Jak zrobić latarnię do samolotu. Przeszklenie kabiny. Lotnictwo cywilne: niestandardowe szyby przednie do samolotów i helikopterów
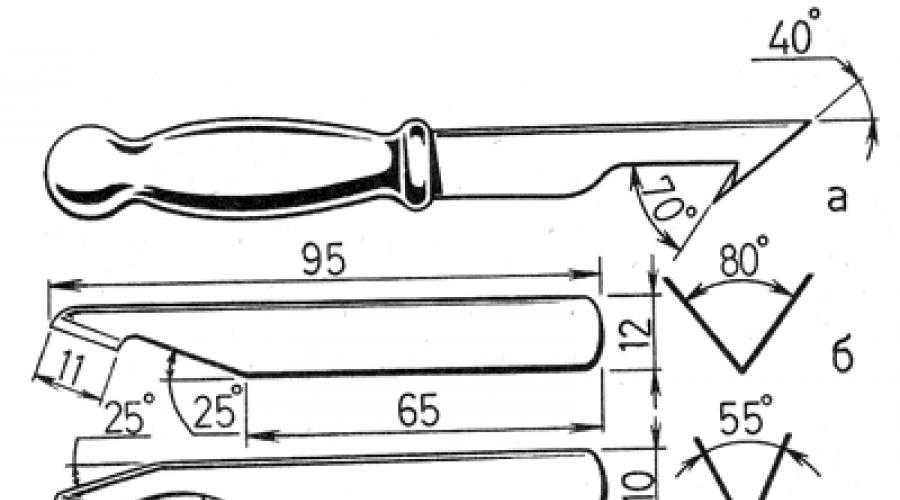
Technologia wytwarzania modeli samolotów z różnych materiałów oraz instrukcje ich obróbki.
Każdy lubi prefabrykowane modele samolotów, ale nie zawsze są one jeszcze dostępne. Ta okoliczność może niektórym wydawać się denerwująca, ale tylko na pierwszy rzut oka. Dość ciekawy i oryginalny model samolotu na blacie można wykonać nawet z papieru, a jeśli używasz drewna lub plastiku, możesz nauczyć się robić modele nie gorsze niż „markowe”, ponieważ nikt nie wymaga od nich latania.
Takie podejście znacznie ułatwia sprawę tym, którzy decydują się poświęcić swój wolny czas na projektowanie i produkcję modeli replik komputerów stacjonarnych. Najważniejsze jest, aby model wyglądał autentycznie na zewnątrz, a to, z czego jest wykonany w środku, nie miało znaczenia. Dlatego podczas pracy nad stołowym „air show” zastosowanie znajdą różnorodne materiały: tektura i papier, drewno, odpady sklejki i styropianu, różne styropianowe opakowania po żywności.
Na początek spróbujcie wykonać model ławkowy słynnego radzieckiego bombowca nurkującego Pe-2 z czasów Wielkiej Wojny Ojczyźnianej w skali 1:72. Na rycinie 6 przedstawiono jego główne rzuty, szablony wykonania korpusu i skrzydła, natomiast na rycinie 7 przedstawiono technologię wykonania. Do wykonania modelu najlepiej użyć miękkiego drewna: osiki, lipy, topoli lub drobnoziarnistego świerku.
Kadłub wykonany jest z solidnego drewnianego bloku, ale jeśli chcesz go wydrążyć, wykonaj półfabrykat z dwóch prętów sklejonych grubym papierem (ryc. 7, a). Jest to konieczne, aby gotowy kadłub można było rozdzielić i wydrążyć od wewnątrz.
Pracę rozpoczynamy od przeniesienia rzutów modelu kadłuba na kalkę. Następnie wklej tę kalkę na obrabiany przedmiot i przeprowadź ją wzdłuż konturu. W ten sam sposób przenieś widok z góry na przedmiot obrabiany (ryc. 7, b). Podczas końcowej obróbki sprawdź poprawność sekcji kadłuba A-A, B-B, B-C (patrz rys. 6) za pomocą szablonów (rys. 7, c).
