Circuit de démarrage de la chaudière TPP 210 a. Démarrage de chaudières à flux direct. Liste de la littérature utilisée
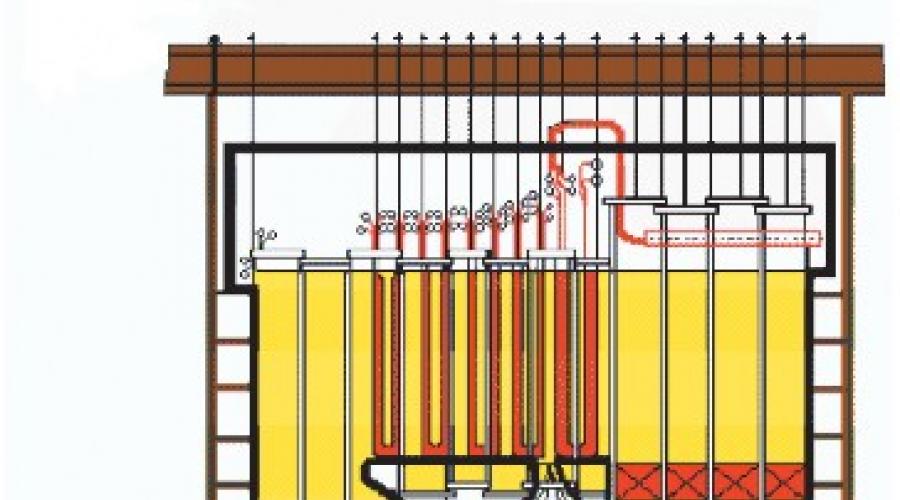
Lire aussi
Docteur en Sciences Techniques G.I. Levchenko, Ph.D. Yu.S. Novikov, Ph.D. P.N. Fedotov, ch.t.n. L.M. Khristich, Ph.D. SUIS. Kopeliovitch, Ph.D. Yu.I. Shapovalov, JSC TKZ "Krasny Kotelshchik"
Magazine "Heat Supply News", n° 12, (28), décembre 2002, pp. 25 - 28, www.ntsn.ru
(d'après un rapport du séminaire « Nouvelles technologies de combustion combustible solide: leur État actuel et utilisation à l'avenir", VTI, Moscou)
Au cours des dernières décennies, l’industrie énergétique nationale s’est largement concentrée sur le gaz et le pétrole. Compte tenu de la présence d’énormes gisements de combustibles solides dans le pays, cet état de fait ne peut guère être justifié pendant une longue période.
À cet égard, il faut reconnaître comme naturel que la « pause gazière » touche à sa fin et qu'il y ait une réorientation vers une expansion décisive de l'échelle d'utilisation de la houille, du lignite et de la tourbe.
Un certain nombre de facteurs y contribuent, notamment :
Une perspective socialement justifiée de relance de l’industrie charbonnière ;
Réduction du rythme de développement des gisements de gaz et des volumes de production gaz naturel;
Croissance de ses besoins d’exportation.
Un ensemble de problèmes financiers et de transport sur les marchés nationaux et étrangers des matières premières énergétiques complique l'adoption d'une stratégie durable et à long terme en matière de politique énergétique.
Dans ces conditions, TKZ OJSC n'a pas diminué son attention sur les questions de combustibles solides au fil des années et a continué à moderniser ses chaudières à charbon pulvérisé, en impliquant les forces scientifiques les plus autorisées (NPO TsKTI, VTI, ORGRES, etc.).
Les développements ont porté sur tous les types de chaudières produites par l'usine au cours des 20 à 30 dernières années. L'objectif principal de ces développements de modernisation est d'augmenter les performances environnementales et économiques des chaufferies, en les rapprochant le plus possible des normes mondiales. Cela a permis de préparer une quantité suffisante de développements techniques pour la mise en œuvre.
Dans ces travaux, les principaux domaines suivants peuvent être distingués, couvrant un large éventail de technologies de traitement et de combustion des combustibles :
1. Diverses modifications de la combustion étagée de combustible solide ;
2. Création d'installations hautement économiques et respectueuses de l'environnement.
Dans ces zones, toute la variété des combustibles russes est couverte : lignites et lignites des bassins de Kouznetsk, Kansk-Achinsk et d'Extrême-Orient, anthracite et ses déchets, tourbe, combustible charbon-eau.
Combustion étagée de combustibles solides
Actuellement émissions nocives dans les gaz de combustion des centrales électriques sont réglementés par deux normes de l'État GOST 28269-89 – pour les chaudières et GOST 50831-95 – pour les installations de chaudières.
Les exigences les plus strictes s’appliquent aux émissions des chaufferies brûlant du charbon pulvérisé. Pour répondre à ces normes lors de la combustion du charbon de Kuznetsk avec élimination des scories solides, il est nécessaire soit d'installer une installation de purification des gaz, soit de mettre en œuvre tous les moyens connus de suppression des NO X.
De plus, la possibilité de réduire les émissions de NO X à ces valeurs par des mesures techniques pour les charbons du bassin de Kuznetsk n'a pas encore été testée et nécessite une confirmation sur les chaudières avec les mesures mises en œuvre.
Une telle chaudière, TKZ, en collaboration avec Sibtekhenergo, a été développée sur la base de la chaudière TPE-214 et fournie au CHPP-5 de Novossibirsk. Sur cette chaudière pour les qualités de charbon « G » et « D », on utilise schéma en plusieurs étapes combustion : gradation horizontale et verticale dans la zone des brûleurs, ainsi que création d'une zone de réduction au-dessus des brûleurs utilisant le gaz naturel comme agent réducteur. L'aérodynamique du four, testée sur modèle réduit, est organisée de manière à éviter les scories des tamis dans tous les modes de fonctionnement de la chaudière. La mise en service de la chaudière TPE-214 au CHPP-5 de Novossibirsk nous permettra d'acquérir de l'expérience dans la maximisation de la réduction possible des émissions de NO X lors de la combustion en chambre de charbon à haute teneur en azote dans le combustible.
Pour la combustion de charbons de Kouzbass à faible réaction (mélanges de « T » et de « SS »), une chaudière TP-87M modernisée a été développée et fournie à la centrale électrique du district d'État de Kemerovo avec l'organisation d'une combustion de charbon en trois étapes dans des conditions de élimination des scories liquides. La chaudière utilise du PPVC de transport de poussière à haute concentration, des brûleurs à production réduite de NO X et des brûleurs spéciaux à poussière et à gaz pour créer une zone de réduction au-dessus des brûleurs principaux avec une utilisation minimale de gaz naturel (3 à 5 %). Pour brûler du charbon pauvre de Kuznetsk, TKZ et VTI reconstruisent les chaudières TP-80 et TP-87, ainsi que les chaudières TPP-210A de Mosenergo CHPP-22, qui utilisent également le PPVK et la combustion à trois étages au gaz naturel. comme agent réducteur.
Pour le charbon dans la région d'Extrême-Orient, un projet de reconstruction à faible coût de la chaudière TPE-215 a été réalisé grâce à une combustion à deux étages.
Pour les charbons du bassin de Kansk-Achinsk, l'usine, en collaboration avec CKTI et SibVTI, a développé et fourni au CHPP-2 de Krasnoïarsk une chaudière d'une capacité de vapeur de 670 t/h (TPE-216), qui utilise un trois- schéma de combustion par étapes utilisant poussière de charbon, et événements spéciaux pour protéger les grilles des scories : apport d'un mélange pauvre en combustible par les becs des brûleurs (GPCv) depuis le côté des grilles du four, soufflage d'air le long des grilles dans la zone de réduction et s'assurer que la température des gaz dans la zone de combustion active ne dépasse pas 1250 °C grâce à l'apport supplémentaire de 10 % de gaz de recirculation provenant de l'air secondaire.
Les mesures technologiques incluses dans le projet (organisation d'une combustion à basse température et augmentation de la teneur en oxyde de calcium dans les cendres) permettent non seulement d'assurer des émissions de NO X au niveau de 220-300 mg/m 3, mais aussi de S0 2 émissions ne dépassant pas 400 mg/m 3.
Pour la tourbe à haute humidité, des projets ont été développés pour la modernisation des chaudières TP-208 et TP-170-1 avec l'organisation d'une combustion à deux étages.
La combustion étagée du carburant dans ses diverses modifications est remède universel réduction significative des émissions de NO X, mais pour certains carburants avec contenu accru l'azote, l'utilisation de cette méthode, même en combinaison avec d'autres mesures intra-four, peut s'avérer insuffisante pour atteindre les exigences standard pour les houilles et les fours avec élimination des scories solides de 350 mg/m 3. Dans ce cas, il est conseillé d'utiliser la méthode de suppression des NO X avec une combinaison séquentielle de combustion en trois étapes et de réduction sélective non catalytique (SNCR) des NO X.
