Монтаж подшипников качения. Как собирают подшипники: технология Демонтаж подшипниковых узлов
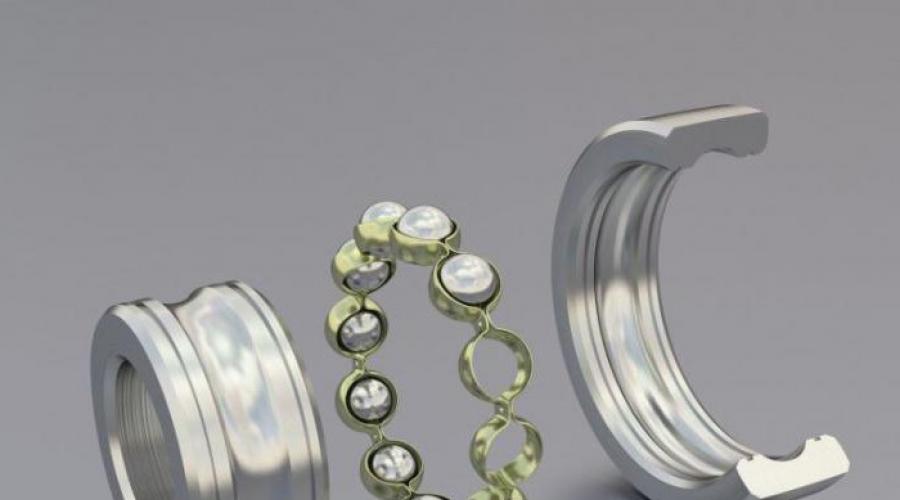
Читайте также
Установка подшипников гарантирует длительную нормальную работу узла только при сочетании следующих основных факторов:
- отсутствие загрязнений;
- необходимый уровень технической компетенции и слесарных навыков исполнителя;
- наличие соответствующего инструмента и оснастки;
- надлежащая подготовка монтажных мест и подшипника;
- соблюдение порядка и правил сборки;
- смазка;
- проверка качества выполненных работ.
Предварительная подготовка к установке подшипников
Порядок подготовки монтажных мест и общеподготовительных мероприятий:
- подготовить рабочее место, максимально снизив риск загрязнения и запыления в процессе работы;
- подготовить измерительный и монтажный инструмент, очистить его;
- осмотреть и очистить посадочные места под установку подшипников: замятия заплечиков, забоины, заусенцы, наклеп, небольшие вспучивания металла следует аккуратно убрать шабером, напильником, мелкой наждачной бумагой или с помощью станочного парка;
- промерить посадочные места и записать результаты;
- проверить валы на прямолинейность оси (отсутствие изгиба): проверку целесообразно проводить при вращении вала в центрах с помощью специальных приборов (увеличение эксцентриситета от сечения к сечению в направлении от края к середине указывает на искривление вала и ведет к необходимости его замены);
- по результатам осмотра и замеров посадочного места установить его соответствие требованиям ГОСТ 3325 по полям допусков, посадкам, требованиям по шероховатости, отклонениям формы и расположения;
- при необходимости – исправить посадочные места или заменить детали на новые с необходимыми параметрами;
- очистить каналы для подвода смазки от стружки, пыли и других загрязнений, продуть их сжатым воздухом;
- приготовить смазку.
- на валу – микрометром;
- в корпусе (подшипниковых щитах) - индикаторным нутромером.
Замеры производятся в нескольких местах с тем, чтобы, помимо величины диаметра, установить величину овальности и конусности посадочного места. Размер определяется как среднее арифметическое трех измерений в каждой из плоскостей с поворотом последовательно на треть окружности (120°).
Подшипники монтируются на вал ротора и в корпус (подшипниковый щит) с определенным натягом или зазором. Разность между диаметром отверстия подшипника и диаметром вала в пользу первого называется зазором. Если же диаметр вала больше, чем диаметр отверстия подшипника, то разность между ними называется натягом. Характер и величина натяга или зазора при сопряжении двух деталей называется посадкой.
При анализе замеров следует помнить, что чаще всего, если технической документацией и конструкцией узла не предусмотрено иное, при установке подшипника одно его кольцо должно иметь прессовую посадку с натягом в 0,01-0,03 мм, а другое - посадку скольжения с зазором от 0 до 0,03-0,04 мм.
Прессовую посадку внутреннего кольца подшипника и скользящую наружного его кольца применяют в случаях, когда вращающейся деталью является вал (например, валы коробки перемены передач, главной передачи трансмиссии и др.).
Если деталь узла вращается на неподвижной шейке (например, на ступице колеса), то прессовую посадку должно иметь наружное кольцо подшипника, а скользящую - внутреннее.
При прессовой посадке кольца предупреждается износ вращающейся детали (шейки вала, ступицы и др.), а при скользящей посадке другого кольца оно может несколько проворачиваться, что устраняет одностороннюю нагрузку тел качения на кольцо, уменьшает его износ и повышает общий срок эксплуатации подшипника.
Встречаются и конструкции с одновременной посадкой и наружного, и внутреннего кольца, что следует учесть при интерпретации результатов замеров и подборе монтажной оснастки.
Посадочное место так же можно промерять специальным калибром нужного размера, при этом применять сам подшипник не рекомендуется.
Нормальная высота упорного бурта (заплечика) сопрягаемой детали должна быть приблизительно равна половине толщины кольца подшипника. Это необходимо для того, чтобы за незакрытую заплечиком поверхность боковины кольца можно было осуществить захват съемником для извлечения подшипника. Для фиксации в осевом направлении кроме заплечиков могут применяться распорные втулки, пружинные стопорные кольца, различные гайки и др.
