Machine CNC pour fabriquer des moules. Presses pour l'estampage à froid et à chaud de la tôle. Inconvénients des fabricants de moules russes
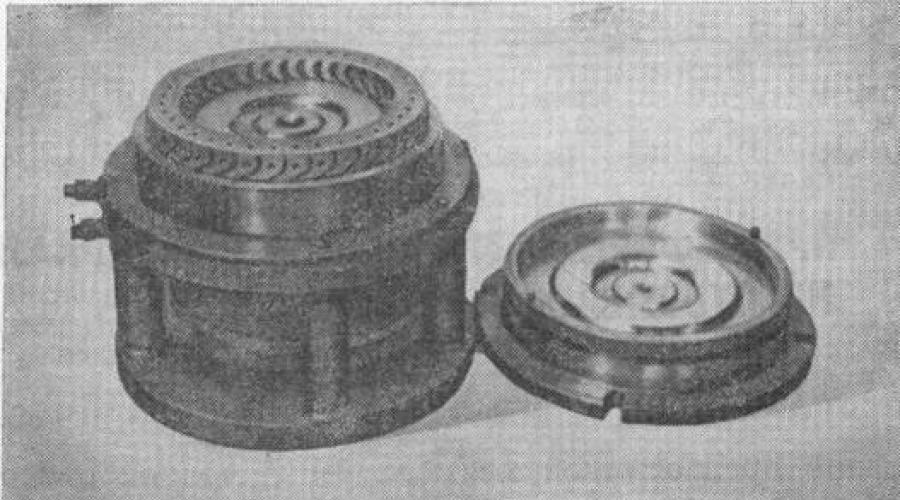
Lire aussi
Pensez-vous encore qu’en Chine tout le monde travaille dans des granges pour un bol de riz ? Aujourd'hui, probablement, personne ne le pense, même s'il y a cinq ans, j'ai entendu de telles déclarations très sérieusement.
Je vous invite à visiter l'usine de moules chinoise. Si quelqu'un ne le sait pas, un moule est un moule en acier dans lequel sont coulées des pièces en plastique. Tous les objets en plastique qui nous entourent, à l'exception peut-être des tuyaux et des profilés, sont fabriqués à l'aide de moules, et dans la plupart des cas, ces moules sont fabriqués en Chine.
La production de moules commence au bureau. Ici, le formulaire est conçu, les composants sont commandés et fournis et le travail avec les clients est effectué. Les espaces ouverts et les cloisons basses sont le style standard des bureaux chinois. Le long du périmètre se trouvent des salles de direction et des salles de réunion.
A côté du bureau, dans une pièce climatisée, se trouve une salle de contrôle qualité. Il y a un équipement de mesure sur lequel des mesures de contrôle des électrodes et des moulages d'essai sont effectués. Un rapport écrit est préparé pour chaque mesure. Les mesures sont principalement prises sur un compteur 3D, et le profil des petites pièces est vérifié sur un microscope informatisé, parfois appelé 2,5D. Ici, la liaison précise des électrodes aux supports a lieu. Grâce à cela, lors de l'installation d'une électrode sur une machine érosive électrique, le grippage peut être évité et un temps précieux sur la machine peut être économisé. Ici, tout est très strict.
Les équipements de précision sont la fierté et la préoccupation particulière de toute production. Deux machines à fil et une machine à percer, équipées de CNC, sont situées dans une pièce séparée dans laquelle un régime climatique constant est maintenu. Les machines Agie Charmilles sont très populaires en Chine, puisque cette entreprise suisse possède sa propre production en Chine.
Pour la plupart des moules, une grande précision de traitement n'est pas requise, c'est pourquoi la base de tout parc de production est constituée de machines conventionnelles avec une automatisation minimale. Dans la plupart des cas, il s’agit de machines de marque taïwanaise fabriquées en Chine.
En général, le processus d’érosion électrique occupe la plus grande part du temps machine dans la production de moules. Premièrement, parce que la plupart des produits modernes ont une forme géométrique plutôt complexe qui nécessite une érosion électrique, et deuxièmement, parce que le processus lui-même est plutôt lent. Avec le perçage électroérosif, le métal est éliminé en raison de sa combustion progressive par une décharge électrique qui se produit entre une électrode de cuivre (ou de graphite) et un moule en acier. Après plusieurs heures de traitement, le trou dans la pièce en acier prend la forme d'une électrode.
Les électrodes pour l'érosion électrique sont fabriquées sur des fraiseuses CNC. En fonction des exigences de précision dimensionnelle du moule, une, deux ou trois électrodes peuvent être fabriquées pour chaque élément : ébauche, finition et finition. La production d'électrodes de cuivre est réalisée sur les machines les plus ordinaires, et pour les machines en graphite plus précises, une vitesse de broche plus élevée et un système d'élimination de la poussière de graphite sont nécessaires. Nous retrouvons Agie.
Pour accélérer l'électroérosion, la majeure partie de l'acier est sélectionnée sur des fraiseuses plus grandes.
Et bien sûr, il n’y a pas d’échappatoire aux fraiseuses manuelles ordinaires. Toutes les machines disposent d'un dispositif d'affichage de coordonnées numériques. Les trous principaux sont percés sur les mêmes fraiseuses. Il est intéressant de noter qu’il n’y a qu’un seul tour dans toute l’usine, et même celui-là prend la poussière dans le coin le plus éloigné. Après tout, près de cent pour cent des pièces cylindriques utilisées dans la production sont des pièces standard achetées.
Le perçage de grandes plaques et de trous profonds dans le moule s'effectue sur une seule perceuse radiale, et une petite machine pneumatique est utilisée pour couper les filetages.
La section de meulage se compose d'une grande et de quatre petites rectifieuses. Comme prévu, ils sont situés dans une pièce séparée, chacun doté d'une hotte aspirante pour éliminer la poussière. Il est surprenant que les petites machines ne soient pas équipées d'entraînements électriques. Les Chinois pensent que le traitement des petites pièces est plus rapide si les mouvements sont effectués manuellement.
Les polisseurs de moules sont généralement de petites filles fragiles, frottant la surface pour obtenir un éclat miroir. Ici, nous rencontrons les garçons. Trois sur cinq utilisent des outils pneumatiques.
