Rysowanie urządzeń do kucia artystycznego. Zrób to sam maszyna do kucia na zimno nie tylko pozwoli Ci zaoszczędzić pieniądze, ale także da Ci możliwość zarobienia pieniędzy. Łączenie części i malowanie
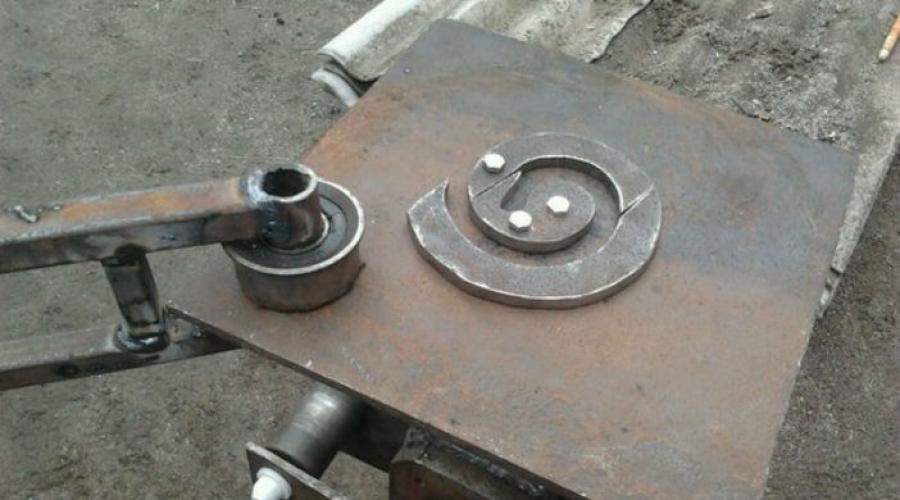
Każdy mistrz, wyposażając domową kuźnię, nabywa minimalny zestaw narzędzi i akcesoriów. Ale z reguły najprostsze operacje technologiczne z metalowymi półfabrykatami są wykonywane tylko na pierwszym etapie.
Wraz ze zdobywaniem doświadczenia z żelazem pojawia się zarówno chęć, jak i potrzeba kucia artystycznego – jest to zarówno ozdoba domu, jak i dodatkowy dochód. Niestety maszyny do nadawania próbek w kształcie spirali - ślimaka - praktycznie nie ma w sprzedaży. Tak czy inaczej, ale rzemieślnicy z reguły robią to własnymi rękami. Tematem tego artykułu są cechy samodzielnego projektowania i montażu ślimaka do kucia na zimno.
Cechy ślimaka
Autor w szczególności postanowił zwrócić uwagę czytelnika na kilka punktów. Pomoże Ci to uniknąć niektórych błędów w przyszłości. Na przykład, mając do czynienia z urządzeniem ślimaka i zasadą jego działania, ktoś będzie chciał złożyć własne urządzenie, inne niż te, których rysunki zostaną przedstawione poniżej.
Takie urządzenie całkowicie (jeśli mówimy o sprzęcie do majsterkowania) pozwoli na gięcie próbek o przekroju (strona kwadratowa) nie większym niż 10–12 mm. Sugerowany jest model ślimaka z „sterowaniem ręcznym”. Przy większej liczbie ogólnych próbek w życiu codziennym prawie nikt nie ma nic do roboty. Maszynę można ulepszyć, instalując napęd i silnik elektryczny.
Ale jak racjonalne jest to w przypadku małej domowej kuźni?
- Kucie na zimno odbywa się przy niskich prędkościach. Gwałtowna zmiana geometrii metalu prowadzi do pojawienia się pęknięć (pęknięć).
- Będziesz musiał wybrać nie tylko moc silnika elektrycznego, ale także przełożenie skrzyni biegów. Plus, aby zamontować obwód automatyki z instalacją odpowiednich elementów (przyciski, rozrusznik itp.). Wszystko to znacznie komplikuje produkcję maszyny.
Wniosek - do domowej kuźni wystarczy ślimak, za pomocą którego można ręcznie zginać wyroby metalowe. Każdy, kto rozumie wszystkie niuanse jego projektu i rozumie przynajmniej coś w elektrotechnice, będzie mógł samodzielnie zainstalować na nim napęd elektryczny.
Robienie ślimaka
Na rysunku pokazano kilka urządzeń. W przybliżeniu tak (w zasadzie) powinno się okazać.
Składanie ślimaka własnymi rękami to jedna z opcji samodzielnego projektowania, gdy nie ma sensu podawać zaleceń wskazujących dokładne parametry wszystkich elementów. Tutaj musisz skupić się na własnym wyobrażeniu o tym, co i jak będzie się zginać (promienie, liczba zwojów spirali itd.). Ale jeśli istota procesu produkcyjnego stanie się jasna, sam montaż nie spowoduje trudności.
urządzenie stacjonarne
Proces kucia na zimno wymaga dużego wysiłku. Jeśli masz już gotowy stół warsztatowy, być może będziesz musiał go wzmocnić. Podczas robienia ślimaka od podstaw rama stołu jest wykonana tylko z metalu - kanał, narożnik, grubościenna rura.
Oczywiste jest, że blat również musi być metalowy. Podczas pracy ślimak będzie poddawany zarówno obciążeniom statycznym, jak i dynamicznym. Dlatego zwykła blacha żelazna nie jest odpowiednia. Tylko płyta i nie mniej niż 4 mm.
Znakowanie i instalacja sprzętu „zamontowanego”
Być może najbardziej kreatywny etap pracy. Wszystko możesz zrobić własnymi rękami. Ale jak, biorąc pod uwagę perspektywę lub ograniczając produkcję tego samego rodzaju próbek?
Opcja 1. Najłatwiejsza. Znaczenie operacji polega na tym, że na blacie narysowany jest kontur spirali.
W rzeczywistości jest to szkic przyszłych części figurowych, na przykład z paska. Następnie wystarczy wyciąć kilka segmentów z grubej taśmy, wygiętej wzdłuż promienia. Są przyspawane do blatu, a mechanizm gięcia jest w zasadzie gotowy.
Ktoś uzna to wykonanie za bardziej atrakcyjne - z solidną listwą.
Ale praktyka pokazuje, że z takim ślimakiem jest trudniej pracować. Na przykład podczas wyjmowania z niego gotowego produktu pojawią się pewne trudności.
Opcja 2. To samo, ale rysuje się kilka konturów. Wzdłuż każdego wiercone są otwory, w których wycinane są nitki. Pozostaje tylko przygotować szablony dla odcinków stopu. Własnymi rękami są z reguły wykonane z grubej tektury lub sklejki.
Wykonane są na nich metalowe nakładki, w których po kolejnym oznakowaniu wiercone są również otwory, pokrywające się z „gniazdami” lądowania w płycie. Taka konstrukcja pozwoli na zorganizowanie na jednym stole produkcji wykrojów spiralnych o różnych promieniach. W zależności od kształtu łuku konieczne będzie jedynie zamontowanie odpowiednich segmentów w określonych miejscach. Ich mocowanie do podstawy jest skręcane. Możesz to zrobić inaczej. Zamiast takich przystanków umieść cylindryczne.
Do mocowania przyciągane są śrubami (od spodu płyty) lub wykonywane są od razu za pomocą nóżek (+gwint) i wkręcane w blat. O wiele wygodniej z nimi. A jeśli masz własny, to wyrzeźbienie go własnymi rękami to kwestia kilku godzin.
Opcja 3. Przygotuj kilka wymiennych modułów, które można zmienić w razie potrzeby.
Ślimak montaż
Zainstalowany lemiesz, zamocowane dźwignie, ogranicznik boczny. Wszystko to widać wyraźnie na rysunkach.
Wszystko, co jest w stodole (garaż, na strychu) przejdzie do akcji - przycinanie rur, prętów, narożników i tym podobnych. Jeśli zasada działania ślimaka jest jasna, nie są wymagane żadne dodatkowe wskazówki.
Kontrola zdrowia
To jest zawsze dorozumiane, więc żadnych komentarzy.
W zasadzie zrobienie ślimaka do kucia na zimno nie jest takie trudne. Co więcej, nie ma jednego standardu dla takich urządzeń. Ktoś powie – czy nie jest łatwiej kupić model fabryczny? Po pierwsze, jak już wspomniano, trzeba długo szukać. Po drugie, nie jest faktem, że jego możliwości będą pokrywać się z fantazjami mistrza. Po trzecie, będziesz musiał zmniejszyć swój portfel o co najmniej 19 000 (ręcznie) i 62 000 (elektrycznie) rubli.
Powodzenia w robieniu ślimaka własnymi rękami!
Kucie na gorąco było znane człowiekowi odkąd zaczął przetwarzać i wykorzystywać metale w swoim życiu. Przed wynalezieniem maszyn do tłoczenia i cięcia metalu kucie na gorąco i odlewanie były jedynymi sposobami wytwarzania narzędzi i broni, sprzętu gospodarstwa domowego i biżuterii.
Aby opanować tradycyjne kowalstwo, trzeba było długo się uczyć i zdobywać doświadczenie. Produkty kowala okazały się bardzo pracochłonne i niepowtarzalne, jest to niewątpliwa zaleta dla twórczości artystycznej i równie oczywista wada, gdy potrzebna jest duża ilość identycznych produktów.
Takie wady kucia na gorąco jak:
- duża pracochłonność
- wysokie wymagania dotyczące kwalifikacji mistrza,
- niska powtarzalność produktu.
Metoda kucia na zimno nie ma wad. Opiera się na właściwości metali do zmiany kształtu w określonych granicach pod wpływem siły mechanicznej. Technologia ma zastosowanie do prętów okrągłych i kwadratowych, taśm metalowych, rur oraz wyrobów walcowanych o różnych profilach. Kilka podstawowych operacji, takich jak
- gięcie przedmiotu pod zadanym kątem i po zadanym promieniu,
- tworzenie loków i spiral,
- skręcanie jednego lub więcej detali wzdłuż osi podłużnej
a połączenie powstałych detali pozwala w rozsądnym czasie i w przystępnej cenie, kilku, a nawet dziesiątki razy niższej niż przy użyciu kucia na gorąco, stworzyć koronkowe ogrodzenia, altany, ławki, elementy wystroju i sprzęty domowe.
