Tecnologías compuestas. Tecnologías modernas intensivas en ciencia. Tecnología compuesta - Sección de tecnología de materiales
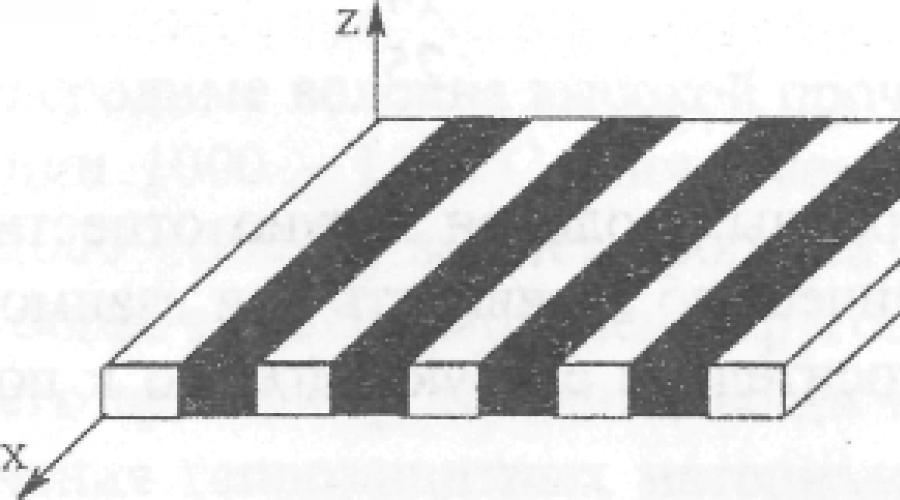
Leer también
La tecnología de cohetes, aeroespacial, ingeniería aeronáutica, ingeniería de energía nuclear, ingeniería química, automotriz, construcción naval, electrónica y muchas otras industrias necesitan materiales con alta resistencia, resistencia al calor, resistencia al calor y resistencia al calor (buena resistencia a la propagación de grietas), baja densidad, ajustable sobre una amplia gama de indicadores de conductividad térmica y eléctrica, características ópticas y magnéticas especiales, etc. ¡Muchos de los materiales industriales existentes ya no pueden! satisfacer estas solicitudes.
Un material con un complejo de tales características sólo puede obtenerse t base de composición. Los materiales compuestos (CM) son materiales que constan de dos o más componentes (componentes de refuerzo y una matriz que los une) y que tienen propiedades específicas que difieren de las propiedades totales de estos componentes.
Si uno de los componentes del CM es continuo en todo el volumen y el otro es discontinuo, desconectado en el volumen de la composición, entonces el primer componente se llama matriz y el segundo se llama refuerzo o elemento de refuerzo. Los componentes de refuerzo pueden ser varias fibras, polvos, microesferas, cristales y "bigotes" de materiales orgánicos, inorgánicos, metálicos o cerámicos. Como té matriz
Se utilizan sustancias sintéticas de alto peso molecular de diversa composición química.
La propia naturaleza fue la primera creadora de materiales compuestos. Por ejemplo, la madera es una composición que consiste en haces de fibras de celulosa de alta resistencia y sección tubular, interconectadas por una matriz de materia orgánica (lignina), que le da rigidez transversal a la madera.
Los componentes de los compuestos no deben disolverse ni absorberse entre sí. Deben tener una buena adherencia y ser compatibles entre sí. Las propiedades del CM no pueden determinarse únicamente por las propiedades de los componentes, sin tener en cuenta su interacción. Cada componente tiene una función específica y contribuye a las propiedades del compuesto. Considere los requisitos para los rellenos de refuerzo, por ejemplo, para fibras.
La forma de hilo de los elementos de refuerzo tiene lados positivos y negativos. La ventaja de las fibras es su alta resistencia y la capacidad de crear un refuerzo solo en la dirección en la que se requiere estructuralmente. La desventaja de esta forma es que las fibras solo pueden transmitir la carga en la dirección de su eje, mientras que en la dirección perpendicular no hay refuerzo y, en algunos casos, incluso puede producirse un ablandamiento.
Las fibras utilizadas como cargas de refuerzo deben tener las siguientes propiedades: alto punto de fusión, baja densidad, alta resistencia en todo el rango de temperaturas de operación, sin toxicidad durante la fabricación y operación.
Se utilizan principalmente tres tipos de rellenos: bigotes, alambre metálico y fibras policristalinas inorgánicas.
Los bigotes se consideran un material prometedor para el refuerzo de matrices hechas de metales, polímeros y cerámicas. Resistencia ultra alta en un amplio rango de temperatura a baja densidad, inercia química con respecto a muchos materiales de matriz. realam, la alta resistencia al calor y la resistencia a la corrosión de los bigotes de óxidos de aluminio y magnesio, el carburo de silicio los convierten en elementos de refuerzo indispensables. Desafortunadamente, todavía existen muchas dificultades en el camino de su aplicación práctica. Es necesario resolver los problemas de obtenerlos a escala industrial, seleccionar los bigotes adecuados, orientarlos en la matriz y métodos para formar composiciones con bigotes.
El alambre de metal hecho de acero, tungsteno, molibdeno y otros metales es menos prometedor que los "bigotes" debido a su alta densidad y menor resistencia. Sin embargo, tiene un costo relativamente bajo y es ampliamente utilizado como refuerzo, especialmente para materiales compuestos de base metálica.
Las fibras inorgánicas policristalinas se producen en grandes cantidades. La desventaja de estas fibras es su muy alta sensibilidad al daño mecánico. Baja densidad, alta resistencia y resistencia química de carbono, boro, vidrio, carburo de silicio. el cuarzo y otras fibras les permiten ser ampliamente utilizados para reforzar plásticos,
Las fibras de carbono se encuentran entre los elementos de refuerzo más prometedores. Tienen baja densidad (1430 - 1830 kg/m3), alta resistencia (3,5 GPa) y módulo elástico (250 - 400 GPa).
Generalmente, las fibras de carbono se dividen en dos tipos principales: fibras de alta resistencia y fibras de alta resiliencia. En la producción, se producen principalmente fibras de alta resistencia. La fuerza de estas fibras en la etapa inicial de desarrollo fue de 2,5 GPa. Mejorando la tecnología (pretratamiento, retardo de fibra, carbonización y acabado), se ha aumentado la resistencia, por ejemplo, para un material convencional a 3,5 GPa.
Los estudios realizados han demostrado que con un aumento en la resistencia de las fibras, la resistencia del material compuesto, por regla general, aumenta linealmente. , : ;.,
Normalmente, las fibras de carbono de alta resistencia se obtienen a una temperatura de carbonización de 1000 - 1500°C, tienen un módulo elástico de 2250 -2350 S/mm 2 . A 2000 - 3000°C debido al proceso de grafitización se pueden obtener fibras con mayor módulo de elasticidad.
Hasta hace poco, las fibras de carbono y los tejidos elaborados con ellas se utilizaban para la fabricación de materiales de protección térmica. Sin embargo, mejora. La tecnología de baño para la obtención de fibras finas combinando alta resistencia y rigidez con otras propiedades especiales (resistencia térmica, conductividad eléctrica, etc.) permitió crear metales y plásticos reforzados con fibras de carbono, que se caracterizan por una baja rigidez y alta resistencia. Tales composiciones se utilizan cada vez más en tecnología espacial, de cohetes y de aviación. Las fibras de carbono más utilizadas son la viscosa y el poliacrilonitrilo.
Dependiendo del contenido de carbono, las fibras de carbono se dividen en tres grupos:
carbonizado (no más del 95% en peso de C); - carbón (91-98% en peso de C);
grafito (más del 98% en peso de C).
La fibra de carbono rígida se obtiene si el proceso tecnológico se diseña de forma que el máximo número de capas base sea paralela al eje de la fibra. Para aumentar la resistencia de las fibras de carbono, es necesario reducir el tamaño de los cristalitos, que tienen una estructura más perfecta. Como métodos tecnológicos que dotan a las fibras de carbono de una mayor rigidez y resistencia, se alean con boro mediante difusión desde la fase gaseosa, fibras irradiadas con neutrones en un reactor nuclear, introduciéndoles bórax antes de la pirólisis, así como estiramientos en procesos de oxidación y grafitización.
Si hay microdefectos en las fibras delgadas que provocan concentraciones de tensión locales, la resistencia de las fibras de carbono disminuye. El carácter defectuoso de las fibras provoca una dependencia lineal de su resistencia con respecto a la longitud: al aumentar la longitud, la resistencia disminuye significativamente y el módulo de elasticidad aumenta ligeramente. Según el nivel de propiedades mecánicas, las fibras de carbono se dividen en tres grupos: bajo, medio, alto (Tabla 1.5)
Tabla 1.5 Propiedades mecánicas de las fibras de carbono
Grupo Densidad Resistencia Módulo de elasticidad
y, g/cm 3 a, GPa E, GPa
Bajo 18 14 42
Medio 18 14 175
Alta 18 25 420
Las desventajas de las fibras de carbono incluyen su tendencia a oxidarse en el aire, actividad química al interactuar con matrices metálicas y adhesión relativamente débil a matrices poliméricas.
El tratamiento superficial de las fibras es un proceso importante en términos de aumentar su adhesión a la matriz. Normalmente se lleva a cabo el tratamiento superficial de las fibras de carbono oxidándolas en fase gaseosa.
La presencia de metales y otras sustancias inorgánicas en ellos afecta las características de las fibras de carbono. En particular, el contenido de metales alcalinos como el sodio y el potasio tiene un efecto negativo sobre la resistencia a la oxidación cuando se calienta, y el fósforo y el boro tienen un efecto positivo.
Todos los materiales compuestos se dividen en isotrópicos y anisotrópicos. Los materiales isotrópicos son materiales que tienen las mismas propiedades en todas las direcciones, mientras que los materiales anisotrópicos son diferentes.
Los elementos de refuerzo pueden tener una forma aproximadamente equibásica o ser partículas cortas (discretas) en forma de aguja orientadas al azar en el espacio. Como tales partículas, normalmente se utilizan segmentos de fibra o "bigotes". En este caso, los QM resultan ser cuasi-isotrópicos, es decir anisotrópico en microvolúmenes, pero isotrópico en el volumen de todo el producto.
Los CM anisotrópicos incluyen materiales cuyas fibras están orientadas en ciertas direcciones: unidireccionales, en capas y reforzadas tridimensionalmente. Las imágenes de los CM anisotrópicos se dan en las Figs. 1.24, 1.25.
