Gramophone miniature en papier de vos propres mains. Haut-parleur passif pour téléphone - pavillon plié Comment les haut-parleurs sont-ils représentés graphiquement dans les schémas
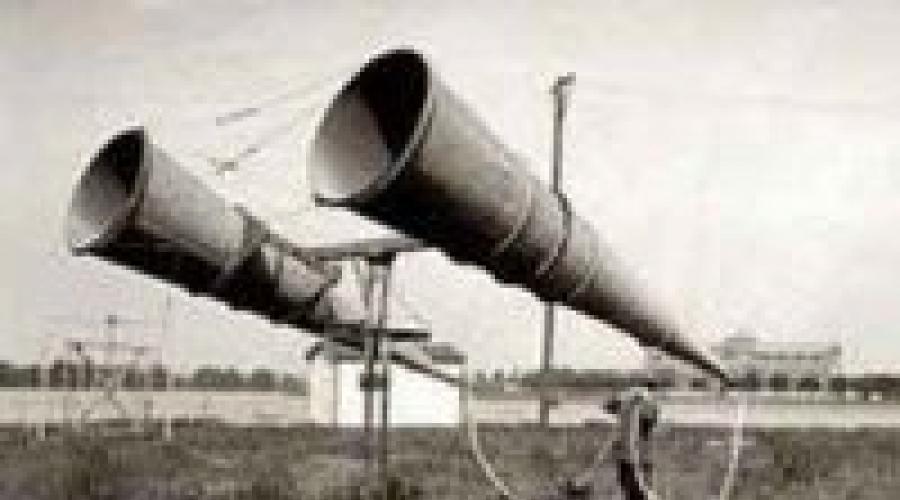
Lire aussi
Conférencier.
Le texte écrit individuel de chaque lecteur crée sa propre image qui reflète le contenu de ce qu'il lit. À l’intérieur, il semble que nous entendions la voix du narrateur ou les voix des personnes participant aux événements décrits dans le texte. Non. Ce ne sont pas les voix décrites par l'ésotérisme et les psychothérapeutes, mais le sentiment de ce que nous imaginons. personnages ou les actions accomplies par eux.
Les perceptions changent lorsque quelqu'un nous lit, et si c'est le cas avec une telle expressivité que l'image de ce qui est décrit devient si vivante et évidente qu'on a l'impression d'une présence et d'une participation complètes à tous les événements.
La situation sera pire si le narrateur vous tourne le dos ou si vous n'entendez pas son murmure, ou si la personne qui lit à haute voix se trouve à plusieurs centaines de mètres de vous. Donc vous ne l'entendrez pas. Alors, que devrions-nous faire?
Histoire courte.
En 1670, Samuel Morland put améliorer légèrement cette situation en inventant le mégaphone. Oui, le même mégaphone que l'on voyait souvent dans les films et qui était utilisé par les réalisateurs et les marins. Modèles similaires il était possible de transmettre des mots par la voix sur une distance allant jusqu'à cinq kilomètres, car les dimensions et le diamètre variaient selon le but recherché. Le son ne se propageait pas comme des ondulations sur l’eau, mais était émis de manière concentrée dans une seule direction. Et plus le haut-parleur est grand, plus les sons de la parole sont entendus loin.
Mais il est difficile d'imaginer, par exemple, quelle serait la taille du klaxon si nous transmettions les voix des acteurs de l'Opéra d'Odessa au parc qui porte son nom. Ville Gorki de Moscou.
En 1876, un brevet est apparu pour la première tête électrodynamique d'Alexander Graham Bell, dont l'invention a incité les concepteurs à développer divers haut-parleurs, et déjà en 1898, Oliver Lodge a développé un prototype. Design moderne tête électrodynamique.
Quel est le principe de fonctionnement d'une enceinte ?
Un dispositif permettant d'émettre un signal électrique converti dans l'espace sous forme d'ondes acoustiques (sonores) est appelé haut-parleur. S'il est placé dans un boîtier fermé, il s'agit déjà d'un système acoustique ou a déjà un nom établi - une colonne sonore.
Un haut-parleur comporte des parties mobiles et fixes qui forment son système fonctionnel.
C’est déjà un peu plus clair : la partie mobile crée vibrations mécaniques- vibration de l'air, que l'on perçoit comme du son, et plus la zone de contact de la partie mobile (diffuseur) avec l'air est grande, plus le signal sonore émis sera fort.
Le deuxième facteur, plus prioritaire, influençant la force est la puissance du son et sa qualité - il s'agit d'une bobine électromagnétique (voix) - tour à tour, fil de cuivre isolé enroulé sur un cadre, fixé bonne colle au cadre.
Le cadre est fait de papier épais ou de feuille de cuivre ou d'aluminium et est fixé au diffuseur par l'arrière. Les fils de la bobine sont connectés à l'étage de sortie de l'amplificateur audio.
Quel est le principe de fonctionnement d'une bobine de haut-parleur ?
Un signal électrique très faible, dont une composante est la fréquence audio, est envoyé à un appareil électrique un amplificateur de fréquence audio dans lequel il est amplifié plusieurs centaines, voire des milliers de fois, et transmis à la bobine électromagnétique d'un haut-parleur.
Bobine mobile a un mouvement libre sur une tige métallique située dans un champ magnétique puissant aimant permanent, forme d'anneau. Lorsqu'un signal électrique amplifié traverse l'enroulement de la bobine acoustique, un champ électromagnétique alternatif est créé, qui se résume en un seul tour de fil enroulé sur le cadre et interagit avec le champ magnétique d'un aimant annulaire permanent.
En fonction de la force du signal électrique fourni à l'enroulement, une bobine fermement fixée au diffuseur entraîne le diffuseur dans mouvements oscillatoires, qui excite l’air qui l’entoure, formant une onde sonore dirigée. Nous entendons du son. Mais les personnes malentendantes peuvent percevoir le son par vibrations – vibrations sonores de l’air, ressenties par la peau ou par vibrations d’objets solides à proximité.
La puissance émise par un haut-parleur sonore dépend dans une certaine mesure de la force champ magnétique aimant annulaire et le diamètre du fil de la bobine mobile enroulée. Ils interagissent parfaitement entre eux grâce au composant stationnaire principal du haut-parleur électrodynamique (champ magnétique électrique alternatif + champ magnétique constant de l'aimant annulaire = mouvement et dynamique).
Dans les grands cercles, un haut-parleur porte un nom court : haut-parleur.
De quoi est faite la partie fixe du haut-parleur ?
La base est solide et cadre léger, appelé support de diffuseur, en acier, en alliage d'aluminium ou en plastique, ce qui est moins courant. En plus du diffuseur, il contient un anneau magnétique, une rondelle de centrage et un système magnétique. Le boîtier comporte des trous pour le montage du haut-parleur dans le système de haut-parleurs, des câbles de bobine mobile flexibles et une grande découpe vitres latérales, pour communiquer les vibrations du diffuseur à l'air.
Quels autres types de haut-parleurs existe-t-il ?
Selon le mode d'émission sonore, l'interaction interne des éléments repose sur différents effets physiques :
- haut-parleur piézoélectrique - basé sur l'effet piézoélectrique (exemple : électronique montre-bracelet avec un signal);
- haut-parleur électrostatique - basé sur l'interaction électrostatique de fines membranes très rapprochées entre lesquelles haute tension, alimenté par un transformateur élévateur (la qualité du son reproduit est la meilleure) ;
- haut-parleur électromagnétique - le diffuseur est constitué de matériaux magnétiques (une membrane métallique) se déplace sous l'influence du champ magnétique d'un électro-aimant (la bobine mobile n'est pas enroulée sur un cadre, mais sur un noyau métallique).
