Récepteur d'air DIY pour compresseur. Comment fabriquer un bon compresseur de vos propres mains à la maison ? Compresseur d'une bouteille de gaz avec compresseur d'un camion
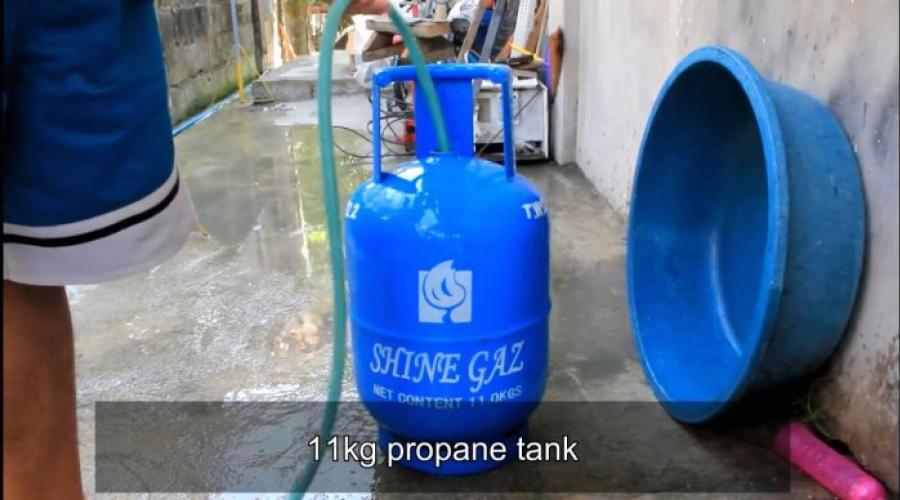
Récemment, les compresseurs ont gagné en popularité parmi les bricoleurs. Ils sont fabriqués sur la base de presque tous les moteurs, calculant la puissance de l'unité de base en fonction du nombre de consommateurs. Pour les ateliers à domicile, les groupes compresseurs à faire soi-même sont demandés.
Les compresseurs de réfrigérateur restent souvent opérationnels après que le réfrigérateur lui-même tombe en panne ou devienne obsolète. Ils sont de faible puissance, mais fonctionnent sans prétention. Et de nombreux maîtres en font des tout à fait décents. installations faites maison. Voyons comment vous pouvez le faire vous-même.
Pièces et matériaux
Pièces requises :- Réservoir de propane de 11 kg ;
- Raccord 1/2" avec filetage interne et bouchon ;
- Plaques métalliques, largeur – 3-4 cm, épaisseur – 2-4 mm;
- Deux roues avec plateforme de montage ;
- Compresseur de réfrigération d'un réfrigérateur ;
- Adaptateur 1/4 pouces ;
- Connecteur de clapet anti-retour en laiton ;
- Connecteur de tuyau en cuivre de ¼ de pouce – 2 pièces ;
- Équipement pour régler la pression du compresseur ;
- Boulons, vis, écrous, fumlenta.
- Inverseur de soudage;
- Tournevis ou perceuse ;
- Fraises à métaux avec revêtement en titane ;
- Une turbine ou une perceuse avec des accessoires abrasifs ;
- Brosse métallique;
- Rouleau pour tubes de cuivre ;
- Clés à molette, pinces.
Assemblage du compresseur
Première étape : préparer le récepteur
Cylindre vide de propane liquéfié rincer abondamment à l'eau. Il est très important d’éliminer ainsi tous les résidus explosifs. mélange gazeux.
Nous superposons l'adaptateur de 1/4 de pouce dans le trou d'extrémité du cylindre. Nous l'échaudons de tous les côtés par soudage et le scellons avec une vis.
