Композитные технологии. Современные наукоемкие технологии. Технология композитов – раздел технологии материалов
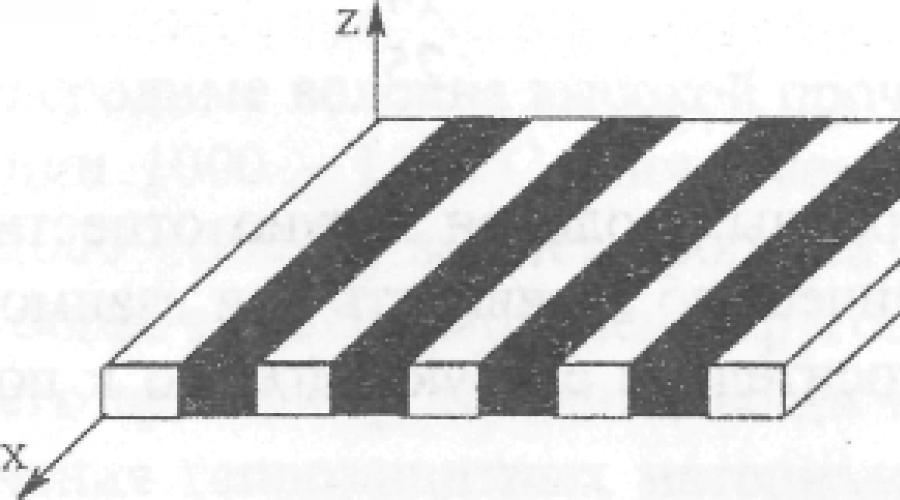
Ракетная техника, космонавтика, авиастроение, ядерная энергетика, химическое машиностроение, автотранспорт, судостроение, электроника и многие другие отрасли промышленности нуждаются в материалах, обладающих высокой прочностью, жаростойкостью, жаропрочностью и термостойкостью (хорошим сопротивлением распространению трещин), малой плотностью, регулируемыми в широких пределах показателями тепло- и электропроводности, специальными оптическими и магнитными характеристиками к др. Многие из существующих промышленных материалов уже не могу! удовлетворить эти запросы.
Материал с комплексом таких характеристик можно получить лишь т основе композиций. Композиционные материалы (КМ) - это материалы, состоящие из двух или более компонентов (армирующих составляющих и связующей их матрицы) и обладающие специфическими свойствами, отличными от суммарных свойств этих компонентов.
Если один из компонентов КМ непрерывен во всем объеме, а другой является прерывистым, разъединенным в объеме композиции, то первый компонент называют матрицей, а второй - арматурой или армирующим элементом. Армирующие компоненты могут представлять собой различные волокна, порошки, микросферы, кристаллы и «усы» из органических, неорганических, металлических материалов или керамики. В качестве матрицы чаете
используются синтетические высокомолекулярные вещества различного химического состава.
Первым создателем композиционных материалов была сама природа. Например, древесина - это композиция, состоящая из пучков высокопрочных целлюлозных волокон трубчатого сечения, связанных между собой матрицей из органического вещества (лигнина), придающего древесине поперечную жесткость.
Компоненты композитов не должны растворяться или иным способом поглощать друг друга. Они должны обладать хорошей адгезией и быть взаимно совместимы. Свойства КМ нельзя определить только по свойствам компонентов, без учета их взаимодействия. Каждая составляющая несет определенную функцию и вносит свой вклад в свойства композита. Рассмотрим требования, предъявляемые к армирующим наполнителям, например, к волокнам.
Нитевидная форма армирующих элементов имеет как положительные, так и отрицательные стороны. Преимущество волокон состоит в высокой прочности и возможности создать упрочнение только в том направлении, в котором это требуется конструктивно. Недостаток такой формы заключается в том, что волокна способны передавать нагрузку только в направлении своей оси, тогда как в перпендикулярном направлении упрочнения нет, а в некоторых случаях может проявиться даже разупрочнение.
Волокна, используемые в качестве армирующих наполнителей, должны иметь следующие свойства: высокую температуру плавления, малую плотность, высокую прочность во всем интервале рабочих температур, отсутствие токсичности при изготовлении и эксплуатации.
В основном применяют три вида наполнителей: нитевидные кристаллы, металлическую проволоку и неорганические поликристаллические волокна.
Нитевидные кристаллы («усы») рассматривают как перспективный материал для армирования матриц из металлов, полимеров и керамики. Сверхвысокая прочность в широком диапазоне температур при малой плотности, химическая инертность по отношению ко многим матричным мате-. риалам, высокая жаростойкость и коррозионная стойкость нитевидных кристаллов оксидов алюминия и магния, карбида кремния делают их незаменимыми армирующими элементами. К сожалению, пока на пути их практического применения стоит много трудностей. Предстоит решить проблемы получения их в промышленном масштабе, отбора годных «усов», ориентации их в матрице, методов формирования композиций с «усами».
Металлическая проволока из стали, вольфрама, молибдена и других металлов менее перспективна, чем «усы» из-за большой плотности и меньшей прочности. Однако она имеет сравнительно невысокую стоимость и ее широко используют в качестве арматуры, особенно для композиционных материалов на металлической основе.
Поликристаллические неорганические волокна получают в больших количествах. Недостаток этих волокон - очень высокая чувствительность к механическим повреждениям. Малая плотность, высокая прочность и химическая стойкость углеродных, борных, стеклянных, карбидокремниевых. кварцевых и других волокон позволяют широко использовать их для армирования пластмасс,
К числу наиболее перспективных армирующих элементов относят углеродные волокна. Они обладают низкой плотностью (1430 - 1830 кг/м 3), высокими прочностью (3,5 ГПа) и модулем упругости (250 - 400 ГПа).
Обычно углеродные волокна разделяют на два основных типа: волокна с высокой прочностью и волокна с высокой упругостью. В производстве, главным образом, изготовляют волокна высокой прочности. Прочность этих волокон на начальной стадии разработок составляла 2,5 ГПа. За счет усовершенствования технологии (предварительной обработки, придания волокнам огнестойкости, карбонизации и завершающей обработки) прочность была повышена, например, для обычного материала до 3,5 ГПа.
Проведенные исследования показали, что с увеличением прочности волокон прочность композиционного материала, как правило, возрастает линейно. , : ;.,
Обычно углеродные волокна высокой прочности получают при температуре карбонизации 1000 - 1500°С, они имеют модуль упругости 2250 -2350 Ы/мм 2 . При 2000 - 3000°С за счет процесса графитации могут быть получены волокна с более высоким модулем упругости.
До недавнего времени углеродные волокна и ткани из них применялись для изготовления теплозащитных материалов. Однако усовершенство-. ванная технология получения тонких волокон, сочетающих высокую прочность и жесткость с другими специальными свойствами (термостойкость, электропроводность и др.) позволила создать армированные угольными волокнами металлы и пластики, отличающиеся малой жесткостью и высокой прочностью. Такие композиции все больше применяются в космической, ракетной и авиационной технике. Чаще всего применяют углеродные волокна из вискозы и полиакрилонитрила.
В зависимости от содержания углерода углеродные волокна делят на три группы:
карбонизованные (не более 95 мас.% С); - угольные (91-98 мас.% С);
графитовые (более 98 мас.% С).
Жесткое углеродное волокно получается, если технологический процесс построен так, что максимальное количество базисных слоев располагается параллельно оси волокна. Чтобы повысить прочность углеродных волокон, следует уменьшить размер кристаллитов, имеющих более совершенное строение. В качестве технологических приемов, придающих углеродным волокнам дополнительную жесткость и прочность, используют легирование их бором с помощью диффузии из газовой фазы, облучение волокон нейтронами в атомном реакторе, введение в них перед пиролизом буры, а также вытягивание в процессах окисления и графитации.
Если в тонких волокнах есть микродефекты, вызывающие локальные концентрации напряжений, то прочность углеродных волокон уменьшается. Дефектность волокон обуславливает линейную зависимость их прочности от длины: с увеличением длины значительно снижается прочность и несколько увеличивается модуль упругости. По уровню механических свойств углеродные волокна делятся на три группы: низкие, средние, высокие (табл. 1.5)
Таблица 1.5 Механические свойства углеродных волокон
Группа Плотность Прочность Модуль упругости
у, г/см 3 а, ГПа Е, ГПа
Низкие 18 14 42
Средние 18 14 175
Высокие 18 25 420
К недостаткам углеродных волокон можно отнести их склонность к окислению на воздухе, химическую активность при взаимодействии с металлическими матрицами, относительно слабую адгезию к полимерным матрицам.
Обработка поверхности волокон является важным процессом с точки зрения повышения их адгезии с матрицей. Обычно осуществляют обработку поверхности углеродных волокон окислением их в газовой фазе.
Влияют на характеристики углеродных волокон присутствие в них металлов и других неорганических веществ. В частности, содержание щелочных металлов типа натрия и калия оказывает отрицательное влияние на устойчивость к окислению при нагревании, а фосфор и бор оказывают положительное влияние.
Все композиционные материалы делятся на изотропные и анизотропные. К изотропным относятся материалы, имеющие одинаковые свойства во всех направлениях, а к анизотропным - разные.
Упрочняющие элементы могут иметь примерно равноосновную форму или быть короткими (дискретными) частицами игольчатой формы, хаотично ориентированными в пространстве. В качестве таких частиц обычно используют отрезки волокон или «усы». При этом КМ получаются квазиизотропными, т.е. анизотропными в микрообъемах, но изотропными в объеме всего изделия.
К анизотропным КМ относят материалы, волокна которых ориентированы в определенных направлениях - однонаправленные, слоистые и трех-мерноармированные. Изображения анизотропных КМ даны на рис. 1.24, 1.25.
