Ventilator za podizanje kotla TPP 210 a. Razvoj dizajna OAO TKZ "Krasny Kotelshchik" za uvođenje novih tehnologija za izgaranje krutih goriva u pećima parnih kotlova. Postupno izgaranje krutih goriva
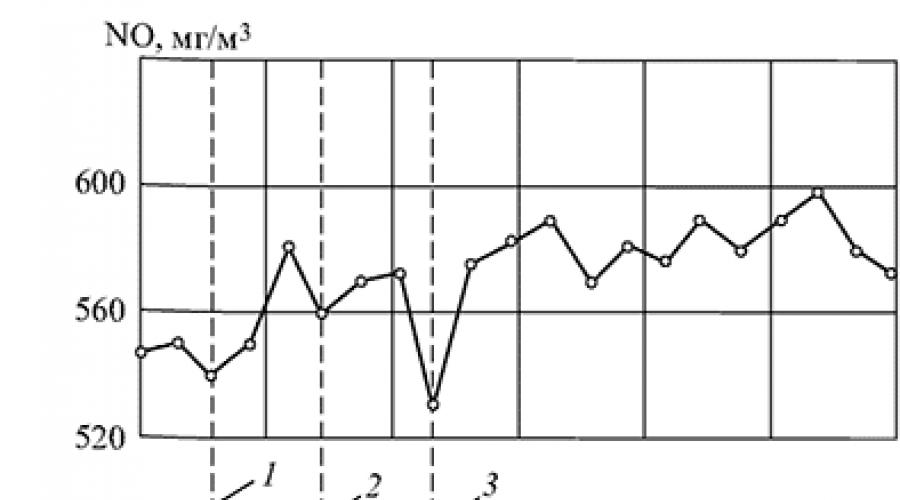
Pročitajte također
Protočni parni kotao TPP-210A razmatra se kao predmet regulacije, analiziraju se postojeći sustavi upravljanja, uočavaju se njegove prednosti i nedostaci, predlaže se strukturni dijagram regulatora toplinskog opterećenja kotla TPP-210A na plinovito gorivo. pomoću regulacijskog mikroprocesorskog kontrolera Remikont R-130
Proračun parametara postavki i modeliranje procesa regulacije toplinskog opterećenja kotla TPP-210A na plinovito gorivo, uključujući, aproksimaciju eksperimentalnih podataka i modeliranje kontrolnog objekta za sustav upravljanja s dvije petlje, proračun postavke sustava upravljanja s dvije petlje, kao i simulacija prijelaznog procesa u regulaciji sustava s dvije petlje. Provedena je komparativna analiza dobivenih prijelaznih karakteristika.
Izvod iz teksta
Po stupnju automatizacije, termoenergetika zauzima jedno od vodećih mjesta među ostalim industrijama. Termoelektrane karakterizira kontinuitet procesa koji se u njima odvijaju. Gotovo svi poslovi u termoelektranama su mehanizirani i automatizirani.
Automatizacija parametara pruža značajne prednosti
Popis korištene literature
Bibliografija
1. Grigoriev V.A., Zorin V.M. „Termoelektrane i nuklearne elektrane“. Imenik. — M.: Energoatomizdat, 1989.
2. Pletnev G. P. Automatizirani upravljački sustavi za termoelektrane: Udžbenik za sveučilišta / G. P. Pletnev. - 3. izd., prerađeno. i dodatni — M.: Ed. MPEI, 2005, - 355 s
3. Pletnev T.P. Automatizacija tehnoloških procesa i proizvodnje u termoenergetici. /MPEI. M, 2007. 320 str.
4. Malokanalni višenamjenski regulacijski mikroprocesorski kontroler Remikont R-130″ Komplet dokumentacije YALBI.421 457.001TO 1−4
5. Pletnev G.P. Zaichenko Yu.P. "Projektiranje, ugradnja i rad automatiziranih upravljačkih sustava za toplinske i energetske procese" MPEI 1995 316 s.- ill.
6. Rotach V.Ya. Teorija automatskog upravljanja toplinskim i energetskim procesima, - M .: MPEI, 2007. - 400s.
7. Kozlov O.S. i dr. Programski kompleks "Modeliranje u tehničkim uređajima" (PK "MVTU", verzija 3.7).
Korisnički priručnik. - M .: MSTU im. Bauman, 2008. (monografija).
Fil S. A., Golyshev L. V., inženjeri, Mysak I. S., doktor tehničkih nauka. sci., Dovgoteles G. A., Kotelnikov I. I., Sidenko A. P., inženjeri JSC LvovORGRES - Nacionalno sveučilište "Lviv Polytechnic" - Trypilska TPP
Izgaranje kamenog ugljena niske reaktivnosti (Vdaf< 10%) в камерных топках котельных установок сопровождается повышенным механическим недожогом, который характеризуется двумя показателями: содержанием горючих в уносе Гун и потерей тепла от механического недожога q4.
Goon se obično određuje laboratorijskom metodom na pojedinačnim uzorcima pepela uzetim iz plinskih kanala posljednje konvektivne površine kotla uz korištenje redovitih instalacija za ispuhivanje. Glavni nedostatak laboratorijske metode je predugo kašnjenje u dobivanju Gong rezultata (više od 4 - 6 sati), što uključuje vrijeme sporog nakupljanja uzorka pepela u instalaciji za ispuhivanje i trajanje laboratorijskog rada. analiza. Tako se u jednom uzorku pepela sve moguće promjene u gongu dugo sumiraju, što otežava brzu i učinkovitu prilagodbu i optimizaciju režima izgaranja.
Prema podacima u promjenjivim i nestacionarnim načinima rada kotla, koeficijent sakupljanja pepela (stupanj pročišćavanja) ciklone izvedbenog podešavanja mijenja se u rasponu od 70 - 95%, što dovodi do dodatnih grešaka u određivanje gonga.
Nedostaci instalacija letećeg pepela prevladavaju se uvođenjem kontinuiranih sustava mjerenja gonga, kao što su analizatori ugljika u letećem pepelu.