Skrzydło wykonane jest z litej płyty. Jeśli nie ma desek o odpowiednich rozmiarach, sklej ze sobą kilka prętów. Przetwarzaj powstały przedmiot w taki sam sposób, jak kadłub. Podczas profilowania skrzydła należy skorzystać z szablonów przekrojów G – D i D – D. Aby nadać skrzydłu poprzeczną literę V, wytnij połączenie części środkowej i konsol, a następnie sklej je pod wymaganym kątem. W ten sam sposób wykonaj gondole silnika i powierzchnie ogonowe. Zadaszenie kokpitu może być również wykonane z drewna. W takim przypadku należy pomalować wszystkie przeszklone powierzchnie czarną farbą.
Przyjrzyjmy się bliżej wykonaniu latarni z przezroczystej plexi. Jest przezroczysty i prawie nie zmienia koloru pod wpływem światła słonecznego. Wraz ze wzrostem temperatury pleksi staje się plastyczna, co umożliwia wyciąganie z niej części o różnych kształtach. Najkorzystniejsza temperatura obróbki to 110-135°C. Przy wyższych temperaturach na powierzchni pleksi pojawiają się bąbelki, co prowadzi do wadliwej pracy.
Metoda ciągnienia (rys. 7, d) polega na ciągnieniu nagrzanej pleksi w drewnianej formie składającej się z półfabrykatu 1 i przelotowego okienka matrycowego 2. Stempel wycina się z kawałka twardego drewna (buk) według rysunek. Następnie pokrywa się go klejem kazeinowym, suszy i dokładnie oczyszcza drobnym papierem ściernym, tak aby drewno nie było odsłonięte. Klej kazeinowy można zastąpić żywicą epoksydową lub emalią, ale w tym przypadku klej pozostaje jedynie w mikropęknięciach, a sam stempel jest całkowicie czyszczony do połysku.
Matryca 2 wycinana jest ze sklejki o grubości 3...4 mm tak, aby otwór był o 1,5 mm większy od wymiarów stempla. Krawędzie matrycy należy dokładnie zaokrąglić i obrobić papierem ściernym. Drewniane klocki 3 przybijane są do matrycy od dołu.
Plexi o grubości 1 mm powinna być około 3 razy większa od otworu w matrycy. Ogrzewa się na zamkniętym ogniu (kuchenka elektryczna), aż zmięknie. Następnie przedmiot kładzie się na matrycy, a stempel szybkim, ciągłym ruchem wciska się w otwór matrycy. Siła jest usuwana po ostygnięciu pleksi. Gotową latarnię usuwa się, a nadmiar materiałów przycina. Aby zapobiec powstawaniu zmarszczek na latarni, należy wykonać matrycę dociskową 5 i podczas ciągnienia dociskać obrabiany przedmiot do matrycy głównej. Czasami na gotowej latarni pozostają odciski nierówności stempla lub struktury drewna. Nieregularności te są traktowane drobnym papierem ściernym, a następnie polerowane.
Podczas montażu modelu należy zwrócić szczególną uwagę na symetrię części i ich prawidłową orientację. Po złożeniu modelu należy dokładnie wypełnić wszystkie szczeliny między częściami. Lepiej jest użyć szpachli epoksydowej, szpachli nitro
АШ -22 lub АШ -30 lub szpachlówka olejowa PF002. Ale możesz sam przygotować kit. W tym celu grudkowatą kredę należy przetrzeć na siatce i rozcieńczyć na szkliwie aż do uzyskania pożądanej grubości. Aby uzyskać bardziej miękką szpachlę, można dodać trochę farby nitro. Przed malowaniem cały model pokrywa się warstwą podkładu, następnie ponownie szpachluje i dokładnie obrabia papierem ściernym.