Arroz. 1.24. Representación esquemática de la estructura del CM por la colocación transversal de fibras.
con longitudinal
Arroz. 1.25. Representación esquemática de la estructura de un CM unidireccional (áreas negras - fibras; blanco - matriz)
La anisotropía tecnológica ocurre durante la deformación plástica de materiales isotrópicos (metales). La anisotropía física es característica de los cristales en relación con las características estructurales de su red cristalina.
En ingeniería se suelen utilizar CM anisotrópicos con cierta simetría de propiedades.
La matriz juega un papel igualmente importante en las composiciones reforzadas, lo que le da forma al producto y hace que el material sea monolítico. Combinando numerosas fibras en un solo todo, la matriz debe permitir que la composición perciba varios tipos de cargas externas: tensión, compresión, flexión, corte, etc. Al mismo tiempo, participa en la creación de la capacidad de carga de la composición. , asegurando la transferencia de fuerzas a las fibras. Debido a la plasticidad de la matriz, las fuerzas de las fibras destruidas o discretas (cortas) se transfieren a las fibras vecinas y la concentración de tensión cerca de varios tipos de defectos disminuye. La matriz también desempeña el papel de una capa protectora que protege las fibras del daño mecánico y la oxidación. Además, la matriz debe proporcionar la resistencia y rigidez del sistema bajo la acción de una carga de tracción o compresión en dirección perpendicular a los elementos de refuerzo. Si la carga de tracción se dirige a lo largo del eje de las fibras paralelas entre sí, para obtener el efecto de refuerzo, el alargamiento relativo final de la matriz debe ser al menos igual al alargamiento relativo de las fibras. Si la carga es perpendicular al eje de las fibras, esto no es suficiente. En este caso, la carga sobre las fibras se transmite solo a través de la matriz, y cuanto mayor sea la concentración de fibras y la relación de los módulos elásticos de los materiales de la fibra y la matriz, mayor debería ser la deformación final de la matriz. . El trabajo de evaluación realizado en modelos elásticos muestra que para garantizar la solidez de CM bajo carga transversal, se necesitan matrices, cuyo alargamiento relativo es varias veces mayor que la deformación promedio de las fibras.
El deseo de obtener la máxima resistencia de la composición tiende a aumentar la fracción volumétrica de fibras. Sin embargo, si el alargamiento relativo de la matriz es pequeño, entonces, en el caso de valores grandes de esta fracción, la solidez del CM puede romperse incluso bajo cargas pequeñas: aparecerán delaminaciones y grietas. Resultó que cuanto más plástica es la matriz, menos se permite el grosor de la capa intermedia de la matriz entre las fibras y más fibras se pueden introducir en el CM.
Dependiendo del material de la matriz, todos los CM se pueden dividir en tres grupos: composiciones con una matriz metálica - materiales compuestos metálicos (MCM), con un polímero - materiales compuestos poliméricos (PCM) y con una cerámica - materiales compuestos cerámicos (CMC). Los CM de polímero generalmente se denominan de acuerdo con el material de las fibras de refuerzo: reforzados con fibras de vidrio se denominan fibra de vidrio (fibra de vidrio), metal - metal-plástico (metal-fibras), orgánico - organoplásticos (organo-fibras), boro - plásticos de boro ( fibras de boro), carbono - fibra de carbono (fibra de carbono), etc.
Para los CM de metal y cerámica, no existen reglas claramente establecidas para la denominación. Más a menudo que otros, el material de la matriz se escribe primero, luego el material de la fibra. Por ejemplo, la designación "cobre-tungsteno" (Cu-W) se refiere a CM con una matriz de cobre y fibras de tungsteno. Pero en la literatura, a veces se indica primero el material de fibra y luego la matriz.
Los materiales compuestos de polímero son los más utilizados en comparación con otros debido a la facilidad de fabricación, capacidad de fabricación, bajo costo y baja densidad. Su principal desventaja es el rango de temperatura de operación limitado. Los aglutinantes poliméricos modernos (matrices) pueden garantizar el rendimiento de los productos a temperaturas que no excedan los 300 - 400 °C.
De acuerdo con su comportamiento durante el calentamiento y el enfriamiento, los aglutinantes poliméricos generalmente se dividen en termoplásticos y termoendurecibles. Las propiedades de los aglutinantes de polímeros termoplásticos permiten obtener productos a partir de ellos mediante moldeo por inyección, extrusión, pulverización y utilizar ampliamente equipos automatizados en su fabricación. Las macromoléculas de los polímeros termoplásticos tienen una estructura lineal y se obtienen a partir de monómeros que tienen dos grupos funcionales, que están unidos entre sí por fuertes enlaces covalentes. Las cadenas macromoleculares están interconectadas por fuerzas débiles de van der Waals.
Los oligómeros termoendurecibles bajo la influencia del calor, los endurecedores, los catalizadores pasan a un estado sólido (curado). Este proceso es irreversible. Los oligómeros son fácilmente solubles en algunos disolventes (alcohol, acetona, etc.), pero después del curado ya no son solubles. Las resinas termoestables están hechas de monómeros que tienen más de dos grupos funcionales. Durante el curado, los monómeros crecen en tres direcciones, formando macromoléculas en red, cuyos elementos estructurales están conectados entre sí por fuertes enlaces covalentes.
El componente principal del aglutinante polimérico es la resina. El punto de reblandecimiento, la solubilidad, la viscosidad y las propiedades finales del ligante dependen de su naturaleza, reactividad, peso molecular y estructura molecular. Además de la resina, la composición del ligante puede incluir: catalizadores o iniciadores, que se introducen en las resinas en pequeñas cantidades para favorecer su curado; plastificantes que dan al polímero un margen de plasticidad y elasticidad; tintes que colorean el material en el color deseado; estabilizadores que evitan la descomposición de los polímeros bajo la acción de la radiación luminosa y las temperaturas elevadas.
Como aglutinante para PCM estructural, operando bajo / cargas, en la mayoría de los casos, se utilizan resinas termoendurecibles. Las resinas epoxi, de poliéster, fenólicas, de organosilicio y de poliimida son las más utilizadas en la producción de PCM estructurales.
Las resinas epoxi constituyen el 90 % de las resinas utilizadas como* aglutinantes para PCM nuevos. Las resinas epoxi se pueden curar, dependiendo del tipo de endurecedor y de su cantidad, tanto a temperatura ambiente como a temperatura elevada. En el primer caso, se habla de resinas de curado en frío, en el segundo, de resinas de curado en caliente.
Las resinas epoxi son conocidas por su versatilidad. Poseen baja retracción, buena adherencia a diversos rellenos, altas propiedades mecánicas, baja absorción de humedad, permiten su procesamiento a temperatura ambiente y varían en un amplio rango de duración y temperatura de curado. Se les pueden agregar solventes, modificadores y plastificantes para cambiar la viscosidad del polímero sin curar, la resistencia química y la plasticidad. Durante su tratamiento térmico no se producen emisiones de productos de reacción volátiles. Son algo más caras que las resinas de poliéster y fenólicas, pero esto se compensa con sus mejores cualidades tecnológicas y operativas.
Por lo general, los CM basados en resinas epoxi se usan hasta 150 °C. En los últimos años, se han desarrollado nuevas resinas epoxi más resistentes al calor, que permiten su uso en GFM que funcionan a 200 °C y más.
Una cualidad muy importante de las resinas epoxi desde el punto de vista tecnológico es su capacidad para permanecer en un estado semicurado durante mucho tiempo, lo que hace posible producir telas, cintas y cables preimpregnados y parcialmente curados ("prepregs"). ) sobre su base, y luego obtener productos.
Las resinas de poliéster son productos de policondensación de ácidos dicarboxílicos insaturados (principalmente ácidos maleico y metacrílico) con alcoholes polihídricos o insaturados (dietilenglicol, trietilenglicol, etc.). Como resultado de la polimerización, se forma un polímero sólido insoluble de estructura tridimensional. Los aglutinantes de poliéster se desarrollaron mucho antes que los aglutinantes de epoxi, y los primeros CM estructurales se fabricaron sobre esta base.
Las principales ventajas de los ligantes de poliéster son su bajo costo y su fácil manejo. Pero son menos fuertes, tienen una adhesión más pobre a la mayoría de las fibras, son más frágiles, se encogen más al curar y tienen una vida útil más baja que las resinas epoxi.
Las resinas fenólicas se obtienen por policondensación de fenoles (hidroxibenceno, cresol, resorcinol, etc.) con aldehídos (furfural, formaldehído, etc.). Estas resinas son de color oscuro y tienen una mayor resistencia a altas temperaturas en comparación con los aglutinantes discutidos anteriormente.
Durante el curado, las resinas fenólicas pasan por tres etapas:
"A" - la formación de resol - el producto de la condensación inicial, que no tiene enlaces cruzados y puede disolverse en alcohol, acetona y otros solventes;
"B" - la formación de resitol - el producto en el que comenzó la formación de enlaces cruzados. Resitol se comporta como una resina termoplástica: se ablanda cuando se calienta y se vuelve duro y quebradizo a temperatura ambiente;
"C" - obtención de resit - un producto termoendurecible (insoluble y que no se funde) completamente curado.
En la etapa de resitol, cuando ya se han eliminado la mayor parte de las sustancias volátiles, se elaboran preimpregnados a partir de resinas fenólicas. Por sí mismas, las resinas fenólicas son muy frágiles.
Sus desventajas incluyen la toxicidad y la necesidad de aplicar altas presiones durante el curado. Los KM a base de resinas fenólicas son materiales diseñados para trabajar a altas temperaturas, ¡ta! cómo son capaces de soportar durante mucho tiempo temperaturas ds 315 ° C, y por poco tiempo, por encima de 3000 ° C.
Las siliconas o resinas de silicona son compuestos sintéticos co6oi que contienen junto con grupos orgánicos! silicio y oxígeno, que se incluyen en la cadena principal en forma de eslabones
KM: en base a ellos, conservan sus propiedades a temperaturas superiores a 260 ° C, se distinguen por su resistencia a la corrosión, resistencia al arco y chispas y una mayor conductividad térmica. Sin embargo, a temperatura ambiente, las propiedades de KM n; a base de resinas de silicona es menor que a base de resinas epoxi, poliéster y fenólicas. Además, son más caros. Sobre la base de resinas de organosilicio, se obtienen CM, que se utilizan en la construcción del carenado) de motores de aviones, cohetes y otros productos que funcionan a altas temperaturas.
Las resinas de poliimida se distinguen por altas tasas de estabilidad térmica y térmica y resistencia a la radiación. Los CM basados en ellos son capaces de funcionar durante mucho tiempo a temperaturas superiores a 300°С. En la etapa final de formación, las resinas de poliimida pierden su plasticidad y solubilidad] se convierten en polímeros de red policíclicos. Las perspectivas para la creación de CM de alta temperatura están asociadas a ellos. Desventajas existentes: resinas de poliimida - la necesidad de utilizar altas temperaturas y presiones durante su curado.