Подготовка подшипника к установке
Если есть такая возможность, то под фактические размеры вала или корпуса следует произвести селективный подбор подшипника из нескольких. Выбор следует остановить на подшипнике, у которого размеры наружного и внутреннего колец в сочетании с реальными размерами посадочного места обеспечат необходимую посадку. Это позволит избежать чрезмерно свободной или недопустимо плотной посадки, а значит, избежать ненормальной работы подшипника, в т.ч. перегрева из-за уменьшения необходимого радиального зазора в нем.
Порядок подготовки подшипника к установке:
- извлечь подшипник из заводской упаковки для проверки (выполняется непосредственно перед установкой подшипника в узел);
- убедиться, что по маркировке и внешнему виду подшипник соответствует необходимому;
- провести предварительную проверку состояния путем осмотра: подшипник открытого типа не должен иметь видимых дефектов – цветов побежалости, ржавчины, трещин, забоин, царапин, должен быть полный комплект тел качения (шариков или роликов) и заклепок (или других соединительных элементов), сепаратор не должен иметь повреждений;
- у подшипников закрытого типа проверить отсутствие повреждений уплотнений или защитных шайб;
- провести промеры ширины, наружного и внутреннего диаметров подшипника специальным инструментом и удостовериться в соответствии посадочным местам;
- расконсервировать и промыть подшипник, если это прямо не запрещено его производителем;
- проверить от руки легкость хода: вращение должно быть плавным без заеданий (при этом следует помнить, что проворот колец открытых подшипников в сухом состоянии до промывки категорически не рекомендуется для исключения риска абразивного повреждения рабочих поверхностей качения из-за возможного присутствия загрязнений);
- провести замеры радиального зазора: для этого одно из колец подшипника закрепляют при горизонтальном положении оси и определяют зазор с помощью индикатора, смещая свободное кольцо под действием измерительного усилия в радиальном направлении в два диаметрально противоположных положения (при этом разница показаний индикатора является искомым значением радиального зазора);
- провести замеры осевого зазора, аналогично тому как это делалось при определении радиального зазора, только в этот раз замер производят при вертикальном положении оси: закрепить одно из колец, другое сместить в осевом направлении в два крайних положения под действием измерительного усилия и зафиксировать разность показаний индикатора;
- нанести смазку в достаточном количестве, если смазочный материал не нанесен производителем.
Расконсервация подшипника
Удаление поверхностного консервационного слоя производится салфеткой, не оставляющей ворс.
Тщательная расконсервация подшипника и его промывка выполняется с применением одного из следующих составов на выбор:
- разогретое масло с температурой около 80 градусов Цельсия;
- антикоррозионный раствор;
- бензин или керосин в чистом виде;
- смесь масла и бензина (керосина).
При использовании разогретого масла или антикоррозионного состава следует поддерживать их температуру на уровне около 80 °С, при этом повышение температуры выше 120 °С не допустимо, поскольку может произойти отпуск колец и тел качения, что резко снизит долговечность подшипника. Внешне отпуск не определить (цвета побежалости появляются при гораздо больших температурах), а фиксацией падения твердости посредством специального прибора на данном этапе никто как правило не занимается – именно поэтому стоит четко контролировать температуру моющего состава.
Расконсервация подшипника может проводится от 10 до 20 минут, в течение которых его полезно периодически встряхивать и немного прокрутить на финальном цикле полоскания, а после – высушить в месте, недоступном для пыли.
После высыхания подшипник для кратковременного хранения необходимо до момента монтажа положить в чистый полиэтиленовый пакет (мешочек) для защиты от пыли. Если до установки подшипника ожидается более двух часов, то его рекомендуется завернуть в чистую бумагу и убрать в картонную упаковку на хранение. Если время хранения после расконсервации превысило два часа, перед установкой подшипника рекомендуется провести его проверку на отсутствие следов коррозии.
Смазка подшипника должна выполняться перед монтажом в соответствии с рекомендациями производителя. Маркировка подшипника по отечественному формату может содержать сведения о требуемой пластичной смазке. Для ЦИАТИМ-201, которая принята по умолчанию стандартной смазкой подшипников, маркировка не применяется. Для остальных вариантов применяется маркировка с буквой «С»:
С1 – ОКБ-122-7
С2 – ЦИАТИМ-221
С3 – ВНИИНП-201
С4 – ЦИАТИМ-221С
С5 – ЦИАТИМ-202
С6 – ПФМС-4С
С7 – ВНИИНП-221
С8 – ВНИИНП-235
С9 – ЛЗ-31
С10 – № 158
С11 – СИОЛ
С12 – ВНИИНП-260
С13 – ВНИИНП-281
С14 – ФИОЛ-2У
С15 – ВНИИНП-207
С16 – ВНИИНП-246
С17 – ЛИТОЛ
С18 – ВНИИНП-233
С20 – ВНИИНП-274
С21 – ЭРА
С22 – СВЭМ
С23 – ШРУС-4
С24 – СЭДА
С25 – ИНДА
С26 – ЛДС-3
С27 – ФАНОЛ
С28 – Chevron SRI-2
С29 – РОБОТЕМП
С30 – ЮНОЛА
С31 – ЛИТИН
С32 – № 158М
С33 – ФИОЛ-2МР
С34 – ШРУС-4М
С35 – BERUTOX FE 18 EP
С36 – ВН-14
Производители подшипников некоторые типы своих изделий делают необслуживаемыми. На пары трения в таких подшипниках в заводских условиях со строгим контролем нанесена особая смазка на весь срок службы. Проводить расконсервацию подшипников описанным выше способом и самостоятельно смазывать не рекомендуется, так как бензин (керосин) или разогретое масло будут способствовать выносу заводского смазывающего состава, а добавление пластичной смазки приведёт к снижению эффективности заводской трибологической системы подшипника.
Закрытые необслуживаемые подшипники достаточно подвергнуть наружной протирке смоченной в бензине салфеткой, не оставляющей ворс.
Правильная установка подшипника
Гидравлические или ручные прессы обеспечивают плавную и ровную установку подшипников с минимальным риском повреждения деталей при использовании соответствующей оправки и аккуратности производства работ.
