Éléments du processus technologique de traitement mécanique. Processus de production et technologiques de traitement mécanique des pièces
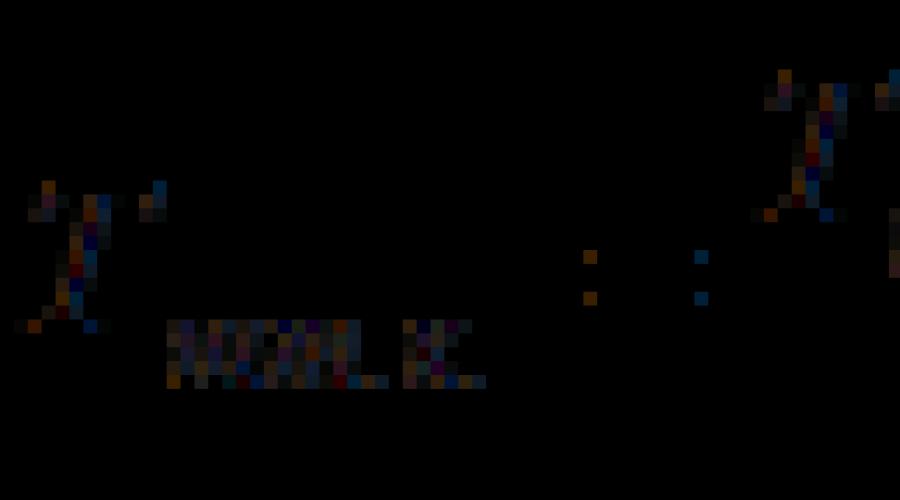
Lire aussi
Envoyer votre bon travail dans la base de connaissances est simple. Utilisez le formulaire ci-dessous
Les étudiants, étudiants diplômés, jeunes scientifiques qui utilisent la base de connaissances dans leurs études et leur travail vous seront très reconnaissants.
Posté surhttp:// www. tout va bien. ru/
Introduction
1. Données initiales pour la tâche
2. Type de production, nombre de pièces par lot
3. Type de pièce et surépaisseurs de traitement
4. Structure du processus technologique
5. Sélection des équipements et appareils
6. Sélection des outils
7. Calcul des conditions de coupe
8. Standardisation des délais, détermination des prix et des coûts usinage détails
9. Informations de base sur les précautions de sécurité lors du travail sur des machines à couper les métaux
10. Conception de l'appareil
11. Préparation de la documentation technique
Littérature
Introduction
L'ingénierie mécanique moderne impose des exigences très élevées en matière de précision et d'état des surfaces des pièces de machines, qui ne peuvent être obtenues principalement que par un traitement mécanique.
La coupe du métal est un ensemble d'actions visant à modifier la forme de la pièce en supprimant la surépaisseur avec des outils de coupe sur les machines à couper le métal, garantissant ainsi la précision et la rugosité spécifiées de la surface usinée.
Selon la forme des pièces, la nature des surfaces à traiter et les exigences qui leur sont imposées, leur traitement peut être réalisé de diverses manières : mécanique - tournage, rabotage, fraisage, emboutissage, meulage, etc. ; électrique - étincelle électrique, impulsion électrique ou anodique-mécanique, ainsi que méthodes de traitement ultrasoniques, électrochimiques, par rayonnement et autres.
Le processus de traitement des métaux par découpe joue un rôle de premier plan dans l'ingénierie mécanique, car la précision des formes et des tailles et la fréquence élevée des surfaces des pièces métalliques des machines ne sont dans la plupart des cas assurées que par un tel traitement.
Ce procédé est utilisé avec succès dans toutes les industries sans exception.
La découpe des métaux est un processus très laborieux et coûteux. Par exemple, en moyenne dans l'ingénierie mécanique, le coût du traitement des pièces par découpe est de 50 à 60 fois supérieur au coût des produits finis.
La découpe des métaux est généralement effectuée sur des machines à couper les métaux. Seulement espèce individuelle les opérations de découpe liées à la métallurgie sont réalisées manuellement ou à l'aide d'outils mécanisés.
Les tendances suivantes sont perceptibles dans les méthodes modernes d’usinage des métaux :
traiter des pièces avec de petites tolérances, ce qui entraîne des économies de métaux et une augmentation de la part des opérations de finition ;
large application méthodes de traitement de durcissement sans élimination des copeaux par laminage avec des rouleaux et des billes de grenaillage, mandrin, ciselage, etc. ;
l'utilisation d'un traitement multi-outils au lieu d'un traitement avec un seul outil et d'outils de coupe à plusieurs tranchants au lieu d'outils à un seul tranchant ;
augmenter les vitesses de coupe et les avances ;
une augmentation de la proportion de travaux effectués sur des machines automatiques et semi-automatiques, des complexes robotiques utilisant des systèmes de contrôle par programme ;
modernisation approfondie des équipements de coupe des métaux ;
l'utilisation de dispositifs à grande vitesse et multi-places pour sécuriser les pièces et les mécanismes lors de l'automatisation des machines universelles de découpe des métaux ;
production de pièces en alliages spéciaux et résistants à la chaleur, dont l'usinabilité est nettement moins bonne que celle des métaux conventionnels ;
participation de technologues au développement de conceptions de machines pour assurer leur haute fabricabilité.
Il est plus rationnel de recevoir immédiatement une pièce finie, en contournant l'étape d'approvisionnement. Ceci est réalisé grâce à l’utilisation de méthodes précises de moulage et de formage et de métallurgie des poudres. Ces processus sont plus progressifs et seront de plus en plus introduits dans la technologie.
1. OriginaldonnéesPartâche
pièce de traitement de coupe mécanique des métaux
Titre d'emploi:
Processus technologique d'usinage d'une pièce.
Les données initiales de la tâche sont présentées dans le tableau 1 :
Tableau 1
Composition chimique de l'acier (GOST 1050-88) dans le tableau 2 :
Tableau 2
Propriétés mécaniques de l'acier 30 GOST 1050-88 dans le tableau 3 :
Tableau 3
Propriétés technologiques de l'acier 30 GOST 1050-88 dans le tableau 4 :
Tableau 4
2 . Taperproduction,quantitédétailsVdes soirées
Le nombre de pièces dans un lot peut être déterminé par la formule :
où N est le programme annuel de production de pièces, pcs.
t est le nombre de jours pour lesquels il est nécessaire de disposer de parts annuelles.
F - nombre de jours ouvrables dans une année.
241 (pcs.) Dans le tableau 1, sélectionnez le type de production :
Tableau 1
Type de production - série.
Production par lots - les produits sont fabriqués ou traités par lots (séries) constitués de pièces similaires de même taille, lancées simultanément en production.
Maintenant, à partir du tableau 2, nous sélectionnons le type de production :
Tableau 2
La production est de taille moyenne et produit de petites pièces (légères), avec des quantités par lot allant de 51 à 300 pièces.
3. VoirblancsEtallocationssurtraitement
Une pièce à usiner est un élément de production à partir duquel la pièce requise est fabriquée en modifiant la forme, la taille, la qualité des surfaces et les propriétés des matériaux. Le choix du type de pièce dépend du matériau, de la forme et de la taille, de sa destination, des conditions de travail et de la charge subie, ainsi que du type de production.
Peut être utilisé pour la fabrication de pièces les types suivants blancs :
a) pièces moulées en fonte, acier, métaux non ferreux, alliages et matières plastiques pour pièces façonnées et boîtiers sous forme de cadres, boîtes, boîtes d'essieux, mâchoires, etc. ;
b) pièces forgées - pour les pièces soumises à la flexion, à la torsion et à la tension. Dans la production en série et en série, les emboutissages sont principalement utilisés, dans la production à petite échelle et individuelle, ainsi que pour les pièces de grandes dimensions - pièces forgées ;
c) produits laminés à chaud et à froid - pour les pièces telles que les arbres, les tiges, les disques et autres formes dont les dimensions transversales ont légèrement changé.
Dans notre cas, il est conseillé de réaliser le couvercle en laminé, car le cercle s'adapte bien aux dimensions de la pièce.
Les allocations de transformation sont indiquées dans le tableau 1 :
Tableau 1 - allocations et tolérances de traitement
DANS dans ce cas Il est préférable de choisir une pièce moulée en acier.
La fonderie est une branche du génie mécanique engagée dans la production d'ébauches ou de pièces façonnées en versant du métal en fusion dans un moule spécial ayant la configuration de l'ébauche. Une fois refroidi, le métal coulé durcit et, à l'état solide, conserve la configuration de la cavité dans laquelle il a été coulé. Le produit final est appelé moulage. Lors de la cristallisation du métal en fusion, les effets mécaniques et propriétés opérationnelles moulages
Reçu par casting divers modèles pièces moulées pesant de plusieurs grammes à 300 tonnes, d'une longueur de plusieurs centimètres à 20 m, avec des parois de 0,5 à 500 mm d'épaisseur. Pour la réalisation de pièces moulées, de nombreuses méthodes de coulée sont utilisées : dans des moules en sable, dans des moules carapaces, à la cire perdue, dans un moule, sous pression, coulée centrifuge, etc. Le champ d'application d'une méthode de coulée particulière est déterminé par le volume de la production, les exigences en matière de précision géométrique et de rugosité de surface des pièces moulées, la faisabilité économique et d'autres facteurs.
4. Structuretechnologiqueprocessus
Itinéraire de fabrication de pièces
1. Forage (machine 2N135) :
a) Percer le trou 35
b) fraisage 38,85
c) (machine T15K6) - alésoir 40
(Mandrin normalisé à 3 mors)
2. Serrurier
3. (marque de machine 16K20F3) tour CNC
a) couper l'extrémité à la taille 163 (-0,3)
b) affûter la sphère R150
(mandrin d'étalement (pince))
4. (marque de machine 16K20F3) tour CNC
a) couper l'extrémité en maintenant la taille 161 (-0,3)
b) affûter la sphère R292
(mandrin d'étalement)
5. Fraiseuse horizontale de marque 6M82G avec une fraise en bout de 8 mm et 10,5 mm de profondeur. (Appareil spécial)
6. Serrurier.
7. Cimentation.
8. Durcissement
9.Vacances
10. Nettoyage et contrôle de la dureté
11.Nettoyage (traitement thermique et calibrage)
12. (marque de machine 2N135) alésoir 40.
13. (marque de machine 3E710A) meulage de surface. Réinitialisez la mouture à la taille 160.
14. Lavage.
15. Testez.
5. ChoixéquipementEtdispositifs
Lors du choix du type de machine et du degré d'automatisation, les facteurs suivants doivent être pris en compte :
1. Dimensions hors tout et forme de la pièce ;
2. La forme des surfaces traitées, leur localisation ;
3. Exigences techniques concernant la précision des dimensions, de la forme et de la rugosité des surfaces traitées ;
4. La taille du programme de production, caractérisant le type de production d'une pièce donnée.
Dans la production unique à petite échelle, des machines universelles sont utilisées ; dans la production en série, outre les machines universelles, les machines semi-automatiques et les machines automatiques sont largement utilisées dans la production à grande échelle et en série - machines spéciales, machines automatiques, machines à agrégats et machines automatiques ; lignes.
Les machines automatiques à commande numérique sont désormais de plus en plus utilisées dans la production en série. contrôlé par programme, permettant de passer rapidement d'un traitement d'une pièce à une autre en remplaçant un programme enregistré, par exemple, sur une bande de papier perforée ou une bande magnétique.
Nous sélectionnons les machines selon les tableaux ci-dessous :
Tableau 1. Tours à décolleter
Indice |
Modèles de machines |
||||
Plus grand diamètre de la pièce, mm |
|||||
Distance entre les centres, mm |
|||||
Vitesse de broche, tr/min |
|||||
Nombre d'étages d'alimentation à étrier |
|||||
Alimentation par étrier. Mm. Transversal longitudinal |
0,08-1,9 0,04-0,95 |
0,065-0.091 0,065-0,091 |
0,074,16 0,035-2,08 |
0,05- 4,16 0,035-2,08 |
|
Puissance du moteur électrique principal, kW |
|||||
Efficacité des machines |
|||||
Force d'avance maximale admissible par le mécanisme, n |
Tableau 2. Fraiseuses horizontales et verticales
Indice |
Modèles de machines |
||||
Horizontal |
Verticale |
||||
Surface de travail de la table, mm |
|||||
Nombre de pas de vitesse de broche |
|||||
Vitesse de broche, tr/min |
|||||
Nombre d'étapes d'alimentation |
|||||
Avance de la table, mm/min : longitudinale transversale |
25-1250 15,6-785 |
||||
Force d'avance maximale autorisée, kN |
|||||
Puissance du moteur principal |
|||||
Efficacité des machines |
Tableau 3. Perceuses verticales
Indice |
Modèles de machines |
|||
2N118 |
2N125 |
2N135 |
||
Plus grand diamètre nominal de perçage.mm |
18 |
25 |
35 |
|
Mouvement vertical de la tête de perçage, mm |
150 |
200 |
250 |
|
Nombre de pas de vitesse de broche |
9 |
12 |
12 |
|
Vitesse de rotation de la broche tr/min |
180-2800 |
45-2000 |
31,5-1400 |
|
Nombre de pieds d'alimentation |
6 |
9 |
9 |
|
Avance de broche.rpm |
0,1-0,56 |
0,1-1,6 |
0,1-1,6 |
|
Couple sur la broche, N |
88 |
250 |
400 |
|
Force d'avance maximale admissible, N |
5,6 |
9 |
15 |
|
Puissance du moteur électrique, kW |
1,5 |
2.2 |
4 |
|
Efficacité des machines |
0,85 |
0,8 |
0,8 |
Dans les tableaux, nous sélectionnons les machines suivantes : 2N135 16K20F3 6M82G 3E10A
6 . Choixoutil
1 Lors du choix d'un outil de coupe, il est nécessaire de partir de la méthode de traitement et du type de machine, de la forme et de l'emplacement des surfaces traitées, du matériau de la pièce et de ses propriétés mécaniques.
L'outil doit garantir la précision requise de forme et de taille, la rugosité requise des surfaces usinées, une productivité et une durabilité élevées, et doit être suffisamment durable, résistant aux vibrations et économique.
Posté surhttp:// www. tout va bien. ru/
Figure 2 - Fraise en bout
Le matériau de la partie coupante de l’outil est de la plus haute importance pour obtenir une productivité d’usinage élevée.