Рис. 1.24. Схематическое изображение структуры КМ поперечной укладкой волокон
с продольно
Рис. 1.25. Схематическое изображение структуры однонаправленного КМ (черные области - волокна; белые - матрица)
Технологическая анизотропия возникает при пластической деформации изотропных материалов (металлов). Физическая анизотропия свойственна кристаллам в связи с особенностями строения их кристаллической решетки.
В технике обычно используют анизотропные КМ с определенной симметрией свойств.
Не менее важную роль в армированных композициях играет матрица, которая придает изделию форму и делает материал монолитным. Объединяя в единое целое многочисленные волокна, матрица должна позволять композиции воспринимать различного рода внешние нагрузки - растяжение, сжатие, изгиб, сдвиг и др. В то же время она принимает участие в создании несущей способности композиции, обеспечивая передачу усилий на волокна. За счет пластичности матрицы усилия от разрушенных или дискретных (коротких) волокон передаются соседним волокнам, а концентрация напряжений вблизи различного рода дефектов уменьшается. Матрице отводится и роль защитного покрытия, предохраняющего волокна от механических повреждений и окисления. Кроме того, матрица должна обеспечивать прочность и жесткость системы при действии растягивающей или сжимающей нагрузки в направлении, перпендикулярном к армирующим элементам. Если растягивающая нагрузка направлена по оси параллельных между собой волокон, то для получения эффекта упрочнения предельное относительное удлинение матрицы как минимум должно быть равно относительному удлинению волокон. Если же нагрузка перпендикулярна к оси волокон, то этого оказывается недостаточно. В этом случае нагрузка на волокна передается только через матрицу и чем больше концентрация волокон и отношение модулей упругости материалов волокна и матрицы, тем больше должна быть предельная деформация матрицы. Оценочные работы, произведенные на упругих моделях, показывают, что для обеспечения монолитности КМ при поперечном нагру-жении нужны матрицы, относительное удлинение которых в несколько раз превышает среднюю деформацию волокон.
Стремление получить максимальную прочность композиции вызывает тенденцию повышения объемной доли волокон. Однако, если относительное удлинение матрицы мало, то в случае больших значений этой доли монолитность КМ может нарушиться даже при небольших нагрузках: появятся расслоения, трещины. Оказалось, что чем пластичнее матрица, тем меньше допускается толщина прослойки матрицы между волокнами и тем больше волокон может быть введено в КМ.
В зависимости от материала матрицы все КМ можно разбить на три группы: композиции с металлической матрицей - металлические композиционные материалы (МКМ), с полимерной - полимерные композиционные материалы (ПКМ) и с керамической - керамические композиционные материалы (ККМ).. Полимерные КМ обычно называют по материалу армирующих волокон: армированные стеклянными волокнами называются стеклопластиками (стекловолокнитами), металлическими - металлопластиками (металло-волокни-тами), органическими - органопластиками (органоволокнитами), борными - боропластиками (бороволокнитами), углеродными - углепластиками (углеволокнитами) и т.п.
В отношении металлических и керамических КМ пока нет четко установленных правил присвоения названий. Чаще других вначале пишут материал матрицы, затем - материал волокна. Например, обозначение «медь-вольфрам» (Cu-W) относится к КМ с медной матрицей и вольфрамовыми волокнами. Но в литературе иногда вначале указывают материал волокна, а затем - матрицы.
Полимерные композиционные материалы получили наибольшее распространение по сравнению с другими благодаря простоте изготовления, технологичности, дешевизне, низкой плотности. Основной их недостаток -ограниченный температурный интервал эксплуатации. Современные полимерные связующие (матрицы) могут обеспечить работоспособность изделий до температур, не превышающих 300 - 400°С.
По поведению при нагреве и охлаждении полимерные связующие принято разделять на термопластичные и термореактивные. Свойства термопластичных полимерных связующих позволяют получать изделия из них литьем под давлением, экструзией, напылением и широко использовать при их изготовлении автоматизированное оборудование. Макромолекулы термопластичных полимеров имеют линейное строение и получаются из мономеров, имеющих по две функциональные группы, которые присоединяются друг к другу прочными ковалентными связями. Между собой макромолеку-лярные цепи связаны слабыми ван-дер-ваальсовскими силами.
Термореактивные олигомеры под действием тепла, отвердителей, катализаторов переходят в твердое состояние (отверждаются). Этот процесс необратим. Олигомеры легко растворяются в некоторых растворителях (спирте, ацетоне и др.), но после отверждения уже не растворимы. Термореактивные смолы получают из мономеров, имеющих более двух функциональных групп. В процессе отверждения мономеры растут в трех направлениях, образуя макромолекулы сетчатого строения, все структурные элементы которых соединены друг с другом прочными ковалентными связями.
Основной компонент полимерного связующего - смола. От ее природы, реакционной способности, молекулярной массы и строения молекул зависят температура размягчения, растворимость, вязкость и конечные свойства связующего. Кроме смолы, в состав связующего могут входить: катализаторы или инициаторы, которые вводят в смолы в небольших количествах к способствуют их отверждению; пластификаторы, придающие полимеру запас пластичности и упругости; красители, которые окрашивают материал в нужный цвет; стабилизаторы, предотвращающие распад полимеров под действием светового излучения и повышенных температур.
В качестве связующих для конструкционных ПКМ, работающих по/ нагрузками, в подавляющем большинстве случаев используют термореактивные смолы. Наиболее широко в производстве конструкционных ПКМ применяют эпоксидные, полиэфирные, фенольные, кремнийорганические и поли-имидные смолы.
Эпоксидные смолы составляют 90% смол, используемых в качеств* связующих для новых ПКМ. Отверждение эпоксидных смол в зависимости о-типа отвердителя и его количества можно производить как при комнатной так и при повышенной температуре. В первом случае говорят о смолах хо лодного отверждения, во втором - о смолах горячего отверждения.
Эпоксидные смолы отличаются универсальностью свойств. Они обладают малой усадкой, хорошей адгезией к различным наполнителям, высокими механическими свойствами, низким влагопоглощением, допускают переработку при комнатной температуре и варьирование в широких пределах длительности и температуры отверждения. В них можно добавлять растворители, модификаторы и пластификаторы, чтобы изменить вязкость неотвер-жденного полимера, химическую стойкость и пластичность. При их термообработке отсутствуют выделения летучих продуктов реакции. Они несколько дороже полиэфирных и фенольных смол, но это компенсируется их лучшими технологическими и эксплуатационными качествами.
Обычно КМ на базе эпоксидных смол используют до 150°С. В последние годы разработаны новые, более термостойкие эпоксидные смолы, которые позволяют применять их в ГЖМ, работающих при 200°С и выше.
Очень важным с технологической точки зрения качеством эпоксидных смол является их способность длительное время находиться в полуотвер-жденном состоянии, что дает возможность изготовлять на их основе предварительно пропитанные и частично отвержденные ткани, ленты и жгуты («препреги»), а затем получать изделия.
Полиэфирные смолы - это продукты поликонденсации ненасыщенных дикарбоновых кислот (в основном, малеиновой и метакриловой) с многоатомными или ненасыщенными спиртами (диэтиленгликолем, триэтиленгли-колем и др.). В результате полимеризации образуется твердый нерастворимый полимер трехмерной структуры. Полиэфирные связующие были разработаны намного раньше, чем эпоксидные, и первые конструкционные КМ изготовлены на их основе.
Основные достоинства полиэфирных связующих - их низкая стоимость и простота обращения. Но они менее прочны, обладают худшей адгезией к большинству волокон, более хрупки, дают большую усадку при отверждении и имеют меньшую жизнеспособность по сравнению с эпоксидными смолами.
Фенольные смолы получают поликонденсацией фенолов (гидрокси-бензола, крезола, резорцина и т.п.) с альдегидами (фурфурол, формальдегид и др.). Эти смолы темного цвета и обладают повышенной по сравнению с рассмотренными ранее связующими высокотемпературной стойкостью.
При отверждении фенольные смолы проходят три стадии:
«А» - образование резола - продукта начальной конденсации, не имеющего поперечных связей и способного растворяться в спирте, ацетоне и других растворителях;
«В» - образование резитола - продукта, в котором началось образование поперечных связей. Резитол ведет себя, как термопластичная смола - он размягчается при нагреве и становится твердым и хрупким при комнатной температуре;
«С» - получение резита - полностью отвержденного термореактивногс (нерастворимого и неплавящегося) продукта.
В резитольной стадии, когда большая часть летучих веществ уже удалена, из фенольных смол изготовляют, препреги. Сами по себе фенольньк смолы очень хрупки.
К недостаткам их следует отнести токсичность и необходимость при менять при отверждении высокие.давления. КМ на базе фенольных смол -это материалы, предназначенные для работы при высоких температурах, та! как способны выдерживать в течение длительного времени температуры дс 315°С, а кратковременно - выше 3000°С.
Кремнийорганические, или силиконовые смолы представляют co6oi синтетические соединения, содержащие наряду с органическими группам! кремний и кислород, которые входят в основную цепь в виде звеньев
КМ -на их основе сохраняют свойства при температуре выше 260°С отличаются коррозионной стойкостью, дуго- и искростойкостью, повышен ной теплопроводностью. Однако при комнатной температуре свойства КМ н; основе силиконовых смол ниже, чем на основе эпоксидных, полиэфирных i фенольных смол. Кроме того, они более дороги. На основе кремнийорганиче ских смол получают КМ, которые используются в конструкциях обтекателе) двигателей самолетов, ракет и других изделий, работающих при высоки: температурах.
