Tworzenie bloków konstrukcyjnych własnymi rękami. Różne klocki do samodzielnego montażu. Przygotowanie bloków żużlowych bez specjalnego wyposażenia
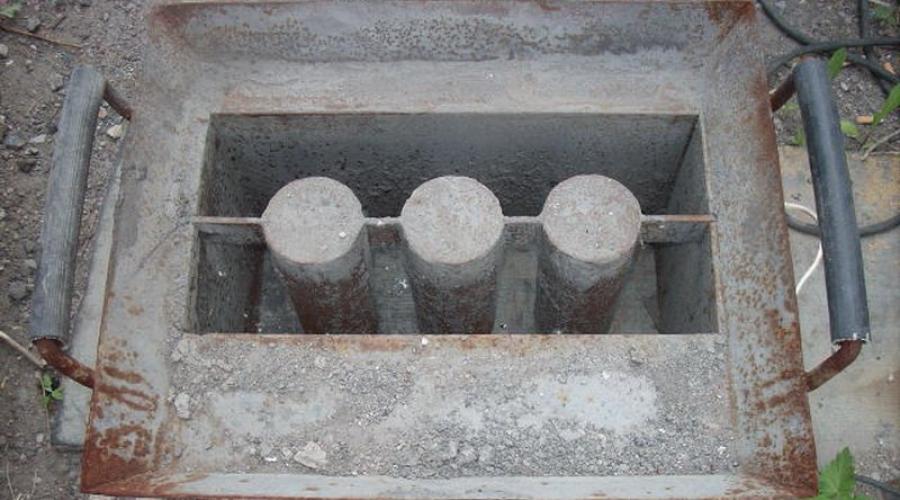
Aby wykonać domowe bloki, wystarczy kilka form do ich odlewania, a także cement, piasek i wypełniacz - żużel lub cegła łamana. Inne rodzaje wypełniaczy (żwir lub kruszony kamień) sprawią, że bloczek będzie bardzo ciężki, a dodatkowo ściana wykonana z takiego materiału latem będzie się szybciej nagrzewać, a zimą wychładzać. Jeśli użyjesz ekspandowanej gliny jako wypełniacza, to chociaż ma ona prawie takie same właściwości termoizolacyjne jak łamana cegła i żużel, będzie kosztować kilka razy więcej.
Formy do produkcji bloczków betonowych budowlanych
Aby samodzielnie wykonać klocki w domu, będziesz potrzebować specjalnych form metalowych lub drewnianych, których wymiary wewnętrzne są różne: 150 x 150 x 300 mm, 175 x 175 x 350 mm lub 200 x 200 x 400 mm. W przypadku małych bloków wygodniej jest murować, a przy dużych blokach budowa odbywa się szybciej.
Aby wykonać składaną metalową formę na jeden blok, potrzebne będą cztery prostokątne żelazne płytki o grubości 3-4 mm (wysokość, szerokość i długość płytek będą zależeć od wybranego rozmiaru formy). Rowki mocujące należy wyciąć po bokach płyt, a uchwyty należy przyspawać do końcowych części formy. W przypadku formy składającej się z czterech bloków będziesz musiał wykonać dwie prostokątne płytki i pięć mniejszych płytek, aby oddzielić przyszłe bloki w formie.
Aby wykonać bloki betonowe własnymi rękami, musisz je zagęścić i stworzyć w nich bąbelki, w tym celu musisz zrobić specjalne urządzenie. Będzie to wymagało jednej prostokątnej płyty żelaznej (w zależności od wielkości formy), małego kawałka walcowanego drutu o przekroju 10 mm i trzech kawałków rury o średnicy 50 mm i długości 150 mm. Na jednym końcu każdej rury należy wyciąć cztery trójkątne „zęby” na głębokość 50 mm. Następnie zęby te należy połączyć ze sobą, tworząc stożek. Szwy między zębami muszą być starannie zespawane. Następnie należy przyspawać uchwyt walcówki do jednej z płaszczyzn płyty, a do drugiej - kawałki rur z tępym końcem.
Drewniana składana forma
Drewniana składana forma
Aby wykonać składaną formę drewnianą, potrzebne będą cztery kawałki desek o grubości 35-50 mm (wymiary będą zależeć od wielkości wybranej formy). Oczywiście drewno jest słabszym materiałem do formowania, dlatego potrzebne są wysokiej jakości i mocne deski. Wszystkie połączenia w formie drewnianej należy zabezpieczyć za pomocą śrub dociągających. W przeciwnym razie konstrukcja drewnianej formy jest taka sama jak metalowa. Uchwyty do formy można wykonać z walcówki o przekroju 10 mm, spłaszczając jej końce i wiercąc w nich otwory o średnicy 6-8 mm.
Aby wykonać bloki konstrukcyjne własnymi rękami, należy przygotować roztwór cementu, piasku i kruszywa (żużla lub cegły łamanej) w stosunku 1:4:6. Dodając wypełniacz do roztworu, należy upewnić się, że jest lepki i lepki, ale nie płynny ani kruchy. Następnie roztwór wlewa się do form, w których podczas upałów twardnieje w ciągu 2 godzin, a ostateczną wytrzymałość uzyskuje w ciągu 1-1,5 dnia. W chłodne dni (+7 ... +18 C) czas utwardzania i całkowitego wyschnięcia wydłuża się 3-5 razy, a w temperaturach poniżej +7 ° C i podczas opadów w ogóle nie zaleca się wykonywania bloków.
Jeśli do zaprawy stosuje się żużel razem z cementem, można całkowicie zrezygnować z piasku, a wówczas stosunek cementu do żużla powinien wynosić 1: 6, a nawet 1: 8.
Przed wlaniem roztworu do formy wszystkie jego części, niezależnie od materiału, z którego są wykonane, należy zwilżyć wodą. Należy pracować na płaskiej powierzchni i wypełnić formę roztworem do 2/3 lub 3/4 objętości (dokładną ilość określa się eksperymentalnie po użyciu urządzenia do robienia pustych przestrzeni).
Po całkowitym stwardnieniu bloku należy go uwolnić od części formy. Surowy blok należy pozostawić do całkowitego wyschnięcia, a części formy wypełnić wodą.
Bloczki można wykonać bezpośrednio na budowie, czyli wypełnić na miejscu. W takim przypadku wymiary formy do napełniania można zwiększyć do 330 x 300 x 600 mm. To jeszcze bardziej przyspieszy proces budowy.
Konsystencja zaprawy cementowej i sposób wylewania są takie same jak w poprzednim przypadku. Możesz przyspawać kilka form do działającej konstrukcji (wystarczą 3-4 formy), a wtedy układanie przebiegnie jeszcze szybciej.
Aby zapobiec przywieraniu mieszanki cementowej do ścianek formy, przed wylaniem jej wewnętrzne wnęki należy obficie zwilżyć wodą lub nasmarować zużytym olejem maszynowym. Po stwardnieniu mieszanki płyty formy odrywa się od ścianek bloku. W procesie wznoszenia ścian należy sprawdzić poziomość i pionowość rzędów. Ogólnie rzecz biorąc, układanie narożników i opaski między blokami w pełni odpowiada metodom murowania półceglanego.
Adobe - mieszanka gliny i słomy do wyrobu domowych klocków
Najtańszym materiałem budowlanym do samodzielnego wykonywania bloczków betonowych w domu jest adobe - mieszanka gliny i słomy. Taniość to nie jedyna zaleta adobe – to materiał trwały, o wysokich właściwościach termoizolacyjnych i łatwy w „produkcji”. Do produkcji bloków Adobe stosuje się również składane formy metalowe lub drewniane. Lepiej jest robić małe bloki, maksymalnie 150 x 150 x 300 mm, ponieważ większe bloki są ciężkie i niewygodne w obróbce, a ponadto nie można w nich zrobić pustych przestrzeni.