Nous plaçons le récepteur sur des roues et des supports. Pour ce faire, on prend des segments des plaques métalliques, pliez-les en biais et soudez-les sur le corps par le bas. Nous soudons des roues avec une plate-forme de montage aux coins. Nous montons un support dans la partie avant du récepteur.Deuxième étape - installer le compresseur
Au-dessus du récepteur, nous plaçons des cadres de montage pour le compresseur constitués de plaques métalliques. Vérifier leur position niveau à bulle, et ébouillanter. Nous installons le compresseur sur les boulons de serrage à l'aide de coussinets en caoutchouc amortisseurs. U de ce genre Le compresseur n'utilisera qu'une seule sortie par laquelle l'air est pompé dans le récepteur. Les deux autres, qui aspirent l’air, resteront intacts.Troisième étape : fixez le clapet anti-retour et l'adaptateur à l'équipement.
Nous sélectionnons un coupe-métal d'un diamètre approprié et utilisons un tournevis ou une perceuse pour percer un trou dans le boîtier pour l'accouplement. S'il y a des formes saillantes sur le corps de l'accouplement, meulez-les avec une perceuse (pour cela, vous pouvez utiliser un papier de verre électrique ordinaire ou une meuleuse avec disque de meulage).
Placez l'accouplement dans le trou et soudez-le sur toute la circonférence. Filetage interne il doit correspondre au pas et au diamètre du filetage de montage du clapet anti-retour.
Nous utilisons du laiton clapet anti-retour pour les petits compresseurs. Nous bouchons la sortie de décharge de pression avec un boulon approprié, car l'ensemble de commande dispose déjà d'une soupape de décharge.
Pour installer un pressostat ou un pressostat avec tout l'équipement de contrôle, nous montons un autre adaptateur 1/4 de pouce. On lui fait un trou au centre du récepteur, non loin du compresseur.
Nous resserrons le clapet anti-retour avec un adaptateur 1/2 pouce.
Nous connectons la sortie du cylindre du compresseur et le clapet anti-retour avec un tube en cuivre. Pour ça outil spécial Nous évasons les extrémités des tubes en cuivre et les connectons avec des adaptateurs filetés en laiton. Resserrer la connexion clés à molette.Quatrième étape - installer l'équipement de contrôle
L'ensemble de l'équipement de contrôle se compose d'un pressostat (pressostat) avec un capteur de contrôle, d'une soupape de sécurité ou d'une soupape de surpression, d'un adaptateur-raccord avec filetage extérieur et plusieurs robinets et manomètres.
Tout d'abord, nous installons le pressostat. Il doit être légèrement surélevé jusqu'au niveau du compresseur. Nous utilisons un raccord d'extension avec un filetage extérieur et vissons le relais à travers le ruban d'étanchéité.
Grâce à l'adaptateur, nous installons un capteur de régulation de pression avec des manomètres. Nous complétons l'ensemble avec une soupape de surpression et deux robinets pour les sorties de tuyaux.Cinquième étape - connectez l'électricité
À l'aide d'un tournevis, nous démontons le boîtier du pressostat, ouvrant l'accès aux contacts. Nous connectons le câble à 3 conducteurs à groupe de contacts, et répartissez chacun des fils selon le schéma de raccordement (y compris la mise à la terre).
De même, nous connectons le câble d'alimentation, équipé d'une fiche pour une prise de courant. Revissez le couvercle du relais en place.Sixième étape – révision et test
Pour transporter le compresseur, nous attachons une poignée spéciale au châssis du compresseur. Nous le fabriquons à partir de morceaux de profil carré et tuyau rond. Nous le fixons aux boulons de serrage et le peignons dans la couleur du compresseur.
Nous connectons l'installation à un réseau 220 V et vérifions sa fonctionnalité. Selon l'auteur, pour obtenir une pression de 90 psi ou 6 atm, ce compresseur a besoin de 10 minutes. A l'aide d'un capteur de réglage, l'activation du compresseur après une chute de pression est également régulée à partir d'un certain indicateur affiché sur le manomètre. Dans son cas, l'auteur a configuré l'installation pour que le compresseur se rallume à partir de 60 psi ou 4 atm.
