Zrób to sam płyty chodnikowe z wiórów marmurowych. Tworzymy sztuczny marmur własnymi rękami. Sposób wykonania sztucznego kamienia
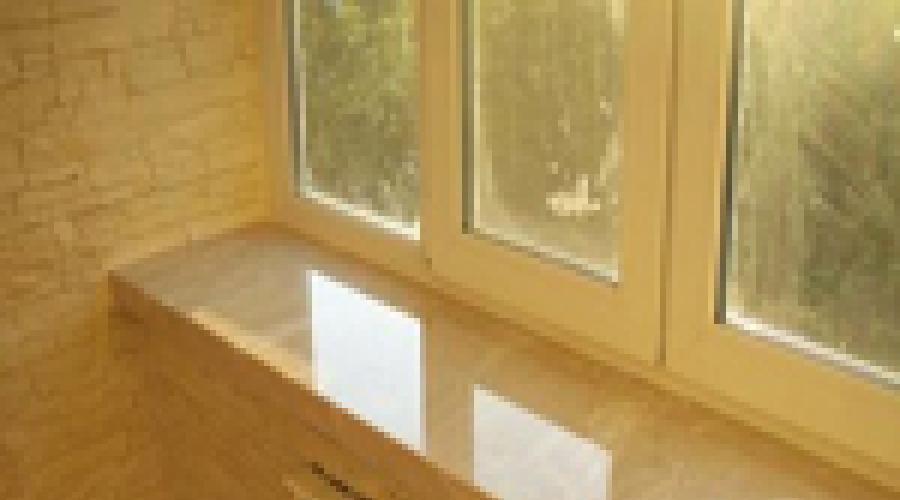
Przeczytaj także
Marmur, który ma doskonałe właściwości dekoracyjne, od zawsze był ceniony w budownictwie. Ale ze względu na wysoki koszt materiału nie każdy może sobie pozwolić na wykorzystanie go do dekoracji wnętrz. Dlatego jako alternatywę opracowano sztuczny materiał imitujący kamień. Został nazwany sztucznym marmurem.
Opis i rodzaje materiałów
Sztuczny marmur to materiał stosowany głównie w hydraulice, do produkcji liniowych materiałów okładzinowych. Z niego powstają parapety, wanny, blaty, stopnie, ozdobne fontanny i rzeźby. Służy do dekoracji biur i pomieszczeń administracyjnych.
Termin „sztuczny marmur” oznacza nie tylko lany marmur, który jest imitacją naturalnego kamienia. Istnieją inne jego odmiany, które znajdują szerokie zastosowanie w budownictwie, przemyśle i dekoracji wnętrz.
Odmiany sztucznego marmuru:
- odlewanie;
- oselkovy (lub gips);
- zmielony (lub posiekany);
- elastyczny (lub płynny).
odlewanie
Największą popularnością cieszy się lany marmur – materiał kompozytowy, który bazuje na utwardzonej żywicy poliestrowej i wypełniaczu mineralnym. Wypełniaczem mogą być wióry marmurowe, piasek kwarcowy itp.
W zależności od wybranych żywic i wypełniaczy materiał może być wykonany jako imitacja naturalnego marmuru, jaspisu, granitu, malachitu, onyksu.
Tak wygląda odlany sztuczny marmur na zdjęciu
Oselkovy
Marmur Oselkovy to kolorowa masa gipsowa zmieszana z wodą klejącą, która jest nakładana na podstawę i nadawana lustrzanemu wykończeniu poprzez polerowanie i szlifowanie. Można ją barwić do różnych materiałów, takich jak lapis lazuli, malachit, różne rodzaje marmuru.
Gips jest głównym materiałem do produkcji marmuru kamiennego. Dodawane są do niego specjalne substancje, które spowalniają wiązanie gipsu. Najczęściej stosuje się klej rozcieńczony w wodzie.
Zaletami marmuru gipsowego są lekkość i wysoka wytrzymałość. Dzięki niemu możesz budować lekkie konstrukcje. Zastosowanie tego materiału w pomieszczeniach mieszkalnych przyczynia się do poprawy mikroklimatu: pochłania nadmiar wilgoci lub oddaje ją, jeśli pomieszczenie jest zbyt suche.
Zdjęcie marmuru oselkovy
Ziemia (mikrokalcyt)
Marmur szlifowany lub kruszony to drobno zdyspergowany wypełniacz pochodzenia mineralnego. Jest to sproszkowana substancja o barwie białej lub szarej. Wykonany jest przez szlifowanie białego marmuru.
Materiał ten jest trwały, o niskiej aktywności chemicznej, odporny na promienie ultrafioletowe. Ma jasny biały kolor i praktycznie nie wchłania wilgoci. Najczęściej wykorzystywana jest do produkcji wyrobów z tworzyw sztucznych, farb i lakierów, ściernych środków czyszczących, papieru, linoleum itp.