Uwaga!
Wadą Adobe jest jego niestabilność na wilgoć. Przed wzniesieniem ścian z cegły należy zapewnić niezawodną hydroizolację fundamentu, a wykończone ściany wymagają tynkowania zaprawą cementowo-piaskową, pokrycia dowolną dostępną siatką polimerową lub metalową i wykończenia.
Domowe bloczki betonowe do budowy
Kolejność pracy przy budowie i produkcji bloczków betonowych jest standardowa: najpierw musisz wybrać miejsce, a następnie wykonać fundament - tutaj musisz zbudować fundament płytowy, możesz użyć płyt fundamentowych, zainstalować komunikację, zbudować ściany, zbudować dach, montaż okien i drzwi oraz wykonanie prac okładzinowych i dekoracji wnętrz kuchni letniej.
Ściany są ułożone w połowie cegły, w letniej kuchni grubość ściany może wynosić jedną cegłę - i to wystarczy. Podczas układania należy wyrównać ściany w pionie i poziomie, za pomocą pionu i sznura rozciągniętego poziomo od jednego rogu domu do drugiego.
Domowa produkcja elementów konstrukcyjnych pozwala obniżyć koszty układania otworów przy późniejszym montażu okien i drzwi. Podczas budowy należy wykonać otwory drzwiowe i okienne w skrzynce budowlanej. Rozmieszczenie okien i drzwi należy ustalić już na etapie planowania. Podczas układania ścian można pozostawić otwory o wymaganej szerokości w miejscach montażu drzwi i okien, a także włożyć drewniane kołki, do których następnie zostaną przymocowane skrzynki pomocnicze. Drewniane zatyczki należy włożyć w drugim rzędzie względem dna pudełka i w przedostatnim rzędzie względem jego góry. Na najwyższym poziomie skrzynki należy zamontować wzmocnione nadproże o grubości 120 mm lub belkę o grubości 70 mm. Końce nadproża należy umieścić 20 cm na ścianach. Jeśli płaszczyzny następnego rzędu muru i górna część ramy znajdują się na różnych poziomach, należy je doprowadzić do żądanej wysokości za pomocą części bloków. i zaprawą lub zmontować szalunek, związać zbrojenie i wypełnić zaprawą cementową.
Po wzniesieniu ścian w miejscach przeznaczonych na okna i drzwi należy zamontować skrzynki, uprzednio zaklinowując narożniki. Następnie należy je wyrównać w poziomie i w pionie, a dopiero potem można przymocować boczne części skrzynki do drewnianych kołków za pomocą gwoździ lub śrub. Pozostałą przestrzeń pomiędzy ścianami, fundamentem, nadprożem i ościeżnicą należy wypełnić po obwodzie pianką akrylową.
Drugim sposobem aranżacji otworów drzwiowych i okiennych jest osadzenie ościeżnic drzwiowych i okiennych w odpowiednich miejscach, a następnie przykrycie ich bloczkami. Zazwyczaj tę metodę stosuje się do dekoracyjnego muru, gdy nie jest zapewniona dalsza dekoracja ścian.
W takim przypadku, aby zapobiec przesuwaniu się ościeżnicy podczas układania, należy podczas układania pierwszego rzędu zacisnąć ją z obu stron klockami, po uprzednim włożeniu wsporników w narożniki. Po drugim rzędzie należy wyrównać skrzynkę w pionie i poziomie, przymocować ją gwoździami lub śrubami po bokach do ściany. Konieczne jest również pozostawienie wylotu 10 cm. Następnie należy zastosować rozwiązanie do wylotów i zacisnąć je blokiem następnego rzędu, ponownie upewniając się, że pudełko jest wypoziomowane. To samo należy zrobić w górnej części ościeżnicy, a także w czwartym i szóstym rzędzie z ościeżnicą okienną. Zworki instaluje się tutaj w taki sam sposób, jak w pierwszym sposobie.
Budowa domu z bloków postępuje szybciej niż z cegieł. Można je kupić swobodnie, jednak wiele osób wykonuje klocki własnoręcznie.
Bloki w budownictwie służą nie tylko do wznoszenia ścian. Użycie bloczków do budowy fundamentów również przyspiesza ten proces. Oczywiście te bloki muszą być bardzo gęste: 1,5 tony na 1 m sześcienny. Wykonywanie bloków własnymi rękami, jeśli na to spojrzeć, nie jest tak niezwykle trudną sprawą.
Gdzie zacząć?
A początkiem wszystkiego jest wykonanie form.
Formularze
W sprzedaży dostępne są formy do klocków konstrukcyjnych o standardowych rozmiarach. A w domu możesz tworzyć klocki w rozmiarach, które Ci odpowiadają. Bierzemy blachę, wycinamy z niej wymagany kształt i spawamy kształt. Formy są również wykonane z drewna; nadają się do bloków Adobe. Tutaj nie jest potrzebne dno. Ale przydadzą się uchwyty po bokach, wygodniej jest z nimi pracować.
Materiał na domowe klocki
Wielką zaletą klocków DIY jest to, że korzystają z materiałów, które już masz lub które możesz łatwo kupić.
Zasadniczo bloki są wykonane z cementu z różnymi wypełniaczami, ale rzemieślnicy, podobnie jak producenci, czasami radzą sobie bez niego. W zależności od wybranego materiału istnieje możliwość wykonania domowych klocków konstrukcyjnych następujących typów:
- beton żużlowy;
- bloki na bazie płynnego szkła;
- cegła suszona na słońcu;
- beton wiórowy lub beton drzewny.
Sposób użycia wypełniacza:
- popiół;
- żużel;
- spadkowicz;
- skruszony kamień;
- gips;
- perłowiec;
- ekspandowana glina;
- trociny;
- słoma;
- połamane cegły i nie tylko.
Bloki bez cementu
Wykonywanie klocków przy użyciu tej technologii nie jest dostępne dla wszystkich, ponieważ mieszanka zawiera płynne szkło. Chyba że ponegocjujesz z najbliższą fabryką wyrobów betonowych i tam kupisz główny komponent. Mieszanka będzie składać się z:
- dwa tuziny części piasku rzecznego;
- półtora tuzina części płynnego szkła;
- 4 części kredy;
- 3 części wapna gaszonego;
- 2 części kaolinu.
Proces produkcji
- Najpierw przesiewa się piasek;
- dodaje się kredę;
- wszystko dobrze się miesza;
- wprowadza się wapno gaszone;
- kaolin lub cegła rozdrobniona na proszek;
- płynne szkło.
Surowiec wyjściowy powinien być jednorodny i przypominać ciasto. Przed wylaniem tej ciastowatej masy należy zwilżyć wnętrza foremek. Jeśli chcesz, możesz dodać kolor do klocków. Aby to zrobić, dodaj:
- kreda dowolnego koloru;
- czerwona cegła zmielona na proszek.
Do takich bloków dodaje się wypełniacze: żużel, keramzyt, wióry. Ich wytrzymałość jest wysoka - są znacznie mocniejsze niż cementowe.
Bloczki z betonu ekspandowanego
Bloczki z betonu gliniastego to jeden z rodzajów bloków żużlowych, w których glina ekspandowana służy jako wypełniacz.
Mieszanina
- cement - 1 część;
- ekspandowana glina - 5 części;
- piasek - 3 części;
- woda - około jednej części.
Technologia
Technologia produkcji pustaków z betonu ekspandowanego jest generalnie taka sama jak każda inna:
- materiał wyjściowy umieszcza się we wstępnie nasmarowanych formach;
- zagęszczony;
- formularz jest usuwany po 10 minutach;
- produkt pozostaje na swoim miejscu;
- po 12 godzinach przenosi się w miejsce chronione przed opadami atmosferycznymi i bezpośrednim działaniem promieni słonecznych.
