Informations générales sur l'installation de ponts roulants. Plateformes, clôtures et galeries pour la maintenance des portiques Dimensions des poutres de la grue à plate-forme Dimensions
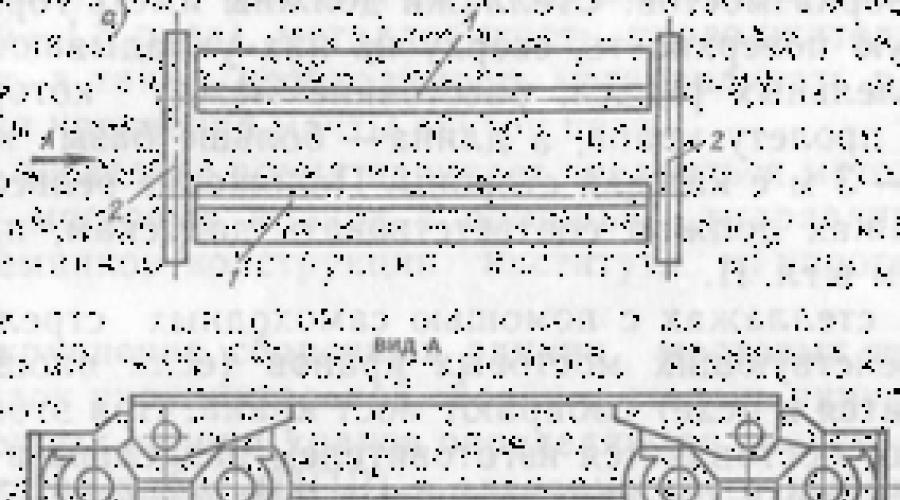
Les règles relatives aux grues réglementent la construction d'escaliers destinés à l'accès depuis l'étage de l'atelier aux plates-formes et galeries de débarquement et de réparation situées le long des voies de la grue, ainsi que des escaliers situés sur la grue elle-même.
Les exigences pour les échelles situées à l'extérieur de la grue et pour les échelles situées sur la grue sont différentes.
Les escaliers permettant d'accéder depuis le sol de l'atelier aux plates-formes et galeries situées à l'extérieur de la grue doivent être inclinés avec un angle d'inclinaison par rapport à l'horizon ne dépassant pas 60° et une largeur d'au moins 600 mm. La largeur des escaliers est considérée comme la distance libre entre les bords intérieurs des garde-corps. Les marches de ces escaliers sont constituées d'au moins 120 mm de large à partir de tôles d'acier ondulées ou lisses à relief fusionné. Pour les escaliers nouvellement installés, l'utilisation de marches en tiges n'est pas autorisée.
L'emplacement des échelles doit empêcher la possibilité de coincer des personnes dessus par une grue en mouvement ou sa cabine. Dans les escaliers déjà terminés dans endroits dangereux Une clôture solide ou grillagée doit être prévue. Les escaliers sur la grue elle-même sont rendus verticaux ou avec n'importe quel angle d'inclinaison requis ; la largeur de ces escaliers est considérée comme étant d'au moins 500 mm.
Pour les échelles d'une hauteur inférieure à 1,5 m situées sur la grue, ainsi que pour les échelles destinées à sortir de la cabine vers la galerie des grues de type pont ou cantilever mobiles, la largeur peut être réduite à 350 mm. Pour plus de commodité et de sécurité d'utilisation, les marches des escaliers verticaux doivent être séparées de la structure métallique de la grue à une distance d'au moins 150 mm, sinon il est difficile de poser le pied sur la marche et risque de tomber du des escaliers ne peuvent pas être exclus.
La clôture des escaliers verticaux est réalisée avec des arcs situés à une distance maximale de 800 mm les uns des autres et reliés entre eux par au moins trois bandes longitudinales. La distance entre les escaliers et l'arc doit être d'au moins 700 et d'au plus 800 mm avec un rayon d'arc de 400 mm.
Une telle clôture est réalisée pour des escaliers d'une hauteur supérieure à 5 m, à partir d'une hauteur de 3 m. Si l'escalier de la grue est situé à un angle supérieur à 75° par rapport à l'horizon, les exigences relatives à une clôture verticale sont alors requises. les escaliers s'y appliquent pleinement. Les protections contre les arcs ne sont pas nécessaires si l'escalier passe à l'intérieur d'une colonne en treillis d'une section ne dépassant pas 900 x 900 mm ou d'une tour tubulaire d'un diamètre ne dépassant pas 1 000 mm.
Si la hauteur des escaliers est supérieure à 10 m, des plates-formes doivent être disposées tous les 6 à 8 m. Si les escaliers sont situés à l'intérieur d'une tour tubulaire, de telles plates-formes ne peuvent pas être aménagées.
Articles populaires
|
Une équipe d'experts de la société Crane-Expert assure l'installation, la maintenance et l'assistance comptable lors de la mise en service des grues à poutre d'atelier,
ainsi que d'autres mécanismes plus petits pour soulever des charges, affectant l'ensemble du cycle de travail spécialisé - de la conception à l'entretien de l'équipement fini.
Zones de service des grues
Les grues sont un domaine d'équipements efficaces, mais très dangereux à utiliser. Ils nécessitent un service constant et soigné et rénovation majeure, ce qui prend énormément de temps. La société Crane-Expert est engagée dans la création de projets, la production et l'installation de plates-formes de service de grues, d'échelles de montée jusqu'au chemin de roulement des grues et de panneaux pour les galeries piétonnes des ponts roulants. Ce processus est divisé en plusieurs étapes.
Conception
Les employés de l'entreprise créent pour eux des projets de plates-formes de service pour assurer le fonctionnement des grues et des galeries. Leur forme et leur résistance dépendent des conditions d'installation et des tâches auxquelles sont confrontés les salariés. Toutes les structures subissent une justification numérique pour plus de solidité.
Construction
Les conceptions calculées en théorie sont assemblées de manière fiable à partir de matériaux durablesà base de produits métalliques. Les consommateurs reçoivent des plates-formes de service et des escaliers sur le chemin qui y mènent, théoriquement justifiés et testés plus d'une fois en production.
Fiabilité et durabilité
La société Crane-Expert a belle expérience maintenance des grues en fonctionnement sur les sites de service créés, leur exploitation et leur réparation. C'est l'un des aspects importants et directions nécessaires maintenir la fonctionnalité des grues. Si vous avez une grue dans votre organisation et qu'il n'y a pas de plate-forme pour sa maintenance, contactez la société Crane-Expert et vos grues seront entretenues à partir de nouvelles plates-formes de grue conçues et installées par nos soins dans le cadre d'un seul contrat.
Pont de soutien robinet électrique possède un pont roulant qui enjambe la travée du bâtiment et repose avec des roues sur les rails du chemin de roulement. Le plus souvent, des ponts à double poutre sont utilisés, qui sont une structure de cadre composée de deux poutres principales spatialement rigides sur lesquelles sont posés des rails pour déplacer un chariot de fret et de deux poutres d'extrémité adjacentes aux poutres principales aux extrémités de la travée.
Sur les poutres principales se trouvent des plates-formes fixes qui servent à accueillir les mécanismes de mouvement de la grue, les armoires électriques et le passage du conducteur et des réparateurs. Toutes les plates-formes ont des garde-corps. Les poutres d'extrémité sont également équipées de garde-corps et sont utilisées pour la fixation des boîtes d'essieux avec roues de roulement, avec lesquelles la grue repose sur les rails du rail de la grue. Aux extrémités de ces poutres se trouvent des tampons et des interrupteurs de fin de course qui limitent le mouvement de la grue le long de la voie ferrée.
Pour faciliter le service constructions métalliques les grues sont équipées de galeries, de plates-formes et d'escaliers. La largeur de passage libre à travers la galerie destinée aux mécanismes d'entretien et aux équipements électriques est généralement d'au moins 500 mm pour les grues à entraînement central et de 400 mm pour les grues à entraînement séparé. Sur une galerie destinée à l'installation de fils de chariots, la largeur de passage entre les garde-corps et les dispositifs supportant les chariots, ainsi que les collecteurs de courant, est fixée à au moins 400 mm. Le revêtement de sol de la galerie, des zones de réparation et du palier est en métal ou en bois sur toute la longueur de la galerie ou de la zone. Les revêtements de sol métalliques sont constitués de tôles d'acier ondulées ou perforées avec des trous d'un diamètre ne dépassant pas 20 mm.
Les plates-formes, galeries, poutres d'extrémité, ainsi qu'une cabine pour l'entretien des câbles de chariot des ponts roulants sont clôturées par des garde-corps d'au moins 1 m de haut avec une clôture continue en partie basse d'une hauteur d'au moins 100 mm. Ce dernier permet d'éliminer la chute involontaire d'outils et de pièces détachées du pont roulant lors de l'entretien de la grue. Des garde-corps et des clôtures sont également installés sur les extrémités des chariots à marchandises et, en l'absence de galerie, le long du pont sur les côtés longitudinaux. Les trappes du plancher de la galerie et des zones de réparation sont équipées de couvercles à ouverture pratique. Si le panneau est articulé, l'angle entre le panneau d'écoutille en position ouverte et le pont ne dépasse pas 75°. Les dimensions de la trappe sont d'au moins 500X500 mm.
Les escaliers permettant d'accéder du sol aux plates-formes et aux galeries ont une largeur d'au moins 600 mm et la distance entre les marches ne dépasse pas 300 mm. Si la hauteur de l'échelle sur la grue est inférieure à 1,5 m, une largeur d'échelle de 500 mm est autorisée. Les escaliers permettant de sortir de la cabine vers la galerie du pont roulant peuvent avoir une largeur d'au moins 350 mm. Les escaliers inclinés avec un angle d'inclinaison par rapport à l'horizon de 75° ou moins sont équipés de garde-corps et de marches plates en tôle d'acier ondulée ou lisse à relief fusionné ; La largeur des marches doit être d'au moins 120 mm. Dans les escaliers verticaux, ainsi que dans les escaliers présentant un angle d'inclinaison par rapport à l'horizon supérieur à 75°, des clôtures en forme d'arc sont installées à une hauteur de 3 m. Ces clôtures sont situées à une distance maximale de 800 mm les unes des autres et sont reliées par au moins trois bandes d'acier longitudinales.
Informations générales sur l'installation de ponts roulants
Lors de l'installation des ponts roulants, les unités d'assemblage sont agrandies, livrées sur le site d'installation et disposées dans la zone de fonctionnement des appareils de levage, elles sont suspendues, les éléments agrandis sont soulevés sur les rails de la grue, les grues assemblées sont assemblées et calibré.
Le choix de la méthode d'installation des supports de pont dépend de leur conception et de leur poids, du lieu d'installation : à l'intérieur ou à l'extérieur du bâtiment, du délai de livraison par les fabricants, de l'état de préparation de l'installation, de la conception de la charpente du bâtiment, ainsi que du type et des caractéristiques des engins de levage disponibles. à l'organisme d'installation.
Les méthodes les plus largement utilisées pour installer des ponts roulants sont : – l'utilisation de grues à tour ou à flèche conçues pour l'installation structures de construction bâtiments; – en utilisant des grues automotrices à flèche ; en utilisant des structures de charpente de bâtiment, y compris des poulies, fixées à des colonnes ou des poutres de montage reposant sur deux fermes adjacentes, moins souvent - directement sur les fermes.
Récemment, la méthode développée par l'Institut Giprometallurgmontazh pour l'installation de grues entièrement assemblées en position basse, utilisant des équipements de lignes de convoyeurs pour l'assemblage et l'installation de blocs de revêtement de construction, s'est généralisée.
La méthode auparavant répandue de montage de grues à l'aide de mâts n'est actuellement utilisée que dans les cas où il n'y a pas d'autres dispositifs ou mécanismes de levage disponibles ou ne peuvent pas être utilisés, par exemple, les conditions de l'atelier ne permettent pas l'utilisation d'une grue automotrice et la structure de sa charpente ne permet pas la pose d'une poutre d'assemblage.
Les principaux inconvénients de cette méthode sont la plus grande intensité de travail par rapport aux autres (1,5 à 1,8 fois), la consommation de métal, la durée du travail, ainsi que la nécessité d'installer des renforts pour fixer le mât à l'intérieur de l'atelier.
