Sztuczny marmur, jego odmiany, właściwości i cechy produkcyjne. Jak zrobić marmur z betonu: technologia. Sztuczny marmur z betonu Produkcja sztucznego marmuru z betonu
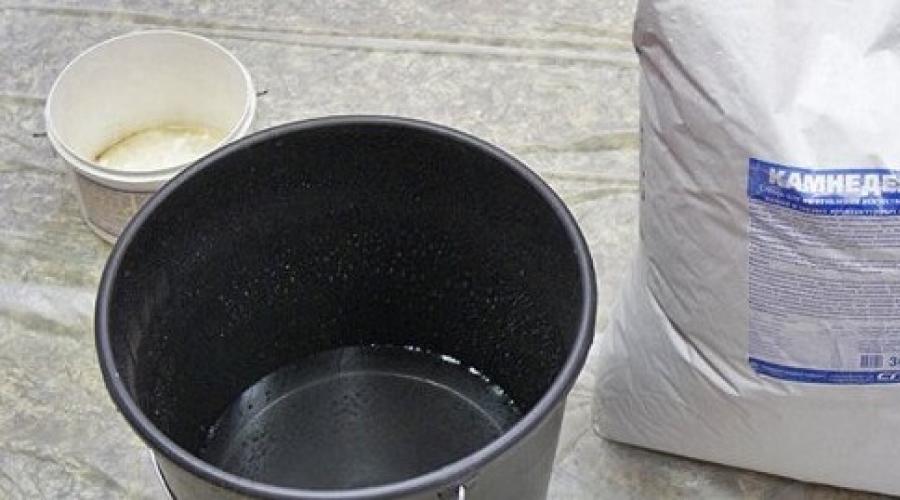
Sztuczny marmur to nowoczesny materiał wykończeniowy, który nadaje się do prac wewnętrznych i zewnętrznych. Różni się od innych estetycznym wyglądem i przystępną ceną. Ponadto, dzięki prostocie technologii produkcji i niskim kosztom materiałów, możesz wykonać go samodzielnie w domu.
Sztuczny marmur – co to jest?
Sztuczny marmur to nowoczesny materiał wykończeniowy, który nadaje się do prac wewnętrznych i zewnętrznych.
Sztuczny marmur to materiał budowlany imitujący kamień naturalny. Można go wytwarzać na trzy sposoby:
- wykonane z betonu;
- gips;
- żywice poliestrowe.
Dodawane są do nich wypełniacze, utwardzacze i barwniki, które po odpowiednim wymieszaniu tworzą smugi, plamy i żyłki powtarzające wzór naturalnego marmuru i nadające mu wyjątkowe właściwości:
- wytrzymałość;
- odporność na ciepło - taki marmur nie pali się i nie przewodzi prądu;
- przyjazność dla środowiska - jest nietoksyczny nawet po podgrzaniu;
- odporność na chemikalia, kwasy, zasady, rozpuszczalniki, aceton i benzynę;
- odporność na wilgoć - materiał nie gnije i nie rozwarstwia się;
- odporność na uderzenia;
- wytrzymałość cieplna.
Zalety sztucznego marmuru obejmują:
- produkcja bezodpadowa;
- łatwość opieki;
- niski koszt w porównaniu do kamienia naturalnego;
- szeroka gama kolorów i kształtów.
Wszystkie znacznie rozszerzają zakres jego zastosowania. Dziś wyroby ze sztucznego marmuru zdobią nie tylko budynki mieszkalne, mieszkania i biura, ale także szkoły, placówki medyczne, w tym stołówki, czy szpitale położnicze. Służy do wykonywania parapetów, blatów, lad barowych, wanien, schodów, wazonów, rzeźb, fontann i zlewozmywaków. Służy do wykończenia pieców, piekarników, grzejników i urządzeń elektrycznych. Niektóre odmiany marmuru są wykorzystywane w przemyśle.
Zlew z odlewu marmurowego
Rodzaje
Istnieją 4 rodzaje sztucznego marmuru:
- castingi są najpopularniejsze. Jest to mieszanina żywic poliestrowych oraz wiórów marmurowych lub piasku kwarcowego, które wsypuje się do specjalnych form w celu utwardzenia. Dzięki takiemu składowi doskonale imituje nie tylko naturalny marmur, ale także jaspis, onyks, malachit czy granit.
- płyn - materiał wykonany z wiórów marmurowych i polimerów akrylowych. Nie tak dawno był stosowany w budownictwie, ale ma wiele zalet, m.in. niski ciężar właściwy, elastyczność i przyjazność dla środowiska. Można go łatwo ciąć nożem lub nożyczkami, zastępuje tapetę i pozwala stworzyć idealnie płaską, bezszwową powierzchnię. Dzięki temu płynny marmur wykorzystywany jest w procesie wykańczania pomieszczeń o nieregularnym kształcie.
- Oselkovy – to masa gipsowa malowana i polerowana na lustrzany połysk utwardzaczami. Swoim spektakularnym wyglądem pozwala imitować nie tylko marmur, ale także malachit czy lapis lazuli. Różni się od innych typów swoimi specjalnymi właściwościami: lekkością i dużą wytrzymałością, dzięki czemu z powodzeniem stosuje się go przy budowie różnych konstrukcji. Często stosowany jest w budynkach mieszkalnych i mieszkaniach w celu poprawy mikroklimatu, gdyż posiada unikalne właściwości pochłaniania lub oddawania nadmiaru wilgoci.
- mikrokalcyt, czyli mielony - powstaje w wyniku mielenia białego marmuru. Powstałą szarą lub białą, proszkową substancję wykorzystuje się do produkcji wyrobów z tworzyw sztucznych, linoleum, papieru, środków czyszczących oraz wyrobów z farb i lakierów.
Praca przygotowawcza
Formy do wytwarzania sztucznego marmuru można kupić lub wykonać samodzielnie.
Najprostszym sposobem na wykonanie sztucznego marmuru jest cement i piasek. Jeśli zastosuje się technologię, w tym przypadku produkty zachowują wszystkie swoje właściwości. Najważniejsze, aby nie robić płyt zbyt cienkich lub grubych. Te pierwsze okazują się kruche, drugie zaś ciężkie.
