Optymalna grubość podłoża pod laminat. Jakie podłoże wybrać pod laminat, wybieramy najlepszą opcję Podłoże metalizowane pod laminat
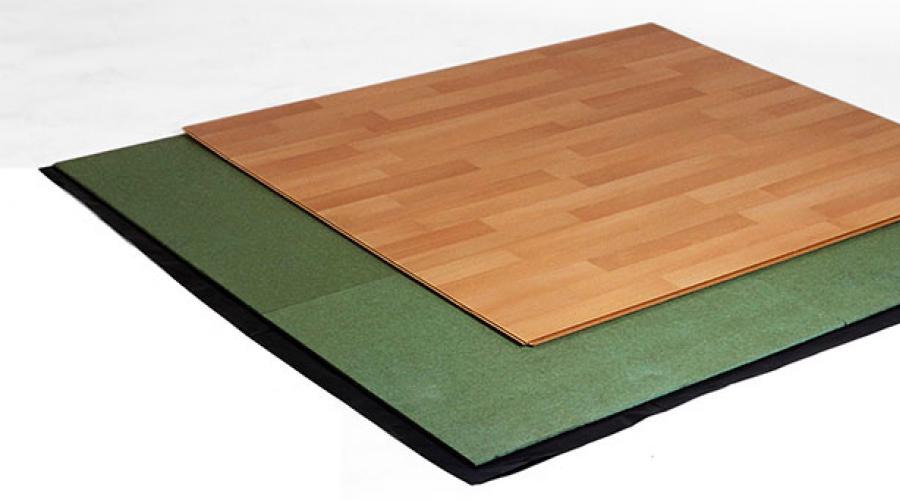
Przy doborze grubości podłoża należy kierować się stanem i jakością podłoża. Podkład o grubości 2 mm można stosować tylko wtedy, gdy podłoga jest w dobrym stanie. W przypadku betonu z niewielkimi wadami warto wybrać podłoże typu isoplate o grubości 3mm.
Podkładki z pianki polietylenowej
Podłoża z pianki polietylenowej zyskały popularność dzięki wysokiej odporności na wilgoć i dobrym właściwościom termoizolacyjnym. Powłoka nie jest interesująca dla gryzoni, owadów i grzybów. Producenci podkładów z pianki PE rozszerzyli swój asortyment o połączenie warstwy z folią metaliczną na bazie aluminium.
Podłoża korkowe
Zastosowanie tego rodzaju podłoża pod laminat ma znaczenie w przypadku układania podłogi pływającej oraz ogrzewania podłogowego. Dobre właściwości izolacyjne, naturalność materiału oraz odporność na pleśń i mikroorganizmy sprawiły, że korek jest liderem w tym segmencie.
Produkowany w postaci arkuszy i rolek jest wygodny przy układaniu na małych powierzchniach. W okresie eksploatacji nie traci swoich właściwości technicznych i wymiarów liniowych. Wady materiału można uznać za prawdopodobieństwo kondensacji na spodniej stronie laminatu i wysoki koszt.
Podłoża bitumiczno-korkowe
Papier pakowy, bitum i wióry korkowe są składnikami folii bitumiczno-korkowych. Opatrunek korkowy wykonany jest z kawałków o wielkości 2-3 mm, co umożliwia powłoce zapewnienie wymiany powietrza na odpowiednim poziomie i zapobieganie kondensacji. Wskazane jest stosowanie takiego podłoża przy układaniu drogiego laminatu.
Podłoża styropianowe
Podstawą podkładu jest ekstrudowana pianka polistyrenowa ze względu na jej zdolność do dobrego niwelowania nierówności podłoża betonowego. Styropian jest najlepszą izolacją podłóg laminowanych. Zamknięta struktura komórkowa materiału i gęstość zapewnia wysoką odporność na wilgoć.
Połączone podłoża
Kategoria podłoży łączonych obejmuje „duet” styropianu i polietylenu. Pomiędzy dwiema warstwami polietylenu znajdują się najmniejsze kulki styropianu. Polietylen o dużej gęstości, który tworzy wierzchnią warstwę, zapobiega przenikaniu wilgoci, która może znajdować się na powierzchni podłogi. Wilgoć z podkładu ciągnącego do warstwy ziarnistej przechodzi przez cienką dolną warstwę, a następnie ze względu na przerwy technologiczne zostaje wyprowadzona.
Przytulna atmosfera jest jednym z głównych wymagań dotyczących przestrzeni życiowej. Po przyjeździe do domu każda osoba pragnie odpocząć, cieszyć się ciszą i spokojem. Jeśli jednak Twoje niespokojne dziecko biega po podłodze, wydawane są wyraźne dźwięki, które zakłócają spokojny odpoczynek. A kiedy sąsiedzi na dole słuchają na dodatek głośnej muzyki, to o ciszy można tylko pomarzyć. Skutecznym rozwiązaniem tego problemu jest zakup podkładu podłogowego. Oczywiście dość trudno jest samodzielnie rozgryźć wszystkie niuanse, ale nasze informacje pomogą Ci z powodzeniem dobrać odpowiednią warstwę izolacyjną.
Zalety podkładu pod podłogi laminowane
Podłoga odgrywa bardzo ważną rolę w renowacji. A wybór materiału na podłogę należy traktować poważnie. Dziś laminat nazywany jest najpopularniejszą powłoką ze względu na swoją trwałość, odporność na zużycie i względną taniość. Jednak zakup samego materiału to połowa sukcesu, ponieważ nadal musisz wybrać podłoże do laminatu.