2000. godine osam kompleta (po dva za svaku posudu) stacionarnih kontinuirano djelujućih analizatora RCA-2000 proizvođača Mark and Wedell (Danska).
Princip rada analizatora RCA-2000 temelji se na fotoapsorpcijskoj metodi analize u infracrvenom području spektra.
Raspon mjerenja 0 - 20% apsolutnih vrijednosti Gonga, relativna pogreška mjerenja u rasponu od 2 - 7% - ne više od ± 5%.
Uzorkovanje pepela za mjerni sustav analizatora vrši se iz plinskih kanala ispred elektrofiltera.
Kontinuirano snimanje gonga provedeno je na samosnimajućem uređaju kontrolne sobe s frekvencijom potpunog ciklusa mjerenja u 3 minute.
Kod spaljivanja pepela različitog sastava i kvalitete stvarne apsolutne vrijednosti Gonga u pravilu su prelazile 20%. Stoga se trenutno koriste analizatori kao indikatori promjena relativnih vrijednosti sadržaja gorivih materija u zahvatu Gv° unutar skale registratora 0 - 100%.
Za grubu procjenu stvarne razine Gonga sastavljena je kalibracijska karakteristika analizatora, a to je odnos između apsolutnih vrijednosti Gonga utvrđenih laboratorijskom metodom i relativnih vrijednosti analizatora G°Gong. U rasponu promjene gonga od 20 do 45%, karakteristika je u analitičkom obliku izražena jednadžbom
Tijekom eksperimentalnih istraživanja i normalnog rada kotla, analizatori se mogu koristiti za obavljanje sljedećih radova:
optimizacija načina izgaranja;
ocjenjivanje promjene gonga tijekom planiranog tehnološkog prebacivanja sustava i jedinica kotlovnice;
određivanje dinamike i razine smanjenja učinkovitosti u nestacionarnom i poststartnom režimu rada kotla, kao iu slučaju naizmjeničnog izgaranja ASh i prirodnog plina.
Tijekom razdoblja termičkog ispitivanja kotla, analizatori su korišteni za optimizaciju načina izgaranja i procjenu učinka planiranog uključivanja opreme na stabilnost procesa izgaranja ugljena u prahu.
Eksperimenti su provedeni pri stacionarnom opterećenju kotla u rasponu od 0,8-1,0 nominalnog i izgaranju ASh sa sljedećim karakteristikama: niža specifična toplina izgaranja Qi = 23,06 - 24,05 MJ/kg (5508 - 5745 kcal/kg), sadržaj pepela po radnoj masi Ad = 17,2 - 21,8 %, vlažnost na radnu masu W = 8,4 - 11,1 %; udio prirodnog plina za rasvjetu plamena prašnog ugljena iznosio je 5-10% ukupnog oslobađanja topline.
Dani su rezultati i analiza eksperimenata optimizacije načina izgaranja pomoću analizatora. Prilikom postavljanja kotla optimizirano je sljedeće:
izlazne brzine sekundarnog zraka mijenjanjem otvaranja perifernih vrata u plamenicima;
izlazne brzine primarnog zraka promjenom opterećenja ventilatora vrućeg puhanja;
udio osvjetljenja plamena prirodnim plinom odabirom (prema uvjetima za osiguranje stabilnosti izgaranja) minimalnog mogućeg broja plinskih plamenika koji rade.
Glavne karakteristike procesa optimizacije načina izgaranja dane su u tablici. jedan.
Dato u tablici. 1, podaci ukazuju na važnu ulogu analizatora u procesu optimizacije, koji se sastoji u kontinuiranom mjerenju i registraciji aktualnih informacija o promjeni H°h, što omogućuje pravovremeno i
jasno utvrditi optimalni način rada, završetak procesa stabilizacije i početak rada kotla u optimalnom načinu rada.
Prilikom optimizacije načina izgaranja, glavna pažnja posvećena je pronalaženju najniže moguće razine relativnih vrijednosti H°un. U ovom slučaju, apsolutne vrijednosti gonga određene su kalibracijskim karakteristikama analizatora.
Dakle, učinkovitost primjene analizatora za optimizaciju načina izgaranja kotla može se grubo procijeniti smanjenjem sadržaja gorivih tvari u zahvatu za prosječno 4% i gubitkom topline od mehaničkog dogaranja za 2%.
U stacionarnim načinima rada kotla, redovito tehnološko prebacivanje, na primjer, u sustavima za prašinu ili plamenicima, remeti proces stabilnog izgaranja ugljena u prahu.
stol 1
Obilježja procesa optimizacije načina izgaranja
Kotao TPP-210A opremljen je s tri sustava za prašinu s mlinovima s kugličnim bubnjem tipa ShBM 370/850 (Sh-50A) i zajedničkom posudom za prašinu.
Iz sustava za prašinu istrošeno sredstvo za sušenje ispušta se u komoru za izgaranje (predpeć) pomoću mlinskog ventilatora tipa MB 100/1200 kroz posebne ispusne mlaznice smještene iznad glavnih plamenika za prašinu i plin.
Predpeć svakog tijela kotla prima puni ispust iz odgovarajućeg vanjskog sustava prašine i polovicu ispusta iz srednjeg sustava prašine.
Istrošeno sredstvo za sušenje je niskotemperaturni vlažni i prašnjavi zrak, čiji su glavni parametri u sljedećim granicama:
udio otpadnog zraka je 20 - 30% ukupne potrošnje zraka tijela (kotla); temperatura 120 - 130°C; udio sitne ugljene prašine, koja nije zahvaćena ciklonom sustava prašine, 10 - 15% produktivnosti mlina;
vlažnost odgovara količini vlage koja se oslobađa tijekom procesa sušenja mljevenog radnog goriva.
Istrošeno sredstvo za sušenje ispušta se u zonu maksimalnih temperatura plamena i stoga značajno utječe na potpunost izgaranja ugljene prašine.
Tijekom rada kotla najčešće se zaustavlja i ponovno pokreće srednji sustav prašine, uz pomoć kojeg se održava potrebna razina prašine u industrijskom bunkeru.
