Méthode de récupération de chaleur en profondeur des gaz de combustion. Récupération de chaleur des fumées. Recyclage en profondeur pour les systèmes de chauffage
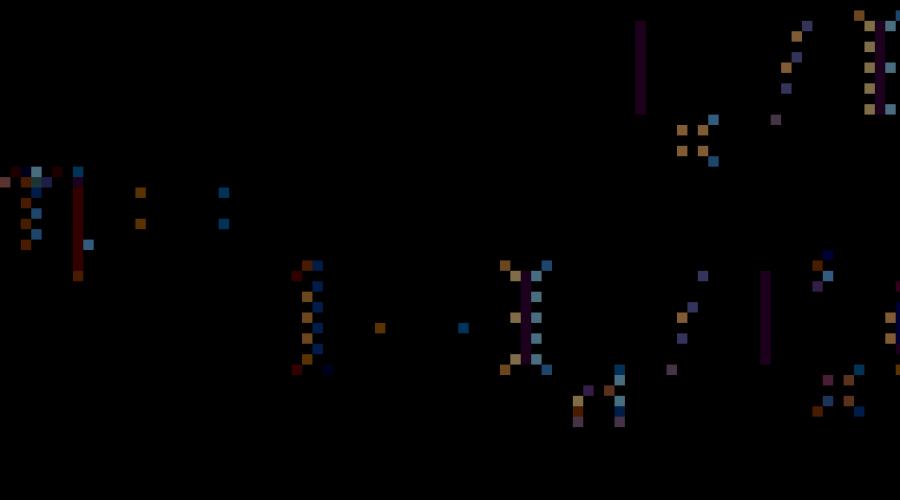
Lire aussi
Description:
Bryansk Heat Networks, en collaboration avec l'institut de conception LLC VKTIstroydormash-Proekt, a développé, fabriqué et mis en œuvre des installations de récupération de chaleur des gaz de combustion (UUTG) provenant de chaudières à eau chaude dans deux chaufferies de Briansk.
Installation de récupération de chaleur des fumées
N.F. Sviridov, R. N. Sviridov, Réseaux thermiques de Briansk,
I. N. Ivukov, B.L. Turk, LLC "Projet VKTIstroydormash"
Bryansk Heat Networks, en collaboration avec l'institut de conception VKTIstroydormash-Proekt LLC, a développé, fabriqué et mis en œuvre des installations de récupération de chaleur des gaz de combustion (UHTG) provenant des chaudières à eau chaude de deux chaufferies de Briansk.
À la suite de cette mise en œuvre, les résultats suivants ont été obtenus :
Les investissements en capital supplémentaires par 1 Gcal/h de chaleur reçue sont plus de 2 fois inférieurs à ceux de la construction d'une nouvelle chaufferie et sont amortis en environ 0,6 an ;
Étant donné que l'équipement utilisé est extrêmement facile à entretenir et utilise un caloporteur gratuit, c'est-à-dire des gaz de combustion (FG) préalablement émis dans l'atmosphère, le coût de 1 Gcal de chaleur est 8 à 10 fois inférieur au coût de la chaleur générée. par les chaufferies ;
Le rendement des chaudières a été augmenté de 10 %.
Ainsi, tous les coûts en mars 2002 pour la mise en œuvre du premier UTG d'une capacité de 1 Gcal de chaleur par heure s'élevaient à 830 000 roubles, et les économies attendues par an seront de 1,5 million de roubles.
Des indicateurs techniques et économiques aussi élevés sont compréhensibles.
Il existe une opinion selon laquelle le rendement des meilleures chaudières domestiques d'une puissance thermique de 0,5 MW et plus atteint 93 %. En réalité, il ne dépasse pas 83 % et voici pourquoi.
Il existe des pouvoirs calorifiques de plus en plus élevés pour la combustion du combustible. Le pouvoir calorifique inférieur est inférieur au pouvoir calorifique supérieur de la quantité de chaleur dépensée pour l'évaporation de l'eau formée lors de la combustion du carburant, ainsi que de l'humidité qu'il contient. Un exemple pour le combustible le moins cher - le gaz naturel : les MD formés lors de sa combustion contiennent de la vapeur d'eau, occupant jusqu'à 19 % de leur volume ; la chaleur de combustion supérieure dépasse la chaleur inférieure d'environ 10 %.
Pour améliorer les performances des cheminées à travers lesquelles les générateurs diesel sont émis dans l'atmosphère, il est nécessaire que la vapeur d'eau présente dans le générateur diesel ne commence pas à se condenser dans les cheminées aux températures ambiantes les plus basses.
Les projets UUTG ont relancé et amélioré des solutions techniques longtemps oubliées visant à recycler la chaleur des générateurs diesel.
UUTG contient des échangeurs de chaleur à contacts et à plaques avec deux circuits indépendants d'eau en circulation et d'eau consommable.
La conception et le fonctionnement de l'UTG ressortent clairement du schéma présenté sur la figure et de la description de ses positions.
Dans un échangeur de chaleur à contact, le DG et l'eau en circulation pulvérisée se déplacent à contre-courant vertical, c'est-à-dire que le DG et l'eau sont en contact direct l'un avec l'autre. Pour maintenir une pulvérisation uniforme de l'eau en circulation, des buses et une buse spéciale en céramique sont utilisées.
L'eau chauffée en circulation, pompée dans son circuit d'eau par une pompe indépendante, transfère la chaleur acquise dans l'échangeur thermique à contact vers l'eau d'alimentation dans l'échangeur thermique à plaques.
Pour le refroidissement requis de l'eau en circulation, seule l'eau froide du robinet doit être utilisée, qui, après chauffage dans l'UTG, est portée à la température requise dans les chaudières des chaufferies existantes et est ensuite utilisée pour l'alimentation en eau chaude des logements.
Dans un échangeur de chaleur à contact, les générateurs diesel refroidis passent en outre à travers un éliminateur de gouttelettes et, ayant finalement perdu plus de 70 % de l'humidité sous forme de condensat de vapeur d'eau, sont connectés à une partie des générateurs diesel chauds (10 à 20 % du volume des générateurs diesel sortant de la chaudière), dirigé directement de la chaudière vers la cheminée, formant ainsi un mélange de générateurs diesel à faible teneur en humidité et avec une température suffisante pour le passage de la cheminée sans condensation de la vapeur d'eau restante .
Le volume d'eau en circulation augmente continuellement en raison de la condensation de la vapeur d'eau présente dans le générateur diesel. L'excédent qui en résulte est automatiquement évacué par une vanne à entraînement électromécanique et peut être utilisé comme eau supplémentaire dans le système de chauffage de la chaufferie. La consommation spécifique d'eau évacuée pour 1 Gcal de chaleur récupérée est d'environ 1,2 tonne. L'évacuation des condensats est contrôlée par les niveaumètres B et H.
Le procédé et l'équipement décrits pour la récupération de chaleur des générateurs diesel sont capables de fonctionner avec des produits de combustion de carburant sans poussière ayant une température maximale illimitée. Dans ce cas, plus la température des gaz de combustion est élevée, plus la température à laquelle l'eau d'alimentation sera chauffée sera élevée. De plus, dans ce cas, il est possible d'utiliser partiellement de l'eau recyclée pour chauffer l'eau de chauffage. Étant donné que l'échangeur thermique à contact fonctionne simultanément comme un dépoussiéreur humide, il est possible d'utiliser pratiquement la chaleur des générateurs diesel poussiéreux en purifiant l'eau en circulation de la poussière à l'aide de méthodes connues avant de l'introduire dans l'échangeur thermique à plaques. Il est possible de neutraliser l'eau en circulation contaminée par des composés chimiques. Par conséquent, l'UTG décrit peut être utilisé pour travailler avec des DG impliqués dans des processus technologiques lors de la fusion (par exemple, fours à sole ouverte, fours de fusion du verre), lors de la calcination (par exemple, briques, céramiques), lors du chauffage (lingots avant laminage) , etc.
Malheureusement, en Russie, il n’existe aucune mesure incitative pour encourager les économies d’énergie.
