Konserwacja urządzeń chłodniczych. Ogólne wymagania i zadania eksploatacji agregatów chłodniczych Planowa konserwacja maszyn chłodniczych
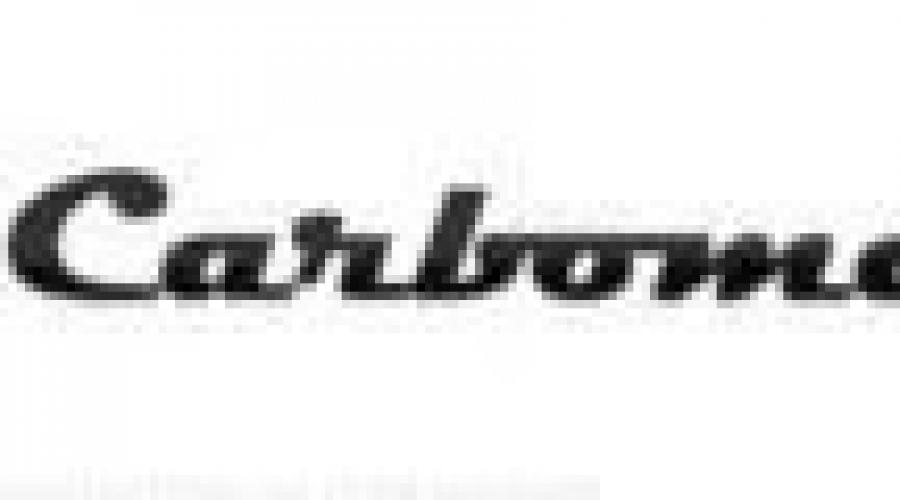
Urządzenia chłodnicze oddawane do eksploatacji w zakładach gastronomiczno-handlowych są zazwyczaj serwisowane, naprawiane i regulowane przez pracowników zakładów remontowo-montażowych (warsztatów) na podstawie umowy.
W przedsiębiorstwach obsługujących urządzenia chłodnicze, dla każdego jego rodzaju lub grupy, przypisywany jest operacyjny sznurowany i numerowany dziennik, w którym składa się akt o uruchomieniu urządzenia. Podczas eksploatacji sprzętu mechanik przedsiębiorstwa lub zakładu naprawczo-montażowego zapisuje w dzienniku informacje o wszystkich pracach przeprowadzonych w celu konserwacji sprzętu, a także o instrukcjach dla personelu konserwacyjnego dotyczących zasad działania . Wszystkie wpisy mechanika w dzienniku są sprawdzane i podpisywane przez administrację przedsiębiorstwa. Dziennik prowadzi dyrektor przedsiębiorstwa lub jego zastępca.
Jeżeli pomiędzy zakładem naprawczo-montażowym a przedsiębiorstwem istnieje umowa na konserwację urządzeń chłodniczych, jest ona przypisywana określonemu zespołowi mechaników. Mechanik zgodnie z planem wykonuje prace konserwacyjne na sprzęcie. Częstotliwość tych prac zależy od ogólnego poziomu konserwacji i eksploatacji urządzeń chłodniczych. Mechanik wykonuje również prewencyjne prace konserwacyjne. Zakres tych prac obejmuje inspekcję instalacji chłodniczej w celu identyfikacji wycieków freonu i ich usunięcia, czyszczenie urządzeń z kurzu i brudu, napinanie pasów transmisyjnych, sprawdzanie uziemienia (lub zerowania), monitorowanie reżimu temperaturowego urządzeń chłodniczych, regulację urządzeń automatyki itp. .
Mechanik instruuje personel na temat urządzenia, zasady działania sprzętu i zasad obsługi. W przypadku awarii lub wyłączenia agregatu chłodniczego z przyczyn niemożliwych do usunięcia przez personel serwisowy, mechanik dyżuruje.
Eksploatowane urządzenia chłodnicze muszą być utrzymywane w należytym stanie sanitarnym. W tym celu sprzęt chłodniczy należy myć przynajmniej raz w tygodniu ciepłą wodą z mydłem, następnie spłukiwać ciepłą czystą wodą, wytrzeć do sucha szmatką i pozostawić otwarty na noc do wietrzenia. Zewnętrzne chromowane i niklowane części urządzeń chłodniczych należy codziennie przecierać szmatkami zwilżonymi wazelinowym olejem technicznym.
Zachowanie jakości produktów podczas przechowywania chłodniczego w dużej mierze zależy od stanu sanitarnego komór. Dlatego konieczne jest okresowe przeprowadzanie kontroli mikrobiologicznej komór w celu szybkiego wykrycia stopnia zanieczyszczenia pleśniami. Komory zaatakowane przez pleśń należy dezynfekować zgodnie z „Przepisami Sanitarnymi dla Przemysłu Chłodniczego”.
Podłogi w celach i korytarzach, klatki schodowe i windy do podnoszenia produktów spożywczych z komór chłodniczych do obiektów produkcyjnych są czyszczone, gdy się zabrudzą, ale przynajmniej raz na zmianę. Zatłuszczone i śliskie podłogi i drzwi w chłodniach o dodatniej temperaturze, w korytarzach i klatkach schodowych myje się gorącym roztworem mydła lub ługu i wyciera do sucha.
Do czyszczenia urządzeń chłodniczych używa się specjalnego sprzętu i przechowuje go oddzielnie od sprzętu używanego do czyszczenia innych pomieszczeń i sprzętu.