Prikazana je dinamika promjena glavnih pokazatelja režima izgaranja tijela kotla - sadržaja gorivih tvari u zahvatu i masene koncentracije dušikovih oksida u dimnim plinovima (NO) - tijekom planiranog isključivanja srednjeg sustava prašine. na sl. jedan.
Na gornjim i svim sljedećim slikama prihvaćaju se sljedeći uvjeti pri izradi grafičkih ovisnosti:
sadržaj gorivih tvari u zahvatu odgovara vrijednostima ljestvica dviju vertikalnih osi koordinata: prosječnih mjerenja Gonga i podataka ponovnog izračuna prema kalibracijskoj karakteristici Gong;
masena koncentracija NO s viškom zraka u ispušnim plinovima (bez redukcije na NO2) uzeta je iz kontinuirano snimanih mjerenja stacionarnog plinskog analizatora Mars-5 MP "Ekomak" (Kijev);
dinamika promjena H°un i NO je fiksirana
tijekom cijelog razdoblja tehnološkog rada i režima stabilizacije; početak tehnološke operacije uzima se u blizini nulte vremenske reference.
Potpunost izgaranja goriva od praha procijenjena je kvalitetom načina izgaranja (KTR), koji je analiziran pomoću dva indikatora Gong i NO, koji su se u pravilu mijenjali u zrcalno suprotnim smjerovima.
Riža. 1. Promjene u indikatorima načina izgaranja kada je srednji sustav prašine zaustavljen
Analiziran je utjecaj planiranog gašenja sustava srednje prašine na pokazatelje KTP (slika 1.) ovisno o slijedu sljedećih tehnoloških operacija:
Operacija 1 - gašenje dovoda sirovog ugljena (CFC) i zaustavljanje dovoda ugljena u mlin smanjilo je opterećenje bubnja SBM, smanjilo finoću ugljene prašine i povećalo temperaturu odvodnog zraka, što je uzrokovalo kratkotrajnost. dugoročno poboljšanje CTE: smanjenje Hn° i povećanje NO; proces daljnje emaskulacije mlina pridonio je uklanjanju prašine iz otpadnog zraka i povećanju viška zraka u pretpeći, što je negativno utjecalo na CTE;
operacija 2 - zaustavljanje SHM-a i smanjenje ventilacije sustava za prašinu najprije je malo poboljšalo CTE, a zatim se, uz kašnjenje s isključenjem ventilatora mlina (MF), CTE pogoršalo;
operacija 3 - zaustavljanje MW i zaustavljanje ispuštanja istrošenog sredstva za sušenje u komoru za izgaranje značajno je poboljšalo CTE.
Dakle, uz sve ostale jednake uvjete, zaustavljanje sustava prašine poboljšalo je proces izgaranja goriva, smanjivši mehaničko nedovoljno izgaranje i povećavši masenu koncentraciju NO.
Tipično kršenje stabilnosti sustava za prašinu je preopterećenje bubnja mlina gorivom ili "prljanje" kuglica za mljevenje mokrim glinenim materijalom.
Utjecaj dugotrajne emaskulacije bubnja krajnjeg glodala na CTE tijela kotla prikazan je na sl. 2.
Gašenje PSU-a (operacija 1) iz razloga sličnih onima koji su razmatrani tijekom gašenja sustava za mljevenje, u prvoj fazi emaskulacije mlina, za kratko je vrijeme poboljšalo CTE. U kasnijoj emaskulaciji mlina do uključivanja PSU (operacija 2), postojala je tendencija pogoršanja CTE i rasta G°un.
Riža. Slika 2. Promjene pokazatelja režima izgaranja tijekom emaskulacije bubnja zadnjeg mlina
Riža. 3. Promjene u indikatorima načina izgaranja pri pokretanju posljednjeg sustava za prašinu i gašenju plinskih plamenika
U manjoj mjeri, automatski rad PSU povremeno destabilizira način rada peći, koji regulira potrebno punjenje mlina ugljenom isključivanjem, a zatim uključivanjem pogona PSU.
Utjecaj načina pokretanja sustava ekstremne prašine na KTP prikazan je na sl. 3.
Uočen je sljedeći utjecaj pokretanja sustava za prašinu na način izgaranja:
Operacija 1 - pokretanje MW i ventilacija (zagrijavanje) putanje sustava za prašinu s ispuštanjem relativno hladnog zraka u pretpeć povećalo je višak zraka u zoni izgaranja i smanjilo temperaturu plamenika, što je dovelo do pogoršanja u CTE;
operacija 2 - pokretanje SHBM-a i nastavak ventilacije trakta negativno je utjecalo na CTE;
operacija 3 - pokretanje PSU-a i punjenje mlina gorivom uz povećanje nominalne potrošnje sredstva za sušenje značajno je pogoršalo CTE.
Može se zaključiti da uključivanje sustava prašine u rad negativno utječe na CTE, povećavajući mehaničko nedogaranje i smanjujući masenu koncentraciju NO.
Predpeć tijela kotla TPP-210A opremljena je sa šest plamenika za prašinu i plin toplinske snage 70 MW, postavljenih u jednom sloju na prednjem i stražnjem zidu, i dva plinsko-uljna plamenika iznad ložišta. kako bi se osiguralo stabilno uklanjanje tekuće troske u cijelom rasponu radnih opterećenja kotla.
Tijekom sagorijevanja ugljene prašine ASh, prirodni plin je dovođen konstantnim protokom (oko 5% ukupnog oslobađanja topline) u plamenike nadognjišta i promjenjivom brzinom protoka kroz glavne plamenike za prašinu kako bi se stabilizirao proces izgaranja. mljevenog ugljena. Opskrba plinom za svaki glavni plamenik obavljena je pri najmanjoj mogućoj brzini protoka, koja odgovara 1,0 - 1,5% ukupnog oslobađanja topline. Stoga je promjena udjela prirodnog plina za rasvjetu baklji provedena paljenjem ili gašenjem određenog broja glavnih plinskih plamenika.
