Frezowanie skrzynek. Technologia frezowania. Wymagania techniczne dotyczące części nadwozia
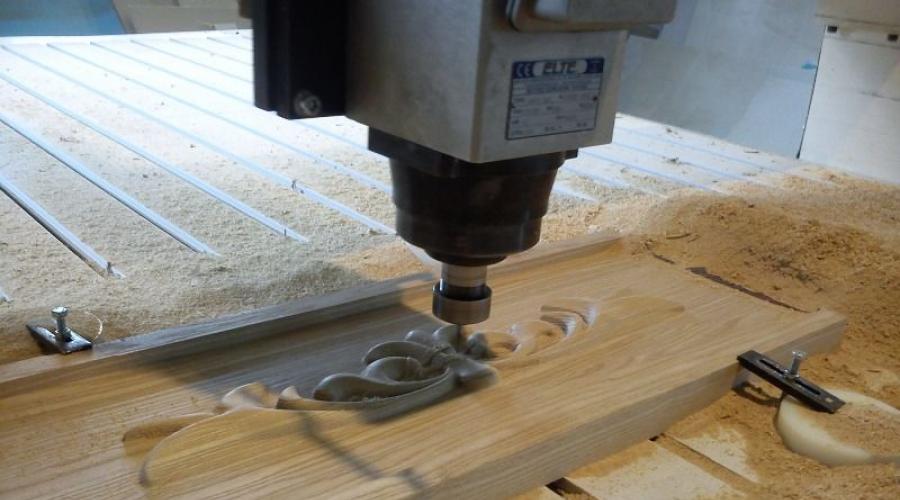
2. Technologia wytwarzania części karoserii
Półfabrykaty części karoserii odlewane są najczęściej z żeliwa i stopów aluminium, rzadziej ze stali lub innych stopów odlewniczych.
Szeroko stosowane jest odlewanie w formach piaskowo-glinianych, formach chłodzących, formach skorupowych i pod ciśnieniem. Rzadziej odlewy z utraconego wosku.
Odkuwki stosowane są jako półfabrykaty wstępne. Stosowany jest także do spawania elementów stalowych.
2.1. Wymagania techniczne dotyczące części nadwozia
Podczas produkcji części karoserii należy zapewnić:
1. Poprawna forma
2. Mała chropowatość (µm)
3. Dokładność względnego położenia głównych podstaw części.
Zatem dla płaszczyzn współpracujących tolerancja prostoliniowości wynosi 0,05...0,2 mm, chropowatość
2. Niska szorstkość
3. Prawidłowe położenie otworów względem głównych podstaw części, tj. dokładność współrzędnych osi otworów, równoległość i prostopadłość osi do płaszczyzn podstawowych itp.
4. Prawidłowe położenie otworów względem siebie (równoległość i prostopadłość osi, odległości międzyosiowe itp.). Na przykład tolerancje równoległości osi otworów i prostopadłości powierzchni końcowych do osi otworów zwykle wahają się odpowiednio od 0,02 do 0,05 mm na 100 mm długości lub promienia.
Wymagania dotyczące dokładności odległości między środkami są ustalane zgodnie z normami i warunkami zapewniającymi normalną pracę kół zębatych (zwykle 7-8 stopni dokładności).
Dokładność kształtu, wielkości i mała chropowatość otworów są niezbędne, aby zwiększyć odporność na zużycie uszczelnień i trwałość łożysk tocznych, zmniejszyć straty tarcia, wycieki cieczy i gazów.
2.2. Wstępne leczenie przypadków
Przed wysłaniem odlewów i odkuwek do warsztatu mechanicznego usuwa się nadlewkę, wlewki i wlewki. W tym celu wykorzystuje się prasy tnące, frezarki, szlifierki, przecinarki taśmowe i inne, zgrzewarki, młoty pneumatyczne, dłuta i inne środki produkcyjne. Ponadto przeprowadzane jest czyszczenie, obróbka cieplna, malowanie wstępne, gruntowanie i kontrola przedmiotu obrabianego.
Podczas czyszczenia usuwane są pozostałości przypalonego piasku formierskiego oraz drobne nierówności, aby poprawić wygląd części, zwiększyć trwałość nałożonej farby, a także zwiększyć trwałość narzędzia tnącego podczas późniejszej obróbki.
Czyszczenie odbywa się za pomocą szczotek stalowych, igłowych, trawienie kwasem siarkowym, a następnie mycie, piaskowanie śrutem, wodą z gruboziarnistą glinką i sodą.
Obróbka cieplna (wyżarzanie niskotemperaturowe odlewów z żeliwa szarego) ma na celu zmniejszenie naprężeń własnych i poprawę urabialności odlewów.
