Grande encyclopédie du pétrole et du gaz. Observations de l'état de corrosion des canalisations
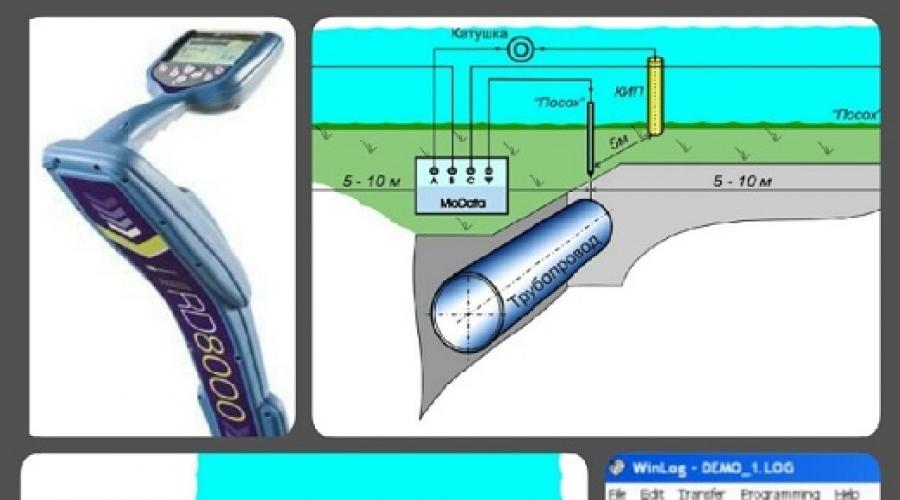
Lire aussi
Évaluation de l'état de corrosion d'un pipeline situé à champ électrique Les lignes électriques PT sont produites en fonction de la différence de potentiel entre le tuyau et le sol et de l'ampleur du courant dans le pipeline.
Lok-schéma d'une évaluation complète de l'état technique de l'unité MG. À l’avenir, l’évaluation de l’état de corrosion des MG LP devrait devenir partie intégranteévaluation complète de l'état technique du gazoduc principal.
Schéma d'émergence et de propagation des errants. Lors de l'évaluation de l'état de corrosion d'un gazoduc, il est important de connaître les valeurs moyennes et maximales de la différence de potentiel.
Les instruments d'évaluation des conditions de corrosion doivent comprendre des capteurs, un système d'enregistrement et des sources d'alimentation appropriées. Lors de l'utilisation de méthodes magnétiques et électromagnétiques, il est possible d'utiliser divers systèmes de magnétisation. Le problème du balayage est résolu soit par un petit nombre de capteurs se déplaçant à l'intérieur du tuyau le long d'une ligne hélicoïdale, soit par un grand nombre de capteurs avançant avec le système magnétisant et situés autour du périmètre de l'appareil. Dans ce cas, il est préférable d'utiliser un système de disposition de capteurs décalés à deux anneaux pour éliminer d'éventuelles omissions de défauts sur la canalisation. Les appareils de type Linenalog produits aux États-Unis sont constitués de trois sections reliées par des charnières. La première section contient des alimentations électriques et des colliers d'étanchéité, la seconde contient un électro-aimant avec un système de cassette pour les capteurs et la troisième contient des composants électroniques et un dispositif d'enregistrement. Ils sont utilisés pour l'inspection des pipelines.
Les forages pour évaluer l'état de corrosion de la canalisation doivent être réalisés avec une ouverture complète de la canalisation et la possibilité d'inspecter sa génératrice inférieure. La longueur de la partie ouverte du tuyau doit être d'au moins trois diamètres.
Un moyen efficace d'évaluer l'état de corrosion d'un équipement (aux étapes de sa conception, de son fonctionnement, de sa rénovation) est la surveillance de la corrosion - un système d'observation et de prévision de l'état de corrosion d'un objet afin d'obtenir des informations en temps opportun sur ses éventuelles défaillances de corrosion.
Dans le tableau 6 fournit une évaluation de l'état de corrosion réel des systèmes d'alimentation en eau chaude provenant de tuyaux noirs dans un certain nombre de villes. De plus, à titre de comparaison, des indices calculés de saturation de l'eau à 60 C, des données sur la teneur en oxygène dissous et en dioxyde de carbone libre dans l'eau et une évaluation de l'activité de corrosion sont donnés.
Répartition des zones de vitesse de déplacement du flux eau-gaz-pétrole pour les pipelines différents diamètres. Des inspections de corrosion des trains de cuvelage sont effectuées pour évaluer leur état de corrosion (à la fois en profondeur et sur la zone du champ), déterminer les paramètres de protection électrochimique, identifier les causes des fuites des trains de cuvelage en cours d'exploitation et surveiller la sécurité.
Sur la base de l'analyse des données ci-dessus sur l'évaluation de l'état de corrosion et de la fiabilité des équipements et des processus technologiques à l'ONGKM, les résultats de la détection des défauts en ligne et externes, des tests mécaniques de corrosion sur le terrain et en laboratoire, des études métallographiques de modèles et d'échantillons, le résultats des diagnostics techniques des structures, ainsi que compte tenu des documents réglementaires et techniques en vigueur (NTD), une méthodologie de diagnostic des équipements et des processus technologiques des gisements de pétrole et de gaz contenant du sulfure d'hydrogène a été développée.
Dans notre pays et à l'étranger, des méthodes et des instruments sont développés pour évaluer l'état de corrosion d'un pipeline sans l'ouvrir. Les méthodes les plus prometteuses reposent sur le passage d'un dispositif spécialement équipé à travers un pipeline, qui détecte les foyers de corrosion sur la paroi du tuyau de l'intérieur et de l'extérieur. La littérature fournit des données sur les méthodes de surveillance de l'état des pipelines. L'attention principale est portée aux méthodes magnétiques et électromagnétiques, la préférence étant donnée à ces dernières. Les méthodes échographiques et radiographiques sont également brièvement décrites ici.
Des modèles qui ne sont décrits par aucune équation mathématique et se présentent sous la forme d'un ensemble de coefficients tabulaires ou de nomogrammes recommandés pour évaluer l'état de corrosion des métaux.
Pour évaluer l'état du revêtement d'une canalisation en cours d'exploitation, il est conseillé d'utiliser la résistance de contact canalisation isolée, des paramètres caractérisant la perméabilité du matériau de revêtement, et la quantité d'antioxydant (pour les compositions stabilisées) restant dans le revêtement. Pour évaluer l'état de corrosion de la paroi du tuyau, il convient d'utiliser les données provenant des mesures des pertes par corrosion du métal sous le revêtement ou aux endroits de son défaut, ainsi que la taille et la position relative des lésions de corrosion sur la paroi du tuyau. La seconde comprend la corrosion locale (cavités, piqûres, taches), unique (avec une distance entre les bords les plus proches des lésions adjacentes de plus de 15 cm), de groupe (avec une distance entre les bords les plus proches des lésions adjacentes de 15 à 0,5 cm ) et étendues (avec une distance entre les bords les plus proches des lésions adjacentes inférieure à 0,5 cm). Des lésions de corrosion uniques n’entraînent pas de défaillances dans les pipelines.
