Équipement pour la production de béton cellulaire. Équipement nécessaire à la production de blocs de béton cellulaire. Équipement pour la production de
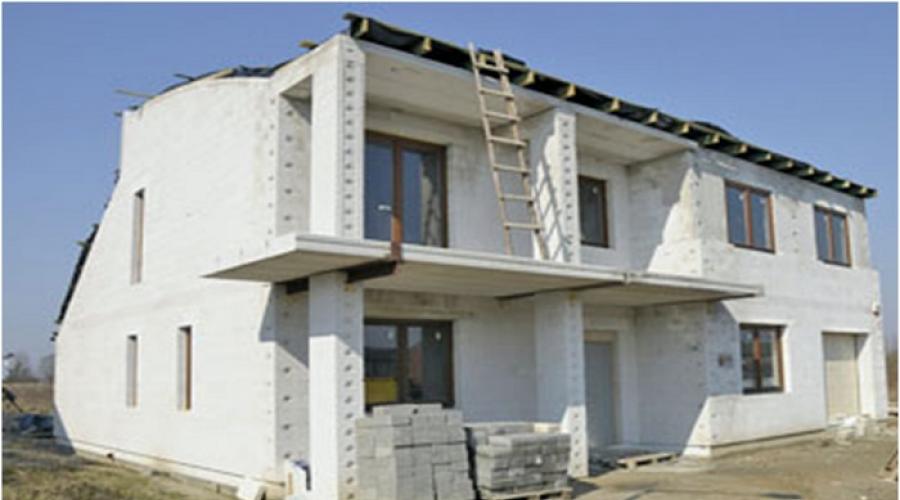
Le secteur de la construction moderne se distingue par la combinaison de méthodes de construction traditionnelles et des technologies de construction les plus récentes. L'utilisation du béton cellulaire a considérablement augmenté l'efficacité du génie civil et amélioré la qualité des travaux de construction. La production généralisée de béton cellulaire pour les besoins de la construction de logements privés souligne la popularité croissante parmi les développeurs d'options économiques pour les matériaux de mur présentant des propriétés de résistance et d'isolation thermique assez élevées.
L'un de ces matériaux de mur de construction populaires est le béton cellulaire, utilisé dans la construction de bâtiments résidentiels de faible hauteur et de dépendances. En raison de sa structure poreuse, il s’agit d’un béton cellulaire et d’une formation artificielle poreuse semblable à une pierre.
Les fabricants de béton cellulaire fabriquent des produits en béton cellulaire sous forme de blocs de diverses configurations qui répondent aux exigences des normes suivantes :
- GOST 31359-2007, établissant des exigences pour le béton cellulaire destiné à la fabrication de blocs et panneaux muraux, de dalles, de linteaux et d'autres éléments de construction ;
- GOST 31360-2007 réglementant les exigences relatives aux produits muraux en béton cellulaire.
GOST 31359-2007 définit les matériaux en béton cellulaire comme un type de béton cellulaire qui diffère des autres matériaux cellulaires par la méthode de formation des pores (clause 4.2). Dans sa structure, le produit en béton cellulaire ressemble à une sorte d'« éponge » en béton, constituée de petites cellules à bulles d'un diamètre ne dépassant pas 3 mm.
Grâce à leur structure finement poreuse, les produits en blocs, que les équipements modernes de production de blocs aérés peuvent produire, ont des propriétés physiques et mécaniques qui les distinguent avantageusement des produits similaires fabriqués à partir d'autres matériaux en béton :
- faible densité spécifique;
- faible conductivité thermique;
- résistance au feu;
- résistance aux champignons et aux moisissures;
- facilité d'usinage;
- fabricabilité et utilisation.
Avantages
Les aspects suivants sont notés comme avantages techniques et économiques des matériaux en béton cellulaire :
- Le poids des blocs de construction en béton cellulaire est plusieurs fois inférieur au poids de produits similaires en brique ou en béton. Un bloc aéré de dimensions standards 300x250x600 mm ne pèse que 30 kg, soit plus de 3 fois moins que le poids du même volume de briques de dimensions 60x125x250 mm.
- La facilité de traitement des produits avec des outils mécaniques conventionnels permet d'ajuster les blocs lors de la construction des bâtiments pour améliorer la qualité de l'assemblage.
- Les qualités élevées d'isolation thermique et phonique des murs en blocs de béton cellulaire garantissent une vie confortable dans les immeubles d'habitation.
- Une résistance au feu fiable aux flammes nues garantit la sécurité incendie du bâtiment.
- La haute technologie de construction lors de l'utilisation de blocs de gaz augmente l'efficacité et la qualité du travail.
- Le coût abordable des blocs de gaz leur confère une compétitivité adéquate sur le marché des matériaux de construction.
- La possibilité d'organiser la production de produits en béton cellulaire en tant qu'entreprise privée, puisque le prix réel de la production de béton cellulaire, d'une mini-usine ou d'un équipement de ligne de type convoyeur est relativement abordable. L'efficacité technologique de la production de matériaux en béton cellulaire crée les conditions préalables pour faire des affaires avec une rentabilité élevée.
Technologie de fabrication de béton cellulaire
Les composants initiaux utilisés par les fabricants de blocs de béton cellulaire dans la production de matériaux en béton cellulaire cellulaire sont :
- Ciment Portland dans des proportions de 50 à 70 % du volume du mélange préparé ;
- Chaux - pas plus de 5 % du volume du mélange ;
- sable de quartz d'une fraction ne dépassant pas 2,1 mm, proportions dans le mélange – 20-40% ;
- eau – 0,8-1,0% ;
- d'additifs complexes générateurs de gaz allant de 0,04 à 0,09 %.