Récemment, la méthode d'installation de ponts roulants à l'aide d'ascenseurs hydrauliques conçue par l'Institut Giprotechmontazh a commencé à être introduite.
Consolidation des unités d'assemblage de ponts roulants.
L'ordre d'assemblage agrandi et le degré d'agrandissement des unités d'assemblage de grues sont déterminés par le plan d'exécution des travaux (WPP), en fonction de la méthode d'installation choisie et des modalités de livraison des grues.
L'assemblage élargi des structures, des mécanismes et des équipements électriques des ponts roulants a pour but d'effectuer le volume maximum de travaux d'assemblage en position basse et, par conséquent, de réduire au minimum le nombre d'opérations effectuées en hauteur. C'est pourquoi la meilleure option est celui dans lequel un pont est soulevé sur les rails de la grue, complètement assemblé en position basse, avec le chariot installé dessus, ou le pont est levé séparément, puis le chariot. Cependant, il n'est souvent pas possible de soulever et d'installer un pont roulant entièrement assemblé sur les rails de grue en raison de la capacité de levage insuffisante des mécanismes et dispositifs existants, de l'espace limité sous la flèche des grues automotrices utilisées et de l'incapacité (due faute de place) pour déployer le pont roulant assemblé dans un plan horizontal au-dessus des voies de la grue. De plus, il n'est pas toujours économiquement réalisable de fabriquer des supports et d'aménager des sites pour l'assemblage des ponts roulants.
Le plus souvent, les ponts roulants sont montés en deux ou quatre unités d'assemblage ; le chariot est monté dans une unité agrandie et la cabine de commande est montée dans l'autre.
Assemblage agrandi de ponts. Les structures métalliques des ponts sont agrandies en position basse dans les cas où le pont est soulevé sur les rails de la grue en un seul bloc. Pour ce faire, sur le site de montage agrandi (si l'espace le permet) ou sur un site spécialement prévu à cet effet, au plus près du site d'installation, des crémaillères pour le montage des ponts sont installées. Les racks doivent avoir une surface horizontale; deux rails parallèles sont posés dessus, dont la distance est égale à la portée de la grue et dont la longueur est de 2,5 à 3 m supérieure à la base de la grue de chaque côté.
Le pont roulant est assemblé sur les crémaillères à l'aide de flèches automotrices ou de ponts roulants opérationnels (si le chantier est situé en atelier). Dans ce cas, si le pont est fourni par le fabricant séparément sous la forme de deux poutres principales et de deux poutres d'extrémité (Fig. 74, a), quatre joints d'assemblage des poutres principales avec les poutres d'extrémité sont assemblés. Si le pont est fourni sous la forme de deux poutres principales avec des parties des poutres d'extrémité (demi-ponts), assembler les joints reliant les parties des poutres d'extrémité : deux - si les poutres principales sont fournies pour une installation avec des moitiés de poutres d'extrémité. poutres d'extrémité (Fig. 74, b), et quatre si Les parties extérieures des poutres d'extrémité sont fixées aux poutres principales et leurs parties médianes (inserts) 3 sont fournies séparément (Fig. 74, c).
Les joints d'assemblage sont assemblés en deux étapes : d'abord, à l'aide de boulons de montage (assemblage), et après alignement et élimination des distorsions, enfin, par soudage, nettoyer les boulons ou les rivets conformément aux instructions des dessins d'exécution.
Lors de l'assemblage d'un pont installé selon le schéma illustré à la Fig. 74, et, dans un premier temps, des poutres d'extrémité avec roues ou équilibreurs sont installées sur les rails posés sur les crémaillères et fixées (temporairement sécurisées) dans dans la bonne position. Après cela, l'une des poutres principales est insérée entre les poutres d'extrémité jusqu'à ce que les trous pour les boulons de montage dans les joints soient alignés et qu'ils soient reliés par des boulons. Ensuite, la deuxième poutre principale est également installée et reliée aux poutres d'extrémité.
Assemblage des ponts roulants fournis selon les schémas présentés à la Fig. 74, b, c, commencez par installer des demi-ponts à roues ou équilibreurs sur les crémaillères. Si les ponts sont fournis selon le schéma montré à la Fig. 74, c, puis les parties médianes des poutres d'extrémité - inserts - sont installées entre les demi-ponts. Ensuite, les demi-ponts sont rassemblés et les trous pour les boulons de montage dans les plaques de couche sont alignés selon le schéma de marquage, après quoi ils sont reliés par des boulons.
74. Schémas de livraison des grues IOSG a - poutres principales et d'extrémité séparées : b - poutres principales avec moitiés de poutres d'extrémité ; c - les poutres principales avec les parties extérieures des poutres d'extrémité et les inserts ; 1 - faisceau principal ; 2 - poutre d'extrémité ; 3 - insérer
Avant l'assemblage, les surfaces des éléments bout à bout sont soigneusement nettoyées de la terre séchée, de la peinture et de la rouille, et les surfaces des éléments bout à bout soudés sont nettoyées jusqu'à un éclat métallique. Lors de l'assemblage des joints, il est nécessaire d'obtenir une coïncidence maximale des trous et de ne pas permettre leur réglage par tension à l'aide de mandrins coniques, car cela crée des contraintes supplémentaires dans le métal. L'étanchéité des patins bout à bout est vérifiée à l'aide d'une jauge d'épaisseur : la plaque de sonde d'une épaisseur de 0,1 mm ne doit pas passer entre le patin et le corps de la poutre d'extrémité.
Les joints rivetés sont assemblés en enfonçant des mandrins (bouchons) dans les trous (pour rivets), qui sont utilisés pour remplir uniformément 10 à 15 % des trous de chaque côté du joint d'assemblage. Dans le même temps, des boulons de montage sont installés, qui sont utilisés pour remplir uniformément 20 à 25 % des trous. Les écrous des boulons ne sont pas complètement serrés.
Pour assembler les joints d'assemblage, en plus des grues de levage, des treuils à levier, des vérins, ainsi que des dispositifs simples pour fixer temporairement les éléments du pont dans la position souhaitée sont utilisés : supports, revêtements, équerres, sabots, etc.
Après avoir assemblé le pont, des plates-formes sont fixées aux murs extérieurs des poutres principales, des escaliers et des clôtures sont installés.
Recueilli à boulons de montage Le pont roulant est vérifié par contrôle et comparaison avec ceux indiqués dans les dessins ou le passeport : l'équerrage du pont, la travée du pont roulant, la voie du chariot de charge, l'ascenseur de construction du pont, l'installation des rails du chariot et des roues de roulement. de la grue.
L'équerrage du pont est vérifié de deux manières : par la différence des diagonales ou par la méthode d'alignement (à l'aide d'un théodolite). Les diagonales sont mesurées en des points symétriques du pont, qui peuvent être les points d'intersection des axes longitudinaux et transversaux des roues de roulement ; en pratique, elles sont réalisées sur des poutres d'extrémité ou des rails de bogie (Fig. 75), mais dans ce cas les dimensions a et a', b et b' doivent être respectivement égales entre elles. Les mesures des diagonales sont souvent effectuées aux points transférés aux poutres d'extrémité depuis les tangentes verticales aux circonférences des boudins des roues de roulement. Si l'équerrage du pont a été vérifié chez le fabricant (une mention correspondante est faite dans le passeport de la grue), alors lors de l'installation, les mesures des diagonales sont effectuées en fonction des repères de contrôle marqués sur les poutres d'extrémité ou les rails de bogie. La différence entre les diagonales d'un pont rectangulaire ne doit pas dépasser 5 mm.
75. Schéma d'alignement d'un pont roulant à l'aide d'un ruban à mesurer
76. Schéma d'alignement d'un pont roulant à l'aide d'un théodolite
1 - théodolite; 2-5 - roues; 6 - marque de visée
Pour les grandes portées de grues, cette méthode de contrôle n'est pas assez précise, car la mesure de grandes longueurs avec un ruban à mesurer nécessite une tension constante sur le ruban d'acier ; De plus, il n'est presque pas toujours possible de mesurer les diagonales sur le pont roulant. Dans ces cas, la deuxième méthode est plus souvent utilisée, à savoir la suivante.
Au point A, aux distances indiquées sur la Fig. 76, installez le théodolite, et au point B - marque de visée 6. Alignez l'axe de visée du théodolite avec le centre de la marque de visée, puis tournez longue-vue théodolite à 90° dans le plan horizontal (le long du membre) et fixez-le. Mesurez ensuite les distances X\, Xr, X3 et X4 depuis un fil à plomb installé le long de l'axe de visée du théodolite jusqu'à la surface d'extrémité des roues le long d'une corde passant par des points éloignés de l'axe d'au moins 300 mm. La longueur de corde est supposée être la même sur toutes les roues. Après cela, le théodolite est transféré au point A', et la marque cible au point B' et des mesures similaires sont effectuées sur les roues.
La condition de rectangle du pont est l'égalité des dimensions xx et x4, Xg et x3, ainsi que xb, prises entre les roues 3 et 4, 2 et 5. L'écart admissible de ces dimensions entre elles est de 3 pour les roues à flasque roues et 4 mm pour les roues à boudin.
La deuxième méthode permet également de vérifier simultanément le désalignement des roues de roulement dans les plans horizontal et vertical, puisque la différence de dimensions xx et X2, Xb détermine le désalignement dans le plan horizontal, et la différence de distances du plan vertical à des points similaires situés aux extrémités de la corde verticale caractérisent le désalignement dans le plan vertical.
Dans la première méthode de vérification de l'équerrage du pont, les désalignements des roues sont déterminés de la même manière, mais au lieu d'une ligne de visée théodolite, une ficelle et un fil à plomb sont utilisés. Les écarts des surfaces d'extrémité des roues par rapport aux plans horizontal et vertical ne doivent pas dépasser i mm pour 1 000 mm de diamètre de roue. La même tolérance est établie pour l'écart des extrémités des roues par rapport au plan général.
Si les écarts par rapport à l'équerrage du pont dépassent les valeurs spécifiées, le désalignement doit alors être éliminé.
Solution la plus courante Forme géométrique ponts roulants est le suivant. À l'un des coins du pont avec une diagonale plus grande, une butée est placée pour empêcher son mouvement longitudinal et transversal, et à l'autre coin - un vérin. Après avoir desserré le serrage des boulons de fixation, dirigez la force du vérin le long de l'axe de la poutre principale, qui est déplacée jusqu'à ce que la différence des diagonales devienne nulle ou dans la tolérance. Une autre façon de corriger la forme du pont consiste à fixer une poutre d'extrémité et à déplacer la seconde dans la direction de l'axe du rail de la grue.
L'écart admissible de la portée de la grue LK, mesurée au milieu des surfaces d'appui des roues de roulement pour les grues avec LK jusqu'à 40 m, est de ±6 mm, pour les grues avec LK supérieure à 40 m - ±7,5 mm.
L'écart dans les joints des rails de bogie 2 en plan et en hauteur ne doit pas dépasser 1 mm, et l'écart au niveau des joints ne doit pas dépasser 2 mm.
L'écart admissible entre la base du rail de bogie et l'entretoise ou la membrure supérieure de la poutre dépend du type de rail et peut être au niveau des bords de la base (voir taille g sur la Fig. 77) à partir de 0,75 mm pour le P4 rail à 2,5 mm pour le rail SKR140. Dans la partie médiane de la semelle, cet écart ne doit pas dépasser 0,3 mm (P4) à 1 mm (skr140).
Les déformations des roues dépassant les tolérances ci-dessus sont éliminées à l'aide d'entretoises installées entre les platines et les boîtes d'essieux des roues dans la poutre d'extrémité ou l'équilibreur, garantissant que la position des roues correspond aux dimensions obtenues lors du montage chez le constructeur et enregistrées dans un formulaire spécial, joint au passeport de la grue.
Le raccordement final des joints d'assemblage lors du soudage est effectué par des soudeurs certifiés selon les règles du Gosgortekhnadzor à une température non inférieure à moins 10 ° C conformément à les pré-requis techniques fabricant.