Pour le fraisage surfacique, je choisis un accessoire d'extrémité avec fixation mécanique pentagonal plaquettes en carbure(GOST 22085-76).
Diamètre de la fraise, mm D = 100
Nombre de dents de coupe z = 12
Paramètres géométriques de la partie coupante de la fraise
Angle du plan principal c = 67є
Angle auxiliaire en plan ц1 = 5є
Angle de coupe principal r = 5є
Angle de dépouille principal b = 10є
Angle d'inclinaison du tranchant principal l = 10°
Angle d'inclinaison des dents inclinées ou hélicoïdales = 10º
Le matériau de la partie coupante de la fraise est de l'acier rapide T15K6 sous la forme d'une plaque pentagonale.
Pour fraiser une rainure, je choisis une fraise à rainure (GOST 8543-71).
Fraise à rainurer
Diamètre de coupe D = 100
Nombre de dents de coupe z = 16
Diamètre du trou d = 32
Largeur de coupe B = 10
Le matériau de la partie coupante de la fraise est un alliage dur VK6M selon GOST (3882-88)
Pour percer un trou, j'en choisis un standard foret hélicoïdal, équipé de plaques en alliage dur et d'une tige conique (GOST 2092-88)
Foret hélicoïdal
Diamètre du foret en mm d = 35
Longueur totale du foret en mm L = 395
Longueur de foret Lo = 275
Paramètres d'affûtage géométrique
angle au sommet 2ts = 120º
angle de coupe principal r = 7є
angle arrière principal b = 19є
angle d'inclinaison du bord transversal w = 55º
l'angle d'inclinaison de la rainure hélicoïdale = 18º
angle au sommet 2к0 = 73є
Le matériau de la partie coupante du foret est de l'acier rapide de qualité T15K6 sous forme de plaques.
Pour meuler la rainure, je choisis une meule cylindrique à profil droit GOST 8692-82
Posté surhttp:// www. tout va bien. ru/
Figure 7 - Meule
Maximum diamètre extérieur, mm D = 100
Hauteur du cercle H = 10
Diamètre du trou de forage d = 16
Dureté (GOST 18118-78) - cercle moyennement dur.
Taille du grain - 50.
Cinquième liant céramique.
2 choix outil de mesure dépend de la forme des surfaces mesurées, de la précision de traitement requise et du type de production.
Pour contrôler la précision requise des surfaces traitées, je choisis l'outil de mesure suivant.
Pieds à coulisse (GOST 166-63).
Compteur interne micrométrique (GOST 10-58).
Pour contrôler la rugosité de la surface traitée, je choisis un profilomètre de type 240 (GOST 9504-60).
7 . CalculModesCoupe
1 La profondeur de coupe t, mm, dépend de la surépaisseur de traitement et la classe de rugosité requise de la surface usinée est inférieure à 5 mm, le fraisage sera alors effectué en une seule passe.
2 La quantité d'avance est choisie dans la littérature de référence en fonction des propriétés mécaniques du matériau à traiter, de l'outil de coupe et de la classe de rugosité de surface requise.
Sur les fraiseuses, l'avance minute Sm, mm/min est ajustée, c'est-à-dire la vitesse de déplacement de la table avec la partie fixe par rapport à la fraise. Les éléments de la couche découpée, et donc les paramètres physiques et mécaniques du processus de fraisage, dépendent de l'avance par dent Sz, c'est-à-dire mouvement de la table avec la pièce (en mm) lors de la rotation de la fraise d'1 dent. La rugosité de la surface usinée dépend de l'avance par tour de la fraise S0, mm/tr.
Il existe la relation suivante entre ces trois valeurs :
où n et z sont respectivement la vitesse de rotation et le nombre de dents de la fraise.
Nous reprenons la valeur d'alimentation Sz de la littérature de référence
Ensuite, en utilisant la formule (2), nous calculons SM
3 La vitesse de coupe estimée est déterminée par la formule empirique
où Cv est le coefficient de vitesse de coupe, qui dépend des matériaux de la partie coupante de l'outil et de la pièce et des conditions de traitement ;
T - durée de vie nominale de la fraise, min ;
m est un indicateur de résistance relative ;
Xv, Yv, Uv, pv, qv, - respectivement, indicateurs du degré d'influence de la profondeur de coupe, de l'avance, de la largeur de fraisage, du nombre de dents et du diamètre de la fraise sur la vitesse de coupe ;
Kv - facteur de correction pour les conditions modifiées.
La signification du coefficient et des exposants dans la formule de vitesse de coupe pour le fraisage
CV = 445 ; qv = 0,2;pv; XV = 0,15 ; Yv = 0,35, nv = 0,2 ; PV =0 ; m = 0,32
Le facteur de correction Kv est déterminé comme le produit d'un certain nombre de coefficients
où Kmv est un coefficient qui prend en compte l'influence des propriétés mécaniques du matériau traité sur la vitesse de coupe ;
Kпv - coefficient prenant en compte l'état de la surface de la pièce ;
Kiv - coefficient prenant en compte le matériel instrumental.
Kpv = 0,8 ; Kiv = 1.
A partir de la formule (4) on trouve le facteur de correction :
Ensuite, en utilisant la formule (3), nous trouvons la vitesse de coupe estimée
Vitesse de rotation de la broche, le régime est calculé à l'aide de la formule
où Vp est la vitesse de coupe de conception, m/min ;
D - diamètre de coupe, mm.
En utilisant la formule (5), nous trouvons la vitesse de broche estimée
Calculons maintenant la vitesse de rotation réelle nf, la plus proche des données du passeport de la machine. Pour ce faire, trouvons cn et déterminons la série entière n
où nz et n1 sont les valeurs maximales et minimales de la vitesse de rotation ;
n est le nombre de pas de vitesse de rotation.
Maintenant, nous déterminons à partir de la série géométrique
n2 = n1 cn = 31 1,261 = 39,091 ;
n3 = n1 c2n = 31 1,2612 = 49,294 ;
n4 = n1 c3n = 31 1,2613 = 62,159
n5 = n1 q4n = 31 1,2614 = 78,383
n6 = n1 q5n = 31 1,2615 =98,841
n4 = n1 c3n = 31 1,2613 = 124,638
n4 = n1 c3n = 31 1,2613 = 157,169
n4 = n1 c3n = 31 1,2613 = 198,19
n4 = n1 c3n = 31 1,2613 = 249,918
n4 = n1 c3n = 31 1,2613 = 315,147
n4 = n1 c3n = 31 1,2613 = 397,4
Ainsi nf = 315,147 tr/min.
Nous pouvons maintenant déterminer Vf en utilisant la formule (7)
où D est le diamètre de la fraise, en mm ;
nf - vitesse de rotation, tr/min.
4 Nous calculons l'alimentation minute en utilisant la formule
En substituant les valeurs dans la formule (8), nous obtenons
Déterminons la valeur de Sm, la plus petite la plus proche des données du passeport de la machine : Sm = 249,65 mm/min
Déterminons l'avance réelle par dent
En substituant les valeurs dans la formule (9), nous obtenons
5 La force de coupe lors du fraisage est déterminée par la formule empirique
où t est la profondeur de fraisage ;
Sz - avance réelle, mm/dent ;
z - nombre de dents de coupe ;
D - diamètre de la fraise, mm
nf - vitesse de rotation réelle de la fraise tr/min.
Les valeurs du coefficient Cp et des exposants Xp, Yp, Up, qp ont les significations suivantes
CP = 545 ; Xp = 0,9 ; Yp = 0,74 ; Haut = 1 ; qp = 1.
La valeur du facteur de correction Kp lors du fraisage dépend de la qualité du matériau traité.
Ensuite, nous obtenons
Le facteur d'utilisation de la puissance de la machine est déterminé par la formule
où Ned est la puissance du moteur d'entraînement, kW ;
Npot est la puissance requise sur la broche, qui est déterminée par la formule
où Ne est la puissance de coupe effective, kW, déterminée par la formule
En substituant la valeur dans la formule (13), nous obtenons
En substituant les valeurs dans la formule (12), nous obtenons
Calculons maintenant le facteur d'utilisation de la puissance de la machine
La durée de vie réelle de l'outil Tf est calculée à l'aide de la formule
Remplaçons les valeurs dans la formule (14) et obtenons
6 Le temps passé pendant le processus de fraisage est déterminé par la formule
où L est la longueur de traitement estimée, en mm ;
je - nombre de passes ;
Sm - avance réelle, mm/min ;
La durée de traitement estimée est déterminée par la formule (16)
où l est la longueur de traitement, mm ;
l1 - taille d'entrée, mm ;
l2 - surcourse de la fraise, mm.
La quantité d'alimentation l1 est calculée à l'aide de la formule (17)
où t est la profondeur de coupe, mm ;
D - diamètre de coupe, mm.
On a
Supposons que la surcourse l2 soit de 4 mm.
Trouvez la longueur de traitement estimée L :
En utilisant la formule (15), nous calculons le temps principal
8 . Rationnementtemps,définitiondes prixEtcoûts de productionmécaniquetraitementdétails
1 Le temps pièce pour l'usinage d'une pièce est calculé par la formule
où t0 est le temps technologique principal, min ;
tв - temps auxiliaire, min ;
tob - temps d'entretien organisationnel et technique du lieu de travail, min ;
tf - temps de pauses pour le repos et les besoins physiques, min.
Le temps technologique principal est égal à la somme des valeurs de temps machine pour toutes les transitions d'une opération donnée.
Ainsi on obtient
où t01, t02, t03 est le temps principal de traitement de chaque surface, que l'on calcule à partir de la proportion
De la proportion (20) on obtient
Trouver t0i
t01 = 0,00456 100 = 0,456 min
t02 = 0,00456 100 = 0,456 min
t03 = 0,00456 100 = 0,456 min
En utilisant la formule (19), nous calculons Уt0 :
Temps auxiliaire - temps d'installation, de fixation et de retrait de la pièce, de fourniture et de retrait des outils, de mise en marche de la machine, de contrôle des dimensions.
En utilisant la littérature, nous obtenons
Le temps d'organisation et d'entretien du poste de travail comprend : le temps de réglage, de nettoyage et de lubrification de la machine, de réception et de rangement des outils, de changement d'outils émoussés, etc.
Le temps d'entretien du lieu de travail, ainsi que le temps de repos et les besoins physiques sont affectés à l'opération et calculés à l'aide de la formule
où b est le pourcentage pour l'entretien du lieu de travail ;
c - pourcentage pour le repos et les besoins physiques.
En utilisant la formule (21) on obtient
Ainsi, en utilisant maintenant la formule (18), nous pouvons calculer tpc
2 Le temps de calcul des pièces pour une opération est calculé à l'aide de la formule (22)
où tпз est le temps préparatoire et final pour l'ensemble du lot de pièces, min ;
n est le nombre de pièces dans le lot.
3 Ce temps est déterminé dans son ensemble pour l'opération et comprend le temps consacré par l'ouvrier à se familiariser avec la carte technologique de traitement de la pièce, à étudier le dessin, à mettre en place la machine, à obtenir, préparer, installer et retirer l'appareil pour effectuer cette opération.
Conformément à la littérature, le temps préparatoire et final est estimé à 30 minutes.
4 Le prix du travail effectué, c'est-à-dire le coût de la main-d'œuvre P est déterminé par la formule (23)
où Ct est le taux de droit de la catégorie correspondante ;
K - coefficient.
La valeur du taux de droit correspondant à la catégorie 4 est prise égale à
St = 247,64 roubles/h
On prend le coefficient K égal à 2,15.
Ainsi, en utilisant la formule (23) on obtient
5 Le coût d'usinage des pièces C comprend le coût de la main d'œuvre P et le coût des frais généraux H et est déterminé par la formule (24)
où N est le coût des frais généraux, frotter.;
P - coût du travail, frotter.
Le coût des frais généraux est pris égal à 1000% du coût de la main d'œuvre
En utilisant la formule (25) nous trouvons H
Ainsi, on calcule le coût d'usinage
9 . Constructiondispositifs
L'objectif du cours est de développer la conception d'un appareil inclus dans l'équipement technologique du processus d'usinage conçu.
Les machines-outils sont conçues pour l'installation et la fixation de la pièce et sont divisées : selon le degré de spécialisation - en universelles, réajustables, préfabriquées à partir de pièces et d'assemblages normalisés ; selon le degré de mécanisation - manuel, mécanisé, automatique ; par objectif - pour les dispositifs de tournage, de perçage, de fraisage, de meulage et autres machines ; par conception - monoplace et multiplace, monoplace et multiposition.
Le choix du type de montage dépend du type de production, du programme de production de pièces, de la forme et de la taille de la pièce et de la précision de traitement requise.
Lors de la conception d'une machine-outil, les tâches principales suivantes sont résolues :
1) élimination d'une opération à forte intensité de main-d'œuvre - marquage des pièces avant traitement ;
2) réduction du temps auxiliaire d'installation, de fixation et de réinstallation de la pièce par rapport à l'outil ;
3) augmenter la précision du traitement ;
réduction du temps machine et auxiliaire grâce au traitement simultané de plusieurs pièces ou au traitement combiné avec plusieurs outils ;
faciliter le travail du travailleur et réduire l’intensité du travail de transformation ;
capacités technologiques croissantes et spécialisation de la machine
Grâce à l'utilisation de l'appareil, la productivité devrait augmenter considérablement et le coût de traitement diminuera.
Comme dispositif de fraisage, nous choisissons un étau machine GOST 18684-73, dans lequel les mâchoires de serrage ont été modernisées. Cette modernisation contribue à faciliter le travail des travailleurs.
10. DécortechniqueDocumentation
Le document principal de la documentation technique est une feuille de route, qui indique toutes les opérations et transitions, ainsi que les équipements, les agencements, les outils de coupe et de mesure et le nombre de travailleurs.
Le profil et les dimensions sont indiqués.
Le deuxième document technologique est la carte d'exploitation. Il indique les transitions vers une opération, son numéro et le matériau de la pièce, sa masse et la dureté de la pièce. Pour toutes les transitions, un outil de coupe et de mesure est spécifié.
De plus, les dimensions de conception, la profondeur de coupe, le nombre de passes, les vitesses de broche et la vitesse des modes de traitement ont été calculés. Le temps machine et auxiliaire a été calculé.
