Kompozitne tehnologije. Savremene naučno-intenzivne tehnologije. Tehnologija kompozita - Sekcija za tehnologiju materijala
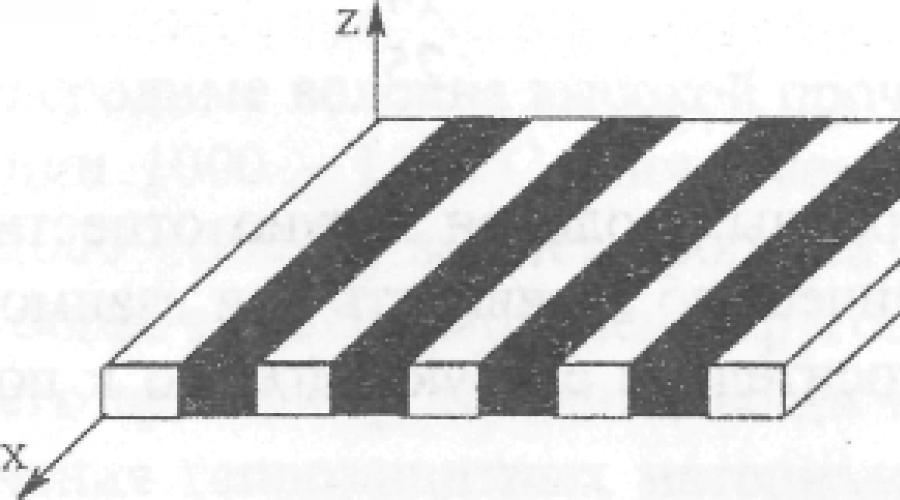
Pročitajte također
Raketna tehnologija, vazduhoplovstvo, inženjering aviona, nuklearna energija, hemijsko inženjerstvo, automobilska industrija, brodogradnja, elektronika i mnoge druge industrije zahtevaju materijale visoke čvrstoće, otpornosti na toplotu, otpornosti na toplotu i toplotu (dobra otpornost na širenje pukotina), niske gustine, podesivih preko širokog raspona pokazatelja toplinske i električne provodljivosti, posebnih optičkih i magnetskih karakteristika itd. Mnogi od postojećih industrijskih materijala više ne mogu! udovoljiti ovim zahtjevima.
Materijal sa kompleksom takvih karakteristika može se dobiti samo t osnova kompozicije. Kompozitni materijali (CM) su materijali koji se sastoje od dvije ili više komponenti (komponente za ojačanje i matrica koja ih povezuje) i koji imaju specifična svojstva koja se razlikuju od ukupnih svojstava ovih komponenti.
Ako je jedna od komponenti CM kontinuirana u cijelom volumenu, a druga je diskontinuirana, nepovezana u volumenu kompozicije, tada se prva komponenta naziva matrica, a druga armatura ili armaturni element. Komponente za ojačanje mogu biti razna vlakna, prahovi, mikrosfere, kristali i "brkovi" od organskih, neorganskih, metalnih materijala ili keramike. Kao matrix čaj
koriste se sintetičke visokomolekularne supstance različitog hemijskog sastava.
Sama priroda je bila prvi tvorac kompozitnih materijala. Na primjer, drvo je sastav koji se sastoji od snopova celuloznih vlakana visoke čvrstoće cjevastog presjeka, međusobno povezanih matriksom organske tvari (lignin), koji drvu daje poprečnu krutost.
Komponente kompozita ne smiju se rastvarati ili na drugi način apsorbirati jedna drugu. Moraju imati dobru adheziju i biti međusobno kompatibilni. Svojstva CM ne mogu se odrediti samo osobinama komponenti, bez uzimanja u obzir njihove interakcije. Svaka komponenta ima specifičnu funkciju i doprinosi svojstvima kompozita. Razmotrite zahtjeve za ojačavajuća punila, na primjer, za vlakna.
Navojni oblik armaturnih elemenata ima i pozitivne i negativne strane. Prednost vlakana je visoka čvrstoća i mogućnost stvaranja armature samo u smjeru u kojem je to strukturalno potrebno. Nedostatak ovog oblika je što vlakna mogu prenijeti opterećenje samo u smjeru svoje ose, dok u okomitom smjeru nema ojačanja, a u nekim slučajevima može doći i do omekšavanja.
Vlakna koja se koriste kao punila za ojačavanje moraju imati sljedeća svojstva: visoku tačku topljenja, malu gustinu, veliku čvrstoću u cijelom rasponu radnih temperatura, bez toksičnosti tokom proizvodnje i rada.
Uglavnom se koriste tri vrste punila: brkovi, metalna žica i anorganska polikristalna vlakna.
Brkovi se smatraju obećavajućim materijalom za ojačanje matrica od metala, polimera i keramike. Ultra-visoka čvrstoća u širokom temperaturnom rasponu pri niskoj gustini, hemijska inertnost u odnosu na mnoge matrične materijale. realam, visoka otpornost na toplotu i otpornost na koroziju brkova od aluminijumskih i magnezijum oksida, silicijum karbida čine ih nezamenljivim elementima za ojačanje. Nažalost, još uvijek postoje mnoge poteškoće na putu njihove praktične primjene. Potrebno je riješiti probleme njihovog dobivanja u industrijskim razmjerima, odabirom odgovarajućih brkova, njihovom orijentacijom u matrici i metodama za formiranje kompozicija sa brkovima.
Metalna žica od čelika, volframa, molibdena i drugih metala manje je perspektivna od "brkova" zbog svoje velike gustine i manje čvrstoće. Međutim, ima relativno nisku cijenu i široko se koristi kao armatura, posebno za kompozitne materijale na bazi metala.
Polikristalna neorganska vlakna proizvode se u velikim količinama. Nedostatak ovih vlakana je njihova vrlo visoka osjetljivost na mehanička oštećenja. Mala gustina, visoka čvrstoća i hemijska otpornost na ugljenik, bor, staklo, silicijum karbid. kvarc i druga vlakna omogućavaju im široku upotrebu za ojačavanje plastike,
Ugljična vlakna su među elementima za ojačanje koji najviše obećavaju. Imaju malu gustinu (1430 - 1830 kg/m3), veliku čvrstoću (3,5 GPa) i modul elastičnosti (250 - 400 GPa).
Općenito, karbonska vlakna se dijele na dva glavna tipa: vlakna visoke čvrstoće i vlakna visoke elastičnosti. U proizvodnji se uglavnom proizvode vlakna visoke čvrstoće. Čvrstoća ovih vlakana u početnoj fazi razvoja bila je 2,5 GPa. Poboljšanjem tehnologije (predobrada, usporavanje vlakana, karbonizacija i završna obrada) povećana je čvrstoća, na primjer, za konvencionalni materijal na 3,5 GPa.
Provedene studije su pokazale da s povećanjem čvrstoće vlakana, čvrstoća kompozitnog materijala u pravilu raste linearno. , : ;.,
Obično se karbonska vlakna visoke čvrstoće dobijaju pri temperaturi karbonizacije od 1000 - 1500°C, imaju modul elastičnosti od 2250 -2350 S/mm 2 . Na 2000 - 3000°C zbog procesa grafitizacije mogu se dobiti vlakna većeg modula elastičnosti.
Do nedavno su se karbonska vlakna i tkanine napravljene od njih koristile za proizvodnju materijala za zaštitu od topline. Međutim, poboljšanje. Tehnologija kupke za dobijanje tankih vlakana koja kombinuje visoku čvrstoću i krutost sa drugim posebnim svojstvima (termička otpornost, električna provodljivost, itd.) omogućila je stvaranje metala i plastike ojačane karbonskim vlaknima, koje karakteriše niska krutost i visoka čvrstoća. Takve kompozicije se sve više koriste u svemirskoj, raketnoj i zrakoplovnoj tehnici. Najčešće korištena karbonska vlakna su viskoza i poliakrilonitril.
Ovisno o sadržaju ugljika, karbonska vlakna se dijele u tri grupe:
karbonizirani (ne više od 95 tež.% C); - ugalj (91-98 tež.% C);
grafit (više od 98 tež.% C).
Kruta karbonska vlakna se dobijaju ako je tehnološki proces projektovan na način da je maksimalni broj osnovnih slojeva paralelan sa osi vlakna. Da bi se povećala čvrstoća karbonskih vlakana, potrebno je smanjiti veličinu kristalita, koji imaju savršeniju strukturu. Kao tehnološke metode koje karbonskim vlaknima daju dodatnu krutost i čvrstoću, legiraju se borom difuzijom iz gasne faze, vlakna se zrače neutronima u nuklearnom reaktoru, uvođenjem boraksa u njih prije pirolize, kao i istezanjem u procesi oksidacije i grafitizacije.
Ako u tankim vlaknima postoje mikrodefekti koji uzrokuju lokalnu koncentraciju naprezanja, tada se snaga karbonskih vlakana smanjuje. Nedostatak vlakana uzrokuje linearnu ovisnost njihove čvrstoće o dužini: s povećanjem dužine, čvrstoća se značajno smanjuje, a modul elastičnosti blago raste. Prema nivou mehaničkih svojstava, karbonska vlakna se dijele u tri grupe: niske, srednje, visoke (tabela 1.5)
Tabela 1.5 Mehanička svojstva karbonskih vlakana
Grupna gustoća Čvrstoća Modul elastičnosti
y, g/cm 3 a, GPa E, GPa
Niska 18 14 42
Srednje 18 14 175
Visoka 18 25 420
Nedostaci karbonskih vlakana uključuju njihovu sklonost oksidaciji na zraku, kemijsku aktivnost pri interakciji s metalnim matricama i relativno slabo prianjanje na polimerne matrice.
Površinska obrada vlakana je važan proces u smislu povećanja njihove adhezije na matriks. Obično se vrši površinska obrada karbonskih vlakana oksidacijom u gasnoj fazi.
Prisustvo metala i drugih anorganskih supstanci u njima utiče na karakteristike karbonskih vlakana. Konkretno, sadržaj alkalnih metala kao što su natrij i kalij ima negativan učinak na otpornost na oksidaciju kada se zagrijava, a fosfor i bor imaju pozitivan učinak.
Svi kompozitni materijali se dijele na izotropne i anizotropne. Izotropni materijali su materijali koji imaju ista svojstva u svim smjerovima, dok su anizotropni materijali različiti.
Elementi za ojačanje mogu imati približno jednak oblik ili biti kratke (diskretne) igličaste čestice nasumično orijentirane u prostoru. Kao takve čestice obično se koriste segmenti vlakana ili "brkovi". U ovom slučaju QM se ispostavlja kvazi-izotropnim, tj. anizotropan u mikrovolumenima, ali izotropan u zapremini cijelog proizvoda.
Anizotropni CM uključuju materijale čija su vlakna orijentirana u određenim smjerovima – jednosmjerna, slojevita i trodimenzionalno ojačana. Slike anizotropnih CM su date na Sl. 1.24, 1.25.
