Application de la récupération de chaleur des gaz de combustion. Méthode d'utilisation profonde de la chaleur des gaz de combustion. Options pour organiser la récupération de chaleur
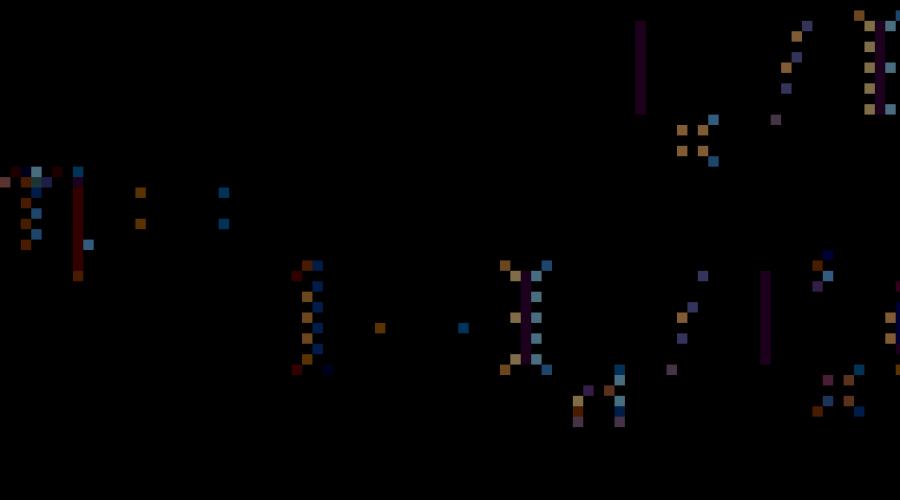
Évaluation de l'efficacité de la récupération en profondeur des productions de combustion des chaudières des centrales électriques
PAR EXEMPLE. Shadek, Candidat ingénieur, expert indépendant
mots clés: produits de combustion, récupération de chaleur, équipement de chaufferie, efficacité énergétique
L'une des méthodes pour résoudre le problème de l'économie de carburant et de l'amélioration de l'efficacité énergétique des chaufferies est le développement de technologies de récupération de chaleur profonde des gaz d'échappement des chaudières. Nous proposons un schéma de processus d'une centrale électrique avec des unités de turbine à vapeur (STU) qui permet une récupération en profondeur de la chaleur des produits de combustion de la chaudière du condenseur STU en utilisant un refroidisseur-condensat avec des coûts minimaux sans l'utilisation d'unités de pompe à chaleur.
La description:
L'un des moyens de résoudre le problème de l'économie de carburant et d'améliorer l'efficacité énergétique des chaufferies est le développement de technologies d'utilisation en profondeur de la chaleur des gaz résiduaires des chaudières des produits de combustion en raison de la présence d'un refroidisseur - condensat de le condenseur PTU.
E. G. Shadek, cand. technologie. Sciences, expert indépendant
L'un des moyens de résoudre le problème de l'économie de carburant et d'augmenter l'efficacité énergétique des chaufferies est le développement de technologies d'utilisation en profondeur de la chaleur des gaz de combustion des chaudières. Nous proposons un schéma technologique d'une centrale électrique avec des unités de turbine à vapeur (STP), qui permet, à un coût minime, sans l'utilisation d'unités de pompe à chaleur, d'effectuer une utilisation en profondeur de la chaleur des produits de combustion sortant de la chaudière en raison de la présence d'un refroidisseur - condensat du condenseur STP.
L'utilisation en profondeur de la chaleur des produits de combustion (CC) est assurée lorsqu'ils sont refroidis en dessous de la température du point de rosée égale à 50–55 0 С pour le gaz naturel CC Dans ce cas, les phénomènes suivants se produisent :
- condensation de la vapeur d'eau (jusqu'à 19-20% du volume ou 12-13% du poids des produits de combustion),
- utilisation de la chaleur physique de la sous-station (40 à 45 % du contenu thermique total),
- utilisation de la chaleur latente de vaporisation (60 à 55 %, respectivement).
Il a été précédemment établi que les économies de combustible avec une utilisation en profondeur par rapport à une chaudière avec une efficacité de passeport (maximale) de 92% sont de 10 à 13%. Le rapport entre la quantité de chaleur utilisée et la puissance calorifique de la chaudière est d'environ 0,10 à 0,12, et l'efficacité de la chaudière en mode condensation est de 105 % en termes de valeur calorifique nette du gaz.
De plus, avec une utilisation profonde en présence de vapeur d'eau dans le PS, l'émission d'émissions nocives est réduite de 20 à 40 % ou plus, ce qui rend le processus respectueux de l'environnement.
Un autre effet de l'utilisation profonde est l'amélioration des conditions et de la durée de vie du chemin de gaz, puisque la condensation est localisée dans la chambre où l'échangeur de chaleur d'utilisation est installé, quelle que soit la température extérieure.
Stockage en profondeur pour systèmes de chauffage
Dans les pays occidentaux avancés, l'utilisation profonde pour les systèmes de chauffage est réalisée à l'aide de chaudières à eau chaude à condensation équipées d'un économiseur à condensation.
La faible température de l'eau de retour (30–40 0 С) avec un graphique de température typique, par exemple 70/40 0 С, dans les systèmes de chauffage de ces pays permet une récupération de chaleur profonde dans un économiseur à condensation équipé de une unité de collecte, d'évacuation et de traitement des condensats (avec son utilisation ultérieure pour l'alimentation de la chaudière). Un tel schéma fournit le mode de fonctionnement à condensation de la chaudière sans liquide de refroidissement artificiel, c'est-à-dire sans l'utilisation d'une pompe à chaleur.
L'efficacité et la rentabilité du stockage profond pour les chaudières de chauffage n'ont pas besoin d'être prouvées. Les chaudières à condensation sont largement utilisées en Occident : jusqu'à 90 % de toutes les chaudières fabriquées sont à condensation. De telles chaudières sont également exploitées dans notre pays, bien que nous n'ayons pas leur production.
En Russie, contrairement aux pays au climat chaud, la température dans la conduite de retour des réseaux de chauffage est généralement supérieure au point de rosée et une utilisation en profondeur n'est possible que dans les systèmes à quatre tuyaux (très rare) ou lors de l'utilisation de pompes à chaleur. La principale raison du retard de la Russie dans le développement et la mise en œuvre de l'utilisation profonde est le faible prix du gaz naturel, les coûts d'investissement élevés dus à l'inclusion des pompes à chaleur dans le système et les longues périodes de récupération.
Stockage en profondeur pour les chaudières des centrales électriques
L'efficacité de l'utilisation en profondeur des chaudières des centrales électriques (Fig. 1) est bien supérieure à celle des chaudières de chauffage, en raison d'une charge stable (KIM = 0,8–0,9) et de grandes capacités unitaires (dizaines de mégawatts).
Estimons la ressource thermique des produits de combustion des chaudières de la station, en tenant compte de leur rendement élevé (90–94%). Cette ressource est déterminée par la quantité de chaleur perdue (Gcal/h ou kW), qui dépend uniquement de la puissance calorifique de la chaudière Q K , et température derrière les chaudières à gaz J 1UX, qui en Russie est accepté au moins 110–130 0 С pour deux raisons:
- augmenter le tirage naturel et réduire la pression (consommation d'énergie) de l'extracteur de fumée ;
- pour éviter la condensation de la vapeur d'eau dans les conduits de fumée, les conduites de gaz et les cheminées.
