Opracowania projektowe OJSC TKZ „Krasny Kotelshchik” w celu wprowadzenia nowych technologii spalania paliw stałych w piecach kotłów parowych. Opracowania projektowe OJSC TKZ „Krasny Kotelshchik” w celu wprowadzenia nowych technologii spalania paliw stałych w piecach kotłów parowych
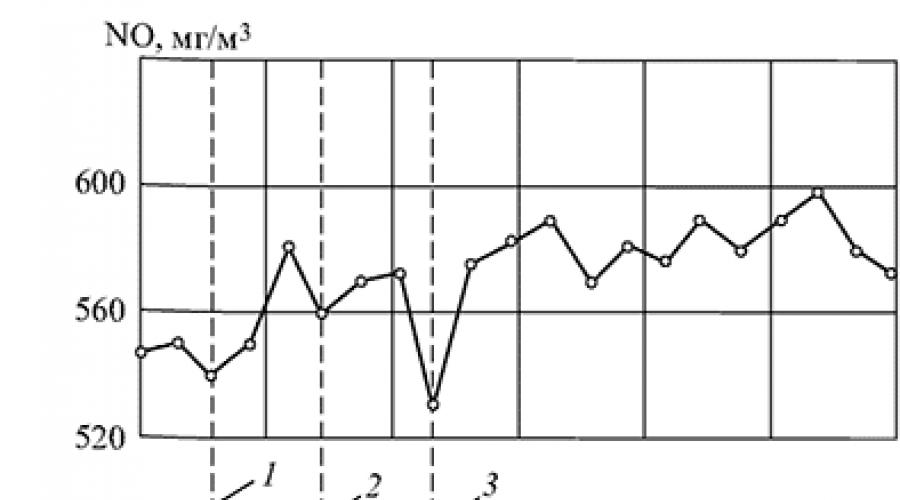
Przeczytaj także
Doktor nauk technicznych ŻOŁNIERZ AMERYKAŃSKI. Lewczenko, dr. Yu.S. Nowikow, dr. P.N. Fiedotow, nauki chemiczne L.M. Khristich, dr. JESTEM. Kopeliowicz, dr. Yu.I. Shapovalov, JSC TKZ „Krasny Kotelszczik”
Magazyn „Heat Supply News”, nr 12, (28), grudzień 2002, s. 25 - 28, www.ntsn.ru
(na podstawie raportu z seminarium „Nowe technologie spalania paliw stałych: ich stan obecny i zastosowanie w przyszłości”, VTI, Moskwa)
W ostatnich dziesięcioleciach krajowa energetyka skupiała się w dużej mierze na paliwach gazowych i olejowych. Biorąc pod uwagę obecność w kraju ogromnych złóż paliw stałych, na dłuższą metę trudno uzasadnić taki stan rzeczy.
W tym względzie za naturalne należy uznać fakt, że „przerwa gazowa” dobiega końca i następuje reorientacja w kierunku zdecydowanego zwiększania skali wykorzystania węgla kamiennego, brunatnego i torfu.
Wpływa na to wiele czynników, m.in.:
Społecznie uzasadniona perspektywa ożywienia górnictwa węglowego;
Spadek tempa zagospodarowania złóż gazowych i wolumenu wydobycia gazu ziemnego;
Wzrost potrzeb eksportowych.
Zespół problemów finansowych i transportowych na krajowym i zagranicznym rynku surowców energetycznych komplikuje przyjęcie długoterminowej i zrównoważonej strategii polityki paliwowej.
W tych warunkach TKZ OJSC nie osłabiła przez lata swojej uwagi problematyce paliw stałych i kontynuowała modernizację swoich kotłów pyłowych, angażując najbardziej autorytatywne siły nauki (NPO TsKTI, VTI, ORGRES itp.).
Opracowaniami objęto wszystkie typy kotłów produkowanych przez zakład na przestrzeni ostatnich 20-30 lat. Głównym celem takich działań modernizacyjnych jest zwiększenie wydajności środowiskowej i ekonomicznej kotłowni, maksymalnie zbliżając je do światowych standardów. Umożliwiło to przygotowanie wystarczającej ilości rozwiązań technicznych do wdrożenia.
W pracach tych można wyróżnić następujące główne obszary, obejmujące szeroki zakres technologii przetwarzania i spalania paliw:
1. Różne modyfikacje etapowego spalania paliw stałych;
2. Tworzenie instalacji wysoce ekonomicznych i przyjaznych środowisku.
Na tych obszarach uwzględniona jest cała gama rosyjskich paliw: węgiel kamienny i brunatny z basenu Kuźnieckiego, Kańsko-Aczyńskiego i Dalekiego Wschodu, antracyt i jego odpady, torf, paliwo węglowo-wodne.
Etapowe spalanie paliw stałych
Obecnie emisję szkodliwych gazów w spalinach elektrowni regulują dwie normy państwowe GOST 28269-89 - dla kotłów i GOST 50831-95 - dla instalacji kotłowych.
Najbardziej rygorystyczne wymagania dotyczą emisji z kotłowni spalających paliwo pyłowe. Aby spełnić te standardy podczas spalania węgla kuźnieckiego z usuwaniem żużla w postaci stałej, wymagana jest albo instalacja oczyszczania gazu, albo zastosowanie wszystkich znanych sposobów tłumienia NO X.
Co więcej, możliwość ograniczenia emisji NO X do tych wartości za pomocą środków technicznych dla węgli Zagłębia Kuźnieckiego nie została jeszcze przetestowana i wymaga potwierdzenia w kotłach za pomocą wdrożonych środków.
Taki kocioł TKZ wraz z Sibtekhenergo został opracowany na bazie kotła TPE-214 i dostarczony do elektrociepłowni Nowosybirsk-5. W tym kotle na węgiel klasy „G” i „D” zastosowano wielostopniowy schemat spalania: stopniowanie poziome i pionowe w strefie palnika oraz utworzenie nad palnikami strefy redukcyjnej z wykorzystaniem gazu ziemnego jako środka redukującego. Testowana na modelu aerodynamika paleniska jest zorganizowana w taki sposób, aby uniknąć żużlowania sit we wszystkich trybach pracy kotła. Uruchomienie kotła TPE-214 w Elektrociepłowni Nowosybirsk pozwoli nam zdobyć doświadczenie w maksymalizacji możliwej redukcji emisji NO X podczas komorowego spalania węgla o dużej zawartości azotu w paliwie.
Do spalania węgli niskoreaktywnych firmy Kuzbass (mieszanki „T” i „SS”) opracowano zmodernizowany kocioł TP-87M, który dostarczono do Państwowej Elektrowni Rejonowej Kemerowo z organizacją trzystopniowego spalania węgla w warunkach usuwania ciekłego żużla. W kotle zastosowano transport pyłu PPPV o wysokim stężeniu, palniki o obniżonej wydajności NO X oraz specjalne palniki pyłowo-gazowe służą do utworzenia strefy redukcyjnej nad palnikami głównymi przy minimalnym zużyciu gazu ziemnego (3 - 5%). Aby spalić chudy węgiel kuźniecki, TKZ wraz z VTI rekonstruuje kotły TP-80 i TP-87, a także kotły TPP-210A w CHPP-22 Mosenergo, które również wykorzystują PPVK i trzystopniowe spalanie gazem ziemnym jako środek redukujący.
Dla węgla z regionu Dalekiego Wschodu zrealizowano niskobudżetowy projekt przebudowy kotła TPE-215 z wykorzystaniem spalania dwustopniowego.
Dla węgli Zagłębia Kansk-Aczyńsk zakład wraz z CKTI i SibVTI opracował i dostarczył do Elektrociepłowni Krasnojarsk kocioł o wydajności pary 670 t/h (TPE-216), w którym wykorzystuje się trój- schemat spalania etapowego z wykorzystaniem pyłu węglowego jako środka redukującego oraz specjalne środki zabezpieczające sita przed żużlowaniem: podanie mieszanki ubogopaliwowej przez dysze palników (GPHV) od strony sit pieca, nadmuch powietrza wzdłuż sit w strefie redukcji i zapewnienie, że temperatura gazu w aktywnej strefie spalania nie przekroczy 1250°C dzięki dodatkowemu doprowadzeniu 10% gazów recyrkulacyjnych z powietrza wtórnego.
Zawarte w projekcie rozwiązania technologiczne (organizacja spalania niskotemperaturowego i podwyższona zawartość tlenku wapnia w popiele) pozwalają nie tylko zapewnić emisję NO X na poziomie 220-300 mg/m 3 , ale także S0 2 emisji nie większej niż 400 mg/m 3.
Dla torfu wysokowilgotnego opracowano projekty modernizacji kotłów TP-208 i TP-170-1 z organizacją w nich spalania dwustopniowego.
Stopniowe spalanie paliwa w różnych jego modyfikacjach jest uniwersalnym sposobem znacznego ograniczenia emisji NO X, jednak w przypadku niektórych rodzajów paliw o dużej zawartości azotu zastosowanie tej metody, nawet w połączeniu z innymi środkami spalania wewnętrznego, może być niewystarczające do spełniają wymagania regulacyjne dla węgli kamiennych i pieców o usuwaniu żużla stałego 350 mg/m3. W takim przypadku zaleca się zastosowanie metody tłumienia NO X z sekwencyjną kombinacją trójstopniowego spalania i selektywnej niekatalitycznej redukcji (SNCR) NO X.
Tworzenie wysoce ekonomicznych i przyjaznych środowisku instalacji
Bazując na wieloletnim doświadczeniu w tworzeniu i rozwoju kotłów parowych w elektrowniach na niemal wszystkie rodzaje paliw stosowanych w energetyce, zakład opracował projekty elektrowni nowej generacji, które pozwolą na przełom na zasadniczo nowy poziom parametry techniczne produkowanego sprzętu.