Полиимидные смолы отличаются высокими показателями тепло- i термостойкости, радиационной стойкости. КМ на их основе способны дли тельное время работать при температурах выше 300°С. На конечной стадш образования полиимидные смолы теряют пластичность и растворимость ] превращаются в полициклические сетчатые полимеры. С ними связаны пер спективы создания высокотемпературных КМ. Недостатки существующи: полиимидных смол - необходимость использовать высокие температуры i давления при их отверждении.
Технология получения изделий из ПКМ включает следующие основ ные стадии:
1. Предварительная обработка поверхности УВ с целью улучшена ее смачиваемости растворами или расплавами связующих.
Углеродные волокна поступают к потребителю покрытыми замасли вателем, который необходим как технологическая добавка. Удаление замас ливателя с поверхности волокон (расшлихтовка) - необходимая операция пе пр.л ттпппиткпй vrx сяязллютим. Яля этого УВ тюпускают через бензин, boiные растворы олеиновой кислоты (2 мас.%), триэтаноламина (1 мас.%) или другие растворители. Удалить замасливатель можно и прокаливанием УВ при 200 - 450°С. Хороший эффект дает отмывка в воде с применением ультразвука. После расшлихтовки некоторые типы волокон усиленно адсорбируют влагу, что ухудшает адгезию к ним связующего и снижает эксплуатационные характеристики ПКМ в целом. Нанесение на поверхность гидрофобных (водоотталкивающих) покрытий, которые повышают прочность связи волокон со связующим и снижают водопоглощение ПКМ, называется стадией аппретирования. Закрепляют аппреты нагревом волокон до 80 - 150°С в течение 20 - 60 мин. В. тех случаях, когда волокна поступают на бобинах, не пригодных для намотки или пропитки, их укладывают на однонаправленную полосу, так называемую ровницу, обеспечивая при этом равномерное натяжение. Эту операцию называют снованием.
2. Приготовление связующего.
Кроме основного компонента (смолы) в связующее в зависимости от его природы вводят различное количество отвердителей, катализаторов, пластификаторов, пигментов. В качестве растворителей используют: ацетон, бензол, толуол, дихлорэтан, четыреххлористый углерод. Очевидно, что при работе с ними нужно соблюдать соответствующие требования техники безопасности.
Разбавители способствуют получению требуемой технологической вязкости связующего и остаются в нем после отверждения. Разбавители одновременно выполняют и роль пластификатора, повышая пластичность от-вержденных связующих. Например, в качестве разбавителя высоковязких эпоксидных смол используют низковязкие эпоксидные смолы диэтиленгли-коля, триэтиленгликоля. Смесь всех компонентов, входящих в состав связующего, называется компаундом.
Важной технологической характеристикой связующего является его жизненность (жизнеспособность) - способность сохранять определенное время (от нескольких минут до нескольких суток) технологическую вязкость в заданных пределах. С течением времени из связующего испаряются растворители, что увеличивает вязкость компаунда, ухудшает его пропиточные характеристики. Если растворитель испаряется медленно, то компаунд обладает высокой жизнеспособностью, однако существенно увеличивается время сушки изделий. Может даже получиться так, что время полного удаления растворителя превысит время отверждения связующего. В этом случае в отвер-жденном полимере будет много пор и газовых пузырей. Применение легколетучих растворителей резко уменьшает жизненность связующего, что также нежелательно. Например, для эпоксидных смол рекомендуется среднелету-чий растворитель толуол или его раствор в этиловом спирте.
При транспортировке и хранении связующего в него иногда попадает влага. Поэтому перед употреблением смолу разогревают в специальных металлических емкостях до 100 - 140°С и по удалении воды разводят растворителями или-разбавителями.
3. Пропитка.
Это операция совмещения наполнителя со связующим путем нанесе^ ния компаунда на поверхность УВ и заполнения им объема между волокна ми.
В настоящее время изделия из ПКМ получают в основном двумя спо собами г «мокрым» и «сухим». При мокром способе волокна пропитываютсз жидким связующим непосредственно перед намоткой, т.е. пропитка техноло гически совмещена с формованием изделия. При сухом способе пропитк; выделена в самостоятельную операцию, в результате которой из УВ и свя зующего. получают препреги. Пропитка и подсушка выполняются на специа лизированных заводах отдельно от намотки, что позволяет расширить диапа зон применяемых полимерных связующих за счет использования различны; растворителей. Связующие с растворителями имеют низкую технологиче скую вязкость, а это позволяет добиться высокого качества в равномерности пропитки. В частично отвержденном состоянии препреги могут находитьс. от нескольких дней до нескольких месяцев в зависимости от температуры ок ружающей среды.
Сухая намотка - более прогрессивный способ, нежели мокрая. Недос татки мокрой намотки сводятся к следующему:
Выбор связующих для мокрой намотки ограничен теми смолам!- которые можно, использовать в жидком виде, например, эпоксидными ил: полиэфирными.
В общем, растворители применять нежелательно, потому что лету чие вещества, удаляясь при отверждении намотанного изделия, приводят образованию пор, пузырей, ухудшают монолитность и прочность.
Использование жидких связующих ухудшает санитарные условия н рабочем месте.
Производительность мокрой намотки ограничена скоростью прс _ питкинитей связующим.
Применение подогрева для уменьшения технологической вязкост..смолы уменьшает жизнеспособность связующего, ускоряет процесс полим< гризации и ухудшает пропиточные свойства смолы.
6. При мокрой намотке трудно отрегулировать концентрацию комш.нентов в изделии. Часть смолы при мокром методе пропадает.
Всех перечисленных недостатков лишена сухая намотка препрегам] Скорость намотки не лимитируется скоростью пропитки и целиком завис* от возможностей намоточного оборудования. Намотка препрегами позволяв использовать широкую номенклатуру смол, обеспечить равномерное pacnpi деление связующего по всему объему изделия, снизить возможность появл й Ппеппеги липки, что дает возможность получать I них изделия сложной формы, повышенной герметичности и низкой пористости. При их формовании остается только обеспечить качественное соединение слоев связующего между собой (аутогезию) и с армирующими волокнами (адгезию).
К числу основных недостатков сухой намотки относится необходимость применять специальные станки и другую технологическую оснастку.
Различают следующие методы пропитки: протягивание арматуры (нитей) через жидкое связующее; купающимся роликом; напыление с принудительной пропиткой.
В производстве ГЖМ с арматурой в виде жгутов, нитей и тканей наиболее распространен метод пропитки протягиванием их через жидкое связующее (рис. 1.26).
Рис. 1.26. Схема вертикальной пропиточной машины; 1 - барабан, 2 -арматура, 3 - ванна с жидким связующим, 4 -- купающиеся ролики, 5 - сушильная шахта, 6 - нагреватели, 7 - вытяжное устройство, 8 - натяжное устройство, 9 - приемный барабан
Арматура (2) сматывается с барабана (шпулярника) (1) и, проходя через систему роликов (4), поступает в ванну (3) с жидким связующим. Пропитанная арматура поступает в сушильную шахту (5), где имеются нагреватели (6) и вытяжное устройство (7). Здесь арматура несколько раз меняет направление движения, чтобы увеличить время ее пребывания в зоне повышенной температуры. В результате из компаунда удаляются летучие вещества и пространство между волокнами заполняется связующим. Высушенный препрег с помощью приводного вала наматывается через натяжное устройство (8) н; приемный барабан.
Для ГЖМ с очень жесткой арматурой (высокомодульные графитовые борные или другие волокна), которая не допускает малых радиусов перегиба удобно использовать метод пропитки купающимся роликом (рис. 1.27).
Рис. 1.27. Схема пропитки купающимся роликом: 1 - арматура, 2 - емкость с жидким связующим, 3 - емкость, 4 - купающийся ролик
При вращении ролик захватывает на свою поверхность связующее переносит его на арматуру.
Метод напыления с принудительной пропиткой позволяет резк уменьшить время заполнения связующим межволоконного пространств; Применяют гидравлическую, вакуумную и механическую принудительны пропитки. .
В процессе гидравлической принудительной пропитки жидкое ев; зующее насосом прокачивается через арматуру.
Вакуумную принудительную пропитку осуществляют засасывание жидкости в вакуумированную камеру, где находится арматура.
Механическая принудительная пропитка более проста. Ее можно ос; ществлять в специальной (клиновой) камере или с помощью отжимного рс лика. Б ^клиновой камере (рис. 1.28) компаунд увлекается движущейся арм; турой в клиновую полость. Здесь за счет уменьшения сечения канала камер: возрастает давление жидкости перпендикулярно к движущейся арматуре. Пс действием этого давления и заполняется пространство между волокнами.
При пропитке с помощью отжимного ролика (рис. 1.286), давлени епосо"бетвующее пропитке и удалению из межволоконною пространства во: душных пузырей.; возникает в виде реакции ролика на натянутую ленту.
Рис. 1.28. Схемы механической принудительной пропитки в клиновой камере (а) и с помощью отжимного ролика (б): 1 - арматура, 2 -связующее, 3 - ролики
4. Формование.
Это операция придания изделию заданной формы и размеров. Формование можно осуществлять на прессах, контактным, вакуумным, автоклавным методами и намоткой.
Перед формованием на прессах предварительно пропитанную ровницу или ткань вручную или на специальных машинах разрезают на куски нужной длины. В зависимости от заданной структуры ПКМ укладывают куски в одном или нескольких чередующихся направлениях. Пакет кладут между плитами гидравлического пресса и уплотняют под давлением от нескольких до десятков атмосфер в зависимости от природы и структуры компонентов. Если арматура пропитана связующим горячего отверждения, то плиты пресса делают обогреваемыми. Этим способом обычно изготовляют листовые материалы типа текстолита.
