Automatska DIP montaža visećih elemenata. Izlazni hitni sklop dip pločice Dip komponente
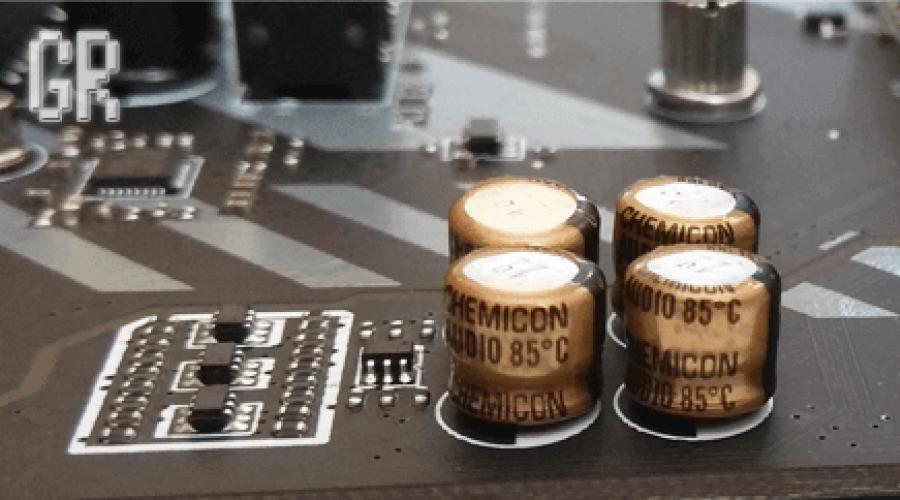
Pročitajte također
Elektroničke komponente na tiskanoj pločici učvršćuju se u metalizirane rupe, izravno na njezinu površinu ili kombinacijom ovih metoda. Cijena ugradnje DIP-a veća je od SMD-a. I iako se sve češće koristi površinsko pričvršćivanje elemenata mikro krugova, lemljenje u rupe ne gubi svoju važnost u proizvodnji složenih i funkcionalnih ploča.
Instalacija DIP-a obično se izvodi ručno. U serijskoj proizvodnji mikro krugova često se koriste instalacije za automatsko lemljenje valovima ili selektivno lemljenje. Učvršćivanje elemenata u prolazne rupe izvodi se na sljedeći način:
- izrađena je dielektrična ploča;
- izbušene su rupe za izlaznu montažu;
- na ploču se nanose električno vodljivi krugovi;
- prolazne rupe su metalizirane;
- Na tretirana područja nanosi se pasta za lemljenje kako bi se elementi učvrstili na površini;
- SMD komponente su instalirane;
- stvorena ploča je lemljena u pećnici;
- izvedena je montirana instalacija radio komponenti;
- gotova ploča se opere i osuši;
- Po potrebi se na tiskanu ploču nanosi zaštitni premaz.
Metalizacija prolaznih rupa ponekad se provodi mehaničkim pritiskom, češće kemijskim djelovanjem. DIP montaža se provodi tek nakon što je završena površinska ugradnja i svi SMD elementi su sigurno zalemljeni u pećnici.
Značajke izlazne montaže
Debljina izvoda montiranih elemenata jedan je od glavnih parametara koji treba uzeti u obzir pri razvoju tiskanih pločica. Na performanse komponenti utječe razmak između njihovih izvoda i stijenki prolaznih otvora. Mora biti dovoljno velik da osigura učinak kapilarnosti, uvlačenje fluksa, lemljenja i ispuštanje plinova za lemljenje.
TNT tehnologija bila je glavna metoda fiksiranja elemenata na tiskanim pločama prije nego što je počela široka uporaba SMD-a. Montaža tiskanih pločica kroz rupu povezana je s pouzdanošću i izdržljivošću. Stoga se pričvršćivanje elektroničkih komponenti metodom izvoda koristi pri izradi:
- napajanje;
- uređaji za napajanje;
- sklopovi za prikaz visokog napona;
- Sustavi automatizacije NPP-a itd.
End-to-end metoda pričvršćivanja elemenata na ploču ima dobro razvijenu informacijsku i tehnološku bazu. Postoje različite automatske postavke za lemne igle. Najfunkcionalniji od njih dodatno su opremljeni grimerima, koji osiguravaju hvatanje komponenti za ugradnju u rupe.
Metode lemljenja TNT:
- fiksacija u rupe bez razmaka između komponente i ploče;
- elementi za pričvršćivanje s razmakom (podizanje komponente na određenu visinu);
- okomita fiksacija komponenti.
Za blisku ugradnju koristi se U-oblik ili ravna letvica. Kod fiksiranja sa stvaranjem praznina i vertikalnim pričvršćivanjem elemenata koristi se ZIG letvica (ili ZIG-lock). Montirano lemljenje je skuplje zbog intenzivnosti rada (ručni rad) i manje automatizacije tehnološkog procesa.
Izlazna montaža tiskanih pločica: prednosti i nedostaci
Brza popularizacija površinski montiranih komponenti na tiskanoj pločici i postupno istiskivanje tehnologije ugradnje kroz rupu posljedica je niza važnih prednosti SMD metode u odnosu na DIP. Međutim, izlazna montaža ima niz neporecivih prednosti u odnosu na površinsku montažu:
- razvijena teorijska baza (prije 30 godina, provodno ožičenje je bila glavna metoda lemljenja tiskanih ploča);
- dostupnost posebnih instalacija za automatizirano lemljenje;
- niži postotak grešaka kod DIP lemljenja (u usporedbi sa SMD), budući da se proizvod ne zagrijava u pećnici, što sprječava rizik od oštećenja elemenata.
Uz navedene prednosti, možemo istaknuti niz nedostataka komponenti za prolaznu ugradnju u odnosu na površinsku montažu:
- povećane veličine kontakta;
- za montažu igle, potrebno je podrezati izvode prije lemljenja ili nakon završetka;
- dimenzije i težina komponenti su prilično velike;
- Svi izvodi zahtijevaju bušenje rupa ili izradu laserom, kao i metalizaciju i zagrijavanje lema;
- Ručna instalacija zahtijeva više vremena i rada.
Također treba uzeti u obzir da se troškovi proizvodnje tiskane pločice povećavaju. To je, prije svega, zbog prevladavajuće upotrebe ručnog rada visokokvalificiranih inženjera. Drugo, DIP sklapanje tiskanih pločica manje je podložno automatizaciji nego SMD i oduzima više vremena. Treće, pričvršćivanje olovnih elemenata zahtijeva stvaranje rupa optimalne debljine za svaki kontakt, kao i njihovu metalizaciju. Četvrto, nakon lemljenja (ili prije njega) potrebno je podrezati izvode komponenti.
Zaglavlja za 8, 14 i 16 pinske DIP komponente
UMOČITI(Dual In-line paket, također DIL) - vrsta kućišta za mikro krugove, mikrosklopove i neke druge elektroničke komponente. Pravokutnog je oblika s dva reda pribadača na dužim stranama. Može biti izrađen od plastike (PDIP) ili keramike (CDIP). Korišteno je keramičko tijelo zbog koeficijenta toplinske ekspanzije, sličnog kao kod kristala. Pri značajnim i brojnim promjenama temperature u keramičkom kućištu nastaju osjetno niža mehanička naprezanja kristala, što smanjuje opasnost od njegovog mehaničkog uništenja ili odvajanja kontaktnih vodiča. Također, mnogi elementi u kristalu mogu mijenjati svoje električne karakteristike pod utjecajem naprezanja i naprezanja, što utječe na karakteristike mikro kruga u cjelini. Kućišta keramičkih čipova koriste se u opremi koja radi u teškim klimatskim uvjetima.
Obično oznaka označava i broj pinova. Na primjer, paket čipova uobičajene TTL logičke serije, koji ima 14 pinova, može se označiti kao DIP14.
U DIP paketu mogu se proizvesti različite poluvodičke ili pasivne komponente - mikrokrugovi, sklopovi dioda, tranzistori, otpornici, sklopke malih dimenzija. Komponente se mogu izravno lemiti na tiskanu ploču, a mogu se koristiti jeftini konektori za smanjenje rizika od oštećenja komponente tijekom lemljenja. U radioamaterskom žargonu takvi se konektori nazivaju "utičnica" ili "krevet". Postoje stezne i stezne vrste. Potonji imaju veći resurs (za ponovno spajanje mikro kruga), ali popravljaju slučaj gore.
DIP paket je razvio Fairchild Semiconductor 1965. godine. Njegov izgled omogućio je povećanje gustoće ugradnje u usporedbi s prethodno korištenim okruglim kućištima. Kućište je dobro prilagođeno za automatizirano sastavljanje. Međutim, dimenzije pakiranja ostale su relativno velike u usporedbi s dimenzijama poluvodičkog kristala. DIP paketi bili su naširoko korišteni 1970-ih i 1980-ih. Nakon toga su paketi za površinsku montažu postali široko rasprostranjeni, posebno PLCC i SOIC, koji su imali manje dimenzije. Neke komponente u DIP paketima nastavljaju se proizvoditi i danas, ali većina komponenti razvijenih u 2000-ima nije dostupna u DIP paketima. Pogodnije je koristiti komponente u DIP paketima pri izradi prototipa uređaja bez lemljenja na posebnim pločama.
DIP paketi dugo su ostali popularni za programabilne uređaje kao što su ROM-ovi i jednostavni FPGA (GAL-ovi) - paket utičnica omogućuje jednostavno programiranje komponente izvan uređaja. Trenutno je ova prednost izgubila svoju važnost zbog razvoja tehnologije programiranja unutar kruga.
zaključke
Komponente u DIP paketima obično imaju od 8 do 40 pinova, a postoje i komponente s manjim ili većim parnim brojem pinova. Većina komponenti ima razmak od 0,1 inča (2,54 milimetra) i razmak redova od 0,3 ili 0,6 inča (7,62 ili 15,24 milimetara). JEDEC standardi također navode moguće razmake redova od 0,4 i 0,9 inča (10,16 i 22,86 milimetara) s do 64 pina, ali takvi se paketi rijetko koriste. U bivšem SSSR-u i zemljama istočnog bloka, DIP paketi su koristili metrički sustav i razmak igle od 2,5 milimetara. Zbog toga se sovjetski analozi zapadnih mikro krugova ne uklapaju dobro u konektore i ploče napravljene za zapadne mikro krugove (i obrnuto). To je posebno izraženo na kućištima s velikim brojem pinova.
Pinovi su numerirani u smjeru suprotnom od kazaljke na satu počevši od gornjeg lijevog kuta. Prvi zatik se određuje pomoću "ključa" - zareza na rubu kućišta. Kada je čip postavljen tako da su oznake okrenute prema gledatelju i ključ prema gore, prva igla će biti na vrhu i lijevo. Brojanje ide niz lijevu stranu tijela i nastavlja uz desnu stranu.