Les boulons propres utilisés pour relier les joints d'assemblage doivent avoir une longueur de partie non filetée de 8 à 10 mm inférieure à l'épaisseur de l'ensemble d'éléments à connecter. Insérez-les fermement dans les trous à l'aide d'un marteau. Le serrage des boulons lors de l'assemblage final des joints doit garantir un ajustement serré des pièces à connecter. Dans un joint serré, une sonde de 0,1 mm d'épaisseur peut être insérée entre les pièces jusqu'à une profondeur ne dépassant pas 20 mm au niveau de n'importe quel joint.
Le rivetage s'effectue à l'aide de marteaux pneumatiques manuels. Il s'agit d'une opération très laborieuse et difficile, c'est pourquoi ils s'efforcent d'effectuer le maximum de travaux de rivetage en position basse, avant de soulever les unités d'assemblage sur les rails de la grue.
Avant de commencer le rivetage, serrez les boulons propres qui fixent les garnitures au niveau des joints.
Ensuite, les trous pour les rivets sont vérifiés avec un calibre d'un diamètre inférieur de 1,5 mm au diamètre nominal du trou et les bavures sur les bords des trous sont éliminées, tandis que la profondeur et la largeur du fraisage des trous ne doivent pas dépasser 1,5 mm.
L'agrandissement des demi-ponts de grue consiste à installer le châssis et l'entraînement du mécanisme de déplacement (s'ils sont fournis séparément), ainsi que les plates-formes. Parfois, lors de l'assemblage agrandi de demi-ponts de grue installés selon le schéma présenté à la Fig. 74, c, au milieu, des parties des poutres d'extrémité sont placées sur l'un des demi-ponts pour réduire les travaux de montage en hauteur. Ce schéma d'agrandissement est utilisé lorsqu'il est possible de faire pivoter le demi-pont agrandi dans un plan horizontal lors du levage.
Le train de roulement du mécanisme de déplacement de la grue, dans lequel les poutres principales reposent directement sur des équilibreurs à roulettes, est installé en les faisant rouler le long des rails sous la poutre principale, et après avoir aligné les trous, ils sont reliés par un axe (arbre de liaison) .
L'installation du train de roulement des grues, dans lequel les poutres principales reposent sur les équilibreurs principaux (Fig. 78), commence par la fixation de petits équilibreurs dotés de roues de roulement. Pour ce faire, de petits équilibreurs sont d'abord installés et temporairement fixés sur les rails, sur lesquels l'équilibreur principal est amené sur le crochet du mécanisme de levage. Les axes sont insérés dans les trous alignés des équilibreurs principal et petit. Ensuite, l'équilibreur principal, assemblé avec des petits, est amené par le même mécanisme de levage jusqu'à l'extrémité de la poutre principale, posée sur les garnitures de traverses, et après avoir aligné les trous, ils sont reliés par un essieu.
La position des équilibreuses à roues est ajustée par des bagues d'espacement installées sur l'essieu de part et d'autre de l'équilibreuse conformément aux marquages d'usine. Une installation incorrecte des bagues d'espacement ou leur absence peut modifier la portée de la grue, ce qui est inacceptable. Les équilibreurs installés sont vérifiés pour le blocage en les balançant sur leurs axes.
L'entraînement du mécanisme de déplacement de la grue est assemblé après l'installation et l'alignement du châssis, ainsi que l'alignement et la connexion de l'arbre de sortie de la boîte de vitesses avec l'axe de la roue motrice dans la poutre d'extrémité ou l'équilibreur - après la connexion finale du montage joints des structures métalliques du pont. L'opération la plus difficile lors de l'assemblage du variateur est l'alignement des accouplements à engrenages de types MZ et MZP (avec un arbre intermédiaire). Condition connexion correcte les arbres sont leur alignement et l’absence de distorsions (dans les limites des tolérances).
78. Schéma d'accrochage des équilibreurs sur les poutres principales
1 - crochet du mécanisme de levage ; 2 - faisceau principal ; 3 - trous ; 4 - équilibreur principal ; b - petit équilibreur
79. Schéma de détermination du désalignement et du déplacement radial des accouplements
une - type MZ ; b - Type MZP
Lors de l'assemblage d'accouplements de type MZ (Fig. 79, a), le déplacement radial a, qui caractérise le désalignement des arbres connectés, et le désalignement, déterminé quantité linéaire s - tn-n ou angle с. Les quantités a, m et n sont déterminées en quatre points (dans deux plans mutuellement perpendiculaires). Le plus grand valeur admissible co = 0°30.
Lors de l'assemblage d'accouplements de type MZP (Fig. 79.6), le déplacement radial a et les distorsions e-b-c sont contrôlés.
Les valeurs admissibles de a, s, b, c et e dépendent des tailles (nombres) des accouplements dans lesquels elles sont indiquées ; documentation technique fabricant.
Au cours du processus d'alignement, les arbres connectés sont alignés, c'est-à-dire que leur alignement est réalisé et les distorsions sont éliminées, après quoi les accouplements sont finalement assemblés.
Enfin, les moteurs électriques et les freins sont installés, la position des moteurs électriques est vérifiée, leurs arbres sont alignés avec les arbres de la boîte de vitesses et fixés à la plaque ou au châssis sous moteur.
Le frein doit être installé de manière à ce que son centre coïncide avec le centre de la poulie de frein. Non parallélisme et désalignement des surfaces des patins par rapport à surface de travail les poulies ne doivent pas dépasser 0,1 mm pour 100 mm de largeur de poulie et le faux-rond radial - 0,05 mm pour 100 mm de diamètre de poulie.
Assemblage intégré de chariots. Les chariots-grues d'une capacité de levage allant jusqu'à 50 tonnes incluses sont fournis par les fabricants entièrement assemblés et prêts à être installés sur le pont roulant.
Les chariots-grues d'une capacité de levage de 80 tonnes et plus sont fournis sous forme d'unités d'assemblage séparées selon les schémas suivants : – le châssis du chariot assemblé avec le mécanisme de déplacement, les mécanismes de levage principaux et auxiliaires - les unités d'assemblage ; – la moitié du châssis avec un mécanisme de déplacement (sans train de roulement) et le mécanisme de levage principal, la moitié du châssis avec un mécanisme de levage auxiliaire et avec le train de roulement du mécanisme de déplacement ; – l'ensemble du châssis du chariot, les mécanismes de déplacement, les ascenseurs principaux et auxiliaires - en tant qu'unités d'assemblage ; – le châssis du chariot est en plusieurs parties, les mécanismes de déplacement, les ascenseurs principaux et auxiliaires sont dans des unités d'assemblage séparées.
Évidemment, la plus grande quantité de travail sur l'ensemble agrandi doit être effectuée lors de la livraison des chariots selon le dernier des schémas ci-dessus (c'est ainsi que sont fournis les chariots-grues d'une capacité de levage de 200/32 tonnes et plus). Le plus grand montage du chariot s'effectue sur un support spécial avec rails ou sur un pont roulant. Vous pouvez assembler le chariot sur une cage de traverse, puis procéder à l'alignement final des trains roulants de son mécanisme de déplacement sur le pont roulant. Tout d'abord, assemblez le châssis du chariot (s'il est fourni par le fabricant en pièces détachées) sur les boulons de fixation et installez les trains roulants du mécanisme de déplacement : roues ou équilibreurs.
Lors du montage du châssis, vérifier son équerrage en mesurant les diagonales aux points marqués à risques chez le constructeur lors du montage de contrôle du chariot ou directement sur le chantier d'installation. La différence entre les diagonales ne doit pas dépasser 3 mm.
Vérifiez ensuite l'installation correcte des roues de roulement ou des équilibreurs de la même manière que les trains de roulement du mécanisme de déplacement de la grue. Dans ce cas, en plus de l'inclinaison des roues de roulement, le déplacement du plan de symétrie vertical de la roue de roulement par rapport au même plan du rail, qui n'est pas autorisé de plus de 2 mm, est vérifié, ainsi que le support du chariot sur les rails du bogie avec toutes les roues (les centres des roues de roulement doivent être situés dans le même plan horizontal) et la base du chariot, mesurée d'un côté et de l'autre, dont la tolérance est de ±2 mm . Après alignement et élimination des déformations du cadre et du châssis, des gélifications sont réalisées l'assemblage final les cadres sont rivetés ou soudés conformément aux instructions des dessins du fabricant. Parfois, le train de roulement du mécanisme de déplacement du chariot est assemblé sur un châssis inversé, qui est ensuite incliné dans la position de conception.
Après rivetage ou soudage du châssis du chariot, le mécanisme de mouvement est enfin assemblé : la boîte de vitesses est installée (au préalable), les accouplements et les arbres sont assemblés et alignés, et ils sont également reliés aux roues, après quoi la boîte de vitesses est sécurisée. Installez ensuite le frein et le moteur électrique avec un demi-accouplement réalisé en forme de poulie de frein, centrez les arbres du moteur électrique et de la boîte de vitesses, du frein et fixez-les avec des boulons. S'il devient nécessaire de placer le demi-accouplement sur l'arbre du moteur électrique, cela se fait à coups légers d'un marteau en bois ou en cuivre, tandis que l'extrémité opposée de l'arbre est arrêtée ; le demi-accouplement est préchauffé à 60-80 °C.
Les unités d'assemblage des mécanismes de levage reposent sur des plaques traitées, il n'est donc pas nécessaire de régler leur position en hauteur avec des patins.
Le mécanisme de levage principal est assemblé dans l'ordre suivant : un tambour avec des roulements en bloc et un support est installé (une fois alignés et fixés, les cales de verrouillage sont martelées et fixées par soudage électrique), de petits engrenages d'un engrenage ouvert et un boîte de vitesses, puis un moteur électrique et un frein.
L'assemblage du mécanisme de levage auxiliaire commence par la boîte de vitesses, puis installe le tambour, le moteur électrique et le frein.
Lors de l'installation des tambours des mécanismes de levage principaux et auxiliaires Attention particulière devrait être donné montage correct et l'alignement des engrenages ouverts.
Les dents de l'engrenage de l'arbre de sortie de la boîte de vitesses doivent être uniformément encastrées entre les dents de l'engrenage mené du tambour. Lors de l'alignement, il est nécessaire de garantir la distance entre les essieux spécifiée dans les dessins et l'absence de désalignement des axes.
L'exactitude de l'assemblage est déterminée par les écarts maximaux du jeu latéral et de l'entraxe, ainsi que par la taille de la zone de contact des dents, qui est vérifiée pour la peinture.
Les moteurs électriques et les freins sont installés après assemblage complet et alignement des mécanismes. En même temps, les accouplements à engrenages et les arbres sont assemblés et alignés. Le désalignement et le déplacement mutuel des arbres des moteurs électriques et des boîtes de vitesses doivent être dans les tolérances spécifiées dans les dessins du fabricant et ne doivent en aucun cas dépasser la valeur admissible pour un accouplement à engrenages du numéro correspondant.
Après l'assemblage du pont roulant ou des demi-ponts d'agrandissement, ainsi qu'après l'assemblage du chariot, avant de soulever les unités d'assemblage sur les rails de la grue, l'équipement électrique est installé. Ce travail est réalisé par une équipe d'électriciens qui, conformément aux plans d'installation électrique, installent les boîtes à bornes et les adaptateurs, représente appareil électrique, poser les faisceaux électriques dans des coffrets et des gaines métalliques.
Installez ensuite les appareils électriques (transformateurs, démarreurs, boîtes de résistances, etc.), en vous assurant que la largeur des passages entre eux et les garde-corps de la clôture du chantier du pont est d'au moins 400 mm. Après cela, connectez les extrémités du câblage électrique aux bornes de l'équipement électrique et installez la mise à la terre de l'équipement électrique et du câblage électrique.
Les cabines de commande des ponts roulants sont généralement installées avec haut degré préparation de l'installation électrique. Mais parfois, l'installation électrique de la cabine doit être effectuée sur le site d'installation, y compris l'installation d'un panneau de protection, de contrôleurs, de lampes, de fins de course et d'interrupteurs d'urgence, de boutons, de boîtes à bornes et de jonction.
De plus, avant de lever le pont (ou les demi-ponts) de la grue, les luminaires de la grue sont installés et connectés.