Analyse approfondie d'un large éventail 1 de données expérimentales d'équilibre, d'essais de mise en service effectués par des organismes spécialisés, de cartes de régime, de rapports statistiques de stations, etc. et des résultats du calcul des valeurs de perte de chaleur avec les produits de combustion sortants q 2 , le quantité de chaleur récupérée 2 Q UT et les indicateurs qui en sont dérivés dans une large gamme de charges de chaudières de la station sont donnés dans le tableau. treize . Le but est de déterminer q 2 et les rapports des quantités Q K , q 2 et Q UT dans les conditions de fonctionnement typiques des chaudières (tableau 2). Dans notre cas, peu importe la chaudière : vapeur ou eau chaude, industrielle ou chauffage.
Indicateurs de tableau. 1, surlignés en bleu, ont été calculés selon l'algorithme (voir référence). Calcul du processus d'utilisation profonde (définition Q UT, etc.) ont été réalisées selon la méthode d'ingénierie donnée et décrite dans. Le coefficient de transfert de chaleur "produits de combustion - condensat" dans l'échangeur de chaleur à condensat a été déterminé selon la méthode empirique du fabricant de l'échangeur de chaleur (OAO Calorific Plant, Kostroma).
Les résultats témoignent de la grande efficacité économique de la technologie d'utilisation profonde pour les chaudières de la station et de la rentabilité du projet proposé. La période d'amortissement des systèmes est de 2 ans pour une chaudière de puissance minimale (tableau 2, chaudière n ° 1) à 3 à 4 mois. Les ratios résultants β, φ, σ, ainsi que les articles sur les économies (tableau 1, lignes 8–10, 13–18) vous permettent d'évaluer immédiatement les capacités et les indicateurs spécifiques d'un processus donné, chaudière.
Récupération de chaleur dans une chaudière à gaz
Le schéma technologique habituel de la centrale électrique prévoit le chauffage du condensat dans un réchauffeur de gaz (partie des surfaces arrière de la chaudière, économiseur) sur les gaz de combustion sortant de la chaudière.
Après le condenseur, des pompes (parfois via une usine de dessalement en bloc - ci-après BOU) le condensat est envoyé au réchauffeur de gaz, après quoi il entre dans le dégazeur. Avec la qualité standard du condensat, le BOU est contourné. Pour éviter la condensation de la vapeur d'eau des gaz d'échappement sur les derniers tuyaux du réchauffeur de gaz, la température du condensat devant celui-ci est maintenue à au moins 60 0 С en recirculant le condensat chauffé vers son entrée.
Pour réduire davantage la température des fumées, un échangeur de chaleur eau-eau est souvent inclus dans la ligne de recirculation des condensats, refroidi par l'eau d'appoint du système de chauffage. Le chauffage de l'eau du réseau est effectué par le condensat d'un réchauffeur à gaz. Avec un refroidissement supplémentaire des gaz de 10 0 С dans chaque chaudière, il est possible d'obtenir environ 3,5 Gcal/h de charge de chauffage.
Pour empêcher le condensat de bouillir dans le réchauffeur de gaz, des vannes d'alimentation de contrôle sont installées derrière celui-ci. Leur but principal est de répartir le flux de condensats entre les chaudières en fonction de la charge calorifique du PTU.
Système de récupération en profondeur avec échangeur de chaleur à condensation
Comme on peut le voir sur le schéma de processus (Fig. 1), le condensat de vapeur du collecteur de condensat est pompé par la pompe 14 vers le réservoir de collecte 21, et de là vers le collecteur de distribution 22. Ici, le condensat est divisé en deux flux à l'aide du système de contrôle automatique de la station (voir ci-dessous) : l'un est fourni à l'unité d'utilisation profonde 4, à l'échangeur de chaleur à condensation 7, et le second au réchauffeur basse pression (LPH) 18, puis au dégazeur 15 La température du condensat de vapeur du condenseur de turbine (environ 20–35 échangeur de chaleur 7 aux 40 0 C requis, c'est-à-dire pour assurer une utilisation en profondeur.
Le condensat de vapeur chauffé de l'échangeur de chaleur à condensation 7 est acheminé via le LPH 18 (ou la dérivation 18) vers le dégazeur 15. Le condensat des produits de combustion obtenus dans l'échangeur de chaleur à condensation 7 est évacué dans le puisard et le réservoir 10. De là il est introduit dans le réservoir de condensat contaminé 23 et pompé par la pompe de vidange 24 dans la réserve de condensat du réservoir 25, à partir de laquelle la pompe à condensat 26 à travers le régulateur de débit est alimentée vers la zone de nettoyage du condensat des produits de combustion (non représenté sur Fig. 1), où il est traité selon une technologie connue. Le condensat purifié des produits de combustion est introduit dans le HDPE 18 puis dans le désaérateur 15 (ou directement dans le 15). A partir du dégazeur 15, le flux de condensat pur est amené par la pompe d'alimentation 16 au réchauffeur haute pression 17, et de celui-ci à la chaudière 1.
Ainsi, la chaleur des produits de combustion utilisée dans l'échangeur de chaleur à condensation économise le combustible consommé dans le schéma technologique de la centrale électrique pour chauffer le condensat de la station devant le dégazeur et dans le dégazeur lui-même.
L'échangeur de chaleur à condensation est installé dans la chambre 35 à la jonction de la chaudière 27 avec la cheminée (Fig. 2c). La charge thermique de l'échangeur de chaleur à condensation est régulée par dérivation, c'est-à-dire l'élimination d'une partie des gaz chauds en plus de l'échangeur de chaleur à condensation par le canal de dérivation 37 avec un papillon des gaz (porte) 36.
Le plus simple serait le schéma traditionnel: un économiseur à condensation, plus précisément les sections de queue de l'économiseur de la chaudière, comme un réchauffeur de gaz, mais fonctionnant en mode condensation, c'est-à-dire avec refroidissement des produits de combustion en dessous de la température du point de rosée. Mais en même temps, des difficultés surgissent dans le plan constructif et opérationnel (maintenance, etc.), nécessitant des solutions particulières.
Différents types d'échangeurs de chaleur sont applicables : à coque et à tube, à tube droit, à ailettes moletées, à conception lamellaire ou efficace avec une nouvelle forme de la surface d'échange de chaleur avec un petit rayon de courbure (régénérateur RG-10, SPC Anod) . Dans ce schéma, en tant qu'échangeur de chaleur à condensation, des sections de bloc d'échange de chaleur basées sur une marque de réchauffeur d'air bimétallique VNV123-412-50ATZ (OAO Calorific Plant, Kostroma) sont prises.
Le choix de la disposition des sections et des raccordements pour l'eau et les gaz vous permet de faire varier et d'assurer la vitesse de l'eau et des gaz dans les limites recommandées (1-4 m/s) . Le conduit de fumée, la chambre, le trajet des gaz sont en matériaux résistants à la corrosion, les revêtements, notamment les aciers inoxydables, les plastiques, c'est une pratique courante.
* Il n'y a pas de pertes de chaleur dues à l'incomplétude de la combustion chimique.
Caractéristiques d'utilisation profonde avec échangeur de chaleur à condensation
Le haut rendement de la technologie permet de réguler la puissance thermique du système dans une large plage, tout en préservant sa rentabilité : le degré de by-pass, la température des produits de combustion derrière l'échangeur à condensation, etc. La charge thermique de l'échangeur de chaleur à condensation QUT et, par conséquent, la quantité de condensat qui lui est fournie par le collecteur 22 ), est déterminée comme optimale (et pas nécessairement maximale) selon des calculs techniques et économiques et des considérations de conception, en tenant compte des paramètres de fonctionnement, des capacités et conditions de la chaudière et de l'organigramme du processus de l'installation dans son ensemble.