Geometrijske dimenzije
Standardna veličina | Najveća duljina tijela, mm | Duljina nogu, mm | Maksimalna širina kućišta, mm | Širina razmaka između nogu, mm |
---|---|---|---|---|
4 kontakta | 5,08 | 2,54 | 10,16 | 7,62 |
6 kontakata | 7,62 | 5,08 | 10,16 | 7,62 |
8 kontakata | 10,16 | 7,62 | 10,16 | 7,62 |
14 kontakata | 17,78 | 15,24 | 10,16 | 7,62 |
16 kontakata | 20,32 | 17,78 | 10,16 | 7,62 |
18 kontakata | 22,86 | 20,32 | 10,16 | 7,62 |
20 kontakata | 25,40 | 22,85 | 10,16 | 7,62 |
22 kontakta | 27,94 | 25,40 | 10,16 | 7,62 |
24 kontakta | 30,48 | 27,94 | 10,16 | 7,62 |
28 kontakata | 35,56 | 33,02 | 10,16 | 7,62 |
32 kontakta | 40,64 | 38,10 | 10,16 | 7,62 |
22 igle (široke) | 27,94 | 25,40 | 12,70 | 10,16 |
24 igle (široke) | 30,48 | 27,94 | 17,78 | 15,24 |
28 iglica (široko) | 35,56 | 33,02 | 17,78 | 15,24 |
32 igle (široke) | 40,64 | 38,10 | 17,78 | 15,24 |
40 kontakata | 50,80 | 48,26 | 17,78 | 15,24 |
42 kontakta | 53,34 | 50,08 | 17,78 | 15,24 |
48 kontakata | 60,96 | 58,42 | 17,78 | 15,24 |
64 kontakta | 81,28 | 78,74 | 25,40 | 22,86 |
Zaklada Wikimedia. 2010.
- DIGIC
- DISC procjena
Pogledajte što je "DIP" u drugim rječnicima:
UMOČITI- može se odnositi na: Sadržaj 1 Kao akronim od tri slova 1.1 U znanosti i tehnologiji 1.1.1 U informatici … Wikipedia
Umočiti- Dip, n. 1. Radnja uranjanja ili poniranja na trenutak u tekućinu. Zavijanje vesala unisono. Glover. 2. Nagib prema dolje; smjer ispod vodoravne crte; nagib; nagib.
3. šupljina ili udubljenje u… … umočiti
Umočiti- vb 1 Umočiti, uroniti, potopiti, sagnuti se, souse, zakucati se mogu usporediti kada znače uroniti osobu ili stvar u ili kao da je u tekućinu. Uranjanje podrazumijeva trenutno ili djelomično uranjanje u tekućinu ili blagi ili površni ulazak u predmet (svećenik ... Novi rječnik sinonima - Dip, v. t. pa, Got. Daupjan, Lith. dubus......
3. šupljina ili udubljenje u… … Kolaborativni međunarodni rječnik engleskog jezika
3. šupljina ili udubljenje u… …- uranjanje u tekuću kupku, ronjenje, tuširanje, namakanje, saginjanje, uranjanje, poniranje, namakanje, namakanje, plivanje; koncept 256 umočiti nešto za potapanje pripravak, razrjeđivanje, infuzija, smjesa, pripravak, otopina, sufuzija, suspenzija; koncepti... ...Novi tezaurus
3. šupljina ili udubljenje u… …- GLAGOL (umočiti, umočiti) 1) (umočiti/umočiti) staviti ili spustiti nakratko u ili u. 2) potonuti, pasti ili se nagnuti prema dolje. 3) (razine ili iznosa) privremeno postati niži ili manji. 4) spustiti ili pomaknuti prema dolje. 5) Brit. spusti snop (a ... rječnik engleskih pojmova
Umočiti-vt. dipped or occas.Now Rare dipt, dipping 1. staviti u ili ispod tekućine na trenutak i zatim brzo izvaditi; uroniti 2. bojati na ovaj način 3. očistiti… … English World dictionary - Dip, v. t. pa, Got. Daupjan, Lith. dubus......
- Dip, v. ja 1. Uroniti u sebe; postati uronjen u tekućinu; potonuti.
Sunčev rub pada; zvijezde žure van. Coleridge. 2. Izvršiti radnju zaranjanja neke posude, kao lonac, kutlača. itd.; u……
Tehnologija površinske montaže nastala je 1960-ih i 20 godina kasnije postala je naširoko korištena u proizvodnji elektronike.
Sada je ova tehnologija neosporni lider. Teško je pronaći moderan uređaj koji nije napravljen pomoću ove tehnologije. Prvo, shvatimo terminologiju. Nadgradna montaža je skraćeno kao SMT(s engleskog S urface M unt T eknologija)).
Tako je poznato da kratica SMD ponekad označava i samu tehnologiju površinske montaže, iako zapravo izraz SMD ima drugačije značenje.
SMD- Ovo SMT(s engleskog S urface D evice, odnosno nadgradnu komponentu ili uređaj. Dakle, SMD treba shvatiti posebno kao komponente i radio komponente, a ne kao tehnologiju u cjelini. Ponekad se SMD elementi nazivaju komponentama čipa, na primjer, kondenzatorski čip ili otpornički čip.
Cijela poanta SMT tehnologije je montiranje elektroničkih komponenti na površinu tiskane ploče. U usporedbi s tehnologijom montaže komponenti kroz rupe (tzv THT - M hrouth H ole M unt), - ova tehnologija ima mnoge prednosti. Ovdje su samo glavni:
Nema potrebe za bušenjem rupa za komponente;
Moguće je ugraditi komponente s obje strane tiskane pločice;
Visoka gustoća ugradnje i, kao rezultat toga, ušteda materijala i smanjenje dimenzija gotovih proizvoda;
SMD komponente su jeftinije od konvencionalnih, imaju manje dimenzije i težinu;
Mogućnost dublje automatizacije proizvodnje u odnosu na THT tehnologiju;
Ako je za proizvodnju SMT tehnologija vrlo korisna zbog svoje automatizacije, onda za malu proizvodnju, kao i za radio amatere, elektroničare, servisere i radiomehaničare, stvara dosta problema.
SMD komponente: otpornici, kondenzatori, mikro krugovi su vrlo male veličine.
Upoznajmo se sa SMD elektroničkim komponentama. Za početnike elektroničara ovo je vrlo važno, jer je u početku ponekad teško razumjeti sve njihovo obilje.
Počnimo s otpornicima. Tipično, SMD otpornici izgledaju ovako.
Obično se na njihovom malom kućištu nalazi brojčano-slovna oznaka u kojoj je kodiran nazivni otpor otpornika. Izuzetak su mikroskopski otpornici na čijem tijelu jednostavno nema mjesta za njegovu primjenu.
Ali, to je samo ako otpornik čipa ne pripada nijednoj posebnoj seriji velike snage. Također je vrijedno razumjeti da se najpouzdanije informacije o elementu trebaju pronaći u podatkovnoj tablici za njega (ili za seriju kojoj pripada).
A ovako izgledaju SMD kondenzatori.
Višeslojni keramički kondenzatori ( MLCC - S ulti L ayer C keramički C kondenzatori). Tijelo im je karakteristične svijetlosmeđe boje, a oznake obično nisu naznačene.
Naravno, postoje i elektrolitski kondenzatori za površinsku montažu. Konvencionalni aluminijski kondenzatori male su veličine i imaju dva kratka izvoda na plastičnoj osnovi.
Budući da to dimenzije dopuštaju, kapacitet i radni napon naznačeni su na kućištu aluminijskih SMD kondenzatora. Sa strane minus terminala na gornjoj strani kućišta nalazi se polukrug obojen crnom bojom.
Osim toga, postoje tantalni elektrolitski kondenzatori, kao i polimerni.
Kondenzatori s tantalovim čipom uglavnom se izrađuju u žutim i narančastim kućištima. Već sam detaljnije govorio o njihovoj strukturi na stranicama web mjesta. Ali polimerni kondenzatori imaju crno tijelo. Ponekad ih je lako zbuniti sa SMD diodama.
Treba napomenuti da su ranije, dok je SMT instalacija bila tek u povojima, bili u uporabi kondenzatori u cilindričnom kućištu koji su bili označeni u obliku pruga u boji. Sada ih je sve rjeđe.
Zener diode i diode sve se više proizvode u crnim plastičnim kućištima. Kućište na strani katode označeno je trakom.
Schottky dioda BYS10-45-E3/TR u DO-214AC kućištu
Ponekad se zener diode ili diode proizvode u paketu SOT-23 s tri terminala, koji se aktivno koristi za tranzistore. To stvara zabunu pri određivanju vlasništva komponente. Imajte ovo na umu.
Osim zener dioda koje imaju plastično kućište, prilično su raširene bezolovne zener diode u cilindričnim staklenim kućištima MELF i MiniMELF.
Zener dioda 18V (DL4746A) u MELF staklenoj kutiji
A ovako izgleda LED indikator SMD.
Najveći problem kod takvih LED dioda je što ih je vrlo teško odlemiti s tiskane pločice običnim lemilom. Sumnjam da ih radioamateri zbog toga žestoko mrze.
Čak i kada koristite stanicu za lemljenje vrućim zrakom, malo je vjerojatno da ćete moći odlemiti SMD LED bez posljedica. Laganim zagrijavanjem prozirna plastika LED diode se topi i jednostavno “sklizne” s baze.
Stoga početnici, pa čak i iskusni, imaju puno pitanja o tome kako odlemiti SMD LED bez oštećenja.
Kao i drugi elementi, mikro krugovi su prilagođeni za površinsku montažu. Gotovo svi popularni mikrosklopovi koji su izvorno proizvedeni u DIP kućištima za montažu kroz rupu također imaju verzije za SMT montažu.
Za uklanjanje topline s čipova u SMD kućištima, koji se zagrijavaju tijekom rada, često se koristi sama tiskana ploča i bakreni jastučići na njenoj površini. Bakreni jastučići na ploči, jako pokositreni lemom, također se koriste kao vrsta radijatora.
Fotografija prikazuje jasan primjer gdje se SA9259 drajver u paketu HSOP-28 hladi bakrenom podlogom na površini ploče.
Naravno, ne samo obične elektroničke komponente, već i cijele funkcionalne jedinice izoštrene su za površinsku montažu. Pogledajte fotografiju.
Mikrofon za mobitel Nokia C5-00
Ovo je digitalni mikrofon za mobitele Nokia C5-00. Njegovo tijelo nema izvode, a umjesto njih se koriste kontaktne pločice („nikli“ ili „jastučići“).
Osim samog mikrofona, u kućište je ugrađen i specijalizirani mikro krug za pojačanje i obradu signala.
Ista stvar se događa s mikro krugovima. Proizvođači se pokušavaju riješiti čak i najkraćih vodova. Fotografija #1 prikazuje linearni stabilizatorski čip MAX5048ATT+ u TDFN pakiranju. Sljedeći pod brojem 2 je čip MAX98400A. Ovo je stereo pojačalo klase D tvrtke Maxim Integrated. Mikro krug je izrađen u 36-pinskom TQFN paketu. Središnja ploča služi za odvođenje topline na površinu tiskane ploče.
Kao što vidite, mikro krugovi nemaju igle, već samo kontaktne jastučiće.
Broj 3 je MAX5486EUG+ čip. Stereo kontrola glasnoće s kontrolom pritiskom na gumb. Kućište - TSSOP24.
Nedavno se proizvođači elektroničkih komponenti pokušavaju riješiti pinova i napraviti ih u obliku bočnih kontaktnih pločica. U mnogim slučajevima, kontaktna površina se prenosi u donji dio kućišta, gdje služi i kao hladnjak.
Budući da su SMD elementi malih dimenzija i ugrađeni na površinu tiskane pločice, svaka deformacija ili savijanje pločice može oštetiti element ili prekinuti kontakt.
Na primjer, višeslojni keramički kondenzatori (MLCC) mogu popucati zbog pritiska na njih tijekom instalacije ili zbog prevelike doze lema.
