Stratégies de maintenance et moyens d'augmenter l'efficacité des travaux de réparation. Amélioration des services de production
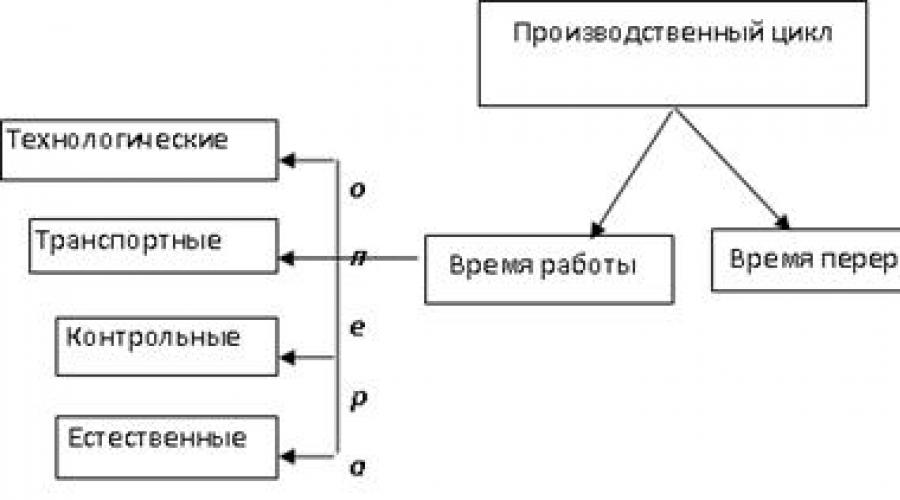
100 roubles bonus pour la première commande
Sélectionnez le type de travail Travail d'études supérieures Cours Résumé Mémoire de maîtrise Rapport sur la pratique Article Rapport Révision Test Monographie Résolution de problèmes Plan d'affaires Réponses aux questions Travail créatif Essai Dessin Compositions Traduction Présentations Dactylographie Autre Augmenter le caractère unique du texte thèse de doctorat Travaux de laboratoire Aide en ligne
Découvrez le prix
Les études menées montrent qu'après une refonte majeure de l'équipement, les cycles de révision ultérieurs sont considérablement réduits. Par exemple, un équipement âgé de 20 ans a un TBO 20 % plus court qu’un équipement âgé de 10 ans. Les coûts d'entretien de routine et de réparation des équipements au cours du deuxième cycle de révision augmentent en moyenne de 9 à 15 % par rapport au premier. À cet égard, trouver des moyens de résoudre ces deux problèmes est d’une importance capitale. les problèmes les plus importantséconomie de réparation du pays, telle que la spécialisation et la concentration de la réparation d'équipements, son transfert sur une base industrielle et la fourniture service de réparation des pièces de rechange.
L’industrie ne profite pas suffisamment de la spécialisation de la production de réparation. La réparation de presque tous les types d'équipements est effectuée dans les ateliers de réparation ou les ateliers des entreprises où ils sont exploités. Un seul type de production de réparation entraîne d'énormes coûts de main-d'œuvre pour la réparation des équipements. Des coûts élevés travail expliqué niveau faible mécanisation du travail des réparateurs, seulement 20 à 30 %, même dans les grandes fermes de réparation.
La réorganisation de l'activité de réparation sur la base de sa spécialisation permettra de passer à des méthodes industrielles de réalisation des opérations de réparation et ainsi d'augmenter le niveau technique de l'industrie de la réparation, libérant une partie des équipements et de la main d'œuvre concentrés dans le service de réparation. pour les besoins de la production principale. La spécialisation des réparations améliore la qualité des réparations, réduit le temps de réparation et réduit la consommation de matériaux. Sur cette base, les coûts de réparation d'une unité de réparation sont réduits.
La recherche et la pratique dans des usines spécialisées avancées indiquent qu'avec l'augmentation du nombre de machines monomodèles simultanément en réparation, l'intensité de travail de tous travaux de réparation est réduite par rapport à l’intensité de travail d’une seule production de réparation. Ainsi, lorsqu'un lot de machines réparées simultanément est porté à 10 unités, l'intensité de travail d'une unité de complexité de réparation est réduite de 20 % ; pour un lot de 20 unités - par 25, pour 50 unités - de 38 % et pour un lot de 100 unités - de 45 %. L'augmentation du nombre de lots de machines monomodèles réparées simultanément affecte également la réduction de l'intensité de travail des machines-outils, tant dans la fabrication de pièces neuves que dans la restauration d'anciennes pièces.
La première étape de spécialisation de la production de réparation est la création d'ateliers de réparation qui effectuent la réparation de certains types d'équipements. La seconde est la création d'usines de réparation, leur spécialisation dans la réparation et la modernisation de certains types de machines et d'unités et dans la fabrication de pièces de rechange pour des équipements d'un certain type. Ces usines peuvent être dotées d’une technologie avancée et utiliser des processus technologiques performants tant dans les opérations d’assemblage que dans la production de pièces de rechange et de composants.
Côté important organisation rationnelle les travaux de réparation consistent à leur fournir des pièces de rechange. La recherche montre que la durée de vie des équipements est de 15 à 25 ans et qu'un changement dans les modèles de production d'équipements se produit après 6 à 8 ans. Ainsi, l'équipement fonctionne dans l'entreprise pendant environ 3 à 4 cycles de réparation et sa réparation nécessite une énorme quantité de pièces de rechange.
