Korozija u kotlu. Korozija i erozija u kotlovima srednjeg i niskog tlaka sa strane peći. Pojave korozije u kotlovima se najčešće javljaju na unutarnjoj toplinski napregnutoj površini, a relativno rjeđe na vanjskoj.
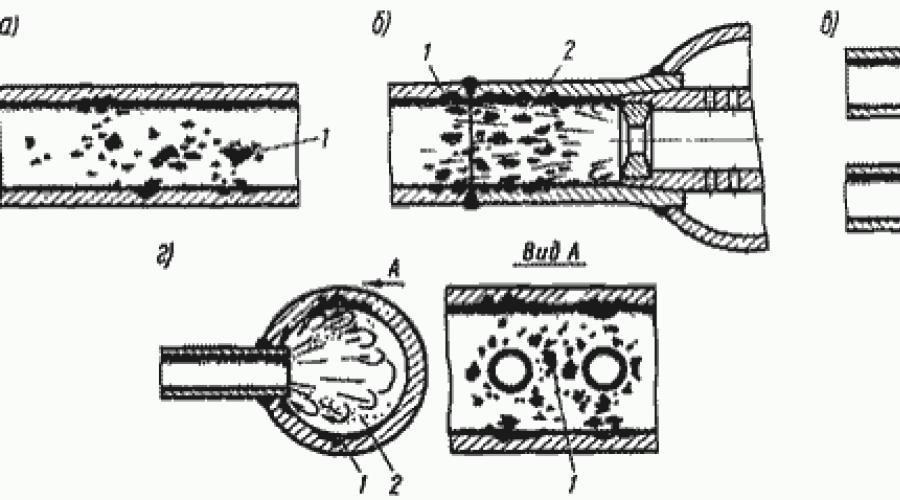
Pročitajte također
Ova korozija po veličini i intenzitetu često je značajnija i opasnija od korozije kotlova tijekom njihovog rada.
Prilikom ostavljanja vode u sustavima, ovisno o njezinoj temperaturi i pristupu zraka, može doći do raznih slučajeva korozije parkiranja. Prije svega, treba napomenuti iznimnu nepoželjnost prisutnosti vode u cijevima jedinica kada su u rezervi.
Ako voda iz ovog ili onog razloga ostane u sustavu, tada može doći do teške korozije za parkiranje u pari, a posebno u vodenom prostoru spremnika (uglavnom duž vodene linije) pri temperaturi vode od 60-70 ° C. Stoga se u praksi često opaža korozija parkiranja različitog intenziteta, unatoč istim načinima isključivanja sustava i kvaliteti vode koja se u njima nalazi; uređaji sa značajnom toplinskom akumulacijom podložni su većoj koroziji od uređaja koji imaju dimenzije peći i grijaće površine, jer se kotlovska voda u njima hladi brže; temperatura mu pada ispod 60-70°C.
Pri temperaturi vode iznad 85-90°C (na primjer, tijekom kratkotrajnog prekida rada uređaja), ukupna korozija se smanjuje, a korozija metala parnog prostora, u kojem se u ovom slučaju opaža povećana kondenzacija pare , može premašiti koroziju metala vodenog prostora. Parking korozija u prostoru pare je u svim slučajevima ujednačenija nego u vodenom prostoru kotla.
Razvoj korozije parkiranja uvelike olakšava mulj koji se nakuplja na površinama kotla, koji obično zadržava vlagu. S tim u vezi, u agregatima i cijevima duž donjeg generatriksa i na njihovim krajevima, tj. u područjima najvećeg nakupljanja mulja, često se nalaze značajne rupe od korozije.
Načini konzerviranja opreme u pričuvi
Za očuvanje opreme mogu se koristiti sljedeće metode:
a) sušenje - uklanjanje vode i vlage iz agregata;
b) punjenje ih otopinama kaustične sode, fosfata, silikata, natrijevog nitrita, hidrazina;
c) punjenje tehnološkog sustava dušikom.
Način konzervacije treba odabrati ovisno o prirodi i trajanju zastoja, kao io vrsti i konstrukcijskim značajkama opreme.
Zastoji opreme prema trajanju mogu se podijeliti u dvije skupine: kratkoročni - ne više od 3 dana i dugoročni - više od 3 dana.
Postoje dvije vrste kratkoročnih zastoja:
a) planirano, povezano s povlačenjem u pričuvu vikendom zbog pada opterećenja ili povlačenja u pričuvu noću;
b) prisilni - zbog kvara cijevi ili oštećenja drugih komponenti opreme, za čije otklanjanje nije potrebno dulje zaustavljanje.
Ovisno o namjeni, dugotrajni zastoji mogu se podijeliti u sljedeće skupine: a) stavljanje opreme u pričuvu; b) tekuće popravke; c) kapitalni popravci.
U slučaju kratkotrajnog zastoja opreme potrebno je koristiti konzerviranje punjenjem deaeriranom vodom uz održavanje prekomjernog tlaka ili plinskom (dušikom) metodom. Ako je potrebno isključivanje u nuždi, tada je jedina prihvatljiva metoda konzervacija dušikom.
Kada je sustav stavljen u stanje pripravnosti ili je u stanju mirovanja dulje vrijeme bez popravka, preporučljivo je izvršiti konzervaciju punjenjem otopinom nitrita ili natrijevog silikata. U tim slučajevima može se koristiti i očuvanje dušika, uz nužno poduzimanje mjera za stvaranje nepropusnosti sustava kako bi se spriječila prekomjerna potrošnja plina i neproduktivan rad dušične tvornice, kao i kako bi se stvorili sigurni uvjeti za održavanje opreme.
Metode očuvanja stvaranjem viška tlaka, punjenje dušikom mogu se koristiti bez obzira na značajke dizajna grijaćih površina opreme.
Kako bi se spriječila parkirna korozija metala tijekom velikih i tekućih popravaka, primjenjive su samo metode konzervacije koje omogućuju stvaranje zaštitnog filma na metalnoj površini koji zadržava svojstva najmanje 1-2 mjeseca nakon ispuštanja otopine za konzerviranje, od pražnjenja i smanjenja tlaka u sustava su neizbježni. Trajanje zaštitnog filma na metalnoj površini nakon tretmana s natrijevim nitritom može doseći 3 mjeseca.
Metode konzerviranja korištenjem vode i otopina reagensa praktički su neprihvatljive za zaštitu od parkirane korozije međupregrijača kotlova zbog poteškoća povezanih s njihovim punjenjem i naknadnim čišćenjem.
Metode očuvanja toplovodnih i niskotlačnih parnih kotlova, kao i druge opreme zatvorenih tehnoloških krugova opskrbe toplinom i vodom, po mnogo čemu se razlikuju od metoda koje se danas koriste za sprječavanje korozije parkiranja u termoelektranama. U nastavku su opisane glavne metode za sprječavanje korozije u stanju mirovanja opreme uređaja takvih cirkulacijskih sustava, uzimajući u obzir specifičnosti njihovog rada.
Pojednostavljene metode čuvanja
Ove metode su korisne za male kotlove. Sastoje se od potpunog uklanjanja vode iz kotlova i postavljanja sredstva za sušenje u njih: kalciniranog kalcijevog klorida, živog vapna, silika gela u količini od 1-2 kg po 1 m 3 volumena.
Ova metoda konzerviranja prikladna je za sobne temperature ispod i iznad nule. U prostorijama grijanim zimi može se provesti jedna od kontaktnih metoda konzervacije. Svodi se na punjenje cijelog unutarnjeg volumena jedinice alkalnom otopinom (NaOH, Na 3 P0 4 itd.), što osigurava potpunu stabilnost zaštitnog filma na metalnoj površini čak i kada je tekućina zasićena kisikom.