Višak lema dovodi do mehaničkog naprezanja na kontaktima. Najmanji zavoj ili udarac izazivaju pojavu pukotina u višeslojnoj strukturi kondenzatora.
Evo jednog primjera kako višak lema na kontaktima dovodi do pukotina u strukturi kondenzatora.
Fotografija preuzeta iz TDK-ovog izvješća "Uobičajeni načini pucanja u višeslojnim keramičkim kondenzatorima za površinsku montažu". Dakle, puno lemljenja nije uvijek dobro.
A sada malo misterija da začinimo našu dugotrajnu priču. Pogledajte fotografiju.
Odredite koji su elementi prikazani na fotografiji. Što mislite što se krije ispod prvog broja? Kondenzator? Možda induktivitet? Ne, to je vjerojatno neka vrsta posebnog otpornika...
A evo i odgovora:
br. 1 - keramički kondenzator veličine 1206;
Br. 2 - NTC termistor (termistor) B57621-C 103-J62 na 10 kOhm (veličina 1206);
Br. 3 - prigušnica za suzbijanje elektromagnetskih smetnji BLM41PG600SN1L(veličina 1806).
Nažalost, zbog svoje veličine, velika većina SMD komponenti jednostavno nije označena. Baš kao u gornjem primjeru, vrlo je lako pobrkati elemente, budući da su svi vrlo slični jedni drugima.
Ponekad ova okolnost komplicira popravak elektronike, osobito u slučajevima kada je nemoguće pronaći tehničku dokumentaciju i dijagram za uređaj.
Vjerojatno ste već primijetili da su SMD dijelovi pakirani u perforiranu traku. On je, pak, upleten u kolut. Zašto je to potrebno?
Činjenica je da se ova traka koristi s razlogom. Vrlo je prikladan za automatsko dopremanje komponenti na montažne strojeve (instalatere).
U industriji se ugradnja i lemljenje SMD komponenti provodi pomoću posebne opreme. Ne ulazeći u detalje, proces izgleda ovako.
Pomoću šablona pasta za lemljenje se nanosi na kontaktne pločice ispod elemenata. Za veliku proizvodnju koriste se strojevi za sitotisak (printeri), a za malu proizvodnju sustavi za doziranje materijala (doziranje lemne paste i ljepila, mase za zalijevanje i dr.). Automatski dozatori potrebni su za proizvodnju proizvoda koji zahtijevaju radne uvjete.
Zatim se automatizirana instalacija SMD komponenti na površini ploče odvija pomoću strojeva za automatsku instalaciju komponenti (instalatera). U nekim slučajevima dijelovi se fiksiraju na površinu kapljicom ljepila. Stroj za ugradnju opremljen je sustavom za preuzimanje komponenti (s iste trake), sustavom tehničkog vida za prepoznavanje istih, kao i sustavom za ugradnju i pozicioniranje komponenti na površinu ploče.
Zatim se obradak šalje u pećnicu, gdje se topi pasta za lemljenje. Ovisno o tehničkom procesu, reflow se može izvesti konvekcijom ili infracrvenim zračenjem. Na primjer, u tu svrhu mogu se koristiti konvekcijske pećnice.
Čišćenje tiskane ploče od ostataka fluksa i drugih tvari (ulja, masti, prašine, agresivnih tvari), sušenje. Za ovaj proces koriste se posebni sustavi pranja.
Naravno, u proizvodnom ciklusu koristi se mnogo više različitih strojeva i uređaja. Na primjer, to mogu biti sustavi za rendgenski pregled, komore za klimatska ispitivanja, strojevi za optički pregled i još mnogo toga. Sve ovisi o opsegu proizvodnje i zahtjevima za konačni proizvod.
Vrijedno je napomenuti da je, unatoč prividnoj jednostavnosti SMT tehnologije, u stvarnosti sve drugačije. Primjer su nedostaci koji se javljaju u svim fazama proizvodnje. Možda ste već vidjeli neke od njih, na primjer, kuglice za lemljenje na ploči.
Nastaju zbog neusklađenosti šablone ili viška paste za lemljenje.
Također nije neuobičajeno da se unutar lemljenog spoja formiraju šupljine. Mogu biti ispunjeni ostacima topitelja. Čudno je da prisutnost malog broja šupljina u spoju pozitivno utječe na pouzdanost kontakta, jer šupljine sprječavaju širenje pukotina.
Neki od nedostataka su čak dobili ustaljena imena. Ovo su neki od njih:
"Nadgrobni spomenik" - to je kada komponenta "stoji" okomito na ploču i zalemljena je jednim izvodom na samo jedan kontakt. Jača površinska napetost s jednog od krajeva komponente tjera je da se izdigne iznad kontaktne pločice.
"Pseće uši" - neravnomjerna raspodjela paste u otisku, pod uvjetom da je ima dovoljna količina. Uzrokuje lemne mostove.
"Hladno lemljenje" - lemljeni spoj loše kvalitete zbog niske temperature lemljenja. Izgled lemljenog spoja ima sivkastu nijansu, kao i poroznu, kvrgavu površinu.
Posljedica " kokica" ("Efekt kokica") prilikom lemljenja mikro krugova u BGA paketu. Greška koja nastaje zbog isparavanja vlage koju apsorbira kućište mikro kruga. Prilikom lemljenja vlaga isparava, unutar kućišta se stvara šupljina koja se urušava i stvara pukotine u mikro krugu Intenzivno isparavanje tijekom zagrijavanja također istiskuje lem iz jastučića, što stvara neravnomjernu raspodjelu lema među kontaktnim kuglicama i stvaranje skakača koji se otkrivaju pomoću rendgenskih zraka. osjetljive komponente.
Prilično važan potrošni materijal u SMT tehnologiji je pasta za lemljenje. Lemna pasta sastoji se od mješavine vrlo malih kuglica lema i topitelja, što olakšava proces lemljenja.
Flux poboljšava sposobnost vlaženja smanjujući površinsku napetost. Stoga, kada se zagriju, otopljene lemne kuglice lako prekrivaju kontaktnu površinu i terminale elementa, tvoreći lemljeni spoj. Flux također pomaže u uklanjanju oksida s površine i također je štiti od utjecaja okoliša.
Ovisno o sastavu topitelja u pasti za lemljenje, može djelovati i kao ljepilo koje fiksira SMD komponentu na pločicu.
Ako ste promatrali proces lemljenja SMD komponenti, možda ste primijetili učinak učinka samopozicioniranja elementa. Izgleda jako cool. Zbog sila površinske napetosti, čini se da se komponenta sama poravnava u odnosu na kontaktnu površinu na pločici, plutajući u tekućem lemu.
Dakle, čini se, tako jednostavna ideja ugradnje elektroničkih komponenti na površinu tiskane pločice omogućila je smanjenje ukupnih dimenzija elektroničkih uređaja, automatizaciju proizvodnje, smanjenje troškova komponenti (SMD komponente su 25- 50% jeftiniji od konvencionalnih) i stoga potrošačku elektroniku čine jeftinijom i kompaktnijom.
Savezna agencija za obrazovanje Ruske Federacije
Tečajni rad
na temu: “DIP instalacija”
Rjazanj, 2008
Vrste SMT sklopova
U elektroničkoj industriji postoji šest uobičajenih tipova SMT sklopova, svaki s vlastitim redoslijedom proizvodnje. Postoji poseban standard koji predstavlja glavne vrste sklopova, podijeljenih u klase.
SMC i IPC dokumentacija za sklopne ploče za površinsku ugradnju, IPC-7070, J-STD-013 i Nacionalni tehnološki plan za elektroničke međukonekcije uključuju klasifikacije sljedećih sklopova za površinsku ugradnju:
Tip 1 - montirane komponente ugrađuju se samo na gornju stranu ili međuspojne strukture
Tip 2 - montirane komponente ugrađene s obje strane ploče ili spojne strukture
Klasa A - samo komponente s provrtom
Klasa B - samo komponente za površinsku montažu (SMD).
Klasa C - mješovita: komponente za provrt i površinsku montažu
Klasa X - složeni mješoviti sklop: prolazna rupa, SMD, fini korak, BGA
Klasa Y - složeni mješoviti sklop: prolazna rupa, površinska montaža, ultra fini korak, CSP
Klasa Z - složeni mješoviti sklop: prolazna rupa, Ultra fini korak, COB, Flip Chip, TCP
U nastavku ćemo razmotriti glavne opcije za postavljanje komponenti na ploču koju koriste programeri.
Riža. 1- Tip 1B: SMT samo gornja strana
Ova vrsta nije uobičajena jer većina dizajna zahtijeva neke DIP komponente. Zove se IPC tip 1B.
Redoslijed procesa: nanošenje paste za lemljenje, ugradnja komponenti, lemljenje, pranje.
Riža. 2 - Tip 2B: SMT gornja i donja strana
Na donjoj strani ploče nalaze se čip otpornici i druge male komponente. Pri korištenju valovitog lemljenja oni će se ponovno rastaliti gornjim (bočnim) protokom vala lemljenja. Postavljanje velikih komponenti na obje strane, kao što je PLCC, povećava troškove proizvodnje jer se komponente na donjoj strani moraju montirati posebnim vodljivim ljepilom. Ovaj tip se naziva IPC tip 2B.
Postupak za provođenje procesa:
nanošenje lemne paste, ugradnja komponenti, lemljenje, pranje donje strane;
Nanošenje paste za lemljenje na gornju stranu PCB-a, ugradnja komponenti, ponovno lemljenje, pranje gornje strane.
Poseban tip: SMT gornja strana u prvom slučaju i vrh i dno u drugom, ali PTH samo gornja strana.
Ova metoda instalacije se koristi kada postoje DIP komponente u SMT sklopu. Proces uključuje postavljanje DIP komponenti u rupe prije SMT lemljenja. Korištenjem ove metode eliminira se nepotrebno lemljenje valovima ili ručno lemljenje PTH komponenti, što značajno smanjuje cijenu proizvoda. Prvi zahtjev je sposobnost komponenti da izdrže sekundarno lemljenje. Osim toga, dimenzije rupa na ploči, jastučići i geometrija šablone moraju biti precizno poravnati kako bi se postiglo dobro lemljenje. Ploča mora imati prorezne rupe i može biti jednostrana i dvostrana, odnosno komponente se mogu postaviti i s gornje i s donje strane.
Obavezni uvjet pri korištenju ove metode je prisutnost kroz metalizirane rupe.
Postupak obrade jednostrane tiskane ploče:
nanošenje lemne paste, ugradnja SMT komponenti, ugradnja PTH komponenti, lemljenje, pranje gornje strane.
Postupak obrade dvostrane tiskane ploče:
nanošenje paste za lemljenje, ugradnja SMT komponenti, reflowing, pranje donje strane;
ugradnja PTH komponenti, lemljenje, pranje gornje strane.
Riža. 4 - Tip 1C: samo gornja strana SMT i samo gornja strana PTH
Ova metoda je mješovita tehnologija montaže. Svi SMT i PTH moduli su instalirani na gornjoj strani ploče. Moguće je instalirati neke komponente kroz rupu (PTH) na gornju stranu ploče gdje se postavljaju SMT komponente za povećanje gustoće. Ova vrsta sklopa naziva se IPC tip 1C.
Postupak za provođenje procesa:
nanošenje paste za lemljenje, ugradnja, reflowing, pranje vrha SMT;
automatsko podešavanje DIP-a, zatim aksijalnih komponenti (kao što su LED);
valovito lemljenje PTH komponenti, pranje.