Aby wyeliminować zapachy w lodówkach, są one okresowo wentylowane lub poddawane działaniu ozonu.
Okres przechowywania produktów ustalany jest zgodnie z zatwierdzonymi normami.
Odpowiedzialność za przestrzeganie przepisów technicznych i sanitarnych dotyczących przechowywania produktów spożywczych spoczywa na kierowniku przedsiębiorstwa. Kontrolę przestrzegania przepisów sanitarnych dotyczących przechowywania artykułów spożywczych sprawują organy Państwowego Dozoru Sanitarnego oraz resortowe służby sanitarne.
Aby zachować wysoką jakość produktów spożywczych podczas przechowywania w komercyjnych urządzeniach chłodniczych (komory składane, szafy, lady i gabloty), konieczne jest ścisłe przestrzeganie reżimu temperaturowego przechowywania. Urządzenia chłodnicze można ładować produktami dopiero po osiągnięciu wymaganej temperatury przechowywania. Lady, szafki i gabloty nie są przeznaczone do chłodzenia żywności, dlatego należy je ładować wyłącznie schłodzoną żywnością. Używanie komercyjnych urządzeń chłodniczych do schładzania gorącej żywności lub napojów jest zabronione. Załadunek urządzeń chłodniczych i umieszczanie w nich produktów musi odbywać się zgodnie z wymaganiami technicznymi. Przy prawidłowym załadowaniu produkty są rozmieszczone równomiernie na całej powierzchni półek tak, aby nie dotykały ścian komory chłodniczej, a między nimi był przepływ powietrza. W przypadku nieprawidłowego obciążenia lub przeładowania sprzętu produktami pogarszają się warunki cyrkulacji powietrza, co prowadzi do nierównomiernego chłodzenia i nagrzewania się warstw wewnętrznych. Nie przykrywać drucianych stojaków urządzeń chłodniczych papierem, tkaniną lub innymi materiałami, które uniemożliwiają cyrkulację powietrza chłodzącego. Nie wolno układać produktów blisko parownika agregatu chłodniczego, minimalna odległość to 40 mm.
Utrzymanie wymaganej temperatury w komorze chłodniczej uzależnione jest od warunków pracy parownika agregatu chłodniczego. Podczas pracy agregatu chłodniczego na ściankach parownika zamarza warstwa śniegu, której grubość ma wpływ zarówno na pracę agregatu chłodniczego, jak i całego wyposażenia. Gdy zamarznie warstwa śniegu o grubości 5-7 mm, kanały między lamelami parownika są zatkane, proces wymiany ciepła między powietrzem a czynnikiem chłodniczym gwałtownie się pogarsza, co prowadzi do wzrostu temperatury w chłodzonej komorze, wzrostu w poborze mocy i zwiększeniu współczynnika czasu pracy. Dlatego konieczne jest terminowe rozmrożenie płaszcza śnieżnego z parownika. Rozmrażanie płaszcza śnieżnego należy przeprowadzać ściśle według instrukcji. Jeśli sprzęt nie jest wyposażony w specjalne automatyczne urządzenia do rozmrażania płaszcza śnieżnego, to podczas rozmrażania wszystkie produkty są usuwane z chłodzonej komory, maszyna chłodnicza jest wyłączana, a drzwi otwierane. Stopiona woda jest zbierana na tackach i usuwana z urządzenia. Jest wycierany do sucha, a następnie włączana jest lodówka. Nie jest możliwe usunięcie powłoki śnieżnej z parownika agregatu chłodniczego środkami mechanicznymi, ponieważ istnieje możliwość uszkodzenia ścianki parownika i zerwania szczelności układu.
Jeśli sprzęt chłodniczy nie jest załadowany produktami, należy go wyłączyć. Na koniec dnia roboczego wszystkie produkty z gablot należy przenieść do komór, szafek lub lad, a lodówki gablot należy wyłączyć.
Personelowi konserwacyjnemu nie zaleca się niepotrzebnego otwierania komór chłodniczych. Zwiększa to temperaturę i wilgotność powietrza w komorze. Oświetlenie w komorach chłodniczych powinno być włączone tylko podczas załadunku lub rozładunku produktów.
Prawidłowe działanie maszyn i urządzeń chłodniczych można ocenić po sposobie ich działania.
Normalna praca urządzeń chłodniczych. Normalny tryb pracy urządzeń chłodniczych jest uważany za tryb optymalny, który zapewnia utrzymanie wymaganej temperatury w komorach chłodniczych przy minimalnych kosztach operacyjnych. Główne koszty operacyjne to prąd i woda chłodząca.
Następujące czynniki wpływają na zużycie energii.
1. Zgodność z zasadami eksploatacji urządzeń chłodniczych. Prawidłowy załadunek i rozmieszczenie produktów w komorach, szafach, gablotach i ladach, skrócenie czasu zwiedzania komór, otwieranie drzwi i ścian przesuwnych, terminowe rozmrażanie płaszcza śnieżnego z parownika agregatu chłodniczego i inne środki zapewniające działanie chłodni maszyna z minimalnym współczynnikiem czasu pracy.
2. Różnica między temperaturą skraplania i wrzenia czynnika chłodniczego. Im mniejsza różnica, tym mniejsze zużycie energii.