Obično se koriste otopine koje sadrže od 1,5-2 do 10 kg/m 3 NaOH ili 5-20 kg/m 3 Na 3 P0 4 ovisno o sadržaju neutralnih soli u izvorišnoj vodi. Manje vrijednosti odnose se na kondenzat, veće na vodu koja sadrži do 3000 mg/l neutralnih soli.
Korozija se može spriječiti i metodom nadtlaka, u kojoj se tlak pare u zaustavljenoj jedinici konstantno održava na razini iznad atmosferskog tlaka, a temperatura vode ostaje iznad 100°C, što onemogućuje pristup glavnom korozivnom agensu, kisiku. .
Važan uvjet za učinkovitost i ekonomičnost bilo koje metode zaštite je najveća moguća nepropusnost parovodnih armatura kako bi se izbjeglo prebrzo smanjenje tlaka, gubitak zaštitne otopine (ili plina) ili ulazak vlage. Osim toga, u mnogim slučajevima korisno je prethodno čišćenje površina od raznih naslaga (soli, mulj, kamenac).
Prilikom primjene različitih metoda zaštite od korozije parkiranja treba imati na umu sljedeće.
1. Za sve vrste konzervacije potrebno je prethodno uklanjanje (pranje) naslaga lako topljivih soli (vidi gore) kako bi se izbjegla pojačana korozija parkiranja u pojedinim područjima štićene cjeline. Ovu mjeru je obavezno provesti tijekom kontaktne konzervacije, inače je moguća intenzivna lokalna korozija.
2. Iz sličnih razloga poželjno je prije dugotrajnog konzerviranja ukloniti sve vrste netopivih naslaga (mulj, kamenac, željezni oksidi).
3. Ako su spojevi nepouzdani, potrebno je odvojiti rezervnu opremu od pogonskih jedinica pomoću utikača.
Propuštanje pare i vode manje je opasno uz očuvanje kontakta, ali je neprihvatljivo kod suhih i plinskih metoda zaštite.
Izbor sredstava za sušenje određen je relativnom dostupnošću reagensa i željom da se dobije što veći specifični sadržaj vlage. Najbolji desikant je granulirani kalcijev klorid. Živo vapno je mnogo lošije od kalcijevog klorida, ne samo zbog nižeg kapaciteta vlage, već i zbog brzog gubitka svoje aktivnosti. Vapno upija ne samo vlagu iz zraka, već i ugljični dioksid, zbog čega je prekriven slojem kalcijevog karbonata, koji sprječava daljnje upijanje vlage.
Marine site Russia no 05. listopada 2016. Napravljeno: 05. listopada 2016. Ažurirano: 05. listopada 2016. Pregledi: 5363Vrste korozije. Tijekom rada, elementi parnog kotla su izloženi agresivnim medijima - vodi, pari i dimnim plinovima. Razlikovati kemijsku i elektrokemijsku koroziju.
Kemijska korozija, uzrokovano parom ili vodom, ravnomjerno uništava metal po cijeloj površini. Stopa takve korozije u modernim brodskim kotlovima je niska. Opasnija je lokalna kemijska korozija uzrokovana agresivnim kemijskim spojevima sadržanim u naslagama pepela (sumpor, vanadijevi oksidi itd.).
Najčešći i opasniji je elektrokemijska korozija, koji teče u vodenim otopinama elektrolita kada se pojavi električna struja, uzrokovano razlikom potencijala između pojedinih dijelova metala koji se razlikuju po kemijskoj heterogenosti, temperaturi ili kvaliteti obrade.
Ulogu elektrolita obavlja voda (kod unutarnje korozije) ili kondenzirana vodena para u naslagama (kod vanjske korozije).
Pojava takvih mikrogalvanskih parova na površini cijevi dovodi do toga da metalni ioni-atomi prelaze u vodu u obliku pozitivno nabijenih iona, a površina cijevi na tom mjestu poprima negativan naboj. Ako je razlika u potencijalima takvih mikrogalvanskih parova neznatna, tada se na granici metal-voda postupno stvara dvostruki električni sloj, što usporava daljnji tijek procesa.
Međutim, u većini slučajeva potencijali pojedinih sekcija su različiti, što uzrokuje pojavu EMF-a usmjerenog od većeg potencijala (anode) prema manjem (katoda).
U tom slučaju metalni ioni-atomi prelaze iz anode u vodu, a višak elektrona se nakuplja na katodi. Kao rezultat toga, EMF i, posljedično, intenzitet procesa uništavanja metala naglo se smanjuju.
Taj se fenomen naziva polarizacija. Ako se anodni potencijal smanjuje kao rezultat stvaranja zaštitnog oksidnog filma ili povećanja koncentracije metalnih iona u anodnom području, a katodni potencijal ostaje praktički nepromijenjen, tada se polarizacija naziva anodna.
S katodnom polarizacijom u otopini blizu katode, koncentracija iona i molekula sposobnih za uklanjanje suvišnih elektrona s metalne površine naglo pada. Iz ovoga proizlazi da je glavna točka u borbi protiv elektrokemijske korozije stvaranje takvih uvjeta kada će se održati obje vrste polarizacije.
To je praktički nemoguće postići, jer voda u kotlu uvijek sadrži depolarizatore - tvari koje uzrokuju poremećaj procesa polarizacije.
Depolarizatori uključuju molekule O 2 i CO 2, ione H +, Cl - i SO - 4, kao i okside željeza i bakra. Otopljeni u vodi, CO 2 , Cl - i SO - 4 inhibiraju stvaranje gustog zaštitnog oksidnog filma na anodi i na taj način doprinose intenzivnom tijeku anodnih procesa. Vodikovi ioni H + smanjuju negativni naboj katode.
Utjecaj kisika na brzinu korozije počeo se očitovati u dva suprotna smjera. S jedne strane, kisik povećava brzinu procesa korozije, budući da je snažan depolarizator katodnih dijelova, s druge strane ima pasivizirajući učinak na površinu.
Uobičajeno, dijelovi kotla izrađeni od čelika imaju dovoljno jak početni oksidni film koji štiti materijal od izlaganja kisiku sve dok ga ne unište kemijski ili mehanički čimbenici.
Brzina heterogenih reakcija (uključujući koroziju) regulirana je intenzitetom sljedećih procesa: dovod reagensa (prvenstveno depolarizatora) na površinu materijala; uništavanje zaštitnog oksidnog filma; uklanjanje produkta reakcije s mjesta njegovog nastanka.
Intenzitet ovih procesa uvelike je određen hidrodinamičkim, mehaničkim i toplinskim čimbenicima. Stoga su mjere za smanjenje koncentracije agresivnih kemikalija pri visokom intenzitetu druga dva procesa, kako pokazuje iskustvo rada kotlova, obično neučinkovite.
Iz toga proizlazi da bi rješenje problema sprječavanja oštećenja od korozije trebalo biti složeno, kada se uzmu u obzir svi čimbenici koji utječu na početne uzroke uništenja materijala.
Elektrokemijska korozija
Ovisno o mjestu strujanja i tvarima koje sudjeluju u reakcijama, razlikuju se sljedeće vrste elektrokemijske korozije:
- kisik (i njegova raznolikost - parking),
- podmulj (ponekad nazvan "ljuska"),
- intergranularni (alkalna lomljivost kotlovskih čelika),
- utor i
- sumporna.