La technologie de base pour la production de béton cellulaire comprend plusieurs étapes :
- Étape 1 - dosage des composants principaux - ciment, sable, chaux - conformément aux proportions de la recette donnée pour le matériau en béton cellulaire.
- Étape 2 – fourniture des principaux composants et de l'eau à une bétonnière cellulaire spéciale. Mélanger soigneusement les composants jusqu'à l'obtention d'un mélange très homogène.
- Étape 3 – ajout d'un agent gonflant au mélange préparé (le plus souvent l'agent gonflant est une suspension aqueuse de poudre d'aluminium). Le processus de mélange poreux. C'est important! Lors de l'interaction chimique de l'aluminium métallique, qui constitue la base de la poudre, avec les mortiers de chaux et de ciment, de l'hydrogène libre est libéré sous forme de bulles de gaz qui « gonflent » la pâte de ciment. Les équipements pour béton cellulaire doivent assurer une libération de gaz uniforme dans tout le volume du mélange afin d'obtenir une structure poreuse uniforme.
- Durcissement du mélange de béton cellulaire sous des formes spéciales, découpe de blocs de la configuration requise. Les produits finis peuvent prendre une grande variété de formes - des parallélépipèdes traditionnels aux blocs en forme de U ou arqués.
Selon le type de traitement de la masse de béton cellulaire durcissant Il existe deux méthodes pour fabriquer des blocs de gaz :
- méthode sans autoclave, dans laquelle la maturation des produits semi-finis jusqu'à un ensemble de résistance régulée se produit naturellement sans exposition forcée à des facteurs externes ;
- méthode d'autoclave ou autoclavage, dans laquelle les produits sont exposés à une pression à des températures élevées dans des chambres d'autoclave.
Caractéristiques de l'autoclavage des produits en blocs de béton cellulaire
Si l'équipement dont est équipée l'usine de blocs de gaz comprend une chambre d'autoclave, les produits de durcissement en autoclave sont bien supérieurs en termes de qualité aux produits fabriqués à l'aide de méthodes non autoclaves. Le retrait des blocs autoclaves pendant le fonctionnement ne dépasse pas 0,5 mm/m, tandis que le même chiffre pour les blocs muraux non autoclaves atteint 5 mm/m. La résistance à la compression des matériaux en béton cellulaire autoclavés atteint 3,2 MPa, pour les matériaux non autoclavés - pas plus de 1,0 MPa. Les blocs de gaz durcis en autoclave ont une structure stable et homogène, qui prédéterminée leurs propriétés de performance en tant que matériau de construction universel. Les bâtiments muraux d'une épaisseur de 375 à 400 mm, construits à partir de produits en béton cellulaire, ont fait leurs preuves dans les conditions météorologiques russes sans isolation supplémentaire.
Le principe de l'autoclavage des matériaux de construction cellulaires est de placer les produits déjà moulés dans un autoclave, dans lequel les blocs seront exposés pendant une longue période à haute pression (jusqu'à 1,2 MPa) et traités à la vapeur d'eau à une température de 190-191 degrés. . C. De telles conditions déclenchent des réactions qui renforcent la densité structurelle du matériau et augmentent sa résistance.
Équipement technique pour la production de béton cellulaire
Pour lancer les activités de production pour la production de produits en béton cellulaire, une ligne technologique pour la production de béton cellulaire est équipée, qui comprend les éléments fonctionnels suivants :
- distributeurs de composants de mélange de béton cellulaire;
- malaxeur à béton cellulaire (mélangeur-activateur) pour préparer un mélange de mousse de béton cellulaire ;
- coffrages pour couler un mélange de béton cellulaire cellulaire et durcissement ultérieur ;
- dispositifs pour couper des blocs de gaz;
- chariots pour déplacer les produits finis vers le stockage.
Pour les travaux utilisant la technologie autoclave, la ligne est équipée d'une chambre autoclave et d'un système de contrôle et de régulation automatique des modes de fonctionnement de l'autoclave.
Avant d'organiser une mini-usine pour la production de blocs de béton cellulaire ou d'autres produits en béton cellulaire, il est nécessaire de déterminer la productivité de la ligne de production. L'équipement technique du site ou de l'usine de production et le degré d'automatisation des opérations technologiques réglementées en dépendent. Pour fabriquer des produits de construction à l'échelle industrielle, vous aurez besoin d'un équipement complètement différent de celui d'une petite production ou de la production de blocs de gaz dans des conditions artisanales. Les lignes de production et technologiques pour la production de produits en béton cellulaire sont divisées en trois catégories.
Mini-lignes
1.Mini-lignes, qui sont des mini-usines d'une capacité de production de 15 à 25 mètres cubes. m/jour de produits en béton cellulaire. Ils ont un faible degré d'automatisation des processus techniques. 2 à 3 ouvriers sont engagés dans l'entretien des actionneurs. La zone de production des mini-usines ne dépasse pas 140-160 mètres carrés. mètres. L'équipement principal comprend :
- bétonnière à gaz;
- dispositifs pour couper les mélanges durcissants;
- moules, plateaux pour le vieillissement des blocs aérés ;
- voies ferrées et chariots pour le transport des produits finis.
Les mini-usines utilisent des mélangeurs de type mobile qui, après avoir mélangé le mélange de béton cellulaire, sont roulés vers des formes fixes fixes pour les remplir du mélange préparé.