При установке подшипников монтажное усилие должно передаваться только через напрессовываемое кольцо:
- через внутреннее - при монтаже на вал;
- через наружное - при монтаже в корпус;
- на торцы обоих колец - если конструктивно подшипник одновременно монтируется на вал и в корпус.
При установке подшипников усилие запрессовки передается равномерно на всю окружность соответствующего кольца подшипника через специальный монтажный стакан. Если нет такого стакана, то можно использовать ровно отторцованую трубу из незакаленной стали с подходящими внутренним и наружным диаметрами. На свободном конце трубы следует установить заглушку со сферической наружной поверхностью, к которой и надлежит прилагать усилие. Разумеется, внутренняя поверхность трубы должна быть чистой и сухой для исключения попадания загрязнений любого вида в подшипник при выполнении работ.
Внутренний диаметр монтажного стакана (трубы) при установке подшипника должен быть немного больше отверстия кольца подшипника, на которое необходимо прилагать усилие, а наружный диаметр стакана (трубы) - немного меньше внешнего диаметра этого кольца.
Правильная установка подшипника выполняется в следующем порядке:
- посадочные места вала, корпуса и подшипника покрыть тонким слоем рабочей смазки (это может быть так же ЦИАТИМ, ЛИТОЛ или их аналоги);
- определить сторону, которой следует ставить подшипник (по общему правилу сторона, на которой нанесено заводское клеймо, должна быть снаружи);
- приставить монтажный стакан с упором в соответствующее кольцо подшипника;
- ровно по осям взаимно позиционировать сопрягаемую деталь, подшипник, монтажный стакан и рабочую плоскость пресса;
- убедиться в примерном соответствии взаимного положения проточек для подачи смазки в корпусах со смазочными отверстиями в наружных кольцах подшипников (необходимо там, где это предусматривает конструкция подшипникового узла);
- приложить небольшую нагрузку и убедиться в отсутствии перекоса в самом начале монтажа (на перекос укажет заедание подшипника, его нужно устранить);
- приложить достаточное по величине и ходу монтажное усилие, контролируя установку подшипника на место;
- игольчатые роликоподшипники монтировать по сборочным единицам либо на вал, либо в отверстие охватывающей детали;
- для установки игольчатых подшипников в отверстии охватывающей детали использовать монтажную втулку: поверхность отверстия покрыть тонким слоем смазки и вставить втулку (ее диаметр должен быть на 0,1-0,2 мм меньше диаметра шейки вала), а игольчатые ролики последовательно ввести в зазор (последний ролик должен входить свободно с зазором от 0,5 до 1 диаметра иглы), после чего устанавить ограничительные кольца и рабочей осью вытолкнуть монтажную втулку;
- разъёмные наружные кольца сферических подшипников скольжения, скреплённые болтами, устанавливать в исходном состоянии без ослабления затяжки болтов;
- конические роликоподшипники монтировать из отдельных сборочных единиц: внутреннее кольцо с роликами напрессовать на вал, наружное кольцо отдельно установить в корпус, а радиальный зазор между наружным кольцом и роликами отрегулировать (например, прокладками под крышку перед окончательной затяжкой винтов, если иной способ не предусмотрен конструкцией узла);
- в конструкциях с регулируемыми радиально-упорными и упорными шариковыми подшипниками после установки так же нужно произвести регулировку осевой «игры» подшипников;
- регулировка подшипников соответствующих систем производится до достижения параметров, установленных в инструкции на данную машину;
- установить стопорное кольцо, распорную втулку, сальник, прокладку, крышку или закрепить подшипник иным способом, как это предусматривает конструкция;
- завершить монтаж или надежно укрыть подшипниковый узел от попадания на него пыли и иных загрязнений на время до полной сборки.
Установка подшипников, как и указано было выше, выполняется с помощью ручного или гидравлического пресса. В исключительных случаях при отсутствии пресса для монтажа с небольшими натягами подшипников малых размеров допустимо нанесение несильных ударов молотком через монтажную трубу с заглушкой. При этом направление ударов должно максимально точно совпадать с осью напрессовываемого подшипника.
При установке подшипников необходимо тщательно следить за обеспечением равномерного, без перекоса, осевого перемещения напрессовываемого кольца. Перекос при монтаже приводит к образованию задиров на посадочной поверхности и неправильной установке подшипника, что сокращает срок его службы или может закончится повреждением.
Необходимые меры предосторожности для исключения попадания в подшипник загрязнений следует предпринимать на всех этапах: при подготовке подшипника и сопрягаемой детали, при установке и сопутствующих операциях, вплоть до полного окончания работ с собираемым узлом или агрегатом.
Так же необходимо выполнить все сборочные операции с учетом конструктивных особенностей таким образом, чтобы смазка нужного качества была в достаточном объеме, а в процессе эксплуатации не выбрасывалась работающей машиной и самопроизвольно не вытекала. Для этого подшипники качения закрывают крышками или устанавливают уплотняющие устройства - фетровые (войлочные) кольца, манжеты, защитные фланцы, защитные шайбы, лабиринтные уплотнители и т. п. За целостностью и надлежащей установкой этих компонентов следует проследить особо.
И, наконец, квалифицированная установка подшипников с соблюдением соосности, правильной посадкой, и регулировкой является еще одним ключевым фактором беспроблемной эксплуатации и залогом большого ресурса.
Установка подшипника нагревом
Нагрев зачастую значительно облегчает установку подшипников, так как при этом используется свойство металла расширяться при повышении температуры. Установка подшипников крупных габаритов в холодном состоянии невозможна, так как требуемое усилие значительно возрастает с увеличением размеров.
При установке подшипника на вал нагревается сам подшипник, при этом, как правило, достаточно разницы температур от 60 до 80 °C между окружающей средой и нагретым внутренним кольцом.
