Compresseur d'air : fabriquez-le à partir d'un réfrigérateur de vos propres mains. Compresseur puissant à faire soi-même Compresseur à membrane à faire soi-même 2 atmosphères
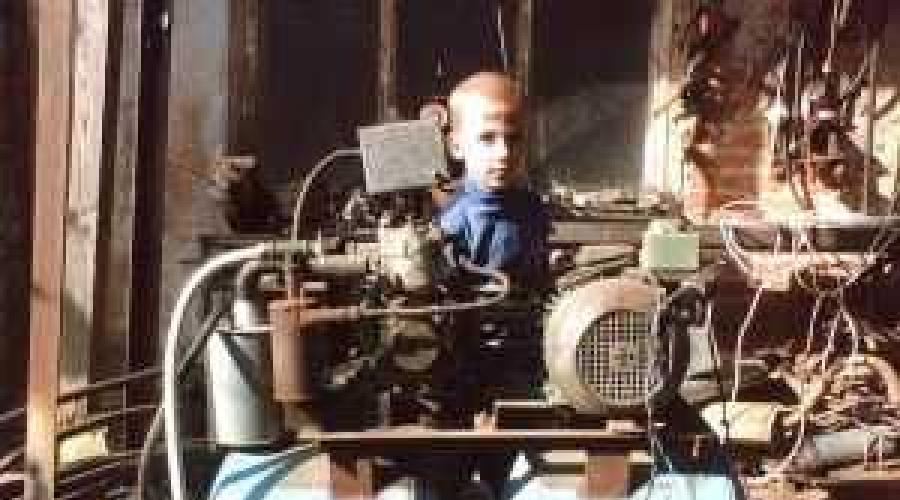
Lire aussi
Un compresseur d'air serait utile dans l'inventaire du garage d'un propriétaire de voiture. Vous pouvez l'utiliser pour peindre une voiture, gonfler des pneus ou fournir de l'air à des outils pneumatiques. Voyons comment fabriquer un compresseur pour peindre de vos propres mains à partir des matériaux disponibles.
L'air comprimé est le véritable assistant d'un vrai maître
Il y a toujours une utilité à un compresseur d'air dans le garage : du simple soufflage de la poussière des surfaces traitées avec un abrasif à la création d'une surpression dans les outils pneumatiques. Une partie considérable de la durée de vie du compresseur est consacrée à la peinture de la voiture. Et cela impose certaines exigences sur le flux d'air créé.
Il doit s'écouler de manière strictement uniforme et ne contenir aucune impureté sous forme de gouttes d'eau, d'huile ou de particules solides en suspension. Les défauts tels que le grain, le galuchat et les cavités sur une couche de peinture fraîchement appliquée sont précisément dus à la pénétration de particules étrangères dans le flux. Des gouttes de peinture et des taches ternes sur l'émail se produisent lorsque le mélange s'écoule de manière inégale.
Les compresseurs d'air de marque du fabricant ont toutes les fonctions nécessaires au fonctionnement idéal d'un aérographe, mais ils coûtent très cher. Vous pouvez économiser de l'argent et créer vous-même un modèle fonctionnel qui n'est pas inférieur aux modèles professionnels en étudiant les informations théoriques et en regardant le matériel vidéo « compresseur à faire soi-même » comme guide. Le principe de fonctionnement de tous les modèles, qu'ils soient faits maison ou professionnels, est assez simple et est le suivant. Un dispositif de stockage d’air comprimé, appelé « récepteur », crée une surpression. L'air peut être pompé manuellement ou mécaniquement.
Lors de l'alimentation manuelle, des ressources financières sont économisées, mais beaucoup d'efforts et d'énergie sont consacrés au contrôle du processus. Avec l'injection automatique, tous ces défauts sont éliminés ; il ne reste plus qu'un changement d'huile de routine dans la pompe à air. Ensuite, l'air comprimé est fourni via le raccord de sortie selon un flux uniforme vers les actionneurs. Comme vous pouvez le constater, il n'y a rien de compliqué et vous pouvez créer un modèle fonctionnel en quelques minutes.
Fabriquer un compresseur simple de vos propres mains
Une option serait de fabriquer un compresseur pour peindre à partir d’une chambre à air de voiture d’occasion. Pour la production, vous aurez besoin de :
- Le récepteur est une caméra de voiture. Possible avec un pneu, possible sans lui
- Compresseur – pompe de voiture avec manomètre
- Mamelon d'un mauvais appareil photo
- Kit de réparation pour caoutchouc
- Poinçon de tailleur
Après avoir rassemblé le matériel nécessaire, nous procédons directement à la fabrication de l'appareil. Nous prenons une chambre à air de voiture inutile et vérifions son étanchéité en la gonflant. Si le ballon retient l’air, alors tout va bien et vous pouvez passer à l’étape suivante. S'il y a des fuites, localisez les zones endommagées et colmatez-les ou vulcanisez-les avec du caoutchouc brut.
Ensuite, un trou est pratiqué dans le récepteur préparé pour un mamelon supplémentaire, à travers lequel un flux uniforme d'air comprimé sortira ensuite. Nous collons le raccord supplémentaire à l'aide d'un kit de réparation en caoutchouc et le connectons au pistolet pulvérisateur. Nous dévissons le mamelon - le flux d'air doit sortir librement. Nous laissons le mamelon dans le mamelon d'origine de la caméra de la voiture - il fonctionnera comme une valve, retenant l'excès de pression.