Učinak gašenja plinskih plamenika (smanjenje udjela prirodnog plina) na CTE tijela kotla prikazan je na sl. 3.
Uzastopno gašenje najprije jednog plinskog plamenika (operacija 4), a zatim i tri plinska plamenika (operacija 5) pozitivno je utjecalo na CTE i dovelo do značajnog smanjenja mehaničkog potpaljivanja.
Učinak uključivanja plinskih plamenika (povećanje udjela prirodnog plina) na CTE prikazan je na sl. 4. Uzastopno uključivanje jednog plinskog plamenika (rad 1), dva plamenika (operacija 2) i jednog plamenika (operacija 3) negativno je utjecalo na CTE i značajno povećalo mehaničko nedogaranje.
Riža. 4. Promjena indikatora načina izgaranja kada su plinski plamenici uključeni
tablica 2
Promjene u sadržaju gorivih tvari u prijenosu tijekom tehnološkog prebacivanja opreme
Oprema | Način rada | ||
smanjenje | povećati |
||
Sustav ekstremne/srednje prašine | |||
kastracija | Hitno | ||
sirova hranilica | |||
Glavni plinski plamenik | Ugasiti | ||
Uključenje, Ubrajanje |
Približna procjena utjecaja dokazanog tehnološkog prebacivanja kotlovske opreme na promjenu CTE (Kun) sažeta je u tablici. 2.
Analiza zadanih podataka pokazuje da se najveće smanjenje učinkovitosti kotlovskog postrojenja u stacionarnim režimima događa kao posljedica puštanja u rad sustava za prašinu i precijenjene potrošnje prirodnog plina za rasvjetu plamena.
Treba napomenuti da je potreba za izvođenjem puštanja u rad sustava za prašinu određena isključivo tehnološkim razlozima, a precijenjenu potrošnju prirodnog plina za rasvjetu plamena u pravilu postavlja operativno osoblje kako bi se spriječilo moguće kršenja stabilnosti procesa izgaranja u slučaju naglog pogoršanja kvalitete AS.
Korištenje analizatora RCA-2000 omogućuje stalne promjene, pravovremene
procijeniti sve promjene u kvaliteti goriva i konstantno održavati vrijednost osvijetljenosti plamena na odgovarajućoj optimalnoj razini uz minimalnu potrebnu potrošnju prirodnog plina, čime se smanjuje potrošnja oskudnog plinovitog goriva i povećava učinkovitost kotla.
nalazima
- Sustav kontinuiranog mjerenja sadržaja gorivih tvari u elektrofilterskom pepelu omogućuje brzu i kvalitetnu procjenu tijeka procesa izgaranja pri izgaranju AS u kotlu TPP-210A, koji se preporučuje za korištenje tijekom puštanja u rad i istraživačkih radova, kao i za sustavno praćenje učinkovitosti kotlovske opreme.
- Učinkovitost korištenja analizatora RCA-2000 za optimizaciju načina izgaranja okvirno se procjenjuje smanjenjem pokazatelja mehaničkog nedozgaranja - sadržaja gorivih materija u zahvatu za prosječno 4% i, sukladno tome, gubitka topline od mehaničkog dogaranja za 2% .
- U stacionarnim načinima rada kotla, redovito tehnološko prebacivanje opreme utječe na kvalitetu procesa izgaranja. Puštanje u rad sustava za prašinu i precijenjena potrošnja prirodnog plina za paljenje plamenika s prahom značajno smanjuju učinkovitost kotlovnice.
Bibliografija
- Madoyan A. A., Baltyan V. N., Grechany A. N. Učinkovito izgaranje niskokvalitetnog ugljena u energetskim kotlovima. Moskva: Energoatomizdat, 1991.
- Korištenje analizatora zapaljivog sadržaja RCA-2000 u prijenosu i analizatora plina Mars-5 za optimizaciju načina izgaranja kotla TPP-210A Tripolskaya TPP / Golyshev L. V., Kotelnikov N. I., Sidenko A. P. et al. - Tr. Kijevski politehnički institut. Energija: ekonomija, tehnologija, ekologija, 2001, br.
- Zusin S. I. Promjena toplinskih gubitaka s mehaničkim dogaranjem ovisno o načinu rada kotlovske jedinice. - Termoenergetika, 1958, br.10.
Kratak opis kotlovske jedinice "Protočni kotao tipa TPP-210"
Kratak opis kotlovske jedinice Protočni kotao tipa TPP-210 (p / p 950-235 GOST 3619-59 model TKZ TPP-210) s kapacitetom pare od 950 tona na sat za superkritične parametre pare projektirao je i proizveo Taganrog biljka "Krasny Kotelshchik". Kotlovska jedinica je dizajnirana za rad u jedinici s kondenzacijskom turbinom K-300-240 kapaciteta 300 MW, proizvođača KhTGZ. Kotao je predviđen za sagorijevanje antracitnog mulja s uklanjanjem tekućeg pepela i prirodnog plina iz Shebelinsky ležišta. Kotlovski agregat je dvokućište s rasporedom svakog kućišta u obliku slova U i regenerativnim grijačima zraka uklonjenim ispod kotla, koji se nalaze izvan zgrade kotlovnice. Školjke kotlova iste izvedbe kapaciteta 475 t/h pare svaka. Trupovi mogu raditi neovisno jedan o drugom. Opći podaci o kotlu: Produktivnost 475 t/h Temperatura pregrijane pare: primarna 565 °C Sekundarna 565 °C Potrošnja sekundarne pare 400 t/h Tlak primarne pare iza kotla 255 kg/cm² Sekundarni tlak pare na ulazu u kotao 39,5 kg/ cm² Tlak sekundarne pare na izlazu iz kotla 37 kg/cm² Temperatura sekundarne pare na ulazu 307 °C Temperatura napojne vode 260 °C Temperatura vrućeg zraka 364 °C Ukupna težina metala kotla 3438 t Širina kotla duž osi stupa 12 m Dubina kotla po osi stuba 19 m Visina kotla 47 m Volumen vode kotlovske jedinice u hladnom stanju 243 m³ Dimenzije peći u tlocrtu (duž osi cijevi): primarna i sekundarna para na izlazu je smanjen na 545 °C) Kotao opslužuju dva aksijalna dimovoda, dva puhala s dvobrzinskim motorima i dva ventilatora vrućeg puhanja. Shema pripreme prašine s bunkerom i transporta prašine do plamenika toplim zrakom. Kotao je opremljen s tri kuglasta mlina s bubnjem ShBM-50 kapaciteta 50 tona prašine na sat. Grijaće površine: rešetke peći 1317 m² Uključujući: NRCh 737 m² THR 747 m² Zasloni za reverznu komoru i strop 1674 m² Pregrijač SVD: uključujući: Parni izmjenjivač topline 800 m² Međukonvektivni paket 1994 m² Konvektivni paket 1994 m² konvektivni 1994m² 1994 m² konvektivni paket 1994m²