Création d'installations hautement économiques et respectueuses de l'environnement
S'appuyant sur de nombreuses années d'expérience dans la création et le développement de chaudières à vapeur pour centrales électriques pour presque tous les types de combustibles utilisés dans le secteur de l'énergie, l'usine a développé des projets de centrales électriques de nouvelle génération qui permettront de réaliser une percée dans fondamentalement nouveau niveau indicateurs techniques des équipements fabriqués.
Modernisation de la chaudière TPP-210 avec l'installation d'un four « épaule »
pour la combustion de charbon à faible réaction
Les difficultés connues de combustion de l'AS et les exigences environnementales croissantes soulèvent la question de l'amélioration continue du processus de combustion de l'AS, en particulier avec l'utilisation de fours dits « d'épaule » avec élimination des scories solides dans lesquels est brûlé un combustible à faible réaction et à haute teneur en cendres. sans éclairage dans la plage de charge utilisée dans la pratique, garantissant un fonctionnement à long terme de la chaudière.
Avantages d'un four « épaule » avec élimination des scories solides par rapport à la technologie utilisée pour brûler les cendres dans un four avec élimination des scories liquides :
Permet l'utilisation de dispositifs de brûleur avec basses vitesses mélange d'air, ce qui augmente le temps de séjour des particules dans la zone du brûleur, créant ainsi Conditions favorables réchauffer les particules et les enflammer ;
Un long séjour des particules dans la zone à haute température est obtenu (au moins 2 fois plus élevé que dans un foyer traditionnel), ce qui garantit une combustion satisfaisante du combustible ;
Permet l'introduction la plus pratique de l'air nécessaire à la combustion au fur et à mesure du développement de la torche ;
Beaucoup moins de difficultés d'élimination des scories ;
Moins de pertes dues à la brûlure mécanique ;
Réduction des émissions d’oxydes d’azote.
Pour un foyer « d'épaule », on utilise un brûleur à fente avec un espace entre les jets d'air primaire et secondaire, dont le principal avantage par rapport à un brûleur vortex :
Pas de mélange prématuré de l’air primaire avec l’air secondaire, ce qui a un effet bénéfique sur l’allumage ; .
Alimentation en air primaire dans la quantité nécessaire uniquement pour brûler les substances volatiles ;
Une combinaison rationnelle avec le foyer, permettant de créer grande multiplicité circulation des fumées jusqu'au pied du chalumeau (dans la zone d'allumage).
Un foyer « d'épaule » étanche au gaz et un TVP, dans la section transversale desquels un économiseur est installé, sont installés sur la chaudière modernisée jusqu'au puits de convection existant.
Combustion de pellets d'anthracite dégradés en lit fluidisé
La combustion est réalisée à l'aide de la technologie de l'Institut polytechnique de l'Altaï dont l'idée principale est la granulation préalable d'un mélange de broyat, de combustible d'origine, de cendres et de calcaire afin de rapprocher la composition du lit fluidisé d'un lit fluidisé monodispersé. mélange. OJSC TKZ "Krasny Kotelshchik" en collaboration avec l'auteur de la technologie a réalisé un projet visant à moderniser l'une des chaudières existantes TP-230 de la centrale électrique du district d'État de Nesvetai pour la combustion industrielle pilote de cendres granulaires de mauvaise qualité dans un lit fluidisé.
Actuellement, à la centrale électrique du district de Nesvetai, il est prévu d'installer une chaudière industrielle pilote D-220 t/h avec un lit fluidisé circulant, dont le développeur général et le fournisseur est Belenergomash OJSC. TKZ est co-exécuteur.
Centrale électrique pour traitements complexes, combustion de scories en fusion et utilisation de déchets de charbon peu réactifs
Au milieu du XXe siècle, le développement des centrales thermiques a suivi la voie d'une augmentation de la puissance unitaire et de l'efficacité des équipements électriques. Dans le même temps, dans les années 50 du XXe siècle, en URSS, ils ont commencé à construire des centrales thermiques avec des unités de puissance de 100, 150 et 200 MW, et dans les années 60, ils ont mis en service des centrales d'une capacité de 300, 500 et 800 MW. MW dans les centrales électriques. Une centrale électrique d'une capacité de 1 200 MW a également été mise en service. Ces blocs disposent de chaudières pour les paramètres de vapeur supercritique.
La transition des chaudières vers des paramètres de vapeur supercritique a été dictée par la faisabilité économique, qui a été déterminée par l'équilibre optimal des économies de combustible dues à une efficacité thermique accrue. cycle et une augmentation des coûts d’équipement et d’exploitation. Refus d'utiliser dans blocs puissants Les chaudières à tambour pour les paramètres de vapeur sous-critiques ont été déterminées par une augmentation significative du coût de la chaudière en raison d'une augmentation de la masse du tambour, qui pour une chaudière unitaire de 500 MW a atteint 200 tonnes. L'installation et le fonctionnement d'une telle chaudière deviennent. beaucoup plus compliqué, donc la puissance optimale des unités de puissance avec des chaudières à tambour supportant la charge de base ne dépasse pas 400 MW. À cet égard, lors de la création de blocs haute puissance Il a été décidé de passer à des chaudières à pression supercritique à passage unique.
Les premières chaudières à passage unique pour les unités de puissance de 300 MW, modèles TPP-110 et PK-39, et les chaudières pour les unités de puissance de 800 MW, les modèles TPP-200, TPP-200-1, ont été fabriquées au début des années 60 du 20e siècle. . Ils étaient constitués de deux corps. Les chaudières à vapeur TPP-110 et PK-39 ont été fabriquées avec une disposition asymétrique des surfaces chauffantes dans chaque boîtier (monobloc).
Dans la chaudière TPP-110, la partie principale du surchauffeur primaire est située dans un boîtier et le reste est situé dans le deuxième boîtier.
une partie de ce surchauffeur et toute la surface de chauffe du surchauffeur intermédiaire. Avec cette disposition des surchauffeurs, la température de la vapeur dans chacun d'eux est régulée en modifiant le rapport « eau d'alimentation - carburant ». De plus, la température de la vapeur intermédiaire est contrôlée dans l'échangeur thermique gaz-vapeur.
La redistribution de la charge thermique entre les corps, qui se produit lors de la régulation de la température de la vapeur, n'est pas souhaitable, car lors de la combustion de pellets d'anthracite et d'autres types de combustibles peu réactifs, la température de l'air chaud diminue, ce qui entraîne une augmentation de la chaleur. pertes dues à la sous-combustion du carburant.
En double coque chaudière à vapeur modèle PK-39, fabriqué selon une conception en forme de T, les surchauffeurs primaire et intermédiaire sont situés dans quatre puits de convection des bâtiments asymétriquement par rapport à l'axe vertical de la chaudière. Lorsque la quantité de produits de combustion dans les puits de convection droit et gauche de chaque bâtiment change, une redistribution de l'absorption de chaleur par les surchauffeurs primaires et intermédiaires se produit, ce qui entraîne une modification de la température de la vapeur. Dans une chaudière à vapeur à double coque avec corps symétriques des modèles TPP-200, TPP-200-1, les puits convectifs de chaque corps sont divisés en trois parties par des cloisons verticales. Dans la partie médiane de l'arbre convectif se trouvent les packages d'un économiseur d'eau, dans les deux parties les plus extérieures se trouvent les packages d'un surchauffeur convectif. haute pression et intermédiaire.
L'expérience d'exploitation des chaudières TPP-110 a confirmé la possibilité de réguler la température de la vapeur primaire et intermédiaire en modifiant le rapport eau alimentaire-combustible dans chacun des bâtiments. Parallèlement, lors du fonctionnement de ces chaudières, un nombre accru d'arrêts d'urgence a été observé. Le fonctionnement des chaudières est devenu nettement plus compliqué. Une image similaire a été observée lors du fonctionnement d'essai de la chaudière PK-39.
Par la suite, à la place de ces chaudières, des unités à double boîtier ont été produites, mais avec une disposition symétrique des surfaces chauffantes dans les boîtiers - blocs doubles (TPP-210, TPP-210A, TGMP-114, PK-41, PK-49, P -50).
L'utilisation de chaudières à double corps avec une disposition symétrique des surfaces chauffantes augmente la fiabilité de l'unité de puissance. À arrêt d'urgence Dans l'un des bâtiments, la centrale peut fonctionner avec une charge réduite sur l'autre bâtiment. Cependant, travailler avec un seul organisme est moins économique. Les inconvénients des chaudières à double coque incluent également la complexité de la disposition des canalisations, un grand nombre de raccords, augmentation du coût.
L'expérience du fonctionnement d'unités de puissance avec des chaudières à pression supercritique a montré que le taux d'utilisation des unités à un boîtier n'est pas inférieur à celui de deux. De plus, en raison de la réduction du nombre de raccords et d'instruments vapeur-eau régulation automatique l'entretien des groupes motopropulseurs équipés de chaudières à simple boîtier est simplifié. Ces circonstances ont déterminé la transition vers la production de chaudières à pression supercritique monocoque.
