Tehnološki pokazatelji sheme obogaćivanja volframovih ruda. Obogaćivanje ruda i naslaga kositra i volframa. Poluindustrijsko ispitivanje razvijene tehnološke sheme za obogaćivanje opće teorije relativnosti i industrijskog postrojenja
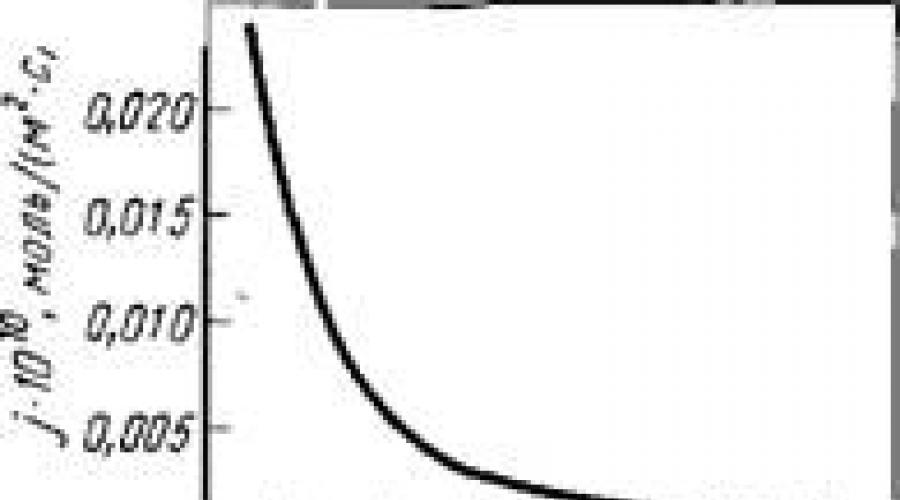
Pročitajte također
Volfram je najvatrostalniji metal s talištem od 3380°C. I to određuje njegov opseg. Također je nemoguće izgraditi elektroniku bez volframa, čak je i nit u žarulji volfram.
I, naravno, svojstva metala određuju poteškoće u njegovom dobivanju ...
Prvo morate pronaći rudu. To su samo dva minerala - šeelit (kalcijev volframat CaWO 4) i volframit (željezo i mangan volframat - FeWO 4 ili MnWO 4). Potonji je poznat od 16. stoljeća pod nazivom "vučja pjena" - "Spuma lupi" na latinskom, odnosno "Wolf Rahm" na njemačkom. Ovaj mineral prati rude kositra i ometa taljenje kositra, pretvarajući ga u trosku. Stoga ga je moguće pronaći već u antici. Bogate volframove rude obično sadrže 0,2 - 2% volframa. U stvarnosti, volfram je otkriven 1781.
Međutim, pronaći ovo je najjednostavnija stvar u rudarstvu volframa.
Dalje - rudu treba obogatiti. Postoji hrpa metoda i sve su prilično složene. Prvo, naravno. Zatim - magnetska separacija (ako imamo volframit sa željeznim volframitom). Sljedeće je gravitacijsko odvajanje, jer je metal vrlo težak i ruda se može isprati, slično kao pri kopanju zlata. Sada i dalje koriste elektrostatičko odvajanje, ali je malo vjerojatno da će metoda biti korisna ubojici.
Dakle, odvojili smo rudu od otpadne stijene. Ako imamo scheelite (CaWO 4), onda se sljedeći korak može preskočiti, a ako volframit, onda ga trebamo pretvoriti u scheelite. Za to se volfram ekstrahira otopinom sode pod tlakom i na povišenoj temperaturi (proces se odvija u autoklavu), nakon čega slijedi neutralizacija i taloženje u obliku umjetnog scheelite, t.j. kalcijev volframat.
Također je moguće sinterirati volframit s viškom sode, tada ne dobivamo kalcij, već natrijev volframit, što nije toliko značajno za naše potrebe (4FeWO 4 + 4Na 2 CO 3 + O 2 = 4Na 2 WO 4 + 2Fe 2 O 3 + 4CO 2).
Sljedeća dva koraka su ispiranje CaWO 4 -> H 2 WO 4 vodom i razgradnja vrućom kiselinom.
Možete uzeti različite kiseline - klorovodičnu (Na 2 WO 4 + 2HCl \u003d H 2 WO 4 + 2NaCl) ili dušičnu.
Kao rezultat, izolirana je volframova kiselina. Potonji se kalcinira ili otopi u vodenoj otopini NH 3, iz koje se isparavanjem kristalizira paravolframat.
Kao rezultat, moguće je dobiti glavnu sirovinu za proizvodnju volframa - WO 3 trioksid dobre čistoće.
Naravno, postoji i metoda za dobivanje WO 3 pomoću klorida, kada se volfram koncentrat tretira klorom na povišenoj temperaturi, ali ta metoda neće biti jednostavna za ubojicu.
Volframovi oksidi se mogu koristiti u metalurgiji kao aditiv za legiranje.
Dakle, imamo volfram trioksid i ostaje jedna faza - redukcija na metal.
Ovdje postoje dvije metode - redukcija vodika i redukcija ugljika. U drugom slučaju, ugljen i nečistoće koje on uvijek sadrži reagiraju s volframom i stvaraju karbide i druge spojeve. Stoga volfram izlazi “prljav”, lomljiv, a za elektroniku je vrlo poželjan čist, jer imajući samo 0,1% željeza volfram postaje krhak i iz njega je nemoguće izvući najtanju žicu za filamente.
Tehnički proces s ugljenom ima još jedan nedostatak - visoku temperaturu: 1300 - 1400 ° C.
Međutim, proizvodnja s redukcijom vodika također nije dar.
Proces redukcije se odvija u posebnim cijevnim pećima, grijanim na način da, dok se kreće duž cijevi, “čamac” s WO3 prolazi kroz nekoliko temperaturnih zona. Prema njemu struji mlaz suhog vodika. Oporavak se događa i u "hladnim" (450...600°C) iu "vrućim" (750...1100°C) zonama; u "hladnom" - do najnižeg oksida WO 2, zatim - do elementarnog metala. Ovisno o temperaturi i trajanju reakcije u "vrućoj" zoni mijenjaju se čistoća i veličina zrna volframa u prahu koji se oslobađaju na stijenkama "čamca".
Dakle, dobili smo čisti metalni volfram u obliku najmanjeg praha.
Ali ovo još nije ingot metala od kojeg se nešto može napraviti. Metal se dobiva metalurgijom praha. Odnosno, prvo se preša, sinterira u atmosferi vodika na temperaturi od 1200-1300 ° C, a zatim se kroz njega propušta električna struja. Metal se zagrijava na 3000 °C i dolazi do sinteriranja u monolitni materijal.
Međutim, radije nam ne trebaju ingoti ili čak šipke, već tanka volframova žica.
Kao što razumijete, ovdje opet nije sve tako jednostavno.
Izvlačenje žice se izvodi pri temperaturi od 1000°C na početku procesa i 400-600°C na kraju. U ovom slučaju se ne zagrijava samo žica, već i matrica. Grijanje se provodi plamenom plinskog plamenika ili električnim grijačem.
Istodobno, nakon izvlačenja, volframova žica je premazana grafitnom mašću. Površina žice mora se očistiti. Čišćenje se provodi žarenjem, kemijskim ili elektrolitičkim jetkanjem, elektrolitičkim poliranjem.
Kao što možete vidjeti, zadatak dobivanja jednostavne volframove niti nije tako jednostavan kao što se čini. I ovdje su opisane samo glavne metode, sigurno ima puno zamki.
I, naravno, čak i sada volfram je skup metal. Sada jedan kilogram volframa košta više od 50 dolara, isti molibden je gotovo dva puta jeftiniji.
Zapravo, postoji nekoliko namjena za volfram.
Naravno, glavni su radio i elektrotehnika, gdje ide volframova žica.
Sljedeća je izrada legiranih čelika koji se odlikuju posebnom tvrdoćom, elastičnošću i čvrstoćom. Dodan zajedno s kromom u željezo, daje takozvane brzorezne čelike, koji zadržavaju tvrdoću i oštrinu čak i kada se zagrijavaju. Koriste se za izradu glodala, svrdla, rezača, kao i drugih alata za rezanje i bušenje (općenito, u alatu za bušenje ima puno volframa).
Od njega se izrađuju zanimljive legure volframa s renijem - visokotemperaturni termoelementi koji rade na temperaturama iznad 2000 ° C, iako samo u inertnoj atmosferi.
Pa, još jedna zanimljiva primjena su volframove elektrode za zavarivanje za električno zavarivanje. Takve elektrode su nepotrošne i potrebno je dopremiti drugu metalnu žicu na mjesto zavarivanja kako bi se osigurao zavareni bazen. Volframove elektrode se koriste u argon-lučnom zavarivanju - za zavarivanje obojenih metala poput molibdena, titana, nikla, kao i visokolegiranih čelika.
Kao što vidite, proizvodnja volframa nije za davna vremena.
A zašto postoji volfram?
Volfram se može dobiti samo gradnjom elektrotehnike – uz pomoć elektrotehnike i za elektrotehniku.
Nema struje – nema volframa, ali ni ne treba.
Izum se odnosi na postupak složene obrade jalovine za obogaćivanje ruda koje sadrže volfram. Metoda uključuje njihovu klasifikaciju na fine i grube frakcije, pužasto odvajanje fine frakcije za dobivanje volframovog proizvoda i njegovo ponovno pročišćavanje. Istodobno se vrši ponovno čišćenje na pužnom separatoru kako bi se dobio sirovi volfram koncentrat, koji se podvrgava doradi na koncentracijskim tablicama kako bi se dobio gravitacijski volfram koncentrat, koji se podvrgava flotaciji kako bi se dobio kondicionirani volfram koncentrat visokog stupnja i proizvod koji sadrži sulfide. Repovi vijčanog separatora i tablice koncentracije se kombiniraju i podvrgavaju zgušnjavanju. Istodobno se odvod dobiven nakon zgušnjavanja dovodi u razvrstavanje jalovine za obogaćivanje ruda koje sadrže volfram, a zgusnuti proizvod se podvrgava obogaćivanju na pužnom separatoru kako bi se dobila sekundarna jalovina i volframov proizvod koji se šalje za čišćenje. Tehnički rezultat je povećanje dubine obrade jalovine za obogaćivanje ruda koje sadrže volfram. 1 z.p. f-ly, 1 tab., 1 ill.
Izum se odnosi na obogaćivanje minerala i može se koristiti u preradi jalovine za obogaćivanje ruda koje sadrže volfram.
Prilikom prerade ruda koje sadrže volfram, kao i jalovine za njihovo obogaćivanje, koriste se gravitacijske, flotacijske, magnetske, kao i elektrostatske, hidrometalurške i druge metode (vidi, na primjer, Burt P.O., uz sudjelovanje K. Mills. Gravitational Tehnologija obogaćivanja Prevod s engleskog - M.: Nedra, 1990.). Dakle, za preliminarnu koncentraciju korisnih komponenti (mineralnih sirovina), koriste se fotometrijsko i lumometrijsko sortiranje (na primjer, prerađivački pogoni Mount Carbine i King Island), obogaćivanje teškim medijima (na primjer, portugalska tvornica Panasquera i engleska tvornica Hemerdan).), jigging (osobito loših sirovina), magnetsko odvajanje u slabom magnetskom polju (na primjer, za izolaciju pirita, pirotita) ili magnetsko odvajanje visokog intenziteta (za odvajanje volframita i kasiterita).
Za preradu mulja koji sadrži volfram poznata je upotreba flotacije, posebice volframita u NRK-u i u kanadskoj tvornici Mount Plisad, a u nekim je tvornicama flotacija u potpunosti zamijenila gravitacijsko obogaćivanje (npr. tvornice Jokberg, Švedska i Mittersil, Austrija).
Također je poznato korištenje pužnih separatora i vijčanih brava za obogaćivanje ruda koje sadrže volfram, starih odlagališta, ustajale jalovine i mulja.
Tako je, na primjer, pri preradi starih odlagališta volframove rude u tvornici Cherdoyak (Kazahstan), početni materijal odlagališta nakon drobljenja i mljevenja do finoće od 3 mm obogaćen je strojevima za šivanje, čiji je proizvod manje veličine potom očišćen na tablica koncentracije. Tehnološka shema uključivala je i obogaćivanje na vijčanim separatorima, na kojima je ekstrahirano 75-77% WO 3 s učinkom proizvoda obogaćivanja od 25-30%. Vijčano odvajanje omogućilo je povećanje ekstrakcije WO 3 za 3-4% (vidi, na primjer, Anikin M.F., Ivanov V.D., Pevzner M.L. „Vijčani separatori za preradu rude“, Moskva, izdavačka kuća „Nedra“, 1970, 132 str.).
Nedostaci tehnološke sheme za preradu starih odlagališta su veliko opterećenje na čelu procesa za operaciju jigginga, nedovoljno visoka ekstrakcija WO 3 i značajan prinos proizvoda obogaćivanja.
Poznata je metoda pridružene proizvodnje volframovog koncentrata preradom molibdenitne flotacijske jalovine (tvornica "Climax molybdenum", Kanada). Jalovina koja sadrži volfram odvaja se pužnom separacijom na volframovu jalovinu (laka frakcija), primarni volframit - kasiteritni koncentrat. Potonji se podvrgava hidrociklonu i ispust mulja se šalje u jalovinu, a frakcija pijeska šalje se na flotacionu separaciju piritnog koncentrata koji sadrži 50% S (sulfida) i izlaz u jalovinu. Komorni proizvod sulfidne flotacije čisti se pomoću pužnog odvajanja i/ili čunjeva kako bi se dobila otpadna jalovina koja sadrži pirit i koncentrat volframit-kasiterit, koji se prerađuje na koncentracijskim tablicama. Istodobno se dobiva koncentrat volframit-kasiterit i jalovina. Sirovi koncentrat nakon dehidracije ponovno se čisti uzastopno čišćenjem od željeza magnetskom separacijom, flotacijskim uklanjanjem monacita iz njega (fosfatna flotacija), a zatim se dehidrira, suši, klasificira i odvaja postupnom magnetskom separacijom u koncentrat sa sadržajem 65 % WO 3 nakon faze I i 68% WO 3 nakon faze II. Također nabavite nemagnetski proizvod - kositreni (kasiterit) koncentrat koji sadrži ~35% kositra.
Ovu metodu obrade karakteriziraju nedostaci - složenost i višestupanjski, kao i visoki energetski intenzitet.
Poznata je metoda dodatne ekstrakcije volframa iz jalovine gravitacijskog obogaćivanja (tvornica "Boulder", SAD). Jalovina gravitacijskog obogaćivanja se drobi, odslađuje u klasifikatoru, čiji se pijesak odvaja na hidrauličkim klasifikatorima. Rezultirajuće klase obogaćuju se zasebno na tablicama koncentracije. Krupnozrnasta jalovina se vraća u ciklus mljevenja, a fina jalovina se zgušnjava i ponovno obogaćuje na stolovima za kašu kako bi se dobio gotov koncentrat, srednji proizvod za ponovno mljevenje, a jalovina se šalje na flotaciju. Grubi flotacijski koncentrat se podvrgava jednom čišćenju. Izvorna ruda sadrži 0,3-0,5% WO 3 ; ekstrakcija volframa doseže 97%, pri čemu se oko 70% volframa dobiva flotacijom. Međutim, sadržaj volframa u flotacijskom koncentratu je nizak (oko 10% WO 3) (vidi, Polkin S.I., Adamov E.V. Obogaćivanje ruda obojenih metala. Udžbenik za sveučilišta. M., Nedra, 1983., 213 str.)
Nedostaci tehnološke sheme za preradu jalovine gravitacijskog obogaćivanja su veliko opterećenje na čelu procesa na operaciji obogaćivanja na koncentracijskim tablicama, višeoperacija, niska kvaliteta dobivenog koncentrata.
Poznata je metoda prerade jalovine koja sadrži scheelite radi uklanjanja opasnih materijala iz njih i prerade neopasnih i rudnih minerala primjenom poboljšanog postupka separacije (separacije) (KR 20030089109, SNAE i sur., 21.11.2003.). Metoda uključuje faze homogenizirajućeg miješanja jalovine koja sadrži scheelite, uvođenje pulpe u reaktor, “filtraciju” pulpe sitom za uklanjanje raznih stranih materijala, naknadno odvajanje pulpe pužnim odvajanjem, zgušnjavanje i dehidraciju nemetalni minerali za dobivanje kolača, sušenje kolača u rotacijskoj sušilici, drobljenje suhog kolača pomoću mlina s čekićem koji radi u zatvorenom ciklusu sa sitom, odvajanje zdrobljenih minerala pomoću „mikronskog” separatora na frakcije sitnih i krupnih zrna (granule), kao i magnetsko odvajanje krupnozrne frakcije za dobivanje magnetskih minerala i nemagnetne frakcije koja sadrži scheelite. Nedostatak ove metode je višestruko djelovanje, korištenje energetski intenzivnog sušenja mokrog kolača.
Poznata je metoda dodatne ekstrakcije volframa iz jalovine postrojenja za preradu rudnika Ingichka (vidi A.B. Ezhkov, Kh.T. v.1, MISiS, M., 2001.). Metoda uključuje pripremu pulpe i njeno odstranjivanje u hidrociklonu (klasa uklanjanja - 0,05 mm), naknadno odvajanje odlupljene pulpe u konusnom separatoru, dvostupanjsko ponovno čišćenje koncentrata konusnog separatora na tablicama koncentracije kako bi se dobio koncentrat koji sadrži 20,6 % WO 3 , s prosječnim iskorištenjem od 29,06%. Nedostaci ove metode su niska kvaliteta dobivenog koncentrata i nedovoljno visoka ekstrakcija WO 3 .
Opisani su rezultati studija o gravitacijskom obogaćivanju jalovine postrojenja za obogaćivanje Ingichkinskaya (vidi S.V. » // Mining Bulletin of Uzbekistan, 2008, br. 3).
Patentiranom tehničkom rješenju najbliže je metoda vađenja volframa iz ustajale jalovine obogaćivanja ruda koje sadrže volfram (Artemova O.S. Razvoj tehnologije vađenja volframa iz ustajale jalovine VMK Dzhida. Sažetak rada kandidata tehni. znanosti, Irkutsko državno tehničko sveučilište, Irkutsk, 2004. - prototip).
Tehnologija vađenja volframa iz ustajale jalovine prema ovoj metodi uključuje operacije dobivanja grubog koncentrata koji sadrži volfram i srednjeg proizvoda, zlatonosnog proizvoda i sekundarne jalovine gravitacijskim metodama mokrog obogaćivanja - pužnom i centrifugalnom separacijom - te naknadnom doradom. dobivenog grubog koncentrata i srednjeg proizvoda korištenjem gravitacijskog (centrifugalnog) obogaćivanja i magnetske separacije kako bi se dobio standardni volframov koncentrat koji sadrži 62,7% WO 3 uz ekstrakciju 49,9% WO 3 .
Prema ovoj metodi, ustajali repovi se podvrgavaju primarnoj klasifikaciji s oslobađanjem 44,5% mase. u sekundarnu jalovinu u obliku frakcije +3 mm. Frakcija jalovine -3 mm dijeli se na razrede -0,5 i +0,5 mm, a od potonjih se pužnim odvajanjem dobivaju krupni koncentrat i repovi. Frakcija -0,5 mm podijeljena je u klase -0,1 i +0,1 mm. Iz klase +0,1 mm se centrifugalnom separacijom izolira grubi koncentrat koji se, kao i koncentrat grubog pužnog odvajanja, podvrgava centrifugalnoj separaciji kako bi se dobio sirovi volfram koncentrat i produkt koji sadrži zlato. Jalovina pužnog i centrifugalnog odvajanja se u zatvorenom ciklusu s klasifikacijom drobi do -0,1 mm i zatim dijeli u klase -0,1 + 0,02 i -0,02 mm. Klasa -0,02 mm uklanja se iz procesa kao sekundarna otpadna jalovina. Klasa -0,1+0,02 mm obogaćuje se centrifugalnim odvajanjem kako bi se dobila sekundarna otpadna jalovina i volframov srednjak, koji se šalje na rafiniranje magnetskom separacijom zajedno s koncentratom za centrifugalnu separaciju, fino mljevenim do finoće -0,1 mm. U tom slučaju dobiva se volfram koncentrat (magnetska frakcija) i srednja smjesa (nemagnetska frakcija). Potonji se podvrgava magnetnoj separaciji II s otpuštanjem nemagnetne frakcije u sekundarnu jalovinu i volfram koncentrat (magnetska frakcija), koji se uzastopno obogaćuje centrifugalnim, magnetskim i ponovno centrifugalnim odvajanjem kako bi se dobio kondicionirani volfram koncentrat sa sadržajem od 62,7% WO 3 uz izlaz od 0,14 % i iskorištenje od 49,9 %. Istodobno, jalovina centrifugalnih separacija i nemagnetska frakcija šalju se u sekundarnu jalovinu, čiji je ukupni učinak u fazi dorade sirovog volframovog koncentrata 3,28% sa sadržajem od 2,1% WO 3 u njima. .