Korozija kisikom promatrano u ekonomajzerima, armaturama, dovodnim i odvodnim cijevima, kolektorima pare i vode i intrakolektorskim uređajima (štitovi, cijevi, odogrijači itd.). Zavojnice sekundarnog kruga kotlova s dva kruga, kotlova za korištenje i parnih grijača zraka posebno su osjetljivi na kisikovu koroziju. Korozija kisika nastaje tijekom rada kotlova i ovisi o koncentraciji kisika otopljenog u kotlovskoj vodi.
Stopa korozije kisika u glavnim kotlovima je niska, što je posljedica učinkovitog rada deaeratora i fosfatno-nitratnog režima vode. U pomoćnim kotlovima s vodenim cijevima često doseže 0,5 - 1 mm / godišnje, iako u prosjeku leži u rasponu od 0,05 - 0,2 mm / godišnje. Priroda oštećenja kotlovskih čelika su male jame.
Opasniji tip kisikove korozije je parking korozija teče tijekom razdoblja neaktivnosti kotla. Zbog specifičnosti rada svi brodski kotlovi (osobito pomoćni) podložni su intenzivnoj koroziji parkiranja. Parking korozija u pravilu ne dovodi do kvarova kotla, međutim, metal korodiran tijekom isključivanja, ceteris paribus, intenzivnije se uništava tijekom rada kotla.
Glavni uzrok korozije parkiranja je prodiranje kisika u vodu ako je kotao pun, odnosno u film vlage na metalnoj površini ako je kotao suh. Važnu ulogu imaju kloridi i NaOH sadržani u vodi, te naslage soli topive u vodi.
Ako su u vodi prisutni kloridi, jednolična korozija metala je pojačana, a ako sadrži malu količinu lužina (manje od 100 mg/l), tada je korozija lokalizirana. Kako bi se izbjegla korozija parkiranja pri temperaturi od 20 - 25 °C, voda treba sadržavati do 200 mg/l NaOH.
Vanjski znakovi korozije uz sudjelovanje kisika: mali lokalni ulkusi (slika 1, a), ispunjeni smeđim produktima korozije, koji tvore tuberkule iznad ulkusa.
Uklanjanje kisika iz napojne vode jedna je od važnih mjera za smanjenje kisikove korozije. Od 1986. godine sadržaj kisika u napojnoj vodi za pomorske i otpadne kotlove je ograničen na 0,1 mg/l.
Međutim, čak i uz takav sadržaj kisika u napojnoj vodi, uočava se korozijska oštećenja elemenata kotla u radu, što ukazuje na prevladavajući utjecaj procesa uništavanja oksidnog filma i ispiranja produkta reakcije iz središta korozije. Najilustrativniji primjer koji ilustrira učinak ovih procesa na oštećenja od korozije je uništavanje zavojnica kotlova s prisilnom cirkulacijom.
Riža. 1. Oštećenja uslijed korozije kisikom
Oštećenja od korozije u slučaju korozije kisikom, obično su strogo lokalizirane: na unutarnjoj površini ulaznih dijelova (vidi sliku 1, a), u području zavoja (slika 1, b), na izlaznim dijelovima i u koljeno zavojnice (vidi sliku 1, c), kao i u parovodnim kolektorima kotlova za korištenje (vidi sliku 1, d). Upravo u tim područjima (2 - područje uzzidne kavitacije) hidrodinamičke značajke strujanja stvaraju uvjete za uništavanje oksidnog filma i intenzivno ispiranje produkata korozije.
Doista, svaka deformacija protoka vode i mješavine pare i vode popraćena je pojavom kavitacija u slojevima uz zid ekspandirajući tok 2, gdje nastali i odmah kolabirajući mjehurići pare uzrokuju uništavanje oksidnog filma zbog energije hidrauličkih mikroudara.
Tome također doprinose izmjenična naprezanja u filmu, uzrokovana vibracijama zavojnica i fluktuacijama temperature i tlaka. Povećana lokalna turbulencija strujanja u tim područjima uzrokuje aktivno ispiranje produkata korozije.
Na direktnim izlaznim dijelovima zavojnica dolazi do uništavanja oksidnog filma uslijed udara o površinu kapljica vode tijekom turbulentnih pulsacija toka smjese pare i vode, čiji disperzno-prstenasti način gibanja ovdje prelazi u dispergirani pri brzina protoka do 20-25 m/s.
U tim uvjetima čak i nizak sadržaj kisika (~ 0,1 mg/l) uzrokuje intenzivno uništavanje metala, što dovodi do pojave fistula u ulaznim dijelovima zavojnica kotlova za otpadnu toplinu tipa La Mont nakon 2- 4 godine rada, au ostalim područjima - nakon 6-12 godina.
Riža. Slika 2. Oštećenja od korozije na zavojnicama ekonomajzera utilizacijskih kotlova KUP1500R motornog broda "Indira Gandhi".
Kao ilustraciju navedenog, razmotrimo uzroke oštećenja namotaja ekonomajzera dvaju kotla na otpadnu toplinu tipa KUP1500R ugrađenih na nosač upaljača Indira Gandhi (tip Alexey Kosygin), koji je u promet ušao u listopadu 1985. godine. veljače 1987. zbog oštećenja zamijenjeni su ekonomajzeri oba kotla. Nakon 3 godine, oštećenja na zavojnicama se pojavljuju i u ovim ekonomajzerima, koji se nalaze u područjima do 1-1,5 m od ulaznog razvodnika. Priroda oštećenja ukazuje (slika 2, a, b) na tipičnu kisikovu koroziju praćenu zamorom (poprečne pukotine).
Međutim, priroda umora u pojedinim područjima je različita. Pojava pukotine (i ranijeg pucanja oksidnog filma) u području zavara (vidi sliku 2, a) posljedica je naizmjeničnih naprezanja uzrokovanih vibracijom snopa cijevi i konstrukcijske značajke spoj zavojnica sa zaglavljem (kraj zavojnice promjera 22x3 zavaren je na zakrivljeni spoj promjera 22x2).
Uništavanje oksidnog filma i stvaranje pukotina od zamora na unutarnjoj površini ravnih dijelova zavojnica, udaljenih od ulaza za 700-1000 mm (vidi sliku 2, b), uzrokovani su izmjeničnim toplinskim naprezanjima koja nastaju prilikom puštanja u rad kotla, kada se vruća površina dovodi hladna voda. U tom je slučaju djelovanje toplinskih naprezanja pojačano činjenicom da rebra zavojnica otežava slobodno širenje metala cijevi, stvarajući dodatna naprezanja u metalu.
Podmuljna korozija obično se promatra u glavnim kotlovima za vodu na unutarnjim površinama sita i parnih cijevi dovodnih snopova okrenutih prema baklji. Priroda podmuljne korozije su ovalne jame veličine duž glavne osi (paralelno s osi cijevi) do 30-100 mm.
Na ulkusima se nalazi gusti sloj oksida u obliku "školjki" 3 (Sl. 3.) Podmuljna korozija se odvija uz prisutnost čvrstih depolarizatora - željeznih i bakrenih oksida 2, koji se talože na toplinski najopterećenijim cijevima. presjeci na mjestima aktivnih središta korozije koji nastaju prilikom razaranja oksidnih filmova .
Na vrhu se formira labav sloj kamenca i produkata korozije.
Za pomoćne kotlove ova vrsta korozije nije tipična, ali pod visokim toplinskim opterećenjima i odgovarajućim načinima obrade vode nije isključena pojava korozije ispod mulja u ovim kotlovima.