La chaudière à vapeur TPP-312A d'une capacité de vapeur de 1 000 t/h (Fig. 2.13) est conçue pour fonctionner au charbon dans une unité dotée d'une turbine de 300 MW. Il produit de la vapeur surchauffée avec une pression de 25 MPa et une température de 545°C et est efficace. 92%. La chaudière est une chaudière monobloc réchauffée en forme de U avec une chambre de combustion prismatique ouverte. Les écrans le long de la hauteur de la chambre de combustion sont divisés en quatre parties : la partie inférieure de rayonnement, celle du milieu, composée de deux parties, et la partie supérieure de rayonnement. La partie inférieure de la chambre de combustion est protégée par des tuyaux cloutés recouverts de carborundum. L'élimination des scories est liquide. A la sortie de la chambre de combustion se trouve un surchauffeur à écran, dans le puits convectif se trouvent des surchauffeurs convectifs de haute et basse pression. La température de la vapeur haute pression est contrôlée par injection d'eau alimentaire, et celle de la vapeur basse pression par un échangeur thermique vapeur-vapeur. Le chauffage de l'air est réalisé dans des aérothermes régénératifs.
Les chaudières à pression supercritique monocoquille suivantes ont été développées et sont en service : charbon pulvérisé TPP-312, P-57, P-67, chaudières à gazole TGMP-314, TGMP324, TGMP-344, TGMP-204, TGMP- 1204. En 2007, TKZ "Krasny Kotelshchik" a fabriqué des chaudières TPP-660 d'une capacité de vapeur de 2225 t/h et d'une pression de vapeur à la sortie de 25 MPa pour les groupes motopropulseurs du TPP "Bar" (Inde). La durée de vie des chaudières est de 50 ans.
Dans la dernière centrale électrique de la TPP de Hemweg aux Pays-Bas (voir section 4), une chaudière à vapeur à double passage utilisant la technologie Benson a été installée (Fig. 2.14) avec une capacité de vapeur à pleine charge de 1980 t/h, conçue par Mitsui. Babcock Energy et conçu pour fonctionner au charbon (comme principal type de combustible) et au gaz dans une unité dotée d'une turbine d'une capacité de 680 MW.
Cette chaudière à rayonnement à pression supercritique produit de la vapeur avec une pression de 26 MPa et une température de 540/568°C.
Il fonctionne selon un mode de pression glissante modifiée, dans lequel la pression d'entrée de la turbine est ajustée à un niveau qui varie en fonction de la charge unitaire.
La chaudière est équipée de trois surchauffeurs avec désurchauffeurs à injection intermédiaire et de deux batteries de réchauffeurs (bien qu'il s'agisse d'un seul cycle de réchauffage). L'économiseur est un serpentin horizontal de tuyaux avec une surface nervurée. Le surchauffeur primaire est conçu comme un bloc horizontal et un bloc vertical. Le surchauffeur à écran secondaire est une unité suspendue à circuit unique, et le dernier étage du surchauffeur est également conçu comme une unité suspendue à circuit unique. La température de la vapeur vive en sortie de chaudière est de 540°C. Le système de réchauffeur de chaudière comporte deux étages : primaire et final. L'étage primaire comprend deux blocs horizontaux, l'étage final de réchauffage est représenté par un bloc vertical en forme de circuit replié situé dans le conduit de la chaudière. En sortie de chaudière la température de la vapeur surchauffée est de 568°C.
Le système de soufflerie de suie de la chaudière se compose de 107 souffleurs pilotés par un automate programmable. L'élimination des résidus de cendres s'effectue par un convoyeur racleur passant sous le foyer et un transport hydraulique jusqu'au réservoir de filtration des résidus de cendres.
Température gaz de combustionà la sortie est d'environ 350°C. Ils sont ensuite refroidis à 130°C dans des aérothermes rotatifs régénératifs.
La chaudière est conçue pour minimiser les émissions de NOx grâce à l'utilisation de brûleurs à faible teneur en NOx et à une pression de soufflage élevée. L'obtention de bonnes performances environnementales est facilitée par la désulfuration des fumées, qui permet d'éliminer le SO 2 des gaz d'échappement.
La chaudière à vapeur gazole moderne TGMP-805SZ (Fig. 2.15) d'une capacité de vapeur de 2650 t/h est conçue pour produire de la vapeur surchauffée avec une pression de fonctionnement de 25,5 MPa et une température de 545 °C pour une turbine à vapeur avec un capacité de 800 MW. La chaudière est à flux direct, au gazole, monocoque, suspendue sur des poutres centrales supportées par les colonnes du bâtiment chaufferie, et peut être installée dans des zones de sismicité de 8 points. Il possède une chambre de combustion ouverte de forme prismatique. Il est formé de panneaux tubulaires entièrement soudés, dans la partie inférieure desquels se trouve un écran inférieur horizontal entièrement soudé, et dans la partie supérieure il y a un conduit de fumée horizontal, fermé sur le dessus par un écran de plafond tubulaire entièrement soudé. Les grilles de la chambre de combustion sont divisées en hauteur en parties de rayonnement inférieure et supérieure.
Il y a 36 brûleurs à gazole situés sur les parois avant et arrière de la chambre de combustion de la chaudière. Dans le conduit de gaz horizontal, cinq surfaces chauffantes par convection verticales sont placées séquentiellement le long du flux de gaz - une surface chauffante génératrice de vapeur incluse dans le trajet vapeur-eau de la chaudière jusqu'à la vanne intégrée, trois parties du haut- surchauffeur à pression et l'étage de sortie du surchauffeur basse pression.
La température de la vapeur secondaire est contrôlée à l'aide de gaz de recirculation. Dans le conduit de gaz inférieur, protégé par des panneaux tubulaires entièrement soudés, l'étage d'entrée du surchauffeur de vapeur basse pression et l'économiseur d'eau sont situés séquentiellement le long du flux de gaz.
L'une des réalisations les plus importantes de l'ingénierie thermique dans le monde à la fin du XXe siècle a été l'introduction de chaudières supersupercritiques, qui sont actuellement capables de fonctionner à une pression de vapeur de sortie de 30 MPa et à une température de 600/650°C. . Cela a été rendu possible grâce aux progrès de la technologie des matériaux capables de résister à des conditions de température et de pression élevées. La « grande industrie énergétique » exploite déjà des chaudières (on les appelle plus souvent « générateurs de vapeur ») d'une capacité de plus de 4 000 t/h. De telles chaudières fournissent de la vapeur à des unités de puissance de 1 000 à 1 300 MW dans des centrales électriques aux États-Unis, en Russie, au Japon et dans certains pays européens.
Actuellement, le développement de nouveaux modèles de chaudières à vapeur pour les unités de puissance des centrales thermiques se poursuit. Dans ce cas, les chaudières sont conçues pour les paramètres de vapeur super-supercritique, supercritique et sous-critique. Par exemple, sur 2 centrales électriques du TPP de Neyveli (Inde) d'une capacité de 210 MW chacune, chaudières à vapeur Ep-690-15.4-540 LT, conçu pour fonctionner sur les lignites indiens à faible teneur en calories. Ce sont des chaudières à tambour avec circulation naturelle, pression sous-critique avec réchauffage, monocoque, avec élimination des scories solides, type tour. La capacité de vapeur d'une telle chaudière est de 690 t/h, les paramètres de vapeur sont de pression 15,4 MPa en sortie de chaudière et 3,5 MPa en sortie de réchauffeur, température de vapeur 540°C.
La chambre de combustion de la chaudière est ouverte et équipée de 12 brûleurs multicanaux à flux direct appariés installés sur toutes les parois du foyer sur deux niveaux. Des souffleurs d'eau et de vapeur sont installés pour nettoyer les surfaces chauffantes.
Il est à noter que le secteur énergétique des pays de la CEI repose sur l'utilisation de deux types de chaudières à vapeur : les chaudières à flux direct et à circulation naturelle. Dans la pratique étrangère, outre les chaudières à passage unique, les chaudières à circulation forcée sont largement utilisées.
En plus des principales - chaudières à vapeur à haute et pression supercritique - d'autres types de chaudières sont actuellement utilisés dans les centrales thermiques : chaudières à eau de pointe, chaudières pour brûler du charbon en lit fluidisé, chaudières à lit fluidisé circulant et chaleur résiduelle chaudières. Certaines d'entre elles deviendront des prototypes de chaudières pour le développement futur de l'ingénierie thermique.
Fil S. A., Golyshev L. V., ingénieurs, Mysak I. S., docteur en ingénierie. Sciences, Dovgoteles G. A., Kotelnikov I. I., Sidenko A. P., ingénieurs d'OJSC LvovORGRES - Université nationale« École polytechnique de Lviv » - Centrale thermique de Trypilska
Combustion de houille peu réactive (rendement Vdaf volatil)< 10%) в камерных топках котельных установок сопровождается повышенным механическим недожогом, который характеризуется двумя показателями: содержанием горючих в уносе Гун и потерей тепла от механического недожога q4.