Il en existe de nombreux autres, divisés par type et bande passante (selon la gamme de fréquences audio), mais le principe principal de tous repose sur l'émission d'ondes acoustiques dans l'espace environnant.
Fonction inverse, percevoir les ondes sonores et les convertir en signal électrique, disposer d'un appareil appelé microphone (micro - très petit + fond - son).
Comment les haut-parleurs sont-ils représentés graphiquement dans les schémas ?
Le dessin d’un haut-parleur et de produits acoustiques similaires ressemble à leur vue latérale. C'est si quelqu'un l'a vu.
Conférencier indiqué par un rectangle avec deux lignes indiquant la connexion du produit au circuit. Un trapèze, rappelant une corne, est fixé sur un côté du rectangle par son côté étroit. A l'intérieur du rectangle, une image indique le type d'appareil sur lequel fonctionne l'enceinte :
- ligne ondulée et ligne droite parallèle - électromagnétique ;
- la ligne ondulée est notre haut-parleur (électrodynamique) ;
- un rectangle avec deux lignes parallèles sur les bords est piézoélectrique ;
- une ligne ondulée avec une flèche bidirectionnelle parallèle - magnétostrictive.
- image d'un condensateur apolaire - électrostatique (sans diffuseur - membrane) ;
Lequel désignations de lettres des haut-parleurs ?
Il y a toujours une lettre latine (B) dans la désignation des éléments acoustiques dans le schéma, et à côté se trouve le type d'appareil acoustique. Exemple : BA – haut-parleur, ВF – téléphone (capsule), VM – microphone, ВQ – élément piézoélectrique, ВS – capteur de son.
Il existe également des désignations dans les symboles russes. Par exemple : GD est une enceinte électrodynamique, KZ est une colonne sonore.
Vous avez maintenant au moins un peu compris le principe d'un haut-parleur et sa désignation dans les schémas.
Il y a quelque chose de très attrayant dans l'équipement qui n'a pas besoin d'être énergie électrique, et le haut-parleur passif du téléphone entre dans cette catégorie. J'ai décidé de vous expliquer comment le construire selon le principe d'une corne pliée. Le design a un son profond (mais bien sûr pas de vraies basses) et amplifie le son deux à trois fois, tout en restant assez compact. Je n'ai aucun doute qu'un klaxon plus grand fournira plus meilleur son, mais bien sûr au détriment de la taille et de la complexité.
ÉTAPE 1 Principe de la corne pliée
La première image montre le fonctionnement de la corne pliée. Le son pénètre dans la gorge du klaxon, dans le trou opposé au haut-parleur du téléphone, se déplace à travers les parois du klaxon en expansion progressive jusqu'à ce qu'il ressorte par la bouche - la plus grande partie du klaxon. La corne est dite pliée uniquement parce que l'espace est économisé en « pliant » la structure. La deuxième image montre le trou qui sera situé directement derrière le haut-parleur du téléphone, dirigeant le son vers la gorge du klaxon. Aucun calcul n'a été effectué pour cette conception. J'ai choisi au hasard une taille qui conviendrait à mon GALAXY SII, puis j'ai fabriqué le klaxon par essais et erreurs. Peut-être que si j'avais fait les calculs, le son aurait été meilleur, mais cette conception est conçue pour les personnes qui n'ont pas de connaissances particulières.
Je n'ai pas utilisé beaucoup de contreplaqué. bonne qualité, 4 mm d'épaisseur, mais il est préférable que le contreplaqué soit de bonne qualité avec surface lisse. Les panneaux de fibres conviennent également. Vous pouvez utiliser des matériaux d'une épaisseur de 3 mm, car pression sonore La corne ne sera pas grande.
Si vous utilisez du contreplaqué, veillez à prendre des précautions pour limiter au minimum l'écaillage des bords. Il peut s'agir d'un morceau de ruban de masquage pour couvrir la ligne de coupe, d'une légère coupe avec une scie ou d'un revêtement protecteur sur du contreplaqué ou du MDF.
La largeur de toutes les pièces, à l'exception des panneaux latéraux, est de 70 mm - c'est la largeur de mon GALAXY SII. Si vous utilisez un téléphone d'une largeur différente, vous devrez alors modifier en conséquence la largeur de toutes les pièces en fonction de la largeur de votre téléphone.
ÉTAPE 2 Assemblage
Fabriquer une corne est très simple - seuls du contreplaqué, de la colle à bois et une pince sont utilisés. J'utilise de la colle PVA, elle ne sèche pas très vite, cela laisse le temps d'aligner et d'ajuster toutes les pièces, mais après séchage elle lie très fortement la matière. Cela fonctionne bien dans les conceptions comme celle-ci qui utilisent des joints bout à bout. Plus vous utilisez de colle, plus la connexion sera solide. Il est préférable de couper toutes les pièces aux dimensions d'un coup et de marquer leur longueur, car... La largeur de tous, sauf les parois latérales, est de 70 mm.
Bien sûr, il y a beaucoup de pièces qui doivent être collées ensemble, je pense qu'il n'est pas nécessaire d'essayer de les coller toutes en même temps. Il est préférable de procéder en plusieurs étapes, pièce par pièce. Cela prendra un peu plus de temps parce que... Vous devrez laisser sécher chaque joint, mais le processus restera simple et facile.
1. Commencez par coller le panneau arrière perpendiculairement au panneau latéral droit. J'ai utilisé un petit bloc pour cela afin de pouvoir les réparer.
2. Pendant qu'ils sèchent, collez ensemble deux morceaux de 30 mm et 65 mm à angle droit. Il faut que le bord d'une pièce d'une taille de 35 mm soit collé sur une pièce d'une taille de 65 mm, et non l'inverse. Ces deux pièces formeront un côté et partie inférieure embout buccal.
3. Une fois que les panneaux arrière et latéraux sont secs, vous pouvez coller la pièce supérieure de 50 mm et la pièce inférieure de 74 mm, et le panneau arrière les soutiendra pendant le séchage. Lors du collage de ces pièces et de celles qui suivent, gardez à portée de main le panneau latéral gauche (qui sera installé en dernier) et utilisez-le pour vérifier l'ajustement des pièces, afin d'éviter toute surprise lors de la mise en place ultérieure du panneau latéral. Vous pouvez également utiliser ce panneau comme pince lestée lors du collage des pièces internes.
4. Deux pièces de 65 et 30 mm, collées préalablement, après séchage, peuvent être mises en place en tenant compte de la distance sur les côtés, comme indiqué sur la photo ci-dessus.
5. La dernière pièce à installer est celle de la taille de 81 mm du panneau avant. En bas, la corne doit avoir une largeur de 7 mm. Ceci est réalisé installation correcte pièces d'une taille de 81 mm en face d'une pièce d'une taille de 30 mm. Dans mon cas, cela s'est produit à la suite d'une légère déviation de la pièce (81 mm) par rapport à un angle droit.