La tecnología para producir productos a partir de PCM incluye las siguientes etapas principales:
1. Pretratamiento de superficie UV para mejorar su humectabilidad con soluciones o masas fundidas de ligantes.
Las fibras de carbono se suministran al consumidor recubiertas con un lubricante, que se requiere como auxiliar de procesamiento. La eliminación del lubricante de la superficie de las fibras (desencolado) es una operación necesaria vrx syayazlyutim. Para este hidrocarburo, se pasa a través de gasolina, soluciones de ácido oleico (2% en peso), trietanolamina (1% en peso) u otros solventes. El lubricante también se puede eliminar calcinando el hidrocarburo a 200 - 450°C. El lavado en agua con el uso de ultrasonido da un buen efecto. Después del desencolado, algunos tipos de fibras absorben fuertemente la humedad, lo que perjudica la adhesión del aglutinante a ellas y reduce las características de rendimiento del PCM en su conjunto. La aplicación de recubrimientos hidrofóbicos (repelentes al agua) a la superficie, que aumentan la fuerza de la unión entre las fibras y el aglutinante y reducen la absorción de agua del PCM, se denomina etapa de encolado. Los apósitos se fijan calentando las fibras a 80-150°C durante 20-60 minutos. En los casos en que las fibras llegan en bobinas no aptas para bobinar o impregnar, se colocan sobre una tira unidireccional, la llamada mecha, asegurando una tensión uniforme. Esta operación se llama deformación.
2. Preparación del aglomerante.
Además del componente principal (resina), dependiendo de su naturaleza, se agregan al aglutinante varias cantidades de endurecedores, catalizadores, plastificantes y pigmentos. Se utilizan los siguientes disolventes: acetona, benceno, tolueno, dicloroetano, tetracloruro de carbono. Obviamente, al trabajar con ellos, debe cumplir con los requisitos de seguridad pertinentes.
Los diluyentes contribuyen a obtener la viscosidad tecnológica requerida del aglutinante y permanecen en él después del curado. Los diluyentes realizan simultáneamente el papel de un plastificante, aumentando la plasticidad de los aglutinantes curados. Por ejemplo, las resinas epoxi de baja viscosidad de dietilenglicol, trietilenglicol se utilizan como diluyente para resinas epoxi de alta viscosidad. Una mezcla de todos los componentes que componen el aglutinante se denomina compuesto.
Una característica tecnológica importante del aglutinante es su vitalidad (viabilidad): la capacidad de mantener un cierto tiempo (de varios minutos a varios días) viscosidad tecnológica dentro de los límites especificados. Con el tiempo, los solventes se evaporan del aglutinante, lo que aumenta la viscosidad del compuesto y empeora sus características de impregnación. Si el solvente se evapora lentamente, entonces el compuesto tiene una alta viabilidad, pero el tiempo de secado de los productos aumenta significativamente. Incluso puede ocurrir que el tiempo de eliminación completa del disolvente exceda el tiempo de curado del ligante. En este caso, habrá muchos poros y burbujas de gas en el polímero curado. El uso de disolventes volátiles reduce drásticamente la viabilidad del aglutinante, lo que tampoco es deseable. Por ejemplo, para resinas epoxi, se recomienda un solvente de volatilidad media tolueno o su solución en alcohol etílico.
Durante el transporte y el almacenamiento del aglutinante, a veces entra humedad. Por lo tanto, antes de su uso, la resina se calienta en recipientes metálicos especiales a 100 - 140 ° C y, después de eliminar el agua, se diluye con solventes o diluyentes.
3. Impregnación.
Esta es la operación de combinar el relleno con el ligante aplicando el compuesto a la superficie del CF y rellenándolo con el volumen entre las fibras.
En la actualidad, los productos de PCM se fabrican principalmente mediante dos métodos: "húmedo" y "seco". En el método húmedo, las fibras se impregnan con un aglutinante líquido justo antes del bobinado, i. la impregnación se combina tecnológicamente con el moldeado del producto. Con el método seco de impregnación; separados en una operación independiente, como resultado de lo cual del hidrocarburo y el aglutinante. conseguir preimpregnados. La impregnación y el secado se realizan en plantas especializadas por separado del bobinado, lo que permite ampliar la gama de ligantes poliméricos utilizados mediante el uso de varios; disolventes. Los aglutinantes con solventes tienen una baja viscosidad tecnológica, y esto permite lograr una alta calidad en la uniformidad de la impregnación. Los preimpregnados pueden estar en un estado parcialmente curado. de varios días a varios meses, dependiendo de la temperatura ambiente.
El bobinado en seco es una forma más progresiva que el bobinado en húmedo. Las desventajas del bobinado húmedo son las siguientes:
La elección de aglutinantes para bobinado en húmedo se limita a aquellas resinas que se pueden utilizar en forma líquida, por ejemplo, epoxi o poliéster.
En general, no es deseable usar disolventes, porque las sustancias volátiles, que se eliminan durante el curado del producto para heridas, conducen a la formación de poros, burbujas y empeoran la solidez y la resistencia.
El uso de ligantes líquidos empeora las condiciones sanitarias en el lugar de trabajo.
La productividad del bobinado húmedo está limitada por la velocidad del aglutinante.
El uso de calentamiento para reducir la viscosidad del proceso de la resina reduce la viabilidad del aglutinante, acelera el proceso de polimerización< гризации и ухудшает пропиточные свойства смолы.
6. Cuando se enrolla en húmedo, es difícil ajustar la concentración de componentes en el producto. Parte de la resina desaparece con el método húmedo.
El bobinado en seco de preimpregnados carece de todos los inconvenientes enumerados] La velocidad de bobinado no está limitada por la velocidad de impregnación y depende completamente* de las capacidades del equipo de bobinado. El bobinado con preimpregnados permite utilizar una amplia gama de resinas, para garantizar una división pacnpi uniforme del aglutinante en todo el volumen del producto, para reducir la posibilidad de pegajosidad Ppeppegy, lo que permite obtener productos de forma compleja, mayor estanqueidad y baja porosidad. Durante su formación, solo queda garantizar una conexión de alta calidad de las capas aglutinantes entre sí (autohesión) y con las fibras de refuerzo (adhesión).
Las principales desventajas del bobinado en seco incluyen la necesidad de utilizar máquinas especiales y otros equipos tecnológicos.
Existen los siguientes métodos de impregnación: refuerzo de tracción (hilos) a través de un aglutinante líquido; rodillo de baño; pulverización con impregnación forzada.
En la producción de GFM con refuerzo en forma de paquetes, hilos y telas, el método más común de impregnación es pasarlos por un aglutinante líquido (Fig. 1.26).
Arroz. 1.26. Esquema de una máquina de impregnación vertical; 1 - tambor, 2 - accesorios, 3 - baño con ligante líquido, 4 - rodillos de baño, 5 - eje de secado, 6 - calentadores, 7 - dispositivo de escape, 8 - dispositivo de tensión, 9 - tambor receptor
La barra (2) se desenrolla del tambor (fileta) (1) y, pasando por el sistema de rodillos (4), ingresa al baño (3) con ligante líquido. La armadura impregnada ingresa al eje de secado (5), donde hay calentadores (6) y un dispositivo de escape (7). Aquí, la armadura cambia de dirección varias veces para aumentar el tiempo de permanencia en la zona de alta temperatura. Como resultado, las sustancias volátiles se eliminan del compuesto y el espacio entre las fibras se llena con un aglutinante. El preimpregnado seco se enrolla con la ayuda de un eje de transmisión a través del tensor (8) n; tambor receptor.
Para GFM con armadura muy rígida (grafito boro de alto módulo u otras fibras), que no permite radios de flexión pequeños, es conveniente utilizar el método de impregnación con rodillos de baño (Fig. 1.27).
Arroz. 1.27. Esquema de impregnación con un rodillo de baño: 1 - accesorios, 2 - recipiente con aglutinante líquido, 3 - recipiente, 4 - rodillo de baño
Durante la rotación, el rodillo captura el ligante en su superficie y lo transfiere al refuerzo.
El método de rociado con impregnación forzada permite reducir drásticamente el tiempo de llenado de los espacios entre fibras con un aglutinante; Aplicar impregnación forzada hidráulica, al vacío y mecánica. .
En el proceso de impregnación forzada hidráulica, líquido ev; el bombeo se bombea a través de la válvula.
La impregnación forzada al vacío se realiza aspirando el líquido a la cámara de vacío, donde se encuentran los accesorios.
La impregnación mecánica forzada es más sencilla. Pueden ser avispas; trabaje en una cámara especial (cuña) o con la ayuda de una cara exprimible. En la cámara de cuña (Fig. 1.28), el brazo móvil se lleva el compuesto; tura en la cavidad de la cuña. Aquí, debido a una disminución en la sección transversal del canal de la cámara: la presión del fluido aumenta perpendicularmente a la armadura móvil. Es con la acción de esta presión que se llena el espacio entre las fibras.
Al impregnar con la ayuda de un rodillo exprimidor (Fig. 1.286), la presión asociada con la impregnación y la eliminación de burbujas de aire del espacio entre fibras surge en forma de una reacción del rodillo a la cinta estirada.
Arroz. 1.28. Esquemas de impregnación forzada mecánica en la cámara de cuña (a) y con la ayuda de un rodillo exprimidor (b): 1 - armadura, 2 - aglutinante, 3 - rodillos
4. Moldura.
Esta es la operación de dar al producto una forma y un tamaño determinados. El conformado se puede realizar en prensas, contacto, vacío, métodos de autoclave y bobinado.
Antes de formar en las prensas, la mecha o tejido preimpregnado se corta manualmente o en máquinas especiales en piezas de la longitud deseada. Dependiendo de la estructura PCM dada, las piezas se colocan en una o varias direcciones alternas. El paquete se coloca entre las placas de una prensa hidráulica y se compacta bajo presión de varias a decenas de atmósferas, dependiendo de la naturaleza y estructura de los componentes. Si el refuerzo está impregnado con un aglutinante de curado en caliente, las placas de prensa se calientan. Este método generalmente se usa para producir materiales laminares como la textolita.
El moldeo por contacto es el enrollado de una cinta o tela impregnada con un rodillo. Normalmente, la densificación se lleva a cabo a temperatura ambiente utilizando resinas de curado en frío. Este método se utiliza en la producción a pequeña escala de productos de gran tamaño y con poca carga.