Ensuite, nous déterminons expérimentalement le niveau de pression d'air requis dans le récepteur en pulvérisant de la peinture sur n'importe quelle surface. L'émail doit reposer uniformément, sans saccades. La quantité de surpression est déterminée à l'aide d'un manomètre et doit être telle que lorsque vous appuyez sur le bouton de l'aérateur, son niveau ne change pas brusquement.
Assembler un tel modèle de compresseur ne sera pas difficile, mais vous serez immédiatement convaincu de l'efficacité des réparations à l'aide d'un compresseur plutôt que d'utiliser des pots de peinture. L'essentiel est de suivre la règle - aucune humidité ni poussière ne doit pénétrer dans la chambre de la voiture et, par conséquent, dans le pistolet pulvérisateur. Sinon, ils se mélangeront à l'émail de la voiture et tous les travaux de peinture devront être refaits. Le modèle assemblé fonctionnera correctement, mais il est préférable d'automatiser l'injection d'air et d'apporter des modifications supplémentaires à la conception.
Compresseur semi-professionnel pour peinture DIY
Selon les experts, les compresseurs faits maison avec récepteurs ont une durée de vie plus longue que les modèles de fabricants nationaux et étrangers. Et cela est compréhensible - tout est fait de vos propres mains et, même si une pièce tombe en panne, son remplacement ne prendra que quelques minutes. Voyons comment fabriquer un compresseur d'air qui n'est pas inférieur aux produits d'entreprises bien connues à partir de matériaux facilement disponibles dont nous aurons besoin selon la liste ci-dessous :
- Manomètre
- Boîte de vitesses avec filtre séparateur d'huile et d'eau
- Relais de contrôle de pression
- Filtre à essence
- Traverse de plomberie (quad) avec filetage intérieur trois-quarts
- Adaptateurs filetés
- Pinces de voiture
- Moteur du compresseur
- Récepteur
- Huile moteur semi-synthétique de viscosité 10W40
- interrupteur à bascule 220 volts
- Tubes en laiton
- Tuyau résistant à l'huile
- Planche épaisse pour base
- Seringue de pharmacie
- Convertisseur de rouille
- Goujons, écrous, rondelles
- Scellant, ruban fumé
- Peinture métal
- Lime aiguille
- Roues de meubles
- Filtre d'alimentation moteur diesel
Trouver tous les composants n’est pas difficile ; vous devez commencer par le cœur de l’ensemble du système : le ventilateur.
Moteur – actionneur d’un compresseur automatique
Nous utiliserons un compresseur d'un vieux réfrigérateur comme moteur. En règle générale, ils sont équipés d'un relais de démarrage, très pratique pour maintenir en permanence un certain niveau de pression dans le récepteur. Il est préférable d'utiliser des compresseurs d'anciens réfrigérateurs de style soviétique ; ils permettent de pomper une pression plus élevée que leurs homologues importés.
Après avoir retiré l'unité de commande de l'ancien réfrigérateur, nettoyez-la de la saleté et de la rouille accumulées. Traitez ensuite avec un convertisseur de rouille pour éviter une oxydation supplémentaire. Cela préparera le carter du moteur pour une peinture ultérieure.
Ensuite, vous devez changer l'huile du compresseur. Un réfrigérateur a rarement fait l'objet d'un entretien régulier et d'un remplacement du lubrifiant, ce qui est tout à fait justifié : le système est complètement isolé des effets de l'atmosphère. Vous pouvez utiliser de l'huile moteur semi-synthétique ; elle n'est en aucun cas inférieure à l'huile pour compresseur et contient en outre de nombreux additifs utiles.
Il y a trois tubes sur le compresseur – 2 ouverts et un scellé. Les extrémités ouvertes sont conçues pour la circulation de l'air, l'un des tubes est l'entrée, l'autre est la sortie. Pour déterminer le chemin emprunté par l’air, mettez brièvement le compresseur sous tension. Et rappelez-vous quel conduit aspire l’air et lequel l’évacue.
Le tube scellé est destiné aux vidanges d'huile de routine. L'extrémité fermée doit être soigneusement retirée. Pour ce faire, nous limons le tube en cercle avec une lime aiguille, en essayant d'empêcher la limaille de métal de pénétrer à l'intérieur du système. Ensuite, nous cassons la pointe sciée et vidons l'ancienne huile dans un récipient pour déterminer la quantité à remplacer. Et remplissez le semi-synthétique en quantité légèrement plus importante à l'aide d'une seringue.
Ensuite, le système de lubrification du moteur doit être désactivé. Pour ce faire, sélectionnez une vis de la taille appropriée, enveloppez-la de ruban adhésif pour la sceller et vissez-la dans un tube. Un ventilateur de réfrigérateur a tendance à laisser échapper de la graisse, c'est-à-dire qu'il y a des gouttelettes d'huile dans le flux d'air de sortie. Ils seront retenus par le séparateur huile/humidité du compresseur. De nos propres mains, nous montons ensuite le moteur avec le relais de démarrage sur un socle en bois dans la position dans laquelle il était fixé au châssis.
Le relais du compresseur est sensible à sa position dans l'espace et son capot supérieur est souvent marqué d'une flèche. Ce n'est qu'avec une installation correcte que le processus de changement de mode se déroulera correctement.
Conteneur d'air comprimé
Les cylindres d'extincteur sont les mieux adaptés au stockage de l'air comprimé. Ils sont conçus pour des pressions élevées, disposent d'une grande marge de sécurité et sont idéaux pour le montage d'accessoires. Considérons le corps métallique d'un extincteur OU-10 d'un volume utile de 10 litres comme récepteur. Ce cylindre est conçu pour une pression de 15 MPa ou 150 bar avec une grande marge de sécurité.