Rice. 1.24. Šematski prikaz strukture CM poprečnim polaganjem vlakana
sa uzdužnim
Rice. 1.25. Šematski prikaz strukture jednosmjernog CM (crne oblasti - vlakna; bijela - matrica)
Tehnološka anizotropija nastaje prilikom plastične deformacije izotropnih materijala (metala). Fizička anizotropija je karakteristična za kristale u vezi sa strukturnim karakteristikama njihove kristalne rešetke.
U inženjerstvu se obično koriste anizotropni CM s određenom simetrijom svojstava.
Jednako važnu ulogu u ojačanim kompozicijama igra matrica, koja proizvodu daje oblik i čini materijal monolitnim. Kombinujući brojna vlakna u jedinstvenu celinu, matrica treba da omogući kompoziciji da percipira različite vrste spoljašnjih opterećenja - napetost, kompresiju, savijanje, smicanje, itd. Istovremeno učestvuje u stvaranju nosivosti kompozicije. , osiguravajući prijenos sila na vlakna. Zbog plastičnosti matrice, sile s uništenih ili diskretnih (kratkih) vlakana prenose se na susjedna vlakna, a koncentracija naprezanja u blizini raznih vrsta defekata se smanjuje. Matrica također igra ulogu zaštitnog premaza koji štiti vlakna od mehaničkih oštećenja i oksidacije. Osim toga, matrica mora osigurati čvrstoću i krutost sistema pod djelovanjem vlačnog ili tlačnog opterećenja u smjeru okomitom na elemente armature. Ako je vlačno opterećenje usmjereno duž osi vlakana paralelnih jedna s drugom, tada da bi se postigao učinak jačanja, krajnje relativno izduženje matrice mora biti najmanje jednako relativnom izduženju vlakana. Ako je opterećenje okomito na os vlakana, onda to nije dovoljno. U ovom slučaju, opterećenje na vlakna se prenosi samo kroz matricu, a što je veća koncentracija vlakana i omjer modula elastičnosti materijala vlakna i matrice, to bi trebala biti krajnja deformacija matrice veća. . Evaluacijski rad na elastičnim modelima pokazuje da su za osiguranje čvrstoće CM-a pri poprečnom opterećenju potrebne matrice čije je relativno istezanje nekoliko puta veće od prosječne deformacije vlakana.
Želja za postizanjem maksimalne čvrstoće sastava teži povećanju volumnog udjela vlakana. Međutim, ako je relativno izduženje matrice malo, tada se u slučaju velikih vrijednosti ove frakcije, čvrstoća CM može slomiti čak i pod malim opterećenjima: pojavit će se raslojavanje i pukotine. Pokazalo se da što je matrica plastičnija, to je manja dozvoljena debljina međusloja matrice između vlakana i što se više vlakana može uvesti u CM.
Ovisno o materijalu matrice, svi CM se mogu podijeliti u tri grupe: kompozicije sa metalnom matricom - metalni kompozitni materijali (MCM), sa polimer - polimerni kompozitni materijali (PCM) i sa keramikom - keramički kompozitni materijali (CMC). Polimerni CM se obično nazivaju prema materijalu armaturnih vlakana: ojačani staklenim vlaknima nazivaju se fiberglass (fiberglas), metal - metal-plastika (metalna vlakna), organski - organoplastika (organo-vlakna), bor - plastika od bora ( borova vlakna), karbonska - karbonska vlakna (karbonska vlakna) itd.
Za metalne i keramičke CM ne postoje jasno utvrđena pravila za imenovanje. Češće od ostalih, prvo se piše materijal matrice, a zatim vlaknasti materijal. Na primjer, oznaka "bakar-volfram" (Cu-W) odnosi se na CM sa bakrenom matricom i volframovim vlaknima. Ali u literaturi se ponekad prvo navodi vlaknasti materijal, a zatim matrica.
Polimerni kompozitni materijali se najčešće koriste u usporedbi s ostalima zbog jednostavnosti proizvodnje, proizvodnosti, niske cijene, male gustoće. Njihov glavni nedostatak je ograničen temperaturni raspon rada. Moderna polimerna veziva (matrice) mogu osigurati performanse proizvoda do temperatura koje ne prelaze 300 - 400°C.
Polimerna veziva se prema ponašanju pri zagrijavanju i hlađenju obično dijele na termoplastična i termoreaktivna. Svojstva termoplastičnih polimernih veziva omogućavaju dobijanje proizvoda od njih brizganjem, ekstruzijom, prskanjem i široku upotrebu automatizovane opreme u njihovoj proizvodnji. Makromolekule termoplastičnih polimera imaju linearnu strukturu i dobijaju se od monomera sa dve funkcionalne grupe, koje su međusobno povezane jakim kovalentnim vezama. Makromolekularni lanci su međusobno povezani slabim van der Waalsovim silama.
Termoreaktivni oligomeri pod uticajem toplote, učvršćivača, katalizatora prelaze u čvrsto stanje (stvrdnjavaju). Ovaj proces je nepovratan. Oligomeri su lako rastvorljivi u nekim rastvaračima (alkohol, aceton, itd.), ali nakon stvrdnjavanja više nisu rastvorljivi. Termoset smole su napravljene od monomera koji imaju više od dvije funkcionalne grupe. Tokom stvrdnjavanja, monomeri rastu u tri smjera, formirajući makromolekule mrežne strukture, čiji su svi strukturni elementi međusobno povezani jakim kovalentnim vezama.
Glavna komponenta polimernog veziva je smola. Tačka omekšavanja, rastvorljivost, viskozitet i konačna svojstva veziva zavise od njegove prirode, reaktivnosti, molekulske težine i molekularne strukture. Osim smole, sastav veziva može uključivati: katalizatore ili inicijatore, koji se unose u smole u malim količinama kako bi se potaklo njihovo očvršćavanje; plastifikatori koji polimeru daju marginu plastičnosti i elastičnosti; boje koje boje materijal u željenu boju; stabilizatori koji sprečavaju razgradnju polimera pod dejstvom svetlosnog zračenja i povišenih temperatura.
Kao vezivo za strukturalni PCM, koji radi pod/opterećenjima, u velikoj većini slučajeva koriste se termoreaktivne smole. U proizvodnji strukturnih PCM-a najčešće se koriste epoksidne, poliesterske, fenolne, organosilicijumske i poliimidne smole.
Epoksidne smole čine 90% smola koje se koriste kao* veziva za nove PCM. Epoksidne smole se mogu stvrdnjavati, ovisno o o-tipu učvršćivača i njegovoj količini, kako na sobnoj tako i na povišenim temperaturama. U prvom slučaju govori se o smolama hladnog očvršćavanja, u drugom o smolama koje očvršćavaju vruće.
Epoksidne smole poznate su po svojoj svestranosti. Imaju nisko skupljanje, dobro prianjanje na različite punilice, visoka mehanička svojstva, nisku apsorpciju vlage, omogućavaju obradu na sobnoj temperaturi i variraju u širokom rasponu trajanja i temperature očvršćavanja. Mogu im se dodati rastvarači, modifikatori i plastifikatori da bi se promenio viskozitet neočvrslog polimera, hemijska otpornost i plastičnost. Tokom njihove termičke obrade nema emisija isparljivih produkta reakcije. Nešto su skuplji od poliesterskih i fenolnih smola, ali to se nadoknađuje njihovim boljim tehnološkim i operativnim kvalitetima.
Tipično, CM na bazi epoksidnih smola se koriste do 150°C. Poslednjih godina razvijene su nove epoksidne smole otpornije na toplotu, koje im omogućavaju da se koriste u GFM koji radi na 200°C i više.
Vrlo važan kvalitet epoksidnih smola sa tehnološke tačke gledišta je njihova sposobnost da dugo ostanu u poluočvrslom stanju, što omogućava proizvodnju predimpregniranih i djelimično očvrsnutih tkanina, traka i kudelja („prepregova” ) na njihovoj osnovi, a zatim dobijaju proizvode.
Poliesterske smole su polikondenzacioni proizvodi nezasićenih dikarboksilnih kiselina (uglavnom maleinske i metakrilne kiseline) sa polihidričnim ili nezasićenim alkoholima (dietilen glikol, trietilen glikol, itd.). Kao rezultat polimerizacije nastaje čvrsti nerastvorljivi polimer trodimenzionalne strukture. Poliesterska veziva razvijena su mnogo ranije od epoksidnih veziva i na njihovoj osnovi su napravljeni prvi strukturni CM.
Glavne prednosti poliesterskih veziva su njihova niska cijena i lakoća rukovanja. Ali oni su manje jaki, imaju lošiju adheziju za većinu vlakana, krhkiji su, više se skupljaju nakon stvrdnjavanja i imaju kraći vijek trajanja od epoksidnih smola.
Fenolne smole se dobijaju polikondenzacijom fenola (hidroksi-benzen, krezol, resorcinol itd.) sa aldehidima (furfural, formaldehid i dr.). Ove smole su tamne boje i imaju povećanu otpornost na visoke temperature u odnosu na prethodno razmatrana veziva.
Tokom sušenja fenolne smole prolaze kroz tri faze:
"A" - formiranje rezola - proizvod početne kondenzacije, koji nema poprečne veze i može se otopiti u alkoholu, acetonu i drugim otapalima;
"B" - formiranje resitola - proizvoda u kojem je počelo formiranje poprečnih veza. Resitol se ponaša kao termoplastična smola - omekšava kada se zagrije i postaje tvrd i krt na sobnoj temperaturi;
"C" - dobijanje resit - potpuno očvrsnut termoreaktivni (nerastvorljiv i neotopljen) proizvod.
U fazi resitola, kada je većina isparljivih supstanci već uklonjena, prepregovi se prave od fenolnih smola. Same po sebi, fenolne smole su vrlo krhke.
Njihovi nedostaci uključuju toksičnost i potrebu primjene visokog pritiska tokom sušenja. KM na bazi fenolnih smola su materijali dizajnirani za rad na visokim temperaturama, ta! kako su u stanju da dugo izdrže temperature ds 315°C, a kratko - iznad 3000°C.
Silikon ili silikonske smole su sintetička jedinjenja koja sadrže zajedno sa organskim grupama! silicijum i kiseonik, koji su uključeni u glavni lanac u obliku karika
KM - na njihovoj osnovi zadržavaju svoja svojstva na temperaturama iznad 260 ° C, odlikuju ih otpornost na koroziju, otpornost na luk i iskre, te povećana toplinska provodljivost. Međutim, na sobnoj temperaturi svojstva KM n; na bazi silikonskih smola je niža nego na bazi epoksidnih, poliesterskih i fenolnih smola. Takođe, skuplji su. Na bazi organosilicijumskih smola dobijaju se CM, koji se koriste u konstrukciji oklopa) motora aviona, raketa i drugih proizvoda koji rade na visokim temperaturama.
Poliimidne smole odlikuju se visokim stopama termičke i termičke stabilnosti i otpornosti na zračenje. CM bazirani na njima su sposobni da rade dugo na temperaturama iznad 300°S. U završnoj fazi formiranja, poliimidne smole gube svoju plastičnost i topljivost] se pretvaraju u policiklične mrežne polimere. Izgledi za stvaranje visokotemperaturnih CM su povezani s njima. Postojeći nedostaci: poliimidne smole - potreba za korištenjem visokih temperatura i pritisaka tokom njihovog očvršćavanja.