La production de pièces de rechange pour leurs propres besoins par chaque entreprise nécessite séparément équipement supplémentaire et un espace de production supplémentaire qui ne peut pas être utilisé efficacement. Par exemple, le coefficient d'utilisation de la capacité de production des machines dans un atelier de réparation mécanique varie selon les types de machines et est de 0,2 à 0,5. Par conséquent, le coût de fabrication des pièces de rechange dans les usines de construction de machines est 3 à 5 fois plus élevé que dans les entreprises spécialisées.
Une façon de répondre aux besoins en pièces de rechange consiste à restaurer les pièces usées et à les réutiliser. Les recherches montrent qu'il est ainsi possible de satisfaire 20 à 25 % des besoins existants en pièces de rechange. En fait, une petite partie d'entre eux est restaurée et réutilisée, ce que confirment les résultats d'une enquête auprès des usines de construction de machines dans l'Oural. Malgré la diversité des méthodes de récupération, pour réutilisation En moyenne, environ 6 % des pièces usées sont restaurées dans les usines de construction de machines. Selon les scientifiques, il est économiquement réalisable de restaurer 25 à 30 % lors des réparations. Dans les meilleures usines de réparation automobile, le nombre de pièces restaurées atteint 60 à 70 %.
Le faible pourcentage de pièces réutilisées s'explique tout d'abord par le système décentralisé de réparation des équipements et de production de pièces détachées existant dans les entreprises. Dans ces conditions, il n'est pas toujours possible d'organiser une restauration rentable des pièces usées, car elle nécessite des connaissances particulières, certains équipements et une concentration importante des travaux de réparation.
À mesure que le niveau de concentration de la production augmente, la part des ressources matérielles réutilisées augmente. Ceci est prédéterminé par le meilleur équipement technique des services de réparation des grandes entreprises. C'est pourquoi il est conseillé de créer des zones et des services de restauration spéciaux dans les grandes entreprises. Nous avons besoin d’usines spécialisées qui restaureraient et renforceraient les pièces usées. Ils peuvent être placés dans de petites villes et des quartiers ouvriers qui ont aujourd'hui perdu de leur importance et dont la population est inoccupée. Tarif sera petit et de nombreuses pièces restaurées de manière moderne, 70 à 80 % moins cher. Il est conseillé de regrouper ces entreprises spécialisées en entreprises manufacturières. Les petits magasins de gros subordonnés directement aux entreprises manufacturières peuvent accepter les pièces usées et en délivrer des remises à neuf. De cette façon, vous pouvez économiser des centaines de milliers de tonnes de métal par an.
Lors de l'analyse des problèmes d'organisation et d'économie de l'industrie de la réparation dans le pays, il ne faut pas autoriser une approche stéréotypée pour les résoudre. Pour les grandes entreprises, associations de production les problèmes des installations de réparation sont résolus d'une manière, pour les petites et moyennes entreprises, d'une autre manière. Les décisions prises devraient assurer une augmentation de l'efficacité de la production principale, que le service de réparation de l'entreprise est appelé à entretenir.
L'analyse des installations de réparation de l'entreprise unitaire Polymerprom vise à identifier les réalisations et les lacunes dans ce domaine, en décrivant les moyens d'éliminer les lacunes et les mesures visant à améliorer le système de maintenance préventive de l'usine.
Les principales orientations pour l'amélioration des installations de réparation de l'entreprise unitaire Polymerprom sont :
1. Organisation de la réparation centralisée des équipements spécialisés. Cette condition est réalisable s'il existe un centre de service du fournisseur d'équipement, puisque plus de 70 % des équipements sont fabriqués à l'étranger.
2. Organisation d'une production spécialisée de pièces détachées pour équipements. Il semble possible, afin de réduire le coût de fabrication des pièces détachées des équipements et d'améliorer leur qualité, de rechercher par appel d'offres un (des) fabricant(s) parmi les entreprises de fabrication et de réparation de machines-outils capables de produire la gamme de pièces nécessaires aux réparations.
3. Poursuite de l'amélioration du système de maintenance préventive programmée des équipements de l'entreprise, qui assurera une supervision claire et une prévention rapide du fonctionnement de l'équipement, ce qui à son tour augmentera sa productivité et augmentera le temps entre les réparations.
4. Améliorer la préparation technique des réparations, y compris l'élaboration de normes processus technologiques, ainsi qu'un soutien matériel.
En raison de la petite taille de l'entreprise, le service de réparation de l'entreprise unitaire Polymerprom est également de taille limitée. Par conséquent, il semble correct de disposer d'un service de réparation centralisé opérationnel dans l'entreprise qui remplit toutes les fonctions d'entretien et de réparation des équipements.
Un système de paiement de primes au temps est appliqué aux employés des services de réparation. Cette forme de rémunération n'est pas assez efficace. La plupart forme efficace la rémunération est une forme contractuelle de rémunération avec l'établissement du montant des indemnités et primes en fonction de la présence de pannes d'équipement dues à la faute de l'employé du service de réparation, ainsi que de la présence de réclamations concernant le fonctionnement de l'équipement depuis le chantier gestionnaires.
Pour augmenter l'efficacité du service de réparation, il semble conseillé d'utiliser un système automatisé de gestion du service de réparation dans l'entreprise.
Il est également nécessaire d'utiliser largement les lignes directrices et recommandations nationales, les développements et les propositions des organismes de recherche et de conception.
Un système automatisé de gestion des services de réparation est un sous-système de gestion fonctionnel, lorsque, avec la division organisationnelle et administrative appropriée, le service du chef mécanicien est le principal centre de coordination et un lien nécessaire dans système intégré la gestion de l'entreprise. L'introduction de ce sous-système permet, grâce à l'utilisation d'ordinateurs et méthodes mathématiques déterminer la stratégie optimale d'entretien et de réparation des équipements, la concentration optimale des volumes de travail et la concentration des équipements pour les conditions de production spécialisée de travaux de réparation.