Izolacja akustyczna
Laminat ma jedną nieprzyjemną cechę: odgłos kroków jest dość głośny. Zarówno dla Ciebie, jak i dla Twoich sąsiadów. Są ku temu dwa powody: sama powłoka jest cienka - w laminacie za najpopularniejszą grubość uważa się 8 milimetrów; a także metodą pływającego układania, w wyniku której pod stopami uzyskuje się rodzaj membrany przenoszącej dźwięki. Aby wytłumić taki hałas uderzeniowy, podczas układania podłóg laminowanych na podkładach kładzie się podkład.
Niektórzy producenci integrują w swoich produktach specjalne systemy dźwiękochłonne – podobna warstwa jest przyklejana z tyłu laminowanych desek podłogowych. Zintegrowany podkład jest powszechnie spotykany w laminatach Grade 33 i Grade 32. Taka powłoka jest bardzo wygodna w układaniu, ale integracja podłoża z laminatem znacznie podnosi koszty produkcji. Dlatego rozsądniejszą decyzją byłby zakup ciepłych podłoży do laminatu w rolkach lub arkuszach. Właściwości dźwiękochłonne takiego materiału producent wskazuje na opakowaniu.
Wyrównywanie powierzchni
Oprócz zmniejszenia hałasu taka warstwa pośrednia między laminatem a podstawą jest w stanie nieznacznie wygładzić nierówności jastrychu pod wykładziną podłogową. To smutne, że nowe podłoże nie zawsze jest gotowe na podłogę laminowaną. Podczas produkcji jastrychu uzyskuje się pewne różnice, a takie odchylenia są niedopuszczalne w przypadku układania wykładzin podłogowych.
Przy układaniu parkietu laminowanego na powierzchni betonowej po kilku miesiącach pojawia się w niektórych miejscach tzw. „luz”. Laminat z reguły ugina się w miejscach, w których odległość między szorstkim jastrychem a podłogą jest maksymalna. Nawet jeśli utworzy się kilkumilimetrowa szczelina, to nierówności podczas chodzenia i tak będą zauważalne.
Dlatego wymagane jest dodatkowe wypoziomowanie podstawy. Do tego potrzebne jest podłoże pod laminat styropianowy, który pozwala uzyskać idealnie płaską powierzchnię podłogi i ukryć drobne różnice. Ale nie daj się ponieść grubości – niedopuszczalne jest stosowanie podłoża o grubości powyżej 3 milimetrów, ponieważ zbyt gruby laminat będzie zwisał na styku desek podłogowych, a łączenia mogą po prostu zostać uszkodzony.
Izolacja wilgoci
Wilgotność ma szkodliwy wpływ na wykładziny podłogowe. Jeśli podczas układania podłogi należy zwrócić uwagę na naturalny proces suszenia, nie będzie problemów z układaniem laminatu. Nowy jastrych betonowy powinien wysychać w sposób naturalny przez co najmniej jeden miesiąc.
W każdym razie nie będzie zbyteczne przeprowadzenie prostego testu, aby sprawdzić, czy podłoże jest gotowe do ułożenia podłogi laminowanej. Wieczorem wyrzuć na podłogę plastikową torbę, a rano sprawdź - jeśli pojawił się na niej pot, to jastrych nie jest jeszcze gotowy do układania laminatu. Podkład pod laminat jest w stanie utrzymać mikroklimat pomiędzy posadzką a podłożem oraz chronić powierzchnię przed wilgocią technologiczną pochodzącą z cementu lub betonu.
Przewodność cieplna
Przewodność cieplna jest szczególnie ważna w przypadku ogrzewania podłogowego. Podłogi laminowane mają nieodłączne właściwości termoizolacyjne. Podłoża pod laminat i „ciepłą podłogę” są również izolatorami ciepła. W ten sposób system „ciepłej podłogi” znajduje się pod dwiema warstwami izolacji termicznej, co zmniejsza wydajność ogrzewania.
Pomyśl o tym, w tym przypadku nie trzeba ponosić kosztów zakupu i montażu ogrzewania podłogowego, a także płacić za zużyty prąd. Podłoże pod laminat ma wysokie właściwości termoizolacyjne i jest w stanie zapewnić dobrą izolację termiczną podłogi.
Właściwości podłoża pod laminat
Tak więc potrzeba ułożenia materiału izolacyjnego pod laminatem nie budzi wątpliwości. Pozostaje tylko wybrać podłoże. Wysokiej jakości podłoża w rolkach i arkuszach nie są zbyt tanie, jednak zdaniem mistrzów oszczędzanie na tym materiale może skończyć się nieprzyjemnymi konsekwencjami, aż do pęcznienia laminatu. W takim przypadku musisz znaleźć kompromis, wiedząc, jakie właściwości powinno mieć podłoże pod podłogą laminowaną.
Specjalny materiał izolacyjny, który nie pozwala na bezpośredni kontakt podłogi laminowanej z podłożem, musi spełniać następujące wymagania:
- być obojętny na interakcje z materiałami alkalicznymi;
- mają właściwości bakteriobójcze;
- pełnić funkcję izolacji termicznej;
- mają wysoką odporność na wilgoć;
- nie promuj rozmnażania gryzoni i szkodliwych owadów;
- dają możliwość usunięcia kondensatu - mikrowentylacja;
- zmniejszyć obciążenie zamka podłogi laminowanej.
