Przyrządy kontrolno-pomiarowe do kotłów parowych i wodnych. Jakie przyrządy kontrolno-pomiarowe są wyposażone w jednostki kotłowe? Pośrednio działające regulatory
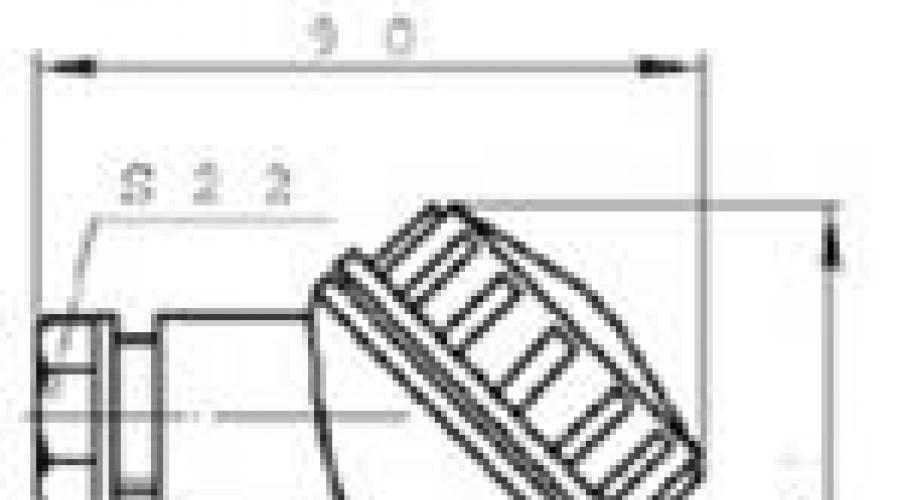
Oprzyrządowanie i automatyka (oprzyrządowanie i automatyka) przeznaczone są do pomiaru, kontroli i regulacji temperatury, ciśnienia, poziomu wody w bębnie oraz zapewnienia bezpiecznej pracy wytwornic ciepła i urządzeń elektroenergetycznych kotłowni.
1. Pomiar temperatury.
Do pomiaru temperatury płynu roboczego stosuje się termometry manometryczne i rtęciowe. Do rurociągu przyspawana jest tuleja ze stali nierdzewnej, której koniec powinien sięgać środka rurociągu, jest napełniany olejem i opuszczany jest do niego termometr.
Termometr manometryczny składa się z żarówki termicznej, rurki miedzianej lub stalowej i sprężyny rurowej o owalnym przekroju, połączonych przekładnią dźwigniową ze strzałką wskazującą.
Ryż. 3.1. Termometr manometryczny
1-cylinder termiczny; kapilara 2-przyłączowa; 3-ciąg; 4-strzałka; 5-tarcz; Sprężyna o średnicy 6; Mechanizm sektorowy 7 plemion
Całość wypełniona jest gazem obojętnym (azotem) pod ciśnieniem 1...1,2 MPa. Wraz ze wzrostem temperatury wzrasta ciśnienie w układzie, a sprężyna przesuwa igłę poprzez system dźwigni. Wskazujące i samorejestrujące termometry manometryczne są mocniejsze od termometrów szklanych i umożliwiają przesyłanie odczytów na odległość do 60 m.
Działanie termometry oporowe– platyna (TSP) i miedź (TCM) opierają się na wykorzystaniu zależności oporu elektrycznego substancji od temperatury.
Ryż. 3.2. Termometry oporowe platynowe, miedziane
Działanie termometr termoelektryczny w oparciu o wykorzystanie zależności termoEMF termopary od temperatury. Termopara, jako czuły element termometru, składa się z dwóch różnych przewodników (termoelektrod), których jeden koniec (pracujący) jest połączony ze sobą, a drugi (wolny) jest podłączony do urządzenia pomiarowego. Przy różnych temperaturach końca roboczego i wolnego w obwodzie termometru termoelektrycznego pojawia się emf.
Najpopularniejsze typy termopar to TXA (chromel-alumel), TKhK (chromel-kopel). Termopary do wysokich temperatur umieszczone są w rurce ochronnej (stalowej lub porcelanowej), której dolna część zabezpieczona jest obudową i pokrywą. Termopary charakteryzują się wysoką czułością, niską bezwładnością i możliwością instalowania urządzeń rejestrujących na dużych odległościach. Termopara jest podłączona do urządzenia za pomocą przewodów kompensacyjnych.
2. Pomiar ciśnienia.
Do pomiaru ciśnienia stosuje się barometry, manometry, próżniomierze, mierniki ciągu itp., Które mierzą ciśnienie barometryczne lub nadciśnienie, a także podciśnienie w mm wody. Art., mm Hg. Art., m woda. Art., MPa, kgf/cm2, kgf/m2 itp. Aby kontrolować pracę pieca kotłowego (podczas spalania gazu i oleju opałowego), można zainstalować następujące urządzenia:
1) manometry (ciecz, membrana, sprężyna) - pokazują ciśnienie paliwa na palniku za zaworem roboczym;
Ryż. 3.3. Tensometry:
1 - membrana; 2 - tensometr aktywny i kompensacyjny; 3 - konsola; 4-strzałka
2) manometry (kształtne, membranowe, różnicowe) - pokazują ciśnienie powietrza na palniku za zaworem regulacyjnym;
3) mierniki ciągu (TNZh, membrana) - pokazują próżnię w palenisku.
Płynny miernik ciągu(TNZh) służy do pomiaru małych ciśnień lub podciśnień.
Ryż. 3.4. Miernik ciśnienia ciągu typu TNZh-N
Aby uzyskać dokładniejsze odczyty, stosuje się mierniki ciągu z nachyloną rurką, której jeden koniec zanurza się w naczyniu o dużym przekroju, a jako płyn roboczy stosuje się alkohol (gęstość 0,85 g/cm3) zabarwiony na kolor magenta. Puszka podłączana jest do króćca „+” z atmosferą (ciśnienie barometryczne) i przez złączkę wlewa się alkohol. Szklana rurka jest połączona złączką „-” (próżniową) z gumową rurką i paleniskiem kotła. Jedna śruba ustawia „zero” skali tuby, a druga ustawia poziom na pionowej ścianie. Podczas pomiaru podciśnienia rurkę impulsową podłączamy do przyłącza „-”, a ciśnienie barometryczne do przyłącza „+”.
Manometr sprężynowy przeznaczony do wskazywania ciśnienia w zbiornikach i rurociągach i montowany jest na odcinku prostym. Elementem czułym jest mosiężna rurka zakrzywiona w owalny sposób, której jeden koniec mocuje się w złączce, a wolny koniec pod wpływem ciśnienia cieczy roboczej zostaje wyprostowany (ze względu na różnicę powierzchni wewnętrznej i zewnętrznej ) i poprzez układ trakcji i sektor przekładni przekazuje siłę na wskazówkę zamontowaną na kole zębatym. Mechanizm ten znajduje się w
obudowa ze skalą, przykryta szkłem i plombowana. Skalę dobiera się tak, aby przy ciśnieniu roboczym wskazówka znajdowała się w środkowej trzeciej części skali. Skala powinna mieć czerwoną linię wskazującą dopuszczalne ciśnienie.
W elektryczne manometry kontaktowe ECM ma dwa stałe, stałe styki na skali i ruchomy styk na wskaźniku roboczym.
Ryż. 3.5. Manometr z przyłączem elektrycznym TM-610
Kiedy strzałka dotknie stałego styku, sygnał elektryczny z nich jest wysyłany do centrali i włącza się alarm. Przed każdym manometrem należy zamontować zawór trójdrogowy w celu jego przepłukania, sprawdzenia i odcięcia oraz rurkę syfonową (uszczelnienie hydrauliczne wypełnione wodą lub kondensatem) o średnicy co najmniej 10 mm w celu zabezpieczenia wewnętrznego mechanizm manometru przed działaniem wysokich temperatur. Przy instalowaniu manometru na wysokości do 2 m od poziomu platformy obserwacyjnej średnica jego korpusu musi wynosić co najmniej 100 mm; od 2 do 3 m – co najmniej 150 mm; 3…5 m – nie mniej niż 250 mm; na wysokości większej niż 5 m instalowany jest obniżony manometr. Manometr należy zamontować pionowo lub pochylić do przodu pod kątem do 30° tak, aby jego odczyty były widoczne z poziomu platformy obserwacyjnej, a klasa dokładności manometrów musi wynosić co najmniej 2,5 – przy ciśnieniach do 2,5 MPa i nie mniej niż 1,5 – od 2,5 do 14 MPa.
Manometrów nie można używać, jeżeli nie posiadają plomby (stemply) lub upłynął termin przeglądu, wskazówka nie powraca do zera na skali (przy wyłączonym manometrze), jest stłuczona szyba lub występują inne szkoda. Pieczęć lub znak instaluje Gosstandart podczas kontroli raz w roku.
Sprawdzanie manometru powinno być przeprowadzane przez operatora przy każdym odbiorze zmiany, a przez administrację co najmniej raz na 6 miesięcy przy użyciu manometru kontrolnego. Manometr sprawdza się w następującej kolejności:
1) wizualnie zauważyć położenie strzałki;
2) za pomocą uchwytu zaworu trójdrożnego podłączyć manometr do atmosfery - strzałka powinna wskazywać zero;
3) powoli obróć pokrętło do poprzedniej pozycji - strzałka powinna wrócić do poprzedniej (sprzed sprawdzenia) pozycji;
4) obrócić uchwyt kranu w kierunku zgodnym z ruchem wskazówek zegara i ustawić go w pozycji, w której rurka syfonu będzie podłączona do atmosfery - w celu przepłukania; 5) obrócić pokrętło kranu w przeciwnym kierunku i ustawić je w pozycji neutralnej na kilka minut, co spowoduje odłączenie manometru od atmosfery i kotła - w celu gromadzenia się wody w dolnej części rury syfonowej;
6) powoli obróć uchwyt kranu w tę samą stronę i ustaw go w pierwotnej pozycji roboczej - strzałka powinna wrócić na swoje pierwotne miejsce.
Aby sprawdzić dokładność wskazań manometrów, do kołnierza sterującego za pomocą wspornika mocuje się manometr kontrolny (modelowy), a uchwyt zaworu ustawia się w pozycji, w której oba manometry są połączone z przestrzenią pod ciśnieniem. Manometr roboczy powinien dawać takie same odczyty jak manometr kontrolny, po czym wyniki zapisuje się w protokole kontroli kontrolnej.
Na wyposażeniu kotłowni należy zamontować manometry:
1) w kotle parowym - źródło ciepła: na korpusie kotła, a jeżeli znajduje się przegrzewacz - za nim, do zaworu głównego; na linii zasilającej przed zaworem regulującym dopływ wody; na ekonomizerze - wlot i wylot wody do zaworu odcinającego i zaworu bezpieczeństwa; NA
sieć wodociągowa – podczas korzystania z niej;
2) w zespole kotła wodnego - źródło ciepła: na wlocie i wylocie wody aż do zaworu odcinającego lub zasuwy; na przewodach ssawnym i tłocznym pomp obiegowych, znajdujących się na tej samej wysokości; na przewodach grzewczych. W kotłach parowych o wydajności pary powyżej 10 t/h i kotłach na gorącą wodę o mocy cieplnej powyżej 6 MW wymagana jest instalacja manometru rejestrującego.