Aby zrobić sztuczny marmur, będziesz potrzebować:
- drobny piasek;
- gatunek cementu 500;
- plastyfikator S-3 (poprawia właściwości techniczne betonu);
- pigment - nieorganiczny barwnik, który nie rozpuszcza się w wodzie, na przykład farba olejna;
- wypełniacz - piasek kwarcowy, wióry marmurowe, dolomit, wapień lub kamyki;
- folia polietylenowa;
- woda.
Aby pracować, musisz przygotować się z wyprzedzeniem:
- pojemnik do przygotowania roztworu;
- mieszarka budowlana z przystawką lub wiertarka udarowa z przystawką mieszającą;
- forma polimerowa - można ją kupić lub wykonać samodzielnie z poliuretanu, gipsu lub tworzywa sztucznego. Można je zastąpić ramą drewnianą ze szkłem umieszczonym u dołu;
Przy wyborze formy ważne jest, aby jej powierzchnia była równa i gładka, a także aby była wyjmowana. W takim przypadku możesz łatwo uzyskać gotowy produkt.
- stół wibracyjny - jest niezbędny przy produkcji sztucznego marmuru w dużych ilościach. Niezależnie od rodzaju wibracji - poziomej czy pionowej, pomaga usunąć pęcherzyki powietrza z roztworu i go zagęścić. W przypadku braku takiego projektu możesz po prostu energicznie potrząsać formą;
- szczotki do smarowania formy;
- rozpylacz żelkotu;
- szlifierka z diamentowymi miseczkami tarczowymi do obróbki gotowej płyty.
Technologia produkcji
Proces przygotowania roztworu do sztucznego marmuru jest prosty. Wymaga to jednak dokładności proporcji, przestrzegania pewnych zasad i obecności minimalnych umiejętności. Lepiej zacząć od stworzenia prostych konstrukcji, stopniowo komplikując zadanie.
Przygotowanie roztworu
Aby przygotować rozwiązanie, potrzebujesz:
- Do czystego, suchego pojemnika wsyp cement i piasek rzeczny w stosunku 1:2. Po dokładnym wymieszaniu tych materiałów do powstałej mieszaniny wrzuca się kawałki marmuru lub kamyki. Jego ilość ustalana jest indywidualnie i wpływa na wielkość frakcji gotowego produktu.
- Po dodaniu wypełniacza do mieszaniny dodaje się barwnik. Jego ilość nie powinna przekraczać 1% całkowitej masy mieszanki.
Na tym etapie ważne jest dokładne wymieszanie kompozycji, aby zachować nierównomierne zabarwienie. Pozwoli to w jak największym stopniu odtworzyć wzór kamienia naturalnego.
- Następnie należy dobrze wstrząsnąć powstałą mieszaninę kilka razy lub umieścić ją na stole wibracyjnym w celu usunięcia powietrza.
- Następnie możesz wlać wodę. Powinno wynosić 0,2 części, ale należy to zrobić w 2 krokach. Za pierwszym razem dodaje się 80% całkowitej objętości, a po dodaniu plastyfikatora (1% wag. cementu) i dokładnym wymieszaniu mieszaniny pozostałe 20%. Po kolejnym mieszaniu i energicznym wstrząśnięciu roztwór jest gotowy.
Przygotowanie i wypełnienie formularza
Powstałą masę można wlać jedynie do suchych i czystych form ustawionych ściśle poziomo. Są one wstępnie pokryte materiałem antyadhezyjnym i żelkotem, a następnie pozostawione do stwardnienia. Idealnie równe płyty uzyskuje się, jeśli roztwór wlewa się małymi porcjami, upewniając się, że równomiernie wypełnia pojemnik. Okresowo formy należy energicznie potrząsać lub ustawiać na stole wibracyjnym w celu usunięcia powietrza.
Możesz zwiększyć wytrzymałość gotowych płyt marmurowych za pomocą zbrojenia. Aby to zrobić, wystarczy włożyć w masę mocny, pomalowany drut.
Wypełniona forma roztworem
Po usunięciu nadmiaru roztworu i wypoziomowaniu formę przykrywa się folią i pozostawia w miejscu chronionym przed opadami atmosferycznymi do stwardnienia na co najmniej jeden dzień. W niektórych przypadkach proces ten może zająć kilka dni. Nie ma sensu dodatkowo nawilżać powierzchni betonu i w jakikolwiek sposób w nią ingerować.
Grube płyty ze sztucznego marmuru mogą później pęknąć z powodu obecności wewnętrznych pustek. Można temu zapobiec stosując stół wibracyjny lub specjalną technikę przygotowania roztworu. Zgodnie z nią nie należy odłączać miksera od masy w trakcie jej miksowania. W ten sposób można uniknąć pojawienia się pęcherzyków powietrza.
Zakończono obróbkę płyty
Po stwardnieniu produkt odwraca się i wyjmuje z formy, usuwając go niczym pokrywkę. Następnie zaleca się pozostawienie go na chwilę na świeżym powietrzu i rozpoczęcie szlifowania. Można to zrobić za pomocą szlifierki.
Ze względu na dużą wytrzymałość gotowych produktów, można je później ciąć wyłącznie tarczami diamentowymi.
Wideo: sztuczny marmur DIY
Wykonanie wyrobów ze sztucznego marmuru własnymi rękami w domu nie stanowi problemu. Potwierdza to po raz kolejny autor tego filmu, pokazując wszystkie etapy głównej pracy:
Technologia wytwarzania marmuru z gipsu
Technologia wytwarzania sztucznego marmuru z gipsu jest prosta i dostępna
Technologia ta jest popularna i składa się z kilku etapów:
- Przygotowanie roztworu roboczego. W tym celu do pojemnika wsypujemy suchy tynk, do którego dodajemy wodę, klej do drewna i żywicę roztopioną wcześniej w gorącej kąpieli. Po dokładnym wymieszaniu do masy wsypuje się pigmenty lub barwniki akrylowe i ponownie miesza aż do powstania żyłek.
Biały sztuczny marmur można otrzymać dodając do roztworu mieszaninę 200 g białego humilaksu, 50 g suchego gipsu i 1 litr alkoholu przemysłowego. Brązowy powstaje przez zmieszanie pomarańczowego humilaksu, a czarny powstaje przez barwnik anilinowy.