Wybór podłogi laminowanej
Jakie podłoże wybrać, bo na rynku jest wiele odmian tego materiału? Przede wszystkim musisz przejść od stanu szorstkiej podstawy podłogi. Jeśli jastrych jest w dobrym stanie i spełnia ustalone tolerancje, możesz bezpiecznie wziąć dwumilimetrowe podłoże. W przypadku, gdy beton ma drobne skazy, zaleca się zakup podłoża o grubości 3 milimetrów pod laminat isoplat.
Na rynku materiałów budowlanych istnieją takie rodzaje podłoży pod podłogi laminowane: pianka polietylenowa, podłoża z ekstrudowanej pianki polistyrenowej, podłoża łączone, bitumiczne z korkiem i materiałami korkowymi. Błędem jest sądzić, że warto kupić podłoże od tego samego producenta, co podłoga laminowana. Nie ma to fundamentalnego znaczenia.
Podkładki z pianki polietylenowej
Podłoża polietylenowe cieszą się dużą popularnością, ponieważ są bardzo odporne na wilgoć, mają dobre właściwości termoizolacyjne, nie są zarażane przez różne grzyby i bakterie oraz nie są interesujące dla owadów i gryzoni. Jest wygodny i łatwy w pracy z takim materiałem, jest ekonomiczny i wytwarza mało odpadów. Nierzadko folia posiada dodatkową warstwę folii metalizowanej. Produkowane są również podłoża foliowe do laminatów z wykorzystaniem aluminium.
Jednak oprócz zalet podłoża z pianki polietylenowej mają również wady. Nie zachowują dobrze kształtu i mogą z czasem zwisać. Ponadto taki materiał izolacyjny boi się promieniowania ultrafioletowego.
Podłoża korkowe
Podkład korkowy jest dobrym materiałem izolacyjnym i stanowi doskonałą bazę pod podłogę pływającą. Jest znany jako doskonały izolator termiczny i jest odporny na pleśń i gnicie. Materiał produkowany jest w rolkach i arkuszach. Stosowany jest jako izolator ciepła w „ciepłych podłogach” oraz podłoże pod podłogi pływające. Zachowuje swoje wymiary liniowe i właściwości techniczne przez cały okres użytkowania.
Wysoki koszt folii korkowych sprawia, że instalowanie jej w przypadku niedrogich podłóg laminowanych, które mają krótki okres użytkowania, jest niepraktyczne. Wadą podkładu z korka pod laminat jest to, że podczas jego stosowania na spodniej stronie laminatu może tworzyć się kondensacja.
Podłoża bitumiczno-korkowe
Folie bitumiczno-korkowe wykonane są na bazie papieru siarczanowego z dodatkiem bitumu, po czym na wierzchu pokrywane są wiórami korkowymi. Opatrunek korkowy składa się z kawałków o wielkości 2-3 milimetrów. Dodatkowo takie podłoże doskonale pochłania dźwięki, a dzięki zawartości bitumu zapobiega wnikaniu wilgoci.
Podłoża bitumiczno-korkowe zapewniają wymianę powietrza na odpowiednim poziomie, wyrównują ciśnienie i zapobiegają tworzeniu się kondensatu. Materiał jest przydatny, gdy planowane jest ułożenie drogiego i trwałego rodzaju laminatu. W przypadku tanich podłóg laminowanych niskiej jakości nie zaleca się stosowania tej powłoki.
Podłoża styropianowe
Ekstrudowana pianka polistyrenowa jest często stosowana jako warstwa izolacyjna pod podłogą laminowaną. Taka folia jest optymalnym rozwiązaniem pod względem odporności na obciążenia. Dodatkowo dobrze wyrównuje nierówności podłoża betonowego. Dzięki tym właściwościom podkład z ekstrudowanej pianki polistyrenowej może być stosowany do pomieszczeń intensywnie eksploatowanych.
Skuteczne pochłanianie drgań i naprężeń gwarantuje podwyższony komfort chodzenia. Styropian dobrze izoluje podłogę laminowaną, a dzięki zamkniętej strukturze jej komórek jest wysoce odporny na wilgoć. Materiał początkowo ma dużą gęstość, dzięki czemu przez bardzo długi czas zachowuje swoją elastyczność i grubość.
Połączone podłoża
Syntetyczne podłoża kombinowane, które są używane do produkcji styropianu i polietylenu, są dziś dość poszukiwane. Najbardziej znanym przykładem takiego materiału jest dobrze znane podłoże Tuplex. Połączona folia jest rodzajem „kanapki”, w której kulki ze styropianu znajdują się pomiędzy dwiema warstwami polietylenu o różnych właściwościach.
Materiał sprzedawany jest w rolkach i ma grubość około 2-3 milimetrów. Dzięki swojej konstrukcji folia jest w stanie przewietrzyć pomieszczenie. Warstwa wierzchnia, wykonana z polietylenu o dużej gęstości, zapobiega wnikaniu wilgoci do podstawy podłogi w przypadku nagłego dostania się wody na podłogę. Cienka dolna warstwa umożliwia przenikanie wilgoci z szorstkiego podłoża do granulek, a stamtąd jest wydobywana z powodu luk technologicznych.
Zaletami podłoża kombinowanego jest jego elastyczność, wytrzymałość i zdolność do zachowania pierwotnej grubości, a także wyrównywania ubytków podłoża.
Podłoża specjalne
Specjalny materiał izolacyjny może z maksymalną skutecznością zredukować odgłosy transportu lub odgłosy kroków. Dzięki stworzeniu naturalnej wentylacji materiał jest w stanie usunąć wilgoć, która dostała się pod wykładzinę podłogową. Zastosowanie specjalnych podłoży skraca czas układania podłogi laminowanej 2-3 krotnie dzięki wbudowanej membranie odpornej na wilgoć. Podłoża specjalne pod wieloma względami mają dobre właściwości, ale charakteryzują się wysokimi kosztami.