La dernière opération restante est une vidange d’huile. Il s’agit d’une partie importante de la maintenance de telles installations, car elles ne disposent pas de fenêtre d’inspection. Et sans huile, ces machines ne peuvent fonctionner que pendant une courte période.
Dévisser boulon de vidange au fond du compresseur et vidangez les déchets dans une bouteille. En tournant le compresseur sur le côté, ajoutez un peu d'huile propre et revissez le bouchon. Maintenant que tout est en ordre, vous pouvez utiliser notre groupe compresseur !
Le compresseur est utilisé pour en libre service voiture, y compris peinture, gonflage des pneus, alimentation en air des outils pneumatiques et autres travaux de réparation. Fabriquer un compresseur pour peindre une voiture - économiquement solution rentable, ce qui ne nécessite pas d'investissements financiers importants.
Principe d'opération
Sur la base du principe de fonctionnement, il existe Divers typeséquipement, mais il est basé sur une technologie - l'air fourni en raison du fonctionnement du moteur est transféré au conteneur et, s'accumulant, atteint niveau supérieur indicateur de pression. Dès que la pression atteint un point critique, l'excès d'air est évacué à l'aide d'une vanne de purge. Ainsi, les compresseurs fonctionnent en maintenant la pression à un certain niveau.
La plupart une condition importante est un indicateur constant du niveau de pression spécifiquement dans les compresseurs utilisés pour peindre une voiture. Cependant, quelle que soit la fonctionnalité de l'outil, ce paramètre est essentiel et la technologie de fabrication et les matériaux utilisés sont donc sélectionnés en fonction de la pression requise. Sur Internet, vous pouvez trouver de nombreux diverses vidéos assemblage de n'importe quel compresseur, cependant, les options les plus populaires sont très peu nombreuses.
Nous assemblons rapidement et facilement
Un des plus Options disponibles compresseur pour travaux de peinture est un instrument fabriqué à partir de caméra de voiture sur roues. C'est elle qui fait office de récepteur. Il faut aussi avoir matériaux suivants et outils :
- Le mamelon d'une autre caméra de voiture.
- Pompe de voiture avec manomètre.
- Consommables pour travailler le caoutchouc.
- Ensemble d'outils automobiles.
La chambre doit être intacte, puisque la fonction principale du récepteur est l'accumulation d'air. Une pompe de voiture agit comme un compresseur dans l'appareil. Nous assemblons le compresseur avec soin en suivant toutes les étapes nécessaires.
Tout d'abord, vous devez faire un trou dans la chambre et coller le mamelon à cet endroit. Ainsi, le mamelon « natif » servira à pomper de l'air dans la chambre, et le nouveau servira à fournir de l'air à l'atomiseur. Ensuite, vous devez régler la pression à l'aide d'un manomètre, en sélectionnant l'indicateur optimal pendant le fonctionnement.
Pour simplifier le travail de fabrication d'un compresseur pour peindre une voiture, vous devez suivre les recommandations suivantes :
- Pour éviter les vibrations lors de l'alimentation en air, la chambre doit être soigneusement sécurisée.
- Vous ne devez pas remplir la chambre de substances en vrac, car cela entraînerait le colmatage des canaux, ce qui signifie que la peinture s'y mélange.
Compresseur avec récepteur
Cette option est de conception beaucoup plus complexe que la précédente. Un tel outil est déjà considéré comme semi-professionnel, ce qui signifie que pour assembler le compresseur, il est nécessaire plus grand nombre outil et matériel. Un élément important d'un tel équipement est un compresseur de réfrigérateur à faire soi-même. Il convient de noter que le compresseur d'un vieux réfrigérateur peut perdre son étanchéité, ce qui signifie que sa fonctionnalité est réduite. Dans de tels cas, il est nécessaire de veiller à changer l'huile. Cette procédure s'effectue comme suit :
- Limez et cassez le tube sur le côté du compresseur.
- Versez de l'huile à l'intérieur à l'aide d'une seringue.
