięcie. Praca z formowanymi i sortowanymi produktami walcowanymi może być również zautomatyzowana w warunkach przemysłowych.
Zalety korzystania z urządzeń SYBERYJSKICH:
- Wszechstronność (można zastosować do dowolnego metalu, w tym metali nieżelaznych i ogniotrwałych);
- Prędkość cięcia;
- Wysoka jakość powierzchni po cięciu;
- Ekonomika (wykorzystywanie sprężonego powietrza);
- Prawie całkowity brak deformacji termicznych produktu, który ma zostać zredukowany;
- Mobilność zamiast dużej masy jednostek chłodzonych powietrzem;
- Łatwy w użyciu.
Urządzenia do zapłonu łuku
Urządzenia do wstępnego zajarzania łuku dzielą się na dwie klasy: zajarzenie łuku od zwarcia i przebicie szczeliny elektroda-produkt za pomocą impulsów wysokiego napięcia.
Zapłon przez zwarcie następuje poprzez krótkotrwały kontakt elektrody z produktem i ich późniejsze oddzielenie. Prąd przepływający przez mikrowystępy elektrody podgrzewa je do temperatury wrzenia, a pole powstające w momencie rozłączenia elektrod zapewnia emisję elektronów wystarczającą do zainicjowania łuku.
Dzięki temu zajarzeniu możliwe jest przeniesienie materiału elektrody do spoiny. Aby wyeliminować to niepożądane zjawisko, zapłon należy przeprowadzić przy niskim prądzie nie przekraczającym 5-20A. Urządzenie zapłonowe musi zapewniać niski prąd zwarciowy, utrzymywać prąd na tym poziomie do momentu powstania łuku, a dopiero potem płynnie zwiększać się do poziomu roboczego.
(UDG-201, ADG-201, ADG-301).
Podstawowe wymagania dotyczące urządzeń do zapłonu szczelinowego (wzbudnicy łuku lub oscylatory):
1) musi zapewniać niezawodną inicjację łuku;
2) nie może zagrażać bezpieczeństwu spawacza i sprzętu.
Wzbudnice można zaprojektować tak, aby inicjowały łuk prądu stałego lub przemiennego. W tym drugim przypadku na wzbudnice stawiane są szereg specyficznych wymagań związanych z momentem zajarzenia łuku. Schemat obwodu oscylatora OSPZ-2M pokazano na ryc.
Ryż. 5.5. Schemat ideowy oscylatora OSPZ-2M. F1 – bezpiecznik; PZF – filtr przeciwhałasowy; TV1 – transformator podwyższający; FV – iskiernik; Cg – kondensator obwodu oscylacyjnego; Cn – kondensator odsprzęgający; TV2 – transformator wysokiego napięcia; F2 – bezpiecznik.
Kondensator Cr jest ładowany z napięcia uzwojenia wtórnego transformatora podwyższającego TV1.
Po naładowaniu go do napięcia przebicia iskiernika FV powstaje obwód oscylacyjny składający się z kondensatora Cr i uzwojenia pierwotnego transformatora wysokiego napięcia TV2. Częstotliwość oscylacji tego obwodu wynosi około 500 - 1000 kHz. Z uzwojenia wtórnego napięcie to o częstotliwości 500 - 1000 kHz i wartości około 10 000 V jest dostarczane do szczeliny elektroda-produkt poprzez kondensator separujący Cn i bezpiecznik F2.
W tym przypadku w tej szczelinie pojawia się iskra, która jonizuje szczelinę, w wyniku czego ze źródła prądu wzbudzany jest łuk elektryczny. Po wzbudzeniu łuku oscylator automatycznie się wyłącza.
Należy pamiętać, że oscylator ma wysokie napięcie.
Nie jest niebezpieczny dla ludzi ze względu na małą moc źródła. Jeżeli jednak obwód źródłowy zawiera półprzewodniki (diody, tyrystory itp.), wówczas możliwe jest ich przebicie przez napięcie oscylatora.
Aby tego uniknąć, oscylator należy podłączyć do źródła za pomocą systemów zabezpieczających (ryc. 5.6).
Jak zrobić przecinarkę plazmową własnymi rękami z falownika?
Schemat podłączenia oscylatora do źródła zasilania.
Dławik jest chroniony przez DZ dla wysokiej częstotliwości oscylatora, ma bardzo dużą reaktancję indukcyjną i nie pozwala na przejście napięcia oscylatora do źródła.
Natomiast kondensator ochronny SZ ma bardzo niską rezystancję dla wysokich częstotliwości, chroniąc źródło przed wysoką częstotliwością i wysokim napięciem oscylatora. Kondensator odsprzęgający Cp chroni oscylator przed napięciem zasilania.
Zalecenia. Typowe błędy operatora MTP podczas cięcia plazmowego i sposoby ich uniknięcia
Używanie materiałów eksploatacyjnych aż do ich awarii
Jeśli spojrzysz na wiele części tego samego typu, które zostały wycięte przy użyciu tej metody, możesz bezbłędnie zidentyfikować te części, dla których dysza lub elektroda była już „w drodze”.
Stosowanie mocno zużytych dysz i elektrod może nie tylko doprowadzić do defektów podczas cięcia detalu, ale także spowodować kosztowne naprawy przecinarki płomieniowej, a nawet przecinarki plazmowej, podczas której przecinarka plazmowa będzie przestojowa.