Dessin Schéma d'une installation de récupération de chaleur des fumées (UHTG) 1 - échangeur de chaleur à contact ; 2 - vanne à entraînement électromécanique pour l'évacuation automatique de l'excès d'eau de circulation formé lors de la condensation de la vapeur d'eau du générateur diesel ; 3 - réservoir de stockage pour faire circuler l'eau chauffée par la chaleur récupérée du générateur diesel ; 4 - DG s'étendant depuis la chaudière ; 5 - une partie du générateur diesel destinée à utiliser leur chaleur ; 6 - cheminée ; 7 - une partie du générateur diesel, qui continue de se déplacer le long du porc existant dans la cheminée (6) ; 8 - vanne qui régule le débit d'une partie du générateur diesel (5) ; 9 - vanne qui régule le débit d'une partie du générateur diesel (7) ; 10 - partie refroidie et séchée du générateur diesel sortant de l'échangeur thermique à contact (1) ; 11 - mélange de générateurs diesel (7 et 10), ayant une différence de température entre le générateur diesel et son point de rosée égale à 15-20°C ; 12 - pulvérisateur d'eau à circulation ; 13 - buse spéciale à surface développée; 14 - décarbonateur, dans lequel le dioxyde de carbone préalablement dissous en est éliminé en soufflant de l'air dans l'eau en circulation ; 15 - air de purge ; 16 - attrape-gouttes ; 17 - système d'alimentation en eau froide ; 18 - eau en circulation chauffée par chaleur récupérée ; 19 - pompe pour pomper l'eau en circulation ; 20 - échangeur de chaleur à plaques pour transférer la chaleur récupérée de l'eau en circulation vers l'eau consommable ; 21 - eau en circulation refroidie dirigée vers le pulvérisateur (12) et évacuée son excès à travers une vanne à entraînement électromécanique (2) ; 22 - eau consommable, chauffée par la chaleur récupérée du générateur diesel. B et H – capteurs pour les niveaux supérieur et inférieur d'eau en circulation dans le réservoir de stockage (3) ; |
Tableau 1 Indicateurs calculés de l'un des UTG mis en œuvre |
|||||||||||||||||||||||||||||||||||||||||||||||||||||||||||
|
Récupération de chaleur des fumées
Les fumées sortant de l'espace de travail des fours ont une température très élevée et emportent donc une quantité importante de chaleur. Dans les fours à foyer ouvert, par exemple, environ 80 % de la chaleur totale fournie à l'espace de travail est évacuée de l'espace de travail par les gaz de combustion, dans les fours de chauffage, environ 60 %. Depuis l'espace de travail des fours, les fumées emportent avec elles plus de chaleur, plus leur température est élevée et plus le coefficient d'utilisation de la chaleur dans le four est faible. A cet égard, il convient d'assurer la récupération de la chaleur des fumées d'échappement, ce qui peut se faire en principe par deux méthodes : avec retour d'une partie de la chaleur prélevée sur les fumées vers le four et sans restituer cette chaleur au four. Pour mettre en œuvre la première méthode, il est nécessaire de transférer la chaleur extraite des fumées vers le gaz et l'air (ou uniquement l'air) entrant dans le four. Pour atteindre cet objectif, les échangeurs de chaleur de types récupérateurs et régénératifs sont largement utilisés, dont l'utilisation permet d'augmenter le rendement du four, d'augmenter la température de combustion et d'économiser du carburant. Avec la deuxième méthode de récupération, la chaleur des fumées d'échappement est utilisée dans les chaufferies thermiques et les unités de turbine, ce qui permet de réaliser d'importantes économies de carburant.
Dans certains cas, les deux méthodes décrites de récupération de chaleur perdue sont utilisées simultanément. Ceci est effectué lorsque la température des fumées après les échangeurs de chaleur à régénération ou à récupération reste suffisamment élevée et qu'une récupération ultérieure de la chaleur dans les centrales thermiques est recommandée. Par exemple, dans les fours à foyer ouvert, la température des fumées après les régénérateurs est de 750 à 800 °C, elles sont donc réutilisées dans des chaudières à chaleur résiduelle.
Examinons plus en détail la problématique du recyclage de la chaleur des fumées d'échappement avec le retour d'une partie de leur chaleur au four.
Il convient de noter tout d'abord qu'une unité de chaleur extraite des fumées et introduite dans le four par air ou gaz (une unité de chaleur physique) s'avère bien plus précieuse qu'une unité de chaleur obtenue dans le four. à la suite de la combustion d'un combustible (une unité de chaleur chimique), puisque la chaleur de l'air chauffé (gaz) n'entraîne pas de perte de chaleur avec les fumées. La valeur d'une unité de chaleur sensible est d'autant plus grande que le facteur d'utilisation du combustible est faible et que la température des gaz de combustion est élevée.
Pour un fonctionnement normal du four, la quantité de chaleur requise doit être fournie à l'espace de travail toutes les heures. Cette quantité de chaleur comprend non seulement la chaleur du combustible, mais également la chaleur de l'air ou du gaz chauffé, c'est-à-dire
Il est clair qu'avec = const une augmentation diminuera. En d'autres termes, l'utilisation de la chaleur des fumées permet de réaliser des économies de combustible, qui dépendent du degré de récupération de chaleur des fumées.
où est l'enthalpie de l'air chauffé et des gaz de combustion s'échappant de l'espace de travail, en kW ou en kJ/période, respectivement.
Le degré de récupération de chaleur peut également être appelé efficacité. récupérateur (régénérateur), %
Connaissant le degré de récupération de chaleur, vous pouvez déterminer l'économie de carburant à l'aide de l'expression suivante :
où I"d, Id sont respectivement l'enthalpie des fumées à la température de combustion et celles en sortie du four.
La réduction de la consommation de carburant grâce à l'utilisation de la chaleur des gaz de combustion fournit généralement un effet économique important et constitue l'un des moyens de réduire le coût du chauffage du métal dans les fours industriels.
En plus d'économiser du carburant, l'utilisation du chauffage à l'air (gaz) s'accompagne d'une augmentation de la température de combustion calorimétrique, qui peut être le principal objectif de la récupération lors du chauffage de fours avec du combustible à faible pouvoir calorifique.
Une augmentation de at entraîne une augmentation de la température de combustion. S'il est nécessaire de garantir une certaine valeur, alors une augmentation de la température de chauffage de l'air (gaz) entraîne une diminution de la valeur, c'est-à-dire une diminution de la part de gaz à pouvoir calorifique élevé dans le mélange carburé.
Étant donné que la récupération de chaleur permet d'importantes économies de combustible, il est conseillé de s'efforcer d'atteindre le degré d'utilisation le plus élevé possible et économiquement justifié. Cependant, il faut immédiatement noter que le recyclage ne peut pas être complet, c'est-à-dire toujours. Cela s'explique par le fait que l'augmentation de la surface de chauffe n'est rationnelle que jusqu'à certaines limites, après quoi elle entraîne déjà un gain très insignifiant d'économie de chaleur.
Actes d'Instorf 11 (64)
CDU 622.73.002.5
Gorfin O.S. Gorfin O.S.
Gorfin Oleg Semenovich, Ph.D., prof. Département des machines et équipements pour la tourbe de l'Université technique d'État de Tver (TvGTU). Tver, Academiccheskaya, 12. [email protégé] Gorfin Oleg S., PhD, professeur à la chaire des machines et équipements pour la tourbe de l'Université technique d'État de Tver. Tver, Académiquecheskaya, 12
Ziouzine B.F. Ziouzine B.F.
Zyuzin Boris Fedorovich, docteur en sciences techniques, professeur, chef. Département des machines et équipements de tourbe TvSTU [email protégé] Zyuzin Boris F., Dr. Sc., professeur, chef de la chaire des machines et équipements pour la tourbe de l'Université technique d'État de Tver
Mikhaïlov A.V. Mikhaïlov A.V.
