Paire de vis. Le principe de fonctionnement d'une pompe à vis. Paires de gérotors et leurs types Paire de billes
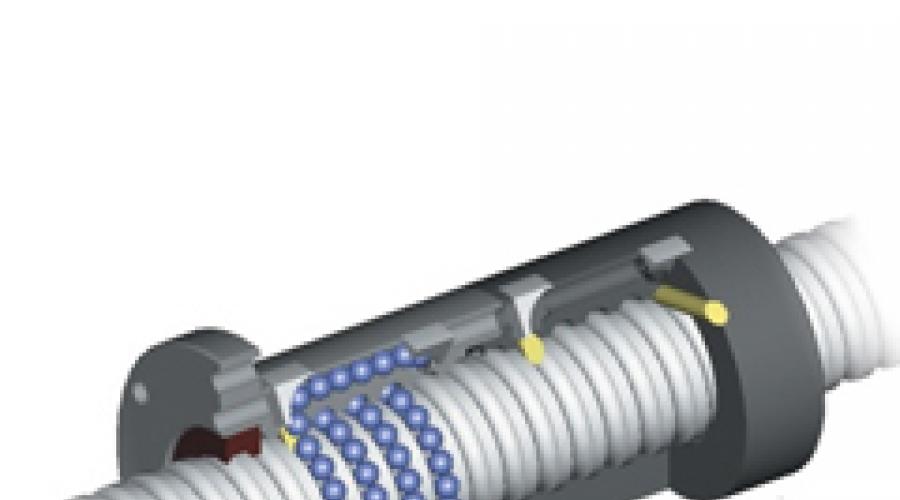
Lire aussi
Vis à billes- un type d'entraînement linéaire qui transforme mouvement de rotation en un traductionnel, qui a trait distinctif- frottement extrêmement faible.
Un arbre (généralement en acier - fabriqué à partir de types d'acier à haute teneur en carbone) avec une forme spécifique de pistes de roulement sur la surface agit comme une vis d'entraînement de haute précision interagissant avec l'écrou, mais pas directement, par friction de glissement, comme dans une vis conventionnelle. transmissions à écrous, mais par billes, par friction de roulement. Cela détermine les caractéristiques de surcharge élevées de la vis à billes et son très haut rendement. La vis et l'écrou sont fabriqués par paire assortie avec des tolérances très serrées et peuvent être utilisés dans des applications qui nécessitent des haute précision. Un écrou à bille est généralement légèrement plus grand qu'un écrou coulissant en raison des canaux de recirculation des billes qui s'y trouvent. Cependant, c'est pratiquement le seul point sur lequel la vis à billes est inférieure. lecteurs de vis frottement de glissement.
Champ d'application des vis à billes
Les vis à billes sont souvent utilisées dans les avions et les fusées pour déplacer les surfaces de direction, ainsi que dans les voitures pour conduire. crémaillère de direction du moteur de direction électrique. La plus large gamme d'applications de vis à billes existe dans l'ingénierie de précision, comme les machines CNC, les robots, les chaînes d'assemblage, les installateurs de composants, ainsi que les presses mécaniques, les machines de moulage par injection, etc.
Historique des vis à billes
Historiquement, la première vis à billes de précision était réalisée à partir d'une vis conventionnelle d'assez faible précision, sur laquelle était installée une structure de plusieurs écrous, tendus par un ressort, puis rodés sur toute la longueur de la vis. En redistribuant les écrous et en changeant la direction de la tension, les erreurs de pas de la vis et de l'écrou pourraient être moyennées. Ensuite, le pas résultant de la paire, déterminé avec une grande répétabilité, a été mesuré et enregistré comme passeport. Un processus similaire est actuellement utilisé périodiquement pour la production.
Application de vis à billes
Pour que la paire de balles puisse servir toute sa période de règlement avec la préservation de tout, incl. paramètres de précision, il est nécessaire de prêter une grande attention à la propreté et à la protection de l'espace de travail, pour éviter le contact de la poussière, des copeaux et autres particules abrasives avec la vapeur. Ce problème est généralement résolu en installant une protection ondulée à la vapeur, en polymère, en caoutchouc ou en cuir, qui empêche les particules étrangères de pénétrer espace de travail. Une autre méthode consiste à utiliser un compresseur - fournissant de l'air filtré sous pression à une hélice ouverte. Les vis à billes, grâce à l'utilisation du frottement de roulement, peuvent avoir une certaine précharge, qui supprime le jeu des engrenages - un certain « écart » entre le mouvement de rotation et de translation qui se produit lors du changement de sens de rotation. L'élimination du jeu est particulièrement importante dans les systèmes avec contrôlé par programme C'est pourquoi les vis à billes avec précharge sont particulièrement souvent utilisées dans les machines CNC.
Inconvénients des vis à billes
En fonction de l'angle d'élévation des chemins de roulement, les vis à billes peuvent être soumises à une transmission inverse : un faible frottement fait que l'écrou ne se bloque pas, mais transmet la force linéaire en couple. Il n'est généralement pas conseillé d'utiliser des vis à billes sur flux manuels. Prix élevé Les vis à billes sont également un facteur qui incite souvent les constructeurs de machines à choisir des engrenages plus économiques.
Avantages des vis à billes
Le faible coefficient de frottement de la vis à billes entraîne une faible dissipation et une efficacité de transmission élevée, bien supérieure à celle de tout autre analogue. L'efficacité des vis à billes les plus courantes peut dépasser 90 %, contre un maximum de 50 % pour les vis à billes métriques et trapézoïdales. Pratiquement aucun glissement augmente considérablement la durée de vie de la vis à billes, ce qui réduit les temps d'arrêt de l'équipement lors des réparations, du remplacement et de la lubrification des pièces. Tout cela, combiné à d'autres avantages, tels qu'une vitesse pouvant être atteinte plus élevée et une consommation d'énergie réduite pour l'entraînement électrique de l'hélice, peut constituer un argument important en faveur d'une vis à billes, par opposition à son coût élevé.