Nous dévissons le dispositif de verrouillage et de démarrage (ZPU) du futur récepteur et à sa place nous vissons un adaptateur, sur les filetages duquel nous enroulons du ruban fumé pour le sceller. Si l'extincteur présente des traces de corrosion, celles-ci doivent être éliminées à l'aide d'abrasifs et d'un convertisseur de rouille.A l'extérieur, tout est facile à faire, mais à l'intérieur il faudra bricoler un peu. Pour ce faire, versez un produit antirouille à l'intérieur du flacon selon les instructions et agitez soigneusement le contenu. Ensuite, nous vissons la croix de plomberie, en utilisant du mastic et du ruban fumé pour l'étanchéité. Ainsi, les deux parties principales de notre compresseur sont prêtes et nous pouvons passer à l’étape suivante.
Installation de pièces d'appareil
Pour faciliter le stockage et le déplacement, il est préférable de disposer toutes les pièces du compresseur de manière compacte sur une seule base. Nous utiliserons une planche de bois comme base sur laquelle nous monterons solidement le moteur - le compresseur et le boîtier de l'extincteur.
Nous fixons le moteur du compresseur à l'aide de tiges filetées enfilées dans des trous pré-percés et d'écrous avec rondelles. Nous plaçons le récepteur verticalement, en utilisant trois feuilles de contreplaqué pour le fixer, dans l'une desquelles nous découpons un trou pour le cylindre.
Nous fixons les deux autres à l'aide de vis autotaraudeuses à la planche de support et les collons à la feuille retenant le récepteur. Sous le bas du récepteur, à la base, on creuse un évidement de taille appropriée. Pour plus de maniabilité, nous vissons des roues fabriquées à partir de ferrures de meubles à notre base. Ensuite nous effectuons les opérations suivantes :
Il ne reste plus qu'à peindre l'ensemble du compresseur et à passer aux tests sur le terrain.
Réglage de la pression dans la chambre du récepteur
Après avoir assemblé la structure, vous devez vérifier sa fonctionnalité. Nous connectons un pistolet pulvérisateur ou un pistolet de gonflage de pneus à la sortie du compresseur. Après cela, avec l'interrupteur à bascule éteint, branchez la fiche sur le réseau. Nous réglons le relais de commande à la pression minimale, puis alimentons le compresseur. La pression créée dans le récepteur est contrôlée à l'aide d'un manomètre. Après s'être assuré que lorsqu'un certain niveau est atteint, le relais coupe le moteur, on vérifie l'étanchéité des conduits d'air et des raccords. C'est facile à faire avec une solution savonneuse.
Après s'être assuré que l'air comprimé ne quitte pas le système, nous le purgeons de la chambre réceptrice. Dès que la pression dans le cylindre descend en dessous du repère réglé, le relais doit fonctionner et démarrer le compresseur. Si tout fonctionne correctement, vous pouvez essayer de peindre des pièces inutiles. Les travaux préliminaires pour préparer la surface à l'application de l'émail ne sont pas nécessaires ici - il est important pour nous de développer des compétences et de déterminer quelle pression sera nécessaire pour peindre le produit. Nous déterminons expérimentalement la valeur en atmosphères à laquelle la surpression est suffisante pour peindre la pièce entière en une couche uniforme avec un nombre minimum d'activations de soufflerie.
Comme vous pouvez le constater, créer un compresseur de voiture de vos propres mains n'est pas particulièrement difficile. Un appareil fabriqué selon la deuxième option nécessite plus de temps de fabrication, mais tout cela sera payant avec une utilisation ultérieure. Le système de contrôle automatique de la pression et de démarrage du compresseur vous permettra de travailler plus facilement, sans être distrait par le contrôle de la chambre de réception. Le compresseur peut être utilisé non seulement pour l'entretien de la voiture. Vous pouvez l'utiliser pour peindre une clôture ou une porte de garage.
Pour qu'un compresseur fabriqué soi-même fonctionne longtemps et correctement, un entretien de routine doit être effectué. Il s'agit avant tout de vidanges d'huile régulières et de remplacement rapide des éléments filtrants. Puisque nous avons solidement fixé le moteur à la base, cela ne sert à rien de le dévisser. Nous utilisons une seringue pour vidanger l'huile. Après avoir dévissé la vis qui ferme l'orifice de remplissage, placez fermement le tuyau sur le tube et pompez les déchets. Nous pompons également de l’huile moteur fraîche à l’aide d’une seringue. Avec les filtres, tout est plus simple : nous les changeons au fur et à mesure qu'ils s'encrassent et le taux de remplissage de la chambre réceptrice diminue.
L'alternative est de le faire soi-même ou d'acheter des produits prêts à l'emploi ?
Aujourd’hui, le marché des offres de compresseurs d’air est très varié. Les pistons, les vibrations, les vis et de nombreuses autres classes de ces dispositifs sont produits à des fins diverses. Les compresseurs prêts à l'emploi peuvent être achetés dans les magasins d'électroménager, les magasins de pièces automobiles et sur des sites Internet spécialisés. La variété des produits proposés est si grande que le choix du produit souhaité prendra beaucoup de temps. Si vous décidez d'acheter un appareil prêt à l'emploi, étudiez attentivement les spécifications techniques, la fourchette de prix et les avis des clients.