Ponadto wszystkie elementy będą dokładnie takie same pod względem kształtu i wielkości, co jest szczególnie ważne przy formowaniu z nich wzorów i ozdób.
Do uzyskania głównych elementów wykorzystywane są specjalne maszyny.
- Gnutik jest jednym z najpopularniejszych. Pozwala na zginanie pręta pod zadanym kątem i wzdłuż zadanego promienia, również w formie fali.
- Ślimak służy do skręcania końca pręta lub rury w spiralę
- Drążek skrętny służy do skręcania drążka wzdłuż jego osi podłużnej.
Urządzenie „Gnutik”
Rolki na stałych ogranicznikach są wymienne, aby umożliwić gięcie prętów i rur pod różnymi kątami i promieniami. Na ruchomym ograniczniku zamocowany jest również wymienny wałek lub klin, w zależności od wymaganego kształtu gięcia.
Na razie prosty przedmiot jest mocowany za pomocą stałych ograniczników i obracając napęd mechanizmu ślimakowego łuku, dosuwany jest do niego ruchomy ogranicznik - klin lub rolka. Kontynuując obracanie napędu, wygnij przedmiot pod żądanym kątem.
Wykonanie gięcia do kucia na zimno własnymi rękami jest dość realistyczne, wystarczy dokładnie śledzić rysunek, obserwując wymiary i naddatki.
Trudności w przydomowym warsztacie mogą powstać przy frezowaniu stali o wysokiej wytrzymałości i wierceniu w niej otworów.
Jeśli w warsztacie nie ma jeszcze takiego sprzętu, lepiej złożyć zamówienie na główne części giętarki w produkcji - takiej pracy nie wykonamy wiertarką i wyrzynarką.
Łączenie i malowanie części
Aby zmontować części w żądany projekt, konieczne jest zapewnienie płaskiej wolnej przestrzeni - na podłodze lub na stole, w zależności od wielkości. Przedmioty obrabiane najlepiej piaskować w celu usunięcia ewentualnej rdzy i oczyszczenia powierzchni przed spawaniem i malowaniem. Piaskarkę można również wykonać niezależnie od używanej butli gazowej, pary dysz i kranów. Do wtryskiwacza można użyć ceramicznego korpusu zużytej świecy zapłonowej. Aby to zrobić, wystarczy posiadać umiejętności spawalnicze i ślusarskie.
Po piaskowaniu części układane są na miejscu montażu. Dla wygody pracy możesz skorzystać z barów-podszewek. Po umieszczeniu części warto ponownie sprawdzić, czy ich położenie jest zgodne z rysunkiem. Ponadto, po zamocowaniu kluczowych elementów konstrukcyjnych za pomocą zacisków, należy je chwycić za pomocą zgrzewania punktowego. Po ostatnim sprawdzeniu wymiarów, kątów i względnej pozycji można przystąpić do spawania wszystkich niezbędnych szwów.
Po spawaniu należy wyczyścić wagę szczotkami drucianymi zamocowanymi w wiertarce, a w trudno dostępnych miejscach ręcznie. Konstrukcja gotowa do malowania. W zależności od dobranych podkładów i farb wykończeniowych, a także sposobu aplikacji, montaż układany jest na listwach amortyzujących lub mocowany w pionie za pomocą tymczasowych ograniczników.
Wygodne jest malowanie struktur o dużej gęstości części za pomocą aerografu, w przypadku rzadkiej siatki będziesz musiał uzbroić się w pędzel, aby zmniejszyć utratę farby.
Produkty kute na zimno
Szeroka gama produktów wytwarzana jest metodą kucia na zimno. Są to przede wszystkim elementy kratownic i ogrodzeń – zarówno same pręty, jak i poprzeczki, zwieńczenia, ozdoby. Z odległości kilku metrów trudno go odróżnić od kutej kraty. Loki i spirale, tworzące misterne wzory i ozdoby, ożywią każdą kratę. Zwykłe ogrodzenie, poza funkcją użytkową, zyskuje więc także wartość artystyczną. Będzie to wymagało gnicka, ślimaka i drążka skrętnego.
Kute stojaki na latarnie, balustrady na mosty nad stawami, markizy i werandy, stoły i ławki świetnie prezentują się w okolicy. Tak, a sama altana nie jest zła do zrobienia z kutego baru. Niespodziewaną lekkość i zwiewność jak na surowy metal nadadzą jej loki i spirale, a skręcone podpórki podkreślą chęć wzniesienia się.
Kute piecyki są również szeroko rozpowszechnione dzisiaj, które również uzupełniają cel gospodarczy o wrażenie estetyczne. Właściwie kocioł ginie wśród baldachimu, wzorzystych ścian i podpór, ozdobionych zagięciami dachu.
Dużą popularnością cieszą się również elementy balustrad, balustrady schodów i balkonów. Loki i spirale są tu również szeroko stosowane, nie tylko jako dekoracja, ale także jako element konstrukcyjny. Tralka skręcona wzdłuż osi podłużnej wygląda bardzo dobrze, a podpory narożne często składają się z kilku skręconych ze sobą prętów. Również na maszynie skrętnej wykonują tzw. „latarka” - kilka prętów wygiętych w spiralę, połączonych końcami przez spawanie.
Kolejnym obszarem zastosowania kucia na zimno są detale dekoracji pomieszczeń i mebli. Klamki i zatrzaski do drzwi, narzędzia i wieszaki kominkowe, stojaki na parasole i gzymsy na zasłony i zasłony - tutaj powszechnie stosuje się małe loki i skręcone pręty.
Meble wykonujemy zarówno do mebli ogrodowych, które nie boją się opadów deszczu i zmiany pór roku, jak i do mebli domowych, łącząc metal z drewnem i tkaniną.
Jednym ze sposobów na dekorowanie obszarów jest użycie produktów kutych. Bardzo dekoracyjnie prezentują się ogrodzenia, ławki, altany, balustrady schodowe i inne podobne konstrukcje. Co więcej, w większości przypadków produkty te nie są fałszerstwem w tradycyjnym tego słowa znaczeniu. Najczęściej odbywa się to nie w kuźni i nie za pomocą młotka i kowadła, ale za pomocą niektórych urządzeń, które pozwalają tworzyć różnorodne wzory i produkty z metalowych pasków i kwadratowych prętów. Do produkcji takich produktów potrzebne będą maszyny do kucia na zimno. Niektóre z nich można wykonać własnymi rękami, inne łatwiej kupić.
Ogrodzenia, balustrady schodowe i balkonowe - można to zrobić również samemu Balustrady ganku są ozdobą, a nie tylko i wyłącznie użytkową oprawą
Jakie urządzenia są używane
Kucie na zimno charakteryzuje się różnymi lokami, zagięciami, skręconymi prętami itp. Niemal każdy typ wykonywany jest na osobnym urządzeniu – konkretnej maszynie. Napęd mogą być ręczne, a może elektryczne. W przypadku małych ilości „dla siebie” stosuje się ręczne maszyny do kucia na zimno. Chociaż nie są zbyt wydajne, są znacznie łatwiejsze w produkcji. Jeśli konieczne jest uruchomienie produkcji, wykonuje się podobne urządzenia, ale z silnikami elektrycznymi. W takim przypadku praca fizyczna prawie nie jest konieczna, ale znacznie wzrasta złożoność produkcji urządzenia. W naszym materiale porozmawiamy o ręcznych maszynach do kucia na zimno.
Jakie urządzenia są używane:
Dla początkującego rzemieślnika najważniejszą maszyną do kucia na zimno jest ślimak. Tylko z jego pomocą można zrobić wiele ciekawych rzeczy - od ogrodzenia i bramy po ławkę i inne podobne produkty. Na drugim miejscu, w zależności od stopnia potrzeb, jest maszyna skrętna. Urozmaica detale. Cała reszta może zostać nabyta lub wykonana w miarę doskonalenia się i zdobywania umiejętności.
Domowe „ślimaki”
W rzeczywistości jest to unowocześniony, ale te ulepszenia ułatwiają robienie loków z dość grubych prętów (przekrój do 10-12 mm) i powtarzanie ich z dużą dokładnością.
Te maszyny do kucia na zimno mają kilka konstrukcji, ale najłatwiejszą opcją do wdrożenia jest okrągły stół z centralną nogą. Dźwignia z rolkami na łożyskach na końcu jest ruchomo przymocowana do nogi. Ułatwiają proces gięcia.
Powierzchnia stołu może być wykonana z blachy stalowej o grubości 10 mm lub większej. Do nogi można użyć dowolnej grubościennej okrągłej rury. Ważne jest, aby konstrukcja była stabilna, ponieważ będą działały siły boczne, dlatego potrzebne są boczne stojaki, rozpórki, a także stabilna podstawa.
Ciągarka do kucia na zimno „Ślimak”
Dźwignia jest łatwiejsza do wykonania z kwadratowej rury o grubej ściance - co najmniej 2-3 mm. Przekrój rury 25*40mm lub więcej. Dźwignię można przymocować do nogi na łożysku lub po prostu wziąć mały kawałek grubościennej rury o większej średnicy, nałożyć go na nogę i przyspawać od dołu listwę oporową, aby dźwignia nie upaść. Opcja łożyska zapewnia łatwiejszy ruch, ale przy smarowaniu działa również druga opcja.
Ważny jest również kształt dźwigni. Dźwignia jest podwójna, górna część działa, dolna podtrzymuje. Wszędzie tam, gdzie istnieją połączenia, pożądane jest dodanie wzmocnienia, ponieważ wysiłki są znaczne.
Na stole zamocowany jest trzpień lub przyrząd - forma, wzdłuż której zginane są loki. Wykonane są w różnych średnicach - dzięki czemu można wykonać loki o różnych średnicach. Takie trzpienie mogą być prefabrykowane – aby uformować więcej zagięć. Każda taka próbka musi mieć pręty, które są zainstalowane w otworach w stole. Więc ten szablon jest naprawiony. Również jego kształt musi być tak zaprojektowany, aby koniec pręta był w nim dobrze osadzony.
Często trzpienie są obrabiane z metalowego koła o odpowiedniej średnicy za pomocą szlifierki, ale istnieją opcje metalowe z przyspawanymi do niego stalowymi płytami, odpowiednio zakrzywionymi.