- Wkładanie gotowej masy do formy. Nadmiar wody można łatwo usunąć za pomocą suchego tynku, który posypuje się na wierzchu. Proces utwardzania gotowego produktu może zająć 8-10 godzin, po czym można go usunąć.
- Aby utworzyć wodoodporną warstwę na wierzchu marmuru gipsowego, jego przednia powierzchnia jest traktowana krzemianem potasu i polerowana miękkim filcem.
Jak zrobić marmur z żywic poliestrowych
Sztuczny marmur wykonany z żywic poliestrowych jest niezwykle trwały
W ten sposób można uzyskać marmur lany o unikalnej fakturze, który ponadto będzie niezwykle odporny na uszkodzenia mechaniczne i chemiczne. Aby to zrobić, należy przygotować polimerobeton z żywicy poliestrowej i wypełniacza, mieszając je w stosunku 25:75. Ten ostatni byłby piaskiem kwarcowym lub innym minerałem rozdrobnionym na okruchy.
Żywicę poliestrową można zastąpić mieszaniną butakrylu i AST-T (akrylanu technicznego), pobranych w równych ilościach. Dodaje się do nich taką samą ilość piasku kwarcowego lub kruszonego kamienia i pigmentów na bazie akrylu.
Powstałą kompozycję układa się w formie, gdzie pozostawia się ją do całkowitego stwardnienia. Możesz zwiększyć jego wytrzymałość za pomocą płyt wiórowych. Jego wymiary powinny być o 5 cm mniejsze od wymiarów formy. Wciśnięcie w masę powoduje później poprawę parametrów technicznych gotowego produktu. Po stwardnieniu i stwardnieniu ten ostatni jest wyjmowany z formy i szlifowany.
Pomimo wysokiej wytrzymałości i doskonałych właściwości technicznych sztucznego marmuru, nadal wymaga on pewnej pielęgnacji.
Możesz zapewnić opiekę, przestrzegając prostych zasad:
- Nie stosować środków czyszczących zawierających olej suszący;
- Niepożądane jest stosowanie detergentów z silikonem;
- Do usunięcia brudu lepiej jest użyć miękkiej szmatki;
- Niepożądane jest używanie pędzli, gąbek i innych urządzeń, które mogą zarysować warstwę wykończeniową;
- Lepiej zastąpić ścierne środki czyszczące do pielęgnacji blatów żelowymi;
- Regularne czyszczenie wyrobów ze sztucznego marmuru najlepiej przeprowadzać za pomocą detergentu lub mydła;
- Błyszczący połysk powierzchni można zachować przecierając je specjalnymi roztworami (1 nakrętka mydła w płynie z naturalnych składników na 3 litry wody) i pocierając suchym ręcznikiem.
Alternatywą dla płytek ceramicznych może być własnoręcznie wykonany sztuczny marmur. Można nim ozdobić kuchnie i ozdobić kominki. Może służyć jako wykładzina podłogowa, demonstrując gościom dobry gust i niezwykłe zdolności.
Betonowy marmur to uniwersalny materiał, który można dość łatwo wykonać własnymi rękami. Po co robić taką imitację prawdziwego marmuru? Marmur był używany od dawna, przez wiele stuleci, do ozdabiania pomieszczeń lub całych budynków. Jest niesamowicie piękny i wygląda bardzo szlachetnie. Jego cenę uzasadnia fakt, że jest to minerał dość trudny do zdobycia (dlatego jest dość drogi). Złoża zlokalizowane są w rzadkich miejscach o ograniczonej dostępności. Poza tym cały proces wydobycia, obróbki materiału, dostawy tylko podnosi cenę, bo są dość skomplikowane.
Gdzie jest używany?
Marmur betonowy wykorzystuje się do tych samych celów co zwykły marmur – do wykańczania elewacji budynków, wnętrz, powierzchni mebli, jako płytki, inne wykładziny podłogowe, zlewozmywaki, kominki i wiele innych. Jeśli prawidłowo wykonasz marmur z betonu własnymi rękami, pozostaniesz na przewadze, ponieważ jest on tańszy pod względem ceny i w niczym nie ustępuje oryginałowi.
Zalety
Materiał ten ma wiele zalet. Po pierwsze, sztuczny marmur jest przyjazny dla środowiska, podobnie jak naturalny marmur. Dla wielu ważny jest fakt, że jego cena znacznie i kilkukrotnie odbiega od ceny kamienia naturalnego. Ogromna zaleta: produkcja jest praktycznie bezodpadowa, a to jest ważne dla natury. Ponadto materiał ten dobrze zatrzymuje ciepło i nie przepuszcza wilgoci. A dla kreatywnych osób jest po prostu niezastąpiony – mogą wybrać dowolny kolor, kształt i z łatwością wykonać marmur w domu.
Materiały i narzędzia
Aby zrobić marmur, będziesz potrzebować specjalnych materiałów i narzędzi. Przygotuj wodę, folię, drobny piasek i farbę olejną w kolorze, jaki chcesz nadać betonowi. Jako wypełniacz będziesz musiał wybrać małe kamyki lub żwir. Nie zapomnij także o cemencie (wymagany oznaczony M400/M500) i dowolnym pojemniku lub wiertle (ważne, aby mieć przystawkę do mieszania) do mieszania. Będziesz także potrzebować formularzy, które zostaną wypełnione sztucznym marmurem. Można je kupić w sklepie lub wykonać samodzielnie, jeśli wybierzesz nietypową konfigurację. W zasadzie komponenty te nie są trudne do zdobycia - można je kupić w każdym sklepie budowlanym.
Jeśli technologia zostanie wykonana prawidłowo, powstały materiał nie będzie w niczym gorszy od prawdziwego marmuru. Na pierwszy rzut oka trudno będzie określić, jak urządzono wnętrze.
Rodzaje mieszanek betonowych do produkcji
Mieszanka betonowa jest kompozycją wody, spoiwa i kruszywa. Wszystkie składniki miesza się w specjalnym urządzeniu - betoniarce. W wyniku specjalnej technologii wymieszania wszystkich niezbędnych składników otrzymujemy sztucznie wytworzony materiał – beton.