11 . BasiqueintelligenceÔtechnologiesécuritéàtravailsurCoupe de métalMachines
Les précautions de sécurité couvrent un ensemble de dispositifs techniques et de règles qui garantissent une vie humaine normale pendant le processus de travail et excluent les accidents du travail. Lorsqu'il travaille sur des machines à couper les métaux, le travailleur doit être protégé contre l'exposition courant électrique, des impacts des pièces mobiles de la machine, ainsi que des pièces à usiner ou des outils de coupe en raison de leur faible fixation ou de leur rupture, des copeaux détachés, de l'exposition à la poussière et au liquide de refroidissement.
Règles générales de sécurité lors du travail sur des machines à couper les métaux
1. Les personnes qui ont subi un examen médical, suivi une formation d'introduction et sont autorisées à travailler de manière indépendante sont instruction initiale sur le lieu de travail, avoir un certificat de protection du travail.
2. Effectuer uniquement des travaux entrant dans le cadre de ses fonctions.
3. Travailler uniquement avec des vêtements de travail et des chaussures de sécurité en bon état et bien rentrés. fourni par les instructions sur la protection du travail.
4. Utilisez uniquement des appareils, équipements et outils réparables et utilisez-les aux fins prévues.
5. Ne laissez pas les machines et équipements allumés (en fonctionnement) sans surveillance.
En cas d'absence, même pour une courte durée, débranchez-le du secteur à l'aide de l'interrupteur secteur.
6. Ne marchez pas sous une charge surélevée.
7. Ne lavez pas les vêtements de travail avec du kérosène, de l'essence, des solvants, des émulsions et ne vous lavez pas les mains avec.
8. Ne touchez pas les parties sous tension des équipements électriques des machines et mécanismes, les pièces à usiner et les pièces en cours de traitement lorsqu'elles tournent.
9. Ne soufflez pas d'air comprimé sur les pièces et n'utilisez pas d'air comprimé pour éliminer les copeaux.
10. Utilisation au travail parquet et gardez-le en bon état et propre.
11. Principaux facteurs de production dangereux et nocifs :
possibilité de choc électrique ;
la possibilité de brûlures et de dommages mécaniques dus aux copeaux ;
augmentation du niveau de bruit;
possibilité de chute des pièces et pièces installées et traitées.
12. Lors de travaux sur des machines, l'utilisation de gants ou de mitaines n'est pas autorisée.
Exigences de sécurité à la fin des travaux.
1. Éteignez la machine et débranchez l'équipement électrique.
2. Rangez le lieu de travail.
3. Essuyez et lubrifiez les parties frottantes de la machine.
4. Nettoyer l'huile et l'émulsion déversées en saupoudrant de sable les zones contaminées.
5. Enlevez les copeaux et la poussière à l'aide d'une brosse à balai.
6. Chiffons utilisés lors du nettoyage et du travail, emporter les chiffons à l'extérieur de l'atelier dans les endroits désignés à cet effet.
7. Lors de la passation d'un quart de travail, informer le contremaître et le travailleur posté de toute déficience constatée et des mesures prises pour les éliminer.
8. Lavez-vous le visage et les mains eau chaude avec du savon ou prendre une douche.
Technique sécurité à travail sur tour à décolleter machine.
1. Avant d'allumer la machine, vous devez vous assurer que son démarrage ne présente pas de danger pour les personnes à proximité de la machine.
3. Fournir fixation fiable détails.
4. Lors du traitement de pièces sur centres, n'utilisez pas de centres avec des cônes usés.
7. Il est interdit de toucher les parties rotatives de la machine avec les mains, ainsi que la pièce à usiner.
8. Pour éviter que les vêtements ne soient happés par les pièces en rotation, vous devez soigneusement rentrer votre combinaison et rentrer vos cheveux sous votre coiffure.
9. Il est interdit de nettoyer, lubrifier, installer ou retirer des pièces pendant que la machine fonctionne.
10. L'accès à l'armoire électrique et au lieu de travail ne doit pas être encombré.
11. Si vous subissez une blessure, vous devez en informer le contremaître de chantier ou le chef d'atelier.
12. Attention !
Pour éviter la surchauffe du moteur, il n'est pas permis d'effectuer plus de 60 démarrages par heure à des tours de broche par minute jusqu'à 250, pas plus de 30 démarrages par heure à des tours supérieurs à 250 par minute et pas plus de 6 démarrages par heure à vitesse de broche 750 par minute.
Bibliographie
1. Manuel du technologue en génie mécanique : En 2 vol. T. /Ed. Kosilova A.G. et Meshcheryakova R.K. M., 1972.-694 p. T. 2 /Éd. Malova A.N. - M. : 1972. - 568 p.
2. Fedin A.P. Science des matériaux et technologie des matériaux : (Directives et devoirs pour papiers de test). - Gomel : BelGUT.-1992.-83 p.
3. Zobnine N.P. et autres. Traitement des métaux par découpe. - M. : Association pansyndicale d'édition et d'imprimerie du ministère des Chemins de fer, 1962. - 299 p.
Lakhtin Yu.M., Leontyeva V.P. Science des matériaux.-M., 1990.-528 p.
Manuel du métalleux. T. 5/. /Éd. B.L. Boguslavski. -M. : Génie Mécanique, 1997. -673 p.
Masterov V.A., Berkovsky V.S. Théorie de la déformation plastique et de la mise en forme des métaux. -M. : Métallurgie, 1989.400 p.
Kazachenko V.P., Savenko A.N., Tereshko Yu.D. Science des matériaux et technologie des matériaux. Partie III. Traitement des métaux par découpe : Un manuel pour la conception de cours - Gomel : BelGUT 1997.-47p.
Publié sur Allbest.ru
...Documents similaires
Développement d'un dispositif de fraisage d'une rainure de clavette. Structure du processus technologique d'usinage d'une pièce. Sélection d'équipements, d'outils ; calcul des conditions de coupe ; rationnement, détermination du coût d'une pièce ; précautions de sécurité.
travail de cours, ajouté le 26/07/2013
Le processus de découpe des métaux, son rôle dans l'ingénierie mécanique. Exigences de base pour la pièce conçue. Sélection d'équipements, d'appareils, d'outils pour le traitement de la pièce. Calcul des conditions de coupe. Type de pièce et allocations de traitement.
travail de cours, ajouté le 26/03/2013
Développement d'un processus technologique pour le traitement mécanique de l'arbre du chargeur de grains multi-godet TO-18A. Détermination du type de production. Calcul des allocations de transformation, des conditions de coupe, des normes de temps, de la précision des opérations. Conception de machines-outils.
travail de cours, ajouté le 07/12/2010
Type de production, nombre de pièces par lot. Type de pièce et allocations de traitement. Structure du processus technologique, sélection des équipements et appareils. Standardisation des délais, détermination des prix et des coûts d'usinage des pièces.
travail de cours, ajouté le 08/03/2016
Développement d'un procédé technologique d'usinage d'une pièce, d'un procédé d'obtention d'une ébauche de corps de vanne. Croquis opérationnels et système technologique assemblage, conception des dispositifs de fixation et d'installation de la pièce, tolérances pour son traitement.
travail de cours, ajouté le 27/01/2012
Détermination de la séquence des opérations technologiques d'usinage de la pièce « Arbre ». Justification du choix des machines, attribution des allocations de transformation. Calcul des conditions de coupe, des normes de temps et des facteurs de charge des machines-outils, leur quantité requise.
travail de cours, ajouté le 29/01/2015
Procédé de fabrication d'ébauches pour la partie inférieure du boîtier de roulement. Type de production, fonction de service de la pièce. Processus de parcours technologique d'assemblage et d'usinage de la carrosserie. Calcul des tolérances pour le traitement des dimensions de la pièce ; modes de coupe.
travail de cours, ajouté le 22/12/2014
Le processus technologique d'usinage de la pièce porteuse, le choix du matériau, le but de la production. Évaluation de la complexité, méthodes de traitement et d'assemblage. Détermination des conditions de coupe, normalisation détaillée d'une opération et préparation d'un dessin de pièce.
travail de cours, ajouté le 26/04/2012
Description et analyse technologique de la partie « Boîtier de frein auxiliaire ». Caractéristiques d'un type de production donné. Sélection de la pièce, sa conception. Développement et justification du processus technologique de traitement mécanique. Calcul des conditions de coupe.
travail de cours, ajouté le 10/02/2016
But et conception de la pièce « vis », parcours technologique d'usinage. Détermination du type de production et du mode d'obtention de la pièce. Calcul des tolérances, sélection des équipements, outils de coupe et de mesure ; sélection des modes de coupe.
Université d'État des communications sur l'eau de Saint-Pétersbourg
Département des technologies de réparation navale
Projet de cours
dans la discipline Fondamentaux de la technologie du génie mécanique naval
Complété:
étudiant du groupe SP-42
Chudin A.S.
Vérifié:
Tsvetkov Yu.
Saint-Pétersbourg
Les procédés technologiques en génie mécanique sont développés afin de :
1) sélectionner la séquence de traitement des pièces la plus appropriée, qui garantira la satisfaction des exigences techniques de la documentation de conception (dessins d'exécution) en termes de propriétés physiques et mécaniques et de paramètres de conception et technologiques (précision dimensionnelle, microrelief, etc.) ;
2) créer la base la plus stricte possible pour rationner le temps consacré à la production pièce individuelle lors d'unités d'usinage ou d'assemblage dans les domaines du sous-ensemble et de l'assemblage général.
Les processus technologiques de traitement mécanique servent de base à la conception des sites de production, des ateliers, etc.
Sur la base d'instructions technologiques plus spécifiques, les services de conception du département du technologue en chef conçoivent les montages, les outils spéciaux de coupe, de mesure et auxiliaires.
L'une des caractéristiques de l'ingénierie mécanique moderne est que la création de nouvelles machines est le plus souvent associée non pas à la conception et à la fabrication de modèles fondamentalement nouveaux, mais dans une plus large mesure à la modernisation et à l'amélioration de modèles éprouvés et bien éprouvés. centrales électriques, moteurs, etc.
Cette situation prédétermine une évolution tout à fait naturelle de la préparation technologique et organisationnelle de la production de construction mécanique.
En technologie, des analogies pour construire des processus technologiques basés sur belle expérience et les traditions de conception pratique.
L’organisation de la production s’oriente à juste titre vers des structures flexibles et rapidement reconfigurables.
Le document principal pour développer un processus technologique est un dessin d'exécution d'une pièce (unité d'assemblage). Les principaux facteurs influençant la conception des processus technologiques sont l'échelle de production et les exigences de qualité de la pièce. Les développeurs ont à leur disposition des catalogues d'équipements de coupe des métaux, d'outils de coupe et de mesure, d'équipements technologiques auxiliaires automatisés ou standardisés. Lors de l'attribution des modes de coupe et du rationnement du temps consacré à l'usinage, les normes générales de construction de machines de l'État et de l'industrie sont utilisées.
2. Analyse technologique du plan d'exécution de la pièce
L'analyse technologique du plan d'exécution d'une pièce (ou de la pièce elle-même) s'effectue dans les deux directions suivantes :
1) tests de conception de pièces pour la fabricabilité ;
2) analyse des propriétés technologiques réelles de la pièce.
Les tests de fabricabilité des conceptions sont effectués conjointement par les services de conception et technologiques au stade de la conception du produit. La tâche principale Un tel développement se réduit à donner aux formes, aux dimensions hors tout et aux méthodes de production des pièces les indicateurs (caractéristiques) les plus acceptables et les plus économiques pour les conditions données. Les tests de fabricabilité des conceptions sont effectués jusqu'à ce que le produit soit mis en production de masse. Tous les coûts associés à l'amélioration des conceptions au stade de leur test de fabricabilité sont attribués aux échantillons de produits prototypes (pièces).
Dans des cas justifiés, un tel développement simplifie les formes géométriques et donne plus de détails aux éléments structurels complexes. formes simples avec un accent sur le traitement mécanique sur des équipements universels.
La fabricabilité est un concept conditionnel, car la même conception, par exemple l'emboutissage, est certainement technologiquement avancée dans la production de masse et ne l'est pas du tout lors de la production de pièces en échantillons uniques, etc.
Un indicateur important de la fabricabilité d'une conception de pièce est l'orientation du travail dimensions linéaires circuits aux conditions spécifiques de production et d'utilisation pour garantir leur exactitude de certaines méthodes. Lors des tests de fabricabilité, dans certains cas, les dimensions maximales (écarts) sont resserrées technologiquement pour créer de meilleures conditions pour baser les pièces pendant l'usinage.
Les propriétés technologiques des pièces sont analysées sur la base des propriétés physiques et mécaniques du matériau et des paramètres de conception et technologiques.
Parmi les propriétés physiques et mécaniques des matériaux, la plasticité, la dureté superficielle et générale, l'état de la pièce, etc. sont pris en compte. Les matériaux plastiques ou cassants déterminent le choix presque sans ambiguïté du matériau de l'outil de coupe, en particulier pour les alliages durs. Lors du traitement des matières plastiques, par exemple l'acier, des alliages titane-tungstène-cobalt plus productifs mais moins durables de type TK (T5K10, T5K6, etc.) sont utilisés. Au contraire, pour le traitement des alliages fragiles (fonte, etc.), des alliages durs plus durables du groupe tungstène-cobalt de type VK (VK3, VK6, etc.) sont utilisés.
Lors de l'analyse technologique de la conception et des caractéristiques technologiques, les éléments suivants sont optimisés :
1) paramètres de précision dimensionnelle (degrés de précision des surfaces externes et des trous, dimensions avec et sans écarts maximaux) ;
2) paramètres du microrelief (intervalles de changements des paramètres du microrelief des surfaces externes et des trous, surfaces avec différentes significations dureté);
3) écarts des surfaces traitées par rapport à la forme et écarts dans la position relative des surfaces de base.
Dans cette analyse, l'attention est portée sur l'impact que chacune de ces caractéristiques (paramètres) a sur la structure et le contenu du processus technologique de traitement mécanique.
3. Structure et conception du processus technologique
Tout processus technologique d'usinage de pièces est structurellement composé de technologies de routage et d'exploitation. Le plus détaillé est la technologie d’exploitation. Il comprend les opérations technologiques. Parmi les principales composantes des opérations technologiques figurent les installations et les transitions technologiques. Les installations font partie d'une opération technologique réalisée avec une fixation constante de la pièce.