El moldeo al vacío de productos de PCM se realiza debido a la diferencia entre las presiones atmosférica e interna (en el volumen donde se encuentra el producto). El moldeo al vacío se utiliza para la fabricación de pequeños lotes de productos, ya que el método es ineficaz y relativamente caro.
En el método de moldeo en autoclave, el producto se forma mediante una ligera presión generada por agua o gas. Este método se puede utilizar para obtener grandes series de piezas grandes de forma compleja.
Una de las formas más comunes de obtener PCM y productos de ellos es el método de bobinado. En este caso, el refuerzo impregnado con un aglutinante se enrolla en un tambor (mandril) con tensión. El bobinado permite automatizar el proceso de moldeo y programar la anisotropía de las propiedades del producto final. El devanado se usa más ampliamente para la fabricación de productos que tienen la forma de cuerpos de revolución (cilindros, esferas, conos, toroides, etc.).
5. curación.
Durante el curado del aglutinante, se crean las estructuras finales; PCM, se forman sus propiedades y se fija la forma del producto. Los principales parámetros tecnológicos de curado son la temperatura y el tiempo. Es necesario cumplir estrictamente con los parámetros desarrollados para cada combinación de ligante y refuerzo.
El curado se puede realizar a temperatura ambiente (curado en frío*), a temperaturas elevadas (curado en caliente), en hornos eléctricos o de inducción con control automático de temperatura, curado por radiación.
Durante el curado se observan dos etapas características por las que pasa sucesivamente el ligante termoendurecible: la etapa inicial, durante la formación de la red polimérica, y la etapa final, durante la formación de la red polimérica. Estas dos etapas están separadas entre sí por el llamado punto de gelificación. El punto de gelificación corresponde al momento en que el ligante pierde su capacidad de pasar a un estado fluido para disolverse en disolventes.
En un cierto rango de temperatura, el aglutinante líquido pasa i estado vítreo. Todas las propiedades del aglutinante cambian drásticamente: el volumen específico disminuye, la dureza aumenta y surge la resistencia a la deformación. La temperatura a la que se produce este fenómeno se denomina temperatura de transición vítrea. La temperatura de transición vítrea no es un punto, sino la temperatura media del intervalo. La transición vítrea no es una transición de fase; el aglutinante vítreo tiene una estructura amorfa y, desde un punto de vista termodinámico, puede considerarse como un líquido sobreenfriado.
Otro punto característico de los materiales poliméricos es la temperatura de degradación, la temperatura a la que comienza una descomposición notable del polímero, acompañada de la ruptura de los enlaces moleculares. La destrucción, como la transición vítrea, ocurre en el rango de temperatura. ¡Sostenibilidad! aglutinante a la destrucción se caracteriza por su estabilidad térmica (estabilidad térmica, estabilidad térmica). Este concepto debe distinguirse de la resistencia al calor, que refleja la capacidad del polímero para ablandarse.
Hasta el agotamiento completo de los grupos reactivos, la reacción de curado puede continuar solo si la temperatura de curado está por encima de la temperatura de transición vítrea. De lo contrario, no se puede lograr un curado completo. Los grupos reactivos aún permanecen en el polímero, pero su tasa de interacción con otros grupos es muy baja debido a la viscosidad muy alta del sistema. Si el SHSM con aglomerante curado de manera incompleta se opera a temperaturas elevadas, el curado continuará. Esto conduce a un cambio en la forma y las dimensiones del producto, la aparición de tensiones internas adicionales.
A menudo, la reacción de curado va acompañada de la liberación de calor, el material se autocalienta y el aglutinante puede endurecerse por completo. El curado en frío de los aglutinantes termoendurecibles se basa en este principio. Sin embargo, para productos críticos, en la mayoría de los casos, se utiliza el curado en caliente.
El refuerzo y el aglutinante en la composición están bajo la acción de tensiones internas, que se pueden dividir en tres tipos: estructurales, de contracción y térmicas.
Las tensiones estructurales son causadas por la tensión tecnológica del refuerzo durante el proceso de bobinado. Antes de retirarlos del mandril, las tensiones estructurales actúan solo en las fibras, están ausentes en el aglutinante.
Se producen tensiones de contracción en las fibras y el aglutinante debido a la disminución del volumen (contracción) del aglutinante durante su curado. La cantidad de contracción puede variar de 2 a 30% en volumen dependiendo de la naturaleza del compuesto.
Los esfuerzos térmicos se deben a la diferencia en los coeficientes de dilatación lineal de la armadura y del aglutinante ya la distribución desigual de temperaturas en el volumen del producto. Como regla general, el coeficiente de expansión lineal de los polímeros es significativamente mayor que el de las fibras.
En un PCM real, todas las tensiones consideradas se suman y el material está bajo la acción de las tensiones resultantes, que se relajan con el tiempo. Para promover una relajación más completa de la tensión y evitar deformaciones y grietas, se recomienda calentar y enfriar lentamente los productos PCM.
Los CFRP con fibras de bajo módulo no se utilizan como estructurales. De ellos se fabrican materiales conductores, de protección térmica y antifricción.
Los CFRP estructurales contienen fibras de carbono de alto módulo (E = 342–540 GPa) y alta resistencia (steg–2,5 GPa) como relleno. Los plásticos de carbono estructural se caracterizan por una baja densidad y un coeficiente de expansión lineal y un alto módulo de elasticidad, resistencia, resistencia al calor, conductividad térmica y eléctrica.
Las propiedades de los plásticos de carbono están determinadas por el material aglutinante, las propiedades, la concentración y la orientación de las fibras. Los CFRP basados en resinas epoxi tienen características de alta resistencia a temperaturas inferiores a 200 °C (Tabla 1.6). Estos PCM se fabrican con mayor frecuencia a partir de preimpregnados disponibles en cintas de varios anchos. La resistencia a la tracción ya la flexión de la fibra de carbono unidireccional puede ser de 1000 - 1600 MPa o más, y el módulo de elasticidad (1 - 2,5) -10 MPa o más. En términos de resistencia y rigidez específicas, los plásticos de carbono dejan muy atrás a los plásticos de vidrio, acero, aluminio y aleaciones de titanio.
Tabla 1.(
Propiedades de los CFRP epóxicos de alto módulo y alta resistencia
Indicadores |
Epoxi CFRP! |
|
altamente modular |
alta resistencia |
|
Densidad, kg / m 3 | ||
Resistencia, MPa, en compresión, tracción y flexión, cortante interlaminar | ||
Módulo de elasticidad en tensión y flexión, GPa | ||
Resistencia a la fatiga en flexión basada en 10 7 ciclos, GPa |
En los plásticos de carbono destinados a la operación a largo plazo a temperaturas de hasta 250 ° C, se utilizan los fenólicos, hasta 300 ° C - organosilicio i hasta 330°C - ligantes de poliimida. Se están desarrollando aglutinantes con temperaturas de funcionamiento de hasta 420°C. Una desventaja aún más pronunciada de los plásticos reforzados con fibra de carbono que la de los plásticos reforzados con vidrio es su baja resistencia al corte interlaminar. Esto se debe a la débil adhesión de los polímeros a las fibras de carbono. Para: aumentar la adherencia, se utilizan varios métodos: grabar la superficie de las fibras con agentes oxidantes (por ejemplo, ácido nítrico), quemar el lubricante; encolado - pre-recubrimiento de las fibras con una fina capa de un monómero humedeciéndolas; whiskering - creciente "bigote" (montón) con fibras de carbono. CFRP, en el que, además de las fibras continuas orientadas, se utilizan bigotes como relleno, ¡lo llamo! viscerizado o vorserizado.
La anisotropía de las propiedades en los plásticos de carbono es aún más pronunciada que en la fibra de vidrio. Está conectado con eso. que la relación de los módulos elásticos del relleno y el aglutinante para plásticos reforzados con fibra de carbono (100 y más) es significativamente mayor que para los plásticos de fibra de vidrio (20-30). Además, los CFRP se caracterizan por la presencia de una diferencia entre las propiedades elásticas de las propias fibras en la dirección a lo largo del eje y perpendicular a él, lo que conduce a una anisotropía adicional. Por lo general, los diseños requieren menos anisotropía mecánica. En este caso, se utilizan materiales con refuerzo cruzado. Al cambiar el contenido de volumen de las fibras y la textura de PCM, es posible cambiar las propiedades de las composiciones en un rango muy amplio.
CFRP se distingue por una alta resistencia a las cargas de fatiga. En términos del límite de resistencia por unidad de masa, los plásticos de carbono son significativamente superiores a los plásticos y metales reforzados con vidrio. Una de las razones de esto es la menor deformación (que, por ejemplo, la fibra de vidrio) al mismo nivel de tensión, lo que reduce el agrietamiento de la matriz polimérica. Además, la alta conductividad térmica de las fibras de carbono contribuye a la disipación de la energía vibratoria, lo que reduce el autocalentamiento del material debido a las fuerzas de fricción internas.
Una valiosa propiedad de la fibra de carbono es su alta capacidad de amortiguación y resistencia a las vibraciones. Según estos indicadores, los plásticos de carbono son superiores a los metales y algunos otros materiales estructurales. La capacidad de amortiguamiento se puede ajustar cambiando el ángulo entre las direcciones de refuerzo y aplicación de carga.
CFRP se utiliza para fabricar estructuras que funcionan para la estabilidad bajo la influencia de un momento de flexión externo, presión o compresión axial: palas de rotor de helicóptero, carcasas de compresor y ventilador, palas de ventilador, estator y discos de rotor de un compresor de baja presión de motores de aviones. El uso de fibra de carbono en estas unidades en lugar de metales permite reducir la masa del motor entre un 15 y un 20%. En tecnología espacial, los plásticos de carbono se utilizan para paneles solares, cilindros de alta presión y revestimientos de protección térmica.
El coeficiente de expansión lineal de los plásticos de carbono unidireccionales de alto módulo en la dirección longitudinal es cercano a cero, y en el rango de 120 - 200 ° C es incluso negativo (-0.5-10 "6 1 / ° C). Por lo tanto, el las dimensiones de los productos hechos de plásticos de carbono cambian muy poco durante el calentamiento y enfriamiento.
Los CFRP tienen una conductividad eléctrica bastante alta, lo que les permite usarse como materiales antiestáticos y de calefacción eléctrica. Con un aumento en el contenido de hidrocarburos en PCM a una cierta fracción de volumen (40–70%), según el tipo de polímeros e hidrocarburos, se observa la forma textil de los hidrocarburos, un aumento en la resistencia y el módulo de elasticidad. Luego, estos indicadores comienzan a deteriorarse debido a la cantidad insuficiente de polímero necesaria para obtener un compuesto monolítico y destruir los hidrocarburos frágiles en la etapa de formación con un alto grado de compactación. El contenido máximo de HC en PCM también está limitado por la mala humectabilidad del aglutinante HC.