La zone d'assemblage est l'endroit où un moule fini est assemblé à partir d'un ensemble de pièces disparates. Un colis standard est reçu ici des fournisseurs, généralement avec des pochettes découpées pour les moules. Des composants standards arrivent également ici et des composants formatifs sont collectés dans d'autres domaines. Sur le site d'assemblage, ils sont installés dans un emballage et mutuellement ajustés.
La technologie permettant d'ajuster avec précision les surfaces de fermeture du moule est assez simple : une peinture spéciale est appliquée sur la matrice et le poinçon, puis le moule est fermé et comprimé avec force. Aux endroits qui nécessitent un ajustement, la peinture s'estompe. Après avoir retiré l'excédent de métal, la surface est à nouveau peinte, le moule est fermé et le processus est répété jusqu'à l'obtention d'un résultat acceptable. Si le formulaire est petit, ce processus est effectué manuellement ou à l'aide d'une grue, et pour les grands formulaires, il existe une presse spéciale. Dans celui-ci, les moitiés du moule sont fixées sur des plaques magnétiques et le processus de fermeture et d'ouverture se déroule en quelques minutes. La particularité de cette presse est que son plateau inférieur se déplace sur le côté, et le plateau supérieur se retourne et se trouve à côté d'elle. Ainsi, le réglage manuel du moule peut être effectué par un mécanicien directement sur la presse, ce qui simplifie et accélère considérablement le processus.
Après assemblage, le moule est envoyé à la zone de test. Il s'agit essentiellement d'une fonderie ordinaire, à une exception près : il n'y a pas d'opérateurs, seulement des régleurs. Le fonctionnement des machines de moulage par injection se limite à l'obtention de quelques pièces moulées d'essai appropriées, après quoi le moule est renvoyé pour assemblage.
Et enfin : la haute direction dans l'atelier. Le directeur de l'usine discute de l'avancement du projet avec le directeur de production.
Formulaires de presse
À catégorie:
Production de pièces moulées de précision
Formulaires de presse
La principale condition pour obtenir une pièce moulée précise est un modèle précis avec une surface exempte de défauts, avec des dimensions précisément maintenues, répondant à toutes les caractéristiques technologiques apparaissant lors de la production de pièces moulées. Pour réaliser un tel modèle, un moule fabriqué avec précision est utilisé. Souvent, lors du choix d’une méthode de coulée à la cire perdue, le facteur déterminant est le coût du maître modèle et du moule. Parfois, il se peut même que le coût de fabrication du maître modèle et du moule soit supérieur aux économies réalisées en convertissant la pièce de l'usinage au moulage.
Les moules pour la coulée de modèles à cire perdue doivent répondre aux exigences de base suivantes : assurer la production de modèles de haute qualité (avec la précision et la propreté de surface spécifiées, sans défauts) ; temps de refroidissement minimum du modèle.
Selon la destination et l'utilisation du moule, ils sont répartis en :
a) pour la production des modèles réels ;
b) pour la fabrication de pièces technologiques auxiliaires (colonnes montantes, collecteurs, bénéfices, etc.).
Sur la base de leur conception, les moules sont classés en moules à empreinte unique (empreinte unique) ; multi-cavités, non reliées par un système de porte ; multi-cavité avec inserts remplaçables pour montage dans les conducteurs.
En termes de degré de mécanisation, les moules peuvent être simples, avec des modèles retirés (manuellement) ; simple, avec retrait manuel des modèles par système de poussée ; complexe, à tiges amovibles. Les moules sont assemblés avec des noyaux et des pièces de moule et démontés manuellement ou à l'aide de machines ; entièrement mécanisé ou automatisé.
Selon les méthodes de fabrication, les moules sont classés en traités mécaniquement ; coulés à partir d'alliages à bas point de fusion; moulés à partir d'alliages de zinc; moulés à partir de matières plastiques; moulé en plâtre; moulé ou pressé à partir de caoutchouc (caoutchouc); traité par galvanoplastie ou métallisation.
Le coût d’un moule dépend principalement de sa complexité ; qui détermine l'intensité du travail de fabrication et le matériau du moule. Ces facteurs sont décidés par le technologue et le concepteur. Lors de la conception d'un moule, le technologue et le concepteur sont guidés par les exigences relatives aux pièces moulées et au nombre de pièces moulées dans la série.
Riz. 1. Moule réalisé par usinage
Les moules produits par traitement mécanique (Fig. 1) sont largement utilisés pour la production de modèles en cire perdue. L'ensemble du moule est fabriqué sur des machines d'usinage sans utilisation de maître modèle. La conception des moules pour pièces moulées simples (sans cavités internes) est relativement simple, tout comme sa fabrication. Il est beaucoup plus difficile et coûteux de fabriquer des moules pour pièces moulées avec des cavités internes ou avec un plan de joint façonné. Les modèles à cavités internes ou à joints profilés (dont les axes ne sont pas parallèles à la direction d'ouverture du moule ou s'étendent en dehors du plan de joint) doivent comporter des tiges escamotables dont la fabrication précise et la mise en place dans le moule sont très laborieuses. intensif. Ces moules sont fabriqués en acier et en alliages d'aluminium. Les alliages d'aluminium sont préférables car ils ont une conductivité thermique élevée. Des pores et des jeux se trouvent souvent dans les billettes coulées en alliages d'aluminium, ce qui détériore la qualité de la surface des modèles.
Les moules sont fabriqués selon la 6ème classe de précision IT avec une rugosité de surface de 0,4 à 0,8 microns selon Hsk. Les zones modèles doivent être équipées de machines modernes de découpe des métaux de précision. Les modèles fabriqués dans de tels moules se distinguent par une grande précision et les moules eux-mêmes sont durables.
Les moules en alliages à bas point de fusion (Fig. 2) sont fabriqués en versant un alliage à bas point de fusion sur un maître-modèle métallique installé dans un cadre en acier. Chaque moitié du moule est remplie de différents alliages dont le point de fusion diffère. Doté d'une partie plate, le modèle est moulé dans une coque en acier avec un mélange de moulage constitué de sable de quartz avec 3% de bentonite ; humidité du mélange 3,5-5,0 %, résistance à l'humidité 0,8-1,0 N/cm2.