Après contact avec les produits de combustion du gaz naturel, le condensat conserve sa haute qualité et nécessite un traitement simple et peu coûteux - décarbonisation (et même pas toujours) et dégazage. Après traitement sur le site de traitement chimique de l'eau (non illustré), le condensat est pompé à travers le régulateur de débit vers la conduite de condensat de la station - vers le dégazeur, puis vers la chaudière. Si le condensat n'est pas utilisé, il est évacué à l'égout.
Dans l'unité de collecte et de traitement des condensats (Fig. 1, pos. 8, 10, Fig. 2, pos. 23–26), un équipement standard bien connu des systèmes d'évacuation en profondeur est utilisé (voir, par exemple,).
L'usine produit une grande quantité d'eau en excès (condensat de vapeur d'eau provenant de la combustion des hydrocarbures et de l'air soufflé), de sorte que le système n'a pas besoin d'être rechargé.
La température des produits de combustion à la sortie de l'échangeur à condensation J 2УХ est déterminé par l'état de condensation de la vapeur d'eau dans les produits de combustion sortants (dans la plage de 40 à 45 0 С).
Afin d'éviter la condensation dans le trajet des gaz et en particulier dans la cheminée, une dérivation est prévue, c'est-à-dire qu'une partie des produits de combustion est dérivée par le canal de dérivation en plus de l'unité d'utilisation profonde de sorte que la température du mélange gazeux derrière celle-ci soit dans la plage de 70 à 90 0 C. Le contournement aggrave tous les paramètres du processus. Le mode optimal est le fonctionnement avec by-pass pendant la saison froide, et en été, lorsqu'il n'y a pas de danger de condensation et de givrage, sans elle.
La température des gaz de combustion des chaudières (généralement 110–130 0 C) permet de chauffer le condensat dans l'échangeur de chaleur à condensation avant le dégazeur jusqu'à la température requise de 90–100 0 C. Ainsi, les exigences technologiques en matière de températures sont satisfaites: les deux chauffage du condensat (environ 90 0 С) et combustion du refroidissement du produit (jusqu'à 40 0 С) avant condensation.
Comparaison des technologies de récupération de chaleur des produits de combustion
Au moment de décider de l'utilisation de la chaleur des produits de combustion de la chaudière, il convient de comparer l'efficacité du système d'utilisation en profondeur proposé et du schéma traditionnel avec un chauffage au gaz comme analogue et concurrent le plus proche.
Pour notre exemple (voir référence 1), nous avons obtenu la quantité de chaleur récupérée de l'utilisation profonde Q UT égal à 976 kW.
Nous supposons que la température du condensat à l'entrée du réchauffeur de gaz à condensat est de 60 0 C (voir ci-dessus), tandis que la température des produits de combustion à sa sortie est d'au moins 80 0 C. Ensuite, la chaleur des produits de combustion utilisée dans le réchauffeur à gaz, c'est-à-dire l'économie de chaleur, sera égale à 289 kW, soit 3,4 fois moins que dans le système d'utilisation profonde. Ainsi, le « prix d'émission » dans notre exemple est de 687 kW, soit, sur une base annualisée, 594 490 m 3 de gaz (avec KIM = 0,85) valant environ 3 millions de roubles. Le gain augmentera avec la puissance de la chaudière.
Avantages de la technologie de recyclage en profondeur
En conclusion, nous pouvons conclure qu'en plus des économies d'énergie, les résultats suivants sont obtenus avec une utilisation en profondeur des produits de combustion d'une chaudière de centrale électrique :
- réduction des émissions d'oxydes toxiques CO et NOx, garantissant la propreté environnementale du processus ;
- obtenir de l'eau supplémentaire en excès et ainsi éliminer le besoin d'eau d'appoint pour la chaudière ;
- la condensation de la vapeur d'eau des produits de combustion est localisée en un seul endroit - dans l'échangeur de chaleur à condensation. Hormis un léger entraînement de brouillard après l'éliminateur de gouttelettes, la condensation est exclue dans le trajet de gaz ultérieur et la destruction associée des conduits de gaz par les effets corrosifs de l'humidité, la formation de glace dans le trajet et surtout dans la cheminée ;
- dans certains cas, l'utilisation d'un échangeur de chaleur eau-eau devient facultative ; il n'y a pas besoin de recirculation : mélange d'une partie des gaz chauds avec des gaz refroidis (ou des condensats chauffés avec des froids) afin d'augmenter la température des produits de combustion sortants pour éviter la condensation dans le trajet des gaz et la cheminée (économie d'énergie, d'argent).
Littérature
- Shadek E., Marshak B., Anokhin A., Gorshkov V. Utilisation profonde de la chaleur résiduelle des générateurs de chaleur // Chaudières industrielles et de chauffage et mini-cogénération. 2014. N° 2 (23).
- Shadek E. La trigénération comme technologie d'économie des ressources énergétiques // Energy Saving. 2015. N° 2.
- Shadek E., Marshak B., Krykin I., Gorshkov V. Échangeur de chaleur à condensation - modernisation des chaufferies // Chaudières industrielles et de chauffage et mini-cogénération. 2014. N° 3 (24).
- Kudinov A. Économie d'énergie dans les installations de production de chaleur. M. : Mashinostroenie, 2012.
- Ravich M. Méthode simplifiée de calculs d'ingénierie thermique. M. : Maison d'édition de l'Académie des sciences de l'URSS, 1958.
- Berezinets P., Olkhovsky G. Technologies prometteuses et centrales électriques pour la production d'énergie thermique et électrique. Section six. 6.2 turbines à gaz et centrales à cycle combiné. 6.2.2. Installations vapeur et gaz. OAO VTI. "Technologies environnementales modernes dans le secteur de l'énergie". Collecte d'informations, éd. V. Ya. Putilova. M. : Maison d'édition MPEI, 2007.
1 Source principale de données : enquêtes sur les chaudières à eau chaude (11 tranches dans trois chaufferies des réseaux de chaleur), collecte et traitement des matériaux.
2 Mode de calcul, notamment Q UT, donné en.
V.S. Galustov, docteur en sciences techniques, professeur, directeur général de SE NPO "Polytechnic"
L.A. Rozenberg, ingénieur, directeur de l'UE Yumiran.
Introduction.
Avec des fumées d'origines diverses, des milliers et des milliers de Gcal de chaleur, ainsi que des milliers de tonnes de polluants gazeux et solides, et de vapeur d'eau sont émis dans l'atmosphère. Dans cet article, nous allons nous intéresser à la problématique de la récupération de chaleur (nous parlerons de l'épuration des émissions de gaz dans le prochain message). L'utilisation la plus profonde de la chaleur de combustion du combustible est réalisée dans les chaudières thermiques, pour lesquelles, dans la plupart des cas, des économiseurs sont prévus dans leur section de queue. La température des fumées après eux est d'environ 130–190°C, c'est-à-dire est proche de la température de rosée des vapeurs acides, qui est la limite inférieure en présence de composés soufrés dans le carburant. Lors de la combustion de gaz naturel, cette limitation est moins importante.
Les gaz de combustion après différents types de fours peuvent avoir une température nettement plus élevée (jusqu'à 300-500°C et plus). Dans ce cas, la récupération de chaleur (et le refroidissement des gaz) est tout simplement obligatoire, ne serait-ce que pour limiter la pollution thermique de l'environnement.
Unités de récupération de chaleur.