Le prix des équipements pour la production de blocs de béton cellulaire sur de telles lignes peut augmenter considérablement lorsqu'ils sont équipés d'options supplémentaires, par exemple un compresseur pour fournir de l'air pour un meilleur mélange du mélange de béton ou des distributeurs automatisés.
Lignes stationnaires
2. Lignes stationnaires capacité de production de 30 à 60 mètres cubes. mètres/jour. Une centrale à béton cellulaire de ce type est équipée d'un malaxeur à béton cellulaire fixe, auquel arrivent des chariots de coffrage mobiles pour être remplis de masse de béton cellulaire cellulaire. Le niveau d'automatisation de la production est assez élevé, ce qui permet d'impliquer un ou deux ouvriers dans le travail. La zone de production des lignes fixes ne dépasse pas 500 mètres carrés. mètres.
Lignes de type convoyeur
3. Lignes de type convoyeur capacité de production de 75 à 150 mètres cubes. mètres/jour. Malgré le degré élevé d'automatisation du contrôle des processus, au moins 8 personnels de service sont nécessaires pour entretenir le complexe. La superficie occupée par l'usine de convoyage pour la production de blocs de béton cellulaire dépasse 600 mètres carrés. mètres.
Problèmes d'organisation lors de l'ouverture de la production de béton cellulaire
L'ouverture d'une usine de production de béton cellulaire nécessitera la préparation d'un certain nombre de documents liés aux spécificités de la fabrication et de la vente de blocs de béton cellulaire. Si l'équipement est utilisé pour la production de béton cellulaire dans des conditions artisanales sans utiliser d'autoclave, aucun permis n'est requis pour de tels travaux. Dans les résolutions du gouvernement de la Fédération de Russie du 13 août 1997 n° 1013 et la norme d'État de la Fédération de Russie du 8 octobre 2001, qui définissent les listes de produits soumis à une certification obligatoire, il n'y a pas de blocs en cellulaire béton et équipements pour leur production. Cependant, dans le cas de l'utilisation de la technologie des autoclaves, le fabricant doit obtenir l'autorisation des autorités du Gosgortekhnadzor ; l'équipement fonctionne à pression élevée ; Séparément, il est nécessaire d'obtenir des autorisations auprès des pompiers, car la puissance électrique de l'autoclave est de 5 à 10 kW. La ville SES peut donner son avis, puisque l'utilisation de poudre d'aluminium devrait prévoir la possibilité de recycler la suspension génératrice de gaz qui en découle.
Il n'y a pas si longtemps, seules les grandes entreprises spécialisées dotées d'équipements coûteux pouvaient produire du béton cellulaire et autres bétons cellulaires.
L'introduction de nouveaux procédés technologiques a considérablement simplifié la production de ces matériaux très demandés, ce qui a donné une impulsion au développement de la production de produits en béton cellulaire par les petites et moyennes entreprises.
Auparavant, il était possible de produire un matériau de construction aussi populaire dans de grandes entreprises disposant d'équipements spéciaux pour la production de blocs de béton cellulaire. Aujourd'hui, un processus technologique amélioré a permis d'établir la production de béton cellulaire dans une entreprise ou à domicile en fonction de la quantité requise, des caractéristiques technologiques et de la disponibilité des fonds. En fonction de l'organisation du processus, ils achètent des équipements fixes, des mini-usines ou de petites installations mobiles, à l'aide desquels des blocs de béton cellulaire sont produits à différents niveaux de densité.
Technologie
Le processus de production de blocs de béton cellulaire ne pose aucune difficulté.
Un groupe de produits en béton se caractérise par une structure cellulaire. Les bulles de gaz occupent jusqu'à quatre-vingt-cinq pour cent du volume, ce qui permet aux blocs finis d'être légers.
La matière première de départ est mélangée dans une bétonnière pendant cinq minutes, après quoi une suspension aqueuse de poudre d'aluminium est ajoutée à la masse, qui réagit avec la chaux. Le processus produit de l'hydrogène, qui forme de nombreux pores qui pénètrent uniformément dans le matériau.
Dès que de la poudre d'aluminium est ajoutée, la masse est versée dans des récipients métalliques spéciaux et un gonflement s'y produit. Pour accélérer le processus de réaction, de prise et de durcissement, le produit semi-fini est soumis à une charge vibratoire. Les endroits inégaux sont retirés de la masse, qui commence à durcir, à l'aide d'un fil métallique, et la matière première restante dans le moule est coupée en morceaux de la taille requise. La production de blocs aérés se poursuit dans une unité autoclave, après quoi les produits sont calibrés sur des unités de broyage.
L'utilisation d'équipements autoclaves dans la technologie de production de béton cellulaire occupe une place particulière, car les propriétés du matériau sont améliorées. Formé et divisé en blocs séparés, le béton cellulaire est envoyé dans des unités d'autoclave et soumis à un traitement de douze heures à la vapeur d'eau.
Ce procédé de fabrication permet d'obtenir un matériau qui ne rétrécit pratiquement pas, se caractérise par une structure homogène et possède de bonnes propriétés d'isolation phonique et de rétention de chaleur.
La deuxième option pour produire du béton cellulaire est la méthode sans autoclave. Le durcissement complet se produit dans des conditions normales ; aucun équipement de haute technologie n'est requis pour la fabrication. Dans ce cas, il devient possible de fabriquer soi-même des blocs de gaz.
Le matériau ne sera pas durable.