Jak zrobić podobną maszynę do kucia na zimno - w następnym filmie. Jest też dobry opis tego, jak doprowadzić końce przedmiotu obrabianego do przyzwoitego stanu - zwykłe surowe krawędzie wyglądają bardzo szorstko. Jest specjalny sprzęt do ich przetwarzania, ale jak się okazało, można sobie bez niego poradzić.
Maszyna skrętna
Jak już wspomniano, te maszyny do kucia na zimno umożliwiają wykonywanie zagięć wzdłużnych na pręcie. To stosunkowo prosta konstrukcja. Głównym zadaniem jest unieruchomienie jednego końca pręta, przymocowanie dźwigni do drugiego, za pomocą którego będzie można przekręcić obrabiany przedmiot.
Jako podstawę odpowiednie jest cięcie profilowanej rury o grubej ściance (co najmniej 3 mm). Zatrzask można spawać z tych samych prętów, pozostawiając kwadratową szczelinę o pożądanej średnicy. Możesz użyć zacisku kablowego o odpowiednim rozmiarze (można go znaleźć w sklepie z osprzętem). Każdy z tych ograniczników jest przyspawany do podstawy.
Uchwyt do liny stalowej - doskonały uchwyt na wędkę
Następnie musisz w jakiś sposób zapewnić uchwycenie i skręcenie drugiej części przedmiotu obrabianego. Można to zrobić za pomocą dwóch zespołów łożysk. Do środka wkładana jest rura o odpowiedniej średnicy, do której z jednej strony przyspawany jest uchwyt - konstrukcja przypomina literę „T”. Z drugiej strony w rurze wykonany jest element ustalający: wiercone są cztery otwory, przyspawane są do nich nakrętki na 12 lub 14 śrub. Efektem jest dobry zatrzask - śruby są dokręcane po włożeniu pręta.
Jeszcze prostsza maszyna do wytwarzania prętów skrętnych metodą kucia na zimno jest w następnym filmie.
Film o domowych urządzeniach i maszynach do kucia na zimno
Osobie, która nie jest obojętna na podrobione produkty, można tylko pozazdrościć. Posiada wszystko, czego potrzebujesz do realizacji najśmielszych projektów projektowych. Urządzenia do produkcji elementów do kucia na zimno można kupić gotowe lub wykonane ręcznie, ale w takim czy innym przypadku możesz być pewien, że będzie z nimi wygodna i łatwa praca. Jednocześnie nie jest wymagana duża siła fizyczna, wystarczy wcisnąć niezbędne przyciski i w porę przekręcić specjalne dźwignie.
Jedyną rzeczą do zapamiętania jest to, że wytwarzanie produktów kutych na zimno wymaga ścisłych zasad i spójności. Innymi słowy, kucie na zimno to stopniowy proces technologiczny, w którym metalowe półfabrykaty są odkształcane w zależności od pożądanego projektu. Aby mieć lepsze pojęcie o tej pracy, musisz dowiedzieć się, jakie są rodzaje kucia, jak nazywa się popularne elementy kute i jak wygląda wykonanie kutych wyrobów własnymi rękami.
W produkcji wyrobów metalowych można wyróżnić 7 rodzajów kucia na zimno. Są to pewne etapy tworzenia elementów, które należy wykonać podczas pracy z półfabrykatami.
Wszystkie prace muszą być wykonywane zgodnie z wymaganiami i zasadami, w przeciwnym razie nie należy liczyć na piękny kuty produkt.
Najważniejszym etapem jest kucie metalowych półfabrykatów. Jest to największy, najbardziej odpowiedzialny, złożony i poważny proces, dlatego należy do niego podchodzić bardzo ostrożnie. Kucie na zimno może mieć kilka rodzajów:
- Projekt - odbywa się pod wysokim ciśnieniem. Jest to konieczne, aby powiększyć obrabiany przedmiot po bokach, zmniejszając jego wysokość.
- Przeciąganie - ten etap polega na podgrzaniu metalowej części, a następnie obróbce młotkiem. Jest to konieczne w celu zmniejszenia pola przekroju poprzecznego poprzez zwiększenie długości metalowego pręta.
- Firmware - ten etap polega na wykonaniu otworów wewnątrz obrabianego przedmiotu. Podczas wykonywania takiej pracy można uzyskać otwory o różnych średnicach i długościach. Jest otwarty i zamknięty.
Przeciąg i przeciąganie sprawiają, że struktura metalowego przedmiotu obrabianego jest bardziej delikatna, dlatego dalsze prace należy wykonywać bardzo ostrożnie, aby zapobiec pęknięciu tej lub innej części konstrukcji.
Narzędzia do kucia na zimno
Produkcja wyrobów kutych na zimno wymaga użycia kilku urządzeń lub maszyn. Jak wspomniano powyżej, można je kupić lub wykonać ręcznie, ale najpierw zastanówmy się, jakie części można uzyskać za pomocą różnych maszyn.

W przypadku produktów ręcznie robionych będziesz musiał wykonać specjalne szablony, które pozwolą na tworzenie elementów o różnych kształtach i rozmiarach.
Jak pracować z mechanizmem ślimakowym, możesz zobaczyć na proponowanym filmie:
- Mechanizm uniwersalny - pozwala na wykonywanie kilku funkcji cięcia, nitowania i formowania wyrobów metalowych. Nawiasem mówiąc, takie urządzenie można łatwo zmontować własnymi rękami, co znacznie zaoszczędzi Twój budżet.
- Gnutik - taki mechanizm pozwala stworzyć deformację łukową metalowej części. Ale tutaj konieczne jest wykonanie dokładnych obliczeń i pomiarów, aby nie pomylić się z promieniem gięcia.
- Twister - mechanizm tego planu pozwala zginać obrabiany przedmiot wzdłuż osi podłużnej gotowego produktu. Zasada działania takiego mechanizmu polega na zginaniu produktu poprzez zaciskanie go z jednej i drugiej strony. W takim przypadku obrotowy uchwyt pozwoli ci przekręcić część.
- Fala - mechanizm takiego planu pozwala uzyskać części przypominające falę z metalowych półfabrykatów. Na takiej maszynie zwyczajowo wykonuje się kraty „Bojarskie” lub „Fala”.
- Pieczątka - nazwa mówi sama za siebie. Taki mechanizm pozwala na nanoszenie stempli z różnymi rzeźbionymi elementami na metalowe części. Każdy mistrz powinien mieć w swoim arsenale kilka takich znaczków, wtedy gotowe produkty będą bardziej zróżnicowane. Zasada jego działania jest bardzo prosta, pod wpływem nacisku na metalowych elementach pozostają wyraźne nadruki z szablonów.
- Węzeł mechaniczny - ten mechanizm umożliwia zginanie metalowych prętów w okrąg. W takim przypadku średnica takich produktów może być inna. Dlatego w arsenale mistrzów takie urządzenie jest niezbędne.
Zrób to sam kucie na zimno, instrukcje krok po kroku i porady ekspertów
Co dziwne, ale wyroby kute można wytwarzać nawet w domu. Oczywiście nie będą one tak pretensjonalne jak elementy obrabiane na gorąco, ale jako wzór dekoracyjny nie mają sobie równych. Wystarczy kilka opisanych wyżej narzędzi, materiałów i co najważniejsze chęci. Reszta to zgodność z technologią.
Proces produkcyjny składa się z kilku etapów:
Rozpoczynając pracę, ponownie sprawdź swoje obliczenia, nawet mały błąd może zepsuć wygląd gotowego produktu, nie mówiąc już o tym, że może nie pasować do zamierzonej kompozycji. Poprawianie i dopasowywanie gotowych części jest zawsze trudniejsze, dużo łatwiej jest sprawdzić wszystko kilka razy.
Po wykonaniu wszystkich szczegółów możesz zacząć montować zamierzoną kompozycję. Do mocowania lepiej zastosować spawanie, ale nie należy z tym przesadzać, aby nie uszkodzić mniejszych elementów.
Ostatnim etapem będzie obróbka gotowego produktu, która polega na szlifowaniu i malowaniu gotowej kompozycji.
Jeżeli zająłeś się produkcją elementów kutych na zimno, to prawdopodobnie przestudiowałeś rynek cenowy i oceniłeś swoje możliwości finansowe. Jeśli nie, najpierw zwróć uwagę na koszt materiałów, niezbędny sprzęt i sposób przetwarzania gotowego produktu. Ale w każdym razie produkt wykonany przez siebie jest wart wszystkich kosztów. I możesz je zmniejszyć na sprzęcie, jeśli zrobisz to sam.
Wyroby kute w architekturze i aranżacji wnętrz od dawna cieszą się dużą popularnością. Kute z metalu kraty na okna i kominki, płot czy tralki schodowe zawsze prezentują się elegancko i atrakcyjnie. Dziś, pomimo nowoczesnych technologii w obróbce metali, ręcznie kute wyroby metalowe cieszą się większą popularnością niż kiedykolwiek. Oczywiście kucie metalu „zrób to sam” nie jest łatwym zadaniem, a bez odpowiedniego przygotowania trudno jest wykonać piękny kuty produkt. Ale ci, którzy chcą opanować to starożytne rzemiosło i są gotowi do ciężkiej pracy fizycznej, będą musieli zapoznać się z rodzajami i technologią kucia metali, zrozumieć metale do kucia, zrozumieć proces kucia i umieć posługiwać się narzędziem kowala.
Kucie metalu
Kucie metalu to proces obróbki metalowego przedmiotu w celu nadania mu określonego kształtu i rozmiaru. W rzeczywistości istnieją dwa rodzaje kucia - na zimno i na gorąco. Podczas ręcznego kucia metalu konieczne jest zrozumienie obu rodzajów kucia, ponieważ każdy ma swoje zalety i wady.
W procesie kucia na gorąco przedmiot obrabiany jest podgrzewany do określonej temperatury, w której metal traci swoją wytrzymałość i staje się plastyczny. Wysoka ciągliwość to główna zaleta kucia na gorąco. Umożliwia łatwe nadanie metalowemu przedmiotowi określonego kształtu i rozmiaru. Również kucie na gorąco pozwala na wykorzystanie większości technologii samego kucia, co ma korzystny wpływ na różnorodne opcje pracy.