Bien sûr, il vaut mieux ne pas économiser d’argent et acheter des produits coûteux de marques célèbres. Mais un achat à gros budget n’en vaut la peine que si vous envisagez de réparer des voitures de manière professionnelle. Choisir des produits peu connus comporte des risques injustifiés. Les modèles bon marché souffrent de matériaux de mauvaise qualité. Il arrive souvent que des pièces de moteur s'envolent instantanément et que les réparations sous garantie prennent plusieurs mois.Du point de vue de la fiabilité, l'assemblage fait main gagne à bien des égards. Premièrement, selon les statistiques, les compresseurs des réfrigérateurs fonctionnent depuis des décennies. Et le vieux réfrigérateur est jeté non pas à cause d'un moteur cassé, mais à cause d'une fuite de réfrigérant ou d'une corrosion des parois et du fond. Et il n'y a rien à dire sur les extincteurs - ils sont fabriqués avec une marge de sécurité décuplée, qui est immédiatement vérifiée en usine. Alors peut-être ne devriez-vous pas acheter un cochon en un clin d'œil, mais fabriquer l'appareil vous-même ? De plus, après avoir étudié le matériel, vous savez comment fabriquer un compresseur de vos propres mains à la maison. Un appareil bien conçu et fonctionnant correctement plaira non seulement au propriétaire, mais fera également l'envie des autres passionnés de voitures.
Un compresseur est un appareil multifonctionnel qui peut être utilisé pour divers besoins quotidiens, tels que gonfler des pneus de voiture, peindre, etc. Mais en raison du coût élevé des modèles d'usine, de nombreux propriétaires envisagent d'assembler eux-mêmes une telle unité. L'option la plus courante pour créer un compresseur de vos propres mains consiste à utiliser un réfrigérateur.
Avantages des appareils d'usine et faits maison
Avant de fabriquer votre propre compresseur d'air à partir d'un réfrigérateur, vous devez le comparer avec un modèle d'usine ordinaire. Cela vous aidera à prendre la bonne décision.
Z les appareils d'usine et faits maison présentent les différences suivantes :

Limites du fonctionnement du moteur
Tous les moteurs de réfrigérateur ne peuvent pas fonctionner dans les mêmes conditions. Certains d’entre eux ont leurs propres limites de fonctionnement.
Plusieurs modes de fonctionnement peuvent être distingués :
- normal - de 16 à 32 degrés;
- tropical - de 18 à 43 degrés;
- subnormal - de 10 à 32 degrés;
- subtropical - de 18 à 38 degrés.
Mais malgré cela, il existe également des modes combinés qui incluent plusieurs plages de fonctionnement.
Ainsi, les appareils faits maison sont beaucoup plus simples et efficaces que ceux d'usine, notamment pour travailler avec l'air.
Travaux de démontage de réfrigérateur
Afin de fabriquer un mini-compresseur de vos propres mains, vous devez vous préparer au travail. Vous devez d’abord retirer le compresseur directement du réfrigérateur. C'est la première étape. Il est situé au bas du réfrigérateur, à l'arrière. Pour le retirer, vous devez préparer un ensemble d'outils de base : une pince, un jeu de clés et des tournevis (bouclés et réguliers).
Il y a deux tubes sur le compresseur lui-même qui se connectent au système de refroidissement du réfrigérateur. Ils doivent être mordus à l'aide d'un coupe-fil ou d'une pince. Il est strictement interdit de les scier avec une scie à métaux, car lors du sciage, de petits morceaux de métal peuvent pénétrer dans le moteur, ce qui peut entraîner des conséquences catastrophiques.
Après cela, vous devez retirer le relais de démarrage. Cela ressemble à une boîte noire ordinaire avec des fils qui en sortent. Vous devez d'abord dévisser les attaches, puis couper les fils menant à la fiche. N'oubliez pas de marquer le haut et le bas du relais afin qu'il n'y ait pas d'erreur lors de l'installation ultérieure. Vous devez également récupérer tous les éléments de fixation de l'unité ; ils peuvent également être utiles lors de la fabrication d'un compresseur haute pression de vos propres mains.
Vérification de la fonctionnalité
Après avoir démonté le réfrigérateur et le compresseur, vous devez vérifier le fonctionnement de toutes les pièces. Cela doit être fait car la pièce a été retirée de l'ancien réfrigérateur et elle risque de ne pas fonctionner pendant longtemps. Il est donc impératif de le faire. Tout d'abord, aplatissez les tubes avec une pince.
Cela doit être fait pour que l'air puisse les traverser. Ensuite, vous devez remettre le relais précédemment retiré dans la même position qu'avant. N'oubliez pas l'installation correcte du relais. Le haut et le bas doivent être en place. S'il est installé d'une manière différente, le compresseur peut tomber en panne, ce qui entraînera des dommages irréparables, voire un grillage.
Il y a des fils directement sur le corps du relais. Il est nécessaire d'y visser le câblage avec une fiche. L'endroit où la connexion sera effectuée doit être enveloppé d'au moins du ruban électrique pour éviter les chocs électriques. Il est conseillé de souder soigneusement la jonction des fils avant de procéder à cette opération.
Après cela, branchez le compresseur dans la prise et observez les performances de l'unité. Si cela ne fonctionne pas, cela signifie que les fils ne sont pas connectés correctement ou que le compresseur ne fonctionne pas. Après avoir allumé le compresseur, l'air devrait sortir des tubes. Ce sera un indicateur des performances de l'appareil. Il faut marquer de quel tube l'air sort et lequel entre.
