Arbres et axes dans l'industrie : applications et types. Conception du procédé technologique de fabrication de la pièce « Axe Matériaux des axes et des arbres
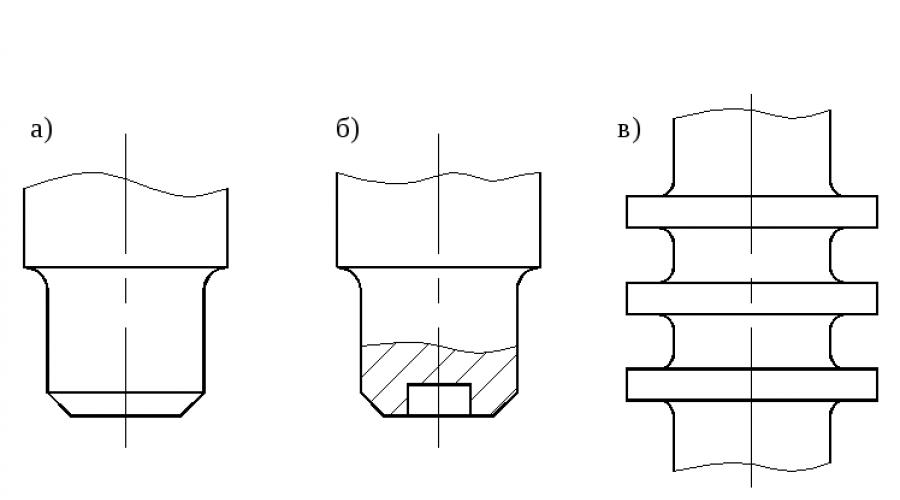
Envoyer votre bon travail dans la base de connaissances est simple. Utilisez le formulaire ci-dessous
Les étudiants, étudiants diplômés, jeunes scientifiques qui utilisent la base de connaissances dans leurs études et leur travail vous seront très reconnaissants.
Publié sur http://www.allbest.ru/
Introduction
À ce stade de développement d’une économie de marché, une grande attention est accordée à la technologie du génie mécanique.
La technologie du génie mécanique est une science qui systématise un ensemble de techniques et de méthodes de traitement des matières premières, des matériaux et des outils de production appropriés afin d'obtenir des produits finis. Le sujet d'étude en génie mécanique est la production de produits d'une qualité donnée avec un programme de production établi au plus bas coût des matériaux, au coût minimum et à une productivité du travail élevée.
Le processus technologique en génie mécanique se caractérise non seulement par l'amélioration de la conception des machines, mais également par l'amélioration continue de leur technologie de production.
Actuellement, en raison du haut niveau de développement de l'électronique dans la construction mécanique, les machines CNC sont largement introduites. L'utilisation de tels équipements permet de réduire : les travaux de plomberie et de finition ; marquage préliminaire; délais de préparation de la production, etc.
Compte tenu de tout cela, j'utilise largement des machines CNC et le projet de thèse considère également un certain nombre de tâches nécessaires pour mener à bien la mission de conception du diplôme.
Ces tâches comprennent :
Augmenter le niveau technique de production ;
Mécanisation et automatisation de la production ;
Développement d'un procédé technologique évolutif pour le traitement de la partie « Axe » ;
Développement de mesures pour accroître encore les économies d'immobilisations, la qualité des produits et réduire le coût de fabrication des pièces.
La bonne solution à tous les problèmes ci-dessus nous permet d’obtenir :
Augmentation de la productivité du travail ;
Libération de certains travailleurs ;
Augmentation de l'effet économique annuel ;
Réduire le délai de récupération des coûts supplémentaires.
1 . Partie technologique
1.1 Description des conditions de fonctionnement, objectif de service de la pièce, analyse de la fabricabilitédétails et faisabilité de transférer son traitement vers des machines CNC
Partie : « Axe » n° B. 5750.0001
Il fait partie intégrante du mécanisme d'entraînement du stabilisateur. La bascule d'entraînement tourne sur l'axe, donc Ctv est appliqué à la surface de Ш40f7. 48-80, trou Ø24H9 pour boulon de montage spécial B. 5750.0001. Pour la fixation avec un boulon de fixation spécial, des rainures 20H11 sont réalisées et 3 trous Ш1,5 sont réalisés pour le verrouillage (verrouillage) 2.2 OST 139502.77, goupille fendue 2,5x 32.029 GOST 397-79.
La fabricabilité de la conception d'une pièce est évaluée par des paramètres qualitatifs et des indicateurs quantitatifs.
Évaluation qualitative de la fabricabilité de la conception
1 La partie « Axe » a une forme géométrique régulière et représente un corps de révolution.
2 Le matériau de la pièce (acier 30KhGSA GOST 4543-71) a une bonne usinabilité.
3 Possibilité d'utiliser un flan d'emboutissage dont la forme géométrique et les dimensions permettent de faibles tolérances d'usinage.
4 La présence d'éléments standardisés d'une pièce confirme la fabricabilité de sa conception.
5 La conception de la pièce a une rigidité suffisante, puisque la condition est remplie
6 La configuration, la précision et la rugosité des surfaces permettent à la pièce d'être traitée à l'aide d'un équipement standard de précision normale et à l'aide d'un outil de coupe standard.
Tableau 1.1 - Précision dimensionnelle et paramètre de rugosité de surface de la pièce
Dimensions des surfaces |
Qualité de précision |
Paramètre de rugosité |
Nombre d'éléments structurels |
Nombre d'éléments unifiés |
|
Évaluation quantitative de la fabricabilité de la conception
1 Coefficient d'unification :
où Que est le nombre d'éléments unifiés ;
Qe - nombre d'éléments structurels.
Coefficient de précision de surface en 2 parties :
où Ti est la qualité de précision des surfaces traitées ;
Tsr. - valeur moyenne de ces paramètres ;
ni - nombre de tailles ou de surfaces pour chaque qualité
3 Coefficient de rugosité de surface des pièces :
où Rai sont respectivement les valeurs des paramètres de rugosité des surfaces traitées ;
Raavg. - valeur moyenne de ces paramètres ;
ni est le nombre de dimensions ou de surfaces pour chaque valeur du paramètre de rugosité.
Conclusion : à partir des coefficients calculés ci-dessus, il ressort clairement que les valeurs numériques de presque tous les indicateurs de fabricabilité sont proches de 1, c'est-à-dire La fabricabilité de la conception de la pièce satisfait aux exigences du produit. Il est conseillé d'usiner la pièce « Axe » sur des machines à commande numérique, car la pièce est bien traitée par découpe et repose de manière pratique.
1.2 Composition chimique etpropriétés mécaniques du matériaudétails
La partie « Axe » est en acier 30KhGSA - un acier allié structurel qui peut résister à des charges de déformation importantes.
Il est recommandé de fabriquer à partir d'acier 30KhGSA : arbres, axes, engrenages, brides, carters, aubes de machines à compresseur fonctionnant à des températures allant jusqu'à 2000C, leviers, poussoirs, structures soudées critiques fonctionnant sous charges alternées, fixations fonctionnant à basses températures.
Les données sur la composition chimique et les propriétés mécaniques du matériau sont placées dans des tableaux provenant de sources pertinentes.
Tableau 1.2 - Composition chimique de l'acier
Tableau 1.3 - Propriétés mécaniques de l'acier
Section, mm |
||||||||
Propriétés technologiques
Soudabilité - soudabilité limitée.
Méthodes de soudage : RDS ; ADS sous protection flux et gaz, ArDS, EShS.
Usinabilité par découpe - à l'état laminé à chaud à HB 207h217 et w=710 MPa.
La sensibilité du troupeau est sensible.
Tendance à tempérer la fragilité - sujette.
1.3 Définition du type de production
En génie mécanique, on distingue les types de production suivants :
Célibataire;
En série (à petite, moyenne, grande échelle) ;
Massif.
Chaque type de production est caractérisé par le coefficient de consolidation de l'opération Kz.o.
Coefficient de consolidation des opérations Kz.o. déterminé par la formule :
où Qop. - le nombre d'opérations différentes réalisées sur le chantier ;
Pm est le nombre de postes de travail (machines) sur lesquels ces opérations sont effectuées.
Selon GOST 3.1108-74, le coefficient de consolidation des opérations est pris égal à
Tableau N°1.4 - Valeur du coefficient de consolidation des transactions
Des calculs ci-dessus, il s'ensuit que la production est en série et que le lot de pièces de lancement doit être déterminé. La taille approximative du lot peut être calculée à l'aide de la formule :
où N est le volume de production annuel, pcs.;
Nombre de jours ouvrables dans une année (365-Twy. - Vacances), jours ;
Le stock requis de pièces dans l'entrepôt en jours varie de 3 à 8 jours
· pour une production unique et à petite échelle 3-4 jours
· pour une production à moyenne échelle 5-6 jours
· pour une production à grande échelle et en série 7-8 jours
La production en série se caractérise par une gamme limitée de produits fabriqués ou réparés en lots périodiquement répétitifs et par des volumes de production relativement importants.
Dans la production de masse, les machines universelles sont largement utilisées, ainsi que les machines spécialisées et partiellement spéciales.
Les équipements sont localisés non seulement en fonction du groupe, mais également en fonction du flux.
L'équipement technologique est universel, ainsi que spécial et universellement préfabriqué, ce qui permet de réduire l'intensité de la main-d'œuvre et le coût de fabrication du produit.
Les travailleurs se spécialisent dans l’exécution de quelques tâches seulement. Le processus technologique est différencié, c'est-à-dire divisé en opérations, transitions, techniques, mouvements indépendants distincts.
Le coût du produit est moyen.
1.4 Analyse des processus d'usine
Chaque pièce doit être fabriquée avec un minimum de coûts de main-d'œuvre et de matériaux. Ces coûts peuvent être réduits dans une large mesure par le choix correct de l'option de processus technologique, son équipement, sa mécanisation et son automatisation, l'utilisation de modes de traitement optimaux et une préparation appropriée de la production. La complexité de fabrication d'une pièce est particulièrement influencée par sa conception et les exigences techniques de fabrication.