6. Collez les pièces de dimensions 11,14,16 mm aux coins conformément à la photo. Ils feront passer le son en douceur (je pense que oui). Vous pouvez mouler les extrémités de ces pièces pour qu'elles s'adaptent mieux aux murs et combler les vides avec du mastic silicone.
7. Collez maintenant le panneau latéral gauche.
ÉTAPE 4 Finition
Une fois assemblé, votre klaxon devrait ressembler à la photo à l'exception du trou du haut-parleur du téléphone et de l'amorce, je l'ai fait plus tard.
Le trou doit être situé directement en face du haut-parleur du téléphone, dans ce cas il a été positionné pour le GALAXY SII, pour les autres téléphones il sera à un endroit différent. Pour autant que je sache, la plupart des téléphones ont des haut-parleurs situés en bas à l'arrière. Si votre enceinte est positionnée plus haut, vous pouvez bien sûr percer un trou à l'emplacement correspondant sur la dalle de 81 mm, mais je ne sais pas comment cela va affecter le son.
Je noterai également que les coins avant supérieurs des panneaux latéraux ont été découpés au ras du bord sur lequel reposera le téléphone une fois la structure assemblée. Il peut être préférable de les marquer et de les couper avant l'assemblage si vous êtes sûr de pouvoir tout mesurer correctement afin qu'il n'y ait pas de mauvaises surprises plus tard lors de l'assemblage.
L’assemblage du klaxon principal est terminé et la conception finale dépend de vous.
J'ai légèrement courbé les bords avant des panneaux latéraux à l'aide d'un gabarit. Le rayon de la courbe du gabarit est de 500 mm.
Enfin, j'ai arrondi les bords des panneaux latéraux. Et j'ai peint le tout avec de la peinture en aérosol. Après cela, j'ai collé les pieds, que j'ai fabriqués à partir de panneaux de fibres de 6 mm d'épaisseur.
Si vous décidez de répéter cette conception, bonne écoute.
Ci-dessous je vais donner un exemple de modification du klaxon pour les propriétaires de téléphones dont les haut-parleurs sont situés en bas, comme l'iPhone.
Modifications de l'ÉTAPE 5 pour les téléphones équipés de haut-parleurs montés en bas
FABRICATION D'UN CORNE POUR UN SYSTÈME COUSTIC
AVEC VOS PROPRES MAINS
L'article présente une technologie de fabrication de cornes qui permet d'en obtenir suffisamment haute précision son dimensions géométriques, et adapté pour une utilisation à la maison.
Cet article est consacré exclusivement aux enjeux technologiques de la fabrication d'une corne ronde ; vous n'y trouverez ni méthodes de calcul des cornes, ni tailles spécifiques, ni éloges pour la corne obtenue, mais seulement comment la fabriquer chez vous, à genoux. , avec une précision suffisante et des coûts de matériaux minimes. On suppose que vous disposez d’un ensemble de coordonnées qui définissent sa géométrie.
Presque tout ce que vous pouvez découvrir en ligne sur les cornes se trouve sur les pages du site Web de Horn : sélection de paramètres, options de conception, applets pour les calculs, liens et bien plus encore. Nous renvoyons vers ce site toute personne désireuse d’approfondir ses connaissances dans ce domaine.
Les doutes
Nous avons donc décidé de réaliser la liaison moyenne fréquence du futur système de haut-parleurs sous la forme d'un haut-parleur. Après avoir sélectionné la tête dynamique, calculé le pavillon et obtenu tous les dessins nécessaires dans AutoCAD, nous avons regardé ces dessins et réfléchi longuement. Comment réaliser une pièce aussi grande (diamètre supérieur à un demi-mètre) avec une forme assez complexe.
L’option de fabriquer une corne à partir de segments a été immédiatement écartée. Il y avait de grands doutes quant à la capacité de garantir une précision acceptable des dimensions géométriques lors de l'utilisation d'un matériau épais (MDF ou contreplaqué), et fabriquer une corne à partir de contreplaqué de 3 mm n'avait pas beaucoup de sens. Et je voulais toujours le faire rond. Puis sont venues des propositions semi-fantastiques comme transformer une corne à partir d’une ébauche solide ou fabriquer un moule pour le moulage par injection. Après avoir sondé les questions sur la disponibilité des équipements appropriés et le coût des travaux, nous avons rapidement abandonné ces idées. Il s'est avéré que soit les coûts de production de plusieurs échantillons expérimentaux étaient inacceptablement élevés, soit il y avait de grandes difficultés technologiques, soit il n'y avait pas d'équipement approprié.
Étant descendus du ciel sur terre et après avoir discuté un peu (notre passe-temps favori), nous avons convenu que le plus option appropriée faire plusieurs échantillons - la corne sera collée. Étant donné que des exigences strictes en matière de respect de la géométrie et de qualité de surface sont imposées à la fois sur la surface intérieure du cornet et sur la surface extérieure besoins spéciaux non, alors nous avons adopté la méthode du collage sur le modèle.
Nous devions maintenant décider sur quoi coller. Trois options ont été envisagées (en principe, toutes les trois conviennent) : une corne collée en papier ou en papier et tissu à l'aide de colle PVA, collage en fibre de verre sur résine polyester et moulage en papier mâché préparé sur PVA. Il nous a semblé que la troisième option était la plus avancée technologiquement ; le coût insignifiant des matières premières était également très attractif.
Pour évaluer les propriétés du matériau, une expérience a été réalisée : un séparateur en polyéthylène provenant d'un grand arrosoir a été utilisé comme modèle, sa forme rappelant beaucoup celle de la future enceinte. Après complètement sec Après la masse moulée, nous avons retiré la pièce finie du modèle improvisé et l'avons étudiée de près. Les résultats ont été très encourageants, la surface intérieure de la corne était pratiquement sans défauts et reproduisait exactement la forme du séparateur, la texture du papier mâché séché ressemblait à un panneau de fibres (mais plus lâche), était très durable, légère et « sourde ». Cela nous a finalement inspiré à fabriquer une corne en papier mâché grandeur nature.
Projet
La figure 1 montre comment nous avons imaginé la conception du pavillon et la fixation de la tête dynamique. Il a été supposé que la tête dynamique était fixée à une bride en contreplaqué moulée sur la gorge du pavillon et, en fait, étant son continuation.
Image 1
La surface intérieure de la bride correspondait au profil de la gorge du cornet. Pour assurer une résistance mécanique suffisante de la fixation de la bride et du renforcement du pavillon lui-même, il faut visser dans la bride huit tiges filetées d'un diamètre de 4 mm et d'une longueur de 200x250 mm, qui sont moulées dans le corps du pavillon (comme pratique l'a montré, il est impossible de retirer le goujon sans détruire le klaxon).
L'épaisseur de la bride a été choisie assez grande - environ 20 mm, dans l'espoir qu'elle surface extérieure pourrait être mis et sécurisé caméra arrière. En cours de route, la bride est utilisée comme élément grâce auquel vous pouvez retirer le cornet fini du modèle. Le dessin de la bride est illustré à la figure 2.