U svakom tijelu kotla nalaze se dva toka (u opisu kotla i u uputama mlaz se naziva navoj). Budući da je dizajn trupa sličan, u budućnosti će biti opisana shema i dizajn jednog trupa. Napojna voda s temperaturom od 260 °C prolazi kroz pogonsku jedinicu i ulazi u ulazne komore ekonomajzera vode Sh325*50, koje su ujedno i ekstremne potporne grede paketa. Nakon prolaska kroz zavojnice ekonomajzera vode, voda s temperaturom od 302 ° C ulazi u izlazne komore Š235*50, koje su srednje potporne grede ove površine. Nakon vodnog ekonomajzera voda se obilaznim cijevima Š159*16 usmjerava na srednje potporne grede ove površine kroz cijevi Š133*15 do donjeg dijela (NRČ). NRC ekrani se sastoje od zasebnih ploča, a grijaće površine ložišta čine jednodijelne višeprolazne trake s prednje i stražnje strane. Dovod vode do ploča vrši se kroz donju komoru, a odvodnju iz gornje. Ovakav raspored ulaznih i izlaznih komora poboljšava hidraulički učinak ploče. Dijagram toka medija kroz NRC zaslone je sljedeći: Prvo, medij ulazi u stražnje ploče zaslona i stražnje ploče bočnog zaslona, a zatim se premosnikom usmjerava na prednji zaslon i prednje ploče bočnih zaslona cijevi Š 135*15. Podloške Ø30 mm ugrađuju se na obilazne cijevi radi poboljšanja hidrodinamike. Nakon LFC-a, medij s temperaturom od 393 °C šalje se cijevima Š133*15 do vertikalnog kolektora Š273*45, a odatle preko premosnih cijevi Š133* ulazi u bočne i prednje zaslone gornjeg dijela zračenja (RTC). 15. Relativni položaj ulaznih i izlaznih komora TRC ploča sličan je položaju RRC ploča. Prolazeći kroz višeprolazne ploče prednjeg i bočnog zaslona TCG-a, para se usmjerava obilaznim cijevima Š133*15 do okomitog razdjelnika za miješanje Š325*45, a odatle ulazi u ploče u obliku slova N stražnjeg zaslona. TRC-a kroz cijevi Š159*16.
Nakon što je prošao višeprolazne ploče prednjeg i bočnog zaslona TRC-a, para se usmjerava obilaznim cijevima Sh133 * 15 na vertikalni razdjelnik za miješanje Sh325 * 45, a nakon zagrijavanja na 440 ° C u blistave površine peći, para se usmjerava na panele zaštitnih bočnih i stražnjih zidova rotacijskih kamera. Prolazeći kroz zaslone reverzne komore, para ulazi kroz cijevi u 1 injekcioni odogrijač Š279*36. U 1 injekcionom odsparivaču, tokovi se prenose po širini dimnog kanala. Nakon pregrijača, para se dovodi do stropnog pregrijača cijevima Š159*16. U stropnom pregrijaču para se kreće od stražnje stijenke dimovodne cijevi prema prednjoj strani kotla i ulazi u izlazne komore stropa Š273*45 s temperaturom od 463 °C. Na parovodima Š273*39, koji su nastavak izlaznih komora stropnog pregrijača, ugrađuju se ventili (VZ) DU-225 ugrađeni u trakt. Nakon stropnog pregrijača, tokovi se prenose po širini plinskog kanala, a para se kroz cijevi Š159*18 usmjerava na ulazna sita prvog stupnja sita pregrijača, koji se nalazi u srednjem dijelu plinskog kanala. Prolaskom kroz ulazne rešetke, para s temperaturom od 502 °C ulazi u drugi injekcioni odpregrijavač Ø325*50, nakon čega se usmjerava na izlazne rešetke prvog stupnja, smještene uz rubove dimovodne cijevi. Komora za primanje pare ulaznih sita i parni vod drugog odzračivača provode prijenos tokova duž širine dimnog kanala. Prije drugog ubrizgavanja postoji parovod Š194*30 za odvođenje dijela pare HPS-a u plinsko-parni izmjenjivač topline, a nakon injektiranja parovod za vraćanje te pare. Drugi odogrijač za ubrizgavanje ima potpornu podlošku. Iza izlaznih sita prvog stupnja nalazi se treći injektorski odogrijač Ø325*50, čiji parni cjevovod prenosi tokove po širini dimovoda. Para se zatim usmjerava na srednje dijelove plinskog kanala i nakon prolaska kroz njih prenosi se parovodom Š325*60 s temperaturom od 514 °C po širini plinskog kanala do izlaznih sita drugog stupanj, smješten uz rubove plinskog kanala. Nakon izlaznih sita drugog stupnja, para s temperaturom od 523 °C ulazi u četvrti injekcioni odpregrijavač Š325*60. I ulazna i izlazna sita oba stupnja sitog pregrijača imaju kostrujnu shemu međusobnog kretanja pare i plinova. Nakon parogrijača, para s temperaturom od 537 °C kroz parovod Š237 * 50 ulazi u konvektivni paket koji je izrađen po sustrujnoj shemi, prolazi kroz njega s temperaturom od 545 °C i dovodi se u turbina. Počevši od ulaznih komora ekonomajzera vode, sve obilazne cijevi i komore SVD trakta izrađene su od čelika 12Kh1MF. Nakon HPC-a turbine, para s tlakom od 39,5 atm. Temperatura od 307 °C šalje se u međupregrijač u dva toka. Jedan "hladni" vod niskotlačne pare prilazi tijelu; oni se prije grijača dijele na dva dijela. U grijaču svakog kućišta postoje dva niskotlačna toka pare s neovisnom regulacijom temperature duž navoja. Izvedba kotla Zidovi komore za izgaranje u potpunosti su zaštićeni cijevima zračećih grijaćih površina. Komora za izgaranje svakog tijela podijeljena je štipaljkama koje čine izbočine prednjeg i stražnjeg zaslona na komoru za izgaranje (predpeć) i naknadno izgaranje. Zasloni u predpećnom prostoru do el. 15.00 potpuno načičkana i prekrivena kromitnom masom. Izolacija komore za izgaranje i stiska u peći smanjuje prijenos topline zračenja iz jezgre baklje, što povećava razinu temperature u predpeći i stoga poboljšava uvjete za paljenje i izgaranje goriva, a također i doprinosi boljem stvaranju tekuće troske. Proces izgaranja AS odvija se uglavnom u predpeći, međutim, izgaranje se nastavlja u naknadnom izgaranju, gdje se mehaničko dogorjevanje smanjuje sa 7,5-10% na 2,5%. Na istom mjestu temperatura plinova se smanjuje na 1210 °C, što osigurava rad grijaćih površina, SVD pregrijača bez troske. Toplinsko naprezanje cjelokupnog volumena peći je Vt=142*103 kcal m 3 /sat, a predpećnog Vtp=491*103 kcal mí/sat.
