Four sous vide : four à arc, à induction, sous vide thermique, ainsi que four à hydrogène. Four de fusion sous vide à induction à fréquence industrielle
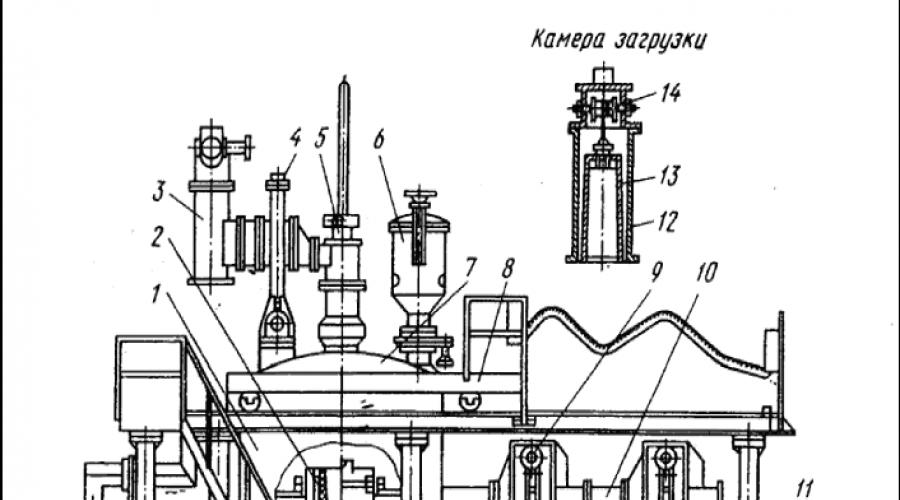
Lire aussi
Boîtier de chambre à vide du four à induction : double couche refroidi à l'eau, en acier spécial SUS304. La mise sous vide est assurée par un anneau en forme de "O". Le boîtier est équipé d'un système de refroidissement par eau (évite le vieillissement du joint torique). La conduite de raccordement du système à vide est située sur le corps de la chambre à vide. L'intérieur du foyer est équipé d'une plate-forme ou d'un trou de coulée. Lors de la coulée, le four est mis en rotation à l'aide d'un entraînement situé à l'extérieur de la chambre.
L'inducteur du four sous vide est fabriqué en cuivre électrique sans oxygène de haute qualité, section carrée TU1 avec refroidissement par eau. Inducteur utilisé entreprise allemande Leybold.
Couvercle du four à induction sous vide: double couche refroidi à l'eau, mur intérieur en acier spécial SUS304. Le couvercle du four est équipé d'une unité de refroidissement par eau, d'une fenêtre d'inspection et d'une unité de verrouillage.
Le four est équipé d'un puissant convertisseur de puissance à thyristors moyenne fréquence, conçu sur la base de thyristors de nouvelle génération, de capteurs de courant et de tension à grande vitesse, garantissant une fiabilité, une immunité au bruit et une polyvalence élevées.
Le système de refroidissement par eau d'un four à vide est divisé en trois parties : le système de refroidissement du convertisseur moyenne fréquence, le système de refroidissement du corps du four, l'inducteur et le système de vide.
Le système de vide se compose généralement d'une pompe mécanique avec une électrovanne de pression différentielle pneumatique (empêche les fuites d'huile de la pompe à vide), d'une pompe Roots, d'une pompe de charge, de vannes pneumatiques, d'une vanne d'alimentation en air, d'une vanne de décharge d'air, d'une conduite de vide, et des tuyaux ondulés.
Le niveau de vide est mesuré à l’aide d’un vacuomètre combiné numérique. Des capteurs avancés de dépressurisation à l'hélium sont utilisés pour mesurer le coefficient d'augmentation de pression, ce qui garantit la fiabilité et la précision des indicateurs techniques.
Utilisé pour connecter des pompes et des conduites de vide connexion rapide métal tuyaux ondulés(réduit les vibrations). Le niveau de vide est mesuré avec un vacuomètre numérique.
MAGMATEX utilise des capteurs avancés de dépressurisation à l'hélium pour mesurer le coefficient d'augmentation de pression, ce qui garantit la fiabilité et la précision des indicateurs techniques.
Vide fours à induction(VIP) selon le mode de fonctionnement sont divisés en fours discontinus et semi-continus.
Les fours discontinus n'ont qu'une seule chambre : la chambre de fusion et de coulée. Après chaque fusion et coulage des moules, la chambre spécifiée est dépressurisée ; supprimez-en le formulaire rempli ; nettoyer et remplir le creuset ; la charge y est à nouveau chargée ; placer un formulaire vide dans la chambre ; fermez la caméra ; l'air en est pompé et une nouvelle fonte est réalisée.
Les fours sous vide semi-continus comportent, en plus de la chambre de fusion et de coulée, des chambres supplémentaires - au moins une verticale et une ou deux horizontales. Chacune des chambres supplémentaires est reliée à une extrémité à la chambre de fusion et de coulée (MPC), et la seconde extrémité est libre. Des chambres supplémentaires sont isolées de la chambre de fusion et de coulée (au niveau des points de connexion) par des joints sous vide. Des volets similaires ouvrent ou ferment les extrémités libres des chambres. En VIP semi-continu, chargement de la charge dans le creuset et sa fusion, dosage et tous types de finitions de LM, alimentation des moules vides (ou moules), leur remplissage, solidification des LM, extraction des formes remplies - toutes ces technologies les opérations sont effectuées sans briser le vide dans le PZK.