Matières premières pour béton cellulaire
Pour obtenir un bloc cellulaire, utilisez un mélange composé des composants suivants :
- sable dont la taille des fractions n'excède pas 2,1 mm et ne contient pas beaucoup d'argile. Ce matériau représente 20 à 40 pour cent de la masse pétrie ;
- chaux (1 à 5 %) ;
- composition de ciment - de 50 à 70 % (grade M 40 ou M 500) ;
- eau pure – 0,25 – 0,8 % ;
- poudre d'aluminium pour la formation de gaz – 0,04 – 0,09 %.
Aperçu de l'équipement requis
Considérons les caractéristiques des lignes de production de béton cellulaire.
Convoyeur
Ce type d'équipement est différent :
- le processus le plus automatisé ;
- participation minimale des ouvriers à la production de blocs ;
- coût important;
- des volumes de production importants ;
- toute l'exhaustivité nécessaire ;
- haut niveau de rentabilité.
Le forfait standard comprend :
- conteneurs et bunkers de matières premières ;
- convoyeurs à bande par lesquels les composants sont fournis ;
- unité pour mélanger la solution;
- unités d'autoclave ;
- formes;
- complexe pour couper la matière première en blocs;
- convoyeur de mélange ;
- usine de concassage;
- chariots;
- télécommande pour contrôler le processus en mode automatique;
- chariot élévateur.
Le prix d'un tel équipement est élevé, atteignant 55 000 000 de roubles. Le montant est important, mais la productivité de la ligne permet de produire au moins trois cent mille mètres cubes de matière en un an.
Pour placer tout le matériel, vous devrez préparer un terrain d'environ quatre mille mètres carrés.
Si vous comparez quel fabricant de blocs aérés est le meilleur, il est alors recommandé de faire attention aux équipements d'occasion. Il existe certains risques, mais le coût de la ligne sera nettement inférieur.
Poursuivant la comparaison des blocs de gaz de différents fabricants, les experts conseillent d'acheter un convoyeur de type Inntech-100. Le coût peut atteindre 3 000 000 de roubles et la productivité est bien inférieure.
La particularité d'une telle ligne est l'immobilité de l'installation de mélange. Les formulaires sont déplacés et remplis automatiquement. Le complexe de découpe est mécanique.
Les lignes de production de blocs allemandes sont très populaires. Ils sont très productifs et sont utilisés pendant une longue période. Le matériel produit avec un tel équipement est de haute qualité.
Stationnaire
Son coût est nettement inférieur à celui de la première option. Mais en termes de productivité, la ligne ne produira pas plus de cinquante mètres cubes de matière par jour.
Le kit d'installation comprend des distributeurs de matières premières et des convoyeurs à bande qui alimentent les composants de l'unité de mélange.
Malheureusement, ce kit n'est pas considéré comme entièrement automatisé. Pour qu'il fonctionne pleinement, vous devrez attirer plusieurs travailleurs.
Pour installer la ligne, vous aurez besoin d'une pièce d'une superficie d'au moins cinq cents mètres carrés.
Mobile
Ce type d'équipement est idéal pour les débutants qui souhaitent fabriquer des blocs pour leur propre usage. À propos, certains spécialistes fabriquent de leurs propres mains de tels équipements pour le béton cellulaire.
La ligne fonctionne à partir d'un réseau de 220 W, alors que d'autres types de machines nécessitent 360 W. Les volumes de production sont faibles - de deux à dix mètres cubes par jour.
Production indépendante
Pour commencer à produire des matériaux de construction à la maison, vous aurez besoin de certains outils pour blocs de béton cellulaire et équipements. Leur ensemble minimum se compose de :
- bétonnière;
- bloquer les formulaires ;
- cordes métalliques destinées à couper l'excès de masse.
En suivant les instructions, fabriquer un bloc de gaz de vos propres mains à l'aide d'un tel ensemble d'équipements est tout à fait possible. Un aspect positif de cette méthode est qu'il est possible de mettre en place le processus de production directement sur le chantier en y installant une machine pour la production de blocs de gaz.
Les blocs de gaz faits maison sont de qualité inférieure aux matériaux fabriqués en usine.
Traitement en autoclave
Nous examinerons ce processus de production plus en détail, nous comprendrons ses différences et ses avantages.
Grâce à un tel traitement, les caractéristiques de qualité du produit fini sont améliorées. Le processus se déroule comme ceci :
- Les blocs, découpés selon les paramètres requis, sont envoyés dans des chambres autoclaves. Une température et une pression élevées sont créées à l’intérieur ;
- le processus de traitement dure douze heures ;
- une fois le traitement en autoclave terminé, les blocs peuvent presque immédiatement être utilisés dans la construction, car ils ont pleinement atteint l'indicateur de résistance requis ;
- la méthode de fabrication sans autoclave implique une exposition de quatre semaines, pendant lesquelles les blocs durcissent finalement.
Analyse comparative de la production en autoclave et hors autoclave
Comparons deux types de matériaux :

Instructions pour fabriquer du matériau en bloc
Ils commencent par assembler une trousse à crayons à partir de planches. Des cavaliers préfabriqués y sont insérés sur toute la longueur, divisant l'ensemble du cadre en cellules. Pour ce faire, utilisez du contreplaqué imperméable. Pour s'assurer qu'il soit bien fixé, des découpes sont pratiquées dans les planches.
Les tailles de cellules doivent correspondre aux tailles de blocs requises. Pour accélérer le processus de production, il est nécessaire de réaliser plusieurs moules de tailles différentes.
Pour éviter que la masse de mortier ne colle aux planches, celles-ci sont traitées avec des composés spéciaux ou de l'huile de machine diluée dans l'eau.