3. Wskaźniki wody.
Podczas pracy kotła parowego poziom wody waha się pomiędzy najniższym i najwyższym położeniem. Najniższy dopuszczalny poziom (LAL) wody w bębnach kotłów parowych ustala się (określa), aby wyeliminować możliwość przegrzania metalowych ścianek elementów kotła i zapewnić niezawodny dopływ wody do rur spustowych obiegów cyrkulacyjnych. Położenie najwyższego dopuszczalnego poziomu (HPL) wody w bębnach kotłów parowych określa się na podstawie warunków zapobiegania przedostawaniu się wody do rurociągu pary lub przegrzewacza. Objętość wody zawartej w bębnie pomiędzy najwyższym a najniższym poziomem określa „rezerwę żywieniową”, czyli: czas, w którym kocioł może pracować bez przedostawania się wody.
Każdy kocioł parowy musi być wyposażony w co najmniej dwa bezpośrednio działające wskaźniki poziomu wody. Wskaźniki wody należy montować pionowo lub pochylone do przodu, pod kątem nie większym niż 30°, tak aby poziom wody był dobrze widoczny ze stanowiska pracy. Wskaźniki poziomu wody podłącza się do górnego bębna kotła za pomocą rur prostych o długości do 0,5 m i średnicy wewnętrznej co najmniej 25 mm lub większej niż 0,5 m i średnicy wewnętrznej co najmniej 50 mm.
W kotłach parowych o ciśnieniu do 4 MPa stosuje się szkło wskaźnikowe (VUS) – urządzenia ze szkłem płaskim o powierzchni falistej, w którym podłużne rowki szkła odbijają światło, sprawiając, że woda wydaje się ciemna, a para jasna. Szybę umieszcza się w ramce (kolumnie) o szerokości szczeliny widokowej co najmniej 8 mm, na której należy wskazać dopuszczalny poziom wody górny i dolny (w postaci czerwonych strzałek) oraz wysokość szyby musi przekraczać dopuszczalne granice wymiarów o co najmniej 25 mm z każdej strony. Strzałka NDU jest zainstalowana 100 mm nad linią spalania kotła.
Linia ognia- jest to najwyższy punkt styku gorących spalin z nieizolowaną ścianą elementu kotła.
Urządzenia wskazujące wodę służące do odłączenia ich od kotła i przeprowadzenia przedmuchu wyposażone są w zawory odcinające (krany lub zawory). Okucia muszą być wyraźnie oznaczone (odlane, wytłoczone lub pomalowane) w kierunku otwierania lub zamykania, a średnica wewnętrzna przelotu musi wynosić co najmniej 8 mm. Aby spuścić wodę podczas płukania, przewidziano podwójny lejek z urządzeniami zabezpieczającymi i rurą spustową do swobodnego odprowadzania, a na linii płomienia kotła zamontowany jest zawór odpowietrzający.
Operator kotłowni ma obowiązek przynajmniej raz na zmianę sprawdzić wziernik wody metodą przedmuchu, przy czym powinien:
1) upewnić się, że poziom wody w kotle nie spadł poniżej poziomu minimalnego;
2) wizualnie zauważyć położenie poziomu wody w szklance;
3) otworzyć zawór odpowietrzający – następuje przepłukanie zaworów pary i wody;
4) zamknąć zawór pary, przedmuchać zawór wody;
5) otwórz kran pary - oba krany zostaną przepłukane;
6) zakręcić kran z wodą, wydmuchać parę;
7) odkręcić kran z wodą – oba krany są odpowietrzone;
8) zamknij zawór odpowietrzający i obserwuj poziom wody, który powinien szybko się podnieść i oscylować wokół poprzedniego poziomu, jeśli szyba nie była zatkana.
Nie zamykaj obu kranów, gdy kran odpowietrzający jest otwarty, ponieważ szklanka ostygnie i może pęknąć, jeśli uderzy w nią gorąca woda. Jeżeli po przedmuchaniu woda w szkle podnosi się powoli lub osiągnęła inny poziom lub nie waha się, należy powtórzyć przedmuchanie, a jeżeli powtórne przedmuchanie nie daje rezultatów, należy oczyścić zatkany kanał .
Gwałtowne wahania poziomu wody charakteryzują się nieprawidłowym wrzeniem na skutek zwiększonej zawartości soli, zasad, szlamów lub usuwania pary z kotła w ilości większej niż jest ona wytwarzana, a także spalania sadzy w kanałach kominowych kotła.
Niewielkie wahania poziomu wody charakteryzują się częściowym „zagotowaniem” lub zatkaniem kranu, a jeśli poziom wody jest wyższy niż normalnie, „zagotowaniem” lub zatkaniem kranu pary. Kiedy kran pary jest całkowicie zatkany, para znajdująca się nad poziomem wody skrapla się, powodując całkowite i szybkie napełnienie szklanki wodą aż do samej góry. Jeżeli kran z wodą jest całkowicie zatkany, poziom wody w szklance będzie powoli się podnosił na skutek kondensacji pary wodnej lub uspokoi się, co może skutkować tym, że bez zauważenia wahań poziomu wody i zobaczenia jej w szklance, może pomyśleć, że w bojlerze jest wystarczająco dużo wody.
Niedopuszczalne jest zwiększanie poziomu wody powyżej dopuszczalnego ciśnienia powietrza, gdyż woda będzie przedostawać się do przewodu parowego, co doprowadzi do uderzenia wodnego i pęknięcia przewodu parowego.
Gdy poziom wody spadnie poniżej NDU, surowo zabrania się zasilania kotła parowego wodą, ponieważ w przypadku braku wody metal ścian kotła staje się bardzo gorący, staje się miękki, a gdy woda doprowadzana jest do korpusu kotła, następuje silne tworzenie się pary, co prowadzi do gwałtownego wzrostu ciśnienia, rozcieńczenia metalu, powstawania pęknięć i pęknięcia rury.
Jeżeli odległość od miejsca obserwacji poziomu wody jest większa niż 6 m, a także w przypadku słabej widoczności (oświetlenia) przyrządów, należy zainstalować dwa obniżone zdalne wskaźniki poziomu; w tym przypadku na walczakach kotła można zamontować jeden VUS bezpośredniego działania. Wskaźniki poziomu obniżonego muszą być podłączone do bębna na oddzielnych armaturach i posiadać urządzenie tłumiące.
4. Pomiar i regulacja poziomu wody w bębnie.
Manometr różnicowy membranowy(DM) służy do proporcjonalnej regulacji poziomu wody w bębnowych kotłach parowych.
Ryż. 3.6. Membrana wskazująca manometr różnicowy z membraną pionową
1 - kamera „plus”; 2 - kamera „minusowa”; 5 - wrażliwa membrana falista; 4- pręt nadawczy; 5 - mechanizm transmisji; 6 - zawór bezpieczeństwa i odpowiednio strzałka wskazująca, wskazująca zmierzone ciśnienie na skali przyrządu
Manometr składa się z dwóch skrzynek membranowych połączonych ze sobą poprzez otwór w membranie i wypełnionych kondensatem. Dolną skrzynkę membranową montuje się w komorze dodatniej wypełnionej kondensatem, natomiast górną w komorze ujemnej wypełnionej wodą i połączonej z mierzonym obiektem (górnym bębnem kotła). Rdzeń cewki indukcyjnej jest połączony ze środkiem górnej membrany. Przy średnim poziomie wody w kotle nie następuje spadek ciśnienia, a skrzynki membranowe są zrównoważone.
Wraz ze wzrostem poziomu wody w korpusie kotła wzrasta ciśnienie w komorze ujemnej, skrzynia membranowa kurczy się, a ciecz spływa do komory dolnej, powodując ruch rdzenia w dół. W tym przypadku w uzwojeniu cewki powstaje pole elektromagnetyczne, które przesyła sygnał przez wzmacniacz do siłownika i zamyka zawór na linii zasilającej, tj. zmniejsza przepływ wody do bębna. Gdy poziom wody opadnie, DM działa w odwrotnej kolejności.
Kolumna poziomu Jednostka sterująca przeznaczona jest do pozycyjnej kontroli poziomu wody w korpusie kotła.
Ryż. 3.7. Kolumna do pomiaru poziomu UK-4
Składa się z cylindrycznej kolumny (rury) o średnicy około 250 mm, w której zamontowane są pionowo cztery elektrody, zdolne do kontrolowania najwyższego i najniższego dopuszczalnego poziomu wody (VDU i NDU), najwyższego i najniższego poziomu wody roboczej w bęben (VRU i NRU), którego działanie opiera się na przewodności elektrycznej wody. Kolumna połączona jest bocznie z objętością pary i wody korpusu kotła za pomocą rur z kranami. Na dole kolumny znajduje się zawór upustowy.
Po osiągnięciu poziomu wody w ASU przekaźnik zostaje włączony, a stycznik przerywa obwód mocy rozrusznika magnetycznego, wyłączając napęd pompy zasilającej. Dopływ wody do kotła zostaje przerwany. Poziom wody w bębnie spada, a gdy spadnie poniżej NRU, przekaźnik zostaje odłączony od zasilania i włączona zostaje pompa zasilająca. Po osiągnięciu poziomu wody w VDU i NDU sygnał elektryczny z elektrod przechodzi przez jednostkę sterującą do odcięcia dopływu paliwa do paleniska.
5. Przyrządy do pomiaru przepływu.
Przepływomierze służą do pomiaru przepływu cieczy (wody, oleju opałowego), gazów i pary:
1) wolumetryczny o dużej prędkości, mierzący objętość cieczy lub gazu według natężenia przepływu i sumujący te wyniki;
2) dławiące, przy zmiennej i stałej różnicy ciśnień lub rotametry.
W komorze roboczej szybki przepływomierz objętościowy(wodomierz, olejomierz) zainstalowany jest talerz obrotowy łopatkowy lub spiralny, który obraca się od cieczy wchodzącej do urządzenia i przekazuje natężenie przepływu do mechanizmu zliczającego.
Wolumetryczny licznik obrotowy(typ RG) mierzy całkowite natężenie przepływu gazu do 1000 m 3 /h, dla czego w komorze roboczej umieszczone są dwa wzajemnie prostopadłe wirniki, które pod wpływem ciśnienia przepływającego gazu wprawiane są w ruch obrotowy, każdy obrót która przekazywana jest poprzez koła zębate i skrzynię biegów do mechanizmu zliczającego.
Przepływomierze przepustnicy przy zmiennym spadku ciśnienia posiadają urządzenia ograniczające - zwykłe membrany (podkładki) komorowe i bezdętkowe z otworem mniejszym niż przekrój rurociągu.
Kiedy przepływ czynnika przez otwór podkładki zwiększa się jego prędkość, ciśnienie za podkładką maleje, a różnica ciśnień przed i za urządzeniem dławiącym zależy od natężenia przepływu mierzonego czynnika: im większa jest ilość substancji , tym większa różnica.