- przy ciepłej pogodzie bloki stwardnieją w nieco krótszym czasie niż miesiąc.
Jeśli planujesz wykonać grube ściany (około 0,5 m), lepsze będą bloki z pustkami. Aby to zrobić, do formy wkładane są drewniane wkładki: okrągłe lub kwadratowe. Aby można je było łatwo wyjąć, przed włożeniem owiń je blachą dachową.
Zalety
- niewielka waga;
- mrozoodporność;
- oddychalność;
- odporność na wilgoć;
- wytrzymałość;
- niska cena.
Dom z bloczków z betonu spienionego buduje się szybciej niż z cegły, do murowania potrzeba mniej zaprawy.
Bloki Adobe
składniki
Jak na tego typu klocki materiał dosłownie leży pod stopami. Wszystko czego potrzebujesz to:
- glina;
- słoma;
- piasek rzeczny;
- woda.
Cechy selekcji
Aby klocki miały cechy spełniające wszystkie wymagania, trzeba wiedzieć coś o cechach doboru komponentów:
- Lepiej przygotować glinę jesienią, przykryć ją folią i pozwolić jej przezimować - poprawi to jej jakość.
- Najpierw przesiej piasek, uwalniając go od zanieczyszczeń.
- Słomę można zabrać z pola, na którym właśnie zebrano pszenicę, żyto lub jęczmień. Jeśli słoma pozostanie ze zbiorów z poprzedniego roku, jakość nie będzie taka sama - wszak leżąc tam zaczyna gnić.
Jak określić procent składników
- glina - 1 metr sześcienny M;
- słoma - 20 kg;
- piasek - 25%.
Aby nie zepsuć całej partii bloków, musisz zrobić małą partię eksperymentalną. Więc robimy to:
- łączymy wszystkie składniki w małych ilościach i zapisujemy proporcje;
- zrobić partię;
- uformuj kulę;
- pozostawić na słońcu do wyschnięcia na około 1 godzinę;
- rzucamy go na ziemię na wysokość półtora metra.
Jeśli wszystkie elementy zostaną wybrane w wymaganych proporcjach, kula pozostanie nienaruszona. Czy dodałeś więcej piasku niż powinieneś? Zapadnie się lub pęknie. Czy wystarczy piasku? Piłka będzie rozmazana. W ten sposób w praktyczny sposób wybieramy najbardziej optymalną opcję.
Przygotowanie
Aby przygotować mieszankę na kilkadziesiąt bloków na raz, należy wykonać w ziemi dołek: okrągły o średnicy około 2,5 m lub prostokątny 1,5x2,5 o głębokości pół metra. Wyłóż jego spód polietylenem. Chociaż wystarczy jakiś gotowy pojemnik: koryto lub stara wanna. Następnie wszystko robi się tak, jak to robiono za dawnych czasów: zakładamy wysokie gumowe buty i chodzimy, mieszając wszystko, aż będzie gładkie.
Produkcja
- Podczas gdy partia jest na etapie produkcji, przygotowujemy platformę dla produktów: wybieramy płaskie, słoneczne miejsce;
- Przynosimy mieszaninę w wiadrach;
- wypełniać formularze;
- kompaktowy;
- nadmiar usunąć przesuwając deskę po górnych krawędziach formy;
- usuń formularz.
Gotowe bloki powinny wyschnąć. Zwykle trwa to kilka dni. Ważne jest, aby nie były narażone na działanie deszczu. Następnie przenoszone są do schroniska i dalej suszone. Będą całkowicie gotowe za 10 dni.
Dom z bloków Adobe okazuje się bardzo ciepły i wygodny. Ponadto ten materiał budowlany jest przyjazny dla środowiska, trwały i ognioodporny. Stosuje się go w budynkach nie wyższych niż 2 piętra.
Bloczki trocinowe (arobolit)
Technologia wytwarzania bloczków z trocin betonowych jest podobna do produkcji bloczków Adobe, ale komponentów nie trzeba wydobywać, ale kupować.
składniki
Zanim zaczniesz robić, musisz kupić:
- cement - M300 lub wyższy;
- piasek - frakcja nie większa niż 1,8 mikrona;
- nie wapno gaszone;
- trociny (drewno iglaste).
Przygotowanie komponentów
- przesiać trociny;
- wymieszać suchy cement i piasek;
- dodaj tutaj limonkę i ponownie wymieszaj;
- dodać trociny i powtórzyć procedurę mieszania;
- wlać wodę;
- Aby składniki dobrze przylegały do siebie, dodaj chlorek wapnia lub siarczan tlenku glinu;
- kontrolujemy jakość mieszanki.
Aby kontrolować jakość, toczymy piłkę i ściskamy ją w dłoniach. Jeśli woda przepływa, jest jej za dużo w mieszance, jeśli kula się kruszy, jest za dużo trocin lub piasku.
Rozpocznijmy produkcję
- Wyłóż formę folią;
- dodać mieszaninę;
- taranujemy;
- Bez wyjmowania z formy pozostawić do stwardnienia na 5 dni;
- wyjąć z formy i dalej wysuszyć.
Proces suszenia zajmie dużo czasu - od 1,5 do 3 miesięcy: wszystko zależy od masy bloku.
Sprzęt
Jeśli konstrukcja jest na dużą skalę, sensowne może być wydawanie pieniędzy na sprzęt do klocków. Przykładowo: na sprzedaż jest mini maszyna do produkcji betonu drzewnego RPB-1500 BL. Jego wydajność wynosi 1 blok trocin o wymiarach 19 x 19 x 39 cm na minutę. Wyprodukowany przez rosyjskiego producenta - INTEK.
Stoły wibracyjne są szeroko stosowane w produkcji elementów konstrukcyjnych. Rozwiązują problem zagęszczania mieszanin. Stół wibracyjny składa się z:
- ruchomy stół;
- silnik;
- panel kontrolny;
- czasami w zestawie znajduje się transformator.
Zagęszczanie mieszanki roboczej następuje pod wpływem wibracji wytwarzanych przez silnik wibracyjny.
Cykl pracy
- umieść formę na ruchomym stole;
- umieścić w formie połowę lub całkowicie suchą mieszankę;
- Uruchom silnik;
- wysuszenie.
Jak wybrać?
Istnieją 3 typy płyt wibracyjnych zdolnych do zagęszczania materiału wagowo:
- do 75 kg;
- od 75 do 160 kg;
- od 160 kg.
Na podstawie tych wskaźników powinieneś wybrać dla siebie optymalną opcję stołu wibracyjnego.
Producenci
Są produkowane przez:
- Rosyjska firma VPK;
- LLC „Stroymash”;
- Zakład „Czerwonego Maku” w Jarosławiu i innych.
Stoły wibracyjne dostarczają także producenci zagraniczni:
- Hiszpania – Enar i Hervisa;
- Niemcy - Wacker;
- Włochy – Batmatic;
- Francja - Paklita.
Po co robić bloki?
Co trzeba do tego mieć?
Z czego wykonane są bloki?
Jak je wyprodukować?
Dlaczego opłaca się samodzielnie tworzyć klocki?
Jaki jest z tego zysk?
Od czego zacząć i jak rozwijać ten biznes?
W tym artykule otrzymasz odpowiedzi na wszystkie postawione pytania i będziesz mógł „włączyć” dla siebie wiarygodne źródło dochodu, które zależy tylko od Ciebie.
A więc rozwiążmy to po kolei.
Po co robić klocki?
Zapewne zauważyłeś, że budownictwo przeżywa boom przez ostatnie 4-5 lat. Budują od małych i średnich budynków prywatnych: garaży, daczy, osiedli, warsztatów, warsztatów, budynków rolniczych, po duże budynki przemysłowe i mieszkalne, magazyny, centra. Specjaliści z branży budowlanej są poszukiwani bardziej niż kiedykolwiek wcześniej.