Modernizacja kotła TPP-210 wraz z montażem pieca barkowego
do spalania węgla niskoreaktywnego
Znane trudności w spalaniu AS oraz rosnące wymagania środowiskowe powodują, że pojawia się pytanie o dalsze doskonalenie procesu spalania AS, w szczególności poprzez zastosowanie tzw. pieców „ramiennych” z odżużlem stałym, w których spalane jest paliwo niskoreaktywne, wysokopopiołowe bez oświetlenia w zakresie obciążeń stosowanych w praktyce, zapewniający długoletnią pracę kotła.
Zalety pieca „ramiennego” z odżużlem stałym w porównaniu do technologii spalania popiołów w piecu z odżużlem ciekłym:
Umożliwia stosowanie urządzeń palnikowych o małych prędkościach mieszaniny powietrza, co zwiększa czas przebywania cząstek w strefie palnika, tworząc w ten sposób korzystne warunki do nagrzania cząstek i ich zapłonu;
Osiąga się długi czas przebywania cząstek w strefie wysokiej temperatury (co najmniej 2 razy większy niż w tradycyjnym palenisku), co zapewnia zadowalające spalanie paliwa;
Umożliwia najwygodniejsze wprowadzanie powietrza niezbędnego do spalania w miarę rozwoju palnika;
Wyraźnie mniejsze trudności z usuwaniem żużla;
Mniejsze straty spowodowane oparzeniami mechanicznymi;
Niższa emisja tlenków azotu.
W przypadku paleniska „ramiennego” stosuje się palnik szczelinowy ze szczeliną między strumieniami powietrza pierwotnego i wtórnego, którego główną zaletą w porównaniu z palnikiem wirowym jest:
Brak przedwczesnego mieszania się powietrza pierwotnego z wtórnym, co korzystnie wpływa na zapłon; .
Dopływ powietrza pierwotnego w ilości niezbędnej jedynie do dopalenia substancji lotnych;
Racjonalne połączenie z paleniskiem, pozwalające wytworzyć wysoki stopień cyrkulacji gazów spalinowych do nasady palnika (w strefie zapłonu).
Na modernizowanym kotle do istniejącego szybu konwekcyjnego na modernizowanym kotle zainstalowano gazoszczelną palenisko „ramienne” oraz TVP, w przekroju którego zamontowano ekonomizer.
Spalanie zdegradowanych peletów antracytu w złożu fluidalnym
Spalanie odbywa się z wykorzystaniem technologii Politechniki Ałtajskiej, której główną ideą jest wstępne granulowanie mieszaniny mielonego, paliwa pierwotnego, popiołu i wapienia w celu zbliżenia składu złoża fluidalnego do monodyspersyjnego mieszanina. OJSC TKZ „Krasny Kotelszczik” wraz z autorem technologii przeprowadziła projekt modernizacji jednego z istniejących kotłów TP-230 w Państwowej Elektrowni Rejonowej Nieświeże w celu pilotażowego przemysłowego spalania popiołów granulowanych o zdegradowanej jakości w złożu fluidalnym.
Obecnie w Państwowej Elektrowni Rejonowej Nesvetay planowana jest instalacja pilotażowego kotła przemysłowego D-220 t/h z obiegowym złożem fluidalnym, którego generalnym wykonawcą i dostawcą jest firma Belenergomash OJSC. TKZ jest współwykonawcą.
Elektrownia do kompleksowego przetwarzania, spalania w stopionym żużlu i wykorzystania niskoreaktywnych odpadów węglowych
Krótki opis zespołu kotłowego „Kocioł przepływowy typu TPP-210”
Krótki opis zespołu kotłowego Kocioł przelotowy typu TPP-210 (p/p 950-235 GOST 3619-59 model TKZ TPP-210) o wydajności pary 950 ton na godzinę na parametry pary nadkrytycznej został zaprojektowany i wykonany przez firmę zakład Taganrog „Krasny Kotelshchik”. Kocioł przeznaczony jest do pracy w bloku z turbiną kondensacyjną K-300-240 o mocy 300 MW produkcji KhTGZ. Kocioł przeznaczony jest do spalania miału antracytowego podczas usuwania żużla ciekłego i gazu ziemnego ze złoża Szebelinskoje. Zespół kotłowy składa się z dwóch obudów o układzie każdej obudowy w kształcie litery U oraz regeneracyjnych nagrzewnic powietrza wymontowanych spod kotła i umieszczonych na zewnątrz budynku kotłowni. Korpusy kotłów tej samej konstrukcji o wydajności 475 t pary na godzinę każdy. Obudowy mogą pracować niezależnie od siebie. Ogólne dane kotła: Wydajność 475 t/h Temperatura pary przegrzanej: pierwotna 565°C wtórna 565°C Zużycie pary wtórnej 400 t/h Ciśnienie pary pierwotnej za kotłem 255 kg/cm2 Ciśnienie pary wtórnej na wlocie kotła 39,5 kg/h cm² Ciśnienie pary wtórnej na wylocie z kotła 37 kg/cm² Temperatura pary wtórnej na wlocie 307 °C Temperatura wody zasilającej 260 °C Temperatura gorącego powietrza 364 °C Całkowita masa metalu kotła 3438 t Szerokość kotła wzdłuż w osi słupów 12 m Głębokość kotła w osi słupów 19 m Wysokość kotła 47 m Objętość wody kotła w stanie zimnym 243 m Wymiary paleniska w planie (wzdłuż osi rur): W powierzchnia NRCh 10800x7550 Na obszarze VRCH 10725x7592,5 (Zgodnie z instrukcją okólnika operacyjnego nr T-4/71 temperatura pary przegrzanej pierwotnej i wtórnej na wylocie zostaje obniżona do 545 °C) Kocioł wyposażony jest w dwa osiowe oddymiacze, dwa dmuchawy z silnikami dwubiegowymi oraz dwa wentylatory nadmuchowe. Schemat przygotowania pyłu za pomocą pojemnika na pył i transportu pyłu do palników za pomocą gorącego powietrza. Kocioł wyposażony jest w trzy młyny kulowe bębnowe ШБМ-50 o wydajności 50 ton pyłu na godzinę. Powierzchnie grzewcze: Ekrany ogniowe 1317 m² W tym: NRCh 737 m² VRCH 747 m² Ekrany komory obrotowej i sufit 1674 m² Przegrzewacz SVD: a) ekrany 1. 510 m² b) ekrany 2. 594 m² Przegrzewacz konwekcyjny 1674 m² Przegrzewacz SVD, w tym w tym: Para wymiennik ciepła 800 mI Pośredni pakiet konwekcyjny 1994 mI Nagrzewnica powietrza 78730 mI Wyjście pakietu konwekcyjnego 1205 mI Ekonomizer konwekcyjny 1994 mI Schemat ścieżki para-woda Ultrawysokociśnieniowa ścieżka pary-woda (SVD) kotła jest dwuprzepływowa z niezależną regulacją mocy i temperatury dla każdego przepływu.
W każdym korpusie kotła znajdują się dwa strumienie (w opisie kotła i instrukcji strumień nazywany jest gwintem). Ponieważ konstrukcja obudów jest podobna, w przyszłości zostanie opisany schemat i konstrukcja jednej obudowy. Przez zespół podający przepływa woda zasilająca o temperaturze 260°C, która trafia do komór wlotowych ekonomizera wody Ř325*50, które są jednocześnie najbardziej wysuniętymi na zewnątrz belkami nośnymi pakietu. Po przejściu przez wężownice ekonomizera woda o temperaturze 302°C wpływa do komór wylotowych Ш235*50, które stanowią środkowe belki nośne tej powierzchni. Za ekonomizerem woda kierowana jest rurami obejściowymi Sh159*16 do środkowych belek nośnych tej powierzchni rurami Sh133*15 i kierowana jest do części dolnej (NRF). Ekrany NRF składają się z oddzielnych paneli, a dolne powierzchnie grzewcze, z przodu i z tyłu, to jednoczęściowe wieloprzebiegowe taśmy. Woda doprowadzana jest do paneli przez dolną komorę, a odprowadzana z górnej. Takie rozmieszczenie komór wlotowych i wylotowych poprawia wydajność hydrauliczną panelu. Schemat przepływu medium wzdłuż ekranów NRF jest następujący: W pierwszej kolejności medium wpływa na panele tylne i panele tylne ekranów bocznych, następnie poprzez obejście kierowane jest na ekran przedni i panele przednie ekranów bocznych rury Ř 135*15. Rury obejściowe wyposażone są w podkładki Ø30 mm poprawiające hydrodynamikę. Za NRF czynnik o temperaturze 393°C rurami Ř133*15 kierowany jest do kolektora pionowego Ř273*45, skąd rurami obejściowymi Ř133*15 wchodzi na ekrany boczne i czołowe górnej części radiacyjnej (URP ). W przypadku paneli VRF względne rozmieszczenie komór wejściowej i wyjściowej jest podobne jak w przypadku paneli NRF. Po przejściu przez wielociągowe panele przedniego i bocznego ekranu magnetowidu para kierowana jest rurami obejściowymi Ř133*15 do pionowego rozdzielacza mieszającego Ř325*45, skąd rurami Ř159*16 wpływa do kolektora w kształcie litery N. panele tylnego ekranu magnetowidu.