Dans le processus technologique d'usine, la partie « Essieu » est traitée comme suit :
005 Salle de contrôle 065 Salle de travail des métaux
010 Virage 070 Marquage
015 Tournage 075 Perçage
020 Retourner 080 Lavage
025 Contrôle 085 Magnétique
030 Thermique 090 Contrôle
035 Sablage 095 Revêtement
040 Tournage 100 Meulage
045 Meulage 105 Travail des métaux
050 Tournage 110 Lavage
055 Marquage 115 Magnétique
060 Fraisage 120 Préparatoire
Comme le montrent les opérations énumérées ci-dessus du processus technologique d'usine, un grand nombre d'opérations de contrôle, de plomberie et de marquage sont utilisées ici, ainsi que des machines universelles à commande manuelle d'ancien modèle.
Je crois que dans ma version du processus technologique d'usinage de la pièce Axis, il est nécessaire d'utiliser des machines CNC performantes dans certaines opérations, ce qui permettra :
Augmenter la productivité du travail ;
Supprimer les opérations de marquage et de plomberie ;
Réduire le temps de réajustement des équipements et d'installation des pièces grâce à l'utilisation de dispositifs d'assemblage universels ;
Réduire le nombre d'opérations ;
Réduisez le temps et l’argent consacrés au transport et au contrôle des pièces ;
Réduire les déchets;
Réduire les besoins en main-d'œuvre ;
Réduire le nombre de machines ;
Appliquer un service multi-machine ;
De plus, dans les opérations de fraisage horizontal et de perçage vertical, il est conseillé d'utiliser des dispositifs spéciaux de changement rapide avec serrage pneumatique, qui assurent une fixation fiable et un positionnement précis de la pièce pendant le traitement, et permettront également :
Réduire le temps de réajustement des équipements ;
Assurer une position fixe et fiable de la pièce dans le luminaire ;
Vous affranchira du marquage préalable avant cette opération
L'utilisation d'outils de coupe spéciaux hautes performances garantit une grande précision et la rugosité nécessaire des surfaces traitées.
1.5 Évaluation technique et économique du choix de la méthode d'obtention de la pièce
Le choix de la méthode d'obtention d'une pièce est l'un des facteurs les plus importants dans la conception et le développement d'un processus technologique.
Le type de pièce et la méthode sont largement déterminés par le matériau de la pièce, le type de production, ainsi que par des propriétés technologiques telles que la forme structurelle et les dimensions globales de la pièce.
Dans la production moderne, l'une des principales orientations du développement de la technologie d'usinage est l'utilisation de pièces de finition présentant des formes structurelles économiques, c'est-à-dire Il est recommandé de déplacer l'essentiel du processus de formage d'une pièce vers l'étape d'ébauche et ainsi de réduire les coûts et la consommation de matière lors de l'usinage.
Dans ma thèse pour la partie « Axe », j'utilise la méthode d'obtention d'une pièce par marquage à chaud sur presses à manivelle.
Avec ce procédé, la forme de la pièce est proche en taille des dimensions de la pièce, réduisant ainsi la consommation de matière et le temps de fabrication de la pièce « Axe », ainsi que le nombre d'opérations d'usinage et, par conséquent, le coût. de cette partie.
1.6 Sélection des bases technologiques
La base est une surface qui remplace un ensemble de surfaces, un axe, un point d'une pièce par rapport auquel sont orientées les autres pièces traitées dans une opération donnée.
Pour augmenter la précision du traitement des pièces, il est nécessaire d'observer le principe de combinaison (unité) des bases, selon lequel, lors de l'attribution des bases technologiques pour le traitement précis d'une pièce, les surfaces qui sont simultanément des bases de conception et de mesure de la pièce doivent être utilisées comme bases technologiques.
Et aussi le principe de constance des bases, qui réside dans le fait que lors du développement d'un processus technologique, il faut s'efforcer d'utiliser la même base technologique, en évitant des changements inutiles dans les bases technologiques.
La volonté d'effectuer le traitement en utilisant une seule base technologique s'explique par le fait que tout changement de base augmente l'erreur de position relative des surfaces traitées.
Après avoir analysé tout ce qui précède, je conclus que pour traiter la pièce « Axe », il est nécessaire de prendre comme surfaces de base les éléments suivants :
Opération 010 Tournage CNC
Installation A : 61,8
Installation B : ? 40.3
: ?40,3
: ?40,3
Opération 025 Rectification cylindrique : trou. SH24H9
1.7 Conception du parcours processus technologique d'une pièce : séquence de traitement ; sélection d'équipement; sélection de machines-outils; sélection d'outils de coupe; sélectionner ou outils auxiliaires
Lors du développement d'un processus technologique, nous sommes guidés par les principes de base suivants :
Tout d'abord, je traite les surfaces qui sont fondamentales pour un traitement ultérieur ;
Après cela, les surfaces avec les tolérances les plus importantes sont traitées ;
Les surfaces dont le traitement est dû à la grande précision de la position relative des surfaces doivent être traitées dans une seule installation ;
Lors du traitement de surfaces de précision, il convient de s'efforcer de respecter deux tolérances principales : la combinaison (unité) des bases et la constance des bases.
Séquence de traitement
Opération 005 Approvisionnement
Opération 010 Tournage CNC
Installation A
Installer et sécuriser la pièce
1 Broyer l'extrémité « proprement »
2 Meuler le chanfrein 1x450
3 Affûter Ø40,4 mm à l=63,5-0,2 mm en conservant R1
4 Meuler le chanfrein 1x450
5 Chanfrein fraisé 1x450
Installation B
Réinstaller, sécuriser la pièce
1 Meuler l'extrémité « proprement » en maintenant l=79,5-0,2 mm
2 Meuler le chanfrein 1x450
3 Affûtage Ø60 mm par passe
4 Fraises Ø23,8 mm par passage
5 Chanfrein fraisé 2,5x450
6 Développez Ø24H9 (+0,052)
7 Contrôle par l'interprète
Opération 015 Fraisage horizontal
Installation A
Installer et sécuriser la pièce
1 Fraisage rainure B=20H11 (+0,13) à l=9,5 mm en maintenant R1
Installation B
Réinstaller, sécuriser la pièce
1 Fraise rainure B=20H11 (+0,13) à l=41 mm
2 Émousser les arêtes vives, limer 2 chanfreins 0,5x450 ; 2 chanfreins 1x450
3 Contrôle par l'interprète
Opération 020 Forage vertical
Installer et sécuriser la pièce
1 Percez 3 trous. Ø1,5 mm par passe, maintien ?1200, l=48 mm
2 Forets 3 chanfreins 0,3x450
3 Contrôle par l'interprète
Opération 025 Thermique
1 Calit 35,5…40,5 HRC
Installer et sécuriser la pièce
1 Broyer Ø40f) à l=60 en utilisant la méthode d'alimentation croisée
2 Contrôle par l'interprète
Opération 035 Contrôle
Sélection d'équipement
Lors du choix de l'équipement, les facteurs suivants sont pris en compte :
Type de production ;
Type de pièce à usiner ;
Exigences relatives à la précision du traitement et à la rugosité de la surface usinée ;
Puissance requise ;
Programme annuel.
Sur la base de ce qui précède, je sélectionne les équipements technologiques.
Opération 010 Tournage CNC
Tour de décolletage CNC 16K20F3
La machine est conçue pour tourner les surfaces externes et internes de pièces à profil étagé et incurvé dans la section axiale dans un cycle semi-automatique spécifié par un programme sur ruban perforé.
Possibilités |
Valeurs numériques |
|
Le plus grand diamètre de la pièce à traiter : |
||
au dessus du lit |
||
au dessus de l'étrier |
||
Le plus grand diamètre de la tige passant à travers le trou de la broche |
||
Longueur maximale de la pièce traitée |
||
Pas de filetage: |
||
Métrique |
||
Nombre de vitesses de broche |
||
Mouvement maximal de l'étrier : |
||
longitudinal |
||
transversal |
||
Avance du pied à coulisse, mm/tr (mm/min) : |
||
longitudinal |
||
transversal |
||
Nombre d'étapes d'alimentation |
||
Vitesse de déplacement rapide de l'étrier, mm/min : |
||
longitudinal et transversal |
||
verticale |
||
Puissance du moteur électrique d'entraînement principal, kW |
||
Dimensions hors tout (sans CNC) : |
||
poids (kg |
Opération 015 Fraisage horizontal
Fraiseuse universelle horizontale 6Р81Ш /10/
La machine est conçue pour effectuer diverses opérations de fraisage, ainsi que des travaux de perçage et d'alésage simples dans des pièces en fonte, en acier et en métaux non ferreux. La machine peut fonctionner en modes semi-automatique et automatique, ce qui rend possible un équipement multi-machines.
Spécifications des machines
Possibilités |
Valeurs numériques |
|
Dimensions du plan de travail (largeur x longueur), mm |
||
Mouvement maximal de la table ; mm : |
||
longitudinal |
||
transversal |
||
verticale |
||
Distance: |
||
de l'axe de la broche horizontale à la surface de la table |
||
de l'axe de la broche verticale aux guides du lit |
||
de l'extrémité de la broche verticale à la surface de la table |
||
Déplacement maximal du manchon de broche vertical, mm |
||
Angle de rotation de la tête de fraisage verticale, dans un plan parallèle à : |
||
mouvement longitudinal de la table |
||
course transversale de la table : |
||
du lit |
||
au lit |
||
Cône de broche intérieur selon GOST 15945-82 : |
||
horizontal |
||
verticale |
||
Nombre de vitesses de broche : |
||
horizontal |
||
verticale |
||
Vitesse de broche, tr/min : |
||
horizontal |
||
verticale |
||
Nombre de flux de table |
||
Avance de la table, mm/min : |
||
longitudinal |
||
transversal |
||
verticale |
||
Vitesse de déplacement rapide de la table, mm/min : |
||
longitudinal |
||
transversal |
||
verticale |
||
Dimensions: |
||
Poids (sans équipement distant), kg |
Opération 020 Forage vertical
Perceuse verticale 2N125
La machine est conçue pour percer, aléser, fraiser, aléser des trous, couper des filetages avec un taraud et couper les extrémités avec des couteaux.