Pojawiają się nowe technologie i materiały budowlane. Ale czy zawsze są dostępne pod względem ceny i technologii dla szerokiego grona programistów?
Dlatego są rzadko stosowane w budownictwie małej i średniej wielkości, zarówno w dużych miastach, jak i małych miasteczkach.
Najbardziej przystępnymi cenowo materiałami budowlanymi pozostają tzw. blok żużlowy i cegła.
Co więcej, cegła jest często gorsza od bloku żużlowego pod względem ceny, przewodności cieplnej i łatwości układania.
Jednak puste w środku elementy konstrukcyjne są wygodne i niedrogie dla większości prywatnych deweloperów.
Tak, ponieważ dzięki swoim właściwościom:
Z łatwością można z nich zbudować niską (2-3 piętra) konstrukcję (garaż, dom, domek, budynek gospodarczy, warsztat itp.), Nawet bez uciekania się do usług murarza. (1 blok = 3-4 cegły);
Ściany z pustaków żużlowych są dźwiękoszczelne i nieprzepuszczalne dla ciepła;
Cena bloku żużlowego jest niższa niż cena cegły, bloku piankowego i innych materiałów budowlanych ze względu na niski koszt i dostępność jego składników (patrz poniżej);
Tylko bloki żużlowe można wykonać samodzielnie. Możesz także samodzielnie wykonać adobe (cegłę ze słomy glinianej).
Jak więc samodzielnie wykonać bloki żużlowe?
Co jest potrzebne do produkcji klocków?
Wiadomo, że bloki żużlowe wytwarzano ze zbrojonego betonu przy użyciu specjalnego sprzętu wykorzystującego komorę parową. Dlatego produkcja wysokiej jakości bloku w domu nie była dostępna.
Ale jeśli jest popyt, podaż jest nieunikniona. I to jest!
Od 1994 roku doświadczenie w produkcji elementów konstrukcyjnych w produkcji indywidualnej i małoseryjnej daje odpowiedź na postawione pytanie.
Czego to wymaga?
Maszyna wibracyjna
- Surowy materiał
- Technologia
- Stosunkowo płaski teren
- Sieć domowa na 220V (bez komentarza).
Wyjaśnijmy każdy punkt bardziej szczegółowo.
Maszyna wibracyjna
Istnieją różne konstrukcje maszyn wibracyjnych. W krajowych warunkach produkcji i małych przedsiębiorstwach ręczna, elektryczna, małogabarytowa wibrator bloków żużlowych MZ30 (14 rok produkcji) z pewnością sprawdziła się w krajach WNP. Popularnie znany jako „Sen dewelopera”
Surowy materiał
Do produkcji klocków potrzebne są następujące komponenty:
Cement- Cement portlandzki gatunek 400. Dopuszczalny jest inny. Ale dobór proporcji jest konieczny. Na przykład przy stosowaniu cementu klasy 300 jego zużycie należy zwiększyć o 10-15%.
Wypełniacze do betonu Mogą to być różne materiały: piasek, tłuczeń kamienny, żużel, żużel granulowany, popiół, trociny, wióry, przesiewy, glina ekspandowana, gips, złom ceglany i inne materiały naturalne i przemysłowe.
W zależności od lokalnych warunków, wymagań dotyczących produkowanych bloków i kosztu można wybrać odpowiedni wypełniacz. Wymienię kilka popularnych kompozycji betonów oraz główne grupy betonów
1). Żużel z zakładów hutniczych (szary lub ciemnoszary o dużej zawartości cementu, przesiana drobna frakcja) – 9 części
Cement – 1 część
Woda 0,5 objętości cementu
2). Żużel ziarnisty z zakładów hutniczych (kolor żółto-zielonkawy o dużej zawartości cementu, przesiana drobna frakcja) – 4 części
Małe pokazy – 4 części
Cement – 1 część
Woda 0,5 objętości cementu
3). Inny beton żużlowy
4). Beton na piasku i kruszonym kamieniu
5). Beton na odpadach ceglanych
6). Beton ekspandowany
7). Beton popiołowy
8). Beton trocinowy
9). Beton perlitowy
10). Beton styropianowy
i inne betony z różnymi kombinacjami powyższych.
Teraz jest jasne, że potoczna nazwa „blok żużlowy” nie jest najdokładniejszą definicją możliwych cegiełek.
Dodatek plastyfikujący- Nie jest to istotny składnik betonu. Ale jego obecność zapewnia: wczesną wytrzymałość bloczków (jest to bardzo ważne przy ograniczonej przestrzeni produkcyjnej), poprawia jakość bloczków (zmniejsza się pękanie i ścieranie bloczków), poprawia wodoodporność i mrozoodporność betonu.
Ilość dodatku jest bardzo mała - około 5g w kostce.
Technologia produkcji elementów konstrukcyjnych:
- Przygotowanie betonu
- Produkcja blokowa
- Suszenie i przechowywanie gotowych bloków.
Przygotowanie betonu(na przykładzie podanej wcześniej drugiej receptury betonu)
1). Wsyp 4 łopaty drobnego przesiewu + 4 łopaty granulowanego żużla
2). Napełnij 1 łyżkę cementu
3). Dokładnie wymieszać
4). Dodaje rozpuszczony UPD do 7-9 litrów wody + 250 ml (pół półlitrowego słoika). Roztwór dodatku przygotowuje się w następujący sposób: do 40-litrowego pojemnika wsypać 0,5 kg UPD i dokładnie wymieszać aż do całkowitego rozpuszczenia.
5). Zamieszać. W tym przypadku beton jest jakościowo impregnowany roztworem UPD.
Produkcja blokowa
1). Do maszyny wibracyjnej wlać gotowy beton za pomocą małej zjeżdżalni. Krótko, przez 1-2 sekundy. włącza wibrator - beton zagęszcza się, za pomocą pacy jednym ruchem wyrównujemy powierzchnię lekko osiadłego betonu.
2). Zamontuj zacisk i bez większego wysiłku dociśnij go, włączając wibrator.
Bloki z okrągłymi i prostokątnymi pustkami wibrują przez 4-5 sekund. aż zacisk opuści się na ograniczniki.
Wąskie pełne bloki (2 szt.) wibrują przez 5-7 sekund.
3). Maszynę podnosisz za pomocą wibracji - blok pozostaje na platformie.
Suszenie i przechowywanie gotowych bloków
W przypadku stosowania UPD gotowe bloki można usunąć z placu budowy i przechowywać w ciągu 5-6 godzin. Bez UPD - za dwa dni.
Po tym czasie bloczki nie kruszą się pod warunkiem zachowania proporcji betonu i technologii ich wytwarzania.
Gotowe bloki zalecam przechowywać w piramidalnych stosach w jednym bloku z niewielką (2-3 cm) szczeliną między blokami - w celu dalszego dosuszenia krawędzi bocznych.
W każdej takiej piramidzie znajduje się 100 elementów. Łatwo policzyć. Przydatne jest oznaczenie każdej piramidy datą i godziną produkcji ostatniego bloku. Przyda się to podczas wdrażania. Możesz wysłać 4 lub 5 dnia.
Miejsce produkcji
- Pokój z gładką betonową podłogą.
Bloki można produkować przez cały rok. Pożądana jest dobra wentylacja i ogrzewanie w zimne dni.
- Otwarta płaska powierzchnia.
Może być betonowy lub ziemny, pokryty folią z tworzywa sztucznego, aby zachować prezentację bloczków (tylna krawędź nie ulega zabrudzeniu).
- Otwarty, stosunkowo płaski teren bez wstępnego przygotowania.
Na takiej platformie można układać gotowe bloki na paletach.