Po przejściu przez panele wielociągowe ekranów przedniego i bocznego VRF para kierowana jest rurami obejściowymi Ř133*15 do pionowego kolektora mieszającego Ř325*45 i po podgrzaniu do temperatury 440°C w powierzchniach radiacyjnych pieca , para rurami obejściowymi Ř149*16 kierowana jest na panele osłonowe ścian bocznych i tylnych kamer obrotowych. Po przejściu przez sita komory obrotowej para wchodzi rurami do 1 schładzacza wtryskowego Ř279*36. W 1 schładzaczu wtryskowym przepływy przekazywane są na całej szerokości kanału gazowego. Za schładzaczem para doprowadzana jest do przegrzewacza sufitowego rurami Ř159*16. W przegrzewaczu sufitowym para przemieszcza się od tylnej ściany przewodu kominowego do przodu kotła i o temperaturze 463°C przedostaje się do komór wylotowych stropu Ř273*45. Na rurociągach pary Sh273*39, stanowiących kontynuację komór wylotowych przegrzewacza sufitowego, zamontowane są w kanale zawory DU-225 (VZ). Za przegrzewaczem sufitowym przepływy prowadzone są przez szerokość kanału gazowego, a para kierowana jest rurami Ø159*18 do ekranów wejściowych pierwszego stopnia przegrzewacza ekranowego, znajdujących się w środkowej części kanału gazowego. Po przejściu przez sita wlotowe para o temperaturze 502°C trafia do drugiego schładzacza wtryskowego Ш325*50, po czym kierowana jest na sita wylotowe pierwszego stopnia, usytuowane wzdłuż krawędzi komina. Komora odbiorcza pary ekranów wlotowych i przewód parowy drugiego przesyłu schładzacza przepływają przez szerokość kanału gazowego. Przed drugim wtryskiem znajduje się przewód parowy Ř194*30 służący do odprowadzania części pary SVD do wymiennika ciepła gaz-para, a po wtrysku przewód parowy służący do powrotu tej pary. Drugi schładzacz wtryskowy posiada podkładkę ustalającą. Za ekranami wyjściowymi pierwszego stopnia znajduje się trzeci schładzacz wtryskowy Ш325*50, którego rurociąg parowy przepuszcza przepływy przez szerokość kanału gazowego. Następnie para kierowana jest do środkowych części kanału gazowego i po przejściu przez nie przesyłana jest rurociągiem parowym Sh325*60 o temperaturze 514°C wzdłuż szerokości kanału gazowego do ekranów wylotowych drugiego stopień, umieszczony wzdłuż krawędzi kanału gazowego. Za ekranami wyjściowymi drugiego stopnia para o temperaturze 523°C trafia do czwartego schładzacza wtryskowego Ř325*60. Zarówno ekrany wejściowe, jak i wyjściowe obu stopni przegrzewacza ekranowego mają bezpośredni wzór przepływu umożliwiający wzajemny ruch pary i gazów. Za schładzaczem para o temperaturze 537°C przewodem parowym Sh237*50 wchodzi do pakietu konwekcyjnego wykonanego w układzie bezpośredniego przepływu, przechodzi przez niego o temperaturze 545°C i doprowadzana jest do turbiny . Począwszy od komór wlotowych ekonomizera wody, wszystkie rury obejściowe i komory ścieżki SVD wykonane są ze stali 12Х1МФ. Za turbiną HPC para o ciśnieniu 39,5 atm. Temperatura 307°C jest przesyłana dwoma strumieniami do przegrzewacza pośredniego. Jedna „zimna” linia pary o niskim ciśnieniu zbliża się do obudowy; rozdzielają się one przed nagrzewnicą. Przegrzewacz każdej obudowy posiada dwa niskociśnieniowe strumienie pary z niezależną regulacją temperatury wzdłuż linii. Konstrukcja kotła Ściany komory spalania są całkowicie osłonięte rurami powierzchni grzewczych radiacyjnych. Komora spalania każdego budynku jest podzielona przewężeniami utworzonymi przez występy ekranów przednich i tylnych na komorę spalania (przedpalenisko) i komory dopalania. Ekrany w obszarze paleniska aż do wysokości. 15,00 w całości nabijana i pokryta masą chromitową. Izolacja komory spalania oraz sprężanie w palenisku ogranicza przenoszenie ciepła promieniowania z rdzenia palnika, co podnosi poziom temperatury w przedpiecu, a co za tym idzie, poprawia warunki zapłonu i spalania paliwa, a także przyczynia się do lepszego powstawanie ciekłego żużla. Proces spalania AS odbywa się głównie w przedpiecu, natomiast spalanie kontynuowane jest w komorze dopalania, gdzie dopalanie mechaniczne zmniejsza się z 7,5-10% do 2,5%. Tam temperatura gazu zostaje obniżona do 1210°C, co zapewnia pracę powierzchni grzewczych i przegrzewacza SVD bez tworzenia żużla. Naprężenie cieplne całej objętości spalania wynosi Vt=142*103 kcal m 3 /h, a przedpiecowego Vtp=491*103 kcal m/h.
Palenisko każdego z dwóch budynków wyposażone jest w 12 palników pyłowo-gazowych turbulentnych rozmieszczonych w dwóch poziomach (po trzy palniki na każdym poziomie przedniej i tylnej ściany paleniska). Dopływ gazu do palników jest peryferyjny, wydajność palnika pyłowego wynosi 0,5 t/godz. Każdy palnik turbulentny posiada wbudowaną dyszę oleju opałowego o mechanicznej atomizacji z chłodzeniem i zorganizowanym dopływem powietrza. Do usuwania ciekłego żużla w piecu wstępnym znajdują się dwa chłodzone otwory spustowe; komora przedpaleniskowa jest wykonana ze spadkiem 80° w stosunku do otworów spustowych i pokryta cegłami szamotowymi. Każdy piec wyposażony jest w dwa (w zależności od liczby otworów spustowych) zmechanizowane zespoły odżużlania. Ciekły żużel jest granulowany w łaźniach wodnych i usuwany do kanałów płuczących żużel. Środek suszący jest odprowadzany przez prostokątne palniki, które znajdują się na bocznych ścianach paleniska w dwóch poziomach: na niższym poziomie znajdują się 4 palniki, a na górnym 2. W piecu znajdują się włazy do prac naprawczych. Palenisko jest osłonięte w dolnej części do wysokości 23,00 m rurami dolnej części radiacyjnej (LRP), a w górnej części rurami górnej części radiacyjnej (URP) od sufitu. Rury tylnej i przedniej szyby NRF mają zagięcia, które tworzą zwężenie spalania. Tylna szyba VRCH w górnej części posiada występ, co poprawia aerodynamikę przepływu gazu na wyjściu z paleniska i częściowo chroni powierzchnie ekranów przed bezpośrednim promieniowaniem z paleniska. Przednie i tylne ekrany NRF są konstrukcyjnie identyczne, każdy ekran składa się z sześciu identycznych taśm, z połączonymi równolegle rurkami Ř42*6, materiał 12Х1МФ. Rurki taśmy najpierw osłaniają pod i dolną część paleniska, a następnie przemieszczają się do pionowego panelu NRF, gdzie wykonują pięć ruchów podnoszenia i opuszczania i wychodzą do górnej komory. Rury NRCh prowadzone są do strzelnic palników, studzienek kanalizacyjnych i wizjerów. Boczne ekrany NRF składają się z czterech paneli, które zostały zaprojektowane w następujący sposób.
Wychodząc z dolnej komory taśma złożona z 17 równolegle połączonych zwojów Ш42*5, materiał 12Х1МФ, najpierw zasłania dolną część bocznej ściany, następnie przesuwa się do części pionowej, gdzie wykonuje również pięć skoków podnoszenia i opuszczania , a następnie wychodzi do górnej komory. Przednie i tylne ekrany NRF posiadają dwie kondygnacje stałych mocowań w odległości 22,00 m i 14,5 m. Kompensacja rozszerzalności cieplnej następuje w wyniku zagięcia rury w miejscu ściskania. Ekrany boczne zawieszone są na stałych mocowaniach na wysokości 21,9 m i można je swobodnie opuszczać. Aby zapobiec przedostawaniu się poszczególnych rur do paleniska, ekrany posiadają pięć pasów ruchomych elementów mocujących. Przednie i tylne ekrany VRCH składają się również z wieloprzebiegowych paneli z ruchami pary podnoszącej i opuszczającej. Para doprowadzana jest do dolnej komory paneli i usuwana z górnych komór. Panele środkowe szyby przedniej i wszystkie panele ekranów bocznych składają się z ośmiu, a panele zewnętrzne szyby przedniej z dziewięciu równolegle połączonych rur tworzących taśmę. Panel tylnego ekranu magnetowidu w kształcie litery N składa się z dwudziestu rur połączonych równolegle. Wszystkie powierzchnie grzewcze VRF wykonane są z rur Ř42*5, materiał 12Х1МФ. Ekrany przednie i boczne VRF zawieszone są na stałych mocowaniach na wysokości 39,975 m i swobodnie rozszerzają się w dół. Tylny ekran magnetowidu ma dwa stałe mocowania 8,2 i 32,6. Kompensacja rozszerzalności cieplnej rur następuje w wyniku zagięcia rur w górnej części tylnego ekranu magnetowidu. Szyby przednie i boczne posiadają siedem rzędów ruchomych mocowań, tylne – trzy. Wszystkie ekrany NRF i VRF mają odstęp między rurami 45 mm. Sufit paleniska i górna część poziomego przewodu kominowego są osłonięte rurami przegrzewacza sufitowego. Łącznie 304 rury połączone równolegle (154 w ciągu) Ř32*4, materiał 12Х1МФ. Na długości rur przegrzewacza sufitowego znajduje się 8 rzędów łączników, które są przymocowane do ramy za pomocą prętów.