Awariom dysz i elektrod można łatwo zapobiec, sprawdzając kilka oznak zużycia materiałów eksploatacyjnych. Doświadczony operator zawsze poinformuje Cię o konieczności wymiany elektrody po odgłosie cięcia i kolorze płomienia łuku (wkładka cyrkonowa po wypaleniu nabiera zielonkawego zabarwienia), a także konieczności zmniejszenia wysokość palnika plazmowego podczas wykrawania.
Ponadto jednym z najlepszych sposobów oceny stanu części tnących jest jakość cięcia. Jeśli jakość cięcia nagle zacznie się pogarszać, jest to powód do sprawdzenia stanu dyszy i elektrody. Rozsądnym podejściem jest prowadzenie rejestru średniego czasu pracy elektrody lub dyszy od wymiany do wymiany. Dysza i elektroda wytrzymują różne rodzaje przekłuć, w zależności od prądu cięcia, rodzaju i grubości materiału.
Na przykład podczas cięcia stali nierdzewnej materiały eksploatacyjne należy wymieniać częściej.
Po ustaleniu na podstawie takiego dziennika średniego czasu życia elektrody dla każdego konkretnego typu wycinanej części, można dokonać planowej wymiany dysz i elektrod bez powodowania uszkodzeń wycinanych części lub awarii przecinarki płomieniowej .
Zbyt częsta wymiana dysz i elektrod
Wśród zużytych dysz i elektrod często można znaleźć takie, które nadają się jeszcze do cięcia.
Zbyt częsta wymiana materiałów eksploatacyjnych jest również bardzo powszechna wśród operatorów maszyn do cięcia metalu CNC, a zwłaszcza maszyn do cięcia plazmowego.
Podczas wymiany dyszy lub elektrody operator musi wyraźnie wiedzieć, na co zwrócić uwagę. Dysza wymaga wymiany w następujących sytuacjach:
1. Jeśli dysza jest zdeformowana od zewnątrz lub od wewnątrz.
Dzieje się tak często, gdy wysokość wykrawania jest zbyt mała i metal nie jest przecinany. Roztopiony metal uderza w zewnętrzną powierzchnię dyszy lub kołpaka ochronnego i odkształca ją.
2. Jeżeli wylot dyszy ma kształt inny niż okrąg. Przy dużej wysokości przebijania, jeśli ruch rozpoczyna się przed cięciem metalu, wówczas łuk odchyla się od prostopadłości do blachy i przechodzi przez krawędź otworu dyszy.
Aby określić, czy elektroda jest zużyta, należy spojrzeć na srebrną metalową wkładkę na końcu elektrody miedzianej (zwykle jest to stop cyrkonu, hafnu lub wolframu). Ogólnie rzecz biorąc, elektrodę uważa się za sprawną, jeśli ten metal w ogóle istnieje, a głębokość otworu w jej miejscu nie przekracza 2 mm w przypadku cięcia plazmą powietrzną lub plazmą tlenową. W przypadku cięcia plazmowego w środowisku gazu ochronnego (azot lub argon) głębokość otworu może sięgać 2,2 mm. Zawirowacz należy wymienić tylko wtedy, gdy dokładna kontrola wykaże zatkane otwory, pęknięcia, ślady łuku lub silne zużycie.
Pierścienie zawirowujące są szczególnie często wymieniane przedwcześnie. To samo dotyczy kołpaków ochronnych, które należy wymienić jedynie w przypadku uszkodzeń fizycznych. Bardzo często kołpaki ochronne można oczyścić papierem ściernym i ponownie wykorzystać.
Używanie nieprawidłowych ustawień plazmy i materiałów eksploatacyjnych
Wybór materiałów eksploatacyjnych do cięcia plazmowego zależy od rodzaju ciętego metalu (stal, miedź, mosiądz, stal nierdzewna itp.), jego grubości, ustawionego prądu łuku na przecinarce plazmowej, gazów plazmotwórczych i ochronnych itp. .
Instrukcja obsługi maszyny do cięcia plazmowego opisuje, jakich materiałów eksploatacyjnych należy używać w różnych warunkach procesu cięcia. Należy przestrzegać trybów i zaleceń dotyczących ustawień cięcia plazmowego podanych w instrukcji obsługi.
Stosowanie materiałów eksploatacyjnych (dysz, elektrod) nieodpowiadających aktualnemu trybowi cięcia plazmowego zwykle prowadzi do przyspieszonej awarii materiałów eksploatacyjnych i znacznego pogorszenia jakości cięcia płomieniowego.
Bardzo ważne jest, aby cięcie plazmowe metalu wykonywać dokładnie takim prądem łuku, na jaki przeznaczone są stosowane materiały eksploatacyjne. Na przykład nie należy ciąć metalu plazmą o natężeniu 100 A, jeśli przecinarka plazmowa ma dyszę 40 A itp.
Najwyższą jakość cięcia uzyskuje się, gdy prąd na przecinarce plazmowej jest ustawiony na 95% znamionowego prądu cięcia, dla którego zaprojektowana jest dysza. Jeśli tryb cięcia plazmowego jest ustawiony na niski prąd łuku, w miejscu cięcia będą widoczne żużle, a na odwrotnej stronie ciętych części będzie widoczna znaczna ilość zadziorów; jakość cięcia płomieniowego będzie niezadowalająca.