Conformément au Système Unifié de Documentation Technologique (USTD) ensemble complet les documents technologiques comprennent un grand nombre formulaires standards(kart). Dans la conception pratique, le type et le nombre de cartes technologiques dépendent de conditions de production spécifiques et sont déterminés par des normes.
Un processus technologique d'itinéraire est une description élargie de la séquence et du contenu des opérations technologiques effectuées pour transformer une pièce en une pièce finie.
Le processus technologique opérationnel est établi sur des fiches opérationnelles spéciales. Contrairement à la technologie des itinéraires, les cartes technologiques opérationnelles fournissent un enregistrement détaillé de la séquence de traitement de chaque surface individuelle avec des détails sur toutes les informations technologiques nécessaires.
Un croquis (dessin technologique opérationnel) est image graphique pièces sous la forme sous laquelle elles « sortent » d’une opération donnée après transformation.
Les informations et symboles suivants sont indiqués sur le dessin opérationnel :
1) surfaces traitées avec des lignes plus épaisses ; numéros de série de ces surfaces ; en même temps, si toutes les surfaces désignées sont traitées avec le même outil dans les mêmes modes de coupe, alors dans la carte technologique opérationnelle, il y aura exactement autant de transitions principales qu'il y a de surfaces traitées ;
2) tous les paramètres de précision des surfaces traitées : des normes de précision et des paramètres de microrelief sont requis, si nécessaire - précision des formes et de la position relative ;
3) surfaces de base (leur représentation graphique est standardisée).
Des croquis des processus technologiques sont élaborés pour chaque opération technologique.
4. Méthodologie de développement de technologies opérationnelles pour l'usinage
Les facteurs suivants influencent le choix de la séquence d'usinage d'une pièce :
1) nature de la production ;
2) exigences relatives à la qualité de la pièce finie en termes de paramètres de précision, d'état et de propriétés physiques et mécaniques de la couche superficielle traitée.
Dans une seule production, les opérations technologiques comprennent un grand nombre d'installations et de transitions pour traiter de nombreuses surfaces externes et internes. Tout cela nécessite des changements et ajustements fréquents des outils, une dépense de temps auxiliaire, etc.
Dans les processus technologiques de production en série conçus pour des machines spéciales, les opérations du même nom sont différenciées et peuvent consister en une transition auxiliaire et une transition principale. Il n'y a pas de réinstallation de pièces en une seule opération, les changements d'outils sont minimisés et le temps consacré au réglage des outils est réduit.
Lors de l'évaluation de l'influence des exigences de qualité de la pièce finie sur la construction du processus technologique, on peut provisoirement se guider par les éléments suivants :
1) tout processus technologique doit être soutenu par un schéma structurel (Fig. 1) ;
2) les étapes du processus technique sont interconnectées avec des paramètres de précision et des méthodes de traitement ;
3) l'augmentation de la dureté de surface jusqu'à HRC 35 ci-dessus nécessite une transition du traitement avec un outil à lame au traitement abrasif ;
4) les ensembles d'outils de centrage lors du traitement des trous sont pris conformément aux paramètres de précision de la surface.
Figure 1. Schéma fonctionnel du processus technologique de fabrication des pièces
Tableau 1. Relation étapes technologiques avec des paramètres de précision lors du traitement avec une lame ou outil abrasif surfaces externes
Étape n° | Options de précision | ||||||
Qualité | Microrelief, microns | Lame | Abrasif | ||||
Rz | Râ | ||||||
000 | Vide | Selon GOST pour les blancs | |||||
005 | |||||||
010 | 14 | 80 | Broyer d'abord | ||||
015 | Traitement thermique : recuit pour soulager les contraintes internes | ||||||
020 | Usinage semi-fini | 11 | 20 | Moudre | |||
025 | |||||||
030 | Finition de l'usinage à la dureté superficielle : | ||||||
HB = 120 – 180 | 9 | 2,5 | Broyer proprement (enfin) | ||||
9 et 7 | 1,25 | Broyer proprement (au préalable) | |||||
HRC = 40 | 9 | 2,5 | |||||
9 et 7 | 1,25 | Pré-broyage Broyer complètement |
Tableau 2. Relation entre les étapes technologiques et les paramètres de précision lors du traitement des surfaces internes avec une lame ou un outil abrasif
Étape n° | Nom et contenu de la scène | Options de précision | Transition technologique lors de l'usinage des outils | ||||
Qualité | Microrelief, microns | Lame | Abrasif | ||||
Rz | Râ | centre | décentré | ||||
000 | Vide | Selon GOST pour les blancs | |||||
005 | Traitement thermique : recuit pour soulager les contraintes internes | ||||||
010 | Usinage grossier | 14 | 80 | Percer | Déchets | ||
015 | Traitement thermique : recuit pour soulager les contraintes internes | ||||||
020 | Mécanique semi-finie | 11 | 20 | Foret à fraiser | Déchets | ||
025 | Traitement thermique pour améliorer les propriétés physiques et mécaniques des pièces conformément aux instructions du dessin | ||||||
030 | Finition mécanique à dureté superficielle : | ||||||
HB = 120 – 180 | 9 | 2,5 | Foret à fraiser Agrandir | Je m'ennuie (enfin) | |||
9 et 7 | 1,25 | Foret Fraise Agrandir préliminaire Agrandir final | |||||
HRC = 40 | 9 | 2,5 | Poncer propre (enfin) | ||||
9 et 7 | 1,25 | Pré-broyage Broyer complètement |
5. Modes de découpe et standardisation du processus technologique (opérations)
Les modes de coupe incluent la profondeur de coupe t mm, l'avance de l'outil S mm/tr (mm/min), la vitesse de coupe V m/min, la puissance de coupe kW.
Les modes de coupe constituent la base de la standardisation des opérations technologiques, de la sélection des équipements et de la configuration de la machine pour effectuer une transition technologique spécifique.
Les modes de coupe sont déterminés par calcul ou attribués selon des tableaux.
Le calcul théorique des conditions de coupe est plus rigoureux. Cependant, les dépendances empiriques calculées donnent plutôt une meilleure idée de la nature de l'interaction divers facteurs que des estimations quantitatives. Par conséquent, les calculs théoriques sont extrêmement rarement utilisés dans les applications pratiques.
L'attribution des modes de coupe à l'aide de tableaux est simple et accessible à l'utilisateur même avec peu d'expérience en conception de processus.
L'attribution des modes de coupe est précédée du choix du matériau de la pièce et du matériau de l'outil.
Le choix du matériau de la pièce à usiner est prédéterminé presque sans ambiguïté par le dessin d'exécution de la pièce.
Parmi les matériaux d'outils utilisés dans le travail des métaux moderne, on utilise des aciers à outils en alliage de carbone, des alliages durs et des matériaux d'outils très durs.
Dans le domaine de la construction mécanique, jusqu'à 70 % des usinages mécaniques impliquent des usinages avec des outils à lame en alliages durs. Tous les alliages durs, conformément aux recommandations des organismes de normalisation internationaux, selon les matériaux pour lesquels ils sont destinés à être transformés, sont répartis dans les trois groupes suivants :
1)P – pour le traitement des aciers au carbone, faiblement et moyennement alliés ; il s'agit d'alliages du groupe titane-tungstène-cobalt tels que le T5K10, le T15K6, etc. ; ils se caractérisent par une résistance à l'usure accrue avec une résistance mécanique relativement faible et permettent des vitesses de coupe allant jusqu'à 250 m/min ;
2)K – pour le traitement de matériaux contenant des copeaux libres, tels que la fonte, etc. ; ce sont des alliages du groupe tungstène-cobalt de type VK ; ils sont plus durables, mais moins résistants à l'usure ;
3)M – alliages durs pour le traitement d’alliages spéciaux.
Lors de l'attribution des modes, déterminez :
1) la découpe comme différence entre les dimensions de la surface usinée sur la précédente sur la transition étant réalisée selon les croquis opérationnels ;
2) avance de l'outil lors du tournage, du perçage, du fraisage, de l'alésage et de la rectification, selon le type d'usinage : ébauche, semi-finition, finition ;
3) vitesse de coupe selon les tableaux.
Il faut garder à l'esprit que la vitesse de coupe dépend de la durabilité du matériau de l'outil et est en quelque sorte imaginaire pour l'opérateur. La vitesse de broche de la machine est toujours importante pour l'opérateur, car la machine peut être réglée sur une vitesse de broche spécifique, et non sur la vitesse de coupe.
Par conséquent, la vitesse de coupe acceptée est recalculée à la vitesse de broche n selon la formule
où D est le diamètre de la surface usinée ou de l'outil central, en mm.
La standardisation du processus technologique revient à déterminer le temps nécessaire pour effectuer chaque opération individuelle et, si nécessaire, l'ensemble du processus technologique.
Sur la base du temps passé sur chaque opération, les salaires des principaux ouvriers de production sont calculés.
Dans la production unitaire, les coûts de temps sont estimés à l'aide du temps dit de calcul à la pièce Tpc.k.. Ce temps est calculé à l'aide de la formule
où Тп.з – temps préparatoire et final pour effectuer l'opération technologique ; il est prévu pour la familiarisation avec les dessins d'exécution, le processus technologique et la mise en place de la machine ;
m – nombre de pièces dans le lot en cours de traitement ;
Tscht. – du temps partiel pour réaliser une opération technologique.
En production de masse, le nombre de pièces traitées est important et, par conséquent, Tp.z./m─>0 et Tpc.k.= Tpc.
Le temps partiel est déterminé dans son ensemble pour une opération technologique selon l'expression :
où TO est l'heure principale d'exécution d'une opération technologique,
TV – temps auxiliaire pour effectuer une opération technologique,
K= (1,03 – 1,10) – coefficient qui prend en compte le temps consacré à l'entretien organisationnel et technique de la machine et au repos.
Le temps principal est déterminé pour chaque transition principale et le temps auxiliaire est déterminé pour toutes les transitions (principale et auxiliaire).
Le temps principal est le temps consacré directement à la découpe. Pour tous types d'usinage :
où Ar est la longueur estimée de la surface traitée.
Le temps auxiliaire est attribué selon des normes sous la forme de la somme de composantes individuelles, à savoir :
où tset est le temps de pose et de dépose de la pièce, pris en compte une fois par opération, s'il n'y a pas de réinstallation de la pièce,
tpr – temps associé à la mise en œuvre de la principale transition technologique ; il est prévu pour l'alimentation (rétraction) d'un outil, la mise en marche (l'arrêt) de la machine, etc. ; est pris en compte autant de fois que les principales transitions de l'opération ;
tn et ts – respectivement, le temps de changement de la vitesse de la broche (outil) et de l'avance de l'outil (pièce) ;
tmeas – temps de mesure, pris en compte pour chaque surface traitée (mesurée) ;
tcm – le temps de changement d'outil, le temps d'installation initiale (réglage) de l'outil est inclus dans le tpr de la première transition technologique principale ;
téléviseurs – il est temps de retirer la perceuse pour éliminer les copeaux ; ne sont fournis que lors du perçage de trous dans des pièces solides.
Dans les travaux de cours, nous acceptons sous condition :
tset =1,2 min., tpr =0,8-1,5 min., ( grandes valeurs pour la semi-finition et les plus petites pour les transitions d'ébauche), tn = ts = 0,05 min., tmeas = 0,08 – 1,2 min. (valeurs plus grandes pour les calibres, valeurs plus petites pour un instrument de mesure universel), tcm = 0,10 min, tvs = 0,07.
partie de traitement d'arbre technologique
Tableau 3. Calcul du temps consacré à la réalisation d'une opération technologique
Nombres | Heure principale, min | |||||||||||||||||||
Opérations | Transition | bouche | tpr | tn | ts | tisme | MTC | |||||||||||||
05 | 1(A) | - | 1,2 | - | - | - | - | - | ||||||||||||
2 | 0,02 | - | 0,8 | - | - | 0,1 | - | |||||||||||||
3 | 0,03 | - | 0,8 | 0,05 | 0,05 | - | 0,1 | |||||||||||||
À = 0,05 min. Télévision = 3,1 minutes. Tsht = 1,05(À + Tv) = 1,05(0,05 + 3,1) = 3,31 min. |
||||||||||||||||||||
010 | 1(A) | - | 1,2 | - | - | - | - | - | ||||||||||||
2 | 0,29 | - | - | - | - | - | - | |||||||||||||
À = 0,29 min. Télévision = 1,2 min. Tsht = 1,05(À + Tv) = 1,05(0,29 + 1,2) = 1,56 min. |
||||||||||||||||||||
015 | 1(A) | - | 1,2 | - | - | - | - | - | ||||||||||||
1 | 0,47 | - | - | - | - | - | - | |||||||||||||
À = 0,47 min. Télévision = 1,2 min. Tsht = 1,05(À + Tv) = 1,05(0,47 + 1,2) = 1,75 min. |
||||||||||||||||||||
025 | 1(A) | - | 1,2 | - | - | - | - | - | ||||||||||||
2 | 0,32 | - | 1,0 | - | - | - | - | |||||||||||||
3 | 0,10 | - | 1,0 | - | 0,05 | - | 0,1 | |||||||||||||
4 | 0,04 | - | 1,0 | 0,05 | - | - | - | |||||||||||||
5 | 0,48 | - | 1,0 | 0,05 | 0,05 | 0,1 | 0,1 | |||||||||||||
6 | - | 1,0 | - | - | 0,1 | - | ||||||||||||||
7 | 0,20 | - | 1,0 | - | 0,05 | - | - | |||||||||||||
Cela = 1,14 min. Télévision = 7,85 minutes. Tsht = 1,05 (To + Tv) = 1,05 (1,14 + 7,85) = 9,44 min. |
||||||||||||||||||||
030 | 1(A) | - | 1,2 | - | - | - | - | - | ||||||||||||
2 | 0,02 | - | 1,0 | - | - | 0,1 | - | |||||||||||||
3 | 0,16 | - | 1,0 | 0,05 | - | 0,1 | - | |||||||||||||
4 | 0,20 | - | 1,0 | 0,05 | - | 0,1 | - | |||||||||||||
5 | 1,1 | - | 1,0 | - | - | 0,5 | 0,1 | |||||||||||||
6 | 0,04 | - | 1,0 | 0,05 | - | 0,5 | 0,1 | |||||||||||||
7 | 0,07 | - | 1,0 | - | - | 0,5 | - | |||||||||||||
8 | 0,05 | - | 1,0 | 0,05 | - | 0,5 | - | |||||||||||||
9 | - | - | 1,0 | - | - | 0,5 | - | |||||||||||||
À = 1,64 min. Télévision = 10,15 minutes. Tsht = 1,05(À + Tv) = 1,05(1,64 + 10,15) = 12,38 min. |
||||||||||||||||||||
040 | 1(A) | - | 1,2 | - | - | - | - | - | ||||||||||||
2 | 2,0 | - | 1,5 | - | - | 0,2 | - | |||||||||||||
À = 2,0 min. Télévision = 2,9 minutes. Tsht = 1,05(À + Tv) = 1,05(2,0 + 2,9) = 5,15 min. |
||||||||||||||||||||
045 | 1(A) | - | 1,2 | - | - | - | - | - | ||||||||||||
2 | 0,5 | - | - | - | - | 0,2 | - | |||||||||||||
3 | 0,5 | - | - | - | - | 0,2 | - | |||||||||||||
4 | 0,5 | - | - | - | - | 0,2 | - | |||||||||||||
Puis = 1,5 min. Télévision = 1,8 min. Tsht = 1,05(À + Tv) = 1,05(1,5 + 1,8) = 3,47 min. |
||||||||||||||||||||
050 | 1(A) | - | 1,2 | - | - | - | - | - | ||||||||||||
2 | 0,48 | - | 1,5 | - | - | 0,2 | - | |||||||||||||
À = 0,48 min. Télévision = 2,9 minutes. Tsht = 1,05(À + Tv) = 1,05(0,48 + 2,9) = 3,55 min. |
||||||||||||||||||||
Nombres | S, mm/tour | n, tr/min | Temps principal T0, min | Temps auxiliaire TV, min | ||||||||||||||||
Opérations | Transition | bouche | tpr | tsun | tn | ts | tisme | MTC | ||||||||||||
instr. | cond. bagues | |||||||||||||||||||
055 | 1(A) | - | - | - | 1,2 | - | - | - | - | - | - | - | ||||||||
2 | 0,3 | 630 | 0,11 | - | 1,5 | 0,07 | - | - | - | - | - | |||||||||
3 | 0,8 | 630 | 0,04 | - | 1,5 | - | 0,05 | 0,05 | - | 0,1 | 0,1 | |||||||||
4 | 1,0 | 250 | 0,08 | - | 1,5 | - | 0,05 | 0,05 | 0,2 | 0,1 | 0,1 | |||||||||
5 | - | - | - | - | 1,5 | - | - | - | - | 0,1 | 0,1 | |||||||||
À = 0,23 min. Télévision = 8,27 minutes. Tsht = 1,05(À + Tv) = 1,05(0,23 + 8,27) = 8,93 min. |
6. Calcul des chaînes dimensionnelles
Calcul des chaînes dimensionnelles lors du remplacement de la dimension de fermeture
Type de recalcul d'une chaîne dimensionnelle dans lequel, quelle que soit la séquence de recalcul, la précision du format A6 sera assurée automatiquement.