À l'aide d'un système automatisé de gestion des services de réparation, il est nécessaire de créer une telle organisation pour la réparation et la maintenance du parc de machines des entreprises dans laquelle l'utilisation de la main-d'œuvre, des ressources matérielles et financières serait optimale et les temps d'arrêt des équipements seraient minimal.
Sur la base des données d'une enquête sur le travail des services de réparation, un modèle économique et organisationnel de gestion de la production de réparation est développé, des formes unifiées de documents sont élaborées, un organigramme de flux de documents est construit et un modèle de communication de l'information est développé, économique et mathématique. les méthodes et modèles de mécanisation et d'automatisation des calculs économiques sont sélectionnés et développés, la quantité requise est déterminée et la composition des moyens techniques. Le modèle économique et organisationnel constitue la base du sous-système créé de production de réparation, détermine les principes de son fonctionnement et les fondements organisationnels du système de gestion, et prend également en compte la nécessité d'un développement généralisé de relations d'autosuffisance, plus utilisation complète principes d’incitations matérielles.
Lors de la conception d'un système de gestion automatisé des services de réparation, il est nécessaire de développer un ensemble de travaux interconnectés pour résoudre les principaux problèmes de la production de réparation. Cet ensemble de travaux se concentre sur la création de sous-systèmes de contrôle fonctionnels et des sous-systèmes de support nécessaires à leur fonctionnement.
Les sous-systèmes fonctionnels mettent en œuvre des fonctions de gestion pour la préparation organisationnelle et technique de la production de réparation, la prévision et la planification à long terme, la planification technique, économique et opérationnelle, la comptabilité, le reporting et l'analyse des activités économiques, ainsi que le contrôle et la régulation du travail des services de réparation.
Les sous-systèmes de support comprennent : le sous-système de support économique-organisationnel, informationnel, mathématique et technique. La fonction principale des sous-systèmes de support est de transformer toutes les informations circulant entre les sous-systèmes fonctionnels et les services de production pour développer une influence de contrôle sur les services de production du service de mécanique en chef.
Le développement d'un système de contrôle automatisé pour le service de réparation de l'entreprise unitaire Polymerprom doit être réalisé par des organismes spécialisés avec la participation de l'entreprise cliente ou par les entreprises s'il existe un nombre suffisant de spécialistes.
Lors de la conception d'un sous-système d'un système de gestion automatisé des services de réparation, il est nécessaire Attention particulière faites attention aux travaux suivants :
1. Création d'une comptabilité automatisée du parc d'équipements disponible par sections et par l'entreprise dans son ensemble ; utilisation des équipements de production en termes de temps et de puissance ; comptabilisation des temps d'arrêt des équipements lors des réparations ; pannes et dysfonctionnements de chaque équipement et unités individuelles, blocs, pièces ; besoins, disponibilité et mouvement des pièces de rechange pour le parc d'équipements existant.
Automatisation des calculs planifiés dans des conditions de travail sur un système préventif planifié basé sur l'utilisation de la technologie informatique moderne, des méthodes mathématiques appliquées et des normes progressives pour les coûts des matériaux et de la main-d'œuvre.
Organisation de la lubrification réglementée des équipements.
Déterminer le moment optimal pour remplacer les équipements usés en fonction du degré de leur dépréciation et des coûts d'entretien de réparation nécessaires.
Le succès du système de gestion automatisé des services de réparation dépend de la manière dont les étapes de travail suivantes sont effectuées de manière complète et précise : développement dispositions générales; inspection avant-projet (diagnostic) du travail des services de réparation ; conception technique; conception détaillée; mise en œuvre du sous-système.
La production de réparation se caractérise par un certain nombre de spécificités qui compliquent le processus de gestion et l'organisation rationnelle des composants structurels (services de réparation). Ces caractéristiques incluent tout d'abord l'hétérogénéité des travaux de réparation.
La justification économique de la faisabilité de l'introduction d'un système de gestion automatisé des services de réparation doit être accompagnée d'un calcul d'efficacité économique.
Les ateliers de réparation mécanique et les services de réparation en atelier doivent être aussi spécialisés que possible, équipés d'équipements modernes permettant l'utilisation de technologies de pointe, de formes avancées d'organisation de la production, de moyens de mécanisation et d'automatisation des processus de production.
La performance des équipes de réparation est assurée par la bonne répartition du travail entre les membres de l'équipe, l'organisation efficace des postes de travail, l'utilisation de méthodes progressives d'organisation des réparations et l'organisation précise des lieux de travail d'entretien.
Une réserve importante pour réduire les coûts de réparation et les temps d'arrêt des équipements lors des réparations est la réutilisation des pièces.
La restauration de pièces vous permet de réduire jusqu'à 60 à 90 % la consommation de ressources matérielles et financières lors de la réparation de pièces. Le coût des pièces reconditionnées représente souvent 10 à 25 % du coût d’une pièce neuve.
Conclusion
Lors de l'exécution de travaux de réparation dans des entreprises industrielles, il est nécessaire de s'efforcer d'obtenir la concentration maximale de travaux similaires dans certaines zones de production des services de réparation. Ils doivent être créés et équipés en pleine conformité avec les tâches qui leur sont assignées et l'étendue des travaux à effectuer.
Les principales orientations pour améliorer le service de réparation de l'entreprise sont :
Organisation de la réparation centralisée des équipements spécialisés ;
Organisation de production spécialisée de pièces détachées pour équipements ;
Poursuite de l'amélioration du système de maintenance préventive programmée des équipements ;
Améliorer la préparation technique des réparations, y compris le développement de processus technologiques standards, ainsi que le support matériel pour les travaux de réparation ;
Améliorer la planification, notamment en établissant des calendriers de travaux de réparation.