Possibilités |
Valeurs numériques |
|
Plus grand diamètre nominal de perçage, mm |
||
Surface de travail de la table |
||
La plus grande distance entre l'extrémité de la broche et la surface de travail de la table |
||
Porte-à-faux de broche |
||
Course maximale de la broche |
||
Mouvement vertical maximal : |
||
tête de forage |
||
Trous de broche conique Morse |
||
Nombre de vitesses de broche |
||
Vitesse de broche, tr/min |
45; 63; 90; 125; 180; 250; 355; 500; 710; 1000; 1400; 2000 |
|
Avance de la broche |
||
Avance de broche, mm/tr |
0,1; 0,14; 0,2; 0,28; 0,4; 0,56; 0,8; 1,12; 1,6 |
|
Puissance du moteur d'entraînement principal mouvement, kW |
||
Efficacité des machines |
||
Dimensions hors tout, mm : |
||
poids (kg |
Opération 030 Rectification cylindrique
Meuleuse cylindrique semi-automatique pour rectification plongeante et longitudinale, précision accrue 3M151
La machine est conçue pour le meulage externe de surfaces cylindriques et coniques plates.
Possibilités |
Valeurs numériques |
|
Les plus grandes dimensions de la pièce installée : |
||
Longueur de meulage la plus longue : externe |
||
Hauteur des centres au-dessus de la table |
||
Mouvement longitudinal maximum de la table |
||
Angle de rotation en o : |
||
dans le sens des aiguilles d'une montre |
||
dans le sens inverse des aiguilles d'une montre |
||
Vitesse de déplacement automatique de la table (régulation continue), m/min |
||
Vitesse de rotation de la broche pièce avec régulation continue, tr/min |
||
Cône Morse de la broche de la poupée mobile et du fourreau de la poupée mobile |
||
Dimensions de la meule la plus grande : |
||
diamètre extérieur |
||
Déplacement de la tête de meulage : |
||
le plus grand |
||
une division du cadran |
||
par tour de la poignée de jogging |
||
Vitesse de rotation de la broche de la meule, tr/min |
||
lors du meulage externe |
||
Vitesse d'avance en plongée de la tête de meulage, mm/min |
||
Puissance du moteur électrique de l'entraînement principal du mouvement, kW |
||
Dimensions hors tout, mm : |
||
poids (kg |
Sélection de machines-outils
Lors du développement d'un processus technologique d'usinage d'une pièce, il est nécessaire de choisir le bon dispositif, qui devrait contribuer à augmenter la productivité du travail, la précision du traitement, à améliorer les conditions de travail, à éliminer le marquage préliminaire de la pièce et à l'aligner lors de son installation sur la machine.
Opération 010 Tournage CNC
Appareil : mandrin à trois mors autocentrant
GOST 2675-80 est inclus dans l'ensemble complet de la machine ; centre tournant
GOST 2675-80.
Opération 015 Fraisage horizontal
Appareil : dispositif de réglage spécial pour le fraisage d'une pièce avec vérin pneumatique intégré.
Opération 020 Forage vertical
Appareil : Tête de division universelle GOST 8615-89 ;
cent dur GOST 13214-79.
Opération 030 Rectification cylindrique
Appareil : mandrin d'entraînement pour travaux de meulage
GOST 13334-67 Pince d'entraînement pour travaux de meulage
GOST 16488-70
Choisir un outil de coupe
Lors du choix d'un outil de coupe, vous devez vous efforcer d'utiliser un outil standard, mais il est parfois conseillé d'utiliser un outil spécial, combiné ou façonné qui vous permet de combiner le traitement de plusieurs surfaces.
Le choix correct de la partie coupante de l'outil est également d'une grande importance pour augmenter la productivité du travail, en augmentant la précision et la qualité de la surface usinée.
Opération 010 Tournage CNC
Installation A
Transition 01, 02, 03, 04 Fraise de poussée passante avec plaques en alliage dur T15K6, 16x25 GOST 18879-73 /7/
Installation B
Transition 01, 02, 03 Fraise coudée de poussée traversante avec inserts en carbure T15K6, 16x25 GOST 18879-73
Caractéristiques techniques du cutter : H=25 mm, H=16 mm, L=140 mm, n=7 mm, l=16 mm, r=1,0 mm.
Transition 04 Fraise pleine Ø23,8 mm en acier rapide R6М5 avec tige conique GOST 12489-71
Caractéristiques techniques de la fraise : D=23,8 mm, L=185 mm, l=86 mm.
Transition 05 Fraise ?450 en acier rapide R6M5 avec queue conique OST-2
Caractéristiques techniques de la fraise : D=32 mm, L=145 mm, l=56 mm.
Alésoir Transition 06 en acier rapide massif Ш24H9 (+0,052) avec tige conique GOST 1672-80
Caractéristiques techniques de l'alésoir : D=24 mm, L=225 mm, l=34 mm
Opération 015 Fraisage horizontal
Transition 01 Coupe-disque à trois faces Sh125 avec couteaux à insert équipés d'un alliage dur T15K6, z=8 GOST 5348-69
Caractéristiques techniques de la fraise : D=100 mm, B=20 mm, d=32 mm, z=8 mm.
Transition 02 Lime à aiguilles plate GOST 1513-77
Caractéristiques techniques du coupeur : L=130 mm.
Opération 020 Forage vertical
Transition 01 Foret hélicoïdal ? 1,5 mm en acier rapide R6M5 avec une tige cylindrique GOST 10902-77
Caractéristiques techniques du foret : d=1,5 mm, L =63 mm, l=28 mm.
Transition 02 Foret hélicoïdal ? 6 mm en acier rapide R6M5 avec une tige cylindrique GOST 10902-77
Caractéristiques techniques du foret : d=6 mm, L =72 mm, l=34 mm
Opération 030 Rectification cylindrique
Transition 01 Meule 300x63x76 PP 24A40NSM25K8
GOST 2424-83.
Caractéristiques techniques du cercle : D = 300 mm, B = 63 mm, d = 76 mm.
1.7.5 Sélection d'un outil auxiliaire
Lors du choix des outils auxiliaires, ils utilisent les mêmes principes que les machines-outils.
Sur la base de ce qui précède, je sélectionne des outils auxiliaires.
À l'opération 010 Tournage CNC :
Installation A
Transition 05 - J'utilise le manchon adaptateur GOST 13598-85
Installation B
Transition 04, 05, 06 - J'utilise le manchon adaptateur GOST 13598-85.
1.8 Détermination des allocations opérationnelles, tolérances, interopérationnellestailles et dimensions de la pièce (pour deuxles surfaces produisentcalcul des allocations par méthode analytique)
La sélection d'une pièce pour un usinage ultérieur et l'établissement des valeurs des surépaisseurs et tolérances rationnelles pour le traitement sont l'une des étapes très importantes dans la conception du processus technologique de fabrication d'une pièce. Du bon choix de la pièce, c'est-à-dire L'établissement de ses formes, dimensions, tolérances de traitement, précision dimensionnelle et dureté du matériau dépend en grande partie de la nature et du nombre d'opérations ou de transitions, de l'intensité du travail de fabrication de la pièce, de la quantité de matière et d'outils consommés et, en fin de compte, du coût de fabriquer la pièce.
Détermination des quotas par méthode analytique
La méthode analytique de détermination des tolérances est basée sur l'analyse des erreurs de production qui surviennent dans des conditions de traitement spécifiques de la pièce.
Pour les surfaces externes ou internes des corps de révolution, les tolérances opérationnelles 2Zi min µm sont déterminées par la formule :
où est la hauteur des microrugosités de surface ;
Profondeur de la couche superficielle défectueuse ;
La valeur totale des écarts géométriques spatiaux ;
Erreur d'installation
On détermine les surépaisseurs intermédiaires et les dimensions intermédiaires lors de l'usinage de la surface du trou ? 24Н9 (+0,052).
Pour plus de clarté et de facilité de détermination des tolérances et des tailles intermédiaires, nous établissons un tableau.
Tableau 1.5 - Calculs des tolérances, tolérances et dimensions intermédiaires pour une surface donnée
Surface de la pièce et itinéraire de traitement |
Tolérance de taille, mm |
Éléments d'indemnité, |
Allocations intermédiaires, mm |
||||||||
Estampage vierge |
|||||||||||
Alésage simple |
|||||||||||
Enfilage |
Vérifier : Tdzag - Tdd =
1400 - 62 = (3758+352) - (2488 + 284)
1338 µm = 1338 µm
Riz. 1.1 - Disposition des champs de surépaisseurs et de tolérances sur la surface usinée
Nous déterminons les tolérances intermédiaires et les dimensions intermédiaires lors du traitement de la surface de l'arbre ?40f7.
Pour plus de clarté et de facilité de détermination des tolérances, tolérances et dimensions intermédiaires, nous établissons un tableau /10/
Tableau 1.6 - Calculs des tolérances, tolérances et dimensions intermédiaires pour une surface donnée
Type de pièce et opération technologique |
Précision de la pièce et de la surface usinée |
Tolérance de taille, mm |
Éléments de tolérance, microns |
Dimensions intermédiaires de la pièce, mm |
Allocations intermédiaires, mm |
||||||
Estampage vierge |
|||||||||||
Tournage grossier |
|||||||||||
Terminer le tournage |
|||||||||||
Meulage par traitement thermique |
Vérifier : Tdzag - Tdd =
1400 - 25 = (2818+468+54) - (1668+257+40)
1375 µm = 1375 µm
Riz. 1.2 - Disposition des champs de surépaisseurs et de tolérances sur la surface usinée
Calcul des tolérances, tolérances, dimensions interopérationnelles sous forme tabulaire
Pour les surfaces restantes de la pièce, je considère les tolérances, les tolérances et les dimensions interopérationnelles à l'aide d'une méthode tabulaire ; je résume les données obtenues dans un tableau ;
Tableau 1.7 - Calcul des tolérances, tolérances et dimensions intermédiaires pour les autres surfaces
Sous-séquence traitement |
Qualité de précision |
Rugosité |
Tolérances mm |
Montant de l'allocation |
Taille de conception, mm |
Taille limite, mm |
Tolérance maximale, mm |
|||
Estampage vierge Tournage simple semi-propre l=79,5 |
||||||||||
Estampage vierge Tournage simple semi-finition ?60 |
Tableau 1.8 - Dimensions interopérationnelles des surfaces de la pièce
1.9 Définition de la normeconsommation (calculer le taux d'utilisation des matériaux et le taux d'utilisation des pièces)
Pour déterminer le taux de consommation de matière, il est nécessaire de déterminer la masse de la pièce. La masse de la pièce est calculée en fonction de son volume et de la densité du matériau. Il faut s'efforcer de faire en sorte que la forme et les dimensions de la pièce soient proches de la forme et des dimensions de la pièce finie, ce qui réduit la complexité de l'usinage, réduit la consommation de matière, d'outils de coupe, d'électricité, etc.