Pour mélanger la solution, vous devrez acheter un mélangeur, un compresseur et des tuyaux. À propos, une telle installation est utilisée non seulement pour la production ponctuelle de blocs, mais également pour organiser une production à petite échelle.
En plus de ce qui précède, vous aurez besoin d'un fil pour couper l'excès de solution.
S'il n'y a pas de distributeur, vous devrez alors peser vous-même la matière première. Il faut ici respecter des proportions précises pour ne pas compromettre la qualité des produits.
Tous les composants sont chargés dans le rapport requis. Cela accélérera le durcissement et augmentera les caractéristiques techniques des blocs. À propos, de telles proportions sont observées non seulement pour la production domestique, mais également pour la production en usine du matériau.
La masse préparée est versée dans des moules; ne remplissez pas à ras bord, car le mélange gonflerait encore. En règle générale, le remplissage est effectué à la moitié du volume.
Une formation de gaz se produit. Après cela, il est nécessaire d'éliminer l'excès de mélange. Ce travail est effectué cinq à six heures après la coulée.
Au bout de quatorze heures, un décapage est effectué. Pour faire décoller les blocs, il est recommandé de tapoter délicatement les parois des moules. Pour gagner en résistance technique, le matériau est laissé dans un espace ouvert ou stocké à l'intérieur.
N'oubliez pas que vous n'obtiendrez peut-être pas le matériau parfait du premier coup.
Conclusion
Nous avons compris comment fabriquer un bloc de gaz. Il ne reste plus qu'à décider de la quantité de matériel, acheter tout ce dont vous avez besoin et commencer le processus de production.
Cette pierre artificielle a depuis longtemps gagné en popularité, notamment dans le domaine des constructions de faible hauteur. Les développeurs individuels ont pu apprécier tous ses avantages, notamment le faible coût des produits. Et la rapidité de construction des bâtiments est telle que, selon cet indicateur, ce représentant de la classe du béton cellulaire occupe l'une des premières places parmi tous les matériaux de construction utilisés.
C'est également intéressant car, si on le souhaite, la production de béton cellulaire peut être organisée n'importe où, et pas seulement dans une entreprise spécialisée. La technologie est si simple que les blocs peuvent être fabriqués indépendamment, pour des besoins spécifiques, dans différentes formes et tailles, ce qui crée une commodité supplémentaire pour un développeur privé.
Quels sont les avantages de produire du béton cellulaire à la maison ?
Lors de la préparation de la construction, il n'est généralement pas possible de calculer le nombre exact de certaines ébauches (par taille). Et ce n’est pas seulement une question d’erreurs de mesure. La particularité de la maçonnerie est que dans chaque rangée suivante, les « briques » sont installées décalées pour éviter la coïncidence des joints verticaux. Par conséquent, vous devez passer du temps à découper les produits, ce qui entraîne finalement un gaspillage de matière. Par conséquent, en règle générale, les blocs sont achetés avec une réserve, ce qui constitue une dépense supplémentaire.
Tous les calculs d'éléments structurels sont « liés » à certaines tailles standards de produits. Mais dans la pratique, les souhaits du propriétaire et les dimensions des blocs achetés ne coïncident pas toujours. Par exemple, l'épaisseur des murs intérieurs. Organiser la production de béton cellulaire à domicile permet de produire de la pierre artificielle avec toute géométrie requise, y compris des configurations complexes (voûtées ou autres).
Les blocs de ce matériau sont préparés de deux manières - en autoclave ou sans utilisation d'équipement spécial. Considérons la dernière option, car pour la construction d'un ou deux bâtiments sur le site, il ne sert à rien de dépenser de l'argent pour acheter des caméras thermiques, qui ne seront pas nécessaires plus tard, mais sont assez coûteuses. Cette méthode présente certaines caractéristiques dont il faut tenir compte.
"Avantages"– coûts minimes, simplicité de la technologie. L'achat de blocs prêts à l'emploi, y compris la livraison sur site, coûtera beaucoup plus cher.
"Inconvénients"– la qualité des produits est inférieure à celle de ceux qui ont été soumis à un traitement thermique. Il n’est donc pas recommandé de construire un bâtiment de plus de 2 étages à partir de tels blocs. De plus, le durcissement se produit naturellement. Par conséquent, la production de béton cellulaire non autoclavé ne peut être réalisée qu'à des températures supérieures à + 5 0C pour assurer une évaporation normale de l'eau.
Vidéo - Production de béton cellulaire à la maison
Équipement
Bétonnière. Il est impossible d'obtenir une composition homogène et de haute qualité du mélange avec un mélange manuel, et cela est déterminé par plusieurs facteurs. Et la qualité des blocs finis est directement liée aux matières premières. Par exemple, de nombreuses caractéristiques (bruit, isolation thermique et bien d'autres) dépendent de la répartition uniforme des bulles d'air dans tout le volume du matériau.
Formes.
Fil fin en acier (pour couper l'excès de masse après coulée).
Composants du mélange pour la production de béton cellulaire
Ciment
Les artisans expérimentés affirment que n'importe quel bloc ne convient pas pour fabriquer soi-même des blocs. Il est recommandé d'utiliser les nuances « 400 » D20.
Le sable de quartz
Idéalement, il faut le passer au tamis, le laver soigneusement (pour éliminer les impuretés) et le sécher.
Suppléments
Chaux (chaux vive), sulfate de sodium, soude caustique, agent gonflant (poudre d'aluminium).
Bien entendu, vous aurez également besoin d’eau propre.