Doté d'un connecteur courbe, le modèle est fixé dans une fausse dalle de plâtre. Avant de couler le plâtre, la surface du modèle est lubrifiée avec de l'huile. Une fois le plâtre durci, le connecteur est nettoyé pour faciliter le retrait du modèle. Ensuite, une deuxième coque est installée sur la coque avec la fausse plaque et le modèle et l'ensemble assemblé sont chauffés lentement jusqu'à la température de coulée de l'alliage à bas point de fusion. Pour couler la première moitié métallique, un alliage avec un point de fusion plus élevé est utilisé. La température du modèle et de la fausse dalle est contrôlée par des copeaux d'alliage coulés sur le modèle. La température doit être telle que les copeaux fondent pour former des boules d'alliage liquide. Un alliage à faible fusibilité ne doit pas être surchauffé à plus de 30-40°C au-dessus de son point de fusion. Sinon, les éléments de l’alliage brûlent et celui-ci cesse d’être eutectique. L'utilisation d'alliages non eutectiques donne une surface de moule rugueuse.
Avant la coulée, les films d'oxyde et les contaminants sont retirés du miroir en alliage fondu. Après la coulée, la coque est soigneusement tapotée pour éliminer les bulles d'air adhérentes du modèle, et le miroir du métal coulé est soigneusement chauffé pour éviter sa solidification prématurée. Une fois le métal refroidi, le moule est démonté et le modèle en est retiré. Le connecteur du moule est nettoyé et des cavités technologiques y sont réalisées (canal d'entrée, collecteur, etc.). Les tiges, poussoirs et axes de centrage sont tournés sur les machines d'usinage. Les trous pour les poussoirs sont obtenus en coulant les poussoirs eux-mêmes ou des broches auxiliaires lors de la fabrication de la seconde moitié du moule. Le modèle doit être fermement connecté au poussoir afin qu'aucune distorsion ne se produise.
Riz. 2. Moule en alliage à faible point de fusion
Riz. 3. Moule en alliage de zinc
La seconde moitié du moule est remplie d'un alliage ayant un point de fusion inférieur à celui utilisé pour la première moitié du moule. Avant de verser, la surface de la première moitié du moule est fumée avec de la suie provenant de la combustion de l'huile. Après avoir coulé et refroidi la seconde moitié du moule, le modèle est retiré et, si nécessaire, la cavité et le connecteur du moule sont ajustés (ajustage des deux moitiés du moule). Les défauts mineurs de la cavité sont corrigés par soudure ou scellés avec de la résine.
Pour la première moitié du moule, on utilise généralement un alliage composé de 80 % de plomb, 14 % d'antimoine et 6 % de zinc avec un point de fusion d'environ 250°C. La seconde moitié du moule est coulée à partir d'un alliage à bas point de fusion contenant 51 % d'étain, 31 % de plomb et 18 % de cadmium avec un point de fusion de 150°C.
La surface de la cavité de travail du moule est grattée et polie. Cette technologie permet d'obtenir un moule avec une précision de classe IT 8-9. Les modèles principaux sont généralement fabriqués en acier au carbone moyen. La surface du modèle est polie. Lors de la réalisation d'un modèle composé de plusieurs pièces, il n'est pas recommandé de les fixer par soudure avec des soudures dures et tendres.
Les modèles à faible point de fusion produits dans des moules coulés ont une surface de haute qualité et une précision dimensionnelle satisfaisante. Cependant, les moules échouent rapidement, c'est pourquoi ils sont recommandés pour la production d'une petite série de pièces moulées. Les moules coulés en alliages à bas point de fusion ne sont pas pratiques à utiliser pour la fabrication de grands modèles en raison du coût important et de la consommation élevée d'alliages à bas point de fusion.
Les moules en alliages de zinc (Fig. 14) sont réalisés en coulant un maître modèle avec un alliage de zinc dans une coque en acier.
Lors de la fabrication de moules complexes ou soumis à des exigences de précision accrues, une pression est appliquée sur le miroir de l'alliage de zinc coulé jusqu'à ce que l'alliage se solidifie complètement. Comparés aux moules en alliages à bas point de fusion, les moules en alliages de zinc sont plus durs, plus résistants, s'usent moins et se déforment sous l'impact, c'est-à-dire que la durabilité d'un moule en alliage de zinc est légèrement supérieure à celle d'un alliage à bas point de fusion.
Le processus de fabrication de moules à partir d'alliages de zinc, qui durcissent sous pression dans la première phase, est similaire au processus de fabrication de moules à partir d'alliages à bas point de fusion. Tout d’abord, un modèle en zinc ou en acier poli est réalisé. Le modèle est moulé avec un mélange de sable et enterré à 1 mm du plan de joint. Avant de couler, le moule en sable est fumé avec de la suie, puis un flacon en acier est installé dessus et l'ensemble est chauffé à 260-280°C. Un alliage de zinc, surchauffé à 410-430°C, est coulé dans la coque. Si le modèle est en alliage de zinc, l'ensemble est initialement refroidi à température ambiante, puis le modèle est à nouveau chauffé à 100-200 ° C pour une meilleure extraction.
Le demi-moule libéré du modèle est traité mécaniquement le long du connecteur et le modèle y est inséré, suivi d'un fumage avec de la suie. Ensuite, la seconde moitié de la coque est installée et l'ensemble est chauffé dans un four à 260-280 °C. L'ensemble chauffé est installé sous presse, rempli d'alliage de zinc et pressé avec un poinçon avec une force d'au moins 10 kN, selon la taille du moule, jusqu'à ce que l'alliage soit complètement solidifié. Après refroidissement à température ambiante, le kit est à nouveau chauffé à 100-200 °C pour faciliter son démontage.
La première moitié coulée du moule est traitée et deux ou trois trous borgnes sont percés sur le plan de joint pour la fixation avec la seconde moitié du moule. Les poussoirs sont fixés dans le moule en coulant un alliage, ou un trou est percé dans le moule pour eux.
La seconde moitié du moule est coulée de la même manière. Le moule est usiné aux dimensions requises, le système d'injection est fraisé, les poussoirs et les tiges sont fabriqués et les dispositifs de serrage sont installés.
Pour fabriquer des moules en alliages de zinc sans pression, un modèle divisé est utilisé. Les deux moitiés sont installées séparément sur des plaques dans la coque, chauffées à 420 °C et remplies d'alliage de zinc à une température de 470 à 490 °C. Après durcissement et refroidissement, la coque est retirée, la plaque est retirée et le modèle est retiré. Le plan de séparation du moule est traité et les deux moitiés sont reliées à l'aide de broches de centrage. Les pièces auxiliaires des moules, telles que les poussoirs, les tiges, les pions de centrage, etc., sont généralement réalisées en acier par usinage. Il est relativement simple et peu coûteux de fabriquer des moules à partir d'alliages de zinc sans pression, mais cette méthode est utilisée avec un simple plan de joint.