Basé sur la méthode d'évacuation du métal liquide d'un creuset vers un moule ou un moule, on distingue les VIP :
a) avec l'ensemble du SCP incliné avec le creuset et le moule coulé, suspendus sur des charnières au boîtier de cette chambre ;
b) avec seulement le creuset incliné à l'intérieur du PZK, et le moule à couler est monté immobile sur un support à l'intérieur de la chambre.
Les fours sous vide à fonctionnement semi-continu comprennent les fours VIAM - 100, VIAM - 24, ISV - 0.6, ULVAK, KONSARK, etc.
Le four VIAM-100 PZK a une forme cylindrique et est situé horizontalement. Approximativement au centre de la chambre se trouve un creuset (avec un inducteur) qui, lors de la vidange du métal liquide, s'incline le long de l'axe du joint. Au-dessous du creuset se trouve une table à rouleaux (avec rouleaux à disques), sur laquelle les moules sont placés pendant le coulage. Une chambre cylindrique verticale est installée sur la partie supérieure du boîtier du SCP, à travers laquelle la charge est chargée dans le creuset sans dépressuriser l'espace de travail de fusion du four. L'axe de la chambre de charge verticale coïncide avec l'axe de symétrie du creuset.
Avant de démarrer le prochain cycle du four
VIAM – 100 il faut : le creuset doit être inspecté, nettoyé et réparé (si nécessaire) ; Fermez le SCP de tous les côtés avec des joints sous vide (c'est-à-dire, isolez-le de toutes les autres chambres) et pompez-en l'air jusqu'à une pression résiduelle de mmHg. Art.; dépressuriser les chambres supérieures et latérales, c'est-à-dire ouvrir leurs joints sous vide externes. À proprement parler, les opérations énumérées sont effectuées avant le début de la première fusion. Si le four fonctionne en mode continu (par exemple, pendant deux équipes), alors le PZK, bien entendu, n'est pas dépressurisé et la charge est chargée dans le creuset immédiatement après la vidange de la dose précédente de métal liquide.
Ensuite, pour reprendre un nouveau cycle de fusion, il faut : prélever une dose des composants de charge dans un panier de chargement spécial, la placer dans la chambre de charge et fermer la chambre avec un joint sous vide externe ; pomper l'air de la chambre de charge jusqu'à une pression résiduelle égale à la pression dans la vanne d'arrêt ; ouvrir le joint sous vide interne entre ces chambres, décharger la charge du panier dans le creuset ; soulevez le panier vide dans la chambre de dosage et fermez le joint sous vide interne ; air soufflé (à pression atmosphérique) dans la chambre de charge ; ouvrir le joint sous vide externe ; collecter une dose de composants de charge dans le panier de chargement, etc. ; commencer à faire fondre la charge dans le creuset.
Le four VIAM-100 dispose également de deux chambres cylindriques supplémentaires horizontales. Ces chambres sont situées sur les côtés (gauche et droit) du bouclier de protection central et y sont reliées par leurs extrémités de travail. Comme mentionné ci-dessus, chaque chambre latérale aux deux extrémités (de travail et libre) est fermée ou ouverte par des volets à vide. Au fond des chambres se trouvent des convoyeurs à rouleaux avec des rouleaux à disques situés au même niveau que les rouleaux de la vanne d'arrêt. Par l'une des chambres latérales (par exemple celle de droite), les moules vides sont introduits dans la chambre de fusion pour être coulés. Appelons la chambre de droite la chambre de chargement. Par l'autre (à gauche), ils sont retirés une fois remplis. Appelons la chambre de gauche la chambre de déchargement. La séquence d'alimentation des moules vides après la fin de la fusion est la suivante : placer les moules à couler sur la table à rouleaux auxiliaire (devant la chambre de droite) de manière à ce que les bols verseurs de formes différentes se trouvent dans un même plan horizontal, le plus pratique pour verser à partir du creuset ; pousser les formulaires sur la table à rouleaux à l'intérieur de la chambre de droite et la fermer avec un joint sous vide externe ; pomper l'air de la chambre de chargement (à droite) jusqu'à une pression résiduelle égale à la pression dans la vanne d'arrêt ; ouvrir le joint sous vide entre ces chambres, soumettre (tour à tour) le premier, le deuxième et les autres moules au coulage, en positionnant chacun d'eux de manière à ce que le bol verseur soit sous le pied du creuset, et remplir les moules (le nombre de moules dépend sur leur teneur en métaux et leurs dimensions hors tout) ; fermer le joint sous vide entre les chambres de fusion et de coulée et de chargement ; introduire de l'air dans la chambre de chargement (à pression atmosphérique), ouvrir la mise sous vide externe et préparer la prochaine arrivée de formulaires.