Pour évaluer l'état revêtement isolant sur une canalisation en cours d'exploitation, il est nécessaire d'utiliser les valeurs de la résistance transitoire de la canalisation, les paramètres caractérisant la perméabilité du matériau de revêtement et la quantité d'antioxydant (pour les compositions stabilisées) restant dans l'isolant. Pour évaluer l'état de corrosion de la paroi du tuyau, il est nécessaire d'utiliser les données provenant des mesures des pertes par corrosion du métal sous le revêtement ou aux endroits de son défaut, ainsi que la taille et les positions relatives des lésions de corrosion sur la paroi du tuyau.
Lors de l'évaluation de l'état de corrosion d'un pipeline, les types de corrosion sont déterminés, le degré de dommage causé par la corrosion à la paroi extérieure des tuyaux avec une caractéristique généralisée des sections, le taux de corrosion maximal et moyen est évalué et l'état de corrosion de la section est prévue pour 3 à 5 ans.
Dans le tableau 9.12 fournit une évaluation de l'état de corrosion du pipeline avec un ensemble complet de facteurs d'influence et de recommandations correspondantes.
En pratique, pour quantifier la résistance à la corrosion des métaux, on peut utiliser toute propriété ou caractéristique d'un métal qui change de manière significative et naturelle au cours de la corrosion. Ainsi, dans les systèmes d'approvisionnement en eau, l'état de corrosion des canalisations peut être évalué par l'évolution de la résistance hydraulique du système ou de ses sections au fil du temps.
Pour trouver la possibilité de réduire les pertes de métal dues à la corrosion et de réduire les pertes directes et indirectes importantes dues à la corrosion, il est nécessaire d'évaluer l'état de corrosion des dispositifs et des communications des systèmes technologiques chimiques. Dans ce cas, il est nécessaire de procéder à la fois à une évaluation de l'état de corrosion du système chimico-technologique et à une prévision du développement possible de la corrosion et de l'impact de ce processus sur les performances des appareils et des communications des systèmes chimico-technologiques. .
La technique de mesure est donnée dans la section II. L'étendue et l'ensemble des mesures nécessaires à l'évaluation de l'état de corrosion d'un ouvrage sont prévus par des instructions départementales approuvées selon les modalités prescrites.
La complexité et l'originalité du processus de corrosion des métaux souterrains et structures en béton armé conditionné conditions spéciales environnement souterrain où interagissent l’atmosphère, la biosphère et l’hydrosphère. À cet égard, une attention particulière est accordée au développement et à la création d'équipements et de systèmes d'évaluation de l'état de corrosion des objets situés sous terre. Une telle évaluation peut être réalisée en mesurant le potentiel moyenné dans le temps de la structure métallique par rapport au sol. Pour déterminer la valeur potentielle moyenne, des dispositifs ont été développés - des intégrateurs de courants vagabonds. Ils sont faciles à fabriquer, ne nécessitent pas d’alimentation électrique spéciale et fonctionnent de manière fiable. L'utilisation de ces dispositifs renseigne sur la nature de la répartition spatiale des zones anodiques, cathodiques et alternées pour choisir l'emplacement de raccordement des moyens de protection électrochimiques et rendre compte intégralement de l'efficacité de son fonctionnement. Ces informations peuvent être utilisées aussi bien lors de la conception, de la construction et de l’installation de nouveaux équipements que pendant leur exploitation. Il devient possible de mettre en œuvre des mesures planifiées pour assurer une haute fiabilité des structures métalliques et en béton armé dans des conditions d'exploitation à long terme.
Une évaluation du risque de corrosion des canalisations souterraines en acier causée par l'influence du transport électrifié fonctionnant au courant alternatif doit être réalisée sur la base des résultats des mesures de la différence de potentiel entre la canalisation et environnement. La technique de mesure est donnée dans la section II. Le volume et l'ensemble des mesures nécessaires pour évaluer l'état de corrosion du pipeline sont déterminés par des instructions départementales approuvées de la manière prescrite.
Le régime est surveillé sur la base des résultats d'analyses d'échantillons d'eau et de vapeur, de lectures de pH-mètres d'eau d'alimentation et de chaudière, de déterminations périodiques de la composition quantitative et qualitative des dépôts, ainsi que de l'évaluation de l'état du métal de la chaudière en termes de corrosion. Le personnel d'exploitation surveille spécifiquement deux indicateurs principaux du régime : la dose de complexe (basée sur la diminution du niveau dans la jauge de mesure de la solution de travail 7, recalculée en fonction de la consommation d'eau alimentaire) et le pH de l'eau de chaudière du compartiment propre. Le découpage d'échantillons représentatifs de tuyaux de surface chauffante, l'analyse qualitative et quantitative des dépôts et l'évaluation de l'état de corrosion du métal par rapport à son état initial au cours des 1 à 2 premières années de fonctionnement du régime sont effectués tous les 5 à 7 000 heures d'ouverture.
Par conséquent, il existe des cas où, en raison d'une détermination inexacte de l'emplacement des défauts de corrosion à la surface et à l'intérieur du pipeline en raison de la réassurance, un remplacement injustifié du pipeline est autorisé dans des zones importantes, ce qui entraîne des dépenses excessives importantes de fonds publics. Par conséquent, une évaluation fiable de l’état de corrosion des pipelines et des réparations rapides et correctes basées sur les données obtenues sont nécessaires. À cet effet, des détecteurs de défauts ont été développés, construits et testés dans notre pays pour évaluer l'état de corrosion des canalisations sans les ouvrir depuis la tranchée.
Le diagnostic est un mot fréquemment utilisé dans monde moderne. Il est devenu si fermement intégré dans notre cycle de vocabulaire quotidien que nous n’y prêtons plus aucune attention particulière. Cassé Machine à laver- diagnostics, entretien de votre voiture préférée - diagnostics, aller chez le médecin - diagnostics. Une personne érudite dira : diagnostic, du grec signifie « la capacité de reconnaître ». Alors, que faut-il réellement reconnaître dans l'état technique d'un objet métallique soumis à la corrosion et dans les systèmes de protection électrochimiques (principalement cathodiques) s'ils sont présents sur l'objet ? Nous en parlerons brièvement dans cette revue.
Tout d’abord, convenons des conditions. Quand le terme diagnostic de corrosion (examen) est utilisé dans 90 % des cas nous parlons de sur la surface extérieure de l'objet en question. Les diagnostics sont effectués, par exemple, sur la surface extérieure des canalisations souterraines, des réservoirs et autres structures métalliques soumises à la corrosion du sol ou à la corrosion par courants vagabonds, la surface extérieure des structures d'amarrage corrodées sous l'influence du sel et eau fraiche etc. Si nous parlons de l'analyse des processus de corrosion sur la surface interne des mêmes pipelines ou réservoirs, alors au lieu des termes « diagnostic » ou « inspection », le terme « surveillance » est généralement utilisé. Différents termes impliquent différents principes assurer la sécurité contre la corrosion - l'étude de l'état de corrosion de la surface extérieure est généralement effectuée de manière discrète, une fois tous les 3 à 5 ans, et la surveillance des processus de corrosion à l'intérieur de l'objet étudié est effectuée soit en continu, soit à de courts intervalles (une fois par mois ).