Production de vis à billes
Les vis à billes les plus précises ne peuvent être produites que par meulage. La vis peut également être réalisée par moletage - une telle vis aura un coût nettement inférieur, mais sa précision sera limitée à une erreur de l'ordre de 50 microns par 300 mm de course.
Précision de la vis à billes
Les vis de haute précision donnent généralement une erreur de l'ordre de 1 à 3 microns par 300 mm de course, et encore plus précisément. Les ébauches de ces vis sont obtenues par usinage grossier, puis les ébauches sont durcies et rectifiées à la perfection. Trois étapes sont strictement nécessaires, car... traitement thermique modifie considérablement la surface de la vis à billes.
Le tourbillonnement dur est comparatif nouvelle technologie travail des métaux qui minimise l'échauffement de la pièce pendant le processus et peut produire des vis de précision à partir d'une pièce durcie. Les vis à billes instrumentées atteignent généralement une précision de 250 nm par centimètre. Ils sont fabriqués par fraisage et meulage sur des équipements ultra précis avec contrôle par des équipements spécialisés de précision submicronique. Les lignes de production de lentilles et de miroirs sont équipées d'équipements similaires. Ces vis sont généralement fabriquées à partir d'Invar ou d'autres alliages d'Invar pour minimiser l'erreur introduite par la dilatation thermique de la vis.
Systèmes de recyclage de balles
Les billes de roulement circulent dans les canaux filetés de l'écrou et les chemins de roulement de la vis. Si vous ne guidiez pas la bille après la fin de son voyage, les billes tomberaient simplement de l'écrou à l'extérieur après avoir atteint la fin de la piste, c'est pourquoi les vis à billes utilisent plusieurs systèmes plus coûteux pour ramener les billes au début - systèmes de recirculation .
Le système externe utilise un tube métallique qui relie l'entrée et la sortie de l'écrou de canal. Les boules sortantes tombent dans le tube, et poussées par les suivantes, elles suivent jusqu'à l'entrée. Système interne consiste à découper un canal similaire à l'intérieur de l'écrou, les billes sortant de l'écrou sont dirigées par un revêtement spécial dans le canal percé, et à la sortie du canal, un revêtement similaire transfère les billes vers l'entrée du tapis roulant. Une option très courante est celle où les balles circulent à travers plusieurs canaux en boucle, où le retour est assuré par un bouchon spécial.
1. Spécifications
Les vis à billes telles que NBS se caractérisent par un contrôle de qualité strict effectué lors de chaque processus de production.
Les vis hautes performances permettent des réductions de couple jusqu'à 70 % par rapport aux vis trapézoïdales traditionnelles dans les applications usage général(transformation du mouvement de rotation en mouvement de translation), et en applications spéciales(transformation mouvement vers l'avant en mouvement de rotation).
1.1 Géométrie des contacts
L'arc gothique apporte une solidité importante à la vis tout en offrant précision et faibles valeurs de couple.
2. Paramètres de sélection des vis à billes NBS (à recirculation de billes)
- Le choix d'une vis à billes (à circulation de billes) est déterminé par les paramètres suivants :
- -Classe de précision
- -Pas de filetage
- -Durée nominale prestations de service
- -Méthode de fixation
- -Vitesse de rotation critique
- -Rigidité
- -Température de fonctionnement
- -Lubrifiant
2.1 Classe de précision
Les vis à billes NBS (billes à recirculation) sont disponibles dans les classes de précision suivantes :
CO. C1. C2. C3. C5. C7. C10
Chaque classe de précision est déterminée par les paramètres suivants :
E. e. e2∏
Le graphique ci-dessous fournit une description de leurs significations.
Terme | Lien | Définition |
Compensation d'accident vasculaire cérébral | T | Compensation de la longueur de course - la différence entre la longueur de course théorique et nominale ; petite valeur de compensation (par rapport à la course nominale) souvent nécessaire pour compenser l'allongement provoqué par une température élevée ou des charges externes. Si cette compensation n'est pas nécessaire, la course théorique est égale à la course nominale. |
Longueur de course réelle | - | La longueur de course réelle correspond au déplacement axial entre la vis et l'écrou. |
Longueur de course moyenne | - | La longueur de course moyenne est la ligne droite qui se rapproche le plus de la longueur de course réelle ; la longueur de course moyenne représente la pente de la longueur de course réelle. |
Écart de longueur de course moyenne | E | L'écart moyen de la longueur de course est la différence entre longueur de course moyenne et théorique. |
Changer de cap | e ézoo e2п |
Un changement de trait est une bande avec deux lignes parallèles de longueur de trait moyenne. Plage maximale de changements sur la longueur de course. Plage de changements mesurée sur une longueur de course typique de 300 mm. Erreur de faux-rond, plage de changement par tour (2 radians). |