Ten model jest wykonany ze styropianu w niemal identyczny sposób. Niezbędne części, np. skrzydło, można wyciąć z arkusza styropianu o grubości 2...3 mm, a następnie „wykończyć” pilnikami igłowymi i papierem ściernym. Kadłub jest sklejony z pakietu płyt styropianowych. Do pokrycia powierzchni modelu bardzo dobrze nadają się cienkie arkusze styropianu z opakowań do żywności lub błyszczący papier powlekany. Wykończenie styropianem pozwala na ukazanie najdrobniejszych szczegółów na powierzchni modelu, w tym nawet nitów. Są doskonale „wybijane” (przekłuwane tępą igłą) na obrabianych przedmiotach od wewnątrz. Można imitować łączenia i szwy skóry, przyklejać do niej włazy i szyjki wypełniające, wykonywać żaluzje i kratki chłodnicy oraz osłony lampek kontrolnych. Niewielka grubość styropianu umożliwia jego efektywne wykorzystanie do produkcji żeberek bomb i rakiet.
Cięcie arkuszy poszycia można wykonać bezpośrednio na gotowym produkcie, szczególnie jeśli przygotowujemy wycinarki do styropianu, jak pokazano na rysunku 8. Największy z nich (a) jest bardzo wygodny w użyciu metalowej linijki do rysowania prostych linii na powierzchni styropianu , wzdłuż którego łatwo rozpada się na kawałki.
Wskazane jest wykonanie kilku takich noży, wykonanych z fragmentów brzeszczotu do metalu (b, c, d) osobno dla każdego rodzaju pracy. Przykładowo, aby wykonać cienką, płytką fugę, nóż należy naostrzyć pod kątem 30°, a w przypadku głębszych i szerszych pod kątem 55° i 80°. Szczególną uwagę należy zwrócić na dokładne narysowanie ołówkiem linii cięcia pojawiających się na rysunku. Okrągłe elementy „łączące” (na przykład włazy) można łatwo wykonać za pomocą zaostrzonych na krawędziach rurek o różnych średnicach. Po lekkim naciśnięciu rurki na styropianie pozostaje słaby ślad; aby uzyskać wymaganą głębokość, należy obrócić rurkę o 2-3 obroty.
Po zakończeniu wszystkich cięć powierzchnię modelu poddaje się drobnoziarnistemu papierowi ściernemu, a poszczególne defekty naprawia się szpachlą. Po zakończeniu wszystkich tych prac możesz rozpocząć malowanie modelu, jeszcze raz uważnie czytając nasze zalecenia dotyczące wykonania tej ważnej operacji.
Jeden lub dwa modele wykonane w tej technologii (rysunki do tej pracy regularnie publikowane są w takich magazynach jak „Wings of the Motherland”, „Model Designer” i „Young Technician” wraz z załącznikiem) - a staniesz się prawdziwym modelem- kopista, a Twój „pokaz lotniczy na stole” zacznie się dość szybko uzupełniać nowymi modelami samolotów, wybranymi wyłącznie na Twoje życzenie.
Jednocześnie sięgając po różnego rodzaju podręczniki, encyklopedie i czasopisma specjalistyczne, uczynisz z siebie prawdziwego specjalistę w dziedzinie lotnictwa.
I kilka słów o organizacji pracy. Naszym zdaniem racjonalne jest np. wykonanie kilku półfabrykatów tego samego typu jednocześnie, gdy odpowiednie narzędzie zostanie dostosowane i wyprodukowane, jak to się mówi, do tej operacji. Dzięki temu bardzo wygodnie jest obracać koła, wykonywać łopaty śmigieł i kabiny stemplowe. Jeśli jest kilka modeli, wygodniej jest je pomalować: praca jest uproszczona, ostateczny czas wykończenia jest skrócony, a farba oszczędzana.
W artykule opisano szczegółowy proces wykonania kaptura do modelu samolotu z rajstop nylonowych i kleju epoksydowego. Wiele osób ma stare rajstopy, ale jeśli jesteś kawalerem i nie nosisz rajstop, możesz je kupić w supermarkecie.