Si les unités d'assemblage sont agrandies du site d'installation des ponts roulants dans la position de conception, elles sont ensuite transportées vers la zone d'installation le long des voies ferrées sur des plates-formes, des chariots spéciaux ou par des véhicules sur remorques. Lorsque le site d'assemblage de consolidation est situé à proximité du site d'installation des ponts roulants, les unités d'assemblage sont livrées sur la zone d'installation par des poseurs de canalisations.
Dans la zone d'installation, les éléments de montage sont disposés selon le mode d'installation choisi et en fonction des disponibilités. espace libre sur le site.
S'il y a suffisamment de place, les unités de montage du cadre sont amenées dans leur intégralité dans la zone d'installation et disposées de manière à ce que les plus lourdes d'entre elles se trouvent dans le rayon d'action des appareils de levage et qu'il ne soit pas nécessaire de les traîner. pour les soulever dans la position de conception.
Si, faute d'espace pour l'aménagement, toutes les unités d'assemblage de grues ne peuvent être livrées sur le site d'installation, elles sont fournies selon un calendrier convenu, précisé avant la livraison de chaque unité agrandie. Le plus efficace est « l'installation à partir de roues », c'est-à-dire le levage des unités d'assemblage de grues directement depuis Véhicule.
Fronde. Cette opération est très critique en production travaux de gréage et doit être réalisée en stricte conformité avec le G1PR, qui indique les schémas d'élingage des unités d'assemblage et le diamètre du câble utilisé pour la fabrication des élingues. Le schéma d'élingage peut être modifié ou la corde remplacée uniquement avec l'autorisation de l'organisation qui a développé le PPR.
Les ensembles de grues doivent être montés par des monteurs expérimentés.
Lors du choix d'une unité d'élingage et du nombre de fils de corde dans une élingue, ils ont tendance à utiliser des élingues avec le moins de fils possible en augmentant le diamètre de la corde, mais pas plus de 39 mm, car la corde grand diamètre il est difficile de faire des nœuds, surtout lors d'une élingage avec un nœud « boucle morte », et d'épisser les extrémités de la corde avec un nœud droit (« figure de huit »).
Lors du levage d'unités d'assemblage de faible masse, l'élingage est réalisé avec une élingue universelle ou légère.
Lors du levage d'unités d'assemblage lourdes, un câble en acier d'une longueur telle que l'élingue est nécessaire pour l'élingage selon le schéma accepté est utilisé.
Dans ces cas, les extrémités des cordes sont reliées par des nœuds droits ou à baïonnette, ainsi qu'à l'aide de diverses pinces.
Les poutres des ponts à caissons sont chevronnées avec diverses unités (Fig. 80). Un simple nœud annulaire (Fig. 80, a) est réalisé avec des élingues universelles ou à partir de morceaux de corde.
Le plus souvent, les poutres sont attachées avec un ou deux nœuds « boucle morte » (noeud coulant) (Fig. 80, b, c). Étant donné que les poutres sont soulevées avec les plates-formes et les éléments des mécanismes de mouvement, le centre de gravité de l'unité d'assemblage soulevée est décalé de l'axe de symétrie de la section de la poutre de la quantité K. Par conséquent, lors de l'élingage, la « boucle morte » " L'unité est décalée (voir Fig. 80.6) de cette valeur, qui peut être déterminée par calcul ou, comme cela se fait dans la pratique, par des essais de levage jusqu'à une hauteur de 100 mm avec réélingage ultérieur, si le besoin s'en fait sentir. Parfois, dans le même but, une élingue auxiliaire avec une entretoise est utilisée (voir Fig. 80, c), qui absorbe le moment de renversement provoqué par un déplacement du centre de gravité.
80. Poutres d'élingage des ponts à caissons
a - un simple nœud en anneau « dans la circonférence » ; b - nœud « boucle morte » déplacé ; c - un nœud « boucle morte » avec une élingue auxiliaire ; g - un nœud avec un fil superposé ; 1 - poutre de pont ; 2 - support ; 3 - élingue ; 4 - revêtement - 5 - plate-forme : 6 - crochet ou support du mécanisme de levage ; 7 - entretoise ; 8 - élingue auxiliaire ; 9 - fil qui se chevauche ; 10 - compression
Les poutres des grues lourdes sont souvent suspendues avec un nœud avec un fil superposé 9 (Fig. 80, d), qui assure une fixation fiable des fils de l'élingue principale et dans lequel ce nœud diffère d'un simple nœud annulaire. Dans ces cas-là, une élingue auxiliaire est également utilisée. Pour assurer la stabilité de la poutre à soulever, la distance L entre les élingues ou l'espacement des branches d'une élingue ne doit pas être inférieure à la moitié de la hauteur de la poutre I, c'est-à-dire L > > 0,5 R.
Pour protéger la corde des dommages causés par les arêtes vives des charges soulevées, des patins métalliques ou des patins en bois sont placés en dessous.
Dans certains cas, le fabricant de la grue ou les installateurs (en accord avec lui) soudent des œillets (avec éléments de renfort) aux membrures supérieures des poutres pour fixer le bloc mobile du mécanisme de levage (Fig. 81). Dans ces cas, il n'y a pas besoin d'élingues en corde, et le bloc mobile du moufle est fixé à la poutre 1 à l'aide de l'axe 5, fixé dans les trous de l'oeillet et de l'oeillet du moufle.
Le pont roulant assemblé est élingué à l'aide d'unités annulaires comme indiqué sur la Fig. 82. Pour éviter la déformation du pont pendant le processus de levage, des entretoises de tuyaux, réglables en longueur, sont installées entre les poutres principales.
Les chariots-grues sont suspendus derrière les poutres du châssis afin que les branches de l'élingue qui entourent les pièces de l'équipement ne les endommagent pas (Fig. 83).
Les chariots de petite capacité de charge sont suspendus avec des élingues universelles ou attachés avec une corde sous le châssis (Fig. 83, a, b). S'il y a des dispositifs d'élingue spéciaux sur le châssis du chariot - bossages, axes, agrafes, etc., les élingues sont alors attachées à ces dispositifs. Des chariots-grues robustes sont suspendus derrière la poutre du châssis principal, qui relie les poutres latérales. En figue. 83, c montre que le chariot est élingué avec deux élingues : la principale, attachant la poutre principale du châssis, et l'intermédiaire, attachée à l'élingue principale et allant au crochet ou au support de la poulie mobile du mécanisme de levage . D'autres systèmes d'élingage de chariots lourds sont également utilisés - sans élingues intermédiaires.
81 Fixation du palan à chaîne à l'œil
1 – poutre de pont ; 2 - renfort : 3 - œil ; 4 - boucle d'oreille à clip bloc ; 5 - doigt
82. Schéma d'élingue de pont roulant 1 - poutre d'extrémité ; 2 - élingue ; 3 - doublure; 4 - faisceau principal ; 5 - entretoise
83. Schémas d'élingage pour chariots ponts roulants
UN. b - élingue universelle ou en corde sous le châssis ; c - élingues principales et intermédiaires ; 1 - élingue intermédiaire ; 2 - élingue principale
Levage d'unités d'assemblage de grues sur des rails de grue. Cette opération est l'opération la plus critique lors de l'installation des ponts roulants et doit être réalisée dans le strict respect du PPR (avec schémas d'installation et instructions pour assurer conditions sécuritaires production d'œuvre). Le schéma d'installation peut être modifié dans les cas où il devient impossible (pour diverses raisons) d'utiliser les mécanismes de levage initialement prévus dans le projet, ou lorsque la situation sur le site d'installation change.
L'opération la plus difficile pour le levage d'ensembles de grues est le levage des poutres principales, des demi-ponts et des ponts entièrement assemblés.
Il existe deux méthodes principales pour les installer sur les rails de grue : – soulever le demi-pont (la poutre principale ou l'ensemble du pont) au-dessus des rails de grue dans une position où il est orienté le long de la travée ou selon un certain angle par rapport à son axe longitudinal , puis le tourner dans un plan horizontal et l'abaisser sur les rails de la grue.
La possibilité d'installer un demi-pont de cette manière est déterminée par la distance entre l'axe du rail de la grue et le mur du bâtiment, ainsi que par la largeur du demi-pont ; – relever le demi-pont en position inclinée - « poisson », lorsqu'un côté est en avance sur l'autre. Après qu'un côté ait dépassé la poutre de grue, le demi-pont est rétracté ou tiré du même côté et le deuxième côté du demi-pont est transporté au-delà de la deuxième poutre de grue, puis le demi-pont est abaissé sur les rails de la grue.
La séquence des unités d'assemblage des grues de levage dépend du degré de leur agrandissement et ne dépend pratiquement pas des mécanismes de levage utilisés à cet effet.
Ainsi, si une grue est montée avec deux demi-ponts (poutres principales avec pièces d'extrémité), alors un demi-pont est d'abord levé sur les rails de la grue, puis l'autre, les joints d'assemblage sont connectés, après quoi le chariot de grue est levé et installé sur la passerelle, suivi de la cabine de contrôle.
Une autre version de ce schéma est souvent utilisée, lorsque les demi-ponts surélevés et installés sur les voies de la grue sont écartés sur une distance dépassant la largeur du chariot de 400 à 600 mm, puis ils sont surélevés entre les demi-ponts écartés au-dessus du rails de chariot, après quoi les demi-ponts sont rapprochés, les joints de montage sont connectés et le chariot est abaissé sur le pont.
Si un pont roulant est assemblé à partir de deux poutres principales et de deux poutres d'extrémité, ils se soulèvent d'abord sur les rails de la grue et y fixent temporairement une poutre d'extrémité, puis la seconde, puis, à leur tour, soulèvent les poutres principales et les joignent à l'extrémité. poutres, puis soulevez et installez le chariot sur le pont, puis montez la cabine.
Dans les cas où le demi-pont d'une grue, dans lequel les poutres principales reposent sur des équilibreurs, ne peut pas être levé avec eux (la capacité de levage des mécanismes existants est insuffisante), les équilibreurs avec chariots d'équilibrage sont d'abord levés et temporairement fixés sur les chenilles de la grue. Ensuite, une poutre principale est levée et ses extrémités sont reliées aux équilibreurs, la deuxième poutre est également levée et installée sur les équilibreurs, après quoi les poutres d'extrémité sont alternativement levées et reliées aux poutres principales. La séquence d'installation du chariot et de la cabine de commande est la même que dans le premier des schémas évoqués ci-dessus, comprenant le levage du chariot entre les demi-ponts séparés, leur rapprochement, la connexion des joints et l'abaissement du chariot sur le pont.
Le plus petit nombre d'ascenseurs se produit dans les cas où les ponts roulants sont installés dans la position de conception par deux ou un bloc de montage : dans le premier cas, un pont et un chariot, dans le second, lorsqu'un pont roulant entièrement assemblé (avec un chariot fixe à son pont) est installé sur des rails de grue.
Quel que soit l'ordre dans lequel le pont roulant est assemblé sur les rails du pont roulant, le raccordement définitif des joints d'assemblage sur le pont roulant ne doit être effectué qu'après son alignement, qui s'effectue de la même manière que lors de l'assemblage du pont dans le position basse.
Pendant le processus d'assemblage, les demi-ponts sont déplacés le long des rails de grue à l'aide de treuils à levier manuel (montage de mécanismes de traction). Les haubans sont contrôlés manuellement pendant le processus de levage, de retournement et d'installation des demi-ponts sur les voies de la grue (avec un câble de chanvre). L'exception concerne les haubans, à l'aide desquels le demi-pont est déplacé sur le côté lors du levage en position inclinée - "poisson". Ces haubans sont fabriqués à partir de câbles en acier et sont actionnés par des treuils à levier manuel.
84. Schéma de levage d'un demi-pont avec deux grues
1 - grue à tour BK-1000 ; 2- demi-pont de la grue montée ; 3 - grue SKR-1500
Les grues à tour ou à flèche (type SKR) sont les plus efficaces pour soulever les unités d'assemblage des ponts roulants, qui sont utilisées pour assembler les structures de construction. Cette méthode est possible lorsque les ponts roulants sont fournis avant ou pendant la construction de la charpente du bâtiment. Dans ces cas, l'installation d'unités de montage ou de grues entièrement assemblées en position basse est effectuée simultanément à l'installation des structures du bâtiment avant son plafond, ou bien une ouverture est laissée dans le plafond suffisante pour alimenter les demi-ponts et les chariots à travers jusqu'au site d'installation ; ensuite, l'ouverture est fermée.