Przegrzewacze parowe ekranowe Na wylocie z pieca znajduje się przegrzewacz ekranowy, który składa się z dwóch rzędów sit. W rzędzie znajduje się 16 ekranów o rozstawie 630 mm, zawieszonych pionowo. Wzdłuż przepływu pary ekrany każdego stopnia są podzielone na wejściowe i wyjściowe, które znajdują się bliżej bocznych ścian przewodu kominowego. Konstrukcyjnie ekrany wlotowy i wylotowy pierwszego stopnia wykonane są identycznie (z wyjątkiem umiejscowienia armatury i rur obejściowych na komorach). Ekran pierwszego stopnia kotła 20 składa się z 42 wężownic Ř32*6, materiał rur to głównie 12Х1МФ, ale 11 wężownic zewnętrznych ma sekcję wylotową wykonaną z rur Ř32*6, materiał 1Х18Н12Т. Na kotle 19 ekranów pierwszego stopnia składa się z 37 wężownic, materiał 1Х18Н12Т. Aby nadać konstrukcji sztywność, ekran połączony jest za pomocą 5 zwojów, które posiadają listwy mocujące wykonane ze stali X20N14S2. Ekrany drugiego stopnia składają się z 45 cewek Ř32*6. Materiał ekranów wejściowych to 12Х1МФ, a pozostałe cewki wykonane są ze stali 1Х18Н12Т. Ekran jest połączony sześcioma cewkami. Komory wejściowa i wyjściowa, za wyjątkiem komór ekranów wyjściowych drugiego stopnia, połączone są w pojedyncze kolektory oddzielone przegrodą. Kamery zawieszone są na drążkach z belek ramy. Ściany komory obrotowej osłonięte są czterema blokami. Bloki wykonane są w formie taśm dwupętlowych. Każdy blok zawiera 38 równolegle połączonych cewek Ш32*6 z materiału 12Х1МФ, które są rozmieszczone poziomo. Bloki posiadają pasy usztywniające. Bloki zawiesza się za pomocą trzech rzędów (na blok) mocowań. W dolnym kanale gazowym znajdują się następujące powierzchnie grzewcze: pakiet konwekcyjny SVD, przegrzewacz ND z wymiennikiem ciepła gaz-para oraz ekonomizer wody. Dla wszystkich powierzchni konwekcyjnych akceptowany jest schodkowy układ wężownic. Wszystkie powierzchnie wykonane są z wężownic równoległych do przodu kotła.
Przegrzewacz konwekcyjny SVD
Pakiet przegrzewaczy konwekcyjnych SVD każdej linii składa się ze 129 wężownic Ш32*6 z materiału 1Х18Н12Т, które spoczywają na stojakach z materiału Х23Н13 i na belkach nośnych, chłodzonych wodą zasilającą. Aby podeprzeć stopnie i zwiększyć sztywność konstrukcji, zastosowano trzy rzędy listew dystansowych wykonanych ze stali 1Х18Н12Т, wysokość pakietu wynosi 557 mm. Przegrzewacz niskociśnieniowy Za pakietem konwekcyjnym SVD znajduje się przegrzewacz LP. Pakiety każdego strumienia są umieszczone w odpowiednich połówkach kanału wylotowego; strumienie nie są przenoszone na szerokość kanału. Przegrzewacz LP składa się z zespołu wyjściowego, zespołu pośredniego i stopnia sterującego. Część wyjściową przegrzewacza ND składa się z 108 podwieszanych wężownic Ř42*3,5, wykonanych ze stali łączonej: Kh2MFSR i 12Kh1MF. Cewki są montowane w pakiety ze stojakami z materiału X17N2, które są zawieszone na kolektorach nośnych pakietu wysokociśnieniowego. Wysokość opakowania 880 mm. Pakiet pośredni składa się również ze 108 podwójnych cewek Ř42*3,5 podwójnych cewek Ř42*3,5, materiał 12Х1МФ. Wysokość opakowania 1560 mm. Cewki spoczywają na stojakach z materiału X17N2, a te na komorach wlotowych pakietu pośredniego Ш325*50, materiał 12Х1МФ. Zatem komory wejściowe pakietu przemysłowego są jednocześnie belkami nośnymi dla tej powierzchni grzewczej. Komory oprócz izolacji posiadają dodatkowe chłodzenie powietrzem, które jest niezbędne podczas trybów rozruchu oraz przy wyłączonej turbinie. Za pakietem przemysłowym wzdłuż przepływu gazu po obu korpusach kotłów TPP-210 zamiast GPP TO zainstalowany jest stopień regulacyjny będący pierwszym stopniem przegrzewacza na przepływie pary, wykonany ze stali perlitycznej i w w celu zapewnienia niezawodnej pracy rurociągów w przypadku znacznego parowania, znajduje się w strefie, w której temperatura gazu na wlocie nie powinna przekraczać 600°C. Jego działanie w całości opiera się na zmianie pochłaniania ciepła przez parę wtórną poprzez zmianę jej dystrybucji poprzez obejściowe linie parowe. Według obliczeń przy obciążeniu znamionowym urządzenia 20% całkowitego przepływu pary przechodzi przez stopień kontrolny. Przy zmniejszeniu obciążenia jednostki do 70% zużycie pary wynosi 88%. Zwiększoną sprawność bloku osiąga się poprzez poszerzenie zakresu obciążeń, przy którym zapewniona jest obliczona temperatura przegrzania wtórnego przy optymalnym nadmiarze powietrza. Powierzchnia sterująca jest zamontowana w wymiarach zdemontowanego GPP TO, kolektory wejściowe są obniżone o 300 mm niżej. Powierzchnia sterująca składa się z części lewej i prawej, a całkowita powierzchnia grzewcza wynosi 2020 m² na obudowę. Obie części są zmontowane z pakietów podwójnych wężownic i mają 4 pętle wzdłuż przepływu gazów z przeciwprądowym ruchem pary. Wężownice wykonane są z rur Ř32*4, stali 12Х1МФ i są ułożone w szachownicę z odstępami 110 i 30 mm. Cewki montowane są w pakiety przy użyciu tłoczonych stojaków ze stali 12X13. Na całej długości każdego opakowania znajduje się 5 stojaków. Dwa z nich zamontowane są na kolektorach chłodzonych wodą, umieszczonych w kanale gazowym, które podczas naprawy są obniżone o 290 mm. Para z HPC wchodzi do komór wlotowych powierzchni sterującej Ш425*20 stal 20. Po przejściu przez wężownice para wchodzi do komór wylotowych o średnicy 426*20 ze stali 12Х1МФ, gdzie miesza się z parą pochodzącą z pary obejściowej linia. Stare zawory RKT wycięto wzdłuż gwintów „B” i „C”, ze starych zaworów RKT usunięto części wewnętrzne, a korpusy RKT zespawano i wykorzystano jako trójniki. Na linii obejściowej pomiędzy kolektorem dolotowym i wylotowym zamontowane są nowe zawory zasuwowe typu RKT. Gdy zawór jest otwarty do 100%, 80% pary przechodzi przez powierzchnię kontrolną i ciśnienie spada. Gdy zawór jest zamknięty, para przepływa przez powierzchnię kontrolną, a temperatura ponownego nagrzewania wzrasta. Zawory sterujące i klawisze sterujące w nowych RKT pozostają takie same. Wymieniono wężownice oszczędzacza wody w obu korpusach (100%). Z drugich kolektorów wtryskowych usunięto podkładki ustalające i odłączono wyloty do GPP TO. Ekonomizer konwekcyjny jest ostatnią powierzchnią grzewczą wzdłuż przepływu spalin, umieszczoną w kanale spalin. Składa się z rur Ř32*6, materiał st20. Komora wyjściowa i wejściowa ekonomizera są jednocześnie belkami nośnymi - ciężar tej powierzchni grzewczej przenoszony jest na nie poprzez zębatki. Rama kotła wykonana jest w formie identycznych ram obu budynków, połączonych ze sobą połączeniami międzykadłubowymi i rusztowaniami przejściowymi. Ciężar powierzchni grzewczej, okładziny i izolacji przenoszony jest za pomocą poziomych belek i kratownic na trzy rzędy słupów pionowych, jeden rząd z przodu kotła, drugi pomiędzy paleniskiem a kanałami spalinowymi i trzeci z tyłu kotła. bojler. Aby wzmocnić ramę, zastosowano szereg nachylonych belek. Wykładzina komina i kanałów kotła wykonana jest w formie oddzielnych paneli. Palenisko i przewody kominowe osłonięte są blachą o grubości 3 mm, co zapewnia dużą gęstość paleniska i przewodów kominowych.
Za przedmiot regulacji uważa się kocioł parowy o przepływie bezpośrednim TPP-210A, analizuje istniejące układy sterowania, wskazuje jego zalety i wady, schemat blokowy regulatora obciążenia cieplnego kotła na paliwo gazowe TPP-210A z wykorzystaniem regulatora Proponuje się sterownik mikroprocesorowy Remikont R-130
Przeprowadzono obliczenia parametrów nastawczych i modelowanie procesu regulacji obciążenia cieplnego kotła TPP-210A na paliwie gazowym, w tym aproksymację danych eksperymentalnych i modelowanie obiektu regulacyjnego dla układu regulacji dwuobwodowej, obliczenie parametrów nastawczych układów sterowania dwuobwodowego, a także modelowanie procesu nieustalonego w regulacji układów dwuobwodowych. Przeprowadzono analizę porównawczą uzyskanych charakterystyk przejściowych.
Fragment tekstu
Pod względem stopnia automatyzacji energetyka cieplna zajmuje jedną z czołowych pozycji wśród innych gałęzi przemysłu. Elektrownie cieplne charakteryzują się ciągłością procesów w nich zachodzących. Prawie wszystkie operacje w elektrowniach cieplnych są zmechanizowane i zautomatyzowane.
Automatyzacja parametrów zapewnia wymierne korzyści
Wykaz używanej literatury
Bibliografia
1. Grigoriew V.A., Zorin V.M. „Elektrownie cieplne i jądrowe”. Informator. - M.: Energoatomizdat, 1989.
2. Pletnev G. P. Zautomatyzowane systemy sterowania dla elektrowni cieplnych: Podręcznik dla uniwersytetów / G. P. Pletnev. — wyd. 3, poprawione. i dodatkowe - M.: Wydawnictwo. MPEI, 2005, - 355 s.