Od razu ostrzegam – proces wykonania jednego okapu czy daszka może zająć kilka dni, gdyż żywica epoksydowa schnie dość długo. Moim zdaniem montaż maski i daszka lepiej rozpocząć już na początkowym etapie produkcji kadłuba niż na końcu budowy modelu.
I jeszcze jedna mała uwaga (z własnego doświadczenia): lepiej pracować z żywicą epoksydową w ciepłym i suchym pomieszczeniu. Kiedy robiłem okap w czasie deszczu na zimnym balkonie, żywica epoksydowa wchłonęła tyle wilgoci, że nie wyschła przez prawie tydzień. Musiałam nagrzać okap w piekarniku.
Materiały:
- Penoplex
- Płyty sufitowe
- Rajstopy nylonowe
- Klej epoksydowy (nie szybko utwardzający się)
- Klej sufitowy
Narzędzia:
- Ostry nóż biurowy
- Znacznik dysku
- Papier ścierny
- Kwadrat
- Różdżka
- Karty plastikowe
- Drut
- Szkło lub słoik
- Mini wiertarka
Krok 1. Szablony rysunków
Na tekturze rysujemy część dziobową, silnik i wirnik, nie zapominając o grubości poszycia kadłuba i rysujemy kształt maski w trzech rzutach.
Wytnij szablony. Potrzebny jest okrąg o średnicy nieco większej niż podstawa przędzarki, aby nadać kapturowi bardziej opływowy kształt i łatwiej określić lokalizację przyszłego otworu.
Krok 2. Klejenie przedmiotu obrabianego
Na arkuszu penopleksu zaznaczamy prostokąty nieco większe niż szablon. Liczba prostokątów zależy bezpośrednio od wielkości przyszłego okapu.
Przyklejamy je w duży blok za pomocą kleju sufitowego. Ponieważ penoplex jest gładszy i nie wchłania kleju, zalecam najpierw pozostawić pomalowane części do wyschnięcia.
Krok 3. Wycinanie półfabrykatu
Zgodnie z szablonem rysujemy kontury przyszłego okapu na gotowym bloku. Następnie rysujemy prostopadłe wzdłuż kwadratu, aby dokładniej narysować kontury na tylnej stronie.
W ten sam sposób rysujemy kontury boczne.
Za pomocą ostrego noża wytnij profil boczny i narysuj linię (oś symetrii).
Wzdłuż tej osi nakładamy szablon, rysujemy kontury i na podstawie konturów po drugiej stronie półwyrobu wycinamy profil przedni.
Wycinamy trzeci profil i przyklejamy okrąg z sufitu.
Blok przetwarzamy papierem ściernym, aby uzyskać gładką powierzchnię.
Krok 4. Praca „epoksydowa”.
Głowicę zawijamy w foliową torebkę (aby ułatwić późniejsze zdjęcie gotowego kapturka) i naciągamy na nią rajstopy w jednej warstwie.
Skręcamy dół rajstop tak, aby rozeszły się wszelkie fałdy, zabezpieczamy je drutem i przyklejamy na klej sufitowy dwa bloki pianki piankowej, tak aby później można było równomiernie ułożyć bloczek.
Rozcieńczamy żywicę epoksydową w szklance i zaczynamy pokrywać nią głowicę za pomocą plastikowej karty.
Proces nie jest szybki, gdyż przy dobrym oświetleniu trzeba zadbać o to, aby żywica epoksydowa równomiernie nasyciła rajstopy i nie powodowała mocnych smug w dolnej części. Gdy blok zostanie całkowicie pokryty żywicą epoksydową, można go umieścić na szafce do wyschnięcia.
Po wyschnięciu żywicy epoksydowej odcinamy nadmiar rajstop od dołu i odrywamy pręty penoplexu.