Pomiar różnicy ciśnień przed i za membraną odbywa się za pomocą manometru różnicowego, z którego pomiarów można obliczyć prędkość przepływu płynu przez otwór podkładki. Membrana normalna wykonana jest w postaci dysku (wykonanego ze stali nierdzewnej) o grubości 3...6 mm z centralnym otworem o ostrej krawędzi i powinna być umieszczona po stronie wlotu cieczy lub gazu i instalowana pomiędzy kołnierzami na prosty odcinek rurociągu. Impuls ciśnienia do manometru różnicy ciśnień wytwarzany jest przez otwory w komorach pierścieniowych lub przez otwory po obu stronach membrany.
W celu pomiaru przepływu pary na rurkach impulsowych do manometru różnicy ciśnień instalowane są naczynia wyrównawcze (kondensacyjne), których zadaniem jest utrzymanie stałego poziomu kondensatu w obu rurociągach. Przy pomiarze przepływu gazu manometr różnicowy należy zamontować nad urządzeniem ograniczającym, tak aby kondensat powstający w rurkach impulsowych mógł spłynąć do rurociągu, a rurki impulsowe na całej długości powinny posiadać spadek w stronę gazociągu (gazociągu). i być podłączony do górnej połowy podkładki. Obliczanie membran i montaż na rurociągach odbywa się zgodnie z przepisami.
6. Analizatory gazów przeznaczone są do monitorowania kompletności spalania paliwa, nadmiaru powietrza oraz określania udziału objętościowego dwutlenku węgla, tlenu, tlenku węgla, wodoru i metanu w produktach spalania.
Ze względu na zasadę działania dzielimy je na:
1) chemiczny(GHP, Orsa, VTI), na podstawie sekwencyjnej absorpcji gazów zawartych w analizowanej próbce;
2) fizyczny, działające na zasadzie pomiaru parametrów fizycznych (gęstość gazu i powietrza, ich przewodność cieplna);
3) chromatograficzny, polegająca na adsorpcji (absorpcji) składników mieszaniny gazowej z określonym adsorbentem (węglem aktywnym) i ich sekwencyjnej desorpcji (uwalnianiu) podczas przechodzenia przez kolumnę z gazowym adsorbentem.
Kotłownia (kotłownia) to konstrukcja, w której podgrzewany jest płyn roboczy (chłodziwo) (zwykle woda) dla systemu grzewczego lub zaopatrzenia w parę, umieszczoną w jednym pomieszczeniu technicznym. Kotłownie podłączane są do odbiorców za pomocą sieci ciepłowniczej i/lub rurociągów parowych. Głównym urządzeniem kotłowni jest kocioł parowy, płomienicowy i/lub wodny. Kotłownie służą do scentralizowanego zaopatrzenia w ciepło i parę lub do lokalnego zaopatrzenia budynków w ciepło.
Kotłownia to zespół urządzeń umieszczonych w specjalnych pomieszczeniach i służących do zamiany energii chemicznej paliwa na energię cieplną pary lub gorącej wody. Jego głównymi elementami są kocioł, urządzenie spalające (piec), urządzenia podające i ciągowe. Ogólnie rzecz biorąc, instalacja kotła to połączenie kotła(ów) i wyposażenia, w tym następujących urządzeń: dostarczanie paliwa i spalanie; oczyszczanie, przygotowanie chemiczne i odpowietrzanie wody; wymienniki ciepła do różnych celów; pompy wody źródłowej (surowej), sieciowe lub obiegowe - do obiegu wody w systemie grzewczym, uzupełniające - w celu zastąpienia wody zużytej przez odbiorcę i nieszczelności w sieciach, pompy zasilające do dostarczania wody do kotłów parowych, recyrkulacja (mieszanie); zbiorniki na składniki odżywcze, zbiorniki kondensacyjne, zbiorniki do przechowywania ciepłej wody; dmuchawy i kanały powietrzne; wyciągi dymowe, tor gazowy i komin; urządzenia wentylacyjne; systemy automatycznej regulacji i bezpieczeństwa spalania paliw; osłona termiczna lub panel sterowania.
Kocioł jest urządzeniem wymiany ciepła, w którym ciepło z gorących produktów spalania paliwa jest przekazywane do wody. W efekcie woda w kotłach parowych zamieniana jest na parę, a w kotłach na gorącą wodę podgrzewana do wymaganej temperatury.
Urządzenie do spalania służy do spalania paliwa i zamiany jego energii chemicznej na ciepło ogrzanych gazów.
Urządzenia podające (pompy, inżektory) przeznaczone są do dostarczania wody do kotła.
Urządzenie ciągu składa się z wentylatorów nadmuchowych, układu kanałów gazowo-powietrznych, oddymiaczy i komina, które zapewniają dopływ wymaganej ilości powietrza do paleniska oraz przepływ produktów spalania przez przewody kotła, a także ich usuwanie do atmosfery. Produkty spalania, przemieszczając się przez kanały kominowe i wchodząc w kontakt z powierzchnią grzewczą, przekazują ciepło wodzie.
Aby zapewnić bardziej ekonomiczną pracę, nowoczesne systemy kotłowe posiadają elementy pomocnicze: ekonomizer wody i nagrzewnicę powietrza, które służą odpowiednio do podgrzewania wody i powietrza; urządzenia do podawania paliwa i odpopielania, oczyszczania gazów spalinowych i wody zasilającej; urządzenia do kontroli termicznej i urządzenia automatyki, które zapewniają normalną i nieprzerwaną pracę wszystkich części kotłowni.
W zależności od wykorzystania ciepła kotłownie dzielimy na energetyczne, ciepłownicze i przemysłowe i ciepłownicze.
Kotłownie energetyczne dostarczają parę do elektrowni parowych wytwarzających energię elektryczną i zwykle stanowią część kompleksu elektrowni. Kotłownie grzewcze i przemysłowe znajdują się w przedsiębiorstwach przemysłowych i zapewniają ciepło dla systemów grzewczych i wentylacyjnych, dostarczania ciepłej wody do budynków i procesów produkcyjnych. Kotłownie grzewcze rozwiązują te same problemy, ale obsługują budynki mieszkalne i użyteczności publicznej. Dzieli się je na wolnostojące, blokujące, tj. sąsiadujących z innymi budynkami i wbudowanych w budynki. Ostatnio coraz częściej buduje się osobne, powiększone kotłownie z myślą o obsłudze zespołu budynków, osiedla mieszkaniowego czy mikrodzielnicy.
Instalowanie kotłowni wbudowanych w budynki mieszkalne i użyteczności publicznej jest obecnie dopuszczalne wyłącznie po odpowiednim uzasadnieniu i porozumieniu z organami inspekcji sanitarnej.
Kotłownie małej mocy (indywidualne i małych grup) składają się zazwyczaj z kotłów, pomp obiegowych i uzupełniających oraz urządzeń ciągu. W zależności od tego wyposażenia określa się głównie wymiary kotłowni.
2. Klasyfikacja instalacji kotłowych
Instalacje kotłowe, w zależności od charakteru odbiorców, dzielą się na energetyczne, produkcyjne oraz ciepłownicze i ciepłownicze. W zależności od rodzaju produkowanego chłodziwa dzieli się je na parę (do wytwarzania pary) i gorącą wodę (do wytwarzania gorącej wody).
Kotłownie energetyczne wytwarzają parę do turbin parowych w elektrowniach cieplnych. Kotłownie tego typu wyposażane są najczęściej w kotłownie dużej i średniej mocy, wytwarzające parę o podwyższonych parametrach.
Przemysłowe kotły grzewcze (zwykle parowe) wytwarzają parę nie tylko na potrzeby przemysłu, ale także do ogrzewania, wentylacji i zaopatrzenia w ciepłą wodę.
Kotły grzewcze (głównie wodne, ale mogą być także parowe) przeznaczone są do obsługi instalacji grzewczych w obiektach przemysłowych i mieszkalnych.
W zależności od skali zaopatrzenia w ciepło kotłownie grzewcze dzielą się na lokalne (indywidualne), grupowe i rejonowe.
Kotłownie lokalne wyposażane są najczęściej w kotły wodne gorące, które podgrzewają wodę do temperatury nie wyższej niż 115°C lub kotły parowe o ciśnieniu roboczym do 70 kPa. Takie kotłownie są przeznaczone do dostarczania ciepła do jednego lub więcej budynków.
Grupowe systemy kotłowe dostarczają ciepło do grup budynków, obszarów mieszkalnych lub małych osiedli. Wyposażone są w kotły parowe i gorącą wodę o większej mocy grzewczej niż kotły lokalnych kotłowni. Kotłownie te są zwykle zlokalizowane w specjalnie skonstruowanych oddzielnych budynkach.
Kotłownie ciepłownicze służą do dostarczania ciepła do dużych obszarów mieszkalnych: są wyposażone w stosunkowo mocne kotły wodne lub parowe.
Ryż. 1.
Ryż. 2.
Ryż. 3.
Ryż. 4.
Zwyczajowo przedstawia się poszczególne elementy schematu instalacji kotła w postaci prostokątów, okręgów itp. i połączyć je ze sobą liniami (ciągłymi, przerywanymi), wskazując rurociąg, przewody parowe itp. Istnieją znaczne różnice w podstawowych schematach kotłowni parowych i wodnych. Kotłownia parowa (ryc. 4, a) składająca się z dwóch kotłów parowych 1, wyposażonych w indywidualne ekonomizery wody 4 i powietrza 5, zawiera grupowy kolektor popiołu 11, do którego spaliny doprowadzane są przez wieprz zbiorczy 12. Do ssania spalin w obszarze pomiędzy popielnikiem 11 a oddymiaczami 7 z silnikami elektrycznymi 8 instaluje się w kominie 9. W celu obsługi kotłowni bez oddymiaczy montuje się klapy 10.
Para z kotłów osobnymi przewodami parowymi 19 wchodzi do wspólnego przewodu parowego 18 i przez nią do odbiornika 17. Po oddaniu ciepła para skrapla się i powraca przewodem kondensatu 16 do kotłowni w zbiorniku kondensatu 14. Przez rurociąg 15, do zbiornika kondensatu dostarczana jest dodatkowa woda z sieci wodociągowej lub chemicznego uzdatniania wody (w celu zrekompensowania objętości niezwróconej od odbiorców).
W przypadku utraty części kondensatu przez odbiorcę, mieszanina kondensatu i dodatkowej wody jest dostarczana ze zbiornika kondensatu za pomocą pomp 13 rurociągiem zasilającym 2, najpierw do ekonomizera 4, a następnie do kotła 1. Powietrze potrzebne do spalania zasysane jest przez wentylatory odśrodkowe 6 częściowo z kotłowni pokojowej, częściowo z zewnątrz oraz kanałami powietrznymi 3 i dostarczane jest najpierw do nagrzewnic powietrza 5, a następnie do palenisk kotłów.