La masse de la pièce est calculée à l'aide de la formule :
où est la densité du matériau, g/cm3
Volume total de la pièce, cm3.
En règle générale, une figure de pièce complexe doit être divisée en parties élémentaires de forme géométrique correcte et les volumes de ces parties élémentaires doivent être déterminés. La somme des volumes élémentaires sera le volume total de la pièce.
Le volume d'un tuyau cylindrique V, cm3 est calculé à l'aide de la formule :
où est le diamètre extérieur du tuyau cylindrique, cm
Diamètre intérieur d'un tuyau cylindrique, cm
h est la hauteur du tuyau cylindrique, cm.
Le bon choix de la méthode d'obtention d'une pièce est caractérisé par deux coefficients :
Kim - taux d'utilisation des matériaux
Kiz - facteur d'utilisation de la pièce
où est la masse de la pièce, g
où est la masse des pertes métalliques (déchets, bavures, par segment, etc.)
Le taux d'utilisation du matériel varie dans les limites suivantes :
Pour coulée 0,65 h 0,75…0,8
Pour estampage 0,55h 0,65…0,75
En location 0,3h 0,5
Après avoir calculé le coefficient d'utilisation du matériau et le coefficient d'utilisation de la pièce, je conclus que ces coefficients se situent dans des limites acceptables. Par conséquent, la méthode choisie pour obtenir la pièce est correcte.
1.10 Détermination des modes de coupe, puissance pour deux
La détermination des modes de coupe et de la puissance peut être effectuée selon deux méthodes :
Analytique (en utilisant des formules empiriques);
Tabulaire
Calcul des conditions de coupe pour deux opérations ou transitions différentes à l'aide de formules empiriques
Nous calculons les modes de coupe et la puissance pour diverses opérations et transitions à l'aide de formules empiriques
Opération 010 Tournage CNC
Installation B
Transition 01 Meuler l'extrémité « proprement » en maintenant l=79,5-0,2 mm
Profondeur de coupe : t=1,0 mm
Avance : S=0,5 mm/tour /10/
Vitesse de coupe V, m/min :
où Cv = 350 ; x=0,15 ; y = 0,35 ; m=0,2 /7/
T - durée de vie de l'outil, min (T=60 min)
Kv = Kmv Knv Kuv KTv KTc Kc Kr
où Kf est un coefficient caractérisant le groupe d'acier selon son usinabilité
Кnv - coefficient prenant en compte l'influence de l'état de surface de la pièce sur la vitesse de coupe (Кnv=0,8) /9/
Kuv - coefficient prenant en compte l'influence du matériau de l'outil sur la vitesse de coupe (Kuv=1,15) /9/
КTv - coefficient prenant en compte la durée de vie des outils en fonction du nombre d'outils travaillant simultanément (КTv=1,0)/9/
KTs est un coefficient qui prend en compte la durée de vie de l'outil en fonction du nombre de machines entretenues simultanément (KTs = 1,0)
Kts - coefficient prenant en compte l'influence de l'angle principal dans le plan c (Kts = 0,7)
Kr - coefficient prenant en compte l'influence du rayon r à la pointe de la fraise (Kr=0,94) /9/
Kv = 0,56 0,8 1,15 1,0 1,0 0,7 0,94 ? 0,34
Vitesse de rotation de la pièce, n tr/min :
où V - vitesse de coupe, m/min
D - diamètre de la surface traitée, mm
Selon les conditions de traitement nous acceptons :
npr= 359 tr/min
Force de coupe, PZ N :
PZ = 10 Cp tx Sy Vn Kp
où Cp = 300 ; x=1,0 ; y = 0,75 ; n= -0,15 /7/
Kr - coefficient influençant la force de coupe
Kr = Kmp·Köp·Kp·Kp·Krp
où n est l'exposant (n=0,75) /9/
Kcr - coefficient prenant en compte l'influence de l'angle principal dans le plan
sur l'effort de coupe (Ktsr=0,89) /9/
Kr - coefficient qui prend en compte l'influence de l'angle de coupe sur la force de coupe (Kr = 1,0) /9/ Kr - coefficient qui prend en compte l'influence de l'angle d'inclinaison de la lame principale sur la force de coupe (Kr = 1.0). Krp est un coefficient qui prend en compte l'influence du rayon au sommet sur l'effort de coupe (Krp = 0,87).
Kr = 1,31 0,89 1,0 1,0 0,87 ? 1.01
D'où l'effort de coupe PZ N :
PZ = 10 300 1.01.0 0.50.75 70-0.15 1.01 ? 947N
Avance minute Sm, mm/min
où So est l'avance par tour de la pièce, mm/tour ;
npr - vitesse de rotation de la pièce acceptée tr/min
Sm = 0,5 359 ? 180 mm/min
Puissance de coupe effective Ne, kW :
où est la force de coupe, N
Vitesse de coupe, m/min
La puissance effective est calculée correctement si la condition est remplie : 1,08 kW 10 0,75
1,08 kW 7,5 kW
Opération 015 Fraisage horizontal
Transition 01 Temps de broyage jusqu'à la taille 20H
Profondeur de coupe : 9 mm
Largeur de fraisage B = 20 mm
Portion : Sz. =0,06 mm/dent /10/
Vitesse de coupe V, m/min :
où Cv = 690 ; m = 0,35 ; x = 0,3 ; y = 0,4 ; u = 0,1 ; p = 0 /5/
T - durée de vie de la fraise, min (T=120 min) ; /7/
B - largeur de fraisage, mm. B = 20 mm
Kv - coefficient affectant la vitesse de coupe
Kv = Kmv Kuv Klv
où Kmv est un coefficient qui prend en compte l'influence des propriétés physiques et mécaniques du matériau traité sur la vitesse de coupe
où Kf est un coefficient caractérisant le groupe d'acier selon l'usinabilité (Kf=0,8)
nv - exposant (nv=1,0)
Kuv - coefficient prenant en compte l'influence du matériau de l'outil sur la vitesse de coupe (Kuv=1,0)
Kv = 0,54 0,8 1,0 ? 0,5
D'où la vitesse de coupe V, m/min :
Vitesse de broche, n tr/min :
où les désignations sont les mêmes
nd=500 tr/min
Vitesse de coupe réelle Vd, m/min :
où les désignations sont les mêmes
Avance minute Sm, mm/min :
où les désignations sont les mêmes
Sm =0,06·8·500=240 mm/min
Selon les conditions de traitement et les données du passeport machine, j'accepte :
Sm = Sv =200 mm/min, l'avance réelle par dent de fraise est alors :
Force de coupe, Pz N :
où Cp = 261 ; x = 0,9 ; y = 0,8 ; u = 1,1 ; = 1,1 ; w = 0,1 /7/
où Kp est le coefficient influençant la force de coupe
où Kmp est un coefficient qui prend en compte l'influence de la qualité du matériau traité sur la force de coupe
où n est l'exposant (n=0,3) /9/
Kmp = ? 1.12 D'où la force de coupe, Pz N :
Puissance de coupe Ncut, kW :
où les désignations sont les mêmes
Vérifier si la puissance d'entraînement de la machine est suffisante
Mettre sous tension la broche de la machine N_(shp,)
où les désignations sont les mêmes
La puissance de coupe effective est calculée correctement si la condition suivante est remplie :
3,56 kW 6 Le traitement est donc possible.
Calcul des modes de coupe et de la puissance pour d'autres opérations et transitions selon les normes en vigueur Pour faciliter l'utilisation ultérieure des modes de coupe calculés, nous établissons un tableau
Tableau 1.9 - Calcul des conditions de coupe pour les opérations de processus technologiques
Profondeur de coupe, mm |
Avance S mm/tour SZ mm/dent |
Vitesse de coupe V, mm/min |
Vitesse de rotation n, tr/min |
Vitesse de coupe réelle Vf m/min |
Avance minute Sm mm/min |
Puissance de coupe Nр, kW |
|
Opération 010 Tournage CNC Transition 01 Broyer la fin « proprement » |
|||||||
Transition 02 Chanfrein de meulage 1x450 |
|||||||
Transition 03 Affûter Ø40,4 mm à l=63,5-0,2 mm, en tenant R1 |
|||||||
Transition 04 Chanfrein de meulage 1x45o |
|||||||
Transition 05 Chanfrein fraisé 1x45o |
|||||||
Installation B Transition 02 Chanfrein de meulage 1x45o |
|||||||
Transition 03 Affûtage Ø60 mm par passe |
|||||||
Transition 04 Fraisage Ø23,8 mm par passage |
|||||||
Transition 05 Chanfrein fraisé 2,5x450 |
|||||||
Transition 06 Développer Ø24H9 (+0,052) |
|||||||
Opération 020 Forage vertical Transition 01 Percez 3 trous. Ø1,5 mm par passe, maintien ?1200, l=48 mm |
|||||||
Transition 02 Foret 3 chanfreins 0,3x450 |
|||||||
Opération 030 Rectification cylindrique Transition 01 Meuler Ø40f) à l=60 mm par avance transversale |
|||||||
1.11 Détermination des normes de temps pour les opérations
La norme technique de temps de traitement d'une pièce est le paramètre principal pour calculer le coût de la pièce en cours de fabrication, le nombre d'équipements de production, les salaires et la planification de la production. La norme de temps technique est déterminée sur la base des capacités techniques des équipements technologiques, des outils de coupe, des équipements des machines et de l'organisation correcte du lieu de travail.
Détermination des normes de temps pour une opération effectuée sur une machine CNC
Opération 010 Tournage CNC
1 Temps de fonctionnement automatique de la machine Ta, min :
Ta = Toa + Twa
où Toa est le temps principal de fonctionnement automatique de la machine, min ;
Тwa - temps de fonctionnement auxiliaire de la machine selon le programme, min.
où l est la longueur de la surface usinée dans le sens de l'avance, en mm ;
l1 - taille d'entrée, mm ;
l2 - valeur de surcourse, mm ;
S - avance par tour de pièce, mm/tour ;
je - nombre de passes.