Figure 2
Étant donné que la corne est un corps de rotation, à l'aide d'une sorte de tour de potier et d'un gabarit précis, il est possible d'assurer une haute précision dans la fabrication d'un modèle à partir d'un matériau plastique. Une erreur ne dépassant pas une fraction de millimètre est tout à fait réalisable. Sur la base de ces considérations, notre version du dispositif de réalisation du modèle a été conçue (Fig. 3).
figure 3
Il se compose d'un poteau central (un tronçon de tuyau épais a été utilisé), sur lequel sont placées deux brides en bas, et un bouchon avec un axe métallique vissé est inséré sur le dessus. La bride supérieure est destinée à la fixation du disque sur lequel sera moulé le modèle, et elle assure également sa perpendiculaire au support, et la bride inférieure est destinée à la fixation de l'ensemble de la structure à l'établi (au final, nous avons utilisé un morceau de une planche large et épaisse). Les brides reposent simplement les unes sur les autres.
Le disque et la base sont fixés aux brides avec des vis à travers des trous percés. Deux bagues sont placées sur la bride inférieure (fixe) et sur l'axe supérieur dans un ajustement coulissant, auxquelles sont soudés des câbles pour la fixation du gabarit.
La conception s'est avérée très pratique pour le travail, puisque le gabarit et le disque peuvent tourner indépendamment autour d'un axe, mais c'est quelque peu compliqué. Tu peux penser à plus conception simple, par exemple, avec un modèle fixe, mais dans tous les cas, deux exigences fondamentales doivent être remplies pour garantir l'exactitude du modèle.
Premièrement, le support (axe de rotation) doit être perpendiculaire au disque sur lequel le modèle est formé. Et bien entendu, les laisses fixant le gabarit doivent avoir une rigidité suffisante.
Deuxièmement, il faut s'efforcer d'assurer un jeu minimal dans les pièces en rotation.
Le gabarit peut être fabriqué à partir de n'importe quel matériau fin (0,8x1,5 mm) et dur - duralumin, acier, fibre de verre.
En fait, une aide extérieure n'est requise que lors de la réalisation de la bride et du gabarit en contreplaqué pour former le modèle (tournage nécessaire). Si cela entraîne des difficultés insurmontables, vous pouvez en principe le faire vous-même.
La bride peut être découpée avec une scie sauteuse et un motif avec un gabarit fixe peut être utilisé pour mouler le modèle. Dans ce cas, le gabarit et le poteau central sont fixés rigidement et perpendiculairement au socle inférieur, et le disque est posé sur le poteau et repose directement sur le socle (pour faciliter la rotation du disque, il convient de placer une entretoise en plastique fin et glissant entre eux).
Des instructions précieuses
Malgré le titre à moitié plaisant de cette section, il y a du vrai là-dedans. Puisqu'à l'avenir les principaux travaux de fabrication d'une corne seront liés au masticage, au ponçage et à la peinture, pour ne pas nous répéter plusieurs fois, nous nous permettrons de donner quelques conseils sur la réalisation de ces travaux et le choix des matériaux. Les peintres professionnels peuvent sauter cette section tout de suite, mais pour ceux qui sont habitués à peindre exclusivement en peignant des fenêtres et des portes, cela peut être utile.
Premièrement, tu dois utiliser uniquement des matériaux de haute qualité provenant de marques connues. C'est nécessaire pour eux application correcte et vérifier la compatibilité (par exemple, les émaux synthétiques n'adhèrent pas bien à certaines marques de mastics). De manière générale, lorsque vous vous rendez dans un magasin pour acheter du matériel, regardez ce qui est écrit dans la notice d'utilisation.
En faisant travail difficile Nous avons principalement utilisé du plâtre et des mastics hydrosolubles à base de liant plâtre (on peut considérer le meilleur mastic pour plaques de plâtre sous le nom commercial « Isogypsum »). Pour les opérations plus délicates, des mastics acryliques hydrosolubles ont également été utilisés - démarrage et finition. Ces mastics n'ont pratiquement aucune odeur, sont excellents pour le ponçage à sec et ont suffisamment
surface dure et permettre l'application de presque toutes les peintures. Les matériaux de peinture et de vernis suivants ont été utilisés : huile siccative naturelle de tournesol, vernis glyphthalique ou pentaphtalique avec n'importe quel numéro commençant par 1 (signe de résistance aux intempéries) et émail pentaphtalique de type PF115 pour réaliser des opérations de peinture intermédiaires. Pour la peinture finale, il est conseillé d'utiliser un émail synthétique phtalique à l'huile séchant à froid importé de haute qualité, qui a une propriété auto-nivelante, et de l'appliquer par pulvérisation. Des résultats satisfaisants peuvent également être obtenus en utilisant des émaux alkydes décoratifs dans des emballages aérosols pour la peinture finale.
Deuxièmement, chaque opération ultérieure de traitement des pièces n'est effectuée qu'après le séchage complet des revêtements précédemment appliqués.
Troisièmement, lors du masticage, n'essayez jamais de corriger les défauts que vous remarquez sur une surface qui vient d'être masticée ; laissez sécher le mastic, poncez la surface, puis corrigez-la. Sinon, le mastic séché atteindra la spatule et vous obtiendrez une surface lunaire au lieu de plusieurs petits défauts, cela demandera dix fois plus d'efforts ; Lors du masticage, respectez le principe : dix dépressions valent mieux qu'une bosse. Vous passerez beaucoup plus de temps à nettoyer cette bosse qu’à la replâtrer.
Quatrièmement, chaque opération ultérieure visant à affiner la surface jusqu'à la qualité souhaitée commence par le ponçage ; cette règle s'applique également aux revêtements multicouches de peinture et de vernis (y compris aux étapes de finition de la peinture). Pour le ponçage, il est pratique d'utiliser du papier de verre à mailles ; pour le traitement grossier, du papier de verre avec une granulométrie de 60 à 200 est utilisé ; pour la finition, du papier de verre avec une granulométrie de 400 à 500 est utilisé. Faites le plein de papier de verre ; au fur et à mesure que vous travaillerez sur les cornes, vous vous y familiariserez.
Cinquièmement, après le ponçage et avant d'appliquer la couche de revêtement suivante, la pièce doit être parfaitement dépoussiérée.
Sixièmement, après avoir terminé la prochaine étape du travail, lavez soigneusement l'outil. Les mastics bruts, parfaitement lavés à l'eau, ne veulent pas du tout être enlevés après séchage, eh bien, il n'y a rien à dire sur les pinceaux - vous devrez simplement jeter un pinceau non lavé.
A la fin de cette section, nous tenons également à vous souligner que le résultat de votre travail de fabrication d'un cor dépend à 99% de votre précision et de votre patience.
Maquettisme
Le dispositif de réalisation du modèle décrit ci-dessus (Fig. 3) comporte deux parties,
que vous devez fabriquer vous-même sont un disque et un modèle. Le disque est découpé à la scie sauteuse (ou à la main) dans un morceau d'aggloméré de 16 mm d'épaisseur. Le diamètre du disque doit dépasser le petit diamètre maximum du modèle de 40x50mm. Cette allocation est nécessaire en raison du retrait du papier mâché, il est nécessaire
faites délibérément le diamètre de la partie plate de la corne (là où l'embouchure de la corne rencontre un plan perpendiculaire à celle-ci), afin de pouvoir la couper plus tard sur mesure. Nous avons essayé de compléter la bouche avec une perle, c'est bien visible sur le gabarit, et cette perle nous a fait une blague cruelle, nous aborderons cette question plus en détail plus tard ;
Pour protéger le disque de l'humidité et éviter toute déformation, il est imbibé deux fois d'huile siccative chauffée. L'huile siccative est appliquée sur la surface de travail (celle où le modèle sera formé) et sur la surface d'extrémité du disque avec une brosse large et douce jusqu'à ce que l'huile siccative cesse d'être absorbée sous vos yeux. Après quelques jours, l'opération est répétée. L'huile siccative est chauffée dans un bain-marie ; en d'autres termes, un récipient contenant de l'huile siccative (de préférence en métal) est placé dans de l'eau bouillante et attendu 15 minutes. Le récipient contenant de l'huile siccative doit être recouvert de quelque chose, sinon les vapeurs d'huile siccative. peut s'enflammer. Vous ne devez en aucun cas essayer de chauffer de l'huile siccative directement sur un feu ; c'est une entreprise dangereuse - l'huile siccative chaude est extrêmement inflammable. Après quelques jours, le disque est recouvert d'une couche de vernis.