Alors, par où commencer pour diagnostiquer l’état de corrosion de l’objet en question ? À partir d'une évaluation du danger potentiel et situation actuelle de choses. Si l'objet est, par exemple, sous l'eau, il est potentiellement possible dans un premier temps de procéder à une inspection visuelle de la présence de défauts de corrosion et de traces de corrosion et, s'ils sont présents, d'évaluer le danger actuel et prévu. Dans les endroits où le contrôle visuel n'est pas possible, le danger potentiel est évalué sur la base de signes indirects. Considérons ci-dessous les principaux paramètres diagnosticables des risques potentiels de corrosion et leur impact sur le processus de destruction par corrosion :

En plus des principaux facteurs indiqués ci-dessus, lors du diagnostic de l'état de corrosion, en fonction des caractéristiques de l'objet, un grand nombre de paramètres supplémentaires sont étudiés, tels que : la valeur du pH du sol ou de l'eau (notamment avec le danger potentiel de stress fissuration par corrosion), la présence de microorganismes corrosifs, la teneur en sel du sol ou de l'eau, la possibilité d'aération et d'humidification de l'objet, etc. Tous ces facteurs peuvent, dans certaines conditions, augmenter fortement le taux de destruction par corrosion de l'objet examiné.
Après avoir étudié les paramètres des risques potentiels de corrosion, des mesures directes de la profondeur des dommages dus à la corrosion sur le site sont souvent effectuées. À ces fins, toute la gamme des méthodes de contrôle non destructif est utilisée : contrôles visuels et de mesure, méthodes par ultrasons, contrôles magnétométriques, etc. Les sites de contrôle sont sélectionnés en fonction de leur dangerosité potentielle sur la base des résultats de l'évaluation réalisée lors de la première étape. Pour les objets souterrains, des tranchées sont réalisées pour donner accès directement à l'objet.
Sur étape finale peut être accompli recherche en laboratoire, par exemple, évaluer le taux de corrosion dans des conditions de laboratoire ou des études métallographiques de la composition et de la structure du métal aux endroits de défauts de corrosion.
Si des diagnostics sont effectués sur un objet déjà équipé de systèmes de protection électrochimique anti-corrosion, en plus d'étudier l'état de corrosion de l'objet lui-même, un diagnostic de l'état de fonctionnement et de la qualité de fonctionnement du système ECP existant est effectué, c'est-à-dire ses performances en général et les valeurs de sortie et paramètres contrôlés en particulier. Nous décrirons le plus paramètres importants Systèmes ECP qui doivent être surveillés lors de la réalisation d’une étude complète des systèmes ECP.
- Potentiel cathodique. Paramètre principal fonctionnement de la cathode et protection de la bande de roulement. Détermine le degré de protection d'un objet contre la corrosion à l'aide des moyens ECP. Les valeurs standard sont fixées par fondamental documents réglementaires pour la protection anticorrosion : GOST 9.602-2005 et GOST R 51164-98. Elle est mesurée aussi bien aux points fixes (centres d'instrumentation et de contrôle) que le long du parcours par la méthode des électrodes déportées.
- Statut des installations ECP : stations de protection cathodique, sacrificielle et de drainage, mise à la terre anodique, instrumentation, brides isolantes, lignes de câbles etc. Toutes les caractéristiques de l'équipement examiné doivent être comprises dans les valeurs spécifiées dans le projet. De plus, vous devez faire une prévision des performances de l’équipement pour la période allant jusqu’à la prochaine inspection. Par exemple, les stations de protection cathodique doivent disposer d'une réserve de courant pour pouvoir réguler le potentiel de protection d'un objet lors du vieillissement inévitable du revêtement isolant. S'il n'y a pas de réserve de courant, il faudra prévoir de remplacer la station de protection cathodique par une plus puissante et/ou de réparer la mise à la terre anodique.
- Impact du système ECP sur les objets tiers. En cas d'erreurs de conception dans les systèmes ECP, celles-ci peuvent avoir un effet néfaste sur les structures métalliques tierces. Cela se produit particulièrement souvent sur les pipelines de champs pétroliers et gaziers, les sites industriels et les installations situées à l’intérieur des zones urbaines denses. Le mécanisme de cette influence est décrit en détail. Une évaluation de cette influence doit nécessairement être réalisée dans le cadre du diagnostic des systèmes ECP.
Sur la base des résultats de l'inspection, un rapport technique doit être établi, qui doit contenir toutes les données numériques des mesures prises, des graphiques des potentiels de protection et des soi-disant traces, une description des défauts et défauts identifiés, des photographies détaillées, etc. . En outre, le rapport doit tirer une conclusion sur le risque de corrosion de l'installation avec la localisation de zones à haut risque et développer solutions techniques sur la protection anticorrosion.
Ainsi, après avoir terminé toutes les étapes de diagnostic, le client reçoit un rapport contenant des informations détaillées en fonction de l'état de corrosion de l'objet et de l'état du système ECP. Mais les informations obtenues par les équipes de diagnostic (parfois avec beaucoup de difficulté, compte tenu des caractéristiques du terrain et du climat) disparaîtront tout simplement et perdront leur pertinence si elles ne sont pas traitées dans un certain délai, c'est-à-dire défaut d'élimination rapide des défauts identifiés lors de l'inspection, ou non-équipement de l'objet d'inspection de moyens anticorrosion supplémentaires. La situation de la corrosion dans une installation évolue constamment et si les informations de diagnostic reçues ne sont pas immédiatement traitées, elles peuvent devenir très obsolètes. Par conséquent, si le propriétaire se soucie de la sécurité de ses installations contre la corrosion, son système de protection anticorrosion est régulièrement mis à niveau sur la base des résultats d'examens de diagnostic régulièrement effectués, et le risque de défaillance due à la corrosion dans ces installations est minime.
Tags : courants vagabonds, diagnostics de corrosion, diagnostics d'état de corrosion, revêtement isolant, influence inductive, sources courant alternatif, risque de corrosion, micro-organismes dangereux pour la corrosion, inspection de la corrosion, fissuration par corrosion sous contrainte, état de corrosion, résistance électrolytique, état du revêtement isolant, protection électrochimique, potentiel électrochimique, ECP
Page 2
Le contrôle de l'état de corrosion des canalisations et câbles existants situés dans la zone d'influence des courants vagabonds est réalisé en mesurant la différence de potentiel entre la canalisation et le sol à l'aide de voltmètres à haute résistance. Les zones anodiques d'un ouvrage souterrain sont très dangereuses et nécessitent des mesures de protection urgentes. Le degré de risque de corrosion dans les zones alternées est évalué en fonction de la valeur du coefficient d'asymétrie (tableau I.
Une analyse de l'état de corrosion des conduites d'eau préfabriquées a montré que leur durée de vie dans les champs West Surgut et Solkinskoye ne dépasse pas 3 à 6 ans. Pendant l'exploitation, 14 km de pipelines ont été entièrement remplacés dans le seul système de maintien de la pression de formation du champ West Surgut. En 1978, 30 ruptures et fistules ont été enregistrées sur les pipelines du champ Solkinskoye et 60 ruptures sur le champ Western Surgutskoye.
Une analyse de l'état de corrosion des structures métalliques OOGKM indique que les délaminages progressifs qui pénètrent à plus de 50 % dans le matériau des parois des équipements de type coque sont inacceptables.
Une analyse de l'état de corrosion des équipements de l'installation de traitement des gaz du champ d'Orenbourg a montré que surface intérieure l'équipement est recouvert d'une couche uniforme d'environ 0,1 mm d'épaisseur, constituée de dépôts pyrophoriques.