Technologia podkładowa pod podłogi laminowane
Podczas układania podłoża pod laminatem nie są wymagane umiejętności zawodowe, doświadczenie zawodowe i specjalne narzędzia, ale należy dokładnie przestrzegać pewnych zasad. Przede wszystkim wydajność i trwałość laminatu zależy od umiejętności pracy. Przy prawidłowym ułożeniu podłoża pod wykładziną podłogową ty i twoi sąsiedzi nie będziecie się pamiętać!
Praca przygotowawcza
Jeśli jastrych jest betonowy, kamienny lub cementowy, należy nałożyć na niego warstwę folii z tworzywa sztucznego w celu uszczelnienia, a następnie rozpocząć układanie podłoża. Grubość polietylenu powinna być nieco większa niż zwykła plastikowa torba - blisko 0,2 milimetra. Wierzchnia warstwa podłogi laminowanej pokryta jest folią ochronną, która chroni powłokę przed wilgocią, dlatego nie należy pozostawiać spodniej powierzchni niezabezpieczonej.
Przed ułożeniem podłoża podłoże należy dokładnie odkurzyć. Bez wątpienia musi być suche. Podłoże można ciąć zwykłymi nożyczkami lub nożem budowlanym, odmierzone linie nanosi się ołówkiem lub markerem za pomocą linijki. Aby osiągnąć maksymalną równość powierzchni, nie można wykonać kilku warstw podłoża. Wystarczy wziąć łódź podwodną, której grubość wynosi 2-3 milimetry.
Jeśli wybierzesz grubszy podkład z laminatu polistyrenowego do nierównomiernego pokrycia, blokady laminatu mogą pęknąć pod naciskiem. Tak, a chodzenie po podłodze w tym przypadku będzie niewygodne, ponieważ panele się wyginają.
Układanie podłoża
Zaleca się układanie podkładu w poprzek kierunku, w którym będą układane panele laminatu. Odbywa się to tak, że kawałek podłogi nie przesuwa się ze swojego miejsca podczas nieostrożnego ruchu. Podczas układania konieczne jest umieszczenie podłoża pod laminatem na ścianach - zapewni to bezpieczeństwo i trwałość powłoki. Jeżeli materiał jest uszkodzony, to w przypadku znalezienia uszkodzonych miejsc należy go pokryć dodatkową warstwą podłoża pod laminat.
Jeśli folia jest falista, należy położyć stronę z falistą powierzchnią, więc lepiej będzie wyrównać podstawę. Jeśli materiał jest z folią aluminiową, to strona z folią powinna być umieszczona do góry.
Dlatego wybierając laminat spośród całej gamy nowoczesnych pokryć podłogowych, zaleca się zakup specjalnej łodzi podwodnej do laminatu, aby zapewnić izolację akustyczną i wygładzić nierówności na szorstkim podłożu. Specjalny materiał izolacyjny posiada szereg pozytywnych właściwości i jest prezentowany na rynku w szerokim asortymencie. Znalezienie odpowiedniego podkładu nie będzie trudne!
Stosunkowo nowy materiał - laminat - zyskuje coraz bardziej widoczne miejsce na rynku materiałów budowlanych jako jeden z najtańszych materiałów, z którymi łatwo się pracuje. Jednocześnie daje doskonały wynik w zakresie percepcji wizualnej wykładziny, łatwości konserwacji i trwałości. Ale taki wynik jest możliwy tylko przy dobrze wykonanym wykończeniu i odpowiednio dobranym podłożu pod laminat.
Funkcjonalne przeznaczenie podłoża pod laminat
Aby z powodzeniem stosować ten rodzaj powłoki, należy spełnić szereg wymagań. Dotyczą one przede wszystkim formowania podłogowego „ciasta”, wielowarstwowego urządzenia, które kompensuje słabości powłoki wykończeniowej i zapewnia, że podłoga w pełni spełnia swoje zadanie użytkowe. Aby to zrobić, przed ułożeniem pod laminatem tworzy się podłoże, któremu przypisuje się następujące zadania:
- ochrona przed parą, której celem jest ochrona ciasta podłogowego przed wilgocią z powietrza pochodzącą od dołu;
- funkcja ocieplająca - minimalizacja strat ciepła z jastrychu podłogowego, co jest szczególnie ważne, gdy płyty podłogowe pierwszego piętra znajdują się nad piwnicą do przechowywania żywności, ze specjalnym reżimem termicznym;
- izolacja akustyczna - odpowiednia dla drugiego i wyższego piętra;
- wyrównanie ubytków w szorstkim jastrychu, co jest szczególnie ważne w przypadku stosowania podłóg laminowanych jako wykończenia podłogi.
Jakie podłoże pod laminat najlepiej wybrać nasi czytelnicy. Aby zrozumieć problem, dowiedzmy się, czym jest laminat.
Podstawą do produkcji takiej płyty jest płyta pilśniowa o wysokiej wytrzymałości. Powierzchnia pokryta jest warstwą żywicy melaminowej lub akrylowej, która stanowi warstwę ochronną. Dekoracyjna warstwa papieru pod przezroczystą powłoką może imitować każdą powierzchnię od drewna po kamień. Dolna warstwa wodoodpornego papieru chroni tekturę przed wilgocią. Dla wielu producentów elementy współpracujące pokryte są warstwą wosku.