Mikhailov Alexander Viktorovich, docteur en sciences techniques, professeur du département de génie mécanique, Université nationale des ressources minérales "Mines", Saint-Pétersbourg, perspective Leninsky, 55, bldg. 1, app. 635. [email protégé] Mikhaïlov Alexandre V., Dr. Sc., professeur à la chaire de construction de machines de l'Université nationale des mines de St. Saint-Pétersbourg, Leninsky pr., 55, bâtiment 1, Apt. 635
L'APPAREIL POUR LA PROFONDEUR
POUR UNE UTILISATION PROFONDE DE LA CHALEUR
RECYCLAGE THERMIQUE DES GAZ DE COMBUSTION
FUMÉES DE TYPE SUPERFICIEL
Annotation. L'article traite de la conception d'un échangeur de chaleur, dans lequel la méthode de transfert de l'énergie thermique récupérée du liquide de refroidissement vers un environnement récepteur de chaleur a été modifiée, permettant d'utiliser la chaleur de vaporisation de l'humidité du combustible lors du refroidissement en profondeur des gaz de combustion. et l'utiliser entièrement pour chauffer l'eau de refroidissement, dirigée sans traitement supplémentaire vers les besoins du cycle de la turbine à vapeur. La conception permet, lors du processus de récupération de chaleur, de purifier les gaz de combustion des acides sulfurique et sulfureux et d'utiliser le condensat purifié comme eau chaude. Abstrait. L'article décrit la conception d'un échangeur de chaleur, dans lequel une nouvelle méthode est utilisée pour transmettre la chaleur recyclée du caloporteur au récepteur de chaleur. La construction permet d'utiliser la chaleur de vaporisation de l'humidité du combustible lors du refroidissement en profondeur des gaz de combustion et de l'utiliser pleinement pour chauffer l'eau de refroidissement allouée sans traitement ultérieur aux besoins du cycle de la turbine à vapeur. La conception permet de purifier les gaz de combustion du soufre et de l'acide sulfureux et d'utiliser le condensat purifié comme eau chaude.
Mots clés : cogénération ; installations de chaudières; échangeur de chaleur superficiel; refroidissement en profondeur des gaz de combustion ; récupération de la chaleur de vaporisation de l'humidité du carburant. Mots clés : Centrale de production combinée de chaleur et d'électricité ; installations de chaudières; chauffage de type superficiel; refroidissement en profondeur des gaz de combustion ; utilisation de la chaleur de la vapeur, formation de l'humidité du combustible.
Actes d'Instorf 11 (64)
Dans les chaufferies des centrales thermiques, l'énergie de vaporisation de l'humidité et du combustible ainsi que les gaz de combustion sont libérés dans l'atmosphère.
Dans les chaufferies gazéifiées, les déperditions thermiques des fumées d'échappement peuvent atteindre 25 %. Dans les chaufferies fonctionnant au combustible solide, les pertes de chaleur sont encore plus élevées.
Pour les besoins technologiques du TBZ, de la tourbe broyée avec une teneur en humidité allant jusqu'à 50 % est brûlée dans les chaufferies. Cela signifie que la moitié de la masse du carburant est constituée d'eau qui, lors de la combustion, se transforme en vapeur et que les pertes d'énergie dues à la vaporisation de l'humidité du carburant atteignent 50 %.
La réduction des pertes d'énergie thermique ne consiste pas seulement à économiser du carburant, mais également à réduire les émissions nocives dans l'atmosphère.
Il est possible de réduire les pertes d'énergie thermique en utilisant des échangeurs de chaleur de différentes conceptions.
Les échangeurs de chaleur à condensation, dans lesquels les gaz de combustion sont refroidis en dessous du point de rosée, permettent d'utiliser la chaleur latente de condensation de la vapeur d'eau et de l'humidité du combustible.
Les plus répandus sont les échangeurs de chaleur à contact et à surface. Les échangeurs de chaleur à contact sont largement utilisés dans l'industrie et l'énergie en raison de leur simplicité de conception, de leur faible consommation de métal et de leur forte intensité d'échange thermique (épurateurs, tours de refroidissement). Mais ils présentent un inconvénient majeur : l'eau de refroidissement est contaminée en raison de son contact avec les produits de combustion - les fumées.
À cet égard, les échangeurs de chaleur surfaciques qui n'ont pas de contact direct entre les produits de combustion et le liquide de refroidissement sont plus intéressants, dont l'inconvénient est la température de chauffage relativement basse, égale à la température du thermomètre humide (50... 60°C).
Les avantages et les inconvénients des échangeurs de chaleur existants sont largement traités dans la littérature spécialisée.
L'efficacité des échangeurs de chaleur à surface peut être considérablement augmentée en modifiant la méthode d'échange de chaleur entre le milieu qui dégage de la chaleur et celui qui la reçoit, comme c'est le cas dans la conception proposée de l'échangeur de chaleur.
Le schéma d'un échangeur de chaleur pour une utilisation approfondie de la chaleur des gaz de combustion est illustré
sur l'image. Le corps 1 de l'échangeur de chaleur repose sur la base 2. Dans la partie médiane du corps se trouve un réservoir isolé 3 en forme de prisme, rempli d'eau courante pré-purifiée. L'eau entre par le haut par le conduit 4 et est évacuée au fond du boîtier 1 par la pompe 5 par la porte 6.
Sur les deux côtés d'extrémité du réservoir 3 se trouvent des chemises 7 et 8, isolées de la partie médiane, dont les cavités à travers le volume du réservoir 3 sont reliées entre elles par des rangées de canalisations parallèles horizontales formant des faisceaux de canalisations 9 en quels gaz se déplacent dans une direction. La chemise 7 est divisée en sections : inférieure et supérieure simple 10 (hauteur h) et les 11 restantes - doubles (hauteur 2h) ; la chemise 8 ne comporte que des doubles pans 11. Le simple pan inférieur 10 de la chemise 7 est relié par un faisceau de tuyaux 9 au bas du double pan 11 de la chemise 8. Ensuite, la partie supérieure de ce double pan 11 de la chemise 8 par un faisceau de tuyaux 9 est relié au bas de la double section suivante 11 de la chemise 7, etc. De manière cohérente, la partie supérieure de la section d'une enveloppe est reliée à la partie inférieure de la section de la deuxième enveloppe, et la partie supérieure de cette section est reliée par un faisceau de tuyaux 9 au bas de la section suivante de la première. chemise, formant ainsi un serpentin de section variable : les faisceaux de tuyaux 9 alternent périodiquement avec les volumes des sections des chemises. Dans la partie inférieure du serpentin se trouve un tuyau 12 d'alimentation en fumées, en partie supérieure se trouve un tuyau 13 pour la sortie des gaz. Les dérivations 12 et 13 sont reliées entre elles par un conduit de dérivation 4, dans lequel est installée une vanne 15, destinée à redistribuer une partie des fumées chaudes contournant l'échangeur de chaleur dans la cheminée (non représentée sur la figure).
Les fumées pénètrent dans l'échangeur de chaleur et sont divisées en deux flux : l'essentiel (environ 80 %) des produits de combustion pénètre dans la section unique inférieure 10 (hauteur h) de la chemise 7 et est envoyé dans les canalisations du faisceau 9. au serpentin de l’échangeur de chaleur. Le reste (environ 20 %) entre dans le conduit de dérivation 14. La redistribution des gaz est effectuée pour augmenter la température des fumées refroidies derrière l'échangeur de chaleur à 60-70°C afin d'éviter une éventuelle condensation de vapeur d'humidité résiduelle du combustible dans le sections de queue du système.
Les gaz de combustion sont amenés à l'échangeur de chaleur par le bas via le tuyau 12 et évacués vers
Actes d'Instorf 11 (64)
Dessin. Schéma de l'échangeur de chaleur (type A - raccordement des tuyaux avec chemises) Figure. Le schéma de l'utilisation de chaleur (le look A - la connexion des tuyaux avec les chemises)
la partie supérieure de l'installation est le tuyau 13. L'eau froide préalablement préparée remplit le réservoir par le haut par le tuyau 4, et est évacuée par la pompe 5 et la vanne 6 situées dans la partie inférieure du boîtier 1. Le contre-courant de l'eau et des fumées augmente l'efficacité de l'échange thermique.
Le mouvement des fumées à travers l'échangeur de chaleur est effectué par un désenfumage technologique de la chaufferie. Pour vaincre la résistance supplémentaire créée par l’échangeur thermique, il est possible d’installer un désenfumage plus puissant. Il convient de garder à l'esprit que la résistance hydraulique supplémentaire est partiellement surmontée en réduisant le volume des produits de combustion dû à la condensation de la vapeur d'eau dans les fumées.
La conception de l'échangeur de chaleur garantit non seulement une utilisation efficace de la chaleur de vaporisation de l'humidité du combustible, mais également l'élimination du condensat résultant du flux de gaz de combustion.
Le volume des sections des chemises 7 et 8 est supérieur au volume des tuyaux qui les relient, donc la vitesse des gaz qui s'y trouvent est réduite.
