Comment fabriquer votre propre bloc de béton. Comment gagner de l'argent en créant des éléments de base. Comment mélanger une solution pour créer un parpaing
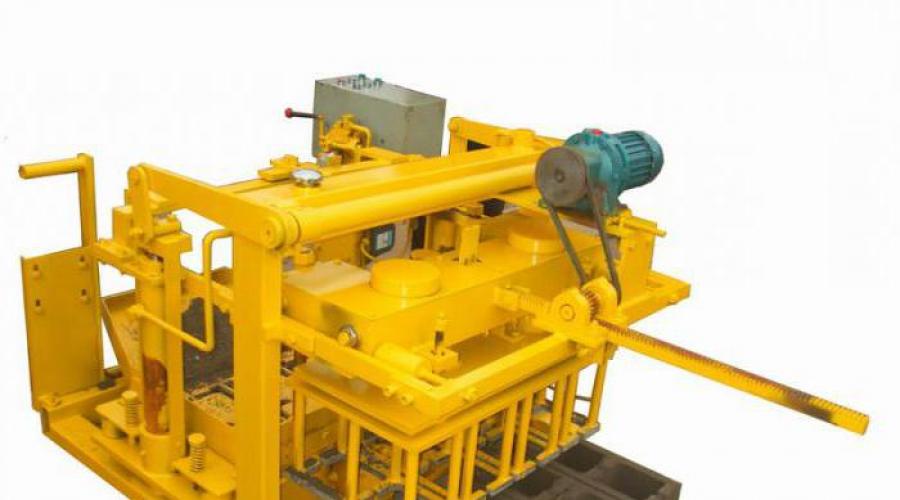
Les blocs de construction sont un matériau courant pour la construction de structures à des fins diverses. Ils diffèrent par leur taille, leurs composants et leur méthode de fabrication, mais ils sont tous populaires. matériau de construction. Les blocs de construction sont fabriqués dans des conditions industrielles, dans ménage Ils fabriquent également des produits en béton et des parpaings, ce qui nécessite un fabricant de blocs de construction DIY. En fonction du matériau utilisé, ces produits sont divisés dans les types suivants :
- béton de laitier;
- béton;
- béton cellulaire;
- béton mousse de fibres;
- béton de polystyrène.
Les parpaings comme matériau de construction
Le parpaing est standard produits en béton, seulement au lieu de gravier lourd et de pierre concassée, une charge sous forme de scories résiduaires est utilisée. Ce remplacement confère au matériau une légèreté par rapport au béton et des propriétés d'isolation thermique supplémentaires, puisque les scories se comparent avantageusement aux pierres concassées lourdes et denses en termes de conductivité thermique.
La fabrication de parpaings nécessite un dosage précis des composants de la solution, à savoir :
- qualité de ciment non inférieure à 400 ou 500, prendre une partie (seau);
- sable de carrière, mélanger 3 parties (seaux);
- laitier, brique calcinée, argile expansée, ce matériau est ajouté à raison de 5 parties (seaux);
- eau.
Pour obtenir des parpaings de même qualité qu'en usine, utilisez une solution de consistance moyennement visqueuse. Une solution liquide réduira la résistance des blocs, et une solution épaisse créera des vides incontrôlables à l'intérieur lorsqu'elle durcira.
Blocs de béton
Des blocs de construction en ciment, sable et pierre concassée sont utilisés pour la construction de murs et d'autres structures si une résistance accrue est requise. Le rapport des composants pour le béton standard est pris dans le rapport 1 : 3 : 6, autres options mélange de béton sont décrits dans les manuels du constructeur et dépendent de la marque de ciment utilisée, de la taille des granulats et du type de sable.
Blocs de sciure de bois de construction
Pour construction bâtiments résidentiels, datchas, chalets utilisent la lumière et la chaleur matériau du mur de la sciure de bois, du sable et de l'eau. Le composant liant de la solution est la chaux. La quantité de matière ajoutée à la solution modifie les propriétés du produit final. Une augmentation de la masse de sciure entraîne une augmentation propriétés d'isolation thermique, mais contribue à une diminution de la force. Avec une augmentation de la quantité de sable dans la solution, la résistance augmente, tandis que la limite de résistance au gel augmente, ce qui augmente les propriétés opérationnelles du matériau. Les blocs sont largement utilisés dans la construction de logements privés comme revêtement pour les structures isolantes.
Les principaux avantages des blocs sont la disponibilité des matériaux et leur prix bas, une longue durée de vie sans destruction, le respect de l'environnement du matériau et la facilité de production. L'installation pour la production de blocs de construction de vos propres mains est disponible en fabrication et est populaire parmi les artisans à domicile. Le béton de sciure est différent temps accru séchage, c'est pourquoi plusieurs trous traversants sont pratiqués à l'intérieur du produit pour améliorer la circulation de l'air.
Les dimensions des blocs de sciure ne sont pas strictement réglementées ; leur largeur est prise comme un multiple de l'épaisseur de la paroi. Si nous parlons de tailles standard, les blocs sont fabriqués selon deux fois l'épaisseur de la brique (140 mm - 65x2 + 10 cm). Lors de la fabrication des pierres de sciure de bois, les ingrédients secs sont d'abord mélangés, puis de l'eau est ajoutée et des mélangeurs à mortier sont utilisés pour le travail.
Blocs de construction en béton cellulaire
Leur préparation implique un processus complexe de saturation de la solution en gaz, difficile à reproduire à la maison. Les blocs de construction en béton cellulaire se distinguent par leur légèreté, leurs propriétés élevées d'isolation phonique et thermique.
Produits en béton fibré pour la maçonnerie
Le béton cellulaire fibré est par nature un matériau de mur respectueux de l’environnement contenant du sable, de la mousse et du ciment. Des machines de haute technologie pour blocs de construction pulvérisent de la mousse dans la masse de la solution, ce qui forme des particules d'espace fermées et uniformes. Pour augmenter la résistance des blocs, les fabricants utilisent un renfort en fibres de polyamide sur toute la masse. Ce matériau mural est très résistant, ne pourrit pas, est léger et durable.
Leurs blocs de béton en mousse de fibres sont produits différentes tailles. Pour murs porteurs utilisez 20x30x60 cm, qui pèse 22 kg. Pour construire un mur de briques de même taille, vous aurez besoin de 18 pierres, elles pèseront 72 kg. Des blocs de plus petite épaisseur (10 cm) sont utilisés dans la construction de murs à l'intérieur d'un bâtiment, de cloisons, et ils sont utilisés pour isoler les sols et les murs. La conductivité thermique du béton cellulaire fibré est 2,7 fois inférieure à celle de la brique et 2 fois inférieure à celle du béton de laitier et des coquillages.