Toa =0,06+0,03+0,25+0,03+0,02+0,03+0,12+0,41+0,71+0,03 = 1,69 min
Tva = Tvha + Toast
où Tvha est le temps d'exécution des mouvements auxiliaires automatiques (approvisionnement d'une pièce ou d'un outil depuis les points de départ jusqu'aux zones d'usinage et retrait, mise à la dimension de l'outil), min ;
où dxx est la longueur à vide, mm ;
Sxx - régime de ralenti, m/min ;
Nombre de sections technologiques.
Toast - temps des pauses technologiques (arrêts, avance de la broche pour vérifier les dimensions, inspection ou changement d'outil), min
où a est le nombre d'arrêts
2 Temps de travail manuel auxiliaire TV, min :
où a=0,0760 ; x = 0,170 ; y = 0,15
Temps auxiliaire associé à l'opération, min
où a=0,36 ; b= 0,00125 ; c = 0,04 ; d = 0,022 ; =0
X® Yo Z® - coordonnées zéro ;
k est le nombre de correcteurs configurés ;
lpl - longueur du ruban de papier perforé, m (lpl=0,5 m)
Temps auxiliaire superposé pour les mesures de contrôle de la pièce, min
où k = 0,0187 ; z = 0,21 ; u = 0,330 /11/
D - diamètre mesuré, mm
L - longueur mesurée, mm
TV = 0,25 + 0,58 + 0,16 = 0,99 min
3 Temps préparatoire et final Тпз, min :
Тпз = а + в nu + c Pp + d Pnn
où a =11,3 ; c = 0,8 ; c = 0,5 ; d = 0,4
nu - nombre d'outils de coupe ;
Рр - nombre de modes de fonctionnement initiaux établis de la machine (Рр=2) ;
Pnn - nombre de tailles sélectionnées par les interrupteurs du panneau de commande (Pnn = 2 h 3)
T nз = 11,3 + 0,8 4 + 0,5 2 + 0,4 3 = 16,7 min
Après avoir déterminé la télévision, elle est ajustée en fonction de la production en série.
4 Facteur de correction de sérialisation :
où a=4,17 ; x =0,216 ;
où npr est le lot productif de pièces, pcs. (article 1.4)
5 pièces de temps Tpcs, min :
où (aorg + aotl) - pourcentage de temps pour l'entretien organisationnel et technique du lieu de travail et le repos (aorg + aotl) = 10% /2/
Délai de traitement d'un lot de pièces :
où les désignations sont les mêmes
T = 3,44 280 + 16,7 = 980 minutes
Détermination des normes de temps pour les opérations effectuées sur les machines universelles
Opération 015 Fraisage horizontal
Installation A
Transition 01
où L est le chemin parcouru par l'outil, mm :
où l est la longueur de la surface traitée, mm ;
l1 - la quantité de pénétration de l'outil, mm ;
l2 - surcourse de l'outil, mm ;
n est la vitesse de rotation de la pièce, tr/min ;
je - nombre de passes.
où est le temps auxiliaire d'installation et de retrait de la pièce, min
Temps auxiliaire associé à la transition, min
Temps auxiliaire associé aux mesures de contrôle, min
Installation B
Transition 01
1 Temps de fonctionnement principal de la machine To, min :
Temps TV auxiliaire, min :
où les désignations sont les mêmes
Haut = 0,48 + 1,0 = 1,48 min
Tobs = 3,5% du Toper
Total = 4% du Toper
où K est le pourcentage total de temps consacré à l'entretien du lieu de travail et au temps consacré au repos et aux besoins personnels
où est le temps préparatoire et final de mise en place de la machine, des outils et des appareils, min
Temps préparatoire et final pour les réceptions supplémentaires, min
Temps préparatoire et final de réception des outils et appareils avant le début et de leur remise après la fin du traitement, min
Opération 020 Forage vertical
Transition 01
1 Temps de fonctionnement principal de la machine To, min :
2 Durée TV auxiliaire, min :
Transition 02
1 Temps de fonctionnement principal de la machine To, min :
2 Durée TV auxiliaire, min :
3 Temps de fonctionnement Toper, min :
Haut = 0,93 + 0,79 = 1,72 min
4 Temps d'entretien du lieu de travail Tobs, min :
Tobs = 4% de Toper
5 Temps de repos et besoins personnels Total, min :
Total = 4% du Toper
6 Norme de temps à la pièce Tsht, min :
7 Temps préparatoire et final Тпз, min :
8 Temps de calcul des pièces Tshk, min :
Opération 030 Rectification cylindrique
Transition 01
1 Temps de fonctionnement principal de la machine To, min :
où est la longueur de course de la table, mm/d. se déplacer
Marge de traitement par côté, mm
Avance longitudinale minute, mm/min
Avance croisée, mm/tr
2 Durée TV auxiliaire, min :
3 Temps de fonctionnement Toper, min :
Surmatelas = 0,3+ 0,81= 1,11 min
4 Temps d'entretien du lieu de travail Tobs, min :
Tobs =9% de Toper
5 Temps de repos et besoins personnels Total, min :
Total = 4% du Toper
6 pièces de temps Tpcs, min :
7 Préparatoire - temps final Тпз, min :
8 Temps de calcul des pièces Tshk, min :
Pour faciliter les calculs ultérieurs, je résume toutes les données obtenues dans un tableau.
Tableau 1.10 - Normes de temps pour toutes les opérations du processus technologique
Calcul et codage de programmes pour des opérations données
Sur la base de tous les calculs effectués ci-dessus, je calcule et code le programme de contrôle pour l'opération 010 Tournage CNC.
Tableau 1.11 - Parcours d'outil
À l'aide des données tabulaires compilées, je code le programme :
Installation A
Installation B
Contrôle du programme
En règle générale, lors de la préparation d'un programme, des erreurs surviennent et sont corrigées au cours du processus de débogage et de mise en œuvre du programme.
Des erreurs se produisent lors de la spécification des données initiales lors du calcul et de l'enregistrement du programme sur le support logiciel. Ainsi, on distingue les erreurs géométriques, technologiques et les erreurs de perforation ou d'enregistrement sur bande magnétique.
Des erreurs géométriques apparaissent lorsque les dimensions d'une pièce, d'une pièce, etc. sont mal spécifiées. Pour identifier les erreurs géométriques, divers types de dispositifs graphiques sont utilisés, par exemple des affichages de coordonnées et graphiques. Les erreurs technologiques sont associées à la sélection continue des outils de coupe, des modes de coupe et à la séquence de traitement de la pièce sur la machine. Les erreurs d'écriture d'un programme sur le support logiciel apparaissent à la suite d'actions incorrectes de la part des technologues lors de la saisie d'informations ou à la suite de dysfonctionnements dans le fonctionnement du dispositif de préparation des données. Ces erreurs apparaissent lors du contrôle du programme de contrôle sur une machine à coordonnées ou sur des machines CNC.
2 . Partie conception
2.1 Description de la conception et du calcul de la machine-outil
Objectif de l'appareil et principe de fonctionnement de l'appareil conçu
La tête de division avec pince de serrage est conçue pour le traitement des rainures lors de l'opération de fraisage de pièces de type « Axe ».
Le principe de fonctionnement de l'appareil est le suivant : L'air comprimé du réseau est amené par un raccord (19) à un vérin pneumatique (20) formé dans le corps de l'appareil et agit sur le piston (22). La force résultante est transmise à travers la butée à billes (37) à trois axes (25), qui soulèvent la coupelle (4) placée dans le manchon de guidage en acier (7).
En remontant, le verre comprime le cône de la pince (5) à trou conique. La pièce est fixée en place.
Lorsque l'alimentation en air est coupée, les doigts (9) sous l'action du ressort (8) ramènent la vitre dans sa position d'origine.
Pour passer à la position suivante, la pince ainsi que la pièce sont tournées avec la poignée (29). Pour se déplacer dans le sens des aiguilles d'une montre, le disque excentrique (27) pousse le verrou (14) hors de la rainure du disque diviseur (28), et le cliquet (30) sous l'action du ressort (31) tombe dans sa rainure suivante.
Lorsque la poignée (29) recule, le cliquet (30) fait tourner le disque diviseur (28) avec le disque (3) et la pince (5) montée dessus avec la pièce jusqu'à ce que le loquet (14) tombe dans la rainure suivante. du disque diviseur et ainsi, cela ne fixera pas la rotation de la pièce de 900.
Le capuchon (6) protège les fentes des pinces des copeaux lors du fraisage.
Calcul et précision
L'erreur de base est l'écart de la position réellement atteinte et est définie comme la distance maximale du champ de dispersion entre les bases technologiques et de mesure dans la direction de la taille maintenue.
L'erreur totale lors de l'exécution de toute opération d'usinage consiste en :
1 erreur dans l'installation de la pièce ;
2 erreur de réglage de la machine
3 erreur de traitement qui se produit lors du processus de fabrication de la pièce. La valeur de l'erreur de base est déterminée par les calculs suivants :
où est l'erreur d'installation de la pièce ;
Erreur de réglage de la machine ;
Erreur de traitement survenant lors du processus de fabrication d'une pièce ;
d - tolérance de taille.
L'erreur d'installation est l'une des composantes de l'erreur totale de la taille de la pièce réalisée. Cela se produit lorsque la pièce est installée dans le montage et comprend l'erreur de positionnement, l'erreur de fixation et l'erreur de position de la pièce, qui dépend de la précision du montage et est déterminée par des erreurs dans la fabrication et l'assemblage de ses éléments installés. et leur usure en fonctionnement.
Des erreurs de réglage de la machine se produisent lors de la mise à la taille de l'outil de coupe, ainsi qu'en raison de l'imprécision des copieurs et des butées pour obtenir automatiquement la taille de la pièce.
L'erreur de traitement qui se produit lors du processus de fabrication d'une pièce sur une machine s'explique par :
1 Imprécision géométrique de la machine ;
2 Déformation du système technologique sous l'influence des forces de coupe ;
3 Imprécision dans la fabrication et usure des outils et accessoires de coupe.
4 Déformations thermiques du système technologique.
Ey = 0,02+0+0,03=0,05 mm
0,05+0,03+0,03 ? 0,13 mm
0,11 mm ? 0,13 mm
Détermination de la force de serrage
Pour déterminer la force de serrage, il est nécessaire de calculer la force de coupe pour l'opération pour laquelle le luminaire est conçu.