En algunos casos, el uso de solo fibras de carbono como relleno no proporciona la viscosidad necesaria, la resistencia a la erosión, la resistencia a la compresión, a la tracción y al corte. Luego, los aglutinantes se refuerzan conjuntamente con fibras de carbono y vidrio o de carbono y boro. ¡El refuerzo combinado le permite ampliar la gama! valores de resistencia, rigidez y densidad de PCM.
La resistencia química de los plásticos de fibra de carbono hace posible su uso en la producción de bombas y sellos resistentes a los ácidos. Las fibras de carbono tienen un bajo coeficiente de fricción, lo que permite su uso como relleno para varios aglutinantes, a partir de los cuales se fabrican cojinetes de juntas, bujes y engranajes.
El desarrollo de la tecnología requiere materiales mecánicamente fuertes y resistentes al calor. Esto despertó un interés particular en los materiales compuestos de carbono-carbono (CCCM) que contienen carbono tanto en forma de relleno de refuerzo como en forma de material de matriz.
En CCCM, la resistencia a altas temperaturas se combina con baja densidad, alta resistencia y módulo de elasticidad, resistencia al calor; soplar. Estos materiales son duraderos durante mucho tiempo a temperaturas de hasta 500°C (en un ambiente oxidante y hasta 3000°C en una atmósfera inerte y en vacío).
El relleno y la matriz de CCCM, dependiendo de la composición y condiciones de carbonización, pueden tener diferentes modificaciones. En la clasificación aceptada, primero se indica la estructura del relleno de carbono, luego la matriz, por ejemplo, material de carbono-carbono, grafito-carbono, grafito-grafito.
En CCCM, el relleno de carbono está contenido en forma de fibras discretas, hilos continuos o estopas, fieltros, cintas, telas con tejido plano i volumétrico, estructuras volumétricas. Las fibras están dispuestas al azar en una, dos y tres direcciones. Se utilizan hidrocarburos de bajo módulo, alto módulo y alta resistencia, obtenidos a partir de viscosa, fibras de poliacrilonitrilo y brea de alquitrán de hulla.
El carbón pirolítico se puede utilizar como matriz, así como la brea de alquitrán de hulla y los polímeros de coque, que dan más del 50 % en peso de coque en el proceso de destrucción térmica. Muy a menudo, se utilizan resinas fenólicas (rendimiento de coque 54–60 % en peso). Es conocido el uso de poliimido (63 - 74 % en peso), resinas de organosilicio (84 - 87 % en peso), productos de condensación de fenol y naftenos con formaldehído (70 % en peso), soles de oligobencimid (74 % en peso). , resinas de furfurilo y otros, polímeros. Cuanto más se mueva y, la fuerza del coque, así como la fuerza de su adhesión al relleno, tci, mayor será la calidad del CCCM.
, .„.„ Para obtener un compuesto con las propiedades deseadas, es necesario determinar la combinación más favorable de relleno y matriz, así como el régimen tecnológico más favorable para obtener una matriz de yraepoj.
Dependiendo del estado de fase de las sustancias que contienen carbono, se distinguen los siguientes métodos de densificación de rellenos de fibra de carbono (CFF) con carbono:
utilizar hidrocarburos en fase gaseosa o vapor (gas natural, propano-butano, benceno, etc.);
utilizar hidrocarburos líquidos caracterizados por un alto contenido de carbono y un alto porcentaje de rendimiento de coque (brea, alquitrán);
combinado, que incluye la impregnación de estructuras porosas con hidrocarburos líquidos y la carbonización, luego la compactación con carbón pirolítico obtenido por pirólisis de hidrocarburos en fase gaseosa.
El proceso de sellado del marco se puede realizar de varias formas.
El método isotérmico proporciona el paso de un gas que contiene carbono sobre la superficie de un marco calentado a una presión relativamente moderada. La desventaja es la duración del proceso, la formación de una costra superficial que impide la penetración de gas en el marco. Este método es más efectivo para productos de pequeño espesor.
En otro método, se establece una diferencia de presión a lo largo de todo el espesor del marco, y el gas que contiene carbón se filtra a la fuerza a través de él. La filtración forzada acelera el proceso de compactación y aumenta considerablemente el espesor de la impregnación. Sin embargo, debido a la disminución de la concentración de gas que contiene carbono sobre el espesor de la capa, la estructura del material resulta ser desigualmente densa.
El más extendido es el método de termogradiente, cuando se establece una cierta diferencia de temperatura en todo el espesor del marco poroso y el gas que contiene carbono pasa desde el lado de la superficie con una temperatura baja. En este caso, se excluye la formación de una costra superficial, lo que contribuye a la producción de material de alta calidad. Este método es más efectivo cuando se compactan estructuras de mediano y gran espesor.
Durante la descomposición térmica de los hidrocarburos en fase gaseosa, se producen simultáneamente varios procesos químicos, que dan como resultado hidrocarburos más ligeros y más pesados, hidrógeno y varios productos sólidos de carbono. La estructura y las propiedades de los productos de carbono son diversas y dependen de las condiciones del proceso. Por ejemplo, los productos de descomposición térmica, dependiendo de la forma geométrica externa, contienen:
carbón en capas o brillante, llamado pirocarbono (PU);
Carbono fibroso o filamentoso; carbón en estado disperso u hollín.
La formación de PU tiene lugar en un amplio rango de temperatura de 700 a 3000°C. La composición de los gases iniciales determina el rendimiento de PU y la velocidad de su deposición. El mayor rendimiento de PU se obtiene del metano, que tiene el peso molecular más bajo. Los hidrocarburos con un alto peso molecular tienen un mayor rendimiento de hollín. En este caso, la presión del gas en el reactor es fundamental.
Existen dos tipos principales de PU, cuya estructura y propiedades están determinadas por la temperatura de formación: baja temperatura (1000 - 1100°C) y alta temperatura (1400 - 2200°C), denominadas pirografito.
El proceso de deposición de PU en fase gaseosa se lleva a cabo en una instalación (Fig. 1.29), que consta de un reactor refrigerado por agua, una estación de control para los sistemas de suministro de gas natural, creando un equipo de vacío, refrigeración y energía. La pieza de trabajo - estructura de carbono (4) está montada sobre calentadores de grafito (3) intercalados entre conductores de corriente (2). Después de la evacuación de la cámara, se alimenta gas natural al reactor. El calentamiento se realiza mediante corriente continua que pasa a través del calentador (3), control de temperatura - ¡mediante termopares móviles de cromo-alumel (5) colocados en cubiertas de cuarzo Al comienzo del proceso, el termopar se instala con una unión en el calentador superficie - centro de la pieza de trabajo a la periferia.
En el caso de la deposición de PU en fase gaseosa, uno de los criterios de calidad del material obtenido es su densidad. Es una función de muchos parámetros y depende de la densidad del marco, la velocidad del frente de pirólisis, la concentración del reactivo y la presión del gas en el reactor.
La formación de carbón pirolítico a partir de la fase gaseosa en UHV se lleva a cabo principalmente a temperaturas de 1100 a 1500 °C y presión reducida en una atmósfera que contiene 91 a 93 % de metano y 7 a 9 % de argón. La grafitización se lleva a cabo en atmósfera inerte.
El proceso tecnológico de obtención de CCCM por el método de fase líquida!* incluye la fabricación de una estructura porosa, su impregnación con hidrocarburos líquidos, carbonización bajo presión y grafitización. Al elegir un material de impregnación para la impregnación, se tienen en cuenta las siguientes características:
viscosidad;
coque de escape;
microestructura de coque;
La estructura cristalina del coque.
Todas estas características dependen de la presión y temperatura en el proceso* de compuestos carbono-carbono. Las resinas fenólicas, de poliamida, polivinilsiloxano, polifenilsiloxano, furfurilo y epoxi novolaca se utilizan con mayor frecuencia como resinas. Una dirección progresiva y prometedora es el uso de breas de petróleo y carbón como material de impregnación. Estos aglutinantes tienen las siguientes ventajas: bajo costo, alto contenido de carbono mientras conservan la termoplasticidad y la capacidad de grafitización de las breas de mesofase preparadas. Las desventajas incluyen: toxicidad, inconstancia de calidad.
W
Arroz. 1.29. Esquema de instalación del método de termogradiente de deposición de pirocarbono en fase gaseosa: 1 - reactor refrigerado por agua, 2 - cables de corriente, 3 - calentador, 4 - marco de carbono, 5 - termopar en un tubo de cuarzo, 6 - mecanismo de movimiento del termopar , 7 - camisa de agua; corrientes: I - gas, II - productos gaseosos de pirólisis, W - agua.
La composición química y las propiedades de las breas varían mucho según la naturaleza de la materia prima y las condiciones tecnológicas. Bajo ciertas condiciones, una fase de cristal líquido (mesofase) puede nuclearse y crecer en breas, lo que asegura la formación de coque grafitante anisotrópico. En este sentido, las breas se distinguen actualmente en isotrópicas (ordinarias, no mesofásicas) y anisotrópicas (mesofásicas).
Durante la carbonización a baja temperatura (550 - 650°C), la mesofase pasa a semicoque sólido. Este proceso va acompañado de un hinchamiento bajo la influencia de los gases desprendidos, lo que conduce a la formación de una estructura de coque finamente porosa. Durante el hinchamiento, se produce una profunda deformación del coque y un aumento del número de estructuras defectuosas, lo que, durante el tratamiento térmico posterior, conduce a la aparición de grietas por contracción.
La formación de la estructura y las propiedades de la matriz de coque de carbono depende de las condiciones del tratamiento térmico, que se pueden dividir condicionalmente en varias etapas:
Carbonización (900 - 1423°C) - descomposición de compuestos orgánicos
y formación de la estructura molecular ordenada de carbón-coque
precristalización (1400 - 2000°C) - ordenamiento de átomos yi
lerod en una estructura más perfecta con la formación de los llamados<
formas básicas de carbono;
grafitización homogénea (2000 - 3000°C) - transformación de transición; ny formas de carbono en grafito cristalino.
En la fig. 1.30 muestra un esquema de una instalación para impregnar tejidos de carbono.