Wybór podłoża
Podłoże jest urządzeniem wielowarstwowym, ale biorąc pod uwagę właściwości materiału powłokowego, szczególną uwagę zwraca się na jego zdolność do niwelowania wpływu różnego rodzaju nierówności na powierzchnię płaszczyzny nośnej podłoża.
Podłoża włókninowe
To chyba najlepszy wybór jako podłoże pod podłogi laminowane. Podkłady podłogowe z włókien różnią się od wszystkich konkurentów nie tylko stosunkiem ceny do jakości, ale także najlepszymi parametrami fizycznymi.
Firma Trioteks zajmuje się produkcją tych podłoży i już ugruntowała swoją pozycję jako niezawodny dostawca wysokiej jakości materiałów.
Zalety podłoży włóknistych:
- Doskonała izolacja przeciwwilgociowa - podłoże pokryte jest folią ochronną, która zapobiega zamoczeniu;
- Izolacyjność akustyczna – dzięki swojej strukturze materiał niemal całkowicie pochłania dźwięk;
- Izolacja termiczna – pod względem właściwości termoizolacyjnych włóknina może konkurować z powłokami korkowymi;
- Doskonale wygładzamy drobne nierówności - główne przeznaczenie podłoży. I z tym najlepiej radzą sobie podłoża firmy „Triotex”.
Podłoża włókniste z biegiem czasu nie ulegają między innymi gniciu i „wgnieceniu”.
Instalacja jest jedną z najłatwiejszych wśród konkurencji. W przeciwieństwie do innych kruchych materiałów (korek, igły, styropian) wystarczy rozwałkować materiał po podłodze i przyciąć go w odpowiednich miejscach.
Podłoga Trioteks nadaje się do każdego celu - do wyrównania podłogi przed ułożeniem laminatu, do izolacji akustycznej i izolacji.
Materiały korkowe
Kruszony materiał naturalny korek jako podłoże formowany jest w rolki na bazie tkaniny, grubość materiału wynosi 2 - 10 mm. Ze względu na swoje właściwości fizyczne jest popularny ze względu na zdolność do wygładzania wgłębień, niwelując ich wpływ na laminat.
Podkład korkowy dobrze sprawdza się również na podłogach drewnianych. W tym przypadku przygotowanie powierzchni polega na usunięciu starej farby za pomocą skrobaków lub specjalnej kompozycji przeznaczonej do tego celu. W tym zakresie należy przymocować skrzypiące deski podłogowe dodatkowymi wkrętami lub gwoździami do legarów podłogowych. Odpryski i pęknięcia należy zlikwidować szpachlówką o specjalnej mieszance do drewna.
Podczas układania podłoża stosuje się zwykłą technologię dla takich przypadków. Na podłodze układane są pasy materiału z blachy, dopuszcza się spoiny zarówno na szerokość jak i na długość, które należy skleić taśmą budowlaną . Uwaga! Podczas układania podłoża miejscowe obrzęki i obrzęki są niedopuszczalne. Na całej powierzchni pomieszczenia powinien ściśle przylegać do podłogi.
Do pozytywnych właściwości tego materiału należy jego niska alergenność. Będąc aglomeracją naturalnego materiału i tych samych spoiw, początkowo jest przyjazny dla środowiska. Pozwala to na zastosowanie takiego materiału w pomieszczeniach mieszkalnych, pokojach dziecięcych, kuchniach i innych podobnych miejscach.
Wśród innych pozytywnych cech odnotowuje się:
- długa żywotność, do 30 lat, przy ścisłym przestrzeganiu technologii przygotowania powierzchni, gdzie stosuje się podłoże korkowe i sam jego montaż;
- odporność materiału na odkształcenia, po odciążeniu rozluźnienie warstwy materiału następuje już po 2 - 2,5 godzinach;
- właściwości wygłuszające - porowata struktura i elastyczność materiału źródłowego skutecznie tłumią zarówno przenikające dźwięki, jak i fale wibracyjne z pracujących urządzeń i urządzeń elektrycznych. Już przy grubości warstwy 2 mm materiał tłumi dźwięki do 12-14 decybeli;
- właściwości termoizolacyjne - niska przewodność cieplna spowodowała zastosowanie go do izolacji ścian, stropów, podłóg i innych wielokierunkowych płaszczyzn;
- materiał jest środkiem antyseptycznym pochodzenia naturalnego, nie narażonym na działanie grzybów i porostów, a także nie służy jako pokarm dla domowych gryzoni.
Unikalną właściwością jest zdolność korka do redukcji tła radioaktywnego i szkodliwego działania innych materiałów budowlanych.
Negatywnym czynnikiem jest wysoka cena materiałów korkowych, którą z powodzeniem rekompensuje zestaw ich pozytywnych właściwości i trwałości.
Dodatkowo niska przewodność cieplna tego podłoża uniemożliwia jego zastosowanie na jakiekolwiek ogrzewanie podłogowe.
Podłoża iglaste
Materiał ten jest wykonany z wiórów i wiórów drewna iglastego, które zostały poddane parowaniu. Podczas prasowania produktów nie stosuje się obcych spoiw, jest to właściwość żywicy zawartej w samym drewnie. Zastosowane materiały i metoda produkcji pozwalają racjonalnie uznać podłoża iglaste za materiał przyjazny dla środowiska.
Głównymi formami wydania są rolki i talerze. Te ostatnie pakowane są w paczki po 7 metrów kwadratowych o wymiarach karty 59 x 89 cm i grubości 3,5 - 7 mm. Podczas układania jako podłoże szwy są klejone taśmą konstrukcyjną.
Początkowo materiał ten miał służyć jako izolator akustyczny, ale ujawniona zdolność tłumienia wstrząsów i wibracji doprowadziła do zastosowania go jako podłoża do różnych wykończeń podłóg.