- Scellez le tube avec une vis avec un joint en caoutchouc.
Afin de compenser l'évaporation abondante de l'huile, il est nécessaire d'installer un filtre séparateur d'huile et d'humidité à l'entrée du récepteur, qui empêchera les liquides étrangers de pénétrer dans la peinture.
Après cela, vous devez percer un trou pour l'adaptateur et l'installer en utilisant, par exemple, soudage à froid. La sortie est équipée d'un filtre à air automobile pour empêcher la saleté et les liquides de pénétrer.
Une fois le montage préliminaire réalisé, vous pouvez assembler le compresseur :
- Les fixations sont vissées sur le filtre séparateur et installées d'un côté sur un tuyau renforcé résistant à l'huile et de l'autre sur le tube du compresseur.
- Toutes les connexions sont serrées avec des pinces et les filetages sont scellés avec du ruban fumé.
- Vissez un couvercle en fonte avec un support de joint en caoutchouc.
- Installez l'interrupteur à bascule, le pressostat, le réducteur, le manomètre et connectez tous les fils.
Une fois l'assemblage terminé, le compresseur doit être réglé et testé. Il est certes plus difficile de réaliser soi-même un tel outil, mais ses fonctionnalités sont bien plus étendues. Pour faciliter l'utilisation, des roulettes de meubles peuvent être installées sur le compresseur.
Défauts les plus courants
- Le récepteur ne maintient pas le niveau de pression réglé lorsque l'alimentation est coupée. Ceci est possible s'il y a une fuite dans le système et qu'elle peut être détectée à l'aide d'une solution savonneuse sur les zones les plus vulnérables suivantes :
- Autoroute;
- soupape à piston;
- soupape de surpression sur le récepteur.
Si une fuite est détectée sur la ligne air comprimééliminer ce dysfonctionnement Vous pouvez utiliser du simple ruban isolant et du scellant. S'il y a un dysfonctionnement au niveau du robinet, alors la vanne doit être remplacée.
- Le moteur ne répond pas au démarrage. Tout d'abord, vous devez vous assurer que la source d'alimentation est en bon état de fonctionnement et l'intégrité du câble, et également évaluer la qualité. connexions de contact et des fusibles. Des réglages de pression incorrects sur le récepteur peuvent également affecter les performances de l'instrument. Pour diagnostiquer ce dysfonctionnement, vous devez purger l'air du réservoir et essayer de démarrer le moteur.
- Pas de pompage. La première cause de tels dommages peut être un endommagement du réseau électrique. Il est également possible que la pression dans le récepteur soit trop élevée.
- Surchauffe du compresseur. Cette situation est possible avec une augmentation conditions de température et lorsque la tension chute dans le réseau, ainsi que lorsque long travail outil.
- L'air à la sortie contient de l'eau. En règle générale, les raisons de ce phénomène sont les suivantes :
- L'eau collectée dans le récepteur a atteint un niveau critique
- contamination du filtre d'entrée :
- niveau accru d'humidité ambiante.
Indubitablement, auto-assemblage L'installation d'un compresseur est un processus complexe et long, mais les avantages sont indéniables. Il est à noter que Entretien un tel outil est beaucoup plus simple et moins cher. Peindre une voiture de vos propres mains à l'aide d'un tel compresseur sera également beaucoup moins cher que dans n'importe quel atelier de réparation automobile. Compresseur de peinture à faire soi-même pour une voiture - durera longtemps avec montage correct et le fonctionnement.
Il n'est pas nécessaire d'acheter un compresseur pour des travaux de peinture ou pour gonfler des roues - vous pouvez le fabriquer vous-même à partir de pièces et d'assemblages usagés retirés d'anciens équipements.
Nous vous parlerons des structures assemblées à partir de matériaux de récupération.Afin de fabriquer un compresseur à partir de pièces et d'assemblages usagés, il faut être bien préparé : étudier le schéma, le trouver à la ferme ou acheter des pièces supplémentaires. Regardons quelques-uns options possibles pour fabriquer votre propre compresseur d'air.