Od czego zacząć produkcję klocków konstrukcyjnych?
1. Wybierz najlepszy lokalny materiał betonowy na podstawie kosztów i dostawy.
2. Oblicz koszt 1 bloku, biorąc pod uwagę składniki betonu.
3. Zdecyduj o miejscu produkcji.
4. Kup maszynę wibracyjną.
5. Opanuj podane technologie.
Na początku beton można przygotować ręcznie. Następnie jest to bardziej wydajne i łatwiejsze - na elektrycznej betoniarce o pojemności 0,2-0,5 metra sześciennego (najlepiej 0,5, biorąc pod uwagę przyszłość).
Dlaczego warto samodzielnie tworzyć elementy konstrukcyjne?
Podam moje rzeczywiste koszty kruszywa z dostawą i cementem, kalkulację kosztów wytworzenia bloczków i zwrotu maszyny wibracyjnej „Marzenie Dewelopera” do produkcji bloków żużlowych w Zaporożu (Ukraina) w 2004 roku na przykładzie wykonanego betonu z granulowanego żużla (szarego) i cementu.
Wstępne dane:
8 metrów sześciennych żużla– 30 dolarów/samochód z dostawą na terenie miasta (KRAZ lub duży MAZ)
Cement:
Proporcja 1:9 - 0,88 metra sześciennego lub 18 worków po 3 dolary = 54 dolary
Cena maszyny wibracyjnej- 200 dolarów
Całkowita objętość roztworu:
Proporcja 1:9 – 8 + 0,88 = 8,88 (metrów sześciennych)
Objętość roztworu na 1 blok żużlowy GOST:
Całkowita objętość: 39 cm x 19 cm x 19 cm = 0,014 (m3)
objętość pustek:
Przy d = 9,5 cm: 3 x 3,14 x 4,75**2 x 15 = 3188 cm3 = 0,003188 m3
Objętość roztworu na 1 blok przy d = 9,5 cm: 0,011 metra sześciennego
Tabela wyników obliczeń:
Notatka:
1. W przypadku bloku żużlowego z 2 prostokątnymi pustkami potrzeba mniej zaprawy (ale wytrzymałość takiego bloku jest mniejsza)
2. Zastępując granulowany żużel lokalnym kruszywem do betonu, które jest dla Ciebie akceptowalne, ceny w Twoim regionie (w Rosji cena detaliczna bloku żużlowego są wyższe) i korzystając z wymiarów bloku żużlowego, możesz łatwo obliczyć koszt 1 szt./blok i zwrot pieniędzy za maszynę dla siebie.
Obliczanie rentowności i zysku:
Przyjmujemy wstępne założenia: |
||
Nazwa |
Zakres wartości |
Wartość referencyjna |
Czas na utworzenie 1 bloku (sek.) bez UPD | ||
Liczba bloków na 1 godzinę, biorąc pod uwagę czas obciążania betonu w 30 sekund. (rzeczy) | ||
Liczba bloków w 1 dzień (8 godzin) sztuk | ||
Cena detaliczna 1 bloku żużlowego (w 2005 r.): na Ukrainie |
2,0 UAH (0,4 USD) 15 rub. (0,5 USD) |
|
Rentowność(Z poprzedniej tabeli wynika, że koszt 1 bloku to 1/3 jego ceny detalicznej) |
||
Produkuj bloki dziennie w ilości: na Ukrainie | ||
Wyprodukuj bloki w ilości: na Ukrainie | ||
Koszt będzie wynosić: na Ukrainie | ||
Zyskiem będzie: na Ukrainie |
Notatka :
- Jeśli zastosujesz UPD, produktywność znacznie wzrośnie.
- Rekord należy do Wiktora Romanowa i Siergieja Rachmaninowa, którzy w lipcu 1998 r. w ciągu jednego dnia wyprodukowali 700 bloków 390*138*188
Rozwój i ekspansja biznesu
1. Zatrudniaj odpowiedzialnych pracowników, godnych ich zainteresowania. (W naszym mieście - 20 kopiejek (0,04 centa) za blok, w regionie - 0,02 centa.)
2. Rozpoczynając sprzedaż, obniż cenę detaliczną, tworząc w ten sposób godną konkurencję i otrzymując wdzięcznych klientów i ich rekomendacje. (Ważne! Jakość musi być godna).
3. W sezonie ciepłym lub w ogrzewanym pomieszczeniu (niezależnie od pory roku) pracę można zorganizować na 2 zmiany.
4. W tym przypadku przedsiębiorca zależy tylko od: obecności napięcia w sieci i zdrowia siły roboczej (na pierwszym etapie, przed zwrotem kosztów, możesz samodzielnie pracować z maszyną).
5. Jeśli to konieczne, wynajmij maszynę „programistom”.
6. Realizuj zamówienia od „programistów” bezpośrednio na ich stronie, oszczędzając im pieniądze na załadunku, transporcie i rozładunku bloków.
7. Ponadto – nie będziesz potrzebować pozwolenia od Państwowego Elektronadzoru, ponieważ cały sprzęt jest przeznaczony do zwykłej sieci domowej!
Dekrety Rządu Federacji Rosyjskiej z dnia 13.08.97 nr 1013, Gosstandart Federacji Rosyjskiej nr 86 z dnia 10.08.2001 i Gosstroy Federacji Rosyjskiej nr 128 z dnia 24.12.2001, wykaz do wyrobów wymagających obowiązkowej certyfikacji nie zalicza się bloczków betonowych budowlanych z różnymi wypełniaczami (żużel, keramzyt, trociny itp.) oraz urządzeń wibracyjnych do ich produkcji.
W ten sposób działalność związaną z produkcją bloków konstrukcyjnych można rozwijać etapami:
- Zacznij od minimalnych kosztów zakupu maszyny wibracyjnej, 1 maszyny z lokalnymi surowcami jako wypełniacz do betonu, 15-20 worków cementu.
Udostępnij bezpłatne ogłoszenia sprzedaży wysokiej jakości bloków żużlowych.
Wyprodukuj 800-1000 bloków. Sprzedaj szybko, obniżając cenę detaliczną.
- Zakup betoniarki oraz kolejną partię surowców + UPD.
Wyrównaj cenę do poziomu detalicznego (opcjonalnie).
Publikuj ogłoszenia darmowe + płatne.
- Produktywnie, dzięki zgromadzonemu doświadczeniu produkcyjnemu, produkujemy bloki wysokiej jakości, realizując zamówienia.
Nie ma już potrzeby reklamowania: wysokiej jakości bloki + reklama ustna załatwią sprawę.
Zorganizuj dwuzmianową produkcję klocków konstrukcyjnych.
Poszerzyć asortyment produkowanych bloków.
Zakup dodatkowych maszyn wibracyjnych i ewentualnie betoniarki.
Rekrutuj twardych pracowników
Miej czas, aby przeznaczyć swoje zyski lub zainwestować je w nowy biznes, który będzie równie zyskowny.
Czego Ci szczerze życzę!
Sukces i dobrobyt!!
„Katalog kompletnych pakietów biznesowych” masterdela.info
napisz na adres: [e-mail chroniony],
Ukraina, Zaporoże, sierpień 2005
Bloki budowlane są powszechnym materiałem do budowy konstrukcji o różnym przeznaczeniu. Różnią się rozmiarem, komponentami, metodą produkcji, ale wszystkie są popularnymi materiałami konstrukcyjnymi ścian. Bloki konstrukcyjne są wytwarzane w warunkach przemysłowych, a produkty betonowe i bloki żużlowe są również wytwarzane w domu, co wymaga maszyny do samodzielnego wytwarzania bloków konstrukcyjnych. W zależności od użytego materiału produkty te dzielą się na następujące typy:
- beton żużlowy;
- Beton;
- gazobeton;
- Pianobeton włóknisty;
- styropian.