La chambre latérale gauche est utilisée comme suit : fermer l'extrémité libre avec un joint sous vide externe (l'extrémité active a été fermée avec un joint sous vide avant le début de la fusion) : pomper l'air de la chambre de refoulement (gauche) jusqu'à une pression résiduelle égale à la pression dans le robinet d'arrêt ; ouvrir le volet sous vide entre ces chambres, déplacer les moules coulés de la salle de fusion vers la chambre de gauche et fermer le volet sous vide, tout en maintenant le « vide » dans la vanne d'arrêt ; alimenter en air (à pression atmosphérique) la chambre de déchargement, ouvrir le volet sous vide externe et dérouler les formulaires remplis sur le convoyeur à rouleaux auxiliaire situé après la chambre de gauche. L'ordre et la durée de fonctionnement de toutes les chambres doivent être coordonnés afin que le temps d'arrêt du four soit minimal. Si des moules en céramique coquille obtenus par moulage à modèle perdu sont utilisés, le temps entre le retrait de ces moules du four de calcination et le coulage ne doit pas dépasser 15 minutes.
Le four VIAM-100 peut fonctionner avec une chambre latérale, par exemple celle de droite, en l'utilisant aussi bien pour charger des formulaires vides que pour décharger des formulaires remplis. La séquence de fermeture et d'ouverture des vannes à vide, de pompage ou d'alimentation en air de la chambre latérale, etc. dépend de l'usage pour lequel elle est utilisée à une étape donnée du fonctionnement du four.
Le four sous vide VIAM-24 se compose de trois chambres principales : fusion et coulée, chargement et alimentation et distribution des moules de coulée.
La vanne de sécurité est dotée forme cylindrique, est situé horizontalement et est fermé aux extrémités par des fonds sphériques, dont celui de devant s'ouvre comme une porte, et celui de derrière s'éloigne le long de l'axe de la chambre. Au centre de la chambre se trouve un creuset (avec un inducteur) fixé au fond arrière, donc si vous déplacez le fond, le creuset est retiré du SCP et à l'aide, par exemple, d'un atelier pont roulant le creuset ou l'inducteur peut être réparé ou remplacé. Lors de la vidange du creuset de métal liquide, celui-ci s'incline dans un plan perpendiculaire à l'axe de sa chambre. Sous le creuset se trouve un convoyeur à rouleaux avec des rouleaux à disques pour la mise en place des moules pendant le coulage.
La chambre de charge est réalisée sous la forme d'un cylindre, est située verticalement sur le boîtier PZK, coaxialement au creuset, et est isolée de l'espace de fusion par un joint sous vide. Le chargement de la charge à travers cette chambre s'effectue de la même manière que dans le four VIAM-100.
La seule chambre latérale a une forme cylindrique, est située horizontalement et son extrémité active est reliée à la vanne de sécurité par un joint sous vide. Un tel obturateur ferme et ouvre l'extrémité libre de la chambre latérale. À l’intérieur de la chambre se trouve un convoyeur à rouleaux avec rouleaux à disques. La séquence d'alimentation des formulaires vides à partir de cette chambre pour le remplissage et la réception des formulaires remplis est la même que dans les chambres similaires du four VIAM-100. Un convoyeur à rouleaux auxiliaire pour les formulaires vides et remplis est également installé devant la chambre.
En figue. La figure 1.5 montre un dispositif pour un vide semi-continu ITP de type ISV - 0.6 pour la coulée de lingots à partir d'alliages résistants à la chaleur et d'aciers spéciaux.
Le four ISV - 0.6 est entretenu comme suit : La vanne de sécurité 1 du four est fermée sur le dessus par un couvercle 7 situé sur un chariot automoteur de type pont 8 à entraînement électrique. Le chariot avec le couvercle se déplace sur les rails vers la droite (selon Fig. 1.5), la vanne d'arrêt s'ouvre, laissant libre accès pour le nettoyage, la réparation et le remplacement du creuset 3.
Riz. 1.5. ITP sous vide type ISV – 0,6
semi-continu :
1 – chambre de fusion et de coulée ; 2 – creuset de fusion ; 3 – chambre de chargement de la charge dans le creuset ; 4 – colonne rotative ; 5 – dispositif de prélèvement d'échantillons de fluide et de mesure de sa température ; 6 – distributeur ; 7 – couvercle de la chambre de fusion et de coulée ; 8 – chariot automoteur à quatre roues ; 9 – mise sous vide ; 10 – chambre de chargement et de déchargement des moules (c'est-à-dire les moules de coulée) ;
11 – chariot pour introduire les moules (moules) dans les chambres de chargement et de fusion-coulée et en retirer les moules remplis ; 12 – boîtier de la chambre de charge ; 13 – panier payant ;
14 – treuil pour abaisser et relever le panier pour la charge
La charge est chargée dans le creuset à l'aide de la chambre de charge 3, qui est une enveloppe cylindrique 12, à l'intérieur de laquelle un panier 13 pour la charge est suspendu à un câble. Le panier contenant la charge chargée est descendu dans le creuset à l'aide d'un treuil 14, après quoi le fond du panier s'ouvre et la charge est versée dans le creuset. La chambre de charge 3 est montée sur une colonne rotative 4, ce qui permet à la chambre 3 d'être déplacée sur le côté pour faciliter le chargement du panier 13 avec une nouvelle portion de charge à l'intérieur. La chambre 3 est séparée de la vanne d'arrêt par un obturateur technologique de vide et reliée au système de vide. Cela permet à la charge d'être chargée dans le creuset sans briser le vide dans la valve scellée.
Le distributeur 6 est conçu pour introduire divers additifs solides dans le creuset lors de la fusion. La chambre de distribution comporte plusieurs sections dans lesquelles les matériaux de remplissage requis sont chargés. Ils sont transférés du distributeur au creuset par une louche rotative spéciale à fond articulé. Tout comme la chambre de charge 3, le distributeur 6 est séparé du SCP par un joint sous vide.