Classe de précision | C0 | C1 | C2 | C3 | C5 | C7 | C10 | |||||||
Longueur progrès [mm] |
depuis: | avant: | ±E | e | ±E | e | ±E | e | ±E | e | ±E | e | e | e |
100 | 3 | 3 | 3.5 | 5 | 5 | 7 | 8 | 8 | 18 | 18 | ±50/ 300mm |
±210/ 300mm |
||
100 | 200 | 3.5 | 3 | 4.5 | 5 | 7 | 7 | 10 | 8 | 20 | 18 | |||
200 | 315 | 4 | 3.5 | 6 | 5 | 8 | 7 | 12 | 8 | 23 | 18 | |||
315 | 400 | 5 | 3.5 | 7 | 5 | 9 | 7 | 13 | 10 | 25 | 20 | |||
400 | 500 | 6 | 4 | 8 | 5 | 10 | 7 | 15 | 10 | 27 | 20 | |||
500 | 630 | 6 | 4 | 9 | 6 | 11 | 8 | 16 | 12 | 30 | 23 | |||
630 | 800 | 7 | 5 | 10 | 7 | 13 | 9 | 18 | 13 | 35 | 25 | |||
800 | 1000 | 8 | 6 | 11 | 8 | 15 | 10 | 21 | 15 | 40 | 27 | |||
1000 | 1250 | 9 | 6 | 13 | 9 | 18 | 11 | 24 | 16 | 46 | 30 | |||
1250 | 1600 | 11 | 7 | 15 | 10 | 21 | 13 | 29 | 18 | 54 | 35 | |||
1600 | 2000 | 18 | 11 | 25 | 15 | 35 | 21 | 65 | 40 | |||||
2000 | 2500 | 22 | 13 | 30 | 18 | 41 | 24 | 77 | 46 | |||||
2500 | 3150 | 26 | 15 | 36 | 21 | 50 | 29 | 93 | 54 | |||||
3150 | 4000 | 30 | 18 | 44 | 25 | 60 | 35 | 115 | 65 | |||||
4000 | 5000 | 52 | 30 | 72 | 41 | 140 | 77 | |||||||
5000 | 6300 | 65 | 36 | 90 | 50 | 170 | 93 | |||||||
6300 | 8000 | 110 | 60 | 210 | 115 | |||||||||
8000 | 10000 | 260 | 140 | |||||||||||
10000 | 12500 | 320 | 170 |
Classe de précision | C0 | C1 | C2 | NO | C5 | C7 | C10 |
le zoo | 3.5 | 5 | 7 | 8 | 18 | 50 | 210 |
e 2π | 2.5 | 4 | 5 | 6 | 8 |
2.2 Précharge et jeu axial
La précharge et le jeu axial des vis à billes NBS sont indiqués dans le tableau ci-dessous.
Classe de préchargement | P0 | P1 | P2 | RZ | RA |
Jeu axial | Oui | Non | Non | Non | Non |
Préchargement | Non | Non | Facile | Moyenne | Fort |
Les tableaux suivants répertorient les directives de base pour la sélection de la classe de précision, de la précharge et du jeu axial des vis à billes NBS.
Classe de précision | Précharge et jeu axial | Type d'écrou | Type de vis mère |
À partir de 10 | RO (avec jeu axial) | Célibataire | Moleté |
C7 | P1 ou RO | Sur demande | Roulé ou redressé |
C5 | Sur demande; norme 0TNBS-P2 |
Sur demande | erreurs d'étape |
C3 | Sur demande; norme 0TNBS-P2 |
Sur demande | Redressé, avec certificat de contrôle erreurs d'étape |
Modèle | Écrou simple | Double écrou |
1605 | 1 ± 3N | 3 ± 6 N |
2005 | 1 ± 3N | 3 ± 6N |
2505 | 2 ± 5 N | 3 ± 6N |
3205 | 2 ± 5 N | 5 ± 8N |
4005 | 2 ± 5 N | 5 ± 8N |
2510 | 2 ± 5 N | 5 ± 8N |
3210 | 3 ± 6 N | 5 ± 8N |
4010 | 3 ± 6 N | 5 ± 8N |
5010 | 3 ± 6 N | 8 ± 12 N |
6310 | 6 ± 10 N | 8 ± 12 N |
8010 | 6 ± 10 N | 8 ± 12 N |
2.3 Pas de filetage
Le choix du pas d'hélice dépend de la formule suivante :
Où:
Ph = pas de vis [mm]
Vmax = vitesse maximum course du système [m/min]
n max = mode de rotation maximal de l'hélice [min 1]
Dans le cas où le résultat de l’équation n’est pas un résultat entier, vous devez choisir le résultat arrondi. grand côté valeur en choisissant parmi les étapes disponibles.
Compte tenu de la variabilité possible des charges axiales, provoquée par exemple par la présence de forces d'inertie, il est nécessaire de calculer la valeur de charge désignée comme « charge dynamique moyenne Pm », qui détermine les mêmes coefficients de charge variables.
2.4.1 Charge dynamique moyenne
Pour calculer une vis à billes soumise à des conditions de fonctionnement variables, on utilise les valeurs moyennes de Pm et n m :
Р m = charge axiale dynamique moyenne [N]
n m = vitesse moyenne[min -1 ]
Dans des conditions de charge continue et de vitesse variable, les valeurs suivantes peuvent être atteintes :
Dans des conditions de charge variable et de vitesse continue, les valeurs suivantes peuvent être atteintes :
Dans des conditions de charge variable et de vitesse variable, les valeurs suivantes peuvent être atteintes :
Le choix de l'hélice en fonction des forces de traction agissant et (ou) requises est déterminé par les valeurs suivantes :
- Capacité de charge statique Soa
- Capacité de charge dynamique Ca
La capacité de charge statique Coa (ou facteur de capacité de charge) est définie comme une charge d'intensité constante agissant sur l'axe de la vis, qui, au point d'impact maximum entre les pièces en contact, établit une déformation permanente égale à 1/10 000 de le diamètre de l'élément roulant.
Les valeurs de Coa sont indiquées dans les tableaux de tailles.
2.5.1 Facteur de sécurité statique a s Le facteur de sécurité statique a s (ou facteur de sécurité statique) est déterminé par l'équation suivante :
2.5.2 Facteur de dureté f H
Le coefficient de dureté prend en compte la dureté superficielle des chemins de roulement :
Où:
dureté du chemin de roulement HsV10 = dureté réelle du chemin de roulement exprimée en unités Vickers avec une charge d'essai de 98,07 N
700HV10 = dureté égale à 700 Vickers à charge d'essai égale à 98,07 (700HV10 ≈ 60 HRC)
2.5.3 Facteur de précision f ac
Le coefficient de précision prend en compte les tolérances de traitement de la vis, et donc la classe de précision correspondant à la norme.