Les grandes tailles de blocs réduisent l'application mortier ciment-sable pour la maçonnerie 20 fois par rapport à la construction d'un mur avec de petites pierres. Le béton de mousse de fibres ne brûle pas, ne change pas de forme lorsqu'il est exposé à des températures élevées et n'émet pas d'impuretés nocives lorsqu'il est chauffé.
Blocs de béton en polystyrène
Le matériau est classé comme un autre type de blocs de béton pour murs légers. Il se distingue du béton standard par de meilleures performances et des coûts de production réduits. Le matériau de mur innovant surpasse en poids tout le béton léger connu, même le béton mousse est une fois et demie plus lourd. Grâce à cet indicateur, les maisons sont construites sans les fondations massives habituelles et le coût de transport des matériaux est réduit.
La production de blocs de mousse de polystyrène consiste à combiner soigneusement du ciment, du sable, des particules de mousse de polystyrène et des additifs spéciaux pour retenir l'air dans la masse totale. Autre caractéristiques physiques Le matériau le place au-dessus des matériaux conventionnels. La faible absorption d'eau et la perméabilité à la vapeur rendent le béton de polystyrène expansé résistant aux gels et dégels répétés, ce qui affecte la durabilité des structures construites. Après la construction des murs matériaux standards un léger retrait se produit tout au long de l’année. Dans le cas des blocs de mousse de polystyrène, ils n'attendent pas aussi longtemps.
Installation pour la production de blocs de construction de vos propres mains
Pour la fabrication de structures de construction appliquer appareil spécial, fonctionnant sur le principe d'un processeur de vibrations.
Une telle machine vibrante ou table vibrante est conçue indépendamment. Une installation faite maison pour la production de blocs de construction réduit considérablement le coût des blocs et, par conséquent, des murs de la maison.
Préparation de la solution
La solution est préparée à partir de sable, de ciment, d'eau et de filler, qui est utilisé comme divers matériaux, comme écrit ci-dessus. Pour vérifier la consistance de la solution et sa fluidité, jetez-en une petite quantité sur le sol. Un mélange de haute qualité ne se répand pas en ruisseaux aqueux ; lorsqu'il est serré dans un poing, il se colle en un morceau.
La production de parpaings implique un nettoyage approfondi des scories des débris étrangers et les parties de charbon non brûlées ne doivent pas pénétrer dans la solution. Parfois, du gypse est ajouté à la solution. Dans ce cas, trois parties de laitier et une partie de gypse sont mélangées et de l'eau est introduite en même temps. Cette solution est rapide à utiliser car le plâtre durcit en quelques minutes. Les scories sont préalablement trempées dans de l'eau avant d'être mélangées. Pour améliorer la qualité des produits de sortie, des additifs plastifiants modernes sont ajoutés à la solution. Leur action augmente la résistance au gel, la résistance à l’eau et la résistance mécanique des blocs.
Selon le but, deux types de blocs de béton sont fabriqués : pleins et creux. Les premiers sont utilisés pour la construction structures durables, murs porteurs, fondations. Le deuxième type de blocs est utilisé comme matériau de cloison ; il isole bien du froid et des bruits extérieurs.
Fabriquer des blocs de béton sans table vibrante
Parmi les deux technologies, l’utilisation d’un coffrage en bois, conçu pour permettre à la solution de s’écouler naturellement sans vibration, est toujours en demande. La mise en solution de la forme préparée s'effectue en plusieurs étapes. Tout d'abord, le récipient est rempli d'un tiers de la solution, après quoi les parois du moule sont soigneusement tapotées avec un marteau autour du périmètre pour un retrait de haute qualité. mortier de béton. Au cours des deux étapes suivantes, la solution est ajoutée selon la technologie originale jusqu'à ce que le moule soit rempli. La production de blocs de construction avec des vides implique l'insertion de deux bouteilles en plastique avec de l'eau, qui l'enlève après prise.
Les formes sont laissées sécher pendant 2 à 5 jours. Retirez ensuite soigneusement les blocs de conception pliable et disposés sur des palettes jusqu'à complètement sec. Avec cette méthode de production, il n’est pas nécessaire d’acheter.
Les outils et équipements suivants seront nécessaires : un tamis pour tamiser le sable, des moules pour le mortier, une auge pour mélanger ou une bétonnière, un marteau pour tarauder, un seau, une pelle, une truelle et des plateaux de séchage.
Procede de fabrication de blocs a l'aide d'une machine vibrante
Pour ce faire, achetez ou fabriquez votre propre machine vibrante pour parpaings. Une forme métallique spéciale est installée sur le plan de la machine et un mélange de béton avec des scories y est versé au tiers. Après cela, une table vibrante est connectée à l'action pendant 20 secondes maximum, ce qui vous permet d'éliminer toutes les bulles d'air inutiles de la solution et le ciment recevra un bon retrait. La solution est versée trois fois dans le moule. Les blocs sont démoulés de la même manière que pour la méthode de fabrication sans vibrations.
Le parpaing ne tolère pas le dessèchement temps chaud sous les rayons du soleil, donc par temps chaud, il est arrosé d'eau et recouvert de toile cirée ou de cellophane afin que l'humidité ne s'évapore pas si activement. Les blocs de béton formés et complètement séchés acquièrent une résistance de 100 % au 28ème jour et sont ensuite prêts à être utilisés dans la construction.
Caractéristiques de la fabrication de parpaings
Les moules sont fabriqués indépendamment, en métal ou en bois ; la largeur des planches est d'au moins 190-200 mm. Ils sont reliés en une structure préfabriquée dont les parties latérales sont détachées pour retirer le bloc fini. DANS conception générale pas plus de 6 cellules sont combinées pour poser du béton. Conception prête posé sur un matériau dense et imperméable, tel qu'une toile cirée, formant le fond du moule.
Si le bois est choisi comme matériau pour le moule, il est prétraité avec des imprégnations ou des apprêts pour augmenter la résistance à l'humidité. Les moules sont fabriqués à partir de bois sec. Ces conditions sont remplies, sinon pendant les travaux l'arbre s'éloignera de l'eau et changera taille géométrique bloc. Les dimensions standards des pierres sont de 400x200x200 mm, mais chaque fabricant privé fabrique des blocs pour sa propre construction.