Jeżeli prąd ustawiony na przecinarce plazmowej będzie zbyt wysoki, żywotność dyszy ulegnie znacznemu skróceniu.
Nieprawidłowy zespół przecinarki plazmowej
Przecinarkę płomieniową należy zmontować w taki sposób, aby wszystkie jej części ściśle do siebie przylegały i nie było wrażenia „luzu”.
Dopasowanie części palnika plazmowego zapewnia dobry kontakt elektryczny i normalną cyrkulację powietrza i chłodziwa przez przecinarkę plazmową. Podczas wymiany materiałów eksploatacyjnych należy starać się rozmontowywać przecinarkę plazmową na czystej powierzchni, aby brud i pył metalowy powstający podczas cięcia plazmowego nie zanieczyścił palnika plazmowego.
Czystość podczas montażu/demontażu przecinarki plazmowej jest bardzo ważna, a mimo to wymóg ten często nie jest spełniony.
Nieprzeprowadzanie regularnej, zaplanowanej konserwacji palnika plazmowego
Bez odpowiedniej konserwacji przecinarka plazmowa może działać przez wiele miesięcy, a nawet lat.
Jednakże kanały gazu i chłodziwa wewnątrz przecinarki plazmowej muszą być utrzymywane w czystości, a dysza i gniazda elektrod muszą być sprawdzane pod kątem zanieczyszczeń lub uszkodzeń. Brud i pył metalowy należy usunąć z przecinarki plazmowej. Do czyszczenia palnika plazmowego należy używać czystej bawełnianej szmatki i środka do czyszczenia styków elektrycznych lub nadtlenku wodoru.
Cięcie metalu bez sprawdzania ciśnienia gazu plazmowego i dopływu chłodziwa do przecinarki plazmowej
Codziennie należy sprawdzać przepływ i ciśnienie gazu plazmowego i chłodziwa.
Jeśli natężenie przepływu jest niewystarczające, części palnika nie będą odpowiednio chłodzone, a ich żywotność ulegnie skróceniu. Niewystarczający przepływ chłodziwa na skutek zużytej pompy, zatkanych filtrów lub niewystarczającej ilości chłodziwa jest częstą przyczyną awarii przecinarki plazmowej.
Stałe ciśnienie gazu plazmowego jest bardzo ważne dla utrzymania łuku cięcia i wysokiej jakości cięcia. Nadmierne ciśnienie gazu plazmotwórczego jest częstą przyczyną trudnego zapłonu łuku plazmowego, mimo że wszystkie pozostałe wymagania dotyczące ustawień, parametrów i procesu cięcia plazmowego są w pełni spełnione. Zbyt wysokie ciśnienie gazu tworzącego plazmę powoduje szybkie uszkodzenie elektrod.
Gaz tworzący plazmę musi zostać oczyszczony z zanieczyszczeń, ponieważ jego czystość ma duży wpływ na żywotność materiałów eksploatacyjnych i palnika plazmowego jako całości. Sprężarki dostarczające powietrze do maszyn do cięcia plazmowego mają tendencję do zanieczyszczania powietrza olejami, wilgocią i drobnymi cząsteczkami pyłu.
Wykrawanie na małej wysokości palnika plazmowego nad metalem
Odległość przedmiotu obrabianego od ciętej dyszy palnika plazmowego ma ogromny wpływ zarówno na jakość cięcia, jak i żywotność materiałów eksploatacyjnych.
Nawet niewielkie zmiany wysokości przecinarki plazmowej nad metalem mogą znacząco wpłynąć na skosy na krawędziach wycinanych części. Szczególnie ważna jest wysokość przecinarki plazmowej nad metalem podczas przebijania.
Częstym błędem jest wykrawanie, gdy wysokość palnika plazmowego nad metalem jest niewystarczająca. Powoduje to rozpryskiwanie się stopionego metalu z otworu przekłuwającego na dysze i kołpaki ochronne, niszcząc te części.
To znacznie pogarsza jakość cięcia. Jeśli przekłucie nastąpi, gdy przecinarka plazmowa dotknie metalu, może nastąpić cofanie się łuku.
Jeśli łuk zostanie „wciągnięty” do palnika plazmowego, wówczas elektroda, dysza, zawirowator, a czasami cały nóż ulegają zniszczeniu.
Zalecana wysokość przekłuwania wynosi 1,5-2-krotność grubości metalu ciętego plazmą. Należy zwrócić uwagę, że przy wykrawaniu odpowiednio grubego metalu zalecana wysokość jest zbyt duża, łuk pilotujący nie dochodzi do powierzchni blachy, w związku z czym nie ma możliwości rozpoczęcia procesu cięcia na zalecanej wysokości. Jeśli jednak wykrawanie zostanie wykonane na wysokości, na której przecinarka plazmowa może zapalić łuk, wówczas na palnik plazmowy mogą spaść odpryski stopionego metalu.
Rozwiązaniem tego problemu może być zastosowanie techniki technologicznej zwanej „skakaniem”. Podczas przetwarzania polecenia włączenia cięcia, cięcie plazmowe zostaje włączone na małej wysokości, po czym przecinarka podnosi się na zadaną wysokość skoku, przy której odpryski metalu nie docierają do przecinarki.
Po zakończeniu wykrawania nóż opuszcza się na wysokość przebijania i zaczyna przesuwać się po konturze.
