Forge à gaz de bricolage. Four de forgeage : procédé de bricolage Forge forge à la maison
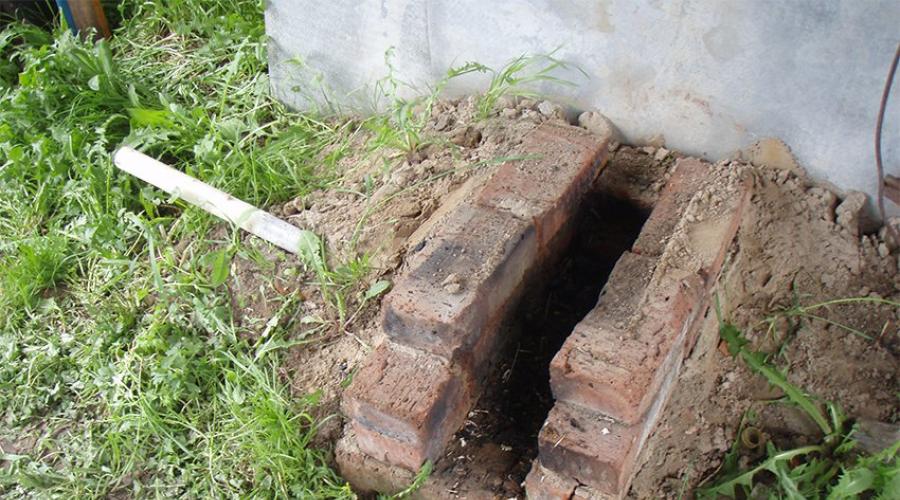
Lire aussi
Si vous faites partie de ces personnes qui fondent le métal dans leurs mains et que vous rêvez d'avoir votre propre forge, alors vous avez besoin d'une forge. Nous vous invitons à utiliser notre exemple et vous pourrez fabriquer vous-même une forge de vos propres mains, ce qui vous aidera à maîtriser l'art de la forge.
La menuiserie ou la menuiserie est bien sûr bonne. La transformation du bois est traditionnelle en Russie. Mais nous voulons parler de métal. Plus précisément, sur le forgeage des métaux. De quoi avez-vous besoin pour commencer à forger ? La première est la forge d'un forgeron.
Vous pourriez être surpris, mais la forge est la chose la plus simple pour organiser une forge.
La tâche de la forge est de chauffer un morceau de métal à une température qui permettra de l'écraser sans le détruire.
La forge est bien sûr le feu. Vous pouvez brûler du gaz, du combustible liquide, du fioul ou du pétrole brut, du charbon et du bois de chauffage. Seul le bois de chauffage produit peu de chaleur jusqu'à ce qu'il se transforme en charbon. Le bois de chauffage ne peut être considéré que comme une matière première pour produire du charbon de bois, mais le charbon de bois est un excellent combustible pour une forge. Peut-être le meilleur, mais aussi le plus cher, mais aussi le plus accessible. Le charbon de bois pour grillades et barbecues est vendu dans tous les supermarchés. Nous nous en tiendrons donc à l’option charbon.
Si nous parlons d'une forge au charbon, il existe alors deux options : avec soufflage latéral et avec soufflage inférieur. Le soufflage latéral est idéal pour le charbon de bois et est également le plus simple à mettre en œuvre. L'option la plus simple est un trou dans le sol où l'air est fourni par un tuyau. Vous pouvez également réaliser une forge en brique et la recouvrir de terre.
Avec l'aide d'une telle forge, les forgerons débutants s'essayent. Un tuyau est inséré dans le tuyau et relié au trou de soufflage de l'aspirateur.
L'inconvénient de cette forge est qu'il faut travailler accroupi, ce qui n'est pas très pratique. Cependant, vous pouvez assembler une boîte de la hauteur requise, la remplir de terre et y faire une forge. Mais puisque nous suivons cette voie, cela vaut la peine de faire quelque chose de plus approfondi. Il y a encore un point. Une forge à soufflage latéral n'est pas très adaptée au charbon, tandis qu'une forge à soufflage inférieur à travers une grille est plus polyvalente à cet égard. Autrement dit, une forge avec soufflerie inférieure peut travailler à la fois sur le charbon de bois et sur la pierre. Mais la conception sera aussi plus compliquée.
Nous aurons besoin:
- tôle d'acier de cinq millimètres d'épaisseur, environ 100x100 cm ;
- tôle d'acier de 2 mm d'épaisseur;
- coin 30x30 ;
- six briques en argile réfractaire ШБ-8 ;
- meuleuse d'angle, communément appelée « meuleuse » ;
- roue de nettoyage;
- meules pour couper l'acier et la pierre;
- machine à souder et électrodes;
- deux vis à oreilles (écrou à œil).
La forge se compose d'une table avec un nid de forge. En dessous, sous le nid du four, se trouve une chambre à cendres dans laquelle l'air est fourni. La table est constituée de tôle d'acier de cinq millimètres d'épaisseur. La taille de la table est arbitraire, mais elle est plus pratique lorsque vous pouvez y placer librement une pince de travail, un tisonnier et une cuillère afin qu'ils soient à portée de main. Nous découpons une bande de 125 mm de large dans une feuille de cinq millimètres ; nous en aurons besoin plus tard et, à partir du morceau restant, nous fabriquons une table.
Schéma d'une forge avec un nid de forge
Au milieu, nous découpons un trou carré pour le futur nid de forge. Vous devez décider de la taille du nid. Un grand nid nécessitera beaucoup de charbon. Un petit ne permettra pas de chauffer de grosses pièces. La profondeur du nid par rapport à la grille compte également. Sans entrer dans les détails, disons qu'une profondeur d'une dizaine de centimètres sera optimale, quelle que soit la taille du nid en plan.
Pour éviter que le métal ne brûle, il doit être recouvert (recouvert) de briques en argile réfractaire. Nous utilisons la brique ShB-8. Ses dimensions sont de 250x124x65 mm. Ces dimensions détermineront la taille du nid de forge - 12,5 cm au niveau de la grille, 25 au sommet, 10 cm de profondeur. Compte tenu de l'épaisseur de la brique, la taille du trou dans la table sera de 38x38 cm.
Dans la pièce découpée, nous découpons un carré de 25 cm de côté. Au centre du carré, nous découpons un trou carré de 12 cm de côté. Nous avons également besoin de quatre plaques en forme de trapèze isocèle avec des longueurs de base. de 38 et 25 cm, une hauteur de 12,5 cm La bande préalablement découpée s'est donc avérée utile. Maintenant, vous devez tout cuisiner.