Pour les matrices métalliques, des feuilles d'une épaisseur ne dépassant pas 3 à 4 mm sont prises. Lors du soudage d'une structure, toutes les soudures sont réalisées depuis l'extérieur afin de ne pas arrondir les coins du bloc. Les vides à l'intérieur du parpaing sont réalisés à l'aide de segments tuyaux métalliques diamètre approprié, par exemple 80 mm. La distance entre les canalisations et la distance aux murs sont contrôlées, la composition est soudée en bandes pour plus de rigidité et de fixation.
Si un équipement est fabriqué pour la production de blocs de construction, alors lors de la fixation du vibrateur à la table, après avoir serré les écrous, ceux-ci sont encore légèrement soudés. Le moteur doit fermer boîtier de protection de tout matériau provenant d'éclaboussures de solution, d'eau, de poussière.
Technologie pour la production de blocs de béton de sciure
Les matériaux disponibles ne sont pas prétraités et vous pouvez les acheter à tout moment. quincaillerie, par conséquent, la production de blocs à partir de sable, de chaux et de sciure de bois commence immédiatement après l'achat. Pour mélanger la solution, utilisez une bétonnière ou un malaxeur à mortier, car le mélange se fait à la main déchets de bois difficile.
La sciure de bois sèche, passée au tamis grossier, est mélangée à du sable et du ciment. De la chaux ou de la pâte d'argile préparée est ajoutée à la solution. Le mélange obtenu est bien mélangé et ensuite seulement de l'eau est ajoutée, en la versant progressivement par petites portions. Pour déterminer si la solution est prête, pressez-la dans votre main, après quoi des empreintes digitales doivent rester sur la masse, ce qui indique les proportions correctes.
Avant de remplir les formulaires avec la solution, ils sont remplis fine couche sciure Les trous internes dans les blocs sont réalisés à l'aide de bouchons en bois d'environ 70 à 80 mm, qui sont installés dans la matrice avant de verser la solution. Le matériau des blocs de construction est placé étroitement dans le moule à l’aide d’un pilon spécial. Le récipient est rempli jusqu'en haut et laissé sécher pendant trois jours. Passé ce délai, la solution gagne environ 40 % de sa résistance requise.
Les moules sont démontés et les blocs sont séchés pendant quatre jours supplémentaires, après quoi la résistance atteint 70 % de la limite requise. Les produits finis sont transférés sur des palettes et protégés des rayons de soleil. Le séchage des blocs est plus rapide si vous laissez des espaces entre les produits pendant le stockage. Il est conseillé de placer les plateaux dans un courant d'air ou d'utiliser un ventilateur pour une ventilation forcée.
Opilko Blocs de béton gagnent 100% de résistance après 3 mois de séchage, mais ils peuvent être utilisés après un mois d'aération. A l'heure actuelle, leur force est de 90 %.
Machines et équipements
Pour fabriquer le nombre de blocs requis pour la construction, une machine de vibroformeuse prête à l'emploi est achetée. La marque TL-105 a de bonnes performances. Et bien que sa puissance ne soit que de 0,55 kW, elle produit environ 150 blocs de béton avec différents granulats par heure de fonctionnement. Son coût approximatif sur le marché est d'environ 42 800 roubles. Les fabricants modernes d'équipements de machines-outils produisent de nombreux types de machines pour la production de blocs dotés de fonctions supplémentaires. Les prix des machines sont différents et le coût des blocs de construction en dépend directement.
Pour les petites constructions privées, une machine vibrante 1IKS convient; elle coûte environ 17 000 roubles, la puissance n'est que de 0,15 kW, un tel équipement produit 30 blocs par heure. Lors de l'achat d'une machine, tenez compte du niveau de production de blocs pour les besoins de la construction.
En conclusion, il convient de noter que fabriquer des blocs de construction de vos propres mains permettra d'économiser considérablement de l'argent sur la production de produits. Le coût ne prend pas en compte salaires, qui est versée au salarié. Le coût du bloc n'inclut pas les frais généraux et de production, les taxes et autres déductions, ce qui rend le matériau de construction moins cher que la maison.
Le parpaing est l’un des matériaux les plus populaires aujourd’hui. Il est utilisé pour la construction d’objets à des fins diverses et de différentes tailles. C'est peut-être petit dépendances ou des bâtiments industriels.
Pour fabriquer des parpaings, on utilise un appareil spécial dont le principe est de faire vibrer le mélange de béton. Pour économiser considérablement sur les matériaux de construction, vous pouvez faire blocs de construction de vos propres mains. Pour ce faire, vous devez acheter ou construire indépendamment une presse vibrante.
Pour commencer à fabriquer des blocs de béton de vos propres mains, vous devez préparer tous les outils et matériaux qui peuvent être nécessaires au processus. Taille standard Le parpaing mesure 390x188x190 mm. L'intérieur du produit reste creux. Deux ou trois trous font office de vides dont la forme et la taille dépendent directement de la configuration de la machine.
Grâce à de tels vides, le parpaing assure une absorption acoustique et une isolation thermique suffisantes de la maison. Mais malgré une structure aussi creuse, le matériau est très résistant et durera de nombreuses années. Une fois que vous commencez à fabriquer, vous pouvez économiser considérablement sur les matériaux de construction.
Initialement, les blocs de béton étaient fabriqués à partir de scories. Afin de préparer une version classique d'un parpaing, certaines proportions doivent être respectées :
- 7 parties de scories de charbon provenant d'un haut fourneau ;
- 2 parts de sable argileux expansé (il vaut mieux privilégier la grosse fraction) ;
- 2 parties de gravier, la fraction ne doit pas être inférieure à 5 et pas supérieure à 215 mm ;
- 1,5 partie de ciment de qualité 500 ;
- 3 parts d'eau.
D'autres matériaux peuvent être utilisés comme charge ; c'est juste que dans la version classique, des scories ont été utilisées. Aujourd'hui, il est difficile de l'obtenir, c'est pourquoi des déchets de briques, de l'argile expansée, des cendres, du gravier, des criblures, de la pierre concassée, du gypse ou de la sciure de bois transformée peuvent être utilisés à la place. La quantité d'eau peut varier légèrement en fonction du mastic. Sa quantité doit être ajustée lors de la préparation de la solution. L'essentiel est qu'il ne soit pas trop sec, mais l'épandage de la solution est également considéré comme inacceptable.