Instalacja kotła wodnego (rys. 4, b) składa się z dwóch kotłów podgrzewających wodę 1, jednego grupowego ekonomizera wody 5, obsługującego oba kotły. Spaliny opuszczające ekonomizer wspólnym kanałem zbiorczym 3 trafiają bezpośrednio do komina 4. Woda podgrzana w kotłach trafia do wspólnego rurociągu 8, skąd jest dostarczana do odbiorcy 7. Po oddaniu ciepła schłodzona woda przez powrót rurociąg 2 jest wysyłany najpierw do ekonomizera 5, a następnie ponownie do kotłów. Woda przepływa przez obieg zamknięty (kocioł, odbiornik, ekonomizer, kocioł) za pomocą pomp obiegowych 6.
Ryż. 5. : 1 - pompa obiegowa; 2 - palenisko; 3 - przegrzewacz; 4 - górny bęben; 5 - podgrzewacz wody; 6 - nagrzewnica powietrza; 7 - komin; 8 - wentylator odśrodkowy (oddymiający); 9 - wentylator dostarczający powietrze do nagrzewnicy
Na ryc. Rysunek 6 pokazuje schemat zespołu kotłowego z kotłem parowym posiadającym górny bęben 12. W dolnej części kotła znajduje się palenisko 3. Do spalania paliwa ciekłego lub gazowego stosuje się dysze lub palniki 4, przez które paliwo razem wraz z powietrzem jest dostarczany do paleniska. Kocioł ograniczony jest ścianami ceglanymi - okładzina 7.
Podczas spalania paliwa wydzielane ciepło podgrzewa wodę do wrzenia w sitach rurowych 2 zainstalowanych na wewnętrznej powierzchni paleniska 3 i zapewnia jej przemianę w parę wodną.
Ryc. 6.
Spaliny z paleniska dostają się do kanałów kotłowych utworzonych przez wykładzinę i specjalne przegrody zamontowane w wiązkach rur. Podczas ruchu gazy przemywają wiązki rur kotła i przegrzewacza 11, przechodzą przez ekonomizer 5 i nagrzewnicę powietrza 6, gdzie są również chłodzone w wyniku przekazywania ciepła do wody wchodzącej do kotła i powietrza dostarczanego do palenisko. Następnie znacznie schłodzone spaliny usuwane są kominem 19 do atmosfery za pomocą wyciągu dymu 17. Spaliny z kotła można usunąć bez oddymiania, pod wpływem naturalnego ciągu wytwarzanego przez komin.
Woda ze źródła wody rurociągiem zasilającym dostarczana jest pompą 16 do ekonomizera wody 5, skąd po podgrzaniu wpływa do górnego bębna kotła 12. Napełnienie korpusu kotła wodą kontrolowane jest za pomocą wskaźnika wody szkło zamontowane na bębnie. W tym przypadku woda odparowuje, a powstała para gromadzi się w górnej części górnego bębna 12. Następnie para trafia do przegrzewacza 11, gdzie pod wpływem ciepła gazów spalinowych zostaje całkowicie wysuszona i wzrasta jej temperatura.
Z przegrzewacza 11 para wchodzi do głównego przewodu parowego 13, a stamtąd do odbiorcy, a po wykorzystaniu jest skraplana i zawracana do kotłowni w postaci gorącej wody (kondensatu).
Straty kondensatu od konsumenta uzupełniane są wodą z wodociągu lub z innych źródeł zaopatrzenia w wodę. Woda przed wejściem do kotła poddawana jest odpowiedniemu uzdatnieniu.
Powietrze potrzebne do spalania paliwa pobierane jest z reguły ze szczytu kotłowni i dostarczane wentylatorem 18 do nagrzewnicy 6, gdzie jest podgrzewane i kierowane do paleniska. W kotłowniach o małej pojemności zwykle nie ma nagrzewnic powietrza, a zimne powietrze jest dostarczane do paleniska albo przez wentylator, albo przez podciśnienie w palenisku wytwarzane przez komin. Instalacje kotłowe wyposażone są w urządzenia do uzdatniania wody (niepokazane na schemacie), oprzyrządowanie i odpowiednią automatykę, co zapewnia ich nieprzerwaną i niezawodną pracę.
Ryż. 7.
Do prawidłowego montażu wszystkich elementów kotłowni należy posłużyć się schematem elektrycznym, którego przykład pokazano na ryc. 9.
Ryż. 9.
Kotły wodne przeznaczone są do wytwarzania ciepłej wody wykorzystywanej do celów grzewczych, zaopatrzenia w ciepłą wodę i innych celów.
Aby zapewnić normalną pracę, kotłownie z kotłami ciepłej wody są wyposażone w niezbędną armaturę, oprzyrządowanie i urządzenia automatyki.
Kotłownia wodna ma jeden czynnik chłodzący - wodę, w przeciwieństwie do kotłowni parowej, która ma dwa czynniki chłodzące - wodę i parę. W związku z tym kotłownia parowa musi mieć oddzielne rurociągi dla pary i wody, a także zbiorniki do gromadzenia kondensatu. Nie oznacza to jednak, że obwody kotłowni ciepłej wody są prostsze niż parowe. Kotłownie wodne i kotłownie parowe różnią się złożonością w zależności od rodzaju stosowanego paliwa, konstrukcji kotłów, pieców itp. Zarówno systemy kotłów parowych, jak i wodnych zwykle obejmują kilka kotłów, ale nie mniej niż dwa i nie więcej niż cztery lub pięć. Wszystkie są połączone wspólną komunikacją - rurociągami, gazociągami itp.
Projekt kotłów o mniejszej mocy pokazano poniżej w paragrafie 4 tego tematu. Aby lepiej zrozumieć budowę i zasadę działania kotłów o różnej mocy, wskazane jest porównanie konstrukcji tych kotłów o mniejszej mocy z budową opisanych powyżej kotłów o większej mocy i znalezienie w nich głównych elementów spełniających te same funkcje , a także zrozumieć główne przyczyny różnic w projektach.
3. Klasyfikacja jednostek kotłowych
Kotły jako urządzenia techniczne do wytwarzania pary lub gorącej wody wyróżniają się różnorodnością form konstrukcyjnych, zasad działania, rodzajów stosowanego paliwa i wskaźników produkcyjnych. Jednak zgodnie ze sposobem organizacji ruchu wody i mieszaniny pary i wody wszystkie kotły można podzielić na dwie następujące grupy:
Kotły z naturalnym obiegiem;
Kotły z wymuszonym ruchem chłodziwa (woda, mieszanina pary i wody).
W nowoczesnych kotłowniach ciepłowniczych i ciepłowniczo-przemysłowych kotły z naturalnym obiegiem służą głównie do wytwarzania pary, a kotły z wymuszonym ruchem chłodziwa działające na zasadzie bezpośredniego przepływu służą do wytwarzania gorącej wody.
Nowoczesne kotły parowe z naturalnym obiegiem zbudowane są z pionowych rur umieszczonych pomiędzy dwoma kolektorami (bębnem górnym i dolnym). Ich urządzenie pokazano na rysunku na ryc. 10, zdjęcie bębna górnego i dolnego wraz z łączącymi je rurami - na ryc. 11, a umiejscowienie w kotłowni pokazano na ryc. 12. Jedna część rur, zwana podgrzewanymi „rurami pionowymi”, jest podgrzewana przez palnik i produkty spalania, a druga, zwykle nieogrzewana część rur, znajduje się na zewnątrz kotła i nazywa się „rurami opadającymi”. W podgrzewanych rurach tłocznych woda jest podgrzewana do wrzenia, częściowo odparowuje i dostaje się do korpusu kotła w postaci mieszaniny pary i wody, gdzie zostaje rozdzielona na parę i wodę. Poprzez opuszczenie nieogrzewanych rur woda z górnego bębna dostaje się do dolnego kolektora (bębna).
Ruch chłodziwa w kotłach z naturalnym obiegiem odbywa się pod wpływem ciśnienia napędowego wytworzonego przez różnicę ciężarów słupa wody w rurach obniżających i słupa mieszaniny pary i wody w rurach wznoszących.
Ryż. 10.
Ryż. jedenaście.
Ryż. 12.
W kotłach parowych z wielokrotnym wymuszonym obiegiem powierzchnie grzewcze wykonane są w postaci wężownic tworzących obwody cyrkulacyjne. Ruch wody i mieszaniny pary i wody w takich obwodach odbywa się za pomocą pompy obiegowej.
W kotłach parowych z przepływem bezpośrednim współczynnik cyrkulacji wynosi jedność, tj. Woda zasilająca po podgrzaniu zamienia się kolejno w mieszaninę parowo-wodną, parę nasyconą i przegrzaną.
W kotłach na gorącą wodę woda poruszająca się w obiegu cyrkulacyjnym jest podgrzewana w jednym obrocie od temperatury początkowej do końcowej.
Ze względu na rodzaj chłodziwa kotły dzielą się na kotły wodne i parowe. Głównymi wskaźnikami kotła na gorącą wodę są moc cieplna, czyli moc grzewcza i temperatura wody; Głównymi wskaźnikami kotła parowego są wydajność pary, ciśnienie i temperatura.
Kotły wodne, których zadaniem jest uzyskanie ciepłej wody o określonych parametrach, służą do zaopatrzenia w ciepło systemów grzewczych i wentylacyjnych, odbiorców domowych i technologicznych. Kotły ciepłowodne, zwykle działające na zasadzie bezpośredniego przepływu ze stałym przepływem wody, instalowane są nie tylko w elektrowniach cieplnych, ale także w ciepłowniach, kotłowniach ciepłowniczych i przemysłowych jako główne źródło zaopatrzenia w ciepło.
Ryż. 13.
Ryż. 14.
Ze względu na względny ruch czynników wymiany ciepła (spalin, wody i pary) kotły parowe (wytwornice pary) można podzielić na dwie grupy: kotły wodnorurowe i kotły płomienicowo-płomieniowe. W wodnorurowych wytwornicach pary woda i mieszanina pary i wody poruszają się wewnątrz rur, a gazy spalinowe przemywają rury na zewnątrz. W Rosji w XX wieku stosowano głównie kotły wodnorurowe Szuchowa. Przeciwnie, w płomienicach spaliny przemieszczają się wewnątrz rur, a woda wypłukuje rury na zewnątrz.
W oparciu o zasadę ruchu wody i mieszaniny pary i wody wytwornice pary dzielą się na jednostki z obiegiem naturalnym i z obiegiem wymuszonym. Te ostatnie dzielą się na obieg bezpośredni i wielokrotny wymuszony.
Przykłady rozmieszczenia kotłów o różnej mocy i przeznaczeniu oraz innego wyposażenia w kotłowniach pokazano na ryc. 14-16.
Ryż. 15.
Ryż. 16. Przykłady rozmieszczenia kotłów domowych i innego sprzętu
Nie można sobie wyobrazić współczesnej energetyki cieplnej bez precyzyjnych przyrządów pomiarowych. Proces technologiczny w obiektach energetycznych musi być stale monitorowany za pomocą czujników lub przetworników, które nie tylko pasywnie odbierają informacje, ale także umożliwiają automatyczną regulację i wyłączenie ochronne w przypadku naruszenia normalnej pracy.