Ciekły
Ten rodzaj marmuru to jeden z najnowszych materiałów wykończeniowych. Składa się z wiórów marmurowych i polimerów akrylowych.
Płynny marmur jest bardzo elastyczny, lekki i przyjazny dla środowiska. Można go łatwo przyciąć nożyczkami lub nożem i przykleić do ścian zamiast tapety. Stosując ten materiał można uzyskać idealnie płaską, bezszwową powierzchnię. Dlatego jest często używany do licowania konstrukcji o nieregularnych kształtach, takich jak łuki, kolumny, obiekty kuliste.
Zastosowanie płynnego marmuru
Produkcja lanego sztucznego marmuru
Technologia produkcji materiału jest dość prosta i wymaga tylko specjalnego sprzętu, pomieszczeń, czasu i zasobów finansowych.
Ekwipunek
Aby uzyskać lany marmur, stosuje się niewielki zestaw sprzętu:
- formy odlewnicze (matryce);
- rozpylacz żelkotu;
- mikser do mieszania kompozycji;
- pędzle do mazania pleśni.
Formy do marmuru wykonane są na bazie kauczuku poliuretanowego. Wysokiej jakości matryce, które charakteryzują się wytrzymałością i nie są podatne na poważne odkształcenia, są bardzo drogie. Jednak ich koszt zwraca się w pełni, ponieważ produkcja ma wysoką opłacalność.
Skład surowców
Do produkcji materiału miesza się żywicę akrylową lub poliestrową i wióry marmurowe w stosunku 4: 1. Do wiązania można również zastosować zaprawę cementową, gips budowlany, zaprawę wapienną z dodatkiem cementu. Ale najczęściej używa się żywic, ponieważ zapewniają one wysoką wytrzymałość materiału.
Funkcję wypełniacza czasami pełnią materiały dekoracyjne (kolorowy piasek, kamyki, kolorowy kwarc). W tym przypadku gotowe produkty nie są analogiem kamienia naturalnego, ale całkowicie nowym rodzajem materiałów wykończeniowych.
Aby uzyskać pożądany kolor, do mieszanki dodaje się pigmenty mineralne. Materiał wykonany jest w różnych kolorach, przeplatanych i smużonych. W tym celu stosuje się specjalną metodę mieszania pigmentów. Pigmenty nie tylko barwią materiał, ale także czynią go bardziej odpornym na wpływy zewnętrzne. Zewnętrzna warstwa ochronna żelkotu nadaje powłoce lśniący połysk.
Technologia produkcji
Technologia wykonania materiału jest bardzo prosta i pracochłonna. Polega na przygotowaniu matrycy, wymieszaniu żywicy poliestrowej i wypełniacza, wlaniu powstałej mieszanki do matrycy i jej utwardzeniu.
Proces odlewania sztucznego marmuru można podzielić na następujące etapy:
- Formy są polerowane, nakładany jest materiał zapobiegający przyleganiu.
- Na formy nakładany jest żelkot. W tym celu stosuje się specjalną instalację lub opryskiwacz kubkowy.
- Żelkot utwardza się.
- Przygotowuje się mieszankę żywicy poliestrowej, wypełniacza, pigmentów i utwardzacza.
- Mieszankę wlewa się do foremek.
- Formy są wibrowane w celu usunięcia powietrza z mieszaniny.
- Materiał jest utwardzony.
- Produkty są wyjmowane z form.
- Prowadzona jest dalsza obróbka materiału (w niektórych przypadkach).
Na filmie produkcja odlewanego marmuru i zlewozmywaków:
Zrób to sam odlany marmur
Całkiem możliwe jest samodzielne wykonanie sztucznego marmuru. Wystarczy zakupić wszystkie składniki materiału, formy do nalewania i postępować zgodnie z instrukcjami.
Aby wykonać lany marmur, potrzebujesz:
- poliuretanowa forma odlewnicza;
- film;
- mikser;
- kutas.
W produkcji wypełniaczem jest CaMg(CO3)2, a utwardzaczem Butanox M-50. W domu zamiast tych substancji można użyć kamyków i cementu.
Materiały do produkcji sztucznego marmuru:
- piasek (rzeka) - 2 części;
- cement - 1 część;
- woda - 0,2 części;
- kamyki (jako wypełniacz) - 25% całkowitej objętości;
- pigment - 1% masy cementu;
- plastyfikator - 1% masy cementu;
- powłoka żelowa.
Kolejność produkcji marmuru lanego:
- Suchą i czystą formę smaruje się żelkotem i pozostawia do wyschnięcia.
- Wymieszaj piasek, kamyki i cement. Do mieszaniny dodaje się plastyfikator, pigment barwiący i wodę (80%), miesza się mikserem do uzyskania plastycznej masy (około 30 sekund). Następnie dodaj resztę wody i ponownie wymieszaj, aż będzie gładka.