Контактное формование - укатывание роликом пропитанной ленты или ткани. Обычно уплотнение проводят при комнатной температуре с использованием смол холодного отверждения. Этот метод используют в мелкосерийном производстве крупногабаритных и малонагруженных изделий.
Вакуумное формование изделий из ПКМ осуществляется за счет разности атмосферного и внутреннего (в объеме, где находится изделие) давлений. Вакуумное формование применяют для изготовления небольших партий изделий, так как метод малопроизводителен и сравнительно дорог.
По методу автоклавного формования изделие формуется небольшим Давлением, создаваемым водой или газом. Этот метод можно использовать для получения больших серий крупногабаритных деталей сложной формы.
Одним из самых распространенных способов получения ПКМ и изделий из них считается метод намотки. В этом случае пропитанная связующим арматура с натяжением наматывается на барабан (оправку). Намотка позво ляет автоматизировать процесс формования и программировать анизотропии свойств конечного продукта. Наиболее широко намотку используют для из готовления изделий, имеющих форму тел вращения (цилиндры, сферы, кону сы, тороиды и др.).
5. Отверждение.
В процессе отверждения связующего создается конечная структур; ПКМ, формируются его свойства и фиксируется форма изделия. Основньк технологические параметры отверждения - температура и время. Необходи мо строго выдерживать параметры, разработанные для каждой комбинацш связующего и арматуры.
Отверждение можно выполнять при комнатной температуре (холодно* отверждение), при повышенных температурах (горячее отверждение), в электрических или индукционных печах с автоматическим регулированием температуры, радиационным способом.
При отверждении наблюдаются две характерные стадии, через которые последовательно проходит термореактивное связующее: начальная - дс возникновения полимерной сетки и конечная - в процессе формирования полимерной сетки. Эти две стадии отделены друг от друга так называемой точкой гелеобразования. Точка гелеобразования соответствует тому моменту когда связующее утрачивает способность переходить в текучее состояние s растворяться в растворителях.
В определенной области температур жидкое связующее переходит i стеклообразное состояние. Все свойства связующего резко меняются: уменьшается удельный объем, увеличивается твердость, возникает сопротивление деформации. Температура, при которой происходит это явление, называется температурой стеклования. Температура стеклования - это не точка, а средняя температура интервала. Стеклование не является фазовым переходом, стеклообразное связующее имеет аморфную структуру и с термодинамической точки зрения может рассматриваться как переохлажденная жидкость.
Еще одной характерной точкой полимерных материалов считают температуру деструкции - температуру, при которой начинается заметное разложение полимера, сопровождающееся разрывом молекулярных связей. Деструкция, как и стеклование, протекает в интервале температур. Устойчивост! связующего к деструкции характеризуется его термостойкостью (термостабильностью, термоустойчивостью). Это понятие следует отличать от теплостойкости, которая отражает способность полимера к размягчению.
До полного исчерпания реакционноспособных групп реакция отверждения может протекать только в том случае, если температура отверждения выше температуры стеклования. В противном случае полного отверждения добиться нельзя. В полимере еще остаются реакционноспособные группы, не их скорость взаимодействия с другими группами очень мала из-за очень высокой вязкости системы. Если ШСМ с неполностью отвержденным связующим эксплуатировать при повышенных температурах, то отверждение будет продолжаться. Это приводит к изменению формы и размеров изделия, появлению дополнительных внутренних напряжений.
Часто реакция отверждения сопровождается выделением тепла, материал саморазогревается, и связующее может затвердеть полностью. На этом принципе основано холодное отверждение термореактивных связующих. Однако для ответственных изделий в большинстве случаев применяют горячее отверждение.
Арматура и связующее в композиции находятся под действием внутренних напряжений, которые можно разделить на три вида: структурные, усадочные и термические.
Структурные напряжения вызываются технологическим напряжением арматуры в процессе намотки. До снятия с оправки структурные напряжения действуют только в волокнах, в связующем их нет.
Усадочные напряжения возникают в волокнах и связующем вследствие уменьшения объема (усадки) связующего при его отверждении. Величина усадки может изменяться от 2 до 30 об.% в зависимости от природы компаунда.
Термические напряжения обусловлены разностью коэффициентов линейного расширения арматуры и связующего и неравномерностью распределения температур в объеме изделия. Как правило, коэффициент линейного расширения у полимеров существенно выше, чем у волокон.
В реальном ПКМ все рассмотренные напряжения суммируются и материал находится под действием результирующих напряжений, которые со временем релаксируют. Чтобы способствовать более полной релаксации напряжений и избежать коробления и растрескивания, рекомендуется медленно нагревать и охлаждать изделия из ПКМ.
Углепластики с низкомодульными волокнами в качестве конструкционных не используют. Из них изготовляют токопроводящие, теплозащитные и антифрикционные материалы.
Конструкционные углепластики содержат в качестве наполнителя высокомодульные (Е = 342 - 540 ГПа) и высокопрочные (ст е г - 2,5 ГПа) углеродные волокна. Для конструкционных углепластиков характерны низкие плотность и коэффициент линейного расширения и высокие модуль упругости, прочность, термостойкость, тепло- и электропроводность.
Свойства углепластиков определяются материалом связующего, свойствами, концентрацией и ориентацией волокон. Углепластики на основе эпоксидных смол имеют высокие характеристики прочности при температурах ниже 200°С (табл. 1.6). Эти ПКМ чаще всего изготавливают из препрегов, выпускаемых в виде лент различной ширины. Прочность при растяжении и изгибе для однонаправленных углепластиков может составлять 1000 - 1600 МПа и более, а модуль упругости (1 - 2,5)-10 МПа и более. По удель ной прочности и жесткости углепластики оставляют далеко позади стекло пластики, сталь, алюминиевые и титановые сплавы.
Таблица 1.(
Свойства высокомодульных и высокопрочных эпоксидных углепластиков
Показатели |
Эпоксидные углепластик! |
|
высокомодульные |
высокопрочные |
|
Плотность, кг/м 3 | ||
Прочность, МПа, при сжатии растяжении и изгибе межслойном сдвиге | ||
Модуль упругости при растяжении и изгибе, ГПа | ||
Усталостная прочность при изгибе на базе 10 7 циклов, ГПа |
В углепластиках, предназначенных для длительной работы при темпе" ратурах до 250°С, используют фенольные, до 300°С - кремнийорганические i до 330°С - полиимидные связующие. Разрабатываются связующие с рабочими температурами до 420°С. Еще более выраженным, чем у стеклопластиков недостатком углепластиков является низкая прочность при межслоевом сдвиге. Это связано со слабой адгезией полимеров к углеродным волокнам. Чтобь: повысить адгезию, используют несколько способов: травление поверхности волокон окислителями (например, азотной кислотой), выжигание замаслива-теля; аппретирование - предварительное покрытие волокон тонким cnoeiv смачивающего их мономера; вискеризацию - выращивание «усов» (ворса) ш углеродных волокнах. Углепластики, в которых кроме ориентированных непрерывных волокон в качестве наполнителя используются усы, называю! вискеризованными или ворсеризованными.
Анизотропия свойств у углепластиков выражена еще более резко, чем у стеклопластиков. Связано это с тем. что отношение модулей упругости наполнителя и связующего у углепластиков (100 и более) существенно выше, чем у стеклопластиков (20 - 30). Кроме того, для углепластиков характернс наличие разницы между упругими свойствами самих волокон в направление вдоль оси и перпендикулярно к ней, что приводит к дополнительной анизотропии. Обычно в конструкциях нужна меньшая анизотропия механически* характеристик. В этом случае используют перекрестно армированные материалы. Меняя объемное содержание волокон и текстуру ПКМ, можно изменять свойства композиций в очень широких пределах.
Углепластики отличает высокое сопротивление усталостным нагрузкам. По величине предела выносливости на единицу массы углепластики значительно превосходят стеклопластики и металлы. Одна из причин этого -меньшая (чем, например у стеклопластиков) деформация при одинаковом уровне напряжений, снижающая растрескивание полимерной матрицы. Кроме того, высокая теплопроводность углеродных волокон способствует рассеиванию энергии колебаний, что снижает саморазогрев материала за счет сил внутреннего трения.
Ценное свойство углепластиков - их высокая демпфирующая способность и вибропрочность. По этим показателям углепластики превосходят металлы и некоторые другие конструкционные материалы. Регулировать демпфирующую способность можно, изменяя угол между направлениями армирования и приложения нагрузки.
Из углепластиков изготовляют конструкции, работающие на устойчивость под воздействием внешнего изгибающего момента, давления или осевого сжатия: лопасти несущего винта вертолетов, корпусы компрессоров и вентиляторов, вентиляторные лопатки, диски статора и ротора компрессора низкого давления авиационных двигателей. Применение в этих узлах углепластиков взамен металлов позволяет на 15 - 20% снизить массу двигателя. В космической технике углепластики применяют для панелей солнечных батарей, баллонов высокого давления, теплозащитных покрытий.
Коэффициент линейного расширения высокомодульных однонаправленных углепластиков в продольном направлении близок к нулю, а в интервале 120 - 200°С даже отрицателен (-0,5-10" 6 1/°С). Поэтому размеры изделий из углепластиков при нагреве и охлаждении изменяются очень мало.
Углепластики обладают довольно высокой электропроводностью, что позволяет применять их как антистатические и электрообогревающие материалы. С увеличением содержания УВ в ПКМ до определенной объемной доли (40 - 70%) в зависимости от типа полимеров и УВ, текстильной формы УВ наблюдается повышение прочности и модуля упругости. Затем эти показатели начинают ухудшаться вследствие недостаточного количества полимера, необходимого для получения монолитного композита и разрушения хрупких УВ на стадии формирования при высокой степени уплотнения. Максимальное содержание УВ в ПКМ ограничивается также плохой смачиваемостью УВ связующим.