Riz. 4. Moule en plastique
Les moules en alliages de zinc sont assez durables, fournissent des modèles de haute qualité et sont relativement peu coûteux. Ils conviennent à la réalisation de pièces moulées en grandes séries, mais sont quasiment inadaptés aux modèles à grandes cavités ou à tiges latérales et inclinées. Les coûts de main-d'œuvre pour la fabrication de moules en zinc sont plus élevés et le coût du matériau est inférieur à celui pour la fabrication de moules en alliages à bas point de fusion.
Les moules obtenus en remplissant le maître modèle de matière plastique (Fig. 4) sont très simples à fabriquer et donc bon marché. Ils ne sont pas assez durables et sont donc utilisés dans la fabrication de pièces moulées en petites séries. Les matériaux du moule sont des résines dentacryliques ou époxy. Étant donné que les plastiques sont moins conducteurs thermiquement que le métal, ils doivent être utilisés pour des moules de petite taille avec une masse uniformément répartie afin que la composition du modèle durcisse uniformément. Pour augmenter la conductivité thermique, il est recommandé d'introduire des charges dans les résines - poudres ou grenailles métalliques.
Les meilleurs maîtres modèles sont en métal poli ; Pour les moulages moins critiques, des modèles en bois sont utilisés. En pratique, différents matériaux peuvent être utilisés pour les modèles qui ne se déforment pas lorsqu'ils sont remplis de plastique. Les modèles en plâtre produisent des impressions de moins bonne qualité que celles en bois, et encore plus en métal.
Avant de couler, le modèle est lubrifié avec une fine couche d'agent démoulant pour mieux séparer le maître modèle de la masse coulée. Les lubrifiants suivants ont fait leurs preuves : solution à 2 % d'huile de silicone dans du trichloréthylène ; Une solution à 2% de cire d'abeille ou de cire de carnauba dans de l'essence et une solution d'huile de ricin dans de l'alcool méthylique ou éthylique. Le lubrifiant est appliqué au pinceau ou par pulvérisation en couche très fine afin que la précision des plus petits éléments de la surface du modèle ne soit pas compromise.
Le processus de fabrication de moules à partir de plastiques est similaire au processus de fabrication utilisant des métaux fondus liquides. Il est préférable d’utiliser des fausses plaques de plâtre. Le plastique est versé à vitesse maximale en un flux continu afin qu'aucune bulle d'air ne se mélange au mélange. Un jet de plastique est dirigé sur le plan du connecteur et le niveau de liquide montant recouvre silencieusement le modèle. Les bulles d'air de la résine remplie de poudre ou de grenaille métallique sont éliminées par vide ou vibration.
Il est recommandé d'utiliser une masse constituée de résine CHS Erox 1200, dans laquelle est remplacée 80 % (en masse) de grenaille d'acier mesurant 0,3-0,5 mm. Le mélange est chauffé à 50 °C sous agitation, le durcisseur P1 y est ajouté à raison de 7 heures pour 100 heures de résine Erox 1200 et le mélange résultant est à nouveau soigneusement mélangé.
Les moules en résine époxy avec charge métallique sont souvent utilisés pour tester la technologie de moulage ou pour produire de petites séries de modèles à cire perdue. Cette méthode ne nécessite pas beaucoup de temps, est peu coûteuse et est toujours utilisée sans traitement mécanique. L'inconvénient des moules en plastique est une précision moindre et une faible conductivité thermique des moules par rapport aux moules en métal.
Les moules en plâtre peuvent être utilisés pour fabriquer des modèles individuels sans exigences particulières quant à leur précision dimensionnelle. La durabilité de ces formes est très faible, mais étant donné les faibles coûts de leur production, elles sont souvent utilisées pour tester des solutions technologiques. Les moules sont détachables, les deux moitiés étant coulées dans des coques pliables en bois ou en métal. La seconde moitié du moule est coulée sur la première, comme sur une fausse dalle. Pour éviter que le plâtre ne colle, le connecteur du premier moule est lubrifié avec un agent démoulant (une solution de cire dans du trichloroéthane, de l'essence ou de l'huile de silicone ; une solution de vaseline dans de l'essence). Les moules en plâtre ne conviennent pas pour y presser la composition du modèle sous pression. La composition du modèle est coulée dans des moules à l'état fondu par coulée libre.
Les moules réalisés en coulant un maître-modèle avec du caoutchouc de silicone sont utilisés pour la réalisation de modèles à cire perdue qui n'ont pas d'exigences de précision, par exemple des modèles d'objets décoratifs ou des modèles pour tester la technologie de coulée en cours de développement (par exemple, la densité des pièces moulées). avec le système de gate sélectionné). De telles formes sont élastiques, de sorte que des modèles avec des pentes négatives peuvent y être réalisés.
Les moules en caoutchouc silicone peuvent également être réalisés sans fausse dalle en coulant l'intégralité du modèle. Après durcissement, la coque en caoutchouc silicone est découpée le long du connecteur. Il est préférable de fabriquer une fausse dalle en gypse.
Les broches de guidage peuvent être coulées dans les deux moitiés du moule ; De plus, il est possible de réaliser un modèle de la cheminée d'injection à partir de la composition du modèle et de le mouler simultanément avec le modèle. Des moules en caoutchouc dans des coques métalliques peuvent être utilisés pour réaliser des modèles en pressant la composition du modèle à basse pression. Dans les moules sans coques, seule la coulée libre de la composition du modèle est autorisée. La très faible conductivité thermique des moules en caoutchouc allonge tout le cycle de production des modèles, mais permet d'obtenir des modèles avec une impression claire et une qualité de surface élevée.
Les moules produits par électroformage peuvent être utilisés pour des modèles très précis et complexes de poids moyen. De tels moules ne conviennent pas à la production de modèles comportant des poches, des rainures et des trous profonds ; leur production est relativement coûteuse, nécessite un équipement spécial et n'est donc pas largement utilisée en Tchécoslovaquie.
Les moules produits par métallisation n'ont pas encore été testés en production, mais ont été examinés par les auteurs du point de vue technique et économique avec les méthodes décrites précédemment.