Riža. 5 - Tip 2C: SMT gornja i donja strana ili PTH gornja i donja strana
Instaliranje komponenti za površinsku montažu i kroz rupe (DIP) na obje strane ploče se ne preporučuje zbog visokih troškova montaže. Ovaj dizajn može zahtijevati mnogo ručnog lemljenja. Također, ne koristi se automatska instalacija PTH komponenti zbog mogućih sukoba sa SMT komponentama na donjoj strani ploče. Ova vrsta sklopa naziva se IPC tip 2C.
Postupak za provođenje procesa:
nanošenje lemne paste, ugradnja, lemljenje, pranje gornje strane SMT;
nanošenje specijalnog vodljivog ljepila kroz šablonu, ugradnja, fiksacija SMT;
automatska ugradnja DIP i aksijalnih komponenti;
maskiranje cijele donje strane PTH komponenti;
ručna ugradnja ostalih komponenti;
ručno lemljenje donje strane PTH komponenti.
Riža. 6 - Tip 2C: samo donja strana SMT ili samo gornja strana PTH
Ovaj tip postavlja površinski nosač na donju stranu ploče, a PTH na gornju stranu. Također je jedan od vrlo popularnih oblika smještaja jer... omogućuje značajno povećanje gustoće komponenti. Tip se zove IPC tip 2C.
Redoslijed obrade (nema PTH sukoba na donjoj strani):
nanošenje ljepila kroz šablonu, postavljanje, sušenje ljepila na donjoj strani SMT;
ručna ugradnja ostalih komponenti;
Alternativni redoslijed obrade (PTH sukobi na donjoj strani):
automatska ugradnja DIP, zatim aksijalnih komponenti;
točkasto nanošenje ljepila (metoda dispenzera), ugradnja, sušenje ljepila na donjoj strani SMT-a;
ručna ugradnja komponenti;
valovito lemljenje PTH i SMT komponenti, pranje.
Riža. 7 - Tip 2Y: SMT gornja i donja strana ili samo PTH gornja strana
Ovaj tip omogućuje postavljanje komponenti za površinsku montažu na obje strane ploče, a DIP komponenti samo na vrh. Ovo je vrlo popularan tip sklopa među programerima, koji omogućuje visoko gustoću postavljanja komponenti. Donja strana SMT komponenti ostaje bez aksijalnih elemenata i nogu DIP komponenti. Na primjer, ne možete staviti čipove između DIP pinova komponente.
Tijek procesa (bez postavljanja komponenti za površinsku montažu (SMT) između pinova komponenti s rupama (PTH) na donjoj strani ploče):
nanošenje lemne paste, ugradnja, lemljenje, pranje gornje strane SMT dijela;
nanošenje ljepila kroz šablonu, postavljanje, sušenje SMT ljepila s donje strane;
automatska ugradnja DIP, a zatim aksijalnih komponenti;
ručna ugradnja ostalih komponenti;
valovito lemljenje PTH i SMT komponenti, pranje;
Alternativni tok procesa (na donjoj strani ploče za površinsku montažu (SMT), komponente se postavljaju između nogu s otvorom (PTH):
nanošenje lemne paste, postavljanje, lemljenje, pranje gornje strane SMT dijela;
automatska ugradnja DIP, zatim aksijalnih komponenti;
točkasto nanošenje ljepila (metoda dispenzera), ugradnja, sušenje ljepila na donjoj strani ploče;
ručna ugradnja ostalih komponenti;
valovito lemljenje PTH i SMT komponenti, pranje.
Riža. 8 - Tehnološki put za montažu tiskanih pločica
Tehnologija ugradnje u rupu
Tehnologija kroz rupu (THT), koja se ponekad naziva i montaža iglom, izvor je velike većine modernih procesa sklapanja elektroničkih modula. Postoji i niz uobičajenih, ali ne sasvim točnih naziva za ovu tehnologiju, na primjer, DIP montaža (naziv dolazi od vrste paketa - Dual In-Line Package - paket s dvorednim rasporedom pinova, široko korištena, ali ne i jedina u ovoj tehnologiji) i provodna montaža (naziv nije sasvim točan, budući da se ugradnja komponenti s provodnicima koristi iu mnogim drugim tehnologijama, uključujući površinsku montažu).
Naime, ova se tehnologija pojavila s početkom korištenja tiskanih ploča kao načina izrade električnih spojeva. Do sada se ugradnja komponenti vršila prostorno pričvršćivanjem komponentnih izvoda na metalne kontakte na konstrukcijskim elementima uređaja ili međusobnim spajanjem komponentnih izvoda. Korištenje tiskanih pločica premjestilo je dizajn komponenti iz svemira u ravninu, što je uvelike pojednostavilo kako proces razvoja dizajna tako i proizvodnju uređaja. Pojava ožičenja tiskanog kruga dovela je do revolucije u proizvodnosti i automatizaciji dizajna elektroničkih uređaja.
Tehnologija kroz rupe, kao što ime sugerira, metoda je montiranja komponenti na tiskanu pločicu u kojoj se igle komponente ugrađuju u prolazne rupe na ploči i lemljene na jastučiće i/ili obloženu unutarnju površinu rupe.
Tehnologija montaže na rupu postala je raširena 50-ih i 60-ih godina 20. stoljeća. Od tada se značajno smanjila veličina komponenti, povećala se gustoća montaže i usmjeravanja ploča, razvijeno je više od jedne generacije opreme za automatizaciju montaže komponenti, ali osnove projektiranja i proizvodnje komponenti pomoću ove tehnologije su ostao nepromijenjen.
Trenutačno, tehnologija kroz rupe gubi svoju poziciju u odnosu na napredniju tehnologiju površinske montaže, posebno u masovnoj i velikoj proizvodnji, potrošačkoj elektronici, računalstvu, telekomunikacijama, prijenosnim uređajima i drugim područjima gdje je visoka proizvodnost, minijaturizacija proizvoda i dobra niska potrebne su karakteristike signala.
Međutim, postoje područja elektronike u kojima je tehnologija kroz rupu i danas dominantna. To su prije svega energetski uređaji, izvori napajanja, visokonaponski sklopovi monitora i drugih uređaja, kao i područja u kojima, zbog povećanih zahtjeva pouzdanosti, veliku ulogu igra tradicija i povjerenje u provjereno, npr. avionika, automatizacija nuklearnih elektrana itd.
Ova se tehnologija također aktivno koristi u pojedinačnoj i maloj proizvodnji s više artikala, gdje je automatizacija procesa irelevantna zbog čestih promjena u proizvedenim modelima. Ove proizvode uglavnom proizvode mala domaća poduzeća za kućanstvo i posebne namjene.
Prije nekog vremena postojala je situacija u kojoj je izbor tehnologije montaže kroz rupe mogao biti diktiran korištenim komponentama. Neke komponente jednostavno nisu bile dostupne u paketima za površinsku montažu. To se posebno odnosilo na našu zemlju, budući da su nam novi proizvodi kasno stigli. Ova situacija se sada značajno promijenila, a većina komponenti opće namjene može se naći ili u obje verzije ili u verziji za površinsku montažu, koja se smatra progresivnijom. Iznimke su komponente napajanja, elektromehanički releji, konektori, veliki promjenjivi otpornici, IC ploče i neke druge komponente, ali mnoge od njih već imaju ekvivalente za površinsku montažu. Postoji ambivalentan stav prema pouzdanosti površinskih elektrolitskih kondenzatora, a njihovi tantalski parnjaci su prilično skupi, tako da se često mogu naći pin-type aluminijske elektrolitske kondenzatore na pločama za površinsku montažu. Sve to zahtijeva korištenje tehnologije mješovite instalacije (istovremena prisutnost SMT i THT komponenti na PCB-u).
Tehnologija ugradnje THT komponenti relativno je jednostavna, uhodana, omogućuje ručne i automatizirane načine montaže te je dobro opremljena montažnom opremom i tehnološkom opremom. Ovaj članak ukratko govori o glavnim operacijama THT tehnologije.
Komponente
EC koji se koriste u tehnologiji montaže kroz rupu mogu se podijeliti u sljedeće glavne skupine prema vrsti kućišta (primjeri kućišta prikazani su na slici 9):
a) EC s aksijalnim (često se koristi oznaka aksijalni) izvodima;
b) EC s radijalnim izvodima (radijalno);
c) SIL, SIP (Single In-Line Package) - višepinski paket s jednorednim rasporedom pinova;
d) DIP (Dual In-Line Package) - kućište s dvorednim rasporedom pinova;
e) konektori, utori;&
e) ploče za IC, uključujući DIP; ZIF (Zero Insertion Force, ploče s nultom silom umetanja za pin IC); PGA (Pin Grid Array, paneli za pin IC s pin matricom);
g) razne komponente složenog oblika.
Riža. 9 - Primjeri THT komponenti: a) s aksijalnim vodovima; b) s radijalnim izvodima; c) u SIL kućištima; d) u DIP pakiranjima; e) spojnice; f) IC ploče; g) EC složenog oblika
Ovo odvajanje komponenti prvenstveno je posljedica osobitosti njihove tehnologije ugradnje. Na primjer, kablovi za aksijalne i radijalne komponente zahtijevaju oblikovanje i obrezivanje, dok većina drugih komponenti ne zahtijeva. Prilikom oblikovanja izvoda, a kao posljedica toga, naknadne ugradnje komponenti s aksijalnim vodovima, one imaju dodatni stupanj slobode (rotacija oko osi), pa su označene prstenima u boji (vidi sl. 9a), što isključuje ugradnju „označeno dolje.”
Također postoje razlike u mehanizmima zahvata, podnožja i fiksiranja različitih skupina komponenti, pa se često komponente u različitim kućištima ugrađuju na svaku svoju opremu.
Tipični redoslijed operacija
Tehnološki proces montaže PCB-a temeljen na THT tehnologiji sastoji se od sljedećih tipičnih koraka:
priprema EC izvoda (formiranje, obrezivanje), često u kombinaciji s automatiziranom instalacijom;
ugradnja komponenti (ručna, automatska);
lemljenje (valni lem, ručno, selektivno);
pranje (ultrazvučno, mlaz).
Neki pogoni zadržali su tehnologiju u kojoj je zbog problema s olovnim premazima i skladištenjem komponenti priprema olova uključivala predkalajisanje, ali suvremena tehnologija to ne omogućuje zbog kvalitetnog pakiranja i olovnog premaza suvremenih komponenti. Ove operacije su navedene u nastavku prema redoslijedu izvršenja.
Izrada zaključaka EK
EC terminali moraju biti posebno pripremljeni prije instalacije. Svrha pripreme:
poravnanje (ravnanje) izvoda (ako je potrebno);
osiguravanje potrebne udaljenosti za montažu između terminala;
razmak između PCB-a i komponente (ako je potrebno);
pričvršćivanje EC-a na tiskanu ploču tijekom ručne instalacije ili prije nego što ploča uđe u instalaciju za lemljenje.
Razmak se obično osigurava tako da se EC stezaljkama da odgovarajući zavoj - tzv. “referentna zima” (slika 2a); samofiksiranje EC na PP prije skupnog lemljenja - posebnim savijanjem dijela olova koji ulazi u rupu PP - brave (slika 2b). Izvođenje cik i locka u isto vrijeme naziva se zig-lock.