Afin de vérifier la consistance de la solution, vous devez en jeter une petite quantité sur le sol. Il est considéré comme normal que le mélange s'étale doucement sans laisser de traces d'eau, mais si le mélange est serré en un poing, il devrait coller ensemble.
Si vous fabriquez vos propres blocs de béton avec du laitier, il est très important de vous assurer qu'il n'y a pas de corps étrangers. Les scories doivent être nettoyées de divers copeaux et terres. Il est inacceptable que la solution inclue du charbon imbrûlé. Afin d'éliminer la contamination, le matériau doit être tamisé à travers un tamis.
Si du gypse est ajouté en plus au parpaing, la proportion de matériaux sera légèrement modifiée. Le gypse (1 partie) est mélangé avec trois parties du mélange de scories, de l'eau est ajoutée lors du mélange. Cette solution doit être utilisée immédiatement après sa préparation, car le plâtre commencera à sécher rapidement. Il est recommandé de tremper les scories dans l'eau pendant un certain temps avant de préparer une telle solution.
Le marché des matériaux de construction modernes propose divers additifs qui améliorent considérablement la qualité du mortier. Vous pouvez ajouter un plastifiant à la solution ; il faut environ 5 g par parpaing. De tels additifs augmentent la résistance au gel, la résistance à l'eau et la résistance.
Il existe deux types de blocs de béton. Ils peuvent être creux ou pleins. Les premiers sont beaucoup plus légers : ils sont utilisés pour construire des murs, car ils ne créent pas trop de charge sur les fondations, de plus, ces blocs ont une bonne isolation phonique et thermique. Les blocs pleins sont le plus souvent utilisés pour construire des fondations.
Afin de fabriquer un parpaing, vous pouvez utiliser deux technologies. L’une est basée sur l’utilisation d’un coffrage en bois dans lequel sèche le mortier de béton. Pour la deuxième méthode, vous devez acheter ou fabriquer vous-même une machine spéciale.
Retour au contenu
Méthode de fabrication à l'aide de moules
Le bois et le métal peuvent être utilisés comme matériau à partir duquel ces formes sont fabriquées. Si du bois est utilisé pour créer la forme, il doit être très bien séché. Il doit en outre être traité avec un produit qui augmentera la résistance à l'humidité. Sinon, après un court laps de temps, les coffrages pourraient se déformer, ce qui affecterait la géométrie des blocs de béton. La taille interne du moule doit être de 400x200x200 mm. Mais ceci n'est pas une limitation ; la forme peut avoir différentes tailles.
Cette forme se compose d'un fond et de parois latérales. Pour accélérer le processus de production, il est recommandé de réaliser plusieurs moules. Pour que tous les coins du moule soient bien remplis, la solution doit être préparée plus liquide. Pour réaliser des blocs creux à l'aide d'un moule à la maison, vous pouvez utiliser des bouteilles en verre vides.
Une fois la solution versée dans le moule, le goulot de la bouteille est abaissé dans le mélange, la surface est nivelée et la hauteur requise du bloc de béton est obtenue. Après 5 à 6 heures, les bouteilles doivent être retirées et les blocs doivent être laissés sécher davantage. Le séchage des blocs dure au moins une journée, après quoi ils peuvent être démoulés et empilés. Avant la construction, ces blocs doivent reposer pendant au moins 1 mois.
Retour au contenu
Blocs de béton utilisant une machine de compactage vibrant
Grâce à un équipement spécial, les blocs de béton sont rendus plus durables et de meilleure qualité. Est-il possible de fabriquer une presse vibrante de vos propres mains ? Assez.
Outils nécessaires pour créer des équipements spéciaux :
- meuleuse pour couper des feuilles;
- Machine de soudage;
- mètre et craie (crayon) pour le marquage ;
- pinces;
- marteau.
Pour réaliser des matrices dans lesquelles le mélange de béton sera coulé, vous devez prendre une tôle d'une épaisseur maximale de 3 mm. La machine doit être équipée d'un moteur de 100 W, de plus, une charge doit être préparée qui créera un déséquilibre et des vibrations.
Pour réaliser une telle machine, il est nécessaire d'utiliser de la tôle d'acier. Des flans en sont découpés :
- 2 pièces mesurant 400x250 mm ;
- 2 pièces mesurant 200x250 mm ;
- visière 400x150 mm;
- côtes – 4 pièces mesurant 40x40 mm ;
- taille de la pince 39,5x19,5 mm.
Une fois tous les flans réalisés, vous pouvez commencer à assembler la matrice principale. Pour cela, des pièces mesurant 400x200 mm et 200x250 mm sont utilisées. Il est très important que chacun coutures de soudureétaient dehors. Sinon, les blocs de béton finis auront des coins arrondis. Le résultat sera une matrice de 400x200x250. Pour faire des vides à l'intérieur d'un parpaing, vous devez utiliser un tuyau d'un diamètre de 80 mm. La longueur des pièces ne doit pas dépasser 250 mm.
Une fois la matrice principale prête, il est nécessaire d'installer des ébauches de tuyaux à l'intérieur. Il est très important de contrôler leur distance les uns par rapport aux autres et aux murs. Toutes les tailles doivent être identiques. Afin de relier les tuyaux entre eux et de leur donner une résistance supplémentaire, des nervures de renforcement préparées mesurant 40x40 mm doivent être utilisées. Cette conception est soudée à la matrice.
À étape finale Cela comprend l'installation d'un vibrateur ; celui-ci est fixé sur le côté le plus long de la matrice. Des boulons sont utilisés pour le fixer. Une fois les boulons serrés, ils sont soudés en place pour plus de solidité. Pour protéger le moteur de l'eau et de la pollution mortier, une visière de protection est soudée sur le dessus. Une jambe est soudée au bord de la visière, ce qui ajoutera une solidité supplémentaire. Pour plus de commodité, les poignées sont soudées aux matrices.
En fonction du résultat souhaité, la forme de réalisation du bloc sera différente. Marché de la construction regorge de fabricants étrangers et nationaux de blocs de béton. Ils produisent du matériel de toute catégorie de complexité. Quand auto-réparation, la possibilité de créer un bloc depuis chez soi est bien réelle.
Attention : l'installation des blocs prendra beaucoup moins de temps que d'autres matériaux en raison de leur taille.