Ale ogrzewanie metalu ma swoje wady. Przede wszystkim jest to konieczność wyposażenia specjalnej kuźni i koszt paliwa do niej. Może to stanowić prawdziwy problem dla tych, którzy chcą kuć na gorąco na obszarach miejskich. Ponadto praca z ogniem jest dość niebezpiecznym zajęciem i wymaga zwiększonego bezpieczeństwa przeciwpożarowego. Innym czynnikiem, który może znacząco wpłynąć na wybór rodzaju odkuwki, jest specyficzna znajomość warunków temperaturowych dla odkuwania metalu.
W przeciwieństwie do kucia na gorąco, kucie na zimno nie wymaga pieca do podgrzewania metalu. Cała istota kucia na zimno polega na nadaniu kształtu metalowemu półfabrykatowi poprzez gięcie, zaciskanie i spawanie. Kucie na zimno jest nieco łatwiejsze do wykonania i nie wymaga dużo miejsca na założenie warsztatu. Cały proces tworzenia gotowego produktu nie wymaga stosowania wysokich temperatur, co ma bardzo pozytywny wpływ na ogólne bezpieczeństwo.
Ale kucie na zimno ma jedną istotną wadę. Cała praca musi być wykonana z określonymi półproduktami bez możliwości poprawienia błędu. Oczywiście nie dotyczy to wszystkich prac kucia na zimno, ale w większości przypadków uszkodzony półfabrykat nadaje się tylko na złom lub podręcznik szkoleniowy.
W każdym razie, niezależnie od rodzaju kucia, będziesz musiał dość dokładnie zapoznać się z wieloma ważnymi punktami. Po pierwsze dotyczy to metali i reżimów temperaturowych ich topienia i kucia. Po drugie, musisz znać i rozumieć technologie kucia metali. Poniżej zastanowimy się, jakie metody technologiczne są wykorzystywane do kucia i jak są stosowane w pracy.
Kucie metalu
Ręczne kucie metalu jest dość czasochłonnym i złożonym zadaniem, które wymaga użycia pewnych metali, a raczej metali o określonych właściwościach. W przypadku ręcznego kucia na zimno lub na gorąco najważniejszą cechą jest ciągliwość metalu, ponieważ od tego zależy prostota i wygoda zmiany kształtu przedmiotu obrabianego. Warto jednak zauważyć, że plastyczność i wytrzymałość metalu są ze sobą powiązane. Gdy jedna z tych cech wzrasta, druga maleje. Dlatego tak ważne jest zrozumienie właściwości metalu i poznanie składu przedmiotu obrabianego.
Ważny! Istnieją inne równie ważne cechy metali. Ponieważ jednak rozważamy kucie elementów dekoracyjnych, takich jak ruszty kominkowe, tralki, płoty itp., nie ma potrzeby skupiania się na odporności na zużycie, odporności na czerwień itp., jak również na elementach stopowych.
Do kucia dekoracyjnego wykorzystywane są następujące metale: miedź, mosiądz, duraluminium, stal, a także inne stopy miedzi, magnezu, aluminium i niklu. W rzeczywistości kucie ręczne wykorzystuje miękki, ciągliwy metal, który można łatwo wyginać lub kształtować. Aby wybrać najlżejszy metal ciągliwy, musisz zajrzeć do Grader of Steel and Alloys. Znajdziesz w nim szczegółowy opis wszystkich metali i stopów wraz z ich charakterystyką i składem.
Pomimo tego, że najbardziej plastycznym metalem jest miedź i jej stopy, rzemieślnicy preferują stosowanie metali żelaznych do kucia na zimno i na gorąco. Ta pozycja wynika z wysokich kosztów metali nieżelaznych. W końcu cena kucia metalu w dużej mierze zależy od kosztu oryginalnego wykroju i nie każdego stać na zakup ogrodzenia czy tralek wykonanych z miedzi. Wybierając miękki metal żelazny do kucia, należy skupić się na stalach o minimalnej zawartości węgla około 0,25%. A także z minimalną ilością szkodliwych zanieczyszczeń, takich jak chrom, molibden, siarka i fosfor. Ponadto należy unikać stali konstrukcyjnych i narzędziowych o wysokiej zawartości węgla od 0,2% do 1,35%. Takie stale są najmniej ciągliwe i trudne do spawania.
Wybierając ten lub inny metal, konieczne jest użycie Grader of Steel and Alloys. Ale jeśli nie ma do niego dostępu, możesz skorzystać z poniższych tabel, aby określić zawartość węgla w stali. Sam proces wyznaczania jest dość prosty, wystarczy przyłożyć obrabiany przedmiot do działającej ostrzałki i spojrzeć na snop iskier, a następnie porównać go ze wskaźnikami w tabeli.
Dziś, dzięki przemysłowej produkcji metalu, nie ma potrzeby tworzenia wykrojów do kucia własnymi rękami. Nowoczesne kuźnie wykorzystują gotowe wyroby fabryczne do kucia na zimno. Najczęściej stosowane formaty blanków to: 30x45 mm, 40x45 mm, 10x10 mm, 12x12 mm, pręty o przekroju 10 mm, 12 mm, 16 mm, 25 mm, 30 mm, 50 mm, blachy o grubości od 3,5 do 6 mm, rury okrągłe 1/2", 3/4", 1", rury profilowe od 20x20 mm do 30x30 mm.
Narzędzie do kucia metalu
Wykonywanie jakichkolwiek prac przy kuciu metalu jest niemożliwe bez specjalnego narzędzia. Sprzęt kowalski do kucia na gorąco jest dość zróżnicowany i obejmuje kowadło, kuźnię, różne młoty, szczypce i wiele innych. Narzędzie do kucia na zimno jest nieco prostsze i składa się z kilku specjalnych maszyn. Oczywiście do kucia zarówno na zimno, jak i na gorąco wykorzystywane są nowoczesne narzędzia, takie jak spawarka, szlifierka i szlifierka. Znając cel konkretnego narzędzia, możesz poprawnie wykonać dowolną pracę.
narzędzie do kucia na gorąco
- Klakson. Nie możesz się bez niego obejść w kuciu na gorąco. W końcu to w nim obrabiany przedmiot można nagrzać do temperatury 1400 ° C. Palenisko to w większości piec przeznaczony do pracy w wysokich temperaturach i z nadmuchem.
- Kowadło. To narzędzie jest podporą, na której wykonywane jest kucie. Samo kowadło występuje w kilku typach, wśród których najpopularniejszym jest kowadło dwurożne o wadze 200 kg. Ale waga może wynosić od 150 do 350 kg.
- Szperaki. Podczas wykonywania różnych kucia artystycznego i dekoracyjnego używa się szperaków. Mają wiele różnych typów, a każdy mistrz może je wykonać dla siebie. Wspólną cechą każdego szperaka jest to, że wkłada się je w kwadratowy otwór w kowadle lub mocuje do drewnianej kłody. Poniższe zdjęcie pokazuje najczęstsze szperaki.
- Młot kowalski oraz Hamulec ręczny. To jest główne narzędzie kowala. Młot kowalski waży od 4 do 8 kg i służy do zadawania silnych ciosów. W zależności od rodzaju pracy i grubości przedmiotu obrabianego dobierana jest również masa młota. Hamulec ręczny waży od 0,5 do 2 kg. Służy do nadania ostatecznego kształtu produktowi.
- Kleszcze. Drugim najważniejszym narzędziem są szczypce do rogów. Bez nich niemożliwe jest przytrzymanie gorącego przedmiotu do obróbki. Istnieje kilka rodzajów kleszczy do skał dla określonego profilu i rozmiaru przedmiotu obrabianego. Poniższe zdjęcie przedstawia roztocza rogów o różnych kształtach.
- Młotki kształtowe. Podczas wykonywania kucia artystycznego wymagane jest tworzenie wygiętych półfabrykatów lub półfabrykatów o określonym kształcie. W tym celu stosuje się młotki kształtowe. Mogą być zarówno niższe, na których odbywa się przetwarzanie, jak i górne. Istnieje wiele opcji młotków kształtowych, a każdy mistrz ma swoje własne. Poniższe zdjęcie pokazuje główne narzędzie pomocnicze.
Oprócz opisanych powyżej stosowane są różne przyrządy pomiarowe, takie jak wspólny ruletka,podwójny zacisk, plac kowalski, szablony oraz kalibry. Wybór narzędzi kowalskich jest ogromny, trudno wymienić wszystko, dlatego każdy mistrz ma swój zestaw tylko niezbędnych i często używanych narzędzi.
Narzędzie do kucia na zimno
- Gnutik(zdjęcie poniżej). Jest to podstawowe narzędzie do kucia na zimno. Jak sama nazwa wskazuje, pozwala na wygięcie metalowego półwyrobu pod określonym kątem. Dodatkowo giętarka umożliwia tworzenie elementów łukowych o określonym promieniu.
- Ślimak. Nazwa mówi sama za siebie. Za pomocą ślimaka możesz tworzyć różne spiralne elementy dekoracyjne. Spirala wykonana jest pod określony szablon, który w razie potrzeby można zmienić na inny, o mniejszym lub większym promieniu.
- Latarka. Maszyna ta przeznaczona jest do tworzenia elementu dekoracyjnego o tej samej nazwie.
- Fala. Pozwala tworzyć elementy przypominające fale. Podczas przeciągania pręta przez tę maszynę uzyskuje się piękny sinusoidalny przedmiot obrabiany.
- tornado. Zgodnie z zasadą działania ta maszyna jest podobna do latarki, ale w przeciwieństwie do niej, twister tylko skręca obrabiany przedmiot wzdłuż osi.
- Maszyna pierścieniowa. Jak we wszystkich poprzednich maszynach, nazwa mówi sama za siebie.
Oprócz opisanych powyżej istnieją również uniwersalne maszyny do nitowania, cięcia, zaciskania i dodawania objętości. Wszystkie opisane powyżej maszyny można wykonać zarówno samodzielnie, jak i kupić w sklepie. Oczywiście domowe urządzenia do kucia na zimno będą nieco gorsze jakościowo od fabrycznych, ale jest to równoważone wyjątkowością elementów tworzonych za ich pomocą. Do produkcji maszyn do kucia na zimno rysunki można znaleźć zarówno w domenie publicznej, jak i kupić od specjalistów.