À partir d'acier de deux millimètres, nous enroulons un tuyau carré d'un côté de 12 et d'une longueur de 20 à 25 cm. Ce sera le réceptacle à cendres. Au milieu de l'un des murs, nous faisons un trou pour le conduit d'air. Nous soudons un tuyau dans le trou. Nous utilisons un morceau de conduite d'eau ordinaire 40.
Le cendrier par le bas est fermé par un couvercle. Nous le faisons avec des vis à oreilles.
La table est prête. Il ne reste plus qu'à le poser sur le socle ou à y souder les pieds du coin. Vous pouvez réaliser la base à partir de blocs de béton cellulaire.
Faites attention à l'ouverture. Un conduit d'air le traversera.
À l'aide d'une meuleuse équipée d'un disque à tronçonner la pierre, nous découpons le revêtement de la brique. Assurez-vous d'utiliser un respirateur et des lunettes de sécurité. Et suivez les précautions de sécurité lorsque vous travaillez avec des meuleuses d’angle.
Vous pouvez brancher un aspirateur et essayer d'allumer la forge.
Tout d’abord, nous déposons des copeaux de bois et du bois de chauffage finement haché. On y met le feu d'un coup faible, et quand le bois brûle bien, on ajoute du charbon. Vous pouvez maintenant augmenter le souffle.
L'aspirateur peut être connecté non pas directement au conduit d'air de la forge, mais via un régulateur d'alimentation en air fait maison. Cet appareil permet de réguler la quantité d'air fournie à la forge, c'est-à-dire de réduire ou d'augmenter le souffle.
En règle générale, un registre est installé pour réguler l'alimentation en air dans le conduit. Mais bloquer le débit augmente la charge sur le moteur de l'aspirateur. Un vieil aspirateur est généralement utilisé et afin de ne pas le surcharger, un régulateur d'alimentation en air est construit. Le flux d’air n’est pas bloqué, mais est dévié vers un autre conduit. A cet effet, une boîte à trois tuyaux a été réalisée. Deux en face de l'autre - l'entrée de la pompe et la sortie du four. Le troisième tuyau, sur la paroi supérieure, est l'endroit où l'excès d'air est évacué. Le troisième tuyau est décalé par rapport aux deux premiers du diamètre des trous.
À l’intérieur se trouve une plaque courbée à angle droit, sur la moitié de la longueur de la boîte. La plaque peut être déplacée d'une position extrême à une autre à l'aide d'un fil machine. Dans la mesure où le trou d'alimentation en air dans la forge est bloqué, le trou d'évacuation s'ouvrira dans la même mesure.
La boîte est fermée par un couvercle avec un trou pour la traction.
Nous disposons désormais d’une forge en activité adaptée à une utilisation en extérieur. Pour vous protéger de la pluie, vous avez besoin d'un auvent, qui doit être ininflammable. Et la forge a besoin d'un parapluie et d'un tuyau pour collecter et éliminer la fumée.
Nous fabriquons le parapluie en tôle de deux millimètres d'épaisseur. Premièrement, un tel parapluie durera plus longtemps et, deuxièmement, il est plus difficile de souder du fer plus fin en utilisant le soudage manuel à l'arc.
Pour qu'un parapluie soit le plus efficace possible, l'inclinaison de ses murs doit être d'au moins soixante degrés par rapport à l'horizon. Le parasol doit être placé au-dessus du foyer de manière à ce qu'un faisceau imaginaire dirigé depuis le point le plus proche du bord du foyer, incliné vers l'extérieur selon un angle de soixante degrés par rapport au plan de la table, tombe à l'intérieur du parasol. Cela signifie que plus le parasol est haut au-dessus de la cheminée, plus il doit être grand. En revanche, plus le parasol est bas au-dessus de la table, plus il est gênant de travailler. Ici, vous devez partir du matériel disponible et de vos données anthropométriques.
Le parasol est soutenu par des poteaux d'angle en acier. Nous plaçons un tuyau sur le parapluie, que nous soudons également à partir d'une tôle d'acier en deux parties. Le tuyau doit être recouvert d'un pare-étincelles constitué d'un treillis métallique.
Si vous dirigez l'air évacué du papillon à travers un conduit d'air (un tuyau d'eau de 1 pouce ira) jusqu'au début de la cheminée, vous obtiendrez un éjecteur qui augmente l'efficacité de l'évacuation des gaz de combustion.
C'est tout. Votre forge est prête. Forgez à votre santé, forgez comme nous, forgez mieux que nous !
Le forgeage à la main devient de plus en plus populaire, à la fois pour répondre à vos propres besoins et pour fabriquer divers produits sur commande. Le chauffage du métal, afin d'augmenter ses caractéristiques plastiques, doit être effectué dans des appareils de chauffage spéciaux, dont le plus simple est une forge. La tâche principale de la forge est d'assurer une augmentation stable de la température du métal jusqu'à la température de forgeage, c'est-à-dire au moins 1 200 °C. Comment fabriquer une forge maison et si cela est possible en principe est discuté ci-dessous.
Classification des types de forges
Elle peut être réalisée selon les principaux indicateurs suivants :
- Selon le type de carburant utilisé. Il existe des fours à gaz, ainsi que des appareils fonctionnant au combustible solide (charbon) ou liquide (fioul).
- Selon les caractéristiques de conception, des forges ouvertes et fermées sont construites.
- Par taille du foyer (surface effective) – petit, moyen et grand.
Les fours à combustible solide, pour lesquels il est nécessaire d'utiliser du charbon à coke, constituent une solution technique efficace pour le tournage vidéo, mais dépassée. Cela nécessitera non seulement d’assurer un approvisionnement continu en charbon de bois de haute qualité, mais également de remédier aux lacunes technologiques, notamment :
- chauffage inégal;
- incapacité à contrôler le processus ;
- augmentation de la teneur en soufre, ce qui augmentera la fragilité pendant le processus de forgeage ;
- augmentation de la consommation de carburant, elle peut atteindre 120 à 150 % du poids ;
- faible efficacité de l'appareil, accompagnée de gaspillage important.
Cependant, de telles conceptions, dans des conditions de production unique de produits, peuvent être utilisées à la maison, surtout s'il s'agit de mini-forges fonctionnant au fioul bon marché.