Najaktivnija korozija zaslonskih cijevi očituje se na mjestima gdje su koncentrirane nečistoće rashladne tekućine. To uključuje dijelove zidnih cijevi s visokim toplinskim opterećenjem, gdje dolazi do dubokog isparavanja kotlovske vode (osobito ako na površini isparavanja postoje porozne naslage niske toplinske vodljivosti). Stoga, u odnosu na prevenciju oštećenja sitastih cijevi povezanih s unutarnjom korozijom metala, potrebno je uzeti u obzir potrebu za integriranim pristupom, t.j. utjecaj na vodeno-kemijski i režim peći.
Oštećenja zidnih cijevi uglavnom su mješovite prirode, mogu se uvjetno podijeliti u dvije skupine:
1) Oštećenja sa znakovima pregrijavanja čelika (deformacija i stanjivanje stijenki cijevi na mjestu uništenja; prisutnost grafitnih zrnaca itd.).
2) Krhki prijelomi bez karakterističnih znakova pregrijavanja metala.
Na unutarnjoj površini mnogih cijevi zabilježene su značajne naslage dvoslojnog karaktera: gornja je slabo vezana, donja je ljuskava, čvrsto vezana za metal. Debljina donjeg sloja ljestvice je 0,4-0,75 mm. U zoni oštećenja dolazi do uništenja kamenca na unutarnjoj površini. U blizini mjesta uništenja i na određenoj udaljenosti od njih, unutarnja površina cijevi zahvaćena je korozijskim jamama i krhkim mikrooštećenjima.
Opći izgled oštećenja ukazuje na toplinsku prirodu razaranja. Strukturne promjene na prednjoj strani cijevi - duboka sferizacija i razgradnja perlita, stvaranje grafita (prijelaz ugljika u grafit 45-85%) - ukazuje na višak ne samo radne temperature zaslona, već i dopuštene za čelik 20.500 °C. Prisutnost FeO također potvrđuje visoku razinu temperature metala tijekom rada (iznad 845 oK - tj. 572 oC).
Krhka oštećenja uzrokovana vodikom obično se javljaju u područjima s visokim toplinskim tokovima, ispod debelih naslaga naslaga i nagnutih ili horizontalnih cijevi, kao i u područjima prijenosa topline u blizini prstenova za zavarivanje ili drugih uređaja koji sprječavaju slobodno kretanje tokova. .Iskustvo je pokazao da se oštećenje vodika događa u kotlovima koji rade na tlakovima ispod 1000 psi. inča (6,9 MPa).
Oštećenje vodikom obično rezultira rupturama s debelim rubovima. Drugi mehanizmi koji pridonose stvaranju pukotina s debelim rubovima su korozijsko pucanje pod naponom, korozijski zamor, lomovi naprezanja i (u nekim rijetkim slučajevima) jako pregrijavanje. Možda će biti teško vizualno razlikovati štetu uzrokovanu oštećenjem vodikom od drugih vrsta oštećenja, ali neke od njihovih značajki ovdje mogu pomoći.
Na primjer, oštećenje vodika gotovo je uvijek povezano s stvaranjem rupa u metalu (vidi mjere opreza dane u poglavljima 4 i 6). Druge vrste oštećenja (osim mogućeg zamora od korozije, koji često počinje u pojedinim školjkama) obično nisu povezane s jakom korozijom.
Kvarovi cijevi kao posljedica oštećenja metala vodikom često se očituju kao stvaranje pravokutnog "prozora" u stijenci cijevi, što nije tipično za druge vrste razaranja.
Za procjenu oštećenja sitastih cijevi treba uzeti u obzir da metalurški (početni) sadržaj plinovitog vodika u perlitnom čeliku (uključujući st. 20) ne prelazi 0,5–1 cm3/100 g. Kada je sadržaj vodika veći od 4--5 cm3/100g, mehanička svojstva čelika značajno se pogoršavaju. U ovom slučaju, potrebno je usredotočiti se uglavnom na lokalni sadržaj zaostalog vodika, budući da se u slučaju krhkih lomova sitastih cijevi, oštro pogoršanje svojstava metala opaža samo u uskoj zoni duž poprečnog presjeka cijevi. uz uvijek zadovoljavajuću strukturu i mehanička svojstva susjednog metala na udaljenosti od samo 0,2-2 mm.
Dobivene vrijednosti prosječnih koncentracija vodika na rubu loma su 5-10 puta veće od njegovog početnog sadržaja za stanicu 20, što nije moglo imati značajan utjecaj na oštećenje cijevi.
Prikazani rezultati pokazuju da se pokazalo da je vodikovo krhkost odlučujući čimbenik u oštećenju zidnih cijevi kotlova KrCHPP.
Zahtijevano je dodatno proučavanje koji od čimbenika presudno utječe na ovaj proces: a) termički ciklus uslijed destabilizacije normalnog režima vrenja u područjima povećanih toplinskih tokova u prisutnosti naslaga na površini isparavanja i, kao rezultat , oštećenje zaštitnih oksidnih filmova koji ga prekrivaju; b) prisutnost korozivnih nečistoća u radnom mediju koje se koncentriraju u naslagama blizu površine isparavanja; c) kombinirano djelovanje faktora "a" i "b".
Posebno je zanimljivo pitanje uloge režima peći. Priroda krivulja ukazuje na nakupljanje vodika u brojnim slučajevima u blizini vanjske površine zaslonskih cijevi. To je prije svega moguće ako se na naznačenoj površini nalazi gusti sloj sulfida, koji su u velikoj mjeri nepropusni za vodik koji difundira s unutarnje površine na vanjsku. Do stvaranja sulfida dolazi zbog: visokog sadržaja sumpora u izgorjelom gorivu; bacajući baklju na ploče zaslona. Drugi razlog hidrogenacije metala na vanjskoj površini je pojava korozijskih procesa kada metal dođe u dodir s dimnim plinovima. Kako je pokazala analiza vanjskih naslaga kotlovskih cijevi, obično su se javljala oba ova uzroka.
Uloga načina izgaranja očituje se i u koroziji sitastih cijevi pod djelovanjem čiste vode, što se najčešće opaža na visokotlačnim parogeneratorima. Središta korozije obično se nalaze u zoni maksimalnih lokalnih toplinskih opterećenja i samo na zagrijanoj površini cijevi. Ova pojava dovodi do stvaranja okruglih ili eliptičnih udubljenja promjera većeg od 1 cm.
Do pregrijavanja metala najčešće dolazi u prisutnosti naslaga zbog činjenice da će količina percipirane topline biti gotovo ista za čistu cijev i cijev koja sadrži kamenac, temperatura cijevi će biti različita.
Pojave korozije u kotlovima se najčešće javljaju na unutarnjoj toplinski napregnutoj površini, a relativno rjeđe na vanjskoj.
U potonjem slučaju, uništenje metala je - u većini slučajeva - posljedica kombiniranog djelovanja korozije i erozije, što ponekad ima prevladavajući značaj.
Vanjski znak razaranja erozije je čista metalna površina. Pod korozivnim djelovanjem proizvodi korozije obično ostaju na njegovoj površini.
Unutarnji (u vodenom okolišu) procesi korozije i kamenca mogu pogoršati vanjsku koroziju (u plinskom okruženju) zbog toplinske otpornosti sloja kamenca i korozijskih naslaga, a posljedično i porasta temperature na površini metala.
Vanjska korozija metala (sa strane kotlovske peći) ovisi o raznim čimbenicima, ali prije svega o vrsti i sastavu goriva koje se spaljuje.