Ważny! Maszyny do kucia na zimno mogą być ręczne lub napędzane silnikami elektrycznymi. Pomimo obecności przekładni, ręczne kucie na zimno jest dość pracochłonnym i czasochłonnym zadaniem, a aby uzyskać duże ilości elementów kutych, lepiej wyposażyć maszynę w silnik elektryczny.
Osobno warto zwrócić uwagę na maszyny przemysłowe do kucia na zimno. Ceny takich maszyn do kucia na zimno wynoszą około 6 000 USD, ale jedna taka maszyna jest w stanie wykonać prawie wszystkie operacje technologiczne kucia na zimno. Przykładem jest maszyna Master 2 firmy MAN. Na filmie demonstrującym kucie na zimno można zobaczyć możliwości tej maszyny.
Zrób to sam kucie metalu
W procesie kucia stosuje się różne techniki i metody kucia, aby nadać przedmiotowi określony kształt. Do wykonania każdego z nich stosuje się określoną technologię i narzędzie do kucia metalu. Technologia kucia metalu metodami na gorąco i na zimno jest znacząco różna. Jak już wspomniano, kucie na gorąco wymaga podgrzania przedmiotu obrabianego w celu zmiany jego kształtu, podczas gdy kucie na zimno tylko wygina przedmiot. Na tej podstawie rozróżnia się główne metody technologiczne, wiedząc, które możesz bezpiecznie zabrać do kucia metalu własnymi rękami.
Zrób to sam kucie metalu na zimno
Kucie na zimno zrób to sam jest dość łatwe i nie wymaga dużego wysiłku. Cała praca podzielona jest na kilka etapów: stworzenie szkicu lub rysunku przyszłego produktu, zakup materiałów oraz sam proces kucia metalu.
Rysunek można wykonać w specjalnym programie komputerowym, kupić gotowy lub narysować ręcznie. Możesz znaleźć plany kucia na zimno za darmo. Aby to zrobić, wystarczy zwrócić się do mistrzów, którzy zajmują się kuciem od ponad roku i poprosić o jeden lub dwa rysunki do szkolenia. W rzeczywistości rysunek służy kilku celom. Po pierwsze, aby wiedzieć, jakie elementy trzeba będzie wykonać metodą kucia na zimno. Po drugie, mając taki projekt w ręku, możesz obliczyć liczbę i rodzaj metalowych półfabrykatów, takich jak pręty, rury kształtowe i tak dalej. Po trzecie, rysunek będzie potrzebny do złożenia wszystkich elementów w jedną całość.
Oddzielnie należy wziąć pod uwagę elementy kucia na zimno, które składają się na projekt. Obecnie można znaleźć całkiem sporo różnych elementów kutych, ale wszystkie można połączyć w kilka klasycznych grup.
- Łapy. Ten element jest zakończeniem metalowego pręta rozwiniętego w jakiejś formie. Do tej grupy należą tzw. Szczyty. Mimo szpiczastego końca, szczupaki wykonane są w podobnej technologii.
- loki. Ta grupa obejmuje kilka wspólnych elementów: wolutę, chervonkę i ślimaka. Spirala lub Bajgiel to pręt, którego końce są wygięte w jednym kierunku. Czerwonka- pręt, którego końce są wygięte w różnych kierunkach. Element ten jest czasem nazywany „dolarem” ze względu na podobieństwo do znaku waluty amerykańskiej. Przecinek lub Ślimak- prosty lok, którego jeden koniec jest wygięty, a drugi prosty.
- Pierścionki. Ten element jest tworzony po prostu: pręt o przekroju okrągłym lub kwadratowym nawija się na półfabrykat maszyny, w wyniku czego uzyskuje się sprężynę, którą następnie tnie się na osobne pierścienie.
- Skręcenie. Ten element jest dość łatwy do rozpoznania po skręcie spiralnym wzdłuż osi. Opcji drążków skrętnych jest sporo, a jedną z najczęstszych jest taki element jak latarka, a także prosty spiralny pręt do kraty lub ogrodzenia.
Cały proces wytwarzania elementów kutych na zimno oparty jest na ogólnie przyjętych technologiach kucia - gięcie, skręcanie, ciągnienie.
Kaptur- jest to technologia polegająca na zwiększeniu długości przedmiotu obrabianego poprzez zmniejszenie jego przekroju. W kuciu na zimno stosowana jest jedna z opcji ciągnienia - walcowanie. To z jego pomocą powstają różne łapy i szczyty. Do tworzenia łap używana jest specjalna maszyna do walcowania. Koniec obrabianego przedmiotu jest wprowadzany, a następnie uruchamiany jest mechanizm zwijający, w wyniku czego koniec jest spłaszczany z podcięciem lub bez. Do produkcji szczytów używana jest prasa. Procedura jest taka sama, ale w rezultacie końcówka jest zwijana i prasowana w określony kształt.
pochylenie się. Ta technologia kucia polega na zaginaniu końcówek lub innej części przedmiotu obrabianego pod określonym kątem. Samo gięcie jest wykonywane na prawie wszystkich maszynach do kucia na zimno. Proces gięcia można prześledzić podczas produkcji przedmiotu na maszynie Snail. Najpierw koniec obrabianego przedmiotu umieszcza się w specjalnym szablonie, a następnie wygina pod określonym kątem. Prace te wykonujemy na maszynie Ślimak.
Pokrętny. Ta technologia kucia polega na skręcaniu przedmiotu obrabianego wzdłuż jego osi. W kuciu na zimno proces ten można zaobserwować za pomocą maszyny Twister, na której powstają różne drążki skrętne. Aby to zrobić, jeden koniec przedmiotu obrabianego umieszcza się w imadle, a drugi koniec obraca się wzdłuż osi. Osobno warto wyróżnić element Latarka. W tym celu stosuje się dwa lub więcej prętów, które są najpierw skręcane wzdłuż osi, a następnie ściskane wzdłuż osi, w wyniku czego pręty rozchodzą się na boki w określonym miejscu.
Montaż wszystkich elementów w jedną konstrukcję wykonywane przez spawanie na specjalnym stole montażowym. Dziś spawarka jest ogólnodostępna i jest niezbędnym narzędziem dla nowoczesnych kowali. Domowe kucie na zimno jest dość powszechne wśród początkujących rzemieślników i prywatnych przedsiębiorców. Nie wymaga specjalnej wiedzy, umiejętności i dużych pomieszczeń do pracy.
Zrób to sam kucie na zimno: lekcja wideo
Zrób to sam kucie metalu na gorąco
W porównaniu do kucia na zimno, ręczne kucie na gorąco jest znacznie trudniejsze i wymaga od mistrza doświadczenia w posługiwaniu się narzędziem oraz dobrej sprawności fizycznej. Praca odbywa się w kilku etapach: wykonanie szkicu lub rysunku, zakup materiałów i kucie.
W rzeczywistości różnica między kuciem na gorąco i na zimno tkwi w procesach technologicznych obróbki metali. Po pierwsze dotyczy sposobu przetwarzania. Po drugie, do kucia na gorąco można użyć prawie wszystkich metalowych półfabrykatów. Ale dla wygody zwyczajowo używa się gotowych prętów kwadratowych i okrągłych. Po trzecie, w artystycznym kuciu na gorąco nie ma ram na elementy gotowego produktu. Oczywiście można trzymać się tworzenia klasycznych elementów kucia – loków, łap, daszków i innych rzeczy, ale kucie na gorąco pozwala wykorzystać pełen potencjał wyobraźni mistrza, co otwiera nieograniczone możliwości. Wszystkie wyroby metalowe kute na gorąco powstają przy użyciu następujących technologii obróbki metalu: spęczanie, ciągnienie, gięcie, skręcanie, cięcie, grawerowanie wzorów i wypełnianie reliefowe.
Projekt stosowany w kuciu metalu w celu zwiększenia przekroju całego przedmiotu obrabianego lub jego części. Podczas kucia, w zależności od potrzeb, przeprowadza się całkowite lub miejscowe nagrzewanie przedmiotu obrabianego w celu spęczania.
Kaptur jest zwiększenie długości przedmiotu obrabianego poprzez zmniejszenie jego przekroju. Można to zrobić albo uderzając młotem kowalskim lub hamulcem ręcznym, albo tocząc metal między wałami maszyny. W przeciwieństwie do kucia na zimno tworzenie szczytów z rysunkiem wymaga dokładnych i dokładnych uderzeń.
pochylenie się. Ta operacja jest wykonywana, aby nadać przedmiotowi wygięty kształt. Jednocześnie należy wziąć pod uwagę, że gięcie grubych detali może prowadzić do ich zniekształcenia, a w celu nadania oryginalnego kształtu konieczne jest wykonanie szkicu. Do gięcia przedmiotu stosuje się różne ostrogi, róg kowadełka, młotki kształtowe i przewodniki.
Pokrętny. Ta technologia kucia polega na skręcaniu przedmiotu obrabianego wzdłuż jego osi. Podobnie jak w przypadku kucia na zimno, przedmiot obrabiany jest mocowany w imadle i obracany. Ale w przeciwieństwie do kucia na zimno, możliwe jest lokalne podgrzanie przedmiotu, co umożliwia łatwe miejscowe skręcanie.
Technologie kucia, takie jak ciąć, wzór nacinania oraz wyściółka reliefowa stosowany w kuciu artystycznym za pomocą dłut. Krawędzie gorących półfabrykatów w zależności od projektu są przycinane i skręcane szczypcami. Ponadto, gdy przedmiot jest gorący, na jego powierzchni wypychany jest inny wzór.
Podczas kucia metalu na gorąco ważne jest poznanie reżimów temperaturowych ogrzewania. Pomoże to w lepszym przetwarzaniu metalu. Kucie metali żelaznych odbywa się w temperaturze 800 - 1250 °C. Oczywiście nie da się zmierzyć gorącego przedmiotu termometrem, a do określenia temperatury trzeba będzie kierować się jego kolorem. Poniższa tabela przedstawia temperatury i kolor półfabrykatu żelaznego.
Kucie na gorąco: lekcja wideo
Kucie metali „zrób to sam” to dość ekscytujący biznes, który wymaga ciągłego doskonalenia. Dotyczy to przede wszystkim tworzenia różnorodnych elementów artystycznych i dekoracyjnych. Ci, którzy dopiero zaczęli kuć, będą musieli ciężko pracować, aby ich praca miała idealny kształt i wysoką jakość.