Conception de forges
Pour créer des conditions de travail plus favorables pour un forgeron, il est plus conseillé de construire des forges fermées. Bien qu'ils soient un peu plus difficiles à fabriquer, ils sont plus efficaces et assurent un chauffage uniforme des pièces, en particulier celles de section ronde ou rectangulaire. Les forges ouvertes restent insignifiantes en termes de taille de produit pour les forges artistiques.
Une forge de type fermé se compose des éléments suivants :
- cadre de support en acier avec crémaillères ;
- foyer;
- doublures;
- robinet-vanne;
- ventilateur;
- tuyaux de cheminée.
Si, lors du forgeage, il n'est pas nécessaire de chauffer complètement le métal, des trous technologiques sont pratiqués dans l'amortisseur. Ils sont équipés d'œillets de fermeture, nécessaires pour réduire les pertes de combustible et accélérer le processus de chauffage.
Lors de l'aménagement d'un atelier, il est économique d'équiper la forge d'un simple récupérateur - une unité qui augmente la température des gaz d'échappement du four. Les fours avec récupérateurs ont un rendement plus élevé et la chaleur générée peut être utilisée, par exemple, pour un four qui effectue un traitement ultérieur des produits forgés - leur soudage à la forge, leur bleuissement, etc.
Étapes de fabrication d'une forge maison
Comment fabriquer une forge de forgeron et par où commencer ? Pour réaliser un four fermé, il faudra d’abord déterminer les dimensions de son foyer. Ils sont déterminés par les performances souhaitées, et dépendent de la consommation de carburant et de l'intensité de la forge. Pour l'option gaz, la vitesse optimale d'alimentation en combustible peut être considérée comme étant de 1 à 1,5 m/s : dans ce cas, les processus de transfert de chaleur dans un espace fermé se dérouleront de manière assez efficace.
La tension de sole N est liée à la productivité du four N par un rapport simple :
où F est la surface du foyer.
Compte tenu de la surface allouée à la forge, ainsi que de la productivité de forge attendue (par exemple, en kg de produits), il est possible d'établir la tension minimale réelle du foyer (elle ne doit pas être inférieure à 100 - 150 kg /m2 ∙h, sinon l'aménagement même d'une mini-version de l'installation de chauffage s'avère peu rentable).
Afin de fabriquer une forge de vos propres mains, vous aurez besoin des matériaux suivants :
- tôle d'acier épaisse résistante à la chaleur;
- brique réfractaire (argile réfractaire ou dinas) ;
- profilés en acier laminé (angles, canaux) pour le montage du cadre du foyer, la fabrication du registre et des poteaux de support ;
- cheminées en acier pour éliminer les gaz générés pendant le processus de chauffage des produits ;
- revêtement ignifuge pour sceller les fissures;
- tôle ou acier large pour revêtement extérieur.
La conception d'un foyer ouvert est beaucoup plus simple : il suffit de l'équiper d'un système de grille et de fournir une alimentation en air qui intensifie le processus de chauffage. Dans ce cas, une hotte de ventilation conventionnelle en acier résistant à la chaleur suffit pour éliminer les produits de combustion.
De plus, lors de la construction, il est judicieux d'utiliser des unités standard. Il convient de mentionner ici un ventilateur pour le four, qui peut être utilisé comme unités produites pour des chaudières à double circuit de haute puissance. Sont également adaptés les tuyaux de ventilation et les cheminées en acier conçus pour le désenfumage des gaz à 300 - 400 °C. Vous pouvez installer une forge de vos propres mains en utilisant les brûleurs de puissantes chaudières à double circuit.
Réalisation du cadre de support
La forge étant une unité stationnaire, vous devez clairement déterminer son emplacement. À la maison, toute la partie de l’atelier ne peut pas être utilisée comme forge. Mais, bien entendu, la forge doit être adjacente à l'un de ses murs, de préférence celui qui ne communique pas avec les bâtiments adjacents, car dans ce cas il est beaucoup plus difficile d'aménager des cheminées et d'installer un ventilateur pour la forge.
Selon les conditions de sécurité incendie, la structure doit être à au moins 1 m du mur principal de l'atelier, et toute utilisation de matériaux à résistance au feu réduite (dont les plaques de plâtre GKLO) est exclue.
Lors de la réalisation d'un cadre de support, il est conseillé d'utiliser des dessins prêts à l'emploi pouvant être achetés ou téléchargés sur Internet. Les dimensions de la forge/mini-forge sont adaptées à vos propres capacités. Il serait bien que les dessins incluent également des photos et/ou des vidéos de la forge en activité.
Les poteaux de support et le cadre sont soudés, pour lesquels de l'acier faiblement allié 09G2S est généralement utilisé. Il a une résistance suffisante, est soudé facilement et de manière fiable et résiste à la corrosion à haute température. Le pas des alvéoles de la plaque du cadre support est déterminé par les dimensions du réfractaire. Le cadre fini est pourvu de trous pour la fixation ultérieure des éléments de revêtement extérieur.
Fabrication de foyer et de toiture
Lors du choix des réfractaires pour l'aménagement de la partie supérieure, ils sont guidés par des considérations de durabilité, du type de produits chauffés, ainsi que de l'intensité d'utilisation de la forge. L'argile réfractaire et les dinas sont utilisés le plus souvent.
L'argile réfractaire est fabriquée selon les spécifications techniques de GOST 390-79. L'achat de produits non certifiés est très dangereux, car il est parfois difficile de distinguer les briques réfractaires par leur couleur des briques ordinaires, qui fondent à 1200°C. Les briques réfractaires adaptées à la maçonnerie doivent être de couleur crème et avoir une faible porosité. Dans ce cas, son poids est d'au moins 5 kg. Il existe de nombreuses vidéos de démonstration sur Internet qui peuvent vous aider à identifier des produits de qualité. Les marques ShPD, ShA et ShB conviennent à la construction de la forge.
Téléchargez GOST 390-79 « Produits réfractaires et semi-acides ignifuges à usage général »
fermer ×
Une forge est un équipement qui permet de chauffer du métal à une température de 1200 degrés. Ses dimensions varient considérablement. Certains sont grands et fixes, d’autres sont petits et portables.
Vous pouvez fabriquer de vos propres mains une forge de n'importe quelle conception, qui fonctionnera à la fois avec du combustible solide et gazeux.
Afin de comprendre comment fabriquer une forge de vos propres mains, vous devez comprendre sa conception. Les processus physiques sont basés sur la combinaison du carbone et de l'oxygène. En d’autres termes, le processus de combustion du carbone se produit, libérant de la chaleur.