En fonction de l'emplacement des grues à tour sur chantier de construction lorsque la capacité de levage d'une grue à la portée de crochet requise n'est pas suffisante, les unités d'assemblage des ponts roulants sont levées par deux grues à tour (Fig. 84).
Les avantages de cette méthode sont que, d'une part, il n'est pas nécessaire d'avoir recours à d'autres engins de levage, et d'autre part, il est possible de combiner l'installation de la charpente du bâtiment et des ponts roulants, ce qui permet de les mettre en service à l'avance puis de les utiliser. non seulement pendant l'installation de l'équipement, avant et avant - pendant la construction des fondations de celui-ci. L'utilisation de grues à tour permet en outre d'installer des ponts roulants à des hauteurs élevées, par exemple dans la partie haute des ateliers de conversion d'oxygène, dans les « étagères » des chevalements de mines, etc.
Le principal facteur entravant l'adoption la plus large de cette méthode est la livraison tardive des ponts roulants, c'est-à-dire après la construction de la charpente du bâtiment, alors que les grues à tour ont déjà été démontées.
De plus, Fie peut toujours être monté sur n'importe quel pont roulant en raison d'une capacité de levage insuffisante. grue à tourà la portée requise de son crochet.
L'utilisation de grues automotrices à flèche de montage pour soulever des ensembles de ponts sur des rails de grue est l'une des méthodes les plus courantes d'installation de ces grues.
Les conditions d'utilisation à cet effet des grues automotrices à l'intérieur d'un bâtiment sont les suivantes : – ouvertures dans le bâtiment pour permettre le passage de la grue dans la zone d'installation ; – des plates-formes nivelées et compactées pour y installer des grues ; - suffisant Capacité de chargement plafonds des sous-sols et des canaux dans la zone de passage des grues ; – la présence de grues automotrices avec des caractéristiques de hauteur de charge qui assurent le levage et l'installation des éléments de la grue montée dans la position de conception ; Ces caractéristiques comprennent la capacité de levage, qui, à une portée de crochet donnée, doit correspondre à la masse de la charge à soulever, ainsi que l'espace sous flèche (dimension a sur la Fig. 85), qui doit assurer le levage des éléments du grue montée sans les reposer sur la flèche et être d'au moins 200 mm.
De plus, la grue d'installation doit s'adapter avec sa flèche aux dimensions du bâtiment dans lequel le pont roulant est installé : la distance h (voir Fig. 85) du haut de la flèche dans sa position la plus haute jusqu'au toit doit être de au moins 200 mm.
85. Schéma d'installation de demi-ponts d'un pont roulant sur des rails de grue à l'aide d'une grue d'installation
86. Schéma de levage d'un chariot de pont roulant à l'aide de deux grues automotrices
1 - appuyez sur ; 2 - traverser; 3 - élingue ; 4 - entretoise entre les poutres principales du pont ; 5 - pont roulant ; 6 - poutre de grue ; 7 - flèche
87. Schéma de levage d'un pont roulant à l'aide d'une grue automotrice avec un équipement de flèche spécial
L'espace sous le support et la capacité de levage souvent limités à la portée du crochet requise sont les principaux obstacles au levage d'un pont ou d'un chariot entièrement assemblé avec une seule grue de montage. Dans de tels cas, les gros éléments sont soulevés à l'aide de deux grues (Fig. 86). Parfois, on utilise à cet effet un équipement de flèche spécialement fabriqué (Fig. 87), qui est une flèche tubulaire avec une traverse dont la portée permet de placer un pont roulant entièrement assemblé dans l'espace de la flèche, et lorsque position verticale La grue à flèche a une capacité de levage maximale.
En figue. La figure 85 montre un schéma de l'installation de deux demi-ponts 2 et 3 d'un pont roulant sur les voies du pont roulant à l'aide d'un pont roulant de montage. La ligne pointillée marque la position de la grue de montage lors du levage du demi-pont I, ainsi que les positions initiales des deux demi-ponts. Le pont-pont selon ce schéma est assemblé comme suit. Tout d'abord, le demi-pont est soulevé de sa position d'origine, déployé dans un plan horizontal au-dessus des voies de la grue et abaissé sur celles-ci, puis, à l'aide de mécanismes de traction de montage, il est entraîné jusqu'à la position indiquée sur la figure. Ensuite, la grue de montage se déplace vers la droite, jusqu'à la position marquée par la position, et avec son aide le demi-pont est soulevé et installé sur les rails de la grue de la même manière que le demi-pont.
Le pont est assemblé en fonction du schéma d'installation du chariot adopté : s'il est alimenté au pont par le côté, alors les demi-ponts sont reliés immédiatement après avoir été levés sur les voies de la grue ; si le chariot est soulevé entre des demi-ponts écartés, ils sont alors réunis après que le chariot soit élevé au-dessus des voies du chariot et avant que le chariot ne soit descendu sur celles-ci. Dans ce cas, la grue de montage pour soulever le chariot est installée sous les demi-ponts écartés au milieu de sorte que sa flèche soit dirigée le long des demi-ponts, et la poulie de chargement est située au dessus du centre de masse du chariot. Après avoir installé le chariot sur le pont roulant, celui-ci est libéré des élingues et la grue de montage est chassée, en abaissant simultanément sa flèche entre les demi-ponts.
Lorsque la capacité de levage d'une grue n'est pas suffisante, les demi-ponts sont ensuite retournés et installés sur les chemins de roulement par deux grues d'assemblage. Dans ce cas, le demi-pont est suspendu des deux côtés, élevé au-dessus des voies de la grue et, en alternant les manœuvres des flèches et le changement de position de la grue, le demi-pont est déployé dans un plan horizontal, après quoi il est abaissé sur la grue. des pistes.
Deux grues de montage soulèvent les demi-ponts en position inclinée - « poisson » (Fig. 88). Une fois qu'un côté du demi-pont est élevé au-dessus des voies de la grue, en tournant les flèches de la grue, le demi-pont est déplacé de ce côté et le deuxième côté du demi-pont est élevé au-dessus des voies de la grue. Ensuite, retournez les bras de la grue verso et en modifiant la hauteur de leur levage, un demi-pont est installé sur les voies de la grue.
88. Schéma de levage d'un demi-pont à l'aide de deux grues de montage
D'après ceux montrés sur la Fig. Les schémas 85 et 88 soulèvent les poutres principales des ponts sur les rails de grue à la différence que selon le deuxième de ces schémas, les extrémités de la poutre principale doivent être surélevées au-dessus de la poutre d'extrémité ou de l'équilibreur (et non des rails de grue), ce qui sont installés avant les poutres principales.
89. Schéma d'installation de la poutre d'extrémité sur les rails de grue
1 - poutre d'extrémité ; 2 - coin ; 3 - pince; 4 - poutre en I ; 5 - colonne ; 6 - rail de grue
Lors de l'installation des grues de montage du côté des plates-formes du demi-pont, si nécessaire, ces plates-formes ne sont pas installées ou le platelage et les garde-corps des clôtures sont découpés aux endroits où passent les flèches des grues.
En figue. 89 montre un schéma d'installation d'une poutre d'extrémité ou d'un équilibreur sur des rails de grue, lorsque le pont roulant est assemblé à partir de quatre poutres (dont deux sont associées au châssis) ou de quatre poutres et équilibreurs, soulevés séparément.
Pour la fixation temporaire des poutres d'extrémité ou des équilibreurs sur les rails de grue, utiliser divers appareils, dont l'un est représenté sur la Fig. 89. Il comprend une poutre en I et un support constitué d'un angle et d'un dispositif de retenue réalisé sous la forme d'une plaque avec une découpe en forme de T. La pince est soudée à l'angle et l'angle à la membrure supérieure de la poutre d'extrémité. La poutre en I est également soudée à la colonne de l'atelier. La pince, tout en maintenant la poutre d'extrémité ou l'équilibreur sur le rail de la grue, n'empêche pas leur mouvement le long du rail de la grue, ce qui est nécessaire pour effectuer les opérations de liaison de la poutre principale avec la poutre d'extrémité ou pour y fixer l'équilibreur.
La poutre d'extrémité (ou équilibreur) est installée sur le chemin de roulement de la grue selon le schéma suivant. Tout d'abord, un dispositif à poutre en I ainsi que des supports sont fixés aux colonnes de l'atelier au-dessus des voies de la grue. Ensuite, la poutre d'extrémité est soulevée à l'aide d'une grue de montage et installée sur le chemin de roulement de la grue. Sans retirer l'élingue, soudez le coin de l'équerre à sa membrure supérieure (ou au corps de l'équilibreur), après quoi la poutre est libérée de l'élingue. La deuxième poutre d'extrémité du pont (ou poutre d'équilibre) est également installée, après quoi, selon l'une des méthodes décrites ci-dessus, une poutre principale est relevée et reliée aux poutres d'extrémité, puis la seconde. Si les poutres principales reposent sur des équilibreurs, alors, en les soulevant une à une, reliez leurs extrémités aux équilibreurs, puis soulevez les poutres d'extrémité et joignez-les aux poutres principales.
La plupart d'une manière simple L'installation de chariots-grues consiste à installer un chariot entièrement assemblé en position basse directement sur le pont roulant avec une ou deux grues d'installation installées sur le côté du pont. Si les caractéristiques des grues automotrices existantes ne le permettent pas, le chariot est installé en le soulevant entre les demi-ponts écartés, comme décrit ci-dessus.
Lorsque la capacité de levage des grues automotrices n'est pas suffisante pour soulever le chariot de cette manière, celui-ci est monté dans des unités d'assemblage séparées : d'abord, le châssis du chariot avec le mécanisme de déplacement et le mécanisme de levage auxiliaire est installé sur le pont roulant, et puis les unités d'assemblage du mécanisme de levage principal sont levées et montées sur son châssis.
90. Schémas d'installation des poutres de montage
91. Poutre de montage
1 - support de nappe d'acier ; 2 - superposition ; 3 - poutre en I ; 4 - tuyau; 5 - côte; 6 - ferme ; 7 - bloc de prise ; 8 -
palan à chaîne
Après le chariot, la cabine de la grue est installée. Pour ce faire, découpez un trou dans le plancher de la plate-forme de travail du pont roulant au centre de la fixation de la cabine pour le passage du crochet de grue de montage, et installez-le dans le parking indiqué sur le schéma d'installation. Après cela, après avoir sécurisé la cabine, ils la soulèvent jusqu'à la position de conception et la fixent au pont roulant.
Lorsque, pour diverses raisons, il est impossible d'utiliser des grues automotrices à tour ou à flèche, les ensembles de ponts roulants, particulièrement lourds, sont soulevés à l'aide de poulies suspendues aux structures de charpente du bâtiment ou à des poutres de montage reposant sur ces structures. Ce mode d'installation nécessite un renforcement préalable obligatoire des structures du bâtiment, sauf dans les cas où ce renforcement est prévu au préalable lors de la conception de la charpente du bâtiment.
L'un des moyens de soulever des ensembles de ponts roulants à l'aide de structures à ossature de bâtiment consiste à suspendre respectivement deux ou quatre poulies au sommet de deux ou quatre colonnes du bâtiment, à l'aide desquelles des demi-ponts, ou un pont roulant entièrement assemblé, sont soulevés «poissons», dans certains cas - avec un chariot fixé au pont afin qu'il ne bouge pas pendant le levage. Avec ce schéma d'installation, les filetages des poulies sont dirigés vers le bas le long des colonnes, où les blocs de sortie sont connectés, et à travers elles vers les treuils situés derrière l'atelier ou à l'intérieur de l'atelier à distance du site d'installation. Les inconvénients de cette méthode sont la nécessité de grandes quantités gréements et treuils, ainsi que d'assurer la stabilité des colonnes contre des forces pour lesquelles elles ne sont pas conçues. Cette méthode est donc rarement utilisée. Parfois, les poulies sont suspendues à deux fermes adjacentes, avec des entretoises placées entre elles.