Figure 2. Schéma de la chaîne dimensionnelle lors du remplacement du maillon de fermeture
Le calcul est effectué sous forme de tableau.
Calcul des tolérances des dimensions des composants dans les chaînes dimensionnelles technologiques | |||||||||||
Dimensions | Distribution | ||||||||||
Désignation | Signification | Uniforme | Même qualité TA6 = 0,4 ; ast = 40 µm. |
||||||||
TAi = =TA6/m | TAik/ /TAi | Gamme de tailles, mm | Aïsr, mm | TAÏ, mm | TAik/ /TAi | ||||||
A1 | 30 | -0,45 | 0,45 | 0,07 | 6,4 | 18 - 30 | 24 | 2,88 | 1,13 | 0,05 | 9 |
A2 | 200 | -0,5 | 0,50 | 0,07 | 7,1 | 180 - 250 | 215 | 5,99 | 2,70 | 0,12 | 4 |
A3 | 25 | +0,2 | 0,20 | 0,07 | 2,9 | 18 - 30 | 24 | 2,88 | 1,13 | 0,05 | 4 |
A4 | 45 | +0,4 | 0,40 | 0,07 | 5,7 | 30 - 50 | 40 | 3,42 | 1,54 | 0,06 | 7 |
A5 | 25 | +0,25 | 0,25 | 0,07 | 3,6 | 18 - 30 | 24 | 2,88 | 1,13 | 0,05 | 5 |
A6 | 5 | +0,2 | 0,40 | - | - | - | - | - | - | - | - |
À | 70 | - | - | 0,05 | - | 50 - 80 | 65 | 4,02 | 1,81 | 0,07 | - |
TAi1=1,13*0,4/9,44=0,05 TAik1/ TAi1=0,45/0,05=9
TAi2=2,70*0,4/9,44=0,12 TAik2/ TAi2=0,50/0,12=4
TAi3=1,13*0,4/9,44=0,05 TAik3/ TAi3=0,20/0,05=4
TAi4=1,54*0,4/9,44=0,06 TAik4/ TAi4=0,40/0,06=7
TAi5=1,13*0,4/9,44=0,05 TAik5/ TAi5=0,25/0,05=5
TAit=1,81*0,4/9,44=0,07
L'analyse des résultats obtenus montre que la modification de la chaîne dimensionnelle linéaire pour des raisons technologiques entraîne un resserrement de leurs valeurs de 2 à 6 fois.
Calcul de la chaîne dimensionnelle selon la méthode « maximum – minimum »
Dans certains cas, par exemple lors de la préparation de l'assemblage des pièces à assembler, il peut être conseillé d'évaluer les éventuelles fluctuations de la taille de fermeture. Cette évaluation est réalisée en calculant la chaîne dimensionnelle, qui inclut la dimension de clôture, en utilisant les écarts maximaux selon la méthode « maximum – minimum ».
Figure 3. Schéma de la chaîne dimensionnelle lors du calcul du maillon de fermeture
A0, es(A0) et ei(A0) – respectivement, la taille, l'écart maximum supérieur et inférieur du maillon de fermeture ;
Auv, es(Auv) et ei(Auv) – respectivement la taille, l'écart maximum supérieur et inférieur de la taille croissante ;
Aium, es(Aium) et ei(Aium) – respectivement la taille, l'écart maximal supérieur et inférieur des dimensions réductrices ;
A2 = Auv = 200 ; es(Auv) = 0; ei(Auv) = -0,5 ;
A1 = A1um = 30 ; es(A1um) = 0; ei(A1um) = -0,45 ;
A6 = A6um = 5 ; es(A6um) = 0,2 ; ei(A6um) = -0,2 ;
A5 = A5um = 25 ; es(A5um) = 0,25 ; ei(A5um) = 0 ;
A4 = A4um = 45 ; es(A4um) = 0,4 ; ei(A4um) = 0 ;
A3 = A3um = 25 ; es(A3um) = 0,2 ; ei(A3um) = 0 ;
TAuv = 0,5 ; TA1um = 0,45 ; TA6um = 0,4 ; TA5um = 0,25 ; TA4um = 0,4 ; TA3um = 0,2 ;
1) Taille nominale du lien de fermeture :
2) Écart limite supérieure :
3) Écart de limite inférieure :
4) Tolérance des dimensions de fermeture :
5) La tolérance est également déterminée :
La conversion a été effectuée correctement.
7. Processus technologique traitement mécanique de l'arbre d'extrémité
Matériel | Détails de masse | |||||||
Nom, marque | Voir | Profil | ||||||
Acier 35 | Estampillage | |||||||
opérations |
Nom et contenu de l'opération | Équipement | Appareil et outil | Tp.z. | ||||
Tsht | ||||||||
000 | Approvisionnement Estampage vierge |
|||||||
005 | Tournant. Terminez la coupe. Fin de l'alignement |
Tournant 1K62 | Mandrin à 3 mors. Coupeur passable. Foret de centrage. | 3,02 | ||||
010 | Tournage CNC. Préliminaire. Traitement des surfaces extérieures. | Tour CNC 1K20F3S5 |
Serrage spécial Coupeur passable. | 6,41 | ||||
015 | Tournage CNC. Couper l'extrémité, traiter la surface extérieure de la bride. | Tour CNC 1K20F3S5 | Serrage spécial. Coupeur passable. | 5,71 | ||||
020 | Thermique. Recuit pour soulager le stress interne. | Spécial | ||||||
025 | Tournant. Traitement semi-fini des surfaces externes et internes. | Tournant 1K62 | Mandrin à 3 mors. Foret hélicoïdal, fraise aléseuse, fraise traversante. | 1,06 | ||||
030 | Tournant. Semi-finition de surfaces extérieures | Tournant 1K62 | Mandrin à 3 mors. Centre. tournant. Fraise à rainures, fraise traversante. | 0,81 | ||||
035 | Chimique-thermique. Cimentation. Durcissement. | Spécial. | ||||||
040 | Meulage interne. Meulage final du trou. | Meulage 3A240 | Dispositif de meulage cylindrique spécial. | 1,94 | ||||
045 | Meulage cylindrique. Ponçage final des surfaces extérieures. | Broyage 3152 | Mandrin à pince, au centre. tourner meuleuse cylindrique | 2,88 | ||||
050 | Forage vertical. Taraudage d'un trou dans une bride d'arbre. | Perceuse verticale 2A125 | Dispositif de serrage. Robinet machine. | 2,82 | ||||
055 | Forage radial. Usinage de trous sur la bride d'arbre | Perceuse radiale 2A53 | Facture spéciale du conducteur. Perceuse, fraiseuse, alésoir. | 1,12 | ||||
060 | Test. Contrôle final de la pièce selon le dessin. |
15,5/1250*0,5=0,025 ;
10/2000*0,2=0,025
25/2000*0,5=0,03;
45/1600*0,5=0,06;
25/1250*0,5=0,04;
70/1000*0,5=0,14;
32/400*0,5=0,16;
60/400*0,5=0,3;
38/400*0,3=0,32;
0,5/1000*0,3=0,10;
20/1000*0,5=0,04;
60/500*0,25=0,48;
31/630*0,25=0,20
5/1000*0,25=0,02;
25/630*0,25=0,16;
80/1600*0,25=0,20;
25/2500*0,25=0,04;
45/2500*0,25=0,07
25/2000*0,25=0,05;
Tableau 4. Commentaire sur le processus technologique d'usinage
Structure | Contenu |
Technologie d'itinéraire | La technologie des itinéraires, tout comme la technologie opérationnelle, est élaborée sur des cartes technologiques standards. Pour simplifier méthodiquement la conception pédagogique dans les cartes technologiques, un certain nombre de graphiques qui ne portent pas fondamentalement une information important, ne sont ni remplis ni marqués. Le parcours processus technologique est construit conformément aux recommandations des lignes directrices sur l'influence des exigences de qualité des pièces sur la structure du processus technique, à savoir : il comprend les étapes préliminaire, semi-finition et finale (finition) traitement. Dans le processus technologique (dans les cartes routières), nous prenons le temps préparatoire et final égal à zéro (correspond aux conditions de production de masse) et ne l'indiquons pas dans les cartes. |
Opération 000 | L'opération de découpage est conçue en mettant l'accent sur la production de masse et c'est pour cette raison que l'emboutissage est choisi comme ébauche. Les tolérances d'usinage sont prises de telle manière qu'elles puissent être supprimées lors des opérations de pré-traitement en un seul passage. Ceci est parfaitement acceptable à des fins éducatives. En pratique, les dimensions des pièces sont prises en compte en tenant compte des tolérances préconisées par les tableaux réglementaires. Ici, les valeurs numériques de tolérances suivantes ont été établies : pour le traitement préliminaire - 2,5 mm, la semi-finition - 0,75 mm et la finale (meulage) - 0,25 mm par côté. Naturellement, ces tolérances déterminent clairement les dimensions de la pièce. Les dimensions maximales d'emboutissage ont été fixées selon une technique d'emboutissage typique : la limite supérieure plus (écart pour l'usure de la matrice) est toujours plus grande, la limite inférieure moins (pour le sous-estampage) est toujours plus petite. De plus, sur le dessin technologique d'emboutissage, les dimensions nominales des surfaces de la pièce finie sont indiquées entre parenthèses. |
Opération 005 | Conçu pour créer une base d'installation sous la forme d'un trou central. De tels trous sont traités technologiquement même dans les cas où ils ne sont pas indiqués sur le dessin (sauf exigences spécialement spécifiées). |
Opération 010 | La conception de la pièce est assez avancée technologiquement pour l’utilisation d’une machine CNC. La particularité de sa conception est que pour amener la chaîne dimensionnelle à un système de coordonnées absolu, il a été nécessaire de transformer la chaîne dimensionnelle de conception en chaîne technologique. Le programme de contrôle a été développé selon un algorithme standard. Étant donné que tous les traitements sont prévus dans le programme, lors du calcul du coût du temps auxiliaire, seul le temps d'installation et de retrait de la pièce a été pris en compte. Les vitesses de rotation de la broche de la machine ont été optimisées en fonction des diamètres des pas de la pièce, les ramenant aux valeurs standards. |
Opération 015 | Le fonctionnement est similaire au précédent sur une machine CNC. Comme lors de l'opération 010, les transitions de contrôle n'ont pas été prévues, puisque le travail selon le programme de contrôle se limite à un contrôle périodique des réglages de la machine. |
Opération 020 | Thermique. Ne nécessite pas de commentaires particuliers et son objectif ressort clairement de carte technologique. Le contenu de ce traitement thermique est déterminé en fonction des procédés technologiques du métallurgiste en chef de l'entreprise. |
Opération 025 | Nous commençons la semi-finition en créant une autre base d'installation pratique sous la forme d'un trou. Ceci se justifie également par le fait que d'après le dessin relatif à l'axe du trou, les pré-requis techniques le long du battement radial de l'une des surfaces extérieures. Les vitesses de coupe lors du tournage transversal et de l'alésage, si nécessaire, peuvent être ajustées en fonction de la vitesse de coupe lors de la coupe longitudinale en introduisant un coefficient de 0,8-0,9. |
Opération 030 | Traitement semi-fini des surfaces externes. Pour l’instant, aucune précision particulière n’est requise. En pratique, toutes choses égales par ailleurs, un tel socle est toujours plus économique. Nous réduisons la préparation de la pièce pour le traitement final à la découpe de rainures technologiques pour la sortie de la meule lors du traitement de finition. |
Opération 035 | Nous incluons cette opération dans la démarche technique à la demande du concepteur (dessin d'exécution). Faisons attention à certaines caractéristiques de cette opération chimico-thermique, à savoir : 1) elle sert à augmenter la dureté superficielle à un tel valeurs numériques, dans lequel un traitement mécanique ultérieur avec un outil à lame devient impossible et une transition vers le meulage est nécessaire ; 2) comme on peut le voir, la surface est saturée de carbone jusqu'à une certaine profondeur ; cette profondeur est contrôlée par les fractures des échantillons, appelées témoins, qui sont spécialement réalisées simultanément au traitement de la pièce. Si nécessaire, la microstructure peut être déterminée à partir de ces échantillons. Lors de la cémentation, les surfaces qui ne sont pas indiquées sur le dessin et ne nécessitent pas de dureté accrue sont protégées de manière particulière avant le traitement chimico-thermique. |
Opération 040 | Traitement final en meulant la ceinture de sécurité. Basé sur la production de masse, un tampon tampon est utilisé comme outil de mesure. |
Opération 045 | Traitement final (finition) des surfaces externes. Inconditionnellement basé sur le trou interne avec compression par le centre rotatif arrière pour augmenter la rigidité système technologique. La longueur des surfaces traitées étant faible, le meulage est réalisé par plongée. Les dimensions sont contrôlées avec des jauges à pince. |
Opération 050 | Ne nécessite aucun commentaire particulier. |
Opération 055 | Nous prévoyons le traitement des trous sur une perceuse radiale dans un gabarit spécial pour éliminer les opérations de marquage du processus technique et garantir la précision spécifiée dans l'emplacement des trous. Nous acceptons l'ensemble des outils de centrage selon les recommandations du référentiel. Contrôle de la précision des trous à l'aide de jauges à tampon. |
Bibliographie
1. Sumerkin Yu.V. Fondamentaux de la technologie du génie mécanique (cours) - Saint-Pétersbourg ; SPGUVK, 2002
2. Sumerkin Yu.V. Fondamentaux de la technologie du génie mécanique des navires : Manuel - Saint-Pétersbourg ; SPGUVK, 2001 – 240 p.