Pour éviter une combustion complète du métal, la quantité d'oxygène n'est pas fournie en totalité. Ceci est régulé par le soufflage d'air. Il ne faut pas non plus trop cuire la pièce dans la forge. Le métal va sécher et devenir dur mais cassant. Un exemple classique est la fonte.
Une forge faite maison pour le forgeage se compose des parties suivantes :
- Table en réfractaires.
- Un foyer ou un foyer avec une grille.
- Chambre à air.
- Evacuation de l'air.
- Conduit d'air soufflé.
- Vanne d'air.
- Caméra.
- Fenêtre à travers laquelle les pièces sont introduites.
- Parapluie.
- Cheminée.
- Creuset.
- Bain désaltérant.
- Chambre gaz-air.

Pour tapisser la table de vos propres mains, des briques réfractaires sont utilisées. Le foyer est basé sur une forme qui comprend un foyer, des barreaux de grille et une chambre à air.
A l'aide du drainage de l'air, le soufflage est ajusté. La cheminée est conçue pour éliminer les gaz accumulés.
Une chambre de trempe n'est pas toujours nécessaire. Il est nécessaire dans le cas du forgeage de l'acier damassé afin que le produit subisse le traitement thermique nécessaire.
Le creuset est l'endroit où la température maximale est maintenue. À la maison, il est fait de briques en argile réfractaire.
Carburant
Les éléments suivants peuvent être utilisés comme carburant :
- Un petit coca. Le pré-allumage se fait avec du bois de chauffage sur lequel est placé du charbon. La température d'inflammation du coke peut atteindre 600 degrés, il est donc placé en dernier.
- Le charbon de bois brûle mieux car il possède une structure microporeuse.
- Charbon. Une fois brûlé, il devrait atteindre le stade du carbone. Il brûle moins bien que le coke, il est donc utilisé pour forger des produits moins critiques.
- Bois de chauffage. Ils sont brûlés dans la coque afin que les impuretés nocives n'atteignent pas le métal.
- Travailler avec des huiles usées.
Forges à combustible solide
Pour savoir comment fabriquer une forge fonctionnant au combustible solide, vous devez étudier les instructions et décider du type. Un four de forge de type fermé est mieux adapté au travail du charbon ou du bois. Il est fabriqué maison à partir de matériaux de récupération. Une forge à charbon de bois ne nécessite pas d'équipement particulier.
Matériel nécessaire :
- Disponibilité de briques réfractaires.
- Brûleur à injection.
- Capot.
Procédure de fabrication :
- Au stade préparatoire, des dessins pour la forge sont élaborés.
- Un cube est fabriqué à partir de briques. Il reste une cavité avec un trou à l'intérieur.
- Grâce à un renfort, le cadre est sécurisé.
- Un brûleur est installé dans l'une des briques latérales.
- Il y a une capuche sur le dessus, ce qui crée des conditions de travail sûres.

Fabriquer une forge pour chauffer le métal de ses propres mains permet de l'ajuster aux conditions nécessaires. Le matériau utilisé doit uniquement être de haute qualité pour garantir le maintien de la sécurité incendie.
Klaxon à gaz
Une forge à gaz DIY devrait être pratique. Ses murs sont en briques réfractaires.
- Des briques réfractaires sont en préparation.
- Les murs de la forge sont pliés. La quantité de matériel varie en fonction de la complexité et de la taille du cas.
- Les surfaces sont traitées à l'aide d'une scie à métaux.
- Tous les éléments s'emboîtent parfaitement. La présence de fissures n'est pas autorisée.
- Un seuil est installé en partie avant.
- Un trou rectangulaire est découpé à l'arrière. Il sert à la fois à la ventilation et au travail avec des pièces longues.
- Un trou du diamètre approprié est découpé sur le côté pour le brûleur à gaz.
- Le brûleur à gaz est en acier inoxydable. Il s'agit d'un tuyau soudé à une extrémité et avec un treillis métallique à l'autre.
Une telle forge a ses avantages :
- Le four est structurellement plus simple qu'une forge à charbon.
- Alimentation en carburant simple et réglage simple de la température.
- Poids léger.
- Faible coût.
Il existe d'autres types de forges à gaz en métal. Il n'y a pas de différences fondamentales entre eux.

Fournaise à l'huile usagée
Étant donné que les produits pétroliers sont chers, il est avantageux d’utiliser une forge utilisant des huiles usagées. Pour fabriquer la forge pendant l'exploitation minière, des pièces qui ont atteint leur durée de vie utile sont utilisées. Après le traitement des fours, un inconvénient important est apparu : le mélange usé ne s'est pas bien enflammé. Pour éliminer ce problème, un compartiment supplémentaire a été intégré à la forge minière. Ici, l'huile est préchauffée avec du charbon ou du bois. Pour améliorer la combustion, les déchets de carburant passent à travers des filtres et du carburant diesel ou de l'essence y est ajouté.
En conséquence, la forge minière présente les avantages d’une flamme jaune et d’une température stable.
Tu peux le faire toi-même:
- Il est réalisé en briques réfractaires, dimensions : 85×48×40 cm.
- La voûte est réalisée sous la forme d'un arc pour maintenir la température.
- Le corps est entièrement recouvert de feuilles de fer. Une épaisseur de 1,5 mm est utilisée sur les côtés, et le haut et le bas sont doublés de feuilles de 2 mm.
- Les supports sont réalisés à partir d'angles en fonction du poids de la structure.
L'air est pompé dans la chambre par un ventilateur. Un réservoir à déchets est installé sur une colline. De là, le pétrole pénètre dans la chambre par un pipeline, où il est capté par l'air, qui se déplace sous une pression de 2 atm. Les déchets sont broyés et introduits dans la buse.
Pour réduire le temps d'allumage, un élément chauffant est installé dans la forge lors des tests. Le temps d'allumage peut prendre jusqu'à 30 minutes. Mais le mélange chaud brûle bien. Maintenant, vous devez vous assurer que la chamotte ne fond pas.
Schéma du four en production :
Fonderie d'aluminium
L'aluminium, qui possède un degré élevé de ductilité, est un métal non ferreux à faible point de fusion. Une forge pour faire fondre l'aluminium est facile à fabriquer de vos propres mains. Il existe de nombreuses conceptions qui utilisent la fusion au four. Ils n’ont pas de différences fondamentales entre eux.
Instructions étape par étape pour créer une forge pour faire fondre l'aluminium :
- Le corps est en brique. Le matériau est sélectionné sans fissures pour éviter les pertes de chaleur.