Un examen de l'état de corrosion des équipements de production de PEHD montre que la principale cause de corrosion des équipements est l'exposition à un environnement agressif contenant du chlorure d'hydrogène formé lors de la décomposition du catalyseur. Le processus de corrosion des équipements entraîne une diminution de leur durée de vie, réparations fréquenteséquipements et contamination du polyéthylène par des produits de corrosion. Les composés de fer entrant dans le polymère affectent négativement ses propriétés physico-chimiques et propriétés mécaniques. Ils provoquent un vieillissement prématuré (destruction) du polymère, une coloration indésirable des produits en gris foncé, augmentent la fragilité et réduisent les propriétés diélectriques du polymère. De plus, lorsque des équipements recouverts de vernis se corrodent, il arrive que des particules de vernis pénètrent dans le polyéthylène, ce qui entraîne son gonflement ou la formation de pores à l'intérieur du polymère.
L’état corrosif de MG LC s’entend comme expression quantitative indicateurs opérationnels de la section MG contenant des défauts d'origine corrosion et (ou) corrosion sous contrainte.
Pour déterminer l'état de corrosion (diagnostic) et détecter en temps opportun d'éventuelles défaillances dues à la corrosion, les machines en fonctionnement sont vérifiées périodiquement.
À l'avenir, la détermination à distance de l'état de corrosion permettra d'effectuer des tests accélérés avec une expérience contrôlée et une modélisation des différentes étapes du processus de corrosion.
Déterminer l'état de corrosion et sélectionner une méthode de protection des gazoducs nouvellement construits avant leur mise en service (avant leur raccordement au réseau existant), mesures électriques. Les gazoducs préalablement nouvellement posés sont shuntés par ceux qui sont exploités afin d'obtenir une image fidèle de l'état électrique des gazoducs, qui se produit après leur connexion au réseau existant. Si, lors des mesures, il est déterminé que les potentiels ne dépassent pas 0,1 V, la connexion est généralement établie sans aucune condition. À des potentiels supérieurs à OD V (jusqu'à 0,6 V), un nouveau gazoduc peut être connecté au gaz, à condition que la protection soit assurée dans un délai de 3 à 5 mois. À des potentiels élevés, les gazoducs nouvellement construits ne peuvent pas être raccordés au gaz avant le dispositif de protection, car après une courte période de temps, le gazoduc peut être détruit par le courant, ce qui peut entraîner de graves conséquences. De nombreux cas sont connus dans la pratique où des gazoducs non protégés ont été détruits par des courants vagabonds 1 à 2 mois après leur mise en service, ainsi qu'avant leur mise en service, en particulier dans les zones des sous-stations de traction ferroviaire.
Une prévision à long terme de l'état de corrosion des tronçons de gazoduc doit être utilisée pour sélectionner les points caractéristiques de surveillance de la dynamique de la corrosion dans les systèmes de surveillance de la corrosion fixes et mobiles et pour ajuster les réglementations de surveillance des paramètres de corrosion et de protection des gazoducs contre divers types corrosion.
Pour contrôler l'état de corrosion, des méthodes de contrôle per-destructif sont utilisées, qui peuvent être utilisées à la fois de manière constante et périodique (ou, si nécessaire, en complément) et à n'importe quelle étape du fonctionnement des objets, quel que soit leur état. Ces méthodes comprennent des méthodes d'émission ultrasonique, radiographique et acoustique pour la détection des défauts de couleur.
Pour déterminer l'état de corrosion d'un système, les paramètres thermodynamiques et expérimentaux de ce système, ainsi que les dépendances empiriques, sont utilisés. Le programme comprend la prévision du potentiel du métal du système, la force du courant de corrosion, l'évolution des courbes de polarisation, la zone d'immunité (active et passive), il permet de trouver les combinaisons de conditions les plus défavorables qui assurer le développement de la corrosion. Les auteurs ont présenté des moyens d'améliorer le programme de prévision de la corrosion, ce qui devrait accroître l'exactitude et la fiabilité de la prévision des quantités caractérisant le système corrosif.
L'état corrosif des canalisations est l'un des principaux facteurs caractérisant les performances du MG LC, la fiabilité et la sécurité de son fonctionnement. La protection des pipelines est déterminée par l'état du revêtement isolant et des systèmes ECP.
Pour installations de protection électrochimique (ECP) le contrôle de l'état technique de chacun est effectué par le biais d'inspections périodiques. Parallèlement, les lectures des instruments de mesure électriques sont vérifiées appareils de controle, mesure de potentiels aux points de drainage, mesure résistance électrique Chaînes courant continu, évaluation de la continuité de fonctionnement de l'installation de protection cathodique à l'aide d'un compteur ou compteur spécial énergie électrique, contrôle connexions de contact, mises à la terre des anodes, unités et unités d'installations.
Les contrôles sont effectués au minimum : 4 fois par mois pour les installations de protection de drainage, 2 fois par mois pour les installations de protection cathodique.
Un contrôle constant du fonctionnement des installations de protection cathodique est assuré par des dispositifs télémétriques. Cela vous permet de réduire les coûts et les délais de détours des installations, de réduire le temps d'interruption de leur fonctionnement à partir du moment où une panne est détectée jusqu'au remplacement ou à la réparation de l'installation, et augmente la précision de réglage et la stabilité des paramètres des équipements ECP.
Lors du contrôle de l'état de protection électrochimique d'un tronçon principal de gazoduc, les éléments suivants sont déterminés :
Niveau de protection cathodique du pipeline ;
L'amplitude des potentiels de polarisation en utilisant la méthode d'arrêt de la source de polarisation (MSS) ou des méthodes d'extrapolation utilisant la même systèmes de mesure;
Courants de polarisation circulant dans le pipeline selon la méthode recommandée par GOST ;
L'ampleur de la résistivité électrique du sol ;
Composition d'échantillons d'électrolyte intercalaire contenus dans les endroits de gonflements, sacs et autres défauts du revêtement isolant.
Surveillance de la sécurité des pipelines consiste à mesurer périodiquement les potentiels « structure-terre » sur toute la longueur du pipeline et à comparer les valeurs obtenues avec la valeur standard, ainsi qu'à déterminer le temps total pendant lequel le pipeline a une valeur de potentiel de protection sur toute sa longueur .
Les potentiels sont mesurés sur toute la longueur du pipeline à l'aide d'une électrode de référence externe avec un pas de mesure de 10 à 20 m au moins une fois tous les cinq ans. Dans ce cas, la première mesure doit être effectuée au moins 10 mois après le remblayage de la canalisation.
Mesures de potentiel dans les colonnes de contrôle et de mesure (CMC) et les électrodes distantes aux points du parcours qui ont valeurs minimales potentiel, produit au moins deux fois par an. De plus, des mesures sont effectuées lors de travaux liés au développement des systèmes ECP, aux changements de mode de fonctionnement des installations de protection cathodique et lors de travaux liés à l'élimination des sources de courants vagabonds.
Sur la base des résultats des mesures potentielles, il convient de construire des graphiques et de déterminer la protection sur toute la longueur, et sur la base des données de télésurveillance du fonctionnement des installations de protection cathodique ou de leurs contrôles techniques, de la protection des canalisations dans le temps.