Généralement, le pistolet est déterminé par une méthode de laboratoire utilisant des échantillons de cendres uniques prélevés dans les conduits de fumée de la dernière surface convective de la chaudière à l'aide d'unités d'entraînement standard. Le principal inconvénient de la méthode de laboratoire est le délai trop long pour obtenir le résultat Gong (plus de 4 à 6 heures), qui comprend le temps d'accumulation lente de l'échantillon de cendres dans l'unité volante et la durée de l'analyse en laboratoire. Ainsi, dans un seul échantillon de cendres, toutes les modifications possibles du gong sont résumées sur une longue période de temps, ce qui rend difficile une analyse rapide et mise en œuvre de haute qualité réglage et optimisation du mode de combustion.
Selon les données, dans les modes de chaudière variables et non stationnaires, le coefficient de collecte des cendres (degré de purification) du cyclone, le point de consigne d'emport, varie dans la plage de 70 à 95 %, ce qui entraîne des erreurs supplémentaires dans déterminer le Gong.
Les inconvénients des usines de cendres volantes sont éliminés en introduisant des systèmes de mesure continue Gong, par exemple des analyseurs de carbone dans les cendres volantes.
En 2000, huit ensembles (deux pour chaque bâtiment) d'analyseurs RCA-2000 stationnaires fonctionnant en continu de Mark et Wedell (Danemark).
Le principe de fonctionnement de l'analyseur RCA-2000 est basé sur la méthode d'analyse par photoabsorption dans la région infrarouge du spectre.
Plage de mesure 0 - 20% valeurs absolues Gong, erreur relative mesures comprises entre 2 et 7 % - pas plus de ± 5 %.
Échantillonnage de cendres pour Système de mesure L'analyseur est réalisé à partir de conduits de gaz devant des précipitateurs électriques.
Un enregistrement continu des Gongs a été réalisé sur un enregistreur de salle de contrôle avec une fréquence d'un cycle complet de mesure toutes les 3 minutes.
Lors de la combustion de cendres de composition et de qualité variables, les valeurs absolues réelles du Gong dépassaient généralement 20 %. Par conséquent, à l'heure actuelle, les analyseurs sont utilisés comme indicateurs de changements dans les valeurs relatives de la teneur en combustibles dans l'entraînement Gv° dans l'échelle d'un enregistreur 0 - 100 %.
Pour une évaluation approximative du niveau de Gong réel, une caractéristique d'étalonnage de l'analyseur a été compilée, qui représente la relation entre les valeurs absolues de Gong déterminées par la méthode de laboratoire et les valeurs relatives de l'analyseur de Gong. Dans la plage de Gong varie de 20 à 45 %, la caractéristique sous forme analytique est exprimée par l'équation
Lors d'études expérimentales et de fonctionnement normal de la chaudière, les analyseurs peuvent être utilisés pour effectuer les travaux suivants :
optimisation du mode de combustion ;
évaluation des changements de Gong lors des commutations technologiques planifiées des systèmes et des unités d'une chaufferie ;
déterminer la dynamique et le niveau de réduction du rendement dans les modes non stationnaires et post-démarrage de la chaudière, ainsi que lors de la combustion alternée des cendres et du gaz naturel.
Lors des tests thermiques de la chaudière, des analyseurs ont été utilisés pour optimiser le mode de combustion et évaluer l'impact de la commutation prévue des équipements sur la stabilité du processus de combustion du charbon pulvérisé.
Les expériences ont été réalisées avec des charges de chaudière fixes comprises entre 0,8 et 1,0 nominal et une combustion de cendres avec les caractéristiques : la plus basse chaleur spécifique combustion Qi = 23,06 - 24,05 MJ/kg (5 508 - 5 745 kcal/kg), teneur en cendres par masse utile Ad = 17,2 - 21,8 %, humidité par masse utile W = 8,4 - 11,1 % ; la part du gaz naturel destiné à éclairer la torche de charbon pulvérisé représentait 5 à 10 % du dégagement de chaleur total.
Les résultats et analyses d'expériences visant à optimiser le régime de combustion à l'aide d'analyseurs sont présentés dans. Lors de la mise en place de la chaudière, les éléments suivants ont été optimisés :
vitesses de sortie de l'air secondaire en faisant varier l'ouverture des registres périphériques des brûleurs ;
vitesses de sortie d'air primaire en modifiant la charge du ventilateur à vent chaud ;
la part de l'éclairage des torchères au gaz naturel en sélectionnant (en fonction des conditions permettant d'assurer la stabilité de la combustion) le nombre minimum possible de brûleurs à gaz en fonctionnement.
Les principales caractéristiques du processus d'optimisation du mode de combustion sont données dans le tableau. 1.
Donné dans le tableau. 1 les données indiquent le rôle important des analyseurs dans le processus d'optimisation, qui consiste en une mesure continue et un enregistrement des informations actuelles sur les changements de G°, ce qui permet de mesurer en temps opportun et
enregistrer clairement le mode optimal, l'achèvement du processus de stabilisation et le démarrage du fonctionnement de la chaudière en mode optimal.
Lors de l'optimisation du régime de combustion, l'attention principale a été portée à la recherche du niveau minimum possible de valeurs relatives de G°un. Dans ce cas, les valeurs absolues de Gong ont été déterminées à partir des caractéristiques d'étalonnage de l'analyseur.
Ainsi, l'efficacité de l'utilisation d'analyseurs pour optimiser le mode de combustion d'une chaudière peut être évaluée grossièrement en réduisant la teneur en combustibles dans l'entraînement de 4 % en moyenne et les pertes de chaleur dues à la sous-combustion mécanique de 2 %.
Dans les modes de chaudière fixes, la réalisation de commutations technologiques standard, par exemple dans les systèmes de poussière ou les brûleurs, perturbe le processus de combustion stable du combustible de charbon pulvérisé.
Tableau 1
Caractéristiques du processus d'optimisation du mode de combustion
La chaudière TPP-210A est équipée de trois systèmes de dépoussiérage avec des broyeurs à tambour à boulets de type ShBM 370/850 (Sh-50A) et d'un bac à poussière commun.
Depuis le système de poussière, l'agent de séchage usé est évacué à l'aide d'un ventilateur de broyeur de type MV 100/1200 dans la chambre de combustion (pré-four) via des buses d'évacuation spéciales situées au-dessus des brûleurs principaux à poussière et à gaz.
Le pré-four de chaque corps de chaudière reçoit une décharge complète du système anti-poussière extrême correspondant et la moitié de l'évacuation du système anti-poussière intermédiaire.
L'agent de séchage usé est de l'air humidifié et poussiéreux à basse température, dont les principaux paramètres se situent dans les limites suivantes :
la part de l'air évacué est de 20 à 30 % de la consommation totale d'air du logement (chaudière) ; température 120 - 130°C ; la part de fines poussières de charbon qui n'ont pas été captées par le cyclone du système de dépoussiérage, 10 à 15 % de la productivité du broyeur ;
L'humidité correspond à la quantité d'humidité libérée lors du processus de séchage du combustible de travail broyé.
L'agent de séchage usé est déchargé dans la zone de températures de flamme maximales et affecte donc de manière significative l'intégralité de la combustion des poussières de charbon.
Lors du fonctionnement de la chaudière, le système de poussière intermédiaire est le plus souvent arrêté et redémarré, à l'aide duquel le niveau de poussière requis est maintenu dans le bac à poussière.
La dynamique des changements dans les principaux indicateurs du mode de combustion du corps de chaudière - la teneur en combustibles dans l'entraînement et la concentration massique d'oxydes d'azote dans les gaz de combustion (NO) - lors d'un arrêt planifié du système de poussière moyen est présentée En figue. 1.
Dans les figures ci-dessus et toutes les suivantes, les conditions suivantes sont acceptées lors de la construction de dépendances graphiques :
la teneur en combustibles dans l'entraînement correspond aux valeurs des échelles de deux axes verticaux coordonnées : mesures moyennes du GUN et données de recalcul basées sur la caractéristique d'étalonnage du Gong ;
la concentration massique de NO avec excès d'air dans les gaz de combustion (sans réduction en NO2) a été prise à partir de mesures enregistrées en continu analyseur de gaz stationnaire Mars-5 MP « Ekomak » (Kiev) ;
la dynamique des changements de G°un et NO est fixée à
pendant toute la durée du fonctionnement technologique et du mode de stabilisation ; le début de l'opération technologique est supposé être proche du rapport de temps zéro.
L'exhaustivité de la combustion du charbon pulvérisé a été évaluée par la qualité du régime de combustion (KFC), qui a été analysée par deux indicateurs Gun et NO, qui, en règle générale, variaient dans des directions opposées.