Możemy zacząć Krok 4 pierwszy, ale pakiet nie jest już potrzebny. To znaczy, aby uzyskać normalną wytrzymałość, potrzebne są co najmniej trzy warstwy rajstop Krok 4 należy to zrobić trzy razy.
Krok 5: Ostatnie kroki
Po wyschnięciu trzeciej warstwy żywicy epoksydowej otrzymujemy bardzo mocny i gładki kaptur.
Teraz pozostaje tylko usunąć blokadę. Aby to zrobić, narysuj markerem linię wzdłuż dolnej krawędzi i za pomocą mini wiertarki (jeśli nie masz takiego narzędzia, możesz użyć piły do metalu lub pilnika igłowego) odetnij wzdłuż niej nadmiar. Praca wiąże się z dużym zapyleniem, dlatego radzę stosować sprzęt ochronny (respirator i okulary).
Wytnij otwór na silnik.
Przeciskamy blok przez otwór i oddzielamy od kaptura folię, w którą był owinięty.
Dość często modelarze stają w obliczu bardzo nieprzyjemnego momentu. Trzeba zrobić nowyprzeszklenie kabiny (latarka).
Ponieważ ten w zestawie albo został zgubiony, uszkodzony, pęknięty, albo ma niewłaściwy kształt lub jest złej jakości. Produkcjalatarnia, a właściwie przezroczyste elementy modelu, to dość ważny moment. Ponieważ części przezroczystych nie można szpachlować ani wzmacniać, jeśli nie są wykonane dokładnie. Część należy wykonać natychmiast i tak dokładnie, jak to możliwe. Istnieje kilka sposobów wykonania lampionów. Chcę się skupić na klasyce, sprawdzonej nie raz. Ciągnąćprzeszklenie kabiny wykonane z plexi przy użyciu stempla i matrycy. Najpierw wykonujemy matrycę, dokładnie wzdłuż konturu kabiny. Można zrobić niewielki margines 0,1-0,2 mm na późniejszą regulację, czyszczenie i polerowanie. Do tego używam kawałków getinaxu, włókna szklanego lub czegoś podobnego.
Następnie z gatunku drewna np. buk, aby nie było włókien i było dość twarde, wykonujemy poncz. Ponadto wszystkie wymiary stempla należy zmniejszyć o grubość przeszklenie kabiny. Lepiej jednak nieco zwiększyć wysokość, aby dolna krawędź latarni znajdowała się nad płaszczyzną matrycy po włożeniu w nią stempla. Lepiej też zaznaczyć na stemplu np. ołówkiem dolną krawędź latarni plus mały margines na wycięcie.
W przypadku dużych łusek odpowiednia może być plexi o grubości 1 mm, ale w przypadku skali około 1:72 trzeba poszukać czegoś znacznie cieńszego lub samemu zmniejszyć grubość.
Nawiasem mówiąc, grubość jest jednym z powodów, dla których niektóre firmy, zwłaszcza produkując modele w technologii LND, zajmują się produkcją przeszklenie kabiny stosuje się filmy. Obecnie z ogromnej liczby opakowań można wybrać półfabrykat o wymaganej grubości. Osobiście z kilku powodów nie przepadam za tymi foliami, a do lampionów używam plexi. Wróćmy jednak do naszego procesu produkcyjnego. Aby zmniejszyć grubość, jedną ze stron przedmiotu obrabianego szlifuję na kawałku papieru ściernego do wymaganej grubości. Zwykle nowa pleksi jest zabezpieczona obustronnie folią. Dlatego usuwamy go z jednej strony, a drugą zostawiamy na razie w spokoju, aby nie zarysować go podczas szlifowania.
Po uzyskaniu wymaganej grubości 0,5-0,6 mm usuń folię. Jeśli to konieczne, jeśli chcesz, aby latarnia była otwarta, możesz ją zmniejszyć. Strona, na którą nałożono folię, będzie stroną wewnętrzną, ponieważ jest gładka i pozbawiona zarysowań. Teraz w pobliżu źródła ciepła, w którym będziemy podgrzewać obrabiany przedmiot, dla ułatwienia pracy możesz wykonać coś w rodzaju pochylni.