Tehnologija proizvodnje proizvoda iz PCM-a uključuje sljedeće glavne faze:
1. UV predtretman površine kako bi se poboljšala njegova kvašenje otopinama ili topljenjem veziva.
Ugljična vlakna se isporučuju potrošaču premazana lubrikantom, koji je potreban kao pomoćno sredstvo u procesu. Uklanjanje maziva s površine vlakana (dedimenzioniranje) je neophodna operacija vrx syayazlyutim. Za ovaj ugljovodonik se propušta kroz benzin, rastvore oleinske kiseline (2 tež.%), trietanolamin (1 tež. %) ili druge rastvarače. Lubrikant se takođe može ukloniti kalcinacijom ugljovodonika na 200 - 450°C. Dobar efekat daje pranje u vodi uz upotrebu ultrazvuka. Nakon dekaliziranja, neke vrste vlakana snažno adsorbiraju vlagu, što narušava prianjanje veziva za njih i smanjuje karakteristike performansi PCM-a u cjelini. Nanošenje hidrofobnih (vodoodbojnih) premaza na površinu, koji povećavaju čvrstoću veze između vlakana i veziva i smanjuju upijanje vode PCM-a, naziva se faza dimenzioniranja. Oblozi se fiksiraju zagrijavanjem vlakana na 80-150°C u trajanju od 20-60 minuta. U slučajevima kada vlakna stižu na bobine koje nisu pogodne za namotavanje ili impregnaciju, polažu se na jednosmjernu traku, tzv. roving, pri čemu se osigurava ravnomjerna napetost. Ova operacija se zove iskrivljavanje.
2. Priprema veziva.
Osim glavne komponente (smole), ovisno o njenoj prirodi, vezivu se dodaju različite količine učvršćivača, katalizatora, plastifikatora i pigmenata. Koriste se sljedeći rastvarači: aceton, benzol, toluen, dihloretan, tetrahlorid. Očigledno, kada radite s njima, morate se pridržavati relevantnih sigurnosnih zahtjeva.
Razrjeđivači doprinose postizanju potrebne tehnološke viskoznosti veziva i ostaju u njemu nakon stvrdnjavanja. Razrjeđivači istovremeno obavljaju ulogu plastifikatora, povećavajući plastičnost očvrslog veziva. Na primjer, epoksidne smole niske viskoznosti od dietilen glikola, trietilen glikola koriste se kao razrjeđivač za epoksidne smole visokog viskoziteta. Mješavina svih komponenti koje čine vezivo naziva se spoj.
Važna tehnološka karakteristika veziva je njegova vitalnost (viabilnost) - sposobnost održavanja određenog vremena (od nekoliko minuta do nekoliko dana) tehnološke viskoznosti u određenim granicama. S vremenom, otapala isparavaju iz veziva, što povećava viskozitet smjese i pogoršava njegove impregnacijske karakteristike. Ako otapalo polako isparava, spoj ima visoku održivost, ali se vrijeme sušenja proizvoda značajno povećava. Može se čak dogoditi da vrijeme potpunog uklanjanja rastvarača premašuje vrijeme očvršćavanja veziva. U ovom slučaju, u osušenom polimeru će biti mnogo pora i mjehurića plina. Upotreba hlapljivih otapala naglo smanjuje održivost veziva, što je također nepoželjno. Na primjer, za epoksidne smole preporučuje se srednje isparljiv toluen ili njegov rastvor u etil alkoholu.
Prilikom transporta i skladištenja veziva ponekad u njega uđe vlaga. Stoga se prije upotrebe smola zagrijava u posebnim metalnim posudama na 100 - 140 °C i nakon uklanjanja vode razrijedi se otapalima ili razrjeđivačima.
3. Impregnacija.
Ovo je operacija spajanja punila sa vezivom nanošenjem smjese na površinu CF-a i punjenjem volumena između vlakana.
Trenutno se proizvodi iz PCM-a proizvode uglavnom na dva načina: "mokro" i "suvo". U mokroj metodi, vlakna se impregniraju tekućim vezivom neposredno prije namotavanja, tj. impregnacija je tehnološki kombinovana sa oblikovanjem proizvoda. Suhim načinom impregnacije; odvojeno u samostalnu operaciju, kao rezultat toga od ugljovodonika i veziva. nabavite preprege. Impregnacija i sušenje se obavljaju u specijalizovanim postrojenjima odvojeno od namotavanja, što omogućava proširenje asortimana polimernih veziva koji se koriste upotrebom raznih; rastvarači. Veziva sa rastvaračima imaju nizak tehnološki viskozitet, što omogućava postizanje visokog kvaliteta u ujednačenosti impregnacije. Prepregi mogu biti u djelimično osušenom stanju. od nekoliko dana do nekoliko mjeseci, ovisno o temperaturi okoline.
Suvo namotavanje je progresivniji način od mokrog. Nedostaci mokrog namotavanja su sljedeći:
Izbor veziva za mokro namatanje ograničen je na one smole!- koje se mogu koristiti u tečnom obliku, na primjer, epoksid ili poliester.
Općenito, nije poželjno koristiti rastvarače, jer hlapljive tvari, koje se uklanjaju tokom stvrdnjavanja proizvoda rane, dovode do stvaranja pora, mjehurića i pogoršavaju čvrstoću i čvrstoću.
Upotreba tečnih veziva pogoršava sanitarne uslove na radnom mestu.
Produktivnost mokrog namotavanja ograničena je brzinom veziva.
Upotreba zagrijavanja za smanjenje viskoznosti procesa smole smanjuje održivost veziva, ubrzava proces polimerizacije< гризации и ухудшает пропиточные свойства смолы.
6. Kod mokrog namotavanja, teško je podesiti koncentraciju komponenti u proizvodu. Deo smole nestaje mokrom metodom.
Suvo namotavanje preprega je lišeno svih navedenih nedostataka] Brzina namotavanja nije ograničena brzinom impregnacije i u potpunosti zavisi* od mogućnosti opreme za namotavanje. Namotavanje prepregom omogućava upotrebu širokog spektra smola, da se obezbedi ravnomerna pacnpi podela veziva po celoj zapremini proizvoda, da se smanji mogućnost lepljivosti Ppeppegy, što omogućava dobijanje proizvoda složenog oblika, povećane nepropusnost i niska poroznost. Prilikom njihovog formiranja ostaje samo osigurati kvalitetnu povezanost vezivnih slojeva međusobno (autohezija) i s ojačavajućim vlaknima (adhezija).
Glavni nedostaci suhog namotavanja uključuju potrebu za korištenjem posebnih strojeva i druge tehnološke opreme.
Postoje sljedeće metode impregnacije: provlačenje armature (navoja) kroz tečno vezivo; valjak za kupanje; prskanje prisilnom impregnacijom.
U proizvodnji GFM-a sa ojačanjem u obliku snopova, niti i tkanina, najčešća metoda je impregnacija provlačenjem kroz tečno vezivo (slika 1.26).
Rice. 1.26. Shema vertikalne mašine za impregnaciju; 1 - bubanj, 2 - armature, 3 - kada sa tečnim vezivom, 4 - valjci za kupanje, 5 - osovina za sušenje, 6 - grejači, 7 - izduvni uređaj, 8 - uređaj za zatezanje, 9 - prihvatni bubanj
Armaturna šipka (2) se odmotava od bubnja (kalem) (1) i, prolazeći kroz sistem valjaka (4), ulazi u kadu (3) sa tečnim vezivom. Impregnirana armatura ulazi u šaht za sušenje (5), gdje se nalaze grijači (6) i izduvni uređaj (7). Ovdje armatura nekoliko puta mijenja smjer kako bi se produžilo vrijeme svog boravka u zoni visoke temperature. Kao rezultat toga, hlapljive tvari se uklanjaju iz smjese, a prostor između vlakana je ispunjen vezivom. Osušeni prepreg se namotava uz pomoć pogonskog vratila kroz zatezač (8) n; prijemni bubanj.
Za GFM sa vrlo krutom armaturom (visokomodulnim grafitnim borom ili drugim vlaknima), koja ne dozvoljava male radijuse savijanja, zgodno je koristiti metodu impregnacije valjka za kupanje (slika 1.27).
Rice. 1.27. Šema impregnacije valjkom za kupanje: 1 - okovi, 2 - posuda sa tečnim vezivom, 3 - posuda, 4 - valjak za kupanje
Prilikom rotacije, valjak hvata vezivo na svojoj površini i prenosi ga na armaturu.
Metoda prskanja sa prisilnom impregnacijom omogućava drastično smanjenje vremena punjenja međuvlaknastih prostora vezivom; Nanesite hidrauličnu, vakuumsku i mehaničku prisilnu impregnaciju. .
U procesu hidrauličke prisilne impregnacije, tekući ev; pumpanje se pumpa kroz ventil.
Vakuumska prisilna impregnacija se vrši usisavanjem tečnosti u evakuisanu komoru, gde se nalaze okovi.
Mehanička prisilna impregnacija je jednostavnija. To mogu biti ose; rad u posebnoj (klinastoj) komori ili uz pomoć lica za stiskanje. U klinastoj komori (Sl. 1.28), jedinjenje se odnosi pokretnom rukom; tura u klinastu šupljinu. Ovdje, zbog smanjenja poprečnog presjeka kanala komore: pritisak tekućine raste okomito na pokretnu armaturu. Pod djelovanjem ovog pritiska popunjava se prostor između vlakana.
Prilikom impregnacije pomoću valjka za stiskanje (slika 1.286), pritisak povezan sa impregnacijom i uklanjanjem mjehurića zraka iz međuvlaknastog prostora nastaje u obliku reakcije valjka na istegnutu traku.
Rice. 1.28. Šeme mehaničke prisilne impregnacije u klinastoj komori (a) i uz pomoć valjka za stiskanje (b): 1 - armatura, 2 - vezivo, 3 - valjci
4. Moulding.
Ovo je operacija davanja proizvodu zadanog oblika i veličine. Formiranje se može vršiti na presama, kontaktnim, vakuumskim, autoklavnim metodama i namotavanjem.
Prije formiranja na presama, prethodno impregnirani roving ili tkanina se reže ručno ili na posebnim mašinama na komade željene dužine. Ovisno o datoj PCM strukturi, komadi se polažu u jednom ili više naizmjeničnih smjerova. Paket se postavlja između ploča hidraulične prese i sabija pod pritiskom od nekoliko do desetina atmosfera, ovisno o prirodi i strukturi komponenti. Ako je armatura impregnirana vrućim vezivom, tada se ploče za presovanje zagrijavaju. Ova metoda se obično koristi za proizvodnju pločastih materijala kao što je tekstolit.
Kontaktno oblikovanje je valjanje impregnirane trake ili tkanine valjkom. Tipično, zgušnjavanje se izvodi na sobnoj temperaturi pomoću smola koje se stvrdnjavaju hladno. Ova metoda se koristi u maloj proizvodnji velikih i lagano opterećenih proizvoda.