3. Pletnev T.P. Automatyzacja procesów technologicznych i produkcji w energetyce cieplnej. /MPEI. M. 2007. 320 s.
4. Małokanałowy wielofunkcyjny regulator mikroprocesorowy Remikont R-130″ Zestaw dokumentacji YALBI.421 457.001TO 1−4
5. Pletnev G.P. Zaichenko Yu.P. „Projektowanie, montaż i eksploatacja zautomatyzowanych systemów sterowania procesami ciepłowniczymi i energetycznymi” MPEI 1995 316 s. - il.
6. Rotach V.Ya. Teoria automatycznego sterowania procesami cieplnymi i energetycznymi, - M.: MPEI, 2007. - 400 s.
7. Kozlov O.S. itp. Pakiet oprogramowania „Modelowanie w urządzeniach technicznych” (PC „MVTU”, wersja 3.7).
Instrukcja obsługi. - M.: MSTU im. Baumana, 2008.
Fil S.A., Golyshev L.V., inżynierowie, Mysak I.S., doktor inżynier. Sciences, Dovgoteles G. A., Kotelnikov I. I., Sidenko A. P., inżynierowie OJSC LwówORGRES - Narodowy Uniwersytet „Politechnika Lwowska” - Trypilska TPP
Spalanie niskoreaktywnych węgli kamiennych (lotny uzysk Vdaf< 10%) в камерных топках котельных установок сопровождается повышенным механическим недожогом, который характеризуется двумя показателями: содержанием горючих в уносе Гун и потерей тепла от механического недожога q4.
Zazwyczaj pistolet jest oznaczany metodą laboratoryjną na podstawie pojedynczych próbek popiołu pobranych z kanałów spalinowych ostatniej powierzchni konwekcyjnej kotła przy użyciu standardowych urządzeń porywujących. Główną wadą metody laboratoryjnej jest zbyt duże opóźnienie w uzyskaniu wyniku Gongu (ponad 4 – 6 godzin), na które składa się czas powolnego gromadzenia się próbki popiołu w komorze muchowej oraz czas trwania analizy laboratoryjnej. Zatem w jednej próbce popiołu sumują się wszystkie możliwe zmiany w pistoletach w długim okresie czasu, co utrudnia szybkie i skuteczne dostosowanie i optymalizację reżimu spalania.
Z danych wynika, że w zmiennych i niestacjonarnych trybach pracy kotła współczynnik popiołów (stopień oczyszczenia) cyklonu, czyli wartość zadana usuwania popiołu, waha się w granicach 70 – 95%, co prowadzi do dodatkowych błędów w wyznaczaniu Gong.
Wady instalacji popiołów lotnych eliminowane są poprzez wprowadzenie systemów ciągłego pomiaru Gongu, np. analizatorów węgla w popiele lotnym.
W 2000 roku osiem zestawów (po dwa na każdy budynek) stacjonarnych, pracujących w sposób ciągły analizatorów RCA-2000 firmy Mark i Wedell (Dania).
Zasada działania analizatora RCA-2000 opiera się na metodzie fotoabsorpcyjnej analizy w zakresie podczerwieni widma.
Zakres pomiarowy 0 - 20% bezwzględnych wartości Gongu, względny błąd pomiaru w zakresie 2 - 7% - nie więcej niż ± 5%.
Próbki popiołu do układu pomiarowego analizatora pobierane są z kanałów gazowych przed elektrofiltrami.
Rejestrację gongów ciągłych przeprowadzono na rejestratorze w sterowni z częstotliwością pełnego cyklu pomiarowego co 3 minuty.
Podczas spalania popiołu o zmiennym składzie i jakości rzeczywiste wartości bezwzględne Gongu z reguły przekraczały 20%. Dlatego obecnie analizatory wykorzystuje się jako wskaźniki zmian względnych wartości zawartości materiałów palnych w porywaniu Gv° w skali rejestratora 0 – 100%.
W celu przybliżonej oceny rzeczywistego poziomu Gongu opracowano charakterystykę kalibracyjną analizatora, która przedstawia zależność pomiędzy wartościami bezwzględnymi Gong określonymi metodą laboratoryjną a wartościami względnymi analizatora Gong. W zakresie zmian Gongu od 20 do 45% charakterystykę w postaci analitycznej wyraża równanie
Podczas badań eksperymentalnych i normalnej pracy kotła analizatory mogą służyć do wykonywania następujących prac:
optymalizacja trybu spalania;
ocena zmian Gongu podczas planowanych przełączeń technologicznych systemów i jednostek kotłowni;
określenie dynamiki i stopnia obniżenia sprawności w trybie niestacjonarnym, porozruchowym kotła, a także podczas naprzemiennego spalania popiołów i gazu ziemnego.
W trakcie badań cieplnych kotła wykorzystano analizatory do optymalizacji sposobu spalania oraz oceny wpływu planowanych załączeń urządzeń na stabilność procesu spalania pyłu węglowego.
Doświadczenia przeprowadzono przy stacjonarnych obciążeniach kotła w zakresie 0,8-1,0 nominalnej oraz spalaniu popiołu o następujących charakterystykach: dolne ciepło właściwe spalania Qi = 23,06 - 24,05 MJ/kg (5508 - 5745 kcal/kg), zawartość popiołu przy masa robocza Ad = 17,2 - 21,8%, wilgotność na masę roboczą W = 8,4 - 11,1%; udział gazu ziemnego do oświetlenia pochodni pyłowej wynosił 5-10% całkowitego wydzielonego ciepła.
Podano wyniki i analizę eksperymentów mających na celu optymalizację reżimu spalania za pomocą analizatorów. Podczas ustawiania kotła zoptymalizowano:
prędkości wylotu powietrza wtórnego poprzez zmianę otwarcia przepustnic obwodowych w palnikach;
prędkości wylotu powietrza pierwotnego poprzez zmianę obciążenia wentylatora nadmuchowego;
udział oświetlenia pochodni gazem ziemnym poprzez dobór (zgodnie z warunkami zapewnienia stabilności spalania) minimalnej możliwej liczby pracujących palników gazowych.
Główne charakterystyki procesu optymalizacji trybu spalania podano w tabeli. 1.
Podane w tabeli. 1 dane wskazują na ważną rolę analizatorów w procesie optymalizacji, który polega na ciągłym pomiarze i rejestrowaniu bieżących informacji o zmianach G°, co pozwala na terminowe i
wyraźnie rejestruje tryb optymalny, zakończenie procesu stabilizacji i rozpoczęcie pracy kotła w trybie optymalnym.
Podczas optymalizacji reżimu spalania główną uwagę zwrócono na znalezienie minimalnego możliwego poziomu względnych wartości G°un. W tym przypadku wartości bezwzględne Gongu wyznaczono z charakterystyki kalibracyjnej analizatora.
Zatem skuteczność wykorzystania analizatorów do optymalizacji trybu spalania kotła można z grubsza ocenić poprzez zmniejszenie zawartości materiałów palnych w porwaniu średnio o 4% i strat ciepła na skutek niedopalenia mechanicznego o 2%.
W stacjonarnych trybach kotła wykonywanie standardowych przełączeń technologicznych np. w instalacjach pyłowych czy urządzeniach palnikowych zakłóca proces stabilnego spalania pyłu węglowego.
Tabela 1
Charakterystyka procesu optymalizacji trybu spalania
Kocioł TPP-210A wyposażony jest w trzy układy odpylające z młynami bębnowo-kulowymi typu ShBM 370/850 (Sh-50A) oraz wspólnym pojemnikiem na śmieci.
Z układu pyłowego zużyty środek suszący odprowadzany jest za pomocą wentylatora młyna typu MV 100/1200 do komory spalania (przedpieca) poprzez specjalne dysze odprowadzające umieszczone nad głównymi palnikami pyłowymi i gazowymi.
Przedpiec każdego korpusu kotła jest odprowadzany w całości z odpowiedniego układu pyłu skrajnego i połowa z układu pyłu środkowego.
Zużytym środkiem suszącym jest niskotemperaturowe nawilżone i zapylone powietrze, którego główne parametry mieszczą się w następujących granicach:
udział powietrza wywiewanego wynosi 20 - 30% całkowitego zużycia powietrza w obudowie (kotle); temperatura 120 - 130°C; udział miału węglowego, który nie został wychwycony przez cyklon instalacji pyłowej, 10 - 15% wydajności młyna;
Wilgotność odpowiada ilości wilgoci wydzielającej się podczas procesu suszenia zmielonego paliwa roboczego.
Zużyty środek suszący odprowadzany jest do strefy maksymalnych temperatur płomienia, co znacząco wpływa na kompletność dopalenia miału węglowego.
Podczas pracy kotła najczęściej wyłączany i ponownie uruchamiany jest środkowy układ pyłowy, za pomocą którego utrzymywany jest wymagany poziom zapylenia w pojemniku na śmieci.
Przedstawiono dynamikę zmian głównych wskaźników trybu spalania korpusu kotła – zawartości substancji palnych w porywaczu oraz stężenia masowego tlenków azotu w spalinach (NO) – podczas planowanego postoju instalacji pyłowej przeciętnej na ryc. 1.
Na powyższym i wszystkich kolejnych rysunkach przy konstruowaniu zależności graficznych przyjęte są następujące warunki:
zawartość substancji palnych w porwaniu odpowiada wartościom skal dwóch pionowych osi współrzędnych: uśrednionym pomiarom pistoletu i danym przeliczeniowym zgodnie z charakterystyką kalibracyjną pistoletu;
stężenie masowe NO w nadmiarze powietrza w spalinach (bez redukcji do NO2) pobrano z rejestrowanych w sposób ciągły pomiarów stacjonarnego analizatora gazów Mars-5 MP „Ekomak” (Kijów);
dynamika zmian G°un i NO jest ustalona na poziomie
przez cały okres eksploatacji technologicznej i trybu stabilizacji; przyjmuje się, że początek operacji technologicznej przypada w pobliżu czasu zerowego.