Przybliżone temperatury wrzenia i skraplania ciekłego czynnika chłodniczego to:
a) temperatura skraplania t do w skraplaczach chłodzonych powietrzem wynosi t do =t powietrze2 + (10 ÷ 12ºС), gdzie tpowietrze2 jest temperaturą powietrza opuszczającego skraplacz. Ogrzewanie powietrza w skraplaczu wynosi 2-4°C;
b) w skraplaczach chłodzonych wodą typu zamkniętego, temperatura skraplania t c =t m wody + (8 ÷ 10ºС), gdzie t m wody jest średnią temperaturą wody chłodzącej. Ogrzewanie wody w skraplaczu wynosi 4-6°C;
c) w wyparkach żebrowych freonowych temperatura wrzenia czynnika chłodniczego jest o 12-15°C niższa niż temperatura komory chłodzonej. W witrynach chłodniczych i szafach domowych różnica temperatur na parowniku może osiągnąć 19-21°C;
d) w wyparkach amoniakalnych z bezpośrednim chłodzeniem temperatura wrzenia czynnika chłodniczego jest o 8-12°C niższa od temperatury powietrza w komorach;
e) w wyparkach freonowych i amoniakalnych do chłodzenia pośredniego nośnika ciepła temperatura wrzenia czynnika chłodniczego jest o 4-6°C niższa niż średnia temperatura nośnika ciepła. Płyn chłodzący w parowniku jest chłodzony o 2-4ºС;
f) średnia temperatura chłodziwa w akumulatorach komorowych jest o 8-10°C niższa od temperatury powietrza w komorach.
3. Nieprawidłowe ustawienie przełącznika niskiego ciśnienia automatycznych chillerów freonowych, gdy ustawiona jest mała martwa strefa. W tym przypadku obserwuje się krótkocyklową pracę maszyny i dużą częstotliwość cykli. Normalna liczba cykli to 5-6 na godzinę.
4. Przepełnienie parownika agregatu chłodniczego ciekłym czynnikiem chłodniczym i uruchomienie sprężarki na mokro. Może to być spowodowane nieprawidłową regulacją termostatycznego zaworu rozprężnego, aw efekcie - spadkiem wydajności sprężarki, wzrostem ciśnienia parownika, wzrostem współczynnika czasu pracy sprężarki oraz zwiększonym zużyciem energii.
5. Awarie sprężarki, awarie zaworów powodujące pogorszenie wydajności, poluzowanie i ślizganie się napędu pasowego, zatkany osadnik zanieczyszczeń itp.
Koszty eksploatacyjne wody chłodzącej w dużych chillerach sięgają 50%, aw małych chillerach, gdzie jest używana tylko do chłodzenia skraplaczy, 25-35%. Spadek przepływu wody chłodzącej do skraplacza związany jest ze wzrostem temperatury skraplania. Wzrost temperatury kondensacji o 1ºС prowadzi do spadku wydajności chłodniczej maszyny o 1-1,2% i wzrostu zużycia energii elektrycznej. Wraz ze wzrostem dostaw wody chłodzącej spada zużycie energii elektrycznej, ale wzrasta zużycie wody chłodzącej. Optymalny przepływ wody chłodzącej należy określić biorąc pod uwagę warunki eksploatacji oraz taryfy za wodę i energię elektryczną. Aby zaoszczędzić wodę chłodzącą, należy zwrócić uwagę na działanie zaworów sterujących wodą, które po zatrzymaniu maszyny powinny odcinać dopływ wody do skraplacza, dochładzacza i sprężarki.
Wizualnymi oznakami normalnej pracy chillera są: równomierne rozłożenie warstwy szronu na powierzchni parownika, brak szronu na rurze ssawnej sprężarki (z wyjątkiem urządzeń niskotemperaturowych, gdy rura ssawna do zaworu ssawnego sprężarki jest zakryta z warstwą szronu), ciepła rura cieczowa, sprężarka i silnik elektryczny pracują cicho, bez wibracji i obcych hałasów, brak iskier i miejscowego nagrzewania się urządzeń elektrycznych, współczynnik czasu pracy odpowiada zalecanym wartościom.
W przypadku różnych urządzeń i maszyn chłodniczych instrukcja obsługi może zalecać charakterystyczne oznaki normalnej pracy.
Rzeczywisty tryb pracy urządzenia zależy od zmierzonych ciśnień i temperatur. Uznaje się to za nienormalne, jeśli rzeczywista wydajność chłodzenia jest mniejsza, a zużycie energii większe niż optymalne. W takim przypadku należy ponownie skonfigurować sprzęt do pracy w trybie normalnym.
Możliwe usterki w działaniu urządzeń chłodniczych. Podczas pracy maszyn i urządzeń chłodniczych pogarszają się ich właściwości. Z powodu zużycia spada wydajność sprężarki, pojawiają się hałasy i wibracje, których nie ma w nowej maszynie itp. Zanieczyszczenia i korozja powierzchni wymiany ciepła powodują wzrost ich odporności termicznej, spadek właściwości wytrzymałościowych.
Zużycie mechaniczne i fizyczne oraz chemiczne jest przyczyną nieprawidłowego działania urządzeń chłodniczych. Wśród wielu naruszeń najczęstsze są następujące: awaria rozruchowego i ochronnego sprzętu elektrycznego, ciągła praca sprężarki automatu chłodniczego, wymagana temperatura w komorze chłodniczej nie jest osiągnięta w przypadku braku płaszcza śnieżnego na parownika, występuje stały przepływ wody chłodzącej do skraplacza (VRV nie zamyka się), gdy sprężarka jest zatrzymana, obce hałasy w sprężarce itp.