Le tableau montre quelques exemples.
La nécessité d'un facteur de sécurité statique a s > 1 est due à la présence possible de chocs et (ou) de vibrations, de couples de démarrage et d'arrêt et de charges aléatoires pouvant entraîner un dysfonctionnement du système.
Le tableau ci-dessous présente les valeurs du facteur de sécurité statique en fonction du type d'application.
La capacité dynamique de charge Ca (ou coefficient de charge dynamique) est une charge dynamique intense et constante agissant sur l'axe de la vis, qui détermine la durée de vie de 10 6 tours.
Les valeurs C a sont indiquées dans les tableaux de tailles.
2.7 Durée de vie nominale L
La durée de vie nominale L (c'est le kilométrage théorique parcouru par au moins 90 % d'un nombre représentatif de vis à billes identiques (à recirculation de billes) soumises aux mêmes conditions de charge sans présenter de signes de fatigue du matériau) est déterminée par les conditions suivantes :
- Ecrou sans précharge
- Ecrou avec précharge
2.7.1 Écrou sans précharge
Pour les vis à billes (à recirculation de billes) avec écrou sans précharge, le calcul de la durée de vie nominale, exprimée en nombre de tours, est déterminé par la formule suivante :
Où:
P m = charge axiale dynamique moyenne impliquée [N]
- Classe de précision des vis de 1 à 5
- Fiabilité jusqu'à 90%
Où:
a 1 = facteur de sécurité
2.7.2 Coefficient a 1
Le coefficient a 1 prend en compte la possibilité de non-déflexion C%.
C% | 80 | 85 | 90 | 92 | 95 | 96 | 97 | 98 | 99 |
un 1 | 1.96 | 1.48 | 1.00 | 0.81 | 0.62 | 0.53 | 0.44 | 0.33 | 0.21 |
Il est à noter que pour C% = 90 a 1 = 1,00
2.7.3 Écrou précontraint
La validité des formules suivantes est conditionnée au maintien d'une précharge constante ; dans le cas contraire, il convient de prendre en compte le cas d'un écrou sans précharge.
Pour les vis à billes (vis à recirculation de billes) avec écrou précontraint, le calcul de la durée de vie nominale, exprimée en nombre de tours, est déterminé par la formule suivante :
Où:
L 10 = durée de vie nominale [tr]
L 10 b - (C a / Pm 2) x 10 6
L 10a et L1 0b sont les ressources nominales pour deux moitiés de l'écrou.
- Cette équation est valable dans les cas suivants :
- Dureté du chemin de roulement = 60HRC
- Classe de précision des vis de 1 à 5 ;
- Fiabilité jusqu'à 90%.
Si les conditions opératoires ne remplissent pas les conditions ci-dessus, la formule suivante doit être utilisée :
Où:
L 10 = durée de vie nominale [tr]
L 10 a = (C a /P m1) 3 X 10 6
L 10 b - (C a / Pm 2) x 10 6
a 1 = coefficient de fiabilité ;
f ho = facteur de dureté (voir facteur de sécurité statique a s)
f ac = facteur de précision (voir facteur de sécurité statique a s)
P m1 et P m2 - charges dynamiques axiales moyennes pour les deux moitiés de l'écrou ;
P r = force de précharge [N]
2.7.4 Durée de vie nominale en heures Lh
Ayant L 10 (durée de vie nominale, exprimée en nombre de tours), on peut calculer la durée de vie nominale en heures de fonctionnement L h ;
Où:
L m = durée de fonctionnement [heures]
n m = vitesse de rotation moyenne [min -1 ]
m i = vitesse [MIN -1 ]
qi = répartition en pourcentage [%]
2.7.5 Durée de vie nominale en km Lkm
Disposant de L 10 (ressource nominale, exprimée en nombre de tours), vous pouvez calculer la ressource nominale de la distance parcourue en km L km.
Où:
L km = durée de vie nominale [km]
P h = pas de vis [mm]
Le tableau suivant fournit une indication de la durée de vie typique des vis à billes pour les applications générales.
2.8 Méthode de montage
En règle générale, il y a types suivants Montage par vis à billes :
Le mode de fixation utilisé est fonction des conditions d'application, garantissant la rigidité et la précision requise.
2.9 Vitesse de rotation critique
La vitesse de rotation maximale de la vis à billes ne doit pas dépasser 80 % de la vitesse critique.
La vitesse de rotation critique est le point auquel l'hélice commence à vibrer, produisant un effet de résonance provoqué par la fréquence de vibration correspondant à la fréquence naturelle de l'hélice.
La valeur de la vitesse critique dépend du diamètre intérieur de la vis mère, du mode de fixation des bords et de la longueur de la déviation libre.
La vitesse critique est mesurée par la formule suivante :
Où:
n cr = vitesse critique [min -1 ]
f kn = facteur de méthode de fixation
d 2 = diamètre intérieur de la broche [mm]
l n = longueur de déformation libre [mm]
Selon le type de fixation, des valeurs f kn sont fournies :
Où:
do = diamètre nominal [mm m]
da = diamètre de la bille [mm]
a = angle de contact (= 45)
La longueur de la flèche libre l n est déterminée en fonction de :
-Écrous sans précharge
l n = distance entre fixations [mm] (dans le cas d'une fixation « monobloc - libre », il faut tenir compte de la distance entre le bord libre de la vis et la douille)
-Ecrou avec précharge
l n = distance maximale entre le demi-écrou et la fixation [mm] (dans le cas d'une fixation « monobloc - libre », il faut tenir compte de la distance maximale entre le demi-écrou et le bord libre de la vis)
n max = vitesse maximale de l'hélice [tours/min]
La charge critique est la charge axiale maximale à laquelle l'hélice peut être soumise sans affecter la stabilité du système ; dans le cas où la charge axiale maximale agissant sur l'hélice atteint ou dépasse la valeur de charge critique, un nouvelle forme impact sur la vis, appelé « charge de pointe », provoquant une déflexion supplémentaire en plus de la simple compression.