В некоторых случаях применение в качестве наполнителя только углеродных волокон не обеспечивает необходимую вязкость, эрозионную стойкость, прочность при сжатии, растяжении и сдвиге. Тогда связующие армируют совместно углеродными и стеклянными или углеродными и борными волокнами. Комбинированное армирование позволяет расширить диапазо! значений прочности, жесткости и плотности ПКМ.
Химическая стойкость углепластиков позволяет применять их в про изводстве кислотостойких насосов, уплотнений. Углеродные волокна имею" низкий коэффициент трения. Это дает возможность использовать их в качест ве наполнителя для различных связующих, из которых делают подшипники прокладки,-втулки, шестерни.
Развитие техники требует механически прочных и термостойких мате риалов. Это вызвало особый интерес к углерод-углеродным композиционнка материалам (УУКМ), содержащим углерод как в виде армирующего напол нителя, так и в виде матричного материала.
В УУКМ высокая температуростойкость сочетается с малой плотно стью, высокими прочностью и модулем упругости, стойкостью к тепловом; удару. Эти материалы длительно работоспособны при температурах до 500°(в окислительной среде и до 3000°С в инертной среде и в вакууме.
Наполнитель и матрица УУКМ в зависимости от состава и условш карбонизации могут иметь разные модификации. В принятой классификацш указывается сначала структура углерода-наполнителя, затем матрицы, на пример, углерод-углеродный, графит-углеродный, графит-графитный мате риал.
В УУКМ углеродный наполнитель содержится в виде дискретных во.локон, непрерывных нитей или жгутов, войлоков, лент, тканей с плоским i объемным плетением, объемных структур. Волокна располагаются хаотиче.ски одно-, двух- и трехнаправленно. Используют низкомодульные, высоко модульные и высокопрочные УВ, полученные из вискозных, полиакрилонит рильных волокон и каменноугольного пека.
В качестве матрицы может использоваться пиролитический углерод, также каменноугольный пек и коксующиеся полимеры, которые в процесс термодеструкции дают более 50 мас.% кокса. Чаще всего применяют феноль ные смолы (выход кокса 54 - 60 мас.%). Известно применение полиймйдо (63 - 74 мас.%), кремнийорганических смол (84 - 87 мас.%), продуктов кон денсации фенола и нафтенов с формальдегидом (70 мас.%), олигобензимида.золов (74 мас.%), фурфуриловых смол и других, полимеров. Чем больше вы ход и, прочность кокса, а также прочность его сцепления с наполнителем, tci .выше качество УУКМ.
, .„.„ Для получения композита с заданными свойствами необходимо опре делить наиболее выгодное сочетание наполнителя и матрицы, а также вь: v 6paTb, наиболее благоприятный технологический режим получения yraepoj ной матрицы.
В зависимости от фазового состояния углеродсодержащих вещест различают следующие способы уплотнения углеродом углеродных волокю стых наполнителей (УВН):
с использованием углеводородов в газовой или паровой фазах (при родный газ, пропан-бутан, бензол и т.п.);
с использованием жидких углеводородов, характеризующихся высо ким содержанием углерода и большим процентом выхода кокса (пеки, смо лы);
комбинированный, включающий в себя пропитку пористых каркасов жидкими углеводородами и карбонизацию, затем уплотнение пиролитиче- ским углеродом, получаемым пиролизом газофазных углеводородов.
Процесс уплотнения каркаса можно производить несколькими способами.
При изотермическом способе предусматривается пропускание угле-родсодержащего газа над поверхностью нагретого каркаса при сравнительно умеренном давлении. Недостаток - длительность процесса, образование поверхностной корки, препятствующей проникновению газа внутрь каркаса. Этот способ наиболее эффективен для изделий малой толщины.
В другом способе по всей толщине каркаса устанавливается разность давлений, и углеродсодержащий газ принудительно фильтруется через него. Принудительная фильтрация ускоряет процесс уплотнения и намного увеличивает толщину пропитки. Однако вследствие понижения концентрации уг-леродсодержащего газа по толщине слоя структура материала получается не-равноплотной.
Наибольшее распространение получил термоградиентный способ, когда по всей толщине пористого каркаса устанавливается определенная разность температур и углеродсодержащий газ проходит со стороны поверхности с низкой температурой. В этом случае исключается образование поверхностной корки, что способствует получению качественного материала. Данный способ наиболее эффективен при уплотнении каркасов средней и большой толщины.
При термическом разложении углеводородов в газовой фазе одновременно протекают различные химические процессы, в результате которых возникают как более легкие, так и более тяжелые углеводороды, водород, различные твердые углеродные продукты. Структура и свойства углеродных продуктов многообразны и зависят от условий протекания процесса. Например, продукты термического разложения в зависимости от внешней геометрической формы содержат:
слоистый или блестящий углерод, получивший название пироуг-лерод (ПУ);
Волокнистый или нитевидный углерод; углерод в дисперсном состоянии или сажу.
Образование ПУ имеет место в широком диапазоне температур от 700 До 3000°С. Состав исходных газов определяет выход ПУ и скорость его отложения. Наибольший выход ПУ получается из метана, имеющего наименьшую молекулярную массу. У углеводородов с большой молекулярной массой на блюдается повышенный выход сажи. Существенное значение при этом имее" давление газа в реакторе.
Известны два основных вида ПУ, структура и свойства которых опре деляются температурой образования: низкотемпературный (1000 - 1100°С) i высокотемпературный (1400 - 2200°С), называемый пирографитом.
Процесс газофазного осаждения ПУ осуществляется в установи (рис. 1.29), состоящей из водоохлаждаемого реактора, станции управления систем подачи природного газа, создания вакуума, охлаждения и силовоп оборудования. Заготовка - углеродный каркас (4) устанавливается на графи товые нагреватели (3), зажатые между тоководами (2). После вакуумированиз камеры в реактор подают природный газ. Нагрев осуществляют прямым про пусканием" тока через нагреватель (3), контроль температуры - подвижным! хромель-алюмелевыми термопарами (5), размещенными в кварцевых чехлах В начале процесса термопара устанавливается спаем у поверхности нагрева теля. При принятой схеме уплотнения ПУ зона пиролиза перемещается о-нентра заготовки к периферии.
При газофазном осаждении ПУ одним из критериев качества получав мого материала является его плотность. Она является функцией многих па раметров и зависит от плотности каркаса, скорости движения фронта пироли за, концентрации реагента и давления газа в реакторе.
Рраждение пироуглерода из газовой фазы на УВН в основном осуще ствляется при температурах 1100 - 1500°С и пониженном давлении в атмо сфере, содержащей 91 - 93% метана и 7 - 9% аргона. Графитация осуществ ляется,в инертной атмосфере.
Технологический процесс получения УУКМ жидкофазным методе!* включает изготовление пористого каркаса, пропитку его жидкими углеводородами, карбонизацию под давлением и графитацию. Выбирая пропиточньц материал для пропитки, учитывают следующие его характеристики:
вязкость;
выхрд кокса;
микроструктуру кокса;
Кристаллическую структуру кокса.
Все эти характеристики зависят от давления и температуры в процесс* гкщче.ния углерод-углеродных композитов. В качестве смол чаще всегс применяют фенольные, полиамидные, поливинилсилоксановые, полифенил-силоксановые, фурфуриловые и эпоксиноволачные. Прогрессивным и перспективным направлением является использование в качестве пропиточной материала, пеков нефтяного и каменноугольного происхождения. Эти свя зующие имеют следующие достоинства: низкую стоимость, высокое содер жание углерода при сохранении термопластичности, способность к графитации подготовленных мезофазных пеков. К недостаткам следует отнести: токсичность, непостоянство качества.
Ш
Рис. 1.29. Схема установки термоградиентного метода газофазного осаждения пироуглерода: 1 - водоохлаждаемый реактор, 2 - токо-подводы, 3 - нагреватель, 4 - углеродный каркас, 5 - термопара в кварцевой трубке, 6 - механизм перемещения термопары, 7 - водяная рубашка; потоки: I - газ, II - газообразные продукты пиролиза, Ш - вода.
Химический состав и свойства пеков изменяются в широких пределах в зависимости от природы исходного сырья и технологических условий. В определенных условиях в пеках может зарождаться и расти жидкокристаллическая фаза (мезофаза), которая обеспечивает образование анизотропного графитирующегося кокса. В связи с этим в настоящее время различают пеки изотропные (обычные, немезофазные) и анизотропные (мезофазные).
При низкотемпературной карбонизации (550 - 650°С) происходит переход мезофазы в твердый полукокс. Этот процесс сопровождается вспучиванием под действием выделяющихся газов, что ведет к образованию мелкопористой структуры кокса. При вспучивании происходит глубокая деформация кокса и увеличение числа дефектных структур, что при последующей термообработке приводит к возникновению усадочных трещин.
Формирование структуры и свойств углерод-коксовой матрицы зависит от условий термообработки, которые можно условно разделить на несколько стадий:
Карбонизацию (900 - 1423°С) - разложение органических соедиш
ний и формирование молекулярной упорядоченной структуры углерод-кокса
предкристаллизацию (1400 - 2000°С) - упорядочение атомов yi
лерода в более совершенную структуру с образованием так называемых пер<
ходных форм углерода;
гомогенную графитацию (2000 - 3000°С) - превращение перехо; ных форм углерода в кристаллический графит.
На рис. 1.30 приведена схема установки для пропитки углеродно ткани.