Przyjrzyjmy się rodzajom urządzeń i kształtom, które można uzyskać za ich pomocą. Przygotowaliśmy dla Ciebie rysunki i filmy tematyczne. Zastanowimy się również nad kolejnością produkcji maszyny do kucia na zimno własnymi rękami.
Jeśli dopiero rozpoczynasz warsztat kucia na zimno i chcesz uniknąć wysokich kosztów, to tworzenie własnych maszyn i osprzętu pomoże Ci stworzyć własną małą firmę bez nadmiernych kosztów.
Podstawowe wyposażenie i maszyny
Maszyny do kucia na zimno przeznaczone są głównie do gięcia po łuku lub pod kątem, a także do skręcania. Mogą być zasilane ręcznie lub elektrycznie.
Główne typy maszyn i urządzeń do kucia na zimno:
- „Gnutik”
- "Tornado"
- "Ślimak"
- "Globus"
- "Fala"
- "Latarka"
Urządzenie „Gnutik”
Zakupiony lub wykonany samodzielnie „Gnutik” to uniwersalne urządzenie, które pozwala uzyskać łuk lub kąt z pręta. Jest to podstawa z suwakiem, na której zamocowany jest ogranicznik o kącie (90° lub inny w zależności od potrzeb) oraz dwa cylindryczne stałe ograniczniki. Przesuwając suwak i ogranicznik narożny, pręt wygina się pod kątem. Aby uzyskać łuk, przewidziany jest trzeci cylinder, obracający się po stronie przeciwnej do ogranicznika narożnego.
Oprawa może być wykonana na platformie poziomej lub pionowej.
Aksonometria urządzenia „Gnutik” - układ pionowy
Aby zeskalować wymiary, oto rysunek dolnego paska tego „Gnutika”.
Dolny pasek
To urządzenie jest uniwersalne. Za pomocą dysz można nie tylko zginać, ale także wycinać i dziurkować otwory. Ale to będzie następny krok.
Uzyskanie łuku na „Gnutiku”
Zdobycie zakrętu na „Gnutiku”
Wygląda jak domowy „Gnutik”:
Urządzenie „Twister”
"Twister" - narzędzie do skręcania prętów, przeważnie o przekroju kwadratowym, wzdłuż osi podłużnej. To proste urządzenie może być ręczne i elektryczne. Zasada działania: oba końce pręta są zamocowane, następnie jedno mocowanie zaczyna się obracać, skręcając metal do wymaganego kształtu.
Wygląd zakupionej instrukcji „Twister”
Zobacz zdjęcie domowej roboty „Twister” z napędem elektrycznym, zmontowanej przy użyciu zużytego sprzętu elektrycznego:
Do produkcji „Lanternów” i „Stożków” jest specjalna maszyna, ale na początek możesz również użyć „Twister”, jak pokazano na filmie (po angielsku, ale wszystko jest bardzo jasne).
Wideo 1. Jak zrobić puste miejsce dla „Latarki” w „Twister”
Urządzenie „Ślimak”
Narzędzie Ślimak jest przeznaczone do tworzenia zawijasów (lub spiral) i „walut” (części w kształcie litery S). Istnieje wiele wzorów.
Jedna z opcji projektowych: 1 - lemiesz ślimakowy; 2 - podstawa maszyny; 3 - rolka dociskowa; 4 - dźwignia sterowania rolką dociskową; 5 - mocowanie podstawy; 6 - palec do mocowania lemieszy; 7 - rowek na rolkę dociskową; 8 - oś dźwigni sterującej; 9 - sprężyna do dociskania wałka; 10 - zacisk do przedmiotu obrabianego; 11 - wiodący udział ślimaka; 12 - główna oś; 13 - dźwignie
Wynik powinien wyglądać mniej więcej tak:
Kolejna lekka konstrukcja do gięcia produktów walcowanych o przekroju do 12 mm:
1 - segment ślimaka; 2 - ekscentryczny; 3 - uchwyt; 4 - podstawa; 5 - płozy prowadzące; 6 - oś; 7 - suwak; 8 - nakrętka osi; 9 - oś montażowa rolki; 10 - wałek; 11 - oś napędowa; 12 - ekscentryczny przewodnik; 13 - środkowy segment ślimaka; 14 - ekscentryczna jagnięcina; 15 - główna noga; 16 - kołek łączący segmenty ślimaka; 17 - śruba korekcyjna; 18 - ucho łączące segmentów ślimaka
Często osprzęt „Ślimak” jest wykonywany na podporze, zwłaszcza jeśli trzeba zginać grube produkty walcowane.
Kilka przydatnych filmów na temat domowych maszyn „Ślimaki”.
Opcja z masywną podstawą na podporze:
Wideo 2. Tworzenie bazy
Wideo 3. Robienie ślimaka
Wideo 4. Obsługa maszyny
Opcja mocowania stołu:
Wideo 5. Część 1
Wideo 5. Część 2
Omówimy te struktury bardziej szczegółowo poniżej.
Urządzenie „Glob”
Takie urządzenie wygląda jak kątomierz szkolny i jest przeznaczone do wykonywania łuków o dużym promieniu gięcia z paska, kwadratu, koła lub sześciokąta. Najpierw jeden koniec przedmiotu jest mocowany za pomocą zagięcia, a następnie jest wyginany na całej długości zgodnie z szablonem. Zasada działania jest nieco podobna do działania maszyny do konserwowania.
Wygląd urządzenia
Wideo 6. Pracuj nad „Globem”
Wykorzystując wyłącznie siłę mięśni, można wykonać łuk o dużej średnicy na szablonie przykręconym lub przyspawanym do stołu warsztatowego. Dobrze jest zgiąć na nim pasek, cienkościenną rurę itp.
Urządzenie „Fala”
Możesz uzyskać produkty w kształcie fali z przedmiotu o przekroju okrągłym, kwadratowym, sześciokątnym lub rurki za pomocą uchwytu „Wave”. Odkształcenie przedmiotu obrabianego następuje między pionowymi rolkami poprzez przewijanie.
Oprawa falowa i produkty wynikowe
Wideo 7. Urządzenie w akcji
Urządzenie „Latarka”
Na tej maszynie wykonuje się wykroje elementów „Lantern” lub „Stożki”, które mogą składać się z 4, 6, 8 lub więcej prętów. Zgodnie z zasadą działania maszyna jest podobna do Twistera, ale tutaj detale są zagięte wokół wału prowadzącego, co tworzy bardziej poprawną i dokładną konfigurację produktu.
Urządzenie „Latarka”
Wideo 8. Praca urządzenia do tworzenia „Latarki”
Urządzenie do kucia na zimno elementu „Clamp”
Element do kucia na zimno „Clamp” jest przeznaczony do mocowania między sobą innych elementów konstrukcyjnych.
Urządzenie do gięcia „Zacisku” można wykonać według załączonych rysunków.
Urządzenia do wykonywania „kurzych łapek”
"Houndstooth" - spłaszczenie z zastosowaniem pięknych nacięć na końcach wykrojów dla nadania elegancji projektowi lub zmniejszenia grubości dla różnych połączeń.
Końce elementów ozdobione „gęsią stopką”
Operację tę można wykonać za pomocą obrabiarki z matrycą lub uchwytem i ciężkiego młota kowalskiego na kowadle. Obie opcje udostępniamy w formie filmów.
Wideo 9. Maszyna do robienia „gęsiej łapki”
Wideo 10. Urządzenia do kucia „kurzych łapek”
Wideo 11. Szczegółowy proces tworzenia pieczątek
Poniżej znajduje się maszyna do walcowania do wykonania tej samej operacji.
Maszyna do toczenia "gęsiej stopki" (rozstaw rolek jest regulowany). Materiały do walcarki: koła zębate i wały - używane części zamienne do kombajnów zbożowych
Zasada działania
Produkcja „Ślimaka” z napędem
Elektryczny „ślimak” ułatwia produkcję loków i „waluty”. Jest to szczególnie cenne, gdy praca nie jest „dla duszy”, ale do wytwarzania dużej liczby tego samego rodzaju produktów w strumieniu przy pracy na zamówienie.
Poniżej przedstawiamy etapy montażu maszyny do gięcia pręta o maksymalnym przekroju 10x10 mm. Silnik 0,5 kW/1000 obr/min pracuje na granicy swoich możliwości. Wykonuje 6 obrotów wału na minutę. Segmenty ślimaka są obrabiane z okrągłego półfabrykatu St.45 bez obróbki cieplnej o wysokości 25 mm i grubości 20 mm. Ślimak osadzony jest na wale na łożyskach tylnego koła motocykla - 7204. Rolka nośna jest sztywno zamocowana w rowku. Koła pasowe są montowane między silnikiem a skrzynią biegów.
Poniżej znajdują się rysunki segmentów ślimaka.
Ślimak element 1
ślimak 2
Ślimak element 3
Centralny element ślimaka
W przypadku masywniejszego pręta (od 12 mm) moc silnika powinna przekraczać kilowat. Poniższe fotografie przedstawiają maszynę z silnikiem o mocy 2,2 kW, 1000 obr/min, dającą moc na wale około 10 obr/min. Jest to maszyna do użytku profesjonalnego. Zastosowano zużytą skrzynię biegów, matrycę wycięto z detalu o grubości 30 mm - najbardziej czasochłonny proces.
Do kucia na zimno potrzebne będzie również kowadło i młotek. Kuźnia nie jest potrzebna, wymagana jest tylko do kucia na gorąco.
Rada! Przed rozpoczęciem pracy narysuj pełnowymiarowy szkic przyszłego projektu. Pomoże to dopasować elementy i nie pomylić się podczas montażu.
Wykonywanie gięcia do kucia na zimno jest strukturalnie dość proste i można je łatwo wykonać niezależnie. Poniżej znajduje się przewodnik krok po kroku.
Odkształcanie plastyczne na zimno metali i stopów to wygodna w gospodarstwie domowym metoda uzyskiwania przestrzennych konstrukcji i profili. W końcu gięcie jako proces obróbki ciśnieniowej nie jest operacją energochłonną, a zatem nie wymaga urządzeń napędowych. Ręczna giętarka do gięcia taśm i prętów (zwana potocznie giętarką do kucia na zimno zrób to sam) jest prosta konstrukcyjnie i może być z łatwością wykonana samodzielnie.