Vakuumsko oblikovanje proizvoda iz PCM-a vrši se zbog razlike između atmosferskog i unutrašnjeg (u zapremini u kojoj se proizvod nalazi) pritisaka. Vakuumsko oblikovanje se koristi za proizvodnju malih serija proizvoda, jer je metoda neefikasna i relativno skupa.
U metodi autoklavnog oblikovanja, proizvod se formira blagim pritiskom koji stvara voda ili plin. Ova metoda se može koristiti za dobivanje velikih serija velikih dijelova složenog oblika.
Jedan od najčešćih načina dobivanja PCM-a i proizvoda od njih je metoda namotavanja. U ovom slučaju, armatura impregnirana vezivom se namota na bubanj (trn) sa zatezanjem. Namotavanje omogućava automatizaciju procesa oblikovanja i programiranje anizotropije svojstava finalnog proizvoda. Namotavanje se najčešće koristi za proizvodnju proizvoda koji imaju oblik tijela okretanja (cilindri, kugle, čunjevi, toroidi itd.).
5. izlečenje.
Tokom očvršćavanja veziva stvaraju se konačne strukture; PCM, formiraju se njegova svojstva i fiksira oblik proizvoda. Glavni tehnološki parametri sušenja su temperatura i vrijeme. Potrebno je striktno pridržavati se parametara razvijenih za svaku kombinaciju veziva i armature.
Stvrdnjavanje se može vršiti na sobnoj temperaturi (hladno* očvršćavanje), na povišenim temperaturama (vruće sušenje), u električnim ili indukcijskim pećnicama sa automatskom regulacijom temperature, stvrdnjavanje zračenjem.
Tokom očvršćavanja uočavaju se dvije karakteristične faze kroz koje sukcesivno prolazi termoreaktivno vezivo: početna faza, tokom formiranja polimerne mreže, i završna faza, tokom formiranja polimerne mreže. Ove dvije faze su odvojene jedna od druge takozvanom gel tačkom. Tačka geliranja odgovara trenutku kada vezivo gubi sposobnost da pređe u fluidno stanje s da bi se rastvorilo u rastvaračima.
U određenom temperaturnom rasponu, tečno vezivo prelazi u staklasto stanje. Sva svojstva veziva se dramatično mijenjaju: smanjuje se specifična zapremina, povećava se tvrdoća i javlja se otpornost na deformacije. Temperatura na kojoj se ovaj fenomen javlja naziva se temperatura staklastog prijelaza. Temperatura staklastog prijelaza nije tačka, već prosječna temperatura intervala. Staklena tranzicija nije fazni prijelaz; staklasto vezivo ima amorfnu strukturu i, sa termodinamičke tačke gledišta, može se smatrati prehlađenom tekućinom.
Još jedna karakteristična točka polimernih materijala je temperatura degradacije - temperatura na kojoj počinje primjetno raspadanje polimera, praćeno prekidom molekularnih veza. Destrukcija, poput staklene tranzicije, se dešava u temperaturnom opsegu. Održivost! vezivo za destrukciju karakteriše njegova termička stabilnost (termalna stabilnost, termička stabilnost). Ovaj koncept treba razlikovati od otpornosti na toplinu, koja odražava sposobnost polimera da omekša.
Do potpunog iscrpljivanja reaktivnih grupa, reakcija očvršćavanja može se odvijati samo ako je temperatura stvrdnjavanja iznad temperature staklastog prijelaza. U suprotnom se ne može postići potpuno očvršćavanje. Reaktivne grupe i dalje ostaju u polimeru, ali je njihova stopa interakcije s drugim grupama vrlo niska zbog vrlo visoke viskoznosti sistema. Ako SHSM sa nepotpuno očvrslim vezivom radi na povišenim temperaturama, očvršćavanje će se nastaviti. To dovodi do promjene oblika i dimenzija proizvoda, pojave dodatnih unutarnjih naprezanja.
Često je reakcija stvrdnjavanja praćena oslobađanjem topline, materijal se samozagrijava, a vezivo može potpuno stvrdnuti. Na ovom principu se zasniva hladno očvršćavanje termoreaktivnih veziva. Međutim, za kritične proizvode, u većini slučajeva koristi se vruće stvrdnjavanje.
Armatura i vezivo u sastavu su pod dejstvom unutrašnjih naprezanja, koja se mogu podeliti na tri tipa: strukturna, skupljajuća i termička.
Konstruktivna naprezanja uzrokovana su tehnološkim naprezanjem armature tokom procesa namotavanja. Prije uklanjanja s trna, strukturna naprezanja djeluju samo u vlaknima, u vezivu ih nema.
Naprezanja skupljanja nastaju u vlaknima i vezivu zbog smanjenja zapremine (skupljanja) veziva tokom njegovog očvršćavanja. Količina skupljanja može varirati od 2 do 30 vol.% u zavisnosti od prirode jedinjenja.
Toplotna naprezanja nastaju zbog razlike u koeficijentima linearne ekspanzije armature i veziva i neravnomjerne raspodjele temperatura u zapremini proizvoda. U pravilu, koeficijent linearne ekspanzije polimera je znatno veći od koeficijenta vlakana.
U stvarnom PCM-u sva razmatrana naprezanja se zbrajaju i materijal je pod djelovanjem nastalih napona, koji se s vremenom opuštaju. Kako biste promovirali potpuniju relaksaciju stresa i izbjegli savijanje i pucanje, preporučuje se polagano zagrijavanje i hlađenje PCM proizvoda.
CFRP s niskomodulnim vlaknima se ne koriste kao strukturni. Od njih se izrađuju provodljivi, toplotno-zaštitni i antifrikcioni materijali.
Strukturni CFRP sadrže karbonska vlakna visokog modula (E = 342–540 GPa) i visoke čvrstoće (steg–2,5 GPa) kao punila. Strukturnu ugljičnu plastiku karakterizira niska gustoća i koeficijent linearne ekspanzije i visoki modul elastičnosti, čvrstoće, otpornosti na toplinu, toplinske i električne provodljivosti.
Svojstva karbonske plastike određuju vezivni materijal, svojstva, koncentracija i orijentacija vlakana. CFRP na bazi epoksidnih smola ima visoke karakteristike čvrstoće na temperaturama ispod 200°C (tabela 1.6). Ovi PCM se najčešće izrađuju od preprega dostupnih u trakama različitih širina. Vlačna čvrstoća i čvrstoća na savijanje za jednosmjerna karbonska vlakna može biti 1000 - 1600 MPa ili više, a modul elastičnosti (1 - 2,5) -10 MPa ili više. U pogledu specifične čvrstoće i krutosti, karbonska plastika ostavlja daleko iza staklene plastike, čelika, aluminija i legura titana.
Tabela 1.(
Svojstva epoksidnih CFRP-a visokog modula i visoke čvrstoće
Indikatori |
Epoxy CFRP! |
|
visoko modularan |
visoke čvrstoće |
|
Gustina, kg / m 3 | ||
Čvrstoća, MPa, na pritisak, zatezanje i savijanje, interlaminarni smicanje | ||
Modul elastičnosti pri zatezanju i savijanju, GPa | ||
Čvrstoća na zamor pri savijanju na bazi 10 7 ciklusa, GPa |
U ugljičnim plastikama namijenjenim za dugotrajan rad na temperaturama do 250 ° C koriste se fenolne, do 300 ° C - organosilicij i do 330°C - poliimidna veziva. Razvijaju se veziva sa radnim temperaturama do 420°C. Još izraženiji nedostatak plastike ojačane karbonskim vlaknima od plastike ojačane staklom je njihova niska međuslojna čvrstoća na smicanje. To je zbog slabe adhezije polimera na karbonska vlakna. Za: povećanje adhezije, koristi se nekoliko metoda: jetkanje površine vlakana oksidirajućim agensima (na primjer, dušičnom kiselinom), sagorijevanje maziva; dimenzioniranje - prethodno premazivanje vlakana tankim slojem monomera koji ih vlaži; brkovi - rastući "brkovi" (gomila) w karbonskim vlaknima. CFRP, u kojem se, osim orijentiranih kontinuiranih vlakana, koriste i brkovi kao punilo, ja to zovem! viscerized ili vorserized.
Anizotropija svojstava kod karbonske plastike je još izraženija nego kod stakloplastike. To je povezano sa tim. da je omjer modula elastičnosti punila i veziva za plastiku ojačanu karbonskim vlaknima (100 i više) znatno veći nego za plastiku od stakloplastike (20–30). Osim toga, CFRPs karakterizira postojanje razlike između elastičnih svojstava samih vlakana u smjeru duž osi i okomito na nju, što dovodi do dodatne anizotropije. Tipično, dizajn zahtijeva manje mehaničke anizotropije. U ovom slučaju koriste se unakrsno ojačani materijali. Promjenom zapreminskog sadržaja vlakana i teksture PCM-a, moguće je promijeniti svojstva kompozicija u vrlo širokom rasponu.
CFRP se odlikuje visokom otpornošću na opterećenja od zamora. U pogledu granice izdržljivosti po jedinici mase, karbonska plastika je znatno superiornija od plastike i metala ojačane staklom. Jedan od razloga za to je niža (od npr. stakloplastike) deformacija na istom nivou naprezanja, što smanjuje pucanje polimerne matrice. Osim toga, visoka toplinska provodljivost karbonskih vlakana doprinosi disipaciji energije vibracija, što smanjuje samozagrijavanje materijala zbog unutrašnjih sila trenja.
Vrijedno svojstvo karbonskih vlakana je njihova visoka sposobnost prigušenja i otpornost na vibracije. Prema ovim pokazateljima, karbonska plastika je superiornija od metala i nekih drugih konstrukcijskih materijala. Kapacitet prigušenja može se podesiti promjenom ugla između smjera armature i primjene opterećenja.
CFRP se koristi za izradu konstrukcija koje rade na stabilnost pod utjecajem vanjskog momenta savijanja, pritiska ili aksijalne kompresije: lopatice rotora helikoptera, kućišta kompresora i ventilatora, lopatice ventilatora, stator i diskovi rotora niskotlačnog kompresora avionskih motora. Upotreba karbonskih vlakana u ovim jedinicama umjesto metala omogućava smanjenje težine motora za 15-20%. U svemirskoj tehnologiji, karbonska plastika se koristi za solarne panele, cilindre visokog pritiska i premaze za zaštitu od toplote.
Koeficijent linearne ekspanzije visokomodulnih jednosmjernih ugljičnih plastika u uzdužnom smjeru je blizu nule, au rasponu od 120 - 200°C čak je negativan (-0,5-10"6 1/°C). dimenzije proizvoda od karbonske plastike se vrlo malo mijenjaju tokom grijanja i hlađenja.