Kompletność spalania pyłu węglowego oceniano na podstawie jakości reżimu spalania (KFC), którą analizowano za pomocą dwóch wskaźników Gun i NO, które z reguły zmieniały się w lustrzanie przeciwnych kierunkach.
Ryż. 1. Zmiany wskaźników trybu spalania przy zatrzymaniu układu średniego pyłu
Analizowano wpływ planowanego postoju instalacji średniopyłowej na wskaźniki WRC (rys. 1) w zależności od kolejności wykonywania następujących operacji technologicznych:
operacja 1 - zatrzymanie podajnika węgla surowego (CCF) i zatrzymanie dopływu węgla do młyna spowodowało zmniejszenie obciążenia bębna CBM, zmniejszenie rozdrobnienia miału węglowego oraz podwyższenie temperatury powietrza odpadowego, co spowodowało krótkotrwałe poprawa CTE: spadek Gun° i wzrost NO; proces dalszej emaskulacji młyna przyczynił się do usunięcia pyłu z powietrza odpadowego i wzrostu nadmiaru powietrza w przedpiecu, co niekorzystnie wpłynęło na współczynnik WRC;
operacja 2 - zatrzymanie wentylatora młyna i zmniejszenie przewietrzania układu pyłowego najpierw nieznacznie poprawiło WRC, a następnie z opóźnieniem w wyłączeniu wentylatora młyna (MF) WRC uległ pogorszeniu;
operacja 3 - zatrzymanie SN i zatrzymanie zrzutu zużytego środka suszącego do komory spalania znacząco poprawiło współczynnik CTE.
Tym samym, przy pozostałych parametrach zatrzymanie układu odpylającego usprawniło proces spalania paliwa, redukując podpalenie mechaniczne i zwiększając stężenie masowe NO.
Typowym naruszeniem stabilności układu pyłowego jest przeciążenie bębna młyńskiego paliwem lub „zasmarowanie” kul mielących mokrym materiałem gliniastym.
Wpływ długotrwałego wysychania bębna młyna walcowo-czołowego na WRC korpusu kotła przedstawiono na rys. 2.
Zatrzymanie zasilacza (operacja 1) z powodów podobnych do rozpatrywanych przy zatrzymywaniu układu odpylającego, w pierwszym etapie kasowania młyna, krótkoterminowo poprawiło współczynnik CTE. Podczas późniejszej kastracji młyna aż do włączenia zasilacza (operacja 2) zaobserwowano tendencję do pogorszenia CTE i wzrostu G°un.
Ryż. 2. Zmiany warunków spalania po opróżnieniu bębna młyna palcowego
Ryż. 3. Zmiany wskaźników trybu spalania przy uruchomieniu układu skrajnego zapylenia i wyłączeniu palników gazowych
W mniejszym stopniu automatyczna praca zasilacza okresowo destabilizuje tryb spalania, który reguluje niezbędne ładowanie młyna węglem poprzez wyłączenie i ponowne załączenie napędu zasilacza.
Wpływ trybu rozruchu układu ekstremalnie zapylonego na WRC pokazano na rys. 3.
Stwierdzono następujący wpływ rozruchów układu odpylającego na tryb spalania:
operacja 1 - uruchomienie SN i przewietrzanie (rozgrzanie) ścieżki układu pyłowego wraz z wpuszczeniem do przedpieca stosunkowo zimnego powietrza spowodowało zwiększenie nadmiaru powietrza w strefie spalania i obniżenie temperatury płomienia, co doprowadziło do pogorszenia współczynnik CTE;
operacja 2 - uruchomienie BBM i kontynuacja wentylacji ciągu miało negatywny wpływ na WRC;
operacja 3 - uruchomienie zasilacza i załadowanie młyna paliwem wraz ze wzrostem zużycia środka suszącego do zużycia nominalnego znacznie pogorszyło współczynnik CTE.
Można stwierdzić, że włączenie działającej instalacji pyłowej wpływa negatywnie na współczynnik CTE, zwiększając mechaniczne niedopalenie i zmniejszając stężenie masowe NO.
Przedpalenisko korpusu kotła TPP-210A wyposażone jest w sześć spiralnych palników pyłowo-gazowych o mocy cieplnej 70 MW, zamontowanych w jednej kondygnacji na ścianie przedniej i tylnej oraz dwa nadziemne palniki na olej napędowy zapewniające stabilne usuwanie ciekłego żużla w całym zakresie obciążeń eksploatacyjnych kotła.
Podczas spalania miału popiołowego gaz ziemny dostarczany był ze stałym natężeniem przepływu (około 5% całkowitego wydzielonego ciepła) do palników napowietrznych oraz ze zmiennym natężeniem przepływu przez główne palniki pyłowo-gazowe w celu stabilizacji procesu spalania pyłu węglowego paliwo. Do każdego palnika głównego doprowadzano gaz z minimalnym możliwym natężeniem przepływu, odpowiadającym 1,0 - 1,5% całkowitego wydzielanego ciepła. Dlatego zmianę udziału gazu ziemnego do oświetlania pochodni realizowano poprzez włączanie lub wyłączanie określonej liczby głównych palników gazowych.
Wpływ wyłączenia palników gazowych (zmniejszenie udziału gazu ziemnego) na współczynnik CTE korpusu kotła przedstawiono na rys. 3.
Kolejne wyłączenie najpierw jednego palnika gazowego (operacja 4), a następnie trzech palników gazowych (operacja 5) wpłynęło pozytywnie na współczynnik CTE i spowodowało znaczne zmniejszenie niedopalenia mechanicznego.
Wpływ włączenia palników gazowych (zwiększających udział gazu ziemnego) na WRC przedstawiono na rys. 4. Sekwencyjne załączenie jednego palnika gazowego (operacja 1), dwóch palników (operacja 2) i jednego palnika (operacja 3) wpłynęło negatywnie na współczynnik WRC i znacznie zwiększyło niedopalenie mechaniczne.
Ryż. 4. Zmiany wskaźników trybu spalania przy włączaniu palników gazowych
Tabela 2
Zmiany zawartości materiałów palnych w porywaniu podczas przełączania procesów urządzeń
Sprzęt | Tryb | ||
zmniejszenie | zwiększyć |
||
System ekstremalnego/średniego zapylenia | |||
Wykastrowanie | Nagły wypadek | ||
Podajnik surowy | |||
Główny palnik gazowy | Zamknięcie | ||
Włączenie |
Przybliżoną ocenę wpływu sprawdzonego przełączenia technologicznego urządzeń kotłowych na zmianę współczynnika WRC (Kun) podsumowano w tabeli. 2.
Z analizy przedstawionych danych wynika, że największy spadek sprawności instalacji kotłowej w trybie stacjonarnym następuje w wyniku uruchomienia pracy układu odpylającego oraz przy nadmiernym zużyciu gazu ziemnego do oświetlenia pochodni.
Należy zaznaczyć, że konieczność przeprowadzenia czynności rozruchowych instalacji odpylającej podyktowana jest wyłącznie względami technologicznymi, a nadmierne zużycie gazu ziemnego do oświetlania pochodni ustalane jest z reguły przez obsługę, tak aby zapobiec ewentualnym naruszenie stabilności procesu spalania w przypadku nagłego pogorszenia jakości komory spalania.
Zastosowanie analizatorów RCA-2000 pozwala na ciągłe zmiany w odpowiednim czasie
ocenić wszelkie zmiany w jakości paliwa i stale utrzymywać wartość świecenia płomienia na odpowiednim optymalnym poziomie przy minimalnym wymaganym zużyciu gazu ziemnego, co pozwala zmniejszyć zużycie deficytowego paliwa gazowego i zwiększyć wydajność kotła.
wnioski
- System ciągłego pomiaru zawartości substancji palnych w naciągu umożliwia szybką i jakościową ocenę przebiegu procesów spalania podczas spalania popiołów w kotle TPP-210A, co jest zalecane do stosowania podczas prac rozruchowych i badawczych, a także do systematycznego monitorowania sprawności urządzeń kotłowych.
- Skuteczność wykorzystania analizatorów RCA-2000 do optymalizacji warunków spalania szacuje się w przybliżeniu poprzez zmniejszenie wskaźników niedopalenia mechanicznego - zawartość substancji palnych w porwaniu średnio o 4% i odpowiednio strat ciepła na skutek niedopalenia mechanicznego o 2%.
- W stacjonarnych trybach kotła standardowe przełączanie technologiczne urządzeń wpływa na jakość procesu spalania. Operacje rozruchowe układu odpylającego oraz nadmierne zużycie gazu ziemnego do oświetlenia palnika pyłowego znacznie zmniejszają sprawność instalacji kotłowej.
Bibliografia
- Madoyan A. A., Baltyan V. N., Grechany A. N. Efektywne spalanie węgli niskiej jakości w kotłach energetycznych. M.: Energoatomizdat, 1991.
- Wykorzystanie analizatora porywania gazów palnych RCA-2000 i analizatora gazów Mars-5 do optymalizacji trybu spalania kotła pyłowego TPP-210A w Tripolskaya TPP/Golyshev L.V., Kotelnikov N.I., Sidenko A.P. i in. Kijowski Instytut Politechniczny. Energia: ekonomia, technologia, ekologia, 2001, nr 1.
- Zusin S.I. Zmiana strat ciepła przy dopalaniu mechanicznym w zależności od trybu pracy zespołu kotłowego. - Elektroenergetyka Cieplna, 1958, nr 10.