Gięcie na zimno metali ciągliwych można przeprowadzić na trzy główne sposoby (schematy pokazano na rys. 1.a, 1.b):
- Swobodny, określony tylko przez skok narzędzia.
- Na przystankach zarówno w kierunku poziomym, jak i pionowym.
- Obrotowe rolki.
Ta ostatnia metoda stosowana jest tylko przy gięciu dużych blach i jest rzadko stosowana w codziennej praktyce. Dodatkowo urządzenie takiej maszyny, nawet prostej, będzie wymagało dużo wolnej przestrzeni w przydomowym warsztacie.
Częściej stosuje się zginanie swobodne (patrz rys. 1.a). W obecności kowadła kowalskiego lub imadła do jego wykonania nie jest potrzebny specjalny sprzęt: wystarczy zamontować listwę lub pręt w szczelinie między szczękami i kolejne uderzenia młotkiem, aby uzyskać wymagany kąt gięcia. Jednak ta technologia gięcia jest bardziej odpowiednia do zgrubnego gięcia metalu, ponieważ nawet na stalowych półfabrykatach działanie obciążenia udarowego pozostawia niepożądane ślady na powierzchni przedmiotu obrabianego - wgniecenia lub wgniecenia. Ponadto stały promień przejścia od pionowej szczeliny kowadełka lub szczeliny szczęki do głównej płaszczyzny roboczej narzędzia eliminuje konieczność często koniecznej regulacji promienia gięcia. Inną wadą swobodnego gięcia jest to, że nie uwzględnia elastycznych właściwości metalu przedmiotu obrabianego. Mówimy o kącie sprężynowania - sprężystym efekcie końcowym materiału, który wyraża się spontanicznym spadkiem początkowo ustawionego kąta gięcia. W tym przypadku promień sprężyny jest parametrem zależnym od materiału giętego przedmiotu. Dlatego należy to wziąć pod uwagę jeszcze przed rozpoczęciem gięcia. Ręczne dostrajanie końcowego kąta „na oko” nie wpływa na jakość gotowego produktu i utrudnia późniejszy montaż konstrukcji, w schemacie której znajdują się gięte elementy.
Gięcie wzdłuż ograniczników to najbardziej zaawansowana technologicznie metoda gięcia na zimno detali o stosunkowo niewielkiej szerokości. Zasada takiego gięcia polega na tym, że oryginalną taśmę lub metalową listwę umieszcza się w specjalnym uchwycie, w którym znajdują się zaciski do równoległego ustawienia przedmiotu obrabianego, a także ograniczniki narzędzia do gięcia. Ponieważ takie narzędzie może być wymienne, a jego skok jest stosunkowo łatwy do regulacji, ta metoda gięcia na zimno w domu jest najbardziej odpowiednia. Schemat metody pokazano na ryc. 1.b.
Dlatego do wysokiej jakości gięcia półwyrobów na zimno wymagane jest proste urządzenie zwane giętarką do kucia na zimno. Jest dość kompaktowy i można go zainstalować na dowolnym stole warsztatowym ślusarza.
Schemat gynika i kolejność prac nad nim
Rozważ projekt urządzenia na przykładzie pokazanym na ryc. 2. Najprostsze urządzenie do kucia na zimno składa się z
Podstawa mocowana do stołu/stołu warsztatowego z ruchomą smyczą, która powoduje zginanie;
Dźwignia poruszająca smyczą;
Limba ze wskaźnikiem kąta obrotu dźwigni;
Wymienne rolki o różnych kątach gięcia;
Regulowane przekładki i szczęki zaciskowe, które utrzymują część na miejscu.
Kolejność etapów wytwarzania zagięcia do kucia na zimno jest następująca. Urządzenie mocuje się do stołu/stołu warsztatowego lub instaluje na nim. Do gięcia metali, które wymagają znacznego wysiłku, lepiej jest zamontować oprawę na stałe, na którą przewidziano otwory w narożniku podporowym. Suwak umieszczony jest w prostokątnej stalowej ramie, której wewnętrzne powierzchnie muszą być szlifowane. Na górnej płaszczyźnie suwaka zainstalowane są następujące części:
- Wymienny stempel, na powierzchni roboczej którego znajdują się wszystkie najczęściej używane opcje gięcia przedmiotów obrabianych: po promieniu, po łuku, z prostym gięciem itp.
- Dźwignia, za pomocą której możesz odwrócić suwak.
- Suwak zatrzymuje się w ramie osprzętu.
Po zainstalowaniu wymiennego narzędzia rama jest przykręcana do powierzchni nośnej łuku, po czym na górnej płaszczyźnie montowane są dwie rolki. Lepiej jest, jeśli rolki mogą poruszać się wzdłuż ramy: pozwoli to na gięcie przedmiotów o różnej grubości lub średnicy. Aby to zrobić, rowki do mocowania rolek mają owalny kształt, licząc na pewien zakres zmian grubości przedmiotu obrabianego. Osie rolek muszą umożliwiać swobodny obrót: zmniejszy to siłę gięcia i zapobiegnie zaciskaniu rolek podczas gięcia produktów wykonanych z mocniejszych metali.
Aby poprawić dokładność gięcia przy wytwarzaniu narzędzia kuźniczego, na narożniku odniesienia często montuje się ramię z podziałkami stopniowanymi pod kątem zgięcia (z uwzględnieniem sprężystości metalu).
Po zamocowaniu przedmiotu obrabianego należy stopniowo przesuwać dźwignię, aż zbliży się do przedmiotu obrabianego, a następnie skorygować jego położenie między rolkami a suwakiem i wyginać do uzyskania wymaganego kąta. Aby ułatwić proces powrotu suwaka do pierwotnej pozycji, można go wyposażyć w sprężynę powrotną. Jego siłę dobiera się biorąc pod uwagę 20-25% siły zginającej. Siłę tę można ustawić za pomocą istniejącego dynamometru lub przy użyciu przybliżonej zależności:
P = 0,25bSσ w, gdzie:
b - szerokość paska (lub średnica pręta);
S to grubość giętego materiału;
σ in - granica czasowej wytrzymałości materiału przedmiotu obrabianego (patrz tabela):
Zatem funkcjonalność gięcia będzie determinowana przez obecność wymiennych stempli, możliwość regulacji położenia przedmiotu obrabianego przed gięciem, a także skalę rozmiaru, która ustala kąt gięcia.
Jakość gięcia na zakręcie domowej roboty
Ten czynnik jest określony przez:
- Być może dokładniejsze rozliczenie odskoku. Uważa się, że metale i stopy o wysokiej ciągliwości (zaliczają się do nich aluminium klasy AD, miedź M0 i M1, a także gatunki stali niskowęglowej) mają współczynnik sprężynowania w zakresie 4-8%, a stale o wyższym procencie węgiel (ponad 0,20 -0,25%), a także większość mosiądzów różni się sprężynowaniem do 10-15%;
- Początkowa twardość materiału przedmiotu obrabianego. Wyżarzony metal praktycznie nie sprężynuje, podczas gdy stal / stop po hartowaniu lub wstępnym odkształceniu (prostowanie, walcowanie odpuszczające, ciągnienie itp.) może zwiększyć swoje właściwości elastyczne o 20-40%;
- Jakość czyszczenia powierzchni przedmiotu obrabianego z rdzy, zgorzeliny i innych zanieczyszczeń powierzchniowych.
Jeśli zwolnienie przedmiotu obrabianego nie jest możliwe, gięcie odbywa się pod większym kątem, biorąc w ten sposób pod uwagę elastyczne właściwości metalu.
Ważna jest również wstępna regulacja zgięcia, na przykład brak luzu podczas ruchu dźwigni, niezawodność instalacji i mocowania wymiennego stempla, chropowatość materiału rolek.
Jeśli chcesz uzyskać dokładniejsze informacje o konstrukcji urządzenia lub wykonać je samodzielnie, możesz skorzystać z rysunku urządzenia przeznaczonego do gięcia pręta (patrz ryc. 3).
Zmiana danego urządzenia do gięcia również taśm i wykrojów jest prosta: wystarczy zwiększyć wysokość rolek 14 i zwiększyć długość dźwigni obrotowej 2.
Film z budowy domowej roboty gnicka można obejrzeć tutaj:
Produkcja tego urządzenia do kucia na zimno metali i stopów ciągliwych pozwala na zwiększenie asortymentu samodzielnie wykonanych wyrobów, poprawę ich jakości i zmniejszenie złożoności pracy.
Sektor prywatny każdego miasta charakteryzuje się dużą ilością eleganckich wyrobów metalowych. Są to metalowe, wzorzyste bramy, piękne ławki, nietuzinkowe balustrady i inne ozdobne ozdoby. Produkty kute nadają pewną estetykę wyglądowi witryny i domu. Wiele osób uważa, że stosowanie metalowych opraw kutych jest bardzo drogie. Lecz nie zawsze tak jest.
Takie produkty powstają przez kucie na zimno. Jeśli kupisz je w sklepie, możesz oczywiście rozłożyć dość dużą kwotę. Dlatego doświadczeni rzemieślnicy własnoręcznie wykonują maszynę do kucia na zimno. Co więcej, jeśli ktoś lubi robić coś samodzielnie, to urządzenie przyda się w gospodarstwie.
A także, angażując się w kucie artystyczne, otrzymujesz dobry dochód. Przecież marnotrawstwo produkcyjne i koszt wstępnej aranżacji są niewielkie. Dlatego sprawy kowala zajmującego się kuciem na zimno mogą szybko iść w górę. Wykonanie kucia, ewentualnie w garażu lub szopie. W związku z tym nie jest wymagany czynsz.
Pojęcie kucia na zimno
Proces kucia na zimno różni się od kucia na gorąco prostotą i bezpieczeństwem procesu. Metal nie jest narażony na działanie wysokich temperatur. W porównaniu z tłoczeniem proces ten oznacza prawie całkowitą eliminację przepływu metalu. Jeśli weźmiemy pod uwagę kucie na zimno, z punktu widzenia samego procesu kucia, to jest to proces nitowania elementów siłą uderzenia.