При установке подшипника в корпус нагреву подвергается последний. Температурная разница при этом находится в прямой зависимости от степени натяга и диаметра посадочного места. Обычно достаточно умеренного нагрева.
Как и в случае с расконсервацией и промывкой, температуру подшипника в любом случае не стоит поднимать выше 120 °C для предотвращения отпуска колец и тел качения с последующим существенным снижением срока службы. Нагрев подшипника так же не должен превышать температурные ограничения для сопряжённых компонентов, таких, например, как неметаллические уплотнения.
Нагрев подшипника производится в масляной ванне или с помощью индукционного нагревателя.
Современные специальные индукционные нагреватели, применяемые для установки подшипников с нагревом, обладают рядом преимуществ:
- быстрый и равномерный разогрев металла;
- защита от перегрева встроенным термостатом;
- автоматическое размагничивание после нагрева;
- неметаллические компоненты подшипника не подвергаются прямому термическому воздействию;
- безопасность выполнения работ.
Встречающиеся рекомендации использовать сильное охлаждение для монтажа подшипников неизбежно приводят к образованию конденсата с риском возникновения коррозии. Поэтому, например, SKF не рекомендует прибегать к такому способу.
Проверка качества установки подшипников
После установки подшипника следует проверить правильность выполненных работ. Если осуществлялся монтаж подшипника нагревом, то проверку необходимо осуществлять после полного охлаждения детали до температуры окружающей среды.
При этом следует:
- проверкой в нескольких точках по окружности убедиться в том, что подшипник вплотную прижат к заплечику: щуп толщиной 0,03 мм (или иного размера, если он установлен производителем) не должен входить между торцами колец подшипника и буртом корпуса механизма или вала;
- проверить легкость вращения подшипника от руки: оно должно быть ровным с равномерным замедлением без местных заеданий и прочих видимых отклонений;
- у шариковых радиальных однорядных подшипников проверить от руки наличие нормального осевой зазора (после охлаждения, если монтаж производился с нагревом): отсутствие качения или малая его величина указывают на недостаточные радиальные зазоры;
- при наличии к тому оснований проверить, чтобы значение радиального зазора в миллиметрах после сборки узла для подшипников, изготовленных с зазорами нормальной группы, не было менее минимально допустимых по ГОСТ 24810 (ориентировочно определяется по формуле Smin = d/3000, где d - номинальный диаметр отверстия подшипника, мм);
- у подшипников с цилиндрическими роликами и без бортов после установки проверить относительное смещение наружного и внутреннего колец в осевом направлении: оно не должно быть более 0,5-1,5 мм для подшипников с короткими роликами и более 1-2 мм - для подшипников с длинными роликами (чем больший размер имеет подшипник, тем ближе возможно смещение к указанным максимальным значениям);
- убедиться в правильности сборки уплотняющих устройств в корпусах (подшипниковых щитах) или кольцевых зазоров в лабиринтовых уплотнениях;
- убедиться в точном соответствии взаимного положения проточек для подачи смазки в корпусах со смазочными отверстиями в наружных кольцах подшипников (там, где это предусматривает конструкция подшипникового узла);
- произвести пробный пуск машины без нагрузки и прослушать работу собранного подшипникового узла с помощью стетоскопа или трубы: подшипники в нормальном состоянии при работе создают тихий, непрерывный и равномерный шум, вибрации и толчки в сборочной единице должны отсутствовать;
- проследить за температурой: в правильно собранном узле подшипник при работе в обычных условиях не должен перегреваться более чем на 30°С относительно температуры окружающей среды.
Для оценки состояния собранных подшипниковых узлов без останова и разборки наилучшие результаты даст применение методов и приборов виброакустической диагностики и приборов для оценки ударной вибрации по методике, изложенной в ГОСТ Р 50891-96 (приложение В).
Если инструментальный контроль не доступен, то при прослушивании следует обратить внимание на следующие явные признаки недостатков выполненных работ и недопустимого состояния подшипникового узла:
- вибрации - при увеличенных зазорах в подшипнике;
- неравномерный громкий шум – сильное повреждение подшипника;
- глухой неравномерный шум, в том числе стучащие звуки - загрязненность подшипника;
- свистящий шум - трения между соприкасающимися деталями, в т.ч. из-за недостаточной смазки;
- звенящий металлический звук - слишком малый зазор в парах трения подшипника;
- равномерный вибрирующий звук - попадание инородных частиц на дорожку качения наружного кольца;
- шум, возникающий время от времени при неизменной частоте вращения - повреждение тел качения;
- шум, проявляющийся при изменении частоты вращения - повреждение колец в результате монтажа или выкрашивания на поверхностях качения.
Причиной повышенной температуры подшипника может быть:
малый зазор в подшипнике;
чрезмерно большой натяг;
отсутствие или недостаток смазки между парами трения;
увеличенное трение из-за износа рабочих поверхностей, взаимного перекоса колец и некоторых иных причин;
комбинация перечисленных выше причин.
Заключение
Правильная установка подшипников требует определенной квалификации в части слесарных навыков, точного измерительного инструмента и специальной оснастки, высокой аккуратности проведения работ с соблюдением установленных правил.
Необходимые меры для исключения попадания в подшипник загрязнений следует предпринимать на всех этапах работ вплоть до полной сборки машины.
Так же необходимо выполнить установку подшипников и все сборочные операции с учетом конструктивных особенностей таким образом, чтобы смазка нужного качества была в достаточном объеме, самопроизвольно не вытекала и не разбрызгивалась.
Подшипники в нормальном состоянии при работе создают тихий, непрерывный и равномерный шум, вибрации, прихваты и толчки в сборочной единице должны отсутствовать, а температура подшипников как правило не должна превышать температуру окружающей среды более чем на 30°С.
Проверки и обслуживание после установки подшипников должны выполняться с учетом рекомендаций производителя.