L'organisation des installations de réparation dans les entreprises est améliorée dans les domaines suivants.
Les services de réparation de l'entreprise doivent être aussi spécialisés que possible, dotés de technologies modernes ou permettant l'utilisation de technologies progressistes, de formes avancées d'organisation de la production, de moyens de mécanisation et d'automatisation des processus de production.
Le moyen le plus efficace consiste à faire appel à des équipes de réparation spécialisées. Parallèlement, il convient de créer des équipes complexes qui réalisent tous les travaux de maintenance technique et de réparation des équipements du site de production attribué à l'équipe.
Parmi les méthodes progressives de réparation, la réparation ganglionnaire est tout d'abord incluse. L'essence de la méthode est que les composants et mécanismes nécessitant une réparation sont retirés et remplacés par des neufs ou par des composants déjà réparés. L'utilisation de cette méthode permet de réduire au minimum les temps d'arrêt des équipements lors des réparations, d'améliorer la qualité des réparations et de réduire les coûts de réparation grâce à la possibilité d'une organisation la plus rationnelle des réparations des composants et des mécanismes.
En outre, la réutilisation des pièces constitue une réserve importante pour réduire les coûts de réparation et les temps d'arrêt des équipements lors des réparations.
Liste de la littérature utilisée :
1. Bakanov M.I., Sherimet A.D. Théorie de l'analyse économique. – M. : Finances et Statistiques, 2011.
2. Latfullin, G.R. Théorie des organisations : manuel pour les universités / G. R. Latfullin, A. V. Raichenko - Saint-Pétersbourg : Peter, 2007.
3. Milner, B.Z. Théorie des organisations : manuel / B. Z. Milner - M. : INFRA-M, 2008.
4. Tertyshnik, Mikhaïl Ivanovitch Économie d'entreprise : Didacticiel pour les étudiants de l'enseignement supérieur les établissements d'enseignementétudiants étudiant dans la spécialité 080101 « Théorie économique » (numéro d'enregistrement de la revue 404 du 03/07/2009, Entreprise unitaire d'État de Moscou) / M. I. Tertyshnik ; État du Baïkal Université d'économie et de droit. - 2e éd. - Moscou : INFRA-M, 2010.
5. Sergueïev I.V. Économie d'entreprise. – M. : Finances et Statistiques, 2013.
6. Analyse des activités économiques des organisations : manuel / édité par. éd. D.A. Pankova, E.A. Golovkova. - 2e éd., rév. - M. : Nouveaux savoirs, 2013.
7. Organisation de la production dans une entreprise (firme) : manuel. manuel / éd. : O. I. Volkov, O. V. Devyatkina - M. : INFRA-M, 2010.
8. Économie d'entreprise : manuel. pour les universités en économie. spécialiste. / [DANS. Y. Gorfinkel et autres] ; édité par V. Ya. Gorfinkel, V. A. Shvandar. - 4e éd. - Moscou : UNITY-DANA, 2014.
9. Économie d'entreprise (en diagrammes, tableaux, calculs) : un manuel pour les étudiants qui étudient dans la direction 521600 « Économie » / V.K. Sklyarenko [etc.] ; édité par V. K. Sklyarenko, V. M. Prudnikova. - Moscou : INFRA-M, 2010.
10. Économie d'une entreprise (entreprise) : un manuel destiné aux étudiants des établissements d'enseignement supérieur étudiant l'économie. spécialités / [O. I. Volkov et autres] ; édité par O. I. Volkova, O. V. Devyatkina; Ross. éco. acad. eux. G. V. Plekhanov. - 3e éd., révisée. et supplémentaire - Moscou : INFRA-M, 2009.
3. Principales orientations pour améliorer les services de réparation et d'inter-réparation
3.1 Réorganisation de la structure de gestion des équipes de réparation équipement technologique
Pour la mise en œuvre la plus réussie et la plus économique des tâches assignées au service de réparation de l'entreprise, il est nécessaire de développer une structure et un schéma de gestion rationnels. Lors de l'élaboration d'un plan de gestion des installations de réparation d'une entreprise, il convient de prendre en compte les technologie moderne gestion, style général travail, ainsi qu'un certain nombre d'autres facteurs dont dépend l'organisation de la gestion des réparations.
1. Les initiateurs de la majorité des travaux de maintenance imprévus des équipements étant le personnel de maintenance, leur travail prédétermine un mode spécifique de gestion des équipes, c'est-à-dire qu'il ne nécessite pas de supervision directe, mais nécessite uniquement une administration (décision de l'assemblée générale problèmes d'organisation, enregistrement des activités réalisées et des travaux effectués) et organisation de l'approvisionnement (pièces de rechange, composants et consommables), ce qui détermine l'inefficacité d'avoir trois managers dans la structure, dont les responsabilités sont essentiellement identiques.
2. Le chargement incomplet de l'équipement lors du travail en deuxième équipe (le rapport moyen de changement d'équipement est de 1,45), réduit le travail du personnel de maintenance en mode veille et effectue une petite partie des activités de maintenance de l'équipement planifiées, ce qui est dû au travail de la plupart des services de support (entrepôts, section mécanique du RMC ) entreprises en mode équipe unique, tout cela rend irrationnelle la présence d'un responsable supervisant le travail de la deuxième équipe des équipes.