Cięcie plazmowe metalu przy zbyt dużej lub zbyt małej prędkości
Rozbieżność pomiędzy prędkością cięcia plazmą a wybranym trybem znacząco wpływa na jakość cięcia. Jeśli ustawiona prędkość cięcia jest zbyt niska, na ciętych częściach będzie występowała duża ilość wypływek i różnych osadów metalu na całej długości cięcia, w dolnej części krawędzi części.
Niskie prędkości skrawania mogą powodować większe szerokości nacięcia i duże ilości odprysków metalu na górnej powierzchni części. Jeżeli prędkość cięcia zostanie ustawiona na zbyt dużą, łuk będzie się cofał, powodując zniekształcenie krawędzi cięcia, wąskie cięcie oraz powstawanie małych kropelek zadziorów i wypływów na dole ciętej krawędzi.
Zadziory powstałe przy dużych prędkościach skrawania są trudne do usunięcia. Przy prawidłowej prędkości cięcia ilość zadziorów, wypływek i ugięcia metalu będzie minimalna. Powierzchnia krawędzi ciętej płomieniowo przy odpowiedniej prędkości powinna być czysta, a obróbka powinna być minimalna. Na początku i na końcu cięcia łuk może „odbiegać” od prostopadłości.
Domowa przecinarka plazmowa ze spawarki inwertorowej: schemat i procedura montażu
Dzieje się tak, ponieważ łuk nie nadąża za palnikiem. Odchylenie łuku prowadzi do tego, że uderza on w boczną powierzchnię dyszy, naruszając w ten sposób jej geometrię. Jeśli tniesz od krawędzi, środek otworu dyszy musi znajdować się dokładnie w jednej linii z krawędzią części. Jest to szczególnie ważne w maszynach kombinowanych, które wykorzystują zarówno głowicę dziurkującą, jak i przecinarkę plazmową.
Odchylenie łuku może również wystąpić, gdy palnik plazmowy przy włączonym cięciu przechodzi przez krawędź arkusza lub gdy linia wyjściowa przecina stare cięcie. Aby zredukować ten efekt, konieczna jest precyzyjna regulacja parametrów taktowania.
Uszkodzenie mechaniczne lub awaria przecinarki plazmowej
Kolizje frezu z blachą, wyciętymi elementami lub krawędziami stołu tnącego mogą spowodować całkowite uszkodzenie plotera. Można uniknąć kolizji pomiędzy obcinakiem a wyciętymi częściami, jeśli program sterujący określi przejścia jałowe wokół, a nie nad wyciętymi częściami.
Przykładowo program optymalnego cięcia ProNest firmy MTC-Software posiada taką funkcję, która pozwala zminimalizować ryzyko awarii palnika plazmowego i zaoszczędzić znaczne pieniądze. Stabilizatory wysokości palnika zapewniają również pewną ochronę przed zderzeniami metali. Jeśli jednak używany jest tylko czujnik wysokości palnika oparty na napięciu łuku, na końcu cięcia mogą wystąpić „dzioby”, ponieważ Napięcie łuku zmienia się w wyniku jego „odgięcia”, a frez przesuwa się w dół w celu kompensacji.
W systemach CNC zastosowano wielostopniowy system zabezpieczenia przed kolizjami z metalem. Stosowany jako czujnik dotykowy mierzący rezystancję pomiędzy anteną wokół palnika a arkuszem, czujnik pojemnościowy i czujnik napięcia łuku. Pozwala to w pełni wykorzystać możliwości każdego typu czujnika. Ponadto, aby chronić przecinarkę, można zastosować „kruche” wsporniki, które w przypadku kolizji pękną szybciej niż przecinarka plazmowa.
W ten sposób kompetentny operator maszyny do cięcia plazmowego może zaoszczędzić w swojej firmie ogromną ilość pieniędzy, czasu i kosztów ogólnych związanych z cięciem plazmowym.
Efektem pracy dobrego operatora sprzętu będzie zwiększona rentowność cięcia plazmowego i wzrost zysku całego przedsiębiorstwa.
Na obecnym etapie rozwoju sprzętu budowlanego najczęściej stosuje się cięcie diamentowe i wiercenie w betonie.
Nie wyklucza się jednak innych technologii cięcia materiałów o wysokiej wytrzymałości, na przykład technologii cięcia plazmowego betonu.
Technologia ta została opracowana i opatentowana pod koniec XX wieku.
Przecinarka plazmowa zrób to sam z falownika do cięcia plazmowego metalu (7 zdjęć + 2 filmy)
Ale sprzęt działający na tej zasadzie dopiero teraz zaczął być używany.
Na czym opiera się zasada cięcia plazmowego? Bardzo prosta. Pod wpływem ciepła generowanego przez sprężony łuk plazmowy topi się nawet gęsty materiał, w tym beton i żelbet. Następnie strumień gorącej plazmy bardzo szybko usuwa stopioną masę.
To właśnie dzięki uzyskaniu przez gazy obojętne właściwości przewodzących prąd elektryczny, a także ich przekształceniu w plazmę, przeprowadzane jest cięcie plazmowe betonu.
W końcu plazma to nic innego jak zjonizowany gaz podgrzany do bardzo wysokich temperatur, powstający, gdy instrument jest podłączony do określonego źródła energii elektrycznej.