Također je moguće pričvrstiti EC koristeći sljedeće metode:
osiguranje opruge izvoda;
nalijeganjem na ljepilo (ljepilo polimerizira na sobnoj temperaturi, a kod staklenih vitrina može biti potrebno postaviti cjevčicu na dio vitrine koji je u kontaktu s ljepilom; također je potrebno osigurati dovoljan broj ljepljivih točaka za pričvršćivanje teških EC-ova);
lemljenje pinova (koristi se za ručnu ugradnju - na primjer, lemljenje dva dijagonalno smještena pina konektora);
savijanje (potpuno ili djelomično - pod kutom od 0 do 45° u odnosu na ravninu PP-a i to samo za izvode promjera manjeg od 0,7 mm (više u tehnički opravdanim slučajevima); potrebno je osigurati najmanju dopuštenu udaljenost od savijeni vod do susjednih CP/pinova/vodiča; savijanje treba izvesti duž tiskanog vodiča, osim ako nije drugačije navedeno u projektnoj dokumentaciji);
pomoću raznih držača (stezaljke, metalni nosači, stezaljke, stezaljke).
Teški elementi (na primjer, transformatori) ili elementi podložni mehaničkom naprezanju (prekidači, potenciometri, kondenzatori za ugađanje) postavljaju se pomoću posebnih držača. Takvi držači osiguravaju pouzdano mehaničko pričvršćivanje odgovarajućih elemenata na tiskanu ploču i sprječavaju lomljenje i lomljenje vodiča pod utjecajem mehaničkih opterećenja.
Riža. 10 - Osiguravanje, formiranjem EC izvoda: a) razmak između PCB-a i komponente (potporni zig); (b) samofiksiranje EC na PP (brava)
Oblikovanje okruglih ili trakastih stezaljki elemenata provodi se pomoću alata za ručnu ugradnju ili posebnih poluautomatskih uređaja na način da se isključe mehanička opterećenja na mjestima gdje su stezaljke pričvršćene na kućište. Pri oblikovanju izvoda nije dopušteno njihovo mehaničko oštećenje, narušavanje zaštitne prevlake, savijanje na spoju izvoda i kućišta, uvijanje u odnosu na os kućišta, pucanje staklenih izolatora i plastičnih kućišta.
Glavna ograničenja (Sl. 11) nametnuta su veličini od tijela EC do osi zakrivljenog izvoda (L) i unutarnjeg polumjera savijanja izvoda (R). Minimalna veličina L, ovisno o vrsti EC, je u rasponu od 0,75 - 4 mm (ali ne manje od 2D izvoda); veličina R ovisi o promjeru izvoda i iznosi najmanje 0,5 - 1,5 mm (ali ne manje od (1-2) D izvoda). Također, ne smije biti deformacija ili stanjivanja na terminalima koji prelaze 10% promjera, širine ili debljine terminala.
Riža. 11 - Osnovni parametri kalupljenja
Nepridržavanje ovih preporuka može dovesti do stvaranja prekomjernih naprezanja na mjestu gdje je provodnik pričvršćen za EC tijelo iu području gdje je provodnik savijen te, kao posljedicu, pojavu pukotina i, moguće, lomova na tim mjestima, posebno pod mehaničkim opterećenjem na sastavljenoj jedinici. Nije dopušteno savijati krute izvode (latice) tranzistora i dioda srednje i velike snage, jer to može dovesti do pucanja njihovih staklenih izolatora i lomljenja nepropusnosti kućišta.
Udaljenost od kućišta do mjesta lemljenja mora biti najmanje 2,5 mm, osim ako se ne poduzmu mjere za dodatno odvođenje topline tijekom procesa lemljenja.
Nemojte vršiti nikakvo oblikovanje, savijanje ili podrezivanje prilikom instaliranja višepinskih IC-ova (IC-ova u DIP paketu, itd.). Za njih se može izvršiti samo ravnanje (poravnanje) izvoda, ako je potrebno.
Uređaji za oblikovanje dostupni su s mehaničkim i električnim pogonom za EC napajanje, kao i mehanički ili pneumatski pogon za sam uređaj za oblikovanje. Učitavanje komponenti vrši se iz vrpci, cjevastih kazeta i raspršivanja. Geometrijski parametri oblikovanja su podesivi; Instalacije su opremljene zamjenjivim kalupnim matricama. Poseban dizajn matrica uređaja za oblikovanje osigurava odsutnost prekomjernog naprezanja i ureza na materijalu na mjestu gdje je olovo savijeno. Primjeri prethodno oblikovanih izvoda različitih THT komponenti prikazani su na slici. 12.
Riža. 12 - Primjeri oblikovanja EC izvoda s aksijalnim (a) i radijalnim (b) vodovima
Produktivnost opreme za kalupljenje u automatskom načinu rada pri utovaru s trake, u pravilu, iznosi do 40 000 EK / sat za EK s aksijalnim vodovima i 20 000 EK / sat s radijalnim; pri utovaru EC iz placera - 7000 odnosno 3000 EC/sat. Kod ručnog dodavanja EC, tipična produktivnost je oko 1500-3000 EC/sat.
Postoje automatski brojači izlaznih komponenti zalijepljenih na traku (do 100 EC/s).
Instaliranje komponenti
igla za lemljenje tiskane ploče
Montaža TNT komponenti se vrši pomoću specijalnih montažnih strojeva, automatiziranih radnih stanica (AWS) ili potpuno ručno.
Automatizirana instalacija
Montažna oprema
Postoje dvije glavne vrste automatizirane opreme na temelju funkcija koje se obavljaju:
stvarni instalacijski strojevi (inserter, od insert - umetnuti), koji umeću EC pinove u rupe na PCB-u, podrezuju ih i savijaju (po izboru) sa stražnje strane PCB-a pomoću glava za montiranje, savijanje i reznih glava; podijeljeni su u skupine prema vrsti komponenti (Axial (Radial) inserter - automatski stroj za montažu EC-a s aksijalnim (radijalnim) vodovima, DIP inserter - automatski stroj za ugradnju EC-a u DIP kućišta, Odd-Form inserter - automatski stroj za ugradnju EC-a u kućišta složenog oblika);
sekvenceri - automatski strojevi za formiranje niza instaliranih EC-ova (tj. priprema programske vrpce koja sadrži sekvencijalno zalijepljene EC-ove različitih standardnih veličina redoslijedom njihove naknadne ugradnje; provodi se lijepljenjem ERE-a s primarnih vrpci prema programu).
Mnogi strojevi za montažu također imaju funkciju sekvencera, tj. može raditi izravno s primarnih traka bez potrebe za pripremom softverske trake.
Valja napomenuti da na suvremenom tržištu, zajedno s onima proizvedenim 90-ih godina. i trenutno se prodaje rabljena (uključujući i renovirana) oprema za montažu kroz rupe (razni modeli Dynapert, Panasert, Amistar, Universal Instruments itd.), postoje moderni modeli raznih proizvođača koji značajnu pozornost posvećuju razvoju automatizirane montaže kroz rupe tehnologija montaže. Mnoge opcije strojeva, koje su prije bile dostupne samo za SMT montažu, postale su sastavni dio moderne opreme za montažu za THT tehnologiju. Servo pogoni za pomake duž koordinatnih osi, upravljanje pomoću PC-a, učitavanje dodavača bez zaustavljanja rada, praćenje pravilnog dodavanja EC-a, istodobna montaža više od jednog PCB-a, automatsko učitavanje/istovaranje PCB-a, ispravljanje grešaka vodljivog uzorka PCB-a, automatska promjena zahvata - sve je to trenutno dostupno i za montažu klinom. Sustavi tehničkog vida koriste se za optičku korekciju položaja EC i očitavanje fiducijalnih oznaka. Montažne glave strojeva opremljene su prvenstveno mehaničkim hvataljkama sa servo pogonom. Standardni EC kutovi rotacije su višekratnici od 90°, međutim, u pravilu je moguće opremiti stroj montažnom glavom sa slobodnim kutom rotacije.
Brojni strojevi imaju mogućnost postavljanja žičane premosnice na tiskane ploče, režući ih neposredno prije postavljanja iz kontinuirane šipke.
Certificirana produktivnost suvremene instalacijske opreme doseže 20.000-40.000 EC/sat s razinom greške instalacije od 100-200 ppm (za jednostavan EC). Produktivnost pri ugradnji EC-a složenog oblika može biti niža za red veličine. Glavni parametri opreme, pored gore navedenih, su geometrijske karakteristike EC i PP koji se ugrađuju:
raspon ili diskretni skup udaljenosti između iglica (redovi iglica);
najveći promjer i visina EC (ovisno o vrsti - s aksijalnim ili radijalnim vodovima);
raspon promjera olova;
raspon ukupnih dimenzija PP.
Uređaji za pokretanje
Za opremanje strojeva za automatsku ugradnju THT komponenti koriste se uređaji za punjenje (dovodnici) sljedećih glavnih tipova (Sl. 13):
traka za EC s radijalnim i aksijalnim vodovima - dizajnirana za postupno dovođenje ERE zalijepljenog u traku; vrpca se može namotati na kolut (Tape and Reel) ili pakirati u “magazin” - kutiju (Ammo Pack);
od cjevastih kazeta za IC u DIP paketu, komponente složenog oblika - s nagnutom transportnom ladicom i horizontalne (za IC koji ne klize slobodno duž nagnute ladice zbog svojih konstrukcijskih značajki - težine, oblika kućišta ili stršećih oštrih izvoda) ;
vibrirajući lijevci za opskrbu raznim EC-ima iz ležišta s mogućnošću njihove istovremene orijentacije prije hvatanja;
matrica (stanična) za EC složenog oblika - od matričnih paleta, časopisa.
Riža. 13 - Primjeri dodavača za THT komponente: a) s aksijalnim izvodima; b) s radijalnim izvodima; c) iz cjevastih kaseta; d) vibrirajući lijevak; e) iz matrix paleta
Brojni modeli opreme opremljeni su hranilicama upravljanim mikroprocesorom, kao i automatskim mjenjačima.
Ručna i poluautomatska ugradnja komponenti
Ova operacija se izvodi na radnim stanicama ili montažnim stolovima. U ovim je uređajima dostava informacija o montaži automatizirana - mjesto ugradnje EC-a na tiskanu ploču i njegova potrebna orijentacija, a također može osigurati automatsku opskrbu potrebne ladice s komponentama instaliranog tipa, te proces fiksiranja PCB na montažnom stolu može se mehanizirati. Radno mjesto može biti dodatno opremljeno uređajima za formiranje EC odvoda. Takva oprema je jeftina, ali niske produktivnosti (1000-2000 EK/h).
Postoje sljedeće opcije za instaliranje EC-a:
S razmakom (opcija II prema OST4 010.030-81). Ovakvim načinom ugradnje lakše je očistiti sastavljene komponente od ostataka fluksa, a manje je i pregrijavanja IC-a tijekom lemljenja. U tom slučaju tiskani vodiči mogu se nalaziti ispod visećeg elementa. Pod određenim uvjetima (pod određenim spektrima udara), otpornost na vibracije i udarce koji se prenose duž ploče se poboljšava, budući da se udar prigušuje vodovima. Međutim, visina jedinice se povećava, a otpornost na izravne mehaničke utjecaje smanjuje. Moguće je da se mjenjač odvoji od jednostranog PP-a kada se na EC primijeni značajan pritisak odozgo.