CFRP imaju prilično visoku električnu provodljivost, što im omogućava da se koriste kao antistatički i električno grijaći materijali. Sa povećanjem sadržaja ugljovodonika u PCM-u na određeni volumni udio (40-70%), ovisno o vrsti polimera i ugljikovodika, tekstilnom obliku ugljikovodika, uočava se povećanje čvrstoće i modula elastičnosti. Tada se ovi pokazatelji počinju pogoršavati zbog nedovoljne količine polimera potrebnog za dobivanje monolitnog kompozita i uništavanje krhkih ugljikovodika u fazi formiranja pri visokom stupnju zbijanja. Maksimalni sadržaj HC u PCM-u je također ograničen slabom kvašenjem HC veziva.
U nekim slučajevima, korištenje samo karbonskih vlakana kao punila ne osigurava potrebnu viskoznost, otpornost na eroziju, tlačnu, vlačnu i smičnu čvrstoću. Zatim se veziva armiraju zajedno sa karbonskim i staklenim ili ugljičnim i borovim vlaknima. Kombinirano ojačanje vam omogućava da proširite asortiman! vrijednosti čvrstoće, krutosti i gustine PCM-a.
Hemijska otpornost CFRP-a omogućava njihovu upotrebu u proizvodnji pumpi i brtvila otpornih na kiseline. Ugljična vlakna imaju nizak koeficijent trenja, što im omogućava da se koriste kao punilo za razna veziva od kojih se izrađuju zaptivni ležajevi, čahure i zupčanici.
Razvoj tehnologije zahtijeva mehanički jake materijale otporne na toplinu. Ovo je izazvalo poseban interes za kompozitne materijale ugljik-ugljik (CCCM) koji sadrže ugljik kako u obliku punila za ojačanje tako i u obliku matričnog materijala.
U CCCM, otpornost na visoke temperature je kombinovana sa malom gustinom, visokom čvrstoćom i modulom elastičnosti, otpornošću na toplotu; udarac. Ovi materijali su dugotrajni na temperaturama do 500°C (u oksidacionom okruženju i do 3000°C u inertnoj atmosferi iu vakuumu).
Punilo i matrica CCCM, u zavisnosti od sastava i uslova karbonizacije, mogu imati različite modifikacije. U prihvaćenoj klasifikaciji prvo je naznačena struktura ugljičnog punila, zatim matrica, na primjer, ugljik-ugljik, grafit-ugljik, grafit-grafit materijal.
U CCCM-u, karbonsko punilo se nalazi u obliku diskretnih vlakana, kontinuiranih niti ili kudelja, filca, traka, tkanina sa ravnim i volumetrijskim tkanjem, volumetrijskih struktura. Vlakna su nasumično raspoređena u jednosmjernom, dvosmjernom i trosmjernom smjeru. Koriste se ugljovodonici niskog modula, visokog modula i visoke čvrstoće, dobijeni od viskoznih, poliakrilonitrilnih vlakana i smole ugljenog katrana.
Kao matrica može se koristiti pirolitički ugljik, kao i katran i polimeri za koksovanje, koji u procesu termičke destrukcije daju više od 50 tež.% koksa. Najčešće se koriste fenolne smole (prinos koksa 54-60 tež.%). Poznato je da se koriste poliimido (63 - 74 tež.%), organosilicijumske smole (84 - 87 tež.%), produkti kondenzacije fenola i naftena sa formaldehidom (70 tež.%), oligobenzimid.soli (74 tež.%), produkti kondenzacije fenola i naftena sa formaldehidom (70 tež.%). , furfuril smole i dr., polimeri. Što se više krećete i, jačina koksa, kao i jačina njegovog prianjanja na punilo, tci, to je veći kvalitet CCCM.
, .„.„ Za dobijanje kompozita sa željenim svojstvima potrebno je odrediti najpovoljniju kombinaciju punila i matrice, kao i najpovoljniji tehnološki režim za dobijanje yraepoj matrice.
Ovisno o faznom stanju tvari koje sadrže ugljik, razlikuju se sljedeće metode zgušnjavanja punila od karbonskih vlakana (CFF) ugljikom:
korišćenje ugljovodonika u gasnoj ili parnoj fazi (prirodni gas, propan-butan, benzol, itd.);
korištenje tekućih ugljovodonika koje karakterizira visok sadržaj ugljika i visok postotak prinosa koksa (smola, katran);
kombinovano, što uključuje impregnaciju poroznih okvira tekućim ugljovodonicima i karbonizaciju, zatim zbijanje pirolitičkim ugljikom dobijenim pirolizom ugljovodonika u gasnoj fazi.
Proces brtvljenja okvira može se izvesti na nekoliko načina.
Izotermna metoda omogućava prolaz plina koji sadrži ugljik preko površine zagrijanog okvira pri relativno umjerenom pritisku. Nedostatak je trajanje procesa, stvaranje površinske kore koja sprječava prodor plina u okvir. Ova metoda je najefikasnija za proizvode male debljine.
U drugoj metodi, razlika tlaka se uspostavlja po cijeloj debljini okvira, a plin koji sadrži ugljik se prisilno filtrira kroz njega. Prisilna filtracija ubrzava proces zbijanja i uvelike povećava debljinu impregnacije. Međutim, zbog smanjenja koncentracije plina koji sadrži ugljik preko debljine sloja, struktura materijala ispada neravnomjerno gusta.
Najrasprostranjenija je termogradijentna metoda, kada se uspostavlja određena temperaturna razlika po cijeloj debljini poroznog okvira i plin koji sadrži ugljik prolazi sa strane površine s niskom temperaturom. U ovom slučaju je isključeno stvaranje površinske kore, što doprinosi proizvodnji visokokvalitetnog materijala. Ova metoda je najefikasnija kod zbijanja okvira srednje i velike debljine.
Tokom termičke razgradnje ugljovodonika u gasnoj fazi, istovremeno se odvijaju različiti hemijski procesi, koji rezultiraju lakšim i težim ugljovodonicima, vodonikom i raznim čvrstim ugljeničnim produktima. Struktura i svojstva ugljeničnih proizvoda su raznoliki i zavise od uslova procesa. Na primjer, proizvodi termičke razgradnje, ovisno o vanjskom geometrijskom obliku, sadrže:
slojeviti ili sjajni ugljik, nazvan pirougljik (PU);
Vlaknasti ili filamentni ugljik; ugljenik u raspršenom stanju ili čađ.
Formiranje PU odvija se u širokom temperaturnom rasponu od 700 do 3000°C. Sastav početnih gasova određuje prinos PU i brzinu njegovog taloženja. Najveći prinos PU se dobija iz metana, koji ima najmanju molekulsku masu. Ugljikovodici visoke molekularne težine imaju povećan prinos čađi. U ovom slučaju, pritisak gasa u reaktoru je bitan.
Postoje dvije glavne vrste PU, čija struktura i svojstva su određene temperaturom formiranja: niska temperatura (1000 - 1100°C) i visoka temperatura (1400 - 2200°C), koja se naziva pirografit.
Proces taloženja PU u gasnoj fazi odvija se u instalaciji (slika 1.29), koja se sastoji od vodeno hlađenog reaktora, kontrolne stanice za sisteme snabdevanja prirodnim gasom, stvarajući vakuum, rashladnu i energetsku opremu. Radni komad - karbonski okvir (4) montiran je na grafitne grijače (3) u sendviču između strujnih vodova (2). Nakon evakuacije iz komore, prirodni gas se dovodi u reaktor. Grejanje se vrši jednosmernom strujom koja prolazi kroz grejač (3), regulacija temperature - pokretnim!hromel-alumel termoelementima (5) smeštenim u kvarcne poklopce.Na početku procesa termoelement se ugrađuje sa spojem na grejaču površina - centar obratka prema periferiji.
U slučaju taloženja PU u gasnoj fazi, jedan od kriterijuma za kvalitet dobijenog materijala je njegova gustina. To je funkcija mnogih parametara i ovisi o gustoći okvira, brzini fronta pirolize, koncentraciji reagensa i tlaku plina u reaktoru.
Formiranje pirolitičkog ugljika iz gasne faze na UHV uglavnom se odvija na temperaturama od 1100-1500°C i smanjenom pritisku u atmosferi koja sadrži 91-93% metana i 7-9% argona. Grafitizacija se vrši u inertnoj atmosferi.
Tehnološki proces dobijanja CCCM metodom tečne faze!* obuhvata izradu poroznog okvira, njegovu impregnaciju tečnim ugljovodonicima, karbonizaciju pod pritiskom i grafitizaciju. Prilikom odabira impregnacionog materijala za impregnaciju uzimaju se u obzir sljedeće karakteristike:
viskozitet;
izduvni koks;
mikrostruktura koksa;
Kristalna struktura koksa.
Sve ove karakteristike zavise od pritiska i temperature u procesu* ugljik-ugljik kompozita. Kao smole najčešće se koriste fenolne, poliamidne, polivinilsiloksanske, polifenilsiloksanske, furfurilne i epoksi novolačne smole. Progresivan i obećavajući pravac je upotreba smola naftnog i ugljenog porijekla kao materijala za impregnaciju. Ova veziva imaju sljedeće prednosti: nisku cijenu, visok sadržaj ugljika uz zadržavanje termoplastičnosti i sposobnost grafitizacije pripremljenih mezofaznih smola. Nedostaci uključuju: toksičnost, nepostojanost kvalitete.
W
Rice. 1.29. Šema ugradnje termogradijentne metode taloženja pirougljika u gasnoj fazi: 1 - vodeno hlađeni reaktor, 2 - strujni vodovi, 3 - grijač, 4 - karbonski okvir, 5 - termoelement u kvarcnoj cijevi, 6 - mehanizam pokreta termoelementa , 7 - vodeni omotač; tokovi: I - gas, II - gasoviti produkti pirolize, W - voda.
Hemijski sastav i svojstva smole variraju u širokom rasponu u zavisnosti od prirode sirovine i tehnoloških uslova. Pod određenim uslovima, tečno-kristalna faza (mezofaza) može nastati i rasti u smoli, što osigurava stvaranje anizotropnog grafitizirajućeg koksa. S tim u vezi, visine se trenutno razlikuju kao izotropne (obične, nemezofazne) i anizotropne (mezofazne).
Pri niskotemperaturnoj karbonizaciji (550 - 650°C), mezofaza prelazi u čvrsti polukoks. Ovaj proces je praćen bubrenjem pod djelovanjem nastalih plinova, što dovodi do stvaranja fino porozne strukture koksa. Prilikom bubrenja dolazi do duboke deformacije koksa i povećanja broja neispravnih struktura, što pri naknadnoj toplinskoj obradi dovodi do pojave pukotina skupljanja.
Formiranje strukture i svojstava ugljično-koksne matrice ovisi o uvjetima toplinske obrade, koji se uvjetno mogu podijeliti u nekoliko faza:
Karbonizacija (900 - 1423°C) - razgradnja organskih jedinjenja
i formiranje molekularno uređene strukture ugljen-koksa
pretkristalizacija (1400 - 2000°C) - uređenje atoma yi
lerod u savršeniju strukturu sa formiranjem tzv<
osnovni oblici ugljika;
homogena grafitizacija (2000 - 3000°C) - prelazna transformacija; bilo koji oblici ugljika u kristalni grafit.
Na sl. 1.30 prikazuje dijagram instalacije za impregnaciju karbonskih tkanina.