Structure du processus
PROCESSUS TECHNOLOGIQUE ET SA STRUCTURE (CONCEPTS DE BASE ET DÉFINITIONS)
Processus de production et technologiques
Processus de production en usine(site, atelier) désigne l'ensemble des processus d'organisation, de planification, d'approvisionnement, de fabrication, de contrôle, de comptabilité, etc., nécessaires à la conversion des matériaux et produits semi-finis arrivant à l'usine en produits finis de l'usine (magasin) . Ainsi, processus de fabrication- il s'agit de l'ensemble de toutes les actions des personnes et des outils de production réalisées pour la fabrication de produits manufacturés dans une entreprise donnée.
Le processus de production est complexe et diversifié. Il comprend : le traitement des ébauches pour en obtenir des pièces ; assemblage de composants et de moteurs et leurs essais ; mouvement à toutes les étapes de la production ; organisation de l'entretien des lieux de travail et des sites; gestion de tous les niveaux de production, ainsi que tous les travaux sur entrainement technique production.
Bien entendu, dans tout processus de production, la place la plus importante est occupée par les processus directement liés à l'atteinte des paramètres de produit spécifiés. De tels processus sont appelés technologiques. Processus technologique- il s'agit d'une partie du processus de production qui contient des actions visant à modifier systématiquement la taille, la forme ou l'état de l'objet de travail et leur contrôle (GOST 3.1109-82).
En production Moteurs d'avion Ils utilisent des procédés variés : fonderie, traitement sous pression et découpe, traitement thermique et physico-chimique, soudage, brasage, assemblage, essais. Ainsi, selon le type de procédé et le type de produit, on distingue le procédé technologique de coulée, par exemple des aubes de turbine ; processus technologique traitement thermique, par exemple, un arbre de turbine ; processus technologique de traitement mécanique, etc. En ce qui concerne les processus de façonnage, on peut formuler qu'un processus technologique est un système d'opérations mutuellement convenues impliquant la transformation séquentielle d'un produit semi-fini en un produit (pièce, pièce...) par façonnage à l'aide de moyens mécaniques, physiques. méthodes mécaniques, électrophysiques-chimiques et autres.
Structure du processus
L'élément principal du processus technologique est le fonctionnement .
Opération- il s'agit d'une partie du processus technologique effectué sur un lieu de travail par un ou plusieurs ouvriers, une ou plusieurs pièces d'équipement avant de passer au traitement de l'ébauche de la pièce suivante.
Pour qu’une opération existe, au moins une des deux conditions spécifiées est suffisante. Si, par exemple, le processus consiste à meuler une pièce sur une rectifieuse et à allier par étincelle électrique cette surface sur une autre, alors quel que soit le nombre de pièces (au moins une pièce), il y aura deux opérations dans le processus technologique, depuis que le lieu de travail évolue (Fig. 2.1).
|
Riz. 2.1. Opérations de processus (fragment)
Toutefois, la transformation sur un lieu de travail peut également comprendre plusieurs opérations. Si, par exemple, le perçage et l'alésage des pièces sont effectués sur une seule perceuse, de telle sorte que tout le lot de pièces soit d'abord percé, puis, selon les circonstances, l'équipement soit réajusté (remplacement des outils, des agencements, modes de traitement, environnement refroidi par lubrifiant, instruments de mesure, etc.), effectuez le déploiement, puis vous obtenez deux opérations - "perçage", la deuxième "déploiement", bien qu'il n'y ait qu'un seul poste de travail.
Un lieu de travail est une partie de la surface (volume) d'un atelier destinée à effectuer une opération par un ou un groupe de travailleurs, dans laquelle équipement technologique, outils, appareils, etc.
Le concept d’« opération » ne fait pas uniquement référence au processus technologique (TP), qui implique le façonnage. Il y a le contrôle, les tests, le lavage, le renforcement, le thermique, etc. opérations.
L'opération se caractérise par :
L'immuabilité de l'objet du traitement ;
Invariance des équipements (lieu de travail);
Cohérence des artistes travaillant ;
Continuité d'exécution.
La conception des procédés technologiques consiste à établir :
Composition (nomenclature) des opérations ;
Séquences d'opérations en TP ;
Une opération est une partie indissociable du processus technique du point de vue de la planification et de l'organisation. C'est l'unité de base de la planification de la production. L'ensemble du processus de production repose sur un ensemble d'opérations :
Intensité du travail ;
Logistique (machines, outils, etc.) ;
Qualification et nombre de travailleurs ;
Espace de production requis ;
La quantité d'électricité, etc. est déterminée par l'exploitation.
L'opération est soigneusement documentée.
L'opération peut comprendre plusieurs transitions. Une transition est une partie d'une opération au cours de laquelle la même surface d'une pièce est usinée, à l'aide du même outil, avec le même mode de fonctionnement de la machine.
![]()
|
![]() |
Riz. 2.2. Transitions technologiques
UN– deux transitions simples (Ι et ΙΙ) ; b– un complexe (explications dans le texte)
En figue. La figure 2.2 montre le fonctionnement des trous de couture à l'aide de la méthode électrochimique. Comme on peut le voir sur la Fig. 2.2, UN les trous sont obtenus séquentiellement lors de la mise en œuvre des transitions Ι et ΙΙ. Pour améliorer les performances, plusieurs transitions simples sont souvent combinées en une seule transition complexe (Fig. 2.2, b); cela vous permet de traiter plusieurs surfaces en même temps.
Une transition technologique peut contenir plusieurs passages. La passe est la partie de la transition au cours de laquelle une couche de métal est retirée (appliquée). La division en passes est nécessaire dans les cas où il n'est pas possible de retirer (appliquer) toute la couche métallique en une seule étape (en raison de la solidité de l'outil, de la rigidité de la machine, des exigences de précision, etc.).
L'opération peut être effectuée dans une ou plusieurs configurations de pièce. Installation représente une partie d'une opération technologique effectuée lors de la fixation d'une pièce.
Dans de nombreux cas, les opérations sont divisées en postes. Position- une position fixe occupée par une pièce fixe en permanence avec un dispositif, par rapport à un outil ou un équipement fixe pour effectuer une certaine partie de l'opération. Ainsi, une position est chacune des différentes positions de la pièce par rapport à l'outil ou de l'outil par rapport à la pièce lorsqu'il est maintenu dans une position, comme par exemple le fraisage de chacune des quatre faces d'une tête de vis lorsqu'elle est maintenue dans une position. luminaire unique.
La différence entre position et réglage est que dans chaque nouveau réglage, la nouvelle position relative de la pièce et de l'outil est obtenue en fixant à nouveau la pièce, et à chaque nouvelle position - sans desserrer la pièce, en déplaçant ou en tournant la pièce ou l'outil. à un nouveau poste. Le remplacement des réglages par des positions réduit toujours le temps de traitement, car tourner un dispositif avec une pièce ou une tête avec un outil prend moins de temps que de détacher, réinstaller et sécuriser la pièce.
J1. Introduction
Technologie est l'ensemble des connaissances sur les méthodes et les moyens de production des produits.
Technologie du génie mécanique étudie les méthodes et moyens de traitement mécanique et d'assemblage des produits.
Selon le programme de la spécialité 151001 - Technologie du génie mécanique, la matière « Technologie du génie mécanique » comprend trois cours distincts.
1. Fondamentaux de la technologie du génie mécanique. Ce cours est fondamental pour les autres disciplines technologiques. Il présente des informations théoriques : termes, définitions et concepts de base nécessaires à la conception de procédés technologiques d'usinage de pièces de machines et à l'élaboration de la documentation technologique.
2. Technologie du génie mécanique, partie 1. Technologie de production de machines . Ce cours étudie la technologie de production de pièces de machines typiques : arbres, pièces de boîtier, engrenages, etc. etc., ainsi que la technologie d'assemblage de produits
3. Technologie du génie mécanique, partie 2. Technologie de production automatisée. Ce cours étudie les caractéristiques de la technologie de fabrication de produits sur des machines à commande numérique, des machines automatiques et semi-automatiques.
De plus, le programme contient des disciplines étroitement liées à la technologie du génie mécanique. Parmi eux : les méthodes physiques et chimiques de traitement des matériaux, la science des matériaux, la technologie des matériaux de structure, la production et le traitement mécanique des pièces, la conception de la production mécanique, les équipements technologiques, la découpe des métaux, les outils de coupe, les machines à couper les métaux et plusieurs autres. .
À la suite de l'étude de ces cours, l'étudiant doit acquérir des connaissances et des compétences suffisantes pour développer une technologie permettant de produire des produits de la qualité requise, dans une quantité donnée, dans les délais prévus et au moindre coût.
Les diplômés du Département de technologie du génie mécanique de l'USTU-UPI reçoivent le diplôme « d'ingénieur » dans la spécialité 151001 - « Technologie du génie mécanique ». La durée de la formation est de cinq ans. Le programme est axé sur la spécialisation « Technologie du génie mécanique. Conception assistée par ordinateur." Les disciplines de spécialisation sont : la modélisation mathématique des procédés en génie mécanique, l'analyse dimensionnelle et la justification de solutions technologiques, l'infographie en conception assistée par ordinateur, la CAO industrielle, etc.
Types de produits
Produit - Il s'agit d'un objet ou d'un ensemble d'objets obtenus à la suite d'actions de travail délibérées.
Selon GOST 2.101-68, les types de produits suivants sont établis.
Détails - des produits fabriqués dans un matériau homogène de nom et de marque sans recourir à des opérations d'assemblage : vissage, soudage, rivetage, etc. etc. Par exemple : arbre, roue dentée, carter d'engrenage, etc. etc.
Unités d'assemblage - les produits dont les composants font l'objet d'une interconnexion au niveau de l'usine de fabrication par le biais d'opérations d'assemblage. Par exemple : boîte de vitesses, machine-outil, voiture, etc. etc.
Complexes - deux ou plusieurs produits spécifiés qui ne sont pas reliés à l'usine de fabrication par des opérations d'assemblage, mais sont destinés à remplir des fonctions opérationnelles interdépendantes. Par exemple, un convoyeur à bande composé d'un moteur électrique, d'une boîte de vitesses, de tambours d'entraînement et entraînés et d'une bande transporteuse. La combinaison de ces produits lors de l'assemblage crée un seul système fonctionnel pour effectuer des opérations de transport.
Trousses - deux ou plusieurs produits non reliés à l'usine de fabrication par des opérations d'assemblage et représentant un ensemble de produits ayant une finalité opérationnelle générale à caractère auxiliaire. Citons par exemple les ensembles d'outils et d'accessoires de rechange (SPTA), les ensembles d'outils de plomberie, etc. etc.
Le produit le plus complexe est une machine.
En voiture est un appareil qui effectue des mouvements mécaniques pour transformer les matériaux, l'énergie et les informations afin de faciliter le travail physique et mental humain.
Procédure de création d'un nouveau produit
Nouveau produit a amélioré les propriétés techniques et de consommation. Le processus de création d'un nouveau produit comprend : l'émission de spécifications techniques, la réalisation de travaux de recherche et développement (R&D), la conception de produits et les activités de production.
Tâche technique Le client développe un nouveau produit. Il fournit des informations sur la destination du produit, ses conditions de fonctionnement, les paramètres techniques et autres nécessaires à la conception.
recherche réalisée dans le cas où le niveau scientifique et technologique existant ne permet pas de résoudre les problèmes posés dans les spécifications techniques. La recherche comprend la définition d'objectifs de recherche, la réalisation d'études théoriques et expérimentales, le traitement des résultats obtenus, l'émission de recommandations et la rédaction d'un rapport. À la suite de la recherche, de nouveaux résultats scientifiques sont obtenus, qui sont utilisés pour créer un nouveau produit présentant des indicateurs techniques et économiques plus élevés.
TOC réalisées pour affiner le design du produit. La R&D comprend la conception, la fabrication et les tests de produits prototypes en laboratoire ou dans des conditions de production. En conséquence, ils vérifient solutions techniques, sur la base duquel ce produit est développé. La nécessité de travaux de recherche et développement est déterminée dans les termes de référence.
La conception des produits selon GOST 2.103 - 68, comprend le développement cohérent d'une proposition technique, d'une conception préliminaire, d'une conception technique et d'une documentation de conception de travail.