W rezultacie zwiększa się wytrzymałość warstwy zewnętrznej, podczas gdy część wewnętrzna nadaje ogólną wiązkość i wytrzymałość na pękanie. Oczywiście sama procedura kucia jest bardzo długa. Dlatego warto bardziej szczegółowo opowiedzieć o pewnej gałęzi kucia na zimno zwanej kuciem artystycznym.
Jest to również w istocie kucie na zimno, a termin „kucie na zimno” będzie używany w przyszłości. Polega na różnych gięciach metalowych źródeł. Struktura metalowej podstawy nie ulega zmianie. Nie zmieniają się również właściwości fizyczne i mechaniczne.
Kucie na zimno polega na formowaniu różnorodnych skręconych elementów i zagięć. Takie wzorzyste elementy wykonujemy na konkretnej instalacji. Ponadto napęd tych instalacji dzieli się na ręczny i elektryczny. Przy dużym nakładzie pracy lepiej jest używać maszyn z napędem elektrycznym, aby zwiększyć szybkość wykonania.
Instalacje ręczne mogą być wykorzystane do produkcji następujących artykułów dekoracyjnych:
- Konstrukcje okienne.
- Komponenty do produkcji balustrad.
- Krzesła, ławki.
- Nogi do mebli.
- Elementy dekoracyjne do bram, bram.
- Szczegóły dotyczące kominków.
Jeśli chodzi o materiał wyjściowy używany do kucia, stosuje się różne rodzaje: aluminium, miedź. Możesz także użyć stopów - duraluminium, stali, mosiądzu, stopu magnezu, stopu niklu.
Zalety metody
W porównaniu z innymi metodami wytwarzania wyrobów metalowych, kucie na zimno ma szereg zalet. Obejmują one:
- Ogrzewanie metalu nie jest potrzebne, co umożliwia uproszczenie procesu produkcyjnego z powodu braku pieca, utrzymującego określoną temperaturę.
- Bezpieczeństwo procesu.
- Łatwość wykonania urządzeń do kucia na zimno.
- Możliwość korekty produktu wykonanego dzięki właściwościom mechanicznym.
- Możliwość wytwarzania urządzeń do wytwarzania identycznych produktów ze standardowymi krokami.
- Oszczędność czasu i pieniędzy podczas pracy.
Obecność tych zalet sprawia, że technologia kucia na zimno jest powszechna.
Rodzaje sprzętu
Istnieje wiele rodzajów maszyn do kucia na zimno. Ustanowiono następujące kategorie:
- Gnutik - przyczynia się do wytwarzania metalowych łuków, które wyginają się pod dokładnym kątem.
- Ślimak - urządzenie, które pozwala uformować spiralę prętów.
- Twister - pozwala uzyskać bardziej skomplikowaną spiralę wzdłuż osi.
- Ring - mechanizm gięcia do produkcji pierścieni i owalnych kształtów.
- Fala - instalacja przeznaczona do gięcia prętów w falę.
- Prasa - umożliwia przeprowadzenie procesu spłaszczania przedmiotu.
- Młotek i kowadło to narzędzia pomagające korygować błędy.
Wykonanie maszyny do kucia na zimno dla każdej z wymienionych kategorii własnymi rękami jest dość łatwe. Wymagane są tylko niektóre narzędzia i materiał metalowy. Co więcej, prawie nie są potrzebne żadne pieniądze.
Wykonanie mechanizmu do kucia na zimno
Uniwersalna maszyna do kucia na zimno jest prawie niemożliwa do wykonania własnymi rękami. Niezbędne jest wykonanie osobnego formularza mechanizmu wydawania przedmiotów.
Podczas produkcji instalacji wymagane jest dobranie następujących materiałów:
- blacha (preferowana grubość 4-5 mm);
- pręty zbrojeniowe, rury profilowe;
- rama dla stabilności urządzenia do kucia na zimno;
- silnik elektryczny i skrzynia biegów w przypadku maszyny napędzanej.
Oczywiście produkcja opraw nie obejdzie się bez narzędzi. Warto mieć przy sobie szlifierkę kątową lub pilnik metalowy, spawarkę, kamień lub papier szmerglowy, imadło i szczypce, a także ołówek, taśmę mierniczą i papier.
Dla początkującego mistrza najłatwiej jest zrobić domową maszynę do kucia na zimno w kształcie ślimaka. Dzięki niej powstają różne formy metalowych prętów do bram i ogrodzeń. Popularny jest również typ instalacji skrętnej. Inne formy obrabiarek można wykonać po zdobyciu doświadczenia z prostymi ustawieniami.
Przyjrzyjmy się szczegółowo produkcji „ślimaka”. To urządzenie przyczynia się do uzyskania różnorodnych konfiguracji spiral, loków, pierścieni. Prosta konstrukcja tego sprzętu przyczynia się do wygodnej obsługi i łatwego dostępu do obrabianego przedmiotu. Przebieg procesu jest możliwy, jeżeli:
- Pręty metalowe.
- Liście i paski ze stali.
- rury profilowe.
- Spawarka.
- Szlifierka kątowa i szczypce.
Aby wykonać domowe maszyny używane w trakcie kucia na zimno, wskazane jest narysowanie schematu lub szkicu przyszłego osprzętu. Początkowo do rysowania rysunku wybierany jest papier milimetrowy.
Następujące etapy pracy:
- Obraz spirali z trzema zwojami jest nakładany na kartkę papieru. Wymiary muszą odpowiadać średnicy wzmocnionego pręta, pod warunkiem, że pasuje on do gwintu. Najlepiej użyć rozmiaru 10 mm. A także linie powinny być narysowane w oparciu o grubość stali, a odległość wewnątrz spirali powinna wynosić 12-13 mm.
- Następnie za pomocą stalowej szlifierki musisz wykonać okrąg o wymaganej średnicy. Jeśli chcesz użyć zdejmowanych kółek, powinieneś wziąć niecienki materiał źródłowy (grubość 4-5 mm), aby ułatwić wymianę.
- Opatrunek mocnego łóżka, które stoi stabilnie na powierzchni podłogi. Ogólnie rzecz biorąc, można betonować nogi, aby uzyskać trwalszą konstrukcję. Ważnym warunkiem jest to, aby obwód ramy był większy niż wymiary koła roboczego.
- Do ramy przyspawany jest metalowy pręt, na którym zamontowane jest urządzenie nośne. Sterowanie ręczne polega na przyspawaniu koła do ramy. W tej sytuacji gięcie metalu jest znacznie łatwiejsze niż podczas procesu obracania.
- Naprawiamy ślimaka na kole. Ślimak dzieli się na trzy części. Końcówka ma wysokość 1 cm w oparciu o grubość prętów. Do następnej części spirali dodaje się 1 cm, co oznacza, że drugi obrót będzie wynosił 2 cm, a trzeci - 3 cm.Jeśli uzyskasz więcej zwojów, powinieneś zwiększyć szczegóły spirali.
- Jeśli konieczne jest wykonanie wymiennych okręgów, wówczas wymienne części są przyspawane do okręgu zgodnie ze szkicem.
- Jeśli istnieje wymienny ślimak, należy zmierzyć położenie każdego rodzaju i przyspawać kołki do każdego elementu. W takim przypadku w kole powstaje luka dla określonego szczegółu.
- Aby uzyskać podrobiony produkt, musisz zacząć od cewki centralnej. Konieczne jest mocne zamocowanie pręta za pomocą imadła lub innego narzędzia.
- Na koniec musisz zrobić dźwignię z dwóch rur profilowych (średnica 15-20 mm). Są spawane za pomocą zworek, których długość jest odległością od środka łożyska do górnego punktu koła plus 5 cm, a następnie jest przyspawana do części łożyska. Do dolnej części dźwigni, która jest wyciętą częścią okrągłą, przyspawany jest pręt o długości odpowiadającej długości najwyższej części ślimaka. Bębenek do gięcia jest spawany prostopadle do obszaru koła.
W ten sposób maszyna domowej roboty jest gotowa. Możesz zacząć produkować potrzebne elementy. Aby to zrobić, pręt jest zamocowany, a następnie spoczywa na nim lufa i rozpoczyna się proces gięcia.
Wideo: zrób to sam maszyna do kucia na zimno.
Maszyna skrętna
Innym popularnym urządzeniem, takim jak maszyna do kucia na zimno zrób to sam, jest drążek skrętny. Służy do kucia spiral w kształcie węża. Do wykonania instalacji potrzebne będą:
- Blacha stalowa.
- Podwójna belka.
- Wice.
- Szczegóły dotyczące elementów złącznych.
- Szlifierka kątowa.
- Spawalniczy.
- Skrzynia biegów i silnik elektryczny.
Aby samodzielnie wykonać tę instalację, musisz wykonać określone kroki:
- Na początek wymagana jest belka, do jednej jej części przyspawana jest blacha.
- Następnie do stali przyspawane jest imadło, które należy jeszcze przymocować śrubami i nakrętkami.
- Płytki są przymocowane do imadła, aby zmniejszyć ryzyko wyskoczenia przedmiotu po pociągnięciu.
- Po drugiej stronie belki zamontowane są rolki zabezpieczające platformę. Ponadto urządzenie z rolkami powinno znajdować się na tej samej wysokości, co konstrukcja imadła.
- Na instalacji umieszcza się imadło z ruchomymi częściami.
- Do wykonania obrotu dołączony jest stalowy uchwyt. W rezultacie przedmiot zostanie wygięty.
- Następnie podłącza się silnik elektryczny, a cały układ osłania stalowa obudowa.
W ten sposób wykonana konstrukcja jest maszyną z ruchomym i stałym blokiem. Ta metoda produkcji maszyny jest dość prosta, ale wymaga pewnego wysiłku w pracy.
Przed wieloma osobami zainteresowanymi metalowymi przedmiotami dekoracyjnymi pojawia się pytanie - jak zrobić maszynę do kucia na zimno własnymi rękami. Po szczegółowym przestudiowaniu tego problemu możesz, bez doświadczenia i warsztatu, zająć się pozyskiwaniem różnych produktów metalowych do celów krajobrazowych.
Maszyna jest po prostu wykonana przy użyciu narzędzi i materiałów, które prawie każdy ma. Co więcej, Twój sprzęt można dostosować do każdego rodzaju produktu.