Pendant que tout sèche, vous pouvez commencer à créer un modèle. Comme nous avions tous les dessins dans AutoCAD, le dessin a été imprimé à l'échelle 1:1. La feuille de papier résultante a été collée sur un morceau de stratifié en fibre de verre avec de la colle qui n'a pas ramolli le papier (de la colle Moment a été utilisée) et traitée le long du contour. Ensuite, ils ont façonné grossièrement le gabarit, en coupant le matériau avec un couteau en métal ; la surface de travail (qui définit la forme de la corne) a été finie avec des limes et du papier de verre.
Si vous disposez d'un ensemble de coordonnées de la génératrice du cornet, alors il est également conseillé de réaliser toute la construction sur une feuille de papier et de la coller sur la feuille destinée à réaliser le gabarit. Naturellement, nous devons nous efforcer de tout faire aussi précisément que possible. Après avoir traité le gabarit le long du contour, l'un des bords de la surface de travail doit être biseauté à un angle de 30 à 45 degrés, le deuxième bord ne doit pas en souffrir. Le gabarit devient asymétrique ; lors de la formation de la surface, il doit être tourné dans un seul sens pour que le bord biseauté s'étende sur la surface du modèle.
Lors de la conception d'un modèle, il est conseillé de faire en sorte que le haut point de ligne, définissant la forme du cornet, coïncidait en hauteur avec le bord supérieur du support, cela facilite grandement son installation, et sous le point inférieur de cette ligne il restait 15 à 20 mm à la surface du disque.
Pour faciliter l'utilisation, pour étapes initiales Pendant le fonctionnement, le matériau appliqué ne glisse pas du disque ; une coque métallique est clouée le long du contour du disque (non représentée sur la figure). Sa hauteur est approximativement égale à la moitié de l'écart entre le gabarit et le disque ; des chutes de fer à toiture ont été utilisées pour sa fabrication.
L'appareil est assemblé et la position du gabarit est soigneusement ajustée par rapport à l'axe de rotation.
Maintenant, en effet, la production du modèle commence.
Étape 1– remplir le volume interne du modèle.
Pour remplir le volume interne du modèle, vous pouvez utiliser n'importe quel matériau - des morceaux de bois à l'argile et mortier de ciment. En conséquence, vous devez obtenir un aspect approximatif d'une corne ; l'écart entre le mastic et le gabarit doit être de 3x15 mm.
Nous avons utilisé un mélange argile fine expansée(pour alléger le poids) avec plâtre de construction dans un rapport de 2:1 en volume. Le mélange est préparé en petites portions dans un large bol souple (il est alors facile d'éliminer les résidus de gypse séchés en les écrasant légèrement), d'abord le mélange est mélangé à sec, puis recouvert d'eau, mélangé à nouveau et versé sur un disque. La forme du mélange est donnée en le nivelant avec une spatule ; tout doit être fait rapidement - la durée de vie du mélange est de 4 à 5 minutes.
Il est nécessaire de surveiller en permanence l'épaisseur du mélange appliqué à l'aide d'un gabarit. N'essayez pas de déplacer le mélange avec un gabarit, il est trop rigide pour cela et le gabarit pourrait perdre son alignement. Les zones saillantes sont déplacées ou supprimées à l'aide d'une spatule. Dans la partie supérieure de la corne et sous le gabarit, l'interstice est trop petit pour utiliser un mélange avec de l'argile expansée ; ces zones ont été remplies de gypse pur ; La procédure de remplissage du volume interne est effectuée en une seule fois sans interruption.
Après la première étape, le modèle présentait un spectacle déchirant et ressemblait à un gros tas de blanc... vous pouvez deviner quoi.
Étape 2– formation de la surface du modèle.
A ce stade, à l'aide d'un mastic à base de liant plâtre, la formation principale de la surface du modèle est réalisée, désormais avec un gabarit. Couvrir le mastic d'eau et bien mélanger à l'aide d'un agitateur mécanique inséré dans une perceuse. La consistance du mastic doit ressembler à de la crème sure très épaisse. A l'aide d'une raclette (spatule en caoutchouc), appliquer couche épaisse appliquez du mastic sur le modèle et nivelez-le avec un gabarit en le déplaçant d'un côté.
Une sorte de rouleau de mastic se forme devant le gabarit ; lorsqu'il devient mince ou que des espaces apparaissent dans le mastic, appliquez une autre portion de mastic. Il est conseillé de calculer la quantité de mastic appliquée de manière à ce que lorsque vous faites le tour complet du modèle avec le gabarit, il n'y ait pratiquement pas de mastic devant le gabarit.
Vous devrez peut-être refaire cette opération (bien sûr, après séchage de la couche précédente), tout dépend de vos qualifications. Avant de commencer le travail, vérifiez si le gabarit tourne librement autour du modèle ; s'il s'accroche aux saillies, retirez-les.
Lors du ponçage d'un modèle, il est pratique d'utiliser un morceau de caoutchouc épais (8x10 mm) de dureté moyenne comme support de papier de verre ; le papier de verre est enroulé autour du caoutchouc ; Il est déconseillé de poncer le modèle en appuyant sur le papier de verre avec la main ; cela pourrait entraîner la formation de surfaces inégales.
Après cette étape de travail, le modèle correspond presque entièrement à la forme donnée.
Étape 3– finition grossière de la surface.
Peut-être que si l'étape précédente des travaux a été effectuée avec soin, vous n'en aurez pas besoin. En fait, il s'agit d'une répétition de l'étape 2, en utilisant uniquement le mastic acrylique de départ.
Après cette étape de travail, le gabarit doit glisser sur la surface sans jeu et avec un léger frottement.
des modèles
Étape 4– protection du modèle contre l'humidité.
La surface du modèle doit être soigneusement protégée de l'humidité ; à cet effet, la surface du modèle est imprégnée d'huile siccative chaude.
Étape 5 - la touche finale surfaces.
Tout d'abord, il est nécessaire de retirer le gabarit ; la vérification de la conformité de la surface du modèle à la forme donnée, si nécessaire, est effectuée en appliquant le gabarit.
Initialement, la surface du modèle est peinte avec une couche de peinture dite de développement. La couleur de la peinture doit contraster suffisamment avec la couleur du mastic. Après avoir poncé la surface avec du papier de verre fin (granulométrie - 300x400), vous verrez de nombreux petits défauts sur la surface - rayures du gabarit, grains de mastic, traces de papier de verre. Tous les défauts constatés sont comblés avec du mastic acrylique de finition.