Champ d'application
Le plus souvent, les blocs de béton sont utilisés comme élément de base des bâtiments : garages, immeubles d'habitation à plusieurs étages, bureaux, maisons privées, chalets d'été Et ainsi de suite. Le champ d'application ne se limite pas aux applications à grande échelle projets de construction. Il est possible de produire/utiliser indépendamment des blocs de béton à la maison. Seule difficulté : il faut utiliser du matériel de chantier complémentaire (séchoir, bétonnière). Une pièce fermée (buanderie) munie d'un radiateur peut être utilisée comme séchoir. Température requise pour un sèche-linge à faire soi-même - 70 degrés. Les coffrages à béton sont utilisés pour les produits suivants :
- matériau de construction en béton;
- décoratif éléments architecturaux(vases, );
- dalles de pavage(le type peut varier);
- clôtures (y compris décoratives);
- dalles de construction en béton armé.
Caractéristique : selon le produit dont nous avons besoin, la qualité, les pièces et le moulage seront différents. Pour créer une forme puis fabriquer le produit de vos propres mains, vous devez calculs précis, surveiller attentivement le processus, suivre les règles de création, connaître les caractéristiques du matériau/futur produit.
Matériel pour la production
La variété des blocs de béton et les caractéristiques de leur application ont amené de nombreux nouveaux matériaux sur le marché. Matière première ce qui donnera à la forme les caractéristiques de qualité peuvent varier en fonction des exigences du produit final. Chaque matériau est conçu pour catégorie de prix, qualité, méthodes de transformation, indicateurs techniques.

Fabrication de produits avec petits détails, création autant que possible copies exactes, nécessite l'utilisation de moules en élastomère. Champ d'application:
- produits volumétriques complexes;
- bas-reliefs de haute précision ;
- constructions architecturales.
La production de ces produits est impossible sans les composants suivants :
- caoutchouc (caoutchouc synthétique);
- formoplaste;
- composés (polyuréthane/silicone).
Consommation approximative de matériau : 10-40 kg/m2.
Inconvénient : fabriquer un tel produit à la maison est extrêmement difficile. Un équipement de cuisson et de broyage spécialisé doit être utilisé. De plus, avant de commencer à travailler sur la substance, vous devriez consulter un spécialiste. En raison de la complexité du travail avec le matériau, une telle consultation est obligatoire.
Plastique
Les structures de grande taille qui ne nécessitent pas de calculs géométriques précis sont mieux réalisées à partir de moules en plastique. Matériaux de base :
- fibre de verre (faible compatibilité avec la matrice cimentaire, c'est pourquoi des fissures et des cassures sont possibles) ;
- plastique dur (sujet à la déformation, le principal domaine d'application est donc les dalles de pavage, les bordures, les pavés en béton);
- feuille Plastique ABS(sujet au délaminage, de la graisse silicone supplémentaire doit être utilisée. Un matériau de petite taille peut en être fabriqué) ;
- feuille/film de polystyrène (représente bien la texture et les contours des objets, est un matériau fragile) ;
- Plastique PVC (le plus durable, de haute qualité. L'adhérence est la plus faible possible, ne nécessite ni nettoyage ni lubrification).
Si vous décidez d'utiliser du plastique pour fabriquer un bloc, veillez à disposer d'un coffrage rigide. C'est le coffrage qui donnera au matériau le relief, la rigidité nécessaire et assurera un retrait facile. En cas de non-conformité de cette règle, soit les produits se désagrègent lors du séchage, soit le résultat sera de mauvaise qualité et de courte durée.
Créer soi-même un formulaire
Veuillez noter que traitement final Le produit doit être réalisé après durcissement complet. Si le produit est cru, actions supplémentaires(par exemple, couper) sont illogiques, inefficaces. Création d'un formulaire :
- Démarrez la production avec les matériaux disponibles. Par exemple, vous pouvez utiliser de la mousse de polystyrène. Découpez le tampon, remplissez-le d'un mélange préalablement préparé (sable et ciment). Vous recevrez un exemplaire du moule de décoration en béton. Vous pouvez utiliser des contenants en plastique des tailles différentes au lieu de timbres.
- Assemblez le produit à partir de chutes de panneaux de particules et de bois. La règle de base est que la surface doit être lisse. S'il est rugueux, des fissures se formeront entre les blocs et la surface ou le béton sera inégalement réparti, ce qui rendra difficile l'enlèvement du produit.
- Remplissez le moule avec le mélange de béton et laissez-le pendant plusieurs jours jusqu'à ce qu'il sèche complètement (selon le type de mélange et le matériau du produit. Indicateurs requis voir les instructions du matériel).
- Après séchage complet, retirer délicatement (par exemple avec une spatule ou un objet similaire) le produit fini.
- Réaliser (si nécessaire) les travaux de décoration requis.
Si vous n'avez pas le temps/l'envie de réaliser la démarche vous-même, utilisez les services entreprises de construction. En contactant l'entreprise dont vous avez besoin, vous pouvez passer une commande pour le formulaire dont vous avez besoin. Expliquez le but de la construction, le matériau souhaité et précisez le calendrier. Pour un prix fixe (à convenir en personne, par téléphone), vous serez informé et votre commande sera acceptée. Ainsi, vous pouvez être sûr de la qualité du produit obtenu, de sa durabilité et de l'exactitude de sa création.
Pourquoi faire des blocs ?
De quoi avez-vous besoin pour cela ?
De quoi sont faits les blocs ?
Comment les produire ?
Pourquoi est-il rentable de créer soi-même des blocs ?
Quel est le bénéfice de cela ?
Par où commencer et comment développer ce business ?
Dans cet article, vous recevrez des réponses à toutes les questions posées et vous pourrez « activer » pour vous-même une source de revenus fiable qui ne dépend que de vous.
Et donc, voyons cela dans l'ordre.
Pourquoi fabriquer des blocs de construction ?
Vous avez probablement remarqué que la construction est en plein essor depuis 4 à 5 ans. Ils construisent depuis des bâtiments privés de petite et moyenne taille : garages, datchas, domaines, ateliers, ateliers, bâtiments agricoles, jusqu'aux grands bâtiments industriels et résidentiels, installations de stockage, centres. Spécialistes spécialités du bâtiment plus demandé que jamais.
De nouvelles technologies et matériaux de construction apparaissent. Mais sont-ils toujours disponibles en termes de prix et de technologie pour un large éventail de développeurs ?
Ils sont donc rarement utilisés dans les petites et moyennes constructions, comme dans grandes villes, et dans les petits villages.
Les matériaux de construction les plus abordables restent ce qu'on appelle le parpaing et la brique.
De plus, la brique est souvent inférieure au parpaing en termes de prix, de conductivité thermique et de facilité de pose.