3. La dispersion d'équipes intégrées distinctes dans toute l'entreprise rend la communication non opérationnelle avec les managers dont la localisation (en raison de l'exercice de fonctions officielles) ne peut être permanente. Lorsqu'il est nécessaire de résoudre rapidement des problèmes de production, des temps d'arrêt injustifiés des équipements se produisent, dus à la répartition irrationnelle des responsabilités entre le patron, le contremaître et le mécanicien.
Les lacunes ci-dessus dans l'organisation structurelle de la gestion du centre commercial nécessitent une réorganisation de la structure de gestion et une révision les descriptions d'emploi certains membres du centre commercial. Conformément à cela, afin d'assurer une organisation plus rationnelle de la gestion du personnel de réparation, il est nécessaire de réorganiser la structure de gestion :
1. Supprimer dans la structure de gestion le poste de mécanicien et ingénieur électricien des centres techniques inclus dans le CR&OK, dont les fonctions sont doublées par les responsabilités professionnelles du mécanicien et ingénieur électricien TsRiOK du CR&OK.
2. Déterminer la responsabilité principale du réparateur d'équipements - supervision directe des réparateurs et des électriciens dans l'entretien des équipements électriques, l'organisation de la production de pièces de rechange et l'exécution de travaux de réparation mécanique.
Un certain nombre de mesures prises permettent de répartir rationnellement les responsabilités entre les acteurs de la structure de gestion de la production de réparation, ce qui permet de :
1. Simplifier la structure de subordination de certaines catégories de personnel de réparation, améliorant ainsi le microclimat psychologique de l'équipe du centre commercial ;
2. Réduisez le temps d'arrêt imprévu des équipements en accélérant les opérations de réparation individuelles - fabrication de pièces de rechange, réalisation de travaux de réparation mécanique.
3.2 Formes progressives et méthodes de réparation
L'augmentation constante des coûts d'entretien des réparations nécessite la recherche de formes et de méthodes de réparation des équipements plus progressistes. Ces formulaires et méthodes comprennent :
spécialisation et centralisation de la réparation des équipements ;
expansion des techniques de réparation avancées;
introduction de technologies avancées pour les travaux de réparation et leur mécanisation ;
améliorer l'organisation du travail du personnel de réparation, etc.
La direction la plus importante doit être considérée comme l'expansion complète de la forme centralisée d'organisation des réparations basée sur la spécialisation des travaux de réparation, c'est-à-dire le développement d'entreprises de réparation spécialisées et la production centralisée de pièces de rechange. L'organisation d'entreprises spécialisées crée les conditions pour application efficace dans la production de réparation d'équipements et d'accessoires de haute performance, de processus technologiques avancés et de méthodes de travail caractéristiques de la production en série et continue.
La centralisation des réparations peut être réalisée à l'échelle des entreprises individuelles, des industries et économie nationale en général. De grands ateliers de réparation peuvent être créés à l’échelle de l’usine pour produire des pièces de rechange et réviser les équipements.
Dans les grands ateliers, il est conseillé de créer des équipes spécialisées pour la réparation d'équipements monomodèles et de composants standards d'équipements divers.
En présence de grande quantité usines d'une certaine industrie dans une région économique, il est conseillé de créer une grande usine de réparation ou un atelier d'importance industrielle au sein de l'entreprise mère pour la production de pièces de rechange et espèce individuelle réparation. La centralisation intersectorielle est conseillée pour réparer les modèles d'équipements les plus populaires utilisant un parc d'échange d'équipements dans l'industrie des machines-outils. Dans ce cas, les réparations doivent être effectuées soit par des usines produisant ces équipements, soit par des usines spécialisées.
Les modalités de réalisation des travaux de réparation sont variées : nodale, séquentielle-nodale, « à contre-courant », standard, etc.
La méthode nodale consiste à remplacer les unités usées de l'unité par des unités de rechange, préalablement fabriquées ou réparées. Dans le même temps, les temps d'arrêt des équipements sont considérablement réduits, puisque la plupart des travaux de réparation sont effectués avant que la machine ne soit retirée pour réparation.
Avec la méthode des nœuds séquentiels, les unités usées de l'unité ne sont pas réparées simultanément, mais séquentiellement en utilisant des interruptions de fonctionnement des unités. Cette méthode est utilisée pour réparer des équipements comportant des unités structurellement distinctes (machines globales).
La méthode « à contre-courant » est utilisée pour réparer les conduites automatisées et nécessite de sérieux travail préparatoire.
Le plus souvent, les équipements de ces lignes sont réparés simultanément à l'arrêt de la ligne ou par tronçons séparés, avec un recours intensif aux méthodes nodales.
Une condition préalable nécessaire à la spécialisation des réparations est l'amélioration de la structure du parc de machines en réduisant le nombre de tailles et de modèles standards de machines et d'unités de base produites dans l'industrie des machines-outils et les usines de construction mécanique.
Large application Les composants et pièces standard de l'industrie des machines-outils peuvent réduire de plusieurs fois le besoin en pièces de rechange et la durée des travaux de réparation.
Les équipements neufs doivent répondre à toutes les exigences de maintenabilité et de haute fiabilité opérationnelle (facilité de démontage et de montage, de contrôle et de réglage, durabilité des pièces associées, etc.). Toute la documentation technique pour la réparation des équipements neufs est fournie par les fabricants.
L'équipement des usines de construction de machines en machines produites en série, combiné à une standardisation généralisée tant dans la construction de machines-outils que dans la production de réparation, permettra de distinguer la réparation en tant que branche spécialisée indépendante de la production de construction de machines.
La solution à ce problème est de réduire les réparations de base aux opérations de remplacement de pièces, d'assemblages et d'assemblages, ce qui est essentiellement la spécialisation des réparations au niveau individuel.