Nedostaci ove metode su višeoperacijski proces koji uključuje 6 operacija klasifikacije, 2 operacije ponovnog mljevenja, kao i 5 centrifugalnih operacija i 3 operacije magnetske separacije uz korištenje relativno skupih aparata. Istodobno, prečišćavanje sirovog volframovog koncentrata do standarda povezano je s proizvodnjom sekundarne jalovine s relativno visokim udjelom volframa (2,1% WO 3).
Cilj ovog izuma je poboljšati metodu prerade jalovine, uključujući ustajalu jalovinu za obogaćivanje ruda koje sadrže volfram, kako bi se dobio koncentrat volframa visokog kvaliteta i proizvod koji sadrži sulfid uz smanjenje sadržaja volframa u sekundarnoj jalovini.
Patentirana metoda za složenu preradu jalovine za obogaćivanje ruda koje sadrže volfram uključuje razvrstavanje jalovine na fine i grube frakcije, vijčano odvajanje fine frakcije za dobivanje proizvoda od volframa, ponovno pročišćavanje volframovog proizvoda i doradu za dobivanje visokokvalitetni volfram koncentrat, proizvod koji sadrži sulfide i sekundarnu otpadnu jalovinu.
Metoda se razlikuje po tome što se dobiveni volframov proizvod podvrgava ponovnom čišćenju na vijčanom separatoru kako bi se dobio grubi koncentrat i jalovina, a grubi koncentrat se podvrgava doradi na koncentracijskim tablicama kako bi se dobio gravitacijski volfram koncentrat i jalovina. Repovi stola za koncentraciju i pužnog separatora za čišćenje se kombiniraju i podvrgavaju zgušnjavanju, zatim se zgušnjavanje dovodi u fazu razvrstavanja na čelu tehnološke sheme, a zgusnuti proizvod se obogaćuje na pužnom separatoru kako bi se dobio sekundarni otpad. jalovine i proizvoda od volframa, koji se šalje na čišćenje. Gravitacijski volfram koncentrat se podvrgava flotaciji kako bi se dobio visokokvalitetni standardni volfram koncentrat (62% WO 3) i proizvod koji sadrži sulfid, koji se obrađuje poznatim metodama.
Metoda se može okarakterizirati činjenicom da se jalovina razvrstava u frakcije, uglavnom +8 mm i -8 mm.
Tehnički rezultat patentirane metode je povećanje dubine obrade uz smanjenje broja tehnoloških operacija i opterećenja na njih zbog odvajanja u glavi procesa najveće količine početne jalovine (više od 90%) u sekundarne jalovine, korištenjem jednostavnijeg dizajna i rada štedljive tehnologije vijčanog odvajanja. To dramatično smanjuje opterećenje na naknadnim operacijama obogaćivanja, kao i kapitalne i operativne troškove, što osigurava optimizaciju procesa obogaćivanja.
Učinkovitost patentirane metode prikazana je na primjeru složene obrade jalovine postrojenja za obogaćivanje Ingichkinskaya (vidi crtež).
Prerada počinje razvrstavanjem jalovine na male i velike frakcije uz odvajanje sekundarne jalovine u obliku velike frakcije. Fina frakcija jalovine podvrgava se pužnoj separaciji s odvajanjem u glavi tehnološkog procesa u sekundarnu jalovinu glavnine izvorne jalovine (više od 90%). To omogućuje drastično smanjenje opterećenja na kasnijim operacijama, kapitalnih troškova i operativnih troškova u skladu s tim.
Dobiveni volfram proizvod se podvrgava ponovnom čišćenju na vijčanom separatoru kako bi se dobio sirovi koncentrat i jalovina. Sirovi koncentrat se podvrgava rafiniranju na tablicama koncentracije kako bi se dobio gravitacijski volfram koncentrat i jalovina.
Jalovina koncentracijskog stola i pužnog separatora za čišćenje se kombiniraju i podvrgavaju zgušnjavanju, na primjer, u zgušnjivaču, mehaničkom klasifikatoru, hidrociklonu i drugim aparatima. Odvod za zgušnjavanje dovodi se u fazu klasifikacije na čelu tehnološke sheme, a zgusnuti proizvod se obogaćuje na vijčanom separatoru kako bi se dobila sekundarna jalovina i volframov proizvod koji se šalje na čišćenje.
Gravitacijski volfram koncentrat dovodi se flotacijom u visokokvalitetni uvjetni volfram koncentrat (62% WO 3 ) kako bi se dobio proizvod koji sadrži sulfid.
Dakle, kondicionirani volfram koncentrat visokog stupnja (62% WO 3 ) izoliran je iz jalovine koja sadrži volfram nakon postizanja relativno visokog iskorištenja WO 3 od ~49 % i relativno niskog sadržaja volframa (0,04 % WO 3 ) u sekundarnoj otpadnoj jalovini.
Dobiveni proizvod koji sadrži sulfide obrađuje se na poznati način, na primjer, koristi se za proizvodnju sumporne kiseline i sumpora, a koristi se i kao korektivni aditiv u proizvodnji cementa.
Visokokvalitetni kondicionirani koncentrat volframa je visoko likvidni tržišni proizvod.
Kao što proizlazi iz rezultata implementacije patentirane metode na primjeru ustajale jalovine za obogaćivanje ruda koje sadrže volfram koncentratora Ingichkinskaya, njegova je učinkovitost prikazana u usporedbi s metodom prototipa (vidi tablicu). UČINAK: osigurava se dodatno dobivanje proizvoda koji sadrži sulfide, smanjenje volumena potrošene slatke vode zbog stvaranja cirkulacije vode. Stvara mogućnost prerade znatno lošije jalovine (0,09% WO 3), značajno smanjenje sadržaja volframa u sekundarnoj jalovini (do 0,04% WO 3). Osim toga, smanjen je broj tehnoloških operacija i smanjeno opterećenje većine njih zbog odvajanja većeg dijela početne jalovine (više od 90%) u glavi tehnološkog procesa u sekundarnu jalovinu, korištenjem jednostavnija i energetski manje intenzivna tehnologija vijčane separacije, koja smanjuje kapitalne troškove za nabavu opreme i operativne troškove.
1. Metoda za složenu preradu jalovine za obogaćivanje ruda koje sadrže volfram, uključujući njihovo razvrstavanje u fine i grube frakcije, pužasto odvajanje fine frakcije za dobivanje volframovog proizvoda, njegovo čišćenje i doradu za dobivanje visokokvalitetnog proizvoda. volfram koncentrat, proizvod koji sadrži sulfid i sekundarnu jalovinu, naznačen time da se dobiveni nakon pužnog odvajanja volfram proizvod podvrgava ponovnom čišćenju na pužnom separatoru kako bi se dobio sirovi volfram koncentrat, a dobiveni sirovi volfram koncentrat se podvrgava doradi na koncentraciji tablice za dobivanje gravitacijskog volframovog koncentrata, koji se podvrgava flotaciji za dobivanje kondicioniranog volframovog koncentrata visokog stupnja i proizvoda koji sadrži sulfide, repove vijčanog separatora i koncentracijsku tablicu kombinirane i podvrgnute zgušnjavanju, dren dobiven nakon zgušnjavanja je uvršten u klasifikaciju jalovine za obogaćivanje ruda koje sadrže volfram, a podvrgnut obogaćivanju na vijčanom separatoru kako bi se dobila sekundarna jalovina i volframov proizvod koji se šalje na čišćenje.
Minerali volframa, rude i koncentrati
Volfram je rijedak element, njegov prosječni sadržaj u zemljinoj kori iznosi Yu-4% (po masi). Poznato je oko 15 minerala volframa, no od praktične važnosti su samo minerali skupine volframita i scheelite.
Volframit (Fe, Mn)WO4 je izomorfna smjesa (kruta otopina) željeza i mangana volframata. Ako u mineralu ima više od 80% željezovog volframata, mineral se naziva feberit, u slučaju prevlasti manganovog volframata (više od 80%) - hübnerit. Smjese koje se nalaze u sastavu između ovih granica nazivaju se volframiti. Minerali skupine volframita obojeni su crnom ili smeđom bojom i imaju veliku gustoću (7D-7,9 g/cm3) i tvrdoću od 5-5,5 na mineraloškoj ljestvici. Mineral sadrži 76,3-76,8% W03. Volframit je slabo magnetičan.
Scheelite CaWOA je kalcijev volframat. Boja minerala je bijela, siva, žuta, smeđa. Gustoća 5,9-6,1 g/cm3, tvrdoća prema mineraloškoj ljestvici 4,5-5. Šelit često sadrži izomorfnu primjesu powellita, CaMo04. Kada je zračen ultraljubičastim zrakama, scheelite fluorescira plavo - plavo svjetlo. Pri sadržaju molibdena većem od 1% fluorescencija postaje žuta. Šelit je nemagnetski.
Volframove rude su obično siromašne volframom. Minimalni sadržaj W03 u rudama, pri kojem je njihova eksploatacija isplativa, trenutno iznosi 0,14-0,15% za velika i 0,4-0,5% za mala ležišta.
Zajedno s mineralima volframa, u rudama se nalaze molibdenit, kasiterit, pirit, arsenopirit, halkopirit, tantalit ili kolumbit itd.
Prema mineraloškom sastavu razlikuju se dvije vrste ležišta - volframit i šelit, a prema obliku rudnih formacija - venski i kontaktni tipovi.
U venskim naslagama minerali volframa se uglavnom javljaju u kvarcnim žilama male debljine (0,3-1 m). Kontaktni tip naslaga povezan je sa zonama kontakta granitnih stijena i vapnenca. Karakteriziraju ih naslage škarne koja sadrži šeelit (skarne su silicificirani vapnenci). Rude tipa skarn uključuju ležište Tyrny-Auzskoye, najveće u SSSR-u, na Sjevernom Kavkazu. Tijekom trošenja venskih naslaga nakupljaju se volframit i šeelit, tvoreći naslaga. U potonjem, volframit se često kombinira s kasiteritom.
Volframove rude se obogaćuju kako bi se dobili standardni koncentrati koji sadrže 55-65% W03. Visok stupanj obogaćivanja volframitnih ruda postiže se različitim metodama: gravitacijom, flotacijom, magnetskom i elektrostatičkom separacijom.
Pri obogaćivanju scheelitnih ruda koriste se gravitacijsko-flotacijske ili čisto flotacijske sheme.
Ekstrakcija volframa u kondicionirane koncentrate tijekom obogaćivanja volframovih ruda kreće se od 65-70% do 85-90%.
Prilikom obogaćivanja ruda složenog sastava ili teškog obogaćivanja, ponekad je ekonomski isplativo iz ciklusa obogaćivanja ukloniti srednju smjesu s udjelom 10-20% W03 za kemijsku (hidrometaluršku) preradu, zbog čega se stvara "umjetni šelit" ili tehnički dobije se volframov trioksid. Takve kombinirane sheme osiguravaju visoku ekstrakciju volframa iz ruda.
Državni standard (GOST 213-73) predviđa sadržaj W03 u koncentratima volframa 1. razreda ne manji od 65%, 2. razreda - ne manji od 60%. Ograničavaju sadržaj nečistoća P, S, As, Sn, Cu, Pb, Sb, Bi u rasponu od stotinki postotka do 1,0%, ovisno o vrsti i namjeni koncentrata.
Istražene rezerve volframa do 1981. procjenjuju se na 2903 tisuće tona, od čega je u NRK-u 1360 tisuća tona. Značajne rezerve imaju SSSR, Kanada, Australija, SAD, Južna i Sjeverna Koreja, Bolivija, Brazil i Portugal. Proizvodnja volframovih koncentrata u kapitalističkim zemljama i zemljama u razvoju u razdoblju 1971. - 1985. varirao je unutar 20 - 25 tisuća tona (u smislu sadržaja metala).
Metode prerade volframovih koncentrata
Glavni proizvod izravne prerade volframovih koncentrata (pored ferovolframa, topljenog za potrebe crne metalurgije) je volframov trioksid. Služi kao početni materijal za volfram i volfram karbid, glavni sastojak tvrdih legura.
Proizvodne sheme za preradu volframovih koncentrata podijeljene su u dvije skupine ovisno o prihvaćenoj metodi razgradnje:
Koncentrati volframa se sinteriraju sa sodom ili obrađuju vodenim otopinama sode u autoklavima. Koncentrati volframa se ponekad razgrađuju vodenim otopinama natrijevog hidroksida.
Koncentrati se razlažu kiselinama.
U slučajevima kada se za razgradnju koriste alkalni reagensi, dobivaju se otopine natrijevog volframata iz kojih se nakon pročišćavanja od nečistoća proizvode krajnji produkti - amonijev paravolframat (PVA) ili volframova kiselina. 24
Kada se koncentrat razgradi kiselinama, dobiva se taloženje tehničke volframove kiseline koja se u kasnijim operacijama pročišćava od nečistoća.
Razgradnja volframovih koncentrata. alkalni reagensi Sinteriranje s Na2C03
Sinteriranje volframita s Na2C03. Interakcija volframita sa sodom u prisutnosti kisika teče aktivno na 800-900 C i opisuje se sljedećim reakcijama: 2FeW04 + 2Na2C03 + l/202 = 2Na2W04 + Fe203 + 2C02; (l) 3MnW04 + 3Na2C03 + l/202 = 3Na2W04 + Mn304 + 3C02. (2)
Ove reakcije se odvijaju s velikim gubitkom Gibbsove energije i praktički su nepovratne. Uz omjer u volframitu FeO:MnO = i:i AG ° 1001C = -260 kJ / mol. Uz višak Na2C03 u punjenju od 10-15% iznad stehiometrijske količine, postiže se potpuna razgradnja koncentrata. Kako bi se ubrzala oksidacija željeza i mangana, ponekad se u punjenje dodaje 1-4% nitrata.
Sinteriranje volframita s Na2C03 u domaćim poduzećima provodi se u cjevastim rotirajućim pećima obloženim šamotnom opekom. Kako bi se izbjeglo taljenje polnjenja i stvaranje naslaga (izraslina) u zonama peći s nižom temperaturom, u punjenu se dodaje jalovina od ispiranja kolača (sadrži željezo i manganove okside) čime se smanjuje sadržaj od W03 u njemu na 20-22%.
Peć, dužine 20 m i vanjskog promjera 2,2 m, pri brzini vrtnje 0,4 o/min i nagibu od 3, ima kapacitet od 25 t/dan u smislu punjenja.
Komponente punjenja (zdrobljeni koncentrat, Na2C03, salitra) se iz spremnika dovode u pužnu mješalicu pomoću automatske vage. Smjesa ulazi u spremnik peći, iz kojeg se dovodi u peć. Nakon izlaska iz peći, sinter komadi prolaze kroz valjke za drobljenje i mlin za mokro mljevenje, iz kojeg se pulpa šalje u gornji stroj za poliranje (slika 1.).
Sheelit sinteriranje s Na2C03. Na temperaturama od 800-900 C, interakcija scheelite s Na2C03 može se odvijati prema dvije reakcije:
CaW04 + Na2CQ3 Na2W04 + CaCO3; (1.3)
CaW04 + Na2C03 *=*■ Na2W04 + CaO + C02. (1.4)
Obje reakcije se odvijaju s relativno malom promjenom Gibbsove energije.
Reakcija (1.4) nastavlja se u znatnoj mjeri iznad 850 C, kada se opaža razgradnja CaCO3. Prisutnost kalcijevog oksida u sinteru dovodi, kada se sinter ispire vodom, do stvaranja slabo topljivog kalcijevog volframata, koji smanjuje ekstrakciju volframa u otopinu:
Na2W04 + Ca(OH)2 = CaW04 + 2NaOH. (1,5)
S velikim suviškom Na2CO3 u naboju, ova reakcija je uvelike potisnuta interakcijom Na2CO4 s Ca(OH)2 da nastane CaCO3.
Kako bi se smanjila potrošnja Na2C03 i spriječilo stvaranje slobodnog kalcijevog oksida, smjesi se dodaje kvarcni pijesak kako bi se kalcijev oksid vezao u netopive silikate:
2CaW04 + 2Na2C03 + Si02 = 2Na2W04 + Ca2Si04 + 2C02;(l.6) AG°100IC = -106,5 kJ.
Ipak, i u ovom slučaju, kako bi se osigurao visok stupanj ekstrakcije volframa u otopinu, u naboj se mora unijeti značajan višak Na2CO3 (50-100% stehiometrijske količine).
Sinteriranje koncentratnog punjenja scheelita s Na2C03 i kvarcnim pijeskom provodi se u pećima s bubnjem, kao što je gore opisano za volframit na 850-900°C. Kako bi se spriječilo taljenje, u punjenje se dodaju deponije za ispiranje (sadrže uglavnom kalcijev silikat) uz smanjenje sadržaja W03 na 20-22%.
Ispiranje mrlja sode. Kada se kolači izluže vodom, u otopinu prelaze natrijev volframat i topljive soli nečistoća (Na2Si03, Na2HP04, Na2HAs04, Na2Mo04, Na2S04), kao i višak Na2C03. Ispiranje se provodi na 80-90°C u čeličnim reaktorima s mehaničkim miješanjem, koji rade u hijerarhiji.
Koncentrati sa sodom:
Elevator dopremanje koncentrata u mlin; 2 - kuglični mlin koji radi u zatvorenom ciklusu s separatorom zraka; 3 - svrdlo; 4 - separator zraka; 5 - vrećasti filter; 6 - automatski dozatori težine; 7 - transportni puž; 8 - vijčani mikser; 9 - spremnik za punjenje; 10 - hranilica;
Bubanj pećnica; 12 - drobilica valjaka; 13 - štapni mlin-lužnik; 14 - reaktor s miješalicom
Divlji način rada ili kontinuirani rotirajući liksivijatori bubnja. Potonji su punjeni šipkama za drobljenje za drobljenje komada kolača.
Ekstrakcija volframa iz sintera u otopinu je 98-99%. Jake otopine sadrže 150-200 g/l W03.
Autoklav o-c Jedna metoda razgradnje volframovih koncentrata
Metoda autoklav-soda predložena je i razvijena u SSSR-u1 u odnosu na preradu scheelitnih koncentrata i srednjaka. Trenutno se metoda koristi u brojnim domaćim tvornicama iu stranim zemljama.
Razgradnja scheelita s otopinama Na2C03 temelji se na reakciji izmjene
CaW04CrB)+Na2C03(pacTB)^Na2W04(pacTB)+CaC03(TB). (1.7)
Pri 200-225 °C i odgovarajućem višku Na2C03, ovisno o sastavu koncentrata, razgradnja se odvija dovoljnom brzinom i potpunošću. Konstante ravnoteže koncentracije reakcije (1.7) male su, rastu s temperaturom i ovise o ekvivalentu sode (tj. broju molova Na2C03 po 1 molu CaW04).
Uz ekvivalent sode 1 i 2 na 225 C, konstanta ravnoteže (Kc = C / C cq) je 1,56 i
0,99 respektivno. Iz ovoga slijedi da je pri 225 C minimalno potrebni ekvivalent sode 2 (tj. višak Na2C03 je 100%). Stvarni višak Na2C03 je veći, jer se brzina procesa usporava kako se ravnoteža približava. Za koncentrate scheelite sa sadržajem 45-55% W03 na 225 C potreban je ekvivalent sode od 2,6-3. Za srednje smjese koje sadrže 15-20% W03 potrebno je 4-4,5 mola Na2C03 na 1 mol CaW04.
CaCO3 filmovi koji nastaju na česticama scheelita su porozni i do debljine 0,1-0,13 mm nije utvrđen njihov utjecaj na brzinu razgradnje scheelita otopinama Na2CO3. Uz intenzivno miješanje, brzina procesa određena je brzinom kemijskog stadija, što potvrđuje visoka vrijednost prividne energije aktivacije E = 75+84 kJ/mol. Međutim, u slučaju nedovoljne brzine miješanja (što je
Javlja se u horizontalnim rotirajućim autoklavima), ostvaruje se srednji režim: brzina procesa određena je i brzinom dovoda reagensa na površinu i brzinom kemijske interakcije.