Le principe de base de la métallisation est l'application de particules de métal liquide par un flux gazeux sur la surface préparée d'un objet à l'aide d'un pistolet de métallisation. Le fil métallique du pistolet est fondu soit par une flamme, le plus souvent de l'oxyacétylène, soit par un arc électrique. Lors de l'impact, sous l'influence de l'énergie cinétique, les particules métalliques se déforment, adhèrent les unes aux autres et à la surface du matériau, et forment une masse fermement connectée qui reproduit fidèlement la forme de l'objet - le modèle. Cette méthode n'est pas utilisée pour tous les types de modèles. Les avions pulvérisés sous un angle par rapport à l'écoulement sont plus difficiles à métalliser ou ne sont pas métallisés du tout lorsque leur surface est grande ou avec un angle d'attaque très prononcé.
Tout moule (acier, alliages à bas point de fusion ou de zinc, plastique) peut être simple, complexe et avec différents degrés de mécanisation. Le moule peut être conçu uniquement pour une configuration de modèle spécifique ou être universel avec des inserts remplaçables. Le moule peut être équipé d'un dispositif de refroidissement par eau, et enfin il peut être utilisé pour réaliser des maquettes ou des systèmes de gate.
Bien entendu, lors de la production de modèles en petites séries ou en production unique, les moules hautement mécanisés ne sont pas utilisés. La technologie et les coûts de fabrication d'un moule à partir de différents matériaux sont différents.
Lors de la conception de moules pour modèles à cire perdue, il est nécessaire de prendre en compte les caractéristiques de conception de leurs éléments, qui peuvent affecter de manière significative le fonctionnement de l'ensemble du moule. Ces éléments sont par exemple :
1) les demi-moules proprement dits, selon la configuration de la coulée (moule sans inserts amovibles ou avec éléments repliables) ;
2) tige (mobile ou fixe) ;
3) poussoirs ;
4) système de refroidissement du moule ;
5) système d'alimentation en composition de modèle du collecteur central (assemblage d'unités de modèle) ;
6) système de fourniture de composition de modèle pour des modèles individuels (modèles soudés) ;
7) système d'évacuation d'air pour moules.
Dans les moules sans insert, le modèle est formé soit dans les deux moitiés, soit dans une seule, généralement la moitié inférieure du moule. Les deux moitiés du moule doivent s'emboîter le long de la surface de joint, qui peut être plate ou profilée. La cavité du moule doit être conçue de telle manière que lorsque le moule est ouvert des deux moitiés, le modèle puisse être facilement retiré.
Dans un moule pliable avec un profil de cavité complexe, pour retirer le modèle, les inserts, tiges et autres éléments doivent en être retirés avant d'ouvrir le moule. De telles solutions ne sont utilisées que dans les cas où la configuration de coulée est très complexe et où il est impossible de créer le plan de joint du moule sans pièces détachables.
La forme complexe des cavités ou des trous du modèle est obtenue à l'aide de tiges placées perpendiculairement ou parallèlement au plan de joint ; dans ce dernier cas - tiges latérales. Il est recommandé de fixer les tiges disposées perpendiculairement par rapport au plan de joint, si la configuration de coulée le permet, dans la moitié inférieure du moule. Pour les petites séries de pièces moulées, les tiges latérales doivent être retirées manuellement ; de très petits noyaux sont retirés du moule avec les modèles.
Riz. 5. Tige composite métallique formant une configuration de cavité complexe
Riz. 6. Emplacement des poussoirs dans le moule
Les poussoirs sont utilisés pour pousser les modèles hors de la cavité de travail du moule ; ils sont situés dans la moitié inférieure du moule (Fig. 17). Le plan de joint doit être choisi de manière à ce que lors de l'ouverture du moule, le modèle reste dans la moitié inférieure. Étant donné que les poussoirs laissent une empreinte sur les modèles, ils doivent si possible être placés sur les surfaces de travail.
Les poussoirs doivent avoir un dispositif de verrouillage, ou des plaques spéciales sont réalisées dans le moule pour empêcher le mouvement des poussoirs lors du pressage de la composition du modèle. Les poussoirs de profilés sont fixes dans le moule (du fait de leur éventuelle rotation autour de leur axe). Le meilleur matériau pour les poussoirs s'est avéré être la fonte grise, destinée aux coussinets selon CSN 42 2456. Les poussoirs sont entraînés par un plateau de pression via un entraînement hydraulique ou manuellement. Les poussoirs reviennent dans leur position initiale dans la plupart des cas grâce à un ressort comprimé.
Dans de nombreux cas, les modèles peuvent être retirés sans poussoirs à l'aide d'air comprimé fourni par un insert perméable aux gaz (Fig. 7).
Pour raccourcir le cycle de durcissement et éliminer le retrait local externe à la surface des modèles, les moules doivent être refroidis. Refroidir le moule avec de l’eau froide est le moyen le plus efficace. Dans les moules sans inserts, les canaux de refroidissement sont réalisés en une ou deux moitiés ; dans les moules avec inserts, les nids pour les inserts sont en outre refroidis. Les dimensions des canaux de refroidissement ne sont généralement pas calculées et le concepteur les détermine en fonction de son expérience et de la possibilité de leur placement dans le moule. Des canaux doivent être prévus à proximité des parties les plus massives du modèle. L'eau potable est souvent utilisée pour le refroidissement. La température de l'eau varie en fonction des conditions météorologiques, ce qui ne permet pas de définir un seul mode de refroidissement. Il est conseillé d'effectuer le refroidissement dans un appareil de réfrigération spécial et de maintenir une température de l'eau constante.
Riz. 7. Démoulage du modèle à l'air comprimé : 1 – ALIMENTATION en air comprimé ; 2 - insert perméable aux gaz
Il est nécessaire de fixer les moitiés supérieure et inférieure des moules ensemble dans le plan de joint. Ceci est assuré dans la plupart des cas par des broches de centrage ou une conception de type saillie-évidement dans des moules en alliages à bas point de fusion ou en plastiques (Fig. 8). Les moitiés en alliage de zinc sont fixées en perçant une cavité dans une moitié du moule avant de couler l'autre moitié.