Une chambre de 10 moules est reliée au SCP. Il est séparé de l'atelier et de la salle de contrôle par des vannes à vide technologiques 9 et relié au système de vide. L'alimentation des moules dans la chambre de moulage, puis dans la vanne d'arrêt, s'effectue sur un chariot 11. Par conséquent, la chambre de moule avec volets à vide fait office de chambre d'écluse, assurant le maintien du vide dans la chambre de fermeture. valve lors du remplacement des moules. La coulée du métal liquide dans les moules se fait en inclinant le creuset à l'aide d'un entraînement électrique. La pression résiduelle dans le four est de 0,6 à 0,7 Pa. Le four est alimenté par une source de thyristors.
Production et fourniture de fours à induction sous vide en Russie et dans les pays de la CEI
Actuellement, la demande d’acier et d’alliages spéciaux pour les secteurs de l’aérospatiale, de l’aviation, du nucléaire et de la production d’électricité augmente rapidement. Dans ces domaines industriels, des valeurs de plus en plus élevées en matière de résistance, de pureté et d'autres propriétés du métal sont souvent requises.
Afin de résoudre le problème de l'amélioration des propriétés qualitatives des métaux fondus, la société MetaCube est prête à proposer des technologies basées sur des méthodes de fusion innovantes pour la production d'aciers et d'alliages aux propriétés technologiques particulières. Ces méthodes incluent la fusion par induction sous vide.
La nécessité de créer des fours à induction sous vide est née de la nécessité d'introduire production industrielle les métaux hautement réactifs et réfractaires, tels que le zirconium, le titane, le niobium, le béryllium et le molybdène, ainsi que le tantale, le tungstène, l'uranium et plusieurs autres. Une particularité de ces métaux est qu'ils s'oxydent intensément lorsqu'ils sont chauffés à l'air et que la fusion doit donc être effectuée sous vide.
Caractéristiques des fours à induction sous vide
La technologie de fusion par induction sous vide permet d'obtenir des métaux hautement purifiés dans une atmosphère sans oxygène. En utilisant des fours à induction sous vide, il est possible de produire des aciers résistants à la chaleur et fortement alliés ainsi que des alliages de précision. Également dans les fours à induction sous vide, il est possible d'effectuer un traitement thermique et une fusion de métaux précieux et métaux des terres rares, ainsi que la fusion de verres spéciaux de haute qualité et leur utilisation pour obtenir des monocristaux. Dans tous les cas, le matériau obtenu dans les fours sous vide se distingue par une pureté accrue et un minimum de déchets.
Un rôle important lors du raffinage dans un four à induction sous vide est joué par le processus d'évaporation des impuretés à faible point de fusion - plomb, arsenic, étain et bismuth. Haute qualité Le vide métallique est en partie assuré par la purification de l'alliage de ces impuretés, qui sont contenues en très petites quantités, ce qui rend impossible leur détermination même avec des méthodes analytiques avancées. Cela est nécessaire lorsque les exigences relatives au matériau sont assez élevées et que l'alliage spécial résultant doit répondre à certaines propriétés.
Un autre avantage des fours sous vide est la possibilité d'obtenir des structures métalliques monocristallines et à grains fins. Dans ce cas, les propriétés du matériau résultant peuvent être prédites.
Modèle | Volume du four, kg | puissance, kWt | Fréquence, kHz | Vide froid ultime, Pa | Consommation d'eau pour le refroidissement, m 3 /heure | Tension d'alimentation, V |
---|---|---|---|---|---|---|
VPI-10 | 10 | 50 | 2,5 | 6,67×10-3 | 5 | 380 |
VPI-25 | 25 | 100 | 2,5 | 6,67×10-3 | 5 | 380 |
VPI-50 | 50 | 100 | 2,5 | 6,67×10-3 | 7 | 380 |
VPI-150 | 150 | 100 | 2,5 | 6,67×10-3 | 13 | 380 |
La température de fonctionnement des fours peut atteindre 2 200 degrés.
- Possibilité de pose longue métal liquide dans un vide profond ;
- Haut degré de dégazage des métaux ;
- Possibilité de recharger le four pendant le processus de fusion ;
- La capacité d'influencer activement l'intensification des processus de désoxydation et de raffinage à tout moment pendant la fusion ;
- La capacité de contrôler et de réguler efficacement l'état de la matière fondue par sa température et sa composition chimique tout au long du processus ;
- Pureté particulière des pièces moulées résultantes en raison de l'absence de toute inclusion non métallique ;
- La capacité de produire un chauffage rapide (chauffage direct dû à la chaleur générée dans la masse fondue), augmentant ainsi la productivité ;
- Haute homogénéité de la masse fondue grâce au mélange actif du métal ;
- Toute forme de matières premières (matières grumeleuses, briquettes, poudre, etc.)
- Haute efficacité et respect de l'environnement.