Рис. 1.30. Схема установки для пропитки углеродной ткани: 1 - расходная катушка, 2 -углеродная ткань, 3 -прижимные вальцы, 4 -электропечь, 5 -- устройство, регулирующее скорость подачи ткани, 6 -приемная катушка; 7 - электропривод, 8 - ванна
Ткань сматывается с расходной катушки (1) и проходит через ваш (8), в которой три высокоскоростные мешалки интенсивно перемешивав порошок пека с водой, создавая стабильную водно-пековую суспензию. IIj дальнейшем прохождении ткани через прижимные валки (3) и электроне 1 (4) вода испаряется и пек, "расплавляясь, пропитывает ткань. Полученнь препрег с помощью электропривода (7) и регулирующего устройства скор сти подачи ткани (5) наматывается на приемную катушку (6). На выходе печи лента"прижимается валом, нагретым до 100 - 120°С и выдавливают! пек в объем ткани.
Предварительная пропитка пористого углеродного каркаса пеком может производиться под давлением от 0,5 до 3 МПа, карбонизация - при давлении 100 - 200 МПа и температуре 900 - 1100°С.
Особенностью УУКМ является относительно высокая пористость углеродной матрицы, а также ее пересеченность трещинами в направлении, перпендикулярном к наполнителю. Трещины в матрице возникают при охлаждении изделия от температуры получения (3000°С) до комнатной вследствие высоких термических напряжений. Для устранения пористости операцию пропитки-карбонизации с последующей графитацией и операцию пропитки пироуглеродом повторяют несколько раз (рис. 1.31).
После многократных повторений цикла пропитка-карбонизация плотность материала может достигать 2000 - 2100 кг/м 3 . Если температура обработки не превышает 800 - 1500°С, происходит карбонизация связующего, а при температурах 2300 - 3000°С получают графитированный материал. Карбонизация углепластика проводится в токе инертного газа или восстановительной атмосфере с повышенным давлением при изотермическом, динамическом или"ступенчатом нагреве; графитация - в инертной атмосфере.
Углеродные
волокна
Намотка Уклада 3 \ ^Изготовление
объемных Вязание изделия \ тканей
структур \
Прошивка
Пропитка пеком
* Карбонизация
Повторная пропитка Повторная карбонизация
Графитация Рис. 1.31. Схема получения УУКМ с использованием метода пропитки
Комбинированный или комплексный метод получения УУКМ может быть реализован по следующим схемам:
Пропитка пеком пористого каркаса, карбонизация под давлением, доуплотнение ПУ из газовой фазы;
Уплотнение каркаса ПУ из газовой фазы до заданной плотност пропитка пеком с последующей карбонизацией, механическая обработка, д уплотнение ПУ.
Этот метод обеспечивает максимальную плотность, высокие физик механические характеристики и не требует дополнительного оборудования.
В тех случаях, когда карбонизация УУКМ проводится без давлени
Процесс может быть осуществлен в обычных обжиговых (газокамерных) п
чах, конструкция которых была рассмотрена ранее. Технология производст]
УУКМ жидкофазным методом в части карбонизации под давлением мож<
быть реализована с использованием прессов.
Графитация (графитизация) осуществляется в печах Ачесона, коне рукция которых была рассмотрена в предыдущих главах.
Свойства УУКМ изменяются в широком диапазоне. Прочность карб низованного УУКМ пропорциональна плотности. Графитация карбонизова: ного УУКМ повышает его прочность. Прочность УУКМ на основе высок: прочных УВ выше прочности КМ на основе высокомодульных УВ, получе! ных при различных температурах обработки. К уникальным свойства УУКМ относится высокая температуростойкость в инертных и восстанов] тельных средах. По способности сохранять форму и физико-механичесю свойства в этих средах УУКМ превосходит известные конструкционные м териалы. Некоторые УУКМ, особенно полученные карбонизацией углепл стика на основе органических полимеров, характеризуются увеличение прочности с повышением температуры эксплуатации от 20 до 2700°С. Пр температурах выше 3000°С УУКМ работоспособны в течение короткого вр мени, так как начинается интенсивная сублимация графита. Чем совершение кристаллическая структура графита, тем при более высокой температуре и меньшей скоростью происходят термодеструктивные процессы. Свойст] УУКМ изменяются на воздухе при длительном воздействии относителы невысоких температур. Так, при 400 - 650°С в воздушной среде происход! окисление УУКМ и, как следствие, быстрое снижение прочности в результ. те нарастания пористости. Окисление матрицы опережает окисление УВ, е< ли последние имеют более совершенную структуру углерода. Скорость оки> ления УУКМ снижается с повышением температуры их получения и умен: шением числа дефектов. Эффективно предотвращает окисление УУКМ пр< питка их кремнийорганическими соединениями из-за образования карбида оксида кремния.
На рис. 1.32 представлены области применения УУКМ.
ационно-стойкие
Рис. 3.32. Области применения УУКМ в условиях высоких тепловых нагрузок
Таким образом, УУКМ используются в различных отраслях техники в тех случаях, когда традиционные материалы неработоспособны, т.е. в условиях высоких тепловых нагрузок и в узлах трения.
Технология композитов решает задачи получения упрочненных материалов. Слово технология происходит, от двух греческих: технэ - мастерство и логос - слово, учение. Обычно в названиях такого типа вторая часть «логия» соответствует понятию «наука». Например, зоология - наука о животных, геология - наука о строении Земли. По аналогии, следовало бы определить технологию как науку о мастерстве.
Технология композитов – раздел технологии материалов
Но слово «наука» рядом со словом «технология» появилось сравнительно недавно. Технология обычно определяется как совокупность способов. Если речь идет о технологии материалов , то это совокупность способов получения и переработки материалов.
Технология композитов - задача для специалиста
Возьмем для примера специалиста по технологии композитов . Какие задачи приходится ему решать? Вот одна из них. Даны: борные волокна, намотанные на бобины; алюминий (в любом виде - листы, проволока, порошок, расплав) можно выбрать по своему усмотрению. Требуется: соединить волокна и алюминиевую матрицу друг с другом, получив при этом высокопрочный бороалюминиевый. Технолог должен решить, как это сделать. Чтобы разговор был более конкретным, давайте обсудим, как получить такой композит в виде листа, в котором все волокна распределены равномерно по сечению и уложены параллельно друг другу. Решить поставленную задачу - это значит дать ответы ни три основных вопроса:- Как обеспечить укладку волокон в заданном направлении?
- Как ввести волокна в матрицу, чтобы получить лист с требуемой структурой и свойствами?
- Как предотвратить разупрочнение и разрушение волокон в процессе изготовления материала, обеспечив в то же время прочную связь их с матрицей?
Как сориентировать волокна в композите
Начнем по порядку. Как сориентировать волокна в композите ? Если бы они были достаточно толстыми, как стальные прутья, которыми армируют , особых проблем не возникало бы. Можно по одному уложить в специально подготовленные гнезда.
Как ввести волокна в матрицу
Но лучше поступить по-другому. В качестве скрепляющего средства использовать сам матричный материал. Тогда можно выполнить сразу две задачи, чтобы выдержать правильно технологию композита: зафиксировать волокна в требуемом положении и одновременно ввести их в матрицу , то есть ответить на второй основной вопрос нашей задачи. Мысль неплохая. Но опять возникает все то же неотвязное - как? Как это сделать? Без знаний физики и химии здесь не обойдешься.Электрохимический метод
Можно использовать электрохимический метод , нанося на барабан с намотанными на него волокнами гальваническое покрытие из матричного металла. Это не очень сложно принципиально, но:- требует много времени,
- не все металлы можно так наносить,
- трудно обеспечить нужный состав матрицы, если речь идет о сложных сплавах.