Dans la proposition technique (GOST 2.118 - 73) une ou plusieurs options pour mettre en œuvre les exigences des spécifications techniques sont à l'étude.
Conception preliminaire (GOST 2.119 - 73) contient des solutions qui donnent idée générale sur la conception et le principe de fonctionnement du produit, en indiquant ses principaux paramètres, par exemple les dimensions.
Projet technique (GOST 2.120 - 73) comprend des dessins de vues générales avec une conception détaillée du produit, suffisants pour créer un kit documentation de travail
Documentation de conception fonctionnelle est développé sur la base de l’ESKD. Il comprend un ensemble de dessins d'unités d'assemblage, de pièces et autres documents nécessaires à la fabrication, à l'assemblage, à l'emballage, au stockage et au transport du produit.
Processus de fabrication
Activités de production dans une entreprise, cela s'appelle un processus de production.
Processus de fabrication selon GOST 14.004 - 83 - il s'agit de l'ensemble de toutes les actions des personnes et des outils nécessaires dans une entreprise donnée pour la fabrication et la réparation de produits.
Le processus de production en génie mécanique comprend : l'organisation et la gestion de la production, la réception et le stockage des matières premières et des produits semi-finis, la préparation technologique de la production, la fabrication et l'assemblage des produits, le contrôle qualité des produits, l'étiquetage, le conditionnement et le stockage des produits finis, transport des produits à toutes les étapes de leur production, approvisionnement et entretien des lieux de travail, chantiers et ateliers, mise à disposition de personnel, c'est-à-dire travailleurs, employés, ingénieurs et travailleurs techniques (E&T) et bien plus encore.
Le processus de production est effectué à entreprise de construction de machines ou usine. Les usines de construction de machines utilisent une grande variété de méthodes de production et de transformation des produits : fonderie, forgeage, estampage, soudage, découpe, traitement thermique, assemblage, etc. Cependant, les méthodes de traitement mécanique des pièces par découpe avec enlèvement de copeaux et assemblage de produits sont les principales. Environ 60 % du temps total est consacré au traitement utilisant ces méthodes. Par conséquent, la production dans les usines de construction de machines est également appelée assemblage mécanique.
La principale unité de production de l'usine est boutique. L'usine de construction de machines comprend une grande variété d'ateliers, répartis dans les groupes suivants :
1. Ateliers d'approvisionnement : fonderie, forge, soudure. Les fonderies produisent des pièces moulées à partir de métaux ferreux et non ferreux. Les forges produisent le forgeage et l'emboutissage de pièces.
2. Ateliers principaux ou de transformation : mécanique, assemblage, thermique, etc.
3. Ateliers auxiliaires : ateliers d'outillage, ateliers de réparation, ateliers de modélisme, etc.
Structure entreprise de construction de machines est étudié en détail dans la conception du cours de production en génie mécanique.
Les ateliers d'usine sont divisés en sites de production. Le site est constitué de lieux de travail.
Lieu de travail selon GOST 14.004 - 83 est élémentaire unité structurelle les entreprises où les exécutants des travaux, les équipements technologiques entretenus, une partie du convoyeur, les équipements et les éléments de main-d'œuvre se trouvent pour une durée limitée. En d'autres termes, un lieu de travail fait partie d'une zone de production équipée en fonction des travaux qui y sont effectués.
Processus technologique et sa structure
Processus technologique est appelé une partie du processus de production contenant des actions ciblées pour changer ou déterminer l'état du sujet du travail.
Grâce à ces actions, les dimensions, la forme, la rugosité et l'état de surface, l'apparence et les propriétés internes des produits sont constamment modifiés et contrôlés. Selon le type d'action, on distingue les procédés technologiques d'usinage, d'assemblage, de coulée, de traitement sous pression, de traitement thermique, de revêtement, etc. etc. Le processus technologique consiste en des opérations technologiques.
Fonctionnement technologique selon GOST 3.1109 - 82, une partie complète du processus technologique est appelée, effectuée sur un seul lieu de travail.
L'opération est réalisée par un ou plusieurs intervenants sur un produit sans passer à la transformation d'un autre produit. L'opération peut inclure l'installation et le retrait répétés de la pièce, le changement d'outils, le type de traitement, les montages, les dispositifs de contrôle et de mesure, etc. etc. Lors de l'exécution d'une opération technologique, la pièce peut être traitée complètement ou seulement partiellement, même avec un seul type de traitement. Le contenu de l'opération détermine l'intensité de main-d'œuvre de sa mise en œuvre et le montant du salaire des travailleurs.
Dans la documentation du processus technologique, le nom de l'opération d'usinage est écrit sous forme d'adjectif en cas nominatif en fonction du type d'équipement sur lequel cette opération est réalisée. Par exemple : tournage, fraisage, perçage, etc. etc. Les opérations sont numérotées par des numéros dans la série progression arithmétique multiples de 5. Par exemple : 5, 10, 15, etc. etc. (GOST 3.1129-93, clause 5.3). Ceci est nécessaire pour réserver des postes en cas de changements dans le processus technologique.
La séquence des opérations technologiques de transformation ou d'assemblage des produits, enregistrées dans l'ordre de leur exécution, est appelée voie technologique. Selon GOST 3.1109-82, l'opération technologique comprend les éléments suivants :
Installation - Cela fait partie d'une opération technologique réalisée avec une fixation constante des pièces en cours de traitement ou de l'unité d'assemblage en cours d'assemblage. Si l'opération est effectuée entièrement avec la pièce fixée inchangée, on dit alors qu'elle est effectuée en une seule configuration.
Transition technologique - il s'agit d'une partie achevée d'une opération technologique, qui est réalisée par les mêmes moyens d'équipement technologique dans des conditions technologiques constantes et dans la position de la pièce. Lors de l'usinage au sein d'une transition technologique, les éléments suivants restent inchangés : l'outil, le montage, la position de. la pièce à usiner et les modes de traitement technologique, c'est-à-dire avance, vitesse de coupe ou vitesse de broche. Le nom de la transition technologique s'écrit avec un verbe à la forme indéfinie, qui correspond au mode de traitement mécanique. Par exemple : affûtage, perçage, fraisage, etc. etc.
Transition auxiliaire - il s'agit d'une partie achevée d'une opération technologique, constituée d'actions humaines et (ou) matérielles qui ne s'accompagnent pas d'une modification des propriétés de l'objet de travail, mais sont nécessaires pour achever la transition technologique. Des exemples de transitions auxiliaires sont l'installation et le retrait d'une pièce sur une machine, le changement d'outils, le prélèvement de puces de test lors du réglage de la machine, etc. Le nom de la transition auxiliaire s'écrit avec un verbe à la forme indéfinie qui correspond à l'action réalisée. Par exemple, installer, supprimer, sécuriser, etc. Dans la documentation technologique, les transitions technologiques et auxiliaires sont numérotées 1, 2, 3,...
Les éléments structurels de la transition technologique sont ouvrier bouger et auxiliaire se déplacer.
Course de travail - il s'agit d'une partie achevée d'une transition technologique, constituée d'un mouvement unique de l'outil par rapport à la pièce, qui s'accompagne de modifications de la forme, de la taille, de l'état de surface ou des propriétés de la pièce.
Mouvement auxiliaire - il s'agit d'une partie achevée de la transition technologique, constituée d'un mouvement unique de l'outil par rapport à la pièce, nécessaire à la préparation de la course de travail. Un exemple de mouvement auxiliaire consiste à amener l'outil sur la pièce, à le déplacer vers position initiale après avoir effectué une course de travail, etc.
L'élément structurel de la transition est la réception.
Réception – Il s’agit d’un ensemble complet d’actions humaines nécessaires pour achever la transition ou une partie de celle-ci et unies par un seul objectif. Par exemple, la transition auxiliaire « installer et retirer une pièce » comprend les techniques suivantes : prendre une pièce, l'installer dans un montage, la fixer, détacher la pièce après traitement, retirer la pièce de la machine. La transition auxiliaire pour le remplacement d'un outil comprend les techniques suivantes : prendre l'outil, l'installer dans la broche de la machine, le retirer de la broche.
Lors du traitement de pièces sur des machines où l'outil ou la pièce est fixé dans des dispositifs rotatifs, élément structurel l’opération technologique est un poste.
Position - il s'agit d'une position fixe occupée par une pièce fixe ou une unité d'assemblage assemblée par rapport à un outil ou un équipement fixe lors de l'exécution d'une certaine partie de l'opération. En d'autres termes, la position est une position fixe de la pièce et de l'outil l'un par rapport à l'autre sur les machines avec appareils rotatifs, par exemple, sur les tours à tourelle. La position est modifiée en faisant tourner la pièce ou l'outil l'un par rapport à l'autre. Dans la documentation technologique, les positions sont désignées par les chiffres romains I, II, III, etc.
Dans la documentation technologique, les règles d'enregistrement du contenu des opérations et des transitions lors du traitement de découpe sont définies par GOST 3.1702-79, selon lesquelles l'enregistrement du contenu de l'opération est effectué sous la forme itinéraire ou opérationnel descriptions. Dans la description opérationnelle, le contenu des transitions auxiliaires est mis en évidence séparément dans le dossier d'opération. Il est permis de ne pas enregistrer de transitions auxiliaires s'il existe des illustrations graphiques.
Selon GOST 3.1702-79, le contenu de l'opération dans la description de l'itinéraire doit inclure :
1. Un mot clé caractérisant la méthode de traitement, exprimé sous forme de verbe sous une forme indéfinie, par exemple : affûter, percer, fraiser, etc. etc. (Annexe 3)
2. Informations Complémentaires sous la forme d'une indication du nombre de surfaces traitées séquentiellement ou simultanément, par exemple 4 trous (Annexe 4, partie 1)
3. Informations complémentaires caractérisant la surface à traiter, par exemple pour un trou : borgne, traversant ou pour une rainure - anneau (Annexe 4, partie 2).
4. Nom de la surface traitée, des éléments structurels ou des éléments de production, par exemple : surface, épaulement, congé, pièce (Annexe 5).
5. Informations sur les tailles ou leurs symboles, par exemple : tailles j 1 =…, d 2 =…, l 1 =…, l 2 =… ou tailles 1, 2, 3, 4, numérotés au dessin (Annexe 6).
6. Informations complémentaires sur la nature du traitement, par exemple : préliminaire, final, simultané, séquentiel, par copieur, selon le dessin, etc. etc. (Annexe 4, partie 4).
L'enregistrement dans l'ordre spécifié est dit complet et est utilisé en l'absence d'illustrations graphiques de l'opération. S'il existe des illustrations graphiques, une notation abrégée est utilisée. Dans ce cas, le contenu de l'opération comprend des paragraphes. 1; 4 ; 5.
Dans une description opérationnelle, l'enregistrement de contenu de transition comprend :
1. Un mot-clé exprimé par un verbe à la forme indéfinie qui correspond à une méthode d'usinage, par exemple : affûter, percer, fraiser. Pour une transition auxiliaire, le mot-clé s'écrit sous forme de verbe sous une forme indéfinie qui correspond à l'action effectuée, par exemple installer, supprimer, sécuriser (Annexe 3).
2. Nom des éléments de production, surfaces usinées, éléments de structure, par exemple collerette, congé, filetage (Annexe 5).
3. Symbole des dimensions et des éléments structurels (Annexe 6).
Regardons la structure de l'opération et son enregistrement à l'aide des exemples suivants.
Exemple 1. Supposons qu'il soit nécessaire d'obtenir un trou dans une pièce solide (sans trou) selon le dessin de la Fig. 5.1, mais fidèle à la taille d =20N8. Des trous de cette taille et de cette précision peuvent être obtenus par traitement séquentiel : perçage, fraisage et alésage sur une perceuse verticale.

La technologie suivante est utilisée lors du traitement : la pièce est installée dans un mandrin à trois mors autocentrant, qui assure le serrage de la pièce et l'alignement de son axe avec l'axe de la broche. Un foret d'un diamètre de 18 mm est installé dans la broche, avec lequel un trou est percé dans un matériau solide. Remplacez ensuite le foret par une fraise et fraisez le trou à une taille de 19,8 mm. Remplacez ensuite la fraise par un alésoir, changez la vitesse de la broche et alésez le trou à la taille souhaitée. d = 20Н8. Ensuite, la pièce est détachée et retirée de la machine. Un schéma de l'opération est présenté sur la Fig. 5.1, b.
Avec une description d'itinéraire, un enregistrement complet du contenu de l'opération ressemblera à ceci :
005. Forage.
d =18 ; ré= 19,8 ; d = 20Н8, séquentiellement,d'après le dessin.
En notation abrégée on aura
005. Forage.
Percer, fraiser et aléser un trou d = 20Н8.
Avec une description opérationnelle, un enregistrement complet du contenu de l'opération ressemblera à ceci :
005 Forage.
1. Installez et supprimez.
d =18.
d=19,8.
d =20Н8
L'opération considérée contient trois transitions technologiques et un certain nombre de transitions auxiliaires. Dans la description opérationnelle, les transitions auxiliaires pour l'installation et le retrait d'une pièce sont généralement combinées en une seule : « Installer et retirer ». Les transitions auxiliaires pour le remplacement des outils sont combinées avec les transitions technologiques et ne sont pas spécifiées séparément. Les techniques incluses dans ces transitions sont répertoriées ci-dessus. Toutes les transitions sont effectuées séquentiellement. Chaque transition technologique consiste en une course de travail associée au traitement d'un trou, tel que le perçage, et des courses auxiliaires associées à l'amenée de l'outil sur la pièce et à son déplacement vers sa position d'origine. De plus, les transitions technologiques incluent des techniques d'activation (désactivation) de la vitesse de rotation de la broche et de l'avance des outils.