Korozija plinsko-uljnih kotlova
Gorivo ulje sadrži organske spojeve vanadija i natrija. Ako se rastaljene naslage troske koje sadrže spojeve vanadija (V) nakupljaju na stijenci cijevi okrenute prema peći, tada se s velikim viškom zraka i/ili temperature površine metala od 520-880 ° C javljaju sljedeće reakcije:
4Fe + 3V2O5 = 2Fe2O3 + 3V2O3 (1)
V2O3 + O2 = V2O5 (2)
Fe2O3 + V2O5 = 2FeVO4 (3)
7Fe + 8FeVO4 = 5Fe3O4 + 4V2O3 (4)
(Spojevi natrija) + O2 = Na2O (5)
Moguć je i drugi mehanizam korozije koji uključuje vanadij (tekuća eutektička smjesa):
2Na2O. V2O4 . 5V2O5 + O2 = 2Na2O. 6V2O5 (6)
Na2O. 6V2O5 + M = Na2O. V2O4 . 5V2O5 + MO (7)
(M - metal)
Spojevi vanadija i natrija tijekom izgaranja goriva oksidiraju se u V2O5 i Na2O. U naslagama koje prianjaju na površinu metala, Na2O je vezivo. Tekućina nastala kao rezultat reakcija (1)-(7) topi zaštitni film magnetita (Fe3O4), što dovodi do oksidacije metala ispod naslaga (temperatura taljenja naslaga (troske) je 590-880° C).
Kao rezultat ovih procesa, stijenke sitastih cijevi okrenute prema peći su jednoliko stanjive.
Povećanje temperature metala, pri kojem spojevi vanadija postaju tekući, olakšano je unutarnjim naslagama kamenca u cijevima. I tako, kada se postigne temperatura popuštanja metala, dolazi do pucanja cijevi - posljedica kombiniranog djelovanja vanjskih i unutarnjih naslaga.
Dijelovi za pričvršćivanje cijevnih sita, kao i izbočine cijevnih zavara, također korodiraju - porast temperature na njihovoj površini se ubrzava: ne hlade se mješavinom pare i vode, kao cijevi.
Gorivo ulje može sadržavati sumpor (2,0-3,5%) u obliku organskih spojeva, elementarnog sumpora, natrijevog sulfata (Na2SO4), koji u naftu ulazi iz formacijskih voda. Na površini metala u takvim uvjetima korozija vanadija je praćena sulfid-oksidnom korozijom. Njihov zajednički učinak je najizraženiji kada naslage sadrže 87% V2O5 i 13% Na2SO4, što odgovara sadržaju vanadija i natrija u loživom ulju u omjeru 13/1.
Zimi, pri zagrijavanju loživog ulja parom u spremnicima (za olakšavanje odvodnje), u njega ulazi dodatna voda u količini od 0,5-5,0%. Posljedica: povećava se količina naslaga na niskotemperaturnim površinama kotla, a očito se povećava korozija cjevovoda loživog ulja i spremnika ulja.
Osim gore opisane sheme za uništavanje kotlovskih sita, korozije pregrijača, festonskih cijevi, kotlovskih snopova, ekonomajzer ima neke značajke zbog povećane - u nekim dijelovima - brzina plinova, posebno onih koji sadrže neizgorene čestice loživog ulja i oljuštene čestice troske.
Identifikacija korozije
Vanjska površina cijevi prekrivena je gustim caklinskim slojem sivih i tamnosivih naslaga. Na strani okrenutoj prema ložištu nalazi se stanjivanje cijevi: ravni dijelovi i plitke pukotine u obliku "oznaka" jasno su vidljive ako se površina očisti od naslaga i oksidnih filmova.
Ako je cijev uništena u nuždi, tada je vidljiva uzdužna uzdužna pukotina.
Korozija kotlova na prah
U koroziji koja nastaje djelovanjem produkata izgaranja ugljena, sumpor i njegovi spojevi imaju odlučujuću važnost. Osim toga, kloridi (uglavnom NaCl) i spojevi alkalnih metala utječu na tijek procesa korozije. Korozija je najvjerojatnija kada ugljen sadrži više od 3,5% sumpora i 0,25% klora.
Leteći pepeo koji sadrži alkalijske spojeve i sumporove okside taloži se na površini metala pri temperaturi od 560-730 °C. U tom slučaju, kao rezultat tekućih reakcija, nastaju alkalni sulfati, na primjer, K3Fe(SO4)3 i Na3Fe(SO4)3. Ova rastaljena troska zauzvrat uništava (otapa) zaštitni oksidni sloj na metalu – magnetit (Fe3O4).
Brzina korozije je najveća pri temperaturi metala od 680-730 °C, s njezinim povećanjem, brzina se smanjuje zbog toplinskog razlaganja korozivnih tvari.
Najveća korozija je u izlaznim cijevima pregrijača, gdje je temperatura pare najviša.
Identifikacija korozije
Na zaslonskim cijevima mogu se uočiti ravne površine s obje strane cijevi koje su podvrgnute korozijskom uništavanju. Ta su područja međusobno smještena pod kutom od 30-45 °C i prekrivena su slojem sedimenata. Između njih je relativno "čisto" područje, podvrgnuto "frontalnom" utjecaju strujanja plina.
Naslage se sastoje od tri sloja: vanjski sloj je porozni elektrofilterski pepeo, međusloj su bjelkasti vodotopivi alkalni sulfati, a unutarnji sloj su sjajni crni željezni oksidi (Fe3O4) i sulfidi (FeS).
Na niskotemperaturnim dijelovima kotlova - ekonomajzeru, grijaču zraka, ispušnom ventilatoru - temperatura metala pada ispod "točke rosišta" sumporne kiseline.
Pri izgaranju krutog goriva temperatura plina se smanjuje sa 1650 °C u baklji na 120 °C ili manje u dimnjaku.
Zbog hlađenja plinova u parnoj fazi nastaje sumporna kiselina, a pri dodiru s hladnijom metalnom površinom pare se kondenziraju u tekuću sumpornu kiselinu. “Točka rosišta” sumporne kiseline je 115-170 °C (možda i više - ovisi o sadržaju vodene pare i sumporovog oksida (SO3) u struji plina).
Proces je opisan reakcijama:
S + O2 = SO2 (8)
SO3 + H2O = H2SO4 (9)
H2SO4 + Fe = FeSO4 + H2 (10)
U prisutnosti željeznih i vanadijevih oksida moguća je katalitička oksidacija SO3:
2SO2 + O2 = 2SO3 (11)
U nekim slučajevima korozija sumporne kiseline pri sagorijevanju ugljena je manje značajna nego pri izgaranju smeđeg, škriljevca, treseta, pa čak i prirodnog plina - zbog relativno većeg oslobađanja vodene pare iz njih.
Identifikacija korozije
Ova vrsta korozije uzrokuje jednolično uništavanje metala. Obično je površina hrapava, s blagim premazom hrđe i slična je površini bez korozivnih pojava. Kod duljeg izlaganja metal može biti prekriven naslagama proizvoda korozije, koji se moraju pažljivo ukloniti tijekom ispitivanja.
Korozija tijekom prekida rada
Ova vrsta korozije pojavljuje se na ekonomajzeru i na onim mjestima kotla gdje su vanjske površine prekrivene spojevima sumpora. Kako se kotao hladi, temperatura metala pada ispod “točke rosišta” i, kao što je gore opisano, ako postoje naslage sumpora, nastaje sumporna kiselina. Možda je međuspoj sumporna kiselina (H2SO3), ali je vrlo nestabilan i odmah prelazi u sumpornu kiselinu.