Rice. 1.30. Šema instalacije za impregnaciju karbonske tkanine: 1 - potrošni namotaj, 2 - karbonska tkanina, 3 - tlačni valjci, 4 - električna peć, 5 - uređaj koji reguliše brzinu dovoda tkanine, 6 - prijemni kotur; 7 - električni pogon, 8 - kupatilo
Tkanina se odmotava od dovodnog kotura (1) i prolazi kroz vaš kotur (8), u kojem tri brze miješalice intenzivno miješaju prah smole s vodom, stvarajući stabilnu smjesu vodene smole. IIj daljim prolaskom tkanine kroz potisne valjke (3) i elektron 1 (4), voda isparava i smola, otapanjem, impregnira tkaninu. Dobijeni prepreg uz pomoć elektro pogona (7) i tkanine Uređaj za kontrolu brzine pomaka (5) je namotan na namotani kalem (6).Na izlazu iz peći, traka se pritisne osovinom zagrijanom na 100 - 120°C i istiskuje! korak u zapremini tkanine.
Predimpregnacija poroznog karbonskog okvira sa smolom može se izvesti pod pritiskom od 0,5 do 3 MPa, karbonizacija - pri pritisku od 100 - 200 MPa i temperaturi od 900 - 1100°C.
Karakteristika CCCM-a je relativno visoka poroznost karbonske matrice, kao i njezino sjecište s pukotinama u smjeru okomitom na punilo. Pukotine u matrici nastaju kada se proizvod ohladi sa proizvodne temperature (3000°C) na sobnu temperaturu zbog visokih termičkih naprezanja. Da bi se eliminisala poroznost, operacija impregnacije-karbonizacije praćena grafitizacijom i operacija impregnacije pirokarbonom se ponavljaju nekoliko puta (slika 1.31).
Nakon višestrukih ponavljanja ciklusa impregnacije-karbonizacije, gustina materijala može dostići 2000 - 2100 kg/m 3 . Ako temperatura obrade ne prelazi 800 - 1500°C, dolazi do karbonizacije veziva, a na temperaturama od 2300 - 3000°C dobija se grafitizirani materijal. Karbonizacija karbonskih vlakana provodi se u struji inertnog plina ili redukcijske atmosfere s povećanim tlakom uz izotermno, dinamičko ili "stepeno zagrijavanje"; grafitizacija - u inertnoj atmosferi.
karbonska vlakna
Namotaj zavojnice 3 \ ^Proizvodnja
proizvodi za pletenje na veliko
strukture \
Firmware
Impregnacija smole
* Karbonacija
Reimpregnacija Rekarbonizacija
Grafitizacija Sl. 1.31. Shema za dobivanje CCCM metodom impregnacije
Kombinirana ili složena metoda za dobivanje CCCM može se implementirati prema sljedećim šemama:
Smola impregnacija poroznog okvira, karbonizacija pod pritiskom, dodatno zbijanje PU iz gasne faze;
Zbijanje okvira od PU od gasne faze do impregnacije unapred određene gustine smolom praćeno karbonizacijom, mehaničkom obradom, zgušnjavanjem PU.
Ova metoda osigurava maksimalnu gustoću, visoke fizičke i mehaničke karakteristike i ne zahtijeva dodatnu opremu.
U slučajevima kada se karbonizacija CCCM vrši bez pritiska
Proces se može izvesti u konvencionalnom pečenju (plinska komora)
šolje, čiji je dizajn razmatran ranije. Tehnologija proizvodnje]
CCCM metodom tečne faze u smislu karbonizacije pod pritiskom mogu<
realizovati pomoću presa.
Grafitizacija (grafitizacija) se provodi u Acheson pećima, o čijem dizajnu je bilo riječi u prethodnim poglavljima.
Svojstva CCCM variraju u širokom rasponu. Snaga karboniziranog CCCM proporcionalna je gustoći. Grafitizacija karboniziranog: nogo CCCM povećava njegovu snagu. Snaga CCCM baziranog na visokim: jakim CF-ovima je veća od jačine CM-ova zasnovanih na CF-ovima visokog modula, više! nyh na različitim temperaturama obrade. Jedinstvena svojstva CCCM-a uključuju otpornost na visoke temperature u inertnim i redukcijskim medijima. U smislu svoje sposobnosti da zadrži svoj oblik i fizička i mehanička svojstva u ovim medijima, CCCM nadmašuje poznate konstrukcijske materijale. Neki CCCM, posebno oni dobiveni karbonizacijom karbonskih vlakana na bazi organskih polimera, karakteriziraju povećanje čvrstoće s povećanjem radne temperature od 20 do 2700°C. Na temperaturama iznad 3000°C, CCCM rade kratko, jer počinje intenzivna sublimacija grafita. Što je kristalna struktura grafita savršenija, to je viša temperatura i niža stopa termodestruktivnih procesa. Osobine] CCCM promjena u zraku uz produženo izlaganje relativno niskim temperaturama. Dakle, na 400 - 650 ° C u zraku se javlja! oksidacija CCCM i, kao rezultat, brzo smanjenje snage kao rezultat. ta povećanja poroznosti. Matrična oksidacija je ispred oksidacije HC, npr< ли последние имеют более совершенную структуру углерода. Скорость оки>CCCM se smanjuje s povećanjem temperature njihove proizvodnje i smanjenjem broja nedostataka. Efikasno sprečava oksidaciju CCCM pr< питка их кремнийорганическими соединениями из-за образования карбида оксида кремния.
Na sl. 1.32 prikazana su područja primjene CCCM.
otporan na obroke
Rice. 3.32. Područja primjene CCCM u uvjetima velikih toplinskih opterećenja
Dakle, CCCM se koriste u različitim granama tehnologije u slučajevima kada su tradicionalni materijali neoperativni, tj. u uslovima visokih termičkih opterećenja i u jedinicama trenja.
T kompozitna tehnologija rješava problem dobijanja očvrslih materijala. Reč tehnologija dolazi od dve grčke reči: techne - zanatstvo i logos - reč, učenje. Obično u nazivima ovog tipa drugi dio "logija" odgovara pojmu "nauka". Na primjer, zoologija je nauka o životinjama, geologija je nauka o strukturi Zemlje. Po analogiji, tehnologiju treba definisati kao nauku o zanatstvu.
Tehnologija kompozita - Sekcija za tehnologiju materijala
Ali riječ "nauka" pored riječi "tehnologija" pojavila se relativno nedavno. Tehnologija se obično definira kao skup metoda. Ako je u pitanju tehnologija materijala, onda je ovo skup metoda za dobijanje i obradu materijala.
Kompozitna tehnologija je zadatak stručnjaka
Uzmimo za primjer specijalista kompozitne tehnologije. Koje zadatke mora riješiti? Evo jednog od njih. Danci: vlakna bora namotana na bobine; aluminij (u bilo kojem obliku - listovi, žica, prah, talina) možete odabrati po vlastitom nahođenju. Potrebno: spojiti vlakna i aluminijsku matricu jedno s drugim, dok se dobije bor-aluminij visoke čvrstoće. Tehnolog mora odlučiti kako to učiniti. Da budemo precizniji, razgovarajmo o tome kako dobiti takav kompozit u obliku lima, u kojem su sva vlakna ravnomjerno raspoređena po poprečnom presjeku i naslagana paralelno jedno s drugim. Da biste riješili problem, morate odgovoriti na tri osnovna pitanja:- Kako osigurati polaganje vlakana u datom smjeru?
- Kako uvesti vlakna u matricu da bi se dobio list sa traženom strukturom i svojstvima?
- Kako spriječiti omekšavanje i uništavanje vlakana u procesu izrade materijala, a istovremeno osigurati njihovu čvrstu vezu sa matricom?
Kako orijentirati vlakna u kompozitu
Počnimo redom. Kako orijentirati vlakna u kompozitu? Da su dovoljno debele, poput čeličnih šipki kojima su ojačane, ne bi bilo posebnih problema. Možete staviti jednu po jednu u posebno pripremljena gnijezda.
Kako umetnuti vlakna u matriks
Ali bolje je to učiniti drugačije. Koristite sam materijal matrice kao pričvršćivač. Tada možete izvršiti dva zadatka odjednom kako biste pravilno održavali kompozitnu tehnologiju: popraviti vlakna u željenom položaju i istovremeno unesite ih u matricu, odnosno odgovoriti na drugo glavno pitanje našeg zadatka. Misao je dobra. Ali opet se javlja ista opsesija – kako? Kako uraditi? Ne možete bez znanja fizike i hemije.Elektrohemijska metoda
Može biti korišteno elektrohemijska metoda, nanošenje galvanskog premaza od matričnog metala na bubanj sa namotanim vlaknima. U principu nije teško, ali:- oduzima puno vremena
- ne mogu se svi metali primijeniti na ovaj način,
- teško je obezbediti željeni sastav matrice kada su u pitanju složene legure.