Bez razmaka (opcija I prema OST4 010.030-81). Elementi bolje podnose mehanička opterećenja (osobito s dodatnim pričvršćivanjem na tijelo s nosačem i sl.), visina jedinice je manja. Poboljšava prijenos topline s komponente na tiskanu ploču, što se često koristi kada uporaba hladnjaka nije praktična. Preporuča se ugradnja komponenti s radijalnim vodovima položenim bočno isključivo bez razmaka (u nekim slučajevima s tehnološkim brtvama ispod kućišta). Duljina EC vodova je smanjena, što poboljšava električne karakteristike uređaja. Međutim, može biti teško očistiti sastavljeni sklop, a također je potrebno osigurati međusobnu izolaciju EC i tiskanih vodiča, metalizirane rupe koje prolaze ispod kućišta (na primjer, korištenjem izolacijskih brtvila i lijepljenjem na tijelo EC i/ili PP).
Vertikalna ugradnja EC (opcija III prema OST4 010.030-81) s aksijalnim vodovima povećava gustoću rasporeda, ali smanjuje proizvodnost, povećava vjerojatnost međusobnog kratkog spoja vodova, povećava visinu jedinice i čini izgled neurednim. U ovom slučaju, potrebno je da kut nagiba EC u odnosu na okomitu os ne prelazi 15 °.
Vrste ugradnje komponenti regulirane su industrijskim standardima, na primjer OST4 010.030-81, i standardima poduzeća. Iako zahtjevi industrijskih standarda trenutno nisu obvezni, često se koriste kao smjernice i referentni dokumenti.
EC-ove treba ugraditi tako da njihovi elementi označavanja, posebno oni koji se odnose na polaritet, budu vidljivi kako bi se osigurala naknadna kontrola ispravne ugradnje.
Riža. 14 - Primjeri PP držača
Ugradnja komponenti može se izvršiti ugradnjom jednog po jednog EC-a i zatim lemljenjem rotiranjem PCB-a, ali je tehnološki naprednija metoda kada se PCB kruto fiksira tijekom instalacije. Posebni uređaji koriste se za učvršćivanje tiskanih ploča i njihovo rotiranje tijekom procesa ugradnje. Postoje držači PCB-a (Sl. 6) opremljeni držačem s oprugom za ploču, koji omogućuje njezino učvršćivanje u vodoravnom, okomitom položaju ili ravnini koja se okreće oko jedne ili dvije osi, te osigurava antistatičku zaštitu tijekom instalacije i lemljenja. Proces ručnog lemljenja EC-a razmatra se u nastavku.
Lemljenje
Unutar THT tehnologije uglavnom se koriste tri metode lemljenja: valovito lemljenje, selektivno i ručno.
Lemljenje valovima
Lemljenje valovima najčešća je metoda lemljenja koja se prvi put pojavila 50-ih godina 20. stoljeća. Koristi se i za proizvode bazirane samo na pin komponentama, iu slučaju mješovite instalacije, kada su THT i SMD komponente istovremeno prisutne na PCB-u.
Tijekom procesa lemljenja, PP se postavljaju na transporter i sukcesivno prolaze kroz nekoliko radnih zona instalacije za lemljenje: zona fluksiranja, zona predgrijavanja, zona lemljenja.
Sljedeći parametri imaju poseban utjecaj na proces lemljenja:
kut nagiba transportera;
brzina pokretne trake;
vrstu korištenog fluksa i njegovu gustoću;
debljina sloja fluksa i ujednačenost njegove primjene;
temperatura i brzina predgrijavanja;
vrsta korištenog lema i stupanj njegove čistoće (bez nečistoća);
temperatura lemljenja;
oblik, visina i stabilnost vala lema;
atmosfera tijekom lemljenja i stupanj njezine čistoće.
Flux uklanja oksidne filmove s lemljenih površina, poboljšava sposobnost vlaženja lema i sprječava oksidaciju prije početka lemljenja. Koriste se topitelji na bazi vode i smole, uključujući one koji ne zahtijevaju čišćenje, kao i topitelji koji se mogu ispirati vodom. Fluksiranje se provodi na jedan od dva glavna načina: prskanjem i korištenjem sredstva za pjenjenje. Mnogi strojevi za valno lemljenje mogu biti opremljeni s obje vrste sredstava za pražnjenje.
Raspršivanje topitelja provodi se, na primjer, pomoću rotirajućeg mrežastog bubnja, gdje struja komprimiranog zraka koja prolazi kroz njegovu mrežicu stvara fini mlaz tekućeg fluksa. Postoje dizajni sredstava za fluksiranje gdje se fluks prvo pretvara u fino raspršeno stanje na radnoj površini ultrazvučne mlaznice, a zatim se raspršuje strujom komprimiranog zraka. Sloj nanesenog topitelja treba biti jednoličan i imati debljinu od 1-10 mikrona u suhom stanju. Odabire se optimalni tlak tijekom prskanja, kao i prati gustoća fluksa. Metoda prskanja ima niz prednosti u odnosu na pjenjenje, posebno je ekonomičnija, a također će omogućiti precizniju kontrolu debljine fluksa.
Protočenje pjene provodi se pomoću filtarskih elemenata (cijevasti filtri ili porozno kamenje (na primjer, plovućac) s veličinom pora od 3 - 35 mikrona), koji tvore homogenu pjenu koja se sastoji od mjehurića malog promjera. Pjena se usmjerava na ploču pomoću mlaznice. Mjehurići pucaju i prskaju fluks na donju površinu PP-a. Što je manja veličina mjehurića pjene, to je bolje vlaženje fluksa, pa je upotreba cjevastih filtara poželjnija od poroznog kamenja. Visina uspona pjene je podesiva (obično ne više od 2 cm).
Zona fluksa završava uređajem "zračni nož", koji služi za uklanjanje viška fluksa s površine PP-a.
Predgrijavanje služi za sprječavanje toplinskog udara PP i EC kao rezultat kontakta s valom vrućeg lema, sušenja (uklanjanje otapala) i aktivacije fluksa. Grijanje se provodi IC modulima s različitim valnim duljinama, kvarcnim grijačima i konvekcijskim sustavima (potonji su posebno učinkoviti ako PCB ima EC s visokim toplinskim kapacitetom).
Zatim transporter s PP-om prolazi izravno u zonu lemljenja, gdje se pomoću pumpe u kadi stvara val rastaljenog lema. Ploče se ugrađuju ili na prste (latice) transportera, obično od titana, ili montiraju na palete. Transporter ima mogućnost podešavanja brzine (0-2 m/min) i kuta nagiba PP u odnosu na val (5-9°), što je bitno za osiguranje odvodnje viška lema. Valni oblik lemljenja može varirati ovisno o korištenom modelu opreme. U početku je korišten simetrični val, ali kasnije je došlo do prijelaza na asimetrične (T-oblika, Z-oblika, W-val itd.), dajući bolje rezultate u pogledu kvalitete lemljenih spojeva (slika 15a) . Proizvođači EC u svojim preporukama navode parametre profila valovitog lemljenja, koji uključuju temperaturu i brzinu predgrijavanja, brzinu porasta temperature kada je izložen valu, maksimalnu temperaturu kojoj je EC izložen tijekom lemljenja i vrijeme držanja tijekom lemljenja, kao i najveća dopuštena brzina hlađenja PP .
Riža. 15 - Val lema: a) simetričan i asimetričan oblik; b) prvi (turbulentni) i drugi (laminaran) za dvovalno lemljenje
Za proizvode bazirane na mješovitoj ugradnji, tzv. “dvostruki” val lema (slika 16b). Prvi val je uzak, dovodi se iz mlaznice pod visokim pritiskom i turbulentnog je karaktera. Njegova je zadaća osigurati vlaženje EC vodova i spriječiti stvaranje šupljina s plinovitim inkluzijama preostalim od raspadanja fluksa. Drugi val je laminaran, njegova brzina istjecanja je manja; uništava mostove nastale prvim valom i dovršava stvaranje lemnih spojeva. Primjer temperaturnog profila dvovalnog lemljenja PP prikazan je na sl. 16.
Riža. 16 - Primjer temperaturnog profila za lemljenje PCB-a bez olova s dvostrukim valom
Slično zoni predgrijavanja, zona lemljenja također završava "zračnim nožem" koji uklanja višak lema i uništava mostove.
Brojni modeli opreme pružaju mogućnost valovitog lemljenja u okruženju inertnog plina (dušika). Dovod dušika koristi se izravno na mjesto lemljenja ili stvaranje dušikovog "tunela" preko svih zona. Svrha korištenja dušika je smanjiti oksidaciju lema i topitelja, stvoriti sjajnije i svjetlije lemne spojeve, smanjiti razinu stvaranja taloga i, kao rezultat toga, eliminirati začepljenje mlaznica.
Ručno lemljenje
Ručno lemljenje predinstaliranih THT komponenti provodi se pomoću analognih i digitalnih stanica za lemljenje.
Pripremljene površine premazuju se topilom neposredno prije lemljenja. Mehanizam djelovanja fluksa je da se oksidni filmovi metala i lema pod djelovanjem fluksa otapaju, olabave i plutaju na njegovoj površini. Oko očišćenog metala stvara se zaštitni sloj fluksa koji sprječava stvaranje oksidnih filmova. Tekući lem zamjenjuje fluks i stupa u interakciju s osnovnim metalom. Sloj lema se postupno povećava i stvrdnjava kada prestane zagrijavanje.
Prilikom izvođenja procesa lemljenja izuzetno je važno održavati potrebnu temperaturu. Niske temperature dovode do nedovoljne fluidnosti lema i slabog vlaženja površina koje se spajaju. Značajno povećanje temperature uzrokuje pougljenje fluksa prije nego što aktivira spojne površine. Treba napomenuti da je temperatura vrha lemilice postavljena na stanici za lemljenje uvijek viša od stvarne temperature lemljenja, što je posljedica toplinskog kapaciteta elemenata koji su uključeni u stvaranje lemnog spoja (sama komponenta i njen vodovi, PCB i elementi vodljivog uzorka). Temperatura se odabire ovisno o korištenom lemu, vrsti i veličini tijela komponente, materijalu i topologiji PCB-a.
Važne karakteristike stanice za lemljenje su:
brzo zagrijavanje vrha na radnu temperaturu;
precizna kontrola temperature vrha s maksimalnom frekvencijom (zbog značajki dizajna spoja između grijača i vrha, položaja termoelemenata i drugih razloga, navedena temperatura vrha može se razlikovati od stvarne);
automatska kalibracija stanice pri promjeni vrha ili lemilice;
brza izmjena savjeta.
Uglavnom digitalne stanice za lemljenje imaju takve mogućnosti, koje omogućuju preciznije podešavanje, održavanje i kontrolu temperature lemilice u usporedbi s analognim, a također vam omogućuju spajanje nekoliko alata na stanicu.
Za lemljenje se obično koristi tekući prašak i žičani lem. Topilo se nanosi četkom na mjesta lemljenja. Za lemljenje na teško dostupnim mjestima, kao i za popravke, koriste se cjevasti lemovi s nekoliko kanala fluksa iznutra. Pretežno se koriste lemovi sa slabo aktiviranim topilima s malom količinom kolofonija (NC, No-clean - nije potrebno čišćenje) ili srednje aktiviranim topiteljima s kolofonijom, kod kojih je čišćenje moguće, ali nije potrebno u normalnim uvjetima rada proizvoda. Za lemljenje jako oksidiranih površina, kao i površina slabo lemljivih, koriste se aktivirani kolofonijski topitelji, koji zahtijevaju naknadno pranje u deioniziranoj vodi ili organskim otapalima na bazi alkohola. Lemovi se koriste i eutektički (Sn-Pb, Sn-Pb-Ag) i bezolovni (Sn-Cu, Sn-Ag-Cu); Isporuka se vrši u kolutima.