Плазменное напыление покрытий
А вот наиболее подходящий вариант. Использовать плазменное напыление покрытий . При этом способе матричный материал расплавляется потоком низкотемпературной плазмы (ионизированного газа со средней температурой около 10 000 К), этим же потоком он распыляется и переносится на поверхность барабана, покрывая волокна и заполняя промежутки между ними. Плазменный поток получают с помощью специального устройства - плазмотрона, в котором рабочий Газ (азот, аргон, водород, гелий и др.) ионизируется под действием дугового разряда. Хотя образующаяся в обычных плазмотронах плазма называется низкотемпературной, этой «низкой» температуры (10 000 К) вполне достаточно, чтобы расплавить любой из существующих в природе материалов. Капельки расплавленного металла долетают до холодного барабана и, отдавая ему тепло, кристаллизуются, образуя равномерное покрытие на барабане, если тот равномерно вращать. Подлежащий распылению материал (в нашем случае - алюминий) обычно вводят в плазменную струю в виде порошка или проволоки. Внешне процесс нанесения плазменных покрытий напоминает окрашивание с помощью краскопульта. Только вместо краскопульта - плазмотрон, а вместо краски - матричный сплав. В принципе не обязательно для этой цели использовать плазму, можно обойтись газовой горелкой или другим устройством, но плазменное напыление весьма удобно и его широко применяют при создании композитов. Полученный после напыления армированный монослой разрезается по одной из образующих цилиндра и разворачивается в плоскость. Прочность покрытия достаточна, чтобы не давать волокнам сместиться относительно друг друга, но недостаточна, чтобы обеспечить высокую прочность композита. Толщина получаемых монослоев составляет обычно полтора-два диаметра волокон, то есть около 200 мкм, а нам, напомню, нужен лист толщиной 5 мм. Как быть? Опять «как?».Прокатка монослоев
На этот раз ответ искать долго не приходится: нужно сделать слоеный пирог из полученных монослоев, то есть собрать их в пакет нужной толщины и каким-то образом уплотнить, соединив неразъемно друг с другом. Это можно сделать, например, прокаткой монослоев или горячим прессованием. В первом случае пакет нагревают в печи и пропускают между вращающимися валками. Во время прокатки происходит соединение монослоев в монолитный материал и уплотнение матричного материала в каждом монослое, что приводит к повышению прочности матрицы и прочности ее связи с волокнами.Горячее прессование монослоев
Иногда более целесообразно уплотнять пакеты из монослоев не прокаткой, а горячим прессованием . Для этого их укладывают в пресс-форму, длина и ширина рабочей плоскости которой соответствует размерам монослоев, и сверху прижимают пуансоном. Пресс-форма обогревается, чтобы можно было обеспечить требуемую температуру процесса. Нагретый пакет уплотняется, отсюда и название - горячее прессование. Для того, чтобы между монослоями возникла прочная связь и чтобы все частички напыленного матричного металла сварились друг с другом, образовав монолит, нужно дать выдержку под давлением, позволив тем самым сделать свое дело диффузионным процессам. Именно эти процессы вместе с давлением обеспечивают высокие механические свойства нашего слоеного пирога. Вот почему такой способ получения композитов иногда называют диффузионной сваркой.Технология композитов в виде прутка или сложного профиля
Применительно к поставленной задаче мы ответили на второй вопрос - как ввести волокна в матрицу. А как быть, если нужно получить композит в виде прутка или сложного профиля? Очередное «как». Можно снова прибегнуть к прокатке пакетов из монослоев , только не в гладких валках, а в калиброванных, то есть имеющих специальные вырезы, которые соответствуют требуемой конфигурации. А можно применить так называемые жидкофазные методы , когда матрица в процессе получения композита находится в жидком состоянии. Волокна, сматываясь с катушек (число катушек равно числу волокон в композите), проходят, не касаясь друг друга, через ванну с расплавленным матричным металлом, смачиваются им и поступают в фильеру, которая формирует пруток нужного сечения. После этого пруток охлаждается, металл матрицы затвердевает, образуя с волокнами композиционный материал. Таким способом можно получать прутки самых разнообразных профилей. Изделия сложного профиля, например лопатки турбин, удобно получать методом пропитки. В литейную форму, рабочая полость которой соответствует форме лопатки, укладывают волокна (как это сделать - отдельный вопрос, который мы рассматривать сейчас не будем, но сделать это можно, хотя и не просто), а затем в форму заливают жидкий матричный металл. Промежутки между волокнами обычно небольшие, и расплавленному металлу заполнить их трудно, а заполнить нужно, причем как можно быстрее, чтобы волокна не успели раствориться в матрице. Поэтому в большинстве случаев пропитку осуществляют под давлением. Литейную форму вакуумируют, а жидкий металл поступает в нее под атмосферным давлением. Как правило, перепада давлений в одну атмосферу достаточно для быстрой и надежной пропитки. Но это только в случае, когда волокна смачиваются расплавленным матричным металлом. Если этого не происходит, нужно принимать меры. Например, углеродные волокна не смачиваются жидким алюминием, поэтому получить угле-алюминий, просто пропитывая графитовые нити алюминием, не удается. Но если предварительно покрыть эти нити тончайшим слоем хрома или никеля (достаточно нанести покрытие толщиной один микрометр), которые хорошо смачиваются алюминием, пропитка будет обеспечена и композит получить можно. Основное занятие технолога - отвечать на вопрос «как?». Как сделать? Правильные ответы на этот вопрос можно дать, если известны ответы на вопрос «почему?». Если представить себе автомеханика, который умеет закручивать болты и гайки, но не знает устройства автомобиля. Грош ему цена. Так же и технолог, не понимающий физики процессов, происходящих при получении материала,- неполноценный специалист. Например, технолог знает, что во многих случаях после нагрева композит разупрочняется. Сразу возникает задача - как с этим бороться? Этот вопрос аналогичен третьему «как?», поставленному в начале беседы. А чтобы решить эту задачу, нужно знать, почему происходит разупрочнение композита. Ответ на эти вопросы и дает технология композита.Роботизированный комплекс для механической обработки изделий из композитных материалов предназначен для механизации и автоматизации одних из самых трудоемких операций в технилогическом цикле:
- Обрезка и удаления технологического облоя
- Фрезерования пазов, выемок и позиционеров под закладные элементы
- Сверление и фрезерование сквозных отверстий сложной формы
- Фрезерование сквозных отверстий больших размеров (оконные проемы, люки и другое)
Роботизированный комплекс позволяет обеспечить следующие примемущества:
- Увеличение скорости обработки по сравнению с ручным способом
- Высокая повторяемость и качество обработки
- Фрезерование с высоким качеством кромки «за один проход»
- Улучшение условий труда
- Создание дополнительных наукоемких рабочих мест
При контактном методе формования стекломатериал вручную пропитывается смолой с помощью кисти или валика. Пропитка может осуществляться одновременно с прикаткой в форме, либо отдельно. Прикатка осуществляется для удаления из ламината воздуха и равномерного распределния связующего.
1В статье представлено современное состояние технологий производства изделий из композиционных материалов, включая сведения о применяемых технологиях, программном обеспечении, оборудовании для создания матриц, оборудовании для создания композиционных изделий, оборудование контроля геометрии изделия и неразрушающего контроля.
композиционные материалы
программное обеспечение
оборудование для создания матрицы
1. Современные композиционные материалы / под ред. П. Крока и Л. Броумана; пер. с англ. – М., 1978.
2. Конструкция и прочность корпусов судов и кораблей из стеклопластика. Иностранное судостроение в 1965 – 1973 гг. // Судостроение, 1973.
3. Фролов С.Е. Методы создания новых макронеоднородных композиционных материалов и технологические решения при изготовлении из них корпусных конструкций // Судостроение № 3 2003, с. 55-59.
4. CAE – технологии в 2012 году: обзор достижений и анализ рынка. – CAD/CAM/CAE Observer #4 (80) / 2013.
5. Интервью В.А. Середка и А.Ю. Софронова журналу CAD/CAM/CAE Observer #2 (78) / 2013.
6. Умные технологии для авиастроения. Повышение конкурентоспособности отечественных авиастроительных предприятий на примере совместных проектов компании «Солвер» и ОАО «ВАСО» // САПР и графика, № 1. 2011. С. 56-62.
7. Лукьянов Н.П. Опыт применения композиционных материалов для постройки кораблей ПМО // Судостроение. № 3. 2007. С. 19-26.
Композиционный материал представляет собой материал, структура которого состоит из нескольких компонентов различных по своим физико-механическим свойствам: металлические или неметаллические матрицы с заданным распределением в них упрочнителей, их сочетание придает композиционному материалу новые свойства. По характеру структуры композиционные материалы подразделяются на волокнистые, упрочненные непрерывными волокнами и нитевидными кристаллами, дисперстноупрочненнные материалы, полученные путем введения в матрицу дисперсных частиц упрочнителей, слоистые материалы, созданные путем прессования или прокатки разнородных материалов .
Сегодня композиционные материалы особенно востребованы в различных отраслях промышленности. Первые суда из стеклопластика были изготовлены во второй половине 30-х годов двадцатого века. С 50-х годов стеклопластиковое судостроение получило широкое распространение в мире, было построено значительное число яхт, рабочих и спасательных катеров и рыболовецких судов, десантно-высадочных судов и др. . Одним из первых применений в авиации композиционных материалов явилось изготовление из углепластика в 1967 г. панелей задней кромки крыла самолета F-111A. В последние годы в изделиях аэрокосмического назначения все чаще можно встретить конструкции из трехслойного «сэндвича» сотовым алюминиевым заполнителем и обшивками из углепластика. В настоящее время порядка 50 % от общей массы самолета Boeing 787 или Airbus A350 составляют композиционные материалы. В автомобилестроении композиционные материалы применяются достаточно давно, в основном получили развитие технологии изготовления аэродинамического обвеса. Ограниченно композиционные материалы применяются для изготовления деталей подвески и двигателя.
Однако до последнего времени на предприятиях использовалась в основном ручная выкладка деталей из композитов, а серийность выпускаемой продукции не требовала глубокой автоматизации процессов. Сегодня с развитием конкуренции на рынке не обойтись без современных средств проектирования и подготовки производства, а также без эффективного оборудования для работы с композитами.
Технологии создания изделий из композиционных материалов
В большинстве случаев в качестве связующего наполнителя используется химически отверждаемая термореактивная смола, процесс отверждения характеризуется экзотермической химической реакцией. В основном используются полиэфирные, эпоксидные, фенольные и высокотемпературные смолы. Чаще всего в изготовлении деталей сложной конфигурации применяют технологии суть которых заключается в выкладке «сухой» основы с последующей пропиткой связующим составом («влажная» формовка, намотка, инжекция, Resin Transfer Molding / RTM) или с поочередной выкладкой «сухой» основы с пленочным клеем (вакуумная пропитка, Resin Film Infusion / RFI). Существует несколько основных технологий изготовления деталей из композиционных материалов, включая ручные и автоматизированные методы:
- пропитка армирующих волокон матричным материалом;
- формирование в пресс-форме лент упрочнителя и матрицы, получаемых намоткой;
- холодное прессование компонентов с последующим спеканием;
- электрохимическое нанесение покрытий на волокна с последующим прессованием;
- осаждение матрицы плазменным напылением на упрочнитель с последующим обжатием;
- пакетная диффузионная сварка монослойных лент компонентов;
- совместная прокатка армирующих элементов с матрицей и др.
Кроме того широкое распространение получила технология изготовления деталей с использованием препрегов (полуфабрикатов, представляющих собой материал основы, пропитанный связующим составом).