La méthode la plus répandue de levage d'unités d'assemblage de ponts roulants utilise des poulies suspendues à des poutres de montage reposant sur deux fermes adjacentes 5 (Fig. 90, a), ou sur deux poutres auxiliaires b (Fig. 90.6), qui reposent sur des fermes voisines. À l'aide de poutres de montage, également appelées poutres de réparation et d'installation (car elles sont utilisées pour abaisser et soulever les unités d'assemblage de grues lors de leurs réparations dans les ateliers existants), jusqu'à 60 % de tous les ponts roulants des ateliers métallurgiques sont installés. Beaucoup plus souvent, la première version de cette méthode est utilisée, lorsque la poutre repose directement sur les fermes de toit de l'atelier le long de l'axe longitudinal de la travée.
92. Schéma de la poulie de poutre d'assemblage
1 - support de bloc mobile ; 2 - branche poly, spasta; 3 - support de bloc fixe ; 4 - poutre de montage ; 5 - bloc de dérivation ; 6 - colonne
93. Schéma de levage d'un demi-pont à l'aide d'une poulie suspendue à une poutre de montage
1 - treillis du toit; 2 - support de bloc fixe ; 3 - cordes; 4 - support de bloc mobile ; 5 - élingue ; 6 - doublure; 7 - demi-pont
Actuellement disponible grand nombre poutres de diverses conceptions, dont plus grande distribution poutres reçues de poutres en I (à partir d'une ou deux poutres en T), de sections en forme de caisson (à partir d'une tôle), ainsi que des poutres d'une structure en treillis : les deux parois latérales d'une telle poutre sont des fermes en treillis.
En figue. 91 montre une vue générale et un schéma d'installation d'une poutre de montage constituée de deux poutres en I reliées par des superpositions de bandes et renforcées par des nervures. La poulie est suspendue à un tuyau fixé aux ailes supérieures des poutres en I et à l'intérieur duquel est insérée une pièce de bois ronde. La poutre est installée sur les faîtes des fermes à l'aide de tables de support.
La capacité de charge des poutres de montage est de 30 à 160 tonnes, la longueur (la plus souvent utilisée) est de 6 et 12 m.
Les poutres unifiées pour la réparation et l'installation de ponts roulants dans les ateliers des entreprises de métallurgie ferreuse ont une conception similaire à celle donnée ci-dessus. Leur capacité de charge est de 50, 70 et 100 tonnes, le schéma de leurs poulies et le sens du fil de défilement sont illustrés à la Fig. 92.
Un palan à chaîne suspendu à une poutre d'assemblage est utilisé pour décharger les unités d'assemblage des véhicules sur lesquels elles sont livrées sur la zone d'installation.
En fonction de la capacité de charge de la poutre de montage et de la masse des unités d'assemblage de la grue, les poutres principales, les demi-ponts, les ponts entièrement assemblés (avec leur rotation ultérieure dans un plan horizontal au-dessus des voies de la grue), ainsi que les frais généraux les chariots-grues sont soulevés à l'aide de palans à poulie (Fig. 93).
Étant donné que les poutres de montage sont installées le long de l'axe de la travée, les poutres d'extrémité ou les équilibreurs sont soulevés sur les rails de la grue à l'aide de deux poulies suspendues aux sommets des colonnes opposées du bâtiment de l'atelier.
94. Schéma d'installation d'un pont-pont à l'aide d'une poutre de montage
1 - poutre de montage ; 2 - position de conception du demi-pont ; 3, 7 - montage des mécanismes de traction ; 4, 13 - palans à chaîne ; 5 - position de conception des poutres d'extrémité ; b- position initiale poutre d'extrémité : 8 - position initiale du demi-pont ; 9 - position initiale du chariot ; 10 - dispositif de fixation temporaire ; 11 - bloc de prise ; 12 - revêtement de sol dormant ; 14 - haubanage en corde de chanvre ; 15 - position intermédiaire demi-pont
Tout d'abord, à l'aide de palans à poulie, les dispositifs 10 sont soulevés et fixés aux colonnes pour fixer temporairement les poutres d'extrémité sur les chemins de roulement de la grue (voir ci-dessus). Ensuite, les poutres d'extrémité sont levées et installées, en utilisant l'une des poulies comme charge et l'autre comme hauban. Ensuite, les demi-ponts sont soulevés à l'aide d'un palan à poulie, en les faisant tourner dans un plan horizontal et en les reliant aux poutres d'extrémité (l'un des demi-ponts n'est pas représenté sur la figure).
Après avoir assemblé le pont, il est déplacé sur le côté par deux mécanismes de traction de montage, après quoi le chariot est soulevé avec un système de poulies au-dessus du niveau des rails du chariot et, à l'aide des mécanismes de traction, le pont est roulé sous le chariot et abaissé sur les rails. Ensuite, la cabine et les autres éléments de la grue sont installés. Le schéma du palan à chaîne est illustré à la Fig. 92, le bloc de poulie fixe est attaché au sommet de la colonne, le fil courant est dirigé vers le bas le long de la colonne et à travers le bloc de sortie et sur le treuil.
Installation entièrement assemblée de ponts roulants selon la méthode du convoyeur. Cette méthode, dans laquelle les ponts roulants sont entièrement assemblés en position basse, puis levés et installés sur des rails de grue à l'aide d'équipements de ligne de convoyage pour l'assemblage et l'installation de blocs de toiture de construction, est la plus progressive et donne le plus grand effet avec un grand volume. des travaux d'installation de grues sur site. Le procédé de convoyeur permet d'organiser l'assemblage en ligne de grues avec un degré élevé de préparation à l'installation, y compris l'exécution du maximum de travaux d'installation électrique et de mise en service en position basse, et donc de réduire au minimum le volume et la durée des travaux. travaux effectués en hauteur après installation de la grue sur les chemins de roulement.
Une condition préalable à l'utilisation de cette méthode est l'installation de ponts roulants lors de la construction du bâtiment de l'atelier, car pour déplacer, soulever et installer des ponts roulants entièrement assemblés sur des rails de grue, il faut un équipement utilisé pour effectuer des opérations similaires avec revêtement. blocs, c'est-à-dire ascenseurs, potences sur rail, portails, etc.
En figue. 95 montre un schéma de l'organisation de l'installation des ponts roulants selon la méthode du convoyeur utilisant un pont roulant à flèche 1 (destiné à l'installation des blocs de toiture d'un bâtiment d'atelier) pour déplacer le pont roulant 2 entièrement assemblé du site de montage agrandi vers la travée dans laquelle elle doit être installée, ainsi que pour soulever la grue et l'installer sur les rails de la grue à iode.
Les unités d'assemblage des grues fournies pour l'installation sont déchargées des véhicules et disposées sur le site de stockage à l'aide d'une ou deux couches de tuyaux, qui déplacent ensuite les éléments de la grue vers le site pour l'assemblage dans la portée de la grue sur chenilles. Cette grue permet d'installer les poutres d'extrémité et principales sur le support de montage et le chariot-grue sur le pont après son assemblage. La séquence des opérations d'assemblage et d'alignement du pont est décrite ci-dessus. Le pont roulant assemblé est roulé à l'autre extrémité du support jusqu'à la portée du pont roulant à l'aide d'un treuil électrique. Ici, ils jouent travaux d'installation électrique, après quoi le pont roulant est transporté par un pont roulant jusqu'au stand et pour l'installation de la cabine. À l'aide d'un camion-grue à l'aide d'une traverse, la cabine du grutier et la cabine d'entretien des chariots sont montées, et des berceaux de montage et des échelles sont suspendus.
Sur le même stand, les mécanismes de déplacement de la grue et du chariot sont testés, et les poulies des mécanismes de levage sont également stockées.
95. Schéma d'organisation de l'installation de ponts roulants selon la méthode du convoyeur utilisant une grue sur rail à flèche 1 - grue sur rail SKU-1500R ; 2 - pont de bord entièrement assemblé ; 3 - camion-grue ; 4 - grue sur chenilles ; 5 - plate-forme pour l'assemblage de la grue ; 6 - plateforme d'installation électrique ; 7 - poseur de canalisations ; 8 - plate-forme de stockage des éléments de grue ; 9 - montage du mécanisme de traction ; 10 - corde de sécurité ; 11, 12 - tribunes
96. Schéma d'organisation du convoyeur méthode d'installation des ponts roulants
en utilisant le portail t - site pour un montage agrandi ; 2 - grues sur chenilles ; 3 - pont roulant entièrement assemblé ; 4 - portail ; 5 - zone d'essais pour l'assemblage des blocs de revêtement en atelier
Ensuite, à l'aide d'un pont roulant, le pont roulant finalement assemblé est déplacé jusqu'à la travée du bâtiment de l'atelier et installé sur les rails de la grue, le démontage est effectué, après quoi deux mécanismes de montage par traction 9 déplacent le pont roulant à l'intérieur de l'atelier.
D'autres variantes de la méthode décrite d'installation des ponts roulants sont également utilisées, qui dépendent principalement de l'équipement de levage et de déplacement des blocs de revêtement et qui est utilisé lors de l'installation des ponts roulants. En figue. La figure 96 montre un schéma d'organisation du procédé de convoyage d'installation de ponts roulants utilisant un portail sur lequel des blocs de revêtement de bâtiment sont déplacés du chantier 5 pour l'assemblage de ces blocs vers une travée d'atelier donnée.
Dans ce cas, de l'autre côté des voies du portail de la décharge, un chantier de montage de consolidation est aménagé, sur lequel, à l'aide de deux grues sur chenilles et de mécanismes de traction d'installation, tout est réalisé travaux d'assemblage y compris l'installation du chariot entièrement assemblé sur le pont roulant. Ici, les travaux d'installation électrique sont effectués et les mécanismes sont testés, les poulies sont stockées, après quoi la grue entièrement assemblée est levée par des grues sur chenilles et installée sur le portail, qui est déplacé vers une baie d'atelier donnée. Après avoir relié les rails du portail aux rails de la grue de l'atelier, la grue est déplacée dans la travée à l'aide de mécanismes de traction de montage.
Installation de systèmes de lubrification pour mécanismes de grue. Les systèmes de lubrification sont installés conformément aux dessins, schémas de marquage et instructions des fabricants.
L'installation de systèmes de lubrification individuels consiste à vérifier la propreté de la surface intérieure des boîtiers de roulements, l'état de fonctionnement des lubrificateurs, à les installer en place et à les remplir de lubrifiant.
Les systèmes de lubrification centralisés sont installés dans l'ordre suivant : – une pompe manuelle de lubrification (station de lubrification) et des doseurs sont installés et fixés aux surfaces d'appui ; – installer et raccorder les unités principales de la canalisation, leurs dérivations vers les départs et les dérivations des départs vers les points lubrifiés ; – remplir les canalisations de lubrifiant ; - configurer et tester le système.
Avant d'installer le système, vous devez vous assurer que la pompe et les doseurs fonctionnent correctement, ainsi que que la surface interne de tous les éléments du pipeline est propre (pas de saleté, ni de rouille). Dans la plupart des cas, les fabricants fournissent tous les éléments des systèmes de lubrification entièrement prêts à être installés.
Cependant, si, lors de l'acceptation pour l'installation, de la saleté ou de la rouille est trouvée sur la surface intérieure des assemblages de canalisations et des coudes, ils doivent alors être lavés et décapés dans des bains. Le décapage est également obligatoire après le soudage pour éliminer le tartre formé sur la surface interne de la canalisation dans la zone de soudage.
La gravure est réalisée dans des solutions d'acides sulfurique, chlorhydrique ou phosphorique. La gravure dans des solutions d'acide sulfurique ou chlorhydrique comprend les opérations suivantes : gravure proprement dite, lavage, neutralisation de la solution de gravure restante, lavage, séchage et lubrification des surfaces gravées. Pour la gravure, utilisez des solutions d'acide sulfurique à 20 % à une température de 50-80°C ou d'acide chlorhydriqueà une température ne dépassant pas 40 °C, car à des températures plus élevées, la libération de vapeurs de chlorure d'hydrogène provenant des bains contenant de l'acide chlorhydrique augmente. Le temps de gravure dépend de l'état de la surface intérieure des unités de canalisation et des coudes, de la température des solutions et peut aller de 2 à 24 heures. Parfois, la gravure est réalisée dans un mélange de solutions acides de composition suivante : acide sulfurique. - 60 g pour 1 litre de solution, acide chlorhydrique - 40 g/ l, urotropine - 6 g/l, sel de table- 25 g/l à une température de 40-50 °C.