Mais les blocs de construction à âme creuse sont pratiques et abordables pour la plupart des promoteurs privés.
Oui, car grâce à ses propriétés :
Il est facile de les utiliser pour construire un ouvrage de faible hauteur (2-3 étages) (garage, maison, chalet, dépendance, atelier, etc.) sans même recourir aux services d'un maçon. (1 bloc = 3-4 briques) ;
Les murs en parpaings sont imperméables au bruit et à la chaleur ;
Le prix du parpaing est inférieur au prix de la brique, du bloc de mousse et d'autres matériaux de construction en raison du faible coût et de la disponibilité de ses composants (voir ci-dessous) ;
Seuls les parpaings peuvent être fabriqués par vous-même. Vous pouvez également fabriquer vous-même de l'adobe (brique d'argile et de paille).
Alors, comment fabriquer soi-même des parpaings ?
Que faut-il pour produire des blocs de construction ?
On sait que les parpaings étaient fabriqués en béton armé équipement spécialà l'aide d'une chambre à vapeur. Par conséquent, la production d'un bloc de haute qualité à la maison n'était pas disponible.
Mais s’il y a une demande, alors l’offre est inévitable. Et c'est!
Depuis 1994, l'expérience dans la production de blocs de construction en production privée et à petite échelle a apporté la réponse à la question posée.
Qu’est-ce que cela nécessite ?
Machine vibrante
- Matières premières
- Technologie
- Zone relativement plate
- Réseau domestique en 220V (aucun commentaire).
Clarifions chaque point plus en détail.
Machine vibrante
Manger différents modèles machines vibrantes. Dans les conditions de production nationale et dans les petites entreprises, la machine vibrante à parpaings manuelle, électrique et de petite taille MZ30 (14e année de production) a fait ses preuves avec confiance dans les pays de la CEI. Populairement connu sous le nom de « le rêve du développeur »
Matières premières
Pour produire des blocs de construction, les composants suivants sont requis :
Ciment- Ciment Portland grade 400. Un autre est acceptable. Mais il est nécessaire de choisir les proportions. Par exemple, lors de l'utilisation de ciment de qualité 300, sa consommation doit être augmentée de 10 à 15 %.
Charges pour béton peut-être le plus différents matériaux: sable, pierre concassée, scories, scories granulées, cendres, sciures, copeaux, criblures, argile expansée, gypse, débris de briques et autres matériaux naturels et industriels.
En fonction des conditions locales, des exigences relatives aux blocs produits et du coût, vous pouvez sélectionner la charge appropriée. Je vais lister plusieurs compositions de béton populaires et les principaux groupes de bétons
1). Scories d'usines métallurgiques (gris ou gris foncé à haute teneur en ciment, fraction fine tamisée) – 9 parts
Ciment – 1 partie
Eau 0,5 volume de ciment
2). Scories granulaires provenant d'entreprises métallurgiques (couleur jaune-verdâtre à haute teneur en ciment, fraction fine tamisée) – 4 parties
Petites projections – 4 parties
Ciment – 1 partie
Eau 0,5 volume de ciment
3). Autres bétons de scories
4). Béton sur sable et pierre concassée
5). Béton sur déchets de briques
6). Béton d'argile expansée
7). Béton de frêne
8). Béton de sciure
9). Béton perlitique
dix). Béton polystyrène
et autres bétons avec combinaison différente répertorié.
Il est désormais clair que le nom actuel de « parpaing » n’est pas le plus approprié. définition préciseéléments de base possibles.
Additif plastifiant- Ce n'est pas un composant essentiel du béton. Mais sa présence assure : une résistance précoce des blocs (ce qui est très important avec un espace de production limité), améliore la qualité des blocs (la fissuration et l'abrasion des blocs sont réduites), et améliore la résistance à l'eau et au gel du béton.
La quantité d’additif est très faible – environ 5 g par bloc.
Technologie de fabrication des blocs de construction :
- Préparation du béton
- Production de blocs
- Séchage et stockage des blocs finis.
Préparation du béton(en utilisant l'exemple de la 2ème recette concrète donnée précédemment)
1). Remplissez 4 pelles de criblures fines + 4 pelles de scories granulées
2). Remplissez 1 pelle de ciment
3). Bien mélanger
4). Ajoute de l'UPD dissous à 7 à 9 litres d'eau + 250 ml (un pot d'un demi-litre). La solution d'additifs est préparée comme suit : verser 0,5 kg d'UPD dans un récipient de 40 litres et bien mélanger jusqu'à dissolution complète.
5). Remuer. Dans ce cas, le béton est imprégné qualitativement de la solution UPD.
Production de blocs
1). Tu t'endors dans la machine vibrante béton prêt à l'emploi Avec petite diapositive. En bref, pendant 1 à 2 secondes. allume le vibrateur - le béton se rétracte, avec une truelle, en un seul mouvement, vous nivelez la surface du béton légèrement déposé.
2). Installez la pince et, sans trop d'effort, appuyez dessus en allumant le vibrateur.
Les blocs avec des vides ronds et rectangulaires vibrent pendant 4 à 5 secondes. jusqu'à ce que la pince soit abaissée sur les butées.
Les blocs complets étroits (2 pièces) vibrent pendant 5 à 7 secondes.
3). Vous soulevez la machine avec vibration - le bloc reste sur la plate-forme.
Séchage et stockage des blocs finis
Lors de l'utilisation d'UPD, les blocs finis peuvent être retirés du site et stockés dans un délai de 5 à 6 heures. Sans UPD - en deux jours.
Passé ce délai, les blocs ne s'effondrent pas si les proportions de béton et la technologie de leur fabrication sont respectées.
Je recommande de stocker les blocs finis en piles pyramidales en un seul bloc avec un petit espace (2-3 cm) entre les blocs - pour un séchage ultérieur des bords latéraux.
Il y a 100 pièces dans chacune de ces pyramides. Facile à compter. Il est utile de marquer chaque pyramide avec la date et l'heure de production du dernier bloc. Cela sera utile lors de la mise en œuvre. Vous pouvez expédier le 4ème ou 5ème jour.
Site de production
- Une pièce avec un sol en béton lisse.
Des blocs peuvent être produits toute l'année. Souhaitable bonne aération et chauffage par temps froid.
- Aire plate ouverte.
Peut être en béton ou en terre, couvert film plastique pour préserver la présentation des blocs (le bord arrière ne se salit pas).
- Une zone ouverte et relativement plate sans préparation préalable.