- En sélectionnant des chutes de tuyaux en acier, des étagères pour barres de grille sont fabriquées à partir de celles-ci. Les matériaux à bas point de fusion ne peuvent pas être utilisés ici.
- Des bandes d'acier jusqu'à 6 mm d'épaisseur sont sélectionnées et utilisées comme grilles.
- Les barres de grille sont vissées.
- Le coke et le charbon peuvent être utilisés comme combustible.
- L'allumage s'effectue à l'aide d'un chalumeau ou d'un chalumeau à gaz.
Une telle forge de forgeron artisanale ne peut être utilisée qu'en espace ouvert, en raison de l'absence de cheminée. Pendant le fonctionnement, de nombreux gaz sont libérés qui ne devraient pas s'accumuler dans un espace confiné.
Mini klaxon
Une petite forge portable est souvent utile à la ferme. Il peut être utilisé non seulement à la forge, mais aussi dans le garage ou à la datcha.
Pour fabriquer une mini-forge de vos propres mains, vous devez disposer de 2 briques réfractaires, d'une scie à métaux, d'une perceuse d'un diamètre de 8 cm et d'une longueur de 15 cm. Il est conseillé d'avoir une pointe pobedite au bout. Pour fixer la structure, 2 épingles sont préparées de 8 cm de diamètre et 21 cm de long. Lors des travaux, vous aurez besoin de 2 scies cloches de 63 et 26 mm de diamètre.
Le mode opératoire est le suivant :
- 2 briques de 250 mm de long sont sciées en deux.
- Deux moitiés d'une brique sont superposées et 2 trous traversants d'un diamètre de 63 mm sont percés à l'aide d'une scie cloche.
- En plaçant la troisième moitié sous eux, des trous traversants pour les goujons sont percés dans deux coins, en diagonale.
- À l’aide d’épingles, un bloc de trois briques est assemblé et assemblé. Tout d'abord, des rondelles sont placées aux extrémités des goujons et des écrous sont vissés.
- Un trou pour le brûleur est percé entre les deux premières briques à l'aide d'une perceuse annulaire de 26 mm. Il se connecte au passage principal, mais ne touche pas le deuxième mur.
Le brûleur est inséré dans ce trou et allumé. Tout métal est introduit dans le passage principal, qui tombe sous la flamme et chauffe en quelques secondes.
Fabriquer une forge à partir d'un poêle ventral
Essentiellement, il s’agit du même poêle ventral, mais sans la grille. L'apparence des forgerons peut prendre la forme d'un cube, d'un parallélépipède et d'un cylindre. Après avoir nettoyé la grille, l'air ne provient pas de l'espace situé en dessous, mais est soufflé à travers un canal latéral réglable. Le four chauffe ainsi mieux. Il retient les gaz plus longtemps, ce qui augmente également la chaleur.
Le procédé de fabrication est le suivant :
- À partir d'un tuyau d'un diamètre allant jusqu'à 300 mm, un anneau de 100 mm de large est découpé. Cette partie s'appelle un collier.
- Une feuille de 4 mm d'épaisseur est prise et un cercle égal au diamètre du collier en est découpé. Ce sera la porte.
- Un morceau de tuyau d'alimentation en air est coupé. Il peut aller de 76 à 102 mm.
- L'amortisseur y est inséré à l'aide d'une poignée, d'un ressort et d'un écrou.
- Une bande de 30 mm de large et de longueur égale au périmètre de la porte est découpée dans une tôle de 3 mm.
- La bande s'adapte autour de la porte et se brûle.
- Un trou est percé sur le côté de la porte et un tuyau d'alimentation en air y est soudé.
- Grâce à un dispositif de verrouillage, la porte est fixée au collier.
- Cet appareil est installé sur le foyer à une distance de 100 mm du bas.
- A l'arrière, en haut, un trou est creusé et une cheminée est installée.
Les inconvénients d'un tel poêle incluent l'absence de cendrier. Cependant, une combustion plus longue entraîne une meilleure combustion des déchets solides. Le retrait des cendres peut être effectué moins fréquemment.
Fabriquer une forge à partir d'un seau
La forge à godets est également conçue pour faire fondre l'aluminium. Pour ce faire, vous avez besoin d'un seau d'une capacité de 10 à 20 litres. De plus, du gypse et du sable. Ce mélange est déposé au fond du seau.
Instructions pas à pas pour une forge fabriquée à partir d'un seau de vos propres mains :
- Le godet sélectionné ne doit pas être galvanisé. Cela est dû au fait que le zinc, lorsqu'il est chauffé, libère des gaz nocifs. Le conteneur est en métal ordinaire.
- Un mélange de gypse et de sable de 5 cm d'épaisseur est placé au fond. Le rapport est de 1:2. Tout d'abord, un tel mélange se forme au fond. Après séchage, les parois intérieures du seau en sont traitées. Le temps de séchage est de 15 à 20 minutes.
- Une raclette à eau est installée en dessous, à travers laquelle l'air est fourni avec un sèche-cheveux.
- Un creuset est inséré dans le seau.
- Le processus d'allumage commence.
- L'aluminium est placé dans un creuset et fond sous l'effet de la chaleur.
De petits objets peuvent être coulés de cette manière.
Une forge de forgeron fabriquée à la main est un appareil ménager indispensable. Cependant, vous devez d’abord lire les instructions d’utilisation. Achetez les dessins nécessaires. Le risque d'incendie doit être complètement éliminé. Le bon endroit a été choisi pour cela. Travailler le métal chaud apportera non seulement du plaisir, mais aussi des avantages.
La forge est indispensable dans les ateliers et les forges pour créer des produits en acier en forgeant du métal chaud à des températures allant jusqu'à +1200°C. Il existe de nombreux modèles différents avec une conception simple et pour différents types de carburant avec des caractéristiques différentes. Comment ne pas se tromper en les choisissant et les construire correctement ?
Structurellement, la forge se compose des éléments suivants :
- base en matériau ininflammable et à haute résistance;
- table ignifuge;
- chambre à combustible avec grille ;
- chambre à air et drainage ;
- conduit d'entrée;
- vanne d'air pour régler l'alimentation en air;
- caméras en forme de tente;
- ouverture pour alimenter les pièces longues;
- parapluie clairon;
- chambre gaz-air;
- bains pour durcir les pièces;
- cheminée pour l'évacuation des produits de combustion;
- four amovible.