Identifikacija korozije
Metalne površine obično su premazane premazima. Ako se uklone, tada će se pronaći područja destrukcije metala, gdje su bile naslage sumpora i područja nekorodiranog metala. Ovaj izgled razlikuje koroziju na zaustavljenom kotlu od gore opisane korozije metala ekonomajzera i ostalih "hladnih" dijelova kotla koji radi.
Prilikom pranja kotla, pojave korozije se više ili manje ravnomjerno raspoređuju po metalnoj površini zbog erozije naslaga sumpora i nedovoljnog isušivanja površina. Uz nedovoljno pranje, korozija je lokalizirana tamo gdje su bili spojevi sumpora.
erozija metala
Pod određenim uvjetima, razni kotlovski sustavi su izloženi erozijskom razaranju metala, kako s unutarnje tako i vanjske strane grijanog metala, a gdje se javljaju turbulentna strujanja velikom brzinom.
U nastavku se razmatra samo erozija turbine.
Turbine su podložne eroziji od utjecaja čvrstih čestica i kapljica kondenzata pare. Čvrste čestice (oksidi) ljušte se s unutarnje površine pregrijača i parovoda, osobito u uvjetima prolaznih toplinskih procesa.
Kapljice kondenzata pare uglavnom uništavaju površine lopatica zadnje faze turbine i odvodnih cjevovoda. Erozivni i korozivni učinci kondenzata pare mogući su ako je kondenzat "kiseo" - pH je ispod pet jedinica. Korozija je također opasna u prisutnosti para klorida (do 12% mase naslaga) i kaustične sode u kapljicama vode.
Identifikacija erozije
Uništavanje metala od udarca kapljica kondenzata najizraženije je na prednjim rubovima lopatica turbine. Rubovi su prekriveni tankim poprečnim zupcima i žljebovima (žljebovima), mogu postojati nagnute konusne izbočine usmjerene prema udarima. Na prednjim rubovima oštrica postoje izbočine i gotovo ih nema na njihovim stražnjim ravninama.
Oštećenja od čvrstih čestica su u obliku praznina, mikrodentina i zareza na prednjim rubovima oštrica. Žljebovi i nagnuti konusi su odsutni.
Identifikacija vrsta korozije je teška, pa stoga nisu rijetke greške u određivanju tehnološki i ekonomski optimalnih mjera za suzbijanje korozije. Glavne potrebne mjere poduzimaju se u skladu s propisima koji određuju granice glavnih pokretača korozije.
GOST 20995-75 „Stacionarni parni kotlovi s tlakom do 3,9 MPa. Pokazatelji kvalitete napojne vode i pare” standardizira pokazatelje u napojnoj vodi: prozirnost, odnosno količinu suspendiranih nečistoća; opća tvrdoća, sadržaj željeza i bakrenih spojeva - sprječavanje stvaranja kamenca i naslaga željeza i bakrenog oksida; pH vrijednost - sprječava alkalnu i kiselinsku koroziju, kao i stvaranje pjene u bubnju kotla; sadržaj kisika - sprječavanje korozije kisika; sadržaj nitrita - sprječavanje korozije nitrita; sadržaj ulja - sprječavanje pjene u bubnju kotla.
Vrijednosti normi određuju GOST ovisno o tlaku u kotlu (dakle, o temperaturi vode), o snazi lokalnog toplinskog toka i o tehnologiji obrade vode.
Prilikom istraživanja uzroka korozije, prije svega, potrebno je pregledati (gdje postoje) mjesta razaranja metala, analizirati uvjete rada kotla u predakcidentnom razdoblju, analizirati kvalitetu napojne vode, pare i naslaga. , te analizirati konstrukcijske značajke kotla.
Pri vanjskom pregledu mogu se posumnjati na sljedeće vrste korozije.
Korozija kisikom
: dijelovi ulaznih cijevi čeličnih ekonomajzera; dovodni cjevovodi pri susretu s nedovoljno deoksigeniranom (iznad normalnog) vodom - "proboji" kisika u slučaju lošeg odzračivanja; grijači napojne vode; sva vlažna područja kotla tijekom gašenja i nepoduzimanje mjera za sprječavanje ulaska zraka u kotao, posebno u stajaćim područjima, pri ispuštanju vode, odakle je teško ukloniti kondenzat pare ili ga potpuno napuniti vodom, npr. vertikalne cijevi pregrijača. Tijekom zastoja korozija je pojačana (lokalizirana) u prisutnosti lužine (manje od 100 mg/l).
Korozija kisika rijetko (kada je sadržaj kisika u vodi znatno veći od norme - 0,3 mg / l) očituje se u uređajima za odvajanje pare bubnjeva kotla i na stijenci bubnjeva na granici razine vode; u odvodnim cijevima. Kod dizajućih cijevi ne dolazi do korozije zbog odzračivanja mjehurića pare.
Vrsta i priroda oštećenja. Čirevi različite dubine i promjera, često prekriveni tuberkulama, čija su gornja kora crvenkasti željezni oksidi (vjerojatno hematit Fe 2 O 3). Dokaz aktivne korozije: ispod kore tuberkula - crni tekući talog, vjerojatno magnetit (Fe 3 O 4) pomiješan sa sulfatima i kloridima. Kod prigušene korozije ispod kore postoji praznina, a dno čira prekriveno je naslagama kamenca i mulja.
Pri pH > 8,5 - čirevi su rijetki, ali veći i dublji, pri pH< 8,5 - встречаются чаще, но меньших размеров. Только вскрытие бугорков помогает интерпретировать бугорки не как поверхностные отложения, а как следствие коррозии.
Pri brzini vode većoj od 2 m/s, tuberkuli mogu poprimiti duguljasti oblik u smjeru mlaza.
. Magnetitne kore su dovoljno guste i mogle bi poslužiti kao pouzdana prepreka prodiranju kisika u tuberkule. Ali često se uništavaju kao posljedica zamora od korozije, kada se temperatura vode i metala ciklički mijenja: česta gašenja i pokretanja kotla, pulsirajuće kretanje mješavine vode i pare, raslojavanje mješavine pare i vode u odvojenu paru i čepovi za vodu slijede jedan za drugim.
Korozija se pojačava s porastom temperature (do 350 °C) i povećanjem sadržaja klorida u kotlovskoj vodi. Ponekad je korozija pojačana produktima toplinske razgradnje određenih organskih tvari u napojnoj vodi.
Riža. 1. Pojava kisikove korozije
Alkalna (u užem smislu - intergranularna) korozija
Mjesta oštećenja metala od korozije. Cijevi u zonama toka topline velike snage (područje plamenika i nasuprot izduženog plamenika) - 300-400 kW / m 2 i gdje je temperatura metala 5-10 ° C viša od vrelišta vode pri danom tlaku; nagnute i horizontalne cijevi, gdje postoji loša cirkulacija vode; mjesta ispod debelih naslaga; zone u blizini potpornih prstenova i u samim zavarima, na primjer, na mjestima zavarivanja uređaja za odvajanje pare unutar bubnja; mjesta u blizini zakovica.
Vrsta i priroda oštećenja. Hemisferične ili eliptične udubine ispunjene produktima korozije, često uključujući sjajne kristale magnetita (Fe 3 O 4). Većina udubljenja prekrivena je tvrdom korom. Na strani cijevi koja je okrenuta prema peći, udubljenja se mogu spojiti, tvoreći takozvani put korozije širine 20-40 mm i duljine do 2-3 m.