Bloki żużlowe jako materiał budowlany
Blok żużlowy jest standardowym produktem betonowym, jednak zamiast ciężkiego żwiru i tłucznia stosuje się kruszywo w postaci żużla odpadowego. To zastąpienie nadaje materiałowi lekkość w porównaniu z betonem i dodatkowe właściwości termoizolacyjne, ponieważ żużel wypada korzystnie w porównaniu z ciężkim i gęstym kruszonym kamieniem pod względem przewodności cieplnej.
Produkcja bloków żużlowych wymaga precyzyjnego dozowania składników roztworu, a mianowicie:
- cement gatunku nie niższego niż 400 lub 500, weź jedną część (wiadro);
- piasek z kamieniołomu, wymieszaj 3 części (wiadra);
- żużel, cegła wypalona, glina ekspandowana, materiał ten dodaje się w ilości 5 części (wiadra);
- woda.
Aby uzyskać bloki żużlowe o tej samej jakości, co w fabryce, użyj roztworu o średnio lepkiej konsystencji. Płynny roztwór zmniejszy wytrzymałość bloków, a gęsty roztwór po stwardnieniu utworzy wewnątrz niekontrolowane puste przestrzenie.
Bloki betonowe
Do budowy ścian i innych konstrukcji, jeśli wymagana jest zwiększona wytrzymałość, stosuje się bloczki budowlane z cementu, piasku i tłucznia kamiennego. Stosunek składników do standardowego betonu przyjmuje się w stosunku 1: 3: 6; inne opcje mieszanki betonowej są opisane w podręcznikach dla budowniczych i zależą od marki użytego cementu, wielkości kruszywa i rodzaju piasku.
Bloki z trocin budowlanych
Do budowy budynków mieszkalnych, daczy i domków letniskowych stosuje się lekki i ciepły materiał ścienny z trocin, piasku i wody. Składnikiem wiążącym roztworu jest wapno. Ilość materiału dodanego do roztworu zmienia właściwości produktu końcowego. Wzrost masy trocin prowadzi do wzrostu właściwości termoizolacyjnych, ale przyczynia się do zmniejszenia wytrzymałości. Wraz ze wzrostem ilości piasku w roztworze wzrasta wytrzymałość, a jednocześnie zwiększa się granica mrozoodporności, co zwiększa właściwości użytkowe materiału. Bloki są szeroko stosowane w budownictwie mieszkaniowym jako okładziny konstrukcji izolacyjnych.
Głównymi zaletami bloków są dostępność materiałów i niska cena, długa żywotność bez zniszczenia, przyjazność dla środowiska materiału i łatwość produkcji. Instalacja do produkcji klocków budowlanych własnymi rękami jest dostępna w produkcji i jest popularna wśród rzemieślników domowych. Beton trocinowy ma wydłużony czas schnięcia, dlatego wewnątrz produktu wykonuje się kilka otworów przelotowych, aby poprawić przepływ powietrza.
Wymiary bloków trocin nie są ściśle regulowane, ich szerokość przyjmuje się jako wielokrotność grubości ścianki. Jeśli mówimy o standardowych rozmiarach, bloki są wykonane zgodnie z podwójną grubością cegły (140 mm - 65 x 2 + 10 cm). Przy wytwarzaniu trocin najpierw miesza się suche składniki, następnie dodaje się wodę i do pracy wykorzystuje się mieszalniki zaprawy.
Bloczki budowlane z betonu komórkowego
Ich przygotowanie wiąże się ze złożonym procesem nasycania roztworu gazami, który jest trudny do odtworzenia w domu. Pustaki z betonu komórkowego wyróżniają się lekkością, wysokimi właściwościami dźwiękochłonnymi i termoizolacyjnymi.
Produkty z pianki włóknistej do murów
Pianobeton włóknisty jest z natury przyjaznym dla środowiska materiałem ściennym zawierającym piasek, pianę i cement. Zaawansowane technologicznie maszyny do budowy klocków natryskują piankę w masę roztworu, która tworzy jednolite, zamknięte cząstki przestrzeni. Aby zwiększyć wytrzymałość bloków, producenci stosują wzmocnienie włóknem poliamidowym w całej masie. Ten materiał ścienny jest bardzo trwały, nie gnije, jest lekki i trwały.
Ich bloczki z pianki włóknistej produkowane są w różnych rozmiarach. Do ścian nośnych użyj 20x30x60 cm, który waży 22 kg. Aby zbudować ceglany mur tego samego rozmiaru, będziesz potrzebować 18 kamieni, będą one ważyć 72 kg. Bloczki o mniejszej grubości (10 cm) stosowane są do budowy ścian wewnątrz budynków, przegród, a także służą do izolacji podłóg i ścian. Przewodność cieplna betonu piankowego jest 2,7 razy mniejsza niż cegły i 2 razy mniejsza niż betonu żużlowego i skał łupkowych.
Duże rozmiary bloków zmniejszają zużycie zaprawy cementowo-piaskowej do murowania 20 razy w porównaniu do budowy ściany z kamieni o małych rozmiarach. Pianobeton włóknisty nie pali się, nie zmienia kształtu pod wpływem wysokich temperatur i nie wydziela szkodliwych zanieczyszczeń po podgrzaniu.
Bloki styropianowe
Materiał zaliczany jest do innego rodzaju lekkich bloczków betonowych. Różni się od betonu standardowego lepszymi parametrami użytkowymi i niższymi kosztami produkcji. Innowacyjny materiał ścienny przewyższa wagą wszystkie znane lekkie betony, nawet piankowy jest półtora razy cięższy. Dzięki temu wskaźnikowi domy budowane są bez zwykłego masywnego fundamentu, a koszt transportu materiału jest zmniejszony.
Produkcja bloków styropianowych polega na starannym połączeniu cementu, piasku, cząstek styropianu i specjalnych dodatków zatrzymujących powietrze w całej masie. Wszystkie inne właściwości fizyczne materiału plasują go o krok wyżej niż materiały konwencjonalne. Niska nasiąkliwość i paroprzepuszczalność sprawiają, że styropian jest odporny na wielokrotne zamrażanie i rozmrażanie, co wpływa na trwałość budowanych konstrukcji. Po wzniesieniu ścian z materiałów standardowych w ciągu roku następuje niewielki skurcz. W przypadku bloczków styropianowych nie trzeba czekać tak długo.
Instalacja do produkcji klocków budowlanych własnymi rękami
Do produkcji konstrukcji budowlanych stosuje się specjalne urządzenie działające na zasadzie procesora wibracyjnego.
Taka maszyna wibracyjna lub stół wibracyjny jest projektowany niezależnie. Własnoręcznie wykonana instalacja do produkcji bloków konstrukcyjnych znacznie obniża koszt bloków i, odpowiednio, ścian domu.
Przygotowanie roztworu
Roztwór przygotowuje się z piasku, cementu, wody i kruszywa, do których stosuje się różne materiały, jak opisano powyżej. Aby sprawdzić konsystencję roztworu pod kątem płynności, niewielką ilość wysypać na ziemię. Wysokiej jakości mieszanka nie rozprowadza się wodnistymi strumieniami, zaciśnięta w pięść skleja się w grudkę.
Produkcja bloków żużlowych polega na dokładnym oczyszczeniu żużla z obcych cząstek, a niespalone części węgla nie mogą przedostać się do roztworu. Czasami do roztworu dodaje się gips. W tym przypadku miesza się trzy części żużla i jedną część gipsu, jednocześnie wprowadzając wodę. Rozwiązanie to jest szybkie w użyciu, ponieważ tynk twardnieje w ciągu kilku minut. Przed zmieszaniem żużel nasącza się wodą. Aby poprawić jakość produktów wyjściowych, do roztworu dodaje się nowoczesne dodatki plastyfikatorów. Ich działanie zwiększa mrozoodporność, wodoodporność i wytrzymałość mechaniczną bloczków.