Les gaz de combustion entrant dans l'échangeur thermique ont une température de 150 à 160 °C. Les acides sulfurique et sulfureux se condensent à une température de 130-140 °C, de sorte que la condensation des acides se produit dans la partie initiale du serpentin. Lorsque la vitesse du flux de gaz dans les parties en expansion de la bobine - les sections de la chemise diminuent et que la densité du condensat d'acides sulfurique et sulfureux à l'état liquide augmente par rapport à la densité à l'état gazeux et à la direction du mouvement du flux de fumées change plusieurs fois (séparation inertielle), le condensat acide précipite et est éliminé des gaz, une partie du condensat de vapeur d'eau, dans le collecteur de condensat acide 16, d'où, lorsque le volet est activé, 17 est évacuées dans les égouts industriels.
La majeure partie du condensat - condensat de vapeur d'eau - est libérée avec une nouvelle diminution de la température des gaz jusqu'à 60-70°C dans la partie supérieure du serpentin et pénètre dans le collecteur de condensat d'humidité 18, d'où il peut être utilisé comme eau chaude sans traitement supplémentaire.
Actes d'Instorf 11 (64)
Les tuyaux des serpentins doivent être constitués d'un matériau anticorrosion ou dotés d'un revêtement anticorrosion interne. Pour éviter la corrosion, toutes les surfaces de l'échangeur de chaleur et des canalisations de raccordement doivent être gommées.
Dans cette conception d'échangeur de chaleur, les gaz de combustion contenant de la vapeur d'humidité du carburant se déplacent à travers les tuyaux du serpentin. Le coefficient de transfert de chaleur dans ce cas ne dépasse pas 10 000 W/(m2 °C), ce qui augmente considérablement l'efficacité du transfert de chaleur. Les tuyaux du serpentin sont situés directement dans le volume du liquide de refroidissement, de sorte que l'échange thermique se produit constamment par contact. Cela permet un refroidissement en profondeur des gaz de combustion jusqu'à une température de 40 à 45 °C, et toute la chaleur récupérée de vaporisation de l'humidité du combustible est transférée à l'eau de refroidissement. L'eau de refroidissement n'entre pas en contact avec les fumées, elle peut donc être utilisée sans traitement supplémentaire dans le cycle de la turbine à vapeur et par les consommateurs d'eau chaude (dans le système d'alimentation en eau chaude, chauffage de l'eau du réseau de retour, besoins technologiques des entreprises, dans les serres et fermes en serre, etc.). C’est le principal avantage de la conception proposée de l’échangeur de chaleur.
L'avantage du dispositif proposé est également que dans l'échangeur de chaleur, le temps de transfert de chaleur de l'environnement des fumées chaudes vers le liquide de refroidissement, et donc sa température, est régulé en modifiant le débit du liquide à l'aide d'une vanne.
Pour vérifier les résultats de l'utilisation d'un échangeur de chaleur, des calculs thermiques et techniques ont été effectués pour une installation de chaudière avec un débit de vapeur de chaudière de 30 tonnes de vapeur/h (température 425 °C, pression 3,8 MPa). 17,2 t/h de tourbe broyée avec une teneur en humidité de 50 % sont brûlées dans le foyer.
La tourbe avec une teneur en humidité de 50 % contient 8,6 t/h d'humidité qui, lorsqu'elle est brûlée, se transforme en gaz de combustion.
Consommation d'air sec (gaz de combustion)
Gfl. g. = a x L x G, ^^ = 1,365 x 3,25 x 17 200 = 76 300 kg de g.g./h,
où L = 3,25 kg sec. g/kg de tourbe - la quantité d'air théoriquement requise pour la combustion ; a =1,365 - coefficient de fuite d'air moyen.
1. Chaleur de récupération des gaz de combustion Enthalpie des gaz de combustion
J = cm x t + 2,5 d, ^zh/kgG. sec gaz,
où ccm est la capacité calorifique des fumées (capacité calorifique du mélange), ^l/kg °K, t est la température des gaz, °K, d est la teneur en humidité des fumées, G. humidité/ kg. d.g.
Capacité thermique du mélange
ссМ = сг + 0,001dcn,
où sg, cn sont respectivement la capacité calorifique du gaz sec (gaz de combustion) et de la vapeur.
1.1. Les fumées à l'entrée de l'échangeur thermique sont à une température de 150 - 160 °C, on prend C. g = 150 °C ; cn = 1,93 - capacité calorifique de la vapeur ; сг = 1,017 - capacité calorifique des fumées sèches à une température de 150 °C ; d150,G/kg. sec d - teneur en humidité à 150 °C.
d150 = GM./Gfl. g. = 8600 /76 300 x 103 =
112,7G/kg. sec G,
où Gvl. = 8600 kg/h - masse d'humidité dans le carburant. scm = 1,017 + 0,001 x 112,7 x 1,93 = 1,2345 ^f/kg.
Enthalpie des fumées J150 = 1,2345 x 150 + 2,5 x 112,7 = 466,9 ^l/kg.
1.2. Fumée à la sortie de l'échangeur thermique à une température de 40 °C
scm = 1,017 + 0,001 x 50 x 1,93 = 1,103 ^f/kg °C.
d40 = 50 G/kg g sec.
J40 = 1,103 x 40 + 2,5 x 50 = 167,6 ^f/kg.
1.3. Dans l'échangeur thermique, 20 % des gaz passent par le conduit de dérivation et 80 % par la batterie.
La masse de gaz traversant le serpentin et participant à l'échange thermique
GzM = 0,8Gfl. g = 0,8 x 76 300 = 61 040 kg/h.
1.4. Récupération de la chaleur
exc = (J150 - J40) x ^m = (466,9 - 167,68) x
61 040 = 18,26 x 106, ^f/h.
Cette chaleur est dépensée pour chauffer l'eau de refroidissement
Qx™= L x l x (t2 - t4),
où W est la consommation d'eau, en kg/h ; sv = 4,19 ^l/kg °C - capacité calorifique de l'eau ; t 2, t4 - température de l'eau
Actes d'Instorf 11 (64)
respectivement en sortie et en entrée de l'échangeur thermique ; on prend tx = 8 °C.
2. Débit d'eau de refroidissement, kg/s
W=Qyra /(st x (t2 - 8) = (18,26 / 4,19) x 106 / (t2 - 8)/3600 = 4,36 x 106/ (t2 -8) x 3600.
À l'aide de la dépendance obtenue, vous pouvez déterminer le débit d'eau de refroidissement à la température requise, par exemple :
^, °С 25 50 75
W, kg/s 71,1 28,8 18,0
3. Le débit de condensats G^^ est :
^ond = GBM(d150 - d40) = 61,0 x (112,7 - 50) =
4. Vérification de la possibilité de condensation de l'humidité résiduelle provenant de la vaporisation du carburant dans les éléments arrière du système.
Teneur en humidité moyenne des fumées à la sortie de l'échangeur thermique
^р = (d150 x 0,2 Gd.g. + d40 x 0,8 Gd.g.) / GA g1 =
112,7 x 0,2 + 50 x 0,8 = 62,5 G/kg sec. G.
D'après le diagramme J-d, cette teneur en humidité correspond à une température de point de rosée égale à tp. R. = 56 °C.
La température réelle des fumées à la sortie de l'échangeur thermique est
tcjmKT = ti50 x 0,2 + t40 x 0,8 = 150 x 0,2 + 40 x 0,8 = 64 °C.
Étant donné que la température réelle des gaz de combustion derrière l'échangeur de chaleur est supérieure au point de rosée, la condensation de la vapeur d'humidité du carburant dans les éléments arrière du système ne se produira pas.
5. Efficacité
5.1. Efficacité d'utilisation de la chaleur de vaporisation de l'humidité du combustible.
La quantité de chaleur fournie à l'échangeur de chaleur
Q ^ h = J150 x Gft g = 466,9 x 76 300 =
35,6 x 106, M Dj/h.
Efficacité Q = (18,26 /35,6) x 100 = 51,3 %,
où 18,26 x 106, МJ/h est la chaleur d'utilisation de la vaporisation de l'humidité du carburant.
5.2. Efficacité de l'utilisation de l'humidité du carburant
Efficacité W = ^cond / W) x 100 = (3825/8600) x 100 = 44,5 %.
Ainsi, l'échangeur de chaleur proposé et son mode de fonctionnement assurent un refroidissement en profondeur des fumées. En raison de la condensation de la vapeur d'humidité du carburant, l'efficacité de l'échange thermique entre les gaz de combustion et le liquide de refroidissement augmente considérablement. Dans ce cas, toute la chaleur latente de vaporisation récupérée est transférée pour chauffer le liquide de refroidissement, qui peut être utilisé dans le cycle de la turbine à vapeur sans traitement supplémentaire.