Organizacja naprawy urządzeń chłodniczych. Aby wydłużyć żywotność urządzeń chłodniczych o wysokich parametrach technicznych, okresowo poddawany jest planowej konserwacji zapobiegawczej (PPR). System PPR ma na celu zapobieganie naprawom awaryjnym i wydłużenie czasu realizacji. Obejmuje to również prace związane z utrzymaniem remontowym, które polega na monitorowaniu stanu sprzętu i przestrzegania zasad jego eksploatacji, a także wykonywaniu szeregu prac zapewniających długoletnią eksploatację maszyn i aparatury.
Planowane naprawy dzielą się na trzy rodzaje: bieżące, średnie i kapitałowe. Każdy rodzaj naprawy obejmuje operacje, które zapewniają bezawaryjną pracę sprzętu do czasu kolejnej zaplanowanej naprawy. Naprawy bieżące i średnie wykonujemy bez demontażu sprzętu. Remont wykonywany jest w zakładzie naprawczo-montażowym, dla którego sprzęt jest demontowany i wysyłany do zakładu.
Przy wykonywaniu prac naprawczych należy bezwzględnie przestrzegać przepisów bezpieczeństwa dotyczących agregatów amoniakalnych i freonowych, zasad eksploatacji technicznej instalacji elektrycznych oraz wymagań innych materiałów instruktażowych.
Podstawy projektowania instalacji wentylacyjnych i klimatyzacyjnych. Nowoczesne podejście do projektowania. Uruchomienie i serwis systemów wentylacji i klimatyzacji
Kurs specjalny z programu o tematyce chłodniczej systemów wentylacyjnych i klimatyzacyjnych:
Temat 1. Podstawowe parametry powietrza. Analiza procesów zmiany stanu powietrza. Temperatura powietrza w termometrze suchym i mokrym. Temperatura punktu rosy. Psychometryczna różnica temperatur. Wilgotność bezwzględna i względna. Zawartość wilgoci. Ciepło właściwe i entalpia. Gęstość suchego i wilgotnego powietrza. Ciśnienie cząstkowe pary wodnej. Procesy ogrzewania, nawilżania, chłodzenia i osuszania. Procesy mieszania powietrza zewnętrznego i wewnętrznego. Przykłady obliczeń.
Temat 2. Obliczenia i dobór urządzeń do oczyszczania i obróbki cieplno-wilgotnościowej powietrza. Ogrzewanie suchym powietrzem. Obliczanie procesów i wyposażenia. Ogrzewanie z nawilżaniem powietrza. Obliczanie procesów i wyposażenia. Nawilżanie powietrza. Obliczanie procesów i wyposażenia. Chłodzenie suchym powietrzem. Obliczanie procesów i wyposażenia. Chłodzenie powietrzem z jednoczesnym osuszaniem. Obliczanie procesów i wyposażenia. Osuszanie powietrza. Obliczanie procesów i wyposażenia. Filtry, urządzenie; lekcje sprzątania; obliczenia i dobór. Dobór sprzętu do lokali o różnym przeznaczeniu. Przykłady obliczeń.
Temat 3. Parametry projektowe powietrza zewnętrznego i wewnętrznego. Szacunkowe parametry powietrza zewnętrznego. Parametry projektowe powietrza wewnętrznego dla pomieszczeń o różnym przeznaczeniu (z uwzględnieniem wymagań SNiP, SanPiN, norm technologicznych itp.).
Temat 4. Obliczanie dopływów ciepła i wilgoci. Wyznaczanie przepływu powietrza. Obliczanie dopływów ciepła w ciepłych i zimnych okresach roku według metody standardowej i wskaźników uśrednionych. Obliczanie dopływów wilgoci w ciepłych i zimnych porach roku. Wyznaczanie zużycia powietrza od warunku spłaty nadwyżek ciepła i wilgoci. Szybkość wymiany powietrza. Zalecane ekstrema wymiany powietrza dla pomieszczeń o różnym przeznaczeniu. Wyznaczenie przepływu powietrza z uwzględnieniem zalecanego współczynnika wymiany powietrza. Przykłady obliczeń.
Temat 5. Budowa procesów obróbki cieplnej i wilgoci powietrza w instalacjach wentylacyjnych i klimatyzacyjnych. Opierając się na diagramie J-d procesów uzdatniania powietrza w systemach wentylacyjnych i urządzeniach lokalnych; budowa procesów uzdatniania powietrza w klimatyzatorach centralnych. Określenie specyficznego obciążenia ciepła, zimna i wilgoci na sprzęcie. Obliczanie wydajności systemu: wydajność ogrzewania, chłodzenia, nawilżania i suszenia. Przykłady obliczeń.
Temat 6. Montaż instalacji wentylacyjnych i klimatyzacyjnych. Obliczanie i selekcja. Montaż systemów wentylacyjnych do pomieszczeń o różnym przeznaczeniu. Dobór sprzętu. Lokalne klimatyzatory. Fancoile. Urządzenie. Obliczanie i selekcja. Montaż klimatyzatorów centralnych z bezpośrednim przepływem i recyrkulacją. Obliczanie i selekcja. Jednostki odzysku ciepła. Urządzenie, obliczenia i dobór. Przykłady obliczeń.
Temat 7. Systemy dystrybucji powietrza. Obliczanie i selekcja. Cel, urządzenie. Sposoby dostarczania powietrza do pomieszczeń. Urządzenia do dystrybucji powietrza. Kanały powietrzne i kanały dystrybucji. Obliczanie i selekcja. Obliczanie systemów dystrybucji powietrza do pomieszczeń o różnym przeznaczeniu.