Подшипник - это важная деталь конструкции, которая обеспечивает вращательные движения деталей при качении или линейном перемещении. Он представляет собой сборочный узел, состоящий из двух круглых пластин: наружного и внутреннего кольца. Внутри конструкции вставлен сепаратор с несколькими шариками, которые и обеспечивают кручение механизма.
Виды подшипников
Подшипники различаются по типу конструкции и материалу изготовления:
- Наиболее часто встречаются в бытовых приборах и знакомы потребителям подшипники с шариками. Они ставятся на приборы, которые не испытывают сильных нагрузок. Например, электродвигатели, деревообрабатывающие станки, редукторы. Применяются в медицинском оборудовании.
- Сферические подшипники обладают самой большой прочностью и выносят даже экстремальные нагрузки, поэтому устанавливают их в таких механизмах, как дробилки либо насосы.
- В мелких деталях бытовой техники часто используются игольчатые подшипники . В механизме таких изделий вставляются тонкие цилиндрические палочки, по форме напоминающие иголку.
- Одними из самых надежных подшипников, выдерживающих достаточные нагрузки, считаются цилиндрические . Используют их в машиностроении: в автомобильном, авиационном и железнодорожном транспорте.
Устройство шарикового подшипника
Рассмотрим первый вариант изделия. Состоит такой прибор из двух металлических пластин, которые имеют специальные желоба или так называемые дорожки качения посередине плоскостей. На большом наружном кольце такой паз располагается внутри, на кольце меньшего диаметра - с наружной стороны.
В центр конструкции вставляется сепаратор со вставленными шариками. Благодаря такой системе качение происходит плавно. Подшипники при установке на механизм можно еще протереть смазочными материалами для лучшего вращательного движения.
Сепаратор состоит из двух частей - так называемых полусепараторов. Эти две детали потом спаиваются при помощи точечной сварки. Иногда их крепят на монтажные усики или методом склепывания. Такие приборы могут иметь один или два ряда шариков.
Устройство роликового подшипника
Другой вариант устройства для вращения деталей состоит из роликов. Это металлические цилиндры или конусы одинакового размера, которые вставляются в сепаратор посередине между двумя кольцами. Такие изделия на порядок крепче и надежнее, чем шариковые подшипники. Применяются они в машиностроении: автомобильном, авиационном и железнодорожном транспорте.
Бывают роликовые вставки цилиндрической или конусной формы, которые ставятся во внутреннюю часть детали в один или в несколько рядов. Ролики цилиндрической формы, после того как собирают подшипник, устанавливаются в гильотинах, мощных редукторах и электродвигателях, шпинделях металлорежущих станков или насосах.
Конусная форма используется в изделиях для косозубых механических передач, в автомобильном транспорте, в ступицах легковых машин.
Подготовка к сборке подшипника
На предприятиях сборочные процессы выполняются на специальном оборудовании, а именно валах. Перед тем как собирать подшипники, проверяют качество поверхностей как вала, так и колец изделия. На них не должно быть никаких повреждений: царапин, заусениц, забоин, нарисованных рисок, пятен коррозии металла, трещин.
Все поверхности тщательно протираются, высушиваются и перед тем как собирать подшипники, смазываются тонким слоем смазочного материала. Только после этого можно начать сборочные операции.
Механический способ
Такой метод используют при небольших размерах деталей, внутренний диаметр которых - до 60 мм. При сборке главное - соблюдать одно важное правило: усилие при механическом сопряжении наружного и внутреннего кольца не должно передаваться на сепаратор. Оно оказывается только на торцы колец.
Также категорически запрещено стучать по кольцу. Легкие удары можно наносить только через дополнительный материал, например втулку, выполненную из мягкого металла. На предприятиях эти задачи выполняют автоматизированные машины на конвеерных лентах.
Поэтапная последовательность сборки
Давайте рассмотрим, как собрать разобранный подшипник:
- Нужно поставить внешнее кольцо в вертикальное положение и смазать его канавку изнутри густой, почти твердой смазкой, но не до конца круга, а приблизительно на три четверти его поверхности.
- После этого нужно вставлять поочередно тонким пинцетом шарики, утапливая их в смазочный материал.
- Перед тем как собрать шариковый подшипник, нужно приложить внутреннее кольцо к шарикам, немного придавив его. Дальше аккуратно начинаем прокручивать по кругу так, чтобы они распределились на равные расстояния один от другого.
- Потом вставляем сепаратор и проворачиваем его так, чтобы шарики нашли свое место в углублениях.
- Когда все шарики защелкнутся в отделениях, можно протереть смазку сухой тряпочкой. Для полного отмывания желательно воспользоваться керосином.
Ремонт подшипника
Бывают случаи, когда подшипник в приборе стал плохо проворачиваться. Причин может быть несколько. Например, набилась грязь в смазку. Для того чтобы дать изделию новую жизнь, его нужно тщательно почистить и промыть. Можно в этих целях использовать бензин.
- Сначала нужно снять крышку сальника, зажать подшипник в тисках и аккуратно тонким сверлом просверлить заклепки сепаратора. Такое можно делать только в том случае, когда имеется несколько старых подшипников, и в случае поломки сепаратора или его одной половинки можно будет собрать целый из других изделий.
- Все заклепки на сепараторе нужно аккуратно срезать болгаркой, чтобы половинка была целая, не погнутая.
- Следующим этапом будет очистка колец и вытряхнутых шариков от грязи, промывка деталей в бензине. Заодно нужно проверить состояние и целостность каждого элемента подшипника.
- Дальше самый трудный этап ремонтных работ - вкладывание всех шариков обратно в конструкцию.
- Перед тем как правильно собрать подшипник, нужно отшлифовать кольца. Сначала вставляется первая половина сепаратора, дальше аккуратно, по одному, в каждый паз нужно поместить шарики так, чтобы они заполнили все отверстия.
- После этого делаются заклепки. Можно использовать медную проволоку.