Riz. 1. Modifications des indicateurs de mode de combustion lors de l'arrêt du système de poussière intermédiaire
L'effet d'un arrêt planifié d'un système à poussière moyenne sur les indicateurs CTE (Fig. 1) a été analysé en fonction de la séquence des éléments suivants opérations technologiques:
opération 1 - l'arrêt de l'alimentation en charbon brut (CCF) et l'arrêt de l'alimentation en charbon du broyeur ont réduit le chargement du tambour CBM, réduit la finesse de broyage de la poussière de charbon et augmenté la température de l'air vicié, ce qui a provoqué un court terme amélioration du CTE : diminution du Gun° et augmentation du NO ; le processus d'émasculation supplémentaire du broyeur a contribué à l'élimination de la poussière de l'air résiduaire et à une augmentation de l'excès d'air dans le pré-four, ce qui a affecté négativement le CTE ;
opération 2 - l'arrêt du ventilateur du broyeur et la réduction de la ventilation du système de poussière ont d'abord légèrement amélioré le CTE, puis, avec un retard dans l'arrêt du ventilateur du broyeur (MF), le CTE s'est détérioré ;
opération 3 - l'arrêt de la MV et l'arrêt de l'évacuation de l'agent de séchage usé dans la chambre de combustion ont considérablement amélioré le CTE.
Ainsi, toutes choses étant égales par ailleurs, l’arrêt du système anti-poussière a amélioré le processus de combustion du carburant, réduisant la sous-combustion mécanique et augmentant la concentration massique de NO.
Une violation typique de la stabilité du système de poussière consiste à surcharger le tambour du broyeur avec du carburant ou à « enduire » les billes de broyage avec de l'argile humide.
L'influence d'un dessèchement prolongé du tambour de la fraise sur le CTE du corps de la chaudière est illustrée à la Fig. 2.
L'arrêt du PSU (opération 1) pour des raisons similaires à celles envisagées lors de l'arrêt du système de poussière, lors de la première étape d'émasculation du broyeur, a amélioré à court terme le CTE. Lors de l'émasculation ultérieure du broyeur jusqu'à l'inclusion du PSU (opération 2), une tendance à la détérioration du CTE et à une augmentation du G°un a été observée.
Riz. 2. Modifications des conditions de combustion lorsque le tambour de la fraise est vidé
Riz. 3. Modifications des indicateurs de mode de combustion lors du démarrage du système de poussière extrême et de l'arrêt des brûleurs à gaz
Dans une moindre mesure, le mode de combustion est périodiquement déstabilisé par le fonctionnement automatique du PSU, qui régule le chargement nécessaire du broyeur en charbon en éteignant puis en rallumant le lecteur PSU.
L'influence du mode de démarrage du système de poussière extrême sur le CTE est illustrée à la Fig. 3.
L'influence suivante des opérations de démarrage du système anti-poussière sur le mode de combustion a été notée :
opération 1 - le démarrage de la VM et la ventilation (réchauffement) du trajet du système anti-poussière avec rejet d'air relativement froid dans le pré-four ont augmenté l'excès d'air dans la zone de combustion et réduit la température de la flamme, ce qui a entraîné une détérioration de la CTE ;
opération 2 - le démarrage du BBM et la poursuite de la ventilation du tractus ont eu un effet négatif sur le CTE ;
opération 3 - le démarrage du PSU et le chargement du broyeur en combustible avec une augmentation de la consommation d'agent de séchage jusqu'à la consommation nominale ont considérablement détérioré le CTE.
On peut conclure que l'inclusion d'un système anti-poussière en fonctionnement affecte négativement le CTE, augmentant la sous-combustion mécanique et réduisant la concentration massique de NO.
Le pré-foyer du corps de chaudière TPP-210A est équipé de six brûleurs à poussière et à gaz à pales à volutes d'une puissance thermique de 70 MW, installés sur un niveau sur les parois avant et arrière, et de deux brûleurs gazole au-dessus du sol. pour assurer une élimination stable des scories liquides sur toute la plage de charges de fonctionnement de la chaudière.
Lors de la combustion de poussières de charbon de cendres, le gaz naturel était fourni à un débit constant (environ 5 % du dégagement de chaleur total) aux brûleurs aériens et à un débit variable à travers les brûleurs principaux à gaz de poussière pour stabiliser le processus de combustion du charbon pulvérisé. carburant. Le gaz était fourni à chaque brûleur principal au débit minimum possible, correspondant à 1,0 à 1,5 % du dégagement de chaleur total. Ainsi, la modification de la part du gaz naturel pour l'éclairage des torches a été réalisée en allumant ou en éteignant un certain nombre de brûleurs principaux à gaz.
L'effet de l'arrêt des brûleurs à gaz (réduction de la part de gaz naturel) sur le CTE du corps de la chaudière est illustré à la Fig. 3.
L'arrêt consécutif d'un brûleur à gaz (opération 4), puis de trois brûleurs à gaz (opération 5) a eu un effet positif sur le CTE et a conduit à une réduction significative de la sous-combustion mécanique.
L'effet de l'allumage des brûleurs à gaz (augmentation de la part du gaz naturel) sur le CTE est illustré à la Fig. 4. L'activation séquentielle d'un brûleur à gaz (opération 1), de deux brûleurs (opération 2) et d'un brûleur (opération 3) a affecté négativement le CTE et a considérablement augmenté la sous-combustion mécanique.
Riz. 4. Modifications des indicateurs de mode de combustion lors de l'allumage des brûleurs à gaz
Tableau 2
Modifications de la teneur en combustibles entraînés lors du changement de processus de l'équipement
Équipement | Mode | ||
diminuer | augmenter |
||
Système pour poussières extrêmes/moyennes | |||
Émasculation | Urgence | ||
Mangeoire crue | |||
Brûleur principal à gaz | Fermer | ||
Inclusion |
Une évaluation approximative de l'influence d'une commutation technologique éprouvée des équipements de chaudière sur l'évolution du CTE (Kun) est résumée dans le tableau. 2.
L'analyse des données présentées montre que la plus grande diminution de l'efficacité d'une installation de chaudière en modes stationnaires se produit à la suite du démarrage du système de poussière et d'une consommation excessive de gaz naturel pour l'éclairage des torchères.
Il convient de noter que la nécessité d'effectuer des opérations de démarrage du système anti-poussière est déterminée uniquement par des raisons technologiques et que la consommation excessive de gaz naturel pour l'éclairage des torches est, en règle générale, établie par le personnel d'exploitation afin d'éviter violations possibles stabilité du processus de combustion en cas de détérioration brutale de la qualité de l'AS.
L'utilisation des analyseurs RCA-2000 permet des changements continus en temps opportun
évaluer tout changement dans la qualité du carburant et maintenir constamment la valeur d'éclairage de la flamme au niveau optimal approprié avec un minimum dépense nécessaire le gaz naturel, qui permet de réduire la consommation de combustible gazeux rare et d'augmenter l'efficacité de la chaudière.
conclusions
- Le système de mesure continue de la teneur en combustibles dans l'entraînement permet une évaluation rapide et de haute qualité de la progression des processus de combustion lors de la combustion des cendres dans la chaudière TPP-210A, dont l'utilisation est recommandée lors de la mise en service et travail de recherche, ainsi que pour le contrôle systématique de l'efficacité des équipements de chaudière.
- L'efficacité de l'utilisation des analyseurs RCA-2000 pour optimiser les conditions de combustion est estimée approximativement en réduisant les indicateurs de sous-combustion mécanique - la teneur en combustibles dans l'entraînement de 4 % en moyenne et, par conséquent, la perte de chaleur due à la sous-combustion mécanique de 2 %.
- Dans les modes de chaudière stationnaires, la commutation technologique standard des équipements affecte la qualité du processus de combustion. Les opérations de démarrage du système de dépoussiérage et la consommation excessive de gaz naturel pour allumer la torche à charbon pulvérisé réduisent considérablement l'efficacité de l'installation de la chaudière.
Bibliographie
- Madoyan A.A., Baltyan V.N., Grechany A.N. Combustion efficace charbons de faible qualité dans chaudières à énergie. M. : Energoatomizdat, 1991.
- Utilisation de l'analyseur de contenu combustible RCA-2000 et de l'analyseur de gaz Mars-5 pour optimiser le mode de combustion de la chaudière à charbon pulvérisé TPP-210A du TPP Tripolskaya/ Golyshev L.V., Kotelnikov N.I., Sidenko A.P. et al. Institut polytechnique de Kyiv. Énergie : économie, technologie, écologie, 2001, n°1.
- Zusin S.I. Evolution des déperditions thermiques avec sous-combustion mécanique en fonction du mode de fonctionnement de la chaudière. - Génie thermique de l'énergie, 1958, n° 10.