Conception de fours sous vide
est un four à haute fréquence constitué d'un creuset réfractaire, placé à l'intérieur d'un inducteur, lui-même situé à l'intérieur d'un boîtier étanche, à partir duquel Les pompes à vide les gaz sont pompés. Le creuset des fours sous vide est fabriqué à partir de matériaux hautement réfractaires en poudre par conditionnement dans un inducteur selon un gabarit. Les fours à induction sous vide sont des unités mécanisées. La coulée du métal peut se produire soit en faisant tourner le four à l'intérieur de la chambre, soit en faisant tourner la chambre elle-même dans son ensemble. Un four de fusion à induction sous vide vous permet d'effectuer de manière indépendante les opérations suivantes : régler la température de la masse fondue, modifier la pression à l'intérieur de la chambre, mélanger la masse fondue et également ajouter d'autres éléments à la masse fondue.
Le principe modulaire de construction des fours sous vide permet d'obtenir une compacité accrue du four, ainsi que la possibilité de connecter des modules supplémentaires - une chambre pour le déchargement, le versement et également le retrait des produits obtenus.
La conception des fours à induction sous vide modernes permet d'installer des moules et d'en décharger des lingots sans rompre le vide dans le four. Les fours à induction sous vide sont le plus souvent des appareils automatisés. Le chargement de la charge, l'introduction d'additifs et d'additifs et la coulée du métal s'effectuent à l'aide d'un entraînement électrique ou hydraulique.
Acheter un four à induction sous vide à petit prix - MetaCube Company
La société MetaCube est prête à vous proposer large choix fours à induction sous vide à bas prix avec livraison et mise en service dans toute la Russie et les pays de la CEI. Notre société possède une vaste expérience dans la fourniture de divers équipements métallurgiques aux entreprises de Russie, du Kazakhstan, de Biélorussie et d'autres pays de la CEI.
La fusion dans un four à induction sous vide permet de résoudre plusieurs problèmes liés à la production d'alliages complexes. Premièrement, lors de la fusion sous vide, en utilisant la désoxydation au carbone et l'augmentation de la température, il est possible de détruire le film d'oxyde à la surface du bain et de fondre et couler les alliages avec un miroir propre. Deuxièmement, la stabilité est assurée composition chimique alliages de chaleur en chaleur et, par conséquent, un niveau constant de propriétés mécaniques. Par exemple, la teneur en aluminium et en titane peut être contrôlée avec une précision de ±0,12 %, tandis qu'en fusion ouverte, avec une précision de 1 %.
Troisièmement, après fusion sous vide, la pureté des alliages augmente considérablement. Par exemple, dans l'alliage de nickel résistant à la chaleur R235 (0,15 % C ; 15,5 % Cr ; 5,3 % Mo ; 10 % Fe ; 2,0 % Ti ; 3,0 % Al) à base de nickel par rapport à la fusion, dans l'air, la teneur en oxygène a diminué de 0,017 à 0,0025 %, azote de 0,004 à 0,002 %, hydrogène de 0,0006 à 0,00005 %. Dans l'alliage Wespalloy (0,07 % C ; 0,4 % Si ; 0,7 % Mn ; 19 % Cr ; 14 % Co ; 4,3 % Mo ; 3,0 % Ti ; 1,3 % Al ; Ni - reste), la teneur en oxygène après fusion sous vide a diminué à 0,0012 % ; azote jusqu'à 0,012 %, hydrogène jusqu'à 0,00025 %.
En figue. 113 montre l'effet de l'azote sur les propriétés de l'alliage résistant à la chaleur ZhS6K- Comme le montre la Fig. DE, pour cet alliage, il est nécessaire d'obtenir une teneur optimale en azote. L'azote a évidemment un effet modificateur sur la structure de l'alliage. L'oxygène dans les alliages résistants à la chaleur a un effet négatif sur les propriétés de résistance à la chaleur, comme le montre clairement la figure. 114, qui montre la dépendance du temps de destruction de l'alliage Udimet-500 sous charge sur la concentration en oxygène.
Les propriétés des alliages Kh20N80 et Kh15N60, fondus en VIP, sont fortement influencées par l'additif REM. Dans le vide, la quantité de métaux des terres rares peut être considérablement réduite. La plupart bons résultats a été obtenu en dopant l'alliage avec 0,10 à 0,15 % de cérium et 1,4 % de silicium ou 0,05 à 0,08 % de cérium et 0,05 à 0,08 % de lanthane. Grâce à l'augmentation de la pureté du métal, la teneur en azote était de 0,007 % ; oxygène 0,001%.
Après VIP, la capacité de survie de l'alliage Kh20N80 est passée de 40 à 70 heures et, en raison d'un alliage supplémentaire de métaux de terres rares sous vide, de 70 à 150-250 heures (96 % de toutes les fusions). La capacité de survie de l'alliage X15N60, moins allié que le X20N80, a dépassé 100 heures. Les propriétés électriques ont également augmenté. Ainsi, pour l'alliage X20N80, la résistivité électrique a augmenté en moyenne de 1,1 à 1,18 Ohm mm2/m. Lorsqu'il est chauffé dans un matériau sous vide, une modification de la résistance électrique de 3 à 8 % se produit en 200 à 400 heures, alors que dans un alliage conventionnel, cela prend 40 à 60 heures.
Selon les auteurs de cet ouvrage, influence positive L'utilisation du cérium dans le VIP réside dans son effet sur la formation de sulfures. Le cérium favorise l'élimination des sulfures en formant des sulfures résistants et réfractaires qui flottent avant ou pendant la cristallisation précoce. La présence de cérium réduit la probabilité de formation de sulfures d'autres éléments, comme le titane, si ce dernier est contenu dans le métal. Le magnésium a un effet similaire sur le soufre.