W zależności od przeznaczenia wykonuje się dwa rodzaje bloczków betonowych – pełne i puste. Te pierwsze służą do wykonywania trwałych konstrukcji, ścian nośnych i fundamentów. Drugi rodzaj bloków służy jako materiał przegrodowy, dobrze izoluje od zimnych i obcych dźwięków.
Wykonywanie bloczków betonowych bez stołu wibracyjnego
Spośród tych dwóch technologii zastosowanie drewnianej formy, która została zaprojektowana tak, aby umożliwić naturalny przepływ rozwiązania bez wibracji, cieszy się niesłabnącym zainteresowaniem. Umieszczenie roztworu w przygotowanej formie odbywa się w kilku etapach. Najpierw pojemnik napełnia się jedną trzecią roztworu, po czym ściany formy są ostrożnie pukane młotkiem na obwodzie, aby uzyskać wysokiej jakości skurcz zaprawy betonowej. W kolejnych dwóch etapach dodawany jest roztwór według oryginalnej technologii, aż do wypełnienia formy. Produkcja bloczków z pustymi przestrzeniami polega na umieszczeniu w nieutwardzonym roztworze dwóch plastikowych butelek z wodą, które po stwardnieniu są wyjmowane.
Formy pozostawia się do wyschnięcia na 2-5 dni. Następnie bloki są ostrożnie wyjmowane ze składanej konstrukcji i układane na paletach aż do całkowitego wyschnięcia. Dzięki tej metodzie produkcji nie ma potrzeby zakupu.
Potrzebne będą następujące narzędzia i sprzęt: sito do przesiewania piasku, formy do zaprawy, koryto do mieszania lub betoniarka, młotek do gwintowania, wiadro, łopata, kielnia i tace do suszenia.
Sposób wytwarzania bloków za pomocą maszyny wibracyjnej
Aby to zrobić, kup lub wykonaj własną maszynę wibracyjną do bloków żużlowych. Na płaszczyźnie maszyny instalowana jest specjalna metalowa forma i wlewa się do niej mieszankę betonową z wypełniaczem żużlowym do jednej trzeciej. Następnie do akcji podłącza się stół wibracyjny na maksymalnie 20 sekund, co pozwala usunąć wszystkie niepotrzebne pęcherzyki powietrza z roztworu, a cement uzyska dobry skurcz. Roztwór wlewa się do formy trzykrotnie. Bloki są wyjmowane z formy w taki sam sposób, jak w przypadku produkcji bezwibracyjnej.
Blok żużlowy nie toleruje suszenia w czasie upałów w otwartych promieniach słońca, dlatego w upalne dni spryskuje się go wodą i przykrywa ceratą lub celofanem, aby wilgoć nie odparowywała tak aktywnie. Uformowane, całkowicie wyschnięte bloczki betonowe uzyskują 100% wytrzymałości w 28 dniu i po tym czasie są gotowe do użycia w budownictwie.
Funkcje wytwarzania bloków żużlowych
Formy wykonuje się niezależnie, przy użyciu metalu lub drewna, szerokość desek wynosi co najmniej 190-200 mm. Są one połączone w prefabrykowaną konstrukcję, której boczne części są odłączane w celu usunięcia gotowego bloku. Ogólny projekt łączy nie więcej niż 6 komórek do układania betonu. Gotową konstrukcję montuje się na gęstym, wodoodpornym materiale, takim jak cerata, tworzącym dno formy.
Jeśli jako materiał na formę wybrano drewno, jest ono wstępnie impregnowane lub podkładowane w celu zwiększenia odporności na wilgoć. Formy wykonane są z suchego drewna. Warunki te są spełnione, w przeciwnym razie podczas pracy drewno odsunie się od wody i zmieni się rozmiar geometryczny bloku. Standardowe wymiary kamieni to 400x200x200 mm, ale każdy prywatny producent wykonuje bloki do własnej konstrukcji.
W przypadku matryc metalowych pobiera się arkusze o grubości nie większej niż 3-4 mm. Podczas spawania konstrukcji wszystkie spoiny wykonuje się od zewnątrz, aby nie zaokrąglać narożników bloku. Pustki wewnątrz bloku żużlowego wykonuje się z kawałków metalowych rurek o odpowiedniej średnicy, na przykład 80 mm. Kontrolowana jest odległość między rurami i odległość od ścian, kompozycja jest spawana w paski w celu zapewnienia sztywności i mocowania.
Jeśli wytwarzany jest sprzęt do produkcji bloków konstrukcyjnych, to podczas mocowania wibratora do stołu, po dokręceniu nakrętek, są one nadal lekko zespawane. Silnik należy osłonić obudową ochronną wykonaną z dowolnego materiału, chroniącą przed rozpryskami roztworu, wodą i kurzem.
Technologia produkcji bloczków trocinowych
Dostępne materiały nie są wstępnie przetworzone i można je kupić w każdym sklepie z narzędziami, dlatego produkcja bloków z piasku, wapna i trocin rozpoczyna się natychmiast po zakupie. Aby wymieszać roztwór, użyj betoniarki lub mieszarki do zapraw, ponieważ ręczne mieszanie odpadów drzewnych jest trudne.
Suche trociny, przesiane przez grube sito, miesza się z piaskiem i cementem. Do roztworu dodaje się wapno lub przygotowane ciasto gliniane. Powstałą mieszaninę dobrze miesza się i dopiero potem dodaje wodę, stopniowo wlewając ją małymi porcjami. Aby określić gotowość roztworu, należy go wycisnąć w dłoni, po czym na grudce powinny pozostać odciski palców, co wskazuje prawidłowe proporcje.
Przed napełnieniem form roztworem wyściela się je cienką warstwą trocin. Wewnętrzne otwory w blokach wykonuje się za pomocą drewnianych kołków o wielkości około 70-80 mm, które wbija się w matrycę przed wylaniem roztworu. Materiał bloków konstrukcyjnych jest szczelnie umieszczany w formie za pomocą specjalnego ubijaka. Pojemnik napełnia się do góry i pozostawia do wyschnięcia na trzy dni. Po tym okresie roztwór zyskuje około 40% wymaganej wytrzymałości.
Formy są demontowane, a bloki suszone przez kolejne cztery dni, po czym wytrzymałość osiąga 70% wymaganego limitu. Gotowe produkty układane są na paletach i chronione przed bezpośrednim działaniem promieni słonecznych. Suszenie bloków jest szybsze, jeśli podczas przechowywania pozostawisz szczeliny między produktami. Zaleca się ustawienie tac w miejscu przeciągu lub zastosowanie wentylatora w celu wymuszonej wentylacji.
Bloczki trocinowe zyskują 100% wytrzymałości po wyschnięciu przez 3 miesiące, ale można je użytkować po miesiącu wietrzenia. W tej chwili ich siła wynosi 90%.
Maszyny i urządzenia
Aby uzyskać wymaganą do budowy liczbę bloków, kupuje się gotową maszynę do wibroformowania. Marka TL-105 ma dobrą wydajność. I choć jego moc wynosi zaledwie 0,55 kW, to w ciągu godziny pracy produkuje około 150 bloczków betonowych o różnym kruszywa. Jego przybliżony koszt na rynku wynosi około 42 800 rubli. Współcześni producenci oprzyrządowania obrabiarkowego produkują wiele typów maszyn do produkcji bloków o dodatkowych funkcjach. Ceny maszyn są różne, a koszt klocków zależy bezpośrednio od tego.