Même dans le premier message, nous avons limité l'éventail de nos intérêts aux processus et dispositifs à contact de phase direct, cependant, pour compléter le tableau, nous rappellerons et évaluerons également d'autres options. Tous les échangeurs de chaleur connus peuvent être divisés en dispositifs de contact, de surface et avec un liquide de refroidissement intermédiaire. Le premier sera discuté plus en détail ci-dessous. Les échangeurs de chaleur de surface sont des appareils de chauffage traditionnels qui sont placés directement dans la cheminée après le four (chaudière) et présentent de sérieux inconvénients qui limitent leur utilisation. Premièrement, ils introduisent une résistance aérodynamique importante dans le trajet des gaz et aggravent le fonctionnement des fours (le vide diminue) avec un aspirateur de fumée design, et le remplacer par un plus puissant peut ne pas compenser les coûts associés en économisant de la chaleur. Deuxièmement, les faibles coefficients de transfert de chaleur du gaz à la surface des tubes déterminent les grandes valeurs de la surface de contact requise.
Les appareils à caloporteur intermédiaire sont de deux types : fonctionnement intermittent avec caloporteur solide et fonctionnement continu avec caloporteur liquide. Les premières sont constituées d'au moins deux colonnes remplies, par exemple, de granit concassé (garnissage). Les gaz de combustion traversent l'une des colonnes, dégageant de la chaleur vers la buse, la chauffant à une température légèrement inférieure à la température des gaz. Ensuite, les gaz de combustion sont transférés vers la deuxième colonne et le fluide chauffé est fourni à la première (généralement de l'air fourni au même four ou de l'air provenant du système de chauffage de l'air), etc. Les inconvénients d'un tel schéma sont évidents (résistance élevée, encombrement, instabilité de température, etc.), et son application est très limitée.
Les appareils à caloporteur intermédiaire liquide (généralement de l'eau) étaient appelés échangeurs de chaleur à contact avec garnissage actif (KTAN), et les auteurs, après une légère amélioration, les appelaient échangeurs de chaleur à caloporteur saturé et condensation (TANTEK). Dans les deux cas, l'eau chauffée par les gaz de combustion restitue ensuite la chaleur reçue à travers la paroi de l'échangeur de chaleur intégré en surface pour nettoyer l'eau (par exemple, les systèmes de chauffage). Par rapport aux appareils de chauffage, la résistance de ces échangeurs de chaleur est beaucoup plus faible et, en termes d'échange de chaleur dans le système gaz de combustion - eau, ils sont complètement similaires à l'appareil de pulvérisation à flux direct qui nous intéresse. Cependant, il existe des différences importantes, dont nous discuterons ci-dessous.
Les développeurs des appareils KTAN et TANTEK ne considèrent pas dans leurs publications les caractéristiques de transfert de chaleur au contact direct des fumées et de l'eau, nous allons donc nous y attarder plus en détail.
Les principaux processus dans les gaz de combustion du système - l'eau.
Le résultat de l'interaction des gaz de combustion chauffés (par composition et propriétés, il s'agit en fait d'air humide) et de l'eau (sous forme de gouttelettes d'une taille ou d'une autre), que nous appellerons un milieu accumulateur de chaleur (il peut être utilisé comme caloporteur principal ou intermédiaire), est déterminé par tout un ensemble de processus.
Simultanément au chauffage, une condensation de l'humidité à la surface des gouttelettes ou une évaporation peut se produire. En fait, il existe trois options pour la direction mutuelle des flux de chaleur et d'humidité (transfert de chaleur et transfert de masse), qui dépendent du rapport des températures de phase et du rapport des pressions partielles de vapeur dans la couche limite (près de la gouttelette) et dans le cœur du flux de gaz (Fig. 1a).
Dans ce cas, le premier cas (supérieur), lorsque les flux de chaleur et d'humidité sont dirigés des gouttes vers le gaz, correspond au refroidissement par évaporation de l'eau ; la seconde (au milieu) - gouttes chauffantes avec évaporation simultanée de l'humidité de leur surface; la troisième version (inférieure), selon laquelle la chaleur et l'humidité sont dirigées du gaz vers les gouttes, reflète le chauffage de l'eau avec condensation de vapeur. (Il semblerait qu'il devrait également y avoir une quatrième option, lorsque le refroidissement des gouttelettes et le chauffage du gaz s'accompagnent d'une condensation d'humidité, mais cela ne se produit pas en pratique.)
Tous les processus décrits peuvent être représentés visuellement sur le diagramme de Ramzin de l'état de l'air humide (diagramme H-x, Fig. 1b).
Déjà de ce qui a été dit, on peut conclure que la troisième option est la plus souhaitable, mais pour comprendre comment l'assurer, il faut rappeler en plus de ce qui a été dit dans :
- la quantité de vapeur d'eau contenue dans 1 m3 d'air humide est appelée humidité absolue de l'air. La vapeur d'eau occupe tout le volume du mélange, donc l'humidité absolue de l'air est égale à la densité de vapeur d'eau (dans des conditions données) pp
- lorsque l'air est saturé de vapeur, il arrive un moment où la condensation commence, c'est-à-dire la teneur en vapeur maximale possible dans l'air est atteinte à une température donnée, qui correspond à la densité de vapeur d'eau saturée pH ;
- le rapport de l'humidité absolue à la quantité maximale possible de vapeur dans 1 m3 d'air à une pression et une température données est appelé humidité relative f ;
- la quantité de vapeur d'eau en kg pour 1 kg d'air absolument sec est appelée teneur en humidité de l'air x ;
- l'air humide en tant que caloporteur est caractérisé par l'enthalpie / (teneur en chaleur), qui est fonction de la température et de la teneur en humidité de l'air et est égale à la somme des enthalpies de l'air sec et de la vapeur d'eau. Sous la forme la plus pratique pour une application pratique, la formule de calcul de l'enthalpie peut être représentée
Je \u003d (1000 + 1,97. 103x) t + 2493. . 103x J / kg d'air sec, où 1000 est la capacité thermique spécifique de l'air sec, J / kg * deg); 1,97 * 103 - capacité thermique spécifique de la vapeur, J / (kg * deg); 2493*103 est un coefficient constant approximativement égal à l'enthalpie de la vapeur à 0°C ; t est la température de l'air, °С ;
I = 0,24 t + (595 + 0,47 t) Xkcal/kg air sec ; où 595 est un coefficient constant approximativement égal à l'enthalpie de la vapeur à 0°C ; 0,24 est la capacité calorifique spécifique de l'air sec, kcal/(kgtrad) ; 0,47 est la capacité calorifique de la vapeur, kcal/(kgtrad) ;
- lorsque l'air est refroidi (dans des conditions d'humidité constante), l'humidité relative augmente jusqu'à atteindre 100 %. La température correspondante est appelée température du point de rosée. Sa valeur est déterminée uniquement par la teneur en humidité de l'air. Sur le diagramme de Ramzin, c'est le point d'intersection de la droite verticale x = const avec la droite φ = 1.
Le refroidissement de l'air en dessous du point de rosée s'accompagne d'une condensation d'humidité, c'est-à-dire séchage à l'air.
Une certaine confusion est causée par des publications qui donnent des valeurs de point de rosée pour divers combustibles solides et liquides de l'ordre de 130-150°C. Il faut garder à l'esprit qu'il s'agit du début de la condensation des vapeurs d'acide sulfurique et sulfureux (on note eetpK), et non de la vapeur d'eau (tp), dont nous avons parlé plus haut. Pour ces derniers, la température du point de rosée est beaucoup plus basse (40-50°C).
Ainsi, trois grandeurs - le débit, la température et la teneur en humidité (ou température de bulbe humide) - caractérisent pleinement les gaz de combustion en tant que source de ressources énergétiques secondaires.