Plazma prskanje premaza
A evo najprikladnije opcije. Koristi plazma prskanje premaza. Ovom metodom, materijal matriksa se topi mlazom plazme niske temperature (jonizovani gas sa prosečnom temperaturom od oko 10.000 K), istom strujom se raspršuje i prenosi na površinu bubnja, pokrivajući vlakna i popunjavanjem praznina između njih. Protok plazme se dobija pomoću posebnog uređaja - plazma baklje, u kojoj se radni gas (azot, argon, vodonik, helijum, itd.) ionizira pod dejstvom lučnog pražnjenja. Iako se plazma formirana u konvencionalnim plazmatronima naziva niskotemperaturnom, ova "niska" temperatura (10.000 K) sasvim je dovoljna da se otopi bilo koji od materijala koji postoje u prirodi. Kapljice rastopljenog metala dospiju do hladnog bubnja i, dajući mu toplinu, kristaliziraju se, formirajući jednoličnu prevlaku na bubnju, ako se ravnomjerno okreće. Materijal koji se raspršuje (u našem slučaju aluminijum) obično se uvodi u mlaz plazme u obliku praha ili žice. Izvana, proces nanošenja plazma premaza podsjeća na slikanje zračnim kistom. Samo umjesto zračnog kista - plazma baklja, a umjesto boje - matrična legura. U principu, nije potrebno koristiti plazmu u tu svrhu, možete se snaći s plinskim plamenikom ili drugim uređajem, ali plazma prskanje je vrlo zgodno i široko se koristi u stvaranju kompozita. Ojačani monosloj koji se dobije nakon prskanja seče duž jedne od generatrisa cilindra i odvija se u ravninu. Čvrstoća premaza je dovoljna da spriječi pomicanje vlakana jedno u odnosu na drugo, ali nije dovoljna da osigura visoku čvrstoću kompozita. Debljina nastalih monoslojeva je obično jedan i pol do dva prečnika vlakana, odnosno oko 200 mikrona, a nama je, da podsjetim, potreban list debljine 5 mm. Kako biti? Opet "kako?".Valjanje monoslojeva
Ovoga puta ne morate dugo tražiti odgovor: od dobijenih jednoslojeva potrebno je napraviti lisnatu tortu, odnosno sakupiti ih u vrećicu potrebne debljine i nekako sabiti, povezujući ih neraskidivo jedno sa drugim. To se može uraditi npr. valjanje monoslojeva ili vruće presovanje. U prvom slučaju, pakovanje se zagreva u rerni i provlači između rolni koje se okreću. Prilikom valjanja, monoslojevi se spajaju u monolitni materijal i matrični materijal se zbija u svakom monosloju, što dovodi do povećanja čvrstoće matrice i jačine njene veze sa vlaknima.Vruće presovanje monoslojeva
Ponekad je svrsishodnije kompaktirati jednoslojne pakete ne valjanjem, već pomoću vruće presovanje. Da bi se to postiglo, postavljaju se u kalup čija dužina i širina radne ravni odgovaraju dimenzijama monoslojeva i odozgo se pritiskaju bušilicom. Kalup se zagrijava tako da se može održati potrebna temperatura procesa. Zagrijano pakovanje je zbijeno, pa otuda i naziv - vruće presovanje. Da bi se stvorila jaka veza između monoslojeva i da bi se sve čestice nanesenog metala matrice zavarile jedna za drugu, formirajući monolit, potrebno je držati pod pritiskom, čime se omogućava difuzijskim procesima da obave svoj posao. Upravo ti procesi, zajedno sa pritiskom, obezbeđuju visoka mehanička svojstva našeg lisnatog testa. Zbog toga se ovaj način dobivanja kompozita ponekad naziva i difuzijsko zavarivanje.Tehnologija kompozita u obliku šipke ili složenog profila
S obzirom na zadatak koji je pred nama, odgovorili smo na drugo pitanje – kako uvesti vlakna u matricu. Ali što ako trebate dobiti kompozit u obliku šipke ili složenog profila? Još jedno "kako". Opet možete pribjeći motajući paketi od jednoslojnih, ali ne u glatkim rolnama, već u kalibriranim, odnosno sa posebnim izrezima koji odgovaraju traženoj konfiguraciji. Ili možete koristiti tzv metode tečne faze kada je matrica u tečnom stanju u procesu dobijanja kompozita. Vlakna, koja se odmotaju od namotaja (broj zavojnica jednak je broju vlakana u kompozitu), prolaze bez dodirivanja jedno drugo kroz kadu sa rastopljenim matričnim metalom, mokre se njome i ulaze u predilicu koja formira šipku. željenog dijela. Nakon toga, štap se hladi, metal matrice se stvrdne, formirajući kompozitni materijal s vlaknima. Na ovaj način se mogu dobiti šipke raznih profila. Proizvodi sa složenim profilom, kao što su lopatice turbine, povoljno se dobijaju impregnacijom. U kalup se postavljaju vlakna čija radna šupljina odgovara obliku oštrice (kako to učiniti je posebno pitanje koje sada nećemo razmatrati, ali to se može učiniti, iako ne lako), a zatim tečnost matrični metal se sipa u kalup. Praznine između vlakana su obično male, te ih je rastopljeni metal teško popuniti, ali ih je potrebno popuniti, i to što je brže moguće kako se vlakna ne bi imala vremena otopiti u matrici. Stoga se u većini slučajeva impregnacija vrši pod pritiskom. Kalup za livenje se evakuiše, a tečni metal ulazi u njega pod atmosferskim pritiskom. U pravilu je za brzu i pouzdanu impregnaciju dovoljna razlika tlaka od jedne atmosfere. Ali to je samo u slučaju kada su vlakna navlažena rastopljenim metalom matriksa. Ako nije, onda morate nešto poduzeti. Na primjer, karbonska vlakna se ne vlaže tekućim aluminijem; stoga se ugljen-aluminij ne može dobiti jednostavnim impregnacijom grafitnih filamenata aluminijem. Ali ako su ove niti prethodno premazane najtanjim slojem hroma ili nikla (dovoljno je nanijeti premaz debljine jednog mikrometra), koji su dobro navlaženi aluminijem, osigurat će se impregnacija i može se dobiti kompozit. Glavno zanimanje tehnologa je da odgovori na pitanje "kako?". Kako to učiniti? Tačni odgovori na ovo pitanje mogu se dati ako su poznati odgovori na pitanje "zašto?". Ako zamislite automehaničara koji zna zategnuti vijke i matice, ali ne poznaje strukturu automobila. Bezvrijedno za njega. Slično, tehnolog koji ne razumije fiziku procesa koji se dešavaju prilikom dobijanja materijala je inferiorni specijalista. Na primjer, tehnolog zna da u mnogim slučajevima kompozit omekša nakon zagrijavanja. Odmah se javlja problem – kako se nositi s tim? Ovo pitanje je slično trećem "kako?" pitanju na početku razgovora. A da biste riješili ovaj problem, morate znati zašto dolazi do omekšavanja kompozita. Odgovor na ova pitanja daje kompozitna tehnologija.Robotski kompleks za mehaničku obradu proizvoda od kompozitnih materijala dizajniran je za mehanizaciju i automatizaciju jedne od radno najintenzivnijih operacija u tehnološkom ciklusu:
- Obrezivanje i uklanjanje tehnološkog blica
- Glodanje žljebova, udubljenja i pozicionera za ugrađene elemente
- Bušenje i glodanje rupa složenog oblika
- Glodanje rupa velikih dimenzija (prozorski otvori, otvori, itd.)
Robotski kompleks omogućava vam da obezbedite sledeće pogodnosti:
- Povećana brzina obrade u odnosu na ručnu obradu
- Visoka ponovljivost i kvalitet obrade
- Glodanje visokog kvaliteta rubova "u jednom prolazu"
- Poboljšanje uslova rada
- Otvaranje dodatnih znanja intenzivnih poslova
At kontaktna metoda Nakon oblikovanja, stakleni materijal se ručno impregnira smolom četkom ili valjkom. Impregnacija se može vršiti istovremeno sa valjanjem u obliku, ili zasebno. Valjanje se vrši radi uklanjanja zraka iz laminata i ravnomjerne raspodjele veziva.
1U članku je prikazano trenutno stanje tehnologija za proizvodnju proizvoda od kompozitnih materijala, uključujući informacije o korištenim tehnologijama, softveru, opremi za izradu matrica, opremi za izradu kompozitnih proizvoda, opremi za kontrolu geometrije proizvoda i ispitivanju bez razaranja. .
kompozitnih materijala
softvera
oprema za izradu matrice
1. Moderni kompozitni materijali / ur. P. Krok i L. Brouman; per. sa engleskog. - M., 1978.
2. Dizajn i čvrstoća trupa brodova i brodova od stakloplastike. Inozemna brodogradnja 1965 - 1973 // Brodogradnja, 1973.
3. Frolov S.E. Metode stvaranja novih makronehomogenih kompozitnih materijala i tehnološka rješenja za izradu trupnih konstrukcija od njih // Brodogradnja br. 3 2003, str. 55-59.
4. CAE - tehnologije u 2012: pregled dostignuća i analiza tržišta. – CAD/CAM/CAE Observer #4 (80) / 2013.
5. Intervju sa V.A. Seredka i A.Yu. Sofronov CAD/CAM/CAE Observeru #2 (78) / 2013.
6. Pametne tehnologije za industriju aviona. Povećanje konkurentnosti domaćih zrakoplovnih preduzeća na primjeru zajedničkih projekata kompanije Solver i JSC VASO // CAD i grafika, br. 1. 2011. str. 56-62.
7. Lukjanov N.P. Iskustvo u korištenju kompozitnih materijala za izgradnju PMO brodova // Brodogradnja. br. 3. 2007. S. 19-26.
Kompozitni materijal je materijal čija se struktura sastoji od nekoliko komponenti koje se razlikuju po svojim fizičkim i mehaničkim svojstvima: metalne ili nemetalne matrice sa datom raspodjelom učvršćivača u njima, njihova kombinacija daje kompozitnom materijalu nova svojstva. Prema prirodi strukture, kompozitni materijali se dijele na vlaknaste, ojačane kontinuiranim vlaknima i brkovima, materijale ojačane disperzijom dobivene unošenjem dispergiranih čestica učvršćivača u matricu, slojevite materijale nastale presovanjem ili valjanjem različitih materijala.
Danas su kompozitni materijali posebno traženi u raznim industrijama. Prvi brodovi od stakloplastike napravljeni su u drugoj polovini 1930-ih. Od 50-ih godina u svijetu se raširila brodogradnja od stakloplastike, izgrađen je značajan broj jahti, radnih i spasilačkih čamaca i ribarskih čamaca, desantnih plovila itd. Jedna od prvih primjena kompozitnih materijala u avijaciji bila je izrada panela od karbonskih vlakana 1967. za stražnju ivicu krila aviona F-111A. Posljednjih godina u avio-svemirskim proizvodima sve je više moguće sresti konstrukcije od troslojnog „sendviča“ sa aluminijskim saćastim punilom i koricama od karbonskih vlakana. Trenutno je oko 50% ukupne mase Boeinga 787 ili Airbusa A350 sastavljeno od kompozitnih materijala. U automobilskoj industriji dugo se koriste kompozitni materijali, uglavnom je razvijena tehnologija za proizvodnju aerodinamičkog kompleta karoserije. Kompozitni materijali se u ograničenoj mjeri koriste za proizvodnju dijelova ovjesa i motora.
Međutim, do nedavno su poduzeća uglavnom koristila ručno polaganje dijelova od kompozita, a serijska proizvodnja proizvedenih proizvoda nije zahtijevala duboku automatizaciju procesa. Danas, sa razvojem konkurencije na tržištu, ne može se bez savremenih alata za projektovanje i pripremu proizvodnje, kao i bez efikasne opreme za rad sa kompozitima.
Tehnologije za izradu proizvoda od kompozitnih materijala
U većini slučajeva, hemijski očvršćavajuća termoreaktivna smola se koristi kao vezivno punilo, a proces očvršćavanja karakteriše egzotermna hemijska reakcija. Uglavnom se koriste poliesterske, epoksidne, fenolne i visokotemperaturne smole. Najčešće se u proizvodnji dijelova složene konfiguracije koriste tehnologije čija je suština polaganje "suhe" podloge nakon čega slijedi impregnacija vezivom ("mokro" oblikovanje, namotavanje, brizganje, Resin Transfer Molding / RTM) ili naizmjenično polaganje "suhe" podloge filmskim ljepilom (vakuumska impregnacija, Resin Film Infusion / RFI). Postoji nekoliko glavnih tehnologija za proizvodnju dijelova od kompozitnih materijala, uključujući ručne i automatizirane metode:
- impregnacija armaturnih vlakana matričnim materijalom;
- formiranje u kalupu traka učvršćivača i matrice dobivene namotavanjem;
- hladno prešanje komponenti praćeno sinterovanjem;
- elektrohemijsko premazivanje vlakana s naknadnim presovanjem;
- taloženje matrice raspršivanjem plazme na učvršćivač, nakon čega slijedi kompresija;
- šaržno difuzijsko zavarivanje jednoslojnih traka komponenti;
- spojno valjanje armaturnih elemenata sa matricom itd.