Palnik plazmowy to specjalne urządzenie techniczne, które wytwarza plazmę, spręża łuk elektryczny i wdmuchuje w niego gaz wytwarzający plazmę.
Należy zaznaczyć, że technologia ta cieszy się coraz większą popularnością wśród specjalistów zajmujących się przemysłową obróbką materiałów.
Różnica pomiędzy cięciem plazmowym betonu a cięciem lancą tlenową polega na tym, że podczas procesu cięcia materiał topi się bardzo intensywnie i jest szybko usuwany z wycinanej bruzdy.
Podczas obróbki temperatura osiąga 6000°C.
Lanca proszkowa stosowana przy cięciu plazmowym zwiększa temperaturę do 10 000 - 25 000°.
Do obsługi sprzętu specjaliści wykorzystują dwie różne technologie cięcia betonu: cięcie strumieniem plazmy i cięcie łukiem plazmowym.
Czym się różnią?
Fakt, że łuk tnący zapala się podczas cięcia strumieniem plazmy pomiędzy elektrodą a końcówką generującą instalacji, ale obiekt oddziaływania znajduje się poza obwodem elektrycznym.
Z palnika plazmowego wydobywa się szybki strumień plazmy i to właśnie jego potężna energia cieplna tnie żelbet, a także inne materiały o wysokiej wytrzymałości.
W przypadku metody cięcia łukiem plazmowym łuk plazmowy zapala się pomiędzy nietopliwą elektrodą a płaszczyzną ciętego materiału. Proces cięcia zachodzi dzięki działaniu kilku składników: energii miejsca łuku przyelektrodowego, a także kolumny plazmy i uciekającego z niej palnika.
Cięcie łukiem plazmowym jest uważane przez praktyków za najbardziej efektywne i często stosowane w obróbce metali.
Technologia cięcia strumieniem plazmy stosowana jest głównie do obróbki materiałów nieprzewodzących.
Cięcie plazmowe zrób to sam - technologia działania
Środki ostrożności podczas pracy z lampą plazmową
Cięcie plazmowe wiąże się z szeregiem zagrożeń: prądem elektrycznym, wysoką temperaturą plazmy, gorącymi metalami i promieniowaniem ultrafioletowym.
Środki ostrożności podczas pracy przy cięciu plazmowym:
Przygotowanie maszyny do cięcia powietrzem i plazmą do pracy
Sposób podłączenia wszystkich elementów urządzenia do cięcia pneumatycznego i plazmowego opisano szczegółowo w instrukcji urządzenia, dlatego od razu przystąp do dodawania dodatkowych odcieni:
- Urządzenie należy zamontować w sposób umożliwiający dostęp powietrza.
Chłodzenie korpusu przecinarki plazmowej pozwala na dłuższą pracę bez przerw i zmniejsza konieczność rzadszego wyłączania urządzenia chłodzącego. Miejsce powinno być takie, aby na urządzeniu nie było kropel stopionego metalu.
- Sprężarka powietrza jest podłączona do palnika plazmowego poprzez separator wilgoci i oleju. Jest to bardzo ważne, ponieważ woda przedostająca się do komory plazmatronu lub kropelki oleju mogą doprowadzić do zniszczenia całej plazmy lub nawet jej eksplozji. Ciśnienie powietrza przekazywane do plazmatronu musi odpowiadać parametrom urządzenia.
Jeśli ciśnienie jest niewystarczające, łuk plazmowy będzie niestabilny i często gaśnie. Jeśli ciśnienie będzie nadmierne, niektóre części lampy plazmowej mogą stać się bezużyteczne.
- Jeśli na obrabiany przedmiot nałoży się rdza, maska lub olej, należy go lepiej oczyścić i usunąć. Chociaż cięcie powietrzem jest plazmowe i może wycinać brązowe części, najlepiej zapomnieć, że podczas podgrzewania rdzy wydzielają się toksyczne opary.
Jeśli planujesz wycinanie zbiorników przechowujących materiały łatwopalne, należy je dokładnie oczyścić.
- Jeśli chcesz uzyskać gładkie, równoległe cięcie bez żużlu i wżerów, musisz wybrać odpowiednie natężenie przepływu i prędkość cięcia.
Poniższe tabele przedstawiają optymalne parametry skrawania dla różnych metali o różnej grubości.
Tabela 2. Moc cięcia plazmowego i prędkość cięcia półfabrykatów z różnych metali.
Parametry cięcia plazmą powietrzną
Wybór prędkości palnika po raz pierwszy będzie trudny, potrzebne jest doświadczenie.
W ten sposób można początkowo kontrolować tę zasadę: palnik plazmowy należy sterować tak, aby iskry były widoczne z tyłu przedmiotu obrabianego. Jeżeli nie widać iskier, przedmiot obrabiany nie będzie cięty. Należy również pamiętać, że zbyt wolne operowanie nożem negatywnie wpłynie na jakość cięcia, są na nim wymiary i kora, a pacha może być również niestabilna, aby się spalić, a nawet wyjść.
Cięcie plazmowe
Możesz teraz kontynuować proces cięcia.
Przed zapłonem łuku elektrycznego plazmatron należy przedmuchać powietrzem, aby usunąć przypadkową kondensację i ciała obce.