Malowanie odbywa się metodą pędzla, zanurzania, natrysku lub w specjalnych instalacjach. Zaawansowane fabryki korzystają z robotów malarskich CNC. Malowanie nieobrobionych powierzchni odlewów po starzeniu wiąże pozostałości masy formierskiej i uniemożliwia jej dalszy kontakt z powierzchniami trącymi.
2.3. Bazowanie wykrojów korpusu
Wybierając wersje robocze baz danych należy:
1. Zapewnić równomierne naddatki na obróbkę otworów
2. Unikaj dotykania wewnętrznych powierzchni obudowy oraz części o dużej średnicy (koła zębate, koła zamachowe, sprzęgła).
Aby to zrobić, w pierwszych operacjach elementy obrabiane są często oparte na głównym otworze lub dwóch ewentualnie bardziej odległych otworach, ponieważ wewnętrzna wnęka korpusu oraz otwory uzyskane w odlewie opierają się na wspólnym pręcie lub prętach połączonych ze sobą. Instalacja odbywa się:
1. W urządzeniach ze stożkami (ryc. 2.1.).
Za pomocą trzpieni krzywkowych lub tłokowych, które wraz z nim są zamocowane w otworach przedmiotu obrabianego, wystające szyjki są instalowane na pryzmatach i innych urządzeniach wsporczych.
Ryż. 2.1. – Schemat oparcia obudowy na trzpieniach stożkowych
Ryż. 2.2. – Schemat mocowania obudowy na trzpieniu rozporowym
Nasza firma świadczy usługi w zakresie frezowania aluminium i metali kolorowych na zamówienie o dowolnej złożoności. Specjalizujemy się w produkcji obudów do sprzętu elektronicznego, w tym szczelnych i wodoodpornych IP69 (do zdalnie sterowanych, niezamieszkanych pojazdów podwodnych).
Obudowy do sprzętu radioelektronicznego (REA) oraz przyrządów kontrolno-pomiarowych i automatyki (oprzyrządowanie i automatyka) znajdują szerokie zastosowanie we wszystkich gałęziach przemysłu i gospodarki narodowej. Wynika to z faktu, że urządzenia elektryczne i radioelektroniczne wymagają ochrony przed wpływami mechanicznymi, fizycznymi i chemicznymi do normalnego funkcjonowania. Warto również zaznaczyć, że aluminiowe obudowy na sprzęt i oprzyrządowanie elektroniczne są bardzo trwałe, dzięki czemu skutecznie chronią znajdujący się w nich sprzęt przed przypadkowym uszkodzeniem. Trwałość takich skrzynek jest również wysoka, ponieważ odpowiednio obrobione nie podlegają korozji atmosferycznej ani chemicznej. Pozwala to na zastosowanie obudów aluminiowych (stopów aluminium) w przemyśle. Produkcja obudów aluminiowych jest ważnym segmentem działalności naszej firmy. Absolutnie żadna nowoczesna produkcja nie może obejść się bez obudów do sprzętu elektronicznego czy oprzyrządowania i automatyki, wykonanych na bazie aluminium i innych metali nieżelaznych.
PRZYKŁADY NASZYCH PRAC FREZARSKICH
Frezowanie metali to technologia wytwarzania różnych części poprzez cięcie za pomocą frezu – specjalnego narzędzia skrawającego.
Obróbka frezarska wykonywana jest z zachowaniem wysokiej jakości i w terminie określonym przez Klienta. Firma posiada najnowocześniejszy sprzęt specjalistyczny, który umożliwi wykonanie każdego rodzaju prac frezarskich. Twoje zamówienie zostanie zrealizowane przez wysoko wykwalifikowanych specjalistów, dzięki których umiejętnościom możliwe jest wyprodukowanie niezbędnych półfabrykatów metalowych przy minimalnych kosztach materiałowych dla klienta. Będą w stanie obrabiać powierzchnie kształtowe, cylindryczne, końcowe i stożkowe.
Frezowanie metali, wykonywane na frezarkach, pozwala na obróbkę powierzchni poziomych, pionowych i nachylonych, a także powierzchni kształtowych i wpustów.
Prace frezarskie, będące specjalizacją naszej firmy, obejmują kompleks procesów technologicznych obróbki detali metalowych poprzez cięcie. Prace frezarskie wykonywane są w celu obróbki powierzchni zewnętrznych i wewnętrznych części z możliwością obróbki powierzchni poziomych, pionowych i nachylonych na frezarkach. Prace frezarskie wykonywane są z określoną prędkością, posuwem i głębokością skrawania, przy czym prędkość posuwu ograniczona jest wytrzymałością cieplną materiału frezu, a dobór głębokości i posuwu uzależniony jest od wytrzymałości narzędzia skrawającego. W zależności od wykonywanej pracy stosuje się frezarki uniwersalne, poziome, pionowe, wzdłużne, obrotowe, bębnowe i inne.