L'industrialisation de la réparation des équipements consiste à rapprocher le niveau organisationnel, technique et économique de la réparation du niveau de fabrication de nouvelles machines dans l'industrie de la machine-outil.
CONCLUSION
Les installations de réparation sont l'une des parties les plus importantes de la structure entreprise manufacturière, puisque l'efficacité de son travail détermine en grande partie le coût des produits, leur qualité et la productivité du travail dans l'entreprise.
Pour résoudre les problèmes d'organisation des installations de réparation dans les entreprises, des systèmes de maintenance et de réparation des équipements technologiques sont développés et appliqués, basés sur le principe de l'actuel Entretien et la maintenance préventive programmée des équipements. Cependant, les particularités du fonctionnement des équipements et la structure des installations de réparation de l'entreprise nécessitent souvent une révision des systèmes de maintenance adoptés pour les équipements technologiques afin de les rationaliser et de prendre en compte les conditions de fonctionnement prévalant dans l'entreprise.
Examen des enjeux sous-jacents à la construction d'un système de maintenance des équipements dans une entreprise de construction mécanique, analyse de l'organisation et des activités de l'atelier de réparation, ainsi que recherche de moyens de l'améliorer. En conséquence, les questions suivantes sont soulevées :
Organiser les réparations programmées et l'entretien courant des équipements à entreprise de construction de machines, en analysant leur efficacité, ainsi qu'en améliorant l'organisation de la maintenance préventive programmée à l'aide d'informations statistiques accumulées sur le nombre et la nature des temps d'arrêt des équipements entretenus ;
Étudier les caractéristiques de la gestion du personnel de réparation, analyser et trouver des moyens d'augmenter l'efficacité de la structure de gestion des réparations adoptée ;
L'organisation des installations de réparation chez Remservis LLC présente un certain nombre de caractéristiques, notamment :
L'organisation de la production de réparation est réalisée sur la base d'un système amélioré Système unifié PPR, inscrite dans le Règlement sur la PPR.
La maintenance des équipements est effectuée conformément au STP adopté dans l'entreprise conformément aux plans et calendriers de maintenance mensuels émis par le PGM.
La maintenance et les réparations programmées des équipements de haute technologie sont effectuées par plusieurs équipes de réparation intégrées, tandis que la grande complexité des équipements nécessite un personnel de réparation hautement qualifié.
Les initiateurs de la plupart des travaux de maintenance imprévus des équipements sont le personnel de maintenance, leur travail prédétermine donc une manière spécifique de gérer les équipes, et ne nécessite qu'une administration.
La production rapide des pièces de rechange par l'atelier de réparation mécanique est effectuée sur place usinage soit sur commande inter-ateliers par les principaux ateliers de mécanique.
À la suite d'une analyse du système d'organisation du service de réparation chez Remservis LLC, il a été proposé de mettre en œuvre un certain nombre de mesures pour améliorer et rationaliser les activités du service de réparation :
D'abolir dans la structure de gestion du centre commercial le poste de mécanicien-réparateur d'équipements, dont les fonctions sont dédoublées par les responsabilités d'emploi d'un contremaître à la réparation des équipements du centre commercial et d'un mécanicien du Centre central des opérations,
Les principaux facteurs d'économie résultant de la mise en œuvre de mesures visant à améliorer la technologie et à organiser les réparations sont la réduction de l'intensité de la main-d'œuvre des travaux de réparation, la réduction des temps d'arrêt des équipements pendant les réparations et l'amélioration de la qualité des réparations des équipements. Par conséquent, les principaux indicateurs pour évaluer la performance du service de réparation sont : densité spécifique travail prévu dans le volume total de travail effectué et le nombre de temps d'arrêt de l'équipement lors de réparations imprévues.
Le calcul des indicateurs d'évaluation de la performance du service de réparation montre que :
La mise en place de mesures visant à améliorer l'organisation de l'entretien des réparations permet d'augmenter la part des travaux prévus.
Outre l'amélioration des indicateurs de performance du service de réparation, la mise en œuvre des mesures proposées aura pour effet d'améliorer la qualité des réparations, qui peut être déterminée par la quantité conditionnelle d'équipements libérés, ce qui indique également la rationalité des propositions.
L'utilisation de formes d'organisation et de systèmes de maintenance des équipements plus progressistes permet non seulement d'améliorer le travail des équipes de réparation intégrées, mais également de rationaliser le retrait des équipements pour les réparations programmées, ainsi :
Réduire les temps d'arrêt des équipements ;
En planifiant en temps opportun les activités individuelles de réparation et d'entretien des équipements, réduire la complexité des travaux de réparation ;
En éliminant les réparations irrationnelles et intempestives, réduisez le coût de l'entretien des réparations ;
En introduisant rapidement des modifications et des changements dans les calendriers PPR, planifiant ainsi les coûts de matériaux et de main-d'œuvre à venir pour les travaux de réparation, réduisez le temps nécessaire aux réparations et augmentez la qualité des réparations.
Bibliographie
1. Fatkhutdinov R.A. Organisation de la production. M. : Infra-M 2000
2. Organisation et planification de la production mécanique, éd. MI. Ipatova. M. : lycée 1998
3. www.retail.ru - hebdomadaire électronique "RETAIL"
4. Vassiliev V.N. "Organisation de la production dans les conditions du marché" Génie mécanique, 99
5. Makarenko M.V., Makhalin O.M., « Gestion de la production » : Manuel. Avantage. Pour les universités - M. : Maison d'édition PRIOR, 1998
6. Fatkhudinov R.A. "Organisation de la production" : manuel INFRA-M. 2001
Complexe ou local ; stratégique, tactique (généralement annuel) ou opérationnel. Les méthodes courantes d'organisation du travail de planification sont les méthodes de réseau et la construction d'opéragrammes. Considérons brièvement ces méthodes. La planification et la gestion du réseau (NPC) sont une méthode graphique-analytique pour gérer les processus de création (conception) de tout système. Schéma du réseau -...