Peć svake od dvije zgrade opremljena je s 12 prašno-plinskih turbulentnih plamenika raspoređenih u dva reda (po tri plamenika u svakom sloju prednje i stražnje stijenke peći). Dovod plina do plamenika je periferni, učinak plamenika na prašinu je 0,5 t/h. Svaki turbulentni plamenik ima ugrađenu mehaničku mlaznicu za raspršivanje ulja s hlađenjem i organiziranim dovodom zraka. Za odstranjivanje tekuće troske pretpeć ima dvije hlađene tape, predpeć je napravljena s nagibom od 80 prema žljebovima i zatvorena je šamotnom opekom. Svaka peć je opremljena s dvije (prema broju zareza) mehanizirane jedinice za uklanjanje troske. Tekuća troska se granulira u vodenim kupelji i uklanja u kanale za pranje troske. Sredstvo za sušenje se ispušta kroz pravokutne plamenike koji se nalaze na bočnim stijenkama pretpeći u dva nivoa: u donjem sloju su 4 plamenika, a u gornjem 2. U peći se nalaze šahtovi za popravke. . Ložište je u donjem dijelu do 23,00 m zaštićeno cijevima donjeg radijacijskog dijela (LRC), au gornjem dijelu - cijevima gornjeg radijacijskog dijela (RTC) sa stropa. Cijevi stražnjeg i prednjeg zaslona NRCH-a imaju zavoje koji tvore stezanje peći. Stražnji zaslon TRC-a u gornjem dijelu ima izbočinu koja poboljšava aerodinamiku protoka plina na izlazu iz peći i djelomično štiti površine zaslona od izravnog zračenja iz peći. Prednji i stražnji zaslon NRCH-a su strukturno identični, svaki zaslon se sastoji od šest identičnih traka, s cijevima spojenim paralelno Sh42 * 6 materijala 12X1MF. Trakaste cijevi se prvo zasjeću ispod i donjeg dijela pretpeći, a zatim prolaze do vertikalne ploče NRCH-a, gdje čine pet prolaza za podizanje i spuštanje i izlaze u gornju komoru. NRCH cijevi su ožičene za puškarnice plamenika, šahtova, peepers. Bočni zasloni NRC-a sastoje se od četiri ploče, koje su izrađene na sljedeći način.
Napuštajući donju komoru, traka, koja se sastoji od 17 paralelno povezanih zavojnica Š42*5, materijala 12H1MF, prvo zaklanja donji dio bočne stijenke, zatim prelazi u okomiti dio, gdje također čini pet pokreta podizanja i spuštanja, te zatim izlazi u gornju komoru. Prednji i stražnji zasloni NFC-a imaju dvije razine fiksnih nosača na razini 22,00 i 14,5 m. Kompenzacija od temperaturnog širenja nastaje zbog savijanja cijevi u štipu. Bočni zasloni su obješeni fiksnim nosačima na 21,9 m i mogu se slobodno spuštati. Kako bi spriječili izlazak pojedinačnih cijevi u peć, zasloni imaju pet pojaseva pomičnih spojnica. Prednji i stražnji zaslon TCG-a također se sastoje od višeprolaznih ploča s pokretima pare za podizanje i spuštanje. Para se dovodi u donju komoru ploča, uklanja se iz gornjih. Srednji paneli prednjeg zaslona i svi paneli bočnih zaslona sastoje se od osam, a krajnji paneli prednjeg zaslona od devet paralelno spojenih cijevi, tvoreći traku. Panel stražnjeg zaslona TCG-a u obliku slova N sastoji se od dvadeset paralelno povezanih cijevi. Sve grijaće površine VRC-a izrađene su od cijevi Š42*5, materijala 12H1MF. Prednji i bočni zaslon TCG-a fiksno su ovješeni na visini od 39,975 m i slobodno se šire prema dolje. Stražnji TCG ekran ima dva fiksna nosača na 8.2 i 32.6. Kompenzacija toplinskog širenja cijevi nastaje zbog savijanja cijevi u gornjem dijelu stražnjeg zaslona TCG-a. Prednji i bočni ekrani imaju sedam redova pomičnih nosača, stražnji - tri. Svi NRC i TRC sita imaju razmak između cijevi od 45 mm. Strop peći i gornji dio vodoravnog dimovoda zaštićeni su cijevima stropnog pregrijača. Ukupno su paralelno spojene 304 cijevi (154 po navoju) Š32*4, materijal 12H1MF. Duž duljine cijevi stropnog pregrijača nalazi se 8 redova pričvršćivača, koji su šipkama pričvršćeni na okvir.