0,2 0,3 0, to 0,5 0,5 0,7 0,8
Kao što se može vidjeti na slici 2, specifična brzina reakcije opada približno obrnuto proporcionalno porastu omjera molarnih koncentracija Na2W04:Na2C03 u otopini. Ovo je
Ryas. Slika 2. Ovisnost specifične brzine razgradnje scheelita otopinom sode u autoklavu j o molarnom omjeru koncentracija Na2W04/Na2C03 u otopini pri
Izaziva potrebu za značajnim viškom Na2C03 u odnosu na minimum potrebnog, određen vrijednošću konstante ravnoteže. Kako bi se smanjila potrošnja Na2C03, provodi se dvostupanjsko protustrujno ispiranje. U tom slučaju se jalovina nakon prvog ispiranja, u kojoj ima malo volframa (15-20% izvornog), tretira svježom otopinom koja sadrži veliki višak Na2C03. Dobivena otopina, koja cirkulira, ulazi u prvu fazu ispiranja.
Razgradnja otopinama Na2C03 u autoklavu koristi se i za koncentrate volframita, međutim, reakcija je u ovom slučaju kompliciranija, jer je praćena hidrolitičkom razgradnjom željeznog karbonata (mangan karbonat je samo djelomično hidroliziran). Razgradnja volframita na 200-225 °C može se prikazati sljedećim reakcijama:
MnW04(TB)+Na2C03(paCT)^MiiC03(TB)+Na2W04(paCTB); (1.8)
FeW04(TB)+NaC03(pacT)*=iFeC03(TB)+Na2W04(paCTB); (1.9)
FeC03 + HjO^FeO + H2CO3; (1.10)
Na2C03 + H2C03 = 2NaHC03. (Ja ću)
Rezultirajući željezov oksid FeO na 200-225 ° C prolazi kroz transformaciju prema reakciji:
3FeO + H20 = Fe304 + H2.
Stvaranje natrijevog bikarbonata dovodi do smanjenja koncentracije Na2CO3 u otopini i zahtijeva veliki višak reagensa.
Za postizanje zadovoljavajuće razgradnje koncentrata volframita potrebno ih je fino samljeti i povećati potrošnju Na2C03 na 3,5-4,5 g-ekv, ovisno o sastavu koncentrata. Volframiti s visokim sadržajem mangana teže se razgrađuju.
Dodavanje NaOH ili CaO u autoklaviranu suspenziju (što dovodi do kaustizacije Na2C03) poboljšava stupanj razgradnje.
Brzina razgradnje volframita može se povećati uvođenjem kisika (zrak) u pulpu autoklava, koji oksidira Fe (II) i Mil (II), što dovodi do razaranja kristalne rešetke minerala na reakcijskoj površini.
sekundarna para
Ryas. 3. Jedinica za autoklav s horizontalno rotirajućim autoklavom: 1 - autoklav; 2 - cijev za punjenje pulpe (para se uvodi kroz nju); 3 - pumpa za pulpu; 4 - mjerač tlaka; 5 - pulpni reaktor-grijač; 6 - samoisparivač; 7 - separator kapljica; 8 - ulaz pulpe u samoisparivač; 9 - drobilica od oklopnog čelika; 10 - cijev za uklanjanje pulpe; 11 - sakupljač pulpe
Ispiranje se provodi u čeličnim horizontalnim rotirajućim autoklavima koji se zagrijavaju živom parom (slika 3.) i vertikalnim kontinuiranim autoklavima uz miješanje pulpe parom koja mjehuri. Približan način procesa: temperatura 225 tlak u autoklavu ~ 2,5 MPa, omjer T: W = 1: (3,5 * 4), trajanje u svakoj fazi 2-4 sata.
Slika 4 prikazuje dijagram baterije za autoklav. Početna pulpa iz autoklava, zagrijana parom na 80-100 °C, pumpa se u autoklave, gdje se zagrijava do
sekundarna para
Jarak. Slika 4. Shema kontinuiranog autoklavnog postrojenja: 1 - reaktor za zagrijavanje početne pulpe; 2 - klipna pumpa; 3 - autoklav; 4 - gas; 5 - samoisparivač; 6 - sakupljač pulpe
200-225 °C živa para. U kontinuiranom radu, tlak u autoklavu se održava ispuštanjem kaše kroz prigušnicu (kalibrirana karbidna perača). Pulpa ulazi u samoisparivač - posudu pod tlakom od 0,15-0,2 MPa, gdje se pulpa brzo hladi zbog intenzivnog isparavanja. Prednosti autoklav-soda razgradnje scheelitnih koncentrata prije sinteriranja su isključenje procesa u peći i nešto manji sadržaj nečistoća u otopinama volframa (osobito fosfora i arsena).
Nedostaci metode uključuju veliku potrošnju Na2C03. Visoka koncentracija viška Na2C03 (80-120 g/l) povlači povećanu potrošnju kiselina za neutralizaciju otopina i, sukladno tome, visoke troškove zbrinjavanja otpadnih otopina.
Razgradnja konc. volframata.
Otopine natrijevog hidroksida razgrađuju volframit prema reakciji izmjene:
Me WC>4 + 2Na0Hi=tNa2W04 + Me(0 H)2, (1,13)
Gdje je Me željezo, mangan.
Vrijednost konstante koncentracije ove reakcije Kc = 2 pri temperaturama od 90, 120 i 150 °C jednaka je 0,68; 2.23 i 2.27.
Potpuna razgradnja (98-99%) postiže se obradom fino usitnjenog koncentrata s 25-40% otopinom natrijevog hidroksida na 110-120°C. Potreban višak lužine je 50% ili više. Razgradnja se provodi u čeličnim zatvorenim reaktorima opremljenim mješalicama. Prolazak zraka u otopinu ubrzava proces zbog oksidacije željezovog (II) hidroksida Fe (OH) 2 u hidratizirani željezov (III) oksid Fe203-«H20 i mangan (II) hidroksida Mn (OH) 2 u hidratizirani mangan (IV) oksid Mn02-lH20.
Korištenje razgradnje s alkalijskim otopinama preporučljivo je samo za visokovrijedne koncentrate volframita (65-70% W02) s malom količinom silicijevih i silikatnih nečistoća. Pri preradi koncentrata niske kvalitete dobivaju se jako onečišćene otopine i teško filtrirani precipitati.
Obrada otopina natrijevog volframata
Otopine natrijevog volframata koje sadrže 80-150 g/l W03, kako bi se dobio volfram trioksid tražene čistoće, do sada su se uglavnom prerađivale po tradicionalnoj shemi koja uključuje: pročišćavanje od spojeva nečistoća elemenata (Si, P, As, F, Mo); taloženje
Kalcij volfram mag (umjetni šelit) s njegovom naknadnom razgradnjom s kiselinama i dobivanjem tehničke volframove kiseline; otapanje volframove kiseline u amonijačnoj vodi, nakon čega slijedi isparavanje otopine i kristalizacija amonijevog paravolframata (PVA); kalcinacija PVA kako bi se dobio čisti volfram trioksid.
Glavni nedostatak sheme je višestupanjski karakter, izvođenje većine operacija u periodičnom načinu rada i trajanje niza preraspodjela. Tehnologija ekstrakcije i ionske izmjene za pretvaranje otopina Na2W04 u otopine (NH4)2W04 je razvijena i već se koristi u nekim poduzećima. U nastavku se ukratko razmatraju glavne preraspodjele tradicionalne sheme i nove varijante tehnologije ekstrakcije i ionske izmjene.
Pročišćavanje nečistoća
Čišćenje silikona. Kada sadržaj Si02 u otopinama prelazi 0,1% sadržaja W03, potrebno je prethodno pročišćavanje od silicija. Pročišćavanje se temelji na hidrolitičkoj razgradnji Na2Si03 kuhanjem otopine neutralizirane na pH=8x9 uz oslobađanje silicijeve kiseline.
Otopine se neutraliziraju klorovodičnom kiselinom, dodaju u tankom mlazu uz miješanje (kako bi se izbjegla lokalna peroksidacija) u zagrijanu otopinu natrijevog volframata.
Pročišćavanje fosfora i arsena. Za uklanjanje fosfatnih i arsenatnih iona koristi se metoda taloženja amonijevo-magnezijevih soli Mg (NH4) P04 6H20 i Mg (NH4) AsC) 4 6H20. Topljivost ovih soli u vodi pri 20 C je 0,058 odnosno 0,038%. U prisutnosti viška iona Mg2+ i NH4 topljivost je manja.
Taloženje nečistoća fosfora i arsena vrši se na hladnoći:
Na2HP04 + MgCl2 + NH4OH = Mg(NH4)P04 + 2NaCl +
Na2HAsQ4 + MgCl2 + NH4OH = Mg(NH4)AsQ4 + 2NaCl +
Nakon dugog stajanja (48 sati) iz otopine se talože kristalni talog amonijevo-magnezijevih soli.
Pročišćavanje od fluoridnih iona. Uz visok sadržaj fluorita u izvornom koncentratu, sadržaj fluoridnih iona doseže 5 g/L. Otopine se pročišćavaju od fluorid - iona precipitacijom magnezijevim fluoridom iz neutralizirane otopine, kojoj se dodaje MgCl2. Pročišćavanje fluora može se kombinirati s hidrolitičkom izolacijom silicijeve kiseline.
Čišćenje molibdena. Otopine natrijevog volframata" moraju se pročistiti od molibdena ako njegov sadržaj prelazi 0,1% sadržaja W03 (tj. 0,1-0,2 t/l). Pri koncentraciji molibdena od 5-10 g/l (na primjer, u preradi scheelite -powellite Tyrny-Auzsky koncentrati), izolacija molibdena je od posebne važnosti, jer je usmjerena na dobivanje molibdenskog kemijskog koncentrata.
Uobičajena metoda je taloženje teško topljivog molibden trisulfida MoS3 iz otopine.
Poznato je da kada se natrijev sulfid doda otopinama volframata ili natrijevog molibdata, nastaju sulfosoli Na23S4 ili oksosulfosoli Na23Sx04_x (gdje je E Mo ili W):
Na2304 + 4NaHS = Na23S4 + 4NaOH. (1.16)
Konstanta ravnoteže ove reakcije za Na2MoO4 je mnogo veća nego za Na2W04(^^0 »Kzr). Stoga, ako se otopini doda količina Na2S, dovoljna samo za interakciju s Na2MoO4 (s blagim viškom), tada nastaje pretežno molibden sulfosol. S naknadnim zakiseljavanjem otopine na pH = 2,5 * 3,0, sulfosol se uništava oslobađanjem molibden trisulfida:
Na2MoS4 + 2HC1 = MoS3 j + 2NaCl + H2S. (1.17)
Oksosulfosoli se razgrađuju s oslobađanjem oksosulfida (na primjer, MoSjO itd.). Zajedno s molibden trisulfidom koprecipitira se određena količina volfram trisulfida.Otapanjem sulfidnog taloga u otopini sode i ponovnim taloženjem molibden trisulfida dobiva se molibdenov koncentrat s udjelom W03 ne većim od 2% uz gubitak od volfram 0,3-0,5% početne količine.
Nakon djelomičnog oksidativnog prženja taloga molibden trisulfida (na 450-500 °C), dobiva se molibden kemijski koncentrat s udjelom od 50-52% molibdena.
Nedostatak metode taloženja molibdena u sastavu trisulfida je oslobađanje sumporovodika prema reakciji (1.17), što zahtijeva troškove za neutralizaciju plinova (koriste se apsorpcijom H2S u skruberu navodnjenom natrijevim hidroksidom riješenje). Odabir molibden trisulfida provodi se iz otopine zagrijane na 75-80 C. Rad se provodi u zatvorenim čeličnim reaktorima, gumiranim ili obloženim caklinom otpornom na kiseline. Trisulfidni precipitati se odvoje od otopine filtriranjem na filter preši.
Dobivanje volframove kiseline iz otopina natrijevog volframata
Volframova kiselina može se izravno izolirati iz otopine natrijevog volframata s klorovodičnom ili dušičnom kiselinom. Međutim, ova se metoda rijetko koristi zbog teškoća ispiranja precipitata od natrijevih iona, čiji je sadržaj u volframovom trioksidu ograničen.
Većim dijelom se iz otopine u početku taloži kalcijev volframat, koji se zatim razgrađuje s kiselinama. Kalcijev volframat se istaloži dodavanjem otopine CaCl2 zagrijane na 80-90 C otopini natrijevog volframata s zaostalom lužnatošću otopine od 0,3-0,7%. U tom slučaju ispada bijeli fino kristalni, lako taloženi talog, natrijevi ioni ostaju u matičnoj tekućini, što osigurava njihov nizak sadržaj u volframskoj kiselini. Iz otopine se taloži 99-99,5% W, matične otopine sadrže 0,05-0,07 g/l W03. Talog CaW04 ispran vodom u obliku paste ili pulpe ulazi u razgradnju klorovodičnom kiselinom kada se zagrije na 90 °:
CaW04 + 2HC1 = H2W04i + CaCl2. (1.18)
Tijekom razgradnje održava se visoka konačna kiselost pulpe (90–100 g/l HCl), što osigurava odvajanje volframove kiseline od nečistoća spojeva fosfora, arsena i dijelom molibdena (molibdinska kiselina se otapa u klorovodičnoj kiselini). Precipitati volframske kiseline zahtijevaju temeljito pranje od nečistoća (osobito od kalcijevih soli
i natrij). Posljednjih godina savladano je kontinuirano pranje volframove kiseline u pulsirajućim stupovima, što je uvelike pojednostavilo rad.
U jednom od poduzeća u SSSR-u, pri preradi otopina natrijevog volframata, umjesto klorovodične kiseline, koristi se dušična kiselina za neutralizaciju otopina i razgradnju precipitata CaW04, a taloženje potonjeg vrši se uvođenjem Ca(N03)2 u rješenja. U tom slučaju, matične tekućine dušične kiseline se zbrinjavaju, čime se dobivaju nitratne soli koje se koriste kao gnojivo.
Pročišćavanje tehničke volframove kiseline i dobivanje W03
Tehnička volframova kiselina, dobivena gore opisanom metodom, sadrži 0,2-0,3% nečistoća. Kao rezultat kiselog kalciniranja na 500-600 C dobiva se volfram trioksid, prikladan za proizvodnju tvrdih legura na bazi volfram karbida. Međutim, proizvodnja volframa zahtijeva trioksid veće čistoće s ukupnim udjelom nečistoća ne većim od 0,05%.
Općenito je prihvaćena metoda amonijaka za pročišćavanje volframske kiseline. Lako je topiv u amonijačnoj vodi, dok većina nečistoća ostaje u sedimentu: silicij, željezni i manganovi hidroksidi, te kalcij (u obliku CaW04). Međutim, otopine amonijaka mogu sadržavati primjesu molibdena, soli alkalnih metala.
Iz otopine amonijaka, kao rezultat isparavanja i naknadnog hlađenja, izdvaja se kristalni talog PVA:
Isparavanje
12(NH4)2W04 * (NH4)10H2W12O42 4N20 + 14NH3 +
U industrijskoj praksi sastav PVA se često piše u obliku oksida: 5(NH4)20-12W03-5H20, što ne odražava njegovu kemijsku prirodu kao sol izopoli kiseline.
Isparavanje se provodi u šaržnim ili kontinuiranim uređajima od nehrđajućeg čelika. Obično je 75-80% volframa izolirano u kristale. Dublja kristalizacija je nepoželjna kako bi se izbjegla kontaminacija kristala nečistoćama. Značajno je da najveći dio nečistoće molibdena (70-80%) ostaje u matičnoj tekućini. Iz matične tekućine obogaćene nečistoćama, volfram se taloži u obliku CaW04 ili H2W04, koji se vraća u odgovarajuće faze proizvodne sheme.
PVA kristali se istiskuju na filteru, zatim u centrifugi, isperu hladnom vodom i osuše.
Volframov trioksid se dobiva toplinskom razgradnjom volframove kiseline ili PVA:
H2W04 \u003d "W03 + H20;
(NH4) 10H2W12O42 4H20 = 12W03 + 10NH3 + 10H20. (1.20)
Kalcinacija se provodi u rotacijskim električnim pećima s cijevi od čelika otpornog na toplinu 20X23H18. Način kalcinacije ovisi o namjeni volframovog trioksida, potrebnoj veličini njegovih čestica. Dakle, za dobivanje volframove žice razreda VA (vidi dolje), PVA se kalcinira na 500-550 ° C, žice razreda VCh i VT (volfram bez aditiva) - na 800-850 ° C.
Volframska kiselina se kalcinira na 750-850 °C. Volframov trioksid dobiven iz PVA ima veće čestice od trioksida dobivenog iz volframove kiseline. U volframovom trioksidu, namijenjenom za proizvodnju volframa, sadržaj W03 mora biti najmanje 99,95% za proizvodnju tvrdih legura - najmanje 99,9%.
Metode ekstrakcije i ionske izmjene za obradu otopina natrijevog volframata
Obrada otopina natrijevog volframata uvelike je pojednostavljena kada se volfram ekstrahira iz otopina ekstrakcijom organskim ekstraktantom, nakon čega slijedi ponovna ekstrakcija iz organske faze otopinom amonijaka uz odvajanje PVA od otopine amonijaka.
Budući da se u širokom rasponu pH=7,5+2,0 volfram nalazi u otopinama u obliku polimernih aniona, za ekstrakciju se koriste anionsko-izmjenjivački ekstraktanti: soli amina ili kvaternarne amonijeve baze. Konkretno, sulfatna sol trioktilamina (i?3NH)HS04 (gdje je R S8N17) koristi se u industrijskoj praksi. Najveće stope ekstrakcije volframa opažene su pri pH=2*4.
Ekstrakcija je opisana jednadžbom:
4 (i? 3NH) HS04 (opr) + H2 \ U120 * "(aq) + 2H + (aq) í̈ \u003d í̈
Í̈ \u003d í̈ (D3GSh) 4H4 \ U12O40 (org) + 4H80; (vod.). (l.2l)
Amin se otapa u kerozinu, kojemu se dodaje tehnička smjesa polihidričnih alkohola (C7 - C9) kako bi se spriječilo taloženje čvrste faze (zbog niske topljivosti soli amina u kerozinu). Približan sastav organske faze: amini 10%, alkoholi 15%, kerozin - ostalo.
Otopine pročišćene od mrlibdena, kao i nečistoće fosfora, arsena, silicija i fluora, šalju se na ekstrakciju.
Volfram se ponovno ekstrahira iz organske faze s amonijačnom vodom (3-4% NH3), čime se dobivaju otopine amonijevog volframata iz kojeg se isparavanjem i kristalizacijom izolira PVA. Ekstrakcija se provodi u aparatima tipa miješalica-taložnik ili u pulsirajućim kolonama s pakiranjem.
Prednosti ekstrakcijske obrade otopina natrijevog volframata su očite: smanjuje se broj operacija tehnološke sheme, moguće je provoditi kontinuirani proces dobivanja otopina amonijevog volframata iz otopina natrijevog volframata, a proizvodne površine se smanjuju.
Otpadne vode iz procesa ekstrakcije mogu sadržavati primjese od 80-100 mg/l amina, kao i nečistoće viših alkohola i kerozina. Za uklanjanje ovih ekološki štetnih nečistoća koristi se pjenasta flotacija i adsorpcija na aktivnom ugljenu.
Tehnologija ekstrakcije koristi se u stranim poduzećima, a primjenjuje se iu domaćim pogonima.
Korištenje smola za ionsku izmjenu smjer je sheme obrade otopina natrijevog volframata koji se natječe s ekstrakcijom. U tu svrhu koriste se niskobazni anionski izmjenjivači koji sadrže aminske skupine (često tercijarne amine) ili amfoterne smole (amfolite) koje sadrže karboksilne i aminske skupine. Pri pH=2,5+3,5 volfram polianioni se sorbiraju na smolama, a za neke smole ukupni kapacitet je 1700-1900 mg W03 po 1 g smole. U slučaju smole u obliku 8C>5~, sorpcija i elucija opisani su jednadžbama, redom:
2tf2S04 + H4W12044; 5^"4H4W12O40 + 2SOf; (1.22)
I?4H4WI2O40 + 24NH4OH = 12(NH4)2W04 + 4DON + 12H20. (l.23)
Metoda ionske izmjene razvijena je i primijenjena u jednom od poduzeća SSSR-a. Potrebno vrijeme kontakta smole s otopinom je 8-12 sati Proces se provodi u kaskadi ionsko-izmjenjivačkih kolona s suspendiranim slojem smole u kontinuiranom načinu rada. Komplicirana okolnost je djelomična izolacija PVA kristala u fazi eluiranja, što zahtijeva njihovo odvajanje od čestica smole. Kao rezultat eluiranja dobivaju se otopine koje sadrže 150-170 g/l W03 koje se dovode u isparavanje i kristalizaciju PVA.