Technologia uruchamiania kotłów przepływowych różni się od tej tym, że nie mają one obiegu zamkniętego, nie ma bębna, w którym para byłaby w sposób ciągły oddzielana od wody i w którym utrzymywałby się określony zapas wody przez pewien czas. Realizowany jest w nich jednorazowy wymuszony obieg medium. Dlatego podczas zapalania (i pracy pod obciążeniem) należy zapewnić ciągły wymuszony ruch czynnika przez ogrzewane powierzchnie i jednocześnie usunąć ogrzany czynnik z kotła i rozpocząć ruch wody w rurach jeszcze przed zapaleniem się palników.
W tych warunkach o sposobie rozpalania decyduje w całości niezawodność, odpowiednie warunki temperaturowe rur metalowych sit, ekranów, przegrzewaczy pary oraz brak niedopuszczalnych pomiarów termohydraulicznych.
Doświadczenie i obliczenia wykazały, że chłodzenie powierzchni grzewczych podczas uruchamiania kotła przepływowego jest niezawodne, jeśli przepływ wody rozpałowej wynosi co najmniej 30% przepływu nominalnego. Przy tym natężeniu przepływu zapewniona jest minimalna prędkość masowa medium na sitach, 450-500 kg/(m2*s), zgodnie z warunkami niezawodności. Minimalne ciśnienie czynnika w ekranach należy utrzymywać w pobliżu nominalnego, tj. dla kotłów 14 MPa - na poziomie 12-13 MPa, a dla kotłów na ciśnienie nadkrytyczne - 24-25 MPa.
Istnieją dwa główne sposoby opalania kotłów jednoprzejściowych: przepływ bezpośredni i separator.
W trybie spalania bezpośredniego czynnik roboczy przepływa przez wszystkie powierzchnie grzewcze kotła, podobnie jak przy pracy kotła pod obciążeniem. W pierwszym okresie rozpalania czynnik ten usuwany jest z kotła poprzez ROU, a po wytworzeniu pary o wymaganych parametrach kierowany jest do głównego rurociągu parowego lub bezpośrednio do turbiny (w zakładach blokowych).
Poniższe rysunki przedstawiają uproszczony schemat uruchomienia kotła ze stanu „zimnego” w trybie przepływu bezpośredniego:
Kolejny rysunek poniżej przedstawia zmiany przepływu wody zasilającej (1), ciśnienia pary za kotłem (2), temperatury czynnika (3), pary świeżej (4) i pary wtórnej (5) oraz temperatury metalu pierwotnego (7) ) i ekrany wtórne (5) przegrzewaczy. Jak widać, na początku rozpałki, gdy ciśnienie pary osiąga wartość 4 MPa, temperatura medium i metalu w ekranach przegrzewacza pośredniego gwałtownie spada z 400 do 300-250°C, co stanowi wyjaśnione otwarciem ROU w celu zrzutu czynnika do systemu drenażowego, a na końcu rozpałki przy ciśnieniu na całej ścieżce pierwotnej 23-24 MPa, warunkami pracy ekranów przegrzewaczy pierwotnego i wtórnego, których temperatura przekracza 600°C, również gwałtownie się pogarszają.
Nadmiernego wzrostu temperatury sit metalowych można uniknąć jedynie zwiększając przepływ wody zapłonowej, a co za tym idzie, zwiększając straty kondensatu i ciepła w porównaniu do trybu rozruchu separatora. Biorąc to pod uwagę, a także fakt, że schemat bezpośredniego przepływu uruchamiania kotła ze stanu „zimnego” nie ma żadnych zalet w porównaniu z separatorem, nie jest on obecnie stosowany do rozruchu.
Tryb bezpośredniego rozruchu kotła przepływowego ze stanu „gorącego” i „niechłodzonego” stwarza niebezpieczeństwo nagłego ochłodzenia najgorętszych elementów kotła i rurociągów pary, a także niedopuszczalnego wzrostu temperatury metalu przegrzewacza w trybie bezprzepływowym z zamkniętymi BROU i ROU w pierwszym okresie rozpalania. Wszystko to utrudnia rozruch ze stanu „gorącego”, dlatego tryb ten został zastąpiony układem rozruchowym separatora.
Jedynym obszarem zastosowania trybu rozruchu bezpośredniego jest rozpalanie kotła dwuzbiornikowego ze stanu „zimnego” oraz rozruch kotła bezpośredniego z rezerwy gorącej po okresie postoju do 1 godziny.
Uruchamiając kocioł dwuzbiornikowy, oba korpusy ogrzewane są naprzemiennie: kotły asymetryczne (na przykład TPP-110) ogrzewane są począwszy od obudowy, która nie posiada przegrzewacza wtórnego. Korpusy kotłów symetrycznych nagrzewają się w losowej kolejności. Pierwszy korpus obu typów kotłów dwupłaszczowych ogrzewany jest w trybie separatora. Rozpalanie drugiego korpusu rozpoczyna się od małego obciążenia elektrycznego bloku i odbywa się w dowolnym trybie.
Kocioł można rozpalić po krótkiej (do 1 godziny) przerwie w trybie bezpośredniego przepływu, gdyż parametry pary zachowują nadal swoje wartości eksploatacyjne, a poszczególne elementy i podzespoły kotła nie miały czasu na znaczne ochłodzenie. W takim przypadku należy preferować tryb bezpośredniego przepływu, ponieważ nie wymaga on specjalnego przygotowania, jakie byłoby wymagane przy przejściu na obieg separacyjny, co pozwala zyskać na czasie i przyspieszyć rozruch kotła. W tym przypadku rozpałka odbywa się w trybie przepływu bezpośredniego z wypuszczeniem całego czynnika roboczego przez ROU lub BROU przez główny zawór pary (MSV), aż temperatura pary pierwotnej i wtórnej przekroczy temperaturę turbiny wlocie pary o około 50°C. Jeżeli temperatura pary w czasie postoju bloku spadnie o mniej niż 50°C, temperatura pary za kotłem zostaje natychmiast podniesiona do wartości nominalnej, po czym następuje przełączenie dopływu pary z ROU do turbiny.
Uruchamiając w ten sposób kocioł z gorącej rezerwy należy mieć na uwadze, że podczas krótkotrwałego postoju kotła wyrównuje się temperatura czynnika na wlocie i wylocie wielu rur sitowych i następuje naturalna cyrkulacja kotła. medium występuje wewnątrz poszczególnych paneli i pomiędzy panelami. Cyrkulacja ta może być tak trwała, że utrzymuje się przez pewien czas po ponownym uruchomieniu pomp zasilających. W efekcie minie trochę czasu, zanim środowisko pracy zacznie stale zmierzać w pożądanym kierunku. Do czasu ustania niestabilnego ruchu czynnika nie zaleca się rozpoczynania rozpalania kotła, aby uniknąć uszkodzenia ogrzewanych rur.
W porównaniu z trybem rozruchu kotła z separatorem bezpośrednim przepływowym charakteryzuje się dużą stabilnością, stosunkowo niskimi temperaturami czynnika roboczego i metalu na całej drodze kotła oraz pozwala na rozruch turbiny przy zmiennych parametrach pary. Sita przegrzewacza pośredniego kotła zaczynają się stygnąć już w początkowej fazie rozruchu, a ich metal nie przegrzewa się do niedopuszczalnych wartości. Rozruch separatora odbywa się za pomocą specjalnego urządzenia rozpałkowego, tzw. zespołu rozpalającego, składającego się z wbudowanego zaworu (2), wbudowanego separatora (7), rozpałki (9) i przepustnicy zawory 5, 6, 8. Separator zabudowany przeznaczony jest do oddzielania wilgoci od pary wodnej i jest rurą o dużym przekroju (425×50 mm), w której zamontowany jest separator wilgoci śrubowy, który jest włączany podczas okres rozpalania kotła pomiędzy powierzchnią wytwarzającą parę (1) i przegrzewającą parę (3) kotła poprzez urządzenia dławiące 5 i 6. Wbudowany zawór 2 służy do odłączenia ekranów i przegrzewacza konwekcyjnego od powierzchni grzewczych wytwarzających parę i znajduje się pomiędzy urządzeniami wyjściowymi ostatniej sekcji powierzchni ekranowych a kolektorami wejściowymi przegrzewaczy ekranowych. Podczas rozpalania kotła główny zawór pary (4) w bloku blokowym pozostaje otwarty, a w usieciowanym TPP zamknięty.
Ekspander zapłonu stanowi stopień pośredni pomiędzy wbudowanym separatorem a urządzeniami do odbioru medium odprowadzanego z separatora. Ponieważ w rozprężaczu utrzymuje się niższe ciśnienie niż w separatorze (zwykle około 2 MPa), czynnik roboczy jest do niego wprowadzany przez przepustnicę 8 i po wielokrotnym dławieniu częściowo odparowuje. Para z rozprężacza zapłonu kierowana jest do kolektora pomocniczego stacji, skąd może być doprowadzana do odgazowywaczy i innych odbiorców, a woda odprowadzana jest do kanału wylotowego wody obiegowej, do rezerwowego zbiornika kondensatu lub (w instalacjach blokowych) bezpośrednio do skraplacza.
Ideą rozruchu separatora kotła przepływowego jest podzielenie procesu rozruchu na trzy fazy, tak aby w każdej z tych kolejno prowadzonych faz była w pełni zapewniona niezawodność wszystkich powierzchni grzewczych, a w w ostatniej fazie możliwe staje się uruchomienie urządzeń energetycznych bloku przy zmiennych parametrach pary, przy jednoczesnym utrzymaniu stałego ciśnienia nominalnego powierzchni wytwarzających parę.