Technologie de travail
Réalisation de moules. Vous pouvez les acheter (préfabriqués) ou les fabriquer vous-même. Vous aurez besoin de planches dont une doit être soigneusement rabotée. On en fabrique une « trousse à crayons », dans laquelle sont insérés des cavaliers, la divisant sur toute sa longueur en compartiments. De tels « inserts » peuvent être découpés dans du contreplaqué résistant à l'humidité. Auparavant, dans les planches, selon des marquages préalablement réalisés, des découpes sont réalisées pour les « inserts ».
Les tailles des cellules déterminent les dimensions des futurs blocs, elles sont donc sélectionnées en fonction des paramètres que doit avoir la pierre artificielle. Pour accélérer le processus de production de béton cellulaire, vous devez préparer plusieurs coffrages différents, pour toutes les tailles standards requises.
Pour éviter que le mélange ne colle aux planches, les surfaces internes des alvéoles sont généreusement lubrifiées avec de l'huile usagée diluée dans de l'eau (3 parts) (huile machine - 1 part). À propos, cela est fait à chaque fois avant de verser à nouveau la solution.
Préparation d'un mélange pour béton cellulaire
Cette étape est toujours la plus difficile. Et ce n’est pas une question de qualité du mélange, mais de proportion d’ingrédients. Il convient de noter immédiatement que la qualité requise des produits finis ne peut être obtenue qu'expérimentalement. Tout dépend de la marque du ciment, du sable et des caractéristiques des autres composants. Même la qualité de l'eau utilisée affecte le déroulement de la réaction chimique qui se produit lors de l'introduction d'un gazogène. C'est pourquoi il n'existe pas de recommandation claire pour la production de béton cellulaire à la maison.
A titre d'exemple, il convient de donner cette proportion (elle a déjà été testée en pratique). Du ciment (100 kg) et du sable (180 kg) sont prélevés. Pour cette quantité vous aurez besoin d’environ 60 litres d’eau. Pour obtenir un lot de qualité, vous devez verser les ingrédients par portions, en petits lots, remplis de plusieurs litres de liquide. Chaque agitation dure environ 5 minutes. Progressivement, d'autres composants sont ajoutés à la solution - le sulfate de sodium et la soude caustique (respectivement 0,5 kg et 1,5 kg). À la toute fin - poudre (0,4 kg). Le mélange résultant est agité pendant environ 1 minute.
Remarque : Le composé de sodium ne peut pas être utilisé. Cela ne sert qu’à accélérer le processus de production.
La solution doit remplir chaque cellule environ à moitié. La réaction commencera et elle commencera à augmenter de volume (montée). Cela se produit en 5 à 8 minutes environ (en fonction de la température extérieure). Après un certain temps, le processus inverse commencera (diminution de la masse).
Lorsqu'il se « calme », la partie supérieure (grumeleuse) est coupée avec un fil métallique. Après cela, la solution est conservée dans des moules jusqu'à ce qu'elle durcisse (environ 20 à 24 heures). Ensuite, les blocs sont retirés des cellules et déplacés vers une zone désignée jusqu'à ce que la masse durcisse enfin.
Conseils pratiques
Il ne sert à rien d'acheter une bétonnière pour une construction ponctuelle. Par exemple, le coût de la bétonnière à gaz la moins chère est d'environ 40 000 à 45 000 roubles. Il est plus logique de louer du matériel. Mais ici, il convient de noter que les frais sont facturés pour chaque jour d'utilisation. Par conséquent, vous devez d'abord tout préparer, effectuer des calculs précis sur le nombre de blocs du même type, puis conclure un contrat de location.
Pour que tous les produits aient la même hauteur, le moule doit être chauffé sur toute sa longueur à la même température. Sinon, la masse dans les cellules extérieures diminuera davantage qu’au centre.
Il faut veiller à ce qu'il n'y ait pas de courants d'air. Par exemple, effectuez des travaux dans une buanderie ou clôturez la zone de tous les côtés.
En réalisant divers inserts en bois dans le moule, il est possible d'obtenir des blocs avec différentes configurations de faces latérales. Par exemple, des évidements à rainure et languette, des poignées pour un transport manuel.
Aujourd'hui, la technologie de production de blocs de béton cellulaire intéresse tous ceux qui envisagent de construire une maison de campagne ou d'ouvrir une entreprise de production de béton cellulaire. Après tout, ce matériau de construction est un très bon choix en termes de résistance et de caractéristiques d'isolation thermique, et en outre, la production de béton cellulaire peut être un projet commercial très rentable.
Que faut-il savoir sur le béton cellulaire ?
Le béton cellulaire est une pierre artificielle dotée de pores d'air microscopiques. Un autre nom est béton cellulaire autoclavé, et cela en soi parle de la technologie de sa production. Les blocs aérés ont d'excellentes caractéristiques d'économie d'énergie précisément en raison de leur structure poreuse. De plus, ils se distinguent par leur poids relativement faible, notamment par rapport à la brique et à d'autres types de céramiques de construction.
Les blocs de béton cellulaire sont un matériau de construction qui peut être utilisé aussi bien pour la construction de cloisons intérieures que pour des structures porteuses. Il ne convient pas aux immeubles de grande hauteur ou aux installations industrielles, mais il a fait ses preuves dans la construction individuelle. Les blocs de gaz relativement légers n'imposent pas de charge importante sur les fondations, ce qui réduit le coût de construction des fondations. De plus, ils sont de grande taille, ce qui accélère le processus de construction.
Composition des blocs de béton cellulaire
Tous les avantages énumérés de ce matériau de construction sont dus à sa composition. Le béton cellulaire n'est constitué que de ciment, de sable de quartz et d'un agent générateur de gaz, qui est de la poudre d'aluminium. Certains fabricants ajoutent du gypse, de la chaux, des cendres et d'autres ingrédients à la composition.