Instructions de montage étape par étape
Avant de commencer, vous devez préparer tous les outils et matériels nécessaires. Ces kits peuvent différer les uns des autres en fonction des attentes du futur propriétaire du compresseur.
En plus du compresseur lui-même, qui est retiré du réfrigérateur, vous devez préparer ce qui suit son:

Ensuite, vous devriez prendre un récipient en plastique de n'importe quelle taille à partir de trois litres. Dans la partie supérieure du conteneur, vous devez percer plusieurs trous pour les tuyaux du compresseur. Insérez ensuite les tubes dans les trous réalisés et remplissez le tout de résine. Dans ce cas, le tube d'entrée doit être situé à une distance de 200 mm du bord du récepteur. Le tube de sortie doit être placé à 10 mm à l'intérieur du récipient.
Le récepteur peut être en plastique, et rien de mal n'arrivera ici. Mais pour une plus grande fiabilité, il est recommandé de le réaliser à partir d'une boîte métallique. Avec ce résultat, plus besoin de tout remplir de résine pour une bonne étanchéité, et les durites sont fermées. De plus, seul un manomètre peut être installé sur un corps métallique.
Pour ce faire, vous devez percer un trou dans le récepteur pour un écrou, qui doit être soudé dans un tel trou. Il existe ensuite la possibilité de visser le manomètre dans l'écrou. Après cela, le travail de création d'un compresseur fait maison à partir d'un réfrigérateur se termine. Tous les matériaux peuvent être utilisés pour la peinture, mais vous pouvez d'abord le nettoyer et l'apprêter pour éviter la corrosion. Après cela, il vous suffit de fixer le récepteur à la base à l'aide d'un fil.
Quelques caractéristiques techniques
Il est assez difficile de déterminer dans un premier temps quelle sera la pression dans le compresseur. Cet indicateur peut dépendre à la fois de la marque de l'appareil et de la durée de son fonctionnement déclaré.
À propos, les anciennes conceptions peuvent parfois donner des résultats encore meilleurs que les nouvelles conceptions d'usine. Le plus important n'est pas le type d'appareil que vous pouvez assembler, mais la manière dont vous devrez prendre soin de son état.
Ces travaux consistent généralement à remplacer les filtres (essence et diesel), ainsi que l'huile de l'appareil. Tous les compresseurs faits maison sont équipés de trois tubes en cuivre. Deux sont utilisés lors de l'installation. C'est le tube d'entrée et de sortie. Le troisième n'a pas été touché. C'est le plus court de tous et scellé à la fin. Elle est chargée de vidanger l'huile de l'appareil. Pour l'entretien, vous devez couper la partie scellée, vidanger l'huile, remplir d'huile neuve et la souder.
Le compresseur est-il réparable ?
En règle générale, le relais doit être sonné lors des réparations. Vous devez également changer l'huile de l'appareil. Si le compresseur ne fonctionne toujours pas, il ne sert à rien de faire autre chose ; il faut arrêter les réparations. Il vaut mieux jeter un tel autocompresseur et en fabriquer un nouveau. De plus, son prix ne dépassera pas mille et demi de roubles.
À propos, comme matériau source pour le compresseur, un moteur à combustion interne avec compresseur peut également être utilisé. De cette façon, vous pouvez obtenir un appareil décent avec une grande puissance. De plus, le groupe de pistons dispose d'une réserve de puissance élevée. Si vous en avez l'opportunité et l'envie, vous pouvez le trouver pour un prix assez bas en excellent état. Avec cette option, les systèmes d'allumage, d'admission et d'échappement doivent être supprimés. Pour son bon fonctionnement, il suffit de lubrifier les pistons, le système de refroidissement et l'étanchéité.
Des structures similaires peuvent être réalisées à partir d’une bouteille de gaz. Il existe également des compresseurs à membrane.
Un compresseur d'air est un appareil qui pulvérise de la peinture. Il est couramment utilisé dans les ateliers et garages pour peindre les voitures ou gonfler les roues. Vous pouvez acheter un tel équipement dans un magasin spécialisé ou le fabriquer vous-même. Contrairement aux modèles d'usine, les équipements faits maison peuvent être plus efficaces et durer beaucoup plus longtemps. De plus, en termes de coûts financiers, la production indépendante sera moins chère.
En utilisant un accessoire de voiture, vous pouvez fabriquer un compresseur de conception simple. Il s'agit d'un appareil électrique prêt à l'emploi - dispositif de gonflage des roues. Le compresseur a deux propriétés positives :
- Pouvoir. L'appareil est capable de créer une haute pression jusqu'à 5 à 6 atmosphères, sans charge inutile sur le moteur. C'est le principal avantage des appareils automobiles. Mais il faudra environ 10 minutes pour gonfler les roues. Par conséquent, le travail est effectué par intermittence, sinon des appareils bon marché pourraient surchauffer pendant cette période. La raison en est les faibles performances des compresseurs automobiles.
- Performance. Par unité de temps, l'appareil est capable de libérer de l'air rapidement et en grande quantité. Grâce à ses performances élevées, le récipient se remplit plus rapidement et l'utilisation directe de l'air comprimé rend le débit de la buse plus fort.