Brève description de la chaudière « Chaudière à flux direct type TPP-210 »
Brève description de la chaudière Une chaudière à passage unique de type TPP-210 (p/p 950-235 GOST 3619-59 modèle TKZ TPP-210) avec une capacité de vapeur de 950 tonnes par heure pour les paramètres de vapeur supercritique a été conçue et fabriquée par l'usine de Taganrog "Krasny Kotelshchik". Le groupe chaudière est conçu pour fonctionner dans une unité avec une turbine à condensation K-300-240 d'une puissance de 300 MW, fabriquée par KhTGZ. La chaudière est conçue pour brûler les chaumes d'anthracite lors de l'élimination des scories liquides et du gaz naturel du champ Shebelinskoye. L'unité de chaudière est composée de deux boîtiers avec une disposition en forme de U de chaque boîtier et d'aérothermes à régénération retirés du dessous de la chaudière et situés à l'extérieur du bâtiment de la chaufferie. Corps de chaudière de même conception d'une capacité de 475 t/heure de vapeur chacun. Les boîtiers peuvent fonctionner indépendamment les uns des autres. Données générales sur la chaudière : Capacité 475 t/heure Température de vapeur surchauffée : primaire 565 °C Secondaire 565 °C Consommation de vapeur secondaire 400 t/heure Pression de vapeur primaire derrière la chaudière 255 kg/cm2 Pression de vapeur secondaire à l'entrée de la chaudière 39,5 kg/ cm² Pression de la vapeur secondaire à la sortie de la chaudière 37 kg/cm² Température de la vapeur secondaire à l'entrée 307 °C Température de l'eau d'alimentation 260 °C Température de l'air chaud 364 °C Poids total du métal de la chaudière 3438 t Largeur de la chaudière le long les axes des colonnes 12 m Profondeur de la chaudière le long des axes des colonnes 19 m Hauteur de la chaudière 47 m Volume d'eau du groupe chaudière à froid 243 m Dimensions du foyer en plan (le long des axes des canalisations) : Dans le zone de NRCh 10800x7550 Dans la zone de VRCH 10725x7592,5 (Conformément aux instructions de la circulaire opérationnelle n° T-4/71, la température de la vapeur primaire et secondaire surchauffée en sortie est réduite à 545 °C) La chaudière est desservie par deux extracteurs de fumées axiaux, deux ventilateurs soufflants avec moteurs à deux vitesses et deux ventilateurs à vent chaud. Schéma de préparation des poussières avec trémie à poussière et transport des poussières vers les brûleurs par air chaud. La chaudière est équipée de trois broyeurs à boulets à tambour ШБМ-50 d'une capacité de 50 tonnes de poussière par heure. Surfaces de chauffe : Grilles de four 1317 m² Dont : NRCh 737 m² VRCh 747 m² Grilles Caméra PTZ et plafond 1674 m² Surchauffeur SVD : a) écrans 1 er 510 m² b) écrans 2 er 594 m² Surchauffeur à convection 1674 m² Surchauffeur SVD, comprenant : Échangeur de chaleur à vapeur 800 m² Ensemble convectif intermédiaire 1994 m² Aérotherme 78730 m² Rendement ensemble convectif 1205 m² Convectif économiseur 1994 m² Schéma du parcours vapeur-eau Le parcours vapeur-eau ultra haute pression (SVD) de la chaudière est double flux avec régulation indépendante alimentation et température pour chaque flux.
Il y a deux flux dans chaque corps de chaudière (dans la description de la chaudière et dans la notice le flux est appelé un thread). Étant donné que la conception des boîtiers est similaire, le schéma et la conception d'un boîtier seront décrits ultérieurement. L'eau d'alimentation à une température de 260 °C traverse l'unité d'alimentation et pénètre dans les chambres d'entrée de l'économiseur d'eau Ш325*50, qui sont également les poutres de support les plus extérieures de l'emballage. Après avoir traversé les serpentins de l'économiseur d'eau, l'eau à une température de 302 °C pénètre dans les chambres de sortie Ø235*50, qui sont les poutres de support médianes de cette surface. Après l'économiseur d'eau, l'eau est dirigée à travers des tuyaux de dérivation Sh159*16 vers les poutres de support médianes de cette surface à travers des tuyaux Sh133*15 et est dirigée vers la partie inférieure (NRF). Les écrans NRF sont constitués de panneaux séparés et les surfaces chauffantes inférieures, ainsi que l'avant et l'arrière, sont des rubans multi-passes monoblocs. L'alimentation en eau des panneaux s'effectue par chambre basse, et la sortie se fait par le haut. Cette disposition des chambres d'entrée et de sortie améliore les performances hydrauliques du panneau. Le schéma d'écoulement du fluide le long des grilles NRF est le suivant : d'abord, le fluide pénètre dans les panneaux arrière des grilles et les panneaux arrière des grilles latérales, puis à travers les tuyaux de dérivation Ø 135*15, il est dirigé vers la grille avant et les parois avant. panneaux des écrans latéraux. Des rondelles Ø30 mm sont installées sur les canalisations de dérivation pour améliorer l'hydrodynamisme. Après le NRF, le milieu avec une température de 393 °C est envoyé par les tuyaux Ш133*15 vers le collecteur vertical Ш273*45, et de là, par les tuyaux de dérivation Ш133*15, entre dans les écrans latéraux et avant de la partie supérieure de rayonnement (URP ). Aux panneaux VRF arrangement mutuel les chambres d'entrée et de sortie sont similaires aux panneaux NRF. Après avoir traversé les panneaux multi-passes des écrans avant et latéraux du magnétoscope, la vapeur est dirigée par des tuyaux de dérivation Ш133*15 vers le collecteur mélangeur vertical Ш325*45, et de là par des tuyaux Ш159*16 elle entre dans le collecteur en forme de N. panneaux de la lunette arrière du magnétoscope.
Après avoir traversé les panneaux multipasses des écrans avant et latéraux du VRCH, la vapeur est dirigée à travers les tuyaux de dérivation Sh133*15 dans le collecteur mélangeur vertical Sh325*45, et après chauffage à 440 °C dans les surfaces de rayonnement du four, la vapeur est envoyée à travers les tuyaux de dérivation Sh149*16 vers les panneaux des parois latérales de blindage et arrière des caméras rotatives. Après avoir traversé les tamis de la chambre rotative, la vapeur entre par des tubes dans 1 désurchauffeur à injection Ш279*36. Dans un désurchauffeur à 1 injection, les flux sont transférés sur toute la largeur du conduit de gaz. Après le désurchauffeur, la vapeur est amenée au surchauffeur de plafond par des tuyaux Ш159*16. Dans un surchauffeur de plafond, la vapeur s'échappe de mur arrière le conduit de fumée se dirige vers l'avant de la chaudière et avec une température de 463 °C pénètre dans les chambres de sortie du plafond Ø273*45. Sur les conduites de vapeur Sh273*39, qui prolongent les chambres de sortie du surchauffeur de plafond, des vannes DU-225 (VZ) intégrées au conduit sont installées. Après le surchauffeur de plafond, les flux sont transférés sur toute la largeur du conduit de gaz et la vapeur est dirigée par des tuyaux Ш159*18 vers les grilles d'entrée du premier étage du surchauffeur à tamis, situées dans la partie médiane du conduit de gaz. Après avoir traversé les grilles d'entrée, la vapeur à une température de 502 °C entre dans le deuxième désurchauffeur à injection Ш325*50, après quoi elle est dirigée vers les grilles de sortie du premier étage situées le long des bords du conduit de fumée. La chambre de réception de vapeur des tamis d'entrée et la conduite de vapeur du transfert du deuxième désurchauffeur s'étendent sur toute la largeur du conduit de gaz. Avant la deuxième injection se trouve une conduite de vapeur Ш194*30 pour évacuer une partie de la vapeur SVD vers l'échangeur thermique gaz-vapeur, et après l'injection il y a une conduite de vapeur pour renvoyer cette vapeur. Le deuxième désurchauffeur à injection possède une rondelle de retenue. Derrière les grilles de sortie du premier étage se trouve un troisième désurchauffeur à injection Ш325*50, dont la conduite de vapeur transfère les flux sur toute la largeur du conduit de gaz. La vapeur est ensuite dirigée vers les parties médianes du conduit de gaz et, après les avoir traversées, est transférée à travers une conduite de vapeur Sh325*60 avec une température de 514 °C sur toute la largeur du conduit de gaz jusqu'aux grilles de sortie du deuxième étage, situé le long des bords du conduit de gaz. Après les grilles de sortie du deuxième étage, la vapeur à une température de 523 °C entre dans le quatrième désurchauffeur à injection Ш325*60. Les écrans d'entrée et de sortie des deux étages du surchauffeur à écran ont un modèle d'écoulement direct pour le mouvement mutuel de la vapeur et des gaz. Après le désurchauffeur, la vapeur à une température de 537 °C traverse la conduite de vapeur Sh237*50 dans un ensemble convectif conçu selon un schéma d'écoulement direct, le traverse à une température de 545 °C et est acheminée vers la turbine. . À partir des chambres d'entrée de l'économiseur d'eau, tous les tuyaux de dérivation et les chambres du chemin SVD sont en acier 12Х1МФ. Après la turbine HPC, de la vapeur avec une pression de 39,5 atm. Une température de 307 °C est envoyée en deux flux vers le surchauffeur intermédiaire. Une conduite « froide » de vapeur basse pression s’approche du boîtier ; elle bifurque devant le réchauffeur. Le surchauffeur de chaque boîtier dispose de deux flux de vapeur basse pression avec contrôle indépendant de la température le long des conduites. Conception de la chaudière Les parois de la chambre de combustion sont entièrement protégées par des tuyaux des surfaces chauffantes par rayonnement. La chambre de combustion de chaque bâtiment est divisée par des étranglements formés par les saillies des écrans avant et arrière dans la chambre de combustion (pré-four) et les chambres de post-combustion. Écrans dans la zone du foyer jusqu'en altitude. 15h00 entièrement clouté et recouvert de masse de chromite. L'isolation de la chambre de combustion et le rétrécissement de la chambre de combustion réduisent le transfert de chaleur du rayonnement du noyau de la torche, ce qui augmente le niveau de température dans le pré-four et améliore donc les conditions d'allumage et de combustion du combustible, et favorise également meilleure éducation laitier liquide. Le processus de combustion de l'AS se produit principalement dans le pré-four, mais la combustion se poursuit dans la chambre de post-combustion, où la sous-combustion mécanique diminue de 7,5 à 10 % à 2,5 %. Là, la température du gaz est réduite à 1210 °C, ce qui garantit le fonctionnement des surfaces chauffantes et du surchauffeur SVD sans scories. La contrainte thermique de l'ensemble du volume de combustion est Vt=142*103 kcal m 3 /heure, et celle du pré-four Vtp=491*103 kcal m/heure.