Nedostatak tehnologije ionske izmjene u odnosu na ekstrakciju je nepovoljna kinetika (vrijeme kontakta 8-12 sati naspram 5-10 minuta za ekstrakciju). Istodobno, prednosti ionskih izmjenjivača uključuju odsutnost otpadnih otopina koje sadrže organske nečistoće, kao i sigurnost od požara i netoksičnost smola.
Razgradnja scheelitnih koncentrata kiselinama
U industrijskoj praksi, uglavnom u preradi visokokvalitetnih koncentrata scheelita (70-75% W03), koristi se izravna razgradnja scheelita klorovodičnom kiselinom.
Reakcija razgradnje:
CaW04 + 2HC1 = W03H20 + CoCl2 (1,24)
Gotovo nepovratno. Međutim, potrošnja kiseline je mnogo veća od stehiometrijski potrebne (250-300%) zbog inhibicije procesa filmovima volframove kiseline na česticama scheelita.
Razgradnja se provodi u zatvorenim reaktorima s mješalicama, obloženim emajlom otpornim na kiseline i zagrijavanim kroz parni plašt. Proces se provodi na 100-110 C. Trajanje razgradnje varira od 4-6 do 12 sati, što ovisi o stupnju mljevenja, kao i o podrijetlu koncentrata (šeeliti različitih naslaga razlikuju se po reaktivnosti).
Jedan tretman ne dovodi uvijek do potpunog otvaranja. U tom slučaju, nakon otapanja volframove kiseline u amonijačnoj vodi, ostatak se ponovno obrađuje klorovodičnom kiselinom.
Tijekom razgradnje scheelite-powellite koncentrata s udjelom od 4-5% molibdena, većina molibdena prelazi u otopinu klorovodične kiseline, što se objašnjava visokom topljivošću molibdenske kiseline u klorovodičnoj kiselini. Dakle, pri 20 C u 270 g/l HC1, topljivost H2MoO4 i H2WO4 je 182 odnosno 0,03 g/l. Unatoč tome, potpuno odvajanje molibdena nije postignuto. Precipitati volframove kiseline sadrže 0,2-0,3% molibdena, koji se ne može ekstrahirati ponovnom obradom klorovodičnom kiselinom.
Kiselinska metoda razlikuje se od alkalnih metoda razgradnje scheelita manjim brojem operacija tehnološke sheme. Međutim, kod prerade koncentrata s relativno niskim sadržajem W03 (50-55%) sa značajnim sadržajem nečistoća, za dobivanje kondicioniranog amonijevog paravolframata potrebno je provesti dva ili tri amonijačna pročišćavanja volframove kiseline, što je neekonomično. . Stoga se razgradnja klorovodičnom kiselinom najviše koristi u preradi bogatih i čistih scheelitnih koncentrata.
Nedostaci metode razgradnje klorovodičnom kiselinom su velika potrošnja kiseline, veliki volumen otpadnih otopina kalcijevog klorida i složenost njihovog zbrinjavanja.
U svjetlu zadataka stvaranja tehnologija bez otpada, zanimljiva je dušična kiselinska metoda razgradnje scheelitnih koncentrata. U ovom slučaju, matične otopine se lako uklanjaju, dobivajući nitratne soli.
DRŽAVNO TEHNIČKO SVEUČILIŠTE IRKUTSK
Kao rukopis
Artemova Olesya Stanislavovna
RAZVOJ TEHNOLOGIJE ZA VAĐENJE VONGRAMA IZ STARE jalovine DZHIDA VMK
Specijalnost 25.00.13 - Obogaćivanje minerala
disertacije za zvanje kandidata tehničkih znanosti
Irkutsk 2004
Radovi su izvedeni na Irkutskom državnom tehničkom sveučilištu.
Znanstveni savjetnik: doktor tehničkih znanosti,
Profesor K. V. Fedotov
Službeni protivnici: doktor tehničkih znanosti,
Profesor Yu.P. Morozov
Kandidat tehničkih znanosti A.Ya. Mašović
Vodeća organizacija: Država St. Petersburg
Institut za rudarstvo (Tehničko sveučilište)
Obrana će se održati 22. prosinca 2004. u /O* sati na sastanku vijeća za disertaciju D 212.073.02 Irkutskog državnog tehničkog sveučilišta na adresi: 664074, Irkutsk, ul. Lermontov, 83, soba. K-301
Znanstveni tajnik Vijeća za disertaciju Prof
OPĆI OPIS RADA
Relevantnost rada. Volframove legure imaju široku primjenu u strojarstvu, rudarstvu, metaloprerađivačkoj industriji te u proizvodnji električne rasvjetne opreme. Glavni potrošač volframa je metalurgija.
Povećanje proizvodnje volframa moguće je zbog uključivanja u preradu složenih po sastavu, teško obogaćenih, siromašnih sadržajem vrijednih komponenti i izvanbilančnih ruda, kroz široku primjenu metoda gravitacijskog obogaćivanja.
Uključivanje u preradu ustajale jalovine iz Dzhida VMK riješit će hitan problem sirovinske baze, povećati proizvodnju traženog volframovog koncentrata i poboljšati ekološku situaciju u Trans-Baikal regiji.
Svrha rada: znanstveno potkrijepiti, razviti i ispitati racionalne tehnološke metode i načine obogaćivanja ustajale jalovine VMK Dzhida koja sadrži volfram.
Ideja rada: proučavanje odnosa između strukturnog, materijalnog i faznog sastava ustajale jalovine Dzhida VMK s njihovim tehnološkim svojstvima, što omogućuje stvaranje tehnologije za preradu tehnogenih sirovina.
U radu su riješeni sljedeći zadaci: procijeniti raspodjelu volframa u prostoru glavne tehnogene formacije Dzhida VMK; proučiti materijalni sastav ustajale jalovine Dzhizhinsky VMK; istražiti kontrast ustajale jalovine u izvornoj veličini prema sadržaju W i 8 (II); istražiti gravitacijsku sposobnost pranja ustajale jalovine Dzhida VMK u različitim veličinama; utvrditi izvedivost korištenja magnetskog obogaćivanja za poboljšanje kvalitete sirovih koncentrata koji sadrže volfram; optimizirati tehnološku shemu za obogaćivanje tehnogenih sirovina iz OTO-a Dzhida VMK; provesti poluindustrijska ispitivanja razvijene sheme za izdvajanje W iz ustajale jalovine FESCO-a.
Metode istraživanja: spektralne, optičke, optičko-geometrijske, kemijske, mineraloške, fazne, gravitacijske i magnetske metode za analizu sastava materijala i tehnoloških svojstava izvornih mineralnih sirovina i proizvoda za obogaćivanje.
Pouzdanost i valjanost znanstvenih odredbi, zaključaka osigurava reprezentativan volumen laboratorijskih istraživanja; potvrđeno zadovoljavajućom konvergencijom izračunatih i eksperimentalno dobivenih rezultata obogaćivanja, korespondencijom rezultata laboratorijskih i pilot ispitivanja.
NARODNA KNJIŽNICA I Spec glyle!
Znanstvena novost:
1. Utvrđeno je da se tehnogene sirovine koje sadrže volfram Dzhida VMK u bilo kojoj veličini učinkovito obogaćuju gravitacijskom metodom.
2. Uz pomoć generaliziranih krivulja gravitacijskog dotjerivanja utvrđeni su granični tehnološki parametri za obradu ustajale jalovine Dzhida VMK različitih veličina gravitacijskom metodom i identificirani uvjeti za dobivanje deponijske jalovine uz minimalne gubitke volframa.
3. Utvrđeni su novi obrasci procesa separacije koji određuju gravitacijsko pranje tehnogenih sirovina koje sadrže volfram veličine čestica +0,1 mm.
4. Za staru jalovinu Dzhida VMK utvrđena je pouzdana i značajna korelacija između sadržaja WO3 i S(II).
Praktični značaj: razvijena je tehnologija za obogaćivanje ustajale jalovine Dzhida VMK, koja osigurava učinkovitu ekstrakciju volframa, što omogućuje dobivanje kondicioniranog volframovog koncentrata.
Provjera rada: glavni sadržaj rada disertacije i njegove pojedinačne odredbe izvještavani su na godišnjim znanstvenim i tehničkim konferencijama Irkutskog državnog tehničkog sveučilišta (Irkutsk, 2001.-2004.), Sveruskoj školi-seminaru za mlade znanstvenike " Leon Readings - 2004" (Irkutsk , 2004), znanstveni simpozij "Rudarov tjedan - 2001" (Moskva, 2001), Sveruski znanstveni i praktični skup "Nove tehnologije u metalurgiji, kemiji, obogaćivanju i ekologiji" (Sankt Peterburg, 2004). .), Plaksinska čitanja - 2004. U cijelosti je disertacijski rad predstavljen na Odsjeku za preradu minerala i inženjersku ekologiju na ISTU, 2004. i na Zavodu za preradu minerala, SPGGI (TU), 2004.
Publikacije. Na temu disertacije objavljeno je 8 tiskanih publikacija.
Struktura i djelokrug rada. Disertacija se sastoji od uvoda, 3 poglavlja, zaključka, 104 bibliografska izvora i sadrži 139 stranica, uključujući 14 slika, 27 tablica i 3 dodatka.
Autor izražava duboku zahvalnost znanstvenom savjetniku, doktoru tehničkih znanosti, prof. K.V. Fedotovu za profesionalno i prijateljsko vodstvo; prof. JE LI ON. Belkova za vrijedne savjete i korisne kritičke napomene iznesene tijekom rasprave o disertacijskom radu; G.A. Badenikova - za savjetovanje o izračunu tehnološke sheme. Autorica iskreno zahvaljuje djelatnicima Zavoda na sveobuhvatnoj pomoći i potpori pri izradi diplomskog rada.
Objektivni preduvjeti za uključivanje tehnogenih formacija u proizvodni promet su:
Neminovnost očuvanja potencijala prirodnih resursa. Osigurava se smanjenjem eksploatacije primarnih mineralnih sirovina i smanjenjem količine štete nanesene okolišu;
Potreba zamjene primarnih resursa sekundarnim. Zbog potreba proizvodnje u materijalu i sirovinama, uključujući one industrije čija je baza prirodnih resursa praktički iscrpljena;
Mogućnost korištenja industrijskog otpada osigurana je uvođenjem znanstveno-tehnološkog napretka.
Proizvodnja proizvoda iz tehnogenih ležišta u pravilu je nekoliko puta jeftinija nego od sirovina posebno iskopanih za tu namjenu, a odlikuje se brzim povratom ulaganja.
Postrojenja za skladištenje otpada od obogaćivanja ruda su objekti povećane opasnosti za okoliš zbog negativnog utjecaja na zračni bazen, podzemne i površinske vode te pokrivač tla na ogromnim površinama.
Plaćanja za onečišćenje oblik su naknade za ekonomsku štetu od emisija i ispuštanja onečišćujućih tvari u okoliš, kao i za odlaganje otpada na teritoriju Ruske Federacije.
Rudno polje Dzhida pripada visokotemperaturnom duboko hidrotermalnom kvarc-volframitnom (ili kvarc-hubneritskom) tipu ležišta, koji imaju veliku ulogu u vađenju volframa. Glavni rudni mineral je volframit, čiji se sastav kreće od ferberita do pobnerita sa svim međučlanovima serije. Šelit je rjeđi volfrat.
Rude s volframitom obogaćuju se uglavnom prema gravitacijskoj shemi; obično se gravitacijske metode mokrog obogaćivanja koriste na strojevima za jigging, hidrociklonima i koncentracijskim tablicama. Magnetsko odvajanje koristi se za dobivanje kondicioniranih koncentrata.
Do 1976. godine, rude u tvornici Dzhida VMK prerađivane su prema gravitacijskoj shemi s dva stupnja, uključujući teško-srednje obogaćivanje u hidrociklonima, dvostupanjsko koncentraciju usko klasificiranih rudnih materijala na stolovima s tri palube tipa SK-22, ponovno mljevenje i obogaćivanje industrijskih proizvoda u zasebnom ciklusu. Mulj je obogaćivan prema posebnoj gravitacijskoj shemi korištenjem domaćih i stranih tablica koncentracije mulja.
Od 1974. do 1996. godine pohranjena je jalovina obogaćivanja samo volframovih ruda. 1985-86 rude su prerađivane prema gravitaciono-flotacijskoj tehnološkoj shemi. Stoga su jalovina gravitacijskog obogaćivanja i sulfidni produkt gravitacije flotacije odloženi u glavno jalovište. Od sredine 1980-ih, zbog povećanog protoka rude koja se isporučuje iz rudnika Inkursky, udio otpada iz velikih
klase, do 1-3 mm. Nakon gašenja Rudarsko-prerađivačke tvornice Dzhida 1996. godine, taložnik je samouništen uslijed isparavanja i filtracije.
2000. godine „Jalovište za hitno ispuštanje“ (HAS) izdvojeno je kao samostalan objekt zbog prilično značajne razlike od glavnog jalovišta u pogledu uvjeta pojavljivanja, obima rezervi, kvalitete i stupnja očuvanosti tehnogenih pijesak. Druga sekundarna jalovina su aluvijalne tehnogene naslage (ATO), koje uključuju ponovno taloženu flotacijsku jalovinu ruda molibdena u području riječne doline. Modonkul.
Osnovni standardi plaćanja za zbrinjavanje otpada unutar utvrđenih granica za Dzhida VMK su 90.620.000 rubalja. Godišnja šteta okoliša od degradacije zemljišta zbog postavljanja jalovine ustajale rude procjenjuje se na 20.990.200 rubalja.
Dakle, sudjelovanje u preradi ustajale jalovine obogaćivanja rude Dzhida VMK omogućit će: 1) rješavanje problema sirovinske baze poduzeća; 2) povećati proizvodnju traženog "koncentrata" i 3) poboljšati ekološku situaciju u regiji Trans-Baikal.
Sastav materijala i tehnološka svojstva tehnogene mineralne formacije Dzhida VMK
Provedena su geološka ispitivanja ustajale jalovine Dzhida VMK. Pri pregledu bočnog jalovišta (Hergentno ispuštanje Tailing Facility (HAS)) uzeto je 13 uzoraka. Na području ATO ležišta uzeto je 5 uzoraka. Površina uzorkovanja glavnog jalovišta (MTF) iznosila je 1015 tisuća m2 (101,5 ha), uzeto je 385 djelomičnih uzoraka. Masa uzetih uzoraka je 5 tona. Svi uzeti uzorci analizirani su na sadržaj "03 i 8 (I).
OTO, CHAT i ATO statistički su uspoređeni u smislu sadržaja "03" pomoću Studentovog t-testa. Uz vjerojatnost pouzdanosti od 95% utvrđeno je: 1) nepostojanje značajne statističke razlike u sadržaju "03 " između privatnih uzoraka bočne jalovine; 2) prosječni rezultati ispitivanja OTO-a u smislu sadržaja "03" 1999. i 2000. godine odnose se na istu opću populaciju; 3) prosječni rezultati ispitivanja glavne i sekundarne jalovine u smislu sadržaja "03". “ međusobno se značajno razlikuju i mineralne sirovine svih jalovina ne mogu se prerađivati po istoj tehnologiji.
Predmet našeg proučavanja je opća relativnost.
Materijalni sastav mineralnih sirovina OTO-a Dzhida VMK utvrđen je analizom običnih i grupnih tehnoloških uzoraka, kao i proizvoda njihove prerade. Slučajni uzorci analizirani su na sadržaj "03 i 8(11). Grupni uzorci korišteni su za mineralošku, kemijsku, faznu i sita analizu.
Prema spektralnoj semi-kvantitativnoj analizi reprezentativnog analitičkog uzorka, glavna korisna komponenta - " i sekundarna - Pb, /u, Cu, Au i sadržaj "03 u obliku scheelite
prilično stabilan u svim veličinskim klasama raznih razlika pijeska i prosječno 0,042-0,044%. Sadržaj WO3 u obliku hübnerita nije isti u različitim veličinama. Visok sadržaj WO3 u obliku hübnerita bilježi se u česticama veličine +1 mm (od 0,067 do 0,145%), a posebno u klasi -0,08+0 mm (od 0,210 do 0,273%). Ova je značajka tipična za svijetli i tamni pijesak i zadržana je za prosječni uzorak.
Rezultati spektralnih, kemijskih, mineraloških i faznih analiza potvrđuju da će svojstva hubnerita, kao glavnog mineralnog oblika \UO3, odrediti tehnologiju obogaćivanja mineralnih sirovina OTO Dzhida VMK.
Granulometrijske karakteristike sirovina OTO s raspodjelom volframa po veličinskim klasama prikazane su na sl. 1.2.
Može se vidjeti da najveći dio materijala uzorka OTO (~58%) ima finoću od -1 + 0,25 mm, od kojih po 17% spada u velike (-3 + 1 mm) i male (-0,25 + 0,1 mm) klase . Udio materijala finoće -0,1 mm iznosi oko 8%, od čega polovica (4,13%) otpada na klasu mulja -0,044 + 0 mm.
Volfram karakterizira mala fluktuacija (0,04-0,05%) u sadržaju u klasama veličina od -3 +1 mm do -0,25 + 0,1 mm i nagli porast (do 0,38%) u klasi veličine -0,1+ 0,044 mm. U klasi sluzi -0,044+0 mm sadržaj volframa je smanjen na 0,19%. To jest, 25,28% volframa je koncentrirano u klasi -0,1 + 0,044 mm s izlazom ove klase od oko 4% i 37,58% - u klasi -0,1 + 0 mm s izlazom ove klase od 8,37%.
Kao rezultat analize podataka o impregnaciji hubnerita i scheelita u mineralne sirovine OTO početne veličine i zgnječenog na -0,5 mm (vidi tablicu 1).
Tablica 1 - Raspodjela zrna i izraslina pobnerita i scheelite po veličinskim klasama početnih i drobljenih mineralnih sirovina _
Razredi veličina, mm Raspodjela, %
Huebnerit Scheelite
Besplatno žitarice | Spojevi žitarice | spojevi
OTO materijal u originalnoj veličini (- 5 +0 mm)
3+1 36,1 63,9 37,2 62,8
1+0,5 53,6 46,4 56,8 43,2
0,5+0,25 79,2 20,8 79,2 20,8
0,25+0,125 88,1 11,9 90,1 9,9
0,125+0,063 93,6 6,4 93,0 7,0
0,063+0 96,0 4,0 97,0 3,0
Iznos 62,8 37,2 64,5 35,5
OTO materijal brušen na -0,5 +0 mm
0,5+0,25 71,5 28,5 67,1 32,9
0,25+0,125 75,3 24,7 77,9 22,1
0,125+0,063 89,8 10,2 86,1 13,9
0,063+0 90,4 9,6 99,3 6,7
Iznos 80,1 19,9 78,5 21,5
Utvrđeno je da je potrebno razvrstavati otopljene mineralne sirovine OTO po veličini od 0,1 mm i odvojeno obogaćivati dobivene klase. Iz velike klase slijedi: 1) odvojiti slobodna zrna u grubi koncentrat, 2) jalovinu koja sadrži izrasline podvrgnuti ponovnom mljevenju, odlivanju, kombiniranju s razlupljenom klasom -0,1 + 0 mm izvorne mineralne sirovine i gravitacijom obogaćivanje za izdvajanje finih zrna scheelite i pobnerita u srednju smjesu.
Za ocjenu kontrasta mineralnih sirovina OTO korišten je tehnološki uzorak koji predstavlja skup od 385 pojedinačnih uzoraka. Rezultati frakcioniranja pojedinih uzoraka prema sadržaju WO3 i sulfidnog sumpora prikazani su na sl.3,4.
0 S OS 0,2 "l Mol O 2 SS * _ " 8
S(kk|Jupytetr"oknsmm"fr**m.% Sadrži gulfkshoYa
Riža. Slika 3 Uvjetne kontrastne krivulje početne Sl. 4 Uvjetne kontrastne krivulje početne
mineralne sirovine OTO prema sadržaju N/O) mineralne sirovine OTO prema sadržaju 8 (II)
Utvrđeno je da su omjeri kontrasta za sadržaj WO3 i S (II) 0,44 odnosno 0,48. Uzimajući u obzir suprotnu klasifikaciju ruda, ispitivane mineralne sirovine prema sadržaju WO3 i S(II) spadaju u kategoriju nekontrastnih ruda. Radiometrijsko obogaćivanje nije
pogodan za vađenje volframa iz male ustajale jalovine Dzhida VMK.
Rezultati korelacijske analize, koji su otkrili matematički odnos između koncentracija \\O3 i S (II) (C3 = 0»0232+0,038C5(u) i r=0,827; korelacija je pouzdana i pouzdana), potvrđuju zaključci o nesvrsishodnosti uporabe radiometrijskog odvajanja.