Temat 8. Chłodnictwo systemów wentylacyjnych i klimatyzacyjnych. Schematy chłodnicze do bezpośredniego chłodzenia i chłodzenia czynnikami chłodniczymi. Montaż urządzeń do chłodzenia systemów wentylacyjnych i klimatyzacyjnych. Obliczanie i dobór urządzeń chłodniczych.
Temat 9. Automatyzacja systemów wentylacji i klimatyzacji. Automatyczna regulacja temperatury powietrza w pomieszczeniu. Automatyczna regulacja wilgotności powietrza w klimatyzowanych pomieszczeniach o różnym przeznaczeniu. Automatyczna ochrona nagrzewnic powietrza przed zamarzaniem; blokowanie napędów elektrycznych urządzeń i zaworów powietrznych. Alarm awaryjnego wzrostu ciśnienia powietrza za filtrem. Opcje zdalnego sterowania. Powiązanie z automatyką maszyny chłodniczej.
Temat 10. Środki oszczędności energii w systemach wentylacyjnych i klimatyzacyjnych. Dobór racjonalnych parametrów powietrza zewnętrznego i wewnętrznego; różnica temperatur roboczych. Wybór energooszczędnego systemu dystrybucji powietrza. Wdrażanie systemów odzysku ciepła i wykorzystanie naturalnego zimna. Wybór opcji chłodzenia i automatyzacji.
Temat 11. Metody projektowania i obliczania systemów wentylacji i klimatyzacji pomieszczeń przedsiębiorstw spożywczych. Główne dokumenty regulacyjne dotyczące projektowania systemów przemysłowych do komfortowej i komfortowej klimatyzacji technologicznej w pomieszczeniach narażonych na działanie ciepła i wilgoci. Projektowanie systemów klimatyzacji technologicznej (przykłady projektowe dla zakładów przetwórstwa mięsnego, mleczarskiego, serowarskiego, rybnego i innych przedsiębiorstw przemysłu spożywczego).
Celem obsługi technicznej agregatu chłodniczego jest ustalenie i utrzymanie określonych warunków temperatury i wilgotności w pomieszczeniach chłodniczych. Głównym zadaniem jest zapewnienie niezawodnej, bezawaryjnej i bezpiecznej pracy wszystkich urządzeń chłodniczych przy minimalnych kosztach produkcji sztucznego przeziębienia.
Prawidłowa organizacja pracy technicznej agregatu chłodniczego musi spełniać wymagania:
niezawodność i trwałość eksploatowanych urządzeń chłodniczych;
bezpieczeństwo i ochrona w pracy.
Koszt produkcji chłodu, związany z oszczędnością energii elektrycznej, robocizny, wody, materiałów eksploatacyjnych, powinien być minimalny.
Ważnym warunkiem normalnej pracy agregatu chłodniczego jest dostępność specjalnie przeszkolonego personelu. Personel obsługujący agregat chłodniczy musi kierować się dokumentacją techniczną agregatu chłodniczego, instrukcją produkcyjną dotyczącą serwisowania całego agregatu, a także poszczególnych jego zespołów i elementów.
Dla ekonomicznej i bezpiecznej pracy agregatu konieczne jest przestrzeganie optymalnego trybu jego pracy, wyposażenie agregatu w oprzyrządowanie, automatykę i urządzenia zabezpieczające, prawidłowe napełnienie układu czynnikiem chłodniczym, utrzymanie powierzchni wymiany ciepła skraplaczy oraz parowniki czyścić i terminowo przeprowadzać planową konserwację zapobiegawczą urządzeń chłodniczych, prowadzić codzienny dziennik agregatu chłodniczego i sporządzać raporty techniczne.
W przedsiębiorstwach handlowych i gastronomicznych sprzęt chłodniczy jest obsługiwany przez mechaników wyspecjalizowanych fabryk urządzeń chłodniczych. Konserwacja obejmuje przeglądy przeprowadzane raz w miesiącu wraz z wykonaniem konserwacji zapobiegawczej i niezbędnych drobnych napraw, usuwanie usterek mogących wystąpić, codzienne przeglądy pracy agregatu chłodniczego.
Zakres obsługi zależy od rodzaju maszyn, rozplanowania instalacji oraz stopnia jej automatyzacji.
Wniosek
Dziś technologia wytwarzania agregatów chłodniczych stoi na bardzo wysokim poziomie. Rozwój nowych modeli agregatów chłodniczych wpłynął dziś nawet na dziedzinę mikroelektroniki. Nie oszczędzono również technologii produkcji maszyn chłodniczych oraz cyfrowych technologii komputerowych.
Zastosowanie w życiu codziennym agregatów sterowanych komputerowo znacząco zwiększa wygodę ich obsługi, pozwala zaoszczędzić czas, a komputerowa kontrola stanu agregatów pozwala na zachowanie jego bardziej niezawodnej i bezpiecznej pracy przez wiele lat.
Zastosowanie w produkcji agregatów chłodniczych sterowanych komputerowo zwiększa wydajność produkcji, zapewnia niezawodną kontrolę temperatury, a tym samym niezawodną konserwację surowców i zapewnienie minimalnych strat.
Być może główną wadą takich instalacji jest złożoność i wysoki koszt naprawy elektronicznych części sterowania komputerowego. Ponadto elementy elektroniczne wymagają specjalnych warunków pracy. Kolejną wadą jest to, że lodówki sterowane komputerowo są dość drogie, ale oszczędność na minimalnych stratach surowców podczas przechowywania w produkcji w pełni uzasadnia koszt jednostek.