Reçu pendant pratique industrielle, acquisition de compétences pour le développement autonome des problématiques d'organisation et de planification des installations électriques entreprise industrielle. Tâche travail de cours– assurer l’organisation, la planification et la gestion des équipements électriques d’une entreprise industrielle. En tant qu'objet pour le cours, un équipement électrique d'atelier arbitraire d'une entreprise industrielle...
Leur conférant des propriétés d’isolation électrique. Comme vous pouvez le constater, la gamme de produits fabriqués par l’entreprise est assez large. Cela conduit à des ventes de produits constamment élevées. 2.2 Analyse de l'organisation de la gestion de la réparation des équipements technologiques à l'UE « Polimerprom » La tâche principale du service de réparation de l'UE « Polimerprom » est d'assurer le fonctionnement constant des équipements et...
Prévention des coûts inutiles. En conséquence, l'économie de l'entreprise est renforcée et l'efficacité de ses activités augmente. 2. Analyse des activités d'une entreprise de transport automobile à l'aide de l'exemple de NPATP LLC 2.1 caractéristiques générales activités de l'entreprise Au cours de la familiarisation avec les principaux documents organisationnels, les informations suivantes sur l'entreprise ont été obtenues. Forme organisationnelle et juridique...
Les installations de réparation sont un ensemble de services généraux d'usine et d'atelier qui exécutent un ensemble de mesures pour le soin et le contrôle de l'état des équipements, ainsi que leur réparation.
Les installations de réparation comprennent des ateliers de réparation, des bureaux de réparation en atelier et des entrepôts pour stocker des pièces de rechange, etc. En outre, l'atelier de réparation comprend un bureau de conception et de technologie, qui effectue des travaux liés à la réparation, à la modernisation et à la maintenance des équipements, un bureau de planification et de production, qui s'occupe de la planification du travail et de la gestion des expéditions, et un bureau de maintenance préventive.
Les tâches de l'atelier de réparation sont de prévenir l'usure prématurée de l'équipement et de le maintenir dans un état de disponibilité opérationnelle constante, afin de minimiser les temps d'arrêt de l'équipement pendant les réparations. coûts minimaux, dans le soin et la surveillance de sa position.
La réparation des équipements de transformation est organisée conformément aux dispositions du Système Unifié de Maintenance Préventive Planifiée (UPSPR).
Système PPR est un ensemble de mesures techniques et organisationnelles planifiées pour l'entretien, la surveillance et la réparation des équipements. Il s'agit du soin et de la surveillance de l'équipement pendant son fonctionnement, c'est-à-dire entretien de révision, inspections et lavages périodiques, tests de précision des équipements ; réparations périodiques d'équipements (petites, moyennes, majeures). Kukharev, O.N. Organisation et gestion de production / O.N. Kukharev - Penza : RIO PGSHA, 2007, - 82 p.
Il convient de souligner qu'une attention particulière dans le système PPR est accordée à mesures préventives. Cela vous permet d'augmenter la durée de vie de l'équipement, de réduire les temps d'arrêt associés aux dysfonctionnements de l'équipement et les coûts associés au fonctionnement de l'équipement. De plus, une partie importante des travaux liés à la maintenance de révision est confiée directement aux ouvriers de production, ce qui augmente leur responsabilité quant à l'état des équipements.
Le système PPR prévoit un enchaînement strict d'activités en alternance et leur mise en œuvre dans un délai prédéterminé. Dans le calendrier de réparation des équipements, conformément aux normes scientifiquement fondées, le calendrier et la composition des prochaines réparations sont établis pour chaque équipement. Dans l'intervalle entre les réparations, des mesures préventives sont appliquées dans le même ordre strict.
Le système PPR permet une préparation complète des réparations ; préparation de la documentation technique, des matériaux, des flans, des pièces de rechange et des composants ; préparation socle de réparation etc. Cela vous permet de minimiser les temps d’arrêt des équipements pendant les réparations et les coûts globaux de réparation.
L'élaboration des plannings et l'organisation des soins et du contrôle de l'état des matériels, qui constituent la base du dispositif PPR, impliquent l'utilisation classification unifiée tous les aspects organisationnels et événements techniques et des normes spéciales.
Pour déterminer le calendrier des travaux de réparation et des opérations de réparation, le cadre réglementaire PPR est utilisé : normes sur la durée des cycles de révision, leur structure, la durée des arrêts prévus des équipements pour réparation.
Durée du cycle de révision (la période de temps entre la mise en service du nouvel équipement et la première révision majeure ou la période de temps entre deux prochaines réparations majeures) est déterminé en fonction de la durée de vie des principales pièces, assemblages et mécanismes. L'ordre d'alternance des travaux de réparation et des inspections pendant le cycle de révision est déterminé en fonction de la durée de vie des principales pièces à remplacer lors d'une réparation particulière.
Le système PPR prévoit l'utilisation d'une unité de mesure spécifique de l'intensité du travail de réparation des équipements - une unité de réparation. Chaque modèle d'équipement se voit attribuer une certaine catégorie de difficulté de réparation ; elle est déterminée en fonction de la conception et caractéristiques technologiques de cet équipement. Normes pour le volume des travaux de réparation, le nombre de temps d'arrêt, la consommation de matériaux, etc. sont fixés par unité de complexité de réparation, ce qui simplifie considérablement les calculs de planification. Laiton AA Fondamentaux du management. - M. : Écoperspective, 2006. - 239 p.