Lorsque l'eau entre en contact avec des gaz chauds, le liquide s'échauffe dans un premier temps et les vapeurs se condensent à la surface des gouttes froides (correspond à la 3ème option de la Fig. 1a) jusqu'à ce que la température correspondant au point de rosée du gaz soit atteinte, c'est-à-dire la frontière de la transition vers le second régime (variante 3 sur la Fig. 1a). De plus, à mesure que l'eau est chauffée et que la pression partielle de vapeur à la surface des gouttelettes augmente, la quantité de chaleur qui leur est transférée en raison du transfert de chaleur Q1 diminue et la quantité de chaleur transférée des gouttelettes aux gaz de combustion en raison de l'évaporation. Q2 augmentera. Cela se poursuivra jusqu'à ce que l'équilibre soit atteint (Q1 = Q2), lorsque toute la chaleur reçue par l'eau à partir des fumées sera restituée au gaz sous forme de chaleur d'évaporation du liquide. Après cela, un chauffage supplémentaire du liquide est impossible et il s'évapore à une température constante. La température atteinte dans ce cas est appelée température de bulbe humide tM (en pratique, elle est définie comme la température indiquée par un thermomètre dont le bulbe est recouvert d'un chiffon humide, d'où s'évapore l'humidité).
Ainsi, si de l'eau à une température égale (ou supérieure) à tM est fournie à l'échangeur de chaleur, alors un refroidissement adiabatique (à contenu thermique constant) des gaz sera observé et il n'y aura pas de récupération de chaleur (sans compter les conséquences négatives - perte d'eau et humidification des gaz).
Le procédé se complique si l'on tient compte du fait que la composition des gouttelettes est polydispersée (du fait des mécanismes de décomposition du liquide lors de la pulvérisation). De petites gouttelettes atteignent instantanément tM et commencent à s'évaporer, modifiant les paramètres du gaz vers une augmentation de la teneur en humidité ;
chauffer et condenser l'humidité. Tout cela se produit simultanément en l'absence de frontières claires.
Il est possible d'analyser de manière exhaustive les résultats du contact direct entre des gouttes d'un milieu accumulant de la chaleur et des gaz de combustion chauds uniquement sur la base d'un modèle mathématique qui prend en compte l'ensemble des phénomènes (transfert de chaleur et de masse se produisant simultanément, changements de paramètres du média, conditions aérodynamiques, composition polydispersée du flux de gouttes, etc.).
La description du modèle et les résultats de l'analyse basée sur celui-ci sont donnés dans la monographie, que nous recommandons au lecteur intéressé. Ici, nous ne notons que l'essentiel.
Pour la plupart des gaz de combustion, la température de bulbe humide se situe entre 45 et 55 °C, c'est-à-dire l'eau dans la zone de contact direct avec les gaz de combustion, comme indiqué ci-dessus, ne peut être chauffée qu'à la température spécifiée, mais avec une récupération de chaleur suffisamment profonde. L'humidification préliminaire des gaz, telle que prévue par la conception TANTEK, non seulement n'entraîne pas une augmentation de la quantité de chaleur utilisée, mais même sa diminution.
Et, enfin, il convient de garder à l'esprit que lors de l'utilisation de la chaleur, même à partir de gaz ne contenant pas de composés soufrés, ils ne doivent pas être refroidis en dessous de 80 ° C (leur évacuation dans l'environnement par le conduit et la cheminée est difficile).
Expliquons ce qui a été dit avec un exemple précis. Laisser les fumées après la chaudière d'une quantité de 5000 kg/h, ayant une température de 130°C et une teneur en humidité de 0,05 kg/kg, entrer en contact avec un fluide récupérateur de chaleur (eau, tH= 15°C). D'après le diagramme H-x, nous trouvons : tM= 49,5°C ; tp= 40°C; Je \u003d 64 kcal / kg. Des calculs sur modèle ont montré que lorsque les gaz sont refroidis à 80°C par un flux polydispersé de gouttelettes de diamètre moyen 480 μm, le taux d'humidité reste en fait inchangé (l'évaporation des petites gouttelettes est compensée par la condensation sur les grosses), tM devient égal à 45°C, et pouvoir calorifique I = 50 kcal/kg . Ainsi, 0,07 Gcal/h de chaleur est utilisée, et le milieu de stockage de chaleur en quantité de 2,5 m3/h est chauffé de 15 à 45°C.
Si nous utilisons TANTEK et procédons préalablement à l'humidification - refroidissement adiabatique des gaz à t-100°C, puis refroidissement à 80°C à X = const, alors les paramètres finaux du gaz seront : tM = 48°C ; I = 61,5°C. Et bien que l'eau chauffe un peu plus (jusqu'à 48°C), la quantité de chaleur utilisée diminue de 4 fois et sera de 0,0175 Gcal/h.
Options pour organiser la récupération de chaleur.
La solution à un problème spécifique d'utilisation de la chaleur des fumées dépend d'un certain nombre de facteurs, dont la présence de polluants (déterminée par le type de combustible brûlé et l'objet du chauffage des fumées), la présence d'un consommateur de chaleur ou directement de l'eau chaude , etc.
Lors de la première étape, il est nécessaire de déterminer la quantité de chaleur qui, en principe, peut être extraite des gaz de combustion disponibles et d'évaluer la faisabilité économique de la récupération de chaleur, car les coûts d'investissement ne sont pas proportionnels à la quantité de chaleur récupérée.
Si la réponse à la première question est oui, alors la possibilité d'utiliser de l'eau modérément chauffée doit être évaluée (par exemple, lors de la combustion de gaz naturel, envoyez-la pour préparer l'eau d'appoint pour les chaudières ou les systèmes de chauffage, et si le produit cible est contaminé par des particules de poussière, utilisez-le pour préparer la masse brute, par exemple, dans la production de produits céramiques, etc.). Si l'eau est trop polluée, il est possible de prévoir un système à deux circuits ou de combiner récupération de chaleur et épuration des fumées (pour obtenir des températures plus élevées (supérieures à 45-5 CPC) ou un étage de surface).
Il existe de nombreuses options pour organiser le processus de récupération de chaleur. L'efficacité économique de l'événement dépend du choix de la solution optimale.
Littérature:
1. Galustov B.C. Procédés et appareils de transfert de chaleur et de masse avec contact de phase direct dans l'ingénierie de l'énergie thermique // Énergie et gestion.— 2003.— n ° 4.
2. Galustov B.C. Appareil de pulvérisation à flux direct en génie thermique - M.: Energoatomizdat, 1989.
3. Soukhanov V.I. et autres Installations de récupération de chaleur et d'épuration des fumées des chaudières à vapeur et à eau chaude - M. : AQUA-TERM, juillet 2001.
4. Planovsky A.N., Ramm V.M., Kagan S.Z. Procédés et appareils de technologie chimique.— M. : Goshimizdat, 1962.—S.736-738.
Récupération de chaleur des gaz de combustion
Les fumées sortant de l'espace de travail des fours ont une température très élevée et emportent donc avec elles une quantité importante de chaleur. Dans les fours à foyer ouvert, par exemple, environ 80 % de toute la chaleur fournie à l'espace de travail est évacuée de l'espace de travail avec les gaz de combustion, dans les fours de chauffage, environ 60 %. De l'espace de travail des fours, les gaz de combustion emportent avec eux plus de chaleur, plus leur température est élevée et plus le facteur d'utilisation de la chaleur dans le four est faible. A cet égard, il convient d'assurer la récupération de la chaleur des fumées, qui peut s'effectuer en principe selon deux méthodes : avec retour d'une partie de la chaleur prélevée sur les fumées vers le four et sans retour de cette chauffer au four. Pour mettre en œuvre la première méthode, il est nécessaire de transférer la chaleur prélevée sur les fumées vers le gaz et l'air (ou uniquement l'air) entrant dans le four. Pour atteindre cet objectif, les échangeurs de chaleur de type récupérateur et régénératif sont largement utilisés, dont l'utilisation permet d'augmenter l'efficacité de l'unité de four, d'augmenter la température de combustion et d'économiser du carburant. Avec la deuxième méthode d'utilisation, la chaleur des fumées est utilisée dans les chaudières thermiques et les centrales à turbine, ce qui permet de réaliser d'importantes économies de combustible.