Sita pregrijači Na izlazu iz peći nalazi se sita pregrijač, koji se sastoji od dva reda sita. U nizu od 16 paravana s nagibom od 630 mm, okomito ovješenih. Tijekom pare, zasloni svake faze podijeljeni su na ulaz i izlaz, koji se nalaze bliže bočnim stijenkama plinskog kanala. Strukturno, ulazni i izlazni zasloni prvog stupnja su identični (osim položaja armatura i obilaznih cijevi na komorama). Zaslon prvog stupnja kotla 20 sastoji se od 42 zavojnice Š32*6, materijal cijevi je uglavnom 12H1MF, ali za 11 ekstremnih zavojnica izlazni dio čine cijevi Š32*6, materijal 1H18N12T. Na kotlu 19 sita prvog stupnja sastoji se od 37 zavojnica, materijal 1X18H12T. Kako bi se konstrukciji dala krutost, zaslon je povezan sa svojih 5 zavojnica, koje imaju pričvrsne trake od čelika X20H14S2. Zasloni drugog stupnja sastoje se od 45 zavojnica Š32*6. Materijal ulaznih paravana je 12Kh1MF, a ostatak zavojnica je izrađen od čelika 1Kh18N12T. Zaslon je povezan sa svojih šest zavojnica. Ulazne i izlazne komore, osim komora izlaznih sita drugog stupnja, spojene su u pojedinačne razdjelnike odvojene pregradom. Komore na šipkama obješene su na grede okvira. Zidovi komore za okretanje zaštićeni su s četiri bloka. Blokovi su izrađeni u obliku traka s dvije petlje. U svakom bloku se nalazi 38 paralelno povezanih zavojnica Š32*6 materijala 12H1MF, koje su smještene vodoravno. Blokovi imaju pojaseve za ukrućenje. Ovjes blokova se izvodi pomoću tri reda (po bloku) pričvršćivača. U dovodnom plinskom kanalu nalaze se sljedeće grijaće površine: konvektivni SVD dimnjak, LP pregrijač s plinsko-parnim izmjenjivačem topline i vodeni ekonomizer. Za sve konvektivne površine usvojen je postupni raspored zavojnica. Sve površine su izrađene od zavojnica paralelnih s prednjom stranom kotla.
Konvektivni pregrijač SVD
Paket SVD konvektivnog pregrijača svake linije sastoji se od 129 zavojnica Š32*6, materijala 1H18N12T, koji su oslonjeni na nosače od materijala H23N13, te na nosače hlađene napojnom vodom. Postoje tri reda odstojnika izrađenih od čelika 1X18H12T kako bi izdržali korake i učinili strukturu čvršćom; paket ima visinu od 557 mm. Niskotlačni pregrijač LP pregrijač se nalazi iza konvektivnog paketa SVD-a. Paketi svakog toka nalaze se u odgovarajućim polovicama spusta, prijenos tokova po širini dimovoda se ne provodi. LP pregrijač se sastoji od izlaznog paketa, međupaketa i kontrolnog stupnja. Izlazni dio LP pregrijača sastoji se od 108 visećih svitaka Sh42*3,5, od materijala kombiniranog čelika: Kh2MFSR i 12Kh1MF. Zavojnice su sastavljene u pakete s nosačima, materijal X17H2, koji su ovješeni na potporne razdjelnike visokotlačnog paketa. Visina pakiranja 880 mm. Međupaket također se sastoji od 108 duplih zavojnica Š42*3,5 duplih zavojnica Š42*3,5 materijala 12H1MF. Visina pakiranja 1560 mm. Zavojnice su bazirane na stalcima, materijal Kh17N2, i one na ulaznim komorama međupaketa Sh325 * 50, materijal 12Kh1MF. Tako su ulazne komore industrijskog paketa ujedno i potporne grede za ovu ogrjevnu površinu. Komore, osim izolacije, imaju dodatno hlađenje zrakom potrebno za vrijeme pokretanja i kada je turbina isključena. Iza industrijskog paketa uz tok plina, na oba tijela kotlova TPP-210, umjesto GPP TO, ugrađen je kontrolni stupanj, koji je prvi stupanj pregrijača uz tok pare, izrađen je od perlitnog čelika i , prema uvjetima pouzdanog rada cijevi sa značajnom devaporizacijom, nalazi se u zoni gdje je temperatura plinova na ulazu ne smije biti veća od 600°C. Njegov se rad u potpunosti temelji na promjeni toplinske apsorpcije sekundarne pare promjenom njezine distribucije kroz obilazne parne cjevovode. Prema proračunima, pri nazivnom opterećenju jedinice, 20% ukupnog protoka pare prolazi kroz regulacijski stupanj. Kada se opterećenje jedinice smanji na 70%, potrošnja pare je 88%.Povećanje učinkovitosti pogonskog agregata postiže se proširenjem raspona opterećenja pri kojima se osigurava projektna temperatura sekundarnog pregrijavanja uz optimalan višak zrak. Upravljačka površina je ugrađena u dimenzijama demontiranog GPP TO, ulazni razdjelnici su spušteni 300 mm niže. Upravljačka površina se sastoji od lijevog i desnog dijela ukupne površine grijanja od 2020 m² po tijelu. Oba dijela su sastavljena od paketa dvostrukih zavojnica i imaju 4 petlje duž strujanja plina s protustrujnim uzorkom strujanja pare. Zavojnice su izrađene od cijevi Sh32*4, čelika 12Kh1MF i raspoređene su u šahovnici s koracima od 110 i 30 mm. Zavojnice se sklapaju u pakete pomoću štancanih stalaka od čelika 12X13. Po dužini svakog paketa postavljeno je 5 stalaka. Dva od njih su ugrađena na vodohlađene kolektore smještene u plinskom kanalu, koji se tijekom popravka spuštaju 290 mm. Para iz HPC-a ulazi u ulazne komore kontrolne površine Sh425*20 čelik 20. Prošavši zavojnice, para