Tipični redoslijed lemljenja za komponente ugrađene u rupe je sljedeći:
čišćenje vrha lemilice (ako je potrebno), servisiranje;
postavljanje temperature vrha lemilice na stanici;
izlaganje, tijekom kojeg se vrh lemilice zagrijava na potrebnu temperaturu;
dovođenje vrha u kontakt (istodobno) s mjenjačem i EC izlazom kako bi se osiguralo njihovo zagrijavanje, kratka brzina zatvarača (0,5 - 1 s);
dovođenje lemne šipke na lemljeni spoj kako bi se stvorila veza između terminala i CP (ne biste trebali nanositi lem izravno na vrh lemilice kako biste izbjegli prerano sagorijevanje fluksa);
Lemljenje olova u krugu na 360°;
istovremeno uklanjanje lemne šipke i vrha lemilice (u smjeru prema gore duž EC izlaza kako bi se formirao kut pravilnog oblika).
Proces lemljenja jednog spoja treba biti što kraći kako bi se izbjeglo pregrijavanje EC-a i ljuštenje mjenjača njegovo ukupno trajanje je od 0,5 do 2 sekunde. Prilikom lemljenja morate paziti da lemilo ni nakratko ne dodiruje tijelo EC-a, te da na njega ne padnu kapljice lema i topitelja. Nakon uporabe vrh lemilice je potrebno pokositriti kako bi mu se produžio vijek trajanja.
Postoje lemilice s istodobnim dovođenjem lemne šipke (lemi se jednom rukom, drugom se može držati EC i/ili PP), kao i stanice za automatsko kontinuirano ili diskretno dovođenje lema do mjesta lemljenja.
Gotovi lemljeni spoj mora ispunjavati sljedeće zahtjeve:
minimalni kut pokrivanja olova lemom koji ga navlaži sa strane lemljenja (270-330°);
minimalni postotak ispunjenosti CP područja otopljenim lemom na strani lemljenja (75%);
minimalno popunjavanje otvora lemom po visini (50-100% ovisno o klasi proizvoda).
Kraj kabla bi trebao biti vidljiv u formiranom lemljenom spoju (ne smije biti viška lema). Površina fileta lema je konkavna, kontinuirana, glatka, sjajna, bez tamnih mrlja ili stranih inkluzija. Lem ne smije dodirivati tijelo EC. Mora postojati razmak (minimalno 1,2 mm) između meniskusa formiranog oblogom kućišta na radijalnim vodovima komponente i lemljenog spoja. Lem se ne smije širiti izvan CP duž vodiča.
Selektivno lemljenje
Selektivno lemljenje je proces selektivnog lemljenja pojedinačnih EC-a na PCB-u bez utjecaja na preostale ugrađene komponente, a obično se izvodi s mini-wave lemom. Također se razvijaju sustavi za selektivno lemljenje laserom i vrućim plinom.
Proces lemljenja minivalnim lemljenjem umnogome je sličan konvencionalnom lemljenju valovima, s bitnom razlikom da se ne lemi cijela PCB, već samo pojedinačni EC-ovi na njoj. Sustav transportera i modul predgrijanja slični su po dizajnu onima koji se koriste u valovitom lemljenju. Flukseri se koriste i za raspršivanje i za točkasti tip s jednom ili više mlaznica. Topilo se selektivno i precizno nanosi na mjesto lemljenja pomoću glave topitelja koju pokreće servo pogon. Moduli za topljenje s posebnim adapterima također se koriste kada je potrebno topiti pojedina područja PP-a. Val u kupki za lemljenje, koji također ima servo pogon (u nekim modelima opreme PP se pomiče), stvaraju se zamjenjivim mlaznicama za oblikovanje valova. Postoje i sustavi selektivnog lemljenja s nekoliko generatora valova, izrađeni u obliku zamjenjive opreme za određeni proizvod. Takvi sustavi imaju veću produktivnost, ali mnogo manju fleksibilnost. Lemljenje se može izvesti u inertnom (dušikovom) okruženju, što osigurava odsutnost oksidacije minivalova lemljenja. Razina minivalova mjeri se beskontaktnim metodama.
Selektivno lemljenje ima niz značajnih prednosti u usporedbi s ručnim i valnim lemljenjem:
smanjenje potrošnje tehnoloških materijala (fluks, lem, inertni plin) i električne energije;
smanjenje vremena proizvodnog ciklusa i broja zaposlenih u području ručnog lemljenja;
uklanjanje potrebe za pranjem;
mogućnost lemljenja različitih EC-a na PCB s različitim lemovima na jednoj instalaciji u jednom ciklusu;
izbjegavanje ljudskog faktora, ponovljivost procesnih parametara kroz cijelu šaržu.
Ove prednosti uzrokuju da se proizvođači sve više udaljavaju od valnog i ručnog lemljenja i koriste lemljenje reflowom za SMD komponente i selektivno lemljenje za pin EC.
Tehnološki proces
Tehnološki proces je složen skup radnji izvođača i opreme za pretvaranje sirovina i komponenti u gotov proizvod. Sastoji se od kompleksa vlastitih tehnoloških procesa za izradu njihovih sastavnih dijelova, dijelova i tehnoloških procesa za montažu, ugradnju, podešavanje i ispitivanje. Tehnološki procesi za izradu određene opreme temelje se na standardnim tehnološkim procesima.
Tipični tehnološki procesi uključuju:
1) ulazna inspekcija komponenti;
2) tehnološko osposobljavanje komponenti i sklopova;
3) montaža;
4) električna instalacija;
5) tehnička kontrola ugradnje i montaže;
6) zaštitu proizvoda od utjecaja vanjske sredine;
7) tehnološko osposobljavanje proizvoda;
8) podešavanje (podešavanje) proizvoda;
9) ispitivanje proizvoda;
10) kontrola izlaza.
Dakle, tehnološki proces izrade bloka, podbloka ili funkcionalne cjeline u pravilu je složen proces, čija je pravilna konstrukcija moguća samo na temelju njegovog idejnog projekta, često uz korištenje matematičkog modeliranja.
Glavni dokumenti u razvoju tehnoloških procesa su tehnološke karte. Na kartama je prikazana struktura tehnološkog procesa i njegov sadržaj, redoslijed operacija, načini rada, korištena oprema, tehnološka oprema, postupci ugradnje, načini podešavanja, upravljanja itd.
Tehnološki procesi se sastoje od pojedinačnih operacija.
Operacija je dio tehnološkog procesa koji na određenom dijelu (ili na skupu od više dijelova ili montažnih jedinica) izvodi jedan radnik (ili posebna grupa radnika) kontinuirano i na jednom radnom mjestu. Procesna operacija je osnovna jedinica planiranja proizvodnje.
U pravilu se tehnološki proces dijeli na operacije, a operacije na prijelaze.
Zaključak
Ovaj kolegij je ispitao postojeće tehnologije površinske montaže. Posebna pažnja posvećena je tehnologiji ugradnje u rupe. Opisane su različite metode za ugradnju komponenti i njihovo lemljenje. Tehnologija ugradnje THT komponenti relativno je jednostavna, uhodana, omogućuje ručne i automatizirane načine montaže te je dobro opremljena montažnom opremom i tehnološkom opremom.
Književnost
1. Površinska montaža: Tehnologija. Kontrola kvalitete / V.N. Grigoriev, A.A. Kazakov, A.K. Dzhincharadze i dr.; Pod općim uredništvom I.O. Shurchkova - M.: Standards Publishing House, 1991 - str. 184.
2. Tehnologija izrade tiskanih pločica / http://en.radioland.net
3. Osnove tehnologije površinske montaže / Suskin V.V. - Ryazan: Uzoroche, 2001.
4. Tehnologije u elektroničkoj industriji / glavni urednik Pavel Pravosudov - Fine Street Publishing LLC, br. 1.2006 - str.
Slični dokumenti
Trenutno stanje tehnologije površinske montaže. Moguće mogućnosti, tehnološke operacije i okruženja za montažu i ugradnju ćelija elektrana, postupak i pravila njihove pripreme i izvedbe. Kriteriji za izbor topitelja, ljepila, lemova, čistača, zaštitnih premaza.
kolegij, dodan 26.01.2011
Razvoj tehnologije za sklapanje i ugradnju pogona niskofrekventnih pojačala. Analiza tehnologije trase, opravdanje procesne opreme, izbor optimalne opcije tehnološkog procesa. Dizajn prostora za montažu i ugradnju.
kolegij, dodan 19.06.2010
Tehnološki proces (TP) kao osnova proizvodnog procesa. Izrada TP za montažu i ugradnju drajvera niskofrekventnih pojačala. Analiza dizajna proizvoda. Projektiranje montažnog i montažnog prostora, opreme za montažne i montažne radove.
kolegij, dodan 21.06.2010
Izrada kompleta tehnološke dokumentacije za proizvodnju stroboskopa: analiza proizvodnosti dizajna proizvoda, izrada tehnološkog dijagrama za montažu proizvoda. Provođenje analize opcija tehnologije rute za montažu i ugradnju dijelova.
kolegij, dodan 14.10.2010
Opis električnih i pogonskih karakteristika vatmetra, njegova konstrukcija, namjena i princip rada. Određivanje zahtjeva za tip i uvjete proizvodnje uređaja. Izrada dizajnerskih i tehnoloških shema za montažu i ugradnju proizvoda.
kolegij, dodan 01.10.2011
Uvođenje eutektičke legure kao lema između spojnih površina kristala i paketa. Eutektičke legure: zlato-germanij ili zlato-silicij. Ugradnja pomoću ljepila i spojeva u proizvodnji poluvodičkih uređaja.
sažetak, dodan 01.09.2009
Izrada opisa sheme električnog kruga. Karakteristike zahtjeva za projektiranje tiskanih pločica, oblikovanje olova, kalajisanje i lemljenje. Određivanje električnih parametara tiskanih vodiča, proizvodnost i pouzdanost dizajna.
kolegij, dodan 16.06.2011
Vrste opreme i raspored audio sustava. Klasifikacija opreme i izbor shema ugradnje komponenti. Ugradnja komponenti. Spajanje i postavljanje pojačala. Ugradnja glazbenih komponenti. Ekonomski troškovi. Sigurnosni zahtjevi.
kolegij, dodan 29.10.2008
Provođenje testa lemljivosti. Ispitivanje toplinske otpornosti lemljenja. Ispitivanje čvrstoće izvoda i njihovih pričvršćenja. Ispitivanje izlaznih krajeva na vlačnu silu. Ispitivanje uvijanjem i savijanjem savitljivih žica.
sažetak, dodan 25.01.2009
Razvoj tehnoloških procesa prema jedinstvenom sustavu pripreme proizvodnje p1e tranzistorskih mjerača. Analiza vrste, uvjeta i godišnjeg programa puštanja u promet. Put dizajna montaže, odabir opreme, optimizacija instalacije.