Ce phénomène, associé aux propriétés élastiques de la pièce, devient d'autant plus sensible que la longueur de déflexion libre de la vis est grande. digne d'attention valeurs par rapport à sa coupe. La valeur de la charge critique est déterminée par la formule suivante :
Où:
P cr = Charge critique [N]
f kp = facteur de méthode de fixation
d 2 = diamètre intérieur de la vis mère [mm] (voir vitesse critique)
l cr = longueur de déformation libre [mm]
Selon le type de fixation, des valeurs fkp sont fournies :
Une pièce - Une pièce | f kр = 40,6 | |
Une pièce - Support | f kp = 20,4 | |
Référence - Référence | f kp = 10,2 | |
Une pièce - Gratuit | f kp = 2,6 |
Pour calculer la charge critique, la valeur de la est déterminée par la distance maximale entre la moitié de l'écrou et la fixation.
Pour plus de sécurité, la charge axiale maximale admissible doit être considérée comme égale à la moitié de la charge critique :
P max = charge axiale maximale admissible [N]
2.11 Dureté
La rigidité axiale d'un système mobile équipé d'une vis à billes est déterminée par la formule suivante :
Où:
K = rigidité axiale du système
P = charge axiale [N]
e = déformation axiale du système [µm]
La rigidité axiale d'un système K est fonction de la rigidité axiale des composants individuels qui le composent : vis mère, écrou, supports, supports de connexion et écrou.
Où:
K s = rigidité axiale de la vis mère
K N = rigidité axiale de l'écrou
K in = rigidité axiale des appuis
Kn = rigidité axiale de l'assemblage éléments de support et des noix
2.11.1 Ks - Rigidité axiale de la vis mère
La valeur de rigidité Ks est fonction du système de fixation.
Méthode de montage : Monobloc - Monobloc
Où:
d 2 = diamètre intérieur (voir vitesse de rotation critique)
l s = distance entre l'axe médian de deux fixations
Méthode de montage : Monobloc - Support
Où:
d 2 = diamètre intérieur [mm] (voir vitesse critique)
l s = distance maximale entre les axes centraux de la fixation et l'écrou [mm].
2.11.2 K N - Rigidité axiale de l'écrou
Double écrou avec précharge
Où:
K = rigidité de la table
F pr = force de précharge [N]
Écrou simple sans précharge
La valeur de K N est déterminée par la formule suivante :
Où:
P = charge axiale [N]
C a = capacité de charge dynamique [N]
2.11.3 Kv - Rigidité axiale des supports
La rigidité axiale des supports de vis est déterminée par la rigidité des roulements.
Dans le cas de roulements à billes radiaux à contact oblique rigides, les formules suivantes s'appliquent :
Où:
bv = déformation axiale du roulement
Q = charge sur chaque balle [N]
β = angle de contact (45°)
d = diamètre des billes [mm]
N = nombre de balles
La rigidité des éléments de support de liaison et des écrous est une caractéristique de la machine, c'est à dire qu'elle ne dépend pas du système de vis, écrou et supports.
2.12 Température de fonctionnement
Dans le cas d'une fixation permanente sur une seule pièce, il faut tenir compte de l'éventuelle dilatation thermique provoquée par l'augmentation de la température de la vis pendant le fonctionnement. Cette dilatation, si elle est correctement prévue, impose une charge axiale supplémentaire au système ; , ce qui peut entraîner un dysfonctionnement du système. Pour résoudre les problèmes, il est nécessaire de précharger suffisamment la vis.
Où:
AL = variation de longueur [mm] a = coefficient de dilatation thermique
(11,7 x 10 -6 [°C -1 ])
L = longueur de vis [mm]
AT = changement de température [°C]
2.13 Lubrification
Pour lubrifier les vis à billes NBS, les instructions suivantes doivent être respectées.
2.13.1 Lubrification avec lubrifiant liquide
Doit être préféré ce type lubrification en cas de fonctionnement sur vitesses élevées rotations. Lubrifiants substances liquides pouvant être utilisées ont les mêmes caractéristiques que les substances utilisées pour lubrifier les roulements (du VG 68 au VG 460). Le choix de la viscosité est fonction des caractéristiques de fonctionnement et de l'environnement d'exploitation : température, vitesse de rotation, charges de fonctionnement ; Il est recommandé de l'utiliser uniquement pour les vis à faible vitesse de rotation classes supérieures viscosité (environ VG 400).
Dans ce cas, il n'y a pas besoin de payer attention particulière pour l'entretien, à l'exception de l'apport constant d'huile lubrifiante dans le système (les intervalles de relubrification sont plus courts que dans les installations lubrifiées à la graisse).
Dans tous les cas, les instructions du fabricant de l'huile liquide doivent être suivies.
2.13.2 Graisse
La lubrification à la graisse est destinée aux faibles vitesses de rotation.
Lors du choix d'un lubrifiant, les réglementations applicables pour la lubrification des roulements doivent être prises en compte ; Il est donc recommandé d'utiliser de la graisse à base de savon de lithium plutôt que des graisses avec additifs solides (telles que les graisses MoS2 ou graphite), sauf à des vitesses de rotation très faibles ; cependant, il est recommandé de suivre les instructions du fabricant de graisse.