Rodzaje oprzyrządowania i automatyki w kotłowni
Z ogólnej nazwy i powyższego możemy wywnioskować, że do bezproblemowej pracy urządzeń gazowych potrzebne są następujące kompleksy:
- zmierzenie;
- naregulowanie;
- ochronny.
Eksploatacja podgrzewaczy wody i elektrowni bez urządzeń ochronnych jest zabroniona, ponieważ w przypadku nietypowych sytuacji i awarii zagrożenie życia ludzkiego i integralności mechanizmów wzrasta wielokrotnie. Przed rozpaleniem dyżurny sprawdzi działanie zabezpieczenia zatrzymującego kocioł. Wprowadzenie tej klauzuli w PTE pomogło w poważnym ograniczeniu negatywnych skutków wypadków.
Cechy działania oprzyrządowania i systemów sterowania urządzeniami kotłowymi
W przypadku rurociągów sieciowych i gazowych dostarczane są zarówno zdalne kompleksy cyfrowe, jak i urządzenia mechaniczne na miejscu. Dzięki temu personel serwisowy może monitorować stan środowiska podczas zwiedzania kotłowni lub w przypadku utraty zasilania. Zabezpieczenie dotyczy najczęściej zasilania paliwem, aby zapobiec wybuchowi w przypadku naruszenia reżimu spalania w kotłach.
Konserwacja oprzyrządowania i automatyki w kotłowniach
W celu prawidłowego działania urządzeń sterujących w obiektach elektrociepłowni tworzy się specjalny warsztat lub oddział. Usługa ta realizuje następujące funkcje:
- codzienny monitoring poprawności odczytów,
- sprawdzanie urządzeń zabezpieczających;
- naprawa i wymiana uszkodzonych urządzeń;
- okresowa weryfikacja urządzeń pomiarowych.
Utrzymanie pracy kotła nie jest możliwe bez stałego nadzoru ze strony operatora kotłowni. Kilka rund na zmianę pomaga utrzymać taki sprzęt pomiarowy w dobrym stanie.
Aparatura i urządzenia automatyki do kotłowni
Głównymi urządzeniami pomiarowymi w kotłowniach gazowych są:
- Manometry. Niezbędne do monitorowania ciśnienia w rurociągach, bez nich działanie jest często niemożliwe. Służą do regulacji procesu spalania w kotłach wodnych i energetycznych poprzez pomiar ciśnienia gazu ziemnego i powietrza.
- Termopary. Chłodziwo musi być dostarczane do miasta w określonej temperaturze. Aby to kontrolować, a tym samym tryb pracy kotłowni, instaluje się kilka konwerterów termicznych.
- Przepływomierze. Charakterystyka ekonomiczna produkcji energii cieplnej i elektrycznej jest związana ze zużyciem środowiska pracy i paliwa. Do ich pomiaru służą cyfrowe urządzenia rejestrujące.
Mechanik oprzyrządowania i automatyki kotłowni gazowych
W nowoczesnej produkcji wszystkie parametry uzyskane z przyrządów pomiarowych gromadzone są w punkcie. Znajdujące się na nim systemy komputerowe umożliwiają dostęp do tych informacji przez określony czas. Kolejność ta jest przydatna do analizy.
Do obowiązków mechanika dyżurnego należą kwestie ogólne:
- zapewnienie sprawności urządzeń sterujących i zabezpieczających;
- okresowe sprawdzanie przyrządów pomiarowych;
- konserwacja oprzyrządowania i automatyki w kotłowni;
- gromadzenie i dostarczanie kompleksowej informacji o parametrach procesu produkcyjnego.
Personel obsługujący pracuje zmianowo, aby zapewnić prawidłową pracę układów pomiarowych w obiektach energetycznych i sieciach ciepłowniczych. Monitoruje także system gromadzenia informacji, aby zapobiec awariom.
Opracowanie projektu automatyki kotłowni odbywa się na podstawie zadania opracowanego w trakcie realizacji części ciepłowniczej projektu. Do ogólnych celów monitorowania i zarządzania pracą każdej elektrowni należy zapewnienie:
Wytwarzanie w każdej chwili wymaganej ilości ciepła przy określonych parametrach ciśnienia i temperatury;
Efektywność spalania paliw, racjonalne wykorzystanie energii elektrycznej na potrzeby własne instalacji oraz minimalizacja strat ciepła;
Niezawodność i bezpieczeństwo, czyli ustalenie i utrzymanie normalnych warunków pracy każdej jednostki, wykluczających możliwość wystąpienia awarii i wypadków zarówno samej jednostki, jak i urządzeń pomocniczych.
Na podstawie powyższych zadań i instrukcji wszystkie urządzenia sterujące można podzielić na pięć grup przeznaczonych do pomiarów:
1. Zużycie wody, paliwa, powietrza i spalin.
2. Ciśnienie wody, powietrza gazowego, pomiar podciśnienia w elementach i kanałach gazowych kotła oraz urządzeniach pomocniczych.
3. Temperatury wody, powietrza i spalin
4. Poziom wody w zbiornikach, odgazowywaczach i innych pojemnikach.
5. Skład jakościowy gazów i wody.
Urządzenia wtórne mogą wskazywać, rejestrować i sumować. Aby zmniejszyć liczbę urządzeń dodatkowych na osłonie termicznej, niektóre wartości są zbierane dla każdego urządzenia za pomocą przełączników; W przypadku wielkości krytycznych maksymalne dopuszczalne wartości są zaznaczone czerwoną linią na urządzeniu wtórnym i są mierzone w sposób ciągły.
Oprócz urządzeń znajdujących się na panelu sterowania często stosuje się lokalną instalację przyrządów kontrolno-pomiarowych: termometry do pomiaru temperatury wody; manometry; różne mierniki ciągu i analizatory gazu.
Procesem spalania w kotle KV-TS-20 sterują trzy regulatory: regulator obciążenia cieplnego, regulator powietrza i regulator podciśnienia.
Regulator obciążenia cieplnego otrzymuje impuls sterujący z głównego regulatora korekcyjnego, a także impulsy przepływu wody. Regulator obciążenia cieplnego działa na organ regulujący dopływ paliwa do pieca.
Regulator całkowitego powietrza utrzymuje stosunek paliwa do powietrza poprzez odbieranie impulsów na podstawie zużycia paliwa z czujnika i spadku ciśnienia w nagrzewnicy powietrza.
Stałą próżnię w palenisku utrzymuje się za pomocą regulatora w palenisku kotła oraz oddymiacza działającego na kierownicę. Pomiędzy regulatorem powietrza i regulatorem podciśnienia istnieje dynamiczne połączenie, którego zadaniem jest podanie dodatkowego impulsu w stanach przejściowych, co pozwala na utrzymanie prawidłowego trybu ciągu podczas pracy regulatora powietrza i podciśnienia.
Dynamiczne urządzenie sprzęgające ma działanie kierunkowe, tzn. regulatorem podrzędnym może być jedynie regulator rozładowania.
Instalowane są regulatory mocy w celu monitorowania zużycia wody sieciowej i zasilającej.
Termometr rozszerzalności rtęci:
Przemysłowe termometry rtęciowe wykonane są z wbudowaną skalą i w zależności od kształtu dolnej części ze zbiornikiem rozróżnia się proste typu A i kątowe typu B, zagięte pod kątem 90° w kierunku przeciwnym do skali. Podczas pomiaru temperatury dolna część termometrów jest całkowicie zanurzona w mierzonym medium, tj. ich głębokość zanurzenia jest stała.
Termometry rozszerzalnościowe są przyrządami wskazującymi znajdującymi się w miejscu pomiaru. Zasada ich działania opiera się na rozszerzalności cieplnej cieczy w szklanym pojemniku w zależności od mierzonej temperatury.
Termometr termoelektryczny:
Do pomiaru wysokich temperatur ze zdalnym przesyłaniem odczytów stosuje się termometry termoelektryczne, których działanie opiera się na zasadzie efektu termoelektrycznego. Termometry termoelektryczne Chromel-Copel wytwarzają termoemf, który znacznie przewyższa termoemf innych standardowych termometrów termoelektrycznych. Zakres stosowania termometrów termoelektrycznych Chromel - Copel wynosi od - 50° do + 600° C. Średnica elektrod wynosi od 0,7 do 3,2 mm.
Manometr rurowo-sprężynowy:
Do pomiaru nadciśnienia cieczy, gazów i pary najczęściej stosowane są manometry o prostej i niezawodnej konstrukcji, wyraźnych wskazaniach i małych wymiarach. Istotnymi zaletami tych urządzeń jest także duży zakres pomiarowy, możliwość automatycznej rejestracji i zdalnej transmisji odczytów.
Zasada działania manometru odkształceniowego opiera się na wykorzystaniu odkształcenia sprężystego elementu pomiarowego, powstającego pod wpływem mierzonego ciśnienia.
Bardzo powszechnym rodzajem urządzeń odkształcalnych służących do wyznaczania nadciśnienia są manometry rurowo-sprężynowe, które odgrywają niezwykle ważną rolę w pomiarach technicznych. Urządzenia te wykonane są z jednozwojowej sprężyny rurowej, która jest metalową elastyczną rurką o owalnym przekroju zagiętą po obwodzie.
Jeden koniec sprężyny śrubowej jest połączony z przekładnią, a drugi jest trwale zamontowany na zębatce podtrzymującej mechanizm przekładni.
Pod wpływem mierzonego ciśnienia rurkowa sprężyna częściowo się rozwija i naciąga smycz, co wprawia w ruch mechanizm zębatkowy i poruszającą się po skali igłę manometru. Manometr posiada jednolitą okrągłą skalę z kątem środkowym 270 - 300°.
Potencjometr automatyczny:
Główną cechą potencjometru jest to, że podaje temperaturę termoelektryczną uzyskaną za pomocą termometru termoelektrycznego. ds. jest równoważone (kompensowane) napięciem o równej wielkości, ale o przeciwnym znaku, pochodzącym ze źródła prądu znajdującego się w urządzeniu, które jest następnie mierzone z dużą dokładnością.
Automatyczny potencjometr małogabarytowy typu KSP2 - urządzenie wskazująco-rejestrujące o długości skali liniowej i szerokości taśmy wykresowej 160 mm. Główny błąd odczytów urządzenia wynosi ±0,5, a błąd rejestracji wynosi ±0,1%.
Zmienność odczytów nie przekracza połowy błędu głównego. Prędkość taśmy wykresowej może wynosić 20, 40, 60, 120, 240 lub 600, 1200, 2400 mm/h.
Potencjometr zasilany jest napięciem przemiennym 220 V, częstotliwość 50 Hz. Pobór mocy urządzenia wynosi 30 V A. Zmiana napięcia zasilania o ±10% napięcia znamionowego nie ma wpływu na odczyty urządzenia. Dopuszczalna temperatura otoczenia wynosi 5 - 50°C, a wilgotność względna powietrza 30 - 80%. Wymiary potencjometru to 240 x 320 x 450 mm. i waga 17 kg.