Biorąc pod uwagę różne kryteria, można wyróżnić różne. Na przykład dla następujących typów:
- ciężki (gatunki M100-M600);
- bardzo ciężki (gatunki M100-M200);
- lekkie (gatunki M35-M400);
- bardzo lekkie (gatunki M25-M200).
Do przygotowania marmuru używamy oznaczeń M400 lub M500. Dzieje się tak dlatego, że beton marmurowy musi być tak samo trwały jak prawdziwy beton. Gęstość użytej mieszanki betonowej powinna wynosić od 1800 do 2500 kilogramów na metr kwadratowy, w zależności od wybranego oznaczenia.
Technologia produkcji
Ostatnio pojawiło się wiele różnych technik wytwarzania marmuru betonowego. Często można je spotkać pod nazwami „sztuczny marmur”, „systrom”, „beton dekoracyjny/kolorowy” i innymi. Ale to tylko różne odmiany nazw, które łączy jedna technologia.
Łączy w sobie wszystkie zalety techniki formowania półsuchego, łącząc ją z tzw. techniką odlewania wibracyjnego. Pozwala to na wykonanie własnymi rękami materiału identycznego z prawdziwym marmurem, przy użyciu zwykłych komponentów wymienionych powyżej i dość standardowego wyposażenia (takiego jak betoniarka).
- to ten sam zwykły beton, tyle że z dodatkiem białych odcieni cementu, co nadaje mu szlachetny wygląd. Czasami do produkcji stosuje się specjalne wypełniacze, na przykład wióry marmurowe, które mogą mieć zupełnie inne odcienie i kolory. Technika ta z dodatkiem wiórów marmurowych powinna łączyć w sobie późniejszą obróbkę. Powstałą powierzchnię należy wypolerować, aby uzyskać efekt prawdziwego marmuru. Również po wypolerowaniu struktura kruszywa będzie się pięknie prezentować.
Przygotowanie mieszanki
Po znalezieniu wszystkich niezbędnych narzędzi i komponentów możesz bezpiecznie rozpocząć przygotowywanie mieszanki do produkcji płyt ze sztucznego marmuru. Przede wszystkim przygotuj czyste naczynie do tego procesu. Rozwiązanie ma zwykłe proporcje, czyli części 1:3. Weź suchy cement żądanego gatunku, a następnie dodaj do niego drobny piasek. Nie zapomnij najpierw przesiać piasek, aby pozbyć się wszelkich niepotrzebnych zanieczyszczeń, które mogą się w nim znajdować. Do tego będziesz potrzebować drobnej siatki, ponieważ piasek jest drobny. Wszystko to należy zrobić, aby osiągnąć jednolitość rozwiązania.
Po dokładnym wymieszaniu dodać wypełniacz. Jak wspomniano wcześniej, jako wypełniacza możesz użyć małych kamyków. W ten sposób uzyskuje się gotowe rozwiązanie.
Następnie, kierując się technologią, warto dodać pigment barwiący, aby nadać sztucznemu marmurowi kolor. Osobliwością jest to, że rozwiązanie nie wymaga dokładnego wymieszania: tworzy to efekt niejednorodności, który staramy się nadać roztworowi, aby uzyskać większe zewnętrzne podobieństwo do skały. Aby uzyskać niezwykły efekt, możesz dodać farby o różnych odcieniach. Tutaj możesz całkowicie poddać się swojej wyobraźni i śmiało eksperymentować. W rezultacie pojawiają się różne zagięcia, plamy i plamy o oryginalnych kształtach. Ale nie powinieneś też być zbyt gorliwy: ilość pigmentu w roztworze nie powinna przekraczać jednego lub dwóch procent suchej masy. Warto też pamiętać: barwnik lepiej wprowadzać porcjami w różne części wypełnianego formularza.
Po dodaniu barwnika do roztworu należy go wstrząśnąć, ale nie należy go dokładnie mieszać. Niektórzy budowniczowie używają stołu wibracyjnego do takiego wstrząsania. Ale jeśli nie masz tego urządzenia, możesz po prostu potrząsnąć miksturą rękami. To nie będzie trudne.
Marmur zaczęto wykorzystywać do wykańczania pomieszczeń i ścian zewnętrznych budynków już w starożytności. Ale nie jest to materiał dostępny dla wszystkich. Cena naturalnego marmuru zaczyna się od 20 tysięcy rubli za metr kwadratowy. Bardziej ekonomicznym zamiennikiem jest sztuczny marmur - wykonany z betonu i innych materiałów. Kamień sztuczny jest 4 razy tańszy niż kamień naturalny, jeśli kupuje się go w sklepach. Ale przy pewnych umiejętnościach możesz to zrobić sam.
Charakterystyka sztucznego kamienia
Sztucznym kamieniem nazywa się nie tylko marmur wykonany z betonu, ale także granit ceramiczny. Technologia produkcji tych materiałów jest prawie identyczna. Ale wykorzystuje się je na różne sposoby.
Granit ceramiczny uważany jest za twardszy i bardziej odporny na uszkodzenia mechaniczne, dlatego częściej niż marmur wykorzystuje się go na powłoki w obszarach o dużym natężeniu ruchu pieszego: posadzki w centrach handlowych, supermarketach, metrze, węzłach komunikacyjnych. W pomieszczeniach mieszkalnych płytki porcelanowe stosuje się do pokrywania ścian i podłóg korytarzy, kuchni i łazienek.
Marmur jest mniej trwały, ale dzięki zastosowanym barwnikom ma piękny wzór. Jej zakres zastosowania to blaty i lady barowe, balustrady ogrodzeń i schodów, elementy dekoracyjne, elementy instalacji wodno-kanalizacyjnej, parapety i sztuczne kolumny.
Niestandardowy marmur betonowy może mieć niemal dowolny kształt, kolor i wzór. Parametry te zależą wyłącznie od wyobraźni i wypłacalności kupującego.
Naturalny marmur jest pod wieloma względami gorszy od swojego sztucznego odpowiednika. Blat wykonany z naturalnego materiału będzie ważył 3-4 razy więcej niż blat o podobnym kształcie i rozmiarze - wykonany z materiału syntetycznego.