3. Couple et puissance nominale
Pour calculer approximativement les valeurs de couple et de puissance du moteur pour convertir le mouvement de rotation en mouvement linéaire, vous devez utiliser ces formules :
Où:
Pmax = maximum charge efficace[H]
Ph = pas de filetage [mm]
ɳ v = efficacité mécanique de l'hélice (env. 0,9)
ɳ t = rendement mécanique de la transmission moteur-hélice
(transmission avec engrenages ɳ t = 0,95+0,98) ;
z = rapport de démultiplication moteur - hélice
Dans le cas d'une liaison directe entre le moteur et l'hélice, z=1 et ɳ 2 =1.
Où:
Nm = puissance nominale du moteur [kW]
Mm = couple nominal [Nm]
Pmax = rotation maximale de l'hélice [min]
z = moteur à engrenages - hélice (Ptah X Z = moteur P)
En cas de transformation mouvement rectiligne en mouvement de rotation, il y a :
M r = couple de charge [Nm]
P max = charge effective maximale [N]
P h = pas de filetage [mm]
ɳ r = rendement mécanique (env. 0,8
4. Exemples d'installation
Code du type d'écrou | Direction vis |
Nominal diamètre vis [mm] |
Pas [mm] | Type de bride | Code de traitement | Classe précision |
Général longueur vis [mm] |
Code précharger |
||
Célibataire ou double |
À bride ou non bridé |
Taper | ||||||||
V = simple W = double |
F = à bride C = à bride |
U je E À M |
R = droite L = gauche |
_ | - | N = pas de coupe S = tranche unique D = double coupe |
C = Redressé F = Moleté |
De 0 C1 C2 C3 C5 C7 À partir de 10 |
- | P0 P1 P2 RZ P4 |
6. Programme de calcul NBS pour vis à billes (avec circulation de billes)
Dans notre boutique en ligne, vous pouvez l'acheter vous-même
Ou en contactant nos spécialistes sur notre numéro gratuit 8 800 700 72 07
Et aussi en envoyant une candidature à l'adresse E-mail vente@site
Paires de gérotors
Dans cet article, je voudrais parler du principe de fonctionnement des pompes à vis (ou gerotor). Les pompes de ce type sont largement utilisées dans l'industrie et les descriptions de leur fonctionnement ne se trouvent pas partout.
Avec le même apparence, ces pompes peuvent avoir des paramètres de fonctionnement complètement différents.
Essayons de comprendre quelle est la différence.
La figure montre une pompe à vis typique en coupe :
Où : 1. Ensemble de roulements, 2. Joint d'arbre, 3. Charnières, 4. Tige, 5. Vis (rotor), 6. Cage (stator).
Paire de gérotors (corps de travail pompe à vis), appelé couple rotor-stator (ou porte-vis). Lorsque le rotor tourne dans le stator, le liquide se déplace dans le canal en forme de spirale du stator. Ainsi, le liquide est pompé.
Le stator est une spirale interne à n+1 fils, généralement en élastomère (caoutchouc), reliée de manière inséparable (ou séparément) à un support métallique (manchon).
Le rotor est une spirale externe en plomb N, généralement en acier avec ou sans revêtement ultérieur.
Il convient de souligner qu'à l'heure actuelle, les unités les plus courantes sont celles dotées d'un stator à 2 démarrages et d'un rotor à 1 démarrage ; cette conception est classique pour presque tous les fabricants d'équipements à vis.
Un point important est que les centres de rotation des spirales du stator et du rotor sont décalés du degré d'excentricité, ce qui permet de créer une paire de friction dans laquelle, lorsque le rotor tourne, des cavités fermées et scellées sont créées à l'intérieur. le stator sur tout l'axe de rotation. Dans ce cas, le nombre de ces cavités fermées par unité de longueur de la paire de vis détermine la pression finale de l'unité, et le volume de chaque cavité détermine sa productivité.
La différence entre les pompes réside précisément dans l’utilisation de paires de géroteurs de géométries différentes.
Il existe quatre principaux types de paires de gerotors, qui sont généralement désignées par des lettres de l'alphabet latin : S, L, D, P.
Dans notre pays et dans les pays voisins, seules les pompes avec des paires S et L sont produites. Les paires D et P, plus difficiles à fabriquer, ne sont fabriquées qu'à l'étranger, par exemple en Allemagne.
Types de paires de gérotors :
1. Géométrie "S":
Vitkov : 1/2
Productivité : 100 %
Différent. pression : 12 bars
Avantages de la géométrie S :
livraison très fluide
dimensions compactes malgré grand nombre pas
grande section transversale d'entrée
faible vitesse débit/capacité d'aspiration élevée
le pompage de particules comprimées est possible
pomper de grosses particules
Il est à noter que le clip avec la géométrie « S » est « verrouillable », c'est-à-dire aucun liquide ne le traversera lorsque la pompe est arrêtée.
2. Géométrie "L":
Vitkov : 1/2
Productivité : 200 %
Différent. pression : 6 bars
Avantages de la géométrie L :
bonnes caractéristiques volumétriques avec un temps d'exécution long grâce à la longue ligne de contact entre le rotor et le stator
dimensions compactes et performances élevées
vitesse de friction inférieure
Ce type de clip est « non verrouillable ». Lorsque la pompe est arrêtée, le liquide peut s'écouler à travers la paire de géroteurs.
3. Géométrie "D" :
Vitkov : 2/3
Productivité : 150 %
Différent. pression : 12 bars
Avantages de la géométrie D :
de très petites dimensions avec hypertension artérielle et productivité
pompage presque sans pulsations
haute précision de dosage
4. Géométrie "P":
Vitkov : 2/3
Productivité : 300 %
Différent. pression : 6 bars
Avantages de la géométrie P :
dimensions compactes avec de très hautes performances
presque pas de pulsation
haute précision de dosage
bons indicateurs volumétriques, longue période de révision en raison de la longue ligne de contact entre rotor et stator
Nous avons donné des exemples de géométrie de paires de géroteurs de même longueur. Les figures montrent que le nombre de tours pour les paires « S » est deux fois plus élevé que pour la paire « L » de même longueur. Cela affecte la pression maximale de la paire de géroteurs. Plus il y a de tours, plus haut pression maximale.