Lors de la fusion sous vide d'alliages résistants à la chaleur dans un four à induction, une évaporation importante d'impuretés de métaux non ferreux se produit. Cette méthode fournit l’un des niveaux les plus faibles de ces impuretés par rapport aux autres méthodes. Ainsi, pour l'acier à haute résistance, selon Chuprin, la teneur en impuretés de métaux non ferreux, en fonction du procédé de fusion, est caractérisée par les données indiquées dans le tableau. 37.
Tableau 37 TENEUR EN IMPURETÉS DE MÉTAUX NON FERREUX DANS L'ACIER À HAUTE RÉSISTANCE
fusion à l'air |
|||||
Avec l'augmentation de la durée d'exposition du métal liquide sous vide, la teneur en impuretés de métaux non ferreux diminue et propriétés mécaniques les alliages augmentent, comme le montre la Fig. 115.
Mais le simple raffinage d'un métal à partir d'impuretés n'améliore pas toujours ses propriétés.
Ainsi, selon K. Ya Shpunt, pour les alliages résistants à la chaleur, en plus du raffinage sous vide, grande importance a une teneur résiduelle en éléments modificateurs magnésium et cérium.
Grâce à la fusion sous vide, les propriétés mécaniques des alliages résistants à la chaleur sont considérablement augmentées. Un exemple est l’amélioration des propriétés d’un alliage résistant à la chaleur fondu dans un four à induction sous vide.
La fusion dans un four à induction sous vide augmente la malléabilité des alliages de cobalt et permet de traiter des alliages habituellement indéformables. Les propriétés des alliages moulés et des pièces moulées de précision telles que les aubes, les soupapes, les rotors de turbine, les guides et autres pièces de moteurs à réaction sont améliorées.
La fusion sous vide permet d'augmenter les propriétés mécaniques des alliages résistants à la chaleur grâce à la complexité de la composition, c'est-à-dire l'introduction de nouveaux composants d'alliage et une augmentation de la teneur en composants de renforcement. Lors d'une fusion conventionnelle à l'air, une augmentation de la teneur en titane, aluminium, molybdène ou d'une composition plus complexe entraîne une diminution des propriétés de résistance à la chaleur.
Effondrement
Un four à induction est un appareil de four utilisé pour fondre des métaux non ferreux (bronze, aluminium, cuivre, or et autres) et ferreux (fonte, acier et autres) grâce au fonctionnement d'un inducteur. Un courant est produit dans le champ de son inducteur, il chauffe le métal et le porte à l'état fondu.
Il sera d’abord affecté par un champ électromagnétique, puis par un courant électrique, puis il passera par l’étape thermique. Conception simple Un tel dispositif de poêle peut être assemblé indépendamment à partir de divers matériaux disponibles.
Principe d'opération
Ce dispositif de four est transformateur électrique avec un enroulement secondaire en court-circuit. Le principe de fonctionnement d'un four à induction est le suivant :
- à l'aide d'un générateur, un courant alternatif est créé dans l'inducteur ;
- une inductance avec un condensateur crée un circuit oscillatoire, elle est réglée sur la fréquence de fonctionnement ;
- dans le cas de l'utilisation d'un générateur auto-oscillant, le condensateur est exclu du circuit du dispositif et dans ce cas, la capacité de réserve propre de l'inducteur est utilisée ;
- Le champ magnétique créé par l'inducteur peut exister dans espace libre ou être fermé à l'aide d'un noyau ferromagnétique individuel ;
- le champ magnétique agit sur la pièce métallique ou la charge située dans l'inducteur et forme un flux magnétique ;
- selon les équations de Maxwell, il induit un courant secondaire dans la pièce ;
- avec du solide et du massif Flux magnétique le courant généré est fermé dans la pièce et un courant de Foucault ou courant de Foucault est créé ;
- après la formation d'un tel courant, la loi Joule-Lenz entre en vigueur, et le résultat obtenu à l'aide d'une inductance et champ magnétique l'énergie chauffe la billette ou la charge métallique.
Malgré travail en plusieurs étapes, le dispositif d'un four à induction peut produire jusqu'à 100 % d'efficacité sous vide ou dans l'air. Si le milieu a une perméabilité magnétique, alors cet indicateur augmentera ; dans le cas d'un milieu constitué d'un diélectrique non idéal, il diminuera.
Appareil
Le four en question est une sorte de transformateur, mais il ne possède pas d'enroulement secondaire ; il est remplacé par un échantillon de métal placé dans l'inducteur. Il conduira le courant, mais les diélectriques ne chauffent pas dans ce processus, ils restent froids.
La conception des fours à creuset à induction comprend un inducteur composé de plusieurs tours tube en cuivre, enroulé sous la forme d'un serpentin, le liquide de refroidissement se déplace constamment à l'intérieur. L'inducteur contient également un creuset, qui peut être constitué de graphite, d'acier et d'autres matériaux.
En plus de l'inducteur, le four possède un noyau magnétique et une pierre de foyer, tous enfermés dans le corps du four. Il comprend:

Dans les modèles de fours haute puissance Le boîtier de la baignoire est généralement assez rigide, il n'y a donc pas de cadre dans un tel appareil. La fixation du boîtier doit résister à de fortes charges lorsque l'ensemble du four est incliné. La charpente est le plus souvent constituée de poutres profilées en acier.