Prijepis
1 SMD komponente Već smo se upoznali s glavnim radio komponentama: otpornicima, kondenzatorima, diodama, tranzistorima, mikro krugovima itd., A također smo proučavali kako se montiraju na tiskanu pločicu. Prisjetimo se još jednom glavnih faza ovog procesa: vodovi svih komponenti prolaze kroz rupe na tiskanoj pločici. Nakon toga se izvodi odsijeku, a zatim se izvrši lemljenje na stražnjoj strani ploče (vidi sl. 1). Taj nama već poznati postupak naziva se DIP editing. Ova instalacija je vrlo prikladna za početnike radio amatere: komponente su velike, mogu se lemiti čak i velikim "sovjetskim" lemilom bez pomoći povećala ili mikroskopa. Zato svi Master Kit setovi za "uradi sam" lemljenje uključuju DIP montažu. Riža. 1. DIP instalacija Ali DIP instalacija ima vrlo značajne nedostatke: - velike radio komponente nisu prikladne za izradu modernih minijaturnih elektroničkih uređaja; - izlazne radio komponente su skuplje za proizvodnju; - tiskana pločica za DIP montažu je također skuplja zbog potrebe za bušenjem velikog broja rupa; - DIP instalaciju je teško automatizirati: u većini slučajeva, čak iu velikim tvornicama elektronike, ugradnja i lemljenje DIP dijelova mora se obaviti ručno. To je vrlo skupo i dugotrajno.

2 Stoga se DIP montaža praktički ne koristi u proizvodnji moderne elektronike, a zamijenjena je tzv. SMD postupkom, koji je danas standard. Stoga bi svaki radioamater trebao imati barem opću ideju o tome. SMD montaža SMD (Surface Mounted Device) preveden je s engleskog kao "površinska komponenta". SMD komponente se također ponekad nazivaju komponentama čipa. Proces montaže i lemljenja komponenti čipa ispravno se naziva SMT proces (od engleskog “surface mount technology”). Reći "SMD instalacija" nije sasvim točno, ali u Rusiji je ovo verzija naziva za tehnički proces koji se ukorijenio, pa ćemo reći isto. Na sl. 2. prikazuje presjek SMD montažne ploče. Ista ploča izrađena na DIP elementima imat će nekoliko puta veće dimenzije. sl.2. SMD montaža SMD montaža ima neosporne prednosti: - radio komponente su jeftine za proizvodnju i mogu biti minijaturne koliko želite; - tiskane ploče su također jeftinije zbog nepostojanja višestrukog bušenja;

3 - instalaciju je lako automatizirati: instalaciju i lemljenje komponenti provode posebni roboti. Također ne postoji takva tehnološka operacija kao što je rezanje olova. SMD otpornici Upoznavanje s komponentama čipa najlogičnije je započeti s otpornicima, kao najjednostavnijim i najraširenijim radio komponentama. SMD otpornik je u svojim fizičkim svojstvima sličan "konvencionalnoj" izlaznoj verziji koju smo već proučavali. Svi njegovi fizički parametri (otpor, točnost, snaga) potpuno su isti, samo je tijelo drugačije. Isto pravilo vrijedi i za sve ostale SMD komponente. Riža. 3. CHIP otpornici Standardne veličine SMD otpornika Već znamo da izlazni otpornici imaju određenu mrežu standardnih veličina, ovisno o njihovoj snazi: 0,125W, 0,25W, 0,5W, 1W itd. Standardna mreža standardnih veličina također je dostupna za čip otpornike, samo u ovom slučaju standardna veličina je označena četveroznamenkastim kodom: 0402, 0603, 0805, 1206 itd. Glavne veličine otpornika i njihove tehničke karakteristike prikazane su na slici 4.

4 sl. 4 Osnovne veličine i parametri chip otpornika Označavanje SMD otpornika Otpornici su označeni šifrom na kućištu. Ako kod ima tri ili četiri znamenke, tada zadnja znamenka označava broj nula. 5. Otpornik s kodom “223” ima sljedeći otpor: 22 (i tri nule desno) Ohm = Ohm = 22 kohm. Kod otpornika "8202" ima otpor od: 820 (i dvije nule s desne strane) Ohm = Ohm = 82 kohm. U nekim slučajevima, oznaka je alfanumerička. Na primjer, otpornik s kodom 4R7 ima otpor od 4,7 Ohma, a otpornik s kodom 0R Ohma (ovdje je slovo R znak za razdvajanje). Postoje i otpornici nultog otpora ili kratkospojnici. Često se koriste kao osigurači. Naravno, ne morate zapamtiti kodni sustav, već jednostavno izmjerite otpor otpornika multimetrom.

5 sl. 5 Označavanje čip otpornika Keramički SMD kondenzatori Izvana su SMD kondenzatori vrlo slični otpornicima (vidi sl. 6.). Postoji samo jedan problem: šifra kapacitivnosti nije označena na njima, tako da je jedini način da se to odredi mjerenjem multimetrom koji ima način mjerenja kapacitivnosti. SMD kondenzatori su također dostupni u standardnim veličinama, obično sličnim veličinama otpornika (vidi gore). Riža. 6. Keramički SMD kondenzatori

6 Elektrolitički SMS kondenzatori Sl.7. Elektrolitički SMS kondenzatori Ovi kondenzatori su slični svojim olovnim parnjacima, a oznake na njima su obično jasne: kapacitet i radni napon. Traka na poklopcu kondenzatora označava njegov negativni terminal. SMD tranzistori sl. 8. SMD tranzistor Tranzistori su mali, pa je na njima nemoguće napisati puni naziv. Ograničeni su na kodne oznake i ne postoji međunarodni standard za oznake. Na primjer, kod 1E može označavati tip tranzistora BC847A, ili možda neki drugi. Ali ova okolnost uopće ne smeta proizvođačima ili običnim potrošačima elektronike. Poteškoće mogu nastati samo tijekom popravaka. Određivanje tipa tranzistora ugrađenog na tiskanu pločicu bez dokumentacije proizvođača za tu pločicu ponekad može biti vrlo teško.

7 SMD diode i SMD LED-ice Fotografije nekih dioda prikazane su na donjoj slici: Sl.9. SMD diode i SMD LED diode Polaritet mora biti naznačen na tijelu diode u obliku trake bliže jednom od rubova. Obično je katodni terminal označen trakom. SMD LED također ima polaritet, koji je označen ili točkom u blizini jednog od pinova, ili na neki drugi način (za više detalja pogledajte dokumentaciju proizvođača komponente). Određivanje tipa SMD diode ili LED-a, kao u slučaju tranzistora, je teško: na tijelu diode je utisnut neinformativni kod, a na tijelu LED-a najčešće nema nikakvih oznaka, osim oznake polariteta. Programeri i proizvođači moderne elektronike malo brinu o njihovoj mogućnosti održavanja. Pretpostavlja se da će popravak tiskane pločice izvršiti serviser koji posjeduje kompletnu dokumentaciju za određeni proizvod. Takva dokumentacija jasno opisuje gdje je na tiskanoj ploči određena komponenta ugrađena. Instalacija i lemljenje SMD komponenti SMD montaža optimizirana je prvenstveno za automatsku montažu specijalnim industrijskim robotima. Ali amaterski radio dizajni također se mogu izraditi pomoću komponenti čipa: uz dovoljno pažnje i pažnje, možete lemiti dijelove veličine zrna riže s najobičnijim lemilom, samo trebate znati nekoliko suptilnosti. Ali ovo je tema za zasebnu veliku lekciju, pa će se više detalja o automatskoj i ručnoj instalaciji SMD-a raspravljati zasebno.

ALCIUM VAULT PRVI SUSRET A. Sabunin [e-mail zaštićen] Stvaranje modernih elektroničkih proizvoda uključuje obradu velikih količina projektnih podataka. Tijekom rada na projektu ovi podaci
GRUNDFOS ELEKTRIČNI MOTORI Tvrtka GRUNDFOS posluje u Rusiji više od 14 godina, a sve ove godine trudili smo se biti uzor poslovnog partnerstva. Naša oprema pouzdano i uspješno služi ljudima i šire
M. B. KATZ SUSTAV SIMBOLA ZA KOTRLJAJNE LEŽAJEVE, BILJNE LEŽAJEVE, KUGLICE I VALJKE Treće izdanje Moskva 2006. M. B. KATS SUSTAV SIMBOLA ZA KOTRLJAJNE LEŽAJEVE, BILJNE LEŽAJEVE,
Zašto LED diode ne rade uvijek onako kako njihovi proizvođači žele? Sergej NIKIFOROV [e-mail zaštićen]Članak je posvećen problemima proizvodnje i uporabe LED dioda i sadrži odgovore na popularna pitanja
DOO "D and m r u s" Relej za nadzor stanja izolacije razvodnih postrojenja IDR-10, Perm Sadržaj 1. Uvod... 3 1.1. Namjena... 3 1.2. Opis uređaja “IDR-10”... 4 1.2.1. Tehničke karakteristike uređaja...
Upute za sonde A do Z Upute Tektronix Probe Selector Ovaj mrežni, interaktivni alat omogućuje odabir sondi prema seriji, modelu ili standardu/primjeni prema
MINISTARSTVO OBRAZOVANJA I ZNANOSTI RUSKE FEDERACIJE Savezna državna proračunska obrazovna ustanova visokog stručnog obrazovanja "NACIONALNO ISTRAŽIVANJE TOMSK POLYTECHNIC"
Sve što ste željeli znati o flash pogonima, ali ste se bojali pitati Andreja Kuznjecova Opisuju se tehničke karakteristike flash pogona i raspravlja se o pitanjima vezanim uz njihov odabir i upotrebu. Što se dogodilo
Mjerenje fizikalnih veličina. Mjerne nesigurnosti, pogreške mjerenja. Mjerenje fizikalnih veličina Mjerenje je usporedba dane fizikalne veličine s prihvaćenom veličinom iste vrste
Savezna agencija za obrazovanje Ruske Federacije (RF) TOMSK DRŽAVNO SVEUČILIŠTE SUSTAVA UPRAVLJANJA I RADIO ELEKTRONIKE (TUSUR) Zavod za elektroničke uređaje (ED) ODOBRENO Voditelj odjela
POGLAVLJE 10 DIZAJN HARDVERA Niskonaponska sučelja Uzemljenje u sustavima s mješovitim signalom Tehnike digitalne izolacije Smanjenje šuma i rad filtriranja napona napajanja
MINISTARSTVO OBRAZOVANJA I ZNANOSTI RUSKE FEDERACIJE Državna obrazovna ustanova visokog stručnog obrazovanja MOSKVSKO DRŽAVNO TEHNIČKO SVEUČILIŠTE "MAMI" G. B. SHIPILEVSKY
Sadržaj Uvod 4 1. Pouzdan softver kao proizvod tehnologije programiranja. 5 1.1. Program kao formalizirani opis procesa obrade podataka. 5 1.2. Pojam ispravnog programa.
Osnovni koncepti rasvjete i njihova praktična primjena U prirodi postoji mnogo elektromagnetskih valova s različitim parametrima: X-zrake, γ-zrake, mikrovalno zračenje itd. (vidi.
Sadržaj Kompletan mjerni sustav... 3 Generator signala... 4 Analogni ili digitalni... 5 Osnovne aplikacije generatora signala... 6 Verifikacija... 6 Testiranje digitalnih modularnih odašiljača
Ministarstvo obrazovanja Ruske Federacije Uralsko državno sveučilište nazvano po A. M. Gorkom Pripremili odjeli za opću fiziku i fiziku magnetskih pojava KRATKE INFORMACIJE O OBRADI REZULTATA
M Vektorska algebra i njezine primjene za studente dodiplomskih i diplomskih studija matematičkih, fizičkih i tehničkih specijalnosti M MG Lyubarsky Ovaj udžbenik nastao je na temelju predavanja iz više matematike, koja