Surveillance de l'état technique des revêtements isolants pendant la construction réalisés sur des chantiers terminés. Le contrôle de continuité est effectué par polarisation cathodique. Les données sur les résultats sont saisies dans la documentation exécutive.
Contrôle des revêtements isolants en fonctionnement réalisée dans le cadre d'un examen complet de la MG. Comparaison des données obtenues lors de l'examen de la MG avec les données documentation exécutive permet d'évaluer l'évolution des propriétés protectrices des revêtements dans le temps et sur la longueur.
La détermination de l'état du revêtement dans la zone étudiée est évaluée en deux étapes en utilisant des méthodes directes et indirectes.
Indirectement basé sur l'analyse des données sur les changements de densité de courant de protection au fil du temps, les résultats des mesures du potentiel pipeline-terre et l'examen électrométrique de la corrosion ;
Méthode directe avec piqûres sélectives.
Méthodes indirectes La détermination de l'état de l'isolation et du système ECP implique des mesures intégrales et locales.
Par méthodes intégrales déterminer les caractéristiques de la section examinée du gazoduc dans son ensemble. Ces méthodes permettent d'évaluer l'état du revêtement sur toute la longueur du profilé et de déterminer les emplacements de pelage et d'endommagement de l'isolant. Dans le même temps, des zones spécifiques individuelles sont identifiées dans lesquelles il est nécessaire d'appliquer des méthodes locales de surveillance des revêtements et des moyens ECP.
Les principaux critères pour déterminer la fréquence de surveillance de l'isolation sans ouvrir la tranchée sont la densité de courant de protection sur la canalisation et la résistance de transition canalisation-terre, qui permettent une évaluation intégrale de la qualité du revêtement isolant. Sur la base de ces données, avec l'aide de chercheurs, ils recherchent les lieux d'endommagement du revêtement isolant et effectuent des fouilles sélectives.
Méthode directe ou piqûre sélective consiste à ouvrir le gazoduc, à nettoyer sa surface du sol, à inspecter visuellement le revêtement isolant et à mesurer la résistance de contact, par exemple à l'aide de la méthode « serviette ». Dans ce cas, il convient d'effectuer des mesures de continuité, d'adhésion, d'épaisseur et de résistance électrique transitoire du revêtement. Un échantillonnage de l'isolation et des tests en laboratoire des revêtements sont effectués tous les 3 ans de fonctionnement. Parallèlement, des échantillons de sol et d'électrolytes du sol sont prélevés pour surveiller le système ECP.
Après l'inspection, l'isolation est ouverte, principalement dans les zones présentant dommages mécaniques et d'autres défauts. Si de la corrosion et d'autres dommages sont détectés dans les zones dégagées, la zone d'inspection s'étend pour déterminer les limites de la section endommagée du tuyau. L'inspection obligatoire comprend la section du joint soudé circonférentiel.
L'état des revêtements isolants est contrôlé par piqûre sélective 3 ans après le début de l'exploitation des revêtements, et une fois par an lorsque les valeurs critiques d'ECP sont atteintes et que la résistance de contact locale est réduite à 10 ohms m.
Les méthodes intégrales et locales sont électrométriques. Ils utilisent des appareils à courant continu et alternatif et sont divisés en contact et sans contact.
L'état de corrosion est évalué par inspection et mesures instrumentales dans des fosses de contrôle. Les déterminations sont faites en premier :
Dans les zones où l'état n'est pas satisfaisant des revêtements protecteurs;
Dans les zones non dotées d'une polarisation cathodique continue de la valeur de protection ;
Dans les sections du tracé présentant un risque de corrosion, qui comprennent des sections chaudes avec une température des produits transportés supérieure à 40° C, les sections de pipelines exploitées au sud du 50e parallèle latitude nord, dans les sols salins (marais salants, solonetzes, solods, takyrs, sors, etc.), sur les sols irrigués ;
Dans les zones de courants vagabonds ;
Dans les zones où les pipelines sortent du sol ;
Aux intersections de pipelines ;
Sur les zones de pente des ravins, ravins et rivières ;
Dans les domaines des eaux usées industrielles et domestiques ;
Dans les zones avec arrosage périodique du sol.
À inspection visuelle et mesure individuelle de l'état de corrosion de la canalisation dans la fosse, on détermine ce qui suit :
Présence et nature des produits de corrosion ;
Profondeur maximale de la caverne ;
Surface endommagée par la corrosion.
Un examen complet de l'état de corrosion des principaux gazoducs et oléoducs existants et de leurs systèmes de protection électrochimique a été réalisé afin de déterminer la dépendance de la présence de dommages de corrosion et de corrosion sous contrainte sur le CPZ externe sur les modes de fonctionnement des équipements ECP, identifier et éliminer les causes de l'apparition et de la croissance de la corrosion et des dommages causés par la corrosion sous contrainte. En effet, les principaux gazoducs et oléoducs ne sont pratiquement pas sujets à l'obsolescence au cours de leur exploitation. La fiabilité de leur fonctionnement est principalement déterminée par le degré de corrosion et d'usure par corrosion sous contrainte. Si l'on considère la dynamique du taux d'accidents des gazoducs pour la période de 1995 à 2003, il devient évident qu'il existe un processus d'augmentation du taux d'accidents au fil du temps en raison de la formation de défauts de corrosion et de corrosion sous contrainte sur le KZP.
Riz. 5.1.
Lorsque l'on considère la dynamique d'élimination des défauts particulièrement dangereux sur les principaux gazoducs existants, il devient évident que pendant l'exploitation, il y a une augmentation des défauts particulièrement dangereux nécessitant une réparation prioritaire, causés par la corrosion externe et les fissures de corrosion sous contrainte (Fig. 5.1). De celui représenté sur la Fig. Le graphique 5.1 montre que presque tous les défauts particulièrement dangereux éliminés sont de nature corrosive ou corrosive sous contrainte. Tous ces défauts ont été détectés sur la surface externe protégée par la cathode.
Les résultats d'examens approfondis de la protection anticorrosion des gazoducs et des oléoducs (présence de piqûres de corrosion et de fissures de corrosion sous contrainte, adhérence et continuité du revêtement isolant, degré de protection électrochimique) indiquent que la solution au problème de la protection anticorrosion des principaux gazoducs et oléoducs à l'aide de revêtements isolants et de polarisation cathodique reste d'actualité à ce jour. Les résultats des diagnostics en ligne en sont une confirmation directe. Selon les données de diagnostic en ligne, dans certaines sections des principaux oléoducs et gazoducs ayant une durée de vie supérieure à 30 ans, la proportion de défauts corrosion externe(y compris la corrosion sous contrainte) atteint 80 % de nombre total défauts identifiés.