W tym celu należy nacisnąć i zwolnić przycisk zapłonu. W ten sposób urządzenie wchodzi w metodę czyszczenia. Po około 30 sekundach można wcisnąć i przytrzymać przycisk zapłonu.
Jak już opisano w zasadzie działania lampy plazmowej, pomiędzy elektrodą a końcówką dyszy zapala się łuk pomocniczy (pilotujący, pilotujący). Zwykle nie świeci się dłużej niż 2 sekundy. Dlatego w tym czasie konieczne jest oświetlenie łuku roboczego (tnącego). Metoda zależy od rodzaju lampy plazmowej.
Jeśli lampa plazmowa działa bezpośrednio, konieczne jest wykonanie zwarcia: po uformowaniu długości zwoju należy nacisnąć przycisk zapłonu - dopływ powietrza zostanie zatrzymany i styk się zamknie.
Zawór powietrza wówczas automatycznie się otwiera, strumień powietrza wypływa z zaworu, jonizuje, zwiększa swój rozmiar i odprowadza iskrę z dyszy lampy plazmowej. Dlatego między elektrodą a metalem części zapala się łuk roboczy.
Ważny! Zajarzenie łuku kontaktowego nie oznacza, że należy przyłożyć palnik plazmowy lub przyłożyć go do przedmiotu obrabianego.
Zapłon płomienia plazmowego
Gdy wskaźnik się zaświeci, lampka zgaśnie.
Jeżeli łuku roboczego nie można załączyć po raz pierwszy, należy zwolnić przycisk zapłonu i wcisnąć go ponownie – rozpoczyna się nowy cykl.
Cechy wytwarzania lampy plazmowej własnymi rękami z konwertera: obwód, etapy pracy, sprzęt
Istnieje kilka powodów, dla których łuk roboczy może się nie zapalić: niewystarczające ciśnienie powietrza, niewystarczający montaż lampy plazmowej lub inne uszkodzenia.
Zdarzają się również przypadki, gdy ostrze tnące jest wyłączone.
Przyczyną będzie najprawdopodobniej noszenie elektrody lub ignorowanie odległości paliwa plazmowego od powierzchni przedmiotu obrabianego.
Odległość między lampą a metalem
Uczyć się więcej:

Cięcie plazmowe metalu ze zdalnym wyłączaniem
Ręczne pneumatyczne cięcie plazmowe wiąże się z problemem zachowania odległości palnika/dyszy od powierzchni metalu.
Podczas pracy ręką jest to dość trudne, ponieważ oddech wymyka się spod kontroli, a cięcie okazuje się nierówne. Optymalna odległość dyszy od przedmiotu obrabianego wynosi 1,6-3 mm; do obserwacji stosuje się specjalne przekładki, ponieważ sama plazma nie może być dociskana do powierzchni przedmiotu obrabianego.
Drabiny znajdują się w górnej części dyszy, następnie plazmatron montuje się na obrabianym przedmiocie i wycina.
Należy pamiętać, że lampa plazmowa musi być mocno prostopadła do przedmiotu obrabianego. Dopuszczalne odchylenia od 10 do 50°. Jeśli obrabiany przedmiot jest zbyt cienki, nóż można trzymać w małym rogu, co zapobiegnie poważnemu odkształceniu cienkiego metalu.
Roztopiony metal nie powinien wpadać do dyszy.
Pracę z cięciem plazmowym można opanować samodzielnie, należy jednak pamiętać o środkach bezpieczeństwa, ale także o tym, że dysza i elektroda to materiały eksploatacyjne, które wymagają terminowej wymiany.
Powiązane artykuły
Możesz być zainteresowany
Przecinarki plazmowe znajdują szerokie zastosowanie w warsztatach i przedsiębiorstwach związanych z metalami nieżelaznymi. Większość małych firm korzysta z domowej przecinarki plazmowej.
Dobrze sprawdza się przy cięciu metali nieżelaznych, gdyż pozwala na miejscowe nagrzewanie wyrobów i nie powoduje ich deformacji. Własna produkcja noży wynika z wysokich kosztów profesjonalnego sprzętu.
W procesie produkcji takiego narzędzia wykorzystywane są komponenty z innych urządzeń elektrycznych.
Falownik przeznaczony jest do wykonywania prac zarówno w środowisku domowym jak i przemysłowym. Istnieje kilka rodzajów przecinarek plazmowych do pracy z różnymi rodzajami metali.
Tam są:
- Przecinarki plazmowe pracujące w środowisku gazów obojętnych, takich jak argon, hel czy azot.
- Przyrządy pracujące w środkach utleniających, takich jak tlen.
- Sprzęt przeznaczony do pracy w atmosferach mieszanych.
- Przecinarki pracujące w stabilizatorach gazowo-cieczowych.
- Urządzenia pracujące ze stabilizacją wodną lub magnetyczną. Jest to najrzadszy rodzaj noża, którego prawie nie można znaleźć na otwartym rynku.
Lub plazmatron jest główną częścią cięcia plazmowego, odpowiedzialną za bezpośrednie cięcie metalu.
Zdemontowana przecinarka plazmowa.
Większość inwerterowych przecinarek plazmowych składa się z:
- dysze;
- elektroda;
- nasadka ochronna;
- dysze;
- wąż gumowy;
- głowice tnące;
- długopisy;
- zatrzymanie rolki.