W pierwszej fazie rozruchu wymuszony obieg czynnika roboczego zorganizowany jest w obiegu zamkniętym: pompa zasilająca - kocioł - jednostka pilotowa - urządzenia odbiorcze czynnika tłocznego (w instalacji blokowej, skraplacz turbinowy) - pompa zasilająca. Eliminuje to możliwość niebezpiecznych wierceń termiczno-hydraulicznych w powierzchniach wytwarzających parę, a straty kondensatu i ciepła są zminimalizowane. Podczas tej fazy rozruchu czynnik roboczy nie ma dostępu do powierzchni przegrzania pary, ponieważ są one odcięte od powierzchni wytwarzających parę przez wbudowany zawór i przepustnicę 17, zamknięte w tym okresie rozruchu, oraz znajdują się w tak zwanym trybie bezprzepływowym. Pomimo faktu, że rury tych powierzchni w trybie bez zużycia nie są chłodzone od wewnątrz parą, temperatura ich metalu utrzymuje się w dopuszczalnych granicach, ponieważ początkowe zużycie paliwa w tym okresie utrzymuje się na stałym, stosunkowo niskim poziomie , nie przekraczające 20% nominalnego zużycia.
Bezpieczeństwo trybu bezprzepływowego przegrzewaczy pary w okresie rozruchu kotła zostało potwierdzone specjalnymi badaniami kotłów TPP-110 i TPP-210. Jak widać przy zużyciu paliwa (gazu ziemnego) do 20% temperatury nominalnej, ścianki najbardziej nagrzanych rur czołowych ekranów nie przekraczają w stanie stacjonarnym dopuszczalnej temperatury 600°C. Biorąc pod uwagę, że zużycie paliwa w początkowym okresie rozruchu kotła jest znacznie mniejsze niż 20% (przykładowo, gdy kocioł pracuje na oleju opałowym, jego zużycie nie przekracza 14-15% wartości nominalnej), można rozważyć tryb bezzużyciowy dla przegrzewaczy pary całkiem akceptowalny w tym okresie rozpalania.
W nawiązaniu do przeprowadzonych eksperymentów stwierdzono, że w żadnym z rozruchów badanych kotłów temperatura ścianek rur w całym stanie bezprzepływowym nie przekroczyła 550°C. Temperatura ta jest niższa od maksymalnej dopuszczalnej dla stali niskostopowej 12Х1МФ, stosowanej zwykle do produkcji rur sitowych I stopnia, a jeszcze bardziej dla stali austenitycznej 1Х18Н12Т, stosowanej na ekrany II stopnia w przegrzewaczach konwekcyjnych pary.
Wyłączenie przegrzewaczy w pierwszej fazie rozruchu ułatwia manewrowanie i sterowanie zespołem kotła, pozwalając po podłączeniu powierzchni przegrzewających płynnie zwiększać parametry pary i jej ilość, przy jednoczesnym zachowaniu stabilności zasilania wodą zasilającą. Za początek drugiej fazy rozruchu uważa się moment, w którym we wbudowanym separatorze zaczyna się uwalniać para, która kierowana jest na powierzchnie przegrzewające się, stopniowo otwierając przepustnicę i stopniowo zwiększając temperaturę i ciśnienie Para. W tej fazie rozruchu kocioł pracuje przy dwóch ciśnieniach: nominalnym – aż do wbudowanego zaworu, który w dalszym ciągu pozostaje zamknięty, oraz „ślizgowym” – za przepustnicą w powierzchniach przegrzania. Tryb ten jest możliwy dzięki temu, że powierzchnie przegrzania pary oddzielone są od powierzchni wytwarzających parę przestrzenią parową separatora, podobnie jak w kotłach bębnowych. W trzeciej fazie rozruchu kocioł zostaje przełączony na tryb przepływu bezpośredniego. Przesyłanie to należy rozpocząć po osiągnięciu przez parę parametrów pary na poziomie 80-85% wartości nominalnych. Stopniowo otwierając wbudowany zawór, doprowadzamy parametry do wartości nominalnej i wyłączamy agregat rozpalający.
Po zakończeniu nagrzewania bloku kotłowego w elektrociepłowni nieblokowej podłącza się go do głównego rurociągu parowego, zachowując zasady podłączenia takie same jak w przypadku kotłów bębnowych. Najważniejszym z nich jest przybliżona równość ciśnienia za kotłem i głównym rurociągiem parowym w momencie podłączenia.
W instalacjach blokowych rozruch kotła łączy się z rozruchem turbiny i przełączanie kotła na przepływ bezpośredni zwykle następuje po osiągnięciu przez blok obciążenia elektrycznego na poziomie 60-70% wartości nominalnej.
Poniższe rysunki przedstawiają charakterystykę rozruchową kotła przelotowego elektrowni cieplnej nieblokowej w trybie separatora: 1 - ciśnienie pary za kotłem; 2 - zużycie wody zasilającej; 3 - maksymalna temperatura czynnika na wylocie z NRCh; 4 - temperatura wody zasilającej; 5 - pośrednia temperatura przegrzania; 6 - temperatura świeżej pary; 8, 7 - maksymalna temperatura metalu ekranów II i przegrzewacza pośredniego; 9 - temperatura gazów spalinowych w komorze wirującej.
Cechy rozpałki podczas „gorącego” startu są następujące. Przed zapaleniem palników temperaturę metalu wbudowanych separatorów obniża się z 490 do 350-320°C poprzez uwolnienie pary z separatorów, przy czym szybkość spadku nie powinna być większa niż 4°C/min. Jednocześnie ciśnienie w kotle spada z nominalnego (25 MPa) do 10-15 MPa. Po 30-40 minutach po ochłodzeniu separatorów według tego samego harmonogramu jak ze stanu „nieschłodzonego”, tj. po ustaleniu minimalnego natężenia przepływu wody zasilającej do zapłonu, ciśnienie przed zamkniętym wbudowanym zaworem wzrasta do 24- 25 MPa, przy początkowym przepływie oleju opałowego włączane są palniki na olej opałowy i jednocześnie otwierają się zawory nadmiarowe 8 wbudowanych separatorów. Następnie przepustnice 5 stopniowo się otwierają. Dalsze czynności są takie same, jak przy uruchamianiu ze stanu „zimnego”. Obniżając ciśnienie w kotle przed rozpaleniem, eliminuje się kondensację pary na sitach, przez co schładzają się mniej niż przy uruchomieniu w trybie przepływu bezpośredniego.
Zespół napędowy z kotłem TPP-210A został awaryjnie zatrzymany przez urządzenia zabezpieczające w związku z awarią pompy zasilającej. W przypadku automatycznego zamknięcia zaworu na przewodzie oleju opałowego nie odcięto całkowicie dopływu paliwa płynnego i w jednym z korpusów kotła w palenisku nadal paliła się niewielka ilość oleju opałowego, co przyczyniło się nie tylko do wzrostu odkształceń cieplnych i zwiększoną cyrkulację w płytach NRF, ale także pojawienie się nieruchomych pojedynczych rur w górnych łukach, pęcherzyków lekko przegrzanej pary, które zajmowały cały przekrój rur i uniemożliwiały przepływ w nich czynnika roboczego. Choć para nadkrytyczna w chwili powstania ma taką samą gęstość jak woda, to już podniesienie jej temperatury o zaledwie kilka stopni powoduje zmniejszenie jej gęstości o kilkadziesiąt procent. Wraz ze wzrostem prędkości wody pęcherzyki pary powinny zostać uniesione przez jej przepływ, ale duże pęcherzyki mogą zostać tymczasowo opóźnione, przez co temperatura metalu odpowiednich rur powinna gwałtownie wzrosnąć.
Po pięciominutowej przerwie kocioł przełączono na przepływ bezpośredni i wbrew zasadom woda zasilająca nie była dostarczana jako pierwsza, lecz jednocześnie z gwałtownym zwiększeniem dopływu oleju opałowego do paleniska. Wkrótce w nieogrzewanej części wylotowej jednej z rur NRF zarejestrowano wzrost temperatury do 570°C. Odstęp pomiędzy automatycznymi rejestracjami tej temperatury wynosił 4 minuty, jednak przed ponownym zarejestrowaniem tej temperatury nastąpiło awaryjne pęknięcie rury, której odcinek w rejonie wlotu palnika nie był chroniony pasami zapalającymi. Kocioł został ponownie wyłączony awaryjnie.
Inny przykład dotyczy pogorszenia separacji, które miało miejsce, gdy zawory nadmiarowe usuwające oddzieloną wilgoć z wbudowanego separatora nie są całkowicie otwarte. Podczas rozpalania kotła przepływowego zawory te były zamykane w celu obniżenia temperatury pary świeżej w przypadku awarii schładzaczy wtryskowych. Ten sposób kontroli wiąże się z nagłymi i znaczącymi zmianami temperatury pary i prowadzi do pojawienia się pęknięć zmęczeniowych w kolektorach przegrzewacza, w pobliżu wbudowanego separatora wzdłuż przepływu pary.
Zamykanie zaworów 8 i otwieranie 5 należy wykonywać powoli, aby uniknąć przedostania się wody do pobliskich kolektorów przegrzewacza na skutek zakłócenia stabilnego ruchu czynnika roboczego w separatorze. Dodatkowo należy wcześniej otworzyć spusty przed i za przepustnicą 5, aby zapobiec wydostawaniu się kondensatu zgromadzonego w rurociągach z jednostki zapłonowej.
Powolne otwieranie przepustnic 5 prowadzi do wydłużenia czasu nagrzewania głównych rurociągów parowych i czasu trwania rozpalania kotła. Oczywiście duże wahania temperatury pary są niedopuszczalne, jednak jeżeli kocioł rozpalany jest tylko kilka razy w roku, nie ma powodu dalej opóźniać rozruchu, aby zapobiec nieznacznemu obniżeniu temperatury pary. Jeśli jednak kocioł jest podgrzewany i często zatrzymywany, nawet niewielkie rozpryski wody na ekrany mogą mieć niebezpieczne konsekwencje. Dlatego przy zapalaniu kotłów jednoprzejściowych należy ściśle przestrzegać harmonogramu rozruchu, który reguluje powolne i stopniowe otwieranie zaworów 5.