Podłoże iglaste pod laminatem ma szereg cennych pozytywnych właściwości:
- wysoka izolacyjność akustyczna stwarza komfortowe warunki życia w pomieszczeniu;
- zastosowanie podłoża iglastego pozwala utrzymać ciepło podłogi;
- gęstość płytek pozwala znacznie zniwelować nierówności podłoża podczas układania zarówno na podłodze betonowej, jak i drewnianej;
- przy montażu podłoża iglastego nie ma potrzeby stosowania dodatkowych klejów, narzędzi i osprzętu;
- brak syntetycznych dodatków, klejów i modyfikatorów pozwala zaklasyfikować ten materiał jako przyjazny dla środowiska;
- podczas pracy podłoże iglaste dobrze zachowuje swój kształt, nie zwisa, zachowując swój kształt przez co najmniej 15 lat.
Istotną wadą materiału jest jego zdolność do pleśnienia w obecności wilgoci.
Dlatego wspomnieliśmy powyżej o konieczności zastosowania paroizolacji jako części podłoża. Ponadto w przypadku stosowania materiału iglastego wymagana jest ochrona przed wilgocią między nim a laminatem, aby zapobiec jego wnikaniu podczas czyszczenia na mokro.
Spieniony polipropylen
Materiał ten jest najpopularniejszym z klasy produktów syntetycznych do stosowania jako podłoże pod wykończenia podłóg, w tym podłóg laminowanych.
Struktura materiału ma strukturę bąbelkową, co tłumaczy jego niską przewodność cieplną i właściwości dźwiękochłonne.
Jednym z powodów dużej popularności spienionego polipropylenu jest jego niska cena, co nie świadczy o jego niewystarczającej jakości. Z powodzeniem wytrzymuje laminowaną powłokę i znośnie zatrzymuje ciepło i dźwięk.
Forma uwalniająca w postaci rolek lub arkuszy wykonana jest z pofalowanej powierzchni, która zapewnia wentylację przestrzeni pod laminatem. Dodatkowo podkład o grubości 3 – 5 mm z powodzeniem radzi sobie z nierównościami podłoża.
Jedną z wad podłoży polipropylenowych jest niszczenie pęcherzyków przy wielokrotnym obciążaniu. Konsekwencją tego jest spłaszczenie materiału z utratą jego podstawowych właściwości.
Ostatnio szeroko stosowane są podłoża foliowe, a metalizacja może być jednostronna lub dwustronna. Taki materiał działa w miejscu montażu jak termos, skutecznie zatrzymując ciepło podłogowe. Grubość podłoża w tym przypadku wynosi 2-5 mm.
Aby uniknąć odizolowania laminatu od elementów grzewczych podczas montażu ogrzewania podłogowego, podkład należy umieścić pod źródłami ciepła, zapobiegając jego przeciekaniu do podłoża podłogowego. W tym przypadku szczególną wagę należy przywiązywać do jakości powierzchni podłoża, niezależnie od materiału, z którego została wykonana.
Ekstrudowany polistyren ekspandowany
Drugim rodzajem podłoży wykonanych z syntetyzowanych materiałów jest polistyren ekstrudowany. Materiał ten ma znacznie wyższą wytrzymałość i jest w stanie wytrzymać znaczne obciążenia przez długi czas.
Forma uwalniania - maty lub talerze o zielonkawym kolorze.
Charakterystyczną cechą materiałów styropianowych jest ich duża gęstość, która nadaje znajdującym się w nich pęcherzykom powietrza dodatkowej wytrzymałości. Pod stałymi dużymi obciążeniami płyty nie zwisają ani nie odkształcają się. Ta sama jakość niezawodnie wygładza szczytowe obciążenia w miejscach nierównych podłóg.
W przypadku ciepłej podłogi głównym celem podłoża jest izolacja termiczna w celu wyeliminowania strat ciepła. Szczególnie ważne jest zastosowanie podłoży na płytach posadzkowych pierwszego piętra, oddzielających go od piwnicy. Pozwala to na utrzymanie mikroklimatu w piwnicy, niezbędnego do przechowywania zapasów oraz zmniejsza zużycie energii na ogrzewanie budynku.
Kolejność układania podłoża
Taką operację należy rozpocząć od dowolnego kąta i postępować jak przy układaniu płytek podłogowych:
- jeśli używasz podłoża arkuszowego, umieść pierwszą kartę w rogu, upewniając się, że róg nie jest przekrzywiony. Jeśli tak, zaznacz linię cięcia dla całego rzędu i odetnij ją nożem biurowym zgodnie z oznaczeniem;
- przy pracy z materiałem w rolce - ostatnią spoinę wykonać na zakład 7 - 10 cm i linijką przeciąć wzdłuż podwójnej warstwy materiału na całej długości. Usuwając wąskie segmenty uzyskujemy idealne połączenie nawet przy nierównym cięciu;
- skleić wszystkie połączone krawędzie taśmą klejącą na całej długości, tworząc szczelną wykładzinę podłogową z podłożem;
- przyklej podłoże taśmą samoprzylepną do ścian na całym obwodzie.
Po ułożeniu podłoża można montować płyty laminowane.