Un four à induction à creuset pour la fusion du métal est installé sur une fondation dans laquelle sont montés les axes du mécanisme de basculement de l'appareil reposant sur leurs roulements.
Le boîtier de la baignoire est fabriqué à partir de Tôles, sur lesquels des raidisseurs sont soudés pour plus de solidité.
Le boîtier de l'unité d'induction sert de lien de connexion entre le transformateur du four et la pierre du foyer. Pour réduire les pertes de courant, il est composé de deux moitiés entre lesquelles se trouve un joint isolant.
Les moitiés sont reliées à l'aide de boulons, de rondelles et de bagues. Un tel boîtier est fabriqué en fonte ou soudé ; lors du choix d'un matériau, la préférence est donnée aux alliages non magnétiques. Le four de fabrication d'acier à induction à deux chambres est livré avec un boîtier commun pour le bain et l'unité d'induction.
DANS petits fours, dans lequel le refroidissement par eau n'est pas assuré, il y a unité de ventilation, cela aide à éliminer l’excès de chaleur de l’appareil. Même si vous installez un inducteur refroidi à l'eau, vous devez aérer l'ouverture proche de la pierre du foyer afin qu'elle ne surchauffe pas.
Les installations de four modernes disposent non seulement d'un inducteur refroidi à l'eau, mais fournissent également eau froide boîtiers. Des ventilateurs alimentés par un moteur d’entraînement peuvent être installés sur le châssis du four. Compte tenu de la masse importante d'un tel dispositif, dispositif de ventilation installé à proximité du poêle. Si un four à induction pour la production d'acier est livré avec une version amovible des unités à induction, chacune d'entre elles est équipée de son propre ventilateur.
Par ailleurs, il convient de noter le mécanisme d'inclinaison, qui pour les petits fours est livré avec un entraînement manuel, et pour les grands, il est équipé d'un entraînement hydraulique situé au niveau du bec de vidange. Quel que soit le mécanisme d'inclinaison installé, il doit garantir que tout le contenu de la salle de bain soit complètement vidé.
Calcul de puissance
Étant donné que la méthode de fusion de l'acier par induction est moins coûteuse que des méthodes similaires basées sur l'utilisation de fioul, de charbon et d'autres sources d'énergie, le calcul d'un four à induction commence par le calcul de la puissance de l'unité.
La puissance d'un four à induction est divisée en active et utile, chacune d'elles a sa propre formule.
Comme données initiales, vous devez savoir :
- la capacité du four, dans le cas considéré par exemple, est de 8 tonnes ;
- puissance unitaire (sa valeur maximale est prise) – 1300 kW;
- fréquence actuelle – 50 Hz ;
- La productivité de l'usine de four est de 6 tonnes par heure.
Il faut également tenir compte du métal ou de l'alliage en cours de fusion : selon les conditions, il s'agit du zinc. Ce point important, le bilan thermique de la fonte fondant dans un four à induction, ainsi que celui d'autres alliages, est différent.
Puissance utile transférée au métal liquide :
- Рpol = Wthéor×t×P,
- Wtheor – consommation spécifique l'énergie, elle est théorique, et montre une surchauffe du métal de 1 0 C ;
- P – productivité de l'installation du four, t/h ;
- t est la température de surchauffe de l'alliage ou de la billette métallique dans le bain du four, 0 C
- Rpol = 0,298×800×5,5 = 1430,4 kW.
Puissance active :
- P = Ppol/Yuterm,
- Rpol – tiré de la formule précédente, kW ;
- Yuterm est le rendement d'un four de fonderie, ses limites sont de 0,7 à 0,85, avec une moyenne de 0,76.
- P = 1311,2/0,76 = 1892,1 kW, la valeur est arrondie à 1900 kW.
Sur étape finale La puissance de l'inducteur est calculée :
- Croûte = P/N,
- R- puissance active installation de four, kW ;
- N est le nombre d'inducteurs prévus sur le four.
- Croûte =1900/2= 950 kW.
La consommation électrique d'un four à induction lors de la fusion de l'acier dépend de ses performances et du type d'inducteur.
Espèces et sous-espèces
Les fours à induction sont divisés en deux types principaux :

En plus de cette division, les fours à induction sont à compresseur, sous vide, ouverts et à gaz.
Fours à induction bricolage
Parmi les méthodes courantes disponibles pour créer de telles unités, on trouve guide étape par étape comment faire un four à induction à partir de inverseur de soudage, avec des pinceaux en spirale nichrome ou en graphite, nous vous présentons leurs caractéristiques.
Groupe générateur haute fréquence
Elle est réalisée en tenant compte de la puissance nominale de l'unité, des pertes de Foucault et des fuites par hystérésis. La structure sera alimentée par un réseau classique de 220 V, mais à l'aide d'un redresseur. Ce type de four peut être équipé de brosses en graphite ou d'une spirale en nichrome.
Pour créer un four, vous aurez besoin de :
- deux diodes UF4007 ;
- condensateurs à film;
- transistors à effet de champ, deux pièces ;
- Résistance de 470 ohms ;
- deux bagues d'accélérateur, elles peuvent être retirées d'un ancien technicien informatique ;
- fil de cuivre Ø section 2 mm.
Les outils utilisés sont un fer à souder et des pinces.