Compresseur d'air fabriqué à partir de pièces de réfrigérateur et d'extincteur
Cette unité fonctionne presque silencieusement. Regardons le schéma conception future et dressez une liste des composants et pièces nécessaires.
1 - tube pour le remplissage d'huile ; 2 - relais de démarrage ; 3 - compresseur ; 4 - tubes de cuivre; 5 - tuyaux ; 6 - filtre à gasoil ; 7 - filtre à essence ; 8 - entrée d'air ; 9 - pressostat ; 10 - croix; onze - soupape de sécurité; 12 - té; 13 - récepteur d'un extincteur ; 14 - détendeur avec manomètre ; 15 - piège à humidité et à huile ; 16 - entrée d'air
Pièces, matériaux et outils nécessaires
Les principaux éléments prélevés sont : un motocompresseur provenant d'un réfrigérateur ( meilleure production URSS) et un cylindre d'extincteur, qui servira de récepteur. S'ils ne sont pas disponibles, vous pouvez rechercher un compresseur provenant d'un réfrigérateur qui ne fonctionne pas dans les ateliers de réparation ou dans les points de collecte de métaux. Un extincteur peut être acheté sur le marché secondaire ou vous pouvez impliquer des amis dans la recherche qui, au travail, ont peut-être radié un extincteur, un extincteur, un extincteur pour 10 litres. Le cylindre de l'extincteur doit être vidé en toute sécurité.
De plus, vous aurez besoin de :
- manomètre (comme pour une pompe, un chauffe-eau) ;
- filtre à gasoil ;
- filtre pour moteur à essence;
- pressostat;
- interrupteur à bascule électrique ;
- régulateur de pression (réducteur) avec manomètre ;
- tuyau renforcé;
- Tuyaux d'eau, tés, adaptateurs, raccords + colliers, quincaillerie ;
- matériaux pour créer un cadre - métal ou bois + roues de meubles ;
- soupape de sécurité (pour soulager surpression);
- entrée d'air à fermeture automatique (pour raccordement, par exemple, à un aérographe).
Un autre récepteur viable provenait d’une roue de voiture tubeless. Un modèle extrêmement économique, mais peu productif.
Récepteur de roue
Nous vous invitons à regarder une vidéo sur cette expérience de l'auteur du design.
Pour peindre une voiture, on utilise généralement un pulvérisateur de peinture. Ce compresseur d'air et un pistolet pulvérisateur qui y est connecté. Si vous envisagez un tel équipement pour votre garage, vous pouvez fabriquer vous-même un compresseur ou acheter un modèle d'usine.
Il est assez évident quoi acheter produit prêt beaucoup plus simple. Cela entraîne moins de coûts de main d’œuvre. Cependant autoproduction- Ce des économies importantes finance. De plus, les experts affirment qu'un puissant compresseur électrique fait maison pour voiture avec relais et récepteur peut être beaucoup plus efficace et durable qu'un produit de série. Ci-dessous, nous vous expliquerons comment fabriquer vous-même un compresseur pour peindre une voiture sous une tension de 220 V.

Évidemment, pour le travail, nous devrons collecter certains matériaux. Ainsi, pour assembler un compresseur d'air 220V fait maison pour peindre une voiture, nous aurons besoin des pièces suivantes :
- manomètre;
- boîte de vitesses avec filtre de protection contre l'huile et l'humidité ;
- relais pour régulation de pression;
- filtre de nettoyage pour moteurs à essence;
- traverse pour eau avec fil à l'intérieur;
- adaptateurs filetés;
- pinces;
- moteur;
- destinataire;
- huile moteur;
- interrupteur pour tension 220 V ;

- tubes en laiton;
- tuyau résistant à l'huile;
- Une planche de bois;
- seringue;
- désoxydant;
- goujons, écrous, rondelles;
- mastic, ruban adhésif fumé;
- émail pour métaux;
- scie ou lime
- roues de meubles;
- filtre moteur diesel.