Riz. 8. Fixation des moitiés de moule à l'aide d'une saillie
Des moules de grandes dimensions ou destinés à la réalisation de modèles en grandes séries sont fixés sur les plateaux d'un dispositif de pressage, le concepteur doit donc prévoir un procédé de fixation des moules sur le plateau d'un tel dispositif. Les moules de petites tailles ou pour modèles de petites séries ne sont pas sécurisés, mais sont installés et retirés manuellement du dispositif pressé.
L'air est évacué du moule à travers les espaces entre les bagues de guidage et les poussoirs le long du plan de joint ou le long de rainures spécialement conçues.
Les moules de presse avec mécanisation complète et automatisation du montage et du démontage conviennent à la fabrication de modèles en grande série ou à la production en série. Les fonderies de fonderie de précision en Tchécoslovaquie ne produisent pas encore ce type de moules, car les pièces moulées sont produites en lots relativement petits. L'utilisation de moules automatisés implique des équipements de pressage performants et des dispositifs de transport associés pour transférer les moules depuis les positions d'assemblage, de pressage, de refroidissement et de démontage.
Si les fonderies utilisent différents types d'équipements de pressage, des modèles de moules correspondants sont également utilisés. Cela crée certaines difficultés, car chaque fonderie doit concevoir et fabriquer des modèles de moules différents. Par conséquent, chaque fonderie de coulée de précision doit disposer de sa propre technologie de fabrication de moules, qui dépend des équipements et des divers dispositifs nécessaires à l'un ou l'autre type de production.
Comparaison économique des méthodes de fabrication de moules individuels. Initialement, les moules à cire perdue étaient fabriqués à partir de métaux par usinage. Afin de réduire les coûts de production et d'étendre l'utilisation du moulage à la cire perdue, d'autres méthodes de fabrication de moules, moins coûteuses et plus rapides, ont été développées et proposées.
Dans ce tableau, les coûts de main d'œuvre sont systématisés par rapport aux coûts (supposés à 100 %) de fabrication de moules en acier par usinage. Les coûts de main-d'œuvre reflètent les coûts associés à la production des mêmes moules simples en utilisant différentes méthodes. Le degré de précision est classé selon un système en cinq points. La différence entre les scores individuels n’est pas équivalente. Par exemple, la différence de précision entre les scores 1 et 2 ou les scores 2 et 3 est plus petite qu’entre les scores 4 et 5. Le temps de solidification a été déterminé expérimentalement à partir des résultats d'observations du refroidissement de modèles identiques en cire perdue dans des moules de différents types.
C'est le temps nécessaire pour conserver le modèle dans le moule puis le retirer sans risque d'endommagement et de déformation lors d'opérations technologiques ultérieures. Les données concernant cette période sont uniquement à titre informatif. Il peut y avoir des écarts par rapport aux valeurs indiquées. Cela dépend par exemple de la composition du modèle utilisée et de la température de son pressage.
La dernière colonne du tableau. 13 contient des informations sur la durabilité des moules. La durabilité des moules réalisés selon la même technologie dépend de nombreux facteurs : la taille des modèles ; la position du plan de joint dans le moule, notamment lorsque le plan de joint passe le long d'une surface ne présentant pas de surépaisseur de traitement ; le nombre et la qualité des poussoirs et, enfin, sur l'entretien minutieux du moule lors de son fonctionnement, de son réglage et de son réglage, ainsi que sur l'état du matériel de pressage. Les données sont tirées de l'expérience pratique dans les fonderies de fonderie de précision, où les moules étaient fabriqués en utilisant les processus technologiques indiqués.
En pratique, des moules usinés seront également utilisés, car il s'agit du seul mode de production permettant de réaliser des moules pour des modèles de grandes dimensions hors tout et pesant plus de 10 kg. Les modèles les plus complexes en configuration, avec un plan de joint complexe et des pièces détachables, seront réalisés dans les mêmes moules. Des modèles de pièces moulées produits en grandes séries avec des exigences élevées en matière de propreté de surface et de précision dimensionnelle sont produits dans des moules en acier obtenus par traitement mécanique.
Les moules Fess en alliages à bas point de fusion sont utilisés dans la production de pièces moulées en petites séries. Il s'agit d'une méthode relativement rapide et fiable qui, compte tenu des raisons évoquées précédemment, trouve toujours une application dans le moulage de précision.
S'il est nécessaire de vérifier le processus technologique conçu lors de la production de pièces moulées individuelles, par exemple pour des besoins de réparation, les moules en plâtre ou en caoutchouc de silicone conviennent. Les moules en résine époxy sont utilisés pour la production urgente de pièces moulées uniques.
D'après un examen des avantages et des inconvénients des moules fabriqués par diverses méthodes, il apparaît qu'à l'heure actuelle et dans un avenir proche, on ne peut pas supposer qu'une seule méthode de fabrication de moules à cire perdue sera utilisée dans une fonderie. Il est économiquement rentable de produire des moules non seulement par traitement mécanique, mais aussi principalement à partir de zinc et d'alliages à bas point de fusion. La mesure dans laquelle les méthodes décrites seront utilisées dépendra du programme de production, de la configuration et des dimensions globales des pièces moulées fabriquées.
Si un technologue développe une technologie pour un nouveau moulage, il doit connaître toutes les circonstances qui influencent le choix du moule. C’est la seule façon de concevoir un moule qui garantira la production la plus économique d’une nouvelle pièce moulée.
Lors de la conception de différents types de moules, les critères suivants sont déterminants :
1) tailles des séries et nombre estimé de pièces moulées ;
2) configuration et dimensions globales des pièces moulées ;
3) précision dimensionnelle requise des pièces moulées ;
4) propriétés thermophysiques du matériau du moule ;
5) les coûts de fabrication des moules ;
6) équipement pour presser la composition du modèle dans un moule.
La principale documentation que le technologue élabore et transfère au concepteur pour la production de dessins et de moules est un dessin de coulée ou un dessin d'un maître modèle avec des instructions détaillées sur le type et la méthode de fabrication du moule.
Aujourd'hui, en Russie, il n'y a pas beaucoup de fabricants de moules pour le moulage par injection de métal. Parallèlement, la plupart des entreprises impliquées dans leur développement achètent du matériel de fonderie à l'étranger. Les principaux fournisseurs sont les pays d’Asie du Sud-Est (Chine, Corée du Sud, Taiwan), ainsi que des entreprises européennes.