- Mieszankę układa się w formie, nadmiar usuwa z brzegów, przykrywa folią i pozostawia do zestalenia na 10 godzin.
- Materiał wyjmuje się z formy i pozostawia na jakiś czas na świeżym powietrzu.
W ten bezpretensjonalny sposób można uzyskać materiał, który można wykorzystać w pierwotnej postaci lub poddać dalszej obróbce w celu nadania pożądanego kształtu.
Technologia samodzielnej produkcji sztucznego marmuru lanego jest pokazana na poniższym filmie:
Plusy i minusy, recenzje
Chociaż skład sztucznego marmuru zasadniczo różni się od jego naturalnego odpowiednika, ma te same właściwości techniczne. Co więcej, poziom wytrzymałości i odporności na zużycie sztucznie wytworzonego materiału jest wielokrotnie wyższy niż materiału naturalnego.
Główne zalety sztucznego marmuru:
- ma wysoki poziom wytrzymałości mechanicznej, nie boi się wstrząsów;
- różni się trwałością, ma długi okres eksploatacji;
- prawie nie przewodzi ciepła i elektryczności, ma wysoki poziom bezpieczeństwa przeciwpożarowego. Dlatego może być stosowany do dekoracji grzejników, kuchenek elektrycznych itp.;
- materiał nie nagrzewa się, nie rozwarstwia się, nie obawia się działania kwasów, zasad, rozpuszczalników, nie wchłania tłuszczu, nie pozostawia plam. Ze względu na tę praktyczność jest często stosowany do dekoracji kuchni i łazienek, wykańczania podłóg w budynkach mieszkalnych, przemysłowych i użyteczności publicznej;
- nie wydziela szkodliwych substancji, jest przyjazny dla środowiska;
- dzięki zewnętrznej powłoce żelkotowej prezentuje się estetycznie i może służyć do celów dekoracyjnych.
Łączy w sobie twardość kamienia naturalnego i łatwość obróbki. W przeciwieństwie do naturalnego marmuru, sztuczny materiał zapewnia większy komfort i jest zawsze ciepły w dotyku.
Wśród wad sztucznego kamienia wielu zauważa, że nie można go uznać za kompletny analog materiału naturalnego. W dotyku bardziej przypomina plastik, a warstwa wierzchnia wygląda jak poliuretan.
Ponadto powłoka żelowa często pęka z czasem. W efekcie materiał ulega odbarwieniu i zniszczeniu.
Średni koszt sztucznego marmuru
Proces produkcji marmuru zapewnia minimalne inwestycje i bardzo wysoką rentowność. Początkowo wydatki ponoszone są na zakup sprzętu, surowców, wynajem lokali i produkcję matryc. W przyszłości koszt produktów zależy głównie od kosztów surowców.
Koszt produkcji szacowany jest na około 5 USD za 1 m2. m., podczas gdy cena rynkowa sięga 30 dolarów za 1 mkw. m lub nawet wyżej.
Różne są uważane za tak piękne, mocne i trwałe jak produkty wykonane z prawdziwego kamienia naturalnego. W końcu jego produkcja była ulepszana w ciągu 30 lat i osiągała wysokie wyniki.
Sztuczny marmur to dobra alternatywa dla kamienia naturalnego, którego koszt nie jest dostępny dla wszystkich. Produkcja marmuru z betonu umożliwia uzyskanie produktu, który nie jest gorszy pod względem właściwości od materiału naturalnego, ale jednocześnie ma bardziej przystępną cenę. Organizacja produkcji nie wymaga od przedsiębiorcy dużych nakładów finansowych i specjalnej wiedzy.
Nasza wycena biznesu:
Inwestycje początkowe - od 50 000 rubli. i wyżej
Nasycenie rynku jest średnie.
Złożoność założenia firmy to 5/10.
Korzyści biznesowe
Produkcja sztucznego marmuru z betonu w domu ma wiele zalet:
- Niezmiennie wysoki popyt na produkty.
- Niski poziom konkurencji.
- Małe koszty na etapie otwarcia.
- Brak czynszu.
- Nie musisz zatrudniać pracowników, możesz to zrobić sam.
- Prosty proces technologiczny.
- Stosunek kosztu i ceny sprzedaży gotowego produktu.
- Wysoka rentowność - do 300%.
Każda osoba, która nie jest związana z budownictwem i może otworzyć przedsiębiorstwo, którego działalnością jest produkcja sztucznego marmuru z betonu.
Ale zanim zrobisz marmur z betonu własnymi rękami, warto szczegółowo rozważyć wszystkie aspekty takiej produkcji: etapy odkrycia, ryzyko, technologię produkcji, koszty finansowe.
Proces wytwarzania sztucznego kamienia
Wiele osób uważa, że bardzo trudno jest zrobić dobrą imitację naturalnego materiału.