Compiler cette liste n’est pas difficile. Après avoir rassemblé tout ce dont nous avons besoin, nous pouvons nous mettre au travail.
Assemblage du moteur
Nous commençons le travail dès le début élément important- un moteur qui créera la quantité de pression d'air requise. Ici, nous pouvons utiliser un moteur provenant d'un réfrigérateur inutile.
Son dispositif comprend un relais, qui sera nécessaire pour maintenir une pression d'air donnée. Les experts affirment que les anciens modèles soviétiques permettent de réaliser davantage haute pression que les nouveaux moteurs importés.
Nous sortons le moteur du réfrigérateur, le nettoyons soigneusement et le traitons avec un produit pour éviter l'oxydation du boîtier. Après cela, il sera prêt à être peint.

Vous devez maintenant changer l'huile du moteur. Les semi-synthétiques conviennent tout à fait à cela - ils ne sont pas pires que l'huile moteur et contiennent de nombreux additifs utiles.
Le moteur comporte 3 tubes : 1 fermé et 2 ouverts, dans lesquels circule l'air. Afin de déterminer les canaux d'entrée et de sortie, nous allumons le moteur et nous rappelons où l'air entre et d'où il sort. Le tube fermé sert uniquement à changer l'huile. En travaillant avec une lime, nous effectuons une coupe de manière à éviter que de la sciure ne pénètre dans le tube. Nous cassons l'extrémité, retirons l'huile et en versons une nouvelle, en utilisant une seringue prévue à cet effet.
Pour sceller le canal après avoir changé l'huile, sélectionnez une vis de section appropriée, enroulez du ruban d'étanchéité autour d'elle et vissez-la fermement dans le tube.
Nous montons le moteur avec le relais sur une planche épaisse, qui servira de base. On choisit la position dans laquelle il se trouvait au réfrigérateur. Ceci est nécessaire car le relais de démarrage est extrêmement sensible à la façon dont il est placé. En règle générale, il y a des marquages correspondants - respectez emplacement correct pour que le relais fonctionne de manière stable et correcte.

Réservoir d'air - élément nécessaire, qui est nécessairement inclus dans le dispositif compresseur. Il doit être conçu pour une certaine pression pour que l'appareil fonctionne correctement. Nous pouvons utiliser de vieux conteneurs d'extincteurs de dix litres comme récepteur - ils sont durables et hermétiques.
Au lieu d'une vanne de démarrage, nous vissons un adaptateur fileté sur le récepteur - pour l'étanchéité, nous utilisons un ruban FUM spécial. Si le futur récepteur présente des poches de rouille, elles doivent être éliminées par meulage et traitement par des moyens spéciaux. Afin d'éliminer les poches de corrosion à l'intérieur, verser le produit et bien agiter. Ensuite, nous installons la croix d'eau à l'aide de mastic. On peut supposer que le récepteur fait maison est prêt.

Assemblage de l'appareil
Nous fixons le récepteur de l'extincteur avec le moteur à une base constituée d'une planche épaisse. Nous utilisons des écrous, des rondelles et des goujons comme moyens de fixation. Le récepteur doit être positionné verticalement. Pour le fixer, nous prenons trois feuilles de contreplaqué, dans l'une d'elles nous faisons un trou pour le cylindre. Nous attachons les deux feuilles restantes à un support en bois et feuille de contreplaqué, qui contient un récepteur fait maison. Vers le bas socle en bois remonter les roues garnitures de meubles pour une meilleure maniabilité du mécanisme.
Nous mettons un tuyau en caoutchouc sur le tube d'entrée du compresseur, auquel nous connectons un filtre de nettoyage pour moteurs à essence. Des pinces supplémentaires ne seront pas nécessaires, car la taille pression d'entrée l'air est relativement bas. Pour éviter la présence d'humidité et de particules d'huile dans le flux d'air, nous installons en sortie un filtre séparateur huile-humidité pour moteurs diesel. Ici, la pression sera déjà assez élevée, c'est pourquoi des pinces spéciales avec fixations à vis doivent être utilisées pour une fixation supplémentaire.