Zaleca się montaż manometrów elektrycznych deformacyjnych w pobliżu kranu ciśnieniowego, mocując je w pionie złączką skierowaną w dół. W przypadku manometrów powietrze otoczenia może mieć temperaturę 5–60°C i wilgotność względną 30–95%. Należy je usunąć z silnych źródeł zmiennego pola magnetycznego (silniki elektryczne, transformatory itp.)
Manometr zawiera sprężynę rurową 1, zamocowaną w uchwycie 2 za pomocą tulei 3. Trzpień magnetyczny 5 jest zawieszony na wolnym końcu sprężyny na dźwigni 4, umieszczonej w przetworniku magnetomodulacyjnym 6 osadzonym obok w uchwycie w tym drugim przypadku do składanego wspornika przymocowane jest urządzenie wzmacniające 7.
Urządzenie zamknięte jest w stalowej obudowie 8 z osłoną ochronną 9, przystosowaną do montażu podtynkowego. Manometr podłącza się do mierzonego ciśnienia za pomocą uchwytu, a przewody przyłączeniowe podłącza się poprzez skrzynkę zaciskową 10. Manometr wyposażony jest w korektor zera 11. Wymiary urządzenia wynoszą 212 x 240 x 190 mm. i waga 4,5 kg.
Manometry typu MPE mogą współpracować z jednym lub kilkoma urządzeniami wtórnymi prądu stałego: automatycznym elektronicznym wskazaniem i rejestracją miliamperomierza typu KSU4, KSU3,
KSU2, KSU1, KPU1 I KVU1, wyskalowane w jednostkach ciśnienia, magnetoelektryczne wskazujące i rejestrujące miliamperometry typu N340 i N349, centralne urządzenia sterujące itp. Automatyczne elektroniczne miliamperometry prądu stałego różnią się od odpowiednich automatycznych potencjometrów jedynie skalibrowanym rezystorem obciążającym podłączonym równolegle do wejście, spadek napięcia, o który z prądu przepływającego przez manometr jest mierzona wielkość.
Miliamperomierze magnetoelektryczne typu N340 i N349 mają skalę i szerokość wykresu 100 mm. klasa dokładności przyrządu 1,5. Taśma mapy napędzana jest z prędkością 20 - 5400 mm/h z mikrosilnika synchronicznego zasilanego z sieci prądu przemiennego o napięciu 127 lub 220 V i częstotliwości 50 Hz.
Wymiary urządzenia to 160 x 160 x 245 mm. i waga 5 kg.
Regulator bezpośredniego działania:
Przykładem regulatora bezpośredniego działania jest zawór regulacyjny.
Zawór składa się z żeliwnego korpusu 1, zamkniętego od dołu pokrywą kołnierzową 2, która zamyka otwór do spuszczania czynnika wypełniającego zawór i do czyszczenia zaworu. Gniazda 3 ze stali nierdzewnej są przykręcone do korpusu zaworu. Tłok 4 jest osadzony w gniazdach. Powierzchnie robocze tłoka są szlifowane w gniazdach 3. Tłok jest połączony z prętem 6, który może podnosić i opuszczać tłok. Pręt pracuje w dławnicy. Uszczelka olejowa uszczelnia pokrywę 7, która jest przymocowana do korpusu zaworu. Aby nasmarować powierzchnie trące pręta, olej jest dostarczany do dławnicy z olejarki 5. Zawór jest sterowany za pomocą dźwigni membranowej składającej się z jarzma 8, głowicy membrany 13, dźwigni 1 i obciążników 16,17. W głowicy membrany gumowa membrana 15 jest zaciśnięta pomiędzy górną i dolną misą, opierając się na płycie 14 zamontowanej na drążku jarzma 9. Pręt 6 jest zamocowany w pręcie 9. Pręt jarzma ma pryzmat 12, na którym spoczywa dźwignia 11, obracająca się na wsporniku pryzmatu 10 zamocowanym w jarzmie 8.
W górnej czaszy głowicy membrany znajduje się otwór, w którym zamocowana jest rurka impulsowa dostarczająca impuls ciśnienia do membrany. Pod wpływem zwiększonego ciśnienia membrana ugina się i ciągnie w dół płytę 14 i drążek jarzma 9. Wzmocnienie utworzone przez membranę równoważone jest ciężarkami 16 i 17 zawieszonymi na dźwigni. Odważniki 17 służą do zgrubnej regulacji zadanego ciśnienia. Za pomocą ciężarka 16 poruszającego się po dźwigni można precyzyjniej regulować zawór.
Nacisk na głowicę membrany przenoszony jest bezpośrednio przez kontrolowane medium.
Mechanizm uruchamiający:
Elementy regulacyjne służą do regulacji przepływu cieczy, gazu lub pary w procesie technologicznym. Ruch organów regulacyjnych odbywa się za pomocą siłowników.
Korpusy regulacyjne i siłowniki mogą występować w postaci dwóch odrębnych zespołów połączonych ze sobą za pomocą dźwigni lub linek lub w postaci kompletnego urządzenia, gdzie korpus regulacyjny jest sztywno połączony z siłownikiem i tworzy monoblok.
Siłownik, otrzymując polecenie od regulatora lub z aparatu sterującego sterowanego przez człowieka, przetwarza to polecenie na mechaniczny ruch regulatora.
Mechanizm jest elektryczny, jednoobrotowy, przeznaczony do przesuwania elementów sterujących w układach sterowania przekaźnikowego i zdalnego sterowania. Mechanizm otrzymuje polecenie elektryczne, którym jest trójfazowe napięcie sieciowe 220 lub 380 V. Polecenie można wydać za pomocą rozrusznika z kontaktem magnetycznym.
Siłownik składa się z części silnika elektrycznego
I - serwonapęd i kolumna sterująca, II zespół serwonapędu. Serwonapęd składa się z trójfazowego asynchronicznego silnika nawrotnego 3 z wirnikiem klatkowym. Z wału silnika moment obrotowy przenoszony jest na skrzynię biegów 4, która składa się z dwóch stopni przekładni ślimakowej. Dźwignia 2 zamontowana jest na wale wejściowym przekładni, który jest połączony przegubowo z korpusem regulacyjnym za pomocą drążka.
Obracając kołem ręcznym 1, przy sterowaniu ręcznym można obracać wał wyjściowy skrzyni biegów bez pomocy silnika elektrycznego. Ręczna obsługa koła zamachowego powoduje rozłączenie mechanicznej przekładni silnika elektrycznego z kołem zamachowym.
Organ regulacyjny ma na celu zmianę przepływu regulowanego medium, energii lub innych ilości zgodnie z wymaganiami technologii.
W zaworach grzybkowych powierzchnia zamykająca i dławiąca jest płaska. Zawór z gładkimi powierzchniami roboczymi typu grzybowego ma charakterystykę liniową, tj. Wydajność zaworu jest wprost proporcjonalna do skoku tłoka.
Regulacja odbywa się poprzez zmianę powierzchni przepływu poprzez ruch postępowy wrzeciona przy jednoczesnym obrocie koła zamachowego za pomocą dźwigni przegubowej poprzez drążek z siłownikiem elektrycznym.
Zawory nie mogą pełnić funkcji odcinającej.
Sterowanie rozrusznikiem:
Rozruszniki PMTR-69 wykonane są w oparciu o magnetyczne styki nawrotne, z których każdy posiada trzy normalnie rozwarte styki mocy podłączone do obwodu zasilania silnika elektrycznego. Dodatkowo urządzenie rozruchowe posiada urządzenie hamujące wykonane na bazie kondensatora elektrycznego i połączone poprzez otwarte styki z jednym z uzwojeń stojana silnika elektrycznego. Kiedy jakakolwiek grupa styków mocy jest zamknięta, styki pomocnicze otwierają się, a kondensator jest odłączany od silnika elektrycznego, poruszając się pod wpływem bezwładności, oddziałuje z resztkowym polem magnetycznym stojana i indukuje emf w jego uzwojeniach.
Styki pomocnicze, zamykając obwód uzwojenia stojana kondensatora, wytwarzają w stojanie własne pole magnetyczne wirnika, a stojan powoduje efekt hamowania przeciwdziałający obrotowi, co zapobiega wybiegowi siłownika. Główną wadą rozruszników jest niska niezawodność (przepalenie styków, zwarcie).
Blok posiada trzy wejścia prądowe i jedno napięciowe. Blok R - 12 składa się z głównych elementów: obwodów wejściowych VxC, wzmacniaczy DC UPT 1 i UPT 2, jednostki ograniczającej MO, natomiast UPT 2 umożliwia odbiór jednego sygnału prądowego i dodatkowego sygnału napięciowego na wyjściu. Blok R - 12 pobiera zasilanie z zasilacza, który otrzymuje dodatkowy sygnał z jednostki sterującej BU.
Sygnał z czujnika doprowadzany jest do węzła obwodu wejściowego, gdzie doprowadzany jest również sygnał z urządzenia nadrzędnego I. Następnie sygnał niedopasowania y trafia do wzmacniacza prądu stałego UPT 1, przechodząc przez sumator, gdzie generowane są sygnały niedopasowania z obwodów wejściowych i sprzężenia zwrotnego. Blok ograniczający sygnał OM zapewnia jego dalszą transformację, ograniczając sygnał do minimum i maksimum. Wzmacniacz UPT 2 jest ostateczną jednostką wzmacniającą. Zespół sprzężenia zwrotnego MD odbiera sygnał z wyjścia wzmacniacza UPT 2 i zapewnia płynne przełączanie obwodów ze sterowania ręcznego na automatyczne. Blok sprzężenia zwrotnego MD zapewnia utworzenie sygnału sterującego zgodnie z prawami sterowania P -, PI - lub PID.
Zabezpieczenie technologiczne.
Aby uniknąć stanów awaryjnych, układy sterowania urządzeniami na wypadek nadmiernych odchyleń parametrów oraz w celu zapewnienia bezpieczeństwa pracy wyposaża się w technologiczne urządzenia zabezpieczające.
W zależności od skutków oddziaływania na sprzęt zabezpieczenia dzieli się na: te, które zatrzymują lub wyłączają jednostki; przeniesienie sprzętu do trybu zmniejszonego obciążenia; wykonywanie operacji lokalnych i przełączanie; zapobieganie sytuacjom awaryjnym.
Urządzenia zabezpieczające muszą być niezawodne w sytuacjach przedawaryjnych i awaryjnych, tzn. w działaniach zabezpieczeniowych nie może dochodzić do awarii ani fałszywych alarmów. Awarie w działaniach ochronnych prowadzą do przedwczesnego wyłączenia urządzeń i dalszego rozwoju awarii, a fałszywe alarmy wyrywają sprzęt z normalnego cyklu technologicznego, co zmniejsza jego wydajność operacyjną. Aby sprostać tym wymaganiom, stosuje się wysoce niezawodne przyrządy i urządzenia oraz odpowiednie konstrukcje obwodów zabezpieczających.
Ochrona obejmuje źródła informacji dyskretnej: czujniki, urządzenia stykowe, styki pomocnicze, elementy logiczne i obwód sterujący przekaźnika. Zadziałanie zabezpieczeń musi zapewnić jednoznaczne działanie, natomiast przejście urządzenia do trybu pracy następuje po przeprowadzeniu zabezpieczenia, po sprawdzeniu i wyeliminowaniu przyczyn będących przyczyną zadziałania.