Le foyer de chacun des deux bâtiments est équipé de 12 brûleurs turbulents à gaz de poussière disposés sur deux niveaux (trois brûleurs dans chaque étage des parois avant et arrière du foyer). L'alimentation en gaz des brûleurs est périphérique, la productivité du brûleur à poussières est de 0,5 t/heure. Chaque brûleur turbulent est doté d'une buse de fioul intégrée à atomisation mécanique avec refroidissement et alimentation en air organisée. Pour éliminer les scories liquides, il y a deux trous de coulée refroidis dans le pré-four ; le pré-four est réalisé avec une pente de 80 par rapport aux trous de coulée et est recouvert de briques en argile réfractaire. Chaque four est équipé de deux (selon le nombre de trous de coulée) unités mécanisées d'élimination des scories. Les scories liquides sont granulées dans des bains-marie et évacuées dans des canaux de lavage des scories. L'agent de séchage est évacué à travers des brûleurs rectangulaires, situés sur les parois latérales de la chambre de combustion sur deux niveaux : il y a 4 brûleurs au niveau inférieur et 2 au niveau supérieur. travaux de réparation Il y a des trous d'homme dans la chambre de combustion. Le foyer est protégé en partie basse jusqu'à une altitude de 23,00 m par des canalisations de la partie inférieure de rayonnement (LRP), et en partie haute par des canalisations de la partie supérieure de rayonnement (URP) du plafond. Les tuyaux des écrans arrière et avant du NRF présentent des coudes qui forment un étranglement de combustion. La vitre arrière du VRCH en partie supérieure présente une saillie, améliore l'aérodynamisme du flux de gaz à la sortie du foyer et protège partiellement les surfaces de l'écran du rayonnement direct du foyer. Les écrans avant et arrière du NRF sont structurellement identiques, chaque écran est constitué de six bandes identiques, avec des tuyaux Ш42*6 connectés en parallèle, matériau 12Х1МФ. Les tuyaux en ruban filtrent d'abord le dessous et la partie inférieure de la pré-chambre de combustion, puis se déplacent vers le panneau vertical NRF, où ils effectuent cinq courses de levage et d'abaissement et sortent dans la chambre supérieure. Les tuyaux NRCh sont acheminés vers les embrasures des brûleurs, les regards et les judas. Les écrans latéraux du NRF se composent de quatre panneaux conçus comme suit.
En sortant de la chambre inférieure, le ruban, composé de 17 bobines Ш42*5 connectées en parallèle, matériau 12Х1МФ, masque d'abord la partie inférieure de la paroi latérale, puis se déplace vers la partie verticale, où elle effectue également cinq courses de montée et de descente. , puis sort dans la chambre haute. Les écrans NRF avant et arrière comportent deux niveaux de fixations fixes au repère 22,00 m et au repère 14,5 m. La compensation de la dilatation thermique s'effectue par pliage des canalisations au pincement. Les écrans latéraux sont suspendus par des attaches fixes au niveau de 21,9 m et peuvent être abaissés librement. Pour empêcher les tuyaux individuels de pénétrer dans la chambre de combustion, les écrans comportent cinq ceintures de fixations mobiles. Les écrans avant et arrière du VRCH sont également constitués de panneaux multi-passes avec mouvements de montée et de descente de la vapeur. La vapeur est fournie à la chambre inférieure des panneaux et évacuée des chambres supérieures. Les panneaux centraux de l'écran avant et tous les panneaux des écrans latéraux sont constitués de huit, et les panneaux extérieurs de l'écran avant de neuf tuyaux connectés en parallèle formant une bande. Le panneau en forme de N de la lunette arrière du magnétoscope est constitué de vingt tuyaux connectés en parallèle. Toutes les surfaces chauffantes du VRF sont constituées de tuyaux Ø42*5, matériau 12Х1МФ. Les écrans avant et latéraux du VRF sont suspendus avec des fixations fixes au niveau de 39,975 m et s'étendent librement vers le bas. L'écran arrière du magnétoscope est doté de deux supports fixes à 8,2 et 32,6. La compensation de la dilatation thermique des tuyaux est due à la courbure des tuyaux dans la partie supérieure de la lunette arrière du magnétoscope. Les écrans avant et latéraux comportent sept rangées de fixations mobiles, l'arrière - trois. Tous les tamis NRF et VRF ont un pas entre tubes de 45 mm. Le plafond du foyer et le haut du conduit horizontal sont protégés par des tuyaux de surchauffeur de plafond. Au total, 304 tuyaux connectés en parallèle (154 par chaîne) Ø32*4, matériau 12Х1МФ. Sur toute la longueur des tuyaux du surchauffeur de plafond, il y a 8 rangées de fixations qui sont fixées au cadre avec des tiges.
Surchauffeurs de vapeur à tamis À la sortie du four se trouve un surchauffeur à tamis composé de deux rangées de tamis. Il y a 16 écrans en rangée au pas de 630 mm, suspendus verticalement. Le long du flux de vapeur, les grilles de chaque étage sont divisées en entrée et sortie, situées plus près des parois latérales du conduit de fumée. Structurellement, les grilles d'entrée et de sortie du premier étage sont réalisées à l'identique (sauf pour l'emplacement des raccords et des canalisations de dérivation sur les chambres). Le tamis du premier étage de la chaudière 20 est constitué de 42 serpentins Ш32*6, le matériau des tuyaux est principalement de 12Х1МФ, mais les 11 serpentins extérieurs ont une section de sortie constituée de tuyaux Ш32*6, de matériau 1Х18Н12Т. Sur la chaudière, les 19 grilles du premier étage sont constituées de 37 serpentins de matériau 1Х18Н12Т. Pour donner de la rigidité à la structure, l'écran est relié par 5 de ses bobines, qui comportent des bandes de fixation en acier X20N14S2. Les écrans du deuxième étage sont constitués de 45 bobines Ш32*6. Le matériau des écrans d'entrée est de 12Х1МФ et le reste des bobines est en acier 1Х18Н12Т. L'écran est relié par ses six bobines. Les chambres d'entrée et de sortie, à l'exception des chambres des grilles de sortie du deuxième étage, sont réunies en collecteurs uniques séparés par une cloison. Les caméras sont suspendues à des tiges aux poutres du cadre. Les parois de la chambre rotative sont protégées par quatre blocs. Les blocs sont réalisés sous forme de bandes à deux boucles. Chaque bloc contient 38 bobines connectées en parallèle Ш32*6 en matériau 12Х1МФ, situées horizontalement. Les blocs sont dotés de ceintures de renforcement. Les blocs sont suspendus à l'aide de trois rangées (par bloc) de fixations. Les surfaces de chauffe suivantes sont situées dans le conduit de gaz inférieur : un ensemble convectif SVD, un surchauffeur ND avec un échangeur thermique gaz-vapeur et un économiseur d'eau. Pour toutes les surfaces convectives, une disposition décalée des serpentins est acceptée. Toutes les surfaces sont constituées de serpentins parallèles à l'avant de la chaudière.