Paleta kolorów kamienia naturalnego jest ograniczona, natomiast sztuczny marmur można pomalować na dowolny odcień, a nawet nadać mu blask.
Techniki wytwarzania
Na skalę przemysłową stosuje się kilka technologii produkcji marmuru. Skład mieszanin zależy od wybranej metody. Do najpopularniejszych należą metody odlewnicze i gipsowe oraz produkcja marmuru z betonu. Technologie produkcji sztucznego marmuru w obu przypadkach mają ze sobą wiele wspólnego.
Metoda odlewania
Marmur metodą odlewniczą wytwarzany jest z piasku kwarcowego lub odpadów z produkcji kamienia naturalnego – wiórów marmurowych. Żywice poliestrowe zapewniają integralność mieszanki, a za pomocą pigmentu produktowi można nadać dowolny odcień. Odlany marmur ma następujące cechy:

Oprócz głównych składników mieszanki, do produkcji marmuru lanego wykorzystuje się szereg narzędzi, preparatów i specjalistycznego sprzętu. Obejmują one:
- formy do napełniania;
- kompozycja antyadhezyjna do obróbki form;
- stół wibracyjny;
- sprzęt do polerowania gotowych konstrukcji marmurowych;
- powłoka żelowa
Do obróbki form po usunięciu stwardniałego kamienia stosuje się mieszanki antyadhezyjne.
W skład takich preparatów wchodzi parafina lub silikon rozpuszczony w nafcie, benzynie lakowej lub benzynie.
Konieczne jest wybranie kompozycji w oparciu o pożądany wygląd kamienia.
Aby uzyskać matową powierzchnię, odpowiednia jest mieszanka silikonowa, a woskowa kompozycja antyadhezyjna nadaje produktowi końcowemu połysk, powierzchnia staje się lekko tłusta.
Procedura wytwarzania lanego marmuru jest następująca:

Żelkot to żywica polimerowa, której za pomocą barwników nadawany jest pożądany odcień. On spełnia kilka funkcji: chroni powierzchnię przed uszkodzeniami, „zamyka” pory produktu i barwi go. Żelkot nakłada się pędzlem lub natryskiem w kilku warstwach. Po wyschnięciu lakieru nawierzchniowego (w przypadku żelkotu jest to około 2-3 godziny) produkt jest gotowy do użycia.
Marmur gipsowy
Alternatywą dla kamienia wykonanego z naturalnych wiórów jest marmur gipsowy. Produkcja według tego przepisu jest znacznie tańsza. Mieszanka bazowa zawiera następujące komponenty:

Najpierw miesza się tynk, klej i wodę, następnie dodaje się żywicę i wszystko miesza się za pomocą miksera. Następnie są dodane składniki do barwienia:
- kolor czarny uzyskuje się za pomocą barwnika anilinowego;
- kawowy odcień można uzyskać dodając pomarańczowy humilax (200 g) i 1 litr alkoholu przemysłowego na 50 kg gipsu;
- W przypadku śnieżnobiałego marmuru stosuje się biały humilax.
Mieszaninę wylewa się do formy i suszy przez 10 godzin w temperaturze pokojowej. Po całkowitym stwardnieniu sztuczny marmur „gipsowy” jest usuwany, traktowany krzemianem potasu, suszony i polerowany filcem.
Marmur gipsowy to najlżejszy rodzaj sztucznego kamienia, ale także jeden z najbardziej kruchych. Na jego podstawie zwykle wykonuje się elementy dekoracyjne, które nie podlegają znacznym obciążeniom.
Na bazie betonu
Aby wyprodukować pojedynczy produkt, nie jest konieczne kontaktowanie się z zewnętrznymi producentami. Jeśli istnieje wiele łatwo dostępnych składników, każdy może stworzyć sztuczny kamień. Możesz zrobić marmur z betonu własnymi rękami. Oprócz cementu marmur zawiera piasek, plastyfikator i wodę. To znacznie zmniejsza koszt sztucznego kamienia w porównaniu z metodą odlewania. Istnieją również pewne wymagania dotyczące tak prostych komponentów.
Do produkcji marmuru z betonu używają następujące materiały i sprzęt:

Produkcja rozpoczyna się od dokładnego przesiania piasku. Pomoże to pozbyć się nadmiaru zanieczyszczeń. Pierwszym, który miesza podstawowe składniki, jest cement i piasek. Proporcje tych składników w kompozycji mogą się różnić w zależności od zakresu zastosowania produktu końcowego.
- W przypadku części, które w przyszłości będą narażone na duże uszkodzenia mechaniczne - krawężniki, okładziny zewnętrzne, płyty chodnikowe - należy wymieszać cement z piaskiem w proporcji 1:3.
- Jeśli planujesz wykonanie blatu, sufitu, elementu schodów lub parapetu ze sztucznego marmuru, to proporcje powinny wynosić 1:2.
- Do elementów dekoracyjnych cement i piasek miesza się w stosunku 1:1.
Następnie mieszaninę rozcieńcza się wodą. Objętość wody oblicza się na podstawie objętości suchej mieszanki: zalecana proporcja to 1 część wody na 2 części mieszanki. Najpierw dodaj około trzech czwartych wody i wymieszaj. Następnie do mieszaniny dodaje się plastyfikator w ilości 1-2% wagowych cementu i miesza.
Dla najlepszego rozprowadzenia plastyfikatora mieszaninę pozostawia się na 10-15 minut, po czym wlewa się pozostałą wodę i ponownie miesza.
Ostatnim składnikiem jest barwnik. Aby uzyskać pożądany odcień, można dodać jeden lub więcej pigmentów. Zwykle zaleca się stosowanie pigmentu w ilości 1% masy cementu (a nie całej mieszanki), jednak skuteczność barwników jest różna, więc ten stosunek może nie dać pożądanego rezultatu. Najpopularniejsze barwniki i ich Zalecane dawki są następujące:
- tlenek tytanu nadaje mieszance biały kolor (lub białe smugi i smugi), zalecane dawkowanie wynosi od 2 do 4%;
- minium - pigment czerwono-pomarańczowy - 5%;
- tlenek chromu barwi kompozycję na zielono i jest dodawany w ilości 3-5% masy cementu;
- Zalecana ilość ochry wynosi 5%, w efekcie marmur jest malowany w odcieniach od jasnożółtego do brązowego.