Ensuite, le cycle est répété - ponçage, peinture, ponçage et réinspection de la surface pour détecter les défauts. Si la surface est uniformément mate, ne présente aucun défaut visible et aucune irrégularité n'est ressentie lorsque vous passez la main dessus, l'étape est terminée. Si vous n'êtes pas satisfait des résultats, le cycle de travail est répété ; trois passes nous ont suffi.
Il s'agit d'une étape de travail très importante ; il faut tenir compte du fait que la surface de contact de la corne moulée avec le modèle est très grande et que les surfaces inégales du modèle rendent son retrait très difficile. Si vous effectuez le travail avec négligence, vous ne pourrez tout simplement pas retirer la corne finie sans détruire le modèle et vous devrez fabriquer au moins deux pièces.
Étape 6– coloration du modèle.
La surface du modèle est peinte deux fois avec de l'émail pentaphtalique.
Étape 7– application d'un revêtement antiadhésif.
Pour faciliter le retrait du cornet fini du modèle et pour protéger en outre le modèle de l'humidité, sa surface est recouverte d'une couche de séparation. Vous pouvez utiliser du mastic ciré pour sol comme couche de séparation, mais nous n'avons pas pu le trouver en vente.
C'est pourquoi nous avons fabriqué notre propre mastic. Après réflexion, nous sommes arrivés à la conclusion que c’était pour le mieux : nous savions exactement ce qui était utilisé. Le mastic est préparé à partir de térébenthine et de cire naturelle, mélangées dans un rapport de 2:1 (en poids). Le mastic se prépare comme suit : versez la cire fondue en un mince filet dans de la térébenthine chauffée au bain-marie sous agitation continue. Le mastic refroidi est appliqué sur la surface du modèle avec une brosse douce en trois couches épaisses (avec séchage intermédiaire de chacune), la dernière couche est soigneusement polie avec un chiffon.
Ceci conclut la production et la préparation du modèle. Les figures 4 et 5 montrent le résultat final de notre travail.
Fabriquer du papier mâché
Il est conseillé de réaliser ce travail en parallèle avec la réalisation du modèle. Vous aurez suffisamment de temps pour cela en raison des interruptions forcées des travaux nécessaires pour que la prochaine couche de mastic sèche complètement.
Le papier de qualité journal convient à la fabrication du papier mâché ; nous avons utilisé de vieux magazines. Pour commencer, vous devez déterminer quantité requise la pâte à papier. Approximativement, le volume requis peut être déterminé en rapprochant le cornet avec deux cônes tronqués le long des surfaces extérieure et intérieure (régler au préalable l'épaisseur de la paroi). La différence des volumes de ces cônes donnera la valeur souhaitée. La production de notre corne a nécessité 2/3 d'un seau de dix litres de pâte à papier.
Ainsi, le papier préparé doit être coupé (haché, déchiqueté, déchiré en lambeaux - c'est à la toute fin du processus) en petits morceaux (10x10 h 20x20 mm). Franchement, le processus de découpe est extrêmement fastidieux ; après le premier magasin, une irrésistible envie est née de le mécaniser en installant scie circulaire coupeur à dents fines, les magazines ont commencé à être entièrement coupés. Le papier découpé est trempé dans l'eau (il doit y avoir beaucoup d'eau) et laissé gonfler pendant 5 à 6 jours. Nous n'avons ajouté aucun antiseptique au papier imbibé.
Figure 4
Après gonflement, de simples morceaux de papier mouillés et d’aspect dégoûtant doivent être transformés en une pâte à papier homogène. Cela se fait commodément dans un seau en plastique à paroi épaisse à l'aide d'un couteau rotatif inséré dans une perceuse. Le seau doit être rempli de papier découpé jusqu'à environ la moitié et ajouter plus d'eau. S'il n'y a pas assez d'eau, la procédure sera extrêmement longue et inefficace.
Au début, un couteau issu d'un vieux moulin à café, vissé sur une longue tige, servait de couteau ; La tige étant plutôt fine, on y plaçait un morceau de tube d'un diamètre approprié ; il servait de roulement et était tenu à la main pendant le fonctionnement. Pour une telle utilisation, la lame du moulin à café s'est avérée plutôt faible ; ses surfaces coupantes avaient constamment tendance à se tordre. Un couteau plus massif a été fabriqué à son image : une plaque d'acier de 100 mm de long a été soudée à une tige de 8 mm dont les bords ont été pliés vers le haut et le tranchant a été affûté. Vous pouvez essayer d'utiliser un mélangeur de construction en affûtant les bords des pétales en spirale.
Le couteau est abaissé dans le seau, la perceuse est allumée et le papier est haché jusqu'à ce que la masse dans le seau commence à ressembler à de la purée. La masse finie doit être bien pressée, l'opération a été effectuée très simplement - la masse a été ramassée à la main et pressée en une poignée (autant qu'elle était suffisamment forte), après quoi elle a été stockée dans un autre récipient. Bien sûr, le travail était accompagné de l'idée de mécanisation : une sorte de presse, mais l'idée n'a pas été réfléchie - la masse s'est rapidement épuisée.
Immédiatement avant le moulage de la corne, de la colle PVA est introduite dans la pâte à papier, à raison d'environ 12 à 20 % du volume de la pâte à papier. Nous avons utilisé environ 1,2 litre de colle.
Figure 5
La pâte à papier additionnée de colle est soigneusement mélangée à l'aide d'un agitateur inséré dans une perceuse. Après avoir pressé un morceau de pâte à papier dans votre main, vos doigts doivent rester légèrement collants. Après séchage, le papier mâché rétrécit d'environ 5 à 10 %, cela doit être pris en compte lors du choix de tous dimensions extérieures et l'épaisseur des parois des cornes.
Moulure en corne
Avant de pouvoir commencer à mouler le cornet, vous devez réaliser trois pièces supplémentaires et préparer la bride.
Tout d’abord, nous devons créer un autre gabarit ; son objectif principal est de garantir l’épaisseur spécifiée des parois de la corne. Il n’existe aucune exigence particulière quant à son exactitude, ni même quant à sa forme. Son apparence et son installation sont illustrés à la figure 6.
Figure 6
L'épaisseur des parois de la corne n'est pas supposée être la même : dans la zone de la bouche, l'épaisseur de la paroi est de 15 mm et augmente progressivement vers la gorge de la corne jusqu'à 30 mm. L'augmentation de l'épaisseur de la paroi est dictée par le fait qu'il y a des pièces encastrées dans la partie supérieure et qu'une plus grande résistance mécanique est requise dans la zone de fixation de la bride.
Deuxièmement, il est nécessaire de réaliser deux revêtements - supérieur et inférieur (Fig. 7.) Le revêtement supérieur est découpé dans un morceau de panneau de particules et vissé à la bride avec des vis. Avec sa partie centrale, il repose contre le support et empêche le rebord de descendre lors du séchage du papier mâché.
Figure 7
La garniture inférieure est découpée dans du contreplaqué de 10 mm et est un carré avec un trou découpé au centre égal au diamètre maximum calculé de l'embouchure de la corne. Son objectif principal est de plaquer le bord inférieur de la corne contre le modèle et d'éviter qu'il ne remonte pendant le processus de séchage.
La préparation de la bride consiste à y visser (de préférence avec de la colle) des morceaux de tiges filetées de 4mm (pièces achetées) et à les plier pour qu'elles soient approximativement parallèles à la génératrice du cornet.