Le schéma ci-dessous montre comment un modèle fait maison est assemblé Compresseur automobile pour peindre des voitures.

Ensuite, nous connectons un filtre pour éliminer l'huile et l'humidité à l'entrée de la boîte de vitesses, dont nous aurons besoin pour découpler la pression dans le moteur et le cylindre. Nous effectuons le raccordement à l'aide d'une croix de plomberie du côté gauche ou droit. De l'autre côté de la croix, nous installons un manomètre pour surveiller le niveau de pression dans le cylindre. Nous montons un relais de réglage sur l'extrémité supérieure de la croix. Toutes les connexions sont scellées avec du mastic.
À l'aide d'un relais, nous pouvons fournir la pression dont nous avons besoin au récepteur, tout en assurant un fonctionnement progressif du mécanisme. Le relais est réglé par deux ressorts, dont l'un fixe la limite de pression supérieure et le second - la limite inférieure. Nous connectons un contact au compresseur, le second est connecté à la phase zéro du réseau. Nous connectons la deuxième entrée réseau du compresseur via un interrupteur à bascule à la phase secteur. L'interrupteur à bascule permettra d'allumer et d'éteindre l'appareil de l'alimentation électrique sans retirer la fiche de la prise. Nous effectuons la soudure et isolons tout contacts électriques. Après avoir peint notre compresseur fait maison car la voiture sera prête pour les tests.

Test et mise en place d'un compresseur maison pour peindre des voitures
Pour les tests, nous connectons un pistolet pulvérisateur à la sortie. Nous mettons l'interrupteur à bascule en position d'arrêt et allumons la prise prise électrique. Réglez le régulateur de relais au maximum petite valeur et allumez l'interrupteur à bascule. Pour le contrôle, nous utilisons un manomètre. Nous nous assurons que le relais fonctionne correctement les bons moments ouvre le réseau. Utiliser de l'eau avec détergent Nous vérifions l'étanchéité de tous les tuyaux et connexions.
Ensuite, nous vidons le récipient d'air comprimé - une fois que la pression atteint un certain niveau, le relais doit allumer le moteur. Si tout fonctionne bien, vous pouvez essayer d'utiliser l'appareil pour peindre un objet approprié. Nous examinons la qualité et veillons à ce que l'appareil fonctionne de manière stable et puisse être utilisé pour travailler sur des voitures.
L'auteur a ensuite utilisé l'unité de camion, il est entraîné par un moteur triphasé de 3 puissance. Un fait intéressant est que le système est équipé d'une lubrification forcée du compresseur sous pression ; la pompe de la voiture de la direction assistée en est responsable. Si le projet vous intéresse, je vous propose de l'étudier plus en détail !
Matériaux et outils utilisés
Liste des matériaux :
- vieux compresseur depuis un camion ;
- moteur triphasé 3 ch ou similaire;
- poulies, courroies, câblages, interrupteurs, etc. ;
- voiture bouteille de gaz ou autre conteneur similaire ;
- tôles d'acier, tubes profilés, cornières ;
- roues pour chariots de jardin et essieux ;
- tubes, flexibles, raccords, manomètre, filtres, etc. ;
- pompe de direction assistée de voiture (l'auteur possède une Audi 80) ;
- des vis, des écrous, du ruban adhésif et plus encore ;
- un grillage (pour faire un bouclier de protection) ;
- colorant.
Liste des outils :
- Scie à onglet ;
- Bulgare ;
- le soudage ;
- Tournevis;
- percer;
- vice, clés etc.