La qualité du nettoyage est contrôlée visuellement. Si la surface n'est pas suffisamment nettoyée, des taches et des zones individuelles d'oxydes non dissous y sont visibles ; une surface bien nettoyée a une couleur gris acier, tandis qu'une surface trop gravée a une couleur noire.
Après gravure, les nœuds et les coudes sont retirés de la solution et maintenus au-dessus du bain pour égoutter la solution, puis transférés dans un bain d'eau dans lequel ils sont lavés, puis transférés dans un bain contenant 3 à 5 % de soude ou de chaux. solution pour neutraliser la solution de gravure restante pendant 1 heure.
Après neutralisation, les produits sont lavés dans un bain avec eau chaude, chauffé à 80-90°C, et séché à l'air.
La surface séchée et gravée doit être lubrifiée avec de l'huile, car elle se corrode très rapidement. À cette fin, les unités de pipeline et les coudes sont immergés dans un bain d'huile et, après en avoir été retirés, ils sont placés sur des racks en position inclinée pour drainer l'huile pendant 2-3 heures.
Toutes les opérations ci-dessus sont effectuées sans interruption ; une fois terminées, les extrémités des nœuds et des coudes sont fermées avec des bouchons.
La gravure dans des solutions d'acide orthophosphorique diffère de celle décrite ci-dessus en l'absence d'opérations telles que le lavage, la neutralisation et la lubrification des surfaces gravées avec de l'huile.
Les composants et les coudes du pipeline préalablement nettoyés des contaminants sont d'abord gravés dans une solution à 15-20 % d'acide orthophosphorique à une température de 50-60 °C pendant 6 à 12 heures (en fonction de l'état de la surface interne des produits). ), vérifier la qualité du nettoyage au fur et à mesure de la gravure dans des solutions d'acide sulfurique ou chlorhydrique, puis transférer dans un bain avec une solution à 2 % du même acide, après avoir égoutté la solution de gravure restante dans un bain avec un Solution à 15-20%. Dans une solution à 2 % d'acide orthophosphorique, un mince film de phosphate se forme à la surface des produits en acier après gravure, qui passive (recouvre) la surface métallique et la protège de la corrosion pendant plusieurs mois. Dans un bain avec une telle solution, les unités de canalisation et les coudes sont maintenus pendant 1 à 2 heures à une température de 50 ° C, après quoi ils sont retirés de la solution, le résidu est laissé s'écouler dans le bain, placé sur un grille et séché air comprimé, préalablement nettoyé de l'humidité et de l'huile et, si possible, chauffé (pour accélérer le séchage). Ensuite, les extrémités des produits sont fermées avec des bouchons pour empêcher la contamination de pénétrer à l'intérieur, ainsi que l'eau, qui détruit film protecteur. La surface gravée et recouverte d'un film passivant a une couleur gris foncé avec une teinte verdâtre à peine perceptible.
Doseurs de lubrifiant avec période de garantie n'a pas expiré et aucun défaut n'a été constaté lors de l'inspection externe, ils sont installés en place et fixés à la structure de la grue avec des vis qui attirent fermement l'alimentateur vers le support.
Si la période de garantie est écoulée mais qu'aucun défaut n'est constaté, les mangeoires sont testées pour détecter les fuites. huile minéraleà la pression d'épreuve spécifiée dans le passeport pendant 2 minutes dans chacune des positions extrêmes des pistons.
Dans ce cas, l'huile ne doit pas fuir à travers les joints de tige et les trous de connexion bouchés dans les boîtiers, et sa fuite par l'une des sorties vers les points lubrifiés ne doit pas dépasser trois gouttes par minute. Les doseurs doivent fonctionner et distribuer la quantité de lubrifiant requise lorsque la différence de pression dans les conduites principales n'est pas supérieure à 1 MPa et que le nombre de courses de piston n'est pas inférieur à 6. Le mouvement des pistons et des tiroirs doit être fluide, sans coincement le long du toute la longueur de course. Les tests et contrôles de fonctionnement sont effectués par pompage lubrifiant alternativement dans chaque ligne. Les mangeoires qui échouent aux tests sont envoyées en réparation et de nouvelles sont installées à la place.
Les canalisations des systèmes sont assemblées à partir d'unités et de coudes fabriqués chez le fabricant. Lorsque le fabricant fournit la tuyauterie sous forme de sections de tuyau droites et de pièces de tuyauterie séparément, les installateurs construisent les principaux assemblages de tuyauterie et se courbent eux-mêmes à partir de tuyaux pré-gravés.
Les raccordements de pipelines sont réalisés principalement sur un plan conique filetage de tuyauà l'aide d'écrous-raccords et de raccords (angles, tés, raccords). L'utilisation d'agents d'étanchéité dans ces joints sous forme de badigeon, de plomb rouge et d'étoupe n'est pas autorisée ; Ils sont assemblés sur vernis nitro de la marque NTs ou vernis bakélite de la marque LBS. Souvent, le cintrage des tuyaux est utilisé à la place des angles et des inserts fabriqués par soudage sont utilisés à la place des tés ; Ainsi, les coudes des lignes vers les départs et des départs vers les points lubrifiés sont dans de nombreux cas réalisés courbés, et les dérivations sont reliées aux lignes par l'intermédiaire de raccords filetés soudés à ces dernières.
Les canalisations sont également reliées par soudage, mais il est nécessaire que le joint soudé se situe entre deux joints filetés. Cela permet, après avoir assemblé le pipeline, de démonter la section avec le joint soudé et de la décaper. Si joint soudé réalisé dans une douille ou avec un raccord soudé à l'extérieur du joint, alors après soudage, il n'est pas nécessaire de faire de gravure.
Après avoir installé le système, les canalisations sont soufflées avec de l'air comprimé pour éliminer les particules solides qui sont entrées à l'intérieur lors de l'assemblage des joints, puis elles sont remplies de lubrifiant à l'aide d'une pompe, fournissant le lubrifiant d'abord par une canalisation principale puis par l'autre. L'une des principales exigences lors de la réalisation de cette opération est d'évacuer l'air des canalisations. L'air entrant dans le système perturbe travail normal. Pour ce faire, lors du remplissage, l'extrémité opposée du pipeline est ouverte et n'est fermée qu'après la sortie de 0,5 kg de lubrifiant.
Au fur et à mesure du remplissage de la canalisation, les sorties vers les départs et les départs se chargent en lubrifiant, pour cela les bouchons installés sur ces sorties sont retirés un à un avant purge. Les robinets ne sont connectés aux alimentations qu'après que 50 à 100 g de lubrifiant sortent de chaque robinet. Le chargeur est considéré comme chargé lorsque 10 à 20 g de lubrifiant en sortent. Après cela, la mangeoire est fermée avec des bouchons. Les robinets des départs vers les points lubrifiés sont facturés comme suit. Débranchez les robinets des alimentations et des points lubrifiés, soufflez-les avec de l'air comprimé et remplissez-les de lubrifiant à l'aide de pompe manuelle jusqu'à ce que 50 à 100 g de lubrifiant contaminé sortent de l'extrémité libre de chaque sortie, qui est retirée. Après cela, la prise est installée en place.
Après avoir rempli le système, ils commencent sa mise en place, qui consiste à vérifier le fonctionnement des doseurs et à déterminer la pression nécessaire à leur fonctionnement. Le fonctionnement des doseurs est vérifié en injectant alternativement du lubrifiant dans les deux conduites.
Lors du pompage dans la première ligne, toutes les tiges doivent être en position haute, lors du pompage dans la deuxième ligne, en position basse. S'il y a une différence dans la position des tiges, les dérivations des canalisations principales vers une partie des alimentateurs sont interverties de sorte que les tiges de tous les alimentateurs soient en position relevée ou abaissée lors du pompage du lubrifiant dans l'une des deux conduites.
La pression à laquelle le système doit fonctionner est déterminée par un manomètre au moment de l'activation de l'alimentation la plus éloignée plus 0,5 MPa. Après avoir vérifié le fonctionnement des départs et déterminé la pression de fonctionnement, les canalisations sont soumises à essai hydraulique test de pression. Une pompe est utilisée pour cela haute pression, qui est utilisé pour injecter du lubrifiant alternativement dans les premier et deuxième pipelines principaux. La pression d'essai dans chaque pipeline est 1,2 fois la pression de service, elle est maintenue pendant 20 à 30 minutes. Pendant ce temps, la chute de pression ne doit pas dépasser 10 %.
Installation de cordes de levage. Une opération critique lors de l'installation des grues est le mouflage des câbles sur les mécanismes de levage, dans laquelle les exigences suivantes doivent être respectées : assurer la sécurité du câble lors de son installation ; éviter les inutiles contraintes internes, causés par les conditions de réserve ; pose initiale correcte de la corde sur le tambour du mécanisme de levage.
Des dommages et la formation de contraintes supplémentaires dans le câble peuvent survenir s'il n'est pas déroulé correctement des bobines ou des tambours. Lors de la réservation, il est nécessaire de respecter l'ordre de câblage du câble dont une extrémité doit faire successivement le tour de tous les rouleaux des cages à blocs puis être fixée au tambour. La deuxième extrémité est également fixée au tambour ou au porte-bloc supérieur. La corde peut être posée manuellement ou en utilisant la méthode de substitution.
En figue. 97 montre le mouflage du mécanisme à poulies du mécanisme de levage principal d'un pont roulant en utilisant la méthode de remplacement. Un tambour ou enrouleur avec câble 1 est installé sous le pont roulant sur des supports dans lesquels ils peuvent tourner librement. La cage mobile du moufle 5 à suspension à crochet est fixée en position basse le long de l'axe de la grue. Également installé sous le robinet treuil électrique 6, sur le tambour duquel est enroulée une fine corde.
Cette corde est passée manuellement à travers tous les rouleaux de poulie et reliée à l'extrémité de la corde de conception enroulée sur le tambour 1. Ensuite, en allumant le treuil électrique, une fine corde est passée à travers tous les rouleaux dans le sens opposé, mais avec la conception corde, qui remplace ainsi la corde fine dans la corde de poulie.
97. Schéma de mouflage d'un palan à chaîne par la méthode de remplacement
a - schéma d'organisation du travail ; b - diagramme de mouflage ; 1 - tambour avec corde ; 2 - support de bloc fixe ; 3 - tambour du mécanisme de levage ; 4 - chariot pont roulant ; 5 - support de bloc mobile ; 6 - treuil électrique
Lors de la réservation grande importance Il a définition précise longueur de la corde, sinon le crochet ne montera pas à la hauteur requise ou n'atteindra pas sa position inférieure.
Si le crochet selon le projet tombe en dessous du niveau du sol de l'atelier (en présence de pièces en retrait), la longueur de la corde doit être augmentée de la distance du sol jusqu'à la position inférieure de l'axe de la cage mobile, multipliée par la multiplicité de la poulie de la grue.
Lors du stockage de nouvelles cordes, la poulie se tord souvent. La torsion peut être éliminée de deux manières : en déroulant d'abord la corde sur toute sa longueur en une ligne droite lors de l'enroulement, ou en déroulant la poulie.
Dans la deuxième méthode, soulevez la charge dont la masse représente 30 % de la masse de la plus grande charge de 150 à 200 mm et laissez la poulie tourner librement, empêchant uniquement la charge d'accélérer. Dans ce cas, le nombre de tours de la cage du bloc inférieur est compté jusqu'à ce que la poulie cesse de tourner.
Après avoir fixé la corde au tambour, le crochet est relevé et abaissé plusieurs fois, répartissant ainsi uniformément la torsion sur toute la longueur de la corde.
Les caractéristiques de l'installation des grues métallurgiques sont déterminées par caractéristiques de conception ponts, chariots et mécanismes pour effectuer des opérations technologiques spéciales. La séquence et les règles d'exécution de toutes les opérations d'assemblage lors de l'installation des grues métallurgiques sont détaillées dans les instructions des fabricants, c'est pourquoi la procédure d'installation des unités d'assemblage agrandies de ces grues est discutée ici.