Produkowane są także specjalne pigmenty do betonu. Ustalając ich dawkowanie, należy postępować zgodnie z instrukcjami producenta.
Po dodaniu barwnika nie należy dokładnie mieszać kompozycji, ponieważ marmur ma nierównomierny rozkład kolorów.
Gotową mieszaninę wlewa się partiami do formy potraktowanej środkami antyadhezyjnymi, zwracając szczególną uwagę na wgłębienia. Jeśli planowany produkt ma duże rozmiary, część kompozycji wlewa się do formy, układa się siatkę lub drut, a dopiero potem dodaje resztę płynnej bazy. Zazwyczaj blaty i masywne płyty, obramowania i wolumetryczne elementy dekoracyjne wymagają wzmocnienia. Po wylaniu formę przykrywa się folią i pozostawia do całkowitego stwardnienia.
Sztuczny marmur twardnieje przez długi czas; zajmie to co najmniej 7-12 dni. Gotowy kamień wyjmuje się z formy, w razie potrzeby poleruje i pokrywa końcową warstwą ochronną z żywicy (żelkot).
Niuanse działania
Przy odpowiedniej obróbce wykończeniowej sztucznego marmuru dowolnego pochodzenia, produkty z niego wykonane będą służyć latami. Jednym ze sposobów na zwiększenie trwałości kamienia jest malowanie powierzchniowe i pokrywanie lakierem wodno-akrylowym.
Dotyczy to szczególnie kamienia stosowanego w dekoracji zewnętrznej, ponieważ światło słoneczne nie wpływa na lakier wodno-akrylowy.
Dzięki temu marmurowy element dekoracyjny nie zmieni koloru i nie pokryje się nieprzyjemnymi żółtymi plamami przez 10-15 lat.
Podczas montażu produktu należy unikać nadmiernego dokręcania elementów złącznych. Płyta marmurowa zainstalowana skośnie lub z silnym naciskiem na narożniki może nie wytrzymać obciążenia i pęknąć. W obliczu pomieszczeń o dużej wilgotności należy monitorować stan instalacji wodno-kanalizacyjnej, aby zapobiec wyciekom i wykopaniu kamienia.
Spadające ciężkie przedmioty o ostrych narożnikach mogą uszkodzić marmur. Nie kroj jedzenia bezpośrednio na blacie; używaj desek do krojenia.
Powierzchnię należy czyścić wyłącznie przy użyciu płynnych środków czyszczących. Kompozycje zawierające materiały ścierne niszczą powłokę ochronną sztucznego kamienia, powodując mikrorysy, w których gromadzą się resztki jedzenia, kurz i inne zanieczyszczenia. Należy porzucić twarde szczotki i metalowe siatki, preferując miękkie tkaniny.
A wnętrzu lokalu można nadać przyzwoity wygląd, używając marmuru do dekoracji. Uważa się, że właściciel mieszkania lub firmy, która stosuje tę technikę, ma dobry gust i wysoki status. Ale kamień naturalny jest dość drogi, a jego sztuczny odpowiednik można wykonać z betonu. Aby to zrobić, będziesz musiał użyć najprostszych składników, w tym wody, cementu i piasku.
Przygotowanie
Zanim zrobisz marmur z betonu, musisz się przygotować. Aby to zrobić, upewnij się, że masz:
- pigment;
- cement;
- piasek;
- plastyfikator.
Ta ostatnia jest substancją poprawiającą właściwości materiału. Do zrobienia marmuru potrzebne będą formy. Do tego można użyć tych wykonanych na bazie polimerów. Jeśli nie możesz ich znaleźć, możesz skorzystać z plastikowych formularzy. Ale do rozwiązania potrzebny będzie cement klasy M 500. Wybierając pigment, możesz preferować farbę olejną. Prezentowany jest w wielu odcieniach.
Rodzaje betonu do marmuru
Produkcja sztucznego marmuru z betonu może wiązać się z zastosowaniem różnego rodzaju mieszanek. Ten ostatni jest kompozycją kruszywa, spoiwa i wody. Mieszanie składników można również wykonać w betoniarce, jeśli ilość pracy jest imponująca. Biorąc pod uwagę różne kryteria, możliwe jest sklasyfikowanie mieszanki betonowej do marmuru według gęstości.
Można uzyskać materiał ciężki, bardzo ciężki, lekki i bardzo lekki. W pierwszym przypadku mówimy o gatunkach z zakresu M 100-M 600. Beton lekki będzie odpowiadał następującym klasom: M 35-M 400; bardzo ciężki i bardzo lekki beton do marmuru odpowiada gatunkom M 100-M 200 i M 25-M 200. Aby przygotować wyrób o dużej wytrzymałości, lepiej jest preferować betony klas M 400 lub M 500. Gęstość Mieszanka betonowa będzie się wahać od 1800 do 2500 kg/m2.
Materiały i narzędzia
Jeśli zdecydujesz się na samodzielne wykonanie marmuru, powinieneś zaopatrzyć się w specjalne narzędzia i materiały. Do tego będziesz potrzebować:
- folia polietylenowa;
- woda;
- Farba olejna;
- drobny piasek.
Przygotowując farbę musisz wziąć pod uwagę odcień materiału, z którego wyjdziesz. Wypełniaczem może być żwir lub małe kamyczki. Jako cement czasami stosuje się materiał klasy M 400. Do mieszania należy przygotować pojemnik i wiertło. Ten ostatni powinien mieć przystawkę do miksowania.
Skład i właściwości preparatu marmurowego
Jeśli zdecydujesz się na marmur z betonu, najlepiej zaopatrzyć się w stół wibracyjny, który możesz wypożyczyć. Do rozwiązania potrzebne będą dwie części piasku i część cementu. Składniki miesza się do uzyskania gładkiej masy, po czym dodaje się pigment. Może pozostawiać plamy charakterystyczne dla marmuru.
Możesz eksperymentować, dodając farby o różnych odcieniach. Po wypełnieniu forma jest potrząsana, a jeśli jest stół wibracyjny, to jest na niej umieszczana. Nawiasem mówiąc, możesz sam wykonać stół wibracyjny. Może być również przydatny do wykonywania płyt chodnikowych. Ostatni etap wytwarzania marmuru z betonu jest najbardziej pracochłonny.