- Podczas układania warstwy wierzchniej tego materiału na drewnianej podłodze zrębu należy usunąć starą farbę. Następnie wskazane jest oderwanie jednej lub dwóch desek i sprawdzenie stanu elementów nośnych - kłody. Jeśli gnicie zostanie stwierdzone przynajmniej w jednym miejscu, będziesz musiał całkowicie zdemontować starą powłokę i wymienić uszkodzone kłody. Jednocześnie należy sprawdzić dostateczność izolacji termicznej iw razie potrzeby uzupełnić jej poziom za pomocą keramzytu, żużla wielkopiecowego lub spienionego piasku. Ponownie domykamy podłogę tymi samymi deskami (jeśli nie ma potrzeby ich wymiany), ostrożnie przykręcamy wkrętami, wpuszczając główki w korpus desek.
- Instalując ogrzewanie podłogowe należy wziąć pod uwagę, że większość nośników ciepła obawia się nierówności podłogi, zwłaszcza folii. A podłoża nie są tutaj zbawieniem. Dobrze będzie ułożyć jastrychy samopoziomujące wzmocnione wiórami włóknistymi i nie myśleć już o nierównościach. Przymusowe naprawy z wymianą mat będą kosztować wielokrotnie więcej.
- Należy wziąć pod uwagę wymagania SNiP, aby poziom podłogi we wszystkich pomieszczeniach krycia był taki sam. Łatwo to wziąć pod uwagę przy budowie domu. A wykonując prace naprawcze w oddzielnym pomieszczeniu, należy pamiętać, że minimalna grubość laminatu z podłożem z najprostszej pianki polistyrenowej wynosi 7-8 cm i należy to wziąć pod uwagę podczas wykonywania prac.
Nieodłącznym atrybutem podłogi jest laminowana blacha podkładowa, która jednocześnie pełni kilka funkcji zapewniających długą żywotność podłogi. Wybierając amortyzator, należy wziąć pod uwagę szereg cech, które wpływają na wiele cech powłoki. Jednym z najważniejszych kryteriów jest optymalna grubość warstwy.
Czy zawsze potrzebne jest wsparcie?
Laminat wykonany jest z materiałów sztucznych, które mają istotne wady:
- wrażliwość na wpływ mechaniczny;
- wypaczenie.
Tylko podłoże pod laminat może zniwelować te wady. W końcu od jej obecności zależą właściwości izolacji cieplnej i akustycznej podłogi, odporność na wilgoć i jej żywotność. W takim przypadku warstwa tłumiąca musi spełniać określone wymagania:
- Materiał musi być obojętny na oddziaływanie z odczynnikami chemicznymi, zwłaszcza alkalicznymi;
- Właściwości bakteriobójcze wykładziny powinny wykluczać możliwość rozwoju pleśni pod powłoką;
- Materiał musi być niejadalny dla owadów i myszy;
- Konstrukcja klapy musi zapewniać wentylację podłogi;
- Wyściółka pod laminat ma za zadanie neutralizować poważne obciążenie systemu blokującego lameli.
Dodatkowo podkład jest w stanie niwelować drobne nierówności na szorstkim podłożu, a także pełnić funkcję amortyzatora łagodzącego uderzenia podczas chodzenia po powierzchni. Na podstawie powyższego staje się jasne, że podłoże w przypadku montażu powłoki laminowanej jest po prostu konieczne.
Grubość podłoża
Grubość podłoża może się zmieniać w znacznym zakresie: od 0,8 do 10 mm. Każdy z typów należy stosować wyłącznie zgodnie ze stanem podłoża oraz grubością płyt laminowanych. Rozważane poniżej rozmiary podkładów są najczęściej spotykane:
- Podłoże pod laminat 2 mm. Cienka warstwa tłumiąca o doskonałych właściwościach amortyzujących. Najczęściej używany do układania lameli, których grubość nie przekracza 5-6 mm;
- Podłoże pod laminat 3 mm. Ten rodzaj wykładziny zmniejsza poziom hałasu podczas chodzenia po powierzchni, nadaje się również do systemu „ciepła podłoga”. Często jest już w pakiecie z laminatem klasy 32 i 33;
- Podłoże pod laminat 5 mm. Gruby amortyzator, który znajduje zastosowanie w lokalach użytkowych. Poprawia wydajność powłoki, wydłużając jej żywotność.
Wskazówka: Ten materiał służy do układania lameli, których grubość przekracza 10 mm. Ponieważ podłoga laminowana „pływa”, cieńsze deski na bardzo grubym podłożu będą zwisać.
Wyznaczenie optymalnej grubości klapy
Wielu ekspertów twierdzi, że grubość podkładu powinna wynosić około 3 mm. To wystarczy, aby zniwelować drobne defekty na szorstkim podłożu i zapewnić amortyzację. Jednak przy znacznych różnicach wysokości rzędu 3 mm klapa będzie praktycznie bezużyteczna. Ale to wcale nie oznacza, że grubsza podszewka może rozwiązać ten problem.
Faktem jest, że miękki materiał wyściółki, na którym kładzie się laminat, może spowodować uszkodzenie zamków znajdujących się na końcach połączonych lameli. Dzieje się tak często podczas eksploatacji posadzki układanej na nierównym jastrychu. W efekcie na powierzchni pojawiają się duże szczeliny, co dodatkowo prowadzi do odrywania się poszczególnych desek od posadzki.
W przypadku klap wykonanych z materiałów sztucznych, takich jak polietylen czy polistyren, lepiej stawiać na małe grubości do 3 mm. Takie materiały szybko odkształcają się i stają się cieńsze w miejscach o największym obciążeniu mechanicznym. Może to prowadzić do luzów między laminatem a podstawą. Dlatego im większa grubość posadzki, tym więcej szczelin powstaje między deskami a jastrychem.