Arroz. 1.30. Esquema de la instalación para impregnación de tejido de carbono: 1 - bobina consumible, 2 - tejido de carbono, 3 - rodillos de presión, 4 - horno eléctrico, 5 - dispositivo que regula la velocidad de alimentación del tejido, 6 - bobina receptora; 7 - accionamiento eléctrico, 8 - baño
La tela se desenrolla del carrete de suministro (1) y pasa a través de su (8), en el que tres agitadores de alta velocidad mezclan intensamente el polvo de brea con agua, creando una suspensión estable de agua-brea. IIj ulterior paso de la tela a través de los rodillos de presión (3) y el electrón 1 (4), el agua se evapora y la brea, "derretiéndose, impregna la tela. El preimpregnado resultante con la ayuda de un accionamiento eléctrico (7) y una tela El dispositivo de control de la velocidad de alimentación (5) se enrolla en un carrete de recogida (6).¡A la salida del horno, la cinta se presiona mediante un eje calentado a 100 - 120 ° C y se exprime! paso en el volumen de la tela.
La preimpregnación del cuadro de carbono poroso con brea se puede realizar a una presión de 0,5 a 3 MPa, la carbonización a una presión de 100 a 200 MPa y una temperatura de 900 a 1100 °C.
Una característica de CCCM es la porosidad relativamente alta de la matriz de carbono, así como su intersección con grietas en la dirección perpendicular al relleno. Las grietas en la matriz se producen cuando el producto se enfría desde la temperatura de producción (3000 °C) hasta la temperatura ambiente debido a las altas tensiones térmicas. Para eliminar la porosidad, la operación de impregnación-carbonización seguida de grafitización y la operación de impregnación con pirocarbono se repiten varias veces (Fig. 1.31).
Después de repetidas repeticiones del ciclo de impregnación-carbonización, la densidad del material puede alcanzar 2000 - 2100 kg/m 3 . Si la temperatura de procesamiento no supera los 800 - 1500°C, se produce la carbonización del aglomerante ya temperaturas de 2300 - 3000°C se obtiene un material grafitado. La carbonización de la fibra de carbono se lleva a cabo en una corriente de gas inerte o una atmósfera reductora con presión aumentada con isotérmica, dinámica o "calentamiento escalonado"; grafitización - en una atmósfera inerte.
fibras de carbono
Bobinado de bobina 3 \ ^Producción
productos de tejer a granel \ telas
estructuras \
firmware
Impregnación de brea
* Carbonatación
Re-impregnación Re-carbonatación
Grafitización Fig. 1.31. Esquema para obtener CCCM utilizando el método de impregnación.
Se puede implementar un método combinado o complejo para obtener CCCM de acuerdo con los siguientes esquemas:
Impregnación de brea del marco poroso, carbonización bajo presión, compactación adicional de PU de la fase gaseosa;
Compactación del marco de PU desde la fase gaseosa hasta una determinada densidad, impregnación con brea seguida de carbonización, procesamiento mecánico, densificación de PU.
Este método proporciona máxima densidad, altas características físicas y mecánicas y no requiere equipo adicional.
En los casos en que la carbonización de CCCM se realice sin presión
El proceso se puede realizar en torrefacción convencional (cámara de gas)
tazas, cuyo diseño se consideró anteriormente. Producción tecnológica]
CCCM por método de fase líquida en términos de carbonización bajo presión puede<
realizarse mediante prensas.
La grafitización (grafitización) se lleva a cabo en hornos Acheson, cuyo diseño se discutió en capítulos anteriores.
Las propiedades de CCCM varían en un amplio rango. La fuerza del CCCM carbonizado es proporcional a la densidad. Grafitización de carbonizados: nogo CCCM aumenta su resistencia. La fuerza de CCCM basada en CF alto: fuerte es más alta que la fuerza de CM basada en CF de alto módulo, ¡más! nyh a diferentes temperaturas de procesamiento. Las propiedades únicas de CCCM incluyen resistencia a altas temperaturas en medios inertes y reductores. En cuanto a su capacidad para conservar su forma y sus propiedades físicas y mecánicas en estos medios, CCCM supera a los materiales estructurales conocidos. Algunos CCCM, especialmente los obtenidos por carbonización de fibra de carbono a base de polímeros orgánicos, se caracterizan por un aumento de la resistencia con un aumento de la temperatura de funcionamiento de 20 a 2700°C. A temperaturas superiores a 3000°C, los CCCM están operativos por un corto tiempo, ya que comienza la intensa sublimación del grafito. Cuanto más perfecta sea la estructura cristalina del grafito, mayor será la temperatura y menor la tasa de procesos termodestructivos. Propiedades] Cambio de CCCM en el aire con exposición prolongada a temperaturas relativamente bajas. Entonces, ¡a 400 - 650 ° C en el aire se produce! oxidación de CCCM y, como resultado, una rápida disminución de la fuerza como resultado. esos aumentos en la porosidad. La oxidación de la matriz está por delante de la oxidación de HC, e< ли последние имеют более совершенную структуру углерода. Скорость оки>CCCM disminuye con un aumento en la temperatura de su producción y una disminución en el número de defectos. Previene eficazmente la oxidación de CCCM pr< питка их кремнийорганическими соединениями из-за образования карбида оксида кремния.
En la fig. 1.32 se presentan las áreas de aplicación de CCCM.
resistente a las raciones
Arroz. 3.32. Áreas de aplicación de CCCM en condiciones de altas cargas térmicas
Por lo tanto, los CCCM se utilizan en diversas ramas de la tecnología en los casos en que los materiales tradicionales son inoperables, es decir. en condiciones de altas cargas térmicas y en unidades de fricción.
T tecnología compuesta resuelve el problema de obtención de materiales endurecidos. La palabra tecnología proviene de dos palabras griegas: techne - artesanía y logos - palabra, enseñanza. Usualmente en nombres de este tipo, la segunda parte "logía" corresponde al concepto de "ciencia". Por ejemplo, la zoología es la ciencia de los animales, la geología es la ciencia de la estructura de la Tierra. Por analogía, la tecnología debería definirse como la ciencia de la artesanía.
Tecnología compuesta - Sección de tecnología de materiales
Pero la palabra "ciencia" junto a la palabra "tecnología" apareció hace relativamente poco tiempo. La tecnología suele definirse como un conjunto de métodos. si se trata de tecnología de materiales, entonces este es un conjunto de métodos para obtener y procesar materiales.
La tecnología compuesta es una tarea para un especialista.
Toma por ejemplo especialista en tecnología de compuestos. ¿Qué tareas tiene que resolver? Aqui esta uno de ellos. Daneses: fibras de boro enrolladas en bobinas; El aluminio (en cualquier forma: láminas, alambre, polvo, fundido) se puede elegir a su discreción. Requerido: conectar las fibras y la matriz de aluminio entre sí, mientras se obtiene un boro-aluminio de alta resistencia. El tecnólogo debe decidir cómo hacerlo. Para ser más específicos, analicemos cómo obtener un compuesto de este tipo en forma de lámina, en la que todas las fibras se distribuyen uniformemente sobre la sección transversal y se apilan paralelas entre sí. Para resolver el problema hay que responder tres preguntas básicas:- ¿Cómo garantizar el tendido de fibras en una dirección determinada?
- ¿Cómo introducir fibras en una matriz para obtener una lámina con la estructura y propiedades requeridas?
- ¿Cómo evitar el ablandamiento y la destrucción de las fibras en el proceso de fabricación del material y, al mismo tiempo, garantizar su fuerte unión con la matriz?
Cómo orientar las fibras en un composite
Comencemos en orden. Cómo orientar las fibras en un composite? Si fueran lo suficientemente gruesas, como las barras de acero con las que están reforzadas, no habría especiales problemas. Puedes poner uno a la vez en nidos especialmente preparados.
Cómo insertar fibras en una matriz
Pero es mejor hacerlo de otra manera. Utilice el propio material de la matriz como sujetador. Luego puede realizar dos tareas a la vez para mantener adecuadamente la tecnología compuesta: arreglar fibras en la posición deseada y al mismo tiempo ingresarlos en la matriz, es decir, dar respuesta a la segunda pregunta principal de nuestra tarea. El pensamiento es bueno. Pero de nuevo, surge el mismo obsesivo - ¿cómo? ¿Cómo hacerlo? No se puede prescindir del conocimiento de la física y la química.método electroquímico
Puede ser usado método electroquímico, aplicando un recubrimiento galvánico de matriz metálica al tambor con fibras enrolladas en él. No es muy difícil en principio, pero:- toma mucho tiempo
- no todos los metales se pueden aplicar de esta manera,
- es difícil proporcionar la composición deseada de la matriz cuando se trata de aleaciones complejas.