La force de coupe pour cette opération est calculée au paragraphe 1.10, puis j'en retire toutes les données pour le calcul.
Pour assurer un serrage fiable de la pièce, il est nécessaire de déterminer le facteur de sécurité à l'aide de la formule :
où est le facteur de sécurité garanti
Coefficient qui prend en compte l'augmentation des efforts de coupe due aux irrégularités aléatoires sur les surfaces usinées
Coefficient caractérisant l'augmentation des efforts de coupe due à la matité de l'outil de coupe
Coefficient prenant en compte l'augmentation des efforts de coupe lors de coupes intermittentes
Coefficient caractérisant les forces de fixation dans le mécanisme de serrage
Coefficient caractérisant l'économie des mécanismes de serrage manuels
Coefficient qui prend en compte la présence de moments tendant à faire tourner une pièce montée sur une surface plane
Alors nous l'acceptons
La force de serrage requise est déterminée par la formule :
La surface du piston du vérin pneumatique est déterminée par la formule :
où - pression du réseau = 0,38 MPa
Le diamètre du vérin pneumatique est déterminé par la formule :
J'accepte le diamètre standard du vérin pneumatique
Détermination de la force de serrage réelle du cylindre
Détermination du temps de tir du cylindre
où est la course de la tige
Vitesse de course de la tige, m/s
Calcul de la faisabilité économique du dispositif
Le calcul de la faisabilité économique de l'utilisation du dispositif conçu est basé sur une comparaison des coûts et de la faisabilité économique.
où sont les économies annuelles sans tenir compte des coûts annuels d'adaptation, frotter.
P - coûts annuels des appareils
Les économies annuelles sont déterminées par la formule
temps unitaire lors du traitement d'une pièce sans montage = 1,52 min
Unité de temps par opération après mise en œuvre du dispositif
Taux horaire pour l'exploitation d'un lieu de travail pour le type de production
25 roubles/heure
N - programme de sortie annuel
Les coûts annuels sont déterminés par la formule :
où est le coût de l'appareil
A - coefficient d'amortissement
Coefficient B prenant en compte la réparation et le stockage des appareils
P = 4500 (0,56+0,11) = 3015 frotter.
D'après les calculs de production et la condition de faisabilité, dans mon cas cette condition est remplie.
J’en conclus que l’utilisation du dispositif conçu est économiquement réalisable.
2.2 Description de la conception et du calcul d'une découpe spécialeoutil
Lors de la conception d'un outil de coupe, certaines conditions doivent être remplies :
Trouvez les angles d’affûtage les plus favorables ;
Déterminer les forces agissant sur les pièces coupantes ;
Sélectionnez le matériau le plus approprié pour la partie coupante et la partie de connexion de l'outil ;
Établir les écarts admissibles dans les dimensions des parties de travail et de connexion de l'outil, en fonction des conditions de travail et de la précision et de la qualité requises de la surface usinée ;
Effectuer les calculs nécessaires des éléments de l'outil de coupe et, si nécessaire, effectuer des calculs de résistance et de rigidité ;
Élaborer un dessin d'exécution de l'outil avec les exigences techniques nécessaires au fonctionnement et à la production ;
Calculer les coûts économiques des matériaux instrumentaux.
Sur la base des conditions ci-dessus, je calcule une fraise à disque à trois faces pour le fraisage de rainures de taille 20h11 en opération 015 Fraisage
Données initiales pour le calcul :
Matériau de la pièce 30HGSA ;
Surépaisseur d'usinage t=9 mm
Documents similaires
Processus technologique de fabrication de la pièce "Couvercle de roulement". Technologie d'usinage. Objectif du service et caractéristiques technologiques de la pièce. Détermination du type de production. Analyse du plan d'exécution de la pièce, parcours technologique.
travail de cours, ajouté le 10/11/2010
Caractéristiques et avantages des machines contrôlées par ordinateur. Objectif du service, analyse du matériau et fabricabilité de la conception de la pièce fabriquée. Version de conception du processus technologique d'usinage d'une pièce, mise en place d'une machine.
travail de cours, ajouté le 19/06/2017
Objectif fonctionnel et conception de la pièce « Levier droit », analyse de la fabricabilité de la conception. Choisir une méthode d'obtention de la pièce initiale. Processus technologique d'usinage d'une pièce. Sélection d'équipement ; machine-outil, mode de coupe.
travail de cours, ajouté le 09/04/2016
Objectif du service et caractéristiques techniques de l'équipement. Analyse de la fabricabilité de la conception des pièces. Développement d'un procédé technologique de traitement d'une pièce. Calcul des allocations et précision du traitement. Conception d'équipements pour la production de rainures de clavette.
travail de cours, ajouté le 16/11/2014
Objectif du service et exigences techniques de la pièce. Contrôle technologique du dessin et analyse de la fabricabilité de la conception. Choisir une méthode d'obtention de la pièce. Conception d'une technologie d'itinéraire pour le traitement des pièces. Calcul des conditions de coupe et des normes de temps.
travail de cours, ajouté le 12/06/2010
Calcul du volume de production et détermination du type de production. Caractéristiques générales de la pièce : destination de service, type, fabricabilité, examen métrologique. Développement d'un itinéraire processus technologique pour la fabrication d'une pièce. Croquis de traitement, d'installation.
travail de cours, ajouté le 13/02/2014
Conception d'un itinéraire processus technologique pour l'usinage d'une pièce. Analyse de la fabricabilité de la conception des pièces. Choisir une méthode d'obtention d'une pièce. Description de la conception et du principe de fonctionnement de l'appareil. Calcul des paramètres de transmission de puissance.
travail de cours, ajouté le 23/07/2013
Calcul du volume de production et de la taille des lots de pièces. Le but de service de la partie « arbre ». Analyse de la conformité des conditions techniques et des normes de précision avec la destination de la pièce. Analyse de la fabricabilité de la conception des pièces. Parcours technologique pour fabriquer une pièce.
travail de cours, ajouté le 10/03/2011
Description et caractéristiques de la pièce fabriquée. Analyse de la fabricabilité de la conception des pièces. Conception d'un processus technologique de traitement mécanique. Développement d'un programme de contrôle. Normalisation technique des opérations de processus technologiques.
travail de cours, ajouté le 22/11/2009
Objectif de service de la pièce. Justification de la méthode d'obtention de la pièce. Développement d'un procédé technologique de fabrication d'une pièce. Justification du choix des bases technologiques. Conception d'outils de coupe. Standardisation technique des opérations des machines.
MÉCANIQUE APPLIQUÉE ET
LES BASES DE LA CONCEPTION
Conférence 8
ARBRE ET AXES
SUIS. SINOTIN
Département de technologie et d'automatisation de la production
Arbres et axes Informations générales
Les engrenages, poulies, pignons et autres pièces de machines rotatives sont montés sur des arbres ou des essieux.
Arbre conçu pour supporter les pièces posées dessus et pour transmettre le couple. Pendant le fonctionnement, l'arbre subit une flexion et une torsion, et dans certains cas une tension et une compression supplémentaires.
Axe- une pièce destinée uniquement à supporter les pièces posées dessus. Contrairement à un arbre, un essieu ne transmet pas de couple et ne subit donc pas de torsion. Les axes peuvent être fixes ou tourner avec les pièces montées sur eux.
Variété d'arbres et d'essieux
Selon leur forme géométrique, les arbres sont divisés en droits (Figure 1), coudés et flexibles.
1 – pointe ; 2 – cou; 3 – roulement
Figure 1 – Arbre droit étagé
Les vilebrequins et les arbres flexibles sont des pièces spéciales et ne sont pas abordés dans ce cours. Les essieux sont généralement droits. Dans leur conception, les arbres droits et les essieux diffèrent peu les uns des autres.
La longueur des arbres et des essieux droits peut être lisse ou étagée. La formation des marches est associée à différentes tensions des sections individuelles, ainsi qu'aux conditions de fabrication et à la facilité d'assemblage.
Selon le type de profilé, les arbres et axes peuvent être pleins ou creux. La section creuse est utilisée pour réduire le poids ou pour être placée à l'intérieur d'une autre pièce.
Éléments structurels des arbres et des essieux
1 Tourillons. Les sections de l'arbre ou de l'axe situées dans les supports sont appelées essieux. Ils sont divisés en épines, cous et talons.
Épine appelé tourillon, situé à l'extrémité d'un arbre ou d'un axe et transmettant une charge majoritairement radiale (Fig. 1).
Figure 2 – Talons
Cou appelé tourillon situé dans la partie médiane de l'arbre ou de l'axe. Les roulements servent de supports aux cols.
Les pointes et les cols peuvent être de forme cylindrique, conique ou sphérique. Dans la plupart des cas, des broches cylindriques sont utilisées (Fig. 1).
Cinquième appelé tourillon qui transmet la charge axiale (Figure 2). Les butées servent de supports aux talons. La forme des talons peut être pleine (Figure 2, a), en anneau (Figure 2, b) et en peigne (Figure 2, c). Les talons peignes sont rarement utilisés.
2 surfaces d'atterrissage. Les surfaces d'appui des arbres et des axes des moyeux des pièces montées sont cylindriques (Figure 1) et moins souvent coniques. Lors des ajustements par pression, le diamètre de ces surfaces est considéré comme étant environ 5 % plus grand que le diamètre des zones adjacentes pour faciliter le pressage (Figure 1). Les diamètres des surfaces d'appui sont sélectionnés conformément à GOST 6336-69 et les diamètres des roulements sont sélectionnés conformément aux normes GOST pour les roulements.
3 zones de transition. Les sections de transition entre deux étages d'arbres ou d'essieux réalisent :
Avec une rainure arrondie pour la sortie de la meule conformément à GOST 8820-69 (Figure 3, a). Ces rainures augmentent la concentration des contraintes et sont donc recommandées aux sections d'extrémité où les moments de flexion sont faibles ;
Figure 3 – Sections de transition du puits
avec un congé * de rayon constant selon GOST 10948-64 (Figure 3, b);
Avec un congé à rayon variable (Figure 3, c), qui contribue à réduire la concentration des contraintes et est donc utilisé sur les zones fortement chargées des arbres et des essieux.