Zasada działania prostej półautomatycznej przecinarki plazmowej jest następująca: gaz roboczy wokół palnika plazmowego nagrzewa się do bardzo wysokich temperatur, przy czym pojawia się plazma przewodząca prąd.
Następnie prąd przepływający przez zjonizowany gaz przecina metal poprzez lokalne topienie. Następnie strumień plazmy usuwa pozostały stopiony metal i uzyskuje się czyste cięcie.
W zależności od rodzaju uderzenia w metal wyróżnia się następujące typy plazmatronów:
- Urządzenia działania pośredniego.
Ten typ plazmatronu nie przepuszcza prądu przez siebie i nadaje się tylko w jednym przypadku - do cięcia produktów niemetalowych. - Bezpośrednie cięcie plazmowe.
Służy do cięcia metali poprzez wytwarzanie strumienia plazmy.
Wykonanie przecinarki plazmowej własnymi rękami
Cięcie plazmowe DIY można wykonać w domu. Zaporowy koszt profesjonalnego sprzętu i ograniczona liczba modeli na rynku zmuszają rzemieślników do samodzielnego montażu przecinarki plazmowej z falownika spawalniczego.
Domową przecinarkę plazmową można wykonać pod warunkiem, że posiada się wszystkie niezbędne elementy.
Przed wykonaniem instalacji do cięcia plazmowego należy przygotować następujące elementy:
- Kompresor.
Część jest niezbędna do zapewnienia przepływu powietrza pod ciśnieniem. - Plasmatron.
Produkt służy do bezpośredniego cięcia metalu. - Elektrody.
Służy do zapalania łuku i tworzenia plazmy. - Izolator.
Chroni elektrody przed przegrzaniem podczas wykonywania cięcia plazmowego metalu. - Dysza.
Część, której wielkość decyduje o możliwościach całej przecinarki plazmowej, składana własnymi rękami z falownika. - Falownik spawalniczy.
Źródło prądu stałego do instalacji. Można zastąpić transformatorem spawalniczym.
Źródłem zasilania urządzenia może być transformator lub falownik.
Schemat działania przecinarki plazmowej.
Źródła transformatorowe prądu stałego charakteryzują się następującymi wadami:
- wysokie zużycie energii elektrycznej;
- duże wymiary;
- niedostępność.
Zalety takiego źródła zasilania obejmują:
- niska wrażliwość na zmiany napięcia;
- więcej mocy;
- wysoka niezawodność.
W razie potrzeby jako zasilanie przecinarki plazmowej można zastosować falowniki:
- skonstruować małe urządzenie;
- zmontować wysokiej jakości przecinarkę plazmową o dużej wydajności i stabilnym łuku.
Ze względu na dostępność i lekkość zasilacza inwertorowego, oparte na nim przecinarki plazmowe można konstruować w domu. Do wad falownika można zaliczyć jedynie stosunkowo małą moc strumienia. Z tego powodu grubość metalowego przedmiotu wycinanego przez inwerterową przecinarkę plazmową jest poważnie ograniczona.
Jedną z najważniejszych części przecinarki plazmowej jest przecinarka ręczna.
Ten element sprzętu do cięcia metalu składa się z następujących elementów:
- uchwyt z nacięciami do układania przewodów;
- przycisk uruchamiania palnika plazmowego;
- elektrody;
- system wirowania przepływu;
- końcówka chroniąca operatora przed odpryskami roztopionego metalu;
- sprężyna zapewniająca wymaganą odległość między dyszą a metalem;
- dysze do usuwania kamienia i nagaru.
Cięcie metalu o różnej grubości odbywa się poprzez zmianę dysz w palniku plazmowym. W większości konstrukcji plazmatronów dysze zabezpieczone są specjalną nakrętką o średnicy umożliwiającej przejście przez stożkową końcówkę i zaciśnięcie szerokiej części elementu.
Za dyszą znajdują się elektrody i izolacja. Aby w razie potrzeby móc wzmocnić łuk, w konstrukcji plazmatronu uwzględniono zawirowator przepływu powietrza.
Przecinarki plazmowe typu „zrób to sam” oparte na inwerterowym źródle zasilania są dość mobilne. Dzięki niewielkim wymiarom sprzęt taki można zastosować nawet w najbardziej niedostępnych miejscach.
Plany
W Internecie dostępnych jest wiele różnych rysunków przecinarki plazmowej. Najłatwiejszym sposobem wykonania przecinarki plazmowej w domu jest użycie źródła falownika prądu stałego.
Obwód elektryczny przecinarki plazmowej.
Najpopularniejszy rysunek techniczny przecinarki plazmowej obejmuje następujące elementy:
- Elektroda.
Element ten jest zasilany napięciem ze źródła zasilania w celu jonizacji otaczającego gazu. Z reguły jako elektrodę stosuje się metale ogniotrwałe, tworząc mocny tlenek. W większości przypadków projektanci spawarek używają hafnu, cyrkonu lub tytanu. Najlepszym materiałem elektrody do użytku domowego jest hafn. - Dysza.
Element automatycznej spawarki plazmowej wytwarza strumień zjonizowanego gazu i przepuszcza powietrze w celu ochłodzenia elektrody. - Chłodnica.
Element służy do usuwania ciepła z dyszy, ponieważ podczas pracy temperatura plazmy może osiągnąć 30 000 stopni Celsjusza.