Ale technologia produkcji sztucznego marmuru z betonu jest prosta i składa się z kilku etapów:
- Mieszanie składników według standardowej receptury przygotowania zaprawy betonowej.
- Dodawanie do mieszanki barwników i żywic poliestrowych, od których zależą podstawowe właściwości materiału.
- Wlewanie roztworu do przygotowanych foremek.
- Uszczelka stołu wibracyjnego.
Następnie musisz poczekać, aż mieszanina całkowicie się zestali, a następnie wyjąć gotowy kamień z foremek. Powstały produkt, podlegający normom i wymaganiom produkcji, będzie spełniał ustalone standardy i charakteryzował się wysokimi cechami jakościowymi.
Sprzęt do produkcji sztucznych materiałów
stół wibracyjny do produkcji
Zakup sprzętu do produkcji sztucznego marmuru nie jest trudny: organizacja warsztatu nie będzie wymagała dużych wydatków. Maszyny wykorzystywane w procesie produkcyjnym są tanie i łatwe w obsłudze.
Obrotowy mieszalnik do betonu
Technologia wytwarzania marmuru z betonu polega na wykorzystaniu następujących urządzeń:
- specjalne formy do produkcji sztucznego marmuru - od 1000 rubli. kawałek;
- stół wibracyjny - od 30 000 rubli;
- mikser, do mieszania roztworu (minimalna objętość 250 l) - od 25 000 rubli.
Minimalna ilość form potrzebnych do stworzenia asortymentu to 10 sztuk. Całkowita cena sprzętu do produkcji marmuru z betonu wynosi 65 000 rubli.
Niuanse produkcji sztucznego kamienia
Jeśli nie ma wystarczającej ilości pieniędzy, możesz odmówić zakupu betoniarki. Roztwór można mieszać ręcznie. Stół wibracyjny i formy to główne wyposażenie, bez którego nie da się otworzyć produkcji sztucznego kamienia. Na pierwszym etapie całą pracę można wykonać samodzielnie. Wraz ze wzrostem bazy klientów i wzrostem wolumenu wytwarzanych produktów konieczne będzie zatrudnienie jednego lub dwóch partnerów.
Zanim wykonasz marmurowy beton, musisz zdecydować o rodzaju wytwarzanego produktu. Najlepiej od razu kupić formy do produkcji płytek, obrzeży, kostki brukowej, tralek i innych rzeczy. Należy pamiętać, że im większy asortyment oferowany kupującemu, tym wyższa rentowność przedsiębiorstwa. Ponadto bardzo wygodnie jest kupić w jednym miejscu płytki lub kostkę brukową i krawężniki.
Przykłady gotowych produktów
Możesz spróbować samodzielnie wykonać ekskluzywne formy, ponieważ ich koszt jest znacznie wyższy niż w przypadku konwencjonalnych urządzeń: od 23 000 rubli. za 1 sztukę. Ale możesz przyjmować zamówienia na produkcję oryginalnych produktów i kupować formy dopiero po przedpłacie.
Nawiasem mówiąc, najlepszą opcją byłby zakup form wykonanych z poliuretanu. Ich zaletą jest wysoka jakość, przystępna cena oraz trwałość.
Surowcami do produkcji marmuru z betonu są następujące materiały: piasek, cement M400, barwnik (pigment), żywice poliestrowe (plastyfikator).
Obliczanie zysku z produkcji tworzywa sztucznego
Miesięcznie można wyprodukować około 1000 m2 sztucznego marmuru, co kosztuje na rynku od 370 rubli. za m2 i więcej. Cena uzależniona jest od grubości produktu, jego wyglądu oraz wykonania. Oznacza to, że minimalny dochód wyniesie około 370 000 rubli. Koszty wyniosą około 100 000 rubli. na miesiąc. Przedsiębiorca może zarobić ponad 250 000 rubli. na miesiąc. Wszystkie inwestycje zwrócą się w ciągu 30-50 dni od rozpoczęcia produkcji.
Zwrot i rentowność przedsiębiorstwa zależy od kompetentnej organizacji marketingu gotowych produktów. Możesz sprzedawać marmur za pośrednictwem wyspecjalizowanych punktów sprzedaży detalicznej lub sklepów internetowych. Reklama w mediach pozwoli Ci pracować na zamówienie. Jednak głównym celem przyciągnięcia nabywców i poszerzenia bazy klientów jest wysoka jakość oferowanych produktów i atrakcyjny koszt.
Marmur do dekoracji pomieszczeń i ścian zewnętrznych budynków zaczęto stosować już w starożytności. Ale ten materiał nie jest dostępny dla wszystkich. Cena naturalnego marmuru zaczyna się od 20 tysięcy rubli za metr kwadratowy. Jako bardziej ekonomiczny zamiennik jest to sztuczny marmur - wykonany z betonu i innych materiałów. Sztuczny kamień jest 4 razy tańszy niż naturalny, jeśli kupujesz go w sklepach. Ale z pewnymi umiejętnościami możesz to zrobić sam.