Rezultati analize odvajanja mineralnih zrna OTO u teškim tekućinama pripremljenim na bazi selen bromida korišteni su za izračunavanje i prikaz krivulja gravitacijskog pranja (slika 5.), iz čijeg oblika, posebno krivulje, proizlazi da OTO Dzhida VMK prikladan je za bilo koju metodu gravitacijskog obogaćivanja minerala.
Uzimajući u obzir nedostatke u korištenju krivulja gravitacijskog obogaćivanja, a posebno krivulje za određivanje sadržaja metala u frakcijama na površini sa zadanim iskorištenjem ili iskorištenjem, izgrađene su generalizirane krivulje gravitacijskog obogaćivanja (sl. 6), rezultati analize koji su dati u tablici. 2.
Tablica 2 - Predviđeni tehnološki pokazatelji obogaćivanja različitih klasa veličine ustajale jalovine Dzhida VMK gravitacijskom metodom_
g Veličina razreda, mm Maksimalni gubici \Y s jalovinom, % Prinos jalovine, % XV sadržaj, %
u repovima na kraju
3+1 0,0400 25 82,5 0,207 0,1
3+0,5 0,0400 25 84 0,19 0,18
3+0,25 0,0440 25 90 0,15 0,28
3+0,1 0,0416 25 84,5 0,07 0,175
3+0,044 0,0483 25 87 0,064 0,27
1+0,5 0,04 25 84,5 0,16 0,2
1+0,044 0,0500 25 87 0,038 0,29
0,5+0,25 0,05 25 92,5 0,04 0,45
0,5+0,044 0,0552 25 88 0,025 0,365
0,25+0,1 0,03 25 79 0,0108 0,1
0,25+0,044 0,0633 15 78 0,02 0,3
0,1+0,044 0,193 7 82,5 0,018 1,017
U pogledu gravitacijske perivosti, klase -0,25+0,044 i -0,1+0,044 mm značajno se razlikuju od materijala drugih veličina. Najbolji tehnološki pokazatelji gravitacijskog obogaćivanja mineralnih sirovina predviđaju se za klasu veličine -0,1+0,044 mm:
Rezultati elektromagnetskog frakcioniranja teških frakcija (HF), gravitacijske analize pomoću univerzalnog magneta Sochnev C-5 i magnetske separacije HF-a pokazali su da je ukupni prinos jako magnetskih i nemagnetskih frakcija 21,47%, a gubici "u njima su 4,5%.Minimalni gubici "s nemagnetskom frakcijom i maksimalnim sadržajem" u kombiniranom slabo magnetskom produktu predviđaju se ako separacijski izvor u jakom magnetskom polju ima veličinu čestica od -0,1 + 0 mm.
Riža. 5 Gravitacijske krivulje perljivosti za ustajalu jalovinu Dzhida VMK
f) klasa -0,1+0,044 mm
Riža. 6 Generalizirane krivulje gravitacijske perljivosti različitih veličinskih klasa mineralnih sirovina OTO
Izrada tehnološke sheme za obogaćivanje ustajale jalovine Dzhida VM K
Rezultati tehnološkog ispitivanja različitih metoda gravitacijskog obogaćivanja ustajale jalovine Dzhida VMK prikazani su u tablici. 3.
Tablica 3 - Rezultati ispitivanja gravitacijskih uređaja
Dobiveni su usporedivi tehnološki pokazatelji za ekstrakciju WO3 u grubi koncentrat tijekom obogaćivanja nerazvrstane ustajale jalovine kako pužnom tako i centrifugalnom separacijom. Minimalni gubici WO3 s jalovinom utvrđeni su tijekom obogaćivanja u centrifugalnom koncentratoru klase -0,1+0 mm.
U tablici. Slika 4 prikazuje granulometrijski sastav sirovog W-koncentrata s veličinom čestica od -0,1+0 mm.
Tablica 4 - Raspodjela veličine čestica sirovog W-koncentrata
Klasa veličine, mm Prinos klasa, % Sadržaj Distribucija AUOz
Apsolutni relativ, %
1+0,071 13,97 0,11 1,5345 2,046
0,071+0,044 33,64 0,13 4,332 5,831
0,044+0,020 29,26 2,14 62,6164 83,488
0,020+0 23,13 0,28 6,4764 8,635
Ukupno 100,00 0,75 75,0005 100,0
U koncentratu je glavna količina WO3 u klasi -0,044+0,020 mm.
Prema podacima mineraloške analize, u odnosu na izvorni materijal, maseni udio pobnerita (1,7%) i rudnih sulfidnih minerala, posebice pirita (16,33%), veći je u koncentratu. Sadržaj stijena - 76,9%. Kvaliteta sirovog W-koncentrata može se poboljšati uzastopnom primjenom magnetskog i centrifugalnog odvajanja.
Rezultati ispitivanja gravitacijskih aparata za izdvajanje >UOz iz jalovine primarnog gravitacijskog obogaćivanja mineralnih sirovina OTO s veličinom čestica +0,1 mm (tablica 5) dokazali su da je najučinkovitiji aparat koncentrator KKEL80N.
Tablica 5 - Rezultati ispitivanja gravitacijskih aparata
Proizvod G,% ßwo>, % rßwo> st ">, %
vijčani separator
Koncentrat 19,25 0,12 2,3345 29,55
Jalovina 80,75 0,07 5,5656 70,45
Početni uzorak 100,00 0,079 7,9001 100,00
wing gateway
Koncentrat 15,75 0,17 2,6750 33,90
Jalovina 84,25 0,06 5,2880 66,10
Početni uzorak 100,00 0,08 7,9630 100,00
tablica koncentracije
Koncentrat 23,73 0,15 3,56 44,50
Jalovina 76,27 0,06 4,44 55,50
Početni uzorak 100,00 0,08 8,00 100,00
centrifugalni koncentrator KC-MD3
Koncentrat 39,25 0,175 6,885 85,00
Jalovina 60,75 0,020 1,215 15,00
Početni uzorak 100,00 0,081 8,100 100,00
Prilikom optimizacije tehnološke sheme za obogaćivanje mineralnih sirovina od strane OTO-a Dzhida VMK uzeto je u obzir: 1) tehnološke sheme za preradu fino raspršenih ruda volframita domaćih i inozemnih postrojenja za obogaćivanje; 2) tehničke karakteristike suvremene opreme koja se koristi i njezine dimenzije; 3) mogućnost korištenja iste opreme za istovremenu provedbu dvije operacije, na primjer, odvajanje minerala po veličini i dehidraciju; 4) ekonomski troškovi izrade hardvera tehnološke sheme; 5) rezultate prikazane u Poglavlju 2; 6) GOST zahtjevi za kvalitetu volframovih koncentrata.
Tijekom poluindustrijskog ispitivanja razvijene tehnologije (sl. 7-8 i tablica 6) prerađeno je 15 tona početnih mineralnih sirovina u 24 sata.
Rezultati spektralne analize reprezentativnog uzorka dobivenog koncentrata potvrđuju da je W-koncentrat III magnetske separacije kondicioniran i da odgovara stupnju KVG (T) GOST 213-73.
Slika 8 Rezultati tehnološkog ispitivanja sheme za doradu grubih koncentrata i srednjaka iz ustajale jalovine Dzhida VMK
Tablica 6 - Rezultati ispitivanja tehnološke sheme
Proizvod u
Koncentrat za kondicioniranje 0,14 62,700 8,778 49,875
Odlagalište jalovine 99,86 0,088 8,822 50,125
Izvorna ruda 100,00 0,176 17,600 100,000
ZAKLJUČAK
Rad daje rješenje hitnog znanstveno-proizvodnog problema: znanstveno utemeljene, razvijene i u određenoj mjeri implementirane učinkovite tehnološke metode za vađenje volframa iz ustajale jalovine rudne koncentracije Dzhida VMK.
Glavni rezultati istraživanja, razvoja i njihova praktična provedba su sljedeći
Glavna korisna komponenta je volfram, prema čijem sadržaju je ustajala jalovina nekontrastna ruda, zastupljen je uglavnom hubneritom, koji određuje tehnološka svojstva tehnogenih sirovina. Volfram je neravnomjerno raspoređen po klasama veličina i njegova je glavna količina koncentrirana u veličini
Dokazano je da je jedina učinkovita metoda obogaćivanja ustajale jalovine Dzhida VMK koja sadrži W gravitacija. Na temelju analize generaliziranih krivulja gravitacijske koncentracije ustajale jalovine koja sadrži W, utvrđeno je da je deponijska jalovina s minimalnim gubicima volframa obilježje obogaćivanja tehnogenih sirovina s veličinom čestica od -0,1 + Omm. . Utvrđeni su novi obrasci procesa separacije koji određuju tehnološke parametre gravitacijskog obogaćivanja ustajale jalovine Dzhida VMK finoće +0,1 mm.
Dokazano je da među gravitacijskim aparatima koji se koriste u rudarskoj industriji za obogaćivanje ruda koje sadrže W, za maksimalno izvlačenje volframa iz tehnogenih sirovina Dzhida VMK u grube W-koncentrate, pužni separator i jalovinu KKEb80N primarnog obogaćivanja tehnogenih sirovina koje sadrže W u veličini - 0,1 mm.
3. Optimizirana tehnološka shema za ekstrakciju volframa iz ustajale jalovine koncentracije rude Dzhida VMK omogućila je dobivanje kondicioniranog W-koncentrata, rješavanje problema iscrpljivanja mineralnih resursa Dzhida VMK i smanjenje negativnog utjecaja. proizvodnih aktivnosti poduzeća na okoliš.
Poželjna upotreba gravitacijske opreme. Tijekom poluindustrijskih ispitivanja razvijene tehnologije vađenja volframa iz ustajale jalovine Dzhida VMK dobiven je kondicionirani "-koncentrat sa sadržajem" 03 62,7% s ekstrakcijom od 49,9%. Razdoblje povrata za postrojenje za obogaćivanje za preradu ustajale jalovine Dzhida VMK za vađenje volframa bilo je 0,55 godina.
Glavne odredbe disertacije objavljene su u sljedećim djelima:
1. Fedotov K.V., Artemova O.S., Polinskina I.V. Procjena mogućnosti prerade ustajale jalovine Dzhida VMK, Obrada rude: Sub. znanstvenim djela. - Irkutsk: Izdavačka kuća ISTU-a, 2002. - 204 str., S. 74-78.
2. Fedotov K.V., Senchenko A.E., Artemova O.S., Polinkina I.V. Upotreba centrifugalnog separatora s kontinuiranim ispuštanjem koncentrata za ekstrakciju volframa i zlata iz jalovine Dzhida VMK, Problemi okoliša i nove tehnologije za složenu preradu mineralnih sirovina: Zbornik radova međunarodne konferencije "Plaksinsky Readings - 2002. ". - M.: P99, Izdavačka kuća PCC "Altex", 2002. - 130 str., str. 96-97.
3. Zelinskaya E.V., Artemova O.S. Mogućnost podešavanja selektivnosti djelovanja kolektora tijekom flotacije ruda koje sadrže volfram iz ustajale jalovine, Usmjerene promjene fizikalno-kemijskih svojstava minerala u procesima prerade minerala (Plaksin Readings), materijali međunarodnog skupa. . - M.: Alteks, 2003. -145 s, str.67-68.
4. Fedotov K.V., Artemova O.S. Problemi prerade ustajalih proizvoda koji sadrže volfram Suvremene metode prerade mineralnih sirovina: Zbornik radova. Irkutsk: Irk. Država. Oni. Sveučilište, 2004. (monografija). - 86 str.
5. Artemova O. S., Gaiduk A. A. Ekstrakcija volframa iz ustajale jalovine tvornice volfram-molibdena Dzhida. Perspektive razvoja tehnologije, ekologije i automatizacije kemijske, prehrambene i metalurške industrije: Zbornik radova znanstveno-praktičnog skupa. - Irkutsk: Izdavačka kuća ISTU-a. - 2004. - 100 str.
6. Artemova O.S. Procjena neravnomjerne raspodjele volframa u jalovini Dzhida. Suvremene metode procjene tehnoloških svojstava mineralnih sirovina plemenitih metala i dijamanata i progresivne tehnologije njihove obrade (Plaksinska čitanja): Zbornik radova s međunarodnog skupa. Irkutsk, 13.-17. rujna 2004. - M.: Alteks, 2004. - 232 str.
7. Artemova O.S., Fedotov K.V., Belkova O.N. Izgledi za korištenje tehnogenog ležišta Dzhida VMK. Sveruska znanstveno-praktična konferencija "Nove tehnologije u metalurgiji, hemiji, obogaćivanju i ekologiji", Sankt Peterburg, 2004.
Potpisano za tisak 12. H 2004. Format 60x84 1/16. Papir za ispis. Offset tisak. Konv. pećnica l. Uch.-ed.l. 125. Naklada 400 primjeraka. Zakon 460.
ID broj 06506 od 26. prosinca 2001. Irkutsko državno tehničko sveučilište 664074, Irkutsk, ul. Lermontova, 83
Ruski fond RNB
1. ZNAČAJ UMJETNE MINERALNE SIROVINE
1.1. Mineralni resursi rudne industrije u Ruskoj Federaciji i podindustrija volframa
1.2. Tehnogene mineralne formacije. Klasifikacija. Potreba za korištenjem
1.3. Tehnogene mineralne formacije Dzhida VMK
1.4. Ciljevi i zadaci studija. Metode istraživanja. Odredbe za obranu
2. ISTRAŽIVANJE MATERIJALNOG SASTAVA I TEHNOLOŠKIH SVOJSTVA STARE jalovine VMK DZHIDA
2.1. Geološko uzorkovanje i procjena raspodjele volframa
2.2. Materijalni sastav mineralnih sirovina
2.3. Tehnološka svojstva mineralnih sirovina
2.3.1. Ocjenjivanje
2.3.2. Proučavanje mogućnosti radiometrijskog odvajanja mineralnih sirovina u početnoj veličini
2.3.3. Analiza gravitacije
2.3.4. Magnetska analiza
3. IZRADA TEHNOLOŠKE SHEME ZA VAĐENJE VONGRAMA IZ STARE JAPOVINE DZHIDA VMK
3.1. Tehnološka ispitivanja različitih gravitacijskih uređaja pri obogaćivanju ustajale jalovine različitih veličina
3.2. Optimizacija sheme obrade GR
3.3. Poluindustrijsko ispitivanje razvijene tehnološke sheme za obogaćivanje opće teorije relativnosti i industrijskog postrojenja
Uvod Disertacija iz znanosti o Zemlji, na temu "Razvoj tehnologije za vađenje volframa iz ustajale jalovine Dzhida VMK"
Znanosti o obogaćivanju minerala prvenstveno su usmjerene na razvoj teoretskih osnova procesa separacije minerala i stvaranje aparata za obogaćivanje, na otkrivanje odnosa između obrazaca raspodjele komponenti i uvjeta separacije u proizvodima obogaćivanja kako bi se povećala selektivnost i brzina odvajanja, njegova učinkovitost i ekonomičnost i sigurnost okoliša.
Unatoč značajnim rezervama minerala i smanjenju potrošnje resursa posljednjih godina, iscrpljivanje mineralnih resursa jedan je od najvažnijih problema u Rusiji. Slaba uporaba tehnologija koje štede resurse doprinosi velikim gubicima minerala tijekom vađenja i obogaćivanja sirovina.
Analiza razvoja opreme i tehnologije za preradu minerala u posljednjih 10-15 godina ukazuje na značajna dostignuća domaće fundamentalne znanosti u području razumijevanja glavnih pojava i obrazaca u razdvajanju mineralnih kompleksa, što omogućuje stvaranje visoko učinkovite procese i tehnologije za primarnu preradu ruda složenog materijalnog sastava te, posljedično, osigurati metalurškoj industriji potreban asortiman i kvalitetu koncentrata. Istovremeno, u našoj zemlji, u usporedbi s razvijenim inozemstvom, još uvijek postoji značajno zaostajanje u razvoju strojograditeljske baze za proizvodnju glavne i pomoćne opreme za obogaćivanje, njezinoj kvaliteti, potrošnji metala, energetskoj intenzivnosti. i otpornost na habanje.
Osim toga, zbog odjelne pripadnosti rudarskih i prerađivačkih poduzeća, složene sirovine prerađivane su samo uzimajući u obzir potrebne potrebe industrije za određenim metalom, što je dovelo do neracionalnog korištenja prirodnih mineralnih resursa i povećanja troškova. skladištenja otpada. Trenutno je akumulirano više od 12 milijardi tona otpada, čiji sadržaj vrijednih komponenti u nekim slučajevima premašuje njihov sadržaj u prirodnim naslagama.
Uz navedene negativne trendove, počevši od 90-ih godina, stanje okoliša u rudarskim i prerađivačkim poduzećima naglo se pogoršalo (u nizu regija koje ugrožavaju postojanje ne samo biote, već i ljudi), došlo je do progresivnog pada vađenje ruda obojenih i željeznih metala, rudarske i kemijske sirovine, pogoršanje kvalitete prerađenih ruda i, kao rezultat toga, uključenost u preradu vatrostalnih ruda složenog materijalnog sastava, koje karakterizira nizak sadržaj vrijednih komponenti , fina diseminacija i slična tehnološka svojstva minerala. Tako je u proteklih 20 godina sadržaj obojenih metala u rudama smanjen za 1,3-1,5 puta, željeza za 1,25 puta, zlata za 1,2 puta, udio vatrostalnih ruda i ugljena porastao je sa 15% na 40% ukupne mase sirovina isporučenih za obogaćivanje.
Utjecaj čovjeka na prirodni okoliš u procesu gospodarskog djelovanja sada postaje globalan. U pogledu razmjera vađenih i transportiranih stijena, transformacija reljefa, utjecaj na preraspodjelu i dinamiku površinskih i podzemnih voda, aktivacija geokemijskog transporta itd. ova je aktivnost usporediva s geološkim procesima.
Neviđeni razmjeri obnovivih mineralnih resursa dovode do njihovog brzog iscrpljivanja, nakupljanja velike količine otpada na površini Zemlje, u atmosferi i hidrosferi, postupne degradacije prirodnih krajolika, smanjenja biološke raznolikosti, smanjenja prirodnog potencijala. teritorija i njihove funkcije za održavanje života.
Postrojenja za skladištenje otpada za preradu rude objekti su povećane ekološke opasnosti zbog negativnog utjecaja na zračni bazen, podzemne i površinske vode te pokrivač tla na velikim površinama. Uz to, jalovina je slabo istražena umjetna ležišta, čije će korištenje omogućiti dobivanje dodatnih izvora rudnih i mineralnih sirovina uz značajno smanjenje razmjera narušavanja geološkog okoliša u regiji.
Proizvodnja proizvoda iz tehnogenih ležišta u pravilu je nekoliko puta jeftinija nego od sirovina posebno iskopanih za tu namjenu, a odlikuje se brzim povratom ulaganja. Međutim, složen kemijski, mineraloški i granulometrijski sastav jalovine, kao i širok raspon minerala sadržanih u njoj (od glavnih i pripadajućih komponenti do najjednostavnijih građevinskih materijala) otežavaju izračunavanje ukupnog ekonomskog učinka njihove prerade i odrediti individualni pristup procjeni svake jalovine.
Slijedom toga, u ovom trenutku pojavio se niz nerješivih proturječnosti između promjene prirode baze mineralnih sirovina, tj. potreba uključivanja u preradu vatrostalnih ruda i umjetnih naslaga, pogoršana ekološka situacija u rudarskim regijama te stanje tehnologije, tehnologije i organizacije primarne prerade mineralnih sirovina.
Problematika korištenja otpada od obogaćivanja polimetalnih, zlatonosnih i rijetkih metala ima ekonomski i ekološki aspekt.
V.A. Chanturia, V.Z. Kožin, V.M. Avdokhin, S.B. Leonov, JI.A. Barsky, A.A. Abramov, V.I. Karmazin, S.I. Mitrofanov i drugi.
Važan dio ukupne strategije rudarske industrije, uklj. volframa, je rast korištenja otpada od prerade rude kao dodatnih izvora rudnih i mineralnih sirovina, uz značajno smanjenje opsega narušavanja geološkog okoliša u regiji i negativnog utjecaja na sve sastavnice okoliša.
U području korištenja otpada od prerade rude najvažnija je detaljna mineraloška i tehnološka studija svakog specifičnog, pojedinačnog tehnogenog ležišta, čiji će rezultati omogućiti razvoj učinkovite i ekološki prihvatljive tehnologije za industrijski razvoj dodatnog izvora. rudnih i mineralnih sirovina.