Comme vous pouvez le voir, chaque paire de gérotors produit une certaine pression maximale (si l'on considère des paires de même longueur).
La question se pose : que faire si vous avez besoin de plus (ou moins) de pression de sortie que telle ou telle paire n'en produit.
Dans ce cas, la longueur de la paire de gerotors est augmentée (diminuée). Ainsi, par exemple, doubler la longueur de la paire « S » entraîne une augmentation de 2 fois de la pression maximale de la pompe, c'est-à-dire la pression augmentera jusqu'à 12 atmosphères.
Les pompes à vis peuvent également être fabriquées en divers modèles pour travailler dans certaines conditions.
Options de configuration de la pompe :
1. Disposition horizontale classique avec cadre porteur
2. Disposition horizontale sans cadre porteur
3. Tarière de support supplémentaire
4. Trémie et alimentateur à vis
5. Mecérateur supplémentaire (broyeur)
Vidéo d'une pompe à vis vide-fût en fonctionnement
Une paire de vis se compose de deux parties (vis et écrou) reliées le long d'une surface de vis. Une paire de vis est utilisée pour convertir le mouvement de rotation en mouvement de translation, ou vice versa.
Les paires de vis sont livrées avec des profils de surface de vis triangulaires, rectangulaires et ronds.
En ingénierie, la surface d’une vis est souvent appelée filetage. Les filetages à profil triangulaire sont divisés en métriques, pouces, trapézoïdaux et poussées.
Paramètres géométriques de base des filetages métriques selon GOST 9150-81 (Fig. 5.3) :
N– hauteur du profil d'origine (triangle équilatéral) ;
d, d 2 , d 1 – diamètres extérieur, médian et intérieur ;
Riz. 5.5. Paires de vis à filetage rectangulaire et triangulaire :
c – vis, d – écrou, R. Et d 2 – pas et diamètre moyen du filetage
étape R.– la distance entre les points similaires les plus proches du contour le long d'une ligne parallèle à l'axe du filetage ;
angle de profil = 60 ;
angle d'hélice du filetage (Fig. 5.4).
P.
Riz. 5.6. Paire de vis : v t Et v un– vitesses circonférentielles et axiales de l'écrou ; d G - diamètre extérieurécrous ; – angle d'hélice
ou
Ici t– période de mouvement de rotation.
Période de rotation de l'écrou
où et n– vitesse angulaire et fréquence de rotation de l'écrou.
Vitesse de translation de l'écrou
Friction dans une paire de vis
Considérons une paire de vis avec un profil de filetage rectangulaire (Fig. 5.7). Nous supposons que la charge axiale F UN sur la vis est concentrée sur un tour et que la réaction de l'écrou s'applique le long de la ligne médiane du filetage, c'est-à-dire d 2 .
Riz. 5.7. Pour déterminer les forces de frottement dans une paire de vis avec un profil de filetage rectangulaire
Le mouvement d'un écrou le long d'une vis peut être considéré comme le mouvement d'un curseur le long d'un plan incliné avec un angle d'inclinaison (Fig. 5.8).
Lorsque le curseur se déplace uniformément, l’équation d’équilibre suivante est valide :
Où F t = M/r 2 – force horizontale agissant sur le curseur (écrou), M– couple d'une paire de forces appliquées à l'écrou à distance r 2 à partir de l'axe de la vis dans un plan perpendiculaire à l'axe (dans le plan horizontal).
D'après le plan de force (Fig. 5.9), il est clair que la force motrice F t, nécessaire au mouvement uniforme du curseur sur un plan incliné, est lié à l'ampleur de la force axiale F UN rapport
F t = F UN tg ( + ),
et couple M les paires attachées à l'écrou
M = F t r 2 = F UN tg ( + ) r 2 .
De la loi de Coulomb-Amonton il résulte
F t = F N = N tg.
À partir du plan de force, nous déterminons la force de frottement agissant dans la paire de vis :
Diviser le numérateur et le dénominateur de cette expression par cos et étant donné que F= bronzage , on obtient
Dans une paire de vis à filetage triangulaire, la force normale N > F UN(Fig. 5.10), donc la force de frottement F t plus que dans la paire de vis à profil rectangulaire évoquée ci-dessus. Respectivement
Riz. 5.10. Relations entre les forces normales et axiales dans des paires de vis avec profils de filetage triangulaires et rectangulaires
angle de frottement et coefficient de frottement F à une paire de vis avec un filetage triangulaire sera plus grande qu'une paire de vis avec un profil de filetage rectangulaire.
Dans une paire de vis à filetage triangulaire, le coefficient de frottement et l'angle seront
Et
.
Les coefficients obtenus pour une paire de vis à profil de filetage triangulaire F et l'angle de frottement sont appelés coefficient réduit et angle de frottement.
La plupart des fabricants de compresseurs offrent une garantie sur les travaux sans révision compresseur jusqu'à 40 000 heures. À conditions idéales, qui ne se produisent pas en fonctionnement réel.
La durée de vie des roulements de support modernes à paires de vis n'a pas encore atteint un niveau où aucune intervention ni aucun remplacement ne sont nécessaires pendant cette période. En moyenne et honnêtement, les roulements fonctionnent de 10 000 à 20 000 heures, selon la qualité des roulements installés dans le bloc vissé en usine et la régularité Entretien du propriétaire du compresseur. Une fois ce temps accumulé, du bruit apparaît sous charge dans la paire de vis, augmentant à mesure que l'usure augmente pendant encore 5 000 à 15 000 000 heures. En conséquence, le compresseur commence à surchauffer et le bloc de vis se bloque en raison de la modification des espaces dans la paire de vis. En cas de surchauffe importante, les extrémités de la paire de vis sont « soudées » au corps, ce qui augmente considérablement les coûts de main-d'œuvre pour réparer l'unité de vis. Ou bien les roulements s'effondrent, laissant derrière eux des dommages imprévisibles - de la surchauffe locale de la paire de vis aux éraflures et aux tiges de vis ébréchées.