Kolejnym nie bez znaczenia problemem jest brak specjalistów od konserwacji takiego sprzętu. Ale większość przedsiębiorstw w Rosji zaprasza specjalistów z zagranicy do obsługi importowanych agregatów chłodniczych, ponieważ większość lodówek sterowanych cyfrowo jest dostarczana z zagranicy.
Niestety w Rosji jest niewiele takich lodówek lub są one produkowane, ale odpowiednio na licencji firm zagranicznych takie jednostki wchodzą na rynek pod marką firmy zagranicznej.
Dlatego konieczne jest rozwijanie w Rosji rozwoju i produkcji chłodziarek i agregatów sterowanych cyfrowo oraz tworzenie nowych technologii ich wytwarzania, aby rosyjskie agregaty chłodnicze stały się konkurencyjne na rynku światowym.
Powiązana informacja:
- Godzina 0:00:00. - metoda tworzenia nowego sprzętu poprzez montaż produktu końcowego z ograniczonego zestawu standardowych i zunifikowanych jednostek i zespołów
- XI. Sytuacja awaryjna, sytuacje niebezpieczne i awarie sprzętu, sytuacje awaryjne w służbach ruchu lotniczego
- Numer biletu 5. Przy doborze pomp i sprężarek do HIF należy wziąć pod uwagę wymagania techniczne dotyczące bezpieczeństwa urządzeń do pracy w środowiskach zagrożonych wybuchem.
![]() |
|
![]() |
![]() |
![]() |
![]() |
![]() |
![]() |
![]() |
![]() |
Regularna konserwacja jest niezbędnym warunkiem trwałości urządzeń chłodniczych w różnych obszarach produkcji i usług publicznych.
Firma „Ecolife” zapewnia profesjonalną konserwację urządzeń chłodniczych w Moskwie i regionie moskiewskim. Zapewnimy stabilną pracę Twojego sprzętu, a w efekcie całego przedsiębiorstwa.
Masz gwarancję na nagłe zatrzymanie urządzeń chłodniczych z powodu awarii trybu, wadliwego działania, zużycia części, zatkania i zanieczyszczenia jednostek.
Lista prac konserwacyjnych dla urządzeń chłodniczych zależy od konkretnego typu urządzenia, cech eksploatacyjnych i konstrukcji.
Koszt pracy
Koszt wyliczany jest indywidualnie w zależności od formy współpracy. Ogólne ceny są dostępne na życzenie.
Pracujemy w całej Moskwie i regionie moskiewskim z wizytą na sprzęcie. Gwarancją naszej pracy jest stosowanie wysokiej jakości komponentów i narzędzi oraz profesjonalizm naszych pracowników w przystępnej cenie. W naszej pracy używamy mało agresywnych detergentów „Frionett” i „Convotherm”, które są dozwolone na terenie Federacji Rosyjskiej.
Umowa na konserwację urządzeń chłodniczych
Zawieramy z klientami umowę na konserwację urządzeń chłodniczych, w specjalnym załączniku, w którym wyszczególniony jest wykaz prac ze wszystkimi środkami do utrzymania sprzętu w stanie roboczym.
Każda pozycja na liście uzgadniana jest z klientem, rodzaj umowy uzależniony jest od długoletniej współpracy, rodzaju i stopnia skomplikowania sprzętu.
Oferujemy trzy standardowe umowy:
1. Jednorazowa umowa serwisowa
2. Stała umowa serwisowa
3. Umowa na konserwację planową (konserwacja roczna z harmonogramem zdarzeń)
Jednorazowa konserwacja urządzeń chłodniczych
Obejmuje diagnostykę, rozwiązywanie problemów i zapobieganie dalszemu funkcjonowaniu sprzętu.
Najpierw wstępna wizyta specjalistów na budowie, sporządzenie kosztorysu z wykazem robót i uzgodnienie terminów.
Za czynności wykonywane w ramach umowy dokonuje się zapłaty po podpisaniu aktów.
Typowa lista prac do jednorazowej konserwacji:
1. Inspekcja i ocena wizualna stanu zewnętrznego, konfiguracji i funkcjonalności
2. Sprawdzanie i regulacja zawiasów i zamków
3. Czyszczenie ramy, sprężarki, skraplacza powietrza
4. Przeciąganie połączeń gwintowanych
5. Sprawdź, czy nie ma wycieku czynnika chłodniczego,
6. Sprawdzenie izolacji termicznej obiegu chłodniczego
7. Sprawdzenie sieci elektrycznych, styków i połączeń
8. Rozwiązywanie problemów, tankowanie obwodu i wymiana zużytych części w razie potrzeby
9. Testowanie trybów pracy
10. Rejestrowanie danych
Na koniec pracy pracownik firmy wydaje zalecenia dotyczące dalszej eksploatacji sprzętu.
W trakcie pracy lista usług może zostać dostosowana w przypadku wykrycia nieprawidłowości podczas procesu kontroli.
Regularna konserwacja urządzeń chłodniczych
Na uzgodniony okres zostaje zawarta umowa o stałej współpracy, w trakcie której nasi specjaliści podejmują wszelkie prace mające na celu utrzymanie stanu sprzętu po stałych stawkach. Dokładny harmonogram prac nie jest ustalony, wszystkie czynności wykonujemy według potrzeb lub na życzenie klienta. Płatność jest dokonywana na podstawie faktu wykonanej pracy każdorazowo po dostarczeniu pracy.