Un moteur à haut régime et un dispositif doté d'un système de pistons volumétriques permettront d'allier puissance et performances. Pour éviter que l'équipement ne s'arrête en cas de surchauffe, il est nécessaire de créer un refroidissement supplémentaire des cylindres. Parfois, des turbines sont utilisées pour l'unité de travail. Dans la vie de tous les jours, les appareils simples ne sont pas souvent utilisés en raison de leur coût élevé. Afin de ne pas avoir à choisir entre puissance et performances, utilisez un récepteur.
Le récepteur est un réservoir de stockage. Pour les appareils industriels, un cylindre en acier est utilisé comme récepteur. Un compresseur assez puissant mais peu efficace remplit lentement le cylindre. En peu de temps, un débit volumétrique d'air peut être fourni par le récepteur, mais uniquement lorsqu'une pression suffisante apparaît. Une fois l’air fourni, il devrait rétablir la pression. Tous les appareils fonctionnent sur ce principe. Pour un compresseur de faible puissance, un moteur électrique issu d'un jouet convient. Cet appareil est souvent utilisé pour alimenter en air un aquarium.
Compresseur fait maison fonctionnel
Contrairement aux appareils fabriqués à partir d’accessoires automobiles, le compresseur d’un réfrigérateur fonctionne en continu. Cela est dû à une bonne puissance et de bonnes performances. De plus, la qualité n'est pas pire que celle des modèles d'usine. Et s'il est possible d'obtenir les composants gratuitement, la production d'un tel appareil coûtera un minimum. L'appareil est conçu pour la peinture et le soufflage, le montage de pneus et offre d'excellentes performances pour les outils pneumatiques. Pour la fabrication d'un compresseur pour 220 V vous aurez besoin des pièces suivantes :
- Moto-compresseur d'un vieux réfrigérateur.
- Tés, tube de remplissage d'huile, durites, raccords, entrées d'air.
- Un réducteur qui surveillera la pression.
- Deux manomètres.
- Récepteur. Un extincteur ou une bouteille de gaz, qui doit être complètement vide, conviennent pour cela. Vous pouvez souder un récipient fait maison en tôle et un tuyau épais.
- Filtre pour la purification de l'air.
- Huile.
- Valve d'urgence.
- Relais de démarrage et pressostat.
- Peinture pour métal.
- Du ruban adhésif, une scie à métaux et de l'huile moteur.
- Clé et seringue.
L'assemblage du compresseur comprend plusieurs étapes :

Compresseur haute puissance
Si la version précédente du compresseur n'est pas assez puissante pour vous, il existe des appareils avec plus haute pression et productivité élevée. Un moteur à combustion interne est utilisé comme compresseur, dont le vilebrequin commence à fonctionner non pas à partir de la combustion du carburant, mais à partir du processus inverse. Dans le même temps, le groupe de pistons de l'appareil dispose d'une grande marge de sécurité. Un moteur électrique d'une puissance de 3 kW ou plus est utilisé comme entraînement, qui peut être acheté à faible coût. Ou utilisez un moteur en état de marche, en retirant le système d'allumage et d'admission, l'échappement, le groupe de démarrage et la boîte de vitesses.

Cet appareil est capable de créer une pression de 10 atmosphères. Très bruyant.
Compresseur d'air de puissance moyenne
D'une bouteille de gaz ou d'un extincteur un compresseur d'air de puissance moyenne est créé. Pour ce faire, connectez un vieil extincteur (cylindre) et un puissant compresseur automatique pour gonfler les roues. Lorsque vous fabriquez vous-même l'appareil, vous devez suivre les règles suivantes :
- Les conteneurs présentant des dommages mécaniques et des dépôts corrosifs ne peuvent pas être utilisés.
- La structure doit être bien fixée.
- Un revêtement en acier doit être réalisé. Ceci est nécessaire si le récepteur se rompt accidentellement.
- Il est nécessaire de prévoir une réserve de pression. Si vous envisagez d'augmenter la pression à 5 atmosphères, sa résistance doit être de 10 atmosphères.
- Pour garantir que le compresseur s'éteint automatiquement lorsque la pression atteint son maximum, un capteur d'arrêt d'urgence est installé. Ou vous devez installer une vanne mécanique qui, si nécessaire, fournira une libération de pression d'urgence.
- L'appareil haute pression ne doit pas être laissé trop longtemps s'il est utilisé dans de rares cas. Pour maintenir l'étanchéité, 0,5 atmosphère suffit.
Ne négligez pas les précautions de sécurité : n'oubliez pas d'installer des capteurs d'urgence. Un pneu surgonflé éclatera tout simplement et si un cylindre en acier explose, vous pourriez être grièvement blessé.
Il est facile de fabriquer un compresseur de vos propres mains. Sa conception peut être simple ou complexe, l'essentiel est de savoir à quoi elle est destinée et combien vous êtes prêt à dépenser pour sa fabrication. Mais n'oubliez pas que l'appareil doit répondre aux exigences techniques de sécurité.
Ensuite, l'auteur a utilisé une unité provenant d'un camion ; elle est entraînée par un moteur triphasé de 3 chevaux. Un fait intéressant est que le système est équipé d'une lubrification forcée du compresseur sous pression ; la pompe de la voiture de la direction assistée en est responsable. Si le projet vous intéresse, je vous propose de l'étudier plus en détail !
Matériaux et outils utilisés
Liste des matériaux :
- un vieux compresseur provenant d'un camion ;
- moteur triphasé 3 CV. ou similaire ;
- poulies, courroies, câblages, interrupteurs, etc. ;
- bouteille de gaz automobile ou autre contenant similaire ;
- tôles d'acier, tubes profilés, cornières ;
- roues pour chariots de jardin et essieux ;
- tubes, flexibles, raccords, manomètre, filtres, etc. ;
- pompe de direction assistée de voiture (l'auteur possède une Audi 80) ;
- des vis, des écrous, du ruban adhésif et plus encore ;
- un grillage (pour faire un bouclier protecteur) ;
- colorant.