Charakterystyka sztucznego kamienia
Sztuczny kamień nazywany jest nie tylko marmurem z betonu, ale także granitem ceramicznym. Technologia produkcji tych materiałów jest niemal identyczna. Ale są używane inaczej.
Gres porcelanowy uważany jest za twardszy i bardziej odporny na uszkodzenia mechaniczne, dlatego częściej niż marmur stosuje się go do powłok w miejscach o dużym natężeniu ruchu pieszych: posadzki w centrach handlowych, supermarketach, metrze, w centrach komunikacyjnych. W pomieszczeniach mieszkalnych ściany i podłogi przedpokojów i kuchni licuje się gresem porcelanowym.
Marmur jest mniej trwały, ale dzięki barwnikom ma piękny wzór. Jej zakres to blaty i lady barowe, balustrady ogrodzeń i schodów, elementy dekoracyjne, detale hydrauliki, parapety i sztuczne kolumny.
Marmur betonowy na zamówienie może mieć niemal dowolny kształt, kolor i wzór. Parametry te zależą wyłącznie od wyobraźni i wypłacalności kupującego.
Naturalny marmur pod wieloma względami przegrywa ze swoim sztucznym odpowiednikiem. Blat wykonany z naturalnego materiału będzie ważył 3-4 razy więcej niż podobny kształtem i rozmiarem - wykonany z materiału syntetycznego.
Paleta kolorów kamienia naturalnego jest ograniczona, natomiast sztuczny marmur można pomalować na dowolny odcień, a nawet sprawić, by błyszczał.
Techniki wytwarzania
Na skalę przemysłową stosuje się kilka technologii produkcji marmuru. Skład mieszanin zależy od wybranej metody. Najbardziej popularne są metody odlewnicze i gipsowe oraz produkcja marmuru z betonu. Technologie wytwarzania sztucznego marmuru w obu przypadkach mają ze sobą wiele wspólnego.
metoda wtrysku
Marmur odlewniczy wytwarzany jest z piasku kwarcowego lub odpadów produkcyjnych kamienia naturalnego - wiórów marmurowych. Integralność mieszanki nadają żywice poliestrowe, a za pomocą pigmentu można nadać produktowi dowolny odcień. Odlewany marmur ma następujące cechy:

Oprócz głównych składników mieszanki do produkcji marmuru lanego stosuje się szereg narzędzi, preparatów i specjalistycznego sprzętu. Obejmują one:
- formy do nalewania;
- kompozycja antyadhezyjna do obróbki pleśni;
- stół wibracyjny;
- sprzęt do polerowania gotowej konstrukcji marmurowej;
- powłoka żelowa.
Formy są traktowane mieszankami antyadhezyjnymi po wykopaniu zamrożonego kamienia.
W skład takich preparatów wchodzi parafina lub silikon rozpuszczony w nafcie, benzynie lakowej lub benzynie.
Należy wybrać kompozycję, skupiając się na pożądanym wyglądzie kamienia.
Mieszanka silikonowa nadaje się do matowego wykończenia, podczas gdy związek uwalniający wosk nadaje gotowemu produktowi błyszczące wykończenie, powierzchnia staje się nieco tłusta.
Procedura wytwarzania marmuru lanego jest następująca:

Żelkot to żywica polimerowa, której za pomocą barwników nadaje się określony odcień. On pełni kilka funkcji: zabezpiecza powierzchnię przed uszkodzeniami, „zamyka” pory produktu i barwi go. Żelkot nakłada się pędzlem lub natryskiem w kilku warstwach. Po wyschnięciu gładzi (w przypadku żelkotu jest to około 2-3 godziny) produkt jest gotowy do użycia.
Marmur gipsowy
Alternatywą dla kamienia z wiórów naturalnych jest marmur gipsowy. Produkcja według tej receptury jest znacznie tańsza. Mieszanka podstawowa zawiera następujące składniki:

Przede wszystkim miesza się gips, klej i wodę, następnie dodaje się żywicę i wszystko miesza się mikserem. Następnie dodany składniki barwiące:
- czarny kolor daje farbę anilinową;
- odcień kawy można uzyskać stosując humilaks pomarańczowy (200 g) i 1 litr alkoholu technicznego na 50 kg gipsu;
- do śnieżnobiałego marmuru stosuje się biały humilaks.
Mieszaninę wlewa się do formy i suszy przez 10 godzin w temperaturze pokojowej. Po całkowitym utwardzeniu, sztuczny marmur „gipsowy” jest wyjmowany, traktowany krzemianem potasu, suszony i polerowany filcem.
Marmur gipsowy to najlżejszy rodzaj sztucznego kamienia, ale także jeden z najbardziej kruchych. Na jego podstawie zwykle wykonuje się elementy dekoracyjne, na których nie odmawia znaczny ładunek.