Программное обеспечение
Задачей конструирования изделия из композиционных материалов является правильный подбор композиции, обеспечивающий сочетание свойств, необходимых в конкретном эксплуатационном случае. При конструировании армированных полимерных композиционных материалов широко используется компьютерная обработка данных, для чего разработано большое количество разнообразных программных продуктов. Их использование позволяет повышать качество продукции, сокращать длительность разработки и организации производства конструкций, комплексно, качественно и быстро решать задачи их рационального проектирования. Учет неравномерности нагрузок позволяет проектировать корпусную конструкцию из армированного композита с дифференцированной толщиной, которая может изменяться в десятки раз.
Современные программные продукты можно условно разделить на две группы: выполняющие пакетный анализ ламинатов в «двухмерной» или «балочной/пластинной» постановке и в трехмерной. Первая группа - это программы типа Laminator, VerctorLam Cirrus и др. «Трехмерное» решение - метод конечных элементов, и тут большой выбор среди имеющихся программных продуктов. На рынке «технология моделирования композитов» существуют различные программные продукты: FiberSim (Vistagy / Siemens PLM Software), Digimat (e-Xstream / MSC Software Corp.), Helius (Firehole Composites / Autodesk), ANSYS Composite PrepPost, ESAComp (Altair Engineering) и др. .
Практически все специализированное программное обеспечение различных компаний, имеет возможность интеграции с системами СAD высокого уровня - Creo Elements/Pro, Siemens NX, CATIA. В целом, работа выглядит следующим образом: выбирается материал слоев, определяются общие параметры пакета слоев, определяется метод формирования слоев, послойный метод применяется для производства несложных деталей, для сложных изделий применяются методы зонного или структурного проектирования. В процессе выкладки слоев задается их последовательность. В зависимости от метода производства изделия (ручная выкладка, формование, выкладка ленты, выкладка волокна) осуществляется послойный анализ материала на возможные деформации. Состав слоев приводится в соответствие с шириной используемого материала.
После завершения формирования слоев пользователь получает данные об изделии, позволяющие использовать их для различных целей, например:
- вывести в виде конструкторской документации;
- использовать в виде исходных данных для раскроя материала;
- исходные данные для лазерного проектора для обозначения контуров мест укладки выкроек.
Переход на современные технологии проектирования и подготовки производства изделий позволяет:
- сократить расход композитных материалов за счет использования точных разверток и раскройных станков;
- увеличить скорость и повысить качество ручной выкладки материала за счет использования точных заготовок и лазерных проекций мест их выкладки;
- добиться высокого уровня повторяемости изделий;
- сокращение влияния человеческого фактора на качество производимых изделий;
- снижение требований к квалификации персонала, занятого укладкой.
Оборудование для создания матриц
Изготовление мастер-модели из дерева процесс трудоемкий и длительный, для уменьшения времени изготовления матрицы и повышения точности используются: трех/пятиосевые фрезерные станки с ЧПУ, контрольно-измерительные машины или 3Д сканеры.
Портальный пятиосевой фрезерный станок, (рис 1), доступен лишь крупным производителям. Небольшие компании используют фрезерные роботоризированные комплексы на линейных блоках (linear robot unit) (рис. 2), либо изготавливают мастер-модели из склеенной заготовки. В этом случае за основу заготовки берется жесткий пустотелый каркас, который обклеивается снаружи и затем целиком обрабатывается. Компании, не имеющие возможность обработать изделие целиком, идут по другому пути: Сначала в CAD-системе при помощи плоскостей строится упрощенная 3D-модель изделия, на основе упрощенной модели проектируется жесткий силовой каркас из фанеры. Затем вся внешняя поверхность представляется в CAD-системе как облицовка внутреннего каркаса. Размеры облицовки подбираются таким образом, чтобы ее можно было отфрезеровать на имеющемся фрезерном станке с ЧПУ (рис 3). Затем точно собранный каркас обклеивается модельной облицовкой. При таком методе точность мастер-модели ниже и требуется ручная доводка стыков облицовки, но это позволяет создавать изделия, размеры которых значительно превышают возможности имеющихся станков с ЧПУ.
Рис. 1. Пятикоординатный фрезерный станок MR 125, способен обрабатывать детали размером 15x5 м и высотой до 2,5 м
Рис. 2. Фрезерный роботоризированный комплекс Kuka
Рис. 3. «Небольшой» пятикоординатный фрезерный станок
Оборудование для создания композитов
Первым шагом механизации процесса формования явилось использование пропиточных машин, которые помимо пропитки собирают стеклоткани или стеклохолсты в многослойные пакеты общей толщиной 4 - 5 мм. Для механизации процессов, снижения вероятности ошибки персонала, увеличения производительности применяется, например, метод напыления, с помощью которого можно получать наружную обшивку, полотнища переборок и другие конструкции из стеклопластика. Метод напыления позволяет получить приформовочные угольники механизированным путем и обеспечить более высокую производительность труда по сравнению с приформовочными угольниками, формованными вручную из полосок стеклоткани или стеклохолста. Следующий этап развития производства изделий из композитов это внедрение установки для автоматизированной намотки выкладки углестеклонаполнителей. Первый «робот» предназначенный для укладки сухой ткани рулонного типа был продемонстрирован американской компанией Magnum Venus Plastech. Впервые в России подобное оборудование внедрено на ОАО «ВАСО». Данное оборудование позволяет изготавливать композитные детали длиной до 8 м и диаметром до 3 м (рис 4) .
Для облегчения ручной выкладки ткани и сокращения отходов применяются раскройные машины для автоматической резки ткани/препрега, лазерные проекторы LAP и LPT для контурной проекции при выкладке препрега на технологическую оснастку. Используя модуль лазерного проецирования (рис 5) имеется возможность автоматически генерировать данные для проецирования непосредственно из 3D-модели композитного изделия. Такая схема работы значительно сокращает временные издержки, увеличивает эффективность процесса, снижает вероятность дефектов и ошибок, и делает управление данными проще. Комплекс «ПО - раскройный станок - проекционный лазер» по сравнению с традиционной выкладкой снижает трудоемкость раскроя примерно на 50 %, трудоемкость выкладки - примерно на 30 %, повышает коэффициент использования материалов, то есть можно сэкономить от 15 до 30 % материала .
Формование углепластиков методом намотки позволяет получать изделия с наиболее высокими деформационно-прочностными характеристиками. Методы намотки делятся на «сухие» и «мокрые». В первом случае для намотки используются препреги в виде нитей, жгутов или лент. Во втором - пропитка армирующих материалов связующим ведется непосредственно в процессе намотки. В последнее время разрабатывается оборудование, в котором для управления схемой ориентации волокон используются компьютерные системы. Это позволяет получать трубчатые изделия, имеющие изгибы и неправильную форму, а также изделия со сложной геометрией. Разрабатывается оборудование для намотки с применением гибкой технологии, когда армирующие волокнистые материалы можно укладывать на оправке в любом направлении.
Рис. 4 Станок для автоматизированной намотки-выкладки углестеклонаполнителей Viper 1200 FPS фирмы MAG Cincinnati
Рис. 5. Система лазерного позиционирования (зеленый контур)
Оборудование для контроля геометрии и внутренней структуры изделия
Обводы изделий часто имеют криволинейные образующие, проверить которые традиционными «плазовыми» методами не представляется возможным. При помощи 3D-сканирования можно определить насколько точно физический образец соответствует компьютерной 3D-модели. Для 3D-сканирования также можно воспользоваться координатно-измерительной машиной (КИМ) типа «рука» или бесконтактной оптической/лазерной системой сканирования. Однако при использовании бесконтактные системы сканирования, как правило, не могут корректно работать с зеркальными и высокоглянцевыми поверхностями. При использовании «измерительных рук» потребуется несколько последовательных переустановов, поскольку рабочее пространство в силу конструкции измерительных рук обычно ограничено сферой радиусом 1,2-3,6 м.
Также у стеклопластиковых материалов есть ряд проблемных направления. Один из основных - это контроль качества готового изделия (отсутствие воздушных полостей) и коррозия в процессе эксплуатации. Для неразрушающего контроля судовых корпусов из композитов достаточно широко применяют рентген, но стремятся к его сокращению по ряду соображений. В последнее время стали появляться публикации описывающие выявление расслоений инфракрасной термографией (тепловизорами). При этом, что тепловизионный, что рентгеновский методы НК обнаруживая расслоения, не позволяют измерять их размеры и определять глубину залегания дефектов, для того чтобы оценивать их влияние на изменение характеристик прочности.
Заключение
В настоящее время в России практически только начинается интенсивное развитие автоматизации сборки композиционных изделий, в том числе оборудование для создания матриц. Чаще всего выполняют только отдельные элементы аэродинамического обвеса для «тюнинга» автомобилей. Успехом является внедрение на средненевском судостроительном заводе системы FiberSIM при проектировании и строительстве базового тральщика проекта 12700 , а также на ВАСО станка автоматической укладки ткани. Но это отдельные примеры, для повышения конкурентоспособности необходимо комплексное внедрение новых технологий.
Библиографическая ссылка
Чернышов Е.А., Романов А.Д. СОВРЕМЕННЫЕ ТЕХНОЛОГИИ ПРОИЗВОДСТВА ИЗДЕЛИЙ ИЗ КОМПОЗИЦИОННЫХ МАТЕРИАЛОВ // Современные наукоемкие технологии. – 2014. – № 2. – С. 46-51;URL: http://top-technologies.ru/ru/article/view?id=33649 (дата обращения: 25.11.2019). Предлагаем вашему вниманию журналы, издающиеся в издательстве «Академия Естествознания»