Liste des outils :
- scie à onglet ;
- Bulgare ;
- le soudage ;
- un tournevis ;
- percer;
- étaux, clés, etc.
Processus de fabrication du compresseur :
Première étape. Installation de roues sur le réservoir
Nous installerons des roues sur le réservoir pour que cette lourde machine puisse être transportée. Pour ce faire, nous installons des pinces en acier fiables sur le réservoir et les resserrons avec des boulons et des écrous. C'est sur ces pinces que nous fixerons ensuite tout le matériel nécessaire.
Lorsque les pinces sont installées, nous fixons l'essieu avec les roues. Nous utilisons un tube profilé rectangulaire comme axe, auquel sont soudés des axes ronds pour les roues. Nous choisissons des roues plus solides, avec des jantes et des roulements en acier, car le poids de l'appareil est assez important.
Il faut également souder un pied à l'avant de la machine ; il est constitué d'un morceau de tube auquel est soudée une pièce de tôle d'acier.
Deuxième étape. Fabriquer un cadre pour l'équipement
Le compresseur, ainsi que le moteur, seront installés au dessus du récepteur, ils seront fixés sur des pinces. Nous fabriquons le cadre à partir d'un coin et également en tôle d'acier. Nous perçons des trous pour le compresseur et coupons les filetages ; nous le fixerons statiquement au cadre à l'aide de vis.
Quant au moteur, il doit pouvoir rouler le long du châssis pour que la courroie puisse être tendue. Nous perçons des trous, puis les combinons avec une meuleuse pour créer des trous oblongs. En tant que dispositif de tension, nous soudons un écrou allongé au cadre et resserrons le boulon. Maintenant, en serrant le boulon, le moteur peut être éloigné et la courroie tendue.
Nous soudons des morceaux de plaques d'acier au cadre, puis installons le cadre au-dessus du récepteur. Une poignée peut également être soudée au cadre afin qu'il y ait quelque chose pour maintenir le compresseur ; l'auteur l'a soudé à partir d'un tube profilé.
Troisième étape. Adaptateur
Il y a un trou de grand diamètre dans le cylindre ; un adaptateur doit être réalisé ici ; l'auteur l'a fabriqué en tôle d'acier. Nous appliquons le morceau de papier sur le trou et utilisons un crayon pour chercher où percer les trous. Eh bien, c'est une question de technique, nous coupons la pièce, perçons des trous et soudons le tuyau. Il est très important que la soudure soit solide et étanche.
Quatrième étape. Tuyau de vidange et d'arrivée
Nous perçons un trou dans le «ventre» du récepteur et soudons l'écrou. Une vis ordinaire sera utilisée comme « robinet ». Cette pièce est nécessaire pour évacuer la condensation du récepteur, qui s'y formera certainement avec le temps.
Cinquième étape. Test de fuite
Pour vérifier l'étanchéité du cylindre, l'auteur y a versé de l'eau puis a créé une pression supérieure à 20 bars. Si aucune fuite n'est détectée à cette pression, le cylindre est assemblé de manière très fiable. Il est important d'inspecter toutes les soudures et la vis de vidange ; ces zones doivent être sèches.
Sixième étape. Équipement de connexion
Ensuite, nous connectons le tuyau du compresseur au récepteur et vissons également un séparateur dans le cylindre pour connecter le tuyau de sélection, le manomètre, la vanne, etc. Toutes les connexions filetées sont soigneusement isolées avec du ruban fumé.
Septième étape. Système de lubrification
Le compresseur a besoin d'une lubrification forcée, pour cela nous avons besoin d'une petite pompe. L'auteur a décidé d'utiliser une pompe de direction assistée de voiture comme pompe ; nous aurons également besoin de tuyaux, d'un manomètre et d'autres pièces de rechange. Le circuit de lubrification est doté d'une vanne à 3 bars ; si la pression d'huile dépasse cette valeur, l'excès d'huile est renvoyé vers le réservoir d'huile.
Huitième étape. Bouclier de protection
Pour la transmission par courroie, vous devez réaliser un écran de protection afin que les vêtements ou autre chose ne s'y coincent pas. Pour cela, nous avons besoin d'une grille en acier ou en aluminium. Nous le coupons, le plions et le cuisons si nécessaire. Eh bien, alors nous vissons la calandre à la voiture.
Chaque garagiste rêve de sa propre source d'air comprimé - en ayant un compresseur dans les poubelles du garage, vous pouvez effectuer vous-même de nombreux travaux de réparation de votre voiture. Mais le coût d'un nouveau compresseur est assez élevé et acheter un ancien à vos risques et périls n'est pas une bonne idée. Bien que, dans de rares cas, vous puissiez tomber sur une offre très rentable. Si vous avez encore besoin de matériel professionnel, vous pouvez vous familiariser avec le catalogue vendu par TekhMash Group of Companies LLC.
Mais dans tous les cas, un compresseur haute pression à faire soi-même est une excellente option qui nécessite des dépenses minimes.