Oparte na betonie
W celu wyprodukowania pojedynczego produktu nie jest konieczne kontaktowanie się z producentami zewnętrznymi. Jeśli istnieje kilka dość przystępnych składników, każdy może stworzyć sztuczny kamień. Możesz zrobić marmur z betonu własnymi rękami. Oprócz cementu marmur zawiera piasek, plastyfikator i wodę. To znacznie obniża koszt sztucznego kamienia w porównaniu do metody odlewania. Takie proste komponenty mają również pewne wymagania.
Do produkcji marmuru z betonu, następujące materiały i sprzęt:

Produkcja rozpoczyna się od starannego przesiewania piasku. Pomoże to pozbyć się nadmiaru zanieczyszczeń. Jako pierwszy mieszają podstawowe składniki - cement i piasek. Proporcje tych składników w kompozycji mogą się różnić w zależności od zakresu produktu końcowego.
- W przypadku części, które w przyszłości będą narażone na duże uszkodzenia mechaniczne - krawężniki, okładziny zewnętrzne, płyty chodnikowe - wymagane jest wymieszanie cementu i piasku w stosunku 1:3.
- Jeśli planowane jest wykonanie blatu, elementu sufitu lub schodów, parapetu ze sztucznego marmuru, to proporcje powinny wynosić 1:2.
- W przypadku elementów dekoracyjnych cement i piasek miesza się w stosunku 1: 1.
Następnie mieszaninę rozcieńcza się wodą. Objętość wody oblicza się na podstawie objętości suchej mieszanki: zalecana proporcja to 1 część wody na 2 części mieszanki. Najpierw wlej około trzech czwartych wody i wymieszaj. Następnie do mieszanki dodaje się plastyfikator w ilości 1-2% wagowo cementu i miesza.
Aby uzyskać jak najlepsze rozprowadzenie plastyfikatora, mieszaninę odstawia się na 10-15 minut, a następnie wlewa się pozostałą wodę i ponownie miesza.
Ostatnim składnikiem jest barwnik. W celu uzyskania pożądanego odcienia można dodać jeden lub więcej pigmentów. Generalnie zaleca się stosowanie pigmentu w ilości 1% masy cementu (a nie całej mieszanki), ale skuteczność barwników nie jest taka sama, więc ten stosunek może nie dać pożądanego rezultatu. Najpopularniejsze barwniki i ich zalecane dawki są następujące:
- tlenek tytanu nadaje mieszaninie biały kolor (lub białe plamy i smugi), zalecane dozowanie to od 2 do 4%;
- minium - czerwono-pomarańczowy pigment - 5%;
- tlenek chromu zabarwia kompozycję na zielono, dodaje się w ilości 3-5% wag. cementu;
- zalecana ilość dla ochry to 5%, w rezultacie marmur malowany jest w odcieniach od jasnożółtego do brązowego.
Istnieją również specjalne pigmenty do betonu. Przy ustalaniu ich dawki postępuj zgodnie z instrukcjami producenta.
Po dodaniu barwnika kompozycji nie należy dokładnie mieszać, ponieważ marmur charakteryzuje się nierównomiernym rozkładem koloru.
Gotową mieszankę wlewa się w częściach do formy potraktowanej preparatami antyadhezyjnymi, zwracając szczególną uwagę na wgłębienia. Jeśli planowany produkt jest duży, część kompozycji wlewa się do formy, układa siatkę lub drut, a dopiero potem dodaje resztę płynnej bazy. Zwykle blaty i masywne płyty, obramowania i wolumetryczne elementy dekoracyjne wymagają wzmocnienia. Po wylaniu formę pokrywa się folią i pozostawia do całkowitego stwardnienia.
Sztuczny marmur twardnieje długo, zajmie to co najmniej 7-12 dni. Gotowy kamień wyjmuje się z formy, w razie potrzeby poleruje i pokrywa ostateczną ochronną warstwą żywicy (żelkot).
Niuanse działania
Przy odpowiednim wykończeniu sztucznego marmuru dowolnego pochodzenia, produkty z niego wykonane przetrwają lata. Jednym ze sposobów na zwiększenie trwałości kamienia jest bejcowanie powierzchni i pokrywanie lakierem wodno-akrylowym.
Dotyczy to zwłaszcza kamienia używanego do dekoracji zewnętrznych, ponieważ światło słoneczne nie ma wpływu na lakier wodno-akrylowy.
Dzięki temu marmurowy element dekoracyjny nie zmieni koloru i nie będzie pokryty nieprzyjemnymi żółtymi plamami przez 10-15 lat.
Podczas montażu produktu należy unikać nadmiernego dokręcania elementów złącznych. Płyta marmurowa ułożona pod kątem lub z silnym naciskiem na narożniki może nie wytrzymać obciążenia i pęknąć. W obliczu pomieszczeń o dużej wilgotności konieczne jest monitorowanie stanu kanalizacji, aby zapobiec występowaniu przecieków i wnikania kamienia podczas kopania.