Proyección de plasma de recubrimientos
Y aquí está la opción más adecuada. Usar pulverización de plasma de recubrimientos. Con este método, el material de la matriz se funde mediante una corriente de plasma a baja temperatura (gas ionizado con una temperatura promedio de unos 10.000 K), con la misma corriente se rocía y se transfiere a la superficie del tambor, cubriendo las fibras y llenando los espacios entre ellos. El flujo de plasma se obtiene mediante un dispositivo especial: una antorcha de plasma, en la que el gas de trabajo (nitrógeno, argón, hidrógeno, helio, etc.) se ioniza bajo la acción de una descarga de arco. Aunque el plasma formado en los plasmatrones convencionales se denomina de baja temperatura, esta temperatura “baja” (10.000 K) es suficiente para fundir cualquiera de los materiales que existen en la naturaleza. Las gotas de metal fundido alcanzan el tambor frío y, dándole calor, cristalizan, formando una capa uniforme en el tambor, si se gira uniformemente. El material a pulverizar (en nuestro caso, aluminio) se suele introducir en el chorro de plasma en forma de polvo o alambre. Externamente, el proceso de aplicación de recubrimientos de plasma se asemeja a la pintura con aerógrafo. Solo en lugar de un aerógrafo, una antorcha de plasma y, en lugar de pintura, una aleación de matriz. En principio, no es necesario usar plasma para este propósito, puede arreglárselas con un quemador de gas u otro dispositivo, pero la pulverización de plasma es muy conveniente y se usa ampliamente en la creación de compuestos. La monocapa reforzada obtenida tras la proyección se corta a lo largo de una de las generatrices del cilindro y se despliega en un plano. La resistencia del revestimiento es suficiente para evitar que las fibras se muevan entre sí, pero no lo suficiente para garantizar una alta resistencia del material compuesto. El espesor de las monocapas resultantes suele ser de uno y medio a dos diámetros de fibra, es decir, unas 200 micras, y nosotros, recordemos, necesitamos una lámina de 5 mm de espesor. ¿Cómo ser? De nuevo "¿cómo?".Laminado de monocapas
Esta vez, no tiene que buscar la respuesta durante mucho tiempo: debe hacer un pastel de hojaldre a partir de las monocapas obtenidas, es decir, recogerlas en una bolsa del grosor requerido y compactarlas de alguna manera, conectándolas inseparablemente. juntos. Esto se puede hacer, por ejemplo, monocapas rodantes o prensado en caliente. En el primer caso, el paquete se calienta en un horno y se pasa entre rodillos giratorios. Durante el laminado, las monocapas se combinan en un material monolítico y el material de la matriz se compacta en cada monocapa, lo que conduce a un aumento de la resistencia de la matriz y de su unión con las fibras.Prensado en caliente de monocapas
A veces es más conveniente compactar paquetes de monocapas no por laminación, sino por prensado en caliente. Para ello, se colocan en un molde cuya longitud y anchura del plano de trabajo corresponde a las dimensiones de las monocapas, y se prensan desde arriba con un punzón. El molde se calienta para que se pueda mantener la temperatura de proceso requerida. El paquete calentado se compacta, de ahí el nombre: prensado en caliente. Para que se forme una unión fuerte entre las monocapas y para que todas las partículas de la matriz metálica depositada se suelden entre sí, formando un monolito, es necesario mantenerlas bajo presión, permitiendo así que los procesos de difusión hagan su trabajo. Son estos procesos, junto con la presión, los que aportan las altas propiedades mecánicas de nuestro hojaldre. Es por eso que este método de obtención de materiales compuestos a veces se denomina soldadura por difusión.Tecnología de composites en forma de barra o perfil complejo
Con respecto a la tarea que nos ocupa, hemos respondido a la segunda pregunta: cómo introducir fibras en la matriz. Pero, ¿qué sucede si necesita obtener un compuesto en forma de barra o un perfil complejo? Otro "cómo". Puede volver a recurrir a paquetes rodantes de monocapas, pero no en rollos lisos, sino calibrados, es decir, que tengan cortes especiales que correspondan a la configuración requerida. O puede usar el llamado métodos de fase líquida cuando la matriz se encuentra en estado líquido en proceso de obtención de un composite. Las fibras, al desenrollarse de las bobinas (el número de bobinas es igual al número de fibras en el compuesto), pasan sin tocarse a través de un baño con matriz metálica fundida, se humedecen y entran en la hilera, que forma una varilla. de la sección deseada. Después de eso, la varilla se enfría, la matriz metálica se endurece y forma un material compuesto con las fibras. De esta forma se pueden obtener barras de una gran variedad de perfiles. Los productos de perfil complejo, como los álabes de las turbinas, se obtienen convenientemente por impregnación. Las fibras se colocan en el molde, cuya cavidad de trabajo corresponde a la forma de la cuchilla (cómo hacer esto es un tema aparte que no consideraremos ahora, pero esto se puede hacer, aunque no fácilmente), y luego el líquido la matriz de metal se vierte en el molde. Los espacios entre las fibras suelen ser pequeños y es difícil que el metal fundido los llene, pero es necesario llenarlos lo más rápido posible para que las fibras no tengan tiempo de disolverse en la matriz. Por tanto, en la mayoría de los casos, la impregnación se realiza bajo presión. El molde de fundición se vacía y el metal líquido entra bajo presión atmosférica. Por regla general, una diferencia de presión de una atmósfera es suficiente para una impregnación rápida y fiable. Pero esto es sólo en el caso de que las fibras estén humedecidas por el metal de matriz fundido. Si no es así, entonces debes tomar medidas. Por ejemplo, las fibras de carbono no se humedecen con aluminio líquido, por lo que no se puede obtener carbono-aluminio simplemente impregnando filamentos de grafito con aluminio. Pero si estos hilos se recubren previamente con la capa más fina de cromo o níquel (basta con aplicar un recubrimiento de un micrómetro de espesor), que están bien humedecidos con aluminio, se asegurará la impregnación y se podrá obtener un compuesto. La principal ocupación del tecnólogo es responder a la pregunta "¿cómo?". ¿Cómo hacer? Las respuestas correctas a esta pregunta se pueden dar si se conocen las respuestas a la pregunta "¿por qué?". Si imagina un mecánico de automóviles que sabe apretar pernos y tuercas, pero no conoce la estructura del automóvil. Sin valor para él. Del mismo modo, un tecnólogo que no entiende la física de los procesos que ocurren al obtener un material es un especialista inferior. Por ejemplo, el tecnólogo sabe que en muchos casos el compuesto se ablanda después del calentamiento. El problema surge de inmediato: ¿cómo lidiar con él? Esta pregunta es similar a la tercera pregunta "¿cómo?" al comienzo de la conversación. Y para resolver este problema, debe saber por qué se produce el ablandamiento del compuesto. La respuesta a estas preguntas la proporciona la tecnología compuesta.complejo robótico para el procesamiento mecánico de productos hechos de materiales compuestos está diseñado para la mecanización y automatización de una de las operaciones más intensivas en mano de obra en el ciclo tecnológico:
- Recorte y eliminación de flash tecnológico.
- Fresado de ranuras, rebajes y posicionadores para elementos empotrados
- Taladrado y fresado a través de agujeros de forma compleja
- Fresado de orificios de gran tamaño (aberturas de ventanas, escotillas, etc.)
complejo robótico le permite brindar las siguientes ventajas:
- Mayor velocidad de procesamiento en comparación con el procesamiento manual
- Alta repetibilidad y calidad de procesamiento
- Fresado con alta calidad de filo “en una sola pasada”
- Mejora de las condiciones de trabajo
- Creación de puestos de trabajo intensivos en conocimientos adicionales
En metodo de contacto Después del moldeado, el material de vidrio se impregna manualmente con resina utilizando una brocha o un rodillo. La impregnación se puede realizar simultáneamente con el enrollado en forma, o por separado. El laminado se lleva a cabo para eliminar el aire del laminado y distribuir uniformemente el aglutinante.
1El artículo presenta el estado actual de las tecnologías para la producción de productos a partir de materiales compuestos, incluyendo información sobre las tecnologías utilizadas, software, equipos para crear matrices, equipos para crear productos compuestos, equipos para controlar la geometría de un producto y ensayos no destructivos. .
materiales compuestos
software
equipo de fabricación de matrices
1. Materiales compuestos modernos / ed. P. Krok y L. Brouman; por. De inglés. - M., 1978.
2. El diseño y resistencia de los cascos de las naves y barcos fabricados en fibra de vidrio. Construcción naval extranjera en 1965 - 1973 // Construcción naval, 1973.
3. Frolov S. E. Métodos para crear nuevos materiales compuestos macro-no homogéneos y soluciones tecnológicas para la fabricación de estructuras de casco a partir de ellos // Construcción naval No. 3 2003, p. 55-59.
4. CAE - tecnologías en 2012: revisión de logros y análisis de mercado. – CAD/CAM/CAE Observer #4 (80) / 2013.
5. Entrevista con V.A. Seredka y A.Yu. Sofronov a CAD/CAM/CAE Observer #2 (78) / 2013.
6. Tecnologías inteligentes para la industria aeronáutica. Aumento de la competitividad de las empresas nacionales de fabricación de aviones en el ejemplo de proyectos conjuntos de la empresa Solver y JSC VASO // CAD y gráficos, No. 1. 2011. P. 56-62.
7. Parque Nacional Lukyanov Experiencia en el uso de materiales compuestos para la construcción de buques PMO // Construcción naval. Nº 3. 2007. S. 19-26.
Un material compuesto es un material cuya estructura consta de varios componentes que difieren en sus propiedades físicas y mecánicas: matrices metálicas o no metálicas con una determinada distribución de endurecedores en ellas, su combinación confiere al material compuesto nuevas propiedades. De acuerdo con la naturaleza de la estructura, los materiales compuestos se dividen en fibrosos, reforzados con fibras continuas y bigotes, materiales reforzados por dispersión obtenidos mediante la introducción de partículas dispersas de endurecedores en la matriz, materiales en capas creados por prensado o laminado de materiales diferentes.
Hoy en día, los materiales compuestos tienen una demanda especial en varias industrias. Los primeros barcos de fibra de vidrio se fabricaron en la segunda mitad de la década de 1930. Desde la década de los 50 la construcción naval en fibra de vidrio se ha generalizado en el mundo, habiéndose construido un número importante de yates, embarcaciones de trabajo y salvamento y barcos de pesca, lanchas de desembarco, etc. Una de las primeras aplicaciones en aviación de los materiales compuestos fue la fabricación de paneles de fibra de carbono en 1967 para el borde de fuga del ala del avión F-111A. En los últimos años, en los productos aeroespaciales, es cada vez más posible encontrar estructuras hechas de un “sándwich” de tres capas con relleno de nido de abeja de aluminio y pieles de fibra de carbono. Actualmente, alrededor del 50% de la masa total de un Boeing 787 o un Airbus A350 está compuesta por materiales compuestos. En la industria automotriz, los materiales compuestos se han utilizado durante mucho tiempo, principalmente se ha desarrollado la tecnología para la fabricación de un kit de carrocería aerodinámica. Los materiales compuestos se utilizan de forma limitada para la fabricación de piezas de suspensión y motor.
Sin embargo, hasta hace poco, las empresas utilizaban principalmente el trazado manual de piezas de compuestos, y la producción en serie de productos manufacturados no requería una automatización profunda de los procesos. Hoy en día, con el desarrollo de la competencia en el mercado, no se puede prescindir de las modernas herramientas de diseño y preparación de la producción, así como de los equipos efectivos para trabajar con composites.
Tecnologías para crear productos a partir de materiales compuestos.
En la mayoría de los casos, se utiliza una resina termoendurecible de curado químico como relleno aglutinante, el proceso de curado se caracteriza por una reacción química exotérmica. Se utilizan principalmente resinas de poliéster, epoxi, fenólicas y de alta temperatura. En la mayoría de los casos, en la fabricación de piezas de configuración compleja, se utilizan tecnologías cuya esencia es colocar una base "seca" seguida de una impregnación con un aglutinante (moldeo "húmedo", bobinado, inyección, Moldeo por transferencia de resina / RTM) o alternativamente colocar una base “seca” con cola de film (impregnación al vacío, Resin Film Infusion / RFI). Existen varias tecnologías principales para la fabricación de piezas a partir de materiales compuestos, incluidos métodos manuales y automatizados:
- impregnación de fibras de refuerzo con material matriz;
- formación en molde de las cintas del endurecedor y de la matriz obtenida por bobinado;
- prensado en frío de componentes seguido de sinterización;
- recubrimiento electroquímico de fibras con posterior prensado;
- deposición de la matriz por proyección de plasma sobre el endurecedor, seguido de compresión;
- soldadura por difusión por lotes de cintas monocapa de componentes;
- laminación conjunta de elementos de refuerzo con una matriz, etc.