- Далее накладываем слой свежей смазки и закрываем крышку сальника.
Отремонтированные таким образом подшипники в агрегаты, мотоцикл или машину ставить не рекомендуется. Можно их использовать для хозяйственных целей на дачном участке или ребенку починить самокат.
Как собрать маленький подшипник?
Сейчас очень популярна среди детей вращающаяся игрушка под названием спиннер. Но что стоит ребенку уронить на пол такой крутящийся предмет? Бывали случаи, когда малыш прибегал к родителям весь в слезах и причитал, что спиннер поломался.
И чаще всего проблема для родителей в том, как собрать рассыпавшийся подшипник. Мелкие изделия гораздо сложнее собрать, но вполне возможно. Для этого нужно будет воспользоваться тонким пинцетом.
Чаще всего в таких игрушках используются простые шариковые подшипники без сепараторов, в которых шарики крутятся по пазам колец. Чтобы собрать все детали вместе, нужно воспользоваться описанным выше механическим способом сборки. Если у вас не получается, то нужно воспользоваться знаниями о свойствах металла.
Одно из колец нужно положить в теплую воду, а другое - в холодильник. От мороза металл станет меньшего размера, а после тепловой обработки расширится. Таким образом сложить вместе их уже будет намного легче. Удачи!
Другие статьи: | ||
Обучение | ||
Отзывы о Подшипник.ру | ||
Монтаж подшипников
Для подготовки подшипников к монтажу предварительно проверяют надписи на упаковке и самих подшипниках.
Распаковывают подшипники непосредственно перед началом работ с ними.
Расконсервацию подшипников производят согласно действующей инструкции по хранению, расконсервации подшипников и их деталей и обращению с ними. Как правило, подшипники расконсервируют в горячем (80-90 °С) минеральном масле, тщательно промывают в 6-8%-ном растворе масла, в бензине или в горячих (75-85°С) антикоррозионных водных растворах, например, следующих составов (в %-тах):
Раствор N1 |
Раствор N2 |
|
Триэтаноломин |
||
Нитрит натрия |
||
Смачиватель ОП |
||
Остальное |
Остальное |
Хранить расконсервированные подшипники более двух часов без защиты от коррозии не рекомендуется.
После расконсервации потребитель подшипников должен обеспечить их защиту от коррозии при контроле, монтаже, сборке и хранении изделий по соответствующей внутризаводской инструкции.
Перед монтажом подшипник следует проверить на соответствие внешнего вида, легкости вращения, зазоров требованиям нормативно-технической документации.
Визуально у подшипников открытого типа должны быть проверены наличие забоин, следов загрязнений, коррозии, полного комплекта заклепок, плотности их установки или других соединительных элементов, полного комплекта тел качения, наличие повреждений сепаратора.
У подшипников закрытого типа следует проверить не повреждены ли уплотнения или защитные шайбы.
Для проверки радиального зазора одно из колец подшипника закрепляют при горизонтальном положении оси и определяют зазор с помощью индикатора, смещая свободное кольцо под действием измерительного усилия в радиальном направлении в два диаметрально противоположные положения. Разница показаний прибора соответствует значению радиального зазора. Проводят три измерения, поворачивая свободное кольцо относительно начального положения оси подшипника. Аналогично проводят измерение осевого зазора, но при вертикальном положении оси подшипника. Закрепляя одно из колец, другое смещают в осевом направлении в два крайних положения под действием измерительного усилия и фиксируют разность показаний индикатора. Радиальные зазоры в радиальных двухрядных сферических роликовых подшипниках и подшипниках с цилиндрическими роликами без бортов на наружных кольцах с диаметром посадочного отверстия свыше 60 мм могут быть измерены с помощью щупа.
Непосредственно перед монтажом необходимо проверить монтажные поверхности корпусов (отверстия и торцы) и валов (посадочные поверхности и торцы) на отсутствие забоин, царапин, глубоких рисок от обработки, коррозии, заусенцев и загрязнений.
Валы, особенно при соотношениях длины и наибольшего диаметра более 8, следует проверять на прямолинейность оси (отсутствие изгиба). Проверку целесообразно проводить при вращении вала в центрах с помощью индикаторов часового типа. Увеличение эксцентриситета в направлении от края к середине указывает на искривление вала.
Необходимо проверить отклонение от соосности всех посадочных поверхностей, расположенных на одной оси, на соответствие нормам, указанным в технической документации.
Если подшипники, служащие опорой одного вала, устанавливают в различные (раздельные) корпуса, соосность корпусов, в соответствии с требованиями технической документации, должна быть обеспечена с помощью прокладок или других средств.
При установке на одну посадочную шейку двух подшипников (радиальных: шариковых, роликовых сферических и цилиндрических) разница в радиальных зазорах не должна превышать 0,03 мм, а по внутреннему и наружному диаметрам колец - не более половины поля допуска.
Сопрягаемые с подшипниками поверхности валов и корпусов должны быть тщательно промыты, протерты, просушены и смазаны тонким слоем смазочного материала или антифреттингвой пастой. Каналы для подвода смазки должны быть очищены от стружки и других загрязняющих частиц и продуты сжатым воздухом.
При монтаже подшипника усилие напрессовки должно передаваться только через напрессовываемое кольцо - через внутреннее при монтаже на вал и через наружное - в корпус. Запрещается проводить монтаж таким образом, чтобы усилие передавалось с одного кольца на другое через тела качения. Если подшипник одновременно монтируется на вал и в корпус, то усилия передаются на торцы обоих колец.
Не допускается приложение монтажных усилий к сепаратору. Нельзя наносить удары непосредственно по кольцу. Допускается нанесение легких ударов по кольцу только через втулку из незакаленной конструкционной стали.
При монтаже подшипников с цилиндрическим отверстием на вал с натягом подшипник целесообразно предварительно нагреть на индукционном нагревателе.