Następnie przechodzimy do samego procesu ciągnięcia. przeszklenie kabiny. W tym celu blankiet z pleksiglasu, trzymany pęsetą lub czymś podobnym, należy podgrzać, aż zacznie się łatwo zginać pod własnym ciężarem. Lepiej jest ogrzewać nad kuchenką elektryczną lub kuchenką gazową, aby pleksi nie wpadła w płomień, ale nad nim się nagrzała. Po nagrzaniu należy bardzo szybko położyć przedmiot polerowaną stroną na matrycy i docisnąć stemplem gładką stronę.
Może Ci się nie udać za pierwszym razem. Dlatego też kolejną zaletą pleksi jest to, że można ją ponownie podgrzać i przyjąć swój pierwotny kształt. Następnie możesz spróbować ponownie. Oczywiście nie można tego robić w nieskończoność. Po uzyskaniu pożądanego efektu przytrzymaj stempel przez kilka sekund, aż plexi całkowicie ostygnie. Następnie wyjmujemy przedmiot z matrycy i ostrożnie zaczynamy wycinać latarnię.
Jeśli wcześniej zaznaczyłeś stempel, to wzdłuż linii znakowania za pomocą pilnika, na przykład z ostrza lub specjalnego, wycinamy żądaną część.
Następnie ustawiamy latarnię na miejscu. Ponieważ strona zewnętrzna nie została poddana obróbce po szlifowaniu, teraz można delikatnie dopasować latarnię do jej kształtu. W razie potrzeby wyostrz krawędzie, ponieważ podczas rysowania ostre krawędzie zapadają się. Następnie czyścimy latarnię wodoodpornym papierem ściernym o różnej granulacji. Następnie polerujemy pastą GOI. Od razu powiem, że proces ten nie jest łatwy, ale po szkoleniu można uzyskać części doskonałej jakości.
W tym artykule przedstawiono proces produkcyjny przeszklenie kabiny wykonany z plexi dla samolotu LaGG-3 produkcji Roden w skali 1:72. Tak ostatecznie wyglądała latarnia. A tak to wygląda na modelu.
Witam Was drodzy i początkujący modelarze.
Czytając artykuły zauważyłem, że wielu modelarzy ma problemy z wykonaniem kokpitów do swoich modeli. Często kabin na zdjęciu albo brakuje, albo są wycięte z butelki i nie mają zbyt estetycznego wyglądu. Modelarze nie chcą robić formy do produkcji właśnie tej kabiny, uznając tę pracę za pracochłonną i niepotrzebną do wykonania jednego modelu. Chcę Cię przekonać, że jest odwrotnie – wszystko jest bardzo proste. I to wcale nie jest drogie.
Będziemy potrzebować: suszarki do włosów, bloku sosnowego, piły do metalu, samolotu i pustej plastikowej butelki.
Zaczynamy od stworzenia szablonów przyszłego formularza. Najpierw wykonujemy szablon górnej części.
.
Następny jest szablon widoku z boku.
. .
No i oczywiście szablon przodu i tyłu naszej przyszłej formy. Szablony te umieszczamy pod kątem zgodnie z widokiem z boku.
. .
.
Skończyliśmy z szablonami, zacznijmy robić formę.
Bierzemy blok, a może paczkę desek połączonych śrubami lub klejem i przenosimy na niego nasz widok z boku. Odetnij nadmiar.
. .
Przenosimy widok z przodu i z tyłu na odpowiednie płaszczyzny.
.
. .
Dla ułatwienia pracy mocujemy blok na spodzie formy. Zaciskamy go w imadle i usuwamy nadmiar za pomocą płaszczyzny.
. .
.
.