Surchauffeur convectif SVD
L'ensemble de surchauffeurs à convection SVD de chaque ligne est constitué de 129 serpentins Ш32*6, en matériau 1Х18Н12Т, qui reposent sur des crémaillères en matériau Х23Н13, et ceux sur des poutres de support, refroidis par l'eau d'alimentation. Pour résister aux marches et conférer de la rigidité à la structure, il y a trois rangées de bandes d'espacement en acier 1Х18Н12Т, le paquet a une hauteur de 557 mm ; Surchauffeur basse pression Derrière l'ensemble convectif SVD se trouve un surchauffeur BP. Les colis de chaque flux sont situés dans les moitiés correspondantes du conduit d'évacuation ; les flux ne sont pas transférés sur la largeur du conduit. Le surchauffeur BP se compose d'un ensemble de sortie, d'un ensemble intermédiaire et d'un étage de commande. La partie de sortie du surchauffeur ND se compose de 108 serpentins suspendus Ш42*3,5, le matériau de l'acier combiné : Kh2MFSR et 12Kh1MF. Les bobines sont assemblées dans des colis avec des supports, en matériau X17N2, qui sont suspendus aux collecteurs de support du colis haute pression. Hauteur du colis 880 mm. Le paquet intermédiaire comprend également 108 doubles bobines Ш42*3,5 doubles bobines Ш42*3,5 en matériau 12Х1МФ. Hauteur du colis 1560 mm. Les bobines reposent sur des crémaillères en matériau X17N2 et celles sur les chambres d'entrée du colis intermédiaire Ø325*50 en matériau 12Х1МФ. Ainsi, les chambres d'entrée de l'emballage industriel sont également des poutres de support pour cette surface chauffante. Les chambres, en plus de l'isolation, disposent d'un refroidissement par air supplémentaire, nécessaire lors des modes de démarrage et lorsque la turbine est éteinte. Derrière l'ensemble industriel le long du flux de gaz sur les deux corps des chaudières TPP-210, au lieu du GPP TO, un étage de contrôle est installé, qui est le premier étage du réchauffeur le long du flux de vapeur, en acier perlitique et selon aux conditions fonctionnement fiable les conduites présentant une désévaporation importante sont placées dans une zone où la température du gaz à l'entrée ne doit pas dépasser 600°C. Son fonctionnement repose entièrement sur la modification de l'absorption thermique de la vapeur secondaire en modifiant sa distribution via des conduites de vapeur de dérivation. Selon les calculs, à la charge nominale de l'unité, 20 % du débit de vapeur total passe par l'étage de contrôle. Lorsque la charge de l'unité est réduite à 70 %, la consommation de vapeur est de 88 %. L'efficacité accrue de l'unité de puissance est obtenue en élargissant la plage de charges à laquelle la température de surchauffe secondaire calculée avec un excès d'air optimal est assurée. La gouverne est installée dans les dimensions du GPP TO démonté, les collecteurs d'entrée sont abaissés de 300 mm plus bas. La surface de commande se compose de parties gauche et droite avec une surface de chauffe totale de 2020 m² par logement. Les deux parties sont assemblées à partir de paquets de doubles serpentins et comportent 4 boucles le long du flux de gaz avec un mouvement de vapeur à contre-courant. Les bobines sont constituées de tuyaux Ш32*4, d'acier 12Х1МФ et sont disposées en damier avec des pas de 110 et 30 mm. Les bobines sont assemblées en colis à l'aide de supports emboutis en acier 12X13. Il y a 5 supports sur toute la longueur de chaque colis. Deux d'entre eux sont installés sur des collecteurs refroidis à l'eau situés dans le conduit de gaz, qui sont abaissés de 290 mm lors des réparations. La vapeur du HPC pénètre dans les chambres d'entrée de la surface de contrôle Ш425*20 en acier 20. Après avoir traversé les serpentins, la vapeur pénètre dans les chambres de sortie d'un diamètre de 426*20 en acier 12Х1МФ, où elle est mélangée à la vapeur provenant de la vapeur de dérivation. doubler. Les anciennes vannes RKT ont été découpées le long des filetages « B » et « C » ; les pièces internes ont été retirées des anciennes vannes RKT et les corps RKT ont été soudés et utilisés comme tés. De nouvelles vannes à guillotine RKT sont installées sur la conduite de dérivation entre les collecteurs d'entrée et de sortie. Lorsque la vanne est ouverte à 100 %, 80 % de la vapeur passe devant la gouverne et la pression diminue. Lorsque la vanne est fermée, la vapeur traverse la surface de commande et la température de réchauffage augmente. Le KDU et les clés de commande des nouveaux RKT restent les mêmes. Les serpentins de l'économiseur d'eau des deux corps ont été remplacés (à 100 %). Les deuxièmes collecteurs d'injection sont démontés rondelles de retenue et les prises vers le GPP TO ont été fermées. L'économiseur convectif est la dernière surface chauffante le long du flux de gaz, située dans le conduit de gaz d'échappement. Il se compose de tuyaux Ш32*6, matériau st20. Les chambres de sortie et d'entrée de l'économiseur sont également des poutres de support - le poids de cette surface chauffante leur est transféré à travers les racks. La charpente de la chaudière est réalisée sous la forme de charpentes identiques des deux bâtiments, reliées entre elles par des liaisons inter-coques et des échafaudages de transition. Le poids de la surface de chauffe, du revêtement et de l'isolation est transféré à l'aide de poutres et de fermes horizontales sur trois rangées de colonnes verticales, une rangée à l'avant de la chaudière, une autre entre le foyer et les conduits d'évacuation et la troisième à l'arrière de la chaudière. Chaudière. Pour renforcer le cadre, une série de poutres inclinées est prévue. Le revêtement des conduits du four et de la chaudière est réalisé sous forme de panneaux séparés. Le foyer et les conduits de fumée sont gainés de tôles de 3 mm d'épaisseur, ce qui garantit haute densité foyers et conduits de fumée.
Une variation de 1,12 à 1,26 entraîne une diminution de 2,5 à 1,5 % pour le deuxième groupe de combustibles. Par conséquent, pour augmenter la fiabilité de la chambre de combustion, l'excès d'air à la sortie du four doit être maintenu au-dessus de 1,2.
Dans le tableau indiqué Dans la plage 1-3 de modifications de la contrainte thermique du volume de combustion et de la finesse de broyage /? 90 (Fig. 6-9, c, d), leur influence sur la valeur n'a pas été détectée. Il n'a pas non plus été possible d'identifier l'influence du rapport des vitesses de l'air secondaire et du mélange poussière-air dans la plage étudiée de leurs évolutions sur l'efficacité du fonctionnement du four. Cependant, en réduisant le débit d'air à travers le canal extérieur (à charges réduites) et en l'augmentant en conséquence à travers le canal intérieur (à débit constant à travers le brûleur), le rendement en scories s'améliore. Les jets de scories deviennent plus minces et leur nombre augmente.
Avec répartition uniforme de la poussière et de l'air. sur les brûleurs et à > >1,15 il n'y a pas de sous-combustion chimique à la sortie du four.
Le rendement brut du générateur de vapeur lors de la combustion du charbon (1/g "14%) et à charge nominale atteint 90,6%.
Les travaux ont obtenu des résultats similaires confirmant que le générateur de vapeur TPP-210A fonctionne de manière économique et fiable également lors de la combustion de cendres (1/g = 3,5 % ; 0rts = 22,2 MJ/kg ; L^ = 23,5 % ; =
Avec un excès d'air dans le four à = 1,26h-1,28, finesse de broyage /?9o = ----6-^8%, dans la plage de charge D< = 0,7-^ 1,0£)н величина потери тепла с механическим недожогом достигает 3%. Максимальный к. п. д. брутто парогенератора при номинальной нагрузке составляет 89,5%.
Les travaux fournissent des données indiquant que lorsque l'anthracite est brûlé chambre de combustion générateur de vapeur TPP-210A valeur de sous-combustion mécanique<74 в условиях эксплуатации примерно в 1,5 ниже, чем при работе котлов ТПП-110 и ТПП-210 с двухъярусным расположением вихревых горелок мощностью 35 МВт.
Les études réalisées, ainsi que l'exploitation industrielle pilote à long terme du générateur de vapeur TPP-210A, ont montré que dans la plage de changements de charge de 0,65 à la charge nominale, la chambre de combustion fonctionne de manière économique et stable, sans dépoussiérage et sans perturbation du régime d'élimination des scories liquides.
La durée de la campagne (avant grosses réparations) du générateur de vapeur avec brûleurs à poussière et à gaz sans leur réparation était de 14 545 heures. En même temps, l'état des brûleurs était satisfaisant ; la combustion des embrasures de briques, la déformation des conduites de gaz et des buses sont insignifiantes.
Lors des inspections de la chambre de combustion lors des arrêts, aucune accumulation de scories sur le foyer ni de scories des parois de la chambre de postcombustion n'a été constatée. L'ensemble de la ceinture cloutée était recouvert d'une pellicule de laitier lisse et brillante. La dérive des surfaces chauffantes par convection n’a pas non plus été observée.
La désactivation d'un ou de deux brûleurs moyens ne réduit pas la stabilité de l'allumage, n'affecte pas le mode d'élimination des scories liquides et n'entraîne pas de violation du régime de température du NRF et du VRF.
LUNTER COMME RESSOURCE ÉNERGÉTIQUE. Réservons d'emblée que l'utilisation de fumier natif (sans litière) pour répondre aux besoins énergétiques est beaucoup plus coûteuse que le fumier de litière, tant en termes de capital qu'en termes d'exploitation...
MÉTHODE COMPLÈTE D'ÉLIMINATION DES LUNTER DE POULET AVEC PRODUCTION D'ENGRAIS ORGANO-MINÉRAUX ET DE GAZ COMBUSTIBLES, DE CHALEUR ET D'ÉNERGIE ÉLECTRIQUE Le fumier est un puissant polluant des bassins du sol, de l'eau et de l'air. En même temps, la litière...