Les fils ont été coupés directement dans le contreplaqué avec un taraud mécanique, les broches ont été pliées à la main. Après cela, vous pouvez commencer à façonner la corne. Nous avons sculpté la corne à quatre mains, l'ensemble du processus a pris environ vingt minutes. La pâte à papier avec la colle introduite est aplatie dans le creux de la main et la surface du modèle est recouverte de ces gâteaux. La masse appliquée sur le modèle est soigneusement nivelée et compactée avec la paume des mains. Après avoir appliqué la première couche de 10 millimètres d'épaisseur, une bride est posée sur le col du modèle et un gabarit est installé. Les épingles sont liées plusieurs fois en cercle avec du fil d'acier doux et la formation de la corne se poursuit. L'épaisseur de la masse appliquée est contrôlée par un gabarit. Aux dernières étapes du formage, la pâte à papier était roulée avec un petit rouleau en caoutchouc. Une fois le moulage terminé, le gabarit est retiré et la garniture supérieure est vissée, puis la garniture inférieure est posée sur le dessus, qui est plaquée contre la surface de la corne. Nous avons utilisé des pinces, qui se sont avérées peu pratiques, car en raison du retrait lors du séchage, elles doivent être serrées. Il serait probablement plus pratique de mettre un poids sur le coussin, par exemple quatre briques dans les coins.
Il y a une longue interruption du travail ; la corne ne peut être touchée que lorsqu'elle est complètement sèche. Notre enceinte a mis presque un mois à sécher. Ce temps peut être bien utilisé pour réfléchir à la qualité de tout ce qui va (ou devrait) sonner.
Retrait du klaxon du modèle
Et maintenant, le moment tant attendu et passionnant est arrivé. La corne est sèche et peut être retirée. Au début, de timides tentatives ont été faites pour retirer la corne à la main - la corne était restée morte et n'a même pas bougé. Taper légèrement sur le klaxon avec un maillet n'a pas non plus donné de résultats et de l'artillerie lourde a été utilisée. Un gros extracteur a été apporté du garage, ses pattes ont été placées derrière la bride et le boulon a été appuyé contre la crémaillère (Fig. 8). En retenant leur souffle, ils ont commencé à tirer, en tapant sur la corne avec un maillet, et à mesure que la vis était serrée, nos visages s'étiraient. L’orateur était aussi immobile qu’un rocher. Comme nous n’avions rien à perdre, nous avons décidé d’attendre que quelque chose se brise. Il n'a fallu que quelques tours de vis supplémentaires et le klaxon a sauté du modèle, notre joie n'avait pas de limites.
Figure 8
Naturellement, nous nous sommes précipités pour voir ce qui s’était passé.
La surface intérieure de la corne était pratiquement sans défauts et reproduisait exactement la forme du modèle ; le modèle lui-même a subi des dommages mineurs - les cornes au niveau de la gorge ont été arrachées. petites zones peintures avec une couche supérieure de mastic. En général, ça va ; après des réparations mineures, le modèle pourrait être réutilisé.
Le klaxon s'est avéré léger et mécaniquement solide. À quoi ressemble la corne avant le traitement final
dans la figure 9.
Figure 9
Finition de la surface du klaxon
L'attention principale a été portée au traitement et à la finition surface intérieure corne, puisque la corne était fabriquée exclusivement à des fins expérimentales, la surface extérieure était simplement peinte sans aucun traitement.
Étape – 1 : traitement mécanique.
Tout d'abord, les bords de l'embouchure de la corne sont traités mécaniquement, les grosses irrégularités sont coupées couteau bien aiguisé, la finition finale de la forme du bord est réalisée avec du papier de verre grossier.
Étape – 2 : protection contre l’humidité.
Après cela, il faut protéger la corne de l'humidité ; le papier mâché est très hygroscopique. Pour ce faire, la surface de la corne est imprégnée de vernis à l'huile. Avant l'imprégnation, la surface intérieure de la corne est légèrement poncée avec du papier de verre grossier (grain 10) pour éliminer le film adhésif. Le vernis est dilué avec un solvant approprié (environ 20 % du volume du vernis est ajouté) et chauffé au bain-marie. L'imprégnation est réalisée jusqu'à ce que le vernis cesse d'être absorbé (la surface intérieure absorbe beaucoup plus fortement le vernis que la surface extérieure). Lorsque nous avons imprégné la corne, elle a absorbé complètement 400 grammes de vernis sans laisser de trace ; peut-être qu'il en aurait été davantage, mais le vernis était épuisé.
Étape – 3 : début du traitement de la surface intérieure.
Pour éliminer les défauts mineurs de la surface intérieure, celle-ci est entièrement remplie de mastic acrylique de départ. Le mastic est réalisé avec une raclette ; au niveau de la gorge du cornet, il n'y a pas assez d'espace pour utiliser une raclette et la courbure est ici trop grande la surface du longeron est recouverte d'un petit morceau de caoutchouc dur ; . Pour fabriquer une mini-raclette, on utilise du caoutchouc dur de 3 à 4 mm d'épaisseur, le bord de travail est formé par meulage sur une pierre émeri.
Pour poncer la surface de la corne, il est pratique d'utiliser plusieurs morceaux de caoutchouc épais. différentes largeurs, enveloppé dans du papier de verre, la largeur de la pièce est choisie de manière à ce que toute la surface du papier de verre soit adjacente à la corne (trois morceaux suffisent - pour la bouche, la partie médiane et la gorge).
Étape – 4 : finition surface intérieure.
La surface de la corne est peinte avec une couche de peinture évolutive (il est conseillé d'utiliser de la peinture dans des tons gris neutres) après ponçage, les défauts identifiés sont comblés avec du mastic acrylique de finition. La surface d'origine du cornet étant de qualité suffisamment élevée, il s'est avéré suffisant d'effectuer cette opération une seule fois.
Étape – 5 : peinture finale.
Si vous êtes satisfait de la qualité de la surface intérieure de la corne, la peinture finale est réalisée avec de l'émail synthétique en deux couches.
Le cornet fini est représenté sur les figures 10 et 11. La surface est d'assez bonne qualité. Ceux qui ne connaissaient pas la technologie de fabrication supposaient que la corne était extrudée ou
moulé en plastique.
Figure 10
Figure 11
Compte rendu
Il est maintenant temps d'évoquer les erreurs que nous avons commises lors de la fabrication du klaxon et de vous avertir.
Il n'y a eu aucune plainte particulière concernant le modèle ; son seul inconvénient était son poids. Bien que nous ayons utilisé de l'argile expansée, la structure entière pesait 30 kilogrammes, même si ce n'est pas beaucoup, compte tenu du poids. taille significative modèle, un tel poids créait certains inconvénients lors du transport. Apparemment, la partie centrale du modèle devrait être remplie de plus de matériau léger, comme la mousse de polystyrène, et appliquez dessus du gypse de 20x30 mm d'épaisseur. Cette épaisseur de gypse assurera une résistance mécanique suffisante.
La question du collier s’est avérée plus désagréable. Nous avons sous-estimé l'ampleur du retrait de la pâte à papier ; en conséquence, lorsque la masse séchait par endroits, le bord de la corne passait sous l'épaule et la possibilité de la presser contre la surface du modèle disparaissait (le coussinet inférieur s'allonger sur l'épaule).