ulazi u izlazne komore promjera 426*20 čelika 12Kh1MF, gdje se miješa s parom koja dolazi iz premosnice. parni cjevovod. Stari RKT ventili su izrezani po linijama "B" i "C" iz starog RKT-a, unutarnji dijelovi su izvađeni, a tijela RKT-a su oparena i korištena kao T-e. Na bajpas liniji između ulaznog i izlaznog kolektora ugrađuju se novi zasuni RKT. Kada se ventil otvori do 100%, para u količini od 80% prolazi pored kontrolne površine i p/p se smanjuje. Kada je ventil zatvoren, para prolazi kroz kontrolnu površinu i temperatura ponovnog zagrijavanja raste. KDU i kontrolni ključevi novog RKT-a ostali su isti. Zavojnice ekonomajzera vode na oba trupa su zamijenjene (100%). Na razdjelnicima drugog ubrizgavanja demontirane su potporne podloške i isključeni su izlazi na GPP TO. Konvektivni ekonomajzer je posljednja ogrjevna površina u protoku plina, smještena u silaznom vodu. Sastoji se od cijevi Š32*6, materijala st20. Izlazne i ulazne komore ekonomajzera također su potporne grede - težina ove grijaće površine prenosi se na njih kroz police. Okvir kotla izrađen je u obliku identičnih okvira obje zgrade, međusobno povezanih međutrupnim vezama i prijelaznim skelama. Težina ogrjevne površine, obloge i izolacije prenosi se uz pomoć horizontalnih greda i rešetki na tri reda okomitih stupova, jedan red uz prednji dio kotla, drugi između peći i odvodnih cijevi i treći na stražnjoj strani kotla. Za učvršćivanje okvira postoji niz kosih greda. Obloga peći, plinski kanali kotla izrađeni su u obliku zasebnih štitova. Peć i dimni kanali obloženi su limovima debljine 3 mm, što osigurava veliku gustoću peći i dimnih kanala.
Promjena am s 1,12 na 1,26 dovodi do smanjenja s 2,5 na 1,5% za drugu skupinu goriva. Stoga, kako bi se povećala pouzdanost komore za izgaranje, potrebno je održavati višak zraka na izlazu iz peći više od 1,2.
U stolu. 1-3 u rasponu promjena toplinskog naprezanja volumena peći i finoće mljevenja /? 90 (sl. 6-9, c, d), njihov utjecaj na vrijednost nije pronađen. Također nije bilo moguće otkriti utjecaj omjera brzina sekundarnog zraka i mješavine prašine i zraka u proučavanom rasponu njihove promjene na učinkovitost rada peći. Međutim, smanjenjem protoka zraka kroz vanjski kanal (pri smanjenim opterećenjima) i odgovarajućim povećanjem zraka kroz unutarnji kanal (pri konstantnom protoku kroz plamenik), izlaz troske se poboljšava. Mlazevi troske postaju tanji i njihov broj se povećava.
S ravnomjernom raspodjelom prašine i zraka. nema kemijskog dogaranja na izlazu iz peći kod plamenika i na > 1,15.
Bruto učinkovitost parogeneratora pri izgaranju ugljena (1/g "14%) i pri nazivnom opterećenju doseže 90,6%.
U radu su dobiveni slični rezultati koji potvrđuju da generator pare TPP-210A radi ekonomično i pouzdano i pri izgaranju AS (1/g = 3,5%; 0pc = 22,2 MJ/kg;
S viškom zraka u peći na = 1,26h-1,28, finoća mljevenja /?9o = ----6-^8%, u području opterećenja D< = 0,7-^ 1,0£)н величина потери тепла с механическим недожогом достигает 3%. Максимальный к. п. д. брутто парогенератора при номинальной нагрузке составляет 89,5%.
U radu su prikazani podaci koji govore da je pri izgaranju antracita u komori za izgaranje parogeneratora TPP-210A vrijednost mehaničkog nedogaranja<74 в условиях эксплуатации примерно в 1,5 ниже, чем при работе котлов ТПП-110 и ТПП-210 с двухъярусным расположением вихревых горелок мощностью 35 МВт.
Provedene studije, kao i dugogodišnji pilot rad generatora pare TPP-210A, pokazali su da u rasponu promjena opterećenja od 0,65 do nominalne vrijednosti, komora za izgaranje radi ekonomično i stabilno, bez odvajanja prašine i bez kršenja pravila. režim uklanjanja tekuće troske.
Trajanje akcije (prije remonta) parogeneratora s plamenicima za prašinu i plin bez njihovog popravka iznosilo je 14545 sati. Istovremeno, stanje plamenika bilo je zadovoljavajuće; paljenje brazdi od opeke, savijanje plinskih cijevi i mlaznica je beznačajno.
Prilikom pregleda komore za izgaranje tijekom isključivanja nije uočeno nakupljanje troske na ognjištu i troska stijenki komore za naknadno izgaranje. Cijeli pojas s klinovima bio je prekriven glatkim, sjajnim filmom troske. Također nije uočen pomak konvektivnih grijaćih površina.
Isključivanje bilo kojeg plamenika ili dva srednja plamenika ne smanjuje stabilnost paljenja, ne utječe na način uklanjanja tekućeg pepela i ne dovodi do kršenja temperaturnog režima LRC-a i TRC-a.
SMELJA KAO ENERGETSKI RESURS. Odmah rezervirajmo da je korištenje domaćeg (bez legla) stelje za podmirivanje energetskih potreba puno skuplje od stelje u kapitalnom i operativnom smislu...
SLOŽENI NAČIN KORIŠĆENJA PILEĆEG GNOJIVA S DOBIVANJEM ORGANOMINERALNIH GNOJIVA I GORIVIH PLINOVA, TOPLINSKE I ELEKTRIČNE ENERGIJE Stajnjak je snažan zagađivač tla, vode i zračnih bazena. Istovremeno, smeće…