Dans chacun de ces cas, nous effectuerons les travaux suivants :
Remplacement des roulements de support de la paire de vis.
- remplacement des joints d'étanchéité d'arbre à vis.
- régler les jeux de travail du bloc à vis.
- restauration des extrémités actives des vis.
- restauration du profil de vis.
- restauration de la tige de l'arbre de la vis d'entraînement.
- restauration du boîtier du bloc à vis.
Le travail est effectué avec le même succès, quel que soit le fabricant de l'unité à vis, que ce soit : Ceccato, Aerzener, GHH-Rand, Rotorcomp, Fini, Enduro, Tamrotor, Termomeccanica, VMC, Arsenal domestique ou tout autre fabricant.
Un exemple de l'œuvre, cliquez sur le titre pour voir :
Réparation de bloc à vis 250 kW
Bloc à double vis avec transmission directe via une boîte de vitesses. L'unité a fonctionné correctement pendant 5 ans, après quoi des bruits et des vibrations sont apparus de plus en plus lors du fonctionnement de l'unité à vis. Le poids de 1 100 kg et les dimensions de l'unité inspirent le respect à quiconque se tient à côté de cette pièce d'ingénierie.
Après avoir convenu de l'étendue des travaux avec le client, nous avons procédé à la détection des défauts du groupe vis avec démontage complet :
L'autopsie a montré une usure complète des paliers d'appui des deux paires de vis, une partie un peu plus, la seconde un peu moins, ainsi que de petites éraflures locales sur l'un des blocs de vis. Apparemment, la puissance incontrôlable de cette unité a aspiré et mangé des déchets très solides :
L'usure des roulements approchait du point critique, ce qui, en plus des débris, affectait également les extrémités des rotors à vis :
Il y avait des copeaux de métal dans le carter et des cavités fermées, ce qui indiquait une usure extrême des roulements ainsi qu'une surchauffe et un blocage imminents. Sans la précision et l'attention du personnel de maintenance des compresseurs, alors un peu plus et le volume des réparations aurait considérablement augmenté :
Après les résultats de la détection des défauts, nous avons commandé de nouveaux roulements pour les paires de vis, les avons remplacés ainsi que les roulements de la boîte de vitesses. Nous avons collecté tous les copeaux de métal, lavé le carter et enlevé toutes les bavures sur les rotors et les couvercles. Les deux unités de vis ont été soigneusement assemblées et ajustées aussi précisément et soigneusement que possible pour éviter les distorsions de la charge pendant le fonctionnement.
Désormais, pour les 4 à 5 prochaines années, le client n'a plus rien à craindre, à l'exception du remplacement en temps opportun de l'huile et des filtres de cette unité.
Réparation de bloc à vis 75 kW
Bloc à vis avec transmission par engrenages. Le problème venait du moteur électrique Siemens, qui a cassé ses roulements et, par conséquent, le réducteur, ce qui a provoqué un blocage. Les clés des engrenages n'ont pas été coupées et ce qui était censé se produire s'est produit : le petit engrenage et la tige du rotor d'entraînement ont été fendus.
L'analyse du matériau de la paire de vis a montré qu'il s'agissait de fonte ordinaire. Efficace en termes de friction, mais difficile à réparer. Cela explique également pourquoi la clé en acier n'a pas été coupée et ne fait que rendre la réparation plus intéressante.
Matériel cassé :
Endommagement de la tige de l'arbre de transmission :
Compte tenu du fait que le coût d'un nouveau bloc à vis est 4 à 5 fois supérieur plus cher que les réparations, le client a pris la décision immédiatement.
La tige et la rainure de clavette ont été restaurées. Veuillez noter encore une fois que le matériau des vis est en fonte :
Nous avons commandé et installé un nouvel équipement :
Bien sûr, nous avons modifié les roulements de support, améliorant simultanément la conception - au lieu d'un roulement de poussée radial, deux ont été installés, ce qui a corrigé l'espace de travail dans la paire de vis et l'a rendu encore plus fiable qu'à sa sortie d'usine :
Réparation groupe à vis Rotorcomp NK100 22kW
Le bloc à vis Rotorcomp du compresseur Renner-Kompressoren nous est parvenu à socle de réparation dans un état bloqué, ayant travaillé honnêtement pendant 5 ans depuis 2007 :
Malgré un entretien régulier du compresseur, le temps a fait des ravages, l'usure des paliers de support a atteint des tolérances critiques, l'huile n'aidait plus à refroidir la paire de vis et les rotors des vis reposaient contre surface de travail, soudé dessus. Ce type de réparation est toujours imprévisible en termes de volume de travail, et après avoir reçu carte blanche du Client, nous avons commencé à démonter le groupe vissé. La décision a été prise de démonter lentement et en douceur afin de minimiser les dommages lors du retrait des pièces soudées. Après une lutte acharnée pour la sécurité, les deux vis ont abandonné avec des pertes minimes pour le portefeuille du client :
Les dommages au couvercle du bloc à vis ont également été minimisés :
Nous avons restauré les surfaces de travail des extrémités des vis et le plan du couvercle à l'aide de machines à souder, de tours et de fraiseuses, ainsi que des connaissances et de l'expérience inestimables de nos mécaniciens. Les roulements de support de la paire de vis ont été remplacés. Nous avons assemblé et configuré l'unité de vis. Renvoyé au client avec des commentaires sur qui contacter et que faire lorsque, après 4 à 5 ans de fonctionnement intensif du compresseur, température de fonctionnement le pétrole recommencera à monter.