La qualité de l'isolation des principaux gazoducs et oléoducs est caractérisée par la valeur de la résistance de transition, déterminée sur la base des paramètres de protection électrochimique. L'un des principaux paramètres de protection électrochimique des canalisations, caractérisant la qualité du revêtement isolant, est l'ampleur du courant de protection cathodique. Les données sur le fonctionnement des équipements ECP indiquent que la valeur du courant de protection du RMS sur la partie linéaire de D 1220 mm sur 30 ans de fonctionnement en raison du vieillissement de l'isolation a augmenté de près de 5 fois. Consommation de courant pour assurer la protection électrochimique de 1 km d'oléoduc dans la zone de potentiels de protection 1,2...2,1 V m.s. e. a augmenté de 1,2 à 5,2 A/km, ce qui indique une diminution proportionnelle de la résistance de transition de l'oléoduc. La résistance transitoire d'isolation après 30 ans d'exploitation des gazoducs et oléoducs est du même ordre (2,6-10 3 Ohm - m 2) sur toute la longueur, à l'exception des zones où des réparations majeures des gazoducs et oléoducs ont été effectuées avec remplacement de l'isolation, tandis que l'ampleur de la corrosion et des contraintes - dommages causés par la corrosion sur la surface externe protégée par la cathode varie dans des limites significatives - de 0 à 80 % du nombre total de défauts identifiés par la détection de défauts en ligne, qui sont localisés à la fois au niveau aux carrefours des zones de protection et à proximité des points de drainage du SCP dans les basses terres et les zones humides du tracé. Eaux souterraines zones humides de la partie centrale Sibérie occidentale Ils se caractérisent par une faible minéralisation (0,04 % en masse) et, par conséquent, une résistance ohmique élevée (60... 100 Ohm·m). De plus, les sols marécageux sont acides. La valeur pH de l'eau des marais atteint 4. La résistance ohmique élevée et l'acidité de l'électrolyte des marais sont les facteurs les plus importants qui influencent le taux de corrosion des gazoducs et des oléoducs et l'efficacité de leur protection électrochimique. Il convient de noter que dans les solutions interstitielles des sols marécageux, la teneur en sulfure d'hydrogène atteint 0,16 mg/l, ce qui est un ordre de grandeur plus élevé que dans les sols ordinaires et les réservoirs fluides. Le sulfure d'hydrogène, comme le montrent les données d'enquête, affecte également l'état corrosif des gazoducs et des oléoducs. L'apparition d'une corrosion du sulfure d'hydrogène due à l'activité des bactéries sulfato-réductrices (SRB) est indiquée, par exemple, par le fait que, dans d'autres conditions identiques, la profondeur maximale de pénétration de la corrosion externe dans les défauts traversants de l'isolation des gaz et les oléoducs dans les marécages stagnants sont supérieurs de 70 % en moyenne à ceux des réservoirs fluides, d'une part, et presque partout, des fissures de corrosion sous contrainte sur le KZP extérieur se trouvent également dans les marécages stagnants à forte teneur en H 2 S , de l'autre. Selon les concepts modernes, le sulfure d'hydrogène moléculaire stimule l'hydrogénation des aciers. L'électroréduction de H 2 S au KZP du pipeline se déroule par les réactions H,S + 2-»2Н alc + S a ~ c et H,S + V-^Hads + HS”ac, qui augmente le degré de remplissage de la couche chimisorbée en hydrogène atomique en c, se diffusant dans la structure des tuyaux en acier. Le dioxyde de carbone est également un stimulateur efficace de l'hydrogénation : HC0 3 +e-> 2H adc +C0 3". Le problème des produits corrosifs et
La destruction par corrosion sous contrainte des oléoducs et des gazoducs dans les zones marécageuses du tracé n'a pas encore été entièrement expliquée et reste d'actualité. Les résultats d'une inspection de corrosion des principaux gazoducs et oléoducs dans les zones marécageuses ont montré que presque toute la surface extérieure des oléoducs et des gazoducs, dans les défauts d'isolation et sous l'isolation pelée, est recouverte de dépôts bruns (ressemblant à de la poudre d'aluminium). Les piqûres de corrosion de profondeur maximale sont localisées dans les dommages traversants de l'isolation. Paramètres géométriques les dommages dus à la corrosion correspondent presque exactement à la géométrie des dommages traversants de l'isolation. Sous l'isolant pelé, dans la zone de contact de la paroi du tuyau avec l'humidité du sol, des traces de corrosion sont constatées sans piqûres de corrosion visibles avec des traces de fissures de corrosion sous contrainte.
Expérimentalement, à l'aide d'échantillons de tuyaux en acier installés sur la paroi d'un oléoduc principal d'un diamètre de 1220 mm (aux génératrices supérieure, latérale et inférieure), il a été déterminé que dans les sols de la région des marais de la taïga de la partie centrale de En Sibérie occidentale, le taux de corrosion des échantillons sans protection cathodique dans les défauts d'isolation traversants atteint 0,084 mm/an. Sous le potentiel de protection (avec composante ohmique) moins 1,2 V m.s. par exemple, lorsque la densité de courant de protection cathodique dépasse la densité limite de courant d'oxygène de 8 à 12 fois, le taux de corrosion résiduelle ne dépasse pas 0,007 mm/an. Ce taux de corrosion résiduelle, selon une échelle de résistance à la corrosion en dix points, correspond à l'état de corrosion très persistant et pour les principaux gazoducs et oléoducs est acceptable. Le degré de protection électrochimique dans ce cas est :
Lors d'un examen complet de l'état de corrosion de la surface externe protégée par cathode des gazoducs et des oléoducs dans les fosses, des piqûres de corrosion d'une profondeur de 0,5... 1,5 mm ont été découvertes dans les défauts d'isolation traversants. Il n'est pas difficile de calculer le temps pendant lequel la protection électrochimique n'a pas supprimé le taux de corrosion du sol jusqu'à ce que valeurs acceptables, correspondant très persistantétat de corrosion des gazoducs et des oléoducs :
à une profondeur de pénétration de la corrosion de 0,5 mm à une profondeur de pénétration de la corrosion de 1,5 mm
C'est pour 36 ans d'activité. La raison de la diminution de l'efficacité de la protection électrochimique des gazoducs et des oléoducs contre la corrosion est associée à une diminution de la résistance transitoire de l'isolation, à l'apparition de défauts traversants dans l'isolation et, par conséquent, à une diminution de la densité de courant de protection cathodique aux jonctions des zones de protection du SCZ à des valeurs qui n'atteignent pas les valeurs de densité de courant limite pour l'oxygène, qui ne permettent pas de supprimer la corrosion du sol à des valeurs acceptables, bien que les valeurs de protection les potentiels mesurés avec la composante ohmique sont conformes à la norme. Une réserve importante qui permet de réduire le taux de destruction par corrosion des gazoducs et des oléoducs est l'identification rapide des zones de sous-protection lorsque 1 1 G / D
La corrélation des défauts de corrosion externe d'un oléoduc avec la durée des pannes sur les lignes aériennes le long du parcours indique que c'est précisément lors des pannes des lignes aériennes le long du parcours et des temps d'arrêt du VL que la corrosion par piqûres se produit dans les défauts d'isolation, le dont le taux atteint 0,084 mm/an.

Riz. 5.2.