Osim toga, široko je rasprostranjena tehnologija izrade dijelova pomoću preprega (poluproizvoda, koji su osnovni materijal impregnirani vezivnim sastavom).
Softver
Zadatak dizajniranja proizvoda od kompozitnih materijala je ispravan odabir kompozicije koja osigurava kombinaciju svojstava potrebnih u određenom operativnom slučaju. Prilikom projektovanja ojačanih polimernih kompozitnih materijala uveliko se koristi kompjuterska obrada podataka za koju je razvijen veliki broj različitih softverskih proizvoda. Njihova upotreba omogućava poboljšanje kvaliteta proizvoda, smanjenje trajanja razvoja i organizacije proizvodnje konstrukcija, sveobuhvatno, efikasno i brzo rešavanje problema njihovog racionalnog projektovanja. Uzimanje u obzir neujednačenih opterećenja omogućava projektiranje strukture trupa od armiranog kompozita različite debljine, koja može varirati desetke puta.
Savremeni softverski proizvodi mogu se podijeliti u dvije grupe: oni koji vrše analizu serije laminata u "dvodimenzionalnoj" ili "greda/ploča" formulaciji i u trodimenzionalnoj. Prva grupa su programi kao što su Laminator, VerctorLam Cirrus itd. "Trodimenzionalno" rješenje je metoda konačnih elemenata, a među dostupnim softverskim proizvodima postoji veliki izbor. Na tržištu "tehnologije kompozitnog modeliranja" postoje različiti softverski proizvodi: FiberSim (Vistagy / Siemens PLM softver), Digimat (e-Xstream / MSC Software Corp.), Helius (Firehole Composites / Autodesk), ANSYS Composite PrepPost, ESAComp (Altair inženjering) i sl.
Gotovo sav specijalizovani softver različitih kompanija ima mogućnost integracije sa CAD sistemima visokog nivoa - Creo Elements/Pro, Siemens NX, CATIA. Općenito, rad je sljedeći: odabire se materijal sloja, određuju se opći parametri paketa slojeva, utvrđuje se metoda formiranja sloja, metoda sloj-po-sloj se koristi za proizvodnju jednostavnih dijelova, za složene proizvode, koriste se metode zonskog ili strukturalnog projektovanja. U procesu polaganja slojeva postavlja se njihov redoslijed. Ovisno o načinu proizvodnje proizvoda (ručno polaganje, oblikovanje, polaganje trake, polaganje vlakana), provodi se sloj po sloj analiza materijala na moguće deformacije. Sastav slojeva se prilagođava širini upotrijebljenog materijala.
Nakon što je formiranje slojeva završeno, korisnik dobiva podatke o proizvodu, što im omogućava da se koriste u različite svrhe, na primjer:
- izlaz u obliku projektne dokumentacije;
- koristiti kao početne podatke za rezanje materijala;
- početni podaci za laserski projektor za označavanje kontura mjesta za polaganje šara.
Prelazak na moderne tehnologije za projektovanje i pripremu proizvodnje proizvoda omogućava:
- smanjiti potrošnju kompozitnih materijala upotrebom preciznih razvrtača i mašina za sečenje;
- povećati brzinu i poboljšati kvalitetu ručnog polaganja materijala upotrebom preciznih blankova i laserskih projekcija mesta njihovog polaganja;
- postići visok nivo ponovljivosti proizvoda;
- smanjenje uticaja ljudskog faktora na kvalitet proizvedenih proizvoda;
- smanjenje zahtjeva za kvalifikacijom osoblja koje se bavi polaganjem.
Oprema za izradu matrice
Izrada master modela od drveta je dugotrajan i dugotrajan proces, za smanjenje vremena izrade matrice i povećanje tačnosti koriste se tro/petoosni CNC glodalice, kontrolno-mjerne mašine ili 3D skeneri.
Portalna petoosna glodalica, (slika 1), dostupna je samo velikim proizvođačima. Male kompanije koriste robotske komplekse za glodanje na linearnim blokovima (linearna robotska jedinica) (slika 2), ili izrađuju master modele od zalijepljenog obratka. U ovom slučaju, kao osnova izratka uzima se kruti šuplji okvir, koji je zalijepljen izvana, a zatim potpuno obrađen. Kompanije koje nemaju mogućnost obrade cijelog proizvoda idu drugačijim putem: prvo, pojednostavljeni 3D model proizvoda se gradi pomoću ravnina u CAD sistemu, a kruti okvir od šperploče se dizajnira na osnovu pojednostavljenog modela. Cijela vanjska površina je tada predstavljena u CAD sistemu kao obloga unutrašnjeg okvira. Dimenzije obloge su odabrane na način da se može glodati na postojećoj CNC glodalici (slika 3). Zatim se precizno sastavljen okvir zalijepi modelnom oblogom. Ovom metodom tačnost glavnog modela je manja i potrebna je ručna završna obrada spojeva obloga, ali to vam omogućava da kreirate proizvode čije dimenzije znatno premašuju mogućnosti postojećih CNC mašina.
Rice. 1. Petoosna glodalica MR 125, sposobna za obradu dijelova veličine 15x5 m i visine do 2,5 m
Rice. 2. Robotski kompleks za glodanje Kuka
Rice. 3. "Mala" petoosna glodalica
Oprema za izradu kompozita
Prvi korak u mehanizaciji procesa oblikovanja bila je primjena strojeva za impregnaciju, koji osim impregnacije, sastavljaju staklene tkanine ili stakloplastike u višeslojne vreće ukupne debljine 4-5 mm. Za mehanizaciju procesa, smanjenje vjerojatnosti pogreške osoblja i povećanje produktivnosti, na primjer, koristi se metoda prskanja, koja se može koristiti za dobivanje vanjske obloge, pregradnih ploča i drugih struktura od stakloplastike. Metoda prskanja omogućava mehanizirano dobivanje kalupnih kvadrata i pruža veću produktivnost rada u odnosu na kalupne kvadrate koji su ručno oblikovani od traka od stakloplastike ili stakloplastike. Sljedeća faza u razvoju proizvodnje proizvoda od kompozita je uvođenje instalacije za automatizirano namotavanje rasporeda punila od karbonskih vlakana. Prvi "robot" dizajniran za polaganje suhe rolne tkanine demonstrirala je američka kompanija Magnum Venus Plastech. Po prvi put u Rusiji takva oprema je uvedena u JSC VASO. Ova oprema omogućava proizvodnju kompozitnih delova dužine do 8 m i prečnika do 3 m (slika 4).
Da bi se olakšalo ručno polaganje tkanine i smanjio otpad, za automatsko sečenje tkanine/preprega koriste se mašine za sečenje, LAP i LPT laserski projektori za konturnu projekciju prilikom polaganja preprega na proizvodnu opremu. Pomoću modula za lasersku projekciju (slika 5) moguće je automatski generirati podatke za projekciju direktno iz 3D modela kompozitnog proizvoda. Ova šema rada značajno smanjuje vremenske troškove, povećava efikasnost procesa, smanjuje vjerovatnoću kvarova i grešaka, te olakšava upravljanje podacima. Softversko rezanje mašinsko-projekcijski laserski kompleks, u poređenju sa tradicionalnim polaganjem, smanjuje radni intenzitet rezanja za oko 50%, napornost polaganja za oko 30%, povećava stopu iskorišćenja materijala, odnosno možete uštedeti od 15 do 30% materijala.
Formiranje plastike ojačane karbonskim vlaknima metodom namotavanja omogućava dobivanje proizvoda s najvišim karakteristikama deformacije i čvrstoće. Metode namotavanja dijele se na "suhe" i "mokre". U prvom slučaju, prepregi se koriste za namotavanje u obliku niti, snopova ili traka. U drugom slučaju, armaturni materijali su impregnirani vezivom direktno tokom procesa namotavanja. Nedavno je razvijena oprema koja koristi kompjuterske sisteme za kontrolu uzorka orijentacije vlakana. To omogućava dobivanje cjevastih proizvoda sa zavojima i nepravilnim oblicima, kao i proizvoda složene geometrije. Oprema za namotavanje se razvija pomoću fleksibilne tehnologije, gdje se armaturni vlaknasti materijali mogu polagati na trn u bilo kojem smjeru.
Rice. 4 MAG Cincinnati Viper 1200 FPS mašina za namotavanje karbonskih vlakana
Rice. 5. Laserski sistem pozicioniranja (zeleni obris)
Oprema za provjeru geometrije i unutrašnje strukture proizvoda
Konture proizvoda često imaju krivolinijske generatrise, koje se ne mogu provjeriti tradicionalnim "plaz" metodama. Koristeći 3D skeniranje, možete odrediti koliko se fizički uzorak podudara s 3D računarskim modelom. Za 3D skeniranje možete koristiti i mašinu za koordinatno mjerenje tipa ruke (CMM) ili beskontaktni optički/laserski sistem za skeniranje. Međutim, kada se koriste beskontaktni sistemi za skeniranje, u pravilu ne mogu ispravno raditi sa zrcalnim i sjajnim površinama. Pri korištenju "mjernih krakova" bit će potrebno nekoliko uzastopnih resetiranja, jer je radni prostor, zbog dizajna mjernih krakova, obično ograničen na sferu polumjera 1,2-3,6 m.
Također, materijali od stakloplastike imaju niz problematičnih područja. Jedna od glavnih je kontrola kvaliteta gotovog proizvoda (odsustvo zračnih šupljina) i korozija tokom rada. Za ispitivanje bez razaranja brodskih trupova izrađenih od kompozita, X-zrake se široko koriste, ali imaju tendenciju da ga smanje iz više razloga. Nedavno su se počele pojavljivati publikacije koje opisuju detekciju raslojavanja infracrvenom termografijom (termovizori). Istovremeno, i termovizijske i rendgenske NDT metode otkrivanja delaminacija ne dozvoljavaju mjerenje njihovih veličina i određivanje dubine defekata kako bi se procijenio njihov utjecaj na promjenu karakteristika čvrstoće.
Zaključak
Trenutno, u Rusiji, intenzivan razvoj automatizacije montaže kompozitnih proizvoda, uključujući opremu za kreiranje matrica, gotovo tek počinje. Najčešće se za "podešavanje" automobila izvode samo pojedinačni elementi aerodinamičkog kompleta karoserije. Uspešna je implementacija sistema FiberSIM na projektovanju i izgradnji baznog minolovca projekta 12700, kao i na VASO automatskoj mašini za polaganje tkanine. Ali ovo su izolirani primjeri, da bi se povećala konkurentnost potrebno je sveobuhvatno uvođenje novih tehnologija.
Bibliografska veza
Černišov E.A., Romanov A.D. SAVREMENE TEHNOLOGIJE ZA PROIZVODNJU PROIZVODA OD KOMPOZITNIH MATERIJALA // Moderne znanstveno-intenzivne tehnologije. - 2014. - br. 2. - str. 46-51;URL: http://top-technologies.ru/ru/article/view?id=33649 (pristupljeno 25.11.2019.). Predstavljamo Vam časopise koje izdaje izdavačka kuća "Akademija prirodne istorije"