Ako kora nije dovoljno stabilna i gusta, tada korozija može dovesti - u uvjetima mehaničkog naprezanja - do pojave pukotina u metalu, osobito u blizini pukotina: zakovice, kotrljajući spojevi, mjesta zavarivanja uređaja za odvajanje pare.
Uzroci oštećenja od korozije. Pri visokim temperaturama - više od 200 ° C - i visokoj koncentraciji kaustične sode (NaOH) - 10% ili više - uništava se zaštitni film (kora) na metalu:
4NaOH + Fe 3 O 4 \u003d 2NaFeO 2 + Na 2 FeO 2 + 2H 2 O (1)
Međuprodukt NaFeO 2 podvrgava se hidrolizi:
4NaFeO 2 + 2N 2 O = 4NaON + 2Fe 2 O 3 + 2N 2 (2)
Odnosno, u ovoj reakciji (2) natrijev hidroksid se reducira, u reakcijama (1), (2) se ne troši, već djeluje kao katalizator.
Kada se magnetit ukloni, natrijev hidroksid i voda mogu izravno reagirati sa željezom kako bi se oslobodio atomski vodik:
2NaOH + Fe \u003d Na 2 FeO 2 + 2H (3)
4H 2 O + 3Fe \u003d Fe 3 O 4 + 8H (4)
Oslobođeni vodik može difundirati u metal i formirati metan (CH 4) sa željeznim karbidom:
4H + Fe 3 C \u003d CH 4 + 3Fe (5)
Također je moguće spojiti atomski vodik u molekularni vodik (H + H = H 2).
Metan i molekularni vodik ne mogu prodrijeti u metal, akumuliraju se na granicama zrna i, u prisutnosti pukotina, šire ih i produbljuju. Osim toga, ovi plinovi sprječavaju stvaranje i zbijanje zaštitnih filmova.
Koncentrirana otopina kaustične sode nastaje na mjestima dubokog isparavanja kotlovske vode: guste naslage soli (vrsta korozije ispod mulja); kriza ključanja mjehurića, kada se na metalu formira stabilan parni film - tamo metal gotovo da nije oštećen, ali je kaustična soda koncentrirana uz rubove filma, gdje se odvija aktivno isparavanje; prisutnost pukotina gdje dolazi do isparavanja, što se razlikuje od isparavanja u cijelom volumenu vode: kaustična soda isparava gore od vode, ne ispire se vodom i nakuplja se. Djelujući na metal, kaustična soda stvara pukotine na granicama zrna usmjerenim unutar metala (vrsta intergranularne korozije je pukotna korozija).
Intergranularna korozija pod utjecajem alkalne kotlovske vode najčešće se koncentrira u bubnju kotla.
Riža. Slika 3. Intergranularna korozija: a - mikrostruktura metala prije korozije, b - mikrostruktura u fazi korozije, stvaranje pukotina duž granice metalnog zrna
Takav korozivni učinak na metal moguć je samo uz istovremenu prisutnost tri čimbenika:
- lokalna vlačna mehanička naprezanja blizu ili malo veća od granice popuštanja, odnosno 2,5 MN/mm 2 ;
- labavi spojevi dijelova bubnja (gore spomenuti), gdje može doći do dubokog isparavanja vode iz kotla i gdje nakupljena kaustična soda otapa zaštitni film željeznih oksida (koncentracija NaOH je veća od 10%, temperatura vode je iznad 200°C i - posebno - bliže 300 ° C). Ako kotao radi s tlakom nižim od tlaka iz putovnice (na primjer, 0,6-0,7 MPa umjesto 1,4 MPa), tada se smanjuje vjerojatnost ove vrste korozije;
- nepovoljna kombinacija tvari u kotlovskoj vodi, u kojoj nema potrebnih zaštitnih koncentracija inhibitora ove vrste korozije. Natrijeve soli mogu djelovati kao inhibitori: sulfati, karbonati, fosfati, nitrati, tekućina sulfita celuloze.
Riža. 4. Pojava intergranularne korozije
Korozijske pukotine se ne razvijaju ako se promatra omjer:
(Na 2 SO 4 + Na 2 CO 3 + Na 3 PO 4 + NaNO 3) / (NaOH) ≥ 5, 3 (6)
gdje je Na 2 SO 4, Na 2 CO 3, Na 3 PO 4, NaNO 3, NaOH - sadržaj natrijevog sulfata, natrijevog karbonata, natrijevog fosfata, natrijevog nitrata i natrijevog hidroksida, respektivno, mg / kg.
Trenutno proizvedeni kotlovi nemaju barem jedan od ovih uvjeta korozije.
Prisutnost silicijevih spojeva u kotlovskoj vodi također može pojačati intergranularnu koroziju.
NaCl u ovim uvjetima nije inhibitor korozije. Gore je prikazano: ioni klora (Sl -) su akceleratori korozije, zbog svoje velike pokretljivosti i male veličine, lako prodiru kroz zaštitne oksidne filmove i stvaraju vrlo topljive soli sa željezom (FeCl 2, FeCl 3) umjesto slabo topljivih željeznih oksida .
U vodi kotlovnica tradicionalno se kontroliraju vrijednosti ukupne mineralizacije, a ne sadržaj pojedinačnih soli. Vjerojatno je iz tog razloga uvedeno racioniranje ne prema naznačenom omjeru (6), već prema vrijednosti relativne alkalnosti kotlovske vode:
SH kv rel = SH ov rel = SH ov 40 100/S ov ≤ 20, (7)
gdje je U q rel - relativna alkalnost kotlovske vode,%; Shch ov rel - relativna alkalnost pročišćene (dodatne) vode, %; Sh ov - ukupna lužnatost pročišćene (dodatne) vode, mmol/l; S ov - mineralizacija obrađene (dodatne) vode (uključujući sadržaj klorida), mg/l.
Ukupna alkalnost tretirane (dodatne) vode može se uzeti jednakom, mmol/l:
- nakon kationizacije natrija - ukupna lužnatost izvorne vode;
- nakon vodik-natrijeve kationizacije paralelno - (0,3-0,4), ili uzastopno s "gladnom" regeneracijom vodikovo-kationitnog filtra - (0,5-0,7);
- nakon kationizacije natrija uz zakiseljavanje i ionizaciju natrijevog klora - (0,5-1,0);
- nakon amonij-natrijeve kationizacije - (0,5-0,7);
- nakon kamencanja na 30-40 ° C - (0,35-1,0);
- nakon koagulacije - (W o ref - D do), gdje je W o ref - ukupna lužnatost izvorne vode, mmol/l; D do - doza koagulansa, mmol/l;
- nakon natrijevog vapna na 30-40 °C - (1,0-1,5), i na 60-70 °C - (1,0-1,2).
Vrijednosti relativne alkalnosti kotlovske vode prema normama Rostekhnadzora prihvaćaju se,%, ne više od:
- za kotlove sa zakovicama - 20;
- za kotlove sa zavarenim bubnjevima i cijevima umotanim u njih - 50;
- za kotlove sa zavarenim bubnjevima i cijevima zavarenim na njih - bilo koje vrijednosti, nije standardizirano.
Riža. 4. Rezultat intergranularne korozije
Prema normama Rostekhnadzora, U kv rel je jedan od kriterija za siguran rad kotlova. Ispravnije je provjeriti kriterij potencijalne alkalne agresivnosti kotlovske vode, koji ne uzima u obzir sadržaj iona klora:
K u = (S ov - [Sl - ]) / 40 u ov, (8)
gdje je K u - kriterij potencijalne alkalne agresivnosti kotlovske vode; S s - salinitet tretirane (dodatne) vode (uključujući sadržaj klorida), mg/l; Cl - - sadržaj klorida u tretiranoj (dodatnoj) vodi, mg/l; Sh ov - ukupna lužnatost pročišćene (dodatne) vode, mmol/l.