Dans certains cas, les deux méthodes décrites de récupération de la chaleur perdue sont utilisées simultanément. Cela se fait lorsque la température des gaz de combustion après les échangeurs de chaleur de type régénératif ou récupérateur reste suffisamment élevée et qu'une récupération de chaleur supplémentaire dans les centrales thermiques est recommandée. Ainsi, par exemple, dans les fours à foyer ouvert, la température des gaz de combustion après les régénérateurs est de 750 à 800 °C, ils sont donc réutilisés dans les chaudières de récupération.
Examinons plus en détail le problème de l'utilisation de la chaleur des fumées avec le retour d'une partie de leur chaleur au four.
Tout d'abord, il convient de noter qu'une unité de chaleur prélevée sur les fumées et introduite dans le four par l'air ou le gaz (une unité de chaleur physique) s'avère beaucoup plus précieuse qu'une unité de chaleur obtenue dans le four car résultant de la combustion de carburant (unité de chaleur chimique), car la chaleur de l'air chauffé (gaz) n'entraîne pas de perte de chaleur avec les gaz de combustion. La valeur d'une unité de chaleur physique est d'autant plus grande que le facteur d'utilisation du combustible est faible et que la température des gaz de combustion est élevée.
Pour un fonctionnement normal du four, la quantité de chaleur requise doit être fournie à l'espace de travail toutes les heures. Cette quantité de chaleur comprend non seulement la chaleur du combustible, mais également la chaleur de l'air ou du gaz chauffé, c'est-à-dire
Il est clair qu'avec = const l'augmentation permettra de diminuer . En d'autres termes, la récupération de la chaleur résiduelle des fumées permet de réaliser des économies de combustible, qui dépendent du degré de récupération de la chaleur des fumées.
où - respectivement, l'enthalpie de l'air chauffé et des gaz de combustion quittant l'espace de travail, kW ou kJ / période.
Le degré de récupération de chaleur peut également être appelé efficacité. récupérateur (régénérateur), %
Connaissant le degré de récupération de chaleur, il est possible de déterminer l'économie de carburant par l'expression suivante :
où je "d, Id - respectivement, l'enthalpie des gaz de combustion à la température de combustion et à la sortie du four.
La réduction de la consommation de combustible grâce à l'utilisation de la chaleur des gaz de combustion a généralement un effet économique important et constitue l'un des moyens de réduire le coût de chauffage du métal dans les fours industriels.
Outre l'économie de combustible, l'utilisation du chauffage à air (gaz) s'accompagne d'une augmentation de la température de combustion calorimétrique, qui peut être l'objectif principal de la récupération lors du chauffage de fours avec un combustible à faible pouvoir calorifique.
Une augmentation de at conduit à une augmentation de la température de combustion. S'il est nécessaire de fournir une certaine valeur, une augmentation de la température de chauffage de l'air (gaz) entraîne une diminution de la valeur, c'est-à-dire une diminution de la proportion de gaz à forte chaleur de combustion dans le mélange de carburant.
Étant donné que la récupération de chaleur peut considérablement économiser du combustible, il est conseillé de viser le degré d'utilisation le plus élevé possible et économiquement justifié. Cependant, il convient de noter immédiatement que le recyclage ne peut pas être complet, c'est-à-dire toujours. Cela s'explique par le fait qu'une augmentation de la surface de chauffe n'est rationnelle que dans certaines limites, après quoi elle conduit déjà à un gain d'économie de chaleur très insignifiant.
À l'heure actuelle, la température des gaz de combustion derrière la chaudière n'est pas inférieure à 120-130 ° C pour deux raisons: pour éviter la condensation de la vapeur d'eau sur les conduits de fumée, les conduits de fumée et les cheminées et pour augmenter le tirage naturel, ce qui réduit la pression de la fumée épuiseur. Dans ce cas, la chaleur des gaz d'échappement et la chaleur latente de vaporisation de la vapeur d'eau peuvent être utilement utilisées. L'utilisation de la chaleur des gaz de combustion et de la chaleur latente de vaporisation de la vapeur d'eau est appelée méthode d'utilisation en profondeur de la chaleur des gaz de combustion. Actuellement, il existe différentes technologies pour mettre en œuvre cette méthode, testées en Fédération de Russie et largement utilisées à l'étranger. La méthode d'utilisation en profondeur de la chaleur des gaz de combustion permet d'augmenter l'efficacité d'une installation consommatrice de combustible de 2 à 3 %, ce qui correspond à une réduction de la consommation de combustible de 4 à 5 kg d'équivalent combustible. pour 1 Gcal de chaleur générée. Lors de la mise en œuvre de cette méthode, il existe des difficultés techniques et des limitations associées principalement à la complexité du calcul du processus de transfert de chaleur et de masse avec une utilisation profonde de la chaleur des gaz de combustion et à la nécessité d'automatiser le processus, cependant, ces difficultés peuvent être résolues avec le niveau actuel de la technologie.
Pour la mise en œuvre généralisée de cette méthode, il est nécessaire d'élaborer des lignes directrices pour le calcul et l'installation de systèmes de récupération de la chaleur profonde des gaz de combustion et l'adoption d'actes juridiques interdisant la mise en service d'installations utilisant du gaz naturel sans l'utilisation de la chaleur profonde des gaz de combustion. récupération.
1. Formulation du problème selon la méthode (technologie) considérée pour augmenter l'efficacité énergétique; une prévision de dépassement des ressources énergétiques, ou une description d'autres conséquences possibles à l'échelle nationale tout en maintenant le statu quo
À l'heure actuelle, la température des gaz de combustion derrière la chaudière n'est pas inférieure à 120-130 ° C pour deux raisons: pour éviter la condensation de la vapeur d'eau sur les conduits de fumée, les conduits de fumée et les cheminées et pour augmenter le tirage naturel, ce qui réduit la pression de la fumée épuiseur. Dans ce cas, la température des fumées sortantes affecte directement la valeur de q2 - perte de chaleur avec les gaz sortants, l'un des principaux composants du bilan thermique de la chaudière. Par exemple, une diminution de la température des fumées de 40°C lorsque la chaudière fonctionne au gaz naturel et un taux d'air en excès de 1,2 augmente le rendement brut de la chaudière de 1,9 %. Ceci ne tient pas compte de la chaleur latente de vaporisation des produits de combustion. À ce jour, la grande majorité des chaudières à eau chaude et à vapeur de notre pays qui brûlent du gaz naturel ne sont pas équipées d'installations utilisant la chaleur latente de vaporisation de la vapeur d'eau. Cette chaleur est perdue avec les gaz d'échappement.
2. Disponibilité des méthodes, méthodes, technologies, etc. pour résoudre le problème donné
Actuellement, les procédés de récupération de la chaleur des gaz d'échappement profonds (VER) sont utilisés en utilisant des appareils de récupération, de mélange et combinés fonctionnant avec diverses méthodes d'utilisation de la chaleur contenue dans les gaz d'échappement. Parallèlement, ces technologies sont utilisées dans la plupart des chaudières mises en service à l'étranger qui brûlent du gaz naturel et de la biomasse.