Principe d'opération
Le principe de fonctionnement de la forge repose sur la réaction chimique de combustion du carbone qui, lorsqu'il réagit avec l'oxygène, forme du dioxyde de carbone avec dégagement de chaleur. De plus, la récupération du métal se produit, ce qui constitue un aspect très important pour la formation de pièces homogènes et à haute résistance.
Pour maintenir un niveau optimal de combustion et de température, des conduits d'air et des chambres à air sont installés à l'intérieur de la chambre à carburant, qui pompent avec force de l'oxygène pur. De ce fait, il est possible d'obtenir des températures supérieures à +1000°C, inaccessibles avec la combustion conventionnelle de combustible solide (charbon ou bois).
Dans le même temps, grâce à la technologie de gonflage, le volume d'air est sélectionné de manière à ce qu'il y ait toujours un léger manque d'oxygène pour que la réaction d'oxydation se produise. Autrement dit, il faut sélectionner un mode de fonctionnement pour éviter la combustion du métal.
Le temps pendant lequel la pièce fondue reste dans le four doit également être limité, car dans une atmosphère de dioxyde de carbone, le métal commencera à réagir avec lui et formera un alliage à haute résistance et fragilité accrue. Ces conséquences négatives peuvent être évitées en introduisant de l'oxygène supplémentaire dans la chambre en quantité telle que le dioxyde de carbone ait le temps de réagir complètement.
Objectif et utilisations
Une forge de bricolage est fabriquée en fonction de son application principale et peut être configurée en conséquence pour des tâches spécifiques. Par conséquent, il est important de comprendre à quoi est destinée chacune de ses parties structurelles :
- un foyer avec une grille, une chambre à air, une vanne et un tuyau sont utilisés pour brûler du combustible et chauffer la pièce métallique en fonction des exigences de température, ils peuvent avoir une conception ouverte ou fermée et ne pas non plus être équipés de pressurisation d'air ;
- le drainage de l'air est utilisé pour réguler l'apport d'oxygène et éviter la fragilisation du métal, vous permet de créer des conditions optimales lors du chauffage et de la fusion de la pièce ;
- une tente ou un parapluie avec une cheminée est utilisé pour éliminer le monoxyde de carbone et d'autres produits de combustion pouvant nuire à la santé humaine ;
- un bain de trempe est nécessaire au refroidissement rapide du métal et à son acquisition de propriétés plastiques et de résistance optimales ;
- un capuchon ou un creuset résistant à la chaleur, utilisé pour élargir la zone de chauffage uniforme, qui permet de faire fondre efficacement du métal (généralement des métaux précieux non ferreux) dans un creuset ;
- chambre gaz-air, utilisée pour sécher l'air, le purifier des impuretés, ainsi que pour introduire des éléments d'alliage, conçue pour fabriquer des produits de haute qualité avec des caractéristiques spécifiées conformément à un schéma de référence spécifique d'états et de phases ;
- la table sert à y placer tous les éléments de la forge, ainsi qu'au refroidissement partiel des pièces, c'est un élément obligatoire de la conception ;
La forge est utilisée aux fins suivantes :
- chauffer le métal pour un forgeage ultérieur ou d'autres types de traitement ;
- fondre sous des formes spéciales;
- traitement thermique pour améliorer certaines propriétés.
Classement des forges
Avant de réaliser une forge, vous devez vous familiariser avec leur classification afin de sélectionner l'option de conception la plus appropriée. Le classement s'effectue selon les critères suivants :
- par type de carburant utilisé ;
- par type de construction;
- selon la taille du foyer.
Types de forges par type de combustible utilisé
Selon le type de combustible utilisé, les forges sont réparties dans les types suivants :
- gaz;
- combustible solide;
- sur le carburant liquide.

Les fournaises à gaz ont la conception la plus simple et sont peu coûteuses à réparer et à entretenir. Ils se caractérisent par un poids minimal, ce qui leur permet d'être portables ou compacts.
Les fours à combustible solide se distinguent par leur capacité à obtenir les températures de chauffage les plus élevées possibles, le coût relativement faible des matériaux de construction et leur fonctionnement sans prétention. Pour leur allumage, il est permis d'utiliser les types de combustibles suivants :
- le charbon ou le coke, caractérisé par un coût élevé et une efficacité accrue (la consommation est jusqu'à 5 fois inférieure à celle du charbon), il ne contient pas d'impuretés étrangères, s'enflamme à des températures supérieures à +450°C ;
- Le charbon, le combustible le plus courant et le plus efficace, émet du gaz de coke lorsqu'il est brûlé, donc lors de l'allumage, il faut attendre qu'il soit complètement évaporé ; il convient pour forger divers éléments décoratifs ou pièces de qualité moyenne ;
- le charbon de bois a une température d'inflammation minimale par rapport aux autres types de combustibles, mais il brûle rapidement et se caractérise par une consommation accrue, il est donc utilisé efficacement pour le petit bois.
Il est permis d'utiliser du carburant diesel, du fioul ou des huiles usées comme carburant liquide. Dans le même temps, il est important de le pré-nettoyer, car la présence d'impuretés provoquera une flamme instable et la libération de composés nocifs dans l'atmosphère.
Cela rend également difficile l’entretien des équipements en raison de blocages fréquents.
Classification par caractéristiques de conception
Une forge artisanale peut être classée selon ses caractéristiques de conception comme suit :
- par méthode d'installation : portable ou fixe ;
- selon la conception de la chambre de combustion : type fermé ou ouvert ;
- selon l'emplacement du boost : avec une buse latérale ou centrale.
Types de forges par taille de foyer
Il existe différentes tailles de forges à foyer : petites, moyennes et grandes. Ils sont déterminés par l'efficacité de fonctionnement de l'installation et dépendent entièrement de l'intensité de la consommation de carburant et des modes de fonctionnement de la chambre à combustible. L'efficacité optimale du débit de carburant est de 1 à 1,5 m/s.
La productivité de la forge est directement proportionnelle à la quantité de tension et à la surface du foyer. Dans ce cas, la tension minimale est considérée comme étant comprise entre 100 et 150 kg/m 2 h. Les valeurs en dehors de cette fourchette ne sont pas économiquement viables.
Comment fabriquer une forge de forgeron ?