Pendant le fonctionnement de l'échangeur de chaleur, les gaz de combustion sont purifiés des acides sulfurique et sulfureux et le condensat de vapeur peut donc être utilisé pour l'apport de chaleur chaude.
Les calculs montrent que l'efficacité est :
Lors de l'utilisation de la chaleur de vaporisation
humidité du carburant - 51,3%
Humidité du carburant - 44,5%.
Bibliographie
1. Aronov, I.Z. Chauffage par contact de l'eau par les produits de combustion du gaz naturel. - L. : Nédra, 1990. - 280 p.
2. Koudinov, A.A. Économie d'énergie dans le domaine de l'énergie thermique et des technologies thermiques. - M. : Génie Mécanique, 2011. - 373 p.
3. Pat. 2555919 (RU).(51) IPC F22B 1|18 (20006.01). Echangeur de chaleur pour récupération de chaleur en profondeur des fumées de type superficiel et son procédé de fonctionnement /
O.S. Gorfin, B.F. Zyuzin // Découvertes. Invention. - 2015. - N°19.
4. Gorfin, O.S., Mikhailov, A.V. Machines et équipements pour le traitement de la tourbe. Partie 1. Production de briquettes de tourbe. - Tver : TVSTU 2013. - 250 p.
Système de condensation des fumées pour les chaudières de l'entreprise “ AprotechIngénierieUN B" (Suède)Le système de condensation des fumées permet de capter et de récupérer de grandes quantités d'énergie thermique contenues dans les fumées de la chaudière humide, qui sont généralement évacuées par la cheminée dans l'atmosphère.
Le système de récupération de chaleur/condensation des fumées permet d'augmenter l'apport de chaleur aux consommateurs de 6 à 35 % (en fonction du type de combustible brûlé et des paramètres d'installation) ou de réduire la consommation de gaz naturel de 6 à 35 %.
Principaux avantages:
- Économie de carburant (gaz naturel) - charge thermique de chaudière identique ou augmentée avec moins de combustion de carburant
- Réduction des émissions - CO2, NOx et SOx (lors de la combustion de charbon ou de combustibles liquides)
- Obtention de condensats pour le système d'appoint de la chaudière
Principe d'opération:
Le système de récupération de chaleur/condensation des fumées peut fonctionner en deux étapes : avec ou sans utilisation d'un système d'humidification de l'air fourni aux brûleurs de la chaudière. Si nécessaire, un laveur est installé avant le système de condensation.
Dans le condenseur, les fumées d'échappement sont refroidies grâce à l'eau de retour du réseau de chaleur. Lorsque la température des fumées diminue, une grande quantité de vapeur d’eau contenue dans les fumées se condense. L'énergie thermique de condensation de la vapeur est utilisée pour chauffer le réseau de chaleur de retour.
Un refroidissement supplémentaire du gaz et une condensation de vapeur d'eau se produisent dans l'humidificateur. Le fluide de refroidissement dans l'humidificateur est l'air soufflé fourni aux brûleurs de la chaudière. Étant donné que l'air soufflé est chauffé dans l'humidificateur et que des condensats chauds sont injectés dans le flux d'air devant les brûleurs, un processus d'évaporation supplémentaire se produit dans les gaz de combustion de la chaudière.
L'air soufflé fourni aux brûleurs de la chaudière contient une quantité accrue d'énergie thermique en raison de l'augmentation de la température et de l'humidité.
Cela entraîne une augmentation de la quantité d'énergie présente dans les gaz de combustion entrant dans le condenseur, ce qui conduit à une utilisation plus efficace de la chaleur par le système de chauffage urbain.
Dans l'unité de condensation des fumées, des condensats sont également produits qui, en fonction de la composition des fumées, seront encore purifiés avant d'être introduits dans le système de chaudière.
Effet économique.
Comparaison de la puissance thermique dans les conditions suivantes :
- Pas de condensation
- Condensation des fumées
- Condensation et humidification de l'air fourni pour la combustion
Le système de condensation des fumées permet à la chaufferie existante de :
- Augmenter la production de chaleur de 6,8 % ou
- Réduire la consommation de gaz de 6,8 % et augmenter les revenus issus de la vente de quotas de CO,NO
- Le montant de l'investissement est d'environ 1 million d'euros (pour une chaufferie d'une capacité de 20 MW)
- La période de récupération est de 1 à 2 ans.
Économies en fonction de la température du liquide de refroidissement dans le tuyau de retour :
Utilisation de la chaleur des fumées dans les chaufferies industrielles au gaz
Utilisation de la chaleur des fumées dans les chaufferies industrielles au gaz
Candidat en sciences techniques Sizov V.P., docteur en sciences techniques Yuzhakov A.A., candidat en sciences techniques Kapger I.V.,
Permavtomatika SARL,
sizovperm@ mail .ru
Résumé : le prix du gaz naturel varie considérablement à travers le monde. Cela dépend de l'adhésion du pays à l'OMC, du fait que le pays exporte ou importe son gaz, des coûts de production du gaz, de l'état de l'industrie, des décisions politiques, etc. Le prix du gaz dans la Fédération de Russie dans le cadre de l'adhésion de notre pays à l'OMC ne fera qu'augmenter et le gouvernement envisage d'égaliser les prix du gaz naturel tant à l'intérieur du pays qu'à l'étranger. Comparons grossièrement les prix du gaz en Europe et en Russie.
Russie – 3 roubles/m3.
Allemagne - 25 roubles/m3.
Danemark - 42 roubles/m3.
Ukraine, Biélorussie – 10 roubles/m3.
Les prix sont tout à fait raisonnables. Dans les pays européens, les chaudières à condensation sont largement utilisées, leur part totale dans le processus de production de chaleur atteint 90 %. En Russie, ces chaudières ne sont généralement pas utilisées en raison du coût élevé des chaudières, du faible coût du gaz et des réseaux centralisés à haute température. Et aussi en maintenant le système de limitation de la combustion des gaz dans les chaufferies.
Actuellement, la question d'une utilisation plus complète de l'énergie du liquide de refroidissement devient de plus en plus pertinente. Le dégagement de chaleur dans l’atmosphère crée non seulement une pression supplémentaire sur l’environnement, mais augmente également les coûts pour les propriétaires de chaufferies. Dans le même temps, les technologies modernes permettent d'utiliser plus pleinement la chaleur des fumées et d'augmenter le rendement de la chaudière, calculé sur la base du pouvoir calorifique inférieur, jusqu'à une valeur de 111 %. Les déperditions thermiques par les fumées occupent la place principale parmi les déperditions thermiques de la chaudière et s'élèvent à 5 ¸ 12% de la chaleur générée. De plus, la chaleur de condensation de la vapeur d'eau formée lors de la combustion du carburant peut être utilisée. La quantité de chaleur dégagée lors de la condensation de la vapeur d'eau dépend du type de combustible et varie de 3,8 % pour les combustibles liquides et jusqu'à 11,2 % pour les combustibles gazeux (pour le méthane) et est définie comme la différence entre la chaleur de combustion supérieure et inférieure. du carburant (Tableau 1 ).
Tableau 1 - Valeurs des pouvoirs calorifiques supérieurs et inférieurs pour différents types de combustibles
Type de carburant |
PCS (Kcal) |
PCI ( Kcal ) |
Différence (%) |
L'huile de chauffage |
|||
Il s'avère que les gaz d'échappement contiennent à la fois de la chaleur sensible et latente. De plus, cette dernière peut atteindre une valeur qui dans certains cas dépasse la chaleur sensible. La chaleur sensible est une chaleur dans laquelle une modification de la quantité de chaleur fournie à un corps entraîne une modification de sa température. La chaleur latente est la chaleur de vaporisation (condensation), qui ne modifie pas la température du corps, mais sert à modifier l'état d'agrégation du corps. Cette affirmation est illustrée par un graphique (Fig. 1, sur lequel l'enthalpie (la quantité de chaleur fournie) est tracée le long de l'axe des abscisses et la température est tracée le long de l'axe des ordonnées).
Riz. 1 – Dépendance du changement d’enthalpie pour l’eau
Dans la section du graphique A-B, l’eau est chauffée d’une température de 0 °C à une température de 100 °C. Dans ce cas, toute la chaleur apportée à l’eau est utilisée pour augmenter sa température. Ensuite, le changement d'enthalpie est déterminé par la formule (1)
(1)
où c est la capacité calorifique de l'eau, m est la masse de l'eau chauffée, Dt – différence de température.