Problemi razmatrani u radu disertacije riješeni su u skladu sa znanstvenim smjerom Odjela za preradu minerala i inženjersku ekologiju Irkutskog državnog tehničkog sveučilišta na temu „Temeljna i tehnološka istraživanja u području prerade mineralnih i tehnogenih sirovina za svrha njegove integrirane uporabe, uzimajući u obzir ekološke probleme u složenim industrijskim sustavima” i filmska tema br. 118 “Istraživanje o mogućnosti pranja ustajale jalovine Dzhida VMK”.
Svrha rada je znanstveno potkrijepiti, razviti i ispitati racionalne tehnološke metode za obogaćivanje ustajale jalovine Dzhida VMK koja sadrži volfram.
U radu su riješeni sljedeći zadaci:
Procijenite distribuciju volframa u cijelom prostoru glavne tehnogene formacije Dzhida VMK;
Proučiti materijalni sastav ustajale jalovine Dzhizhinsky VMK;
Istražiti kontrast ustajale jalovine u izvornoj veličini prema sadržaju W i S (II); istražiti gravitacijsku sposobnost pranja ustajale jalovine Dzhida VMK u različitim veličinama;
Utvrditi izvedivost korištenja magnetskog obogaćivanja za poboljšanje kvalitete sirovih koncentrata koji sadrže volfram;
Optimizirati tehnološku shemu za obogaćivanje tehnogenih sirovina iz OTO-a Dzhida VMK; provesti poluindustrijska ispitivanja razvijene sheme za izdvajanje W iz ustajale jalovine FESCO-a;
Razviti shemu lanca uređaja za industrijsku preradu ustajale jalovine Dzhida VMK.
Za provedbu istraživanja korišten je reprezentativni tehnološki uzorak ustajale jalovine Dzhida VMK.
Pri rješavanju formuliranih problema korištene su sljedeće metode istraživanja: spektralne, optičke, kemijske, mineraloške, fazne, gravitacijske i magnetske metode za analizu sastava materijala i tehnoloških svojstava početnih mineralnih sirovina i proizvoda obogaćivanja.
U obranu se iznose sljedeće glavne znanstvene odredbe: Utvrđuju se zakonitosti distribucije početnih tehnogenih mineralnih sirovina i volframa po veličinskim klasama. Dokazuje se nužnost primarne (preliminarne) klasifikacije po veličini 3 mm.
Utvrđene su kvantitativne karakteristike ustajale jalovine rude prerade ruda VMK Dzhida u smislu sadržaja WO3 i sulfidnog sumpora. Dokazano je da izvorne mineralne sirovine spadaju u kategoriju nekontrastnih ruda. Otkrivena je značajna i pouzdana korelacija između sadržaja WO3 i S(II).
Utvrđeni su kvantitativni obrasci gravitacijskog obogaćivanja ustajale jalovine Dzhida VMK. Dokazano je da je za izvorni materijal bilo koje veličine učinkovita metoda za ekstrakciju W gravitacijsko obogaćivanje. Određeni su prediktivni tehnološki pokazatelji gravitacijskog obogaćivanja početnih mineralnih sirovina u različitim veličinama.
Utvrđene su kvantitativne zakonitosti u raspodjeli ustajale jalovine koncentracije rude Dzhida VMK po frakcijama različite specifične magnetske osjetljivosti. Sukcesivno korištenje magnetskog i centrifugalnog odvajanja dokazano poboljšava kvalitetu sirovih proizvoda koji sadrže W. Tehnološki načini magnetske separacije su optimizirani.
Zaključak Disertacija na temu "Obogaćivanje minerala", Artemova, Olesya Stanislavovna
Glavni rezultati istraživanja, razvoja i njihove praktične provedbe su sljedeći:
1. Provedena je analiza trenutne situacije u Ruskoj Federaciji s mineralnim resursima rudne industrije, posebice industrije volframa. Na primjeru VMK Dzhida pokazuje se da je problem uključivanja u preradu jalovine ustajale rude relevantan, koji ima tehnološki, ekonomski i ekološki značaj.
2. Utvrđen je materijalni sastav i tehnološka svojstva glavne W-noseće tehnogene formacije Dzhida VMK.
Glavna korisna komponenta je volfram, prema čijem sadržaju je ustajala jalovina nekontrastna ruda, uglavnom je zastupljen hubneritom, koji određuje tehnološka svojstva tehnogenih sirovina. Volfram je neravnomjerno raspoređen po klasama veličina, a njegova glavna količina je koncentrirana u veličini -0,5 + 0,1 i -0,1 + 0,02 mm.
Dokazano je da je jedina učinkovita metoda obogaćivanja ustajale jalovine Dzhida VMK koja sadrži W gravitacija. Na temelju analize generaliziranih krivulja gravitacijske koncentracije ustajale jalovine koja sadrži W, utvrđeno je da je deponijska jalovina s minimalnim gubicima volframa obilježje obogaćivanja tehnogenih sirovina s veličinom čestica od -0,1 + 0 mm. Utvrđeni su novi obrasci procesa separacije koji određuju tehnološke parametre gravitacijskog obogaćivanja ustajale jalovine Dzhida VMK finoće +0,1 mm.
Dokazano je da su među gravitacijskim uređajima koji se koriste u rudarskoj industriji za obogaćivanje ruda koje sadrže W, pužni separator i KNELSON centrifugalni koncentrator prikladni za maksimalno izvlačenje volframa iz tehnogenih sirovina Dzhida VMK u grubi W- koncentrati. Učinkovitost primjene KNELSON koncentratora potvrđena je i za dodatnu ekstrakciju volframa iz jalovine primarnog obogaćivanja tehnogenih sirovina koje sadrže W, veličine čestica 0,1 mm.
3. Optimizirana tehnološka shema za ekstrakciju volframa iz ustajale jalovine obogaćivanja rude Dzhida VMK omogućila je dobivanje kondicioniranog W-koncentrata, rješavanje problema iscrpljivanja mineralnih resursa Dzhida VMK i smanjenje negativnog utjecaja proizvodne aktivnosti poduzeća na okoliš.
Bitne značajke razvijene tehnologije za vađenje volframa iz ustajale jalovine Dzhida VMK su:
Uska klasifikacija prema veličini hrane za operacije primarne prerade;
Poželjna upotreba gravitacijske opreme.
Tijekom poluindustrijskog ispitivanja razvijene tehnologije vađenja volframa iz ustajale jalovine Dzhida VMK, dobiven je kondicionirani W-koncentrat s udjelom WO3 od 62,7% uz ekstrakciju od 49,9%. Razdoblje povrata za postrojenje za obogaćivanje za preradu ustajale jalovine Dzhida VMK za vađenje volframa bilo je 0,55 godina.
Bibliografija Disertacija o znanostima o Zemlji, kandidat tehničkih znanosti, Artemova, Olesya Stanislavovna, Irkutsk
1. Tehničko-ekonomska procjena tehnogenih naslaga obojenih metala: Pregled / V.V. Olenin, L.B. Eršov, I.V. Beljakova. M., 1990. - 64 str.
2. Rudarske znanosti. Razvoj i očuvanje unutrašnjosti Zemlje / RAS, AGN, RANS, MIA; Ed. K.N. Trubetskoy. M.: Izdavačka kuća Akademije rudarskih znanosti, 1997. -478 str.
3. Novikov A.A., Sazonov G.T. Stanje i izgledi za razvoj rudne i sirovinske baze obojene metalurgije Ruske Federacije, Rudarski časopis 2000. - br. 8, str. 92-95.
4. Karelov S.V., Vyvarets A.D., Distergeft JI.B., Mamyachenkov S.V., Khilai V.V., Naboychenko E.S. Procjena ekološke i ekonomske učinkovitosti prerade sekundarnih sirovina i industrijskog otpada, Izvestiya VUZov, Rudarski časopis 2002 - br. 4, str. 94-104.
5. Mineralni resursi Rusije. Ekonomija i menadžment Modularne koncentracijske tvornice, Posebno izdanje, rujan 2003. - HTJI TOMS ISTU.
6. Beresnevich P.V. i dr. Zaštita okoliša tijekom rada jalovine. M.: Nedra, 1993. - 127 str.
7. Dudkin O.B., Polyakov K.I. Problem tehnogenih ležišta, Obogaćivanje rude, 1999. - br. 11, S. 24-27.
8. Deryagin A.A., Kotova V.M., Nikolsky A.JI. Procjena mogućnosti uključivanja u eksploataciju umjetnih ležišta, Rudarsko istraživanje i korištenje podzemlja 2001 - br. 1, str. 15-19.
9. Chuyanov G.G. Jalovina postrojenja za obogaćivanje, Izvestia VUZ, Rudarski časopis 2001 - br. 4-5, str. 190-195.
10. Voronin D.V., Gavelya E.A., Karpov S.V. Proučavanje i obrada tehnogenih naslaga, Obogaćivanje ruda - 2000. br. 5, S. 16-20.
11. Smoldyrev A.E. Mogućnosti rudarske jalovine, Rudarski časopis - 2002, br. 7, str. 54-56.
12. Kvitka V.V., Kumakova L.B., Yakovleva E.P. Prerada ustajale jalovine prerađivačkih postrojenja u Istočnom Kazahstanu, Mining Journal - 2001 - br. 9, str. 57-61.
13. Khasanova G.G. Katastarska procjena tehnogeno-mineralnih objekata Srednjeg Urala Zbornik radova visokih učilišta, Rudarski časopis - 2003 - br. 4, S. 130136.
14. Tumanova E.S., Tumanov P.P. Mineralne sirovine. Tehnogene sirovine // Handbook. M.: CJSC "Geoinformmark", 1998. - 44 str.
15. Popov V.V. Ruska mineralna baza. Stanje i problemi, Rudarski časopis 1995 - br. 11, str. 31-34.
16. Uzdebaeva L.K. Ustajala jalovina - dodatni izvor metala, Obojeni metali 1999. - br. 4, str. 30-32.
17. Fishman M.A., Sobolev D.S. Praksa obogaćivanja ruda obojenih i rijetkih metala, vol. 1-2. -M.: Metallurgizdat, 1957 1960.
18. Fishman M.A., Sobolev D.S. Praksa obogaćivanja ruda obojenih i rijetkih metala, vol. 3-4. Moskva: Gosgortekhizdat, 1963.
19. Leonov S.B., Belkova O.N. Proučavanje minerala za perivost: Udžbenik. - M.: "Intermet Engineering", 2001. - 631s.
20. Trubetskoy K.N., Umanets V.N., Nikitin M.B. Klasifikacija tehnogenih ležišta, glavne kategorije i pojmovi, Rudarski časopis - 1990. - br. 1, str. 6-9.
21. Upute za primjenu Klasifikacije rezervi na ležišta volframovih ruda. M., 1984. - 40 str.
22. Betekhtin A.G., Golikov A.S., Dybkov V.F. i dr. Tok ležišta minerala Izd. 3. revizija i dodaj./Pod. Ed. P.M. Tatarinov i A.G. Betekhtina-M.: Nedra, 1964.
23. Khabirov V.V., Vorobyov A.E. Teorijske osnove za razvoj rudarske i prerađivačke industrije u Kirgistanu / Ed. akad. N.P. Laverov. M.: Nedra, 1993. - 316 str.
24. Izoitko V.M. Tehnološka mineralogija volframovih ruda. - L.: Nauka, 1989.-232 str.
25. Izoitko V.M., Boyarinov E.V., Shanaurin V.E. Značajke mineraloške i tehnološke procjene ruda u poduzećima industrije volfram-molibdena. M. TSNIITSVETMET i inform., 1985.
26. Mineloška enciklopedija / Ed. C. Freya: Per. s engleskog. - Ld: Nedra, 1985.-512 str.
27. Mineraloško proučavanje ruda obojenih i rijetkih metala / Ed. A.F. Lee. Ed. 2. M.: Nedra, 1967. - 260 str.
28. Ramder Paul Rudni minerali i njihovi izrasline. M.: IL, 1962.
29. Kogan B.I. rijetki metali. Status i izgledi. M.: Nauka, 1979. - 355 str.
30. Kochurova R.N. Geometrijske metode kvantitativne mineraloške analize stijena. - Ld: Lenjingradsko državno sveučilište, 1957.-67 str.
31. Metodološke osnove za proučavanje kemijskog sastava stijena, ruda i minerala. Ed. G.V. Ostroumova. M.: Nedra, 1979. - 400 str.
32. Metode mineraloških istraživanja: Priručnik / Ur. A.I. Ginzburg. M.: Nedra, 1985. - 480 str.
33. Kopchenova E.V. Mineraloška analiza koncentrata i rudnih koncentrata. Moskva: Nedra, 1979.
34. Određivanje mineralnih oblika volframa u primarnim rudama i rudama kore trošenja hidrotermalnih kvarcnih tvornica. Uputa NSAM br. 207-F-M .: VIMS, 1984.
35. Metodičke mineraloške studije. M.: Nauka, 1977. - 162 str. (AN SSSRIMGRE).
36. Panov E.G., Chukov A.V., Koltsov A.A. Ocjena kvalitete sirovina za reciklažu rudarskog i preradnog otpada. Istraživanje i zaštita mineralnih sirovina, 1990. br.4.
37. Materijali Republičkog analitičkog centra PGO "Buryatgeologia" o proučavanju materijalnog sastava ruda ležišta Kholtoson i Inkur i tehnogenih proizvoda tvornice Dzhida. Ulan-Ude, 1996.
38. Giredmetovo izvješće "Proučavanje sastava materijala i perivosti dvaju uzoraka ustajale jalovine Rudarsko-prerađivačke tvornice Dzhida". Autori Chistov L.B., Okhrimenko V.E. M., 1996.
39. Zelikman A.N., Nikitin JI.C. Volfram. M.: Metalurgija, 1978. - 272 str.
40. Fedotov K.V. Numeričko određivanje komponenti brzine strujanja fluida u centrifugalnim aparatima, Obrada rude - 1998, br. 4, S. 34-39.
41. Shokhin V.I. Metode gravitacijskog obogaćivanja. M.: Nedra, 1980. - 400 str.
42. Fomenko T.G. Gravitacijski procesi prerade minerala. M.: Nedra, 1966. - 330 str.
43. Voronov V.A. O jednom pristupu kontroli otkrivanja minerala u procesu mljevenja, Obogaćivanje rude, 2001. - br. 2, str. 43-46.
44. Barsky JI.A., Kozin V.Z. Analiza sustava u preradi minerala. M.: Nedra, 1978. - 486 str.
45. Tehnološka procjena mineralnih sirovina. Metode istraživanja: Priručnik / Ed. P.E. Ostapenko. M.: Nedra, 1990. - 264 str.
46. Sorokin M.M., Shepeta E.D., Kuvaeva I.V. Smanjenje gubitaka volframovog trioksida sulfidnim otpadnim proizvodima. Fizičko-tehnološki problemi razvoja minerala, 1988, br. 1, str. 59-60.
47. Izvješće Centra za istraživanje i razvoj "Ekstekhmet" "Procjena perljivosti sulfidnih proizvoda nalazišta Kholtoson". Autori Korolev N.I., Krylova N.S. i sur., M., 1996.
48. Dobromyslov Yu.P., Semenov M.I. i dr. Razvoj i implementacija tehnologije za integriranu preradu otpadnih proizvoda pogona za preradu kombinata Dzhida. Kompleksno korištenje mineralnih sirovina, Alma-Ata, 1987, br. 8. str. 24-27.
49. Nikiforov K.A., Zoltoev E.V. Dobivanje umjetnih volframovih sirovina iz niskokvalitetne pobneritne sredine prerađivačke tvornice. Kompleksno korištenje mineralnih sirovina, 1986. br. 6, str. 62-65.
50. Metodologija utvrđivanja spriječene štete u okolišu / Dr. Odbor Ruske Federacije za zaštitu okoliša. M., 1999. - 71 str.
51. Rubinshtein Yu.B., Volkov JI.A. Matematičke metode u preradi minerala. - M.: Nedra, 1987. 296 str.
52. Suvremene metode mineraloških istraživanja / Ed. E.V. Rožkov, v.1. M.: Nedra, 1969. - 280 str.
53. Suvremene metode mineraloških istraživanja / Ed. E.V. Rožkov, v.2. M.: Nedra, 1969. - 318 str.
54. Elektronska mikroskopija u mineralogiji / Ed. GR. Vijenac. Po. s engleskog. M.: Mir, 1979. - 541 str.
55. Feklicchev V.G. Dijagnostički spektri minerala. - M.: Nedra, 1977. - 228 str.
56. Cameron Yu.N. Rudarska mikroskopija. M.: Mir, 1966. - 234 str.
57. Volynsky I.S. Određivanje rudnih minerala pod mikroskopom. - M.: Nedra, 1976.
58. Vyalsov JT.H. Optičke metode dijagnostike rudnih minerala. - M.: Nedra, 1976.-321 str.
59. Isaenko M.P., Borishanskaya S.S., Afanasiev E.L. Odrednica glavnih minerala ruda u reflektiranoj svjetlosti. Moskva: Nedra, 1978.
60. Zevin L.S., Zavyalova L.L. Kvantitativna radiografska fazna analiza. Moskva: Nedra, 1974.
61. Bolshakov A.Yu., Komlev V.N. Smjernice za procjenu koncentracije ruda nuklearno-fizikalnim metodama. Apatiti: KF AN SSSR, 1974.-72 str.
62. Vasiliev E.K., Nakhmanson M.S. Kvalitativna rendgenska fazna analiza. - Novosibirsk: Nauka, SO, 1986. 199 str.
63. Filipova N.A. Fazna analiza ruda i proizvoda njihove prerade. - M.: Kemija, 1975.-280 str.
64. Blokhin M.A. Metode rendgenskih spektralnih studija. - M., Fizmatgiz, 1959. 386 str.
65. Tehnološka procjena mineralnih sirovina. Pilot postrojenja: Priručnik / Ed. P.E. Ostapenko. M.: Nedra, 1991. - 288 str.
66. Bogdanovich A.V. Načini poboljšanja gravitacijskog obogaćivanja sitnozrnih ruda i mulja, Obogaćivanje rude, 1995. - br. 1-2, S. 84-89.
67. Plotnikov R.I., Pshenichny G.A. Fluorescentna rendgenska radiometrijska analiza. - M., Atomizdat, 1973. - 264 str.
68. Mokrousov V. A., Lileev V. A. Radiometrijsko obogaćivanje neradioaktivnih ruda. M.: Nedra, 1978. - 191 str.
69. Mokrousov V.A. Proučavanje raspodjele veličine čestica i kontrasta minerala za procjenu mogućnosti obogaćivanja: Smjernice / SIMS. M.: 1978. - 24 str.
70. Barsky L.A., Danilchenko L.M. Obogaćivanje mineralnih kompleksa. -M.: Nedra, 1977.-240 str.
71. Albov M.N. Ispitivanje mineralnih naslaga. - M.: Nedra, 1975.-232 str.
72. Mitrofanov S.I. Proučavanje minerala za pranje. - M.: Metallurgizdat, 1954.-495 str.
73. Mitrofanov S.I. Proučavanje minerala za pranje. - M.: Gosgortekhizdat, 1962. - 580 str.
74. Uralska državna rudarsko-geološka akademija, 2002., str. 6067.
75. Karmazin V.V., Karmazin V.I. Magnetske i električne metode obogaćivanja. M.: Nedra, 1988. - 303 str.
76. Olofinsky N.F. Električne metode obogaćivanja. 4. izd., revidirano. i dodatni M.: Nedra, 1977. - 519 str.
77. Mesenyashin A.I. Električno odvajanje u jakim poljima. Moskva: Nedra, 1978.
78. Polkin S.I. Obogaćivanje ruda i naslaga rijetkih metala. M.: Nedra, 1967.-616 str.
79. Priručnik o obogaćivanju ruda. Posebni i pomoćni procesi, ispitivanja perivosti, upravljanje i automatizacija / Ed. O.S. Bogdanov. Moskva: Nedra, 1983. - 386 str.
80. Priručnik o obogaćivanju ruda. Osnovni procesi./Ur. O.S. Bogdanov. M.: Nedra, 1983. - 381 str.
81. Priručnik o obogaćivanju ruda. U 3 sveska. Ch. izd. O.S. Bogdanov. T.Z. tvornice za obogaćivanje. Rep. Ed. Yu.F. Nenarokomov. M.: Nedra, 1974.- 408 str.
82. Rudarski časopis 1998. - broj 5, 97 str.
83. Potemkin A.A. Tvrtka KNELSON CONSENTRATOR svjetski je lider u proizvodnji gravitacijskih centrifugalnih separatora, Rudarski časopis - 1998., br. 5, str. 77-84.