W przypadku małych konstrukcji prywatnych odpowiednia jest maszyna wibracyjna 1IKS, która kosztuje około 17 000 rubli, moc wynosi tylko 0,15 kW, taki sprzęt wytwarza 30 bloków na godzinę. Kupując maszynę należy wziąć pod uwagę poziom produkcji bloków na potrzeby konstrukcyjne.
Podsumowując, należy zauważyć, że tworzenie klocków własnymi rękami znacznie zaoszczędzi pieniądze na produkcji produktów. Cena nabycia nie uwzględnia wynagrodzenia wypłaconego pracownikowi. Koszt bloku nie obejmuje kosztów ogólnych i produkcyjnych, podatków i innych odliczeń, dzięki czemu materiał budowlany jest tańszy niż dom.
Możesz znacznie obniżyć koszty finansowe budowy mieszkań, jeśli wykonasz gazobeton własnymi rękami w domu. Wyroby z betonu komórkowego są bardzo często stosowane w budownictwie.
Łatwo jest z nich zbudować różnorodne budynki przy dużych oszczędnościach w zaprawie.
Co to jest gazobeton
Bloczki budowlane z betonu komórkowego mogą mieć różne rozmiary i kształty. Ale ich skład jest prawie zawsze taki sam. Możesz wykonać bloczki z betonu komórkowego własnymi rękami z:
- wysokiej jakości cement;
- Limonka;
- piasek kwarcowy;
- gips;
- proszek aluminiowy;
- woda.
Technologia produkcji tego materiału jest dość prosta. Beton komórkowy możesz produkować na podwórku swojego domu lub bezpośrednio na placu budowy. Gotowe bloczki to równoległościany wykonane z porowatej masy betonowej zawierającej wiele drobnych porów powietrza. Mierzą około 3 mm. Pory powstają poprzez dodanie pasty lub proszku aluminiowego do roztworu. Czasami oprócz wymienionych składników do kompozycji dodaje się inne substancje w bardzo małych ilościach. Są potrzebne do zmiany niektórych parametrów materiału budowlanego.
Zgodnie z metodą produkcji beton komórkowy można wytwarzać metodami autoklawowymi i nieautoklawowymi. Pierwsza metoda nie nadaje się do użytku domowego. Wymaga drogiego sprzętu. Metoda bez autoklawu jest prostsza; pozwala na samodzielne rozpoczęcie produkcji betonu komórkowego w domu. Podczas produkcji wykorzystuje się reakcję wody z proszkiem aluminiowym, w wyniku czego wydziela się ogromna ilość dwutlenku węgla, który tworzy pory wewnątrz bloków. Masa po pewnym czasie twardnieje. Dzieje się to w warunkach naturalnych. Korpus bloku zawiera wiele porów o średnicy od 1 do 3 mm.
Mini-zakład do produkcji betonu komórkowego nieautoklawizowanego
Główną zaletą bloku gazowego jest porowata struktura. Pory nadają materiałowi lekkość i wysokie właściwości termoizolacyjne. Gęstość dla betonu komórkowego utrzymuje się na poziomie 300-1200 kg/m3. Aby pory mocno trzymały się w betonie, należy je umieścić w mocnej formie, która określa wielkość przyszłego bloku. Masa twardnieje w ciągu 2 godzin. Następnie bloki można wyjąć z formy i umieścić na stojakach do całkowitego stwardnienia. Ostateczna wytrzymałość powstaje dopiero w 28 dniu naturalnego suszenia bloków.
Wykonywanie betonu komórkowego własnymi rękami
Produkcja betonu komórkowego w domu wymaga pewnych narzędzi. Musisz przygotować:
- szlifierka z tarczą;
- piła do drewna;
- wiertarka elektryczna;
- samolot;
- piła do metalu do obróbki metalu;
- ostry nóż;
- młotek hydraulika;
- łopata do zaprawy;
- mikser do mieszania mieszaniny;
- linijka;
- konstrukcja suszarki do włosów;
- Mistrz OK,
- stalowy sznurek do cięcia bloków;
- szpachla;
- waga;
- dłuto i dłuto;
- wiadro pomiarowe
Za pomocą kubka pomiarowego i wagi mierzy się składniki niezbędne do rozwiązania. Produkcja bloków gazowych odbywa się z następujących komponentów:
- Gatunek cementu portlandzkiego M400-M500 - 50-70%;
- przesiany piasek kwarcowy - od 20 do 40%;
- wapno jako plastyfikator - 1-5%;
- proszek lub pasta aluminiowa - 0,04-0,09%;
- woda - 0,25-0,8%.
Składana forma metalowa Wylewanie lekkiego betonu Usuwanie nadmiaru zaprawy betonowej Bloki po rozbiórce
Mieszankę dokładnie miesza się i układa w formy o różnych kształtach. To może być całkiem trwałe pudełko. Jego wysokość jest równa wysokości bloków. Całkowita objętość wynosi 4-9 bloków gazowych. Formy mogą być wykonane z drewna lub metalu. Wskazane jest, aby konstrukcja była składana. Bardziej złożoną opcją jest pudełko z ogniwami, które może być wykonane z drewna o grubości 30-40 mm lub metalu o grubości 4-6 mm. Przegrody wewnętrzne mogą być wykonane ze sklejki. Jego grubość powinna wynosić 12-15 mm. Przed wylaniem zaprawy powierzchnie od wewnątrz należy nasmarować olejem technicznym i całą konstrukcję wygrzać suszarką do temperatury 40˚. Mieszankę wylewa się do poziomu połowy wysokości pudełka. Pozostała przestrzeń zostanie wypełniona w miarę rozszerzania się kompozycji i tworzenia się porów.
Reakcja uwolnienia gazu trwa 6-8 minut. Roztwór najpierw podnosi się, a następnie lekko kurczy. Po obkurczeniu można odciąć górną część przygotowanym sznurkiem i wyjąć bloki z formy. Chłodzenie bloków powinno odbywać się w warunkach naturalnych. Nie zaleca się stosowania wentylatorów. Zaleca się montaż formy na płaskiej, poziomej powierzchni. Lepiej jest przygotować kilka pudełek na raz, aby wymieszać znaczną ilość roztworu. Miejsce pracy musi być osłonięte przed wiatrem i opadami atmosferycznymi. Rozmiary bloków można wybrać według własnego uznania.
Wnioski w temacie
Jak zrobić bloki gazowane w domu? Czy ta opcja jest możliwa? Z czego oni są zrobieni? W końcu potrzebujesz specjalnego sprzętu i sprzętu do produkcji betonu komórkowego w domu. Możesz budować ściany domów znacznie niższym kosztem, jeśli sam wykonasz bloki gazowane. Tylko materiały budowlane do autoklawów wymagają specjalnego sprzętu. Tak powstają w produkcji materiały betonowe. W domu możesz przygotować bloki tylko metodą bez autoklawu. Aby to zrobić, potrzebujesz wysokiej jakości cementu portlandzkiego, piasku z minimalnymi domieszkami gliny, wapna, wody, proszku aluminiowego i innych substancji, które zmienią właściwości gotowego produktu.
Mieszankę dobrze miesza się i wlewa do foremek, które można również wykonać samodzielnie. Po 2 godzinach wierzchołki bloków odcina się metalowym sznurkiem, same bloki są usuwane i układane do suszenia. Ostateczne suszenie trwa 4 tygodnie. W tym czasie bloki zyskują prawdziwą siłę. Do produkcji betonu komórkowego na 1 m3 bloczków potrzeba 90 kg cementu, 300 litrów wody, 0,5 kg proszku aluminiowego, 35 kg wapna i 375 kg piasku. To jest przybliżony skład.
Bloczki z betonu komórkowego są materiałem do budowy ścian. Charakteryzuje się wysoką jakością i trwałością. Szeroko stosowany w budownictwie niskim. Aby zbudować własny dom, całkiem możliwe jest tworzenie bloków własnymi rękami.