Des moyens efficaces pour réduire la concentration de contraintes dans les zones de transition consistent à tourner les rainures de dégagement (Figure 4, a), à augmenter les rayons de congé et à percer par étapes de grand diamètre (Figure 4, b).
Figure 4 – Méthodes pour augmenter la résistance à la fatigue des arbres
La pièce sur laquelle sont montées les pièces tournantes de la machine, qui met effectivement en œuvre l'axe géométrique de rotation de ces pièces, est appelée axe ou arbre.
L'essieu est destiné uniquement à supporter des pièces en rotation. Les axes peuvent être fixes par rapport à la machine ou tourner avec les pièces montées sur eux. Dans tous les cas, l'axe ne perçoit que des charges de flexion provenant des forces agissant sur les parties rotatives des machines.
L'arbre, contrairement à l'essieu, supporte non seulement les pièces en rotation, mais transmet également le couple. En conséquence, les arbres sont soumis non seulement à des forces de flexion, mais également à un couple.
Le couple est lié à la puissance transmise et au nombre de tours de l'arbre par le rapport
Où N- puissance, kWt ;
n- nombre de tours d'arbre, tr/min.
En fonction de la forme de l'axe géométrique de l'arbre, on les distingue : arbres droits et vilebrequins. Les vilebrequins sont généralement considérés comme une conception spéciale plutôt que comme une conception standard. Les arbres droits peuvent être lisses s'ils ont un diamètre constant sur toute la longueur ou étagés.
Un groupe spécial se compose d'arbres avec une forme changeante de l'axe géométrique - les arbres flexibles.
Les sections de support des essieux et des arbres sont appelées essieux. Selon le système de chargement, la direction des réactions d'appui peut être radiale ou axiale.
Les tourillons qui perçoivent les réactions d'appui dans la direction radiale sont appelés tenons s'ils sont d'extrémité, ou tourillons s'ils sont situés à distance de l'extrémité de l'arbre.
Les tourillons qui perçoivent les réactions d'appui axial sont appelés talons. Le même problème de conception peut être résolu en utilisant à la fois un arbre et un axe.
UN- le tambour est monté sur un axe fixe, une roue dentée d'entraînement en rotation de l'arbre est fixée au tambour ; b- le tambour est fixé sur un axe rotatif ; V- le tambour est fixé sur l'arbre, l'engrenage est également fixe, le couple de l'engrenage au tambour est transmis par l'arbre.
Quand " UN"l'axe subit une flexion unilatérale, dans le cas de " b"la charge sur l'essieu est alternée, donc le diamètre de l'essieu doit être plus grand. Mais en option" b"Accès plus facile aux roulements. Avantage de cette option" V" offre un accès libre aux unités de friction ; le montage de l'engrenage sur l'arbre plutôt que sur le tambour simplifie la conception.
Les diamètres des sièges d'essieu et d'arbre sont choisis en standard, ce qui permet d'utiliser des outils de mesure et des roulements standards. Les tailles disponibles sont sélectionnées parmi une gamme de numéros préférés.
Le passage sur un arbre étagé d'un diamètre à un autre ne s'effectue pas brusquement, mais à l'aide d'un congé afin de réduire les contraintes de fatigue qui surviennent sous des charges alternées.
Une réduction significative de la masse de l'arbre ou de l'essieu avec une légère diminution du moment résistant peut être obtenue en utilisant un arbre creux. Les essieux et les arbres sont des pièces critiques dont la résistance doit être calculée. L'axe est considéré pour le pliage. L'arbre, en plus de la flexion, est vérifié pour une vitesse critique. Dans certains cas, en plus de la résistance, il est nécessaire de vérifier la rigidité de l'arbre.
Étant donné que les arbres et les essieux sont des éléments structurels assez chargés, des matériaux à haute résistance sont utilisés pour leur fabrication. Ainsi, si la machine est en métaux ferreux, l'arbre ou l'essieu est en acier 45, dans les structures en acier inoxydable - en 3X13, etc. Il convient de noter que ces nuances d'acier peuvent être soumises à des méthodes de durcissement et d'autres traitements thermiques.
Une conception spéciale est constituée d'arbres flexibles utilisés pour transmettre le mouvement entre les pièces si l'emplacement relatif de leurs axes de rotation change pendant le fonctionnement. Exemple: utilisation d'un vibrateur dans les travaux de béton.
Une conception courante est un arbre flexible, constitué d'un certain nombre de couches de fil d'acier enroulées successivement les unes sur les autres. La première couche à partir du centre est enroulée sur le fil central - le noyau, qui peut ensuite être retiré de l'arbre ou laissé à l'intérieur de celui-ci. Structurellement, l'arbre flexible est similaire à un ressort de torsion hélicoïdal multicouche et à plusieurs fils avec des bobines et des couches étroitement adjacentes les unes aux autres. Les couches adjacentes ont des directions d'enroulement opposées. Le sens de rotation de l'arbre doit être tel que le ressort formant la couche externe se tord plutôt qu'il ne se déroule.
Auparavant, nous parlions des engrenages comme d'un mécanisme global et considérions également les éléments directement impliqués dans la transmission du mouvement d'un maillon du mécanisme à un autre. Ce thème présentera des éléments destinés à la fixation des pièces du mécanisme directement impliquées dans la transmission du mouvement (poulies, pignons, engrenages et vis sans fin, etc.). En fin de compte, la qualité du mécanisme, son efficacité, ses performances et sa durabilité dépendent en grande partie des détails qui seront discutés plus loin. Le premier de ces éléments du mécanisme sera les arbres et les essieux.
Arbre(Fig. 17) - une partie d'une machine ou d'un mécanisme conçu pour transmettre un couple ou un couple le long de sa ligne médiane. La plupart des arbres sont des pièces rotatives (mobiles) de mécanismes ; des pièces directement impliquées dans la transmission du couple (engrenages, poulies, pignons de chaîne, etc.) y sont généralement fixées.
Axe(Fig. 18) - une partie d'une machine ou d'un mécanisme conçu pour supporter des pièces rotatives et n'intervient pas dans la transmission de la rotation ou du couple. L'axe peut être mobile (rotatif, Fig. 18, a) ou fixe (Fig. 18, b).
Classification des arbres et des essieux :
1. Selon la forme de l’axe géométrique longitudinal :
1.1.droit(axe géométrique longitudinal - ligne droite), par exemple, arbres de boîtes de vitesses, arbres de boîtes de vitesses de véhicules à chenilles et à roues ;
1.2. coudé(l'axe géométrique longitudinal est divisé en plusieurs segments, parallèles entre eux et décalés les uns par rapport aux autres dans le sens radial), par exemple le vilebrequin d'un moteur à combustion interne ;
1.3. flexible(l'axe géométrique longitudinal est une ligne de courbure variable, qui peut changer pendant le fonctionnement du mécanisme ou lors des activités d'installation et de démontage), sont souvent utilisés dans l'entraînement du compteur de vitesse des voitures.
2. Par finalité fonctionnelle :
2.1. arbres de transmission, ils portent des éléments transmettant le couple (engrenages ou roues à vis sans fin, poulies, pignons, accouplements, etc.) et sont pour la plupart équipés de pièces d'extrémité qui dépassent des dimensions du corps du mécanisme ;
2.2. arbres de transmission sont destinés, en règle générale, à distribuer l'énergie d'une source à plusieurs consommateurs ;
2.3. arbres principaux- les arbres qui portent les corps de travail des actionneurs (les arbres principaux des machines-outils qui portent la pièce ou l'outil sont appelés broches).
3. Arbres droits selon leur conception et leur surface extérieure :
3.1. lisse les arbres ont le même diamètre sur toute la longueur ;
3.2. fait un pas les puits se distinguent par la présence de sections de diamètres différents ;
3.3. creux les arbres sont équipés d'un trou traversant ou borgne, coaxial à la surface extérieure de l'arbre et s'étendant sur la majeure partie de la longueur de l'arbre ;
3.4. cannelé les arbres le long de la surface cylindrique extérieure ont des saillies longitudinales - des cannelures, uniformément espacées autour de la circonférence et conçues pour transmettre le moment de charge depuis ou vers les pièces directement impliquées dans la transmission du couple ;
3.5. arbres combinés avec des éléments directement impliqués dans la transmission du couple (arbre de transmission, arbre à vis sans fin).
Éléments structurels du puits sont présentés dans la Fig. 19.
Pièces de support les arbres et les essieux par lesquels les charges agissant sur eux sont transmises aux parties du corps sont appelés tourillons. Le tourillon situé dans la partie médiane de l'arbre est généralement appelé cou. Le tourillon d'extrémité de l'arbre, qui transmet uniquement la charge radiale ou la charge radiale et axiale simultanément aux pièces du boîtier, est appelé épine, et le tourillon d'extrémité transmettant uniquement la charge axiale est appelé cinquième. Les éléments des pièces du boîtier interagissent avec les tourillons de l'arbre, permettant à l'arbre de tourner, de le maintenir dans la position requise pour un fonctionnement normal et de prendre la charge de l'arbre. En conséquence, les éléments qui perçoivent une charge radiale (et souvent avec radiale et axiale) sont appelés roulements, et des éléments conçus pour absorber uniquement les charges axiales - butées.
Un épaississement annulaire d'un arbre de courte longueur, formant un tout avec lui et destiné à limiter le mouvement axial de l'arbre lui-même ou des pièces montées sur celui-ci, est appelé épaule.
La surface de transition d'un diamètre d'arbre plus petit à un diamètre d'arbre plus grand, qui sert à supporter les pièces montées sur l'arbre, est appelée épaule.
La surface de transition de la partie cylindrique de l'arbre à l'épaulement, réalisée sans enlever de matière des surfaces cylindriques et d'extrémité (Fig. 20. b, c), est appelée filet. Le congé est destiné à réduire la concentration des contraintes dans la zone de transition, ce qui entraîne à son tour une augmentation de la résistance à la fatigue de l'arbre. Le plus souvent, le congé est réalisé sous la forme d'une surface radiale (Fig. 20. b), mais dans certains cas, le congé peut être réalisé sous la forme d'une surface à double courbure variable (Fig. 20. c). La dernière forme de congé permet une réduction maximale de la concentration des contraintes, mais nécessite un chanfrein spécial dans le trou de la pièce montée.