Cependant, il existe encore dans notre pays des fabricants auprès desquels vous pouvez commander un moule pour la fabrication de produits métalliques. Dans notre brève revue, nous attirons votre attention sur plusieurs de ces entreprises dans diverses villes de Russie.
Cinq fabricants de moules de Russie
CJSC "NTC-BULAT"
La seule entreprise métropolitaine de notre revue qui fabrique des produits métalliques sur commande depuis plus de 10 ans. Les services proposés par l'entreprise couvrent tout le cycle de création d'un moule : de l'élaboration de la documentation technique et de la conception au tournage de certaines pièces (en savoir plus sur le tournage).
L'entreprise dispose de sa propre large base de production et produit indépendamment des moules clé en main, plutôt que de commander des produits en Chine. Les clients de NTC-BULAT CJSC sont de nombreux grands fabricants de pièces automobiles, d'équipements de lutte contre l'incendie, médicaux, électroniques et autres de tout le pays.
Usine de moisissures de Kaluga
Une grande entreprise qui produit un grand nombre de moules pour couler non seulement des alliages métalliques, mais aussi du caoutchouc, du caoutchouc et du plastique. Les employés de la société Kaluga possèdent une vaste expérience dans la fabrication de moules à coins, de moules à plans de joint multiples, de systèmes d'éjection à plusieurs étages et de nombreux autres types de produits.
Kaluga Mold Plant utilise des équipements multifonctionnels modernes et développe des moules pour tout type de moulage à partir de zéro.
Usine d'équipement technique de Yaroslavl
YaZTO développe depuis plusieurs années des moules à canal froid pour la fabrication de pièces par injection de métaux non ferreux. L'entreprise est l'un des leaders sur ce segment de marché.
Parmi les avantages de l'entreprise figurent non seulement une expérience riche, mais aussi, par exemple, un prix inférieur de 10 % à la moyenne du marché. Lors de la fabrication des moules, les employés de l'usine d'équipement technique de Yaroslavl utilisent des équipements japonais et pour le tournage, des machines CNC allemandes.
Les clients de YaZTO sont de nombreux fabricants nationaux et étrangers de pièces automobiles.
Usine de construction de machines nommée d'après V.V. Vorovski
L'entreprise, située à Ekaterinbourg, produit des moules de complexité variable pour la coulée de métaux, de caoutchouc et de plastiques. ZiV produit également des matrices pour l'emboutissage à froid du métal (aluminium, cuivre, acier) et de la paronite avec des dimensions jusqu'à 300x500x400 mm selon les plans du client. Le coût d'un moule fini varie de 30 000 à 100 000 roubles.
L'histoire de l'usine remonte à plus de 90 ans et son personnel compte un grand nombre d'employés ayant dix ans d'expérience ou plus. La base de production de l'entreprise est constamment mise à jour avec des équipements modernes.
TOCHTSVETLIT LLC
Fabricant de moules à Riazan, réalisant un cycle complet de leur production. L’entreprise est prête à entreprendre le développement des dessins et des conceptions du moule ou à le produire selon les dessins du client.
TOCHTSVETLIT LLC existe depuis 1999. Durant cette période, l'entreprise a réussi à s'imposer comme un partenaire commercial fiable et l'un des principaux fabricants de moules de la région. La base de production de l’entreprise est équipée d’équipements importés modernes.
Inconvénients des fabricants de moules russes
Parmi les défauts qui caractérisent presque tous les fabricants de moules russes figurent :
- Longue période de production. En règle générale, la création d'un moule complexe en Russie prend 4 à 6 mois. En Chine, un processus similaire dure 40 à 50 jours ;
- Opportunités limitées. Malheureusement, la plupart des fabricants russes sont à la traîne des entreprises de Chine, de Corée du Sud et d'Europe occidentale en termes de complexité des moules qu'ils produisent ;
- Prix. Le prix des moules russes est à la fois leur inconvénient et leur avantage. Les produits nationaux sont déjà plus chers que les produits chinois, mais restent moins chers que ceux d’Europe occidentale.
Avantages des moules russes
Malgré les inconvénients mentionnés, commander des moules auprès de fabricants russes présente également de nombreux avantages :
- La qualité des produits. Les fabricants russes sont aujourd'hui de dignes concurrents de l'Europe et de la Chine dans cet indicateur ;
- Facilité de contrôle de la production. Créer un outil aussi précis qu’un moule nécessite une maîtrise totale de toutes les étapes de production. Avec les fabricants russes, c'est beaucoup plus simple : il n'y a pas de barrière linguistique ou culturelle, et le facteur distance est réduit au minimum ;
- Simplicité du service de garantie ;
- La possibilité d'évaluer les produits d'un fabricant en particulier avant de lui commander un moule.
L'emboutissage, réalisé à l'aide d'une presse à métaux, est l'une des opérations technologiques les plus courantes pour le traitement de ce matériau. L'essence de cette procédure est de donner à une pièce en métal la forme requise, pour laquelle une déformation plastique est utilisée, en éliminant un certain relief, des motifs ou en perforant des trous. Les presses pour le traitement des métaux, selon la liste des tâches auxquelles elles sont destinées, diffèrent les unes des autres tant par leurs paramètres techniques que par leur conception.
Types d'opérations et d'équipements technologiques d'emboutissage
L'emboutissage en tant que méthode de traitement des ébauches métalliques peut être :
- chaud;
- froid.
Le premier implique que le métal est traité à chaud. Le grand avantage du marquage à chaud est que lorsqu'il est réalisé, les caractéristiques de la pièce à usiner sont améliorées (en particulier, la structure métallique devient plus dense et plus uniforme). Pendant ce temps, aucune couche de tartre n'est créée à la surface des pièces métalliques traitées à l'aide de la technologie, tandis que les dimensions des produits finis sont plus précises et leur surface est plus lisse.
Selon le type de pièce à emboutir, une telle opération technologique peut être en feuille ou volumétrique. L'emboutissage du premier type est utilisé pour le traitement des ébauches de tôle ; cette technologie permet de produire :
- plats;
- bijoux;
- arme;
- équipements et instruments médicaux;
- pièces de montres, d'équipements ménagers, de climatisation et électriques ;
- pièces pour compléter l'équipement automobile;
- pièces de machines-outils et autres produits d'ingénierie.