3. Une brève description de la méthode proposée, sa nouveauté et sa notoriété, la disponibilité des programmes de développement ; entraîner une mise en œuvre massive à l'échelle nationale
La méthode la plus couramment utilisée de récupération de chaleur des gaz de combustion profonds est que les produits de combustion du gaz naturel après la chaudière (ou après l'économiseur d'eau) avec une température de 130-150°C sont divisés en deux flux. Environ 70 à 80 % des gaz sont envoyés par le conduit de fumée principal et pénètrent dans l'échangeur de chaleur à condensation de type surface, le reste des gaz est envoyé dans le conduit de dérivation. Dans l'échangeur de chaleur, les produits de combustion sont refroidis à 40-50°C, tandis qu'une partie de la vapeur d'eau est condensée, ce qui permet d'utiliser à la fois la chaleur physique des fumées et la chaleur latente de condensation d'une partie de la vapeur d'eau qu'ils contiennent. Les produits de combustion refroidis après le séparateur de gouttelettes sont mélangés aux produits de combustion non refroidis passant par le conduit de dérivation et à une température de 65-70°C, ils sont évacués par un extracteur de fumée à travers la cheminée dans l'atmosphère. En tant que milieu chauffé dans l'échangeur de chaleur, l'eau de source pour les besoins du traitement chimique de l'eau ou de l'air, qui entre ensuite dans la combustion, peut être utilisée. Pour intensifier l'échange de chaleur dans l'échangeur de chaleur, il est possible d'amener la vapeur du dégazeur atmosphérique dans le carneau principal. A noter également la possibilité d'utiliser la vapeur d'eau déminéralisée condensée comme eau de source. Le résultat de l'introduction de cette méthode est une augmentation du rendement brut de la chaudière de 2 à 3%, compte tenu de l'utilisation de la chaleur latente de vaporisation de la vapeur d'eau.
4. Prévision de l'efficacité de la méthode dans le futur, en tenant compte :
- la hausse des prix des ressources énergétiques ;
- la croissance du bien-être de la population ;
- introduction de nouvelles exigences environnementales ;
- autres facteurs.
Cette méthode améliore l'efficacité de la combustion du gaz naturel et réduit les émissions d'oxydes d'azote dans l'atmosphère en raison de leur dissolution dans la condensation de la vapeur d'eau.
5. Liste des groupes d'abonnés et des objets où cette technologie peut être utilisée avec une efficacité maximale ; la nécessité de recherches supplémentaires pour élargir la liste
Cette méthode peut être utilisée dans les chaudières à vapeur et à eau chaude utilisant du gaz naturel et liquéfié, du biocarburant comme combustible. Pour élargir la liste des objets où cette méthode peut être utilisée, il est nécessaire d'étudier les processus de transfert de chaleur et de masse des produits de combustion du mazout, du carburant diesel léger et de diverses qualités de charbon.
6. Identifier les raisons pour lesquelles les technologies écoénergétiques proposées ne sont pas appliquées à grande échelle ; esquisser un plan d'action pour éliminer les obstacles existants
L'application massive de cette méthode dans la Fédération de Russie n'est généralement pas effectuée pour trois raisons:
- Manque de sensibilisation à la méthode ;
- La présence de limitations techniques et de difficultés dans la mise en œuvre de la méthode ;
- Manque de fonds.
7. Disponibilité de restrictions techniques et autres sur l'application de la méthode sur divers objets ; en l'absence d'informations sur d'éventuelles limitations, il est nécessaire de les déterminer en testant
Les limites techniques et les difficultés de mise en œuvre de la méthode comprennent :
- La complexité du calcul du processus d'utilisation des gaz humides, puisque le processus de transfert de chaleur s'accompagne de processus de transfert de masse ;
- La nécessité de maintenir les valeurs définies de température et d'humidité des gaz de combustion, afin d'éviter la condensation des vapeurs dans les conduits de gaz et la cheminée ;
- La nécessité d'éviter le gel des surfaces d'échange de chaleur lors du chauffage de gaz froids;
- Dans le même temps, il est nécessaire de tester les conduits de gaz et les cheminées traités avec des revêtements anticorrosion modernes afin de réduire les restrictions de température et d'humidité des gaz de combustion sortant après l'installation de récupération de chaleur.
8. Le besoin de R&D et de tests supplémentaires ; thèmes et objectifs du travail
Le besoin de R&D et d'essais supplémentaires est indiqué aux paragraphes 5 et 7.
9. Incitations existantes, coercition, incitations à la mise en œuvre de la méthode proposée et nécessité de les améliorer
Il n'existe pas de mesures existantes pour encourager et contraindre l'introduction de cette méthode. L'intérêt de réduire la consommation de carburant et les émissions d'oxydes d'azote dans l'atmosphère peut stimuler l'introduction de cette méthode.
10. La nécessité d'élaborer de nouvelles lois et réglementations ou de modifier celles qui existent
Il est nécessaire d'élaborer des lignes directrices pour le calcul et l'installation de systèmes de récupération de chaleur des gaz de combustion profonds. Peut-être est-il nécessaire d'adopter des actes juridiques interdisant la mise en service d'installations consommant du gaz naturel sans l'utilisation d'une récupération de chaleur profonde des gaz de combustion.
11. Disponibilité des décrets, règles, instructions, normes, exigences, mesures d'interdiction et autres documents réglementant l'utilisation de cette méthode et obligatoires pour l'exécution ; la nécessité d'y apporter des modifications ou la nécessité de modifier les principes mêmes de la formation de ces documents ; la présence de documents réglementaires préexistants, de réglementations et la nécessité de leur restauration
Il n'y a pas de questions concernant l'application de cette méthode dans le cadre réglementaire existant.
12. Disponibilité des projets pilotes mis en œuvre, analyse de leur efficacité réelle, lacunes identifiées et propositions d'amélioration de la technologie, compte tenu de l'expérience accumulée
Il n'y a pas de données sur la mise en œuvre à grande échelle de cette méthode dans la Fédération de Russie, il existe une expérience de mise en œuvre dans les CHPP de RAO EES et, comme mentionné ci-dessus, une grande expérience a été accumulée dans l'utilisation profonde des gaz de combustion à l'étranger. L'Institut panrusse de génie thermique a réalisé des études de conception d'installations d'utilisation en profondeur de la chaleur des produits de combustion pour les chaudières à eau chaude PTVM (KVGM). Les inconvénients de cette méthode et des suggestions d'amélioration sont donnés au paragraphe 7.
13. La possibilité d'influencer d'autres processus lors de l'introduction massive de cette technologie (changements de la situation environnementale, impact possible sur la santé humaine, fiabilité accrue de l'approvisionnement énergétique, changements dans les horaires de chargement quotidiens ou saisonniers des équipements électriques, changements dans les indicateurs économiques de production et transport d'énergie, etc.)
L'introduction massive de cette méthode réduira la consommation de carburant de 4 à 5 kg d'équivalent carburant. par Gcal de chaleur générée et affectera l'environnement en réduisant les émissions d'oxydes d'azote.
14. Disponibilité et suffisance des capacités de production en Russie et dans d'autres pays pour la mise en œuvre massive de la méthode
Les installations de production spécialisées de la Fédération de Russie sont en mesure d'assurer la mise en œuvre de cette méthode, mais pas dans une version monobloc ; lors de l'utilisation de technologies étrangères, une version monobloc est possible.
15. La nécessité d'une formation spéciale de personnel qualifié pour le fonctionnement de la technologie mise en œuvre et le développement de la production
Pour mettre en œuvre cette méthode, une formation de profil existant des spécialistes est nécessaire. Il est possible d'organiser des séminaires spécialisés sur la mise en œuvre de cette méthode.
16. Méthodes de mise en œuvre suggérées :
1) financement commercial (avec recouvrement des coûts) ;
2) un concours pour la mise en œuvre de projets d'investissement développés à la suite de travaux sur la planification énergétique pour le développement d'une région, d'une ville, d'un établissement ;
3) financement budgétaire pour des projets efficaces d'économie d'énergie avec de longues périodes de récupération;
4) introduction d'interdictions et d'exigences obligatoires pour l'utilisation, contrôle de leur respect;
5) autres offres.