Des normes relatives à l'intensité de main-d'œuvre des réparations sont établies pour les équipements technologiques et de manutention, les équipements électriques et thermiques. Ils se différencient selon les types d'opérations de réparation, les réparations et la nature du travail (ferronnerie, machines-outils et autres).
Des normes de temps d'arrêt sont établies pour certaines conditions (composition de l'équipe de réparation, technologie de réparation, conditions organisationnelles et techniques, etc.) et sont différenciées pour les équipements de production non automatisés et le retrait des équipements pour réparation par zone. Ils sont installés pour divers types réparations et opérations de réparation et divers quarts de travail des équipes de réparation.
Les taux de consommation de matériaux pour la réparation des équipements sont déterminés par la méthode de calcul. Des normes uniformes pour la consommation de matériaux lors de la réparation des équipements sont établies pour les aciers au carbone et alliés, l'acier moulé, l'acier façonné, les métaux non ferreux, etc.
Des normes spéciales sont établies pour les poids lourds et équipement unique Et équipement spécial usines de montres et d’instruments. Base normative La PPR fait l’objet d’un suivi systématique et d’un ajustement en vue d’une réduction normes actuelles par la mise en place de mesures organisationnelles et techniques. Le système PPR établit également des normes pour la maintenance inter-réparation. L'étendue des travaux de maintenance de révision ne peut pas être réglementée et déterminée avec précision. À cet égard, le nombre de réparateurs (opérateurs de machines, mécaniciens, lubrifiants) est déterminé selon des normes de service établies empiriquement.
La préparation technique des réparations comprend le développement de la technologie de réparation divers modèleséquipements, procédés technologiques de fabrication de pièces de rechange, réparation et restauration de pièces et d'assemblages, conception d'équipements technologiques.
Basique documentation technique, utilisés lors de l'organisation des réparations, sont : des albums de dessins de pièces de rechange, de composants et de mécanismes, de projets de modernisation d'équipements, ainsi que des passeports et des instructions pour l'entretien et le fonctionnement des équipements.
Des albums de dessins pour les pièces de rechange sont utilisés, par exemple, lors de la planification du besoin et de la production de pièces de rechange ; développement de technologies pour la fabrication, la réparation et la restauration de pièces de rechange; mener des travaux de normalisation et d'unification; constitution d'un stock de pièces détachées ; introduction de substituts, etc.
Presque toute la documentation provient généralement des fabricants d’équipements. Les installations exploitant les équipements ne reconstituent les archives techniques qu'en l'absence de l'une ou l'autre documentation ou correction de la documentation originale.
L'expérience montre qu'environ 80 % du volume total des travaux de réparation est constant et identique pour des équipements du même modèle et du même type de réparation. Dans ces conditions, le document technologique principal peut être un processus technologique standard de réparation d'équipements d'un seul modèle.
Dans les cas où les opérations de réparation ont un contenu similaire aux opérations correspondantes effectuées lors de la fabrication de nouveaux équipements, la tâche consiste à utiliser au maximum la technologie progressive de la production principale lors de la réparation des équipements. Plus le degré de concentration de travaux de réparation similaires est élevé, plus l'efficacité de l'introduction d'une technologie progressiste est élevée. Quant aux travaux de réparation spécifiques, l'amélioration de la technologie pour leur mise en œuvre suit la voie d'une mécanisation maximale des procédés, de la réutilisation des pièces (métallisation, soudage, utilisation de la méthode de réparation dimensionnelle, etc.), de l'utilisation généralisée de substituts métalliques, d'une haute -équipements performants, augmentation de l'équipement des processus technologiques, introduction d'opérations augmentant la résistance à l'usure des pièces, etc.
Le support matériel pour les réparations consiste en la préparation en temps opportun de tous matériel nécessaire, pièces de rechange, ensembles et mécanismes et création d'un stock de pièces de rechange. Les besoins en matériaux, produits semi-finis, produits achetés, pièces de rechange et ensembles achetés sont calculés sur la base des taux de consommation et des réserves, en fonction du volume des travaux de réparation.
Livraison dans les délais des matériaux, des produits semi-finis, produits finis et les pièces de rechange sont fournies par le service approvisionnement, en tenant compte du calendrier de retrait des équipements pour réparation établi par le planning.
Un enjeu important dans l'organisation de la réparation des équipements est la constitution et la régulation d'un stock de pièces détachées. Les pièces de rechange sont des pièces de rechange qu'il est économiquement possible de stocker en stock, maintenues à un niveau strictement défini.
L'assortiment de pièces de rechange comprend généralement : des pièces d'usure dont la durée de vie est inférieure à la période de révision ; pièces dont la durée de vie dépasse la période de révision, mais requises dans grandes quantités(pièces identiques comprises dans l'équipement d'un ou différents modèles); des pièces volumineuses, complexes et à forte intensité de main-d'œuvre fabriquées à partir de pièces forgées (moulées) obtenues de l'extérieur ; pièces de rechange pour équipements de haute précision, uniques et limitant la production ; pièces de rechange pour lignes automatiques; pièces sujettes à des pannes soudaines (pièces fusibles, etc.).
L'état du parc de pièces de rechange peut être surveillé à l'aide du taux de rotation du parc de pièces de rechange.
Une diminution du taux de rotation à 0,3 ou moins indique la nécessité de revoir la structure du parc de pièces de rechange. La quantité maximale de stock ne doit généralement pas dépasser les besoins de trois semaines. . Vikhansky O.S. Gestion stratégique. - M. : Gardariki, 2002. - 292 p.