Нагретый подшипник устанавливают на вал и доводят до места небольшим усилием. При этом сторона подшипника, на которой нанесено заводское клеймо, должна быть снаружи.
Для монтажа крупногабаритных подшипников наиболее целесообразным является применение гидравлического распора, обеспечивающего наиболее качественную установку подшипника, отсутствие каких-либо повреждений монтажных поверхностей и высокую производительность. Особенно целесообразен этот способ для монтажа подшипников с внутренним коническим отверстием диаметром более 120-150 мм.
При посадке подшипника в корпус с натягом рекомендуется перед монтажом предварительно охладить подшипник жидким азотом (-160 °С) или сухим льдом, либо нагреть корпус.
Наиболее целесообразными являются способы монтажа, при которых осуществляется одновременное и равномерное давление по всей окружности монтируемого кольца. При таких способах не возникает перекос монтируемого кольца. Для осуществления подобных способов применяют трубы из незакаленной конструкционной стали, внутренний диаметр которых несколько больше диаметра отверстия кольца, а наружный немного меньше наружного диаметра кольца. На свободном конце трубы следует установить заглушку со сферической наружной поверхностью, к которой и прилагают усилие при монтаже.
Усилие при монтаже следует создавать с помощью механических либо гидравлических прессов и приспособлений.
При отсутствии механических и гидравлических приспособлений и монтаже с небольшими натягами подшипников малых размеров допустимо нанесение несильных ударов молотком через монтажную трубу с заглушкой.
При любых способах монтажа, особенно при монтаже с помощью молотка, необходимо тщательно следить за обеспечением равномерного, без перекоса, осевого перемещения кольца. Наличие перекоса при монтаже приводит к образованию задиров на посадочной поверхности, неправильной установке подшипника, приводящей к сокращению срока его службы, а в отдельных случаях - к разрыву монтируемого кольца.
Двухрядные сферические шариковые и роликовые подшипники с коническим отверстием устанавливают на цилиндрическом валу с помощью закрепительных и стяжных втулок, а на валах с конической шейкой - непосредственно на шейку вала. Монтаж подшипников с диаметром отверстия до 70 мм и нормальными натягами целесообразно осуществлять с помощью монтажной втулки, навертываемой на резьбовой конец вала. Нажимная часть воздействует на торец закрепительной втулки или непосредственно на торец внутреннего кольца (при монтаже без закрепительных и стяжных втулок). Подшипники с диаметром отверстия свыше 70-100 мм следует монтировать гидравлическими методами. Так как по мере осевого продвижения закрепительной втулки внутреннее кольцо подшипника деформируется (расширяется), радиальный зазор уменьшается. Радиальный зазор необходимо контролировать с помощью щупа. Допустимое минимальное значение радиального зазора в миллиметрах после сборки узла для подшипников, изготовленных с зазорами нормальной группы по ГОСТ 24810, ориентировочно может быть определено по формуле
где d - номинальный диаметр отверстия подшипника, мм.
Крупногабаритные (с диаметром отверстия более 300 мм) сферические роликовые подшипники целесообразно перед монтажом разогреть до 60-70°С,
При монтаже игольчатого подшипника без сепаратора последняя игла должна входить с зазором, равным от 0,5 до 1 диаметра иглы. Иногда для выполнения этого условия устанавливают последнюю иглу с меньшим диаметром.
В процессе установки подшипников (особенно воспринимающих осевые усилия) там, где это возможно, с помощью щупа толщиной от 0,03 мм или по световой щели следует убедиться в плотном и правильном прилегании торцов колец подшипника к торцам заплечиков. Аналогичной проверке должны быть подвергнуты противоположные торцы подшипников и торцы прижимающих их в осевом направлении деталей.
Необходимо проверить правильность взаимного расположения подшипников в опорах одного вала. Вал после монтажа должен вращаться от руки легко, свободно и равномерно.
Осевой зазор радиально-упорных и упорных подшипников устанавливают осевым смещением наружного и внутреннего колец с помощью прокладок, гаек, распорных втулок. Для проверки осевого зазора в собранном узле к торцу выходного конца подводят измерительный наконечник индикатора, укрепленного на жесткой стойке. Осевой зазор определяют по разнице показаний индикатора при крайних осевых положениях вала. Вал смещают в осевом направлении до полного контакта тел качения с поверхностью качения соответствующего наружного кольца.
Для повышения точности вращения, особенно в быстроходных узлах, например, станочных электрошпинделях, зазоры в радиально-упорных подшипниках выбирают, создавая стабильный преднатяг на подшипники. Это достигается приложением к вращающемуся кольцу подшипника осевого усилия через тарированную пружину. При этом тела качения точно фиксируются на дорожках качения.
Для предотвращения «закусывания» крупных подшипников при монтаже или в процессе эксплуатации перед установкой их в разъемные корпуса допускается производить расшабривание поверхностей полуотверстий в местах разъема. Полноту прилегания крупных подшипников к посадочным местам в разъемных корпусах проверяют с помощью калибра и краски (отпечатки краски должны составлять не менее 75% общей посадочной площади). В разъемных корпусах с помощью щупа проверяют также плотность и равномерность прилегания основания крышки (зазор не более 0,03 -0,05 мм).
В собранном узле необходимо проверить наличие зазоров между вращающимися и неподвижными деталями. Особое внимание следует обратить на наличие зазоров между торцами неподвижных деталей и торцами сепараторов, которые иногда выступают за плоскость торцов колец.
Следует проверить также совпадение проточек для подачи смазки в корпусах со смазочными отверстиями в наружных кольцах подшипников.
Для подшипников с цилиндрическими роликами и без бортов после монтажа должно быть проверено относительное смещение наружного и внутреннего колец в осевом направлении. Оно не должно быть более 0,5-1,5 мм для подшипников с короткими роликами и более 1-2 мм - для подшипников с длинными роликами (большие значения даны для подшипников больших размеров).