La section du graphique BC montre le processus d’ébullition de l’eau. Dans ce cas, toute la chaleur fournie à l'eau est consacrée à sa conversion en vapeur, tandis que la température reste constante - 100°C. La section C-D du graphique montre que toute l'eau s'est transformée en vapeur (évaporée), après quoi de la chaleur est dépensée pour augmenter la température de la vapeur. Ensuite, le changement d'enthalpie pour la section A-C est caractérisé par la formule (2)
Où r = 2500 kJ/kg – chaleur latente de vaporisation de l'eau à pression atmosphérique.
La plus grande différence entre les valeurs calorifiques les plus élevées et les plus basses, comme le montre le tableau. 1, méthane, donc le gaz naturel (jusqu'à 99 % de méthane) offre la rentabilité la plus élevée. À partir de là, tous les autres calculs et conclusions seront donnés pour le gaz à base de méthane. Considérons la réaction de combustion du méthane (3)
De l'équation de cette réaction, il résulte que pour l'oxydation d'une molécule de méthane, deux molécules d'oxygène sont nécessaires, c'est-à-dire Pour une combustion complète de 1 m 3 de méthane, il faut 2 m 3 d'oxygène. L'air atmosphérique, qui est un mélange de gaz, est utilisé comme comburant lors de la combustion de combustible dans les chaudières. Pour les calculs techniques, la composition conditionnelle de l'air est généralement considérée comme composée de deux composants : l'oxygène (21 % en volume) et l'azote (79 % en volume). Compte tenu de la composition de l'air, pour réaliser la réaction de combustion, la combustion complète du gaz nécessitera un volume d'air 100/21 = 4,76 fois supérieur à celui de l'oxygène. Ainsi, pour brûler 1 m 3 de méthane il faudra 2 ×4,76=9,52 air. Comme le montre l’équation de la réaction d’oxydation, le résultat est du dioxyde de carbone, de la vapeur d’eau (gaz de combustion) et de la chaleur. La chaleur dégagée lors de la combustion du carburant selon (3) est appelée pouvoir calorifique net du carburant (PCI).
Si vous refroidissez la vapeur d'eau, dans certaines conditions, elle commencera à se condenser (passage de l'état gazeux à l'état liquide) et en même temps une quantité supplémentaire de chaleur sera libérée (chaleur latente de vaporisation/condensation) Fig. 2.
Riz. 2 – Dégagement de chaleur lors de la condensation de la vapeur d’eau
Il convient de garder à l’esprit que la vapeur d’eau contenue dans les gaz de combustion a des propriétés légèrement différentes de celles de la vapeur d’eau pure. Ils sont en mélange avec d'autres gaz et leurs paramètres correspondent aux paramètres du mélange. La température à laquelle commence la condensation est donc différente de 100 °C. La valeur de cette température dépend de la composition des gaz de combustion, qui, à son tour, est une conséquence du type et de la composition du combustible, ainsi que du taux d'excès d'air.
La température des gaz de combustion à laquelle commence la condensation de la vapeur d'eau dans les produits de combustion du carburant est appelée point de rosée et ressemble à la Fig. 3.
Riz. 3 – Point de rosée du méthane
Par conséquent, pour les fumées, qui sont un mélange de gaz et de vapeur d'eau, l'enthalpie évolue selon une loi légèrement différente (Fig. 4).
Figure 4 – Libération de chaleur du mélange vapeur-air
D'après le graphique de la Fig. 4, deux conclusions importantes peuvent être tirées. Premièrement, la température du point de rosée est égale à la température à laquelle les fumées ont été refroidies. Deuxièmement, il n’est pas nécessaire de le parcourir comme sur la Fig. 2, toute la zone de condensation, ce qui est non seulement pratiquement impossible mais aussi inutile. Ceci, à son tour, offre diverses possibilités pour mettre en œuvre l’équilibre thermique. En d’autres termes, presque n’importe quel petit volume de liquide de refroidissement peut être utilisé pour refroidir les gaz de combustion.
De ce qui précède, nous pouvons conclure que lors du calcul du rendement de la chaudière sur la base du pouvoir calorifique inférieur avec utilisation ultérieure de la chaleur des fumées et de la vapeur d'eau, le rendement peut être considérablement augmenté (plus de 100 %). À première vue, cela contredit les lois de la physique, mais en réalité, il n'y a pas de contradiction ici. L'efficacité de tels systèmes doit être calculée sur la base du pouvoir calorifique supérieur, et la détermination de l'efficacité basée sur le pouvoir calorifique inférieur ne doit être effectuée que s'il est nécessaire de comparer son efficacité avec celle d'une chaudière conventionnelle. Ce n'est que dans ce contexte qu'une efficacité > 100 % a du sens. Nous pensons que pour de telles installations, il est plus correct de donner deux rendements. L’énoncé du problème peut être formulé comme suit. Pour utiliser davantage la chaleur de combustion des gaz de combustion, ceux-ci doivent être refroidis à une température inférieure au point de rosée. Dans ce cas, la vapeur d’eau générée lors de la combustion du gaz va se condenser et transférer la chaleur latente de vaporisation au liquide de refroidissement. Dans ce cas, le refroidissement des fumées doit être effectué dans des échangeurs de chaleur d'une conception spéciale, dépendant principalement de la température des fumées et de la température de l'eau de refroidissement. L'utilisation de l'eau comme liquide de refroidissement intermédiaire est la plus intéressante, car dans ce cas, il est possible d'utiliser de l'eau à la température la plus basse possible. De ce fait, il est possible d'obtenir une température d'eau à la sortie de l'échangeur thermique, par exemple 54°C, puis de l'utiliser. Si la conduite de retour est utilisée comme liquide de refroidissement, sa température doit être aussi basse que possible, ce qui n'est souvent possible que si les consommateurs disposent d'installations de chauffage à basse température.
Les gaz de combustion des chaudières de grande puissance sont généralement évacués dans un tuyau en béton armé ou en brique. Si des mesures particulières ne sont pas prises pour le chauffage ultérieur des fumées partiellement séchées, le tuyau se transformera en un échangeur de chaleur à condensation avec toutes les conséquences qui en découlent. Il existe deux manières de résoudre ce problème. La première méthode consiste à utiliser un by-pass, dans lequel une partie des gaz, par exemple 80 %, passe à travers l'échangeur de chaleur, et l'autre partie, à hauteur de 20 %, passe à travers le by-pass puis est mélangée avec le gaz partiellement séchés. Ainsi, en chauffant les gaz, on déplace le point de rosée à la température requise à laquelle le tuyau est assuré de fonctionner en mode sec. La deuxième méthode consiste à utiliser un récupérateur à plaques. Dans ce cas, les gaz d'échappement traversent plusieurs fois le récupérateur et s'échauffent ainsi.
Considérons un exemple de calcul d'un tuyau typique de 150 m (Fig. 5-7), qui a une structure à trois couches. Les calculs ont été effectués dans le progiciel Ansys -CFX . Il ressort clairement des figures que le mouvement du gaz dans le tuyau a un caractère turbulent prononcé et, par conséquent, la température minimale sur le revêtement peut ne pas être dans la zone de la pointe, comme il ressort de la méthodologie empirique simplifiée. .
Riz. 7 – champ de température à la surface du revêtement
Il convient de noter que lors de l'installation d'un échangeur de chaleur dans un chemin de gaz, sa résistance aérodynamique augmentera, mais le volume et la température des gaz d'échappement diminueront. Cela entraîne une diminution du courant de l'extracteur de fumée. La formation de condensats impose des exigences particulières aux éléments du parcours gazeux en termes d'utilisation de matériaux résistant à la corrosion. La quantité de condensat est d'environ 1 000 à 600 kg/heure pour 1 Gcal de puissance utile de l'échangeur de chaleur. La valeur du pH du condensat des produits de combustion lors de la combustion du gaz naturel est de 4,5 à 4,7, ce qui correspond à un environnement acide. En cas de faible quantité de condensat, il est possible d'utiliser des blocs remplaçables pour neutraliser le condensat. Cependant, pour les grandes chaufferies, il est nécessaire d'utiliser une technologie de dosage de soude caustique. Comme le montre la pratique, de petits volumes de condensats peuvent être utilisés comme appoint sans aucune neutralisation.