84. Bogdanovich A.V. Odvajanje u centrifugalnom polju čestica suspendiranih u tekućini u pseudostatskim uvjetima, Obogaćivanje ruda - 1992. br. 3-4, S. 14-17.
85. Stanoilovich R. Novi pravci u razvoju gravitacijske koncentracije, Obogaćivanje ruda 1992 - br. 1, S. 3-5.
86. Podkosov L.G. O teoriji gravitacijskog obogaćivanja, Obojeni metali - 1986 - №7, str. 43-46.
87. Bogdanovich A.V. Intenziviranje procesa gravitacijskog obogaćivanja u centrifugalnim poljima, Obogaćivanje ruda 1999 - br. 1-2, S. 33-36.
88. Polkin S.I., Obogaćivanje ruda i naslaga rijetkih i plemenitih metala. 2. izd., prerađeno. i dodatni - M.: Nedra, 1987. - 429 str.
89. Polkin S.I., Laptev S.F. Obogaćivanje kositrenih ruda i naslaga. - M.: Nedra, 1974.-477 str.
90. Abramov A.A. Tehnologija obogaćivanja ruda obojenih metala. M.: Nedra, 1983.-359 str.
91. Karpenko N.V. Ispitivanje i kontrola kvalitete proizvoda za obogaćivanje. - M.: Nedra, 1987.-214 str.
92. Andreeva G.S., Goryushkin S.A. prerada i obogaćivanje minerala aluvijalnih naslaga. M.: Nedra, 1992. - 410 str.
93. Enbaev I.A. Modularna centrifugalna postrojenja za koncentraciju plemenitih i plemenitih metala iz aluvijalnih i tehnogenih ležišta, Obrada ruda 1997. - br. 3, str.6-8.
94. Chanturia V.A. Tehnologija prerade ruda i naslaga plemenitih metala, Obojeni metali, 1996 - br. 2, S. 7-9.
95. Kalinichenko V.E. "Postrojenje za dodatno vađenje metala iz jalovine postojeće proizvodnje, Obojeni metali, 1999. - br. 4, str. 33-35.
96. Berger G.S., Orel M.A., Popov E.L. Poluindustrijsko ispitivanje perljivosti ruda. M.: Nedra, 1984. - 230 str.
97. GOST 213-73 "Tehnički zahtjevi (sastav,%) za volframove koncentrate dobivene iz ruda koje sadrže volfram"
99. Fedotov K.V., Artemova O.S., Polinskina I.V. Procjena mogućnosti prerade ustajale jalovine Dzhida VMK, Obrada rude: Sub. znanstvenim djela. Irkutsk: Izd-vo ISTU, 2002. - 204 str., S. 74-78.
100. Fedotov K.V., Artemova O.S. Problemi prerade ustajalih proizvoda koji sadrže volfram Suvremene metode prerade mineralnih sirovina: Zbornik radova. Irkutsk: Irk. Država. Oni. Sveučilište, 2004. (monografija). 86 str.
101. Artemova O.S., Fedotov K.V., Belkova O.N. Izgledi za korištenje tehnogenog ležišta Dzhida VMK. Sveruska znanstveno-praktična konferencija "Nove tehnologije u metalurgiji, hemiji, obogaćivanju i ekologiji", Sankt Peterburg, 2004.
Pošaljite svoj dobar rad u bazu znanja je jednostavno. Upotrijebite obrazac u nastavku
Studenti, diplomski studenti, mladi znanstvenici koji koriste bazu znanja u svom studiju i radu bit će vam jako zahvalni.
Objavljeno na http:// www. sve najbolje. en/
Rudarsko-metalurški kombinat Navoi
Državni rudarski institut Navoi
Kemijsko-metalurški fakultet
Zavod za metalurgiju
Objašnjenje
za završni kvalifikacijski rad
na temu: "Izbor, opravdanje i proračun tehnologije prerade volfram-molibdenske rude"
Diplomirani: K. Saifiddinov
Navoi-2014
- Uvod
- 1. Opći podaci o načinima obogaćivanja volframovih ruda
- 2. Obogaćivanje molibden-volframovih ruda
- 2. Tehnološki odjeljak
- 2.1 Proračun sheme drobljenja s izborom opreme
- 2.2 Proračun sheme mljevenja
- 2.3 Izbor i proračun SAG mlinova
- Popis korištene literature
Uvod
Minerali su temelj nacionalnog gospodarstva, a ne postoji niti jedna industrija u kojoj se ne koriste minerali ili proizvodi njihove prerade.
Značajne mineralne rezerve mnogih ležišta Uzbekistana omogućuju izgradnju velikih visokomehaniziranih rudarskih i prerađivačkih i metalurških poduzeća koja vade i prerađuju stotine milijuna tona minerala s visokim tehničkim i ekonomskim pokazateljima.
Rudarska industrija se bavi čvrstim mineralima iz kojih je, uz današnju razinu tehnologije, preporučljivo vaditi metale ili druge mineralne tvari. Glavni uvjeti u razvoju mineralnih nalazišta su povećanje njihovog izvlačenja iz crijeva i njihova integrirana uporaba. To je zbog:
- značajni troškovi materijala i rada u istraživanju i industrijskom razvoju novih ležišta;
- rastuće potrebe različitih sektora nacionalnog gospodarstva za gotovo svim mineralnim komponentama koje čine rudu;
- potrebu za stvaranjem tehnologije bez otpada i na taj način spriječiti onečišćenje okoliša proizvodnim otpadom.
Iz tih razloga, mogućnost industrijske upotrebe ležišta određena je ne samo vrijednošću i sadržajem minerala, njegovim rezervama, geografskim položajem, uvjetima rudarstva i transporta, drugim gospodarskim i političkim čimbenicima, već i dostupnošću učinkovite tehnologija prerade iskopanih ruda.
1. Opći podaci o načinima obogaćivanja volframovih ruda
Volframove rude se u pravilu obogaćuju u dvije faze - primarnom gravitacijskom koncentracijom i doradom sirovih koncentrata različitim metodama, što se objašnjava niskim sadržajem volframa u prerađenim rudama (0,2 - 0,8% WO3) i visokim zahtjevima kvalitete kondicioniranih koncentrati (55 - 65% WO3), ukupno obogaćenje je oko 300 - 600.
Primarne rude i placeri volframita (hubnerit i ferberit) obično sadrže niz drugih teških minerala, stoga tijekom primarnog gravitacijskog obogaćivanja ruda imaju tendenciju izolacije skupnih koncentrata koji mogu sadržavati od 5 do 20% WO3, kao i kasiterit, tantalit-kolumbit, magnetit, sulfidi i dr. Prilikom dorade zbirnih koncentrata potrebno je dobiti kondicionirane monomineralne koncentrate, za koje se može flotacija ili flotacija sulfida, magnetsko odvajanje magnetita u slabom magnetskom polju, a u jačem - volframita. biti korišteni. Moguće je koristiti električno odvajanje, gravitacijsko obogaćivanje na stolovima, flotaciju minerala otpadnih stijena i druge procese za odvajanje minerala, tako da gotovi koncentrati ispunjavaju zahtjeve GOST-a i tehničkih specifikacija ne samo u pogledu sadržaja baze metala, ali i po sadržaju štetnih nečistoća.
Uzimajući u obzir visoku gustoću minerala volframa (6 - 7,5 g/cm 3), metode gravitacijskog obogaćivanja mogu se uspješno koristiti tijekom obogaćivanja na strojevima za šivanje, koncentracijskim stolovima, bravama, mlaznim i vijčanim separatorima itd. Uz fino raspršivanje vrijednih minerala , flotacija ili kombinacija gravitacijskih procesa s flotacijom. Uzimajući u obzir mogućnost pojave mulja volframita tijekom gravitacijskog obogaćivanja, flotacija se koristi kao pomoćni proces čak i pri obogaćivanju grubo raspršenih volframitnih ruda za potpunije izvlačenje volframa iz mulja.
Ako se u rudi nalaze veliki komadi volframa bogati volframom ili veliki komadi otpadne stijene, razvrstavanje rude veličine čestica 150 + 50 mm na tračnim transporterima može se koristiti za odvajanje bogatog grudastog koncentrata ili komada stijene koji osiromašuju ruda dostavljena za obogaćivanje.
Pri obogaćivanju scheelitnih ruda također se koristi gravitacija, ali najčešće kombinacija gravitacijskih metoda s flotacijom i flotacijskom gravitacijom ili samo flotacijom.
Prilikom sortiranja scheelitnih ruda koriste se luminiscentne instalacije. Šelit, kada je zračen ultraljubičastim zrakama, svijetli jarkim plavim svjetlom, što vam omogućuje da odvojite komade scheelite ili komadiće otpadne stijene.
Scheelite je lako plutajući mineral karakteriziran visokim kapacitetom mulja. Ekstrakcija scheelita značajno se povećava s obogaćivanjem flotacijom u usporedbi s gravitacijom, stoga se u obogaćivanju scheelitnih ruda u zemljama ZND-a flotacija sada koristi u svim tvornicama.
Tijekom flotacije volframovih ruda javlja se niz teških tehnoloških problema koji zahtijevaju pravo rješenje ovisno o materijalnom sastavu i povezanosti pojedinih minerala. U procesu flotacije volframita, hübnerita i ferberita teško je odvojiti od njih okside i hidrokside željeza, turmalina i drugih minerala koji ujednačavaju njihova flotacijska svojstva s mineralima volframa.
Flotaciju scheelite iz ruda s mineralima koji sadrže kalcij (kalcit, fluorit, apatit i dr.) provode sakupljači anionskih masnih kiselina, koji osiguravaju njihovu dobru floatabilnost s kalcijevim kationima scheelite i drugim mineralima koji sadrže kalcij. Odvajanje scheelita od minerala koji sadrže kalcij moguće je samo uz korištenje takvih regulatora kao što su tekuće staklo, natrijev silikofluorid, soda itd.
2. Obogaćivanje molibden-volframovih ruda
Na Tyrnyauzskaya U tvornici se obogaćuju molibdensko-volframove rude ležišta Tyrnyauz, koje su po materijalnom sastavu složene ne samo vrijednih minerala s vrlo finom diseminacijom, već i pripadajućih minerala lanca. Rudni minerali - šeelit (desetine postotka), molibdenit (stotine postotka), powellit, djelomično ferimolibdit, halkopirit, bizmutin, pirotin, pirit, arsenopirit. Nemetalni minerali - skarne (50-70%), rogovi (21-48%), granit (1-12%), mramor (0,4-2%), kvarc, fluorit, kalcit, apatit (3-10%) i tako dalje.
U gornjem dijelu ležišta 50–60% molibdena predstavljaju powellit i ferimolibdit, au donjem dijelu njihov sadržaj opada na 10–20%. Šelit sadrži molibden kao izomorfnu nečistoću. Dio molibdenita oksidiranog s površine prekriven je filmom powellita. Dio molibdena raste vrlo fino s molibdošeelitom.
Više od 50% oksidiranog molibdena povezano je sa šeelitom u obliku inkluzija powellita, produkta razgradnje čvrste otopine Ca(W, Mo)O 4 . Slični oblici volframa i molibdena mogu se izolirati samo u zajednički koncentrat uz naknadno odvajanje hidrometalurškom metodom.
Od 1978. godine u tvornici je u potpunosti rekonstruirana shema pripreme rude. Ranije se ruda nakon grubog drobljenja u rudniku do tvornice prevozila kolicima žičarom. U odjelu za drobljenje tvornice ruda je usitnjena do - 12 mm, istovarena u bunkere i potom usitnjena u jednom stupnju u kuglastim mlinovima koji rade u zatvorenom ciklusu s dvostrukim spiralnim klasifikatorima, do 60% klase - 0,074 mm .
Novu tehnologiju pripreme rude zajednički su razvili Institut Mehanobr i tvornica i puštena u rad u kolovozu 1978. godine.
Shema pripreme rude predviđa grubo drobljenje početne rude do -350 mm, prosijavanje prema klasi 74 mm, odvojeno skladištenje svake klase u bunkerima radi preciznije kontrole isporuke velikih i malih klasa rude u mlin za samo mljevenje.
Samomljevenje krupno drobljene rude (-350 mm) vrši se u mlinovima tipa "Cascade" promjera 7 m (MMS-70X X23) uz dodatno mljevenje krupnozrne frakcije do 62% klase - 0,074 mm u mlinovima MSHR-3600X5000, koji rade u zatvorenom ciklusu sa jednospiralnim klasifikatorima 1KSN-3 i postavljeni u novogradnji na padini planine na oko 2000 m nadmorske visine između rudnika i pogonske tvornice.
Dobava gotovog proizvoda od samobrusnog tijela do flotacije provodi se hidrauličkim transportom. Hidrotransportna trasa je jedinstvena inženjerska građevina koja osigurava transport gnojnice na visinskoj razlici većoj od 600 m. Sastoji se od dva cjevovoda promjera 630 mm, dužine 1750 m, opremljenih bunarima za umirivanje promjera 1620 mm i visine 5 m (126 bušotina za svaki cjevovod).
Korištenje hidrauličkog transportnog sustava omogućilo je likvidaciju radionice za teretnu žičaru, zgrade srednjeg i finog drobljenja te mlinova MShR-3200X2100 u pogonu za preradu. U glavnoj zgradi tvornice izgrađena su i puštena u rad dva glavna odjela za flotaciju, novi odjeli za završnu obradu scheelita i molibdena, talionica tekućeg stakla, te optočni vodoopskrbni sustavi. Fronta zgušnjavanja sirovih flotacijskih koncentrata i srednjaka značajno je proširena ugradnjom zgušnjivača promjera 30 m, što omogućuje smanjenje gubitaka kod zgušnjavanja drenaža.
Novootvoreni objekti opremljeni su suvremenim sustavima upravljanja procesima i lokalnim sustavima automatizacije. Dakle, u samobrusnoj zgradi automatizirani upravljački sustav radi u načinu izravnog upravljanja na temelju računala M-6000. U glavnoj zgradi uveden je sustav za centraliziranu kontrolu materijalnog sastava pulpe pomoću rendgenskih spektralnih analizatora KRF-17 i KRF-18 u kombinaciji s računalom M-6000. Ovladan je automatizirani sustav uzorkovanja i dostave uzoraka (pneumatskom poštom) u ekspresni laboratorij, upravljan računalnim kompleksom KM-2101 i izdavanjem analiza na teletip.
Jedna od najtežih faza obrade - fino ugađanje sirovih scheelitnih koncentrata prema metodi N. S. Petrova - opremljena je automatskim sustavom upravljanja i upravljanja koji može raditi u načinu rada "savjetnik" operateru flotacije ili u način izravnog upravljanja procesom, podešavanje brzine protoka supresora (tekuće staklo), razine pulpe u operacijama čišćenja i drugih parametara procesa.
Ciklus flotacije sulfidnih minerala opremljen je automatskim sustavima upravljanja i doziranja za kolektor (butil ksantat) i supresor (natrijev sulfid) u ciklusu flotacije bakar-molibden. Sustavi rade koristeći ionsko selektivne elektrode kao senzore.
U vezi s povećanjem obima proizvodnje, tvornica je prešla na preradu novih sorti ruda koje se odlikuju nižim sadržajem nekih metala i većim stupnjem njihove oksidacije. To je zahtijevalo poboljšanje reagensnog načina flotacije sulfid-oksidiranih ruda. Konkretno, u ciklusu sulfida korišteno je progresivno tehnološko rješenje - kombinacija dvije aktivne i selektivne vrste koncentrata pjene. Kao aktivno sredstvo za pjenjenje koriste se reagensi koji sadrže terpenske alkohole, a kao selektivno sredstvo razvijen je novi LS reagens za obogaćivanje višekomponentnih ruda, a prvenstveno Tyrnyauzovih.
U ciklusu flotacije oksidiranih minerala sakupljačima masnih kiselina koriste se intenzivirajući aditivi modifikatorskog reagensa na bazi niskomolekularnih karboksilnih kiselina. Radi poboljšanja flotacijskih svojstava pulpe cirkulirajuće srednje smjese uvedena je regulacija njihovog ionskog sastava. Metode kemijskog rafiniranja koncentrata našle su širu primjenu.
Iz samomljevenog mlina ruda ide na prosijavanje. Klasa +4 mm ponovno se melje u kugličnom mlinu. Izlaz mlina i proizvod ispod sita (-4 mm) klasificiraju se I i II.
U kuglični mlin se ubacuje 690 g/t sode i 5 g/t transformatorskog ulja. Odvod klasifikatora ulazi u glavnu flotaciju molibdena, gdje se unosi 0,5 g/t ksantata i 46 g/t terpineola. Nakon čišćenja flotacijom I i II, molibdenski koncentrat (1,2-1,5% Mo) se podvrgava pari s tekućim staklom (12 g/t) na 50-70°C, čišćenju flotacijom III i ponovnom mljevenju na 95-98% klase --0,074 mm s opskrbom 3 g/t natrijevog cijanida i 6 g/t tekućeg stakla.
Gotov koncentrat molibdena sadrži oko 48% Mo, 0,1% Cu i 0,5% WO 3 s iskorištenjem Mo od 50%. Jalovina kontrolnih flotacija III i IV operacije čišćenja se zgušnjava i šalje u bakreno-molibdensku flotaciju uz dovod 0,2 g/t ksantata i 2 g/t kerozina. Dvostruko očišćeni bakreno-molibdenski koncentrat nakon parenja s natrijevim sulfidom ulazi u selektivnu flotaciju, pri čemu se oslobađa koncentrat bakra koji sadrži 8-10% Cu (s ekstrakcijom od oko 45%), 0,2% My 0,8% Bi.
Repovi kontrolne flotacije molibdena, koji sadrže do 0 2% WO 3 , šalju se na flotaciju scheelite, koja se provodi po vrlo razgranatoj i složenoj shemi. Nakon miješanja s tekućim staklom (350 g/t), provodi se glavna flotacija scheelite s natrijevim oleatom (40 g/t). Nakon prve flotacije čišćenja i zgušnjavanja do 60% čvrstog scheelita koncentrat se pari s tekućim staklom (1600 g/t) na 80--90 °C. Nadalje, koncentrat se čisti još dva puta i ponovno ide na paru na 90--95°C s tekućim staklom (280 g/t) i ponovno tri puta.
2. Tehnološki odjeljak
2.1 Proračun sheme drobljenja s izborom opreme
Koncentracija koja se projektira namijenjena je preradi volframovih ruda koje sadrže molibden.
Ruda srednje veličine (f=12±14 jedinica na ljestvici profesora Protodjakonova) karakterizira gustoća c = 2,7 t/m 3 , ulazi u tvornicu sa sadržajem vlage od 1,5%. Maksimalni komad d=1000 mm.
Po proizvodnosti pogon za preradu spada u kategoriju srednje produktivnosti (tablica 4/2/), prema međunarodnoj klasifikaciji - u skupinu C.
Do tvorničke rude D max. =1000 mm se isporučuje iz površinskog kopa.
1. Odredite produktivnost radionice za grubo drobljenje. Izvedbu izračunavamo prema Razumovu K.A. 1, str. 39-40. Projekt je usvojio isporuku rude 259 dana u godini, u 2 smjene po 7 sati, 5 dana u tjednu.
Faktor tvrdoće rude /2/
gdje je: Q c. ostalo - dnevna produktivnost radnje za drobljenje, t/dan
Koeficijent koji uzima u obzir neujednačena svojstva sirovina /2/
gdje je: Q h..c. dr - satna produktivnost drobilice, t/h
k n - koeficijent koji uzima u obzir neujednačena svojstva sirovina,
n dana - procijenjeni broj radnih dana u godini,
n cm - broj smjena po danu,
t cm - trajanje smjene,
k" - faktor obračuna tvrdoće rude,
Izračun godišnjeg fonda radnog vremena:
C \u003d (n dana n cm t cm) \u003d 259 2 5 \u003d 2590 (3)
Korištenje tijekom vremena:
k u \u003d 2590/8760 \u003d 0,29 CU = 29%
2. Proračun sheme drobljenja. Izračun provodimo prema stranicama 68-78 2.
Prema zadatku, vlažnost početne rude iznosi 1,5%, t.j. e.
Postupak izračuna:
1. Odredite stupanj drobljenja
2. Prihvaćamo stupanj drobljenja.
3. Odredite maksimalnu veličinu proizvoda nakon drobljenja:
4. Odredimo širinu utora za istovar drobilice, uzimajući, prema tipičnim karakteristikama, Z - grubost zdrobljenog proizvoda u odnosu na veličinu utora za istovar.