Sur une telle plate-forme, vous pouvez disposer des blocs prêts à l'emploi sur des palettes.
Par où commencer à produire des blocs de construction ?
1. Sélectionnez le meilleur matériau de béton local en fonction du coût et de la livraison.
2. Calculez le coût d'un bloc en tenant compte des composants du béton.
3. Choisissez le site de production.
4. Achetez une machine vibrante.
5. Maîtriser les technologies données.
Dans un premier temps, le béton peut être préparé à la main. Par la suite, c'est plus efficace et plus simple - sur une bétonnière électrique d'un volume de 0,2 à 0,5 mètre cube (de préférence 0,5, en tenant compte de l'avenir).
Pourquoi est-il avantageux de créer vous-même les éléments de base ?
Je donnerai mes coûts réels pour les granulats avec livraison et ciment, le calcul du coût de production des blocs et le retour sur investissement de la machine vibrante "Developer's Dream" pour la production de parpaings à Zaporozhye (Ukraine) en 2004 en utilisant l'exemple du béton fabriqué à partir de laitier granulé (gris) et de ciment.
Donnée initiale:
8 mètres cubes de scories– 30 dollars/voiture avec livraison en ville (KRAZ ou grand MAZ)
Ciment:
Proportion 1:9 - 0,88 mètres cubes ou 18 sacs de 3 dollars = 54 dollars
Prix de la machine vibrante- 200 dollars
Volume total de solution :
Proportion 1:9 – 8 + 0,88 = 8,88 (mètres cubes)
Volume de solution pour 1 parpaing GOST :
Volume total : 39 cm x 19 cm x 19 cm = 0,014 (m3)
volume des vides :
Avec d = 9,5 cm : 3 x 3,14 x 4,75**2 x 15 = 3188 cc = 0,003188 m3
Volume de solution pour 1 bloc à d = 9,5 cm : 0,011 mètre cube
Tableau des résultats des calculs :
Note:
1. Pour un parpaing avec 2 vides rectangulaires, moins de mortier est nécessaire (mais la résistance d'un tel bloc est moindre)
2. En remplaçant le laitier granulé par un granulat local pour béton qui vous convient, les prix de votre région (en Russie le prix de détail d'un parpaing est plus élevé) et en utilisant les dimensions d'un parpaing, vous pouvez facilement calculer le coût de 1 pc/bloc et le retour sur investissement de la machine pour vous-même.
Calcul de la rentabilité et du bénéfice :
Nous acceptons les hypothèses initiales : |
||
Nom |
Plage de valeurs |
Valeur de référence |
Temps pour former 1 bloc (sec.) sans UPD | ||
Nombre de blocs par heure, en tenant compte du temps de chargement du béton en 30 secondes. (des choses) | ||
Nombre de blocs en morceaux de 1 jour (8 heures) | ||
Prix public d'un parpaing (en 2005) : en Ukraine |
2,0 UAH (0,4 $) 15 roubles. (0,5$) |
|
Rentabilité(Il résulte du tableau précédent que le coût d'un bloc est égal à 1/3 de son prix de détail) |
||
Produire des blocs par jour à hauteur de : en Ukraine | ||
Produire des blocs d'un montant de : en Ukraine | ||
Le coût sera : en Ukraine | ||
Le bénéfice sera de : en Ukraine |
Note :
- Si vous appliquez UPD, la productivité augmentera considérablement.
- Le record appartient à Viktor Romanov et Sergei Rachmaninov, qui ont produit 700 blocs 390*138*188 en une journée en juillet 1998.
Développement et expansion des affaires
1. Embauchez des employés responsables, dignes de leur intérêt. (Dans notre ville - 20 kopecks (0,04 centimes) par bloc, dans la région - 0,02 centimes.)
2. Lorsque vous démarrez les ventes, réduisez le prix de détail, créant ainsi une concurrence digne et recevant des clients reconnaissants et leurs recommandations. (Important ! La qualité doit être digne).
3. En saison chaude ou dans une pièce chauffée (quelle que soit la saison), le travail peut être organisé en 2 équipes.
4. Dans ce cas, l'entrepreneur ne dépend que de : la présence de tension dans le réseau et la santé de la main-d'œuvre (dans un premier temps, avant le retour sur investissement, vous pouvez travailler vous-même avec la machine).
5. Le cas échéant, louez la machine à des « développeurs ».
6. Exécutez les commandes des « développeurs » directement sur leur site, leur permettant ainsi d'économiser de l'argent sur le chargement, le transport et le déchargement des blocs.
7. De plus, – vous n'aurez pas besoin de l'autorisation de l'Autorité nationale de surveillance électronasale, puisque tous les équipements sont conçus pour un réseau domestique ordinaire !
Décrets du gouvernement de la Fédération de Russie du 13/08/97 n° 1013, Gosstandart de la Fédération de Russie n° 86 du 08/10/2001 et Gosstroy de la Fédération de Russie n° 128 du 24/12/2001, la liste Les produits nécessitant une certification obligatoire ne comprennent pas les blocs de béton de construction avec diverses charges (laitier, argile expansée, sciure de bois, etc.), ainsi que les équipements de formation de vibrations pour leur production.
Ainsi, l'activité de production de blocs de construction peut se développer par étapes :
- Commencer avec coûts minimaux pour l'achat d'une machine vibrante, 1 machine de matières premières locales comme enduit à béton, 15-20 sacs de ciment.
Proposez des publicités gratuites pour la vente de parpaings de haute qualité.
Produisez 800 à 1 000 blocs. Vendez rapidement en réduisant le prix de vente au détail.
- Achetez une bétonnière et le prochain lot de matières premières + UPD.
Nivelez le prix au détail (facultatif).
Publiez des annonces gratuites + des annonces payantes.
- De manière productive, avec l'expérience de production accumulée, produisez des blocs de haute qualité et parvenez à honorer les commandes.
Il n'est plus nécessaire de faire de la publicité : haute qualité les blocs + la publicité de bouche à oreille feront l'affaire.
Organiser une production de blocs de construction en 2 équipes.
Élargir la gamme de blocs produits.
Achetez des machines vibrantes supplémentaires et éventuellement une bétonnière.
Recruter des travailleurs acharnés
Ayez le temps de dépenser vos bénéfices ou de les investir dans nouvelle entreprise, tout aussi rentable.
Ce que je vous souhaite sincèrement !
Succès et prospérité !!