Voici un schéma pour un four à induction :
Les fours de fusion portables à induction de ce type sont créés dans l'ordre suivant :
- Les transistors sont situés sur les radiateurs. Étant donné que pendant le processus de fusion du métal, le circuit de l'appareil chauffe rapidement, le radiateur correspondant doit être sélectionné avec des paramètres élevés. Il est permis d'installer plusieurs transistors sur un générateur, mais dans ce cas, ils doivent être isolés du métal à l'aide de joints en plastique et en caoutchouc.
- Deux starters sont fabriqués. Pour eux, on prend deux anneaux préalablement retirés de l'ordinateur, du fil de cuivre est enroulé autour d'eux, le nombre de tours est limité de 7 à 15.
- Les condensateurs sont combinés dans une batterie pour produire une capacité de 4,7 μF en sortie ; ils sont connectés en parallèle.
- S'enroule autour de l'inducteur fil de cuivre, son diamètre doit être de 2 mm. Le diamètre intérieur du bobinage doit correspondre à la taille du creuset utilisé pour le four. Au total, 7 à 8 tours sont effectués et les extrémités longues sont laissées pour pouvoir être connectées au circuit.
- En tant que source de circuit assemblé Une batterie de 12 V est connectée ; elle dure environ 40 minutes de fonctionnement du four.
Si nécessaire, le boîtier est constitué d'un matériau à haute résistance à la chaleur. Si un four de fusion par induction est fabriqué à partir d'un inverseur de soudage, alors boîtier de protection doit être présent, mais il doit être fondé.
Conception de pinceau en graphite
Un tel four est utilisé pour fondre n'importe quel métal et alliage.
Pour créer un appareil, vous devez préparer :
- pinceaux en graphite;
- granit en poudre;
- transformateur;
- brique en argile réfractaire;
- fil d'acier;
- aluminium fin.
La technologie d'assemblage de la structure est la suivante :

Appareil avec spirale nichrome
Un tel appareil est utilisé pour fondre de gros volumes de métal.
Comme Fournitures pour arrangement poêle fait maison utilisé:
- nichrome;
- fil d'amiante;
- morceau de tuyau en céramique.
Après avoir connecté tous les composants du four selon le schéma, son fonctionnement est le suivant : après alimentation courant électrique sur une spirale en nichrome, il transfère la chaleur au métal et le fait fondre.
La création d'un tel four s'effectue dans l'ordre suivant :

Cette conception se caractérise par des performances élevées ; elle refroidit longtemps et chauffe rapidement. Mais il ne faut pas oublier que si la spirale est mal isolée, elle grillera rapidement.
Prix des fours à induction prêts à l'emploi
Les conceptions de poêles faites maison coûteront beaucoup moins cher que celles achetées, mais elles ne peuvent pas être créées en grands volumes, donc sans options prêtes à l'emploi pour la production en série de la masse fondue est indispensable.
Les prix des fours à induction pour la fusion des métaux dépendent de leur capacité et de leur configuration.
Modèle | Caractéristiques et fonctionnalités | Prix, roubles |
INDUTHERM MU-200 ![]() |
Le four prend en charge 16 programmes de température, la température de chauffage maximale est de 1400 0C, le mode est contrôlé par un thermocouple de type S. L'unité produit une puissance de 3,5 kW. | 820 mille |
INDUTHERM MU-900 ![]() |
Le four fonctionne à partir d'une alimentation de 380 W, contrôle de la température se produit à l'aide d'un thermocouple de type S et peut atteindre jusqu'à 1 500 0C. Puissance – 15 kW. | 1,7 millions |
UPI-60-2 |
Ce mini four de fusion à induction peut être utilisé pour fondre des métaux non ferreux et précieux. Les pièces sont chargées dans un creuset en graphite et chauffées selon le principe du transformateur. | 125 mille |
IST-1/0,8 M5 ![]() |
L'inducteur du four est un panier dans lequel un circuit magnétique est construit avec une bobine. Unité 1 tonne. | 1,7 millions |
UI-25P ![]() |
Le dispositif de four est conçu pour une charge de 20 kg, il est équipé d'une inclinaison à engrenages de l'unité de fusion. Le poêle est livré avec un bloc de batteries de condensateurs. Puissance d'installation – 25 kW. Le chauffage maximum t est de 1600 0C. | 470 mille |
UI-0.50T-400 ![]() |
L'unité est conçue pour une charge de 500 kg, la puissance la plus élevée de l'installation est de 525 kW, sa tension doit être d'au moins 380 W, la température maximale de fonctionnement est de 1850 0C. | 900 mille |
ST10 ![]() |
Cuire entreprise italienneéquipé d'un thermostat numérique, le panneau de commande intègre la technologie SMD, à action rapide. L'unité universelle peut fonctionner avec différentes capacités de 1 à 3 kg, pour cela elle n'a pas besoin d'être réajustée. Il est destiné aux métaux précieux, sa température maximale est de 1250 0C. | 1 million |
ST12 ![]() |
Four à induction statique avec thermostat numérique. Il peut être complété par une chambre de coulée sous vide, qui permet d'effectuer la coulée juste à côté de l'installation. Le contrôle s'effectue à l'aide de l'écran tactile. Température maximale– 1250 0С. | 1050 mille |
IChT-10TN | Le four est conçu pour une charge de 10 tonnes, c'est une unité assez grande, et pour son installation il faut prévoir un atelier fermé. | 8,9 millions |