Les produits métalliques finis obtenus grâce à la technologie ne nécessitent pas de raffinement supplémentaire. La formation de leurs paramètres géométriques lors de l'emboutissage volumétrique se produit sous des formes spéciales dans lesquelles du métal chaud ou froid est soumis à une extrusion.
La presse est généralement utilisée pour :
- production d'ébauches métalliques par forgeage;
- pressage et pressage d'arbres, de roulements et d'engrenages ;
- effectuer un estampage de feuilles et de volumes.
Selon le principe de fonctionnement, les machines à presser peuvent être de type mécanique ou hydraulique et effectuer le traitement des métaux par des méthodes statiques ou par impact.
Les équipements de pressage mécanique peuvent être conçus selon leur conception :
- excentrique;
- manivelle.
Les machines à manivelle sont utilisées aussi bien pour le froid que pour le chaud. Cet équipement d'emboutissage est également utilisé pour effectuer des opérations technologiques telles que l'emboutissage, la découpe et la découpe. La presse hydraulique est utilisée pour les opérations technologiques d'emboutissage et de forgeage d'ébauches métalliques en vrac.
Selon leur fonctionnalité, les machines à presser sont divisées dans les types suivants :
- universel;
- spécial;
- spécialisé.
Une machine à presser universelle possède la fonctionnalité la plus large ; un tel équipement peut être utilisé pour effectuer presque toutes les opérations de forgeage. Des filières ou presses spécialisées sont utilisées pour mettre en œuvre un processus technologique. Les presses spéciales utilisées pour l'emboutissage de produits d'un type ont une fonctionnalité minimale, alors que leur fonctionnement est basé sur une seule technologie.
Conception et principe de fonctionnement des équipements de pressage
La conception de tout équipement d'emboutissage se compose des éléments suivants :
- moteur d'entraînement ;
- mécanisme de transmission de mouvement ;
- mécanisme d'actionnement.
Selon la façon dont le moteur d'entraînement de la presse est relié à son actionneur, on distingue les machines avec connexion :
- mécanique;
- non mécanique, réalisée par liquide, gaz ou vapeur.
Le mécanisme d'actionnement dont est équipé l'équipement d'emboutissage peut être constitué de traverses, d'un curseur, de rouleaux, de rouleaux et de femmes.
Presses à manivelle
L'élément structurel principal de ces presses est le mécanisme à manivelle, qui convertit le mouvement de rotation qu'il reçoit de l'entraînement en mouvement alternatif du curseur. L'actionneur, équipé d'une presse à emboutir de ce type, est relié directement au curseur, capable de développer une force allant jusqu'à 100 tonnes. Le mouvement du curseur dans de telles presses se produit à la même fréquence.
Les presses à manivelle peuvent être des équipements simples, doubles ou triples. A l'aide de telles machines, vous pouvez effectuer les opérations technologiques suivantes :
- estampage à l'aide de matrices de type ouvert et fermé ;
- découpe de tôles;
- micrologiciel ;
- formation du produit fini par extrusion ;
- traitement combiné.
Dans les cas où un équipement plus puissant est nécessaire pour former un produit fini à partir d'une billette métallique, des machines de type hydraulique sont utilisées.
Presses hydrauliques
À l'aide d'une presse hydraulique, vous pouvez presser des pièces métalliques à la fois plus grandes et plus épaisses. De tels équipements pour l'emboutissage de tôles, l'emboutissage, le forgeage, le pliage et d'autres opérations technologiques, selon le modèle spécifique, peuvent développer des forces de 150 à 2 000 tonnes, voire plus.
Les principaux éléments structurels dont chacun est équipé sont deux cylindres de diamètres différents, remplis de fluide de travail et communiquant entre eux. Chacun de ces vérins hydrauliques possède un piston qui crée la pression du fluide de travail ou se déplace sous son influence. C'est le mouvement des pistons dans les vérins hydrauliques qui assure le mouvement de l'actionneur de l'équipement. La quantité de force qu'une telle presse à emboutir peut créer est déterminée par la différence de diamètres de ses vérins hydrauliques.
Presses à forger radiales
Une machine de forgeage radial est une presse de formage sur laquelle des ébauches métalliques préchauffées sont transformées en produits finis de configuration cylindrique. La conception des presses de ce type est la suivante :
- un four à induction dans lequel la pièce est préchauffée ;
- convoyeur pour introduire la pièce dans la zone de traitement ;
- des mécanismes de préhension, à l'aide desquels la pièce métallique en cours de traitement, en rotation constante, traverse la zone de forgeage ;
- une vis sans fin reliée à un moteur électrique et responsable du fonctionnement des mécanismes de préhension ;
- quatre arbres avec des boîtes d'essieux excentriques qui transmettent le mouvement à une bielle avec percuteur, entre lesquelles un curseur est fixé (les arbres eux-mêmes reçoivent la rotation d'un moteur électrique d'entraînement via un entraînement par courroie trapézoïdale) ;
- des tambours à copier, responsables de l'approche synchrone des percuteurs et du mouvement ultérieur de la pièce ;
- un embrayage à ressort qui assure le freinage de la pièce pendant son traitement par les percuteurs.
Laissez-nous une demande et nous vous enverrons une proposition technique et commerciale dans l'heure !
Équipements pour la production de presses pour moules : de l'application à la mise en service
Les machines capables de créer des moyens de production sont toujours très appréciées, car la possibilité d'obtenir rapidement presque n'importe quel modèle pour créer des produits uniques vous permet de résoudre les problèmes les plus complexes sans aucun problème avec une perte de temps et d'argent minimale. Les moules de coulée sont devenus très répandus en raison du développement de la production de plastique. L'amélioration constante des matières premières, garantissant leur durabilité et leur sécurité, a conduit à la mise en œuvre de projets de plus en plus ambitieux et audacieux, dont l'étape principale est la préparation et l'achèvement des lignes correspondantes.
Un paramètre extrêmement important pour tout produit en plastique est son apparence et sa fonctionnalité. Ces paramètres sont largement déterminés par la qualité des gabarits utilisés, c'est pourquoi des exigences particulières sont imposées à la fabrication de moules de coulée. Une précision de production élevée, le respect des normes techniques et des exigences établies permettent d'obtenir des produits fiables et de haute qualité. Toute nouvelle conception nécessite de nouveaux composants, et ceux qui sont usés doivent être remplacés régulièrement. L'utilisation de machines modernes sur les lignes de production garantit une demande croissante de produits et la prospérité de l'entreprise.