«Catalogue de packages commerciaux complets» masterdela.info
mail à : [email protégé],
Ukraine, Zaporojie, août 2005
L'un des matériaux les plus courants pour la construction de murs porteurs et de cloisons de bâtiments résidentiels, ainsi que de petits bâtiments industriels sont des blocs de béton. Leur popularité est due à leur faible coût, à leur excellent caractéristiques de performance Et gros montant variétés, ce qui vous permet de choisir le bon bloc pour presque toutes les tâches.
Les instructions données dans cet article vous aideront à apprendre à fabriquer vous-même des blocs de béton et vous présenteront également leurs types existants.
Blocs de béton pour murs
Types de pierres artificielles en béton
Examinons les principaux types et caractéristiques des blocs de construction en béton, les plus courants dans la construction moderne.
parpaing
Ces pierres murales sont fabriqués selon la méthode de vibrocompression de mortier de béton sur des plates-formes spéciales.
La composition du mélange à partir duquel le parpaing est fabriqué peut comprendre :
- pierre concassée pour produits en béton;
- combat de briques;
- sciure;
- argile expansée
Caractéristiques Les blocs de béton avec laitier laissent beaucoup à désirer, mais du fait que leur prix est l'un des plus bas du marché, les parpaings sont largement utilisés dans la construction privée.
Mais le coût est presque le seul avantage, car ils sont loin derrière les autres matériaux dans les paramètres suivants :
- durabilité;
- paramètres d'économie de chaleur ;
- force.
Le principal champ d'application des blocs est petits bâtiments, qui ne sera pas soumis à de lourdes charges :
- hangars;
- garages;
- cuisines d'été;
- ateliers et ainsi de suite.
Photo de parpaing
Un matériau moins courant composé des composants suivants :
- matière organique (principalement bois) ;
- élément liant (poudre);
- durcisseur.
Essentiellement, cette pierre artificielle est constituée de sciure de bois enfermée dans une coque en béton.
Les avantages du matériau sont évidents :
- poids léger du bloc de béton ;
- propriétés d'isolation thermique élevées;
- bonne isolation phonique;
- échange d'air efficace.
Pour protéger les blocs de impact négatif environnement, les pierres sont traitées avec une solution spéciale. Cela empêche la formation de moisissures et empêche la pourriture.
Arbolite est parfait pour la construction de petites maisons adaptées à résidence à l'année sans utilisation d'isolation thermique supplémentaire.
Bloc d'arbolite
Blocs de gaz et blocs de mousse
Les blocs de béton cellulaire, selon GOST, qui détermine leurs caractéristiques techniques, doivent être constitués à 70 à 85 % de pores (cellules) créés artificiellement et remplis d'air. Les plus courants sont les blocs de mousse et de gaz.
Ces matériaux présentent les avantages suivants :
- Ils sont légers, de sorte que le transport des blocs de béton et leur installation dans une construction privée ne nécessitent pas l'utilisation d'équipements spéciaux ;
- facile à traiter - donne la forme désirée bloc cellulaire Vous pouvez utiliser une scie à métaux ordinaire pour le bois ;
- les murs en blocs de béton cellulaire retiennent bien la chaleur et possèdent d'excellentes propriétés d'isolation phonique.
Les blocs de béton cellulaire sont fabriqués à partir d'une solution contenant du sable, du ciment et des granulats. Pour former de la mousse, de la chaux, de la poudre d'aluminium ou un autre agent moussant sont ajoutés.
Note!
Contrairement au béton cellulaire, le béton cellulaire est soumis à traitement supplémentaire dans un four autoclave, où il est exposé à haute température sous haute pression (10-12 MPa).
En conséquence, ce matériau acquiert une résistance accrue : il est presque impossible de l'effriter ou de le casser.
Bloc de béton cellulaire
Autoproduction de blocs
Technologie de production Pierre artificielle depuis mortier de ciment avec du mastic est relativement simple, ce qui permet de réaliser soi-même des blocs de béton.
Travail préparatoire
Sur stade initial les dimensions du futur bloc devraient être déterminées. Quand fait soi-même paramètres de chacun élément individuel pris en fonction de la largeur de mur requise.
L'épaisseur du fond du bloc ne doit pas être inférieure à 2 cm et les parois des vides ne doivent pas être inférieures à 4 cm. Dans ce cas, une pierre standard mesurant 20x20x40 cm avec des vides à l'intérieur pèse environ 40 kg, ce qui fait c'est pratique pour la pose de murs.
Pour la production, vous aurez besoin de toute surface plane recouverte d'un film plastique et de moules spéciaux sans fond.
Le matériel pour les formulaires sera :
- planches;
- contre-plaqué.
Pour protéger l'arbre des dommages, partie intérieure les formes sont gainées tôle. Les inserts sont fabriqués de la même manière, grâce à quoi bloc fini des vides se forment. Ils améliorent les propriétés d'isolation thermique du matériau et le rendent plus léger.
Moules pour fabriquer des blocs de béton
Vous pouvez produire des blocs de béton de vos propres mains plus rapidement si vous réalisez plusieurs coffrages en un seul bloc à la fois. Pour ce faire, vous avez besoin de contreplaqué ou d'une planche d'une largeur égale à la hauteur du futur bloc. Le matériau est scié en morceaux et fixé avec des vis autotaraudeuses. Ensuite, des partitions internes sont créées.
Conseil!
Pour que le bloc congelé se sépare facilement du moule, toutes ses pièces doivent être lubrifiées avec du kérosène, de l'huile de machine ou de l'antigel.
Processus de fabrication
Pour couler des blocs de béton, vous aurez besoin des matériaux suivants :
- gravier fin;
- ciment;
- sable;
- eau;
- citron vert;
- fil de renfort.
La quantité de chaque composant est déterminée en fonction de vos besoins en pierre artificielle. Les proportions de ciment, sable et gravier sont prises dans le rapport 1:3:5.
Il est préférable d'utiliser une bétonnière pour mélanger la solution de béton.
Pour faciliter la présentation, nous diviserons l'ensemble du processus ultérieur en plusieurs étapes.
Bloc de béton fait maison
La technologie décrite ci-dessus vous permet de fabriquer des blocs de béton de vos propres mains sans trop d'effort. Caractéristiques produits finis Ils ne seront pratiquement en aucun cas inférieurs aux analogues vendus dans les supermarchés de la construction, et leur taille correspondra parfaitement à vos besoins. De plus, cela peut réduire considérablement le coût d'achat des matériaux de construction et de leur livraison.
La vidéo de cet article vous aidera à vous familiariser plus en détail avec le matériel.