Polega na szlifowaniu. Po wyschnięciu form produkty należy poddać obróbce. Powoduje to powstawanie dość dużej ilości kurzu, dlatego należy wcześniej zaopatrzyć się w kilka wiader wody. Alternatywnym rozwiązaniem jest podłączenie węża o dobrym ciśnieniu wody.
Wymagania technologiczne
Betonowy marmur nie może okazać się gorszy niż kamień naturalny. Należy jednak przestrzegać technologii. Nawet parapety mogą być wykonane z marmuru, ale w tym celu trzeba znaleźć plastikowe tace. Formularze możesz wypełnić samodzielnie. Aby to zrobić, plastikowe panele są ze sobą łączone. W tej samej technologii można również wytwarzać polimerobeton, jednak zamiast cementu w tym przypadku zastosowane zostaną spoiwa w postaci żywic termoaktywnych. Pomiędzy nimi:
- furan;
- fenolowy;
- epoksyd.
Przy wytwarzaniu polimerobetonów do składników dodaje się więcej wypełniacza niż przy wytwarzaniu konwencjonalnej zaprawy betonowej.
Technologia betonu i marmuru może wyglądać nieco inaczej. Jako proporcję możesz zastosować standardowy stosunek od jednego do trzech. Wypełniaczem w tym przypadku będzie węglan wapnia lub inne neutralne wypełniacze. Jeśli zdecydujesz się przygotować polimerobeton, rozwiązanie łączy się w proporcjach od jednego do czterech. Wypełniaczami będą materiały gruboziarniste. Do tych celów można użyć pokruszonego żwiru lub grubego piasku. Materiały do tego to:
- kwarc;
- wapień;
- piaskowiec;
- dolomit.
Przy wykonywaniu sztucznego marmuru z betonu nie wystarczy prawidłowo przygotować zaprawę. Ważne jest, aby śledzić kolejne etapy technologii. Na przykład po wlaniu mieszaniny do foremek powierzchnia jest pokryta folią z tworzywa sztucznego. W celu uzyskania większej wytrzymałości materiału wzmacnia się go drutem.
Gdy tylko mieszanina zostanie wlana do form, w środku należy umieścić klatkę wzmacniającą. Po stwardnieniu mieszaniny produkty wyjmuje się z formy i szlifuje. Aby to zrobić, możesz użyć tarcz diamentowych w postaci miseczek lub młynka. Po wykonaniu tej operacji powierzchnia powinna być gładka, przypominająca w ten sposób naturalny marmur.
Na przykład
Jeśli zdecydujesz się na wykonanie betonowego marmuru własnymi rękami, musisz pamiętać, że produkty są dość trwałe i można je obrabiać tylko za pomocą narzędzia diamentowego. Skuteczną metodą jest cięcie żelbetu tarczami diamentowymi i wiercenie otworów w betonie za pomocą diamentu.
Więcej o technologii
Jeśli przeczytasz artykuł, znasz skład betonowego marmuru. Ważne jest również zainteresowanie cechami technologii. W procesie takiej produkcji można uzyskać sztuczny marmur, zwany także betonem kolorowym lub dekoracyjnym, a także systrum. Są to jednak tylko różne odmiany nazw, które łączy w jedną technologię.
Pochłonął wszystkie zalety techniki formowania półsuchego i techniki odlewania wibracyjnego. Pozwala to na wykonanie materiału, który będzie identyczny z naturalnym marmurem. Komponenty są najtańsze i najprostsze. Ogólnie rzecz biorąc, beton dekoracyjny jest zwyczajny, ale dodaje się do niego białe odcienie cementu, co nadaje produktom szlachetny wygląd.
Czasami produkcja marmuru z betonu wiąże się z użyciem specjalnych wypełniaczy, w tym zrębków marmurowych. Może mieć różnorodne odcienie i kolory. Podejście to łączy się z późniejszym przetwarzaniem. Powierzchnię należy wypolerować, aby uzyskać efekt prawdziwego marmuru. Dodatkowo końcowy etap pozwala na atrakcyjne ukazanie struktury kruszywa.
Jak i w jakiej objętości dodać wodę?
Po połączeniu suchych składników można je dodać do wody. Połącz go ze składnikami w proporcji jeden do dwóch. Najpierw wlej 80% płynu i wszystko dobrze wymieszaj. Następnie dodaje się plastyfikator, który zwiększa wytrzymałość produktu.
Składnik ten będzie stanowił 1% całkowitej masy. Następnie mieszaninę dobrze miesza się i pozostawia na 10 minut. W tym czasie kompozycja staje się plastyczna i lepka. Dopiero potem możesz wlać pozostałą wodę.
Wreszcie
Aby uzyskać efekt naturalnego marmuru, utwardzony produkt należy przeszlifować i wypolerować przy użyciu odpowiednich narzędzi. Powierzchnia jest gładka i przyjemna w dotyku. Poza tym jest bardzo piękna. Teraz pozostaje tylko zainstalować marmur na swoim miejscu. Jednak wcześniej powierzchnia jest przygotowywana: jest czyszczona i wolna od ciał obcych. Jest to poprawne, jeśli materiał jest przyklejony do szorstkiej podstawy. W przypadku obecności kurzu przyczepność może zostać zmniejszona.
Na rynku budowlanym pojawiła się alternatywa dla cementu, która z punktu widzenia przyjazności dla środowiska produkcji nie jest bezpieczna dla atmosfery. Każdego roku na świecie produkuje się około 2 miliardów ton cementu, a każda tona uwalnia do atmosfery 0,4 tony dwutlenku węgla. Inżynierowie długo pracowali nad tym problemem, aż do wynalezienia płynnego granitu – nowego słowa w technologii wytwarzania materiałów wykończeniowych. Ma wiele zalet w porównaniu do innych materiałów wykończeniowych: ognioodporność, wszechstronność, jakość, bezpieczeństwo, wytrzymałość.
Definicja płynnego granitu
Płynny granit to sztuczny płynny kamień.