Jeśli grubość powłoki wraz z podkładem syntetycznym nie jest wystarczająca do wyrównania podłogi z innym pomieszczeniem, lepiej wybrać nieco grubszą podłogę korkową. Po pierwsze jest mało odkształcony i sprasowany, a po drugie ma znacznie dłuższą żywotność. Taka potrzeba pojawia się przy remontach mieszkań prywatnych.
Często poziom podłogi w korytarzu i pokojach okazuje się inny, co prowadzi do pojawienia się małych parapetów. Problem ten mogą wyeliminować gęste podłoża o grubości 3-4 mm.
Rodzaje przepustnic i ich rozmiary
Grubość podłoża pod laminatem zależy nie tylko od wielkości i grubości lameli, ale również od rodzaju użytych materiałów. Dlatego przed zakupem podłogi powinieneś przestudiować jej odmiany:
- Izolon. Ten rodzaj materiału ma doskonałą wodoodporność, dzięki czemu można go układać w pomieszczeniach o dużej wilgotności. Jednocześnie istnieje kilka rodzajów izolonu:
- O grubości od 1 do 1,5 mm. Produkowany jest w rolkach, których szerokość wynosi 80-90 cm;
- O grubości od 2 do 10 mm. Dostępna w postaci taśm o szerokości do 50 cm;
- O grubości od 20 do 60 mm. Najczęściej produkowane w formie płyt prostokątnych.
- materiał foliowy. Produkowany jest na bazie izolonu, dodatkowo zawiera cienką warstwę folii, czasem na podłożu samoprzylepnym. Amortyzator doskonale zatrzymuje ciepło i jest odporny na wilgoć. Dostępne w rolkach o szerokości do 120 cm i grubości do 5 mm;
- Podłogi z korka. Bardzo wytrzymały materiał z dobrą izolacją akustyczną i cieplną. Jest kilka jego rodzajów:
- W postaci arkusza o grubości od 2 do 4 mm. Jest traktowany specjalnym środkiem antyseptycznym, który zapobiega rozwojowi pleśni pod podłogą;
- Podłoga z elastycznego korka. Posiada dobrą izolację akustyczną. W tym przypadku grubość warstwy waha się od 1 do 5 mm;
- Amortyzator bitumiczno-korkowy. Trwała powłoka, która wytrzymuje duże obciążenia. Z reguły producenci produkują podłoża o grubości warstwy do 5 mm.
- Podszewka kompozytowa. Składa się z 3 głównych warstw: folia-polistyren-folia. Zwykle sprzedawany w rolkach o grubości warstwy 3 mm;
- Materiał styropianowy. Jeden z najtańszych amortyzatorów o grubości od 0,5 do 6 mm. Jednak przy dłuższym użytkowaniu może stać się cieńszy, co doprowadzi do uszkodzenia podłogi.
Cechy stylizacyjne
Po podjęciu decyzji o optymalnym rozmiarze podłogi i jej rodzaju, należy ją zamontować. Proces jest dość prosty, więc poradzi sobie nawet początkujący, który nigdy nie naprawiał podłogi. Ważne jest jedynie, aby postępować zgodnie z instrukcjami, które pozwolą prawidłowo ułożyć podłogę.
Arkusz układany jest w dwóch etapach:
- Pierwszy etap
- Przed rozpoczęciem pracy szorstką podstawę należy oczyścić z kurzu i brudu, a następnie wysuszyć;
- Następnie konieczne jest zapewnienie dodatkowej hydroizolacji podłogi;
- W tym celu najczęściej stosuje się trwałą folię z tworzywa sztucznego, którą umieszcza się na górze podstawy;
- Aby odciąć nadmiar folii, użyj zwykłych nożyczek;
- Ważne jest, aby folia zachodziła na ściany;
- W trakcie układania materiału warstwa hydroizolacyjna może się odsunąć. Dlatego pożądane jest przymocowanie go taśmą samoprzylepną.
- Druga faza
- Teraz musisz umieścić podłoże prostopadle do lameli. Jest to konieczne, aby podczas montażu lub eksploatacji wykładziny podłogowej poszczególne jej elementy nie poruszały się;
- Podobnie jak w przypadku folii hydroizolacyjnej, podłoże powinno zachodzić na ściany, utworzy to miskę;
- Jeżeli warstwa pośrednia ma pofałdowaną powierzchnię, pożądane jest, aby była ułożona przodem do podłoża. Wtedy pomoże to wyrównać bazę;
- W przypadku tłumika foliowego pożądane jest, aby folia była podwinięta;
- Podczas układania warstwy rolki połącz sąsiednie arkusze za pomocą molowej taśmy klejącej;
- Aby naprawić poszczególne płytki korka lub igieł, musisz użyć zszywacza lub kleju.
Ważny! Zdecydowanie nie zaleca się układania klapy w kilku warstwach w celu wypoziomowania podłoża. Może to prowadzić do bardzo katastrofalnych konsekwencji. Po pierwsze, pod wpływem obciążenia powłoki, podłoga ulegnie obwisaniu i system blokujący ulegnie uszkodzeniu, a po drugie warstwy ściółki mogą przesuwać się względem siebie, co doprowadzi do powstania pustek pod podłogą .
Z zastrzeżeniem wszystkich zasad wyboru podłoża, a także sposobu jego ułożenia, wykładzina posłuży Ci przez co najmniej 10 lat. Jednocześnie warstwa tłumiąca zapewni dobry poziom izolacji akustycznej i cieplnej. Ponadto wysokiej jakości warstwa znacznie zmniejsza obciążenie zamków między płytami laminowanymi, dzięki czemu podłoga pozostaje „nowa” przez długi czas.