Cela a entraîné des écarts mineurs dans le profil de l'embouchure de la corne, cela n'est pas visible sur les photos, les écarts sont trop faibles, mais il existe un précédent. Par conséquent, nous recommandons de ne pas utiliser de perle du tout au bord de la bouche, ou de la rendre beaucoup plus petite en hauteur.
Un autre problème que nous avons rencontré était la bride. En raison du retrait du papier mâché, un espace d'environ 5 mm s'est formé entre le corps de la corne et la bride. Nos calculs selon lesquels les épingles traversant la pâte à papier la maintiendraient en place se sont révélés erronés. Le problème de l'élimination de l'écart a été résolu simplement, il a été comblé mastic acrylique, dont l'excédent, après séchage, a été coupé avec un couteau bien aiguisé. Peut-être que la solution à ce problème serait d'éviter d'installer la bride au stade du moulage du pavillon. Dans ce cas, le tampon supérieur peut être utilisé comme gabarit qui définit l’orientation des goujons. Après séchage, la corne est parée
à la hauteur requise et la bride est installée, mais dans ce cas, des difficultés peuvent survenir avec l'installation correcte de la bride. Alors, peut-être vaut-il mieux tout laisser tel quel, d'autant plus que l'écart est facile à éliminer.
Conclusion
Les avantages incontestables de la technologie décrite sont la possibilité d'obtenir plusieurs cornes identiques avec une précision de génératrice suffisamment élevée et le faible coût des matériaux utilisés, mais le principal inconvénient est la forte intensité de travail.
Dans l'article, nous avons essayé de décrire toutes les étapes du travail de manière aussi détaillée que possible, dans l'espoir qu'une personne qui sait (et veut) travailler de ses mains, mais n'a pas suffisamment d'expérience, puisse aller jusqu'au bout. avec un minimum d'erreurs. Des solutions déjà éprouvées vous sont présentées. En fait, tout ne s’est pas bien passé et certaines choses ont dû être refaites à plusieurs reprises.
En résumé, nous pouvons dire que nous avons été satisfaits de la façon dont apparence du klaxon fabriqué et les résultats de ses tests acoustiques.
BONNE CHANCE À TOI!
Evgeny Karpov, Alexandre Naidenko
Adresse d'administration du site :
VOUS NE TROUVEZ PAS CE QUE VOUS CHERCHEZ ? GOOGLE:
Un de mes petits rêves est devenu réalité : j'ai reçu un gramophone. Et même s’il est tout petit, personne n’a quelque chose de pareil. Il est fabriqué à la main. Il y a donc un nouvel ajout à ma collection d’objets miniatures faits à la main.
De nos jours, le gramophone ne se trouve que dans les musées, les antiquaires et les collectionneurs. Si quelqu’un le garde à la maison, c’est probablement comme élément décoratif et non comme élément décoratif. Et il y a environ 100 ans, il y a eu un véritable boom du gramophone qui a balayé de nombreux pays. Tout le monde voulait posséder ce miracle de la technologie.
Je vous suggère de créer votre propre gramophone miniature. Je pense que les amateurs de miniatures de maisons de poupées trouveront la master class utile.
Commençons. Par tradition, j'ai choisi le prototype (à gauche). Cela s'est avéré assez similaire (à droite).
Pour le travail dont j'avais besoin : du papier épais, une serviette, du fil (10-12 mm d'épaisseur), de la colle PVA, de la super colle transparente, un bâton de colle de bureau pour papier, peinture acrylique Couleurs variées.
Master class sur la création d'un gramophone de marionnettes en papier
1 La partie la plus visible d'un gramophone est l'amplificateur de son, on l'appelle également tuyau acoustique ou cornet. Je l'ai fait en papier. Je ne peux pas vous dire exactement l’épaisseur du papier, mais il est nettement plus épais que le papier ordinaire. papier de bureau avec une densité de 80 g/m2. J'ai découpé les pièces selon le schéma à raison de 10 pièces.

2 À l'aide d'un bâton de colle, j'ai collé toutes les pièces ensemble. Ce n'est pas aussi simple qu'il y paraît. Il a fallu BEAUCOUP d’efforts pour obtenir des courbes douces. Le résultat est la partie supérieure volumineuse du tuyau
3 Afin de réduire la partie de la corne, j'ai tordu un cône étroit et dense (4-5 couches de papier). J'ai aligné le bord et je l'ai courbé, en imitant la partie incurvée inférieure de l'amplificateur de son. Ensuite, j'ai relié les parties supérieure et inférieure avec de la colle.
4 Pour fixer le tuyau au corps, j'ai utilisé un petit morceau de fil avec une boucle à une extrémité. J'ai inséré la corne finie dans une boucle et je l'ai collée avec de la super colle.

5 À l'aide de colle PVA et de morceaux de serviette, j'ai augmenté la densité du tuyau tout en masquant les points de collage.
7 Comme mon gramophone était destiné à être un objet antique, je l'ai partiellement recouvert de peinture bleu-vert pour un effet vieillissant.
8 Étape finale peinture. J'ai pris de la peinture acrylique décorative couleur vieux cuivre. J'ai peint la corne avec un pinceau sec. Pour renforcer l'effet, j'ai essuyé certains endroits avec une serviette afin que la peinture bleue puisse transparaître. Le résultat est une patine cuivrée presque réelle.

9 Maintenant, prenons soin du corps. Je l'ai découpé dans le même papier que la corne. (schéma ci-dessus). Le résultat était une boîte de 45 sur 45 mm avec une hauteur de 15 mm.
10 De plus, j'ai découpé plusieurs carrés de 47 et 49 mm de côté, que j'ai collés en haut et en bas de la boîte. Et la touche finale : 4 petits carrés de 5 sur 5 mm en guise de pattes.
11 Sur la partie avant de la boîte se trouve petit décor. Pour obtenir une similitude avec l'original, je propose le schéma d'éléments suivant. Même si vous n’êtes pas obligé de faire la décoration.
12 La prochaine étape est l'amorçage. J'utilise habituellement du blanc mat à ces fins. peinture au plafond. Mais la peinture acrylique blanche ordinaire fera également l’affaire.

13 Pour réaliser une imitation de bois sur papier, après séchage de l'apprêt, j'ai recouvert la boîte de peinture rouge. Ensuite, j'avais besoin de peinture acrylique marron et d'un gros pinceau sec. Elle essuya l'excédent de peinture sur une serviette et, à l'aide d'un pinceau presque propre, le déplaçant dans une seule direction, l'appliqua sur la boîte. Cela s’est avéré assez similaire à la structure d’un arbre.
14 J'ai réalisé le mécanisme qui déclenche le système de ressort à partir de fil. En trempant une extrémité du fil dans du vernis à ongles, vous pouvez obtenir une poignée soignée.
15 Pour faire un trou pour le manche, vous pouvez utiliser une aiguille épaisse, un poinçon, ou comme moi, utiliser une perceuse.
16 Le gramophone original a une membrane avec une aiguille fixée sur le côté étroit du tuyau. La membrane de mon gramophone était un petit engrenage provenant d'un mécanisme d'horlogerie.

17 Maintenant, le compte rendu. Ici, tout est aussi simple que décortiquer des poires. Tout ce dont vous avez besoin est une imprimante couleur. J'ai collé la plaque imprimée sur une couche de papier plus épais.
18 Il ne reste plus qu'à tout relier. Pour que ce soit clair, j’ai esquissé les détails mentionnés dans différents points de la master class.