Planowana coroczna konserwacja urządzeń chłodniczych
Planowana roczna konserwacja obejmuje zestaw regularnych czynności zgodnie z ustalonym harmonogramem. W porozumieniu z klientem specjaliści udają się do miejsca pracy zgodnie z planem, oceniają stan sprzętu i podejmują wszelkie niezbędne działania w celu dalszej pracy w pożądanym trybie.
Regularna konserwacja pomoże zidentyfikować poważne problemy na czas i podjąć środki zapobiegawcze w celu ich wyeliminowania. Terminowa kontrola może zapobiec nagłej awarii i zatrzymaniu sprzętu. Wszystkie prace prowadzone są ściśle według zaplanowanego harmonogramu, w tym harmonogramu płatności.
Planowa konserwacja maszyn chłodniczych
Okresowość | Wykaz prac przy konserwacji maszyn chłodniczych | Dodatkowa lista prac dla przepompowni agregatu chłodniczego |
Miesięczny |
Oględziny, |
Kontrola procesów korozyjnych w głównych zespołach mechanizmów, |
Kwartalny |
Sterowanie skraplaczem powietrza, |
Tankowanie i analiza płynu chłodzącego, |
Raz na semestr |
Monitorowanie stanu i czyszczenie kondensatorów, |
|
Rocznie |
Inspekcja wnęk wewnętrznych i łożysk wentylatorów, |
Czyszczenie wszystkich filtrów |
Raz na 2 lata | . wymiana oleju w sprężarce | |
Raz na 3 lata | . uzupełnienie płynu chłodzącego i czyszczenie całego układu |
usługi dodatkowe
Każdemu klientowi, z którym zawarliśmy umowę zapewniamy usługi dodatkowe, w tym bezpłatne konsultacje i zalecenia dotyczące eksploatacji urządzeń chłodniczych. Ponadto nasi klienci otrzymują rabat na części zamienne i komponenty do urządzeń chłodniczych.
Aby uzyskać szczegółowe informacje i zostawić prośbę o indywidualną obsługę, możesz zadzwonić do nas telefonicznie lub wypełnić formularz na stronie. Nasi eksperci skontaktują się z Państwem w najbliższym czasie i udzielą szczegółowych porad w interesujących Państwa kwestiach.
Maszyny i aparatura agregatów chłodniczych powinny być tak usytuowane, aby zapewnić ich normalną konserwację i naprawę.
Konserwacja agregatu chłodniczego polega na przygotowaniu go do pracy, uruchomieniu, regulacji dopływu czynnika chłodniczego do układu wyparnego, utrzymaniu agregatu chłodniczego w czasie pracy, zatrzymaniu i wyłączeniu maszyn i urządzeń, przestrzeganiu przepisów bezpieczeństwa, konserwacji maszyn i pomieszczeń roboczych czyste iw dobrym stanie, a także wypełnienie niezbędnej dokumentacji sprawozdawczej.
Rozpoczęcie dyżuru personelu zmianowego rozpoczyna się od sprawdzenia wpisów w dzienniku pracy stacji chłodniczej, a kończy się kontrolą temperatury w głównych punktach cyklu chłodniczego oraz sprawdzeniem działania urządzeń stacji chłodniczej.
Obie zmiany - zdanie i odbiór - podpisują w dzienniku dostawę i akceptację zmiany.
Pracownicy okresowo sprawdzają ilość i gęstość solanki, dopływ wody do skraplaczy, sprawność wentylacji awaryjnej, dostępność niezbędnych części zamiennych, materiałów i narzędzi oraz środków ochrony osobistej. Szczególną uwagę należy zwrócić na sprawdzenie stanu części trących sprężarek i pomp, pracy układu olejowego, zaworów i uszczelek.
Dla wygody personelu konserwacyjnego na rurociągach wody chłodzącej zainstalowane są lampki obserwacyjne lub inne urządzenia do monitorowania przepływu wody.
W różnych miejscach chłodni rozmieszczone są również gniazda na przyrządy potrzebne zarówno do stałego monitorowania pracy instalacji, jak i do okresowych badań. Manometry, termometry, amperomierze i inne przyrządy pomiarowe montuje się tak, aby po uruchomieniu instalacji znajdowały się w polu widzenia kierowcy i jego pomocnika.
Automatyczne zawory sterujące są zwykle duplikowane przez ręczne. Pozwala to na kontynuowanie produkcji chłodu w przypadku awarii części automatyki urządzeń sterujących.
Średnie i duże agregaty chłodnicze są głównie obsługiwane z ręcznym układem rozruchowym. Ich obsługa techniczna jest dość skomplikowana i wymaga od obsługi głębokiej znajomości fizycznych podstaw pozyskiwania zimna, rozmieszczenia maszyn, aparatury, przyrządów, armatury oraz zasad ich obsługi.
Aby ułatwić pracę personelu w maszynowniach stacji chłodniczych, zamieszczane są schematy rurociągów, plany rozmieszczenia urządzeń, informacje o głównych parametrach agregatów chłodniczych, wskaźniki zużycia czynnika chłodniczego, oleju, energii elektrycznej, plakaty bezpieczeństwa, harmonogramy przeglądów prewencyjnych i napraw.