Avant de fabriquer une forge de vos propres mains, vous devez préparer le matériel et les outils nécessaires. Cela minimisera les coûts de temps
Instructions pour créer une forge mobile à combustible solide
Avant de commencer les travaux, vous devez rassembler les outils suivants :
- Machine de soudage;
- percer;
- déposer;
- jeu de clés;
- couteau à mastic;
- roulette;
- niveau;
- serrer;
- marqueur;
- bulgare

Après avoir préparé un dessin d'une forge, vous devez acheter des matériaux pour sa construction :
- tôle d'acier de 2-3 mm d'épaisseur (recommandé 09G2S) ;
- roues pivotantes 4 pièces ;
- tuyaux profilés carrés d'une épaisseur de paroi d'au moins 2 mm ;
- ciment réfractaire;
- escargot aérien;
- éléments de fixation : boulons et écrous ;
- tuyau en acier inoxydable le long du diamètre de la sortie de la volute ;
- adaptateur.
Une forge à charbon mobile de type ouvert est fabriquée étape par étape comme suit :
- Nous prenons une tôle d'acier et la marquons avec un marqueur en fonction de la taille du bureau.
- Nous découpons le plateau avec une meuleuse et nettoyons les bords avec une lime.
- Nous marquons un trou rectangulaire sur la tôle découpée pour l'embouchure de la forge et le découpons avec une meuleuse.
- Nous prenons la deuxième tôle d'acier et marquons les éléments des pièces pour la bouche trapézoïdale de la forge.
- Nous découpons les éléments de ventilation puis les soudons en une seule structure.
- Nous soudons la bouche à la surface de travail de la table à la place du trou découpé.
- Nous retournons la structure avec la bouche vers le bas, marquons les emplacements pour l'emplacement des murs pour le placement des charbons.
- Nous découpons les côtés de la surface de travail de la table en acier.
- Nous soudons les côtés de manière à ce qu'il n'y ait pas d'espace au niveau des coutures et que la couture elle-même soit solide et continue, nous centrons avec précision les éléments structurels.
- Pour la partie inférieure de l'évent, nous découpons des parois en acier pour l'alimentation des conduits d'air, puis les soudons.
- Nous réalisons un fond amovible pour l'évent, conçu pour éliminer les cendres.
- Nous y attachons la pédale à l'aide de leviers.
- Sur le mur d'alimentation en air d'un tuyau, nous faisons un trou le long du diamètre du tuyau.
- Nous découpons des éléments dans des tubes profilés en acier et soudons un cadre pour fixer la surface de travail.
- Au bas du cadre, nous soudons une barre pour fixer l'escargot, puis la fixons avec des boulons.
- Nous préparons le tuyau pour le conduit d'air.
- Nous fixons le conduit d'air à la cochlée et à l'évent si nécessaire, nous fournissons une fixation supplémentaire pour renforcer la structure.
- Nous fixons les roues pivotantes au bas du cadre avec des boulons.
- Nous enduisons les joints de jointure avec du mastic ignifuge.
- Nous formons une couche réfractaire sur la surface de travail du foyer à base de mortier de ciment réfractaire.
Une forge à charbon doit être testée en la chauffant aux températures de fonctionnement, mais seulement après que la couche de ciment ait complètement durci.
Instructions pas à pas pour fabriquer une forge à gaz
Pour fabriquer une forge à gaz, vous devez préparer à l'avance les matériaux suivants :
- brique réfractaire;
- tôles d'acier résistant à la chaleur d'une épaisseur d'au moins 5 mm ;
- tôles fines en acier inoxydable (épaisseur jusqu'à 2 mm) pour le revêtement extérieur ;
- tubes profilés en acier;
- tuyaux de cheminée en acier inoxydable;
- mastic ignifuge;
- brûleurs standards utilisés dans les chaudières à gaz ;
- ventilateur pour pomper l'air.
Vous aurez également besoin des outils suivants :
- Machine de soudage;
- Bulgare;
- percer;
- déposer;
- roulette;
- marqueur.

Une forge à gaz est fabriquée dans l'ordre suivant :
- Nous prenons des briques réfractaires et en construisons le corps de la forge. Si nécessaire, nous traitons les extrémités avec une meuleuse dotée d'un accessoire spécial pour béton afin d'assurer un joint étanche.
- Dans la partie avant de la structure, nous créons une petite marche en briques réfractaires, conçue pour maintenir la température optimale.
- Nous faisons un trou rectangulaire à l'arrière pour la ventilation.
- Nous fabriquons une base à partir d'une tôle d'acier épaisse aux dimensions du corps en brique de la forge.
- Nous soudons des tubes profilés aux extrémités de la tôle afin que les briques à l'intérieur soient immobiles.
- Sur le côté de la chambre de combustion, nous avons percé un trou pour alimenter un tuyau de gaz avec un brûleur installé.
- Nous avons découpé la partie supérieure de la forge dans une tôle d'acier épaisse.
- Nous soudons les coins du corps en bas et en haut.
- Nous perçons un trou dans les coins et resserrons les parties inférieure et supérieure de la forge avec des épingles.
- Nous découpons un support pour la forge dans des tubes profilés, puis soudons toutes les pièces conformément au dessin.
- Nous installons la forge sur le stand.
- Nous attachons un tuyau à la chambre pour éliminer les produits de combustion.
- Nous plaçons un brûleur à gaz à l'intérieur de la chambre et le fixons au point d'entrée dans la chambre.
- L'extérieur du corps est gainé de tôle d'acier mince, après avoir préalablement découpé dans les tôles des pièces aux dimensions requises. Nous soudons toutes les coutures avec une couture continue.
L'autofabrication d'une forge est non seulement un processus peu coûteux et relativement simple, mais vous permet également d'obtenir une installation adaptée à des besoins spécifiques.
Une forge est un équipement très utile qui peut aider un artisan à fabriquer divers produits métalliques. Avoir une forge peut résoudre de nombreux problèmes liés à la réparation d’anciens produits ou à la fabrication de nouveaux produits.
Bien entendu, il est toujours possible d'acheter des équipements d'usine de ce type si le besoin s'en fait sentir. Vous pouvez également recourir à l'aide d'ateliers de forgeron, que l'on trouve certainement dans presque toutes les localités. Mais il existe une opportunité de créer une forge de vos propres mains. Ayant certaines compétences dans la manipulation des outils qui aideront dans ce domaine, il n'y aura rien de difficile à cela. Vous devez faire un effort, trouver tous les composants, les outils nécessaires, y consacrer du temps, mais vous aurez votre propre forge à utiliser, que vous pourrez installer dans votre atelier.