Większość obwodów maszyny do cięcia plazmowego implikuje następujący algorytm działania przecinarki oparty na strumieniu zjonizowanego gazu:
- Pierwsze naciśnięcie przycisku start włącza przekaźnik zasilający jednostkę sterującą urządzenia.
- Drugi przekaźnik dostarcza prąd do falownika i łączy elektryczny zawór oczyszczania palnika.
- Silny strumień powietrza dostaje się do komory palnika i ją oczyszcza.
- Po określonym przez rezystory czasie załącza się trzeci przekaźnik, który zasila elektrody instalacji.
- Uruchamia się oscylator, dzięki czemu gaz roboczy znajdujący się pomiędzy katodą i anodą zostaje zjonizowany. Na tym etapie pojawia się łuk pilotujący.
- Kiedy łuk dociera do metalowej części, pomiędzy palnikiem plazmowym a powierzchnią zapala się łuk, zwany łukiem roboczym.
- Wyłączenie dopływu prądu w celu zajarzenia łuku za pomocą specjalnego kontaktronu.
- Wykonywanie prac związanych z cięciem lub spawaniem. W przypadku zaniku łuku przekaźnik kontaktronowy ponownie włącza prąd i zapala rezerwowy strumień plazmy.
- Po zakończeniu pracy po wyłączeniu łuku czwarty przekaźnik uruchamia sprężarkę, której powietrze chłodzi dyszę i usuwa resztki spalonego metalu.
Najbardziej udanymi schematami przecinarki plazmowej jest model APR-91.
Czego potrzebujemy?
Rysunek przecinarki plazmowej.
Aby stworzyć spawarkę plazmową, musisz zdobyć:
- źródło prądu stałego;
- plazmatron.
Ten ostatni obejmuje:
- dysza;
- elektrody;
- izolator;
- sprężarka o wydajności 2-2,5 atmosfery.
Większość współczesnych rzemieślników wykonuje spawanie plazmowe podłączone do zasilacza inwertorowego. Plazmatron zaprojektowany z wykorzystaniem tych elementów do ręcznego cięcia powietrzem działa w następujący sposób: naciśnięcie przycisku sterującego powoduje zapalenie łuku elektrycznego pomiędzy dyszą a elektrodą.
Po zakończeniu pracy, po naciśnięciu przycisku wyłączającego, sprężarka podaje strumień powietrza i zrzuca z elektrod pozostały metal.
Zespół falownika
Jeśli falownik fabryczny nie jest dostępny, możesz zamontować domowy.
Falowniki do przecinarek opartych na plazmie gazowej z reguły mają następujące elementy:
- jednostka mocy;
- sterowniki wyłącznika zasilania;
- blok mocy.
Palnik plazmowy w sekcji.
Przecinarki plazmowe czy sprzęt spawalniczy nie mogą obejść się bez niezbędnych narzędzi w postaci:
- zestaw śrubokrętów;
- lutownica;
- nóż;
- piły do metalu;
- łączniki gwintowane;
- druty miedziane;
- PCB;
- mika.
Zasilacz do cięcia plazmowego jest montowany na bazie rdzenia ferrytowego i musi posiadać cztery uzwojenia:
- pierwotny, składający się ze 100 zwojów drutu o grubości 0,3 milimetra;
- pierwszy wtórny z 15 zwojów kabla o grubości 1 milimetra;
- drugie wtórne z 15 zwojów drutu 0,2 mm;
- trzeci jest wtórny z 20 zwojów drutu 0,3 mm.
Notatka! Aby zminimalizować negatywne skutki skoków napięcia w sieci elektrycznej, uzwojenie należy wykonać na całej szerokości drewnianej podstawy.
Jednostka napędowa domowego falownika musi składać się ze specjalnego transformatora. Aby utworzyć ten element, należy wybrać dwie żyły i nawinąć na nie drut miedziany o grubości 0,25 milimetra.
Na szczególną uwagę zasługuje układ chłodzenia, bez którego inwerterowe zasilanie palnika plazmowego może szybko zawieść.
Rysunek technologii cięcia plazmowego.
Podczas pracy z urządzeniem, aby osiągnąć jak najlepsze rezultaty należy przestrzegać zaleceń:
- regularnie sprawdzaj prawidłowy kierunek strumienia plazmy gazowej;
- sprawdź właściwy dobór sprzętu zgodnie z grubością produktu metalowego;
- monitorować stan materiałów eksploatacyjnych palnika plazmowego;
- upewnić się, że zachowana jest odległość strumienia plazmy od przedmiotu obrabianego;
- zawsze sprawdzaj prędkość cięcia, aby uniknąć żużla;
- od czasu do czasu diagnozuj stan działającego układu zasilania gazem;
- wyeliminować wibracje elektrycznego plazmatronu;
- Utrzymuj czyste i uporządkowane miejsce pracy.
Wniosek
Urządzenia do cięcia plazmowego są niezbędnym narzędziem do dokładnego cięcia wyrobów metalowych. Dzięki przemyślanej konstrukcji palniki plazmowe zapewniają szybkie, równe i wysokiej jakości cięcie blach bez konieczności późniejszej obróbki powierzchni.
Większość rzemieślników z małych warsztatów woli samodzielnie montować mini frezy do pracy z cienkim metalem. Z reguły samodzielnie wykonana przecinarka plazmowa nie różni się charakterystyką i jakością pracy od modeli fabrycznych.