Processus de fabrication du compresseur :
La première étape. Installation de roues sur le réservoir
Nous installerons des roues sur le réservoir pour que cette lourde machine puisse être transportée. Pour ce faire, nous installons des pinces en acier fiables sur le réservoir et les resserrons avec des boulons et des écrous. C'est à ces pinces que l'on fixera ensuite le tout équipement nécessaire.
Lorsque les pinces sont installées, nous fixons l'essieu avec les roues. Nous utilisons un axe rectangulaire comme tube profilé, auxquels sont soudés les axes ronds des roues. Nous choisissons des roues plus solides, avec roues en acier et sur roulements, car le poids de l'appareil est assez important.
Il faut également souder un pied à l'avant de la machine ; il est constitué d'un morceau de tube auquel est soudée une pièce de tôle d'acier.
Deuxième étape. Fabriquer un cadre pour l'équipement
Le compresseur, ainsi que le moteur, seront installés au dessus du récepteur, ils seront fixés sur des pinces. Nous fabriquons le cadre à partir d'un coin et également en tôle d'acier. Nous perçons des trous pour le compresseur et coupons les filetages ; nous le fixerons statiquement au cadre à l'aide de vis.
Quant au moteur, il doit pouvoir rouler le long du châssis pour que la courroie puisse être tendue. Nous perçons des trous puis les combinons avec une meuleuse pour créer des trous oblongs. En tant que dispositif de tension, nous soudons un écrou allongé au cadre et resserrons le boulon. Maintenant, en serrant le boulon, le moteur peut être éloigné et la courroie tendue.
Nous soudons des morceaux de plaques d'acier au cadre, puis installons le cadre sur le dessus du récepteur. Une poignée peut également être soudée au cadre afin qu'il y ait quelque chose pour maintenir le compresseur ; l'auteur l'a soudé à partir d'un tube profilé.
Troisième étape. Adaptateur
Il y a un trou dans la bouteille grand diamètre, ici vous devez fabriquer un adaptateur, l'auteur l'a fabriqué en tôle d'acier. Nous appliquons le morceau de papier sur le trou et utilisons un crayon pour chercher où percer les trous. Eh bien, c'est une question de technique, nous coupons la pièce, perçons des trous et soudons le tuyau. Il est très important que la soudure soit solide et étanche.
Quatrième étape. Tuyau de vidange et d'arrivée
Nous perçons un trou dans le «ventre» du récepteur et soudons l'écrou. Une vis ordinaire sera utilisée comme « robinet ». Cette pièce est nécessaire pour évacuer la condensation du récepteur, qui s'y formera certainement avec le temps.
Cinquième étape. Test de fuite
Pour vérifier l'étanchéité du cylindre, l'auteur y a versé de l'eau puis a créé une pression supérieure à 20 bars. Si aucune fuite n'est détectée à cette pression, le cylindre est assemblé de manière très fiable. Il est important de tout inspecter soudures et la vis de vidange, ces endroits doivent être secs.
Sixième étape. Équipement de connexion
Ensuite, nous connectons le tuyau du compresseur au récepteur et vissons également un séparateur dans le cylindre pour connecter le tuyau de sélection, le manomètre, la vanne, etc. Tous connexions filetées isoler soigneusement avec du ruban adhésif fumé.
Septième étape. Système de lubrification
Le compresseur a besoin d'une lubrification forcée, pour cela nous avons besoin petite pompe. L'auteur a décidé d'utiliser une pompe de direction assistée de voiture comme pompe ; nous aurons également besoin de tuyaux, d'un manomètre et d'autres pièces de rechange. Le circuit de lubrification est doté d'une vanne à 3 bars ; si la pression d'huile dépasse cette valeur, l'excès d'huile est renvoyé vers le réservoir d'huile.
Huitième étape. Bouclier de protection
Pour la transmission par courroie, vous devez réaliser un écran de protection afin que les vêtements ou autre chose ne s'y coincent pas. Pour cela, nous avons besoin d'une grille en acier ou en aluminium. Nous le coupons, le plions et le cuisons si nécessaire. Eh bien, alors nous vissons la calandre à la voiture.