Il convient de souligner que le principal problème mentionné ci-dessus dans la conception des systèmes est la différence trop importante d'enthalpie par unité de volume de substances, et le problème technique qui en résulte est le développement de la surface d'échange thermique côté gaz. L'industrie de la Fédération de Russie produit en série des échangeurs de chaleur similaires, tels que KSK, VNV, etc. Considérons à quel point la surface d'échange thermique côté gaz est développée sur la structure existante (Fig. 8). Un tube ordinaire dans lequel de l'eau (liquide) circule à l'intérieur et de l'air (gaz d'échappement) de l'extérieur le long des ailettes du radiateur. Le rapport de chauffage calculé sera exprimé par un certain
Riz. 8 – dessin du tube chauffant.
coefficient
K =S nar /S vn, (4),
Où S nar – surface extérieure de l'échangeur de chaleur mm 2, et S vn – zone interne du tube.
Dans les calculs géométriques de la structure, nous obtenons K =15. Cela signifie que la surface extérieure du tube est 15 fois plus grande que la surface intérieure. Cela s'explique par le fait que l'enthalpie de l'air par unité de volume est plusieurs fois inférieure à l'enthalpie de l'eau par unité de volume. Calculons combien de fois l'enthalpie d'un litre d'air est inférieure à l'enthalpie d'un litre d'eau. Depuis
enthalpie de l'eau : E in = 4,183 KJ/l*K.
enthalpie de l'air : E air = 0,7864 J/l*K. (à une température de 130 0 C).
L’enthalpie de l’eau est donc 5 319 fois supérieure à l’enthalpie de l’air, et donc K =S nar /S vn . Idéalement, dans un tel échangeur de chaleur, le coefficient K devrait être de 5319, mais comme la surface extérieure par rapport à la surface intérieure est développée 15 fois, la différence d'enthalpie essentiellement entre l'air et l'eau est réduite à la valeur K = (5319/15) = 354. Développer techniquement le rapport des aires des surfaces internes et externes pour obtenir le rapport K =5319 très difficile voire presque impossible. Pour résoudre ce problème, nous allons essayer d'augmenter artificiellement l'enthalpie de l'air (gaz d'échappement). Pour ce faire, pulvérisez de l'eau (condensat du même gaz) depuis la buse dans les gaz d'échappement. Pulvérisons-le en quantité telle par rapport au gaz que toute l'eau pulvérisée s'évapore complètement dans le gaz et que l'humidité relative du gaz atteigne 100 %. L'humidité relative du gaz peut être calculée sur la base du tableau 2.
Tableau 2. Valeurs d'humidité absolue des gaz avec une humidité relative de 100 % pour l'eau à différentes températures et pressions atmosphériques.
T°C |
A,g/m3 |
T°C |
A,g/m3 |
T°C |
A,g/m3 |
86,74 |
|||||
D'après la figure 3, il est clair qu'avec un brûleur de très haute qualité, il est possible d'atteindre une température de point de rosée dans les gaz d'échappement T rosée = 60 0 C. Dans ce cas, la température de ces gaz est de 130 0 C. La teneur absolue en humidité du gaz (selon le tableau 2) à T rosée = 60 0 C sera 129,70 g/m3. Si de l'eau est pulvérisée dans ce gaz, sa température chutera fortement, sa densité augmentera et son enthalpie augmentera fortement. Il convient de noter que cela n'a aucun sens de pulvériser de l'eau au-dessus de 100 % d'humidité relative, car... Lorsque le seuil d'humidité relative dépasse 100 %, l'eau pulvérisée cesse de s'évaporer en gaz. Effectuons un petit calcul de la quantité d'eau pulvérisée requise pour les conditions suivantes : Tg – température initiale du gaz égale à 120 0 C, T montée - point de rosée du gaz 60 0 C (129,70 g/m 3), requis IT : Tgk - la température finale du gaz et Mv - la masse d'eau pulvérisée dans le gaz (kg.)
Solution. Tous les calculs sont effectués par rapport à 1 m 3 de gaz. La complexité des calculs est déterminée par le fait qu'à la suite de l'atomisation, la densité du gaz ainsi que sa capacité thermique, son volume, etc. changent. De plus, on suppose que l'évaporation se produit dans un gaz absolument sec et. l'énergie nécessaire au chauffage de l'eau n'est pas prise en compte.
Calculons la quantité d'énergie donnée par le gaz à l'eau lors de l'évaporation de l'eau
où : c – capacité calorifique du gaz (1 KJ/kg.K), m – masse de gaz (1 kg/m 3)
Calculons la quantité d'énergie cédée par l'eau lors de son évaporation en gaz.
Où: r – énergie latente de vaporisation (2500 KJ/kg), m – masse d'eau évaporée
Par substitution, nous obtenons la fonction
(5)
Il convient de garder à l'esprit qu'il est impossible de pulvériser plus d'eau que ce qui est indiqué dans le tableau 2 et que le gaz contient déjà de l'eau évaporée. Grâce à la sélection et aux calculs, nous avons obtenu la valeur m = 22 g, Tgk = 65 0 C. Calculons l'enthalpie réelle du gaz résultant, en tenant compte du fait que son humidité relative est de 100 % et qu'une fois refroidi, de l'énergie latente et sensible sera libérée. Alors selon on obtient la somme de deux enthalpies. Enthalpie du gaz et enthalpie de l'eau condensée.
E voz = Par exemple + Evod
Par exemple on trouve dans la littérature de référence 1,1 (KJ/m 3 *K)
ÉvodNous calculons par rapport au tableau. 2. Notre gaz, refroidissant de 65 0 C à 64 0 C, libère 6,58 grammes d'eau. L'enthalpie de condensation est Évod=2500 J/g ou dans notre cas Évod=16,45 KJ/m 3
Résumons l'enthalpie de l'eau condensée et l'enthalpie du gaz.
E voz =17,55 (J/l*K)
Comme nous pouvons le constater en pulvérisant de l’eau, nous avons pu augmenter l’enthalpie du gaz de 22,3 fois. Si avant de pulvériser de l'eau, l'enthalpie du gaz était E air = 0,7864 J/l*K. (à une température de 130 0 C). Ensuite, après pulvérisation, l'enthalpie est Évoz =17,55 (J/l*K). Cela signifie que pour obtenir la même énergie thermique sur le même échangeur de chaleur standard de type KSK, VNV, la surface de l'échangeur de chaleur peut être réduite de 22,3 fois. Le coefficient K recalculé (la valeur était de 5319) devient égal à 16. Et avec ce coefficient, l'échangeur de chaleur acquiert des dimensions tout à fait réalisables.
Un autre problème important lors de la création de tels systèmes est l'analyse du processus de pulvérisation, c'est-à-dire quel diamètre de goutte est nécessaire lorsque l'eau s'évapore dans le gaz. Si la gouttelette est suffisamment petite (par exemple 5 µM), alors la durée de vie de cette gouttelette dans le gaz avant évaporation complète est assez courte. Et si la taille d’une gouttelette est par exemple de 600 µM, elle reste naturellement beaucoup plus longtemps dans le gaz avant de s’évaporer complètement. La solution à ce problème physique est assez compliquée par le fait que le processus d'évaporation se produit avec des caractéristiques en constante évolution : température, humidité, diamètre des gouttelettes, etc. Pour ce processus, la solution est présentée dans, et la formule de calcul du temps d'évaporation complète évaporation ( ) les gouttes ressemblent
(6)
Où: ρ et - densité du liquide (1 kg/dm 3), r – énergie de vaporisation (2500 kJ/kg), λ g – conductivité thermique du gaz (0,026 J/m 2 K), d 2 – diamètre de goutte (m), Δ t – différence de température moyenne entre le gaz et l’eau (K).
Puis, d'après (6), la durée de vie d'une gouttelette d'un diamètre de 100 μM. (1*10 -4 m) est τ = 2*10 -3 heures ou 1,8 secondes, et la durée de vie d'une goutte d'un diamètre de 50 µM. (5*10 -5 m) est égal à τ = 5*10 -4 heures ou 0,072 secondes. Ainsi, connaissant la durée de vie d'une goutte, sa vitesse de vol dans l'espace, la vitesse d'écoulement du gaz et les dimensions géométriques du conduit de gaz, on peut facilement calculer le système d'irrigation du conduit de gaz.