Do najskuteczniejszych metod obróbki metali, oprócz toczenia, zalicza się frezowanie. Metodą frezowania można obrabiać stale niehartowane, metale nieżelazne i stopy, chociaż w niektórych przypadkach możliwa jest również obróbka stali hartowanych. Cechą frezowania wykonywanego przy użyciu wieloostrzowego narzędzia skrawającego (freza) jest nieciągłość skrawania przez każdy ząb narzędzia. Frezowanie polega na cięciu tylko tej części przedmiotu obrabianego, z którą stykają się zęby frezu.
Podczas frezowania geometria przedmiotu obrabianego zależy bezpośrednio od kształtu narzędzia, dlatego w zależności od przedmiotu obrabianego stosuje się różne typy frezów. Aby uzyskać czyste powierzchnie, stosuje się frezowanie współbieżne, a w celu zwiększenia produktywności stosuje się frezowanie współbieżne. Frezowanie zgrubne wykonywane jest przy użyciu frezów o dużych skokach płytek i wiąże się z dużą głębokością skrawania, natomiast obróbka wykańczająca zmniejsza zarówno głębokość, jak i prędkość obróbki.
Frezowanie przy użyciu wieloostrzowych narzędzi skrawających jest jedną z najpowszechniejszych technologii obróbki metali. Frezowanie jako proces technologiczny skrawania metalu odbywa się za pomocą frezów, które umożliwiają frezowanie powierzchni w poziomie, pionie i pod kątem.
Technologię tę stosuje się do frezowania czołowego, czołowego, obwodowego i kształtowego części. Frezowanie walcowo-czołowe stosuje się do rowków, podcięć i rowków (w tym rowków przelotowych), frezowanie czołowe stosuje się do obróbki dużych powierzchni, a frezowanie kształtowe stosuje się do obróbki profili (na przykład kół zębatych). Frezowanie, podobnie jak toczenie, odbywa się przy różnych prędkościach, posuwach i głębokościach skrawania z możliwością zmiany tych parametrów dla konkretnych części.
Nowoczesne, precyzyjne urządzenia frezujące firmy DATRON (Niemcy) pozwalają nam na obróbkę materiałów takich jak aluminium, miedź i ich stopy, tworzywa sztuczne oraz tekstolit.Produkcja obudów sprzętu elektronicznego
Firma zainstalowała nowoczesny, precyzyjny sprzęt frezujący z DATRON(Niemcy); YCM(Tajwan): umożliwia obróbkę takich materiałów jak aluminium, miedź, stal i ich stopy, tworzywa sztuczne oraz tekstolit.YCM zaprezentowało także centrum obróbcze tokarsko-frezarskie YCM-GT-250MA.
Rozwój programów sterujących dla maszyn CNC odbywa się z wykorzystaniem systemu modelowania geometrycznego i przetwarzania oprogramowania dla maszyn CNC Mastercam.
Obecnie oferujemy:
- Produkcja części metalowych i plastikowych.
- Frezowanie i grawerowanie paneli czołowych i obudów sprzętu elektronicznego.
- Tworzenie form i modeli odlewniczych.
- Różne rodzaje grawerów i oznaczeń.
- Różne rodzaje produktów tokarskich.
Możliwości produkcyjne:
- Dokładność wykonania części metalowych wynosi 1 mikron.
- klasa chropowatości według GOST 2789-59 - 10.
- Maksymalny rozmiar obrabianego detalu to 1000mm x 650mm x 250mm.
- Maksymalna głębokość zamkniętych okien i wpustów wewnętrznych wynosi 50mm.
- maksymalna głębokość otworów gwintowanych M2-4 wynosi 12mm, M5-10 wynosi 16mm (otwory gwintowane mogą być nie tylko metryczne, ale także o dowolnym skoku).
- Minimalna średnica frezu wynosi 0,2 mm.
- Maksymalne wejście frezu w kształcie litery T wynosi 4,5 mm.
- Kąt cięcia frezu na jaskółczy ogon wynosi 5-15 stopni.
W możliwie najkrótszym czasie możliwe jest wykonanie wysokiej jakości prototypów, a także produkcja na małą skalę.
Części mogą mieć złożone zakrzywione powierzchnie i dużą liczbę przejść technologicznych.
Dane wejściowe do zamówienia i oceny akceptowane są w formie modelu 3D dowolnego nowoczesnego CAD lub w formacie IGS, STEP. W przypadkach, gdy konieczne jest wyjaśnienie właściwości, rodzajów gwintów itp. może być wymagany rysunek.