Ainsi, le béton cellulaire est réalisé à base de composants secs mélangés à de l'eau. Toute eau techniquement propre qui répond aux exigences de GOST 23732-79 convient à ces fins. La température de l'eau est importante. Il est souhaitable qu'elle ne soit pas inférieure à 45°C, car cela accélérerait le durcissement des blocs, augmenterait leur résistance, ce qui serait bénéfique pour l'entreprise car cela augmenterait la productivité de la ligne dans son ensemble. Ainsi, de nombreux fabricants chauffent l’eau car une température plus élevée signifie un matériau de meilleure qualité. Cela permet également de réduire la quantité de ciment utilisée, car chauffer l’eau stimule l’activité des composants secs du mélange.
La production de béton cellulaire nécessite une approche assez sérieuse dans le choix du sable. Théoriquement, le sable de carrière et le sable de rivière conviennent à ces fins, mais il est important qu'ils contiennent le moins de particules de limon ou d'argile possible. Il est également important de choisir la granulométrie - pas plus de 2 mm. La technologie de production de béton cellulaire par autoclave permet de remplacer le sable par des scories ou des cendres issues de la production métallurgique. Les cendres des centrales thermiques contribuent à produire du béton cellulaire de plus faible densité. Cela contribue à réduire davantage les coûts de production des matériaux.
Pour la production de blocs de béton cellulaire, les qualités de ciment Portland M400 et M500 sont requises. Il est préférable que le ciment Portland réponde aux exigences de GOST 10178-85. Mais la poudre d'aluminium doit être de qualité PAP-1 ou PAP-2 - elle agit comme un générateur de gaz. Parfois, une pâte spéciale est utilisée dans le même but. Il peut également s'agir d'une suspension, car l'aluminium en poudre n'est pas si pratique lors du mélange de la solution. Des suspensions basées sur celui-ci peuvent également être utilisées.
Sur quoi est basé l’effet de la poudre d’aluminium ? Il réagit avec le mortier de ciment ou de chaux, qui ont des propriétés alcalines, et au cours de ce processus chimique, des sels de calcium (aluminates) et de l'hydrogène gazeux se forment, ce qui assure la formation de pores.
Pour la production de béton cellulaire, il est très important de calculer correctement la consommation de chaque composant de la matière première. Il existe des recommandations standard pour les blocs de gaz autoclavés. Sur la base de cette recette, tout le volume du mélange est rempli de 50 à 70 % de ciment, de 0,04 à 0,09 % de poudre d'aluminium et jusqu'à 20 à 40 % de sable. De plus, vous aurez besoin d'eau (0,25-0,8 %) et de chaux (1-5 %). Ainsi, pour obtenir 1 mètre cube de béton cellulaire, il faut prendre jusqu'à 90 kg de ciment, jusqu'à 300 litres d'eau, de la chaux - 35 kg, du sable - 375 kg, de la poudre d'aluminium - 0,5 kg. Mais cette quantité peut être ajustée dans les conditions d'une production spécifique, en fonction des caractéristiques qualitatives des matières premières elles-mêmes.
De quel équipement aurez-vous besoin ?
La technologie de fabrication du béton cellulaire est relativement simple. Cependant, vous ne pourrez pas vous contenter de méthodes artisanales ici. Vous devez acheter un équipement spécial, qui est généralement commandé sous forme de package auprès du fabricant ou de son représentant officiel - c'est l'option la plus rentable. Il ne s’agit pas d’une simple installation, mais de toute une mini-usine automatisée. Parfois, le fabricant propose même les services d'un spécialiste qui conseillera sur l'installation d'une telle ligne, aidera à sa mise en place et sélectionnera la composition optimale du mélange utilisé pour un tel équipement.
Mini-usine de production de béton cellulaire non autoclavé
La gamme comprend divers appareils et, en théorie, chacun d'entre eux peut être acheté séparément si, pour une raison quelconque, l'un d'entre eux tombe en panne. Nous parlons d'éléments tels que des coffrages et des palettes mobiles destinées à leur transport, des dispositifs de découpe de blocs finis, des malaxeurs de béton cellulaire, des distributeurs de matériaux en vrac, etc. Mais l'essentiel est un four autoclave, car nous parlons spécifiquement de la production de blocs de gaz autoclave, qui se distinguent par les caractéristiques de qualité les plus élevées.
Les équipements pour la production de béton cellulaire sont divisés en plusieurs types. Le choix d'une option spécifique dépend de la productivité quotidienne requise, du nombre de travailleurs que l'entrepreneur envisage d'embaucher et de la manière dont les équipes seront organisées. Les options suivantes sont possibles :
- Les lignes fixes ont une productivité quotidienne allant jusqu'à 60 mètres cubes de produits finis. En règle générale, ils nécessitent des entrepôts et des installations de production d'une superficie d'au moins 500 m². La principale caractéristique de ces lignes est que les moules sont amenés jusqu'à un mélangeur installé en permanence et y sont remplis de solution, après quoi toutes les autres étapes technologiques sont réalisées. Il s'agit d'une technologie très simple ; pour entretenir une telle ligne, il suffit d'embaucher un employé supplémentaire.
- Des lignes de convoyeurs sont nécessaires lorsqu'une productivité élevée est requise - jusqu'à 75 à 150 m³ par jour. Ici, la production s'effectue à un rythme plus rapide (bien entendu, le temps de maturation du produit ne change pas, cela ne dépend pas de la ligne). Cependant, les lignes de convoyage nécessitent de grands locaux industriels et pour les entretenir, vous aurez besoin d'au moins 8 personnes, bien que la plupart des processus technologiques se déroulent ici automatiquement.