После завершения сборочных операций и введения в подшипниковые узлы смазочного материала, предусмотренного технической документацией, следует проверить качество монтажа подшипников пробным пуском сборочной единицы на низких оборотах без нагрузки. При этом прослушивают шум вращающихся подшипников с помощью стетоскопа или трубы. Правильно смонтированные и хорошо смазанные подшипники при работе создают тихий, непрерывный и равномерный шум. Свистящий шум свидетельствует о недостаточном смазывании или наличии трения между соприкасающимися деталями узла. Звенящий металлический звук может быть вызван слишком малым зазором в подшипнике. Равномерный вибрирующий звук вызывается попаданием инородных частиц на дорожку качения наружного кольца. Шум, возникающий время от времени при неизменной частоте вращения, свидетельствует о повреждении тел качения. Шум, проявляющийся при изменении частоты вращения, может быть обусловлен повреждением колец в результате монтажа или наличием усталостных выкрашиваний на поверхностях качения. Стучащие звуки возможны вследствие загрязнения подшипника. Неравномерный громкий шум создают сильно поврежденные подшипники.
Производители насосов в своем оборудовании используют большое разнообразие видов и типов монтажа для подшипников, основанное на приложениях и требованиях по нагрузке. На небольших процессных насосах и насосах общего назначения, обычно, можно увидеть один ряд радиальных подшипников и двойной ряд упорных подшипников.
В то время, как машины становятся больше, скорости выше, а радиальные и осевые нагрузки испытываемые валом и подшипниковым узлом растут, производители часто переходят к большим шариковым или роликовым подшипникам и сдвоенным парам радиально-упорных подшипников, чтобы справиться с возросшей нагрузкой. Безусловно, когда поднимается тема о сдвоенных радиально-упорных подшипниках, также поднимается вопрос о том, как их правильно установить.
"СПИНА К СПИНЕ"
Многие производители устанавливают на вал пару радиально-упорных подшипников в конфигурации "спина к спине". Это когда более широкие внешние дорожки соприкасаются друг с другом, а подшипники зафиксированы на валу с помощью стопорной шайбы и контрагайки. Это позволяет радиальному и упорному подшипнику переносить большие осевые нагрузки в обоих направлениях. При обычной установке, когда вы смотрите на подшипники, правильно установленные на валу, вы можете увидеть существенное количество шарикоподшипников с внешней стороны, и как более широкий фланец одного подшипника соприкасается с широким фланцем другого.
"ЛИЦОМ К ЛИЦУ"
Другим, не менее эффективным методом является установка подшипников на валу "лицом к лицу". В этом случае внутренние дорожки удерживаются вместе с помощью стопорной шайбы и контрагайки, но прочная несущая способность такого расположения не реализуется до тех пор, пока не будут зафиксированы внешние дорожки подшипников. Обычно это делается с помощью сепаратора подшипника, хотя иногда для загрузки дорожек подшипника используются пружины. С использованием сепаратора процедура может потребовать прокладок между сепаратором и корпусом подшипника, чтобы установить предварительную загрузку или внутренний рабочий зазор. Если используются пружины, то необходимо использовать те, что имеют правильный коэффициент упругости, а не просто любые пружины. Хоть эта настройка и является более сложной, компоновка "лицом к лицу" может устранить большую несоосность между валом и корпусом и обеспечить при этом радиальные подшипники жесткой несущей способностью, а также долгим сроком службы.
"ТАНДЕМ"
Третий способ заключается в монтировании радиально-упорных подшипников на валу в тандеме. Это когда оба подшипника имеют одно и то же направление. Такое расположение делает очень загруженную компоновку упорного подшипника, но оно не несет никакой радиальной нагрузки и воспринимает осевую нагрузку только в одном направлении. В набор должен быть добавлен третий радиально-упорный или радиальный подшипник, чтобы воспринимать радиальные нагрузки. В сочетании с очень надежным радиальным подшипником, это позволяет переносить максимальные нагрузки в осевом направлении.
Всегда должна приниматься во внимание информация от производителя оборудования, чтобы правильно ориентировать любые составные пакеты подшипников для обеспечения их правильной установки. При правильной установке, данные компоновки обеспечат долгий срок службы. При неправильной, могут привести к поломке почти сразу.
Чтобы узнать какой способ установки будет лучше в конкретных условиях для вашего оборудования, читайте ниже.
О-образная схема или «спина к спине»
В подшипниках, которые установленны спина к спине или по О-образной схеме, линии нагрузки расходятся по направлению к оси подшипников. При таком способе установки подшипники воспринимают осевые нагрузки как в одну сторону, так и в другую. При этом каждый подшипник воспринимает действующие силы только в одном направлении.
Плюсы установки подшипников по О-образной схеме:
- Обеспечение высокой жесткости подшипникового узла
- Восприятие моментных нагрузок
Х-образная схема или «лицом к лицу»
В подшипниках, которые установленны лицом к лицу или по Х-образной схеме, линии нагрузки сходятся по направлению к оси подшипников. При таком способе установки подшипники воспринимают осевые нагрузки как в одну сторону, так и в другую. При этом каждый подшипник воспринимает действующие силы только в одном направлении.
Результат установки подшипников по О-образной схеме:
- Узел менее пригоден для восприятия моментных нагрузок
Схема «тандем»
В случае, если осевая и радиальная грузоподъёмность одного подшипника недостаточна для обеспечения надежной работы оборудования, применяют схему «тандем». Подшипники устанавливаются в одном направлении. Линии нагрузки в этом случае проходят паралельно друг другу. Осевая и радиальная нагрузки распределяются между подшипниками равномерно.
Данная схема установки подшипников позволяет воспринимать нагрузки, действующие только в одном направлении. Если имеется риск воздействия сил в другом направлении, то необходимо установить еще один подшипник или более для компенсации нагрузок.