5. Provjerite usklađenost odabrane sheme drobljenja s proizvedenom opremom.
Zahtjevi koje drobilice moraju zadovoljiti prikazani su u tablici 1.
stol 1
Prema širini usisnog otvora i rasponu podešavanja ispusnog razmaka, prikladne su drobilice marke ShchDP 12X15.
Izračunajmo učinak drobilice prema formuli (109/2/):
Q mačka. \u003d m 3 / h
Q frakcija. = Q kat. · sa n · k f · k cr. k ow. k c, m 3 / h (7)
gdje je c n - nasipna gustoća rude = 1,6 t / m 3,
Q mačka. - učinak drobilice za putovnice, m 3 / h
k f . , k ow. , k kr, k c - korekcijski faktori za tvrdoću (zdrobivost), nasipnu gustoću, finoću i sadržaj vlage u rudi.
Vrijednost koeficijenata nalazi se prema tablici k f =1,6; k cr = 1,05; k ow. =1%;
Q mačka. \u003d S pr. / S n Q n \u003d 125 / 155 310? 250 m3/h
Pronađimo stvarne performanse drobilice za uvjete definirane projektom:
Q frakcija. = 250 1,6 1,00 1,05 1 1 = 420 t/h
Na temelju rezultata izračuna određujemo broj drobilica:
Primamo za ugradnju ShchDP 12 x 15 - 1 kom.
2.2 Proračun sheme mljevenja
Shema mljevenja odabrana u projektu je vrsta VA Razumov K.A. stranica 86.
Postupak izračuna:
1. Odrediti satnu produktivnost radnje za mljevenje , što je zapravo satna produktivnost cijele tvornice, budući da je mljevenica glavna zgrada za pripremu rude:
gdje je 343 broj radnih dana u godini
24 - kontinuirani radni tjedan 3 smjene po 8 sati (3h8=24 sata)
K in - koeficijent iskorištenosti opreme
K n - koeficijent koji uzima u obzir neujednačena svojstva sirovina
Prihvaćamo: K in \u003d 0,9 K n \u003d 1,0
Skladište krupno usitnjene rude osigurava dvodnevnu zalihu rude:
V= 48 127,89 / 2,7 = 2398,22
Prihvaćamo početne podatke
Razmotrimo ukapljivanje u odvodnim i klasifikacijskim pijescima:
R 10 \u003d 3 R 11 \u003d 0,28
(R 13 preuzeto iz retka 2 na stranici 262 ovisno o veličini šljive)
u 1 -0,074 \u003d 10% - sadržaj klase - 0,074 mm u drobljenoj rudi
u 10 -0,074 \u003d 80% - sadržaj klase je 0,074 mm u klasifikacijskom odvodu.
Prihvaćamo optimalno cirkulacijsko opterećenje C opt = 200%.
Postupak izračuna:
Faze mljevenja I i II prikazane su dijagramom tipa BA str. 86 sl. 23.
Izračun sheme B svodi se na određivanje težine proizvoda 2 i 5 (prinosi proizvoda nalaze se općom formulom r n \u003d Q n: Q 1)
Q 7 \u003d Q 1 C opt \u003d 134,9 2 \u003d 269,8 t / h;
Q 4 \u003d Q 5 \u003d Q 3 + Q 7 \u003d 404,7 t / h;
g 4 \u003d g 5 \u003d 300%;
g 3 \u003d g 6 \u003d 100%
Izračun provodimo prema Razumov K.A. 1 str. 107-108.
1. Proračun sheme A
Q 8 \u003d Q 10; Q 11 \u003d Q 12;
Q 9 = Q 8 + Q 12 = 134,88 + 89,26 \u003d 224,14 t / h
g 1 \u003d 100%; g 8 \u003d g 10 \u003d 99,987%;
g 11 \u003d g 12 \u003d Q 12: Q 1 \u003d 89,26: 134,88 \u003d 66,2%;
g 9 = Q 9: Q 1 = 224,14: 134,88 \u003d 166,17%
Tehnološka shema obogaschenijarude molibdena i volframa.
Izračunnakvalitativno-kvantitativna shema.
Početni podaci za izračun kvalitativno-kvantitativnih shemas.
Ekstrakcija volframa u konačni koncentrat - e volfram 17 = 68%
Ekstrakcija volframa u kolektivnom koncentratu - e volfram 15 = 86%
Ekstrakcija volframa u koncentrat molibdena - e volfram 21 = 4%
Ekstrakcija molibdena u konačnom koncentratu - e Mo 21 = 77%
Iskorištavanje molibdena u jalovini flotacije volframa - e Mo 18 = 98%
Dobivanje molibdena u kontrolnom flotacijskom koncentratu - e Mo 19 =18%
Ekstrakcija molibdena u kolektivnom koncentratu - e Mo 15 \u003d 104%
Izlaz skupnog koncentrata - g 15 = 36%
Izlaz volframovog koncentrata - g 17 = 14%
Izlaz molibdenskog koncentrata - g 21 \u003d 15%
Izlaz koncentrata kontrolne flotacije - g 19 = 28%
Odredite prinos proizvoda obogaćivanja
G 18 = g 15 - G 17 =36-14=22%
G 22 = g 18 - G 21 =22-15=7%
G 14 = g 13 + g 19 + g 22 =100+28+7=135%
G 16 = g 14 - G 15 =135-36=99%
G 20 = g 16 - G 19 =99-28=71%
Odrediti masu proizvoda obogaćivanja
P 13 = 127,89 t/h
P 1 4 = P 13 xG 14 = 127,89x1,35=172,6 t/h
P 1 5 = P 13 xG 15 = 127,89h0,36=46,0 t/h
P 1 6 = P 13 xG 16 = 127,89h0,99=126,6t/h
P 1 7 = P 13 xG 17 = 127,89h0,14=17,9 t/h
P 1 8 = P 13 xG 18 = 127,89h0,22=28,1 t/h
P 1 9 = P 13 xG 19 = 127,89h0,28=35,8 t/h
P 20 = P 13 xG 20 = 127,89h0,71=90,8 t/h
P 21 = P 13 xG 21 = 127,89h0,15=19,1 t/h
P 22 = P 13 xG 22 = 127,89h0,07=8,9 t/h
Odredite ekstrakciju proizvoda obogaćivanja
Za volfram
e volfram 13 =100 %
e volfram 18 = e volfram 15 - e volfram 17 =86-68=28 %
e volfram 22 = e volfram 18 - e volfram 21 =28-14=14 %
e volfram 14 = e volfram 13 + e volfram 22 + e volfram 19 =100+14+10=124 %
e volfram 16 = e volfram 14 - e volfram 15 =124-86=38%
e volfram 20 = e volfram 13 - e volfram 17 + e volfram 21 =100 - 68+4=28%
e volfram 19 = e volfram 16 - e volfram 20 =38-28=10 %
za molibden
e Mo 13 =100%
e Mo 22 = e Mo 18 - e Mo 21 =98-77=11 %
e Mo 14 = e Mo 13 + e Mo 22 + e Mo 19 =100+11+18=129 %
e Mo 16 = e Mo 14 - e Mo 15 =129-94=35 %
e Mo 17 = e Mo 15 - e Mo 18 =104-98=6%
e Mo 20 = e Mo 13 - e Mo 17 + e Mo 21 =100 - 6+77=17%
e Mo 19 = e Mo 16 - e Mo 20 =35-17=18%
Odredite količinu metala u proizvodu Oh obogaćivanje
Za volfram
14 \u003d 124 x0,5 / 135 \u003d 0,46%
15 \u003d 86x0,5 / 36 \u003d 1,19%
16 \u003d 38 x0,5 / 99 \u003d 0,19%
17 \u003d 68 x0,5 / 14 \u003d 2,43%
18 \u003d 28 x 0,5 / 22 \u003d 0,64%
19 \u003d 10 x0,5 / 28 \u003d 0,18%
20 \u003d 28 x 0,5 / 71 \u003d 0,2%
21 \u003d 14 x0,5 / 15 \u003d 0,46%
22 \u003d 14 x0,5 / 7 \u003d 1%
Za molibden
14 \u003d 129 x 0,04 / 135 \u003d 0,04%
15 \u003d 94x0,04 / 36 \u003d 0,1%
16 \u003d 35 x0,04 / 99 \u003d 0,01%
17 \u003d 6 x0,04 / 14 \u003d 0,017%
18 \u003d 98 x 0,04 / 22 \u003d 0,18%
19 \u003d 18 x0,04 / 28 \u003d 0,025%
20 \u003d 17 x0,04 / 71 \u003d 0,009%
21 \u003d 77 x0,04 / 15 \u003d 0,2%
22 \u003d 11 x0,04 / 7 \u003d 0,06%
Tablica 3. Tablica kvalitativno-kvantitativne sheme obogaćivanja
broj operacije prod. |
|
Q, t/h |
, % |
bakar , % |
bakar , % |
cinkov , % |
cinkov , % |
|
ja |
I. faza mljevenja |
|||||||
stiže |
||||||||
zdrobljena ruda |
||||||||
izlazeći |
||||||||
zdrobljena ruda |
||||||||
II |
Klasifikacija |
|||||||
stiže |
||||||||
Izmelbchennsth proizvod jaUmjetnost. mljevenje |
||||||||
Izmelbchennsth proizvod II sv .mljevenje |
||||||||
izlazeći |
||||||||
odvod |
||||||||
pijesak |
||||||||
III |
Mljevenje I ja pozornica |
|||||||
stiže |
||||||||
Klasifikacija pijeska |
||||||||
izlazeći |
||||||||
zgnječenosth proizvod |
||||||||
IV |
Kolektivno Wo 3 -Mo flotacija |
|||||||
stiže |
||||||||
Klasifikacija odvoda |
||||||||
|
||||||||
RepoviMo flotacijai |
||||||||
izlazeći |
||||||||
koncentrat |
||||||||
reps |
||||||||
V |
Kontrolirajte flotaciju |
|||||||
stiže |
||||||||
Repkolektivna flotacija |
||||||||
izlazeći |
||||||||
koncentrat |
||||||||
reps |
||||||||
VI |
Volfram flotacija |
|||||||
stiže |
||||||||
Koncentratkolektivna flotacija |
||||||||
izlazeći |
||||||||
koncentrat |
||||||||
reps |
||||||||
Mo flotacija |
||||||||
stiže |
||||||||
Reps Wo 3 flotacija |
||||||||
izlazeći |
||||||||
koncentrat |
||||||||
reps |
Proračun sheme voda-mulj .
Svrha proračuna sheme voda-mulj je: osigurati optimalne omjere W:T u radu sheme; određivanje količine vode dodane u operacijama ili, obrnuto, oslobođene iz proizvoda tijekom operacija dehidracije; određivanje odnosa W:T u produktima sheme; utvrđivanje ukupne potražnje za vodom i specifične potrošnje vode po toni prerađene rude.
Za postizanje visokih tehnoloških pokazatelja prerade rude, svaka operacija tehnološke sheme mora se izvesti na optimalnim vrijednostima L:T omjera. Ove vrijednosti su utvrđene na temelju ispitivanja perljivosti rude i radnih praksi pogona za preradu.
Relativno niska specifična potrošnja vode po toni prerađene rude objašnjava se postojanjem unutartvorničke cirkulacije vode u postrojenju koje se projektira, budući da se preljevi zgušnjivača dovode u ciklus mljevenja-klasifikacije. Potrošnja vode za ispiranje podova, uređaja za pranje i druge namjene iznosi 10-15% ukupne potrošnje.
Tablica 3. Tablica kvalitativno-kvantitativne sheme obogaćivanja.
ope br.voki-toki prod. |
Naziv operacija i proizvoda |
Q, t/h |
, % |
R |
W |
|
ja |
I. faza mljevenja |
|||||
stiže |
||||||
zdrobljena ruda |
0 , 0 25 |
|||||
izlazeći |
||||||
zdrobljena ruda |
||||||
II |
Klasifikacija |
|||||
stiže |
||||||
Izmelbchennsth proizvod jaUmjetnost. mljevenje |
||||||
Izmelbchennsth proizvod II sv .mljevenje |
||||||
izlazeći |
||||||
odvod |
||||||
pijesak |
||||||
III |
Mljevenje I ja pozornica |
|||||
stiže |
||||||
Klasifikacija pijeska |
||||||
izlazeći |
||||||
zgnječenosth proizvod |
||||||
IV |
Kolektivno Wo 3 -Mo flotacija |
|||||
stiže |
||||||
Klasifikacija odvoda |
||||||
Kontrolni flotacijski koncentrat |
||||||
Mo repovi flotacijai |
||||||
izlazeći |
||||||
koncentrat |
||||||
Reps |
||||||
V |
Kontrolirajte flotaciju |
|||||
stiže |
||||||
Repkolektivna flotacija |
||||||
izlazeći |
||||||
koncentrat |
||||||
Reps |
||||||
VI |
Volfram flotacija |
|||||
Ulazi |
||||||
Koncentratkolektivna flotacija |
||||||
izlazeći |
||||||
Koncentrat |
||||||
Reps |
||||||
Mo flotacija |
||||||
Ulazi |
||||||
Reps volframflotacija |
||||||
izlazeći |
||||||
koncentrat |
||||||
reps |
Izbor i proračun drobilice.
Izbor vrste i veličine drobilice ovisi o fizičkim svojstvima rude, potrebnom kapacitetu drobilice, veličini drobljenog proizvoda i tvrdoći rude.
Volframo-molibdenska ruda po jačini je ruda srednje jakosti.
Maksimalna veličina komada rude koja ulazi u operaciju drobljenja je 1000 mm.
Za drobljenje rude koja dolazi iz rudnika prihvaćam za ugradnju čeljusnu drobilicu s jednostavnim ljuljanjem čeljusti SHDP 12x15. *
Učinak drobilice, Q je jednak:
Q \u003d q * L * i, t / h,
gdje je q - specifična produktivnost čeljusne drobilice po 1 cm 2 površine ispusnog proreza, t/(cm 2 * h);
L je duljina razmaka za istovar čeljusne drobilice, cm;
i - širina otvora za pražnjenje, vidi /4/
Prema praksi odjela za drobljenje koncentracijskog postrojenja, specifična produktivnost čeljusne drobilice je 0,13 t/cm 2 * sat.
Izvedba čeljusne drobilice određena je:
Q= 0,13*150*15,5 = 302,25 t/h.
Drobilica prihvaćena za ugradnju osigurava zadanu produktivnost za rudu.
Maksimalna veličina komada u hrani za drobilicu bit će:
120 * 0,8 = 96 cm.
Odabir i izračun rešetke
Ispred drobilice postavljena je rešetka od 95 cm (950 mm).
Potrebna površina probira određena je formulom:
gdje je Q* - produktivnost, t/h;
a - koeficijent jednak širini razmaka između rešetke, mm. /5/ Prema uvjetima rasporeda, širina rešetke je 2,7 m, a dužina 4,5 m.
Praksa odjela drobljenja tvornice pokazuje da ruda koja se isporučuje iz kamenoloma sadrži oko 4,5% komada većih od 950 mm. Komadi ove veličine dopremaju se prednjim utovarivačem u rudogradilište, gdje se drobe i ponovno utovarivačem dopremaju na rešetku.
2.3 Izbor i proračun SAG mlinova
U posljednje vrijeme u preradi zlatonosnih ruda u svjetskoj i domaćoj praksi u prvoj fazi mljevenja sve su češći mlinovi poluautogenog mljevenja s naknadnom cijanizacijom. U tom slučaju se isključuje gubitak zlata s otpadom od željeza i strugotine, smanjuje se potrošnja cijanida tijekom cijanizacije, a poboljšavaju se sanitarni uvjeti rada na kvarc silikatnim rudama. Stoga prihvaćam mlin za poluautogeno mljevenje (SAG) za ugradnju u prvu fazu mljevenja.
1. Nalazimo specifičnu produktivnost za novoformiranu klasu operativnog mlina PSI, t / (m 3 * h):
gdje je Q produktivnost radnog mlina, t/h;
- sadržaj klase -0,074 mm u ispustu mlina,%;
- sadržaj klase -0,074 mm u izvornom proizvodu, %;
D - promjer operativnog mlina, m;
L je duljina radnog mlina, m.
2. Specifičnu produktivnost projektiranog mlina utvrđujemo prema novoformiranoj klasi:
gdje je q 1 specifična produktivnost radnog mlina za istu klasu;
K i - koeficijent koji uzima u obzir razlike u mljevenju rude predviđene za preradu i prerađene rude (Ki=1);
K k - koeficijent koji uzima u obzir razliku u veličini početnih i konačnih proizvoda mljevenja u postojećim i projektiranim tvornicama (K k =1);
K D - koeficijent koji uzima u obzir razliku u promjerima bubnjeva projektiranih i operativnih mlinova:
K D = ,
gdje su D i D 1 odnosno nazivne promjere bubnjeva namijenjenih za ugradnju i rad mlinova. (KD = 1,1);
K t - koeficijent koji uzima u obzir razlike u tipu projektiranih i pogonskih mlinova (Kt=1).
q \u003d 0,77 * 1 * 1 * 1,1 * 1 = 0,85 t / (m 3 * h).
Prihvaćam za ugradnju mlin za mljevenje "Kaskad" promjera 7 m i dužine 2,3 m radnog volumena 81,05 m 3
3. Određujemo produktivnost mlinova za rudu prema formuli:
gdje je V radni volumen mlina. /4/
4. Odredite procijenjeni broj mlinova:
n-101/125,72 = 0,8;
tada će prihvaćena vrijednost biti jednaka 1 . Mlin "Kaskad" daje navedene performanse.
Odabir zaslona i izračun II faze probira .
Pražnjenje polusamomljevenih mlinova pumpama...
Slični dokumenti
Izbor tehnološke sheme obogaćivanja željezne rude. Proračun snage i odabir vrste separatora obogaćivanja. Određivanje učinkovitosti separatora za suhu magnetsku separaciju s gornjim dovodom. Tehnički parametri separatora 2PBS-90/250.
kontrolni rad, dodano 01.06.2014
Određivanje ukupnog stupnja drobljenja za drobilicu. Izbor stupnja drobljenja. Proračun i izbor drobilica, rešetkasto sito. Proračun sita druge faze drobljenja. Proračun sheme mljevenja i odabir opreme za mljevenje i razvrstavanje.
seminarski rad, dodan 20.01.2016
Proučavanje materijalnog sastava rude. Izbor i proračun mlinova prve i druge faze mljevenja, hidrociklona, magnetskih separatora. Proračun odstranjivača mulja za operaciju odstranjivanja. Zahtjevi kvalitete koncentrata. Proračun sheme voda-mulj.
seminarski rad, dodan 15.04.2015
Izbor i opravdanje sheme mljevenja, razvrstavanja i obogaćivanja rude. Proračun prinosa proizvoda i sadržaja metala. Proračun kvalitativno-kvantitativne sheme i sheme voda-mulj. Metode upravljanja tehnološkim procesima putem automatizacije.
seminarski rad, dodan 23.10.2011
Izbor i opravdanje sheme drobljenja i mljevenja, opreme za drobljenje, razvrstavanje i mljevenje. Karakteristike veličine izvorne rude. Proračun stupnjeva drobljenja, sita, mlinova, klasifikator. Karakteristike veličine sita.
seminarski rad, dodan 19.11.2013
Geološke karakteristike ležišta. Karakteristike prerađene rude, razvoj i proračun njezine sheme drobljenja. Izbor i proračun opreme za odjel drobljenja. Određivanje broja smjena i troškova rada za pružanje tehnologije drobljenja.
seminarski rad, dodan 25.02.2012
Tehnologija obogaćivanja željezne rude i koncentrata, analiza iskustava stranih poduzeća. Karakteristike mineralnog sastava rude, zahtjevi za kakvoćom koncentrata. Tehnološki proračun sheme voda-mulj i kvalitativno-kvantitativnog obogaćivanja.
seminarski rad, dodan 23.10.2011
Izrada kvalitativno-kvantitativne sheme pripremnih radnji za drobljenje, prosijavanje željezne rude: izbor metode, prinos proizvoda. Pregled preporučene opreme. Magnetsko-gravitacijska tehnologija i flotacijsko obogaćivanje željezne rude.
seminarski rad, dodan 09.01.2012
Značajke i faze implementacije tehnologije drobljenja. Pročišćeni proračun sheme probira. Izbor i proračun drobilica. Utvrđivanje potrebe opreme za pripremu rude, pomoćne opreme. Sigurnosni propisi u radnji za drobljenje.
seminarski rad, dodan 12.01.2015
Izbor i proračun glavne tehnološke opreme za preradu mineralnih sirovina, hranilica. Proračun operacija probira. Odabir i opravdanje količine osnovne opreme, njihovih tehničkih karakteristika, namjene i glavnih funkcija.