Cet appareil est utilisé par les artisans pour les opérations suivantes : chauffer le métal avant de le forger, de le cimenter, ainsi que d'autres opérations. Dans des conditions artisanales, un maître utilisant une forge est capable d'atteindre des températures allant jusqu'à 1 100 degrés, dans certains cas même jusqu'à 1 200. Les forges sont généralement de gros équipements fixes, mais il existe également de petits exemples portables. En principe, créer votre propre forge n'est pas si difficile. Des conseils pour créer une telle forge seront donnés dans l'article ci-dessous.
Pour utiliser une forge de conception traditionnelle, vous devez posséder certaines compétences et expériences, et vous assurer également d'avoir les connaissances nécessaires sur le combustible le plus approprié à choisir. Si vous utilisez un combustible tel que le gaz naturel pour le chauffage, il est peu probable que cela vous permette de forger quelque chose d'important, mais cela contribuera à simplifier considérablement la conception. Le fait est qu'une forge à gaz peut être assemblée en une demi-heure ou une heure, en utilisant uniquement six briques en argile réfractaire et quelques morceaux d'acier. Parallèlement, la qualité et la température du chauffage vous permettront de travailler avec des métaux non ferreux et des petits produits.
Dispositif de klaxon
Afin de passer aux astuces pour créer une forge maison, vous devez d'abord vous familiariser avec la structure traditionnelle d'un tel appareil :
Comment fonctionne la forge
Pour qu'un utilisateur puisse fabriquer lui-même une forge, il doit d'abord comprendre le principe de son fonctionnement, afin de pouvoir ensuite travailler avec ce qu'il possède sans perdre en qualité. Il existe une réaction chimique pour la combustion du carbone : 2C+O2=2СО2+188,1 kcal. C'est ce qui sous-tend le fonctionnement de tout appareil. La réaction montre immédiatement que le carbone est un agent réducteur assez puissant, c'est-à-dire qu'il se combine avidement avec l'oxygène.
Cette capacité réductrice du carbone est en partie utilisée dans la forge pour empêcher l'oxydation de la pièce, c'est-à-dire pour empêcher le métal présent dans l'appareil de brûler. Une autre propriété très importante du carbone est son pouvoir calorifique élevé. Cette propriété est que si vous soufflez suffisamment d'air dans la masse de carburant, ce qui serait suffisant pour le carbone, vous pouvez alors le brûler assez rapidement, ce qui entraînera un dégagement de chaleur supplémentaire. Cela lui permettra de développer une température plus élevée.
À empêcher l'oxydation du métal, le souffle dans la forge doit être réglé pour que le combustible manque un peu d'oxygène. Mais il ne faut pas oublier que si la pièce est surexposée, une carburation se produira. Cela signifie que le métal deviendra trop sec, c'est-à-dire cassant.
Il convient de dire quelques mots sur les différents types de combustibles pouvant être utilisés pour faire fonctionner une forge. Ce sont des conseils qui vous aideront mieux vaut s'occuper des forges :

Forges de bricolage
Vous pouvez passer à la procédure de fabrication de votre propre appareil de ce type. Vous trouverez ci-dessous quelques-unes des options les plus populaires pour fabriquer une forge de vos propres mains. Ils diffèrent par leur structure, mais le principe de fonctionnement est similaire pour tous.
Mini klaxon
Une si petite forge de forgeron composée de six briques est la meilleure option pour les forgerons débutants.
Les étagères de la grille peuvent être fabriquées à partir de chutes de tuyaux en acier ordinaires, tandis que les grilles elles-mêmes peuvent être constituées de bandes d'acier de 4 à 6 mm d'épaisseur. La figure montre que les barres de la grille doivent être tordues en biais avec une vis afin de capter le flux de souffle. Les types de combustibles suivants conviennent pour cette option : le charbon ou le coke. Le soufflage et l'allumage s'effectuent au chalumeau, au gaz ou au brûleur gaz-air.
Il ne faut pas oublier que lors de l'utilisation d'un chalumeau, il faut mettre une cloison, avec une fenêtre sous la buse, en amiante entre la lampe et l'appareil. Cela doit être fait car la forge émet intensément de la chaleur, ce qui peut faire exploser la lampe. Cette forge artisanale doit être utilisée à l’extérieur, car elle ne dispose pas de parasol avec cheminée.
Vous pouvez fabriquer une forge de forgeron portable de vos propres mains à partir d'un col de cygne. La conception peut être comprise à partir de la figure ci-jointe. Le revêtement ici est du sable réfractaire, mélangé à de la marne réfractaire.
La suralimentation ne doit pas nécessairement être effectuée avec le ventilateur d'une sirène manuelle, comme indiqué ci-dessus. En principe, vous pouvez utiliser n'importe quel appareil approprié à portée de main. Il peut être fixé à l'aide d'une onduleuse métallique. Soit dit en passant, cela rendra le travail avec des éléments longs un peu plus pratique. Dans ce cas, vous devrez utiliser une purge d'air à l'extrémité aveugle du conduit.
Bien entendu, une telle forge portable a plus de capacités que la forge artisanale à six briques décrite ci-dessus, car son espace de travail est plus grand et ouvert au sommet. Mais il convient de mentionner l'existant inconvénients d'un tel appareil :
- Une telle forge a une conception non séparable et lors du nettoyage de la tuyère, les dépôts de carbone tombent. En conséquence, le conduit d'air est perforé. Pour nettoyer, il faut casser la doublure.
- Cette forge artisanale ne peut brûler que du charbon de bois ou du coke.
- Son fonctionnement est très coûteux : la consommation de carbone est comparable à la même consommation de charbon dans les vraies forges.
- Il peut fonctionner à des températures relativement basses : seulement jusqu'à 900 degrés.
Stationnaire
Il s'agit de la version la plus sérieuse, la plus complexe et la plus productive d'une forge artisanale. Il vous permet d'effectuer manipulations plus complexes.
Conception
La séquence de fabrication peut être identifiée en examinant la figure ci-dessous.
Les photographies sont numérotées afin que vous puissiez suivre l'ensemble du processus de construction d'une telle forge artisanale.
Petit conseil aux artisans qui réaliseront une telle forge : il ne faut pas pressuriser la douche à air avec un aspirateur. Dans ce cas, il est possible que le carburant va exploser. Il est préférable de trouver un escargot sur un poêle de voiture et d'utiliser ensuite cet appareil particulier. Le drainage pour réguler le soufflage ne convient pas non plus, car le boost sera trop faible. Il est préférable d'intégrer le papillon des gaz dans le conduit d'air et le couvercle inférieur de la tuyère ne doit être amovible que pour un nettoyage ultérieur.