Vous pouvez créer une opération avec une structure différente, dans laquelle toutes les transitions seront effectuées en parallèle. Pour ce faire, la perceuse verticale est équipée d'un dispositif à tourelle en forme de table rotative avec quatre mandrins auto-centrants à trois mors et une tête de perçage à trois broches : la première broche pour la perceuse, la seconde pour la fraise. et le troisième pour l'alésage. La vue générale de la tête de perçage multibroches est représentée sur (Fig. 5.2). Les broches ont des vitesses de rotation différentes, mais la même avance verticale. Le traitement des pièces est effectué en un seul temps de travail. broche. Le schéma de cette opération est présenté sur la Fig. 5.1, ch. Selon le schéma, trois parties sont traitées simultanément dans cette opération. Le traitement s'effectue comme suit. Dans la première position, la pièce est installée et la pièce finie est retirée. Les deuxième, troisième et quatrième positions sont utilisées pour le perçage, le fraisage et l'alésage. La pièce est déplacée d'une position à l'autre à l'aide d'une table rotative. Les positions sont indiquées par des chiffres romains. L’opération a donc une structure parallèle, car toutes les transitions technologiques se confondent. Un enregistrement complet du contenu de l'opération dans la description de l'itinéraire est le suivant :
005 Forage.
Percer, fraiser et aléser un trou traversant en respectant les dimensions d =18 ; ré= 19,8 ; d = 20Н8, simultanément.
Avec une description opérationnelle, le dossier complet de l'opération ressemblera à ceci :
005 Forage.
1. Installer et supprimer
Simultanément:
2. Percez un trou en conservant la taille d =18.
3. Fraisez le trou en conservant la taille d=19,8.
4. Agrandissez le trou en conservant la taille d =20Н8.
Exemple 2. Qu'il soit nécessaire de traiter un rouleau selon le dessin (Fig. 5.4a). Un dessin de la pièce à usiner est présenté sur la Fig. 5.4, b. L'opération est réalisée dans deux installations.
Des croquis d'installations sont présentés à la Fig. 5.4, c ; G.
Le traitement est effectué sur tour avec installation de l'arbre au centre avec un mandrin d'entraînement (Fig. 5.3). Le centre avant est installé dans la broche de la machine. Le centre arrière est monté dans le fourreau de la poupée mobile. Avec une description d'itinéraire, un enregistrement complet du contenu de l'opération ressemblera à ceci :
005. Tournant.
Affûtez les surfaces en conservant les dimensions 1 à 5 séquentiellement, selon le dessin.
Dans la description opérationnelle, nous aurons l'entrée suivante :
005. Tournant.
Installer et supprimer.
1. Affûter les surfaces en respectant les dimensions 3.4.
Réinstaller
2. Affûtez les surfaces en conservant les dimensions 1,2,5.
Un processus technologique est une partie du processus de production qui contient un changement constant de taille, de forme, apparence objet de la production et de leur contrôle.
Éléments de processus: opération, installation, position, traitement, transition, passage, technique de travail, mouvement.
Un processus technologique est généralement divisé en parties appelées opérations.
Opération représente une partie achevée du processus technologique. O. est conçu pour changer la géométrie et paramètres physiques produits pour 1 poste de travail avec 1 travailleur.
Opération effectué en continu sur un lieu de travail.
Une opération est l’unité de base de la planification de la production et de la comptabilité. Au début des opérations, l'intensité de main-d'œuvre pour la fabrication des pièces est déterminée, les normes de temps et les prix sont fixés, le nombre requis d'équipements, d'accessoires et d'outils est fixé et le traitement est déterminé.
Composition O. : SIDA : machine, appareil, outil, pièce.
Installation- il s'agit de la détermination de la position de la pièce sur la machine à l'aide de machines-outils.
Afin de pouvoir représenter la structure de l'opération et prendre en compte le temps consacré à son exécution, il a fallu diviser l'opération en parties distinctes, appelées transitions.
Position– il s'agit d'une position fixe occupée par la pièce fixe avec le dispositif de fixation par rapport à l'outil. (tours tournants avec axe de rotation horizontal et vertical de la tête.)
Traitement. Les objectifs du traitement de la fourrure sont de modifier les propriétés, les caractéristiques géométriques et les dimensions de la pièce.
Transition technologique– il s’agit de l’usinage mécanique d’une ou plusieurs pièces, avec un ou plusieurs outils, dans des conditions technologiques et d’installation constantes.
Conformément à cela, la transition directement liée à la mise en œuvre de l'impact technologique est appelée la principale (forage). Une transition constituée des actions d'un ouvrier ou de mécanismes nécessaires pour réaliser la transition principale est dite auxiliaire (installation et fixation d'une pièce).
Passage – traitement de surfaces individuelles avec la même installation de la pièce à usiner.
Course de travail appelé mouvement relatif unique de l'outil et de la pièce, à la suite duquel une couche de matériau est retirée de sa surface. Pour pouvoir usiner une pièce, celle-ci doit être installée et fixée dans un support sur la table de la machine. Chaque nouvelle position fixe d'un objet de production, ainsi que le dispositif dans lequel l'objet est installé et sécurisé, est appelé un poste de travail. position.
Mouvement - Ce actions individuelles machine (allumer, éteindre).
Une technique de travail est un ensemble complet d'actions humaines lors de l'exécution d'une certaine partie d'une opération, utilisée lors de l'exécution d'une transition ou d'une partie de celle-ci. Par exemple : allumez la machine, changez d'alimentation, etc.
La réception fait partie de la transition auxiliaire.
Types de production
Il existe trois types de production : I/masse, 2/série, 3/unique.
Unique : La production unique est appelée production caractérisée par un petit volume de production de produits identiques, une production répétée de produits qui, en règle générale, ne sont pas prévues. Il n’existe pas de production cyclique caractéristique de la production de masse.
Le manque de répétabilité de la fabrication conduit à la recherche des moyens les plus simplifiés pour fabriquer des produits. Le plus souvent, les ateliers d'expérimentation, de réparation, etc. fonctionnent de cette façon. Les travailleurs ici sont comme
généralement hautement qualifiés. Les équipements et accessoires sont universels. Le coût de production est élevé.
1. étendue de la gamme de produits manufacturés 2. petit volume de leur production, des dizaines de pièces par an. 3. couverture universelle de différents types de produits. 4. flexibilité en termes d'utilisation d'équipements universels (par exemple, un tour à décolleter, un outil standard de coupe ou de mesure)5. Le processus technologique de fabrication d'une pièce a un caractère compacté, c'est-à-dire plusieurs opérations ou transformations complètes du produit fabriqué sont effectuées sur une seule machine 6. C/c est relativement élevé 7. qualifications des travailleurs – 5 – 6 catégories, élevées. Machine 8 – équipement universel de précision. 9. Le coefficient a consolidé les opérations de plus de 40. 10. Un système de documentation simplifié est utilisé. 11. Il n'existe pas de normes techniques ; une normalisation expérimentale et statistique du travail est utilisée. 12. billettes : laminage à chaud, coulée en terre, pièces forgées
Série : (à petite, moyenne, grande échelle - dépend du lot V)
à petite échelle : 1. qualification esclave 5-6 catégorie, 2. satnka - semi-automatique 3. coefficient d'opération de fixation 20 - 40
moyen : 1. qualification esclave 4ème catégorie, 2. satnki - machines semi-automatiques 3. coefficient d'opération de vissage 10-20
production à grande échelle : 1. qualification esclave 3ème catégorie, 2. automatique. Satnki, modules de production 3. coefficient de fixation de l'opération de 1 à 10
1. une gamme limitée de produits est fabriquée en lots répétitifs périodiquement 2. le volume de production est supérieur à celui d'une seule production, périodiquement en lots répétitifs 3. ébauches - laminées à chaud et à froid, moulage par injection, moulage, estampage 4. Le processus technologique est principalement différencié, c'est-à-dire divisé en départements opérations effectuées sur la zone définie machines 5. lors du choix des équipements technologiques (utilisant des dispositifs auxiliaires et spéciaux), il est nécessaire de calculer les coûts et les délais de récupération, ainsi que les équipements liquéfiés. Effet. 6. c/c inférieur à celui d'une seule production
En gros:
Massive - production caractérisée par un grand volume de produits produits en continu
fabriqués ou réparés sur une longue période de temps, au cours de laquelle une seule opération de travail est effectuée sur la plupart des lieux de travail. En production de masse pour chaque opération
l'équipement le plus productif et le plus coûteux /automatique, semi-automatique/ est sélectionné, le lieu de travail est équipé d'appareils et d'appareils complexes et performants, en
En conséquence, avec un grand volume de production de produits, le coût de production le plus bas est obtenu.
1. coefficient fixe =1. 2. qualification 3-4 (1 opération répétitive est effectuée sur chaque lieu de travail) 3. automatique. satnki, modules de production. 4 production en ligne 5. la précision requise est obtenue grâce à des méthodes d'obtention automatique des dimensions sur des machines personnalisées.
1.gamme étroite de produits. 2. grand volume de production de produits, produit en continu au cours de la période actuelle. longue période de temps 3. Le processus technologique est développé en détail, qui se caractérise par une faible intensité de travail et une faible production par rapport à la production en série de produits s/c. 4. l'utilisation de la mécanisation et de l'automatisation des processus industriels. 5. utilisation de la technologie. processus avec des opérations élémentaires. 6. utilisation de promotions à grande vitesse. appareils, ainsi que des instruments de coupe et de mesure. 7. Utilisez le modèle
Qualité de surface
La qualité d'une surface est l'ensemble de toutes ses propriétés de service et, en premier lieu, sa résistance à l'usure, résistance à la corrosion, la résistance à la fatigue, ainsi que certaines autres propriétés. La qualité de la surface est évaluée par deux paramètres :
Caractéristiques géométriques
Caractéristiques géométriques- ce sont les paramètres de l'écart de la surface par rapport à l'idéal spécifié. La surface peut être non plane, ovale, découpée, etc. La surface peut être représentée sous une forme agrandie sous la forme d’une ligne ondulée.
Géométrie. Les caractéristiques de qualité de la surface traitée sont déterminées par l'écart de la surface réelle par rapport à la surface nominale. Ces écarts peuvent être divisés en 3 types : rugosité, ondulation et écart par rapport aux droits. géom. formes..
La rugosité est un ensemble d'irrégularités, de surfaces traitées avec des pas relativement petits. La rugosité de la surface est déterminée par son profil, qui se forme dans la section transversale de cette surface
La rugosité et l'ondulation sont des caractéristiques de la qualité de surface qui ont une grande influence sur de nombreuses propriétés de performance des pièces de machines.
Les microrugosités considérées se forment lors du processus d'usinage par copie de la forme des outils de coupe, déformation plastique de la couche superficielle des pièces sous l'influence de l'outil d'usinage, son frottement contre la pièce, ses vibrations, etc.
La rugosité de surface des pièces a un impact significatif sur la résistance à l'usure, la résistance à la fatigue, l'étanchéité et d'autres propriétés de performance.
L'ondulation occupe une position intermédiaire entre les écarts de forme et la rugosité de la surface. L'apparition d'ondulations est associée à des processus dynamiques provoqués par la perte de stabilité du système machine-dispositif-outil-pièce et exprimés par l'apparition de vibrations.
L'ondulation de la surface est un ensemble d'irrégularités qui se répètent périodiquement dans lesquelles les distances entre les collines ou les dépressions adjacentes dépassent la longueur de base de la rugosité de la surface existante.
L'écart de forme est l'écart de la forme d'une surface réelle ou d'un profil réel par rapport à la forme d'une surface nominale ou d'un profil nominal.
La précision est le degré auquel les valeurs réelles des paramètres géométriques correspondent à leurs valeurs spécifiées (calculées).
Les propriétés physiques et mécaniques comprennent dureté et tension.
Des contraintes résiduelles se produisent après l'usinage, les opérations de découpage et pendant le meulage (le matériau de la couche superficielle subit un durcissement, un ramollissement, sa structure et sa microdureté changent et des contraintes résiduelles se forment). Après les opérations d'approvisionnement, les ébauches obtenues sur presse sont soumises à un traitement thermique. traitement.
Types de traitement thermique et contraintes résiduelles :
Normalisation– chauffer la pièce puis la refroidir à l'air. Dans ce cas, la contrainte résiduelle est supprimée et une dureté supérieure à celle lors de la cuisson se forme. Brûlant– caractérisé par le fait que la pièce est soulagée des contraintes résiduelles suite au chauffage du four, suivi d'un refroidissement à l'intérieur de celui-ci au rythme du refroidissement du four. Durcissement peut se produire dans solutions salines, dans l'eau, dans l'huile. La contrainte résiduelle est déterminée par des méthodes de calcul et expérimentales.
En expérimentant. méthodes résiduelles les contraintes sont déterminées par des calculs basés sur la déformation de l'échantillon après en avoir retiré la couche contrainte. Cette méthode est destructeur.
11. Usinage de précision. Erreur totale. Système de lutte contre le SIDA. Types d'erreurs.
Sous précision du traitement vous devez comprendre le degré de correspondance entre la valeur réelle de l'indicateur et la valeur nominale.
La précision des paramètres géométriques est un concept complexe qui comprend :
Précision dimensionnelle des éléments des pièces ;
Précision formes géométriques surfaces des éléments de pièces ;
Précision de la position relative des éléments des pièces ;
Rugosité des surfaces des pièces (microgéométrie) ;
Ondulation des surfaces (macrogéométrie).
L'augmentation de la précision des pièces initiales réduit l'intensité du travail et le traitement mécanique du traitement mécanique, réduit les valeurs des tolérances et conduit à des économies de métal.
La précision de la pièce dépend d'un certain nombre de facteurs :
Écart par rapport à la géom. forme de la pièce ou de son département. éléments.
Écart des dimensions réelles des pièces par rapport aux dimensions nominales
Déviation des surfaces et des axes des pièces par rapport à la position relative exacte (du parallélisme, de la perpendiculaire, de la concentricité)
Parce que La précision du traitement dans des conditions industrielles dépend de nombreux facteurs ; le traitement sur des machines est effectué non pas avec une précision réalisable, mais avec une précision économique.
Mécanique de précision Ec. traitement- une telle précision, avec un chat. le traitement min s/c est réalisé dans des conditions de fonctionnement normales (le travail est effectué sur des machines en état de marche en utilisant les dispositifs et outils nécessaires avec une consommation de temps normale et une utilisation normale des travailleurs) Précision réalisable– précision, cat. peut être obtenu par un traitement dans un max. conditions favorables requises pour cette production par des ouvriers hautement qualifiés avec une augmentation significative du temps passé, sans compter la transformation.
Aides : machine, appareil, outil, pièce.
L'erreur de mesure totale est une combinaison d'erreurs résultant d'un grand nombre de facteurs.
Erreurs : théoriques, erreurs causées par l'action d'aides à la force élastique, erreurs causées par la déformation de la pièce sous l'influence de forces déséquilibrées, dues à la chaleur, dues à l'usure de l'outil de coupe, erreur de positionnement