Jego zalety wynikają z faktu, że w przeciwieństwie do płynnego granitu zawiera oczyszczone wióry marmurowe (80%) i żywicę poliestrową (20%). Twardnieje po dodaniu przyspieszacza i utwardzacza. W procesie reakcji chemicznych uwalniają się wszystkie szkodliwe substancje, a gotowy produkt będzie przyjazny dla środowiska.
Płynny granit można stosować w każdym pomieszczeniu: mieszkaniach, biurach, szkołach, kuchniach letnich na wsi i tak dalej. Powierzchnie do natryskiwania to: drewno, kamień, metal, porcelana, włókno szklane, ceramika, płyta wiórowa i pilśniowa. Produkty z płynnego granitu przypominają produkty z kamienia naturalnego, ponieważ zawiera on wióry marmuru i nie trzeba już używać dużych kawałków kamienia. Paletę kolorystyczną materiału urozmaicają setki barwnych barwników, dzięki którym płynny granit wpasuje się w każde pomieszczenie.
Osobliwości
- Kolor gleby nie wpływa na kolor płynnego kamienia;
- Przyjemny w dotyku;
- Materiał jest nietoksyczny, bezwonny;
- Odporność na wilgoć uzyskuje się poprzez dodanie utwardzacza;
- Z biegiem czasu nie traci swojego wyglądu, jest trwały - żywotność produktów przekracza 25 lat;
- Łatwo jest usunąć brud z powierzchni;
- Przy zmianie temperatury produkt wykonany z płynnego kamienia nie traci swojego kształtu i właściwości.
Komponenty do płynnego kamienia:
- Plastelina;
- Włókno szklane;
- Żywica chemiczna;
- Podsadzkarz;
- Utwardzacz;
- Aceton;
- Zapalenie kalcyny;
- Powłoka żelowa;
- Klej topliwy;
- Płyta wiórowa, płyta pilśniowa.
Metody wytwarzania
- Metoda odlewania - gotową mieszaninę wlewa się do specjalnej formy aż do całkowitego wyschnięcia. Następnie gotowy produkt jest usuwany i przetwarzany.
- Metoda natryskowa – płynny kamień nanosi się na powierzchnię za pomocą opryskiwacza w kilkumilimetrowej warstwie.
Metoda natrysku bezpośredniego
Metoda natrysku bezpośredniego - na obrabiany przedmiot nakłada się specjalny podkład i pozostawia do wyschnięcia. Warstwę płynnego kamienia nakłada się za pomocą opryskiwacza. Po wyschnięciu przeprowadza się szlifowanie i polerowanie.
Metoda zapylenia wstecznego
Metodę odwrotnego zapylania stosuje się, jeśli przedmiot nie jest częścią mebla. Obrabiany przedmiot kładzie się na powierzchni formierskiej (płyta wiórowa, tafla szkła, stół) i kreśli wzdłuż jego konturu. Wzdłuż konturu montowana jest strona wykonana z płyty wiórowej lub tworzywa sztucznego. Nakładana jest warstwa środka antyadhezyjnego. Następnie na powierzchnię natryskuje się płynny kamień. Po częściowym stwardnieniu należy spryskać ziemię tak, aby warstwa kamienia nie prześwitowała. W ten sposób powstaje forma, do której wlewa się żywicę poliestrową. Produkt wyjmuje się z formy po całkowitym stwardnieniu.
Zobacz zdjęcia tapet w stylu prowansalskim do kuchni.
Technologia produkcji
Pomieszczenie, w którym produkowany jest płynny granit, musi składać się z dwóch pomieszczeń. Pierwsze pomieszczenie jest niezbędne do bezpośredniej produkcji, a drugie do polerowania powstałego produktu. Temperaturę w pomieszczeniach należy utrzymywać na poziomie 20-24 stopni. Musi być wentylacja.
Przygotowanie powierzchni rozpoczynamy od usunięcia z niej brudu i kurzu. Przed malowaniem powierzchnię przemywa się wodą i dokładnie suszy. Wszelkie uszkodzenia, zadrapania, pęknięcia należy naprawić.
Etapy produkcji:
- Przygotować mieszaninę mieszając przezroczysty żelkot (żywica polimerowa) z granulatem za pomocą wiertarki w stosunku 2:1. Utwardzacz dodaje się przed natryskiem.
- Powstałą mieszaninę nanosi się na produkt. Można go nakładać na dwa sposoby: natrysk bezpośredni i natrysk odwrócony.
- Powierzchnia gotowego produktu jest szlifowana i polerowana.
Poznaj główne elementy nietypowego projektu kuchni.
Obszar zastosowań
Producenci
- GRANITO-FARFALLA to firma zajmująca się produkcją blatów i parapetów z płynnego granitu. Jakość produktów zapewniają materiały i urządzenia renomowanych, światowych producentów. Firma stale dąży do udoskonalania technologii i poprawy parametrów technicznych.
- „GRANIT” to firma produkująca wypełniacz dekoracyjny GraniStone do produkcji płynnego kamienia oraz gotową płynną kompozycję AquaGranit, na bazie poliestrowej żywicy izoftalowej i akrylu.
- „Płynny Granit” to firma produkująca blaty, parapety ze sztucznego kamienia, panele ścienne i listwy drzwiowe z granitu.
Przeczytaj o stylu Fusion we wnętrzu kuchni.
Produkty wykonane z płynnego kamienia charakteryzują się pięknym, atrakcyjnym wyglądem oraz różnorodną kolorystyką i wzornictwem. Doskonale komponują się z dowolnymi materiałami wykończeniowymi. Jakość, bezpieczeństwo i trwałość uzupełniają listę zalet tego materiału.
Produkcja wyrobów z płynnego granitu: wideo
wnioski
Dbając o płynny granit, jak zawsze, należy odpowiedzialnie podejść do wyboru środków czyszczących, w przeciwnym razie szybko się on zużyje i odkształci. Kolejną wadą stosowania kamienia jest niski stopień przyczepności żywicy do powierzchni, przez co mogą pojawiać się pęcherze i łuszczenie się. Aby temu zapobiec, nie trzeba obrabiać powierzchni. Nieuzasadniona zawyżona cena kamienia jest niekorzystna dla kupujących. Producenci ją przeceniają, powołując się na czas produkcji, niebezpieczne warunki pracy i koszty pracy.