Projektując zabezpieczenia termiczne kotłów, turbin i innych urządzeń cieplnych, przewiduje się tzw. priorytet działań ochronnych, czyli wykonanie w pierwszej kolejności działań zabezpieczających powodujących większy stopień odciążenia. Wszystkie zabezpieczenia posiadają niezależne źródła zasilania oraz możliwość rejestracji przyczyn zadziałania, a także sygnalizacji świetlnej i dźwiękowej.
Alarm technologiczny.
Ogólne informacje o sygnalizacji.
Alarm procesowy, będący częścią systemu sterowania, ma za zadanie powiadamiać personel obsługujący o niedopuszczalnych odchyleniach parametrów i trybu pracy urządzenia.
W zależności od wymagań stawianych sygnalizacji można ją podzielić na kilka rodzajów: sygnalizacja zapewniająca niezawodność i bezpieczeństwo pracy urządzeń; system alarmowy rejestrujący zadziałanie zabezpieczeń urządzeń i przyczyny zadziałania; alarm, informujący o niedopuszczalnych odchyleniach podstawowych parametrów i wymagający natychmiastowego wyłączenia urządzeń; sygnalizowanie awarii zasilania różnych urządzeń i urządzeń.
Wszystkie sygnały przesyłane są do urządzeń świetlno-dźwiękowych centrali. Istnieją dwa rodzaje alarmów dźwiękowych: ostrzegawczy (dzwonek) i alarmowy (syrena).
Alarmy świetlne wykonujemy w wersji dwukolorowej (światła czerwone lub zielone) lub przy wykorzystaniu paneli podświetlanych, które wskazują przyczynę alarmu.
Nowo odebrane sygnały na tle tych już sterowanych przez operatora mogą pozostać niezauważone, dlatego obwody sygnalizacyjne projektuje się tak, aby nowy sygnał był podświetlany poprzez miganie.
Schemat funkcjonalny urządzenia alarmowego.
Obwód alarmowy zasilany jest z zasilacza prądu stałego, co zwiększa ich niezawodność. Sygnał włączenia alarmu CB podawany jest do modułu przerywania sygnału przekaźnikowego BRP, a następnie równolegle do tablicy świetlnej ST i urządzenia dźwiękowego ładowarki. Jednocześnie w PDU obwód jest zaprojektowany w taki sposób, aby zapewniał przerywane podświetlenie wyświetlacza i stały sygnał dźwiękowy.
Po odebraniu sygnału i usunięciu dźwięku obwód musi być gotowy na przyjęcie kolejnego sygnału, niezależnie od tego, czy parametr sygnalizacji powrócił do wartości nominalnej.
Każdemu sygnałowi świetlnemu musi towarzyszyć dźwięk, aby zwrócić uwagę personelu obsługującego.
Środki sygnalizacyjne.
Elektroniczny manometr kontaktowy.
Do pomiaru i sygnalizacji ciśnienia stosuje się manometr typu EKM ze sprężyną rurkową. Manometr posiada korpus o średnicy 160 mm. z tylnym kołnierzem i złączem promieniowym. Urządzenie zawiera strzałkę 1, ustawienie strzałek sygnału 2 i 3 (minimum i maksimum), ustawienie zadanych wartości ciśnienia za pomocą klawisza. Pudełko 4 z zaciskami do podłączenia obwodu alarmowego do urządzenia. Mechanizm manometru zamknięty jest w obudowie 5. Urządzenie komunikuje się z mierzonym medium poprzez złączkę 6.
Po osiągnięciu któregokolwiek z określonych ciśnień granicznych styk oznaczony strzałką wskaźnikową styka się ze stykiem znajdującym się na odpowiedniej strzałce sygnalizacyjnej i zamyka obwód alarmowy. Urządzenie stykowe zasilane jest z sieci prądu stałego lub przemiennego o napięciu 220 V.
W kotłowniach grzewczych zasilanych gazem i paliwem płynnym stosuje się złożone układy sterowania, z których każdy w zależności od przeznaczenia i mocy kotłowni, ciśnienia gazu, rodzaju i parametrów chłodziwa ma swoją specyfikę i zakres.
Główne wymagania dotyczące systemów automatyki kotłowni:
— zapewnienie bezpiecznej pracy
— optymalna regulacja zużycia paliwa.
Wyznacznikiem doskonałości stosowanych systemów sterowania jest ich samokontrola, tj. przesłanie sygnału o awaryjnym wyłączeniu kotłowni lub jednego z kotłów i automatyczne zarejestrowanie przyczyny, która spowodowała awaryjne wyłączenie.
Szereg produkowanych na rynku systemów sterowania umożliwia półautomatyczne uruchamianie i wyłączanie kotłów zasilanych gazem i paliwem płynnym. Jedną z cech systemów automatyki kotłowni zgazowanych jest pełna kontrola nad bezpieczeństwem urządzeń i jednostek. System specjalnych blokad ochronnych musi zapewniać odcięcie dopływu paliwa w przypadku:
— naruszenie normalnej kolejności operacji rozruchowych;
— wyłączenie wentylatorów nadmuchowych;
— spadek (wzrost) ciśnienia gazu poniżej (powyżej) dopuszczalnej wartości granicznej;
— naruszenie ciągu w palenisku kotła;
— awarie i zgaszenie palnika;
— spadek poziomu wody w kotle;
— inne przypadki odchyleń parametrów pracy jednostek kotłowych od normy.
W związku z tym nowoczesne systemy sterowania składają się z przyrządów i urządzeń zapewniających kompleksową regulację trybu i bezpieczeństwo ich działania. Wdrożenie złożonej automatyki wiąże się z redukcją personelu serwisowego w zależności od stopnia automatyzacji. Niektóre stosowane systemy sterowania przyczyniają się do automatyzacji wszystkich procesów technologicznych w kotłowniach, w tym do trybu zdalnego kotłów, który pozwala kontrolować pracę kotłowni bezpośrednio z centrum sterowania, podczas gdy personel jest całkowicie usunięty z kotła domy. Jednak w przypadku kotłowni dyspozytorskich wymagany jest wysoki stopień niezawodności działania organów wykonawczych i czujników systemów automatyki. W niektórych przypadkach ograniczają się one do stosowania „minimalnej” automatyki w kotłowniach, przeznaczonej do kontrolowania tylko podstawowych parametrów (automatyka częściowa). Na produkowane i nowo opracowywane układy sterowania kotłowniami grzewczymi stawiane są szereg wymagań technologicznych: agregacja, tj. możliwość ustawienia dowolnego schematu z ograniczonej liczby zunifikowanych elementów; konstrukcja bloku - możliwość łatwej wymiany uszkodzonego bloku. Dostępność urządzeń pozwalających na zdalne sterowanie zautomatyzowanymi instalacjami poprzez minimalną liczbę kanałów komunikacyjnych, minimalną bezwładność i najszybszy powrót do normalności w przypadku ewentualnej nierównowagi systemu. Pełna automatyzacja pracy urządzeń pomocniczych: regulacja ciśnienia w kolektorze powrotnym (zasilającym sieć ciepłowniczą), ciśnienia w głowicy odgazowywacza, poziomu wody w zbiorniku akumulacyjnym odgazowywacza itp.
Ochrona kotłowni.
Bardzo ważne: W pozycjach blokowania należy używać wyłącznie urządzeń chronionych odgromów.
Zabezpieczenie kotła na wypadek sytuacji awaryjnych jest jednym z głównych zadań automatyki kotłowni. Tryby awaryjne powstają głównie w wyniku nieprawidłowych działań personelu konserwacyjnego, głównie podczas uruchamiania kotła. Obwód zabezpieczający zapewnia określoną kolejność działań podczas rozpalania kotła i automatycznie zatrzymuje dopływ paliwa w przypadku wystąpienia warunków awaryjnych.
Schemat ochrony musi rozwiązać następujące problemy:
— kontrola nad prawidłowym wykonaniem działań przedstartowych;
— włączenie urządzeń ciągu, napełnienie kotła wodą itp.;
— monitorowanie normalnego stanu parametrów (zarówno podczas rozruchu, jak i podczas pracy kotła);
— zdalne zapalenie zapalarki z panelu sterowania;
— automatyczne odcięcie dopływu gazu do zapalarek po krótkotrwałej wspólnej pracy zapalarki i palnika głównego (w celu sprawdzenia spalania pochodni palników głównych), jeżeli pochodnie zapalarki i palnika posiadają wspólne urządzenie sterujące.
Wyposażenie kotłów w zabezpieczenia podczas spalania dowolnego rodzaju paliwa jest obowiązkowe.
Kotły parowe, niezależnie od ciśnienia i wytwarzania pary podczas spalania paliw gazowych i ciekłych, muszą być wyposażone w urządzenia zatrzymujące dopływ paliwa do palników w przypadku:
— zwiększanie lub zmniejszanie ciśnienia paliwa gazowego przed palnikami;
— zmniejszenie ciśnienia paliwa płynnego przed palnikami (nie należy tego robić w przypadku kotłów wyposażonych w dysze obrotowe);
— zmniejszenie lub zwiększenie poziomu wody w bębnie;
— zmniejszenie ciśnienia powietrza przed palnikami (dla kotłów wyposażonych w palniki z wymuszonym dopływem powietrza);
— zwiększenie ciśnienia pary (tylko wtedy, gdy kotłownie pracują bez stałego personelu konserwacyjnego);
Kotły ciepłowodne spalające paliwa gazowe i ciekłe muszą być wyposażone w urządzenia automatycznie odcinające dopływ paliwa do palników w przypadku:
— podwyższenie temperatury wody za kotłem;
— zwiększenie lub zmniejszenie ciśnienia wody za kotłem;
— zmniejszenie ciśnienia powietrza przed palnikami (dla kotłów wyposażonych w palniki z wymuszonym dopływem powietrza);
— zwiększenie lub zmniejszenie ilości paliwa gazowego;
— zmniejszenie ciśnienia paliwa ciekłego (w przypadku kotłów wyposażonych w palniki obrotowe nie należy tego wykonywać);
— zmniejszenie próżni w piecu;
— zmniejszenie przepływu wody przez kocioł;
— wygasają płomienie palników, których wyłączenie podczas pracy kotła jest niedopuszczalne;
— nieprawidłowe działanie obwodów zabezpieczających, w tym utrata napięcia.
W przypadku kotłów wodnych o temperaturze podgrzewania wody wynoszącej 115°C i niższej, zabezpieczenie przed redukcją ciśnienia wody za kotłem i ograniczeniem przepływu wody przez kocioł może nie być zapewnione.
Alarm technologiczny w kotłowniach.