Nasza forma jest prawie gotowa, pozostaje tylko przerobić ją papierem ściernym. Na wszystko spędziliśmy dwie godziny.
.
Wszystko zależy od butelki. Radzę używać niebieskich lub kolorowych - przezroczyste wyglądają gorzej. Naszą formę wkładamy do butelki i podgrzewamy suszarką do włosów. W razie potrzeby przymocuj butelkę do formy za pomocą śrub.
.
Wytnij i wypróbuj.
.
Wszystko pasuje. Kabinę zabezpieczamy taśmą aluminiową. Za pomocą cienkiej rurki imitujemy nity.
.
. .
Jak mówiłem, to proste.
Powodzenia wszystkim w budynkach i lotach.
Jak zrobić baldachim do kokpitu w domu i przy minimalnych kosztach?
Myślałem, że ten temat już dawno nie był aktualny, jednak biorąc pod uwagę ilość otrzymanych pytań, rozumiem, że się wzruszyłem. Dlatego też postanowiłam poświęcić osobny artykuł temu, jak wykonuję lampiony na modelu z plastikowej butelki. To, co cieszy w tym procesie, to fakt, że biznes łączy się z przyjemnością. A koszty są naprawdę minimalne i sprowadzają się do kosztu napoju, z którego plastikowa butelka posłuży jako materiał. Nie wiem jak nikomu, ale mi z jakiegoś powodu najbardziej podobają się lampiony wykonane z butelek po piwie. Przejdźmy jednak do rzeczy…
Właściwie nie ma zbyt wiele do zrobienia, musisz zrobić puste miejsce. Aby to zrobić, bierzemy blok, użyłem lipy, jest bardziej jednolity i łatwiejszy w obróbce. W pierwszej kolejności poddajemy obróbce powierzchnie boczne, aby uzyskać pożądany kształt powierzchni dolnej. Wymiary można pobrać z rysunku, widoku z góry lub bezpośrednio mierząc kadłub. Powinno wyglądać jak trapez. Następnie na kawałku papieru lub tektury Whatman kopiuję profil przyszłej budki z rysunku i wykonuję wzór. Używam go do zaznaczenia półwyrobu z naddatkiem na długości i na dole:
Następnie oczywiście góra półfabrykatu jest przetwarzana wzdłuż konturu. Jest wiele sposobów, najpierw możesz to zrobić:
a potem tak:
Po 20-30 minutach otrzymasz coś takiego:
Nakładamy oznaczenia na końce przedmiotu obrabianego:
,
Skopiowałem kontury bezpośrednio z kadłuba na ten sam papier Whatmana i wykonałem wzory.
Następnie wstępnie przetworzyłem tył pustego miejsca:
,
Następnie oderwał przód:
Teraz pozostaje tylko dopracować naszą niezdarną (w dosłownym tego słowa znaczeniu) pracę i nadać jej skończony wygląd. 20 minut szlifowania i otrzymujemy fajny blank:
Teraz będziesz musiał odłożyć na chwilę swoją pracę i trochę odpocząć, zwłaszcza że jest to po prostu konieczne, aby kontynuować pracę.
Oceniając wizualnie (a może i instrumentalnie) wymiary naszego blanku, kierujemy się do sklepu, w którym prezentowany jest największy możliwy asortyment napojów w dużych, plastikowych opakowaniach. Nie wiem dlaczego, ale wolę budki przyciemniane na brązowo, więc zostałam „zmuszona” poszukać w dziale piwnym wykroju na latarnię. 2,5-litrowa butelka piwa Bolszaja Krużka była niemal doskonała zarówno pod względem formy, jak i zawartości. Po wykorzystaniu zawartości przedmiotu obrabianego zgodnie z jego przeznaczeniem ostrożnie odetnij spód i włóż w niego półfabrykat. Aby uniknąć konieczności nadmiernego kurczenia się plastiku, w jakiś sposób mocujemy półfabrykat wewnątrz przedmiotu obrabianego.