Vrijednost K u može se uzeti:
- za kotlove s zakovanim bubnjevima s tlakom većim od 0,8 MPa ≥ 5;
- za kotlove sa zavarenim bubnjevima i cijevima umotanim u njih s tlakom većim od 1,4 MPa ≥ 2;
- za kotlove sa zavarenim bubnjevima i na njih zavarenim cijevima, kao i za kotlove sa zavarenim bubnjevima i cijevima umotanim u njih s tlakom do 1,4 MPa i kotlovima sa zakovanim bubnjevima s tlakom do 0,8 MPa - ne normirati.
Podmuljna korozija
Ovaj naziv kombinira nekoliko različitih vrsta korozije (alkalne, kisikove itd.). Nakupljanje labavih i poroznih naslaga i mulja u različitim zonama kotla uzrokuje koroziju metala ispod mulja. Glavni razlog: onečišćenje napojne vode željeznim oksidima.
Nitritna korozija
. Zaslon i kotlovske cijevi kotla na strani okrenutoj prema peći.
Vrsta i priroda oštećenja. Rijetki, oštro ograničeni veliki ulkusi.
. U prisutnosti nitritnih iona (NO - 2) u napojnoj vodi više od 20 μg / l, temperatura vode je veća od 200 ° C, nitriti služe kao katodni depolarizatori elektrokemijske korozije, obnavljajući se u HNO 2, NO, N 2 (vidi gore).
Parno-vodena korozija
Mjesta oštećenja metala od korozije. Izlazni dio zavojnica pregrijača, cjevovodi pregrijane pare, horizontalne i blago nagnute cijevi za generiranje pare u područjima slabe cirkulacije vode, ponekad uz gornju generatricu izlaznih svitaka ekonomajzera kipuće vode.
Vrsta i priroda oštećenja. Plakovi gustih crnih oksida željeza (Fe 3 O 4), čvrsto vezani za metal. S fluktuacijama temperature, kontinuitet plaka (kore) je prekinut, ljuske otpadaju. Ujednačeno stanjivanje metala s izbočinama, uzdužnim pukotinama, lomovima.
Može se identificirati kao korozija ispod kaše: u obliku dubokih jama s nejasno omeđenim rubovima, češće u blizini zavarenih spojeva koji strše unutar cijevi, gdje se nakuplja kaša.
Uzroci oštećenja od korozije:
- medij za pranje - para u pregrijačima, parnim cjevovodima, parnim "jastucima" ispod sloja mulja;
- temperatura metala (čelik 20) je veća od 450 ° C, toplinski tok u metalni dio je 450 kW / m 2;
- kršenje načina izgaranja: troska plamenika, povećana kontaminacija cijevi iznutra i izvana, nestabilno (vibracijsko) izgaranje, produljenje baklje prema cijevima zaslona.
Kao rezultat: izravna kemijska interakcija željeza s vodenom parom (vidi gore).
Mikrobiološka korozija
Uzrokuju ga aerobne i anaerobne bakterije, javlja se na temperaturama od 20-80 °C.
Mjesta oštećenja metala. Cijevi i posude do bojlera s vodom navedene temperature.
Vrsta i priroda oštećenja. Tuberkuli različitih veličina: promjer od nekoliko milimetara do nekoliko centimetara, rijetko - nekoliko desetaka centimetara. Tuberkule su prekrivene gustim željeznim oksidima – otpadnim produktom aerobnih bakterija. Unutar - crni prah i suspenzija (željezni sulfid FeS) - proizvod anaerobnih bakterija koje reduciraju sulfate, ispod crne formacije - okrugli ulkusi.
Uzroci oštećenja. U prirodnoj vodi uvijek su prisutni željezni sulfati, kisik i razne bakterije.
Željezne bakterije u prisutnosti kisika stvaraju film od željeznih oksida, ispod kojeg anaerobne bakterije reduciraju sulfate u željezni sulfid (FeS) i sumporovodik (H 2 S). Zauzvrat, sumporovodik dovodi do stvaranja sumporne (vrlo nestabilne) i sumporne kiseline, a metal korodira.
Ova vrsta korozije ima neizravan učinak na koroziju kotla: protok vode brzinom od 2-3 m / s otkida tuberkule, nosi njihov sadržaj u kotao, povećavajući nakupljanje mulja.
U rijetkim slučajevima, ova korozija može nastati u samom kotlu, ako se tijekom dugog zaustavljanja kotla u rezervi napuni vodom temperature 50-60 ° C, a temperatura se održava zbog slučajnog prodora pare iz susjedni kotlovi.
"Kelirana" korozija
Mjesta oštećenja od korozije. Oprema u kojoj se para odvaja od vode: bubanj kotla, separatori pare u i izvan bubnja, također - rijetko - u cjevovodu napojne vode i ekonomajzeru.
Vrsta i priroda oštećenja. Površina metala je glatka, ali ako se medij kreće velikom brzinom, tada korodirana površina nije glatka, ima udubljenja u obliku potkove i "repove" orijentirane u smjeru kretanja. Površina je prekrivena tankim mat ili crnim sjajnim filmom. Nema očitih naslaga, a nema ni produkata korozije, jer je "kelat" (organski spojevi poliamina posebno uneseni u kotao) već reagirao.
U prisutnosti kisika, što se rijetko događa u kotlu koji normalno radi, korodirana površina se "razveseli": hrapavost, metalni otoci.
Uzroci oštećenja od korozije. Mehanizam djelovanja "kelata" opisan je ranije ("Industrijske i toplinske kotlovnice i mini-CHP", 1 (6) ΄ 2011, str. 40).
Korozija "kelata" nastaje kada je predoziranje "kelatom", ali čak i pri normalnoj dozi moguće, budući da je "kelat" koncentriran u područjima gdje dolazi do intenzivnog isparavanja vode: nukleatno vrenje zamjenjuje se filmastim. U uređajima za odvajanje pare postoje slučajevi posebno destruktivnog djelovanja "kelatne" korozije zbog velikih turbulentnih brzina vode i smjese pare i vode.
Sva opisana oštećenja od korozije mogu imati sinergijski učinak, tako da ukupna šteta od kombiniranog djelovanja različitih korozijskih čimbenika može premašiti iznos štete od pojedinih vrsta korozije.
U pravilu, djelovanje korozivnih sredstava pojačava nestabilni toplinski režim kotla, što uzrokuje korozijski zamor i pobuđuje koroziju toplinskog zamora: broj pokretanja iz hladnog stanja je veći od 100, ukupan broj pokretanja je veći od 200 Budući da su ove vrste razaranja metala rijetke, pukotine, puknuće cijevi imaju izgled identičan metalnim lezijama od raznih vrsta korozije.
Obično su za utvrđivanje uzroka razaranja metala potrebne dodatne metalografske studije: rendgenska, ultrazvučna, boja i detekcija kvarova magnetskim prahom.
Različiti istraživači su predložili programe za dijagnosticiranje vrsta oštećenja od korozije na kotlovskim čelicima. Program VTI (A.F. Bogachev i suradnici) poznat je - uglavnom za visokotlačne kotlove, a razvoj udruge Energochermet - uglavnom za nisko- i srednjetlačne kotlove i kotlove na otpadnu toplinu.