Une petite dépression sur la surface cylindrique d'un arbre, réalisée le long d'un rayon par rapport à l'axe de l'arbre, est appelée rainure(Fig. 20, a, d, f). Une rainure, comme un congé, est très souvent utilisée pour concevoir la transition de la surface cylindrique d'un arbre à la surface d'extrémité de son épaulement. La présence d'une rainure dans ce cas offre des conditions favorables à la formation de surfaces d'appui cylindriques, puisque la rainure est l'espace de sortie de l'outil qui forme la surface cylindrique lors de l'usinage (fraise, meule). Cependant, la rainure n'exclut pas la possibilité de formation d'une marche sur la surface d'extrémité de l'épaulement.
Une petite dépression sur la surface d'extrémité de l'épaulement de l'arbre, réalisée le long de l'axe de l'arbre, est appelée saper(Fig. 20, d). La contre-dépouille offre des conditions favorables à la formation de la surface d'appui d'extrémité de l'épaulement, puisque c'est un espace de sortie de l'outil qui forme cette surface lors de l'usinage (fraise, meule), mais n'exclut pas la possibilité de la formation d'un pas sur la surface cylindrique de l'arbre lors de son traitement final.
Ces deux problèmes sont résolus en introduisant un arbre dans la conception rainure inclinée(Fig. 20, e), qui combine les avantages d'une rainure cylindrique et d'une contre-dépouille.
Riz. 21. Variétés de configurations de tourillons |
Les tourillons d'arbre peuvent prendre la forme de différents corps de rotation (Fig. 21) : cylindrique, conique ou sphérique. Les cous et les colonnes vertébrales sont le plus souvent réalisés cylindrique(Fig. 21, a, b). Les tourillons de cette forme sont technologiquement avancés en matière de fabrication et de réparation et sont largement utilisés avec les roulements et les roulements. DANS forme de cône ils fabriquent des tourillons d'extrémité (pointes, Fig. 21, c) d'arbres, fonctionnant généralement avec des paliers lisses, afin d'assurer la possibilité de régler l'écart et de fixer la position axiale de l'arbre. Les goujons coniques assurent une fixation plus précise des arbres dans la direction radiale, ce qui réduit le faux-rond de l'arbre à grande vitesse. L'inconvénient des goujons coniques est leur tendance à se coincer lorsque l'arbre se dilate sous l'effet de la température (augmentation de la longueur).
Journaux sphériques(Fig. 21, d) compensent bien les désalignements des roulements et réduisent également l'influence de la flexion de l'arbre sous l'influence des charges de fonctionnement sur le fonctionnement des roulements. Le principal inconvénient des tourillons sphériques est la complexité accrue de la conception du roulement, ce qui augmente le coût de fabrication et de réparation de l'arbre et de son roulement.
Les talons (Fig. 22) selon la forme et le nombre de surfaces de friction peuvent être divisés en solide, anneau, peigne Et segmentaire.
Talon solide(Fig. 22, a) est le plus simple à fabriquer, mais se caractérise par une répartition inégale importante de la pression sur la zone d'appui du talon, une élimination difficile des produits d'usure par les fluides lubrifiants et une usure considérablement inégale.
Talon annulaire(Fig. 22, b) de ce point de vue est plus favorable, bien qu'un peu plus difficile à fabriquer. Lorsque le lubrifiant est fourni à la région axiale, son flux se déplace le long de la surface de friction dans la direction radiale, c'est-à-dire perpendiculairement à la direction de glissement, et presse ainsi les surfaces de frottement les unes des autres, créant des conditions favorables au glissement relatif des surfaces.
Riz. 22. Quelques formes de talons. |
Talon segmenté peut être obtenu à partir d'un anneau en appliquant plusieurs rainures radiales peu profondes, situées symétriquement en cercle, sur la surface de travail de ce dernier. Les conditions de frottement dans un tel talon sont encore plus favorables par rapport à celles décrites ci-dessus. La présence de rainures radiales favorise la formation d'un coin liquide entre les surfaces frottantes, ce qui conduit à leur séparation à des vitesses de glissement réduites.
Talon peigne(Fig. 22, c) comporte plusieurs courroies de support et est conçu pour absorber des charges axiales d'ampleur significative, mais dans cette conception, il est assez difficile d'assurer une répartition uniforme de la charge entre les arêtes (une grande précision de fabrication est requise, à la fois le talon lui-même et la butée). L'assemblage d'unités avec de telles butées est également assez compliqué.
Les extrémités de sortie des arbres (Fig. 923) ont généralement cylindrique ou forme conique et sont équipés de rainures de clavette ou de cannelures pour transmettre le couple.
Les extrémités d'arbre cylindriques sont plus faciles à fabriquer et sont particulièrement préférées pour la coupe de cannelures. Les extrémités coniques centrent mieux les pièces qui y sont montées et sont donc préférables pour les arbres à grande vitesse.
Les pièces tournantes de machines sont montées sur des arbres ou des axes qui assurent une position constante de l'axe de rotation de ces pièces.
Les arbres sont des pièces conçues pour transmettre un couple le long de leur axe et pour supporter les pièces de machines en rotation.
Les arbres, selon leur destination, peuvent être divisés en arbres de transmission, parties porteuses des engrenages - engrenages, poulies, pignons, accouplements (Fig. , UN et b), et sur arbres principaux machines et autres arbres spéciaux qui, en plus des pièces de transmission, portent les parties actives des machines, des moteurs ou des outils - roues ou disques de turbine, manivelles, mandrins de serrage, etc. (Fig. V Et d)
Selon la forme de l'axe géométrique, les arbres sont divisés en arbres droits et coudés.
Essieux– les pièces conçues pour supporter des pièces en rotation et ne transmettant pas de couple utile.
Riz. 12.1 Principaux types d'arbres et d'essieux :
a – arbre de transmission lisse ; b – arbre étagé ;
c – broche de machine ; g - arbre de turbine à vapeur ; d – vilebrequin ;
e – axe du chariot rotatif ; g – axe non rotatif du chariot.
Les pièces de support des arbres et des essieux sont appelées tourillons. Les essieux intermédiaires sont appelés cous, Terminal - pointes.
Arbres droits selon formulaire divisé en arbres de diamètre constant (arbres de transmission et de navire à travées multiples, fig. , UN, ainsi que les arbres qui transmettent uniquement le couple) ; arbres étagés (la plupart des arbres, Fig. Dieu); arbres avec brides pour raccordement sur toute la longueur, ainsi que arbres avec engrenages coupés ou vis sans fin. Selon la forme de la section transversale, les arbres sont divisés en arbres lisses, cannelés, ayant un profil de connexion à engrenage (cannelure) sur une certaine longueur, et en profil.
Longueur de l'arbre déterminé par la répartition des charges sur la longueur.
En règle générale, les diagrammes des moments le long des arbres sont considérablement inégaux. Le couple n'est généralement pas transmis sur toute la longueur de l'arbre. Les diagrammes des moments de flexion vont généralement à zéro aux supports d'extrémité ou aux extrémités des arbres. Par conséquent, selon les conditions de résistance, il est permis et conseillé de concevoir des arbres de section variable se rapprochant de corps de résistance égale. En pratique, je réalise des arbres étagés. Cette forme est pratique à fabriquer et à assembler ; Les épaulements d'arbre peuvent absorber des forces axiales importantes.
La différence entre les diamètres des marches est déterminée par : les diamètres standards des surfaces d'appui des moyeux et des roulements, une surface d'appui suffisante pour absorber les forces axiales à des rayons d'arrondi des bords et des tailles de chanfrein donnés et, enfin, les conditions de les assemblées.
Tourillons Les arbres (cols) fonctionnant dans les paliers lisses sont : a) cylindriques ; b) conique ; c) sphérique (Fig.). L'application principale concerne les broches cylindriques. Pour faciliter l'assemblage et la fixation de l'arbre dans la direction axiale, les tourillons d'extrémité sont généralement constitués d'un diamètre légèrement plus petit que la section adjacente de l'arbre (Fig.).
Les tourillons d'arbre pour roulements (Fig.) se caractérisent par une longueur plus courte que les tourillons pour roulements lisses.
Les tourillons pour roulements sont souvent fabriqués avec des filetages ou d'autres moyens de fixation des bagues.
Riz. 12.4 Concevoir des moyens pour augmenter l'endurance
arbres dans les zones d'atterrissage : a – épaississement de la partie moyeu de l'arbre ;
b – arrondi des bords du moyeu ; c – amincissement du moyeu ; g – déchargement
rainures; d – bagues ou remplissages dans le moyeu en matériau à faible module
élasticité.
Endurance de l'arbre est déterminé par des volumes relativement faibles de métal dans les zones de concentration de contraintes importante. Par conséquent, une conception spéciale et des mesures technologiques visant à augmenter l’endurance des arbres sont particulièrement efficaces.
Les moyens structurels permettant d'augmenter l'endurance des puits sur les sites d'atterrissage en réduisant les pressions sur les bords sont illustrés à la Fig. .
En renforçant les pièces du moyeu par grenaillage de surface (roulage à rouleaux ou à billes), la limite d'endurance des arbres peut être augmentée de 80 à 100 %, et cet effet s'étend aux arbres d'un diamètre allant jusqu'à 500 à 600 mm.
La résistance des arbres aux endroits des connexions à clavette, à engrenages (cannelées) et autres connexions détachables avec le moyeu peut être augmentée : en utilisant des connexions cannelées en développante ; connexions cannelées avec un diamètre interne égal au diamètre de l'arbre dans les zones adjacentes, ou avec une sortie en douceur des cannelures vers la surface, garantissant une concentration minimale de contraintes ; rainures réalisées avec un coupe-disque et ayant une sortie douce vers la surface ; connexions sans clé.
Charges axiales et sur les arbres à partir des pièces montées sur eux sont transférés des manières suivantes. (riz.)
1) charges lourdes - en focalisant les pièces sur les rebords de l'arbre, en installant des pièces ou des anneaux de montage avec interférence (Fig. , UN Et b)
2) charges moyennes - avec écrous, broches directement ou à travers des anneaux de montage, connexions de bornes (Fig. ,c - d);
3) charges légères et protection contre les mouvements par des forces aléatoires - verrouillage des vis directement ou via des anneaux de montage, des connexions de bornes, des anneaux à ressort (Fig. , d-g).