Lors d'un examen complet des systèmes de protection électrochimique des principaux gazoducs et oléoducs, il a été constaté que dans le domaine des potentiels de protection cathodique de 1,5...3,5 V m.s. e. (avec composant ohmique) densité de courant de protection cathodique j un dépasse la densité de courant limitant l'oxygène j 20... 100 fois ou plus. De plus, aux mêmes potentiels de protection cathodique, la densité de courant, selon le type de sol (sable, tourbe, argile), varie considérablement, près de 3...7 fois. En conditions de terrain, en fonction du type de sol et de la profondeur de pose de la canalisation (profondeur d'immersion de la sonde indicatrice de corrosion), la densité de courant limite pour l'oxygène, mesurée sur une électrode de travail en acier 17GS d'un diamètre de 3,0 mm, variait entre 0,08...0, 43 A/m", et la densité de courant de la protection cathodique aux potentiels avec une composante ohmique de
1,5...3,5 V m.s. e., mesuré sur la même électrode, a atteint des valeurs de 8... 12 A/m 2, ce qui provoque une libération intense d'hydrogène sur surface extérieure pipeline. Une partie des atomes d'hydrogène dans ces modes de protection cathodique pénètre dans les couches proches de la surface de la paroi du pipeline, l'hydrogénant. Sur contenu accru l'hydrogène dans des échantillons prélevés dans des pipelines soumis à une destruction par corrosion sous contrainte est indiqué dans les travaux d'auteurs nationaux et étrangers. L'hydrogène dissous dans l'acier a un effet adoucissant, ce qui conduit finalement à une fatigue due à l'hydrogène et à l'apparition de fissures de corrosion sous contrainte dans les zones de protection des canalisations souterraines en acier. Le problème de la fatigue par l'hydrogène des aciers pour tubes (classe de résistance X42-X70) a attiré une attention particulière de la part des chercheurs ces dernières années en raison de la fréquence croissante des accidents sur les principaux gazoducs. La fatigue de l'hydrogène sous la pression de fonctionnement changeant cycliquement dans le pipeline est observée presque dans forme pure lors d'une surprotection cathodique, lorsque j KZ /j >10.
Lorsque la densité de courant de protection cathodique atteint la densité de courant limite pour l'oxygène (ou dépasse légèrement, pas plus de 3 à 5 fois, ce), le taux de corrosion résiduel ne dépasse pas 0,003 à 0,007 mm/an. Excédent important (plus de 10 fois) j K t au-dessus de j ne conduit pratiquement pas à une suppression supplémentaire du processus de corrosion, mais conduit à une hydrogénation de la paroi du pipeline, ce qui provoque l'apparition de fissures de corrosion sous contrainte sur le KZP. L'apparition d'une fragilisation par l'hydrogène lors de changements cycliques de la pression de fonctionnement dans le pipeline est une fatigue par l'hydrogène. La fatigue des pipelines par l'hydrogène se produit lorsque la concentration d'hydrogène cathodique dans la paroi du pipeline ne diminue pas en dessous d'un certain niveau minimum. Si la désorption de l'hydrogène de la paroi du tuyau se produit plus rapidement que le développement du processus de fatigue, lorsque le court-circuit dépasse /pr de 3 à 5 fois maximum, la fatigue par l'hydrogène
invisible. En figue. La figure 5.3 montre les résultats de la mesure de la densité de courant des capteurs d'hydrogène avec le SCZ activé (1) et désactivé (2) sur le pipeline Gryazovets.

Riz. 5.3.
et déconnecté (2) SPS au CP I ; 3 - potentiel de protection cathodique avec le SCZ activé - (a) et la dépendance des courants du capteur d'hydrogène sur le potentiel de la canalisation avec le SCZ activé et désactivé au CP 1 - (b)
Le potentiel de protection cathodique pendant la période de mesure était compris entre moins 1,6... 1,9 V m.s. e. L’avancement des résultats des mesures électriques du tracé présentés dans la Fig. 5.3a, indique que la densité maximale du flux d'hydrogène dans la paroi du tuyau avec le RMS activé était de 6... 10 μA/cm2. En figue. 5.3, b Les zones de changement dans les courants des capteurs d'hydrogène et les potentiels de protection cathodique avec le SCZ activé et désactivé sont présentées.
Les auteurs des travaux notent que le potentiel du pipeline avec le RMS désactivé n'a pas diminué en dessous de moins 0,9... 1,0 V m.s. e., ce qui est dû à l’influence de la SCZ adjacente. Dans le même temps, les densités de courant des capteurs d'hydrogène avec le SCZ activé et désactivé diffèrent en
2...3 fois. En figue. La figure 5.4 montre les courbes d'évolution des courants des capteurs d'hydrogène et des potentiels de protection cathodique au KP 08 du nœud Krasnoturinsky.
L'avancée des études expérimentales illustrées à la Fig. 5.4 indique que la densité maximale du flux d'hydrogène dans la paroi du tuyau n'a pas dépassé 12... 13 μA/cm 2. Les potentiels de protection cathodique mesurés étaient compris entre moins 2,5 et 3,5 V m.s. e. Il a été montré ci-dessus que le volume d'hydrogène libéré au CPC dépend de la valeur du critère sans dimension jK z/u pr. À cet égard, il est intéressant de comparer les résultats des diagnostics en ligne des principaux oléoducs et gazoducs existants avec les modes de protection cathodique.

Riz. 5.4.
Dans le tableau 5.1 présente une comparaison des résultats des diagnostics en ligne avec les résultats d'une étude complète des systèmes ECP des oléoducs et gazoducs existants dans la partie centrale de la Sibérie occidentale. Les résultats des mesures électrochimiques sur la partie linéaire des oléoducs et gazoducs existants indiquent que dans différents sols aux mêmes valeurs du potentiel mesuré, les densités de courant de protection cathodique varient dans de larges limites, ce qui oblige à contrôler en plus le cathodique densité de courant de protection lors de la sélection et de l'ajustement des potentiels de protection des canalisations souterraines par rapport à la densité de courant limitant l'oxygène. Des mesures électrochimiques supplémentaires le long du tracé des principaux gazoducs et oléoducs existants empêcheront ou minimiseront la formation de contraintes locales élevées dans la paroi des pipelines causées par la molisation de l'hydrogène (avec une énergie figurative élevée). Une augmentation du niveau de contraintes locales dans la paroi du pipeline est associée à une modification de la triaxialité de l'état de contrainte dans les zones locales enrichies en hydrogène cathodique, où se forment des microfissures, précurseurs de fissures de corrosion sous contrainte sur le CCP externe.