Les méthodes de mise en œuvre suggérées sont :
- financement budgétaire;
- attraction des investissements (période de récupération 5-7 ans);
- introduction d'exigences pour la mise en service de nouvelles installations consommatrices de combustible.
Pour ajouter une description de la technologie d'économie d'énergie au Catalogue, remplissez le questionnaire et envoyez-le à marqué "au catalogue".
La chaleur des gaz de combustion sortant des fours, en plus du chauffage de l'air et du combustible gazeux, peut être utilisée dans des chaudières de récupération pour générer de la vapeur. Alors que le gaz et l'air chauffés sont utilisés dans l'unité de four elle-même, la vapeur est envoyée à des consommateurs externes (pour la production et les besoins énergétiques).
Dans tous les cas, il faut s'efforcer d'obtenir la plus grande récupération de chaleur, c'est-à-dire de la restituer dans l'espace de travail du four sous forme de chaleur provenant des composants de combustion chauffés (combustible gazeux et air). En effet, une augmentation de la récupération de chaleur entraîne une réduction de la consommation de combustible et une intensification et amélioration du procédé technologique. Cependant, la présence de récupérateurs ou de régénérateurs n'exclut pas toujours la possibilité d'installer des chaudières de récupération. Tout d'abord, les chaudières à récupération de chaleur ont trouvé une application dans les grands fours avec une température relativement élevée des gaz de combustion: dans les fours de fusion d'acier à foyer ouvert, dans les fours à réverbère de fusion du cuivre, dans les fours rotatifs pour le grillage du clinker de ciment, dans la méthode sèche de la production de ciment, etc.
Riz. 5.
1 - surchauffeur ; 2 - surface du tuyau ; 3 - extracteur de fumée.
La chaleur des gaz de combustion des régénérateurs des fours à foyer ouvert à une température de 500 à 650 ° C est utilisée dans les chaudières à récupération de chaleur à tubes de gaz avec circulation naturelle du fluide de travail. La surface de chauffe des chaudières à tubes de gaz est constituée de tubes de fumée à l'intérieur desquels les gaz de combustion passent à une vitesse d'environ 20 m/s. La chaleur des gaz vers la surface chauffante est transférée par convection, et donc une augmentation de la vitesse augmente le transfert de chaleur. Les chaudières à tubes à gaz sont faciles à utiliser, ne nécessitent pas de revêtement et de cadres lors de l'installation et ont une densité de gaz élevée.
Sur la fig. La figure 5 montre une chaudière à tubes de gaz de l'usine de Taganrog avec une productivité moyenne D cf = 5,2 t/h avec l'attente de faire passer des gaz de combustion jusqu'à 40 000 m 3 /h. La pression de vapeur générée par la chaudière est de 0,8 MN/m 2 ; température 250 °C. La température des gaz avant la chaudière est de 600 °C, derrière la chaudière de 200 à 250 °C.
Dans les chaudières à circulation forcée, la surface de chauffe est constituée de serpentins dont l'emplacement n'est pas limité par les conditions de circulation naturelle, et donc ces chaudières sont compactes. Les surfaces des serpentins sont constituées de tuyaux de petit diamètre, par exemple d = 32×3 mm, ce qui allège le poids de la chaudière. Avec une circulation multiple, lorsque le rapport de circulation est de 5 à 18, la vitesse de l'eau dans les tubes est importante, au moins 1 m / s, ce qui entraîne une diminution de la précipitation des sels dissous de l'eau dans les serpentins et du cristallin le tartre est lavé. Cependant, les chaudières doivent être alimentées avec de l'eau purifiée chimiquement par des filtres cationiques et d'autres méthodes de traitement de l'eau qui répondent aux normes d'eau d'alimentation des chaudières à vapeur conventionnelles.

Riz. 6.
1 - surface de l'économiseur ; 2 - surface d'évaporation; 3 - surchauffeur ; 4 - tambour collecteur; 5 - pompe de circulation ; 6 - piège à boues ; 7 - extracteur de fumée.
Sur la fig. La figure 6 montre la disposition des surfaces de chauffe des serpentins dans les cheminées verticales. Le mouvement du mélange vapeur-eau est assuré par une pompe de circulation. Les conceptions de chaudières de ce type ont été développées par Tsentroenergochermet et Gipromez et sont fabriquées pour des débits de gaz de combustion allant jusqu'à 50 - 125 000 m 3 / h avec une production moyenne de vapeur de 5 à 18 t / h.
Le coût de la vapeur est de 0,4 - 0,5 RUR/t au lieu de 1,2 - 2 RUR/t pour la vapeur extraite des turbines à vapeur des centrales de cogénération et de 2 - 3 RUR/t pour la vapeur des chaudières industrielles. Le coût de la vapeur se compose des coûts énergétiques liés à l'entraînement des extracteurs de fumée, des coûts de préparation de l'eau, des amortissements, des réparations et de l'entretien. La vitesse des gaz dans la chaudière est de 5 à 10 m/s, ce qui assure un bon transfert de chaleur. La résistance aérodynamique du trajet du gaz est de 0,5 à 1,5 kN / m 2, de sorte que l'unité doit avoir un tirage artificiel de l'extracteur de fumée. L'augmentation du tirage qui accompagne l'installation de chaudières à récupération de chaleur améliore généralement le fonctionnement des fours à foyer ouvert. De telles chaudières se sont généralisées dans les usines, mais leur bon fonctionnement nécessite une protection des surfaces chauffantes contre l'entraînement des particules de poussières et de laitier et un nettoyage systématique des surfaces chauffantes de l'entraînement par soufflage à la vapeur surchauffée, lavage à l'eau (lorsque la chaudière s'arrête ), par vibration, etc.

Riz. 7.
Pour utiliser la chaleur des fumées des fours à réverbère de fusion du cuivre, des chaudières à tubes d'eau à circulation naturelle sont installées (Fig. 7). Dans ce cas, les gaz de combustion ont une température très élevée (1100 - 1250 ° C) et sont pollués par des poussières allant jusqu'à 100 - 200 g / m 3, et une partie de la poussière a des propriétés abrasives (abrasives) élevées, le l'autre partie est à l'état ramolli et peut scories la surface de chauffe de la chaudière. C'est la forte teneur en poussières des gaz qui oblige pour l'instant à abandonner la récupération de chaleur dans ces fours et à limiter l'utilisation des fumées dans les chaudières de récupération.
Le transfert de chaleur des gaz vers les surfaces d'évaporation de l'écran se déroule de manière très intensive, ce qui assure une vaporisation intensive des particules de scories, le refroidissement, la granulation et la chute dans l'entonnoir à scories, ce qui élimine les scories de la surface de chauffage par convection de la chaudière. L'installation de telles chaudières pour l'utilisation de gaz à température relativement basse (500 - 700 ° C) n'est pas pratique en raison du faible transfert de chaleur par rayonnement.
Dans le cas d'équipements de fours à haute température avec récupérateurs de métaux, il est conseillé d'installer des chaudières de récupération directement derrière les chambres de travail des fours. Dans ce cas, la température des fumées dans la chaudière chute à 1000 - 1100 °C. Avec cette température, ils peuvent déjà être dirigés vers la partie résistante à la chaleur de l'échangeur de chaleur. Si les gaz transportent beaucoup de poussière, la chaudière de récupération de chaleur est agencée sous la forme d'une chaudière de granulation de laitier à tamis, ce qui assure la séparation de l'entraînement des gaz et facilite le travail de l'échangeur de chaleur.