Que faut-il pour cela ? Tout d’abord, vous devez savoir comment fonctionne le compresseur de base du kit. Et voici le moteur, le compresseur (unité), le récepteur, les pièces de connexion. Le moteur transmet les mouvements de rotation à la poulie du compresseur via un entraînement par courroie. Le compresseur entraîné absorbe l'air atmosphérique, qui pénètre ensuite dans la chambre de compression. Le mouvement du piston réduit le volume utile du cylindre, comprimant inévitablement l'air. L'air comprimé pénètre ensuite dans un récipient appelé récepteur, puis, à travers des tuyaux, il active le système pneumatique, pulvérise de la peinture et fournit de l'énergie à divers outils. Le récepteur est nécessaire pour éliminer les pulsations causées par une compression inégale de l'air par un compresseur à piston.
Deuxièmement, lors de la création d'un compresseur haute pression de vos propres mains, vous devez décider dans quel but vous envisagez d'utiliser le compresseur, car c'est le facteur déterminant pour trouver les éléments nécessaires. En choisissant un groupe haute pression de 10 atmosphères, vous pouvez vous munir d'air comprimé pendant une longue période pour faire fonctionner tout type d'outils pneumatiques. Pour une telle machine, un conteneur est nécessaire comme récepteur, capable de résister à une telle pression interne. Un extincteur bien conservé, autrefois utilisé, un récipient provenant d'une bouteille de gaz ou un récipient fait maison fabriqué en soudant un morceau de tuyau bouché peuvent servir de récepteur. Mais en même temps, la qualité des soudures et l'état du métal doivent résister à une pression interne non inférieure à une fois et demie la pression de fonctionnement du compresseur. Cela garantira complètement l'utilisation en toute sécurité d'un récepteur fait maison.
L'intérieur du conteneur doit être protégé de la corrosion. Il existe de nombreux liquides spéciaux disponibles à la vente pour de telles opérations. Ensuite, vous pouvez donner un aspect esthétique au cylindre en le peignant. Le récepteur peut être installé horizontalement ou verticalement, selon sa forme et les souhaits de l'auteur de l'idée. Après avoir décidé de la position du conteneur, vous devez commencer à percer des trous - dans la partie inférieure, le trou est nécessaire pour évacuer périodiquement les condensats qui s'accumulent au fond du conteneur.
Le robinet de vidange doit pouvoir résister à la pression créée par le compresseur. Pour correspondre au diamètre et au pas de filetage du tuyau du robinet, un filetage interne est découpé dans un trou nouvellement percé.
Ensuite, le robinet est vissé - pour plus de fiabilité, vous pouvez utiliser des joints ou du mastic silicone. Ensuite, la même chose est faite dans la partie médiane du récepteur pour y introduire de l'air et dans la partie supérieure pour sortir. Il est nécessaire d'installer un clapet anti-retour à l'entrée du conteneur afin que l'air n'ait pas la possibilité de s'échapper en sens inverse vers le compresseur.
A la sortie, une vanne de passage de pression et de diamètre appropriés est vissée. Il est préférable de réaliser le trou de sortie en haut du récepteur, car dans ce cas le maximum de liquide restera au fond du cylindre. Le manomètre peut être monté en lui faisant un trou séparé et en y coupant un filetage approprié, ou en le fixant au tuyau de sortie, jusqu'au robinet. Grâce au manomètre, il sera possible de surveiller le fonctionnement d'un compresseur haute pression artisanal et, si nécessaire, de soumettre l'installation à des réglages plus précis. Un autre point important est que pour que le compresseur puisse s'éteindre et refroidir périodiquement pendant cette période, vous devez faire attention à la taille du récepteur. Vous ne devriez pas le rendre petit - plus le récepteur est grand, moins vous devrez allumer le compresseur souvent.
En tant qu'unité principale, vous pouvez utiliser les compresseurs d'un vieux réfrigérateur domestique ou d'une unité usagée en bon état. Les passionnés de voitures utilisent souvent un compresseur de 12 volts pour gonfler les roues. Il existe de nombreuses options. L'essentiel est de décider dans quel but le compresseur est nécessaire et quelle quantité d'air est nécessaire. Les avantages des motocompresseurs frigorifiques sont qu’ils ont déjà un moteur dans leur conception. De plus, ils génèrent un niveau de bruit extrêmement faible. Les inconvénients incluent le fait que lorsqu'il travaille avec de l'air et non avec du gaz fréon, le compresseur doit changer fréquemment l'huile lubrifiante. Quant aux pompes électriques de gonflage des pneus, elles constituent également un bon choix pour créer un compresseur haute pression de vos propres mains. Mais en même temps, vous devrez lui fournir un courant continu de 12 volts, c'est-à-dire que vous aurez besoin d'une alimentation supplémentaire. Et le volume du récepteur doit être conçu spécifiquement pour un modèle spécifique, car la durée de fonctionnement périodique de ces pompes est limitée et il faudra qu'elle ait le temps d'acquérir la pression requise dans le récepteur avant de s'éteindre.
Pour une plus grande facilité d'utilisation du compresseur, vous pouvez adapter une pièce très utile : un pressostat. Il est préférable de l'installer sur le récepteur. Grâce à ce dispositif, vous pouvez réguler correctement le démarrage et l'arrêt de l'unité, ce qui est nécessaire pour contrôler la pression dans le récepteur et assurer un fonctionnement uniforme du compresseur et du moteur électrique.
Le pressostat éliminera le besoin d'allumer et d'éteindre manuellement le compresseur, ce qui signifie éliminer le risque de surchauffe du moteur électrique et de destruction des éléments du groupe compresseur causé par une surpression excessive.