Upuszczenie ciężkich przedmiotów o ostrych narożnikach może uszkodzić marmur. Nie kroj żywności bezpośrednio na blacie, używaj desek do krojenia.
Powierzchnię należy czyścić wyłącznie płynnymi środkami czyszczącymi. Kompozycje z materiałami ściernymi niszczą powłokę ochronną sztucznego kamienia, powodują mikrorysy, w których gromadzą się resztki jedzenia, kurz i inne zanieczyszczenia. Twarde szczotki i metalowe siatki należy odrzucić na rzecz miękkich tkanin.
Współczesne analogi tradycyjnych materiałów naturalnych są dziś szeroko stosowane. Zalety zastosowania sztucznego kamienia w aranżacji wnętrz są niezliczone, wystarczy wspomnieć wyjątkową wytrzymałość materiału i stosunkowo niski koszt. Możliwość samodzielnego wykonania, łatwość montażu i obróbki gotowego produktu, a także zastosowanie innowacyjnych technologii w produkcji marmuru – wszystkie te aspekty zostały szczegółowo opisane w informacji tego artykułu.
Zalety sztucznego marmuru
Zastosowanie kamienia naturalnego w projektowaniu budynków mieszkalnych i użyteczności publicznej ma ponad sto lat pozytywnego użytkowania. Takie okładziny zawsze były prerogatywą wyższych warstw społeczeństwa, ale wraz z pojawieniem się sztucznych analogów taki luksus stał się bardziej przystępny.
Zalety zastosowania sztucznego kamienia we wnętrzu:
- Doskonała wytrzymałość i właściwości użytkowe.
- Wysoki stopień dekoracyjności wyrobów ze sztucznego kamienia.
- Stosunkowo przystępna cena.
- Możliwość samodzielnej produkcji.
- Łatwa instalacja.
- Materiał jest niepalny i chemicznie obojętny.
- Stosunkowo lekka waga.
- Trwałość powierzchni.
- Nie ma potrzeby specjalnej opieki.
- Trwałość koloru jest utrzymywana w bezpośrednim świetle słonecznym.
- Materiał charakteryzuje się niską higroskopijnością i może być stosowany w wilgotnym środowisku.
Zlewozmywaki ze sztucznego marmuru wyróżniają się doskonałym designem i bezproblemową obsługą. Samodzielna produkcja sztucznego marmuru znacznie obniży koszty i pozwoli uzyskać oryginalne konfiguracje i kolory gotowych produktów.
Na rynku budowlanym pojawiła się alternatywa dla cementu, która z punktu widzenia ekologicznej produkcji nie jest bezpieczna dla atmosfery. Na świecie produkuje się rocznie około 2 miliardów ton cementu, a każda tona uwalnia do atmosfery 0,4 tony dwutlenku węgla. Inżynierowie długo pracowali nad tym problemem, aż wynaleźli płynny granit - nowe słowo w technologii wytwarzania materiałów wykończeniowych. Posiada wiele zalet w stosunku do innych materiałów wykończeniowych: odporność ogniowa, uniwersalność, jakość, bezpieczeństwo, trwałość.
Definicja płynnego granitu
Granit płynny to sztuczny płynny kamień.
Jego zalety wynikają z faktu, że w przeciwieństwie do płynnego granitu zawiera oczyszczone wióry marmurowe (80%) i żywicę poliestrową (20%). Twardnieje po dodaniu do niego przyspieszacza i utwardzacza. W procesie reakcji chemicznych uwalniane są wszystkie szkodliwe substancje, a w stanie gotowym produkt będzie już przyjazny dla środowiska.
Granit płynny może być stosowany w dowolnych pomieszczeniach: mieszkaniach, biurach, szkołach, kuchniach letnich w kraju i tak dalej. Powierzchnie do natrysku to: drewno, kamień, metal, porcelana, włókno szklane, ceramika, płyta wiórowa i płyta pilśniowa. Produkty z płynnego granitu przypominają produkty z kamienia naturalnego, ponieważ zawierają odłamki marmuru i nie ma już konieczności używania dużych kawałków kamienia. Gama kolorystyczna materiału jest zróżnicowana dzięki setkom kolorowych barwników, które umożliwiają dopasowanie płynnego granitu do każdego pomieszczenia.
Osobliwości
- Kolor gleby nie wpływa na kolor płynnego kamienia;
- Przyjemny w dotyku;
- Materiał jest nietoksyczny, bezwonny;
- Odporność na wilgoć uzyskuje się poprzez dodanie utwardzacza;
- Nie traci swojego wyglądu z biegiem czasu, jest trwały - żywotność produktów wynosi ponad 25 lat;
- Łatwo usuwa zabrudzenia z powierzchni;
- Wraz ze zmianami temperatury wyrób z płynnego kamienia nie traci swojego kształtu i właściwości.