Comparaison des résultats des diagnostics en conduite avec les résultats d'un examen complet des systèmes
protection électrochimique des gazoducs et oléoducs existants dans la partie centrale de la Sibérie occidentale
Distance, |
Distribution du potentiel de protection (0WB) (Personne A/m 2) |
Signification critères j k.z ^Jxvp |
opération, mm |
Densité défauts une perte méthane, |
Densité défauts délaminage, | |||
Lily partie de l'oléoduc principal D 1220 mm |
||||||||
Distance, |
Densité de courant limite pour l'oxygène (LrHA/m 2 |
Répartition du potentiel de protection et densité de courant de protection cathodique (Cils>A/m 2) |
Signification critères Ук.з ^ Ур |
Profondeur de pénétration maximale de la corrosion pour toute la période opération, mm |
Densité défauts une perte métal, |
Densité des défauts délaminage, pièces/km |
Durée totale du temps d'arrêt du VCS pour toute la période d'exploitation (selon l'organisme exploitant), jours |
|
Analyse des résultats présentés dans le tableau. 5.1, compte tenu de la durée du temps d'arrêt, le RMS indique une relation inversement proportionnelle entre la densité des défauts de corrosion et la valeur du critère sans dimension jK s/ j, y compris lorsque ce rapport était égal
zéro. En effet, la densité maximale de défauts corrosion externe observé dans les zones où la durée d'arrêt des équipements de protection électrochimique (selon les organismes exploitants) dépassait les valeurs standards. En revanche, la densité maximale de défauts de type délaminage observé dans les sections de plaines inondables marécageuses de l'itinéraire, où la durée du temps d'arrêt des équipements ECP n'a pas dépassé les valeurs standard. Une analyse des modes de fonctionnement des SCP dans les zones avec une durée minimale de leur temps d'arrêt sur fond d'une large dispersion de données indique une relation presque proportionnelle entre la densité de défauts du type délaminage et critère jK 3 / / lorsque la densité de courant de la protection cathodique dépassait la densité de courant limite pour l'oxygène de dix fois ou plus pendant longue période fonctionnement (avec une durée minimale de temps d'arrêt du VCS). L'analyse des modes de protection cathodique en comparaison avec les défauts de corrosion et de corrosion sous contrainte sur le KZP confirme les conclusions formulées précédemment selon lesquelles le rapport jK 3 / jnp peut servir de critère adimensionnel pour surveiller le taux de corrosion résiduelle d'une canalisation à différents potentiels de protection cathodique, d'une part, afin d'éviter la formation de défauts sur le PSC corrosion externe et pour déterminer l'intensité de l'hydrogénation électrolytique de la paroi du pipeline - d'autre part, afin d'éliminer la formation et la croissance de défauts tels que délaminage près de la surface protégée cathodiquement.
Données du tableau 5.1 indiquent que le temps d'arrêt maximum de presque tous les SCP sur toute la période d'exploitation des principaux oléoducs et gazoducs, sur 36 ans, s'est élevé en moyenne à 536 jours (presque 1,5 an). Selon les organismes d'exploitation, pour l'année, le temps d'arrêt du VCS a été en moyenne de 16,7 jours, pour le trimestre de 4,18 jours. Cette durée d'arrêt du SCP sur la partie linéaire des oléoducs et gazoducs examinés est pratiquement conforme aux exigences des documents réglementaires et techniques (GOST R 51164-98, clause 5.2).
Dans le tableau 6.2 présente les résultats de la mesure du rapport de la densité de courant de protection cathodique à la densité du courant limite pour l'oxygène génératrice supérieure oléoduc principal D 1220 mm. Le calcul du taux de corrosion résiduelle du pipeline à des potentiels de protection cathodique donnés est déterminé par la formule 4.2. Donné dans le tableau. Les données 5.1 et 5.2 indiquent que pour toute la période d'exploitation de l'oléoduc principal, en tenant compte du temps d'arrêt des équipements de protection électrique
(selon l'organisme exploitant), la profondeur maximale de pénétration de la corrosion sur le KZP externe ne doit pas dépasser 0,12...0,945 mm. En effet, la densité de courant limite pour l'oxygène au niveau de la pose des tronçons d'oléoducs et de gaz étudiés variait de 0,08 A/m 2 à 0,315 A/m 2 . Même avec une valeur maximale de la densité de courant limite pour l'oxygène de 0,315 A/m 2, la profondeur maximale de pénétration de la corrosion sur 36 ans de fonctionnement avec un temps d'arrêt RMS prévu de 1,15 an ne dépassera pas 0,3623 mm. Cela représente 3,022 % de l’épaisseur nominale de la paroi du pipeline. Cependant, dans la pratique, la situation est différente. Dans le tableau 5.1 présente les résultats des diagnostics en conduite d'une section de l'oléoduc principal D u 1220 mm après son exploitation pendant 36 ans. Les résultats des diagnostics en ligne indiquent que l'usure maximale par corrosion de la paroi du pipeline dépassait 15 % de l'épaisseur nominale de la paroi du pipeline. La profondeur maximale de pénétration de la corrosion a atteint 2,0 mm. Cela signifie que le temps d'arrêt de l'équipement ECP ne répond pas aux exigences de GOST R 51164-98, clause 5.2.
Les mesures électrométriques effectuées, présentées dans le tableau. 5.2 indiquent qu'avec un mode de protection cathodique donné, le taux de corrosion résiduelle n'a pas dépassé 0,006...0,008 mm/an. Ce taux de corrosion résiduelle, selon une échelle de résistance à la corrosion en dix points, correspond à l'état de corrosion résistant à la corrosion et pour les principaux oléoducs et gazoducs est acceptable. Cela signifie que sur 36 ans d'exploitation du pipeline, en tenant compte des informations sur les temps d'arrêt des équipements ECP selon l'organisme exploitant, la profondeur de pénétration de la corrosion ne dépasserait pas 0,6411 mm. En effet, pendant la période d'arrêt programmé des équipements ECP (1,15 ans), la profondeur de pénétration de la corrosion était de 0,3623 mm. Sur la période de fonctionnement de l'équipement ECP (34,85 ans), la profondeur de pénétration de la corrosion était de 0,2788 mm. La profondeur totale de pénétration de la corrosion sur le KZP serait de 0,3623 + 0,2788 = 0,6411 (mm). Les résultats des diagnostics en conduite indiquent que la profondeur maximale réelle de pénétration de la corrosion sur 36 ans d'exploitation dans la section examinée de l'oléoduc principal, D u 1220 mm, était de 1,97 mm. Sur la base des données disponibles, il est facile de calculer le temps pendant lequel la protection électrochimique n'a pas réussi à réduire le taux de corrosion du sol à des valeurs acceptables : T = (1,97 - 0,6411) mm/0,08 mm/an = 16,61 ans. La durée du temps d'arrêt des équipements ECP sur un gazoduc principal d'un diamètre de 1020 mm circulant dans un couloir technique, sur lequel se trouve la plaine inondable de la rivière. Obligatoirement, des fissures de corrosion sous contrainte ont été découvertes, ce qui coïncide avec la durée d'arrêt du SCP sur l'oléoduc principal, puisque les SCP du gazoduc et de l'oléoduc sont alimentés à partir d'une seule ligne aérienne située le long du parcours.
Dans le tableau 5.3 présente les résultats de la détermination du temps d'arrêt réel du SCP pendant toute la période d'exploitation (36 ans) des principaux oléoducs et gazoducs sur la base de mesures électrométriques.
Tableau 5.2
Répartition du taux de corrosion résiduelle dans les sections de gazoducs et d'oléoducs en exploitation dans la partie centrale de la Sibérie occidentale
Tableau 5.3
Résultats de la détermination du véritable temps d'arrêt du SCP pendant toute la période d'exploitation (36 ans) des principaux gazoducs et oléoducs sur la base de mesures électrométriques
Distance, |
Maximum vitesse possible corrosion des canalisations sans court-circuit, mm/an |
Taux de corrosion résiduelle des canalisations pour un mode de court-circuit donné, mm/an |
Profondeur maximale de pénétration de la corrosion sur la surface protégée cathodiquement, mm |
Réel |
Partie linéaire de l'oléoduc principal D 1220 mm |
||||
Pièce linéaire gazoduc principal L 1020 mm |
||||
Analyse des résultats présentés dans le tableau. 5.3 indique que temps réel le temps d'arrêt des équipements de protection électrochimique dépasse largement sens normatif, ce qui est à l'origine d'une usure corrosive intense de la paroi du pipeline du côté extérieur protégé par la cathodie.