Ci-dessous, nous examinerons la mise en œuvre de la conception du système en tenant compte des relations obtenues ci-dessus. On pense que l'échangeur de chaleur des fumées doit fonctionner en fonction de la température extérieure, sinon le tuyau de la maison sera détruit lorsque de la condensation s'y formera. Cependant, il est possible de fabriquer un échangeur de chaleur qui fonctionne quelle que soit la température extérieure et présente une meilleure évacuation de la chaleur des gaz d'échappement, même à des températures inférieures à zéro, malgré le fait que la température des gaz d'échappement sera, par exemple, de +10. 0 C (le point de rosée de ces gaz sera de 0 0 C). Ceci est assuré par le fait que pendant l'échange thermique, le contrôleur calcule le point de rosée, l'énergie d'échange thermique et d'autres paramètres. Considérons le schéma technologique du système proposé (Fig. 9).
Selon le schéma technologique, les éléments suivants sont installés dans l'échangeur de chaleur : des registres réglables a-b-c-d ; échangeurs de chaleur d-e-zh; capteurs de température 1-2-3-4-5-6 ; o Arroseur (pompe H, et un groupe de buses) ; contrôleur de contrôle.
Considérons le fonctionnement du système proposé. Laissez les gaz d'échappement s'échapper de la chaudière. par exemple, une température de 120 0 C et un point de rosée de 60 0 C (indiqué sur le schéma par 120/60). La sonde de température (1) mesure la température des gaz d'échappement de la chaudière. Le point de rosée est calculé par le contrôleur par rapport à la stœchiométrie de la combustion des gaz. Une porte (a) apparaît sur le trajet du gaz. Il s'agit d'un volet de secours. qui se ferme en cas de réparation, de dysfonctionnement, de révision, d'entretien du matériel, etc. Ainsi, le registre (a) est entièrement ouvert et laisse passer directement les gaz d'échappement de la chaudière dans le désenfumage. Avec ce schéma, la récupération de chaleur est nulle ; en effet, le schéma d'évacuation des fumées est rétabli tel qu'il était avant l'installation de l'échangeur de chaleur. En état de fonctionnement, la porte (a) est complètement fermée et 100% des gaz entrent dans l'échangeur thermique.
Dans l'échangeur thermique, les gaz entrent dans le récupérateur (e) où ils sont refroidis, mais en aucun cas en dessous du point de rosée (60 0 C). Par exemple, ils ont refroidi jusqu'à 90 0 C. Aucune humidité n'y a été libérée. La température des gaz est mesurée par la sonde de température 2. La température des gaz après le récupérateur peut être réglée avec une vanne (b). Une régulation est nécessaire pour augmenter l'efficacité de l'échangeur de chaleur. Étant donné que lors de la condensation de l'humidité, la masse présente dans les gaz diminue en fonction du refroidissement des gaz, il est possible d'en éliminer jusqu'à 2/11 de la masse totale des gaz sous forme d'eau. D'où vient ce chiffre ? Considérons la formule chimique de la réaction d'oxydation du méthane (3).
Pour oxyder 1 m 3 de méthane, il faut 2 m 3 d'oxygène. Mais comme l'air ne contient que 20 % d'oxygène, il faudra 10 m 3 d'air pour oxyder 1 m 3 de méthane. Après avoir brûlé ce mélange, on obtient : 1 m 3 de dioxyde de carbone, 2 m 3 de vapeur d'eau et 8 m 3 d'azote et autres gaz. Nous pouvons éliminer par condensation un peu moins de 2/11 de tous les gaz résiduaires sous forme d'eau des gaz d'échappement. Pour ce faire, les gaz d'échappement doivent être refroidis à la température extérieure. Avec libération de la proportion appropriée d’eau. L'air extrait de la rue pour la combustion contient également une légère humidité.
L'eau libérée est évacuée au fond de l'échangeur thermique. En conséquence, si la totalité de la composition des gaz (11/11 parties) passe le long du trajet de la chaudière-récupérateur (e)-unité de récupération de chaleur (e), alors seules 9/11 parties des gaz d'échappement peuvent passer de l'autre côté. du récupérateur (e). Le reste - jusqu'à 2/11 parties du gaz sous forme d'humidité - peut tomber dans l'échangeur de chaleur. Et pour minimiser la résistance aérodynamique de l'échangeur thermique, la porte (b) peut être légèrement ouverte. Dans ce cas, les gaz d’échappement seront séparés. Une partie passera par le récupérateur (e), et une partie par la porte (b). Lorsque la porte (b) est complètement ouverte, les gaz passeront sans refroidissement et les lectures des capteurs de température 1 et 2 coïncideront.
Un système d'irrigation avec une pompe H et un groupe de buses est installé le long du trajet des gaz. Les gaz sont irrigués avec l'eau libérée lors de la condensation. Les injecteurs qui projettent de l'humidité dans le gaz augmentent fortement son point de rosée, le refroidissent et le compriment de manière adiabatique. Dans l'exemple considéré, la température du gaz chute fortement jusqu'à 62/62, et comme l'eau pulvérisée dans le gaz s'évapore complètement dans le gaz, le point de rosée et la température du gaz coïncident. Ayant atteint l'échangeur de chaleur (e), de l'énergie thermique latente y est libérée. De plus, la densité du flux gazeux augmente brusquement et sa vitesse diminue brusquement. Tous ces changements améliorent considérablement l’efficacité du transfert de chaleur. La quantité d'eau pulvérisée est déterminée par le contrôleur et est liée à la température et au débit de gaz. La température du gaz devant l'échangeur thermique est surveillée par le capteur de température 6.
Ensuite, les gaz entrent dans l'échangeur de chaleur (e). Dans l'échangeur de chaleur, les gaz se refroidissent, par exemple, jusqu'à une température de 35 0 C. En conséquence, le point de rosée de ces gaz sera également de 35 0 C. Le prochain échangeur de chaleur sur le chemin des gaz d'échappement est le chaleur échangeur (g). Il sert à chauffer l'air de combustion. La température d'alimentation en air d'un tel échangeur de chaleur peut atteindre -35 0 C. Cette température dépend de la température minimale de l'air extérieur dans une région donnée. Étant donné qu'une partie de la vapeur d'eau est éliminée des gaz d'échappement, le débit massique des gaz d'échappement coïncide presque avec le débit massique de l'air de combustion. Laissez l'échangeur de chaleur, par exemple, être rempli d'antigel. Une porte (c) est installée entre les échangeurs de chaleur. Cette porte fonctionne également en mode discret. Lorsqu'il fait chaud dehors, cela ne sert à rien d'extraire de la chaleur de l'échangeur thermique (g). Il arrête son fonctionnement et la porte (c) s'ouvre complètement, laissant passer les gaz d'échappement en contournant l'échangeur de chaleur (g).
La température des gaz refroidis est déterminée par le capteur de température (3). Ces gaz sont ensuite envoyés vers le récupérateur (e). Après l'avoir traversé, ils sont chauffés à une certaine température proportionnelle au refroidissement des gaz de l'autre côté du récupérateur. La porte (d) est nécessaire pour réguler l'échange thermique dans le récupérateur, et son degré d'ouverture dépend de la température extérieure (de la sonde 5). Ainsi, s'il fait très froid dehors, alors la porte (d) est complètement fermée et les gaz sont chauffés dans le récupérateur pour éviter le point de rosée dans la canalisation. S'il fait chaud dehors, alors la porte (d) est ouverte, tout comme la porte (b).
CONCLUSIONS :
Une augmentation de l'échange thermique dans un échangeur de chaleur liquide/gaz se produit en raison d'une forte augmentation de l'enthalpie du gaz. Mais la pulvérisation d'eau proposée doit se faire à des doses strictement mesurées. De plus, le dosage de l'eau dans les gaz d'échappement tient compte de la température extérieure.
La méthode de calcul qui en résulte permet d'éviter la condensation d'humidité dans la cheminée et d'augmenter considérablement l'efficacité de la chaudière. Une technique similaire peut être appliquée aux turbines à gaz et autres dispositifs à condensateur.
Avec la méthode proposée, la conception de la chaudière ne change pas, mais est seulement modifiée. Le coût de modification représente environ 10 % du coût de la chaudière. La période de récupération aux prix actuels du gaz est d'environ 4 mois.
Cette approche permet de réduire considérablement la consommation de métal de la structure et, par conséquent, son coût. De plus, la résistance aérodynamique de l'échangeur de chaleur diminue considérablement et la charge sur l'extracteur de fumée est réduite.
LITTÉRATURE:
1.Aronov I.Z. Utilisation de la chaleur des fumées des chaufferies gazéifiées. – M. : « Énergie », 1967. – 192 p.
2.Thaddeus Hobler. Transfert de chaleur et échangeurs de chaleur. – Leningrad : Publication scientifique d'État de la littérature chimique, 1961. – 626 p.