Además, se ha generalizado la tecnología de fabricación de piezas mediante preimpregnados (productos semiacabados, que son el material base impregnado con una composición aglomerante).
Software
La tarea de diseñar un producto a partir de materiales compuestos es la correcta selección de una composición que proporcione una combinación de propiedades requeridas en un caso operativo particular. Al diseñar materiales compuestos de polímeros reforzados, se usa ampliamente el procesamiento de datos por computadora, para lo cual se han desarrollado una gran cantidad de productos de software. Su uso permite mejorar la calidad de los productos, reducir la duración del desarrollo y la organización de la producción de estructuras, resolviendo de manera integral, eficiente y rápida los problemas de su diseño racional. Tener en cuenta las cargas desiguales permite diseñar una estructura de casco hecha de un compuesto reforzado con un espesor diferenciado, que puede variar decenas de veces.
Los productos de software modernos se pueden dividir en dos grupos: los que realizan análisis por lotes de laminados en una formulación "bidimensional" o "viga/placa" y en una tridimensional. El primer grupo son programas como Laminator, VerctorLam Cirrus, etc. La solución "tridimensional" es el método de elementos finitos, y hay una gran selección entre los productos de software disponibles. Hay varios productos de software en el mercado de "tecnología de modelado compuesto": FiberSim (Vistagy / Siemens PLM Software), Digimat (e-Xstream / MSC Software Corp.), Helius (Firehole Composites / Autodesk), ANSYS Composite PrepPost, ESAComp (Altair Ingeniería) y etc.
Casi todo el software especializado de varias empresas tiene la capacidad de integrarse con sistemas CAD de alto nivel: Creo Elements / Pro, Siemens NX, CATIA. En general, el trabajo es el siguiente: se selecciona el material de la capa, se determinan los parámetros generales del paquete de capas, se determina el método de formación de capas, se utiliza el método capa por capa para producir piezas simples, para productos complejos, se utilizan métodos de diseño estructural o zonal. En el proceso de disposición de las capas, se establece su secuencia. Dependiendo del método de producción del producto (replanteo manual, moldeo, replanteo de la cinta, replanteo de la fibra), se realiza un análisis capa por capa del material para detectar posibles deformaciones. La composición de las capas se ajusta al ancho del material utilizado.
Una vez que se completa la formación de capas, el usuario recibe datos sobre el producto, lo que permite utilizarlos para diversos fines, por ejemplo:
- salida en forma de documentación de diseño;
- utilizar como dato inicial para corte de material;
- datos iniciales para un proyector láser para marcar los contornos de los lugares para patrones de colocación.
La transición a tecnologías modernas para diseñar y preparar la producción de productos permite:
- reducir el consumo de materiales compuestos mediante el uso de escariadores y cortadoras de precisión;
- aumentar la velocidad y mejorar la calidad del trazado manual del material mediante el uso de espacios en blanco precisos y proyecciones láser de sus lugares de trazado;
- lograr un alto nivel de repetibilidad del producto;
- reducir la influencia del factor humano en la calidad de los productos fabricados;
- reducción de requisitos a la calificación del personal ocupado con la colocación.
Equipo de fabricación de matrices
Hacer un modelo maestro de madera es un proceso que requiere mucho tiempo y tiempo, para reducir el tiempo de fabricación de la matriz y aumentar la precisión, se utilizan fresadoras CNC de tres / cinco ejes, máquinas de control y medición o escáneres 3D.
La fresadora de pórtico de cinco ejes, (Fig. 1), está disponible solo para grandes fabricantes. Las pequeñas empresas utilizan complejos robóticos de fresado en bloques lineales (unidad de robot lineal) (Fig. 2), o hacen modelos maestros a partir de una pieza de trabajo encolada. En este caso, se toma un marco hueco rígido como base de la pieza de trabajo, que se pega en el exterior y luego se procesa por completo. Las empresas que no tienen la capacidad de procesar todo el producto siguen un camino diferente: primero, se construye un modelo 3D simplificado del producto usando planos en un sistema CAD, y se diseña un marco rígido de madera contrachapada basado en el modelo simplificado. A continuación, toda la superficie exterior se representa en el sistema CAD como el revestimiento del marco interior. Las dimensiones del revestimiento se seleccionan de tal manera que se puedan fresar en una fresadora CNC existente (Fig. 3). Luego, el marco ensamblado con precisión se pega con el revestimiento del modelo. Con este método, la precisión del modelo maestro es menor y se requiere el acabado manual de las juntas del revestimiento, pero esto le permite crear productos cuyas dimensiones superan significativamente las capacidades de las máquinas CNC existentes.
Arroz. 1. Fresadora de cinco ejes MR 125, capaz de procesar piezas con un tamaño de 15x5 m y una altura de hasta 2,5 m
Arroz. 2. Complejo robotizado de fresado Kuka
Arroz. 3. Fresadora de cinco ejes "pequeña"
Equipos para crear composites.
El primer paso en la mecanización del proceso de moldeo fue el uso de máquinas de impregnación que, además de la impregnación, ensamblan tejidos de vidrio o fibra de vidrio en bolsas multicapa con un espesor total de 4 a 5 mm. Para mecanizar procesos, reducir la probabilidad de error del personal y aumentar la productividad, por ejemplo, se utiliza el método de aspersión, que se puede utilizar para obtener revestimiento exterior, paneles de mampara y otras estructuras de fibra de vidrio. El método de proyección permite obtener escuadras de moldeo mecanizadas y proporciona una mayor productividad de mano de obra en comparación con las escuadras de moldeo moldeadas manualmente a partir de tiras de fibra de vidrio o fibra de vidrio. La siguiente etapa en el desarrollo de la producción de productos a partir de materiales compuestos es la introducción de una instalación para el bobinado automático del trazado de rellenos de fibra de carbono. La compañía estadounidense Magnum Venus Plastech demostró el primer "robot" diseñado para colocar tela seca tipo rollo. Por primera vez en Rusia, dicho equipo se presentó en JSC VASO. Este equipo permite producir piezas compuestas de hasta 8 m de largo y hasta 3 m de diámetro (Fig. 4).
Para facilitar la disposición manual de la tela y reducir el desperdicio, se utilizan máquinas de corte para el corte automático de tela/preimpregnado, proyectores láser LAP y LPT para la proyección de contornos cuando se coloca preimpregnado en el equipo de producción. Usando el módulo de proyección láser (Fig. 5), es posible generar automáticamente datos para la proyección directamente desde un modelo 3D de un producto compuesto. Este esquema de trabajo reduce significativamente los costos de tiempo, aumenta la eficiencia del proceso, reduce la probabilidad de defectos y errores y facilita la gestión de datos. El complejo de láser de proyección de máquina de corte de software, en comparación con la colocación tradicional, reduce la intensidad de trabajo de corte en aproximadamente un 50%, la laboriosidad de la disposición en aproximadamente un 30%, aumenta la tasa de utilización de materiales, es decir, puede ahorrar de 15 a 30% del material.
La formación de plásticos reforzados con fibra de carbono por el método de bobinado permite obtener productos con las más altas características de deformación y resistencia. Los métodos de bobinado se dividen en "seco" y "húmedo". En el primer caso, los preimpregnados se utilizan para enrollar en forma de hilos, paquetes o cintas. En el segundo caso, los materiales de refuerzo se impregnan con un aglutinante directamente durante el proceso de bobinado. Recientemente, se ha desarrollado un equipo que utiliza sistemas informáticos para controlar el patrón de orientación de la fibra. Esto permite obtener productos tubulares con curvaturas y formas irregulares, así como productos con geometría compleja. El equipo de bobinado se está desarrollando utilizando tecnología flexible, donde los materiales fibrosos de refuerzo se pueden colocar sobre el mandril en cualquier dirección.
Arroz. Bobinadora de fibra de carbono 4 MAG Cincinnati Viper 1200 FPS
Arroz. 5. Sistema de posicionamiento láser (contorno verde)
Equipo para el control de la geometría y estructura interna del producto.
Los contornos de los productos a menudo tienen generatrices curvilíneas, que no se pueden verificar utilizando los métodos tradicionales de "plaz". Con el escaneo 3D, puede determinar qué tan cerca se parece una muestra física a un modelo de computadora 3D. Para el escaneo 3D, también puede utilizar una máquina de medición por coordenadas (CMM) de tipo brazo o un sistema de escaneo láser/óptico sin contacto. Sin embargo, cuando se utilizan sistemas de escaneo sin contacto, por regla general, no pueden funcionar correctamente con superficies de espejo y de alto brillo. Cuando se utilizan "brazos de medición", se requerirán varios reinicios sucesivos, ya que el espacio de trabajo, debido al diseño de los brazos de medición, suele estar limitado a una esfera con un radio de 1,2 a 3,6 m.
Además, los materiales de fibra de vidrio tienen varias áreas problemáticas. Uno de los principales es el control de calidad del producto terminado (la ausencia de cavidades de aire) y la corrosión durante la operación. Para las pruebas no destructivas de cascos de barcos hechos de compuestos, los rayos X se usan ampliamente, pero tienden a reducirlos por varias razones. Recientemente, han comenzado a aparecer publicaciones que describen la detección de delaminaciones por termografía infrarroja (cámaras termográficas). Al mismo tiempo, tanto los métodos NDT de imágenes térmicas como de rayos X que detectan delaminaciones no permiten medir sus tamaños y determinar la profundidad de los defectos para evaluar su efecto sobre el cambio en las características de resistencia.
Conclusión
En la actualidad, en Rusia, el desarrollo intensivo de la automatización del ensamblaje de productos compuestos, incluidos los equipos para crear matrices, apenas comienza. En la mayoría de los casos, solo se realizan elementos individuales del kit de carrocería aerodinámica para el "ajuste" de los automóviles. La implementación del sistema FiberSIM en el diseño y construcción del dragaminas base del proyecto 12700, así como en la máquina automática de colocación de telas VASO, es un éxito. Pero estos son ejemplos aislados, para aumentar la competitividad es necesaria una introducción integral de nuevas tecnologías.
Enlace bibliográfico
Chernyshov E.A., Romanov A.D. TECNOLOGÍAS MODERNAS PARA LA FABRICACIÓN DE PRODUCTOS A PARTIR DE MATERIALES COMPUESTOS // Tecnologías modernas intensivas en ciencia. - 2014. - Nº 2. - Pág. 46-51;URL: http://top-technologies.ru/ru/article/view?id=33649 (consultado el 25/11/2019). Traemos a su atención las revistas publicadas por la editorial "Academia de Historia Natural"