Aby ostrzec personel obsługujący o odchyleniach głównych parametrów technologicznych od normy, zastosowano technologiczny alarm świetlny i dźwiękowy. Obwód sygnalizacji procesowej kotłowni dzieli się z reguły na obwody alarmowe dla kotłów i urządzeń pomocniczych kotłowni. W kotłowniach, w których zatrudniony jest stały personel konserwacyjny, należy przewidzieć instalację alarmową:
a) zatrzymanie kotła (w przypadku zadziałania zabezpieczenia);
b) przyczyny zadziałania ochrony;
c) obniżenie temperatury i ciśnienia paliwa płynnego we wspólnym rurociągu do kotłów;
d) zmniejszenie ciśnienia wody w linii zasilającej;
e) zmniejszenie lub zwiększenie ciśnienia wody na rurociągu powrotnym sieci ciepłowniczej;
f) podwyższanie lub obniżanie poziomu w zbiornikach (odgazowywacz, układy zaopatrzenia w ciepłą wodę akumulacyjną, kondensat, woda zasilająca, magazynowanie paliw płynnych itp.) oraz obniżanie poziomu w zbiornikach wody płuczącej;
g) podwyższenie temperatury w zbiornikach magazynujących ciekłe dodatki;
h) awaria urządzeń instalacji zasilania kotłowni paliwem płynnym (w przypadku ich eksploatacji bez stałego personelu konserwacyjnego);
i) podwyższenie temperatury łożysk silnika elektrycznego zgodnie z wymaganiami producenta;
j) obniżenie wartości pH wody uzdatnionej (w programach uzdatniania wody z zakwaszeniem);
k) wzrost ciśnienia (pogorszenie próżni) w odgazowywaczu;
m) zwiększanie lub zmniejszanie ciśnienia gazu.
Przyrządy kontrolno-pomiarowe do kotłowni.
Przyrządy do pomiaru temperatury.
W układach zautomatyzowanych pomiar temperatury odbywa się z reguły na podstawie monitorowania właściwości fizycznych ciał funkcjonalnie powiązanych z temperaturą tych ostatnich. Urządzenia do regulacji temperatury ze względu na zasadę działania można podzielić na następujące grupy:
1. termometry rozszerzalnościowe do monitorowania rozszerzalności cieplnej cieczy lub ciał stałych (rtęć, nafta, toluen itp.);
2. termometry manometryczne do kontroli temperatury poprzez pomiar ciśnienia cieczy, pary lub gazu zamkniętego w układzie zamkniętym o stałej objętości (np. TGP-100);
3. urządzenia z termometrami rezystancyjnymi lub termistorami do monitorowania rezystancji elektrycznej przewodników metalowych (termometry rezystancyjne) lub elementów półprzewodnikowych (termistory, TCM, TSP);
4. urządzenia termoelektryczne do monitorowania siły termoelektromotorycznej (TEMF) wytwarzanej przez termoparę z dwóch różnych przewodników (wartość TEMF zależy od różnicy temperatur pomiędzy złączem a wolnymi końcami termopary podłączonej do obwodu pomiarowego) (TPP, TCA , THC itp.);
5. pirometry radiacyjne do pomiaru temperatury na podstawie jasności, barwy lub promieniowania cieplnego ciała żarzącego się (FEP-4);
6. Pirometry radiacyjne do pomiaru temperatury metodą efektu cieplnego promieniowania ciała żarzącego się (RAPIR).
Przyrządy do pomiaru temperatury wtórnej.
1. Logometry służą do pomiaru temperatury w połączeniu z termometrami
2. Mostki oporowe o standardowych kalibracjach 21, 22, 23, 24, 50-M, 100P itp.
3. Miliwoltomierze przeznaczone są do pomiaru temperatury wraz z
4. Potencjometr z termoparami o standardowych kalibracjach TPP, TXA, TXK itp.
Przyrządy do pomiaru ciśnienia i podciśnienia (w kotłowniach).
Zgodnie z zasadą działania przyrządy do pomiaru ciśnienia i podciśnienia dzielą się na:
- ciecz - ciśnienie (próżnia) jest równoważone wysokością słupa cieczy (w kształcie litery U, TJ, TNZh-N itp.);
- sprężyna - nacisk równoważy siła odkształcenia sprężystego wrażliwego elementu (membrana, sprężyna rurowa, mieszek itp.) (TNMP-52, NMP-52, OBM-1 itp.).
Konwertery.
1. Transformator różnicowy (MED, DM, DTG-50, DT-200);
2. Prąd (SAPHIRE, Metran);
3. Styk elektryczny (EKM, VE-16rb, DM-2005, DNT, DGM itp.).
Do pomiaru podciśnienia w piecu kotłowym najczęściej stosuje się urządzenia w modyfikacji DIV (Metran22-DIV, Metran100-DIV, Metran150-DIV, Sapphire22-DIV)
Przyrządy do pomiaru przepływu.
Do pomiaru przepływu cieczy i gazów stosuje się głównie dwa rodzaje przepływomierzy - zmienny i stały różnicowy. Zasada działania przepływomierzy zmiennoróżnicowych opiera się na pomiarze spadku ciśnienia na oporze wprowadzonym do przepływu cieczy lub gazu. Jeśli zmierzysz ciśnienie przed oporem i bezpośrednio za nim, wówczas różnica ciśnień (różnica) będzie zależała od natężenia przepływu, a zatem od natężenia przepływu. Takie rezystancje instalowane w rurociągach nazywane są urządzeniami ograniczającymi. Normalne membrany są szeroko stosowane jako urządzenia ograniczające w systemach kontroli przepływu. Zestaw membran składa się z krążka z otworem, którego krawędź tworzy z płaszczyzną krążka kąt 45 stopni. Dysk umieszczony jest pomiędzy obudowami komór pierścieniowych. Pomiędzy kołnierzami a komorami montowane są uszczelki uszczelniające. Z komór pierścieniowych pobierane są próbki ciśnieniowe przed i za membraną.
Manometry różnicowe (manometry różnicy ciśnień) DP-780, DP-778-float stosowane są jako przyrządy pomiarowe i przetworniki nadawcze, w komplecie z zmiennymi przetwornikami różnicowymi do pomiaru przepływu; Mieszki DSS-712, DSP-780N; Transformator różnicowy DM; „SZAFIR” – aktualny.
Urządzenia wtórne do pomiaru poziomu: VMD, KSD-2 do współpracy z DM; A542 do pracy z SAPPHIRE i innymi.
Przyrządy do pomiaru poziomu. Alarmy poziomu.
Przeznaczony do sygnalizacji i utrzymywania w określonych granicach poziomu wody i ciekłych mediów przewodzących prąd elektryczny w zbiorniku: ERSU-3, ESU-1M, ESU-2M, ESP-50.
Urządzenia do zdalnego pomiaru poziomu: UM-2-32 ONBT-21M-selsinny (zestaw przyrządu składa się z czujnika DSU-2M i odbiornika USP-1M; czujnik wyposażony jest w metalowy pływak); Pływak UDU-5M.
Do określenia poziomu wody w kotle często stosuje się tę metodę, ale orurowanie nie jest klasyczne, tylko odwrotnie, tj. wybór dodatni jest zasilany z górnego punktu kotła (rurka impulsowa musi być wypełniona wodą), minus z dolnego punktu i ustawiana jest odwrotna skala urządzenia (na samym urządzeniu lub wyposażeniu dodatkowym). Ta metoda pomiaru poziomu w kotle wykazała swoją niezawodność i stabilność. Obowiązkowo należy zastosować dwa takie urządzenia na jednym kotle, jeden regulator na drugim do alarmowania i blokowania.
Przyrządy do pomiaru składu materii.
Automatyczny stacjonarny analizator gazów MH5106 przeznaczony jest do pomiaru i rejestracji stężenia tlenu w spalinach kotłowni. Od niedawna w projektach automatyki kotłowni włączane są analizatory CO-tlenku węgla.
Konwertery typu P-215 przeznaczone są do stosowania w układach ciągłego monitorowania i automatycznej regulacji wartości pH roztworów przemysłowych.
Urządzenia zabezpieczające przed zapłonem.
Urządzenie przeznaczone jest do automatycznego lub zdalnego zapłonu palników zasilanych paliwem ciekłym lub gazowym, a także do zabezpieczenia zespołu kotła w przypadku zgaśnięcia palnika (ZZU, FZCh-2).
regulatory bezpośredniego działania.
Sterownik temperatury służy do automatycznego utrzymywania zadanej temperatury mediów ciekłych i gazowych. Regulatory są wyposażone w kanał bezpośredni lub zwrotny.
Pośrednio działające regulatory.
Automatyczny system sterowania „Kontur”. System Kontur przeznaczony jest do stosowania w obwodach automatycznej regulacji i sterowania w kotłowniach. Urządzenia regulacyjne typu R-25 (RS-29) tworzą wraz z siłownikami (MEOK, MEO) prawo regulacji „PI”.
Układy automatyki ogrzewania kotłowni.
Zestaw sterujący KSU-7 przeznaczony jest do automatycznego sterowania jednopalnikowymi kotłami wodnymi o mocy od 0,5 do 3,15 MW, pracującymi na paliwach gazowych i ciekłych.
Dane techniczne:
1. autonomiczny
2. z najwyższego poziomu hierarchii kontroli (z centrum kontroli lub publicznego urządzenia kontrolnego).
W obu trybach sterowania zestaw zapewnia następujące funkcje:
1. automatyczny start i stop kotła
2. automatyczna stabilizacja próżni (dla kotłów z ciągiem), prawo kontroli pozycyjnej
3. pozycyjna kontrola mocy kotła poprzez załączenie trybu spalania „wysoki” i „mały”.
4. zabezpieczenie awaryjne, zapewnienie zatrzymania kotła w przypadku sytuacji awaryjnych, włączenie sygnału dźwiękowego i przypomnienie przyczyn wypadku
5. sygnalizacja świetlna pracy zestawu i stanu parametrów kotła
6. komunikacja informacyjna i komunikacja zarządcza z wyższym szczeblem hierarchii zarządzania.
Funkcje ustawiania urządzeń w kotłowniach.
Konfigurując zestaw sterowania KSU-7 należy zwrócić szczególną uwagę na kontrolę płomienia w palenisku kotła. Podczas montażu czujnika należy przestrzegać następujących wymagań:
1. ustawić czujnik na strefę maksymalnego natężenia pulsacji promieniowania płomienia
2. pomiędzy płomieniem a czujnikiem nie powinno być żadnych przeszkód, płomień musi zawsze znajdować się w polu widzenia czujnika
3. Czujnik należy zamontować z nachyleniem uniemożliwiającym osadzanie się różnych frakcji na jego wzierniku
4. temperatura czujnika nie powinna przekraczać 50 C; dla których konieczne jest ciągłe przedmuchanie przez specjalną złączkę w obudowie czujnika, aby zapewnić izolację termiczną pomiędzy obudową czujnika a urządzeniem palnikowym; Zaleca się montaż czujników FD-1 na specjalnych rurkach
5. jako element główny zastosować fotorezystory FR1-3-150 kOhm.
Wniosek.
Ostatnio szeroko stosowane są urządzenia oparte na technologii mikroprocesorowej. Tak więc zamiast zestawu sterującego KSU-7 produkowany jest KSU-EVM, co prowadzi do wzrostu wskaźników doskonałości stosowanych systemów bezpieczeństwa, działania urządzeń i jednostek.