Lors de l'installation des grues de chargement à meneaux après l'assemblage du pont sur les rails de la grue (ou le levage du pont assemblé), le châssis du chariot principal avec le châssis et les mécanismes de déplacement, de rotation et de levage de la colonne est soulevé sur le pont. Parallèlement, la partie inférieure du chariot principal est assemblée, à partir de la cabine de commande. La cabine est installée sur la plateforme de travail sur des supports. Avant l'installation et la fixation sur la plate-forme de commande, la colonne est nettoyée du revêtement de conservation et vérifiée pour sa rectitude et l'absence d'entailles ; la courbure des faces des colonnes ne doit pas dépasser 1 mm sur une longueur de 1 m. Après avoir fixé la colonne au chantier, un cadre avec des mécanismes y est inséré et installé le long de l'axe d'oscillation. Ensuite, le coffre avec l'embout buccal est assemblé.
Après avoir assemblé la partie inférieure du chariot principal, l'arbre est posé sur la colonne à l'aide d'une grue automotrice ou de poulies liées au châssis du chariot principal. L'arbre avec la colonne est fixé en position verticale (pour plus de stabilité) avec des entretoises ou des crémaillères. Ensuite, une traverse avec une suspension du mécanisme de levage de la colonne est placée sur la tête de la colonne et sécurisée.
Après cela, l'ensemble arbre avec colonne et cabine est soulevé et fixé au châssis du chariot principal.
L'arbre est soulevé à l'aide de palans à poulie suspendus au châssis du chariot ou à la poutre de montage, ou à l'aide d'un mécanisme de levage à colonne.
L'installation des grues de fonderie diffère de l'installation des grues à usage général en ce sens que le pont principal est d'abord assemblé sur les rails de la grue, puis le pont auxiliaire, après quoi les chariots sont assemblés. Les ponts de grues de coulée lourde sont assemblés sur des rails de grue à partir de demi-ponts ou éléments individuels, lorsque la masse des éléments (bogies d'équilibre, poutres de pont) et la capacité de charge des mécanismes de montage existants ne permettent pas de les agrandir en demi-ponts. Ces grues sont le plus souvent montées à l'aide de palans à poulie suspendus à des poutres de montage. Pour la même raison, les chariots principaux des grues de coulée lourde sont montés sur le pont roulant à partir d'unités d'assemblage agrandies, et les chariots auxiliaires sont entièrement assemblés, sous la forme sous laquelle ils arrivent du fabricant. Pour l'élingage des chariots principaux des grues de coulée, on utilise souvent un dispositif de l'Institut Giprometallurgmontazh, constitué d'une traverse qui, par l'intermédiaire de quatre tiges coulissantes, est reliée de manière articulée à deux patins placés sous la poutre centrale du châssis du chariot.
Lors de l'installation de grues pour le dénudage des lingots, après avoir assemblé le pont et installé le chariot dessus, un puits, préalablement assemblé avec une cabine, des plates-formes et des échelles en un seul élément d'assemblage agrandi, y est suspendu et fixé.
La spécificité de ces grues est la fixation d'un mécanisme d'éjection des lingots avec des pinces, qui, en règle générale, provient du fabricant assemblé. Posé en position horizontale à proximité d'une fosse de réparation spéciale de 4,6 m de profondeur, ce mécanisme est descendu dans la fosse à l'aide d'une poulie suspendue à une poutre sur le châssis du chariot, ou mécanisme de levage principal.
Si le mécanisme d'éjection arrive démonté, il est assemblé en position horizontale à côté de la fosse de réparation et descendu dans celle-ci. Après cela, le pont roulant et le chariot sont installés au-dessus de la fosse de réparation afin que le mécanisme d'éjection puisse être soulevé et inséré dans le puits directement depuis la fosse sans le déplacer dans le sens horizontal.
Si à ce moment-là l'installation du mécanisme de levage principal du chariot-grue n'est pas encore terminée, le mécanisme d'éjection est alors soulevé avec la même poulie avec laquelle il a été descendu dans la fosse de réparation. Après avoir soulevé le mécanisme le long des guides de l'arbre, fixez-le temporairement et la poursuite des travaux effectué après l'achèvement de l'installation du mécanisme de levage principal et des travaux d'installation électrique.
Lorsque le mécanisme de levage principal fonctionne, le mécanisme d'éjection est monté comme suit.
Des cordes de levage sont fixées au tambour, elles se plient autour des blocs du mécanisme d'éjection et sont d'abord fixées à son équilibreur. Les cordes du mécanisme de commande des pinces sont passées à travers des blocs et solidaires des leviers de ce mécanisme et du tambour. Ensuite, le mécanisme d'éjection est soulevé de la fosse jusqu'à la position de conception inférieure (à l'ouverture maximale de la pince) et temporairement fixé dans l'arbre sur deux poutres placées sous les parties saillantes de la cartouche. Après cela, les cordes libérées sont tirées et rattachées au fléau et aux leviers (sans couper leurs extrémités). Après avoir élevé le mécanisme d'éjection jusqu'à la position de conception supérieure (avec une ouverture minimale de la pince), les cordes sont fixées au contrepoids pour équilibrer le mécanisme de commande de la pince.
La technologie d'installation de robinets de puits (à pince) est similaire à la technologie d'installation de robinets pour le dénudage des lingots.
Le démontage des ponts roulants s'effectue dans la plupart des cas à l'aide de potences automotrices ou de poulies suspendues à des poutres de montage. Les mâts d'installation sont beaucoup moins utilisés à cette fin (pour les mêmes raisons qu'ils sont rarement utilisés pour l'installation de grues).
Il est prometteur d'utiliser des ascenseurs hydrauliques conçus par Giprotechmontazh pour le démontage des ponts roulants.
Les grues ne peuvent être démontées que s'il existe un PPR spécialement développé.
Avant le début des travaux de démontage, des mesures préparatoires sont effectuées, notamment : – la préparation des mécanismes et équipements de levage requis, y compris l'installation de treuils, la liaison des poulies et des poulies, l'installation de dispositifs de fixation temporaire des poutres d'extrémité ou des équilibreurs sur la grue. pistes, etc. ; – préparation et installation des échafaudages nécessaires au démontage de la grue ; – clôturer la zone de travail dangereuse et préparer un site pour le placement des unités d'assemblage de grue retirées.
En installant des patins sous les roues de la grue et du chariot pour éviter leur mouvement spontané,
et après avoir mis les mécanismes de la grue hors tension, ils commencent à la démonter.
Tout d'abord, le chariot est suspendu et retiré du pont roulant. Si la capacité de charge des mécanismes et équipements existants est inférieure à la masse du chariot assemblé, celui-ci est alors démonté en le nombre minimum d'éléments requis et retiré un par un.
Pour les mêmes raisons, le pont roulant est entièrement retiré ou démonté en deux demi-ponts ou en un autre nombre d'éléments conformément au PPR.
Les opérations de démontage du pont s'effectuent dans l'ordre inverse de son montage.
Les patins de montage sont retirés par coupage au gaz, après avoir fixé au préalable la poutre principale (ou demi-pont), qui doit être retirée en premier, et fixé temporairement les poutres d'extrémité ou les équilibreurs aux rails de la grue.
L'abaissement des demi-ponts, des poutres individuelles ou d'un pont assemblé s'effectue selon des schémas inverses de ceux adoptés lors de l'installation de la grue.
À catégorie : - Installation de grues de chargement
Nécessité d'installer des plates-formes spéciales pour l'inspection et la maintenance des mécanismes situés à l'extérieur de la grue, le Règlement des grues (article 229) prévoit uniquement les grues suspendues monopoutre (support et suspension) et bipoutre, si elles sont installées dans un bâtiment et n'ont pas de plates-formes ni de galeries situées sur le robinet lui-même. Dans d'autres cas, la faisabilité de la construction de plates-formes est déterminée par l'organisme qui conçoit l'installation des grues ou par l'entreprise qui les exploite.
Les plates-formes peuvent être fixes ou mobiles. Dans les chantiers fixes, la distance entre le sol et la dimension inférieure de la grue à desservir doit être d'au moins 1800 mm, cependant, à cette distance, l'accès aux mécanismes est très difficile. Pour créer des conditions de service normales, cette distance peut être réduite en installant dans l'escalier une porte verrouillable avec verrouillage électrique automatique, qui coupe la tension des fils principaux du chariot de la zone de réparation.
L'escalier doit avoir une porte, une fois ouverte, la section chariot dans la zone d'atterrissage est automatiquement mise hors tension. Les trolls sont allumés une fois la grue réparée à l'aide d'un interrupteur dans la zone de réparation. Pour le schéma électrique de blocage de l'entrée du chantier de réparation, voir 7.13.
Des solutions approximatives pour les sites de réparation stationnaires sont présentées sur la Fig. 4. 16-4. 22.
Exigence relative à la porte de la plate-forme de réparation des grues suspendues monopoutre et bipoutre, lorsque la distance entre le sol de la plate-forme de réparation et parties inférieures la grue est inférieure à 1800 mm et lorsque l'alimentation électrique de la grue est réalisée non pas par des fils de chariot, mais par un câble flexible. À cet égard, la nécessité d'un dispositif de verrouillage pour relâcher automatiquement la tension du câble flexible dans ce cas
Figure 4.18 Plate-forme de réparation en bout de travée pour ponts roulants électriques monopoutres à commande depuis la cabine d'une capacité de levage de 1 à 5 tf d'une portée de 4,5 à 10,5 m : 1 - plate-forme ; 2 - chaîne; 3 - accentuation ; 4 - cabine
doit être déterminé en tenant compte du nombre de grues fonctionnant dans une travée, de la méthode de fonctionnement des grues (depuis la cabine ou depuis le sol) et de la possibilité de prendre d'autres mesures pour empêcher les personnes d'entrer dans la zone de réparation pendant le fonctionnement des grues et les rencontrer. Le site de réparation est conçu pour une charge de grue uniformément répartie de 20U kgf/cm2, et la zone du site est désignée
Graphique 4.19. Chantier de réparation en bout de travée des ponts roulants électriques monopoutres à commande depuis la cabine d'une capacité de levage de 1 à 5 tf d'une portée de 13,5 à 23,5 m (1-4, voir Fig. 4. 18) :
pour la réparation des palans électriques, sur le poids concentré de l'acier électrique de la capacité de charge correspondante. Pour les ponts roulants à deux poutres, il est conseillé de prévoir dans la voiture de réparation (voir 7.5) des zones d'inspection et de changement des roues de roulement de la grue, s'il y a une distance d'au moins 600 mm de l'extrémité de la grue à le mur du bâtiment. L'accès à ces sites est assuré depuis le pont roulant ou par une trappe dans le pont qui est fermée pendant le fonctionnement des grues. L'accès à un tel chantier de réparation est soumis à autorisation.
Les ponts roulants commandés depuis la cabine (sauf monopoutre et suspendus) doivent être équipés de cabines de desserte des câbles principaux du chariot et de pantographes s'ils sont situés en dessous du tablier de la galerie du pont (article 230 du Règlement des Grues). La trappe permettant d'accéder à cette cabine depuis le pont de la passerelle doit être équipée d'un couvercle avec serrure.
Les dimensions de la cabine pour l'entretien des chariots principaux et de leurs pantographes ne sont pas réglementées et sont généralement prises à 1000X1400 avec une hauteur d'au moins 1800 mm. La superficie de la cabine ne doit pas être inférieure à 800X800 mm. La cabine doit être clôturée avec un garde-corps d'au moins 1 m de haut avec un ourlet continu le long du fond et une hauteur de 100 mm. Il est suspendu à une distance de 1 000 à 1 100 de l'axe du rail de la grue. Lorsque l'alimentation électrique s'effectue par câble, les cabines ne sont pas aménagées. Le plancher de la cabine est recouvert d'un tapis diélectrique.
Graphique 4.20. Chantier de réparation de grues monopoutres électriques suspendues à deux et trois travées d'une capacité de levage de 1 à 5 t (1-3 - voir Fig. 4. 18)