SYSTEM KONTROLI RENTGENOWSKIEJ
Korzystamy z zaawansowanych technologii z zakresu fluoroskopii. Rozdzielczość wynosi 1,3 Mp, co zapewnia rozpoznawanie do 0,5 µm, co czyni system niemal wyjątkowym.Obudowy urządzeń elektronicznych/kuchenek mikrofalowych, radiatory/radiatory elektroniki z reguły zawierają drobne elementy konstrukcyjne: gwinty do mocowania płytek drukowanych, otwory na złącza, rowki do układania i mocowania uszczelek itp. Uniwersalne centra obróbcze często nie są w stanie szybko poradzić sobie z frezowaniem małych elementów urządzeń elektronicznych ze względu na małą prędkość obrotową narzędzia skrawającego, dlatego optymalne jest wysokoobrotowe frezowanie 3D CNC.
Wysokoobrotowe frezowanie aluminium 3D CNC to nowoczesna, dynamicznie rozwijająca się dziedzina obróbki skrawaniem metali. Przy tego typu obróbce nie sprawdzają się klasyczne wzory na obliczanie sił skrawania, gdyż prędkość międzycząsteczkowego rozrywania metalu różni się znacznie od szybkości oddzielania metalu podczas standardowego frezowania „na siłę”.
Przy wysokoobrotowym frezowaniu aluminium wzrasta znaczenie usuwania ciepła i wiórów ze strefy skrawania, dlatego chłodzenie odbywa się za pomocą alkoholu technicznego dostarczanego do strefy skrawania za pomocą sprężonego powietrza. Daje to dodatkowe korzyści w przypadku braku konieczności mycia części po frezowaniu - aluminiowe i miedziane obudowy urządzeń elektronicznych/mikrofal, radiatory/radiatory elektroniki wychodzą dosłownie błyszczące.
Również jedną z niezaprzeczalnych zalet frezowania wysokoobrotowego jest czystość obrabianych powierzchni. Szybkie frezowanie 3D CNC pozwala bez szlifowania uzyskać wymagane parametry chropowatości i płaskości powierzchni odprowadzających ciepło obudów REA/mikrofal oraz radiatorów/promienników urządzeń radioelektronicznych.
Frezowanie z dużą prędkością wymaga zakupu specjalnych, drogich narzędzi z węglików spiekanych. Niestety, „standardowe” frezy nie nadają się do tego typu obróbki, a to znacznie zawęża wybór narzędzi skrawających.
Kolejną zaletą w stosunku do frezowania „standardowego” jest to, że „wiercenie” otworów pod różne średnice gwintów nieprzelotowych lub przelotowych można wykonać jednym frezem węglikowym z dużą prędkością, bez konieczności wymiany narzędzia skrawającego. To znacznie skraca czas przetwarzania, a co za tym idzie, staje się tańsze.
Mechaniczne gwintowanie w obudowach przyrządów do urządzeń elektronicznych/kuchenek mikrofalowych często prowadzi do pęknięcia kranów wewnątrz prawie gotowej części. Zwiększa to koszt części dla Kupującego, ponieważ Dostawca musi wliczyć w koszt wytworzenia partii dodatkowe koszty zapasów technologicznych. Negatywnym czynnikiem w obróbce gwintów w aluminium, miedzi i tworzywach sztucznych jest niska jakość powstałych gwintów: brak prostopadłości do powierzchni głównej, „zakleszczanie” pierwszych zwojów nacinanych gwintów ze względu na konieczność wielokrotnego wkręcania wejść i zakręcić krany.
Szybkie frezowanie aluminium 3D CNC pozwala uniknąć tego problemu: frezowanie gwintów odbywa się za pomocą specjalnych frezów z węglików spiekanych poruszających się po spiralnej ścieżce.
Kolejnym poważnym problemem w produkcji „gatunkowych” obudów jednostek REA/mikrofalowych jest ręczna obróbka faz, zadziorów i ostrych krawędzi, gdyż Bardzo trudno jest ręcznie uzyskać wysoką jakość obrobionych powierzchni części aluminiowych.
Szybkie frezowanie CNC 3D aluminium, miedzi i tworzyw sztucznych pozwala na usuwanie fazek, zadziorów i ostrych krawędzi z dużą szybkością, dokładnością i jakością przy użyciu specjalnych pogłębiaczy węglikowych. Ten rodzaj obróbki frezarskiej znacząco podnosi walory konsumenckie wytwarzanych produktów i zmniejsza ryzyko wystąpienia uszkodzeń poszczególnych części.