Komponenty do płynnego kamienia:
- Plastelina;
- włókno szklane;
- Żywica chemiczna;
- Podsadzkarz;
- utwardzacz;
- Aceton;
- zwapnienie;
- Powłoka żelowa;
- gorący klej;
- Płyta wiórowa, płyta pilśniowa.
Metody produkcji
- Metoda odlewania - gotową mieszankę wlewa się do specjalnej formy, aż do całkowitego wyschnięcia. Następnie gotowy produkt jest usuwany i przetwarzany.
- Metoda natryskowa - płynny kamień nakłada się na powierzchnię kilkumilimetrową warstwą za pomocą pistoletu natryskowego.
Metoda bezpośredniego natrysku
Metoda natrysku bezpośredniego - na przedmiot nakładany jest specjalny podkład, który pozostawia do wyschnięcia. Za pomocą spryskiwacza nakłada się warstwę płynnego kamienia. Szlifowanie i polerowanie odbywa się po wyschnięciu.
metoda zapylania wstecznego
Metoda zapylania odwrotnego - stosowana, jeśli obrabiany przedmiot nie jest częścią mebla. Obrabiany przedmiot jest umieszczany na powierzchni formującej (płyta wiórowa, tafla szkła, stół) i otaczany wzdłuż konturu. Wzdłuż konturu montowana jest strona wykonana z płyty wiórowej lub tworzywa sztucznego. Nakładana jest warstwa antyadhezyjna. Następnie na powierzchnię natryskiwany jest płynny kamień. Gdy częściowo stwardnieje, podłoże jest spryskiwane, aby warstwa kamienia nie prześwitywała. Okazuje się, że forma, w której wylewa się żywicę poliestrową. Produkt jest usuwany z formy po całkowitym stwardnieniu.
Zobacz zdjęcia tapety w stylu prowansalskim do kuchni.
Technologia produkcji
Pomieszczenie, w którym odbywa się produkcja płynnego granitu powinno składać się z dwóch pomieszczeń. Pierwsze pomieszczenie jest niezbędne do bezpośredniej produkcji, a drugie do polerowania powstałego produktu. Temperatura w pomieszczeniach powinna być utrzymywana na poziomie 20-24 stopni. Musi być wentylacja.
Przygotowanie powierzchni rozpoczyna się od usunięcia z niej brudu i kurzu. Przed malowaniem powierzchnia jest myta wodą i dokładnie suszona. Wszelkie uszkodzenia, rysy, pęknięcia muszą być naprawione.
Etapy produkcji:
- Przygotowanie mieszanki poprzez wymieszanie wiertłem transparentnego żelkotu (żywicy polimerowej) z granulkami w proporcji 2:1. Utwardzacz dodaje się przed natryskiem.
- Powstałą mieszaninę nakłada się na produkt. Istnieją dwa sposoby aplikacji: natrysk bezpośredni i natrysk odwrotny.
- Powierzchnia gotowego produktu jest szlifowana i polerowana.
Poznaj główne elementy niezwykłego projektu kuchni.
Obszar zastosowań
Producenci
- GRANITO-FARFALLA to firma zajmująca się produkcją blatów i parapetów z płynnego granitu. Jakość produktów zapewniają materiały i sprzęt znanych światowych producentów. Firma nieustannie dąży do ulepszania technologii, podnoszenia wydajności technicznej.
- GRANITE to firma produkująca wypełniacz dekoracyjny GraniStone do produkcji płynnego kamienia oraz gotową do użycia kompozycję płynną AquaGranit, wykonaną z poliestrowej żywicy izoftalowej i akrylu.
- "Płynny Granit" to firma produkująca blaty, parapety ze sztucznego kamienia, panele ścienne oraz okładziny do drzwi granitowych.
Przeczytaj o stylu Fusion we wnętrzu kuchni.
Produkty z płynnego kamienia mają piękny atrakcyjny wygląd, są zróżnicowane pod względem kolorystycznym i według. Doskonale komponują się z dowolnymi materiałami wykończeniowymi. Jakość, bezpieczeństwo i trwałość dopełniają listę zalet tego materiału.
Produkcja produktów z płynnego granitu: wideo
Wyniki
Dbając o płynny granit, jak również należy odpowiedzialnie podchodzić do wyboru środków czyszczących, w przeciwnym razie szybko się zużyje i odkształci. Kolejną wadą stosowania kamienia jest niski stopień przyczepności żywicy do powierzchni, przez co mogą pojawiać się pęcherze i łuszczenie. Aby temu zapobiec, nie musisz obrabiać powierzchni. Niekorzystnie wysoka cena kamienia jest niekorzystna dla kupujących. Producenci przeceniają to, odnosząc się do czasu produkcji, szkodliwych warunków pracy i kosztów pracy.