Aby zorientować personel operacyjny w schematach rozgałęzionych rurociągów, są one pomalowane na kolory warunkowe. Najczęściej używane kolory to:
dla rurociągów czynnika chłodniczego: wylot - czerwony, ciecz - żółty, ssanie - niebieski;
dla rurociągów solankowych: ciśnienie - zielony, powrót - brązowy;
dla wodociągów: ciśnienie - niebieski, powrót - fioletowy.
Jeśli występuje kilka parametrów zimnych, na malowane rurociągi nakładane są również pierścienie warunkowe, pokazujące, do której maszyny należy ten rurociąg.
Sprawna i niezawodna praca każdego agregatu chłodniczego zależy nie tylko od dobrego stanu technicznego urządzenia, ale również od jego prawidłowej pracy. Operatorzy, ich pomocnicy, aparaty, dyżurni mechanicy i elektrycy, podlegli kierownikowi zmiany stacji chłodniczej, bezpośrednio monitorują pracę urządzeń.
Ich głównym zadaniem jest utrzymanie zadanych parametrów pracy maszyn chłodniczych przy najmniejszym zużyciu energii i materiałów eksploatacyjnych oraz ścisłe przestrzeganie przepisów bezpieczeństwa.
Aby pomyślnie wykonać zadania stojące przed personelem obsługującym, konieczne jest:
wysoka jakość i użyteczność sprzętu;
zaopatrzenie w urządzenia kontrolno-pomiarowe;
dostępność części zamiennych, narzędzi i urządzeń naprawczych;
dostępność czynnika chłodniczego, chłodziwa, wody, olejów smarowych, powietrza oprzyrządowania, materiałów eksploatacyjnych i zasobów energii;
prawidłowe napełnianie układów czynnikiem chłodniczym i chłodziwem; brak zanieczyszczeń na powierzchniach wymiany ciepła; terminowe zapobieganie i naprawa; prowadzenie dziennika zmian z identyfikacją naruszeń trybu pracy;
wysokie kwalifikacje personelu serwisowego.
Działanie agregatów chłodniczych regulują specjalne instrukcje. Nieprzestrzeganie ich może prowadzić do zakłócenia procesu technologicznego dla odbiorców chłodu i wzrostu zużycia energii na pozyskanie chłodu.
Sekwencja poszczególnych czynności podczas rozruchu i wyłączenia oraz procedura konserwacji uzależniona jest od cech konstrukcyjnych i eksploatacyjnych agregatu chłodniczego, co musi znaleźć odzwierciedlenie w instrukcji konserwacji.
W tym rozdziale omówiono podstawowe zasady i techniki obsługi najpopularniejszych typów dużych agregatów chłodniczych, które w każdym indywidualnym przypadku należy określić zgodnie z instrukcjami rozruchowymi producentów urządzeń. Po przestudiowaniu tych technik przyszły mechanik lub aparatczyk będzie w stanie opanować procedurę uruchamiania, regulowania i zatrzymywania agregatów chłodniczych dowolnych systemów.
Do obsługi przemysłowych urządzeń chłodniczych dopuszczone są osoby, które ukończyły osiemnaście lat, przeszły badania lekarskie i posiadają zaświadczenie o ukończeniu szkolenia w wybranej przez siebie specjalności.
Personel serwisowy musi dobrze znać i ściśle przestrzegać zasad i instrukcji obsługi i naprawy sprzętu i urządzeń stacji chłodniczych. Maszynownie stacji chłodniczych są miejscem pracy kierowcy i jego pomocnika. Działy pompowania i sprzętu są obsługiwane przez aparatczyków, którzy podlegają kierowcy i koordynują z nim wszystkie swoje działania.
Pracownicy stacji chłodniczych corocznie zdają egzaminy komisji kwalifikacyjnej. Wyniki egzaminu są dokumentowane. Osoby, które zdadzą te egzaminy, otrzymują specjalne certyfikaty.
pytania testowe
1. Jakie zadania są postawione przed personelem obsługującym instalacje chłodnicze?
2. Wymień warunki niezbędne do pomyślnego działania agregatu chłodniczego.
3. Powiedz nam, jak układ jest wypełniony amoniakiem i freonem?
4. Jak przygotowuje się solankę?
5. Opowiedz nam o przygotowaniach do uruchomienia agregatu chłodniczego.
6. Jak wygląda rozruch agregatu chłodniczego ze sprężarkami tłokowymi i turbosprężarkami?
7. Wymień oznaki normalnej pracy sprężarki tłokowej.
8. Opowiedz nam o smarowaniu sprężarki.
9. Jak regulowana jest praca agregatu sprężarkowego?
10. Jakie wahania temperatury powinny towarzyszyć normalnej pracy amoniakalnej instalacji chłodniczej?
11. Opisz procedurę wyłączania agregatu chłodniczego sprężarkowego.
12. Co wiesz o procedurach konserwacji parowników i skraplaczy?
13. Co powoduje pogorszenie wymiany ciepła w parowniku i skraplaczach?
14. Opowiedz nam o przygotowaniach do uruchomienia turbozespołów freonowych.
15. Jaka jest normalna praca instalacji freonu turbochłodniczego?
16. Opowiedz nam o cechach działania propylenowych turbozespołów.
17. W jaki sposób chłodziarki absorpcyjne są napełniane roztworem woda-amoniak?
18. Opisz, jak uruchamiać i zatrzymywać chłodziarkę absorpcyjną.
19. Opowiedz nam o działaniu pomp odśrodkowych.
20. Co powoduje korozję urządzeń chłodniczych?
21. Jak działa ochrona bieżnika?