- Les mini-lignes ne peuvent pas se vanter d'une productivité élevée, jusqu'à 15 mètres cubes de blocs finis par jour. La différence avec les lignes fixes est que le mélangeur s'y déplace et que les coffrages sont installés de manière fixe. Le principal avantage est qu'ils n'ont pas besoin de grandes surfaces de production, 140 à 160 m² suffisent, ils sont donc populaires comme option de départ.
Dans la construction privée, on utilise souvent des installations mobiles, nécessaires à l'autoproduction de blocs de gaz. Cela s'avère payant et, selon les experts, les coûts de construction sont réduits d'environ 30 %. Les unités mobiles sont fournies complètes avec un compresseur. Ils fonctionnent même avec l’électricité domestique.
Étapes de production
Il existe deux types de béton cellulaire : autoclavé ou non autoclavé. Cette dernière option est moins chère, bien que le matériau obtenu ait une résistance moindre. Cependant, étant donné que le coût de sa production est inférieur (pas besoin d'acheter un autoclave, de l'entretenir, de payer un supplément pour l'énergie), il s'agit d'une option assez populaire, elle mérite donc d'être examinée plus en détail. Si un entrepreneur a l'intention de produire du béton cellulaire non autoclavé, la technologie de production doit être réduite aux étapes principales suivantes :
- Dosage précis de tous les composants décrits ci-dessus, puis mélangez-les soigneusement. Si vous disposez du matériel adapté, cette étape ne prend pas plus de 10 minutes.
- À l'aide d'un équipement spécial, la masse préparée est déchargée dans des moules spéciaux (ils ne sont remplis qu'à moitié, car le mélange augmentera de volume lors de la formation de gaz). Ce processus aura lieu dans les 4 heures. Pendant ce temps, le mélange remplit le volume qui lui est imparti dans le formulaire, et parfois même cela ne lui suffit pas. Puis après 2 heures, l'excédent peut être retiré.
- Le processus de durcissement des produits dure environ 16 heures, après quoi ils sont démontés et rechargés sur des palettes, où ils acquerront ce qu'on appelle la résistance au revenu. Cette étape prend encore 2-3 jours. Après cela, les produits peuvent être envoyés à l'entrepôt, mais il est encore trop tôt pour les vendre, car ils ne gagneront en force de marque que le 28ème jour.
La production de blocs de béton cellulaire à l'aide d'un autoclave dans les premières étapes n'est pratiquement pas différente de la technologie décrite ci-dessus. Vous devez d'abord mesurer la quantité requise de tous les composants (il est conseillé de le faire à l'aide de distributeurs, cela contribuera à améliorer la précision). Ensuite, toute cette masse est chargée dans le mélangeur et soigneusement mélangée. Parfois, les experts suggèrent d'utiliser une bétonnière à ces fins. Ensuite, un gazogène est introduit - cela se produit après 10 à 15 minutes de mélange des ingrédients initiaux. La poudre d'aluminium réagit dans tous les cas avec la solution ; elle ne nécessite pas d'autoclavage pour cela.
Le produit semi-fini est versé dans des moules, conservé pendant les 4 à 6 heures requises, après quoi les blocs de gaz sont découpés. Ils devraient rester assis pendant encore 10 à 18 heures avant de reprendre des forces.
Mais le plus important est de savoir comment se déroule l'autoclavage après toutes les procédures décrites ci-dessus. Les blocs formés sont rechargés dans un four spécial, dans une chambre scellée, où, à haute température, chaque bloc est traité avec de la vapeur d'eau saturée. La pression doit également être élevée - jusqu'à 12 kg/cm².
Le béton non autoclavé sèche naturellement, mais cela n’est pas nécessaire pour les produits autoclavés. Néanmoins, ils doivent également être conservés pendant environ 28 à 30 jours dans un entrepôt, où ils gagneront en force de marque.
Il ne suffit pas de savoir fabriquer du béton cellulaire, il faut aussi être capable de le livrer au consommateur. Pour ce faire, les blocs de gaz sont emballés dans un film rétractable spécial et transportés sur des palettes en bois.
Construction de maisons en béton cellulairetrès populaire, en raison du fait que ce type de matériau de construction présente de bonnes caractéristiques et des prix relativement bas, et au cours de la longue histoire d'utilisation du béton cellulaire, il a reçu de nombreux wow les critiques.
Se compose de plusieurs étapes clés. Nous décrirons la technologie de production de blocs de béton cellulaire et vous parlerons de l'équipement nécessaire utilisé dans la technologie de production de béton cellulaire.
Blocs de séchage
Après environ 1,5 à 2 heures, les produits acquerront la forme souhaitée
résistance, vous devez alors les retirer des moules et les envoyer dans un entrepôt chaud ou dans des chambres de cuisson à la vapeur pour terminer les processus de durcissement.
Sont également utilisées des options permettant de couler non pas des blocs individuels, mais la masse entière qui, après séchage, est découpée en blocs.
La différence entre le béton cellulaire autoclavé et le béton cellulaire non autoclavé
- béton cellulaire autoclavé , gagne en résistance à haute pression et haute température dans des fours spéciaux (chambres de séchage), appelés autoclave
- béton cellulaire non autoclavé , durcit en milieu naturel, à pression atmosphérique, ou on utilise un traitement chaleur-humidité utilisant la chaleur